连铸保护渣概述
合金钢连铸保护渣的基本功能

1.3保护蕾保温性蹙的评价方法 通常模拟保护碴在结晶器内的受热状况,在实验室采用底部单向加热的加热
炉.用热电偶翻量相同时刻时各渣层的温度分布或不同时刻时同一测量点的温度变 化情况,阻此数据来评价保护渣的保温性能【11.也可通过备渣层的温度分布采用模 型计算确定保护蓬的导温系数(测量装置见图1)【:】, 采用导温系数运一热伤性参 盏亲评价保护渣的保温性能更加直观、准确.从图2可知,粉末状和空心颗粒保护 渣的导温系数比实心颗粒小,因此它们的保温性更好.
}
l
等低告垒钢及台金锅时.碱度过高而润滑性错较差的保护渣惩易诱发铸坯皮下星欹
}
{
裂纹,握寝谷部裂纹及角裂纹.
在协调保护渣润滑与控甫Ⅱ传热功能的研究中.重庆大学通过采用对渣膜有着色
秘
全国特钢连铸委员会学术讨论击
2000'重庆
氧化物夹杂.针对不同类型的夹杂物及相应的钒种浇注:疑固特性,可采用不同的保
护渣理论和方法. 2.1 啊N和啊CN夹杂物的宰【化处理治
理论分析和大量生产实践均表明,含钛不锈钢在精烁、钢水转运及浇注过程牛。
容易产生1悄和TjCN夹杂物,它们是结晶器钢液面上出现“冷皮”现象的主要三
月面铜液洁净度,希望合金铜连铸保护渣具有较强的吸收夹杂物的能力.除此之外, 熔渣吸收夹杂后,其轱度、凝固温度、结晶性能婷物性参数应相对稳定,避免它们 的急剧变‘匕_危害铸垤质量和连铸工艺顺行.通常,可将舍金钢连铸过程中出现的常
见的典型夹杂物分为三类:钛化台物夹杂(1Ⅲ,TicN,Tj02),~:0,类夹杂.稀土
为了保证保护渣的润滑特性,直控制保护淹在冷擞过程中结晶湿度较低,甚三
不析出晶体,通过粘度一温度关系彗线It∞”4l可考察保护渣的润滑特性。一翌要求
小方坯连铸中碳钢铸坯表面缺陷与保护渣性能选择
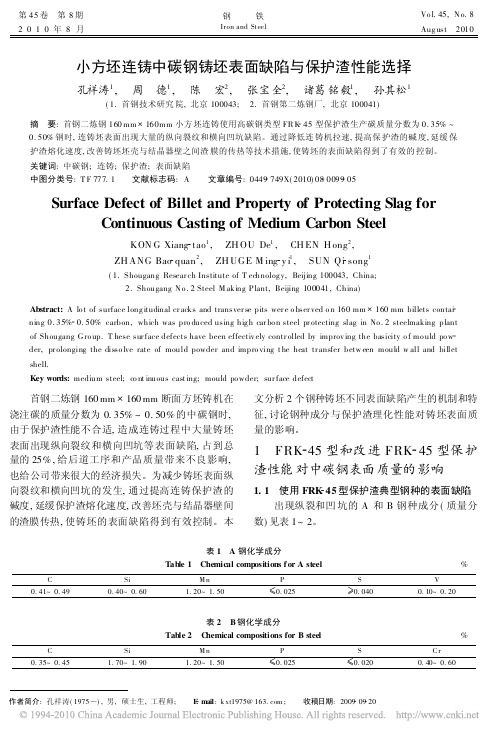
第45卷 第8期 2010年8月钢铁Iron and SteelVo l.45,N o.8Aug ust 2010小方坯连铸中碳钢铸坯表面缺陷与保护渣性能选择孔祥涛1, 周 德1, 陈 宏2, 张宝全2, 诸葛铭毅1, 孙其松1(1.首钢技术研究院,北京100043; 2.首钢第二炼钢厂,北京100041)摘 要:首钢二炼钢160mm 160mm 小方坯连铸使用高碳钢类型FR K 45型保护渣生产碳质量分数为0.35%~0.50%钢时,连铸坯表面出现大量的纵向裂纹和横向凹坑缺陷。
通过降低连铸机拉速,提高保护渣的碱度,延缓保护渣熔化速度,改善铸坯坯壳与结晶器壁之间渣膜的传热等技术措施,使铸坯的表面缺陷得到了有效的控制。
关键词:中碳钢;连铸;保护渣;表面缺陷中图分类号:T F 777.1 文献标志码:A 文章编号:0449 749X(2010)08 0099 05Surface Defect of Billet and Property of Protecting Slag forContinuous Casting of Medium Carbon SteelKON G Xiang tao 1, ZH OU De 1, CH EN H ong 2,ZH ANG Bao quan 2, ZH UGE M ing y i 1, SUN Qi song 1(1.Shougang Resear ch Institute of T echnolog y,Beijing 100043,China;2.Shougang N o.2Steel M aking P lant,Beijing 100041,China)Abstract:A lo t of surface long itudinal cr acks and transver se pits wer e o bser ved o n 160mm 160mm billets contai ning 0.35% 0.50%carbon,which was pro duced using hig h car bo n steel pr otecting slag in No.2steelmaking plant of Shougang G ro up.T hese sur face defects have been effectiv ely contr olled by improv ing the basicity o f mo uld po w der,pr olonging the disso lve rate of mould powder and impro ving t he heat tr ansfer betw een mould w all and billet shell.Key words:medium steel;co nt inuous cast ing;mould po wder;sur face defect作者简介:孔祥涛(1975 ),男,硕士生,工程师; E mail :k xt1975@ ; 收稿日期:2009 09 20首钢二炼钢160mm 160mm 断面方坯铸机在浇注碳的质量分数为0.35%~0.50%的中碳钢时,由于保护渣性能不合适,造成连铸过程中大量铸坯表面出现纵向裂纹和横向凹坑等表面缺陷,占到总量的25%,给后道工序和产品质量带来不良影响,也给公司带来很大的经济损失。
板坯连铸结晶器保护渣卷渣及其影响因素的研究
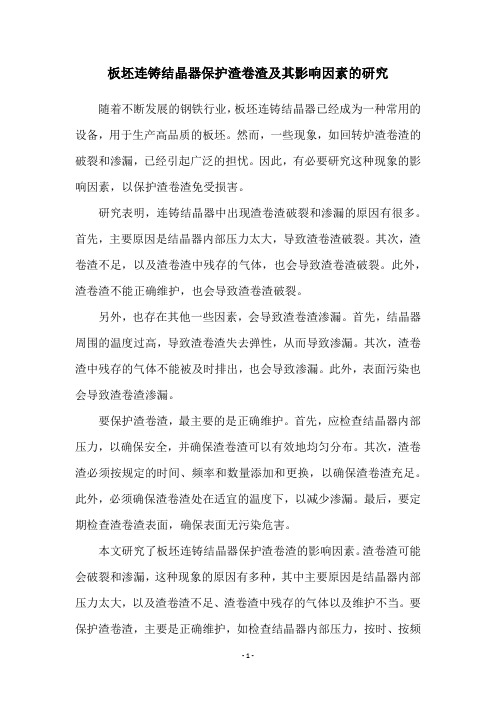
板坯连铸结晶器保护渣卷渣及其影响因素的研究随着不断发展的钢铁行业,板坯连铸结晶器已经成为一种常用的设备,用于生产高品质的板坯。
然而,一些现象,如回转炉渣卷渣的破裂和渗漏,已经引起广泛的担忧。
因此,有必要研究这种现象的影响因素,以保护渣卷渣免受损害。
研究表明,连铸结晶器中出现渣卷渣破裂和渗漏的原因有很多。
首先,主要原因是结晶器内部压力太大,导致渣卷渣破裂。
其次,渣卷渣不足,以及渣卷渣中残存的气体,也会导致渣卷渣破裂。
此外,渣卷渣不能正确维护,也会导致渣卷渣破裂。
另外,也存在其他一些因素,会导致渣卷渣渗漏。
首先,结晶器周围的温度过高,导致渣卷渣失去弹性,从而导致渗漏。
其次,渣卷渣中残存的气体不能被及时排出,也会导致渗漏。
此外,表面污染也会导致渣卷渣渗漏。
要保护渣卷渣,最主要的是正确维护。
首先,应检查结晶器内部压力,以确保安全,并确保渣卷渣可以有效地均匀分布。
其次,渣卷渣必须按规定的时间、频率和数量添加和更换,以确保渣卷渣充足。
此外,必须确保渣卷渣处在适宜的温度下,以减少渗漏。
最后,要定期检查渣卷渣表面,确保表面无污染危害。
本文研究了板坯连铸结晶器保护渣卷渣的影响因素。
渣卷渣可能会破裂和渗漏,这种现象的原因有多种,其中主要原因是结晶器内部压力太大,以及渣卷渣不足、渣卷渣中残存的气体以及维护不当。
要保护渣卷渣,主要是正确维护,如检查结晶器内部压力,按时、按频率、按数量添加和更换渣卷渣,保持温度适宜,以及定期检查渣卷渣表面,以防止渣卷渣受损害。
以上就是关于《板坯连铸结晶器保护渣卷渣及其影响因素的研究》的3000字文章。
保护渣简介

保护渣的性能测定一、保护渣的作用1)绝热保温向结晶器液面加固体保护渣覆盖其表面,减少钢液热损失。
由于保护渣的三层结构,钢液通过保护渣的散热量,比裸露状态的散热量要小10倍左右,从而避免了钢液面的冷凝结壳。
尤其是浸入式水口外壁四周覆盖了一层渣膜,减少了相应位置冷钢的聚集。
2)隔绝空气,防止钢液的二次氧化保护渣均匀地覆盖在结晶器钢液表面,阻止了空气与钢液的直接接触,再加上保护渣中碳粉的氧化产物和碳酸盐受热分解溢出的气体,可驱赶弯月面处的空气,有效地避免了钢液的二次氧化。
3)吸收非金属夹杂物,净化钢液加入的保护渣在钢液面上形成一层液渣,具有良好的吸附和溶解从钢液中上浮的夹杂物,达到清洁钢液作用。
4)在铸坯凝固坯壳与结晶器内壁间形成润滑渣膜在结晶器的弯月面处有保护渣的液渣存在,由于结晶器的振动和结晶器壁与坯壳间气隙的毛细管作用。
将液渣吸入,并填充于气隙之中,形成渣膜。
在正常情况下,与坯壳接触的一侧,由于温度高,渣膜仍保持足够的流动性,在结晶器壁与坯壳之间起着良好的润滑作用,防止了铸坯与结晶器壁的粘结;减少了拉坯阻力;渣膜厚度一般在50~200μm5)改善了结晶器与坯壳间的传热在结晶器内,由于钢液凝固形成的凝固收缩,铸坯凝固壳脱离结晶器壁产生了气隙,使热阻增加,影响铸坯的散热。
保护渣的液渣均匀的充满气隙,减小了气隙的热阻。
据实测,气隙中充满空气时导热系数仅为0.09W/m·K,而充满渣膜时的导热系数为1.2W/m·K,由此可见,渣膜的导热系数是充满空气时的13倍。
由于气隙充满渣膜,明显地改善了结晶器的传热,使坯壳得以均匀生长。
二、保护渣的构成1)液渣层当固体粉状或粒状保护渣加入结晶器后与钢液面相接触,由于保护渣的熔点只有1050℃~1100℃,因而靠钢液提供的热量使部分保护渣熔化,形成液渣覆盖层。
这个液渣覆盖层约10~15mm厚,它保护钢液不被氧化,又减缓了沿保护渣厚度方向的传热。
在拉坯过程中,结晶器上下振动。
结晶器保护渣概要课件

保护渣的粒度与结构
保护渣的粒度大小和结构对保 护渣的功能和性能有重要影响。
粒度太大会影响保护渣的流动 性,粒度太小则会影响保护渣 的粘附性和热稳定性。
02
结晶器保护渣的化学组成与物 理性能
保护渣的化学组成
保护渣主要由硅酸盐矿物、玻璃 相、碳质材料等组成。
不同种类的保护渣的化学组成不 同,主要通过改变硅酸盐矿物和 玻璃相的比例来调节保护渣的物
理性能。
碳质材料在保护渣中主要起到粘 结剂的作用,提高保护渣的粘度
和稳定性。
保护渣的物理性能
保护渣应具有良好的流动性、粘附性和热稳定性。
均匀性
保护渣在结晶器中的分布应尽可能均匀,以避免局部过热或 产生偏析。可以通过优化保护渣的粒度、密度和流动性等性 质,以及采用先进的给料装置和工艺控制技术,来提高保护 渣的均匀性。
保护渣的粒度与结构调整
粒度
保护渣的粒度对其流动性和吸收能力具有重要影响。可以根据结晶器的尺寸和 工艺要求,选择合适的粒度分布,以提高保护渣的流动性和吸收效果。
保护渣在结晶器中能够对钢水流动起 到稳定作用,主要表现在以下几个方 面
保护渣能够吸收钢水表面的渣子和杂 质,减少钢水流速的变化,稳定钢水 流动;
保护渣能够覆盖和保护钢水表面,减 少钢水的蒸发和流动,稳定钢水温度;
保护渣能够通过自身形变和与结晶器 壁的摩擦,消耗铸坯表面的液态薄膜, 有利于结晶器振动,稳定铸坯形状和 尺寸。
保护渣的结构应尽可能均匀, 避免出现大颗粒聚集和空隙。
03
保护渣简介

我叫保护渣,是钢铁工业冶金辅料大家庭中的一员,可由以SiO2、CaO、Al2O3为主要成分的硅酸盐基料,如水泥熟料、硅灰石、长石、石英、火山灰等配制而成。
根据形态的不同,我分为粉末型、实心颗粒型和空心颗粒型。
根据基料加工和熔剂配入方式的不同,我的生产方法有预熔型、混合型和烧结型。
混合型就是将各种原材料混合均匀、磨细、烘干或成浆、喷雾造粒;预熔型就是将原料和熔剂进行预熔,去除其中的挥发物,形成保护渣的基料,配入少量熔剂和炭质材料,制成各种需要的产品系列;烧结型生产方法既避免了无氟预熔渣在炉内下料困难、流动性差、基料熔化不均的现象,又可解决混合型生产方法中熔剂在使用过程中挥发大和水分难去除的问题。
在连铸作业时,每吨钢水中我的用量只有一公斤左右,虽然我的用量很少,却是影响连铸稳定生产和改善铸坯表面质量的关键,好比炒菜时的味精,有了我的参与,才能“烹饪”出平整光洁的铸坯。
我被加入至结晶器之后,在高温钢液的热量作用下,逐渐升温并发生烧结、熔化,在结晶器钢液面上形成双层、三层或多层的渣层结构,然后流入铸坯与结晶器壁的间隙中,在结晶器壁的冷却下,靠结晶器壁侧凝固形成固态渣膜,宛如鸡蛋清和鸡蛋壳之间的那层内膜,横亘在坯壳与结晶器之间,润滑铸坯并控制铸坯的传热。
随着结晶器振动和拉坯的进行,液渣和部分固渣膜被带出结晶器下口,在二冷水作用下与铸坯分离,由此完成保护渣的消耗过程。
我在进出结晶器的过程中,所发挥的作用可归结为:对结晶器钢液面绝热保温,避免钢液面结壳凝固;保护钢液面不受空气二次氧化;吸收钢液中上浮的夹杂物;润滑运动的铸坯;均匀和调节凝固坯壳向结晶器的传热。
而人们对于我的研究、生产和使用,就是如何有效地发挥这五项功能,确保不出现漏钢等生产事故并获得无缺陷的连铸坯。
根据连铸作业中所浇钢种、铸坯断面形状、大小、拉速和振动参数等的不同,技术人员经常为我量身打造在熔渣粘度、表面张力、熔化温度、熔化速度以及熔化均匀性等方面的特殊性能,并形成一系列专用保护渣,如高速连铸结晶器保护渣、超低碳钢用连铸结晶器保护渣、薄板坯连铸结晶器保护渣……以便更好地适应连铸技术的发展,满足对产品的更高要求。
连铸保护渣的主要理化性能指标有哪些项目

保护渣的主要理化性能指标有哪些项目?
检验保护渣理化性能的指标主要有:
(1)熔化温度。
由于多组分的熔渣通常没有固定的熔点,因而把具有一定流动性时的温度定义为“熔化温度”,通常称之为“半球点”。
(2)熔化速度。
熔化速度是指保护渣在一定温度下单位时间内其熔化的量。
(3)分熔倾向。
渣粉在熔化过程中总是低熔点的组分先熔化,高熔点的组分后熔化,由此会破坏熔渣层的均匀性。
(4)粘度。
粘度是指保护渣在一定温度下的粘滞程度,一般是在1300℃时测定的。
(5)表面张力。
表面张力是研究渣—钢界面现象和界面反应的重要参数。
对连铸结晶器保护渣渣层分析
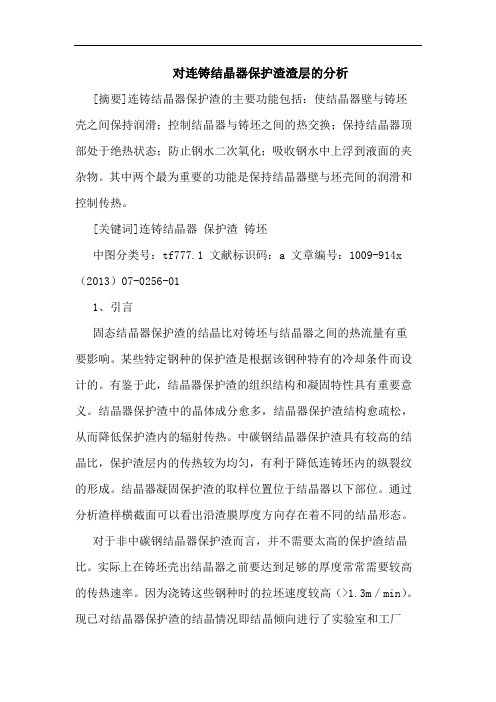
对连铸结晶器保护渣渣层的分析[摘要]连铸结晶器保护渣的主要功能包括:使结晶器壁与铸坯壳之间保持润滑;控制结晶器与铸坯之间的热交换;保持结晶器顶部处于绝热状态;防止钢水二次氧化;吸收钢水中上浮到液面的夹杂物。
其中两个最为重要的功能是保持结晶器壁与坯壳间的润滑和控制传热。
[关键词]连铸结晶器保护渣铸坯中图分类号:tf777.1 文献标识码:a 文章编号:1009-914x (2013)07-0256-011、引言固态结晶器保护渣的结晶比对铸坯与结晶器之间的热流量有重要影响。
某些特定钢种的保护渣是根据该钢种特有的冷却条件而设计的。
有鉴于此,结晶器保护渣的组织结构和凝固特性具有重要意义。
结晶器保护渣中的晶体成分愈多,结晶器保护渣结构愈疏松,从而降低保护渣内的辐射传热。
中碳钢结晶器保护渣具有较高的结晶比,保护渣层内的传热较为均匀,有利于降低连铸坯内的纵裂纹的形成。
结晶器凝固保护渣的取样位置位于结晶器以下部位。
通过分析渣样横截面可以看出沿渣膜厚度方向存在着不同的结晶形态。
对于非中碳钢结晶器保护渣而言,并不需要太高的保护渣结晶比。
实际上在铸坯壳出结晶器之前要达到足够的厚度常常需要较高的传热速率。
因为浇铸这些钢种时的拉坯速度较高(>1.3m/min)。
现已对结晶器保护渣的结晶情况即结晶倾向进行了实验室和工厂的实验研究。
试验室的大部分试验研究,均是在对保护渣控制加热或控制冷却的试验条件下进行,然后再对凝固的保护渣进行分析研究。
在对保护渣的结晶研究中广泛使用了差热分析方法(dta)。
在本研究中,为了确定液态结晶器保护渣在冷却时的结晶温度,在实验时将保护渣的温度变化与参照试样进行了对比。
采用差热分析的方法研究表明,结晶器保护渣的结晶趋势随cao/sio2的比值、li2o、tio2和zro2含量的增加而增强,随b2o3含量的减少而增强。
fonseca等人对自己所采取的保护渣样进行了研究,结果表明,中碳钢保护渣结晶层厚度和保护渣层总厚度均比低碳钢保护渣高。
- 1、下载文档前请自行甄别文档内容的完整性,平台不提供额外的编辑、内容补充、找答案等附加服务。
- 2、"仅部分预览"的文档,不可在线预览部分如存在完整性等问题,可反馈申请退款(可完整预览的文档不适用该条件!)。
- 3、如文档侵犯您的权益,请联系客服反馈,我们会尽快为您处理(人工客服工作时间:9:00-18:30)。
连铸保护渣概述1 连铸保护渣的组成 (1)2 连铸保护渣的作用 (2)3 连铸保护渣进入结晶器的行为 (3)4 保护渣的主要理化性能指标 (5)二战后,战后恢复及经济发展的需求成为钢铁冶金工业发展的主要驱动力。
自50年代始,连铸技术的出现促进了钢铁冶金工业的蓬勃发展。
自60年代连铸结晶器保护渣技术的出现取代菜籽油以来,使连铸钢品种、连铸断面种类、连铸坯的质量、连铸生产率得以大幅度提高。
近年来,以高拉速、高连浇率、高作业率、及高质量为特征的高效连铸得到迅速的发展,成为钢铁企业降低成本、降低能耗、减少投资成、开拓市场、在激烈的世界钢铁市场竞争中利于不败之地的重要技术创新和钢铁企业结构优化的必然需要。
从70年代开始,连铸技术在装备先进的钢铁企业的板坯连铸浇铸速度逐渐提高,从1.0m/min左右上升到2.0/min 左右,目前最大铸速可达3.0/min,日本住友正在开发5.0m/min的大板坯连铸技术,意大利在小方坯连铸上拉速已经达到 5.0/min。
因此,以高拉速为主要特征的高效连铸技术的开发、应用、推广是优化我国连铸技术,提高连铸水平的重要发展方向。
由于高效连铸中的高拉速使结晶器中的热流及摩擦力增大、结晶器中钢液面波动加剧、出结晶器的铸坯坯壳变薄、渣耗急剧下降造成润滑不良和传热不均等,使得从常速连铸到高速连铸遇到了粘结漏钢和铸坯表面质量差两大难题,目前,为解决这些问题,就必须研究和开发具有相应物理和化学性能的结晶器保护渣,保证连铸过程中结晶器内的物理化学反应处于良好的状态。
以连铸连轧为基础的紧凑型生产流程是降低冶金产品生产成本、提高企业经济效益的一个重要途径,无缺陷铸坯生产技术是实现连铸连轧的关键,这对铸坯表面质量提出了更高要求,连铸保护渣对高表面质量铸坯的生产起着重要的保障作用,为此,国内外各炼钢厂都在寻求适合本厂连铸工艺特点的无缺陷铸坯生产用结晶器保护渣。
近十年来,国内外连铸保护渣的开发,以满足连铸生产的需要、充分发挥保护渣的作用为主要目的,同时在保护渣原料、制作工艺、保护渣的基础理论研究方面进行了大量的工作。
连铸结晶器保护渣已经成为连铸工艺过程必须的关键性材料,对铸坯质量及连铸工艺顺行发挥着不可替代的作用。
1 连铸保护渣的组成现用的保护渣一般由三部分组成:基料、助熔剂和熔速调节剂。
基料一般为CaO-SiO2-A12O3系的物质为基础,通过CaO、SiO2、A12O3加入量的合适搭配来确定其主要的性能。
同时加入适量的Na2O,CaF2,K2O,MgO,BaO,Li2O,B2O3,MnO等化合物作助熔剂,根据加入的物质的特性的差别来调节熔点和粘度,并且稳定保护渣的组成。
接着根据各钢种及操作工艺加入不同量、不同种类的碳素材料作为熔速调节剂,保证保护渣的铺展性和性能的稳定性。
2 连铸保护渣的作用加入结晶器钢液面的保护渣,在钢水释放的热量作用下,逐渐升温并发生烧结、熔化,在结晶器钢液面上形成双层、三层或多层的渣层结构。
流入铸坯与结晶器壁间隙的保护渣,在结晶器壁的冷却下,靠结晶器壁侧凝固形成玻璃体和结晶体组成的固态渣膜,靠坯壳一侧维持液渣的状态。
随着结晶器振动和拉坯的进行,液渣和部分固渣膜被带出结晶器下口,在二冷水作用下与铸坯分离,由此完成保护渣的消耗过程。
保护渣从加入到离开结晶器这一过程中所发挥的作用可归结为:(1)防止钢液特别是钢液弯月面的二次氧化。
保护渣加入到结晶器内的钢液面上,熔化后形成一定厚度的液渣层,并均匀覆盖钢液面,该液渣层起到了隔绝钢液与空气接触的作用,进而可防止钢液的二次氧化。
(2)对裸露的钢液绝热保温。
钢液表面的凝固和弯月面初生坯壳的提前凝固对铸坯表面将产生不良影响。
因为钢液中的上浮夹杂物有可能被凝固的铁的结晶器捕集,形成一个有金属和氧化物组成的硬壳结构,被卷入坯后可能造成严重的缺陷。
渣的保温作用可以通过覆盖在钢液面上具有温度低,体积密度小的粉渣层来实现。
(3)吸收和溶解非金属夹杂物。
进入结晶器的钢液不可避免地带入非金属夹杂物,此外结晶器内铸坯液相穴内上浮到钢液弯月面的夹杂物有可能被卷入坯壳形成表面和皮下夹杂缺陷。
从热力学的观点来看,硅酸盐渣系能吸收和溶解此类非金属夹杂物,但其溶解速度受到许多因素的影响。
研究表明,低粘度、高碱度、低Al2O3和高CaF2及Na2O含量的渣对吸收夹杂有利。
(4)控制传热的速度和均匀性。
由于结晶器和铸坯之间形成的渣膜,坯壳向水冷结晶器铜壁和敞开浇注比较有很大的变化,传热的均匀性得到了改善。
(5)在结晶器和坯壳之间起到润滑作用,使铸坯顺利拉出。
熔融的保护渣随铸坯的拉出而进入铸坯与结晶器的间隙,形成0.1~1.5mm厚的渣膜。
在结晶器的一侧,由于温度较低而呈固态,在坯壳的一侧,由于温度高于渣的结晶温度而呈液态,因此能够减小铸坯和结晶器间的摩擦3 连铸保护渣进入结晶器的行为连铸保护进入结晶器中会发生如图1所示的行为。
由图可知保护渣进入结晶器会出现如下关键现象:(1)保护渣融化;(2)形成渣熔池;(3)熔渣流入结晶器和铸坯之间;( 4)形成固态渣和液态渣膜。
图1保护渣在结晶器内行为示意图当保护渣加入到结晶器内钢液上,就覆盖在钢液面上,分为粉渣层、烧结层及熔渣层(如图2),当结晶器有规律地上下振动时,熔渣渗入到结晶器壁与坯壳之间的缝隙中,形成一层极薄的渣膜,这层渣膜贴在结晶器的一面为固态渣膜—玻璃态,而贴在铸坯的一面为液态渣膜—流动的液体(如图2),两层之间的温度及状态是逐渐过渡的,对润滑和传热方面起着重要作用,液态渣膜能够润滑凝固坯壳与结晶器之间的界面,防止二者发生粘结,结晶器与铸坯间摩擦力的大小是保护渣润滑效果的直观体现,摩擦力减小,有利于铸坯润滑,改善铸坯的表面质量,保证连铸工艺顺行,避免粘结漏钢发生,具有良好润滑作用的保护渣,应能使坯壳与结晶器间的摩擦力降至最小;由于结晶器冷却水作用形成的固态渣膜层对于控制传热具有重要作用,从高温钢水到结晶器冷却水的传热机理是非常复杂的,该传热过程包括以下几个环节(如图3):(1)凝固坯壳的传热;(2)保护渣渣膜的传热;(3)固态渣膜与铜结晶器壁间界面传热;(4)结晶器的传热。
因为凝固坯壳和结晶器壁的导热系数比较大,液渣层传热能力较强,所以量从高温钢水传输到结晶器冷却水的限制性环节是固态渣膜与铜结晶器壁之间的界面传热。
根据Shibata.H 的研究结果,由于固相接触,存在于结晶器与固态渣膜之间的界面热阻的大小与表面粗糙度有关,又因为结晶器壁是光滑的,所以影响结晶器与固态渣膜之间界面热阻大小的关键因素是固态渣膜表面粗糙度。
液渣层越厚,润滑越好,而液渣层厚度增加将导致固渣层减薄,不利于传热,这就要求固态渣膜有良好的传热性能。
图2结保护渣分布示意图图3保护渣固态渣膜和液态渣膜温度分布示意图4 保护渣的主要理化性能指标连铸过程对保护渣的物理及化学性质有着一定的要求,因此在保护渣的研制和试用过程中要对熔化温度、粘度等基本性质要进行测定。
化学成分及碱度。
常用的碱度为渣中的CaO与SiO2的比值,即CaO/ SiO2,一般CaO/ SiO2在0.7~1.5之间,碱度主要影响保住渣的粘度—温度曲线、吸收夹杂的能力、结晶性能并进而影响传热特性。
碱度取值主要由浇注的钢种决定,通常,高碳钢、含易氧化元素较多的合金钢保护渣碱度较低其值约为0.7~1.0;裂纹敏感性较强的中碳钢保护渣粘度较高,约为1.0~1.5;而普通碳素钢中的低碳钢、中碳钢及低合金钢保护渣碱度取值居中,约为0.9~1.0。
熔化温度(熔点)。
保护渣是由多种氧化物和氟化物组成的多元体系,因此没有固定的熔化温度,因此定义熔化温度为,保护渣在升温过程中由固态转变为液态的温度。
对于多组分硅酸盐熔渣,熔化温度是一个区间。
熔化温度对熔渣层厚度和保护渣消耗等有重要影响。
熔化温度主要测试方法有热分析法、淬火法、差热分析法以及半球点法和三角锥法。
各种分析法有时差别很大,比较精确地方法有热分析法、差热分析法、和淬火法,但是操作和分析复杂。
目前,保护渣采用半球点法作为保护渣熔化温度分析的行业标准。
通常人们把当以一定升温速度加热到使试样由圆柱形变成半球形的温度称为熔化温度,简称为熔点。
一般认为应低于结晶器内钢液弯月面的温度,也有人主张应比结晶器下段的坯壳温度低50℃。
这样控制保护渣的熔化温度的目的在于,使粉渣在弯月面处保持熔融状态,并使结晶器上部铸坯凝固壳表面的渣膜处于粘滞的流动状态,起到充分润滑铸坯的作用。
保护渣的熔点过高,熔渣层厚度减小,影响保护渣的润滑能力,可能导致纵向裂纹的出现,甚至可能发生漏钢事故;熔点过低,会影响保护渣的绝热保温性能,导致铸坯表面产生冷皮,横向裂纹等缺陷。
国内外保护渣的研究表明,大多数板坯保护渣的熔化温度控制在1050~1200℃。
流动性能。
粘度是表示熔渣中结构微元体移动能力大小的一项物理指标,即在一定温度下河一定剪切力作用下熔渣流入坯壳与结晶器间隙能力的大小。
它是衡量保护渣润滑性能的重要指标。
现在大多测其在1300℃条件下的值,常用保护渣的粘度(1300℃下测定)为0.05~0.15Pa·S。
粘度直接影响到熔渣吸收氧化物夹杂的速度和润滑铸坯的效果。
它受化学成分和温度的控制,生产中主要靠助熔剂来调节。
保护渣粘度过低,液渣大量流入缝隙,造成渣膜不均匀,局部凝固变缓,导致凝固坯壳变形,引起纵裂和拉漏事故;粘度过大,会使铸坯表面粗糙。
粘度的测试方法有斜舟法、振动法、圆柱体旋转法。
凝固温度是指熔渣从液态向固态转变的温度,理论上应对应熔渣的液相线温度,但为便于测试,国内外目前习惯将粘度—温度曲线的转折点温度Tbr定义为凝固温度。
连铸保护渣的凝固温度对连铸坯的润滑与传热有重要影响,对裂纹敏感性钢种的浇注有重要意义。
结晶性能。
保护渣的结晶性能主要包括结晶温度和以一定冷却条件下的结晶率、结晶速度以及结晶析出物相组织等内容。
结晶性能影响着铸坯受到的摩擦力以及铸坯向结晶器壁传热的,对铸坯表面裂纹缺陷和粘结及漏钢事故由很大的影响。
结晶温度是指熔融保护渣在一定降温速度下开始析出晶体的温度。
结晶温度对保护渣润滑铸坯和控制传热有重要影响。
目前对结晶温度的测试及评价主要有差热法(DTA)、示差扫描量热法(DSC)、热丝法和粘度—温度曲线法等;结晶率是指凝固渣膜中结晶相所占的比例。
结晶率也对保护渣的传热和润滑功能有重要作用。
目前对结晶率测试及评价主要有观察法、X射线法、热分析法、热膨胀系数法以及理论预测等。