乙烯裂解炉炉管的焊接指导
乙烯装置中裂解炉工艺控制方案分析
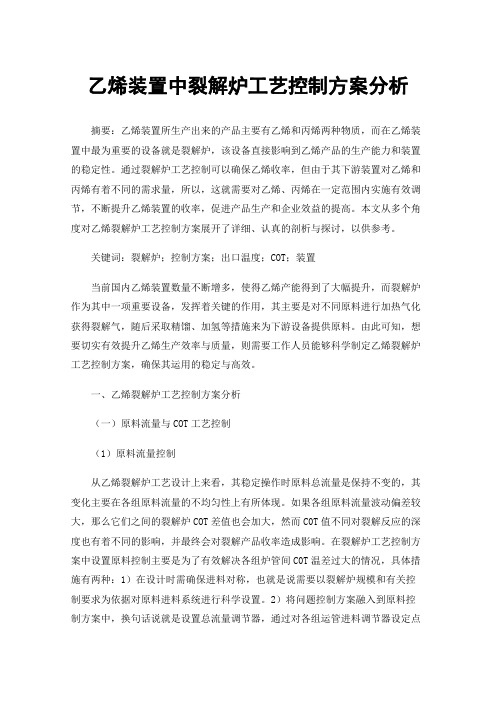
乙烯装置中裂解炉工艺控制方案分析摘要:乙烯装置所生产出来的产品主要有乙烯和丙烯两种物质,而在乙烯装置中最为重要的设备就是裂解炉,该设备直接影响到乙烯产品的生产能力和装置的稳定性。
通过裂解炉工艺控制可以确保乙烯收率,但由于其下游装置对乙烯和丙烯有着不同的需求量,所以,这就需要对乙烯、丙烯在一定范围内实施有效调节,不断提升乙烯装置的收率,促进产品生产和企业效益的提高。
本文从多个角度对乙烯裂解炉工艺控制方案展开了详细、认真的剖析与探讨,以供参考。
关键词:裂解炉;控制方案;出口温度;COT;装置当前国内乙烯装置数量不断增多,使得乙烯产能得到了大幅提升,而裂解炉作为其中一项重要设备,发挥着关键的作用,其主要是对不同原料进行加热气化获得裂解气,随后采取精馏、加氢等措施来为下游设备提供原料。
由此可知,想要切实有效提升乙烯生产效率与质量,则需要工作人员能够科学制定乙烯裂解炉工艺控制方案,确保其运用的稳定与高效。
一、乙烯裂解炉工艺控制方案分析(一)原料流量与COT工艺控制(1)原料流量控制从乙烯裂解炉工艺设计上来看,其稳定操作时原料总流量是保持不变的,其变化主要在各组原料流量的不均匀性上有所体现。
如果各组原料流量波动偏差较大,那么它们之间的裂解炉COT差值也会加大,然而C0T值不同对裂解反应的深度也有着不同的影响,并最终会对裂解产品收率造成影响。
在裂解炉工艺控制方案中设置原料控制主要是为了有效解决各组炉管间C0T温差过大的情况,具体措施有两种:1)在设计时需确保进料对称,也就是说需要以裂解炉规模和有关控制要求为依据对原料进料系统进行科学设置。
2)将问题控制方案融入到原料控制方案中,换句话说就是设置总流量调节器,通过对各组运管进料调节器设定点进行调整,以实现对总进料流量进行控制。
其主要是为了确保当原料总量需求发生改变的时候可以通过控制系统并结合实际操作情况对各组裂解炉的流量进行配置,从而有效降低总流量变化对C0T所造成的影响。
乙烯裂解炉安装工序验收指导书

上海惠生化工工程有限公司标准
乙烯裂解炉安装工序验收指导书
WO-CMFU100501C-2007
20??-??-??发布20??-??-??实施上海惠生化工工程有限公司发布
目次
1 范围 (2)
2 引用文件 (2)
3 乙烯裂解炉主要工序验收要求 (2)
本文件所有权属WISON。
未经本公司的书面许可,不得进行任何方式的复制;不得以任何理由、任何方式提供给第三方或用于其它目的。
第1 页共10 页
WO-CMFU100501C-2007
第 2 页 共 10 页
1 范围 1.1 为了保证乙烯裂解炉安装质量,特制定本指导书。
1.2 本指导书规定了乙烯裂解炉安装验收的要求。
1.3 本指导书适用于乙烯裂解炉安装。
2 引用文件
GB50205-2001 钢结构工程施工质量验收规范
SH3507-2004 石油化工钢结构工程施工及验收规范
SH/T3511-2000 乙烯装置裂解炉施工技术工程
SH3534-2001 石油化工筑炉工程施工及验收规范
3 乙烯裂解炉主要工序验收要求
第
3 页共10
第
4 页共10
第
5 页共10
第
6 页共10
第
7 页共10
第
8 页共10
注:“专业”为土建、钢结构、设备等;“分项”为相应专业下的小类别,如设备专业中容器、换热器、塔等第
9
页
共
10
WO-CMFU100501C-2007 Array
第10 页共10 页。
P11焊接工艺卡

中国石油天然气第六建设公司兰州项目经理部
兰州石化公司60万吨/年乙烯改扩建工程乙烯装置裂解炉区
P11炉管焊接工艺卡
焊接方法选择:GTAW+SMAW(氩电联焊)
焊接材料:焊丝:H08CrMoVA 焊条:E5515-B2(R307)
坡口型式:V
预热及后热
加热方式:氧-乙炔火焰加热
预热温度(允许最低值): 150℃
后热温度:300-350℃恒温15-30min后保温缓冷
热处理
加热方式:电加热
执处理温度:724±20℃保温时间:2h
升温速度:300℃以上时≤167℃/h
冷却速度1:300~649℃时167~270℃/h
冷却速度2 :649℃以上时≤56℃/h
——摘自中国石油天然气股份公司兰州石化公司60万吨/年乙烯改扩建工
程乙烯装置裂解炉区《炉管焊接施工技术措施》A版
1。
乙烯裂解炉管的结焦机理及其防护措施
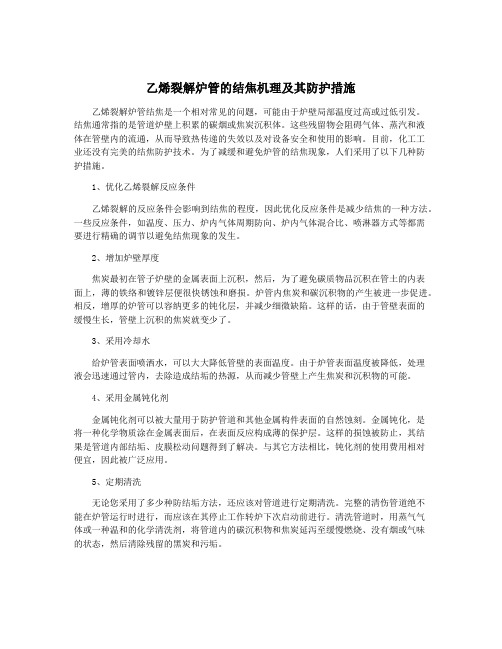
乙烯裂解炉管的结焦机理及其防护措施乙烯裂解炉管结焦是一个相对常见的问题,可能由于炉壁局部温度过高或过低引发。
结焦通常指的是管道炉壁上积累的碳烟或焦炭沉积体。
这些残留物会阻碍气体、蒸汽和液体在管壁内的流通,从而导致热传递的失效以及对设备安全和使用的影响。
目前,化工工业还没有完美的结焦防护技术。
为了减缓和避免炉管的结焦现象,人们采用了以下几种防护措施。
1、优化乙烯裂解反应条件乙烯裂解的反应条件会影响到结焦的程度,因此优化反应条件是减少结焦的一种方法。
一些反应条件,如温度、压力、炉内气体周期防向、炉内气体混合比、喷淋器方式等都需要进行精确的调节以避免结焦现象的发生。
2、增加炉壁厚度焦炭最初在管子炉壁的金属表面上沉积,然后,为了避免碳质物品沉积在管土的内表面上,薄的铁络和镀锌层便很快锈蚀和磨损。
炉管内焦炭和碳沉积物的产生被进一步促进。
相反,增厚的炉管可以容纳更多的钝化层,并减少细微缺陷。
这样的话,由于管壁表面的缓慢生长,管壁上沉积的焦炭就变少了。
3、采用冷却水给炉管表面喷洒水,可以大大降低管壁的表面温度。
由于炉管表面温度被降低,处理液会迅速通过管内,去除造成结垢的热源,从而减少管壁上产生焦炭和沉积物的可能。
4、采用金属钝化剂金属钝化剂可以被大量用于防护管道和其他金属构件表面的自然蚀刻。
金属钝化,是将一种化学物质涂在金属表面后,在表面反应构成薄的保护层。
这样的损蚀被防止,其结果是管道内部结垢、皮膜松动问题得到了解决。
与其它方法相比,钝化剂的使用费用相对便宜,因此被广泛应用。
5、定期清洗无论您采用了多少种防结垢方法,还应该对管道进行定期清洗。
完整的清伤管道绝不能在炉管运行时进行,而应该在其停止工作转炉下次启动前进行。
清洗管道时,用蒸气气体或一种温和的化学清洗剂,将管道内的碳沉积物和焦炭延泻至缓慢燃烧、没有烟或气味的状态,然后清除残留的黑炭和污垢。
总之,需要注意的是减少管道的结焦现象不是通过单一的措施就可实现的,而是需要多方面的工作。
燃气管道工程聚乙烯PE管道焊接作业指导书
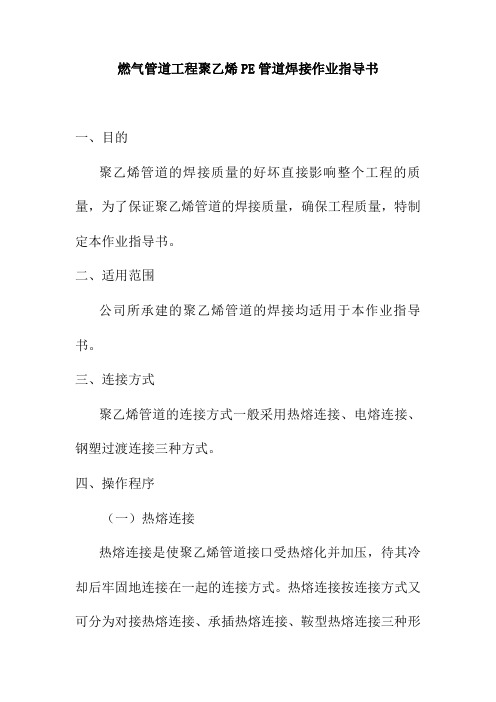
燃气管道工程聚乙烯PE管道焊接作业指导书一、目的聚乙烯管道的焊接质量的好坏直接影响整个工程的质量,为了保证聚乙烯管道的焊接质量,确保工程质量,特制定本作业指导书。
二、适用范围公司所承建的聚乙烯管道的焊接均适用于本作业指导书。
三、连接方式聚乙烯管道的连接方式一般采用热熔连接、电熔连接、钢塑过渡连接三种方式。
四、操作程序(一)热熔连接热熔连接是使聚乙烯管道接口受热熔化并加压,待其冷却后牢固地连接在一起的连接方式。
热熔连接按连接方式又可分为对接热熔连接、承插热熔连接、鞍型热熔连接三种形式。
1、对接热熔连接对接热熔连接是将平板电热模(电加热板)插入两管材接口间,对管材的连接面进行加热,当两管材的连接面加热到熔融状态时,抽出电热模板,用力将两管道端面挤压在一起,形成均匀一致的凸缘,待冷却后即熔接牢固。
该方法工艺简单,操作方便,常用于聚乙烯管道的直管连接。
(1)准备工作:用切割机、平锯或其它工具将管材切断,管道端面应与管轴线保持垂直,然后用洁净的布擦去管端铣刀、平板电热模上的油脂、灰尘、水分,检查对接机的液压系统和电路是否正常并运行,使全部设备出于工作状态。
(2)固定连接管材:卸开机架内的夹具,将待熔接的两管材分别搁置在机架左右的两组夹具上并固定,开动液压驱动装置,记录夹具滑行的最小驱动压力,然后让夹具的滑行端返回。
(3)管端表面铣平直:以最小驱动压力推动机架滑行端向前,使待熔接的两端面紧贴在双面铣的两面进行铣削,然后拿出铣刀,再以最小夹具驱动压力推动滑行端,使铣削后的两管端面接触,检查两管轴线和两管端面完全接触的程度,要求两管端面缝隙不大于0.5mm,错边量不大于壁厚的10%。
(4)管端待接面加热:平板电热模加温并恒定温度在210-220℃时,将平板插入到两管端之间,搁置在两夹具间的机架主轴上,开动液压系统,以加热压力推动夹具滑行端,使两管端面紧压在平板电热模两侧,此时由于管端受热熔化形成反边。
(5)移开平板电热模:两管端反边高度达到一定值后,开动液压系统,使滑行端脱离平板电热模一侧,同时操作者将平板电热模平行向已离开的滑行端移动,使之脱离另一侧管端,迅速抽出平板电热模,开动液压系统,推动滑行端,使两管端面以一定的压力贴压在一起。
乙烯生产—管式炉裂解流程

• 目的:
• 提高分离操作温度,节约低温能量和材料。
• 除去部分水份和重质烃,减少后面干燥和低温的负担。
• 要求:
• P↑,设备材料要求增加,动力消耗也增加。
• P↑,精馏塔釜温↑,不饱和烃及重组分聚合
• P↑,α↓,分离困难。
∴生产中一般控制30~40atm。
• 采用多段压缩:
压缩升温时二烯烃、烯烃易聚合,∴为防止结焦,控制排气温度<100℃,采
侧壁烧嘴
管式裂解炉的炉型
( 二
1.鲁姆斯裂 解炉
)
管 式
2.凯洛格毫
裂
秒裂解炉
解
炉
的
炉 型
C裂解炉
SRT型裂解炉即短停留时间炉,是美国鲁姆
斯(Lummus)公司于1963年开发,1965
年工业化,以后又不断地改进了炉管的炉型
超伯的解选斯一温及裂缩的中司的超洛一下0解致.择特种度1炉解短收应,乙短(种,炉使秒性(炉和子炉停率用扬烯K停炉使。裂S毫(裂S型烃eR的,留,最子生留型物解秒lt5Tlo解,分o0结 该时 对 多 石 产时。料炉炉n型g~U炉 压e构炉间不的油装间1在结g由炉S19)简条&,型,同炉化置裂炉构0C7于是08公称件W裂先的改的型工均解管复毫年管目司e的U解后不善裂。公采炉内杂秒开径b前S在选技s推断裂解中司用简的,C)发较t世6e择术炉出改解原国和此称停投,0成小r界),年是。了进选料的齐种留资U所功,上公使S代根它,择有燕鲁裂S时相以所,R大R司生开据是是性较山石解间对T也需在T型在炉成始停美-为,大石油炉缩较称炉高乙7,的研留国Ⅰ了提的油化。短高为0管裂烯是产年究时斯~进高灵化工到。毫数解装美品代开间通Ⅵ一乙活工公因0秒量温置.国中开发、-0型步烯性公司裂裂多度5凯乙发的裂韦~。解, 烷等管副是产一品程较,少没,有乙弯烯头收,率阻较力高降而小命,名烃的分。压低,
乙烯裂解炉管的结焦机理及其防护措施

乙烯裂解炉管的结焦机理及其防护措施乙烯裂解炉管结焦是裂解工艺中常见的问题之一,主要是由于乙烯在高温下裂解生成的碳黑物质沈积在炉管内壁而导致的。
结焦会增加炉管的阻塞程度、降低传热效率,甚至会引起炉管损坏,严重影响生产运行。
乙烯裂解炉管结焦的机理主要有以下几个方面:1. 易结焦物质存在:乙烯裂解过程中,会产生一些易结焦的碳黑物质,如多环芳香烃等。
这些物质在高温下容易聚集在炉管内壁形成结焦。
2. 温度分布不均匀:乙烯裂解炉管内温度分布不均匀,部分区域温度偏高会加剧易结焦物质的形成。
为了预防乙烯裂解炉管结焦问题,可以采取以下防护措施:1. 控制乙烯裂解过程参数:合理控制乙烯裂解炉的操作参数,如温度、压力、速度等,以减少易结焦物质的生成和沉积。
可增加炉内空气流动,促进物质的扩散和排除。
2. 清洗和保护炉管内壁:定期对乙烯裂解炉管进行清洗,以去除已经沉积的结焦物质。
在炉管内壁上涂覆一层防结焦的保护层,减少结焦物质的附着。
3. 使用抗结焦材料:选用抗结焦能力强的材料制作炉管,如高温合金钢等,能够减少结焦物质的黏附和附着。
4. 提高传热效率:改善乙烯裂解炉的传热方式和热交换设备,提高传热效率,减少炉管温度梯度的差异,从而减少结焦的发生。
5. 定期检查和维护:定期对乙烯裂解炉进行检查,及时发现和处理炉内的结焦问题。
还要定期维护和更换炉管,以保持其良好的工作状态。
乙烯裂解炉管结焦是一个常见的问题,其机理主要包括易结焦物质的生成和沉积、温度分布不均匀以及炉管内物质的沉积。
为了预防结焦问题,需要合理控制裂解过程参数、清洗和保护炉管内壁、使用抗结焦材料、提高传热效率,并定期检查和维护炉管。
只有采取多种综合措施,才能有效防止乙烯裂解炉管结焦问题的发生。
烯烃厂裂解炉辐射段“镍铬微合金”炉管的焊接

制 相 析 出。但碳 含量 过 高 ,二次 碳 化物 大 量 析 出 ,
会降 低合金 的韧性 、恶 化焊 接 性 ,因此 炉 管 合 金 W
材 料 的组 织 和性 能发 生 变化 ,结 果 会 使 炉 管 局 部 开
裂 或腐 蚀穿 孔 。
W 、Mo b等元 素 作 用 :都 是 同溶 强 化 元 素 , 、N 能 提高合 金 的高 温强 度 ,抑制 碳 的 扩 散 速 度 ,但 是
加入 过量 则 会影 响合 金 的抗 氧 化性 能 ,并 促 进 O 相 - 析 出 ,降低合 金 的强度 和韧 性 。 N b、T 、V元 素 作 用 :它 们 形 成 碳 氮 化 物 ,改 i 变 晶界 碳 化物 形 态 ,细 化 M ,使 其 均 匀 弥 散 分 C
命 。裂解炉 管 W 一 般 控制 在 15 % ~ . 0 。 .0 20 % Mn元 素作 用 :它 能改善 焊 接性 能 ,但促 进 o相 r
析 出 ,加 入 量 过 多 能 降 低 合 金 的 抗 氧 化 性 能 。一 般
W 控 制 在 15 以 下 。 .%
熔 深小 ,易 出 现 焊 口根 部 的熔 合 不 良及 促使 凝 固 裂
变强 度要 求 高 。为 此 ,焊 接 材 料 选 取 高 匹配 的镍 基
焊材 :焊 丝牌 号 E N c 一3 R ir ,塑性 较好 ,化 学成 分如
表 2所 示 。 表 2 E N C - 3的 化 学 成 分 ( 量 分 数 ) ( ) R ir 质 %
- 1、下载文档前请自行甄别文档内容的完整性,平台不提供额外的编辑、内容补充、找答案等附加服务。
- 2、"仅部分预览"的文档,不可在线预览部分如存在完整性等问题,可反馈申请退款(可完整预览的文档不适用该条件!)。
- 3、如文档侵犯您的权益,请联系客服反馈,我们会尽快为您处理(人工客服工作时间:9:00-18:30)。
上海格群信息科技有限公司
乙烯裂解炉辐射段炉管的焊接
前言
中原石化总厂十万吨裂解炉,辐射段炉管所用材料为(Cr35Ni45+微合金),辐射段出口材料为
20Cr32NiNb。Cr35Ni45的合金系统较之以前的Cr25Ni35有了较大的发展,增加了Cr、Ni元素含量,
相应提高了耐高温性能。炉管采用离心浇铸的方法生产,其原始铸态表面为均匀分布有颗粒状凸起的
“珍珠”表面,这种表面不仅有利于热交换,而且对抗氧化和抗燃气腐蚀有利。管子的内表面有很薄
一层疏松组织,炉管的基体组织相当致密,主要由沿半径方向分布的柱状晶组成,内部没有气孔、夹
杂及缩孔等铸造缺陷。管件(包括180º弯头、90º吊耳弯头、Y型管等)为静态浇铸法生产,合金成
分不均匀,存在较大成分偏析,焊接时易产生裂纹。
1 焊接性分析
1.1 化学成分分析
炉管材料Cr35Ni45的化学成分见表1。
表 1Cr35Ni45的化学成分
化 学 成 分 (%)
C Si Mn P S Cr Ni Mo W Nb Cu Al
0.4~ 0.6 1.2~ 1.8 ≤ 1.5 ≤ 0.03 ≤ 0.03 30~ 37 40~ 47 ≤ 0.5 ≤0.30 0.5~ 1.5 ≤ 0.25 ≤
0.05
为了深刻认识炉管中主要元素及微量元素的作用,查阅了一些文献,并对其在耐热铸钢中的作用
进行了分析。
C:C与Cr、Mo、Ti、V、Nb等形成一次碳化物M7C3和NbC。在高温时效过程中,基体中的过饱和
固溶碳以细小弥散的M23C6析出,提高了钢的强度。另外增加碳含量还能抑制б相析出。但碳含量过高,
二次碳化物大量析出,会降低合金的韧性、恶化焊接性。因此Cr35Ni45合金含碳量不超过0.60%,
但Si是促进б相析出元素,加入量过多,使焊接性恶化、降低持久强度。裂解炉管硅含量一般控制
在1.50%~2.00%。
Mn:它能改善焊接性能,但固熔强化促进б相析出,加入量过多能降低合金的抗氧化性能。一般
控制在1.5%以下。
Cr:它是合金中主要的固溶强化元素和碳化物形成元素。它在材料表面形成致密的Cr2O3保护膜,
上海格群信息科技有限公司
对合金的抗氧化、强度、抗渗碳性能起着决定性作用。但Cr含量过高会导致б相析出,因而降低合
金的强度和韧性。
Ni:它是形成和稳定奥氏体,提高抗渗碳、抗氧化、高温强度和韧性的主要元素。对于裂解炉来
说,其抗渗碳性能的优劣是十分重要的,也是影响裂解炉寿命的主要因素。由于裂解炉在运行过程中
管内壁会产生渗碳,渗碳层的出现一方面在管内壁会产生附加应力,另一方面渗碳也使炉管材料的组
织和性能发生变化,结果会使炉管局部开裂或腐蚀穿孔。
W、Mo、Nb都是固溶强化元素,能提高合金的高温强度,抑制碳的扩散速度,但是加入过量则会
影响合金的抗氧化性能,并促进б相析出,降低合金的强度和韧性。
Nb、Ti、V它们形成碳氮化物,改变晶界碳化物形态,细化M23C6,使其均匀弥散分布,延迟碳化
物粗化过程,从而提高合金的高温蠕变强度
Al:它在奥氏体不锈钢中形成AlN,促进长期蠕变时б相形成和粗化,降低蠕变寿命。因此认为
Al在奥氏体耐热钢铸管中是有害元素,其含量应严格控制。
1.2 焊接性分析
炉管材料为铁基高铬镍合金,焊接性较差,焊接工艺措施稍有不当,便会出现问题,表现如下:
1.2.1 由于合金元素含量较多,导热性差,焊缝与母材容易过热,造成晶粒粗大,使接头力学
性能和耐蚀性能下降;
1.2.2 焊接时易出现热裂纹及再热裂纹;
1.2.3 对应变时效敏感。焊后如果残余应力较大,在时效过程或工作温度高于时效温度时,易
产生“应变时效”裂纹;
1.2.4 对焊道熔池裂纹较敏感;
1.2.5 焊接熔池液态金属流动性差,铁水发粘,熔深小,易出现焊口根部的熔合不良及促使凝
固裂纹的产生。
2 焊接方法及焊接材料的选取
焊接方法:主要考虑小的热输入及小的熔合比,故采用手工钨极氩弧焊。
焊接材料:因炉管用在高温条件下,所以高温强度,蠕变强度要求高,因此,炉管本体焊接材料
选取与母材相匹配的高碳同质焊材:牌号XTM,其公称成分为35Cr45Ni,具体化学成分见表2。
辐射段炉管出口材料为20Cr32NiNb,与辐射段炉管Cr35Ni45相焊时,焊接材料选择Inconel 82,
该焊材为镍基焊材,塑性较好,其化学成分见表3。
表2 焊丝XTM的化学成分
上海格群信息科技有限公司
化 学 成 分 (%)
C Si Mn P S Cr Ni Ti Zr Nb
0.42~ 0.48 0.5~ 1.8 1.0~ 2.5 ≤ 0.015 ≤ 0.015 34~ 37 43~ 47 0.05~ 0.15 0.05~ 0.10 0.5~
1.0
表3 焊丝Inconel 82的化学成分
化 学 成 分 (%)
C Si Mn P S Cr Ni Ti Nb+Ta
≤ 0.10 ≤ 0.50 2.5~ 3.5 ≤ 0.03 ≤ 0.015 18.0~ 22.0 ≥ 67 ≤
0.75
2.0~3.0
3 焊接
在焊接工艺评定的基础上,针对现场的实际情况,制定了现场的焊接工艺技术措施。
3.1 坡口型式
由于炉管材料的液体金属流动性不如一般钢铁材料,焊接工艺不良时很容易发生未熔合现象。如
果加大焊接电流以增大高温合金熔池金属的流动性,不但效果不大,而且还会造成过热的不良影响。
为使熔合良好且有一定熔深,坡口设计应与结构钢有所区别,坡口角度应适当增大,根部钝边应适当
减小。具体坡口型式见图1所示:
3.2 焊接工艺参数
表4 焊接工艺参数
焊材 牌号 规格 (mm) 焊接电流(A) 电弧电压 (V) 焊接速度(cm/min) 氩气流量
(L/min)
XTM InconeI82 2.4×2.4
Ф2.5
80~100 11~13 8~10 10~15
3.3 焊接
3.3.1 对口要求
管道对口应做到内壁平齐,如有错口,不得大于0.5mm, 对口时不得采用强力组对,应做到无
应力对口;
3.3.2 焊接工艺要点
图1
上海格群信息科技有限公司
焊接前应用丙酮清洗坡口,以防有害杂质对焊缝造成危害;焊接时,焊缝背面应充氩保护,氩气
纯度不小于99.99%;引弧时应在坡口内,以免在坡口外引弧对母材造成伤害;炉管开始焊接时,不
得将炉管组对时所用的工卡具拆除,至少焊接三层后方可拆除,以免由于外加因素产生的附加外应力,
使焊缝产生裂纹;焊接时应采用小线能量和小截面焊道;底层焊接时,应采用小电流,使电弧垂直对
准坡口中心,电弧应稍作摆动,保证坡口根部熔合良好。底层焊接时,打底厚度要相对较厚,以免底
层焊道强度不足,产生裂纹;打底完成经检验合格后,应及时进行次层的焊接,以防产生裂纹;次层
焊接时,应采用窄焊道技术,从第三层以上,应采用多道焊接技术;焊接时,应逐层对焊缝外观进行
检查;合格后方可焊接次层;多层焊时,应控制层间温度在100℃以下,以防接头过热,焊缝热影响
区晶粒粗大,使接头的强度下降;收弧时应填满弧坑,收弧时应先停弧,滞后停气,以防产生火口裂
纹.
3.4 焊接检验
渗透探伤:坡口着色,底层着色,面层着色。
射线探伤:100%射线探伤。
3.5 现场焊接实例
以辐射段出口的焊接为例,见图2所示.
1
2
3
4
A(现场安装焊口)
5
6
7
图2 十万吨炉辐射段出口
1-废锅
2-螺栓
3与废锅相联法兰
4-直管
5-支撑杠
6-Y型管
7-辐射段炉管
上海格群信息科技有限公司
3.5.1 焊接时出现的问题
A为现场安装焊口,件号4(材料为20Cr32NiNb)与件号6(材料为Cr35Ni45)相焊,焊接材料
选择Inconel 82,该焊材为镍基焊材,塑性较好。焊接方法为纯氩弧焊,组对完成后进行底层焊接,
底层焊接时,在焊缝中心处产生沿焊缝方向裂纹,经砂轮打磨补焊仍产生裂纹。
3.5.2 原因分析
3.5.2.1 材料本身的因素,该种材料较为难焊,易产生裂纹。
3.5.2.2 在底层焊接时,焊缝必将产生横向收缩,焊缝下部管子由于本身重力因素,不能向上
移动,焊缝上部由于与废热锅炉相联法兰已经把紧,不能自由伸缩。由于焊口两端的相对固定,焊缝
不能自由收缩,焊缝产生较大内应力,且底层焊缝厚度较薄,当内应力超过材料的强度极限时,焊缝
产生裂纹。
3.5.3 解决措施
3.5.3.1 在焊口下部的Y型管或90°弯管上加支撑杠或吊链,焊接时使支撑杠或吊链处于受力
状态,不能松动,以免由于焊口下方管子自重对焊缝产生的附加外应力。当焊接3层或3层以上时方
可将支撑杠或吊链撤除。
3.5.3.2 将与废热锅炉相连的法兰螺栓松开,让焊口上方的管子或法兰处于自由伸缩状态,确
保焊口无附加外应力。
3.5.3.3 底层焊接时,打底厚度要相对较厚,确保焊缝有足够的强度。
3.5.4 实际效果
采用上述措施后,焊接时未出现焊接裂纹,效果良好,满足了炉管的焊接技术条件要求。
4 结束语
炉管焊接时,除采用正确的焊接工艺外,还应采用合理的坡口型式及相应的技术措施,尤其是无
附加外应力,确保焊口处于自由状态,从而避免裂纹的产生。