乙烯裂解炉炉管的焊接指导
乙烯改造工程裂解炉炉体配管施工作业指导书_secret

编码:XXXXXX重大一般XXXXXXX65万吨/年乙烯改造裂解炉炉体配管施工作业指导书编制: 校审: 批准:***集团XXXXXXXXXX 工程项目经理部XXXX 年XX 月10日目录1 工程概况 (1)2 施工部署 (2)3 质量要求及控制措施 (8)4 H S E管理和控制措施 (9)5 施工机具及措施用料 (12)1工程概况1.1使用范围本作业指导书只适用于XXX65万吨/年乙烯改造裂解炉炉本体配管施工。
裂解炉炉体配管主要包括对流段炉管间连接管,辐射段与对流段间跨越管,汽包与废热锅炉TLE(以下简写为TLE)间的上升管、下降管的配管施工。
跨越管的平衡机构安装及调试的具体方法请见<<XXXX万吨/年乙烯改造工程裂解炉炉管施工作业指导书>>,在本作业指导书中只做一般性介绍。
1.2编制依据1)XXX设计院设计的施工图2)XXX设计院的设计文件00794-11-917-101 XXX万吨/年乙烯改造乙烯裂解炉《E—BA1101~1104乙烯裂解炉施工与安装技术说明》《E—BA1101~1104裂解炉炉衬材料订货技术要求》《E—BA1101~1104乙烯裂解炉内衬施工技术要求》3)SH/T3511-2000《乙烯装置裂解炉施工技术规程》SH3506-2000《管式炉安装工程施工及验收规程》SH3505-1999《石油化工施工安全技术规程》《E-BA1101~1104乙烯裂解炉总体施工方案》1.3工程概述XXX公司65万吨/年乙烯改造工程10万吨/年裂解炉,采用美国ABBLummus和****技术发展中心联合研制的蒸汽管式热解技术,其中E-BA-1101、1102为石脑油裂解炉,E-BA-1103、1104为重质油裂解炉。
各部分组成及主要实物量如下:1.3.1对流段炉管对流段盘管组由******公司***石化设备厂制造,E-BA1101、E-BA 1102对流段盘管组由六个加热盘管组构成:LMPH(下部混合预热段)、USSH/LSSH(超高压蒸汽过热段)、UMPH(上部混合预热段)、LFPH(下部进料预热段)、BFW(锅炉给水预热段)、UFPH(上部进料预热段)每个加热盘管组由翅片管/光管、回弯头、带衬里的端管板、中间管板等组成,盘管组之间由弯头、集合分配器、短管等组成的联络管连接。
裂解炉新旧辐射炉管、Y型件的焊接技术

《 化工装备技术》 第 2 8卷 第 3期 20 07年
4 3
裂 解 炉 新 旧辐 射 炉 管 、Y型 件 的焊 接 技术
李复 员 朱正 写 王起顺 张小 宇
( 国石 油 兰 州 石 化 公 司 石 油 化 工 厂 ) 中
摘
要
针 对 乙烯裂 解 炉辐 射 炉 管使 用 周期短 ,分析 了辐射 炉 管及 其 焊缝 失效 的原
( 稿 日期 :2 0 -32 ) 收 070 —4
验、试验已完成并合格且资料齐全并符合要求 的前 提下 才能进 行 。 ( )压力容器制造完成后 ,经联合检查 1
合格后 方 可进行 ;
( ) 应严 格按 照 检验 、试 验 的程 序 和 要 2
维普资讯
改进焊接工艺 ,选用高质量的焊条材料 ,提高
焊缝质 量 。 1 辐射 炉 管失效 简述 及分 析 由于 各 种 原 因 裂解 炉 经 过 4年左 右 运 行
因 ,对 回收 再利 用的 旧辐射 炉管 ,提 出 了新 旧辐射 炉 管与新 旧 Y型 件 的焊接 工 艺。
关键 词 裂 解 炉 辐射 炉管
Y型件 焊接 工 艺 裂纹
渗碳
裂 解 过程 而 引 起 的裂 解 炉炉 管 中的结 焦 反应 。
0 概 述
结 焦会增 加 炉管管 壁热 阻 ,降低传 热 系数 ,导
严重者导致断裂。从大量的分析来看,渗碳较
严 重 的是 在 Y 型件 焊 缝 附 近 ,此 处 的 渗 碳 速
度较其 它地方快 , 碳量较其 它焊缝 处严 重 渗 得多。经多次温度的升降 ,渗碳后材质的物理
性 能 和机械 性能 发生 了变 化 ,在管 内壁产 生 附
浅谈大庆石化乙烯装置裂解炉炉管焊接质量控制措施

除缺陷后 仍按正式焊接工艺规范补焊 . 补焊后再进行射线探伤 裂解 炉是乙烯装置的关键设备 . 具有结构布局紧凑 . 安装 工程 量 ( 2 ) 不合格的焊缝必须进行返修 ( 3 ) 要求焊后热处理的炉管 , 应在热处理前 返修 . 如在热处理后还 大, 施工 工序复杂 , 炉体施工各专业交叉作 业 , 工序衔接紧密 , 上下 工 返修后应重新进行热处理并做硬度测试 序制约性强 , 管内部清洁及保护要求高 . 管子坡 口加工 、 组装 精度及 弹 需返修 . 簧支 吊架的调节要求严格 . 炉管 、 管道材质复杂 , 涉及镍合金 、 不锈 钢 、 5 . 焊 接接 头质 量 检 验 铬钼钢 、 碳 钢等 , 既有同种材质焊接 . 也 有异种材料的焊接 . 尤其是 辐 5 . 1焊缝外观检查 射段 炉管 的焊接质量控制难度更大 ( 1 ) 焊接接头应在焊完后立 即去除渣皮 、 飞溅物 . 清理干净焊缝表 1 . 裂解 炉 炉 管 焊 前 准 备 面, 并 根据检验方法的要求 . 对焊接接头表面进行相应的打磨 处理 ( 2 ) 焊缝外观成形应 良好 , 焊缝与母材金 属应圆滑过渡 . 焊缝 宽度 ( 1 ) 编 制施 工组织设计 、 施工方 案 、 施工流程等技术文件 , 并按 审 以每边 盖过坡 口边缘 2 mm为宜 批后 的施工组织设计 、 施 工方案 、 施工流程等技术文件组织施工 5 _ 2无 损 检测 ( 2 ) 焊接工艺评定的选 用。根据设计要求和相关规范规定选择 焊 ( 1 ) 辐射段炉管及对流段 管口配管和跨接管焊缝内部质量应符合 接工 艺评定报告 . 焊接工艺评定要覆盖所有的材质和厚度 。 图纸 、 规范要求 。 ( 3 ) 焊接工艺 。 ( 2 ) 所 有对接焊缝坡 口、 焊 道根 部及表 面进行磁粉检测或液体渗 根据焊接 工艺评定结果 , 按照 图纸 、 设计文件 、 标准规范 、 法律 法 规等相关要求编制科学的 、 系统 的、 切实可行的焊接工艺 透检验 , 液体渗透检验结果应符合 J B 4 7 0 8 . 5中 I 级为合格 1 ) 炉管材质规格 。 裂解炉炉管是多材质 、 多规格的复杂系统 。由7 6 . 焊 后 热 处理 f P WH T1 个类 别组 成 , 直 径 从  ̄3 8 m m 到 中3 2 3 . 8 m m, 厚度 由 8 mm到 3 3 . 3 2 m m ( 1 ) 根据设计要求及焊接工艺 评定 . 炉管焊接完成后 P 1 1 、 P 2 2以 2 ) 焊接方法。炉管采用全氩弧焊( G T A W1 焊接, 采用高频起弧焊机 及 N 0 8 8 1 1 要进行热处理 . 而异种钢之间的焊缝不用做热处理 测 温宜 起焊点应在两定位焊缝之间 , 在坡 口内引弧 , 不得在非焊接部位引弧 . 采用热电偶 . 并用 自动记录仪记录热处理曲线. 测温点应在加热区内 焊丝前端应置于保护气体中。管线焊接 时, 管内应 防止穿堂风 . 采用多 ( 2 ) 热处理的加热范围. 应为 以焊缝中心为基准 , 两侧各不小 于焊 层焊时 . 施焊过程应控制层间温度 . 层间温度控制在 1 2 0 %以下 . 各层焊 缝宽度的三倍且不小于 2 5 m m的区域 . 加热 区以外 的 l O O m m范 围应 道的接头应错开 3 0 m m ~ 5 0 a r m, 接弧处应保证熔合 . 收弧弧坑应填满 在 予 以保温 焊接工艺评定所确定 的焊接线能量范 围内. 宜选择较小的焊接线能量 ( 3 ) 热处理后 , 应对焊缝 、 热影响 区及其附近母材分别抽检 表面布 ( 4 ) 施工方法 。 氏硬度 , 抽检 比例为 1 0 % 斯 测硬度值应 ≤2 2 5 H B , 否则 . 必须重新进行 1 ) 坡V I 形式 。 壁厚相等接头 : 壁厚不相等接头形式: 急冷换热器坡 热处理并做硬度测试 口形 式 : E F 一 3 1 2 0 ~ E F 一 3 1 6 0模块跨接管坡 口形 式等等 7 . 质 量 控 制措 施 2 ) 坡1 2 1 加工 炉管 的切割及坡 口加工宜采用机械方法. 若采用等 ( 1 ) 炉管及管件 的焊接 , 应采用 多层多道的焊接方法 对铬钼钢材 离子切割 . 应清理其加工 表面 . 若采用砂轮机对坡 V I 进 行加 工时必须 质 的底层焊道 , 宜采用氩弧焊方法进行焊接 。用奥 氏体焊材焊接底层 使用 不锈钢砂轮片 焊道时 . 管内应充氩气保护 3 ) 炉管组对 。焊缝间隙和错边量对焊接质量有重要影响 . 不同壁 ( 2 ) 底层 焊道完成后 , 应立即进行下一层的焊接 , 且应连续焊完。 厚的管子 、 管件组对时 , 内壁差大于 0 . 5 mm, 外壁差大于 2 mm。焊件组 ( 3 ) 严禁在坡 口以外的母材表面引弧 、 试验 电流 , 尽量避免电弧擦 对前 . 清理 坡 口表面及其两侧母材不 少于 2 0 m m范围 内的区域 . 不得 伤母材 . 不能随意在管道上焊接临时支撑物 采用强力组对定位 定位焊缝的尺寸及 间距应符合的规定 8 . 结 束 语
裂解炉管道焊接及热处理施工技术措施

DREP100万吨/年乙烯装置工程裂解炉区及锅炉给水系统文件名称:裂解炉管道焊接及热处理施工技术措施文件编号:裂解炉-02-HJ-03文件类别: 02****目录1、工程概况 (3)1.1工程简介 (3)1.2管道主要材质焊接材料选用表 (3)1.3焊接工艺特点 (4)1.4编制依据 (4)2、焊接施工程序 (5)3、主要施工方法 (5)3.1、坡口加工 (5)3.2定位焊 (5)3.3、焊前预热 (6)3.4、焊接 (7)3.4.1碳钢A106B、API5L B及A516GR65钢管线焊接 (7)3.4.2低温钢(A333GR6)的焊接 (8)3.4.3铬钼钢P11管线焊接 (8)3.4.4P22(A6912.25C R)管线焊接 (10)3.4.5P91管线焊接 (11)3.4.6铸造高铬镍耐热合金钢管及其与其它钢的异种钢焊接 (12)3.4.7TP321H、TP304L奥氏体钢焊接 (13)3.4.8异种钢管线焊接 (14)3.5焊后热处理 (14)3.6、焊接检验和焊后返修 (16)4、施工设备、检测工具及施工手段用料 (17)5、质量、HSE保证措施 (18)5.1质量保证措施 (18)5.2、HSE保证措施 (20)6、竣工资料的收集、整理 (20)附件:工作危险性分析(JHA)报告 (22)1、工程概况1.1 工程简介中国石油独山子石化公司改扩建炼油及新建乙烯工程,管道安装为裂解炉区工艺管线、炉本体管线、炉前管廊管线、高压锅炉给水区管线及高压锅炉给水管廊管线。
管道最高设计温度920℃,设最高压力22MPa。
管道主要包括DN15-DN2000以及少量其它规格的管线;管线壁厚最薄为δ 2.27mm,最厚为33.32mm。
管道材质主要有G-X45NiCrSiNb45-35、G-X40NiCrSiNb35-25、G-X10NiCrSiNb32-20、TP321H、TP304L、P91、A691 2.25Cr、P22、P11、A333GR6、A106 B及API5L B钢。
乙烯裂解炉新_旧炉管间的焊接研究

MFB" 堆焊
无表面裂纹 未裂
1
MFB" 原焊接工艺 未堆焊 无表面裂纹 未裂
5
MFB" 原焊接工艺 2’ 基堆焊
;H= " H 年 ! 个月 MFB" 原焊接工艺 未堆焊
无表面裂纹 未裂 无表面裂纹 未裂
ห้องสมุดไป่ตู้
H
MFB" 原焊接工艺 <用做焊接试样 >
MFB" 堆焊
无表面裂纹 未裂
注:表中未特别注明堆焊后表面有裂纹就表示堆焊后无裂纹
新炉管 1:0 ;
旧炉管 50 " < != 666 , > "0 5 < 56 666 , >
因而,新、旧炉管之间的焊接存在一定的困难,主要有 ?" @ : !旧炉管内壁渗碳、氧化和腐蚀,使塑性和韧性明显下降,在 焊接应力作用下极易产生裂纹;"旧炉管变形、弯曲和鼓胀造 成接头组对时错边和中心偏移,形成应力集中;#旧炉管渗碳 层与基体间密度和热胀系数的差异,造成局部应力增大;$旧 管材晶内弥散碳化物聚集及晶界碳化物网块状化,使材料塑性 和韧性下降,无论裂纹是何种成因,只要生成将以声速扩展至 整管壁厚。因此,新、旧炉管之间的焊接成功率极低。提高 新、旧炉管之间的焊接成功率,对于中度以上损伤的旧炉管难 度较大。文献 ?"@ 介绍了采用固溶处理方法消除旧炉管的损 伤。从 AB!6 型炉管的试验结果看, !! 和 !" 均有提高,但冲 击韧度无明显提高。因此,在常温下焊接时,如果有裂纹源存 在时,在焊接应力作用下仍然不可避免产生裂纹。主要因为: 一是,固溶处理无法消除旧炉管氧化、腐蚀等损伤;二是,由 于渗碳层的 #< C> 远高于基体 % 相在固溶处理温度下的饱和溶 碳量,因此,晶界粗大的网块状碳化物组织、晶内聚集在一起 的二次碳化物在固溶处理中不可能有明显的变化,相反,与渗 碳层相连的组织在固溶处理过程中 #<C> 会大幅度升高,带来 与渗碳相似的后果。
厚壁乙烯裂解炉管焊接工艺

21/4Cr-1Mo厚壁乙烯裂解炉管焊接工艺进行了Cr-1Mo炉管焊接工艺试验和接头性能检验,选择了合适的焊接规范和热处理回火参数,接头经回火脆化敏感性试验,其脆化温度增量远低于控制指标。
我厂承制的北京燕山石化6 万t/a乙烯裂解炉对流段,材料全部由日本进口。
其中一组炉管材料为Cr-1Mo,规格为,其设计压力21.9 MPa,设计温度516 ℃,属于高温高压工况条件。
我厂虽有多年制造裂解炉对流段的经验,但材料一般以碳钢为主,且壁厚都在12 mm以内。
对于高温高压炉管材料的焊接,国内外研究较多的是Cr5Mo及12CrMoV等,但对于厚壁Cr-1Mo炉管的焊接则研究较少。
为了合理确定其焊接线能量、预热温度及焊后热处理制度,因此对其进行了探讨。
2 焊接工艺试验及分析2.1 预热温度试验用Cr-1Mo钢管,壁厚27 mm,进行常温和不同预热温度下的斜Y型加强拘束抗裂性试验,试验焊接规范E=10.2 kJ/cm(I=110 A,U=14 V,v=9cm/min),试验焊缝焊后经48 h放置,用着色探伤检查焊缝表面和用低倍光学显微镜观察断面,其表面和断面裂纹率见表2。
表2 抗裂性试验结果试验表明,Cr-1Mo钢冷裂倾向比较大,随着预热温度的提高,接头抗冷裂能力得以改善。
当Tr≥200 ℃时,冷裂纹全部消除,因此,焊前预热温度选择在200 ℃左右即可满足抗裂要求。
2.2 焊接线能量从前面试验可知,在预热温度200 ℃,焊接线能量E为10 kJ/cm左右时,焊缝不出现裂纹,那么,此时的E值应为临界值(下限值)。
从成型来看,在此规范下进行根部打底和第二、三层过渡,全位置成型良好,反面余高也在控制指标范围内,而其它焊层的规范在使接头获得良好的综合力学性能前提下应尽可能选择大一些,以提高生产效率。
因此,须确定一个线能量上限值,为此选用两种方案进行试验:①10 kJ/cm规范打底过渡,20 kJ/cm规范填充和盖面。
②10 kJ/cm规范打底过渡,30 kJ/cm规范填充和盖面。
浅谈裂解炉炉管安装与焊接
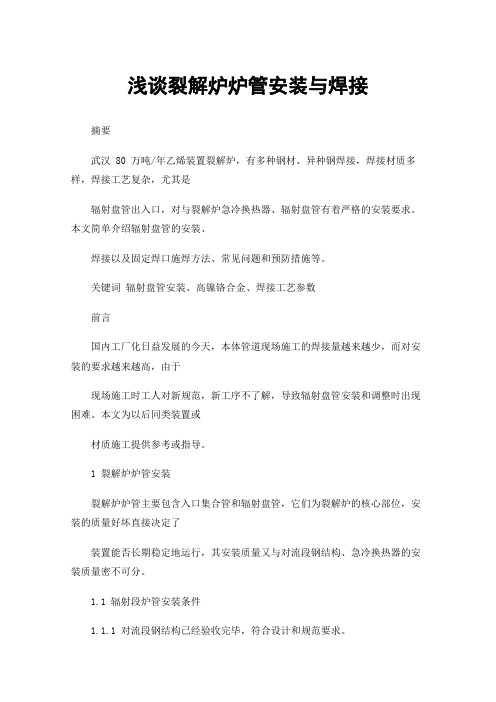
浅谈裂解炉炉管安装与焊接摘要武汉 80 万吨/年乙烯装置裂解炉,有多种钢材、异种钢焊接,焊接材质多样,焊接工艺复杂,尤其是辐射盘管出入口,对与裂解炉急冷换热器、辐射盘管有着严格的安装要求。
本文简单介绍辐射盘管的安装、焊接以及固定焊口施焊方法、常见问题和预防措施等。
关键词辐射盘管安装、高镍铬合金、焊接工艺参数前言国内工厂化日益发展的今天,本体管道现场施工的焊接量越来越少,而对安装的要求越来越高,由于现场施工时工人对新规范,新工序不了解,导致辐射盘管安装和调整时出现困难。
本文为以后同类装置或材质施工提供参考或指导。
1 裂解炉炉管安装裂解炉炉管主要包含入口集合管和辐射盘管,它们为裂解炉的核心部位,安装的质量好坏直接决定了装置能否长期稳定地运行,其安装质量又与对流段钢结构、急冷换热器的安装质量密不可分。
1.1 辐射段炉管安装条件1.1.1 对流段钢结构已经验收完毕,符合设计和规范要求。
1.1.2 辐射盘管在急冷换热器安装前已经用临时支撑挂于辐射段炉膛内。
1.1.3 急冷换热器已经安装完毕并找正,急冷换热器入口标高、中心线、垂直度已经进行验收满足设计值,并符合规范要求。
1.2 辐射盘管安装在安装过程中,出现第二程炉管紧靠、交错;入口集合管中心偏移等问题,根据现场的实际情况制订安装要求。
1.2.1 按设计图纸将辐射盘管弹簧吊架位置在钢结构梁上放线,并将吊板与钢结构点焊,吊板间距经验收合格后将吊杆和连接扁担相连,检查吊杆是否垂直,连接扁担是否水平。
1.2.2 调整辐射盘管90°吊耳弯头、吊杆、连接扁担标高使之处于设计值,然后将弹簧吊架与90°吊耳弯头、吊杆、吊板相连。
1.2.3 确认辐射盘管出口处于设计所示的标高和位置,将辐射盘管出口与急冷换热器入口按正式焊接工艺点焊,组对时不得将辐射盘管强行就位,检查辐射盘管是否处于自由悬吊状态,此时拆除临时支撑和包装卡具;1.3 入口集合管安装条件1.3.1 现场已对入口集合管进行吹扫,并确认管内无异物,防止阻塞文丘里管。
裂解炉炉管焊接方法

8.1.3裂解炉焊接★辐射段炉管的焊接1 焊接方法采用全氩弧焊(GTAW)方法。
2 焊接工艺评定。
采用公司裂解炉熔铸管HP50SiΦ101.6 ×8编号86-46的焊评。
按JB4708标准的规定,炉管的壁厚均在有效范围之内。
3 焊工。
焊工应取得ASME或国内标准熔铸管相应位置合格的资格。
4 焊机。
采用的氩弧焊机应具有有效的引弧和衰减功能。
1图8.1.3-1为焊口位置示意图。
6 表8.1.3-1为焊接工艺一览表。
图8.1.3-1 焊口位置示意图7 焊接工艺要求7.1 坡口加工。
采用U型坡口,使用机械加工法。
坡口附近不得重力碰撞。
坡口附近要用丙酮清洗,不准有任何脏物。
7.2 采用点焊法组装。
严禁强行组对。
每焊口点焊2-3处,长度5-10mm。
弧坑要填满,焊前将焊点磨成斜坡。
7.3 背面氩气保护的办法可采用水溶纸或局部管内通气。
7.4 焊丝要保持干燥。
不准有水、油、污物。
7.5 为了防止裂纹,底层焊肉要在3mm左右。
采取焊两层的方法。
第一遍不能穿透过高,保证内部穿透0-2mm,小规范快速焊,紧接着焊第二遍。
8 焊接注意事项8.1 焊接环境在 5ºc 以上,空气湿度<90%,风力不大于2级。
8.2 焊前不预热,焊后不进行热处理。
但坡口附近潮湿可用气焊烤干。
8.3 横焊采用迭焊法。
焊炬仅作轻微摆动。
每层接头错开10-20mm。
9 焊缝检查9.1底层焊后作着色检查(PT),同时确认坡口无裂纹。
(坡口焊前作肉眼检查)9.2 焊缝外部加强高≯2mm,可采用打磨法修正。
内侧穿透0-2mm,采用射线检查确定。
9.3 焊缝外观检查合格后,100%进行射线检查,采用GB3323标准,Ⅱ级合格。
- 1、下载文档前请自行甄别文档内容的完整性,平台不提供额外的编辑、内容补充、找答案等附加服务。
- 2、"仅部分预览"的文档,不可在线预览部分如存在完整性等问题,可反馈申请退款(可完整预览的文档不适用该条件!)。
- 3、如文档侵犯您的权益,请联系客服反馈,我们会尽快为您处理(人工客服工作时间:9:00-18:30)。
乙烯裂解炉辐射段炉管的焊接
前言
中原石化总厂十万吨裂解炉,辐射段炉管所用材料为(Cr35Ni45+微合金),辐射段出口材料为20Cr32NiNb。
Cr35Ni45的合金系统较之以前的Cr25Ni35有了较大的发展,增加了Cr、Ni元素含量,相应提高了耐高温性能。
炉管采用离心浇铸的方法生产,其原始铸态表面为均匀分布有颗粒状凸起的“珍珠”表面,这种表面不仅有利于热交换,而且对抗氧化和抗燃气腐蚀有利。
管子的内表面有很薄一层疏松组织,炉管的基体组织相当致密,主要由沿半径方向分布的柱状晶组成,内部没有气孔、夹杂及缩孔等铸造缺陷。
管件(包括180º弯头、90º吊耳弯头、Y型管等)为静态浇铸法生产,合金成分不均匀,存在较大成分偏析,焊接时易产生裂纹。
1 焊接性分析
1.1 化学成分分析
炉管材料Cr35Ni45的化学成分见表1。
表 1Cr35Ni45的化学成分
化学成分 (%)
C Si Mn P S Cr Ni Mo W Nb Cu Al
0.4~ 0.6 1.2~
1.8
≤
1.5
≤
0.03
≤
0.03
30~
37
40~
47
≤
0.5
≤
0.30
0.5~
1.5
≤
0.25
≤
0.05
为了深刻认识炉管中主要元素及微量元素的作用,查阅了一些文献,并对其在耐热铸钢中的作用进行了分析。
C:C与Cr、Mo、Ti、V、Nb等形成一次碳化物M7C3和NbC。
在高温时效过程中,基体中的过饱和固溶碳以细小弥散的M23C6析出,提高了钢的强度。
另外增加碳含量还能抑制б相析出。
但碳含量过高,二次碳化物大量析出,会降低合金的韧性、恶化焊接性。
因此Cr35Ni45合金含碳量不超过0.60%,但Si是促进б相析出元素,加入量过多,使焊接性恶化、降低持久强度。
裂解炉管硅含量一般控制在1.50%~2.00%。
Mn:它能改善焊接性能,但固熔强化促进б相析出,加入量过多能降低合金的抗氧化性能。
一般控制在1.5%以下。
Cr:它是合金中主要的固溶强化元素和碳化物形成元素。
它在材料表面形成致密的Cr2O3保护膜,
对合金的抗氧化、强度、抗渗碳性能起着决定性作用。
但Cr含量过高会导致б相析出,因而降低合金的强度和韧性。
Ni:它是形成和稳定奥氏体,提高抗渗碳、抗氧化、高温强度和韧性的主要元素。
对于裂解炉来说,其抗渗碳性能的优劣是十分重要的,也是影响裂解炉寿命的主要因素。
由于裂解炉在运行过程中管内壁会产生渗碳,渗碳层的出现一方面在管内壁会产生附加应力,另一方面渗碳也使炉管材料的组织和性能发生变化,结果会使炉管局部开裂或腐蚀穿孔。
W、Mo、Nb都是固溶强化元素,能提高合金的高温强度,抑制碳的扩散速度,但是加入过量则会影响合金的抗氧化性能,并促进б相析出,降低合金的强度和韧性。
Nb、Ti、V它们形成碳氮化物,改变晶界碳化物形态,细化M23C6,使其均匀弥散分布,延迟碳化物粗化过程,从而提高合金的高温蠕变强度
Al:它在奥氏体不锈钢中形成AlN,促进长期蠕变时б相形成和粗化,降低蠕变寿命。
因此认为Al在奥氏体耐热钢铸管中是有害元素,其含量应严格控制。
1.2 焊接性分析
炉管材料为铁基高铬镍合金,焊接性较差,焊接工艺措施稍有不当,便会出现问题,表现如下:
1.2.1 由于合金元素含量较多,导热性差,焊缝与母材容易过热,造成晶粒粗大,使接头力学性能和耐蚀性能下降;
1.2.2 焊接时易出现热裂纹及再热裂纹;
1.2.3 对应变时效敏感。
焊后如果残余应力较大,在时效过程或工作温度高于时效温度时,易产生“应变时效”裂纹;
1.2.4 对焊道熔池裂纹较敏感;
1.2.5 焊接熔池液态金属流动性差,铁水发粘,熔深小,易出现焊口根部的熔合不良及促使凝固裂纹的产生。
2 焊接方法及焊接材料的选取
焊接方法:主要考虑小的热输入及小的熔合比,故采用手工钨极氩弧焊。
焊接材料:因炉管用在高温条件下,所以高温强度,蠕变强度要求高,因此,炉管本体焊接材料选取与母材相匹配的高碳同质焊材:牌号XTM,其公称成分为35Cr45Ni,具体化学成分见表2。
辐射段炉管出口材料为20Cr32NiNb,与辐射段炉管Cr35Ni45相焊时,焊接材料选择Inconel 82,该焊材为镍基焊材,塑性较好,其化学成分见表3。
表2 焊丝XTM的化学成分
C Si Mn P S Cr Ni Ti Zr Nb
0.42~ 0.48 0.5~
1.8
1.0~
2.5
≤
0.015
≤
0.015
34~
37
43~
47
0.05~
0.15
0.05~
0.10
0.5~
1.0
表3 焊丝Inconel 82的化学成分
化学成分 (%)
C Si Mn P S Cr Ni Ti Nb+Ta
≤0.10
≤
0.50
2.5~
3.5
≤
0.03
≤
0.015
18.0~
22.0
≥
67
≤
0.75
2.0~
3.0
3 焊接
在焊接工艺评定的基础上,针对现场的实际情况,制定了现场的焊接工艺技术措施。
3.1 坡口型式
由于炉管材料的液体金属流动性不如一般钢铁材料,焊接工艺不良时很容易发生未熔合现象。
如果加大焊接电流以增大高温合金熔池金属的流动性,不但效果不大,而且还会造成过热的不良影响。
3.2
焊材牌号规格
(mm)
焊接电流
(A)
电弧电压
(V)
焊接速度
(cm/min)
氩气流量
(L/min)
XTM InconeI82 2.4×2.4
Ф2.5
80~100 11~13 8~10 10~15
3.3 焊接
3.3.1 对口要求
管道对口应做到内壁平齐,如有错口,不得大于0.5mm,对口时不得采用强力组对,应做到无应力对口;
3.3.2 焊接工艺要点
图1
焊接前应用丙酮清洗坡口,以防有害杂质对焊缝造成危害;焊接时,焊缝背面应充氩保护,氩气纯度不小于99.99%;引弧时应在坡口内,以免在坡口外引弧对母材造成伤害;炉管开始焊接时,不得将炉管组对时所用的工卡具拆除,至少焊接三层后方可拆除,以免由于外加因素产生的附加外应力,使焊缝产生裂纹;焊接时应采用小线能量和小截面焊道;底层焊接时,应采用小电流,使电弧垂直对准坡口中心,电弧应稍作摆动,保证坡口根部熔合良好。
底层焊接时,打底厚度要相对较厚,以免底层焊道强度不足,产生裂纹;打底完成经检验合格后,应及时进行次层的焊接,以防产生裂纹;次层焊接时,应采用窄焊道技术,从第三层以上,应采用多道焊接技术;焊接时,应逐层对焊缝外观进行检查;合格后方可焊接次层;多层焊时,应控制层间温度在100℃以下,以防接头过热,焊缝热影响区晶粒粗大,使接头的强度下降;收弧时应填满弧坑,收弧时应先停弧,滞后停气,以防产生火口裂纹.
3.4 焊接检验
渗透探伤:坡口着色,底层着色,面层着色。
射线探伤:100%射线探伤。
3.5 现场焊接实例
以辐射段出口的焊接为例,见图2所示.
3.5.2 原因分析
3.5.2.1 材料本身的因素,该种材料较为难焊,易产生裂纹。
3.5.2.2 在底层焊接时,焊缝必将产生横向收缩,焊缝下部管子由于本身重力因素,不能向上移动,焊缝上部由于与废热锅炉相联法兰已经把紧,不能自由伸缩。
由于焊口两端的相对固定,焊缝不能自由收缩,焊缝产生较大内应力,且底层焊缝厚度较薄,当内应力超过材料的强度极限时,焊缝产生裂纹。
3.5.3 解决措施
3.5.3.1 在焊口下部的Y型管或90°弯管上加支撑杠或吊链,焊接时使支撑杠或吊链处于受力状态,不能松动,以免由于焊口下方管子自重对焊缝产生的附加外应力。
当焊接3层或3层以上时方可将支撑杠或吊链撤除。
3.5.3.2 将与废热锅炉相连的法兰螺栓松开,让焊口上方的管子或法兰处于自由伸缩状态,确保焊口无附加外应力。
3.5.3.3 底层焊接时,打底厚度要相对较厚,确保焊缝有足够的强度。
3.5.4 实际效果
采用上述措施后,焊接时未出现焊接裂纹,效果良好,满足了炉管的焊接技术条件要求。
4 结束语
炉管焊接时,除采用正确的焊接工艺外,还应采用合理的坡口型式及相应的技术措施,尤其是无附加外应力,确保焊口处于自由状态,从而避免裂纹的产生。