线材生产工艺.ppt
不锈钢线材生产工艺
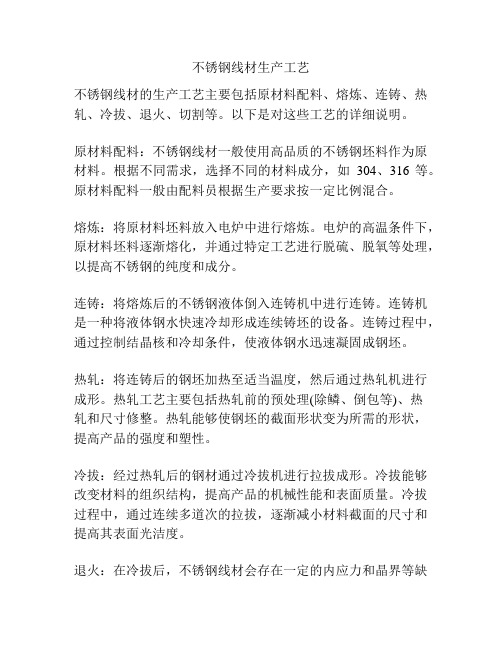
不锈钢线材生产工艺不锈钢线材的生产工艺主要包括原材料配料、熔炼、连铸、热轧、冷拔、退火、切割等。
以下是对这些工艺的详细说明。
原材料配料:不锈钢线材一般使用高品质的不锈钢坯料作为原材料。
根据不同需求,选择不同的材料成分,如304、316等。
原材料配料一般由配料员根据生产要求按一定比例混合。
熔炼:将原材料坯料放入电炉中进行熔炼。
电炉的高温条件下,原材料坯料逐渐熔化,并通过特定工艺进行脱硫、脱氧等处理,以提高不锈钢的纯度和成分。
连铸:将熔炼后的不锈钢液体倒入连铸机中进行连铸。
连铸机是一种将液体钢水快速冷却形成连续铸坯的设备。
连铸过程中,通过控制结晶核和冷却条件,使液体钢水迅速凝固成钢坯。
热轧:将连铸后的钢坯加热至适当温度,然后通过热轧机进行成形。
热轧工艺主要包括热轧前的预处理(除鳞、倒包等)、热轧和尺寸修整。
热轧能够使钢坯的截面形状变为所需的形状,提高产品的强度和塑性。
冷拔:经过热轧后的钢材通过冷拔机进行拉拔成形。
冷拔能够改变材料的组织结构,提高产品的机械性能和表面质量。
冷拔过程中,通过连续多道次的拉拔,逐渐减小材料截面的尺寸和提高其表面光洁度。
退火:在冷拔后,不锈钢线材会存在一定的内应力和晶界等缺陷,为了消除这些缺陷,需要进行退火处理。
退火过程中,将不锈钢线材加热至适当温度,然后慢慢冷却,以恢复其本身的塑性和韧性。
切割:经过退火处理后的不锈钢线材,根据客户要求,通过切割机进行切割。
切割机能够将长线材切断成所需长度的线材,以便进一步加工或使用。
以上是不锈钢线材的生产工艺。
这些工艺保证了不锈钢线材的质量和性能,使其能够广泛应用于建筑、机械、船舶等领域。
《拉拔工艺》课件

因此,
,即绞盘的圆周速度大于线的运动速度是实现带滑动拉拔
的基u本n 条件vn。
un vn
基本若条定件义也:可描述Rn为:u滑n为u动n滑v率n动率,则。实现带滑动拉拔的 Rn 0
c 如何保证
un vn
取决于拉线机的设计,不能改变,因此只能控制
在稳u定n 拉拔过程中,下式应成立:
un vn
,使
取3道次。 取4道次。 取3道次。 取3道次。
1 1.25, 2 1.27, 3 1.26, 4 1.22, 5 1.23 6 1.24, 7 1.24, 8 1.26, 9 1.27, 10 1.26
11 1.23, 12 1.23, 13 1.17
7)线材拉拔配模设计
a 保证产品性能 对软态产品而言,性能由成品退火参数决定,确定总加 工率时只要避开临界变形程度即可;对硬态、半硬态产品而言,应根据加 工硬化曲线查出规定性能所要求的加工率,以此算出坯料尺寸。
b 保证操作顺利进行 针对衬拉管材而言,因为这时既有减径量又有减壁 量,若二者变形量设计不当,会导致操作不能进行。例如,若总减径量< 总减壁量,则当管坯直径达到成品尺寸时,其壁厚仍大于成品壁厚,此时 由于芯头无法放入而不能继续减壁。因此,衬拉时,
5 3.5: n ln(5 / 3.5)2 3.04 ln1.26
3.5 2.3:
ln(3.5 / 2.3)2
n
3.6
ln1.26
2.3 1.6: n ln(2.3 /1.6)2 3.1 ln1.26
1.6 1.2: n ln(1.6 /1.2)2 2.5 ln1.26
道次延伸系数分配:
《拉拔工艺》
拉拔配模:根据成品的要求(有时还包括坯料尺寸)来确定拉拔 道次及各道次所需模孔形状、尺寸的工作。
铜线拉丝工艺理论知识

PPT文档演模板
铜线拉丝工艺理论知识
铜导体为什么需要退火软化处理?
• 电线电缆导体经冷拔加工后,均存在硬化现象, 抗拉强度和屈服强度明显增加,塑性和韧性普遍 降低,伸长率的变化尤为显著。欲消除冷拔硬化 现象,提高延伸率,就必须进行退火处理,以消 除内部应力及缺陷,使之恢复到冷加工前的物理 及机械性能。如铜导体经550℃退火处理后,导线 柔软,不易被拉断。同时,导体的电阻率降低约 2.1%,减小了线路损耗。因此,退火软化是电线 电缆及漆包线生产过程的主要环节之一。
1.3 建议:由于真空退火炉工艺落后,能耗大,产品质 量不稳定,生产成本高,市场竞争能力低,建议尽 快淘汰真空退火炉。
PPT文档演模板
铜线拉丝工艺理论知识
2 热管式退火炉
热管式退火炉 也是比较传统的 退火工艺,其设 备的结构示意图 如图2所示。它 主要有:不锈钢 管、加热棒、测 温热电偶、冷却
水及导轮组成。
•导轮 •放线盘
•加热棒
•退火不锈钢管 •导轮
•收线盘
•冷却水
•图2 管道式退火炉结构示 意图
PPT文档演模板
铜线拉丝工艺理论知识
2 热管式退火炉
• 2.1 优点:技术简单,设备简陋,设备投资低,对 操作人员要求低,能够实现多头退火。
• 2.2 缺点:耗电量大,退火一吨铜丝耗电在225度 电以上;无法实现退火速度自动跟踪;穿线麻烦, 设备庞大。
垫、固定螺栓等组成。
•图1 真空退火炉结构示 意图
PPT文档演模板
铜线拉丝工艺理论知识
1 真空退火炉
1.1优点:技术简单,设备简陋,设备投资 低,对操作 人员要求低。
1.2缺点:耗电量大,退火一吨铜丝耗电在230度电以 上;生产工艺不稳定,一旦漏气全炉均会氧化变色; 真空炉内的上下、左右温度不均匀,会出现内外电 线软硬不均,更有甚者,还会出现电线粘连现象; 不能在线连续退火,且退一罐线的周期太长。
轧材种类及其生产工艺流程(PPT 94页)

钢材的冷加工生产工艺流程
• 钢材的冷加工生产工艺流程包括冷轧和冷 拔。
• 其特点是必须有加工前的酸洗和加工后的 退火相配合,以组成冷加工生产线。
• 直到现在仍然在一些国家的钢材生产中占重要地位。 • 近二十年来迅速发展起来的连续铸钢技术,将钢水直接铸
成一定断面形状和规格的钢坯,省去了铸锭、初轧等许多 工序,大大简化了钢材生产工艺过程,其生产工艺流程示 意如图6-2。 • 优点:不仅可以大大简化钢材生产工艺过程,而且有着节 约金属、提高成材率、节约燃料消耗、降低生产成本、改 善劳动条件、提高劳动生产率及改善枝晶偏析,提高钢材 质量等许多优点。
• 铝合金的比强度大,某些铝合金的比强度及比刚 度可赶上甚至超过了钢。
• 铜及其合金一般可分为紫铜、普通黄铜 (Cu-Zn)、特殊黄铜、青铜及白银(CuNi)等。它们具有很好的导电、导热、耐蚀 及可焊等性能,故和铝材一样广泛应用于 各部门。
• 钛及钛合金的力学性能和耐蚀性能高,比 强度和比刚度都很大,因而是航空、航天、 航海、石油化工等工业部门中极有发展前 途的结构材料。
在50万-300万t之间,以年产80万t-200万t者居多,可称为板、 带生产的中、小型系统。
2.型钢生产系统:规模往往并不很大。 大型:年产100万t以上; 中型:年产30万-100万t; 小型:年产30万t以下。
3.混合生产系统: 在一个钢铁企业中可同时生产板 带钢、型钢或钢管时,称为混合系统。
7.1轧材的种类
• 按金属与合金种类的不同,可分为各种钢材 以及铜、铝、钛等有色金属与合金材料;
Φ5.5线材轧制工艺

Φ5.5mm线材轧制工艺的分析与测定高海建摘要:分析了Φ5.5mm线材的生产工艺特征及工艺要求;介绍了马钢借助先进的记录仪及对大量生产数据的采集,找出了生产Φ5.5mm线材时高速区频繁堆钢的原因,进而优化了高速区工艺控制参数及时序上的设定,模索出一套Φ5.5mm线材的专用生产工艺,使班产量由300t提高到500~600t。
关键词:高速线材轧机;Φ5.5mm线材;轧制工艺分类号:TG335.6+3Analysis and measurement of rolling process for Φ5.5mm wireGAO Hai-jian(Maanshan Iron & Steel Co., Ltd., Maanshan 243003, China)Abstract:The technology characteristics and requirements of rolling Φ5.5mm wire are analyzed. The reasons of steel pushing in high-speed zone are found out. The control and setting of process parameters are optimized, and a special rolling technology for Φ5.5mm wire is found out. Based on them, the output of per shift can be increased from 300t to 500~600t.Key words:high-speed wire mill; Φ5.5mm wire; rolling technology▲1 前言近年来,线材工业生产技术取得了飞速发展,其显著特点是,成品轧机速度大幅度提高,从60年代中期第1套高线轧机的50m/s 左右提高到当今的140m/s。
棒线材生产工艺培训

生产工艺-加热
加热:线材生产属于热轧一种形式,轧制 之前的钢坯原料需要先经过加热到一定温 度。
加热目的:提高塑性,降低变形抗力,改 善内部组织,消除铸锭缺陷。
加热要求:严格执行加热制度,钢坯整体 温度均匀,无过热、过烧等现象。
生产工艺-开轧温度
开轧温度:咬入第一架轧机时的轧件温度。 我们经常把开轧温度和加热温度混为一谈,这是
精轧机组前后设置有轧件控冷装置,精轧机组后设有剪切、 精整、收集等装置。
主要设备
两条高线主要设备的选择,根据钢坯断面、产品规 格及其尺寸精度的要求,全线均采用无扭轧制。共 分4个机组,由粗轧6架、中轧6架、预精轧6架、精 轧10架、共28个机架组成。
A、B线轧机配置相同,B线和A线的不同在于B线考 虑了预留减定径机组,A线不设减定径机组也不考 虑预留。粗轧机组由4架Φ610/520mm和2架 Φ480/420mm轧机组成;中轧机组由4架 Φ480/420mm和2架Φ380/320mm轧机组成;预精轧 机组前4架由Φ380/320mm轧机组成。以上轧机均为 短应力线轧机,平立交替布置。
高速无扭精轧
高速无扭精轧工艺是现代线材生产的核心 技术之一,它是针对以往各种线材轧机存 在诸多问题,综合解决产品多品种规格、 高断面尺寸精度、大盘卷和高生产率的有 效手段。唯精轧高速度才能有高生产率。 才能解决大盘重线材轧制过程的温降问题。 精轧的高速度要求轧制过程中轧件无扭转, 否则事故频发,轧制根本无法进行。因此, 高速无扭精轧是高速线材轧机的一个基本 特点。
棒材主要设备及工艺特点
全轧线共有18架轧机,分为粗轧、中轧、精轧机组。
轧机平-立交替布置的轧机组成,其中:1-10架为闭口轧机, 11-18架为短应力线轧机,第14、16、18架为平/立可转换轧 机,各架轧机均由直流电机单独传动,在中轧机组及精轧机 组前各设一台启停式飞剪对轧件进行切头、切尾及事故碎断。 整个轧线采用全连续、全无扭轧制,粗、中轧机组采用微张 力轧制,精轧机组之间和精轧机组各架轧机之间均设置立活 套,实行无张力控制轧制。根据产品规格的不同,粗轧机组 轧出的Ф72mm圆轧件在中轧和精轧机组轧制6~12道次, Ф12~40mm带肋钢筋(其中:Ф12~22mm带肋钢筋用切分 法生产) 、Ф18-22树脂锚杆用热轧钢筋。成品最大轧制速 度为18m/s。
《材料成型技术》课件

锻造
通过对金属进行加热和冷却,使其在压力下改变形 状,常用于制造零件和工具。
挤压
将材料穿过模具的缝隙,使其变形成所需形状,常 用于制造管道、线材等。
铸造
将液态材料注入模具中,待冷却后得到所需形状, 广泛应用于汽车、航空等行业。
成型
通过热塑性材料的加热和压力,将其形成所需形状, 常见于塑料制品生产。
常见的材料成型技术
局限性
• 材料限制 • 工艺复杂性 • 有限的成型尺寸
材料成型技术的发展趋势
1
智能化制造
通过引入自动化和智能化技术,提高生产效率和质量。
2
新材料应用
开发和使用新型材料,提高产品性能和使用寿命。
3
环保节能
减少能源消耗和废弃物产生,实现可持续发展。
总结和展望
材料成型技术在各个领域都扮演着重要角色,随着科学技术的进步,我们可以期待在未来看到更多创新和突破。
《材料成型技术》PPT课 件
材料成型技术是一门研究材料加工和加工工艺的学科,涵盖了大量不同类型 的材料和方法,对各个领域的工业和科研都具有重要的意义。
什么是材料成型技术
材料成型技术是通过加热、压力、变形等方式将原材料转变为所需形状和尺寸的工艺。它包括了常见的加工方法, 如锻造、铸造、挤压等。
不同类型的材料成型技术
航空航天领域对高强度和轻质的材料需求较高, 成型技术为其提供了多种解决方案。
3 电子产品
4 建筑领域
成型技术在电子产品制造中的应用包括电路板、 塑料外壳等部件的生产。
通过材料成型技术可以生产建筑中常见的构件, 如钢结构、玻璃幕墙等。
材料成型技术的优势与局限性
优势
• 高效生产 • 多样化的产品形状 • 成本效益
挤出工艺简介ppt课件
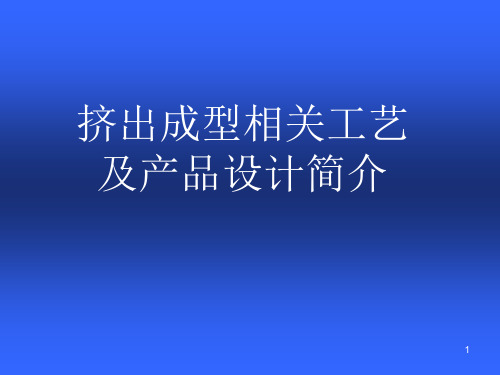
1
挤出成型简介
挤出成型一般用于热塑性塑料的管材、棒材、 板材、薄膜、线材等连续型材的生产,所得到的 塑件均具有稳定的截面形状。
粉状和粒状
预热和干燥
挤出机加热
开动螺杆
加料 调整
牵引
冷却
定型
卷取(切割)
后处理
挤出成型工艺流程图
挤出成型
成品
2
挤出工艺示意图
3
挤出成型原理和特点
• 挤出挤出过程中的温差和温度波动,都会影 响塑件的质量,使塑件产生残余应力,各点强 度不均匀,表面灰暗无光。
10
2.压力
• 在挤出过程中,由于塑料流动的阻力、螺 杆槽深度的变化、过滤板、过滤网和口模产生 阻碍等原因,在塑料内部形成一定的压力,而 这种压力是塑料经历物理状态变化而达到均匀 密实的重要条件。
6
2.挤出成型阶段
• 均匀塑化的塑料熔体随螺杆的旋转向 料筒前端移动,在螺杆的旋转挤压作用 下,通过一定形状的口模而获得与口模 形状一致的型材。
7
3.定型冷却阶段
• 塑件离开机头口模后,首先通过定型 装置和冷却装置,使其冷却变硬而定型。 在大多数情况下,定型和冷却是同时进 行的,只有在挤出各种管材和棒材时, 才有一个独立的定型过程。
12
4.牵引速度
• 从机头和口模中挤出的成型塑件,在 牵引力作用下将会发生拉伸取向,拉伸 取向程度越高,塑件沿取向方位上的拉 伸强度也越大,但冷却后长度收缩也大。 通常,牵引速度可与挤出速度相当,两 者的比值称为牵引比,一般应略大于1。
13
挤出成型产品设计要点
请做过挤出成型产品的同仁现身说法。传 授宝贵经验。
14
Hale Waihona Puke • 压力随时间的变化也会产生周期性波动,对 塑件质量有不利的影响,如局部疏松、表面不 平、弯曲等。为了减小压力波动,应合理控制 螺杆转速,保证加热和冷却装置的温控精度。