国内电弧增材制造技术的研究现状与展望
基于电弧的金属增材制造技术研究现状
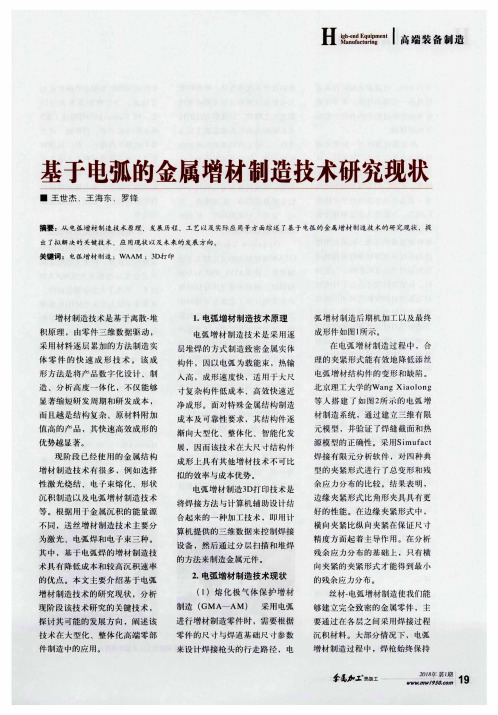
增 材 制 造 技 术是 基 于 离 散 一堆 积 原 理 , 由零 件 三 维 数 据 驱 动 , 采用材料逐层 累加的方法制造实 体零 件的 快 速 成 形技 术 。 该成 形方法是将产品数字化设计 、制 造 、分 析 高 度 一 体 化 ,不 仅 能 够 显 著缩 短研 发 周 期 和 研 发 成 本 , 而且越 是结 构复杂、原材料附加 值 高的产品 ,其快速 高效成形的 优 势 越 显 著 。
1.电弧增材制造 技术原理
电弧 增 材 制造 技 术 是 采 用逐 层堆焊 的方式 制造致密 金属实体 构 件 , 因 以 电弧 为载 能 束 ,热 输 入 高 ,成 形 速 度快 ,适 用 于 大 尺 寸 复杂 构件 低 成本 、高 效 快 速 近 净成形 。面对特殊金属结构制造 成 本 及 可靠 性 要 求 ,其 结 构 件 逐 渐 向大 型化 、整体化 、智能化发 展 , 因而 该 技 术 在 大 尺 寸 结 构 件 成 形 上 具 有 其 他 增 材 技 术 不 可 比 拟 的效 率 与 成 本优 势 。
H iMgh -e nnd E qu ipment l高端装备制造
基于电弧的金属增材制造技术研究现状
● 王 世杰 .王海 东 .罗锋
摘要 :从 电弧 增 材制 造技 术 原理 、 发展 历程 、 工 艺以 及实 际应 用等方 面综 述 了基 于 电弧的 金属增 材 制造技 术的研 究现 状 ,提 出 了拟 解 决的 关键技 术、应 用现 状 以 及未 来的 发展 方 向。 关键 词 : 电弧增 材制 造 ;wAAM ;3D打 印
现 阶 段 已 经 使 用 的 金 属结 构 增材制造技 术有很多 ,例如选择 性 激 光 烧 结 、 电 子 束熔 化 、 形状 沉 积 制 造 以 及 电弧 增 材 制 造 技 术 等 。根 据 用 于 金属 沉 积 的 能 量 源 不同 ,送丝增材制造技术主要分 为 激 光 、 电弧 焊 和 电子 束 三 种 。 其 中 ,基 于 电弧 焊 的 增 材 制 造 技 术 具 有 降 低 成 本 和 较 高 沉 积 速 率 的 优 点 。本 文 主 要 介 绍 基 于 电弧 增 材 制 造 技 术 的 研 究 现 状 ,分 析 现 阶 段 该 技 术 研 究 的 关 键 技 术 , 探 讨 其 可 能 的 发 展 方 向 ,阐 述 该 技 术 在 大 型化 、 整体 化 高 端 零 部 件制 造 中 的应 用 。
电弧熔丝增材制造综述物理过程 研究现状 应用情况及发展趋势

基本内容
2、新材料探索:探索新型高性能金属材料和非金属材料的熔丝堆积工艺,以 满足更为严苛的应用环境和高性能要求。
基本内容
3、复合制造:结合其他增材制造技术,如激光熔化、电子束熔化等,实现多 种工艺的复合制造,进一步提高制造效率和灵活性。
基本内容
4、智能化控制:加强数值模拟和人工智能技术在电弧熔丝增材制造中的应用, 实现工艺过程和产品质量的智能化控制。
二、电弧熔丝
二、电弧熔丝
电弧熔丝是一种利用电阻热效应进行加热的熔融金属制作方法。该技术具有 制作速度快、节约材料等优点,在航空航天领域具有广阔的应用前景。
1、电弧熔丝制作原理及种类
1、电弧熔丝制作原理及种类
电弧熔丝制作的基本原理是利用电极与金属丝之间的电阻热效应进行加热。 加热后,金属丝在电弧作用下熔化并滴落到制作件上,从而逐渐形成制作件。根 据加热方式的不同,电弧熔丝可分为脉冲电弧熔丝和直流电弧熔丝两种。
电弧熔丝增材制造铝合金:研究进展与未来展望
电弧熔丝增材制造技术是一种基于熔丝沉积的金属3D打印技术。通过电弧熔 化铝合金丝材,逐层堆积实现零部件的近净成形。这一技术具有降低成本、提高 材料利用率、优化产品设计等优点,为铝合金制造开辟了新的途径。
电弧熔丝增材制造铝合金:研究进展与未来展望
目前,电弧熔丝增材制造铝合金的研究主要集中在工艺优化、性能提升和新 产品开发等方面。在工艺优化方面,研究重点集中在探索工艺参数对成型质量的 影响,如电流、电压、送丝速度等。此外,铝合金材料的开发与选用也是关键。 高性能铝合金的引入,如铝锂合金、高强铝合金,可有效提高制件的综合性能。
基本内容
引言:电弧熔丝增材制造是一种先进的制造技术,通过熔化金属丝材并精确 控制其沉积形态,实现复杂三维结构的快速制造。由于其独特的优势,电弧熔丝 增材制造在航空、航天、汽车、电子等领域得到了广泛的应用。本次演示将重点 综述电弧熔丝增材制造的物理过程、研究现状、应用情况及发展趋势,以期为相 关领域的研究和应用提供有益的参考。
金属材料电弧增材制造技术研究现状

金属材料电弧增材制造技术研究现状摘要:金属材料电弧增材制造技术是一种先进的制造方法,通过在金属表面产生电弧并加热金属粉末以逐层堆叠形成三维构件。
本文对该技术的研究现状进行了综述。
主要内容包括该技术的原理、优点和应用领域。
同时,还对该技术存在的问题提出了解决方案,并展望了未来的发展趋势。
通过深入研究和实践,金属材料电弧增材制造技术有望在制造业中发挥更重要的作用。
关键词:金属材料;电弧增材制造技术;解决方案引言金属材料电弧增材制造技术是一种先进的制造方法,通过利用电弧和金属粉末的相互作用,逐层堆叠形成三维构件。
该技术具有高效、灵活和可定制性强等优点,在制造业中逐渐得到广泛应用。
本文旨在综述金属材料电弧增材制造技术的研究现状,包括其原理、应用领域以及存在的问题与解决方案。
同时,通过对未来发展趋势的展望,希望为该技术的进一步推广与应用提供参考和启示。
1.金属材料电弧增材制造技术概述金属材料电弧增材制造技术是一种先进的制造方法,其基本原理是通过在金属表面产生电弧并将金属粉末加热,使其逐层堆积形成所需的三维构件。
该技术相比传统的制造方法具有许多优点,包括高效、灵活性强和可定制性高等。
它能够实现快速原型制作、零件修复和复杂结构的打印,广泛应用于航空航天、汽车、医疗器械等领域。
电弧增材制造技术不仅可使用多种金属材料,还能够利用多种工艺参数进行控制,以获得理想的制造效果。
然而,该技术仍存在着一些挑战,例如成本、工艺控制和材料质量等方面的问题。
因此,进一步研究和改进该技术的关键参数和工艺流程是非常必要的。
2.金属材料电弧增材制造技术的研究现状金属材料电弧增材制造技术目前已经在全球范围内得到广泛的研究和应用。
在国内外相关研究中,学者们致力于推动这一技术的进一步发展和优化。
研究方向包括材料选择与开发、工艺参数优化、设备改进等。
通过实验和数值模拟方法的结合,研究人员不断探索电弧增材制造技术的优化途径,提高打印效率和制造质量。
基于多丝电弧增材制造研究现状

基于多丝电弧增材制造研究现状目录一、内容描述 (2)1.1 研究背景 (2)1.2 研究意义 (3)1.3 国内外研究现状概述 (4)二、多丝电弧增材制造技术原理及设备 (6)2.1 多丝电弧增材制造技术原理 (7)2.2 多丝电弧增材制造设备构成 (8)2.3 设备主要参数及其对加工影响分析 (9)三、多丝电弧增材制造材料研究 (11)3.1 增材制造材料的选择原则 (12)3.2 常见金属材料多丝电弧增材制造性能分析 (13)3.3 材料研发趋势与创新 (14)四、多丝电弧增材制造工艺优化 (15)4.1 工艺参数优化 (16)4.2 焊接参数优化 (17)4.3 操作技巧与注意事项 (18)4.4 工艺稳定性及其提升策略 (19)五、多丝电弧增材制造工程应用研究 (20)5.1 在航空航天领域的应用 (22)5.2 在汽车制造领域的应用 (23)5.3 在生物医疗等领域的应用案例分析 (25)六、存在问题与挑战 (25)6.1 技术难题及原因分析 (27)6.2 面临的技术瓶颈及突破方向 (28)6.3 对未来技术发展的展望 (29)七、结论与展望 (30)7.1 研究成果总结 (31)7.2 存在的问题及解决方案 (32)7.3 对后续研究的建议与展望 (33)一、内容描述随着科技的不断发展,多丝电弧增材制造技术在材料科学、制造工程和航空航天等领域的应用越来越广泛。
本文档将对基于多丝电弧增材制造的研究现状进行全面梳理和分析,以期为相关领域的研究者提供一个全面了解该技术的参考。
我们将介绍多丝电弧增材制造技术的起源和发展历程,包括其在传统电弧增材制造技术基础上的创新和突破。
我们将重点关注多丝电弧增材制造技术在不同材料、结构和性能方面的应用研究,以及在航空发动机、船舶制造、汽车零部件等领域的实际应用案例。
我们还将对多丝电弧增材制造技术的关键技术和发展趋势进行深入剖析,包括电极设计、电流控制、熔池管理、表面质量控制等方面的关键技术研究。
丝材电弧增材制造技术研究现状及展望
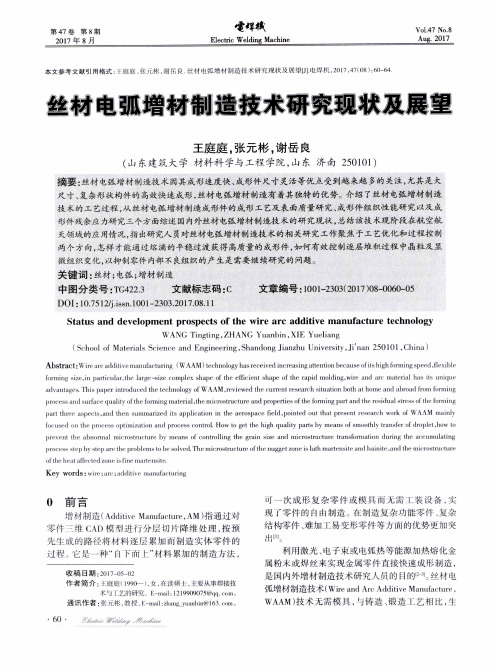
DOI : 1 0 . 7 5 1 2 / j . i s s n . 1 0 0 1 - 2 3 0 3 . 2 0 1 7 . 0 8 . 1 l
St a t us a nd de v e l op me nt pr o s p e c t s o f t he wi r e ar c a dd i t i v e ma nu f a c t ur e t e c h no l o g y
“l 1 . 1 ni ng s i z e , i n p at l i l ‘ I la f t , t he l a l i z P c o mpl e x s h a pe o f t he e l f i ( ’ I P I 1 t s h ap e o t t h e r a pi d m( ) hl i ng , wi l e H l l d l l U _ l t t 1 M h Hs i t s t mi l t m
H d v an t a g e s . Thi s p a pe r i t o dl i ( ! e d t he t e e hn o l o g ) o t W AAM . I - e v i l we d t h e e U l T e l l t r e s  ̄ r h s i l ua t i on b o t h a t ] l O l l l e ̄ l l l d| l I l r I ) l i d f r , , m ’ n in f g I ) 1 I l ( ’ t H i l l l S [ 1 l f ' t l ( ‘ q ua l i t y( J f t l 1 t { ) I - l 1 i r n g l l l t t t e l ‘ i a 1 . t i l e I I I i C I O S t l 3 . 1 ( ‘ t u t ’ P a nd p r o t ) e  ̄ l i e s o fl } l e f ) r n / i n g p a l _ t a l 1 ( { l l l p r t s i ( 1 u ll s l r l s t ) f 1 l I 1 t } t } l ’ mi n g p a r t t i m t as | l P ( ‘ l s . a l l ( 1 I J l e l l S 1 . 1 l nma r i z e d i l s a ppl i c a t i m1 i n t i l e a el ‘ os p a e e t i e ht . p o i n t e d( ) t i t t h a i p r e s t l I 1 r e s e d l ’ t ・ h WO I k o t AA M mai n l y
铝合金电弧增材制造技术研究现状及进展

铝合金电弧增材制造技术研究现状及进展作者:张江帅来源:《中国化工贸易·中旬刊》2018年第03期摘要:铝合金作为工业生产中广泛应用的一种合金,具有塑性好、强度较高、抗腐蚀性好等优点,是我国未来重点发展的高性能轻型合金材料,在汽车制造、航空领域应用广泛。
传统的制造铝合金构件的方法如铸、锻等不能够实现复杂形状的制造,由于电弧增材制造技术(WAAM)成本低、沉积效率高、成型件冶金性能好等优点,目前,许多学者在铝合金电弧增材制造方面开展了一系列研究。
关键词:特点及优势;增材制造;总结及展望1 电弧增材制造技术特点及优势增材制造技术,是中国制造2025的重点发展技术。
与传统的减法制造(如数控加工)相比,增材制造具有自由度高、成型复杂度高、自动化程度高等优点,特别是能够生产传统方法无法生产的钛和镍合金,在制造业中越来越受到重视。
电弧增材制造(WAAM)是以电弧为载能束的增材制造技术,利用气体金属电弧焊(GMAW)、钨极气体保护焊(GTAW)或等离子弧焊(PAW)等作为热源,逐层堆叠熔化的丝材从而形成金属零件的方法。
相比于激光或者电子束作为热源的增材制造方法,电弧增材制造具有沉积效率高、成型尺寸大、成本低廉等优势,能够低成本高效生产复杂金属构件。
2 铝合金电弧增材制造2.1 TIG电弧增材制造TIG电弧增材制造是以非熔化极气体保护电弧焊作为热源的增材制造方法,采用氩气作为保护气,通过不断熔化丝材堆叠成构件。
具有气孔少、熔池可见、熔渣少、堆焊层致密等优点,同时也存在残余应力、变形较大等缺点。
哈尔滨工业大学的王计辉利用TIG(非熔化极气体保护电弧焊)堆焊成型2219铝合金并对其成型工艺、试样组织特征和力学性能进行了研究。
北京航空航天大学的孙红叶等人对AL-6.3Cu进行了TIG堆焊成型,研究了焊接参数对成形尺寸的影响,并且对比分析了变极性钨极氩弧焊和复合超高频脉冲方法变极性钨极氩弧焊对成型件的影响。
结果发现复合超高频脉冲方法变极性钨极氩弧焊更有利于提高成型件的力学性能。
多丝电弧增材制造研究现状
图3 双丝MIG焊增材制造系统平台[17]
图4 双丝MIG焊增材试样 [17]
为了解决电弧增材时熔敷效率和热输入之间的 矛盾关系,哈尔滨工业大学的耿正等[18] 提出了一种 高熔敷率、低热输入的Tri-Arc双丝电弧系统。TriArc是一种采用三台焊接电源、两根焊丝产生三电弧 的焊接方法。如图5所示,VPPS、PPS1、 PPS2分别 是一可变极性电源和两个直流脉冲电源,通过三台 电源之间进行相互协调,控制电源的极性和脉冲关 系,可以建立三条电弧。三条电弧分别是焊丝E1与 工件所产生的电弧A1、焊丝E2与工件所产生的电弧 A2,以及焊丝E1和焊丝E2产生的电弧M。部分电流 会从两根焊丝之间流过,降低了热输入,M弧的存 在也保证了熔敷率。
10 2021年 第7期
热加工
图5 Tri-Arc增材系统示意[18]
电弧增材制造专题
Arc Additive Manufacturing Topic
图6 高速摄像拍摄的M弧形态 [19]
焊丝之间流过的一种焊接方法。通过调节工件与双 焊丝之间的距离来调节间接电弧的热输入,图7为传 统电弧焊和双丝间接电弧焊的对比。
本文综述了国内外学者为兼顾多丝电弧增材制 造技术的高熔敷效率与低热输入和控制熔滴平稳过 渡而做出的改进与发展,列举了异质多丝合金化研 究现状,分析了其优缺点和存在的主要问题,并展 望了未来多丝增材制造的发展趋势。
2 多丝电弧增材制造技术的发展与改进
2.1 高熔敷率和低热输入的兼顾 为了寻求更高的熔敷效率,1955年美国Union
在全球工业4.0的背景下,越来越多的学者通过 改进设备、新技术研发等手段改进或提高焊丝的熔 敷效率提高产品制造效率[11]。一般来说,影响电弧 增材制造成形效率的因素包括送丝量、送丝速度、 熔敷速度、熔敷功率、路径规划、工装设计等,使 用多丝电弧增材技术便是提高效率的一种选择。相 比于单丝电弧增材系统(如TIG焊、MIG焊)使用 单一焊丝增材,多丝电弧增材技术使用两根及以上 的焊丝并在必要时配以多个电源进行增材。由于多 丝电弧增材技术可以采用异质焊丝的特点,这就为 增材成分调控提供了基础。
铝合金电弧增材制造技术研究发展现状
英国学者在焊接工程研究中心做了大量研究,
利用堆焊技术将金属形状沉积技术应用于飞机机身 快速制造上,这使得许多航天企业都使用WA A M技 术,并使直接成形大型结构件越来越方便,缩短了 大型结构件的研制周期[30]。
针对航空航天领域的铝合金轴承、机舱截面、 框架梁及格栅等典型结构零件,首都航天机械有限 公司、北京航兴机械制造有限公司、华中科技大学 等都进行了研究,并进行了应用试生产,如管道支 撑件(2219合金)、壳体模拟零件(4043合金)、 框架梁结构(5B06合金)及网格结构(4043合金) 等 。 [31-35]
图2 WAAM工作原理 2.3 电弧增材制造技术应用
电弧增材制造相对于其他制造技术来说,其特 点如下:制造周期短;自动化程度高;原材料利用 率高,对零件尺寸的限制少。
电弧增材技术虽没有普遍使用,但是在少量重 要领域,电弧增材技术应用确实很多,如:全焊缝 金属成分高,密度高,力学性能好,已用于生物医 学、航空航天等领域,并且有望在更多领域得到广 泛使用[25-29]。
究现状 基于GMAW增材制造研究的同时,国外许 多研究者也将研究方向转至基于G TAW的电弧增材 制造技术,因其热输入较G M AW小,成形精度会更 高。
美国Southern Methodist大学OUYANG等[44]采用 G TAW工艺堆焊5356铝合金构件进行研究,结果表 明,影响零件尺寸精度和表面质量的主要因素有电 弧长度、基板预热温度和层间温度,图4所示为快速 成形件。挪威科技大学相关研究人员利用电弧增材 制造技术制备5183铝合金薄壁结构,结果表明,成 形样件微观组织和力学性能良好,但是需要进一步 优化工艺参数,以减少气孔和热裂纹产生。
电弧增材制造技术研究发展现状
电弧增材制造技术研究发展现状胡韬郭纯何梓良魏宝丽陈丰(安徽科技学院机械工程学院,安徽滁州233100)摘要:简要阐述了电弧增材制造技术的发展历史,分析了国外电弧增材制造研究发展现状,对电弧增材制造技术的发展前景进行了展望。
关键词:电弧增材;CMT技术;激光视觉传感技术0引言电弧增材制造技术是一种建立在电焊技术基础上的智能化、数字化的连续堆焊技术,其原理是使用焊接工艺中普遍应用的气体保护焊技术,以高温电弧为热源,熔化作为原材料的丝材,再进行一层一层堆叠,最后形成所需的零件。
1电弧增材制造技术的发展历史增材制造技术根据所使用的热源不同,主要分为激光增材制造技术、电子束增材制造技术和电弧增材制造技术以及金属固相增材技术。
其中,电弧增材制造技术是由德国科学家率先提出的一项新技术,该技术以金属焊丝为原料,采取埋弧焊接的方式,按照预先设计好的路径将融化的材料层层堆积,最后凝固成型,形成大尺寸零件。
20世纪90年代,英国的Ribeiro等人对这项技术又进行了进一步发展,同时期的Spencer等人为了零件的快速制造也做了一些工艺上的研究,这些研究对后来的电弧增材制造技术造成了极大影响。
其后的发展过程中得益于20世纪90年代以来的数字化和信息化技术的高速发展,在近30年的发展过程中成形控制和性能控制这两大问题的解决也使得电弧增材制造技术愈发成熟。
电弧增材制造技术采用传统的熔化极气体保护焊方式,其特点是热输入量较高,成型过程中输出热源反复在刚刚产生和成型的部位上移动,使其热积累量变高,使得材料在堆叠过程中会产生飞溅、形成多个气孔等一系列问题。
1.1CMT(冷金属过渡)技术CMT(冷金属过渡)技术的提出和应用则在一定程度上解决了上述难题。
电弧增材的过程中由于丝材要熔化堆叠,在持续不断的堆叠中就难免会让熔池的热积累量越来越高,不断的热量输入所产生的热量积累可能会使熔池产生飞溅问题,为此CMT技术应运而生。
相对于传统的气体保护焊,CMT技术产生的电弧温度和熔化丝材产生的熔滴温度比较低,主要得益于冷热循环交替原理。
丝材电弧增材制造常用材料及其缺陷研究进展
丝材电弧增材制造常用材料及其缺陷研究进展随着近年来增材制造技术的不断发展和成熟,丝材电弧增材制造已成为一种重要的制造技术,广泛应用于航空、汽车、机床等领域。
本文将就丝材电弧增材制造的常用材料及其缺陷研究进展进行探讨。
一、丝材电弧增材制造常用材料1.钛及钛合金钛及钛合金具有质轻、高强度、良好的抗腐蚀性和热应力耐受性等优点,被广泛应用于航空和医疗等领域。
然而,其加工过程中易产生气孔、裂纹等缺陷,并且会出现氧化和氮化等问题,影响制造质量。
2.镍基合金镍基合金具有高温抗氧化、抗腐蚀性能良好等特性,广泛应用于航空和航天等领域。
但由于其硬度较高,加工难度较大,且易引起热裂纹和形变等问题。
3.不锈钢不锈钢具有耐磨、抗腐蚀等特性,被广泛应用于航空、医疗、船舶等领域。
然而,由于其成分复杂,易产生过热现象,导致缺陷的生成。
4.铝及铝合金铝及铝合金具有良好的导热性、导电性、低密度等特性,被广泛应用于汽车、飞机等领域。
但其熔点较低,制造过程中易形变、产生裂纹和缩孔等缺陷。
二、丝材电弧增材制造常见缺陷1.气孔气孔是增材制造过程中的常见缺陷,主要是由于气体在熔池中的溶解度降低,随着熔池凝固,气体从熔池中析出形成气孔。
钛及钛合金、镍基合金等材料由于易氧化、易氮化,使得制造过程中氧化和氮化产生的气体也会造成气孔的形成。
2.裂纹裂纹是增材制造过程中的重要缺陷,危害产品的力学性能,甚至会导致制品的破裂。
裂纹的产生原因主要是由于制造过程中温度梯度大,冷却速率快,造成局部过热和冷却应力无法释放,从而形成裂纹。
3.缩孔缩孔是增材制造过程中的另一种重要缺陷,主要是由于材料在熔池凝固时发生收缩,产生的拉伸应力无法得到释放而形成的。
缩孔会影响产品的力学性能和外观,严重者甚至会导致制品的破裂。
三、常用材料缺陷治理措施为了解决丝材电弧增材制造中常见的缺陷,提高制造质量和工艺效率,人们采取了许多有效的缺陷治理措施,如下所述:1.加强预处理通过提高预热温度、控制钛及钛合金中的氧、氮等元素含量、对不锈钢进行预脱气等预处理措施,可以有效减少气孔、裂纹等缺陷的产生,提高制造质量。
- 1、下载文档前请自行甄别文档内容的完整性,平台不提供额外的编辑、内容补充、找答案等附加服务。
- 2、"仅部分预览"的文档,不可在线预览部分如存在完整性等问题,可反馈申请退款(可完整预览的文档不适用该条件!)。
- 3、如文档侵犯您的权益,请联系客服反馈,我们会尽快为您处理(人工客服工作时间:9:00-18:30)。
国内电弧增材制造技术的研究现状与展望
摘要:本文简述了电弧(电熔)增材制造技术特点、优势和发展历史,详细分
析了国内在电弧增材制造工艺、质量控制、电弧增材制造材料性能三方面的研究
情况,并基于目前的研究现状,提出了电弧增材制造技术在制造工艺、质量控制
和材料性能三方面研究的建议。
关键词:电弧增材制造,研究现状,展望
1引言
增材制造,是一种新型的金属“降维”制造工艺,通过对三维数字模型进行分
层切片处理,再按照预先规划好的路径将材料逐层累加的制造方式,是一种自下
而上,化零为整的制造方法,在复杂结构零部件制造方面有很大优势。
电弧增材
制造(Arc welding additive manufacturing,简称WAAM)技术,也称为电熔增材制造
技术(Electrical additive manufacturing,简称EAM )是采用电弧为热源的增材制
造技术,通过熔化金属丝材或粉末,逐层堆积出金属零部件的制造方法,具有丝
材利用率高、生产效率高,成本底,零件的尺寸不受成形缸或真空室的限制,易
于修复零件等优点。
和传统的铸造、锻造技术相比,制造过程无需模具,整体制
造流程短,制造周期短,柔性化程度高,易于实现数字化、智能化,对设计的响
应快,可实现零部件的拓扑优化设计,在小批量、复杂构件的个性化定制方面具
有很大技术和成本优势。
20世纪70年代,德国学者提出了电弧增材制造的概念,并采用该技术制造
了一金属容器。
20世纪80年代,美国使用等离子弧焊、熔化极气体保护焊技术
制造出了镍基合金金属构件,20世纪90年代,随着增材制造技术的发展,电弧
增材制造技术也得到了空前的发展,在装备、工艺及材料性能研究方面均取得了
很大突破。
2电弧增材制造技术研究现状
目前国内外用于WAAM制造的电弧种类主要为熔化极气体保护焊(GMAW),钨极惰性气体保护焊(GTAW)、等离子弧焊(PAW)等,尤其是配以冷金属过
度的熔化极气体保护焊,因其热输入小,电弧稳定性好等特点,得到了广泛发展
和应用。
今年来,国内各大高校针对电弧增材制造的研究也在不断深入,主要集
中在成形控制、过程监控和成形件性能研究等方面。
2.1工艺与成形研究
电弧增材制造在制造过程中液态熔池较大,电弧的可控性难,故成形控制是
电弧增材制造的发展的主要瓶颈之一。
电弧增材制造的在成形设备方面,主要有
两种方式,一种是焊接设备与多功能数控机床复合,另一种是焊接设备与多轴机
械手复合,实现柔性制造。
成形控制方面的研究主要集中在工艺优化、过程监控
以及实时反馈等方面,在工艺优化环节主要是通过实验,针对不同的增材方法,
研究合适的工艺参数,例如打印速度,丝径,送丝速度,电流,电压等。
沈泳华[[[]沈泳华.电弧增材制造成形系统设计和成形规律研究[D].南京:南京航空航天大学,2017]]研究了以KUKA焊接机器人和Fronius数字化焊机为主要设备的GMAW
冷金属过渡电弧增材制造系统和成形规律,采用“反切削法”实现了电弧增材制造
成形路径规划系统,并研究了不同工艺条件下的表面成形质量。
熊俊[[[] 熊俊.多
层单道GMA增材制造成形特性及熔敷尺寸控制[D].哈尔滨:哈尔滨工业大学,2014]]研究了单道熔化极气体保护增材制造的工艺特性和成形质量,表明熔敷电
流是决定成形形貌的决定因素,良好的成形电流区间为100~180A。
柳建等人[[[]
柳建,朱胜,殷凤良,等.工艺参数对堆焊熔敷成形极限倾角的影响规律[J].沈
阳工业大学学报,2012,34(5):515—5 19.]]采用逐层横向偏移焊枪的方式成形
倾斜面,揭示了工艺参数对堆焊成形极限倾斜角的影响规律,结果表明极限倾角
是由熔滴的表面张力、悬空部分自重力和电弧力平衡的结果。
电流大小决定表面
成形情况成形,极限倾角为450。
2.2质量检测方面的研究
建立可靠的内部缺陷无损检测方法是增材制造技术实现工程应用基础,鉴
于增材制造技术的特点,成形和成性在同一时空完成,且其内部质量们无法在后
续工序检测,只能通过破坏性检测或在使用过程中发现,故增材制造的过程监控
和过程质量检测尤为重要。
基于增材的技术特点,其内部缺陷应采取主动控制。
无损检测技术一般分为在线检测(过程中检测)和事后检测两种。
良好的在线检测
是实现内部缺陷的主动控制前提。
在线检测可以及时发现缺陷,采取及时的补救
措施,形成闭环控制。
与事后检测相比,可以降低补救难度,节省时间。
在线检
测目前有两种方法,其一是在线监测,通过监测制造过程特征参数来评价过程的
稳定性,进而间接判断增材制造件的内部质量,常见的方法有熔池尺寸监测、熔
池温度监控等,其二是在线无损监测,直接将无损监测技术如超声波技术、视觉
监测、温度场监测技术运用到在线过程,直接检测是否存在缺陷。
刘磊[[[] 刘磊.
电弧熔积增材过程中在线检测的研究与实现[D].武汉:华中科技大学,2016.]]以分散检测为出发点的永磁扰动检测方法,该方法可以成功检测出宽度0.3mm的开放性缺陷,直径0.8mm的内部气孔以及埋藏深度3mm,直径1mm的内部缺陷。
袁久鑫等人[[[] 袁久鑫,秦训鹏,张进鹏,等.基于激光超声的电弧增材制造内部缺
陷深度检测[J].中国机械工程,2020]]了通过仿真与实验的方法,研究了激光超声
的内部缺陷深度检测,研究表明该方法可以检测出最大深度10mm处1mm的圆
形缺陷,随着缺陷尺寸的减小,检测深度降低。
目前的电弧增材制造内部质量检
测主要集中在制造过程中的研究,以在线特征参数监测和在线无损检测为主,对
于缺陷容限、评价标准等方面的研究鲜有报道。
2.3材料性能方面的研究
增材制造是将传统制造方式的材料制备和部件制造工序结合在了增材一个
工序中,以小熔池,微冶金,快速凝固,实现材料制备和部件制造,过程中小熔
池的结晶冷却速度极快,其结晶条件和传统钢锭的结晶条件存在很大差异,且材
料经历了多次不平衡热循环,最终交货状态一般为消应力状态,故在性能方面和
传统的铸、锻也存在较大差异。
笔者研究了电熔增材制造EAM08CrMo的性能,
表明电弧增材制造EAM08CrMo具有良好的机械性能,尤其是冲击韧性,机械性
能在宏观上没有厚度效应和方向性[[[]严连菊. 电熔增材制造EAM08CrMo 钢性能研究[J].电焊机.2019,49(4):111-215]]。
张亚斌等研究了热处理参数对增材制造反应堆
压力容器用钢16MND5材料性能的研究,表明电熔增材制造过程中材料残余应力
对材料性能有较大影响,消应力处理可以较好的消除内部残余应力,改善材料性
能[[[] 张亚斌,严连菊,罗英,等.热处理参数对电熔增材材料EAM16MND5组织
和性能的研究[J].电焊机.2019,49(4):212-215]]。
王小彬等研究了EAM16MND5微观
组织和性能的,表明EAM16MND5满足核电规范RCC-M的标准要求,奥氏体晶粒度可达9.5级[[[]王小彬,张亚斌,谢常胜,等. 电熔增材制造反应堆压力容器用
16MND5 钢的组织与力学性能[J].金属热处理,2019,44(4):141-145]]。
周高
斌等研究了EAM16MND5的热老化性能,表明EAM16MND5经过450℃,3000H
时效处理后,组织稳定,强度略有提升,裂纹扩张能量降低[[[] 周高斌,谢常胜,
罗英,等.热老化对电熔增材制造材料EAM16MND5组织和力学性能的研究[J].电
焊机.2019,49(4):67-72
]]。
电弧(电熔)增材制造材料具有优异的性能,针对材料物理特性、疲劳、断
裂韧性等方面的研究尚无报道,研究尚未成体系。
3建议与展望
电弧增材制造技术的研究地,在过去几年取得了很大突破,2018年初,南
方增材制造的SAP制冷机端盖(图1)安装到了大亚湾核电站,实现了电熔增材
制造件的首次工程应用,该示范应用给电弧增材制造的发展也带来了更多希望。
为了电弧增材制造技术更好的为制造业赋能,取得更广泛的工程应用,提出如下
建议:
在成形及工艺研究方面,目前的研究主要集中在工艺参数对成形精度的研究方面,建议加强路径控制程序方面数字化、自动化研究,从部件整体出发规划路径,优化成形方式,提升制造精度。
在质量控制方面,其一建议建立电弧增材制造过程中工艺特征参数和内部质
量关系的数据库,提升过程监控的精准度。
其二建议从材料的应用情况入手,开
展电弧增材材料内部缺陷的演化行为,逆向研究电弧增材材料在各种应用环境下
的缺陷容限量,为制定电弧增材制造材料内部质量评价最好技术准备。
其三建议
进一步开展电弧增材制造内部缺陷的形成机理,为实现制造过程中内部缺陷的主
动控制,减少内部缺陷,改善内部质量提供依据。
在性能研究方面,建议加强电弧增材制造材料的基础研究,开展电弧增材制
造材料显微特征及其演化规律方面的研究,为进一步开展各项宏观性能的研究提
供科学依据,并为制定电弧增材材料评价体系打好技术基础。
工作简历:
主要从事焊接技术、电熔增材制造工艺、材料研发工作
参考文献。