煤气化工艺预案的选择
煤化工煤气化工艺方案

煤化工壳牌炉煤气化工艺方案一、工艺流程简述(-)气化装置本装置采用Shell干煤粉气化技术,以永城无烟粉煤为原料,生产以H2+C0为主要成分的粗合成气,经后工序变换、净化后作为合成甲醇的原料气。
1、磨煤及枯燥合格粒度的原料煤(包括湿渣和无烟煤)由原料贮运系统通过胶带输送机送入磨前碎煤仓。
碎煤仓中的无烟煤通过称重给煤机送到磨煤机中磨粉,同口寸根据无烟煤的流量,石灰石仓中的石灰石粉按一定比例配到磨煤机中混磨。
假设飞灰循环时,来自飞灰缓冲仓的飞灰也按比例参加磨中。
从热风炉(燃料为甲醇弛放气,开工时采用柴油)送来的热烟气送入煤磨中对煤粉枯燥,在磨粉的同时,经旋转别离器分选,将枯燥后合格的煤粉吹入煤粉袋式过滤器别离收集,经旋转给料器、螺旋输送机送入煤粉贮仓中贮存。
别离后的尾气经循环风机加压后大局部循环至热风炉循环使用,局部排入大气。
为控制系统惰性化,设置。
2、CO浓度在线分析,根据需要补充氮气。
2、煤粉加压及给料煤粉贮存在煤粉贮仓中,当煤粉锁斗处于常压状态时,关闭煤粉锁斗出口的下阀,翻开煤粉锁斗进口的上阀,使煤粉贮仓的煤粉自流进入煤粉锁斗,料满后关闭上阀,通入高压氮气加压后翻开下阀使煤粉自流进入煤粉给料仓中,卸完后关闭下阀,排出氮气降至常压,再循环上述过程O煤粉给料仓中的煤粉由管道通过高压C02送往气化炉喷嘴。
锁斗减压或气化炉喷嘴调试排气经煤粉仓装料袋滤器过滤,收集的煤粉进入煤粉贮仓,气体排入大气。
3、煤气化来自粉煤给料罐的粉煤,用高压二氧化碳送至煤气化烧嘴。
同时, 来自空分的加压氧气经预热后也进入气化烧嘴。
气化炉为立式压力容器,炉内为水冷壁组成的气化室,煤气化烧嘴位于气化室中下部,烧嘴二个一组对称布置。
由煤气化烧嘴喷入的煤粉、氧及蒸汽的混合物在1500°C高温下,瞬间完成煤的气化反响,生成(CO+田)含量很高且夹带飞灰的粗煤气,由下向上从气化炉顶排出。
为防止飞灰粘结在后续设备,在炉出口处喷入循环返回的低温煤气,将其急冷至900°C,使飞灰成为固态,再进入合成气冷却器回收热量,煤气温度降至350°C左右进入后序设备。
初探煤气化工艺方案的选择

初探煤气化工艺方案的选择随着能源需求的不断增加,煤作为一种丰富的化石燃料资源,越来越成为人们关注的焦点。
煤气化技术是将煤转化成可用于燃料、化学品和能源的气体产品,是煤能够得以广泛应用的关键技术。
在进行煤气化工艺方案的选择时,需要根据煤的性质、热力学参数和经济效益等多个方面进行综合考虑,下面就从这三个方面来初步探讨一下煤气化工艺方案的选择。
一、煤的性质煤的性质主要包括煤种、灰分、挥发分等指标。
在选择煤气化工艺方案时,需要根据煤的性质,确定合适的气化方式。
对于高挥发分的煤,常用的气化方式为流化床气化和喷锅气化,而对于低挥发分的煤,则更适合采用固定床气化等方式。
在确定煤种后,还需要进行煤的预处理,如煤的粉碎、干燥等,以达到更好的气化效果。
二、热力学参数热力学参数主要包括气化温度、气化压力、气化剂、气化反应等方面的指标。
在选择煤气化工艺方案时,需要根据热力学参数的调节,确定合适的气化反应条件。
在气化反应过程中,气化剂的选择很关键,常用的气化剂有氧气、水蒸气等,不同的气化剂会对气化产物有很大的影响。
同时,气化温度和气化压力也是决定气化效率和气化产物品质的重要因素。
因此,在选择煤气化工艺方案时,需要对煤的热力学参数进行分析和优化,以达到更高的气化效率和更好的产物品质。
三、经济效益在进行煤气化工艺方案的选择时,经济效益也是需要重视的方面。
煤气化工艺方案的选择,要从整个项目的角度出发,综合考虑技术的成熟度、建设投资、运营成本、产品市场和环保要求等多个方面,以实现最大经济效益和社会效益。
在现代化社会,环保要求越来越严格,因此,在选择煤气化工艺方案时,也需要优先考虑环保要求的满足程度。
总之,煤气化工艺方案的选择需要考虑到多个方面的因素,需要进行综合分析和协调,在选择方案时也要有整体观念,达到最佳综合效益。
作为一种关键的煤化工技术,煤气化工艺的发展将有助于推动煤的能源利用和清洁化,更好地满足人们的能源需求和环境保护要求。
煤气化工艺方案的选择
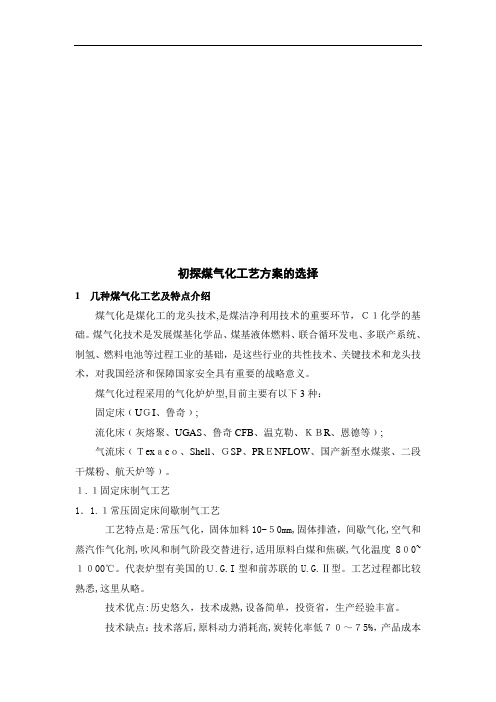
初探煤气化工艺方案的选择1几种煤气化工艺及特点介绍煤气化是煤化工的龙头技术,是煤洁净利用技术的重要环节,C1化学的基础。
煤气化技术是发展煤基化学品、煤基液体燃料、联合循环发电、多联产系统、制氢、燃料电池等过程工业的基础,是这些行业的共性技术、关键技术和龙头技术,对我国经济和保障国家安全具有重要的战略意义。
煤气化过程采用的气化炉炉型,目前主要有以下3种:固定床﹙UGI、鲁奇﹚;流化床﹙灰熔聚、UGAS、鲁奇CFB、温克勒、KBR、恩德等﹚;气流床﹙Texaco、Shell、GSP、PRENFLOW、国产新型水煤浆、二段干煤粉、航天炉等﹚。
1.1固定床制气工艺1.1.1常压固定床间歇制气工艺工艺特点是:常压气化,固体加料10-50mm,固体排渣,间歇气化,空气和蒸汽作气化剂,吹风和制气阶段交替进行,适用原料白煤和焦碳,气化温度800~1000℃。
代表炉型有美国的U.G.I型和前苏联的U.G.Ⅱ型。
工艺过程都比较熟悉,这里从略。
技术优点:历史悠久,技术成熟,设备简单,投资省,生产经验丰富。
技术缺点:技术落后,原料动力消耗高,炭转化率低70~75%,产品成本高,生产强度低,程控阀门多,维修工作量大,废气、废水排放多,污染严重,面临淘汰。
1.1.2常压固定床连续制气常压固定床连续制气工艺的技术特点:常压气化,固体加料,床体排渣,连续制气,富氧空气﹙氧占50%﹚或氧气加蒸汽做气化剂,无废气排放,适用煤种白煤和焦碳。
技术优点是:连续制气,炉床温度稳定,约为900~1150℃,操作简单,程控阀门少,维修费用低,生产强度大,碳转化率高,约80~84% 。
技术缺点:需要空分装置,投资比较大。
固定床连续制气工艺的技术突破在于以氧气或富氧空气加蒸汽做气化剂,由于气化剂中氧含量的增加,气化反应过程中,燃烧产生的热量与煤的气化和蒸汽分解所需要的热量能够实现平衡,可以得到稳定的反应温度和固定的反应床层,可以实现连续制气,不用专门吹风,无废气排放,生产强度和能源利用率都有了很大的提高。
煤炭气化燃烧技术使用计划方案

煤炭气化燃烧技术使用计划方案一、实施背景煤炭气化燃烧技术是一种能够将煤炭转化为合成气的技术,具有高效、清洁、便捷等优点。
随着全球环境问题的日益突出,煤炭气化燃烧技术得到了越来越广泛的应用和重视。
在我国,煤炭是主要的能源资源,但其燃烧会释放出大量的污染物,对环境造成严重的影响。
因此,推广煤炭气化燃烧技术,可以有效地减少煤炭燃烧所产生的污染物排放,提高能源的利用效率,符合国家节能减排的政策要求。
二、实施计划步骤(一)技术研究和开发通过对煤炭气化燃烧技术的深入研究和开发,探索出适合我国国情的煤炭气化燃烧技术,提高技术水平,降低成本,提高效率。
(二)试点示范在适当的地区进行试点示范,验证技术的可行性和经济性,为推广应用提供可靠的数据支持。
(三)推广应用将煤炭气化燃烧技术推广到更多的领域,包括工业生产、城市供暖、发电等领域,提高能源利用效率,减少污染物排放。
三、适用范围煤炭气化燃烧技术适用于煤炭资源丰富的地区,包括工业生产、城市供暖、发电等领域。
特别是在工业生产中,煤炭气化燃烧技术可以取代传统的燃煤锅炉,降低污染物排放,提高能源利用效率。
四、创新要点(一)技术创新通过技术创新,开发出适合我国国情的煤炭气化燃烧技术,提高技术水平,降低成本,提高效率。
(二)政策创新制定相关政策,鼓励企业推广应用煤炭气化燃烧技术,提高能源利用效率,减少污染物排放。
(三)市场创新通过市场创新,鼓励企业进行技术创新和产品创新,提高产品质量和竞争力,推动煤炭气化燃烧技术的发展。
五、预期效果(一)减少污染物排放煤炭气化燃烧技术可以将煤炭转化为合成气,减少煤炭燃烧所产生的污染物排放,对环境保护具有重要意义。
(二)提高能源利用效率煤炭气化燃烧技术可以提高能源利用效率,降低能源消耗成本,对于我国的能源安全具有重要意义。
(三)促进经济发展推广煤炭气化燃烧技术,可以促进工业生产和城市供暖的发展,提高经济效益和社会效益。
六、达到收益(一)环境保护通过减少污染物排放,保护环境,提高生态环境质量。
煤化工气化方式的选择.pdf
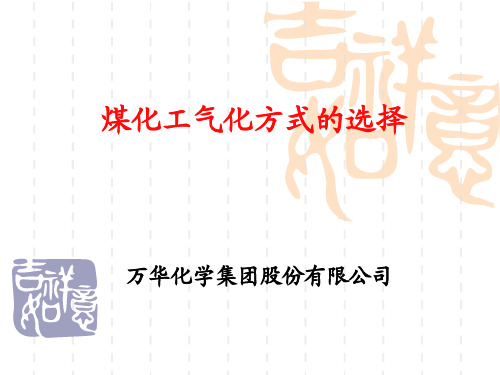
清华盈德丰喜水冷壁;(600吨/天耗煤)
一、煤化工常用的气化方式
气流床(粉煤、国内) 激冷流程 1、HT-L加压粉煤气化炉(1200吨/天,七台在线); 2、SE干煤粉气化炉; 2、两段式干煤粉气化炉; 3、多喷嘴干煤粉气化炉; 4、齐耀柳化炉(柳化鹿寨2000吨/天)
二、气化技术的选择
4、全流程作经济性分析 对前、后工序的投资和运营作经济分析 前工序:煤的输送、研磨、储存; 后工序:三废处理、CO变换、气体净化、
气体压缩; 装置的维护及更换。
二、气化技术的选择
5、全流程的能耗 煤的输送:制备1吨煤的水煤浆10 kWh,制
备1吨干煤粉30 kWh,输送1吨水煤浆约2 kWh,输送1吨干煤粉60 kWh;粉煤要干燥 到含水分3%; 气化压力:水煤浆气化尽量高压,6.5 MPa 甚至到8.7 MPa;粉煤气化最高只能到4.0 MPa; 净化采用低温甲醇洗在4.0 MPa下能耗很高。
二、气化技术的选择
6、气化装置的环保性能的分析 气化形成的废水数量、组分处理难易; 气化形成的废渣处理方式; 气化废气的处理问题。
三、气化炉的选择误区
1、热壁炉与冷壁炉的比较
冷壁炉能扩大煤种范围,消化高熔点、高灰分的煤,实现 原料煤本地化;解决耐火砖磨损需换砖,不能长周期运行 问题;
同样多的煤有效气体产生量少了1%-1.5%:水煤浆的水分 近40%,被加热到反应温度,同时把热量传到水冷壁副产 蒸汽,因而多消耗了煤和氧气,氧耗增加使CO2也增加了, 相当于用氧气生产了蒸汽;
1、成熟、可靠且先进的工程技术和工艺技 术。成熟可靠是指有在线的运行装置;技 术先进是指:(1)产品质量好;(2)单 位产品的原材、辅材、公用工程的消耗低; (3)环保性能好;(4)系统本质安全。
【技术】煤制天然气四种气化技术选型探讨

【技术】煤制天然气四种气化技术选型探讨以煤为原料生产化工产品的煤气化技术很多,按照气固相之间相接触的方式不同,可将煤气化工艺分为三类,分别有固定床气化、气流床气化和流化床气化工艺。
自20世纪50年代加压煤气化技术实现工业化以来,随着科技的发展,煤气化技术也日趋先进和成熟。
目前已成功开发了煤种适应性广、气化压力高、生产能力大、气化效率高、污染少的多种新一代煤气化工艺。
煤气化技术的选择,必须根据项目所在地的原料特性、技术风险、投资、能耗进行综合比较,通过企业自己的实力与产品定位,通盘考虑、审慎决策。
总之,没有最好的气化方案,只有最适合的气化方案。
选择成熟、合理的气化方案必将产生更大的经济、环保与节能减排效益。
本文选取具有代表性的、工艺成熟、应用广泛的气流床和固定床气化技术:Shell方案、提质+E-gas方案、碎煤加压气化方案以及碎煤熔渣加压气化(BGL)方案,重点从原料适应性、气化规模、技术可靠性、投资及能耗方面进行分析论证,选择合适的煤气化技术方案,以提高项目的技术可靠性、经济性,降低投资风险。
1原料煤适应性比较不同的煤气化工艺要求有不同煤种特性。
项目拟使用的煤种性质见下表。
不同煤种有不同的适应工艺。
从上表可以看出,原料煤全水和内水含量较高,煤种特性为灰分适中(空气干燥基灰含量为15.36%,质量分数)、灰熔点较低(流动温度1220℃)。
①Shell气化方案对煤质的适应性较广,本项目的灰含量为15.36%,对采用膜式水冷壁的气化炉来说较为有利。
②E-gas水煤浆气化要求原煤成浆性指标D≤10,根据煤炭成浆性计算得到其收到基原煤成浆性指标,属于较难成浆的煤种。
如采用水煤浆气化,可先对原料煤进行提质干燥,得到的半焦产品制得水煤浆的浓度为63%。
③碎煤加压气化供煤条件较苛刻,要求块煤以5~50mm的粒度进料,一般要求热稳定性≥70%,黏结指数≤4。
综上所述,从各气化工艺的要求的煤质来看,除了E-GAS水煤浆气化须采用褐煤提质满足成浆性要求,其他气化工艺均适应该煤种。
13种煤气化工艺的优缺点及比较解析
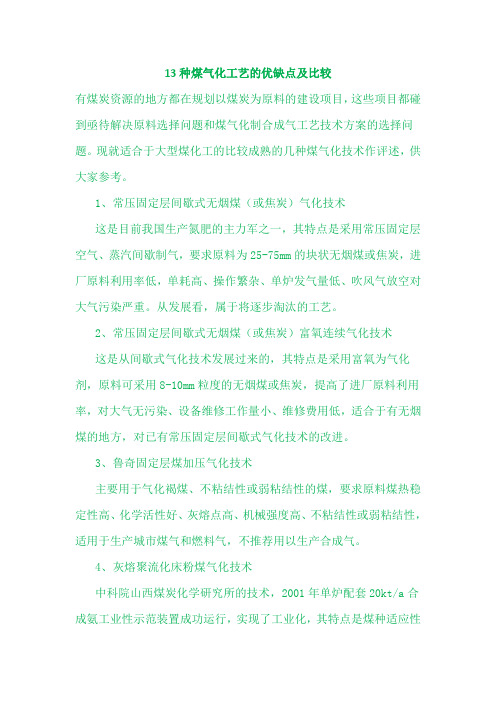
13种煤气化工艺的优缺点及比较有煤炭资源的地方都在规划以煤炭为原料的建设项目,这些项目都碰到亟待解决原料选择问题和煤气化制合成气工艺技术方案的选择问题。
现就适合于大型煤化工的比较成熟的几种煤气化技术作评述,供大家参考。
1、常压固定层间歇式无烟煤(或焦炭)气化技术这是目前我国生产氮肥的主力军之一,其特点是采用常压固定层空气、蒸汽间歇制气,要求原料为25-75mm的块状无烟煤或焦炭,进厂原料利用率低,单耗高、操作繁杂、单炉发气量低、吹风气放空对大气污染严重。
从发展看,属于将逐步淘汰的工艺。
2、常压固定层间歇式无烟煤(或焦炭)富氧连续气化技术这是从间歇式气化技术发展过来的,其特点是采用富氧为气化剂,原料可采用8-10mm粒度的无烟煤或焦炭,提高了进厂原料利用率,对大气无污染、设备维修工作量小、维修费用低,适合于有无烟煤的地方,对已有常压固定层间歇式气化技术的改进。
3、鲁奇固定层煤加压气化技术主要用于气化褐煤、不粘结性或弱粘结性的煤,要求原料煤热稳定性高、化学活性好、灰熔点高、机械强度高、不粘结性或弱粘结性,适用于生产城市煤气和燃料气,不推荐用以生产合成气。
4、灰熔聚流化床粉煤气化技术中科院山西煤炭化学研究所的技术,2001年单炉配套20kt/a合成氨工业性示范装置成功运行,实现了工业化,其特点是煤种适应性宽,可以用6-8mm以下的碎煤,属流化床气化炉,床层温度达1100℃左右,中心局部高温区达到1200-1300℃,煤灰不发生熔融,而只是使灰渣熔聚成球状或块状排出。
床层温度比恩德气化炉高100-200℃,所以可以气化褐煤、低化学活性的烟煤和无烟煤,以及石油焦,投资比较少,生产成本低。
缺点是气化压力为常压,单炉气化能力较低,产品中CH4含量较高(1%-2%),环境污染及飞灰综合利用问题有待进一步解决。
此技术适用于中小氮肥厂利用就地或就近的煤炭资源改变原料路线。
5、恩德粉煤气化技术恩德炉实际上属于改进后的温克勒沸腾层煤气化炉,适用于气化褐煤和长焰煤,要求原料为不粘结或弱粘结性、灰分小于25%-30%,灰熔点高(ST大于1250℃)、低温化学活性好的煤。
煤炭地下气化技术可行性与建议技术方案
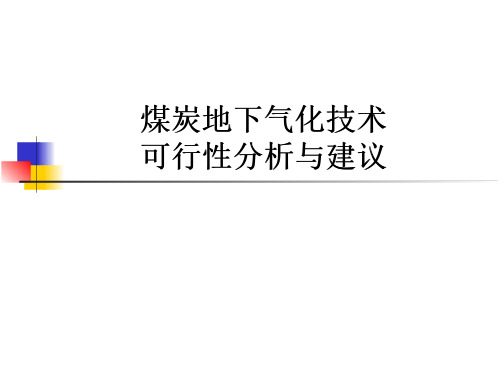
■ 煤炭地下气化的效益在很大程度上取决于地区地质构 造的研究程度。总的要求是要确切搞清地下气化地区 的地质构造、煤层的贮存状况、产状、厚度、煤质情 况以及水文地质情况,即矿床的勘探程度要达到建竖 井所需的详细勘探要求。
(一)煤炭地下气化原理
➢ 煤炭地下气化原理与一般的煤气化 原理相同,区别在于它的气化炉直 接设在地下煤层,将空气或氧气或 水蒸气鼓入地下煤层的反应区,生 成的煤气由钻孔排出,主要成分是 H2、CO、CO2、N2和少量的CH4、 H2S和O2,残存的灰渣留在原处。
➢ 从地面向煤层施工两个钻孔1、2, 通过火力、电力、水力或定向钻进 等方法将两孔贯通形成气化通道, 在连通的空腔内点燃煤层进行气化 反应。空气或水蒸汽从孔1压入, 产生的煤气从孔2排出,获得煤炭 资源有用组分。
① 有利于深部煤炭资源低成本回收;
② 可以采用较高的气化压力;
③ 操作灵活;
④稳定气化时间较长,有利于工艺控制。
四、辽河油田煤炭地下气化 需要解决的主要问题
1、辽河油田深部煤层地质勘探与精 细勘测问题
■ 与地面气化炉生产过程不同,煤炭地下气化用煤是地 下自然赋存条件下的煤层,气化的稳定与气化效率受 煤的渗透性、膨胀性、胶结性、热传导率和热扩散系 数的影响较大。
■ 1976年,比利时和原西德签署了深部煤层地下气化试 验协议,1979年在比利时成立了地下气化研究所,进 行UCG实验室研究和现场试验。
■ 1978~1987年,在比利时的图林(Thulin)采用高压 气化进行现场试验,试验生产的煤气用于发电。采用 小直径定向钻孔和CRIP工艺,试验基本成功。
- 1、下载文档前请自行甄别文档内容的完整性,平台不提供额外的编辑、内容补充、找答案等附加服务。
- 2、"仅部分预览"的文档,不可在线预览部分如存在完整性等问题,可反馈申请退款(可完整预览的文档不适用该条件!)。
- 3、如文档侵犯您的权益,请联系客服反馈,我们会尽快为您处理(人工客服工作时间:9:00-18:30)。
初探煤气化工艺方案的选择1 几种煤气化工艺及特点介绍煤气化是煤化工的龙头技术,是煤洁净利用技术的重要环节,C1化学的基础。
煤气化技术是进展煤基化学品、煤基液体燃料、联合循环发电、多联产系统、制氢、燃料电池等过程工业的基础,是这些行业的共性技术、关键技术和龙头技术,对我国经济和保障国家安全具有重要的战略意义。
煤气化过程采纳的气化炉炉型,目前要紧有以下3种:固定床﹙UGI、鲁奇﹚;流化床﹙灰熔聚、UGAS、鲁奇CFB、温克勒、KBR、恩德等﹚;气流床﹙Texaco、Shell、GSP、PRENFLOW、国产新型水煤浆、二段干煤粉、航天炉等﹚。
1.1固定床制气工艺1.1.1常压固定床间歇制气工艺工艺特点是:常压气化,固体加料10-50mm,固体排渣,间歇气化,空气和蒸汽作气化剂,吹风和制气时期交替进行,适用原料白煤和焦碳,气化温度800~1000℃。
代表炉型有美国的U.G.I型和前苏联的U.G.Ⅱ型。
工艺过程都比较熟悉,那个地点从略。
技术优点:历史悠久,技术成熟,设备简单,投资省,生产经验丰富。
技术缺点:技术落后,原料动力消耗高,炭转化率低70~75%,产品成本高,生产强度低,程控阀门多,维修工作量大,废气、废水排放多,污染严峻,面临淘汰。
1.1.2常压固定床连续制气常压固定床连续制气工艺的技术特点:常压气化,固体加料,床体排渣,连续制气,富氧空气﹙氧占50%﹚或氧气加蒸汽做气化剂,无废气排放,适用煤种白煤和焦碳。
技术优点是:连续制气,炉床温度稳定,约为900~1150℃,操作简单,程控阀门少,维修费用低,生产强度大,碳转化率高,约80~84% 。
技术缺点:需要空分装置,投资比较大。
固定床连续制气工艺的技术突破在于以氧气或富氧空气加蒸汽做气化剂,由于气化剂中氧含量的增加,气化反应过程中,燃烧产生的热量与煤的气化和蒸汽分解所需要的热量能够实现平衡,能够得到稳定的反应温度和固定的反应床层,能够实现连续制气,不用专门吹风,无废气排放,生产强度和能源利用率都有了专门大的提高。
1.1.3 固定床加压气化工艺:前西德鲁奇公司(Lurgi)开发。
工艺特点:加压气化,固体加料,固体排渣,连续气化,氧气和蒸汽作气化剂,设有加压的煤锁斗和灰储斗,适用煤种:褐煤、次烟煤、活性好的弱粘结煤。
技术优点:加压气化3.1 MPa,生产强度大,碳转化率高约90%。
技术缺点:反应温度略低700~1100 ℃,甲烷含量较高,煤气当中含有焦油和酚类物质,气体净化和废水处理复杂,流程较长,投资比较大。
1.2 流化床工化工艺流化床气化工艺的总体特点是:以粉煤或小颗粒的碎煤为原料气化,气化剂以一定的速度通过物料层,物料颗粒在气化剂的带动下悬浮起来,形成流化床,由于物料层处于流化状态,煤粉和气化剂之间混合更允分,接触面积更大,煤粉和气化剂迅速地进行气化反应,反应产生的煤气出气化炉后去废热回收和除尘洗涤系统,反应产生的灰渣由炉底排出。
气流床反应物料之间的传热和传质速率更快,过程更容易操纵,生产能力也有了较大的提高。
下面就流化床气化工艺进展过程中的几种工艺的技术特点分不作一下介绍。
1.2.1 温克勒﹙W inkier﹚常压流化床气化工艺:是前西德莱菌褐煤公司和伍德公司20世纪20年代开发的,是世界上最早的流化床气化工艺。
工艺特点:常压气化,粉煤进料粒度小于9.5mm,干法排渣 ,氧气或空气加蒸汽作气化剂,炉体上部有分离空间,使煤气当中夹带的半焦和灰颗粒分离,同时用一次空气加蒸汽进一步气化,气化温度815~1100℃,碳转化率70~73%,适用煤种:褐煤、次烟煤、弱粘结性煤。
要紧技术问题:炉底的炉箅经常出现局部高温,结渣,偏炉现象。
炉出口气体带出物较多,排灰的含碳量较高。
2.2.2恩德常压流化床气化工艺:是朝鲜恩德郡七.七化工厂20世纪60年代在常压温克勒气化工艺的基础上开发的。
工艺特点:常压气化,粉煤进料粒度小于10mm,干法渣,氧气或空气加蒸汽作气化剂,取消了炉箅,改造为布风喷嘴向炉内送气,解决了炉底结渣的问题,气化温度950~1050 ℃,在炉气出口增设了旋风分离气,返料从炉底入炉循环使用。
技术优点:煤种适从性宽,可气化褐煤、次烟煤、弱粘结性煤,返料循环使用,碳转化率可达76%,极少产生焦油。
技术缺点:气化压力低,难以实现大规模生产,排灰含碳量高。
1.2.3循环流化床粉煤气化工艺CFB:20世纪70年代鲁奇公司开发。
工艺特点:该技术的工艺过程和恩德粉煤气化工艺比常相似,所有不同的是CFB技术的旋风分离器分离的粉尘直接从气化炉上部进入气化炉炉膛,多重循环,使循环物料和新奇物料之比高达40倍以上,导致碳粒的反复气化,因而碳的转化率专门高,可达90%。
由于夹带固体物料的速度大大低于气流速度,气体和固体间的滑动速度较大,因而物料和气化剂间的混介更充分,接触时刻更长,气化效率较高。
能够用蒸气加空气、富氧空气、氧气作气化剂,但产气品质不一样。
技术优点:循环流化床气化,碳的转化率更高了,单炉生产能力大,煤种适应广。
技术缺点:排灰的含碳量仍然比较高。
1.2.4灰熔聚粉煤循环流化床汽化工艺:美国煤气研究所在美国能源部﹙DOE﹚的资助下于20世纪70年代开发。
该技术是在常压循环流化床气化工艺的基础上进展起来的,它的技术突破在于采纳了灰聚熔技术,所谓灰聚熔指的是:在炉底中心有一个氧气或空气入口,该处由于氧气或空气的进入,形成一个局部的高温区,在那个地点灰渣中未反应的碳进一步反应,煤灰则在高温下开始软化同时相互粘结在一起,当熔渣的密度和重量达到一定的程度时灰球就会克服气流的阻力落入炉底。
灰熔聚技术极大地降低了排灰的碳含量,大幅度提高了碳的转化率,是循环流化床气化技术进展史上的重要里程碑,灰熔聚技术使循环流化床气化炉的碳转化率提高到96-98%,气化温度954~1038℃。
技术特点:灰熔聚循环流化床气化工艺具有循环流化床工艺的一切优点,而且大大提高了碳的转化率,气化剂分两路进入,从炉底排灰管进入一路气化剂的氧含量较高,以实现灰熔聚,U-Gas炉操作压力为0.69~2.41 MPa,有带压的煤斗和灰斗,煤气中无焦油,无废气排放。
目前的问题是出口气带灰较多,不能长周期运行。
1.2.5高压灰熔聚粉煤循环流化床汽化工艺:美国煤气研究所IGT20世纪80年代开发。
该技术是在常压灰熔聚粉煤循环流化床气化工艺的基础上进展起来的,也有进料的煤斗和排灰的灰斗,所不同的是它的操作压力可达2.7~3.4MPa。
该技术对设备阀门的要求比较高,尚未广泛推广开来。
1.3 气流床气化工艺气流床气化工艺的共同特点是:煤进料的粒度比粉煤流化床气化的进料粒度更小,反应物料被气化剂夹带,以气流床的形式进行反应,因而反应进行得更快。
一般要求反应的温度和操作的压力都比较高。
1.3.1柯伯斯-托切可粉煤气流床气化工艺:前西德﹙Kopper-Tobek﹚公司20世纪40年代开发。
流程简述:粉碎研磨合格的煤粉用氮气输送到煤储斗当中,再由螺旋给料机送至混合器,在混合器当中,粉煤在氧气和蒸气的携带下经烧嘴进入气化炉,氧气,蒸气和粉煤一起并流进入气化炉,在气化炉内发生强烈的氧化反应,产生高达2000℃的高温,反应后产生的水煤气先进入废热锅炉回收热量,然后进入洗涤除尘系统。
反应产生的灰份被炉内的高温融化沿气化炉的炉壁流入激冷槽内,冷却固化后由捞渣机排出。
该工艺的要紧技术特点是:粉煤进料小于0.1mm,熔融排渣,常压气化,操作简单,产气当中无焦油和酚及烃类物资,甲烷含量低等特点。
要求煤的活性好,灰熔点适宜。
该技术的缺点是:氧耗高,对气化炉耐火砖的要求高,显热回收设备多,投资比较大。
1.3.2谢尔粉煤气流床气化工艺:谢尔﹙Shell﹚国际石油公司在柯伯斯-托切可粉煤气流床气化工艺的基础上开发的。
工艺过程:与柯伯斯-托切可粉煤气流床气化技术的工艺过程差不多相同,所不同的是该工艺的废热锅炉和气化炉不是联体的,而是分开的,而且高温煤气在进入废热锅炉前先和洗涤冷却后的冷煤气混合激冷到1000℃以下再进入废热锅炉,有效地防了熔融灰渣粘结到废热锅炉壁上。
技术特点:粉煤进料粒度90%通过170目筛网,气流床反应,加压气化3.0~4.OMPa,气化温度1340℃熔融排渣,夹套水冷,煤种适应宽,几乎能够气化所有煤种,气化效率高,一般98%以上,产品气当中有效气成分在90%以上,无焦油类物资,适应于制气和商业化联合发电装置IGCC。
技术缺点是:技术费用高、投资大,采纳的夹套水冷壁使用寿命只有25年,而且该技术难以实现国产化。
1.3.3德士古水煤浆加压气化工艺:美国德士古﹙T exaco﹚公司20世纪70年代开发。
工艺过程:磨制合格的水煤浆由泵加压后和氧气经特制的烧嘴喷入气化炉,水煤浆被高效雾化并蒸干水分后和氧发生复杂的氧化还原反应生成水煤气,生成的水煤气和熔渣一起进入气化炉下面的激冷室,熔渣被冷却固化后经锁灰斗收集排出,水煤气激冷后出气化炉激冷室去洗涤除尘系统。
技术特点:水煤浆进料,加压气化,纯氧作气化剂,熔融排渣, 原料适应范非比常广,碳转化率高94-98%,有效气成分高达84%,废物排放少,生产能力大,前景宽敞。
水煤浆浓度65%,粒度99%通过14目筛网。
技术缺点:氧耗比较高,投资大、技术费用高。
2 其它制气技术2.1“热-电-煤气”三联产煤制气技术“热-电-煤气”三联产煤制气技术是在热电联产的基础上以较少的投资获得高品质、低成本煤气的一种制气方法。
该技术利用热电厂循环流化床锅炉的循环热灰对煤(次烟煤、褐煤等)进行干馏产出煤气经净化后供给用户。
“热-电-煤气”三联产煤制气的实质是:原料煤在送入锅炉之前先将煤中的挥发分提出,产出煤气。
提出挥发分的煤变成半焦。
半焦作为要紧燃料直接送入锅炉炉膛燃烧。
锅炉产生蒸汽用于发电、供热,从而实现热、电、煤气三联产。
1-CFB锅炉燃烧室; 2-旋风分离器;3-热灰输送阀;4-热分解反应器;5-煤斗;6-气液分离器;7-半焦输送阀;8-罗茨鼓风机图1 热-电煤气三联产工艺流程示意图优点:⑴原料煤为劣质煤(褐煤、次烟煤等),煤种在我国分布广,价格低。
⑵工艺过程反应条件和气(常压、中温)。
⑶工艺过程无氧化反应,差不多上不增加CO2气体排放。
⑷节能效果显著,工艺部分与热电联产相结合,综合热效率可达90%。
局限:⑴制煤气工艺的实现必须依附于循环流化床锅炉的正常运行。
⑵对原料煤的煤种有一定的限制。
3 煤气化技术进展趋势世界现代煤炭气技术的特点及进展趋势是:⑴气化压力向高压进展气化压力由常压、低压﹙﹤1.0MPa﹚向高压﹙2.0~8.5MPa﹚气化进展,从而提高气化效率、碳转化率和气化炉能力,实现气化装置大型化和能量高效回收利用,降低合成气的压缩能耗或实现等压合成﹙如甲醇低压合成﹚,降低生产成本。