转炉高效冶炼不锈钢技术(DOC)
转炉炼钢用的工艺方案

转炉炼钢用的工艺方案一、炼钢的“火炉”——转炉说起炼钢,大家第一反应肯定是钢铁工厂里那熊熊燃烧的火焰吧。
没错,那就是我们所说的转炉!这家伙可不简单,不光能炼钢,而且炼出来的钢可是强度、硬度、韧性一个不拉的。
转炉炼钢的基本原理其实很简单。
钢铁从铁矿石中提炼出来,炼钢时就得把这些原料放进大大的炉子里。
然后,炉子就开始加热,让铁矿石里的杂质去掉,剩下的就是我们需要的钢铁啦。
我都能感受到那种高温和火花飞溅的场面,真的是一团火热的激情啊!这个转炉就像一台巨大的“翻锅”机器,炉内的金属液体不停翻滚,铁和废料的氧化反应使得不纯净的物质和钢铁分离。
锅里的金属液面也像个能“说话”的小孩子,随着温度的升高,“咚咚”的响声就像是敲响了钢铁之路的号角。
那时,原料在转炉里翻腾,好像是给它们洗个大澡,把那些脏东西洗得干干净净,剩下的钢才够强硬够耐用,才能在后面的各个环节中“大展身手”。
二、转炉炼钢的具体步骤咱们聊聊转炉炼钢的具体流程。
其实它的流程并不复杂,先把炉子加热到一千多度。
炉内有个叫“空气氧化”的过程,通过向炉子里吹入氧气,把金属液体里的杂质(比如硫、磷、碳啥的)氧化掉。
简直就是给它们“瘦身”,再把这些氧化物赶出去。
就像你去美容院做面部护理,精致的五官都需要多做几道工序,一点点剔除杂质。
整个过程相当于“减肥塑形”,把钢液处理得轻松优雅。
等到这些杂质被“清理”掉之后,炉子就得加入合金元素了。
不同的钢需要不同的合金配方,就像煮汤一样,你得根据不同的口味放进去适当的食材。
比如说,做不锈钢时,得加点铬,增强钢铁的抗腐蚀能力。
而如果是造汽车的钢,可能要加点锰,增强钢的强度。
一块块普通的钢铁,经过转炉这一“魔法”的洗礼后,成了“超级英雄”,强大到无敌!三、转炉炼钢的特点大家知道,转炉炼钢可不是一蹴而就的事情,它有几个显著的特点。
首先就是它的效率超高,特别适合大规模生产。
想想看,一台转炉在短短几个小时内就能处理几百吨的钢铁。
真的是“快准狠”,每一吨钢铁的生产都像是赛车比赛一样快速而精准。
转炉工艺技术

转炉工艺技术转炉工艺技术是一种炼钢方法,通过使用转炉来将生铁转化为钢材。
这种工艺技术具有高效、环保等优点,因此在现代炼钢领域得到广泛应用。
转炉工艺技术的基本原理是在转炉内加入生铁和废钢,然后通过高温熔炼的过程将其转化为合格的钢材。
转炉的炉体由耐火材料构成,能够承受高温和高压的作用。
在炉口处还设有喷口,用来喷入石灰、氧气等物质,调节反应条件。
转炉工艺技术主要有两个阶段:冶炼阶段和调温阶段。
在冶炼阶段,先将炉体加热至适宜的温度,然后加入废钢和生铁。
废钢中的杂质和含碳量会对炉内氧气的消耗产生影响,因此要根据废钢的质量和含碳量来调节氧气的喷入量。
通过废钢和生铁的熔炼,炉内的氧气会和碳发生反应,生成一定量的二氧化碳和一氧化碳,从而将炉内的过剩碳消耗掉,使得钢材的碳含量降低。
在冶炼阶段过后,需要进行调温阶段。
调温的目的是降低熔融钢液的温度,以便在下一步工艺中将其浇制成钢坯。
调温的方法主要有三种:一是通过喷吹冷风,即将冷风喷入转炉中,通过热交换来降低钢液的温度;二是通过喷吹水雾,即喷入水雾来降低炉内的温度;三是通过喷吹冷却物质,如纸浆或粉末来吸收炉内的热量。
这三种调温方法都能有效地降低钢液的温度,确保钢材的质量。
转炉工艺技术相对于其他炼钢方法有许多优点。
首先,转炉的生产效率高。
转炉冶炼的周期短,炉型大,能够一次性冶炼大量的原料,提高生产效率。
其次,转炉冶炼的过程对环境的影响小。
由于转炉工艺是在密闭的炉腔内进行,污染物的排放量较少,能够有效地防止废气和废水的污染。
此外,转炉冶炼能够利用废钢回收再利用,提高资源利用率,减少废物的产生。
总而言之,转炉工艺技术是一种高效、环保的炼钢方法。
通过合理地控制和调节冶炼条件,能够将生铁和废钢转化为合格的钢材,提高钢铁行业的生产效率和产品质量。
转炉工艺技术的广泛应用,推动了钢铁行业的发展,对于国民经济和社会发展起到了重要的促进作用。
转炉炼钢新技术 文档
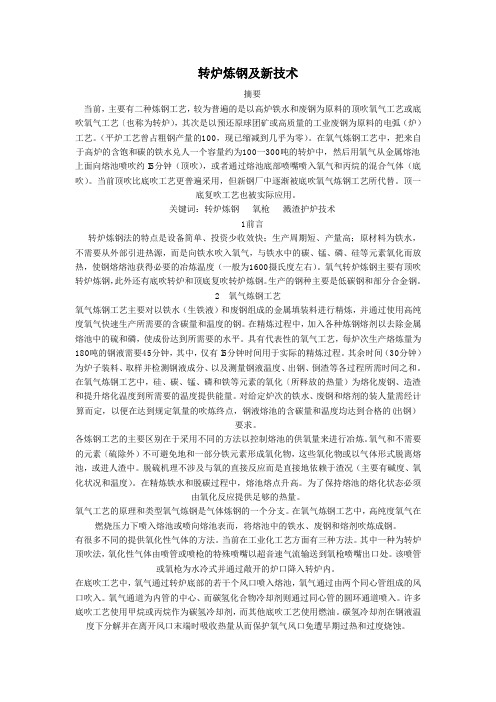
转炉炼钢及新技术摘要当前,主要有二种炼钢工艺,较为普遍的是以高炉铁水和废钢为原料的顶吹氧气工艺或底吹氧气工艺〔也称为转炉),其次是以预还原球团矿或高质量的工业废钢为原料的电弧(炉)工艺。
(平炉工艺曾占粗钢产量的100,现已缩减到几乎为零)。
在氧气炼钢工艺中,把来自于高炉的含饱和碳的铁水兑人一个容量约为100一300吨的转炉中,然后用氧气从金属熔池上面向熔池喷吹约I5分钟(顶吹),或者通过熔池底部喷嘴喷入氧气和丙烷的混合气体(底吹)。
当前顶吹比底吹工艺更普遍采用,但新钢厂中逐渐被底吹氧气炼钢工艺所代替。
顶一底复吹工艺也被实际应用。
关键词:转炉炼钢氧枪溅渣护炉技术1前言转炉炼钢法的特点是设备简单、投资少收效快;生产周期短、产量高;原材料为铁水,不需要从外部引进热源,而是向铁水吹入氧气,与铁水中的碳、锰、磷、硅等元素氧化而放热,使钢熔熔池获得必要的冶炼温度(一般为1600摄氏度左右)。
氧气转炉炼钢主要有顶吹转炉炼钢,此外还有底吹转炉和顶底复吹转炉炼钢。
生产的钢种主要是低碳钢和部分合金钢。
2 氧气炼钢工艺氧气炼钢工艺主要对以铁水(生铁液)和废钢组成的金属填装料进行精炼,并通过使用高纯度氧气快速生产所需要的含碳量和温度的钢。
在精炼过程中,加入各种炼钢熔剂以去除金属熔池中的硫和磷,使成份达到所需要的水平。
具有代表性的氧气工艺,每炉次生产熔炼量为180吨的钢液需要45分钟,其中,仅有l5分钟时间用于实际的精炼过程。
其余时间(30分钟)为炉子装料、取样并检测钢液成分、以及测量钢液温度、出钢、倒渣等各过程所需时间之和。
在氧气炼钢工艺中,硅、碳、锰、磷和铁等元素的氧化〔所释放的热量)为熔化废钢、造渣和提升熔化温度到所需要的温度提供能量。
对给定炉次的铁水、废钢和熔剂的装人量需经计算而定,以便在达到规定氧量的吹炼终点,钢液熔池的含碳量和温度均达到合格的(出钢)要求。
各炼钢工艺的主要区别在于采用不同的方法以控制熔池的供氧量来进行冶炼。
转炉高效炼钢技术创新
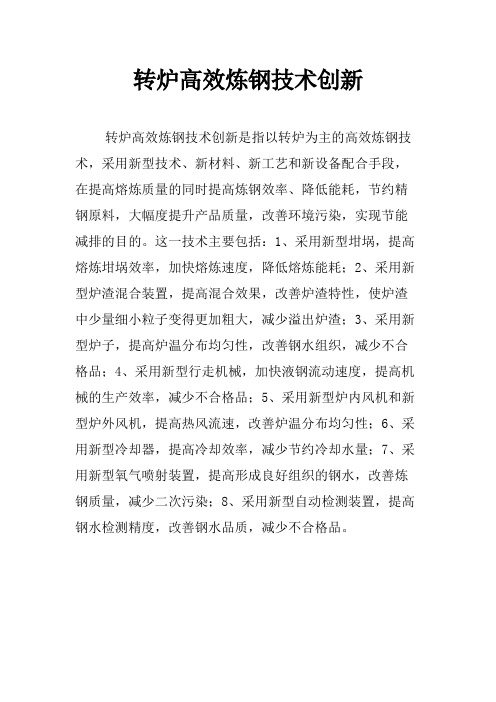
转炉高效炼钢技术创新
转炉高效炼钢技术创新是指以转炉为主的高效炼钢技术,采用新型技术、新材料、新工艺和新设备配合手段,在提高熔炼质量的同时提高炼钢效率、降低能耗,节约精钢原料,大幅度提升产品质量,改善环境污染,实现节能减排的目的。
这一技术主要包括:1、采用新型坩埚,提高熔炼坩埚效率,加快熔炼速度,降低熔炼能耗;2、采用新型炉渣混合装置,提高混合效果,改善炉渣特性,使炉渣中少量细小粒子变得更加粗大,减少溢出炉渣;3、采用新型炉子,提高炉温分布均匀性,改善钢水组织,减少不合格品;4、采用新型行走机械,加快液钢流动速度,提高机械的生产效率,减少不合格品;5、采用新型炉内风机和新型炉外风机,提高热风流速,改善炉温分布均匀性;6、采用新型冷却器,提高冷却效率,减少节约冷却水量;7、采用新型氧气喷射装置,提高形成良好组织的钢水,改善炼钢质量,减少二次污染;8、采用新型自动检测装置,提高钢水检测精度,改善钢水品质,减少不合格品。
不锈钢的三种冶炼工艺

不锈钢的三种冶炼工艺
嘿,朋友们,今天咱们来聊聊不锈钢,这玩意儿可真是无处不在,从厨房的
锅碗瓢盆到建筑的装饰,哪儿都能见到它的身影。
但你知道不锈钢是怎么炼成的吗?别急,我这就给你细细道来。
电弧炉冶炼
首先,咱们得从电弧炉冶炼说起。
这可是个技术活儿,得把废钢和铁矿石扔
进炉子里,然后通上电,让它们在高温下熔化。
这个过程就像是在大锅里煮东西,只不过这“锅”是金属做的,而且温度高得吓人。
电弧炉的好处是能回收利用废钢,既环保又经济。
但缺点嘛,就是冶炼过程中会产生大量的二氧化碳,对环境不太友好。
转炉冶炼
接下来是转炉冶炼,这玩意儿就像是个大转盘,把铁水倒进去,然后一边转
一边吹氧,让铁水里的杂质氧化掉。
这个过程就像是在做化学实验,得精确控制氧气的量,不然不锈钢的质量就受影响。
转炉冶炼的优点是速度快,效率高,但缺点是成本高,而且对原料的要求也比较高。
真空感应炉冶炼
最后,咱们得聊聊真空感应炉冶炼。
这可是个高科技的东西,得在真空环境
下进行。
把原料放进炉子里,然后通上电,让它们在真空中熔化。
这个过程就像是在做太空实验,得精确控制温度和时间,不然不锈钢的质量就受影响。
真空感应炉冶炼的优点是能生产出高质量的不锈钢,但缺点是成本高,而且设备复杂。
结语
好了,朋友们,这就是不锈钢的三种冶炼工艺。
每种工艺都有它的优点和缺点,就像是我们生活中的选择一样,没有完美的答案,只有最适合的选择。
下次当你看到不锈钢制品时,不妨想想它们是怎么炼成的,也许会让你对这些看似普通的金属有更深的认识。
咱们下次再聊,拜拜!。
转炉冶炼工艺技术

转炉冶炼工艺技术转炉冶炼是一种常见的冶炼工艺技术,主要应用于钢铁冶炼中。
转炉冶炼工艺技术在20世纪初开始发展,并逐渐成为钢铁工业的主要生产工艺之一。
本文将介绍转炉冶炼工艺技术的基本原理及其优点。
转炉冶炼工艺技术是利用转炉进行钢铁冶炼的一种方法。
转炉是一种采用喷吹技术加热和冶炼原料的设备。
转炉冶炼工艺技术主要包括以下几个步骤:先将炼钢原料(如生铁、废钢材等)装入炉中,然后通过喷吹技术喷吹高温氧化剂(如氧气)和燃料(如煤气)进入炉腔。
喷吹氧气和燃料的高温火焰将炉内的原料加热到高温,并使其中的杂质氧化和燃烧,最终得到理想的钢铁产品。
转炉冶炼工艺技术有一些明显的优点。
首先,由于采用喷吹技术进行加热,转炉冶炼工艺技术的加热效率较高,能够迅速将原料加热到所需温度,从而提高了生产效率。
此外,喷吹技术还能够控制炉内的化学反应过程,从而使得冶炼过程更加稳定可控。
其次,转炉冶炼工艺技术还能够适应多种原料的冶炼需求。
由于喷吹氧气的高温火焰能够迅速加热和燃烧炉内的杂质,因此转炉冶炼工艺技术适于冶炼含有高杂质原料,如废钢材等。
最后,由于转炉冶炼工艺技术的操作相对简单,不需要进行复杂的炉膛维修和保养工作,因此能够降低生产成本,提高钢铁冶炼的经济效益。
然而,转炉冶炼工艺技术也存在一些问题。
首先,由于转炉冶炼工艺技术需要喷吹氧气进行加热和燃烧,因此会消耗大量的氧气和燃料,从而增加了生产成本。
其次,由于转炉冶炼工艺技术需要高温火焰进行加热和燃烧,因此会产生大量的烟尘和有害气体,对环境造成污染。
为了解决这些问题,现代转炉冶炼工艺技术通常采用了一系列的环保措施,如烟气脱硫、烟尘除尘等,以降低环境污染。
综上所述,转炉冶炼工艺技术是一种利用转炉进行钢铁冶炼的方法。
转炉冶炼工艺技术具有加热效率高、冶炼稳定可控、原料适应性强等优点,但也存在氧耗高、环境污染等问题。
随着科技的不断进步,转炉冶炼工艺技术将进一步完善,为钢铁行业的发展做出更大贡献。
转炉用铁水冶炼不锈钢的技术进展_林企曾

产厂家列于表 1 。 由表 1 可知生产工艺有两类 ,一类是全铁水
冶炼 ,一类是部分铁水冶炼 。全铁水工艺视使用 合金料不同又分为两类 :一类采用高碳铬铁作合 金料 ,其厂家以新日铁八幡厂 、室兰厂以及台湾中 钢公司为代表[2 ][3 ][4 ] ; 另一类则采用铬矿砂作合 金料 ,先进行熔融还原变成含铬铁水后再进行转 炉脱碳精炼 ,这类工艺以川崎制铁千叶厂和日本 钢管福山厂为代表[5][6] 。部分铁水工艺是先用小 电炉熔化废钢和合金 ,再倒入转炉并兑入铁水吹 炼 ,这类工艺以巴西阿谢西塔厂为代表[7] 。
·12 ·
林企曾等 :转炉用铁水冶炼不锈钢的技术进展
图 4 川崎千叶厂转炉生产不锈钢冶炼成分和温度的变化
表 2 转炉用全铁水工艺生产的不锈钢品种结构 %
新日铁八幡厂
川崎制铁千叶厂
奥氏体不锈钢 1. 6 奥氏体不锈钢
35
11. 13 %Cr 钢 15. 4 马氏体不锈钢 19. 6
16 %Cr 钢
另一类是以铁水为原料不使用电弧炉化钢而是在转炉内用铁水加铬矿或铬铁合金直接熔融还原或初脱碳然后再经真空处理最终脱碳精炼这种方法由于采用廉价的铁水作原料可以降低不锈钢生产成本因而在一些钢铁联合企业中得到了应用
2000 年 10 月 第 16 卷 第 5 期
炼 钢 Steelmaking
Keywords refining in converter stainless steel trend of development
1 前 言
不锈钢 的 冶 炼 方 法 视 原 料 的 不 同 主 要 有 两 类 ,一类是以固态原料为主 ,如废钢或合金 ,先在 电炉中熔化炉料 ,然后在各种不同的转炉中精炼 (包 括 AOD 、CLU 、K —OBM、KCB 、MRP、LD —OB 等) 。既可采用最终为 VOD 真空处理的三步法 , 也可采用只在转炉后进行简单钢包处理的二步 法 。这种方法用电炉作为初炼炉 ,主要用于熔化 炉料 ,生产不锈钢粗钢水 。目前世界上大多数由 不锈钢厂采用的电炉 + AOD 二步法冶炼不锈钢 , 其产量总计已突破 1 000 万 t ,占世界不锈钢总产 量的 68. 7 %[1 ] 。
转炉炼钢 工艺流程

转炉炼钢工艺流程
转炉炼钢是一种重要的炼钢工艺,主要用于生产各种类型的钢材。
它的工艺流程包括预处理、炉内冶炼和炉外精炼等几个环节。
首先是预处理环节。
在转炉炼钢之前,需要对原料进行预处理,以确保炉内的冶炼过程能够顺利进行。
这包括原料的装料和计量,以及加入合适的石灰和矿渣等辅料来调节炉内的化学成分。
接下来是炉内冶炼。
转炉炼钢时,首先将预处理好的原料装入转炉中,并通过高温燃烧器将煤气喷入转炉底部,使炉内温度升高。
同时,通过转炉顶部的吹氧管向炉内喷入高压氧气,以促进原料的燃烧和脱碳反应。
在冶炼过程中,还会根据需要加入适量的合金元素,以调整炉内的化学成分和物理性能。
在炉内冶炼完成后,还需要进行炉外精炼。
精炼过程主要是通过在转炉炉顶加装精炼装置,如真空搅拌炉、中间接钢重复纯化和CAS-OB联合炉等,对炉内钢液进行精炼处理。
通过精炼,可以进一步控制钢液的成分和净化度,提高钢材的质量。
最后是钢液的出炉和连铸。
炼钢结束后,将炉内的钢液倒入包括倒钢车和连铸机在内的后续工艺设备中。
在连铸中,钢液被注入到结晶器中,在冷却过程中逐渐凝固成坯料。
然后坯料经过一系列的加工和处理,最终成为各种规格和形状的钢材。
总的来说,转炉炼钢的工艺流程较为复杂,但由于其高效、灵活和适应性强等优点,受到了广泛的应用。
通过精细控制每个
环节的参数和操作,可以获得高质量的钢材,满足不同行业和领域的需求。
- 1、下载文档前请自行甄别文档内容的完整性,平台不提供额外的编辑、内容补充、找答案等附加服务。
- 2、"仅部分预览"的文档,不可在线预览部分如存在完整性等问题,可反馈申请退款(可完整预览的文档不适用该条件!)。
- 3、如文档侵犯您的权益,请联系客服反馈,我们会尽快为您处理(人工客服工作时间:9:00-18:30)。
转炉高效冶炼不锈钢技术转炉高效冶炼不锈钢技术1 前言不锈钢以其优良的特性在化学、电力、交通运输、航空航天工业、食品加工、民用等方面得到了广泛的应用,自1912年德国Crupp公司在感应炉上成功地开发出不锈钢冶炼工艺,并成功应用于生产实践以来,90多年来围绕着低成本、高效率生产不锈钢技术,世界不锈钢生产商进行了不懈的努力,开发出了多种不锈钢生产工艺技术。
20世纪80年代以来,随着铁水预处理技术应用日益成熟,铁水脱硅、脱磷和脱硫技术开发成功并应用于工业化生产,为转炉提供低磷、低硫铁水创造了条件。
同时转炉顶底复吹技术日益完善,开发出了较强的、便少调节的、可供多种气体的底吹功能,使转炉吹炼不锈钢的条件更加优越,铬的氧化损失进一步降低。
更为重要的是炉外精炼技术的发展十分迅猛,特别是RH- OR、RH-KTB、VOD等真空吹氧脱碳技术的开发,不仅可以减轻转炉冶炼不锈钢的脱碳任务,而可以改善不锈钢的质量和扩大转炉的不锈钢的品种。
因此,随着铁水预处理,顶底复吹和炉外精炼技术献发展使得转炉冶炼不锈钢的生产规模逐步扩大。
2 不锈钢冶炼工艺采用转炉生产不锈钢工艺路线如表1所示。
不锈钢的冶炼方法根据原料的不同主要有三类,一类是以固态原料为主,如废钢或合金,先在电炉中熔化炉料,然后在不同的转炉中精炼(包拒AOD、CLU、K—OBM、KCB、MRP、LD—0B等)。
既可以采用最终为VOD真空处理的三步法,也可以采用只在转炉后简单钢包处理的二步法。
这种方法用电炉作为初炼炉,主要用于熔化炉料,生产不锈钢母液。
目前世界上大多数的不锈钢厂采用电炉+AOD二步法冶炼不锈钢,占不锈钢总产量献65%以上。
第二类是以铁水为原料,不使用电炉熔化废钢,而是转炉内用铁水加铬矿或铬铁合金直接灶融还原或初脱碳,然后再经真空处理最终脱碳榨炼,这种方法由于铁水作为原料,可以降低不锈钢的生产成本,因而在一些钢铁联合企业中得到了应用。
第三类是以部分铁水为原料,采用的电炉+转炉进行冶炼,再经真空精炼。
这种工艺的思路是把EAF+AOD和EAF+VOD的优点结合起来,达到快节奏、低成本、低氩耗的生产超低碳、超低氮的不锈钢目的。
该工艺采用脱磷铁水与EAF熔化炉的高温合金预熔液混合兑入转炉,在转炉内完成脱碳、脱硫、还原、粗调合金成分等任务,然后再进行真空处理,完成最终脱碳及合金成分调整等精炼工作。
表1 转炉用铁水冶炼不锈钢的主要生产工艺路线序号国家生产厂工艺路线产品组成产量/(万t·a-1)投产时间1 日本新日铁八幡HM De-P+1×120tLD-OB+VODCr系:98.4%Ni-Cr:1.6%24.1 1983Cr 系:63.1% Ni-Cr:36.9% Cr 系:主产品2 日本川崎千叶(No.4)1×185t SR-KCB(铁水+废钢)+1×185t DC-KCB+VOD/RH-KTB601996.53 中国台湾中钢HM De- P+120t CSCB+VOD1994.7 4 南非ISCOR Pretoria厂HM De-P+1×90tUHP+1×125t K-OBM-S+VOD501996.75 巴西AcesitaHM De-P+2×33t EFA+1×75t MRP-L+VOD301996.56 日本室兰厂HM De-P+155t LD-CB+RH-OB501972注:HM 为铁水,De-P 表示铁水脱磷,SR-KCB 即熔融还原转炉,DC-KCB 即脱碳转炉,LD-OB 即新日铁开发的顶底复合冶炼方法,MRP-L 即曼内斯曼德马克开发的精炼方法,CSCB 即台湾中钢开发的顶底复合冶炼方法。
3 转炉冶炼不锈钢的关键技术3.1 脱碳保铬由于不锈钢的主要合金——铬元素在高温下很容易氧化,因此在转炉冶炼不锈钢不但要具有足够的脱碳能力,同时还抑制铬元素的氧化损失。
根据冶金学原理,钢水温度越高越有利于脱碳反应的进行;转炉内CO的分压越低有利于铬的还原,在吹氧脱碳的同时,可抑制铬元素的氧化损失。
为了符合热力学理论的要求,在转炉通常采用的是稀释精炼法即以大流量的底吹惰性气体来稀释转炉内因脱碳反应所产生的CO的浓度,降低CO的分压。
同时,也可促进钢水的搅拌,加速脱碳反应。
此外,在钢水温度控制方面,首先要克服热源不足的问题,然后才能有效达到高温(≥1700℃)操作。
3.2 热补偿由于不锈钢是高合金钢,在冶炼时需加入大量的冷料合金,如仅以铁水的显热和氧化热在转炉内炼钢,其热能显然是不够的。
据高碳铬铁、镍铁[w(Ni)=25%]及铁水冶炼430、304不锈钢的物料平衡分析结果可知:冶炼430钢种的热不足率为5.29%,冶炼304钢种的热不足率为12.35%。
根据台湾中钢针对304、316、410、420和430等钢种通过数学模型计算出加废钢和加17%废钢的计算结果,则上述各钢种的热量不足率如表2所示。
表2 中钢不锈钢转炉冶炼的热不足率%钢种不加废钢加17%的废钢SUS 430 5.4 14.2SUS 410 6.1 15.0SUS 420 8.0 16.8SUS 304 11.5 21.8SUS 316 14.6 23.8由此可见,采用脱磷铁水单转炉冶炼400系列低合金牌号不锈钢有着明显的优势,新日铁和台湾中钢的产品结构也证明了这一点。
冶炼304以上高合金牌号不锈钢时在不加废钢时热不足率在10%以上。
为了解决转炉冶炼不锈钢时热量不足的问题,川崎千叶第四炼钢厂、台湾中钢等都是通过向转炉中加入焦碳,通过焦碳反应产生的CO二次燃烧放出的热量来补偿熔池的热量。
但是如果加入大量的焦碳会增加转炉的冶炼周期,同时还会增加转炉和后工序的脱硫负担。
3.3 炉底寿命由于顶底复吹转炉在冶炼不锈钢时,其底吹气体的流量是冶炼低碳钢的20倍以上,采用双重吹管,加上高温操作的因素,皆会加速炉底耐火材料的熔损。
因此,降低成本底耐火材料熔损速度技术,提高炉底耐火材料的寿命,成为降低转炉冶炼不锈钢成本重要一环。
为了解决转炉不锈钢时炉底寿命较低的问题,开发出了可更换炉底技术。
炉底寿命的长短,取决于底吹喷嘴的寿命。
底吹喷嘴通常为双层套管形式,内管根据冶炼不同的阶段要求喷吹氧气、氢气或氮气,外管吹入冷却性气体,在喷嘴区域形成保护性“蘑菇头”,以提高喷嘴的寿命,降低耐火材料的消耗,同时可确保钢液充分搅拌。
常用的冷却气体有天然气、丙烷和丁烷。
常用冷却气体的保护气体的冷却效果如表3所示。
表3 常用冷却气体的保护气体的冷却效果序号气体名称裂解能(298~1623)K/(kJ·mol-1)显热/(kJ·mol-1)总热量/(kJ·mol-3)1 天然气77.4 107.4 8 1432 丙烷103.7 240.8 15 3913 丁烷125.6 307.6 19 5253.4 高效脱硫技术一般不锈钢成品的硫的质量分数要求在3.0×10-5以下,因此要求钢水的硫含量就尽可能在此水平,减轻后工序精炼的脱硫的负担。
但由于转炼不锈钢热量不足,需加入焦炭,通常焦炭中硫的质量分数在0.5%左右。
据中钢的统计,在不加入废钢时,焦炭含硫量含硫量,片所有的原料(铁水、焦炭和合金)总硫量的一半以上。
若加入废钢,须加入更多的焦炭.则焦炭所,片比例高达三分之二以上。
所以,转炉工艺需有足够的脱硫能力,才能使钢水硫含量降至规定的范围内。
根据文献转炉的脱硫主要是在不锈钢冶炼还原期进行,脱硫率与还原期的炉渣有正相关性,炉渣的碱度愈高愈有利少脱硫反应((CaO)+[S]=CaS)+[O])的进行。
若碱度在1.5以上时,由脱硫率可达80%以上。
转炉工艺加上后工序精炼的脱硫功能,可以使处理后的钢水含硫的质量分数稳定在2.0×10-5左右。
4 转炉高效冶炼不锈钢的工艺4.1 铁水预处理对于不锈钢来讲,钢中的P是有害元素。
在不锈钢冶炼过程中钢水含有大量的铬,从热力学角度分析,高铬钢液脱P困难,目前无高效、简单的脱磷手段;而采用铁水作为原料,可以利用铁水预处理工艺将铁水中的P脱到一个较低的水平,质量分数一般为0.015%,避免采用废钢为原料时带入P高的问题,解决转炉冶炼过程中的脱磷难题。
4.2 转炉顶底复吹冶炼技术国外应用转炉生产不锈钢的厂家较多,其冶炼任务是熔化原料,生产不锈钢母液、快速脱碳。
就其冶炼特点,可以分为单转炉冶炼、双转炉冶炼和电炉转炉联合冶炼几种模式。
在这里重点介绍单转炉和双转炉冶炼不锈钢模式。
4.2.1单转炉模式单转炉冶炼不锈钢以新日铁八幅厂、室兰厂和台湾中钢为代表,新日铁八幅厂生产不锈钢工艺流程图见图1所示。
该工艺是在一个转炉完成不锈钢冶炼。
经过脱硅、脱硫和脱磷铁水兑入顶底复吹转炉中,转炉的冶炼大致可以用分为三个阶段;第一阶段是铁水脱碳期,此阶段的主要功能是用氧气进行铁水脱碳反应及热补偿作业,因为铁水经过脱硅、脱硫和脱磷后其温度己降至1200~1250℃,铁水中硅质量分数也只有0.05%以下,所以需要以添加焦炭的方式来补偿热源不足;第二阶段为脱碳保铬期,此阶段需从料仓中连续添加大量的高碳铬铁及适量的高碳锰铁、镍粒等合金料,以氧气来继续进行脱碳反应,温度控制在1700℃以上,同时需通入较大流量的惰性气体进行底吹,增加熔池的搅拌功能步{降低炉内CO的分压,脱碳保铬;第三阶段为还原期,当碳质量分数脱至0.2%~0.3%时,转炉的脱碳任务结束,停止吹氧,此时渣中的氧化铬含量较高,需进行还原回收金属铬,可通过添加硅铁或铝来进行。
转炉冶炼结束后,钢水再经VOD或RH等精炼设备进行最终的脱碳和合金成分的调整。
台湾中钢CSCB转钢冶炼不锈钢的吹炼模式图见图2。
4.2.2双转炉模式双转炉冶炼不锈钢工艺是以川崎制铁千叶厂No.4车间为代表,生产工艺流程见图3。
不锈钢冶炼采用两个转炉进行。
由于冶炼不锈钢时,铬和镍合金的费用占整个不锈钢冶炼成本的较大,因此该公司为了降低冶炼不锈钢的成本,开发出了铬矿熔融还原工艺。
该工艺是在不锈钢精炼前,将铬矿砂和焦炭从炉子的顶部加入熔融还原转炉(SR- KCB)中,利用焦炭和氧气反应热以及炭的还原能力将铬矿熔融并铬矿还原进入钢液中,从而生产不锈钢的初炼钢液。
然后将熔融还原成含铬的钢液再在脱碳转炉(DC- KCB)脱碳、精炼工艺。
(1)铬矿的熔融还原日木川崎制铁千叶厂No.4车间熔融还原操作大致可以分三个阶段:第一阶段为返回料熔化期:连续吹炼熔化不锈钢返回料,并升温到预定的温度(1813~1833K);第二阶段为熔融还原期:根据供氧速度,将铬矿和小块焦炭按一定的比例加入炉中,一边保持熔池温度恒定,一边进行熔融还原反应。
由于铬矿的还原依赖于炉内二次燃烧产生的热量来进行,因此要不断调整顶枪的供氧条件和铬矿的加入速度。