克劳斯法硫磺回收方法
用液相克劳斯反应从烟气中回收硫磺

用液相克劳斯反应从烟气中回收硫磺
用液相克劳斯反应从烟气中回收硫磺
利用液相克劳斯反应直接从烟气脱硫过程回收硫磺.考察了吸收液pH、NaHSO3和NaHS的添加顺序、NaHS添加量对硫产率的影响.在反应前将Na2S酸化、NaHSO3溶液的初始pH为2.3左右、n(SO32-)/n(S2-)为4.21的条件下,反应后得到的硫磺全部为斜方晶体(即α-硫),硫产率为58%.
作者:刘效峰李玉平 Liu Xiaofeng Li Yuping 作者单位:北京理工大学,化工与环境学院,北京,100081 刊名:化工环保ISTIC PKU 英文刊名:ENVIRONMENTAL PROTECTION OF CHEMICAL INDUSTRY 年,卷(期):2005 25(4) 分类号:X701 关键词:二氧化硫液相克劳斯反应回收硫磺综合利用。
克劳斯法(硫回收)

克劳斯法- 正文将硫化氢转变为硫磺的工业方法,由英国人C.F.克劳斯于1883年发明。
此法广泛用于煤、石油、天然气的加工过程(如合成氨原料气生产、炼厂气加工等),在脱硫产生的含硫化氢气体中回收硫,并可解决炼厂废气对大气的污染问题。
克劳斯法回收硫的纯度可达到99.8%,可作为生产硫酸的一种硫资源,也可作其他部门的化工原料。
克劳斯法的主要化学反应为:自脱硫装置来的酸性气全部进入燃烧炉(见图),其中的硫化氢有三分之一可氧化成二氧化硫,并与未氧化的硫化氢一起进入转化器,进行催化转化。
为完成部分燃烧反应,通入燃烧炉的空气需严格控制,这是克劳斯法的操作关键。
燃烧炉的温度约为1200℃,燃烧产物中除二氧化硫、水和氮外,还有少量由硫化氢直接分解而生成的元素硫。
为回收热量,燃烧产物在进入转化器之前先经废热锅炉发生蒸汽。
转化器为一固定床反应器,内装有氧化铝催化剂(见金属氧化物催化剂),入口温度控制在220~240℃。
由于过程为放热反应,出口温度为270~300℃。
自转化器出来的反应产物进入冷凝冷却器,液态硫磺流至硫磺罐。
为达到较高的硫回收率,工业装置一般还设有二级、三级甚至四级转化器。
在转化器中能否达到较高的转化率,关键是要控制H2S/SO2的摩尔比,使之保持为2,同时要使用性能较好的氧化铝催化剂。
采用两级转化时,硫的回收率可达93%~95%,三级转化时可达94%~96%,四级转化时可达95%~97%。
从克劳斯装置排出的尾气中还含有一定数量的二氧化硫(8000~18000ppm)。
按环保要求,还需将尾气进行处理,使最终排入大气的尾气中含二氧化硫量在300ppm左右,使硫的总回收率达99.8%左右。
克劳斯法硫磺回收工艺技术现状及发展趋势

克劳斯法硫磺回收工艺技术现状及发展趋势1. 克劳斯法硫磺回收原理克劳斯法是一种将含硫污水中的硫酸盐还原成硫磺的化学过程。
其原理是通过还原反应,使硫酸盐转化为硫醇,并进一步转化为元素硫。
克劳斯法将含硫污水中的硫酸盐转化为硫磺,同时释放出二氧化碳和水。
这种方法简单、原理清晰,对硫磺回收效果良好。
目前,克劳斯法硫磺回收工艺技术在化工、冶金等行业得到了广泛应用。
在化肥生产过程中,硫磺是必不可少的原料,而化肥生产废水中常含有大量硫酸盐,采用克劳斯法可以将硫酸盐回收为硫磺,节约了资源并减少了对环境的污染。
在冶金行业,由于冶炼过程中废气中含有大量硫化氢,采用克劳斯法可以将硫化氢转化为硫磺,实现了硫磺的回收。
克劳斯法硫磺回收工艺技术具有技术成熟、工艺简单、回收效率高的特点。
在实际应用中,该技术被广泛应用,并取得了显著的经济和环保效益。
克劳斯法硫磺回收工艺技术成为了当前硫磺回收的主要技术之一。
1. 技术改进方向目前,虽然克劳斯法硫磺回收工艺技术已经相对成熟,但仍然存在一些问题亟待解决。
现有的克劳斯法硫磺回收工艺技术存在能耗高、产物纯度较低、设备运行稳定性等方面的问题。
未来的发展方向主要包括降低能耗、提高产物纯度、改善设备运行稳定性等方面。
2. 配套设备的研发克劳斯法硫磺回收工艺技术需要配套的设备进行生产实施,例如还原反应器、脱硫器、结晶器等。
未来的发展趋势是研发更加高效、节能、环保的配套设备,以满足克劳斯法硫磺回收工艺技术的需求。
3. 与其他技术的结合应用随着科学技术的不断发展,克劳斯法硫磺回收工艺技术将与其他技术相结合,以期达到更好的效果。
可以将克劳斯法与生物技术相结合,利用微生物对硫酸盐进行生物降解,进而进一步提高硫磺回收效率。
还可以将克劳斯法与化学物理技术相结合,以达到降低产物纯度、提高能效等方面的目标。
4. 环保化发展随着社会对环保意识的不断提高,环保化已成为各行业的发展趋势。
克劳斯法硫磺回收工艺技术的发展趋势将更加注重环保化,努力达到减少废物排放、减少资源消耗等目标。
克劳斯法硫磺回收工艺技术现状及发展趋势

克劳斯法硫磺回收工艺技术现状及发展趋势随着工业化进程的不断深入,硫磺资源的开发和利用已经成为全球性的热点话题。
硫磺是一种非常重要的化工原料,在化肥、农药、橡胶、化工等多个领域都有着广泛的应用。
大量的工业生产过程中会产生硫磺废气,如果不进行合理的处理和回收,不仅会对环境造成严重的污染,还会浪费大量的资源。
硫磺的回收和再利用技术的研究和开发成为了当今工业界的重要课题之一。
在硫磺回收技术中,克劳斯法硫磺回收工艺技术是一种非常有效的方法。
克劳斯法是一种使用空气中氧气将二氧化硫氧化为三氧化硫,再进一步还原为硫磺的工艺方法。
这种方法在硫磺的回收过程中具有诸多优势,如能够高效回收硫磺、减少排放污染物等。
克劳斯法硫磺回收工艺技术已经在工业生产中得到了广泛的应用。
目前,克劳斯法硫磺回收工艺技术在全球范围内得到了越来越多的关注和应用,其技术现状和发展趋势备受瞩目。
现在,本文将从技术现状和未来发展趋势两个方面入手,对克劳斯法硫磺回收工艺技术进行深入的分析和探讨。
1. 技术原理及流程克劳斯法硫磺回收工艺技术的原理是利用雷电产生的电场和静电作用来促进空气中的氧气与二氧化硫发生氧化反应,生成三氧化硫。
然后,利用氢气将三氧化硫还原为硫磺。
具体的流程包括以下几个步骤:(1)将二氧化硫气体通入反应器中,利用雷电产生的静电场促进二氧化硫与空气中的氧气发生反应生成三氧化硫。
(2)将生成的三氧化硫与氢气在高温条件下发生还原反应,生成硫磺和水蒸气。
(3)通过冷却和凝结,将硫磺和水蒸气分离成为液态硫磺和液态水。
2. 技术优势克劳斯法硫磺回收工艺技术具有以下几个方面的优势:(1)高效回收:该工艺技术能够高效、快速地将二氧化硫转化为硫磺,回收率较高。
(2)减少污染:该工艺技术的产物中不含有硫化物和氮氧化物等污染物,对环境污染小。
(3)资源综合利用:回收的硫磺可以再次应用于化肥、农药等领域,实现资源的综合利用。
3. 应用现状克劳斯法硫磺回收工艺技术已经在一些工业生产中得到了广泛的应用。
克劳斯硫回收操作规

克劳斯硫回收操作规程1. 岗位任务及意义我厂所采用的原料煤硫含量较高,如果不加以回收,就会污染空气。
本岗位接受低温甲醇洗岗位送来的硫化氢尾气,通过克劳斯回收装置回收,并制成固体硫磺。
本装置H2S的总转化率90-95%;COS不发生克劳斯反应,通过尾气烟囱直接放空。
年产硫磺1万吨,回收硫磺不仅经济效益可观还可以消除污染。
2. 工艺原理及流程叙述2.1工艺原理克劳斯法回收硫的基本反应如下:H2S+1/2O2→S+H2O (1)H2S+3/2O2→SO2+H2O (2)2H2S+SO2→3S+2H2O (3)反应(1)(2)在燃烧室中进行,在温度1150℃-1300℃,压力0.06MPa和严格控制气量的条件下,将硫化氢燃烧成二氧化硫,为催化反应提供(H2S+CS2)/SO2为2/1的混合气体。
此气体通过Al2O3基触媒,按反应(3)生成单质硫。
2.2流程叙述来自上游甲醇洗工序的酸性气温度为37.2℃,压力为0.22MPaG,经进料管分离罐(V1301)分出挟带液后,按一定比例分成两股,其中一股去H2S燃烧炉(F1301)。
该流股经过控制阀后压力降为0.06 MPaG进入H2S燃烧炉(F1301),在H2S燃烧炉(F1301)中,酸性气和一定比例的反应空气发生燃烧反应,反应生成SO2的和燃烧反应剩余的H2S进一步发生部分克劳斯反应,反应后的酸性气体温度可达800℃以上。
高温酸性气随后进入H2S余热回收器(E1301)回收器废热并副产蒸汽,同时将反应生成的单质硫部分冷凝。
H2S余热回收器(E1301)一共有四程换热管(PASS1~4)回收本工序工艺气的废热,高温酸性气废热的回收是通过其中的第一、二换热管(PASS1、PASS2)进行的。
高温酸性气全部通过PASS1后温度降为600℃,然后分成两股,其中一股流经PASS2温度进一步降至185℃,然后和未经过PASS2的流股混和。
通过调整两个流股的比例可使混合后的温度控制在约300℃。
克劳斯硫磺回收主要设备及操作条件
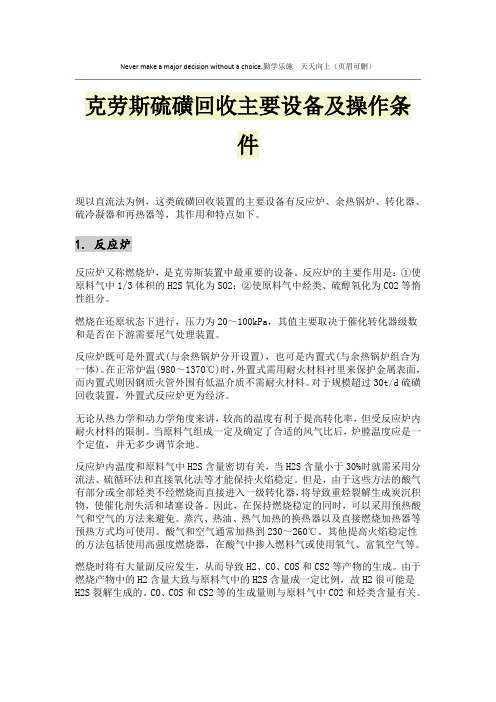
Never make a major decision without a choice.勤学乐施天天向上(页眉可删)克劳斯硫磺回收主要设备及操作条件现以直流法为例,这类硫磺回收装置的主要设备有反应炉、余热锅炉、转化器、硫冷凝器和再热器等,其作用和特点如下。
1. 反应炉反应炉又称燃烧炉,是克劳斯装置中最重要的设备。
反应炉的主要作用是:①使原料气中1/3体积的H2S氧化为SO2;②使原料气中烃类、硫醇氧化为CO2等惰性组分。
燃烧在还原状态下进行,压力为20~100kPa,其值主要取决于催化转化器级数和是否在下游需要尾气处理装置。
反应炉既可是外置式(与余热锅炉分开设置),也可是内置式(与余热锅炉组合为一体)。
在正常炉温(980~1370℃)时,外置式需用耐火材料衬里来保护金属表面,而内置式则因钢质火管外围有低温介质不需耐火材料。
对于规模超过30t/d硫磺回收装置,外置式反应炉更为经济。
无论从热力学和动力学角度来讲,较高的温度有利于提高转化率,但受反应炉内耐火材料的限制。
当原料气组成一定及确定了合适的风气比后,炉膛温度应是一个定值,并无多少调节余地。
反应炉内温度和原料气中H2S含量密切有关,当H2S含量小于30%时就需采用分流法、硫循环法和直接氧化法等才能保持火焰稳定。
但是,由于这些方法的酸气有部分或全部烃类不经燃烧而直接进入一级转化器,将导致重烃裂解生成炭沉积物,使催化剂失活和堵塞设备。
因此,在保持燃烧稳定的同时,可以采用预热酸气和空气的方法来避免。
蒸汽、热油、热气加热的换热器以及直接燃烧加热器等预热方式均可使用。
酸气和空气通常加热到230~260℃。
其他提高火焰稳定性的方法包括使用高强度燃烧器,在酸气中掺入燃料气或使用氧气、富氧空气等。
燃烧时将有大量副反应发生,从而导致H2、CO、COS和CS2等产物的生成。
由于燃烧产物中的H2含量大致与原料气中的H2S含量成一定比例,故H2很可能是H2S裂解生成的。
克劳斯法硫磺回收工艺技术探讨

斯炉内进行燃烧,使硫化氢与氧气发生氧化反应生成二氧化硫,之后,二氧化硫在催化剂的作用下和没有发生燃烧反应的硫化氢气体发生催化反应,最终生成硫磺。
在传统克劳斯法的基础上,工作人员经过对其反应流程的优化,形成了超优克劳斯法。
超优克劳斯法充分利用了现代的技术和工艺,基于热力学平衡角度对传统克劳斯法进行优化,主要涉及到发展新型的催化剂、选择使用富氧燃烧技术等。
这些新的工艺和技术的使用,使超优克劳斯法硫磺回收工艺对于硫元素的回收率大大提升。
通过相关实践结果,可以表明,采用超优克劳斯法硫磺回收工艺对硫的回收率能够达到99.4%以上。
这大大降低了石油化工生产对环境造成的污染。
超优克劳斯法通常由一个高温段以及三个反应段所共同组成。
高温段的设备主要有硫化氢燃烧炉以及废热锅炉,硫化氢在燃烧炉内发生氧化反应生成二氧化硫,在所有二氧化硫中大约有三分之一的硫化氢会发生反应。
剩下的硫化氢会和生成的二氧化硫在催化剂的作用下生成硫磺。
其化学反应方程式为:2H 2S + SO 2→3S + 2H 2O 。
之后,会继续进行加氢催化反应。
二氧化硫会在该反应段被尾气中的氢气与一氧化碳还原为单质硫和硫化氢。
最后,在最后一个反应段向反应器中通入过量的空气,以便于使剩余的硫化氢全部发生氧化反应,最终生成水和单质硫。
超优克劳斯法硫磺回收工艺的核心对尾气中的二氧化硫进行加氢还原反应,使其生成硫化氢,之后又运用过量的氧气使硫化氢发生反应生成单质硫。
和常规克劳斯法尾气处理工艺的主要区别是,超优克劳斯法硫磺回收工艺的加氢过程不需要单独的制氢过程,而是利用反应本身所产生的氢气就能够实现,且不需要对过程气进行升温或者降温过程;另外,尾气中的硫化氢也不需要再使用溶剂进行吸收,优化和改造成本相对较低,具有较高的经济价值。
3 克劳斯法硫磺回收工艺的优势(1)在石油化工生产硫回收过程中,克劳斯法硫磺回收工艺具有工艺简便、操作简单、成本较低等优势,且该反应的化学稳定性相对较高。
超级克劳斯硫磺回收工艺及应用

超级克劳斯硫磺回收工艺及应用摘要:克劳斯硫磺回收工艺自20世纪30年代实现工业化后,已经广泛用于合成氨和甲醇原料气生产、炼厂气加工、天然气净化等煤、石油、天然气的加工过程中。
克劳斯工艺具有流程简单、操作灵活、回收硫磺纯度高(质量分数可达99.8%)、投资费用低、环境及规模效益显著等特点,产品硫磺可作为生产硫酸的一种硫资源,也可作其它部门的化工原料。
本文对超级克劳斯硫磺回收工艺及应用进行了分析探讨,仅供参考。
关键词:硫磺回收;超级克劳斯;工艺一、超级克劳斯硫磺回收工艺从石油,石化、冶金、化肥等行业含H2S等硫化物的酸性气中回收利用硫,根据工艺流程选择和当地产品销路情况,产品可以制成硫磺或硫酸。
对含(一)、S酸性气体的处理,用H2S制取硫磺,工业生产中多采用固定床催化氧化,典型的方法有克劳斯工艺。
利用克劳斯装置净化尾气中的硫化物回收硫磺工艺已得到了迅速发展,其具体工艺流程有20多种,主要有传统克劳斯工艺,低温克劳斯工艺、超级克劳斯(SuperClaus)工艺,带有SCOT尾气处理的克劳斯工艺等。
其中超级克劳斯工艺是在两级普通克劳斯转化之后,第三级改用选择性氧化催化剂,将H2S直接氧化成元素硫,传统克劳斯工艺要求H2S/SO2摩尔比值为2的条件下进行,而此种工艺却维持选择性氧化催化段在富H2S条件下举行,一改以往单纯增加级数来提高H2S的回收率的方法。
超级克劳斯工艺改变了以往单纯提高H2S和SO2反应进程的方法,在传统克劳斯转化的最后一级转化段使用新型选择性氧化催化剂,由此来改进克劳斯工艺的硫回收技术。
在通入过量空气的情况下,超级克劳斯工艺可将来自克劳斯段最后一级过程气中剩余的H2S选择性地氧化为单质硫。
超级克劳斯反应器出口的过程气(含有非常少量的H2S)进入深冷器中,将过程气中的硫磺最大限度地捕集下来,从而将硫磺回收率提高到99%以上。
超级克劳斯工艺流程图见下图。
二、技术特点1、操作灵活方便由于超级克劳斯工艺采用过量空气操作,从而产生较少的SO2,因此对空气的控制要求不是很严格,不要求精确控制H2S和SO2的比例,而是将最后一级克劳斯转化器出口过程气中H2S体积分数控制在0.6%~1.5%,因此可以采用简单的流量控制回路,使操作灵活方便、弹性范围大,操作下限可以达到15%;超级克劳斯催化剂具有良好的热稳定性、化学稳定性和机械强度,有害物质排放少,催化剂使用寿命长达8~10年;过程气中高浓度水含量不会影响H2S的转化率,装置运行平稳可靠,维修方便,非计划性停车时间少于1%。
- 1、下载文档前请自行甄别文档内容的完整性,平台不提供额外的编辑、内容补充、找答案等附加服务。
- 2、"仅部分预览"的文档,不可在线预览部分如存在完整性等问题,可反馈申请退款(可完整预览的文档不适用该条件!)。
- 3、如文档侵犯您的权益,请联系客服反馈,我们会尽快为您处理(人工客服工作时间:9:00-18:30)。
克劳斯法硫回收一、工艺设计三高无烟煤:元素分析含硫3.3%造气:121332Nm3含硫化氢1.11% 含COS0.12% 约17克/Nm3低温甲醇洗:净化气含硫0.1ppm 送出H2S含量为35%左右的酸性气体3871Nm3。
本岗位主要任务是回收低温甲醇洗含硫CO2尾气中的H2S组份,通过该装置回收,制成颗粒状硫磺。
同时将尾气送到锅炉燃烧,使排放废气达到国家排放标准,本装置的正常硫磺产量约为16160吨/年。
二、工艺方法1、常用硫回收工艺(1) 液相直接氧化工艺有代表性的液相直接氧化工艺有:ADA法和改良ADA法脱硫、拷胶法脱硫、氨水液相催化法脱等。
液相直接氧化工艺适用于硫的“粗脱”,如果要求高的硫回收率和达到排放标准的尾气,宜采用固定床催化氧化工艺或生物法硫回收工艺。
(2) 固定床催化氧化工艺硫回收率较高的Claus工艺是固定床催化氧化硫回收工艺的代表。
Claus硫回收装置一般都配有相应的尾气处理单元,这些先进的尾气处理单元或与硫回收装置组合为一个整体装置,或单独成为一个后续装置。
Claus硫回收工艺及尾气处理方式种类繁多,但基本是在Claus硫回收技术基础上发展起来的,主要有:SCOT工艺、SuperClaus工艺、Clinsulf工艺、Sulfreen工艺、MCRC工艺等。
2. 克劳斯硫回收工艺特点常规Claus工艺是目前炼厂气、天然气加工副产酸性气体及其它含H2S 气体回收硫的主要方法。
其特点是:流程简单、设备少、占地少、投资省、回收硫磺纯度高。
但是由于受化学平衡的限制,两级催化转化的常规Claus工艺硫回收率为90-95%,三级转化也只能达到95-98%,随着人们环保意识的日益增强和环保标准的提高,常规Claus工艺的尾气中硫化物的排放量已不能满足现行环保标准的要求,降低硫化物排放量和提高硫回收率已迫在眉睫。
一般克劳斯尾气吸收要经过尾气焚烧炉,通过吸收塔,在吸收塔用石灰乳溶液或稀氨水吸收,生成亚硫酸氢钙或亚硫酸氢铵,通过向溶液空气,转化为石膏或硫酸铵,达到无害处理,我公司硫回收尾气送至锅炉燃烧并脱硫后排放。
3、克劳斯法制硫基本原理克劳斯硫回收装置用来处理低温甲醇洗的酸性气体,使酸性气中的H2S转变为单质硫。
首先在燃烧炉三分之一的H2S与氧燃烧,生产SO2,然后剩余的H2S与生成的SO2在催化剂的作用下,进行克劳斯反应生成硫磺。
其主要反应式为:H2S+ 3/2O2= SO2+H2O+519.2kJ2H2S+ SO2=3S+2 H2O +93kJ由于酸气中除H2S外,通常含有CO2、H2O、烃类等化学反应十分复杂,伴有多种副反应发生。
克劳斯法的工艺流程有三种:(1)部分燃烧法(2)分流法(3)燃硫法(2)分流法本装置采用分流法:将三分之一的酸性气体通入燃烧炉,加入空气使其燃烧生成SO2,而其余三分之二酸性气走旁路,绕过燃烧室,与燃烧后的气体汇合进入催化剂床层反应,这种可处理H2S含量为35%左右的酸性气体,并采用三段转化,三级冷凝工艺流程,该法回收硫的纯度较高(99.8%)。
三、原材料及产品主要技术规格:1、原材料技术规格型号为LYTS-01TiO2 LYTS-811,是白色氧化铝催化剂,堆密度~0.7g/cm3,一次装填量30m3。
物理性质:外形尺寸直径4~6mm,比表面≥300m2/g,孔容≥0.40ml/g,堆密度≥0.65kg/l,抗压碎强度>140N/粒,磨耗率<0.3%,催化剂寿命在3年左右。
2、原材料消耗量3、产品技术规格、动力消耗及消耗量4*消耗定额以每吨硫磺计四、装置布置及主要设备由于液态硫的特殊性,对产生液硫的设备均设置在EL5.000平面上,以便于液硫的流动,其余设备根据高差要求,布置在不同平面上。
整个装置占地约600m2。
1、酸气燃烧炉Φ2600×8526 δ=14 V=170m3 设计温度1400 ℃设计压力0.06MP 卧式是克劳斯法制硫工艺中最重要的设备。
在此1/3体积的H2S与空气燃烧生成SO2,保证过程气中H2S:SO2摩尔比为2:1,同时烃类燃烧转化为CO2等惰性组分,并或多或少生成元素硫。
1)火焰温度燃烧炉温度必须保持在920℃以上,否则火焰不能稳定燃烧,最好反应温度在1250~1300左右。
过高设备、耐火材料选择困难,并生成多种氮、硫氧化副产物,导致下游催化剂硫酸盐化而失活。
炉温同H2S浓度密切相关,一般低于40%必须采用分流法。
2)花墙使过程气有一个稳定且充分接触的反应空间,同时使气流均匀进入废热锅炉。
3)炉停留时间高温克劳斯反应一般在1s即可完成,受原料气含量、炉混合均匀程度、燃烧室结构等影响,停留时间一般在1~2.5s。
4)火嘴使酸气和空气等气体有效混合均匀提供一个提供一个使杂质和H2S能够完全燃烧的稳定火焰。
2、废热锅炉Φ45×3.5×60000 n=97 F=119m2 设计温度管程300~1000℃壳程190℃设计压力管程0.06MP 壳程0.77MP 汽包DN800×6000 卧式带汽包从反应器出口气流中回收热量并发生蒸汽,同时使过程气温度降至下游设备所要求的温度并冷凝回收硫。
3、一二三段转化器F1200×7000 ф3800×9882 V=170m3 设计温度390℃设计压力0.06MP 卧式部用隔板隔成三段,触媒装填量30m3, 每段装填量约8~10m3转化器的功能是使过程气中的H2S和SO2在床层上继续克劳斯反应生成元素硫,同时使过程气中COS、CS2等有机硫化物在催化剂床层上水解为H2S和CO2,主要反应在一级反应器中进行,一级反应器实际空速远远大于二、三级,考虑有机物水解要求,一级转化器出口应控制在310~340℃,由于各级冷凝分离了大量产物硫,也不存在有机物水解问题,二、三级转化器在较低温度下操作,可获得较高转化率。
4、一二段换热器、一二三段冷凝器卧式列管换热器、冷凝器一段换热器:F1300×6619 F=159m2 Φ45×3×4000 n=289 设计温度管程280℃壳程230℃设计压力0.06MP二段换热器:F1400×8689 F=269m2 Φ45×3×6000 n=323 设计温度管程380℃壳程145℃设计压力0.05MP一段冷凝器:F1100×8539 F=284m2 Φ38×3×6000 n=403 设计温度管程315℃壳程145℃设计压力管程0.05MP 壳程1、43MP二段冷凝器:F1000×8279 F=222m2 Φ38×3×6000 n=315 设计温度管程220℃壳程165℃设计压力管程0.05MP 壳程1、43MP 三段冷凝器:F1000×8279 F=222m2 Φ38×3×6000 n=315 设计温度管程260℃壳程165℃设计压力管程0.05MP 壳程1、43MP 换热器冷凝器的作用是把转化器生成的元素硫冷凝成液体,同时回收热量。
5、一二三段液硫捕集器立式包括容器、盘管、丝网、波纹管一二三段液硫捕集器:F1200×4163 V=3.84m3 设计温度170℃设计压力容器0.06MP 盘管0.7MP功能是从冷凝器出口尽可能回收液硫和硫雾沫,捕集效果好坏对硫产量影响至关重要。
6、液硫封立式包括夹套、容器两部分F1100×6×3600 V=0.57/2.81m3 设计温度夹套147℃容器160℃设计压力夹套0.3MP 容器常压通过建立液硫液位,利用液硫压力封住系统中工艺气体,防止串出系统,造成危害。
7、液硫储槽包括盘管和容器两部分F2500×8×2500 立式V=12.28m3 设计温度夹套160℃容器160℃设计压力夹套0.3MP 容器常压8、定型设备J61501A、B 空气鼓风机71m3/h 80kpa 132kwJ61503A、B 尾气风机211m3/h 升压15kpa 90kwJ61502A、B 液硫泵 1.24m3/h H=40m 7.5kw硫磺造粒机(成套)含液硫过滤单元,气动球阀,针形调节阀处理量2t/h 9.99kw12930×1210×18600五、工艺流程1、主要工艺流程来自低温甲醇洗的富H2S气体(35%、3871Nm3/h,30 ℃,0.05MPa)进入本装置后分为两部分,一股为总量的1/3去酸气燃烧炉(B61501)与空气鼓风机(J61501)送来的空气一起进行完全燃烧,燃烧后的气体先先于脱盐水换热降温再进入废锅进行余热回收,用来产生0.65MPa低压饱和蒸汽,然后与另一部分气体(总量2/3)混合后温度约为230℃,进入一段换热气(C61502)与来自液硫捕集器(F61501)的低温气体进行换热,这时会有一部分硫冷凝下来,再进入一段的冷凝器(C61503)用低压锅炉给水进一步冷却至160℃左右,使硫继续冷凝通过液硫捕集器(F61501)将硫雾滴捕集后,进入换热器(C61502)将温度升至反应适宜的温度225℃后,进入反应器(B61501)二段进行克劳斯反应,反应后气体经过二段换热器(C61504)与从液硫捕集器(F61502)来的低温气体换热,再经二段冷凝器(C61505)用锅炉水冷却至150℃左右,经液硫捕集器(F61502)分离液硫,由二段换热器(C61504)升温至215℃后进入反应器(B61501)三段再次进行克劳斯反应。
从反应器(B61501)三段出来的气体245℃依次进三段冷凝器(C61506)冷却至150℃和液硫捕集器(F61503)冷凝分离其中的液硫,分离液硫后的尾气由尾气风机(J61503)加压后排往锅炉装置进一步处理。
各级液硫捕集器与换热器冷凝下来的液态硫磺汇入液硫封(F61504)中,正常情况下由液硫封溢流管线CLS-61507溢流至液硫储槽(F61505),再由液硫泵(J61502)送往造粒机(L61501),将液态硫磺用冷却水冷却成固态粒状硫磺作为硫磺产品送出。
液硫流程气相流程2、辅助物料工艺流程六、影响操作的因素1、原料气中H2S含量原料气中H2S含量高可增加硫回收率和降低装置投资。
原料气中H2S含量与硫回收率和投资关系上游脱硫装置有效降低酸气中CO2,对改善克劳斯装置原料气质量非常有利。
2、原料气和过程气中杂质组分含量1)CO2原料气中一般含有CO2,它不仅起稀释作用,也会和H2S在炉反应生成COS、CS2,这两种作用都将导致硫回收率降低。
当原料气中CO2 从3.6%上升至43.5%,随尾气排放的硫量将增加52.2%。