陶瓷烧结炉工艺原理及烧结方式
陶瓷烧结的三个阶段
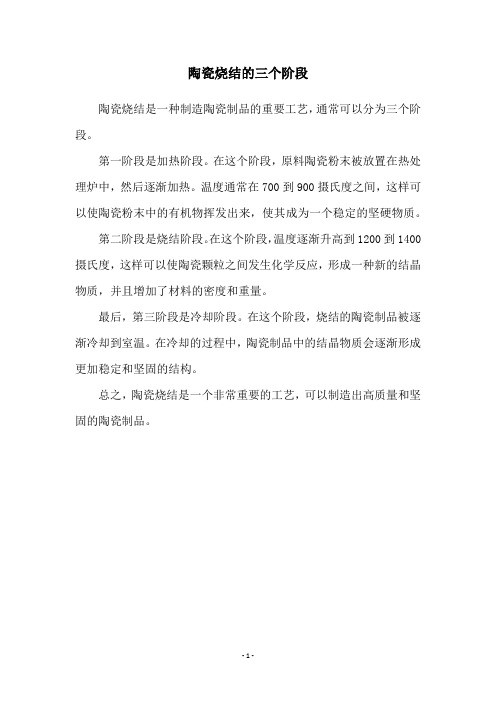
陶瓷烧结的三个阶段
陶瓷烧结是一种制造陶瓷制品的重要工艺,通常可以分为三个阶段。
第一阶段是加热阶段。
在这个阶段,原料陶瓷粉末被放置在热处理炉中,然后逐渐加热。
温度通常在700到900摄氏度之间,这样可以使陶瓷粉末中的有机物挥发出来,使其成为一个稳定的坚硬物质。
第二阶段是烧结阶段。
在这个阶段,温度逐渐升高到1200到1400摄氏度,这样可以使陶瓷颗粒之间发生化学反应,形成一种新的结晶物质,并且增加了材料的密度和重量。
最后,第三阶段是冷却阶段。
在这个阶段,烧结的陶瓷制品被逐渐冷却到室温。
在冷却的过程中,陶瓷制品中的结晶物质会逐渐形成更加稳定和坚固的结构。
总之,陶瓷烧结是一个非常重要的工艺,可以制造出高质量和坚固的陶瓷制品。
- 1 -。
烧结的工艺流程
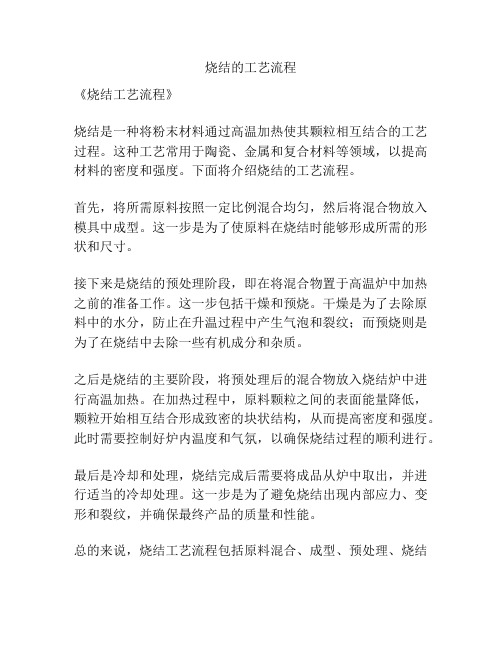
烧结的工艺流程
《烧结工艺流程》
烧结是一种将粉末材料通过高温加热使其颗粒相互结合的工艺过程。
这种工艺常用于陶瓷、金属和复合材料等领域,以提高材料的密度和强度。
下面将介绍烧结的工艺流程。
首先,将所需原料按照一定比例混合均匀,然后将混合物放入模具中成型。
这一步是为了使原料在烧结时能够形成所需的形状和尺寸。
接下来是烧结的预处理阶段,即在将混合物置于高温炉中加热之前的准备工作。
这一步包括干燥和预烧。
干燥是为了去除原料中的水分,防止在升温过程中产生气泡和裂纹;而预烧则是为了在烧结中去除一些有机成分和杂质。
之后是烧结的主要阶段,将预处理后的混合物放入烧结炉中进行高温加热。
在加热过程中,原料颗粒之间的表面能量降低,颗粒开始相互结合形成致密的块状结构,从而提高密度和强度。
此时需要控制好炉内温度和气氛,以确保烧结过程的顺利进行。
最后是冷却和处理,烧结完成后需要将成品从炉中取出,并进行适当的冷却处理。
这一步是为了避免烧结出现内部应力、变形和裂纹,并确保最终产品的质量和性能。
总的来说,烧结工艺流程包括原料混合、成型、预处理、烧结
和冷却处理这几个主要阶段。
通过精确地控制每个环节,可以获得致密、坚固和具有优良性能的烧结制品。
(整理)陶瓷烧成与烧结

7 烧成与烧结7.1 烧成原理为制定合理的煅烧工艺,就必须对物料在烧成时所发生的物理化学变化的类型和规律有深入的了解。
但是物料烧成时的变化较所用的原料单独加热时更为复杂,许多反应是同时进行的。
一般而言,物料的烧成变化首先取决于物料的化学组成,正确的说是物料中的矿物组成。
使用不同的地区的原料,即使物料的化学组成相同,也不能得到完全相同的烧成性质。
其次,物料的烧成变化在很大程度上还取决于物料中各组分的物理状态,即粉碎细度、混合的均匀程度、物料的致密度等,因为物料的烧成是属于液相参与的烧结过程,因此物料的分散性和各组分的接触的密切程度直接影响固相反应、液相的生成和晶体的形成。
此外,烧成温度、时间和气氛条件对物料的烧成变化影响也很大。
要将这些复杂的因素在物料烧成过程中的变化上反映出来是困难的。
为研究方便本书以长石质陶瓷坯体为例进行讨论。
7.1.1 陶瓷坯体在烧成过程中的物理化学变化陶瓷坯体在烧成过程中一般经过低温阶段、氧化分解阶段和高温阶段。
1.低温阶段(由室温~300℃)坯料在窑内进行烧成时,首先是排除在干燥过程中尚未除去的残余水分。
这些残余水分主要是吸附水和少量的游离水,其量约为2~5%。
随着水分排除固体颗粒紧密靠拢,发生少量的收缩。
但这种收缩并不能完全填补水分所遗留的空间,因此物料的强度和气孔率都相应的增加。
在120~140℃之前,由于坯体内颗粒间尚有一定的孔隙,水分可以自由排出,可以迅速升温,随着温度进一步提高,坯体中毛细管逐渐变小,坯体内汽化加剧,使得开裂倾向增大。
例如,当加热至120℃时,一克水占有的水蒸气容积为:22.4×(1+120/273)/18=1.79(升)。
如果坯体中含有4~5%的游离水,则100克坯体的水蒸气体积达7.16--8.95升,相当于坯体体积的155倍。
这些水蒸气主要由坯体的边角部位排出。
为了保证水分排出不致使坯体开裂,在此阶段应注意均匀升温,速度要慢(大制品30℃/时,中小制品50~60℃/时),尤其是厚度和形状复杂的坯体更应注意。
陶瓷膜的烧结原理
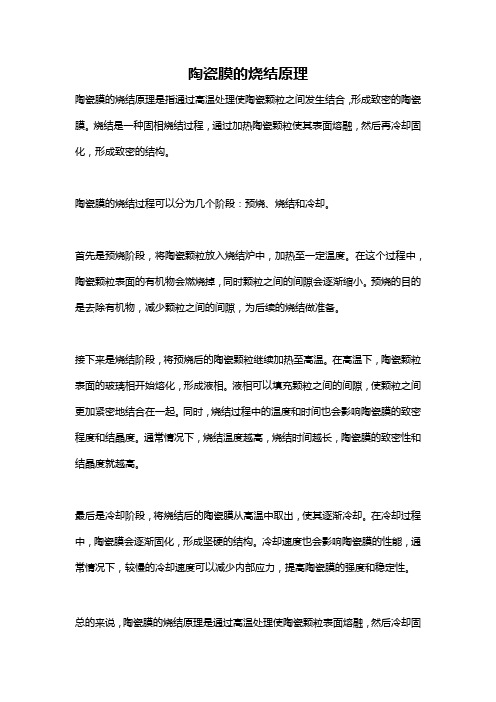
陶瓷膜的烧结原理
陶瓷膜的烧结原理是指通过高温处理使陶瓷颗粒之间发生结合,形成致密的陶瓷膜。
烧结是一种固相烧结过程,通过加热陶瓷颗粒使其表面熔融,然后再冷却固化,形成致密的结构。
陶瓷膜的烧结过程可以分为几个阶段:预烧、烧结和冷却。
首先是预烧阶段,将陶瓷颗粒放入烧结炉中,加热至一定温度。
在这个过程中,陶瓷颗粒表面的有机物会燃烧掉,同时颗粒之间的间隙会逐渐缩小。
预烧的目的是去除有机物,减少颗粒之间的间隙,为后续的烧结做准备。
接下来是烧结阶段,将预烧后的陶瓷颗粒继续加热至高温。
在高温下,陶瓷颗粒表面的玻璃相开始熔化,形成液相。
液相可以填充颗粒之间的间隙,使颗粒之间更加紧密地结合在一起。
同时,烧结过程中的温度和时间也会影响陶瓷膜的致密程度和结晶度。
通常情况下,烧结温度越高,烧结时间越长,陶瓷膜的致密性和结晶度就越高。
最后是冷却阶段,将烧结后的陶瓷膜从高温中取出,使其逐渐冷却。
在冷却过程中,陶瓷膜会逐渐固化,形成坚硬的结构。
冷却速度也会影响陶瓷膜的性能,通常情况下,较慢的冷却速度可以减少内部应力,提高陶瓷膜的强度和稳定性。
总的来说,陶瓷膜的烧结原理是通过高温处理使陶瓷颗粒表面熔融,然后冷却固
化,形成致密的陶瓷膜。
烧结过程中的温度、时间和冷却速度等因素都会影响陶瓷膜的性能。
陶瓷膜的烧结原理在陶瓷材料的制备中具有重要的意义,可以用于制备各种功能性陶瓷膜,如过滤膜、分离膜和传感器等。
材料学中的陶瓷材料烧结工艺
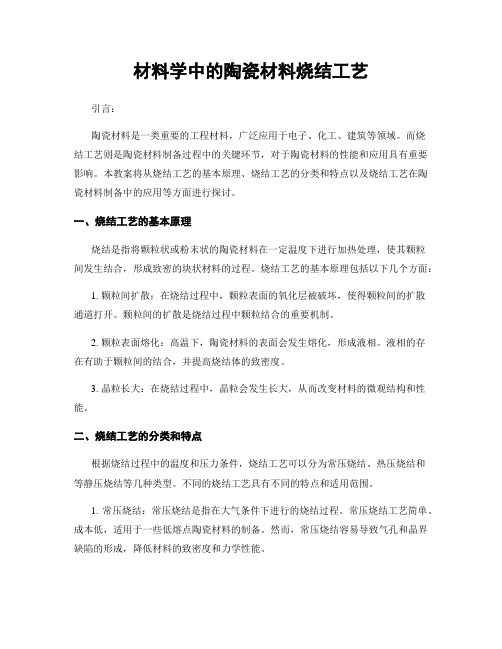
材料学中的陶瓷材料烧结工艺引言:陶瓷材料是一类重要的工程材料,广泛应用于电子、化工、建筑等领域。
而烧结工艺则是陶瓷材料制备过程中的关键环节,对于陶瓷材料的性能和应用具有重要影响。
本教案将从烧结工艺的基本原理、烧结工艺的分类和特点以及烧结工艺在陶瓷材料制备中的应用等方面进行探讨。
一、烧结工艺的基本原理烧结是指将颗粒状或粉末状的陶瓷材料在一定温度下进行加热处理,使其颗粒间发生结合,形成致密的块状材料的过程。
烧结工艺的基本原理包括以下几个方面:1. 颗粒间扩散:在烧结过程中,颗粒表面的氧化层被破坏,使得颗粒间的扩散通道打开。
颗粒间的扩散是烧结过程中颗粒结合的重要机制。
2. 颗粒表面熔化:高温下,陶瓷材料的表面会发生熔化,形成液相。
液相的存在有助于颗粒间的结合,并提高烧结体的致密度。
3. 晶粒长大:在烧结过程中,晶粒会发生长大,从而改变材料的微观结构和性能。
二、烧结工艺的分类和特点根据烧结过程中的温度和压力条件,烧结工艺可以分为常压烧结、热压烧结和等静压烧结等几种类型。
不同的烧结工艺具有不同的特点和适用范围。
1. 常压烧结:常压烧结是指在大气条件下进行的烧结过程。
常压烧结工艺简单、成本低,适用于一些低熔点陶瓷材料的制备。
然而,常压烧结容易导致气孔和晶界缺陷的形成,降低材料的致密度和力学性能。
2. 热压烧结:热压烧结是在高温和压力条件下进行的烧结过程。
热压烧结可以提高材料的致密度和力学性能,减少气孔和晶界缺陷的形成。
然而,热压烧结工艺复杂、设备要求高,适用范围有限。
3. 等静压烧结:等静压烧结是指在高温和等静压条件下进行的烧结过程。
等静压烧结可以提高材料的致密度和力学性能,且适用范围广。
然而,等静压烧结工艺对设备要求高,操作复杂。
三、烧结工艺在陶瓷材料制备中的应用烧结工艺在陶瓷材料制备中具有广泛的应用,下面将从几个方面进行论述。
1. 陶瓷材料的制备:烧结工艺是制备陶瓷材料的重要方法之一。
通过烧结工艺,可以将陶瓷粉末烧结成致密的块状材料,从而改变材料的微观结构和性能。
陶瓷闪烧炉原理

陶瓷闪烧炉原理陶瓷闪烧炉是一种用于制造陶瓷制品的烧结设备,其原理是通过高温加热使陶瓷原料发生化学反应,从而实现陶瓷制品的烧结。
陶瓷闪烧炉主要由炉体、加热装置、控温系统和排气系统等部分组成。
其中,炉体是陶瓷闪烧炉的主体结构,负责容纳和加热陶瓷原料。
加热装置通常采用电阻加热器或燃烧器等形式,通过加热使炉内温度达到所需的高温。
控温系统则用于监测和控制炉内温度,确保烧结过程的稳定性和精确性。
排气系统则用于排除炉内产生的废气和烟尘,保证炉内环境的清洁与安全。
在陶瓷闪烧炉中,陶瓷原料通常是由粉末状的氧化物、碳酸盐或氮化物等组成。
烧结过程中,这些原料在高温下发生化学反应,形成陶瓷晶体结构,从而实现陶瓷制品的烧结。
烧结过程主要包括三个阶段:加热阶段、烧结阶段和冷却阶段。
在加热阶段,陶瓷原料被加热至高温,使其达到烧结温度。
在烧结阶段,原料开始熔化并形成液相,溶解并重新结晶,从而使陶瓷晶体结构形成和增长。
在冷却阶段,炉内温度逐渐下降,陶瓷制品逐渐冷却固化。
陶瓷闪烧炉的原理是利用高温加热使陶瓷原料发生物理和化学变化,从而实现陶瓷制品的烧结。
在烧结过程中,陶瓷原料的颗粒间相互结合,形成致密的陶瓷晶体结构,从而赋予陶瓷制品优良的物理和化学性质。
陶瓷闪烧炉的原理是基于热力学和反应动力学的基础上。
热力学研究了物质在不同温度和压力下的物性和能量变化规律,而反应动力学研究了物质在化学反应中的速率和机理。
陶瓷闪烧炉的原理还可以通过材料的热膨胀系数来解释。
热膨胀系数是材料在温度变化时长度或体积的变化率。
在陶瓷闪烧炉中,陶瓷原料的热膨胀系数与温度密切相关。
当温度升高时,陶瓷原料的热膨胀系数增大,颗粒间的间隙减小,从而促进颗粒的结合和烧结。
陶瓷闪烧炉是一种利用高温加热使陶瓷原料发生化学反应的设备。
它通过控制炉内温度和烧结过程,使陶瓷原料的颗粒结合形成致密的陶瓷晶体结构,从而实现陶瓷制品的烧结。
陶瓷闪烧炉的原理基于热力学和反应动力学的研究,以及材料的热膨胀系数的变化。
烧结工艺知识点总结大全

烧结工艺知识点总结大全一、烧结原理1. 烧结是指将粉末材料在一定温度下加热,使其颗粒间发生结合,形成致密的块状产品。
烧结的基本原理是固相扩散,即热力学上的固相之间的扩散过程。
2. 烧结过程中主要有三种力学过程,分别为颗粒间的原子扩散、颗粒间的表面扩散和颗粒间的体扩散。
这三种扩散方式相互作用,共同促进颗粒间发生结合。
3. 烧结过程中温度、时间和压力是影响烧结效果的重要因素。
通过控制这些参数,可以使烧结过程更加均匀和有效。
二、烧结设备1. 烧结设备主要包括热处理炉、烧结炉、烧结机等。
不同的烧结设备适用于不同的烧结材料和工艺要求。
2. 烧结设备的主要部件包括燃烧室、加热炉、炉膛、热风循环系统、控制系统等。
这些部件共同作用,实现对粉末材料的加热和烧结作用。
3. 热处理炉是常见的烧结设备之一,主要通过电阻加热、气体燃烧等方式对粉末材料进行加热处理,适用于各种金属和非金属材料的烧结工艺。
三、烧结工艺控制1. 烧结工艺控制是烧结过程中的关键环节,可以通过控制温度、时间、压力等参数,实现对烧结过程的精确控制。
2. 烧结工艺控制的主要方法包括PID控制、自适应控制、模糊控制等。
这些控制方法通过对烧结过程中的各个参数进行实时监测和调整,以实现对烧结过程的精确控制。
3. 在实际生产中,烧结工艺控制可以通过计算机控制系统实现自动化,提高生产效率和产品质量。
四、烧结材料选型1. 烧结工艺适用于各种粉末材料,包括金属粉末、陶瓷粉末、粉末冶金材料等。
根据不同的材料性质和要求,选择合适的烧结工艺和设备。
2. 烧结材料的选型考虑因素包括原料种类、粒度、成分、形状等。
根据不同的要求,选择合适的烧结材料,可以有效提高产品质量和生产效率。
3. 在烧结材料选型过程中,也需要考虑成本、资源利用率和环境保护等方面的因素,以实现经济、环保和可持续发展。
五、烧结工艺的应用1. 烧结工艺广泛应用于金属、陶瓷、粉末冶金、电子材料等行业。
在金属制品生产中,烧结工艺可以用于制造各种粉末冶金制品、焊接材料、钎焊材料等。
陶瓷材料的烧结机理分析

陶瓷材料的烧结机理分析陶瓷材料是一种广泛应用于建筑、医疗、电子等领域的重要材料。
而其中的烧结过程是陶瓷材料制备中至关重要的步骤之一。
了解陶瓷材料的烧结机理,对于提高陶瓷制品的品质和性能具有重要意义。
1. 烧结过程的定义和意义烧结是指在高温条件下,将陶瓷粉体进行加热处理,使其颗粒相互结合,形成致密的陶瓷坯体的过程。
烧结过程可以消除颗粒间的空隙,通过界面扩散促进结晶生长,同时改善材料的物理性能和化学稳定性。
2. 烧结机理的基本原理烧结机理包括颗粒间的物理和化学变化。
在烧结过程中,陶瓷粉体受热后,其表面发生熔化,形成初熔液相。
然后,颗粒间通过表面张力作用力,逐渐减小间隙,相互融合。
同时,陶瓷粉体中的固相反应也会发生,导致晶体生长和晶界形成。
3. 影响烧结过程的因素烧结过程受到多种因素的影响,包括温度、时间、气氛和成分等。
首先,适宜的烧结温度是实现优质陶瓷制品的关键。
过高的温度可能导致烧结体发生融化,而过低的温度则会影响颗粒间的结合。
其次,烧结时间也会对材料的烧结效果产生影响。
适当延长烧结时间可以增强晶粒的生长和结合,但过长的时间则可能导致晶界生长过大和晶粒增长不均匀。
此外,气氛对陶瓷烧结的效果也有着重要作用。
常用的气氛有氧气气氛、氮气气氛和氢气气氛等,不同气氛下的烧结机理和效果也不同。
最后,陶瓷材料的成分和添加剂也会对烧结过程和机理产生影响。
不同的材料配比和添加剂种类和含量会对烧结后的结构和性能产生显著差异。
4. 烧结机理的应用烧结机理的深入了解可以帮助优化陶瓷材料的烧结过程,提高产品的质量和性能。
在陶瓷制备的实践中,可以调控烧结温度、时间和气氛,优化材料的成分配比,以实现理想的烧结效果。
此外,还可以通过添加剂的引入,改变材料的结构和特性,进一步提升陶瓷制品的综合性能。
总结:陶瓷材料的烧结机理是制备高性能陶瓷制品的关键环节。
通过对烧结过程的认知和理解,可以优化烧结条件,提高产品的质量和性能。
烧结温度、时间、气氛以及材料的成分和添加剂等都是影响烧结机理的重要因素。
- 1、下载文档前请自行甄别文档内容的完整性,平台不提供额外的编辑、内容补充、找答案等附加服务。
- 2、"仅部分预览"的文档,不可在线预览部分如存在完整性等问题,可反馈申请退款(可完整预览的文档不适用该条件!)。
- 3、如文档侵犯您的权益,请联系客服反馈,我们会尽快为您处理(人工客服工作时间:9:00-18:30)。
陶瓷烧结炉工艺原理及烧结方式
陶瓷烧结是指坯体在高温下致密化过程和现象的总称。
随着温度升高,陶瓷坯体中具有比表面大,表面能较高的粉粒,力图向降低表面能的方向变化,不断进行物质迁移,晶界随之移动,气孔逐步排除,产生收缩,使坯体成为具有一定强度的致密的瓷体。
烧结的推动力为表面能。
烧结可分为有液相参加的烧结和纯固相烧结两类。
烧结过程对陶瓷生产具有很重要的意义。
为降低烧结温度,扩大烧成范围,通常加入一些添加物作助熔剂,形成少量液相,促进烧结。
一般粗线条结炉的燃烧方法主要有以下几种:
热压烧结、热等静压、放电等离子烧结、微波烧结、反应烧结、爆炸烧结。
固相烧结一般可表现为三个阶段,初始阶段,主要表现为颗粒形状改变;中间阶段,主要表现为气孔形状改变;最终阶段,主要表现为气孔尺寸减小。
烧结是在热工设备中进行的,这里热工设备指的是先进陶瓷生产窑炉及附属设备。
烧结陶瓷的窑炉类型很多,同一制品可以在不同类型的窑内烧成,同一种窑也可以烧结不同的制品。
主要常用的有间歇式窑炉,连续式窑炉和辅助设备。
间歇式窑炉按其功能可分为电炉,高温倒焰窑,梭式窑和钟罩窑。
连续式窑炉的分类方法有很多种,按制品的输送方式可分为隧道窑,高温推板窑和辊道窑。
与传统间歇式窑炉相比较,连续式窑具有连续操作性,易实现机械化,大大改善了劳动条件和减轻了
劳动强度,降低了能耗等优点。
温度制度的确定,包括升温速度,烧成温度,保温时间和冷却速度等参数。
通过飞行坯料在烧成过程中性状变化,初步得出坯体在各温度或时间阶段可以允许的升、降温速度(相图,差热-失重、热膨胀、高温相分析、已有烧结曲线等)。
升温速度:低温阶段,氧化分解阶段,高温阶段。
烧成温度与保温时间:相互制约,可在一定程度上相互补偿,以一次晶粒发展成熟,晶界明显、没有显著的二次晶粒长大,收缩均匀,致密而又耗能少为目的。
冷却速度,随炉冷却,快速冷却。
压力制度的确定,压力制度起着保证温度和气氛制度的作用。
全窑的压力分布根据窑内结构,燃烧种类,制品特性,烧成气氛和装窑密度等因素来确定。
倒焰窑中,最重要的是在烟道内形成微负压,窑底处于零压。
隧道窑的预热带和烧成带都为负压,冷却带一般在正压下操作。