太阳能光伏组件工艺流程
光伏组件生产工艺

光伏组件生产工艺光伏组件生产是指通过一系列工艺步骤,将太阳能电池片、玻璃、背板等材料组装在一起,制成太阳能电池板的过程。
下面详细介绍光伏组件生产工艺:1. 制备太阳能电池片:首先,通过硅块或硅粉制备出多晶硅材料。
然后,将多晶硅材料加热熔化,在石墨模具中进行结晶,形成多晶硅棒。
接着,将多晶硅棒切片成较薄的硅片,即太阳能电池片。
2. 表面处理:对太阳能电池片的表面进行处理,以增加电池片的光吸收能力和电荷收集效率。
通常采用酸洗、气相沉积、蚀刻等工艺。
3. 电场加速老化:通过将太阳能电池片置于电场中,模拟气候环境,进行加速老化测试,评估电池片的质量和稳定性。
4. 备注和分选:对电池片进行视觉检查,发现外观缺陷或缺陷,进行标注并进行分类。
5. 背板生产:背板是太阳能电池板的支撑材料,通常采用铝合金、钢板等材料制成。
通过剪切、冲压、折弯等工艺处理,制备出合适尺寸和形状的背板。
6. 清洗:将太阳能电池片、玻璃等材料进行清洗,去除杂质和污染物,以确保组件的质量和效率。
7. 组件组装:将太阳能电池片、玻璃、背板等材料组装在一起。
首先,将太阳能电池片固定在玻璃上,通常使用胶水或硅胶进行粘合。
然后,将背板固定在玻璃背面,形成一个完整的太阳能电池板。
8. 背板密封:将太阳能电池板进行密封,以防止湿气和灰尘进入,并增加电池板的稳定性和耐久性。
9. 电池板测试:对组装好的太阳能电池板进行电气性能测试和外观检查,确保组件的质量和效果。
10. 包装:对通过测试的太阳能电池板进行包装,以保护其不受损坏或污染。
以上就是光伏组件生产的工艺流程。
随着技术的不断发展,光伏组件生产工艺也在不断改进,以提高效率和质量,同时降低成本。
光伏电池组件生产工艺

光伏电池组件生产工艺
光伏电池组件生产工艺是将硅片、玻璃、铝框等材料通过一系列工艺流程加工成光伏电池组件,用于太阳能发电。
下面以常规硅基光伏电池为例,分步骤阐述其生产工艺。
1. 硅片切割:先将硅棒切成薄片,然后采用线切割技术将硅片切成150-200微米厚的晶片。
这一步是整个工艺流程的起点。
2. 体液深度腐蚀:将硅片浸泡在碱性液体中,利用化学反应将硅片表面的极薄氧化层和部分硅材料腐蚀掉,形成较深的反向电场。
3. 清洗与蚀刻:经过深度腐蚀后,用酸性液体将硅片表面的微小瑕疵清洗掉,再蚀刻一层透明氧化硅。
4. 消光排笔:用液态聚合物在硅片的上下两个金属电极之间涂一层厚度约为25微米的消光层,以减少电极反射而影响电池效率。
5. 金属化:将铜、铝等金属蒸镀在消光排笔上,形成上下两个电极。
上铝下铜为常规电池的铺设方式,这一步完成后形成的晶体管就是PN结。
6. 切割、选级和分装:将硅片切割成多个电池,不同电池在制造过程中,由于材料、设备等方面的原因,也可能出现不同级别的电池,此时要进行筛选,将同一级别的电池分装装配并进行电学特性测量。
7. 等离子体清洗:为了去除硅片表面的杂质,提高器件性能,需要在高温、低压等条件下使用等离子体清洗法,清除氧化物和其他杂质。
8. 包装和组装:最后将生产的电池安装在玻璃上,用透明胶粘合在铝框上。
平板太阳能电池组件由多个电池板拼接而成,通常为36个或72个板拼接而成。
本文所述的光伏电池组件生产工艺中,每一步都需要准确的技术参数和工艺条件,以确保电池的品质,最终达到预期的发电效果。
同
时,这也反映了光伏电池、太阳能等新能源产业对于技术的要求是有多高的。
太阳能光伏组件工艺流程

太阳能光伏组件工艺流程1.硅料准备:太阳能光伏组件的主要材料是硅,硅料准备是工艺流程的第一步。
硅料一般以高纯度多晶硅为主,通过与氢气反应生成氯化硅,再经过还原反应制得硅气。
硅气被冷凝成小颗粒或棒状,然后经过冶炼、熔炼等工艺步骤得到硅锭。
2.硅片生产:硅锭通过切割机切割成硅片。
硅片表面进行化学抛光,去除氧化层和其他杂质,然后通过酸处理,利用等离子刻蚀技术去除表面残留的氧化层,得到表面光亮的硅片。
3.电池片生产:硅片经过磷掺杂、扩散、蚀刻、电极印制和器件隔离等工艺步骤形成太阳能电池片。
首先,在硅片表面喷涂磷酸二氢铵溶液,然后进行扩散烧结过程,通过高温高压的条件,使磷元素在硅片中扩散形成n型硅片,形成p-n结。
然后,在硅片正负两侧分别印刷上导电铝和导电银电极,通过层层烧结、蚀刻等工艺步骤,形成电池片的正负电极和器件隔离结构。
4.组件加工:电池片经过磨边、打孔、清洗等加工步骤,形成太阳能光伏组件。
首先,对电池片进行磨边处理,去除边缘毛刺和表面缺陷。
然后,在组件上打孔,以便后续的组件的串并联。
最后,通过喷水或者超声波清洗等工艺步骤,去除表面的杂质和污染物,使电池片表面干净。
5.测试:组件加工完成后,需要进行测试,以确保其质量和性能。
测试包括外观检查、电气特性测试等。
外观检查主要检查组件外观是否完整,有无破损、刮花等缺陷。
电气特性测试主要测试组件的开路电压、短路电流、最大功率等关键指标,评估组件的性能。
6.封装:测试合格的组件需要进行封装,以保护其内部电池片免受环境的损害。
常见的封装方式有玻璃封装和背板封装。
玻璃封装是将组件表面覆盖一层透明玻璃,利用背单面多层复合材料将电池片与后面的材料粘合在一起。
背板封装则是将组件背面用背板封住,并加入密封胶进行固定,使电池片与背板紧密连接。
以上就是太阳能光伏组件工艺流程的简要介绍,从硅料准备到最终的封装,每个步骤都十分重要。
这些步骤的精确操作和质量控制,直接影响太阳能光伏组件的性能和可靠性。
太阳能光伏组件生产流程
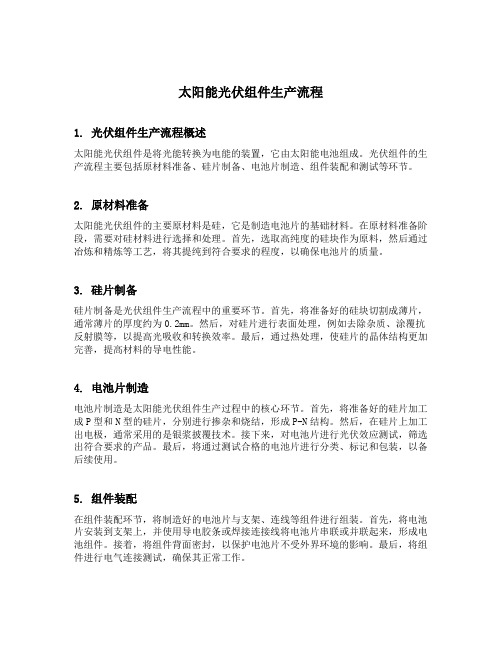
太阳能光伏组件生产流程1. 光伏组件生产流程概述太阳能光伏组件是将光能转换为电能的装置,它由太阳能电池组成。
光伏组件的生产流程主要包括原材料准备、硅片制备、电池片制造、组件装配和测试等环节。
2. 原材料准备太阳能光伏组件的主要原材料是硅,它是制造电池片的基础材料。
在原材料准备阶段,需要对硅材料进行选择和处理。
首先,选取高纯度的硅块作为原料,然后通过冶炼和精炼等工艺,将其提纯到符合要求的程度,以确保电池片的质量。
3. 硅片制备硅片制备是光伏组件生产流程中的重要环节。
首先,将准备好的硅块切割成薄片,通常薄片的厚度约为0.2mm。
然后,对硅片进行表面处理,例如去除杂质、涂覆抗反射膜等,以提高光吸收和转换效率。
最后,通过热处理,使硅片的晶体结构更加完善,提高材料的导电性能。
4. 电池片制造电池片制造是太阳能光伏组件生产过程中的核心环节。
首先,将准备好的硅片加工成P型和N型的硅片,分别进行掺杂和烧结,形成P-N结构。
然后,在硅片上加工出电极,通常采用的是银浆披覆技术。
接下来,对电池片进行光伏效应测试,筛选出符合要求的产品。
最后,将通过测试合格的电池片进行分类、标记和包装,以备后续使用。
5. 组件装配在组件装配环节,将制造好的电池片与支架、连线等组件进行组装。
首先,将电池片安装到支架上,并使用导电胶条或焊接连接线将电池片串联或并联起来,形成电池组件。
接着,将组件背面密封,以保护电池片不受外界环境的影响。
最后,将组件进行电气连接测试,确保其正常工作。
6. 组件测试与包装在组件生产流程的最后阶段,对已装配好的组件进行测试和包装。
测试主要包括光电转换效率、电流和电压等性能参数的测量,以验证组件的质量和性能。
同时,还需要对组件进行外观检查,确保无损坏和缺陷。
最后,将测试合格的组件进行包装,以便运输和存储。
结论太阳能光伏组件生产流程包括原材料准备、硅片制备、电池片制造、组件装配和测试等环节。
每个环节都对组件的质量和性能起着重要的作用。
光伏组件的生产工艺流程
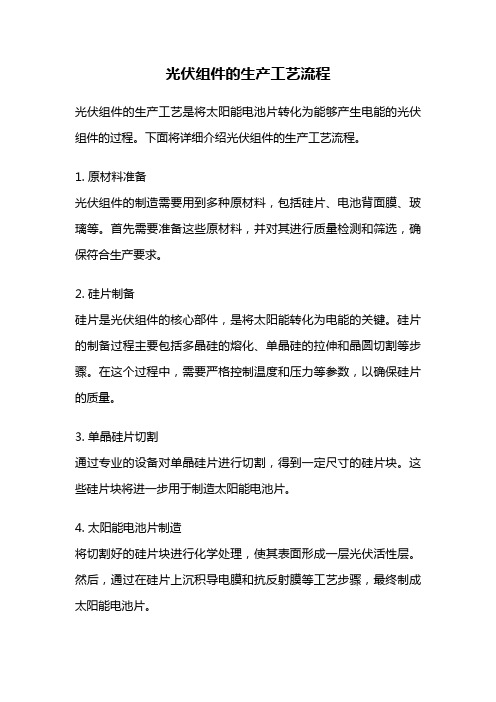
光伏组件的生产工艺流程光伏组件的生产工艺是将太阳能电池片转化为能够产生电能的光伏组件的过程。
下面将详细介绍光伏组件的生产工艺流程。
1. 原材料准备光伏组件的制造需要用到多种原材料,包括硅片、电池背面膜、玻璃等。
首先需要准备这些原材料,并对其进行质量检测和筛选,确保符合生产要求。
2. 硅片制备硅片是光伏组件的核心部件,是将太阳能转化为电能的关键。
硅片的制备过程主要包括多晶硅的熔化、单晶硅的拉伸和晶圆切割等步骤。
在这个过程中,需要严格控制温度和压力等参数,以确保硅片的质量。
3. 单晶硅片切割通过专业的设备对单晶硅片进行切割,得到一定尺寸的硅片块。
这些硅片块将进一步用于制造太阳能电池片。
4. 太阳能电池片制造将切割好的硅片块进行化学处理,使其表面形成一层光伏活性层。
然后,通过在硅片上沉积导电膜和抗反射膜等工艺步骤,最终制成太阳能电池片。
5. 电池片组装将制造好的太阳能电池片进行组装,主要包括电池背面膜的粘贴和电池片的排列等步骤。
这个过程需要严格控制温度和湿度等环境条件,以确保组装的质量和性能。
6. 封装将组装好的电池片放入透明的玻璃和EVA膜中,然后使用专业的设备进行真空封装。
封装的目的是保护电池片免受外界环境的影响,并提高光伏组件的稳定性和耐久性。
7. 检测和质量控制在生产过程的每个环节,都需要进行严格的检测和质量控制。
包括对原材料的检测、生产过程的监控和成品的最终检测等。
只有通过了各项质量检测的光伏组件,才能出厂销售。
8. 成品包装和出厂经过检测合格的光伏组件将进行包装,并贴上相关的标签和说明书。
然后,按照订单要求进行装箱和出厂,准备运往各个客户的地方。
总结:光伏组件的生产工艺流程包括原材料准备、硅片制备、单晶硅片切割、太阳能电池片制造、电池片组装、封装、检测和质量控制、成品包装和出厂等步骤。
这些步骤在整个生产过程中起着至关重要的作用,确保了光伏组件的质量和性能。
通过不断优化和改进工艺流程,可以提高光伏组件的效率和可靠性,推动光伏产业的发展。
光伏组件工艺
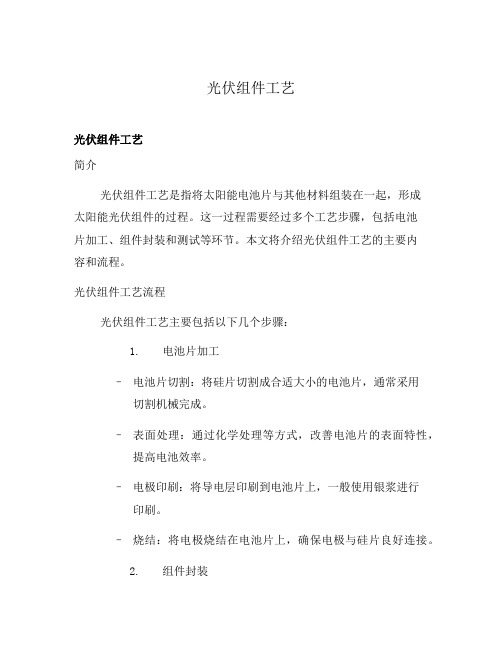
光伏组件工艺光伏组件工艺简介光伏组件工艺是指将太阳能电池片与其他材料组装在一起,形成太阳能光伏组件的过程。
这一过程需要经过多个工艺步骤,包括电池片加工、组件封装和测试等环节。
本文将介绍光伏组件工艺的主要内容和流程。
光伏组件工艺流程光伏组件工艺主要包括以下几个步骤:1.电池片加工–电池片切割:将硅片切割成合适大小的电池片,通常采用切割机械完成。
–表面处理:通过化学处理等方式,改善电池片的表面特性,提高电池效率。
–电极印刷:将导电层印刷到电池片上,一般使用银浆进行印刷。
–烧结:将电极烧结在电池片上,确保电极与硅片良好连接。
2.组件封装–回流焊接:将电池片与封装组件(例如玻璃、EVA膜)固定在一起,采用热加工方法使其连接牢固。
–边框粘接:在组件边框与玻璃之间加入粘合剂,增加组件的强度和密封性。
–排气:在封装组件内注入稀有气体并排出空气,减少氧气和水分对组件的影响。
3.组件测试–输出功率测试:通过光照条件下的测试,测量组件的输出功率和效率。
–绝缘电阻测试:测试组件的绝缘电阻,判断组件的电气安全性能。
–外观检查:检查组件外观是否完好,是否有损坏或缺陷。
前沿技术和挑战光伏组件工艺在不断发展中,出现了一些前沿技术和挑战。
•高效电池片制造技术:提高电池片制造工艺和材料的效率,使光伏组件的转换效率更高。
•新型封装材料:研发具有更好光传递和封装性能的材料,提高光伏组件的性能和寿命。
•工艺自动化:引入自动化设备和智能控制技术,提高工厂生产效率和质量稳定性。
•组件可回收利用:研究光伏组件的回收利用技术,减少废弃组件对环境的影响。
结束语光伏组件工艺是太阳能光伏产业的重要环节,其工艺流程和技术不断发展,推动着光伏产业的进步和创新。
随着科技的进步,相信光伏组件工艺将继续取得突破,为清洁能源的发展做出更大的贡献。
光伏组件生产流程
光伏组件生产流程一、概述光伏组件是太阳能发电的核心部件,其生产流程包括硅片制备、电池片制备和组件制造三个过程。
本文将详细介绍光伏组件生产流程。
二、硅片制备1. 硅原料准备硅原料通常采用高纯度石英矿石,经过选矿、粉碎、洗涤等工艺处理,得到高纯度的硅金属。
2. 炉内反应将硅金属投入到电弧炉中进行加热,同时向其中加入氢气,使其发生化学反应生成氯化硅。
反应后的氯化硅经过冷却结晶得到多晶硅块。
3. 晶棒拉制将多晶硅块放入拉棒机中进行加热,在拉棒机中形成一个小孔,并通过旋转和上下拉伸的方式逐渐拉长形成单晶硅棒。
4. 切割将单晶硅棒切割成薄片,即所谓的“切片”,并进行表面抛光处理,以便后续工艺处理。
三、电池片制备1. 清洗对表面抛光处理后的硅片进行清洗,以去除表面的杂质和污染物。
2. 磷掺杂将硅片放入扩散炉中进行加热,并向其中加入磷酸二氢钠等掺杂剂,使其在硅片表面形成一层掺杂层。
3. 金属化在电池片表面涂上金属膜,通常采用铝或银等金属。
4. 刻蚀通过光刻技术将电池片表面的金属膜进行刻蚀,形成电极。
5. 焊接将两个电极焊接在一起,形成电池片。
四、组件制造1. 清洗对电池片进行清洗处理,以去除表面的杂质和污染物。
2. 封装将电池片放置在透明的聚合物基板上,并用胶水或其他粘合剂固定。
然后在基板上涂覆一层聚合物保护膜,形成太阳能电池组件。
3. 测试对太阳能电池组件进行测试,检测其输出功率、效率等性能指标是否符合要求。
4. 包装对测试合格的太阳能电池组件进行包装,通常采用纸箱或木箱等方式进行包装,以保护其在运输过程中不受损坏。
五、总结以上就是光伏组件生产流程的详细介绍。
整个生产过程需要严格的质量控制和检测,以确保最终产品的性能和质量。
随着太阳能技术的不断发展和成熟,光伏组件生产将会越来越普及和广泛应用。
太阳能电池组件生产的主要工艺流程
太阳能电池组件生产的主要工艺流程:测试分选→单片焊接→串联焊接→叠层→中间测试→层压→装框注胶→清洗→最终测试(1)测试分选电池片分选主要是为了检出不合格的电池片,同时,电池片的颜色一般呈蓝褐色、蓝紫色、蓝色、浅兰色等几种不同档次的蓝色,对电池片进行颜色分选并分档放置,保证单个组件所用到的电池片为同档次的颜色,从而使单个组件生产出来后颜色外观美观,各电池单片之间无明显色差现象。
若电池片不经过色差分选就直接做组件,做出来的组件外表颜色“参差不齐”,不美观。
因此,为了保证电池片的质量、外观和生产顺利高效率的运行,通过初选将缺角、栅线印刷不良、裂片、色差等电池片筛选出来。
在标准测试环境(温度25±2℃、湿度≤60%RH、光强1000±50W)下,绘制I-V曲线图,根据电池片的开路电压Voc、短路电流Isc、工作最佳功率Pm、工作最佳电压Vm、工作最佳电流Im、填充因子FF、转换效率n等指标把电池电性参数相近的电池分到一类,之后根据生产、工艺的数据分析要求,和客户的分档要求,对电池片进行测试并分档。
(2)单片焊接单片焊接将汇流带焊接到电池正面(负极)的主栅线上,从上至下,匀速焊接。
单片焊接的目的是将连接带(锡铜合金带)平直地焊接到电池片的主栅线上,要求保证电气和机械连接良好,外观光亮;焊带的长度约为电池边长的2倍,多出的焊带在串联焊接时与后面的电池片的背面电极相连。
(3)串联焊接背面焊接是将电池片接在一起形成一个电池片的串组,电池的定位主要靠一个膜具板,上面有放置电池片的凹槽,槽的大小和电池的大小相对应,槽的位置已经是设计好的,不同规格的组件使用不同的模板,操作者使用电烙铁和连接带(锡铜合金带)将单片焊接好的电池片的正面电极(负极)焊接到另一片的背面电极(正极)上,以此类推,依次将电池片串接在一起,并在组件串的正负极焊接出为叠层时准备的引线。
(4)叠层背面串接好且经过检验合格后,将电池片串、钢化玻璃和切割好的EVA 、背板(TPT)按照一定的层次敷设好,玻璃事先涂一层试剂(primer)以增加玻璃和EVA的粘接强度。
太阳能光伏组件工艺流程
EVA
—准备组—
太阳能光伏组件工艺流程
13
● TPT/TPE/背板
❖ 特性:能很好的与空气隔绝 ;极好的抗 氧化和抗潮湿性;能长期防止粘合剂的 水解;具有良好的电绝缘性能;和EVA的 完美结合。
❖ 常见缺陷:破损、污渍、折痕、脱层 、穿孔等。
TPT
—准备组—
太阳能光伏组件工艺流程
14
★具体裁切动作视频
8
具体分选动作视频
点击鼠标左键 或点右键”播放 影片”。
—分太选阳能组光—伏组件工艺流程
9
★具体分选作业视频
太阳能光伏组件工艺流程
分选过程中常见问题
● 操作不当: ❖ 取放电池片不规范,造成电池片破损、脏污
❖ 违反工艺操作将电池片裸露在外,造成电池片氧化、发黄
● 防护措施不当: ❖ 未戴指套、指套破损或没有及时更换指套,汗渍、指纹印在 电池片上,无法祛除。
❖ 特性:除去焊接金属表面的氧化膜,在焊接物表面形成液态的保 护模,在焊接的瞬间,可以将熔融的焊锡取代,并顺和完成焊接
—准备组—
太阳能光伏组件工艺流程
★烘焊带动作视频
—准备组—
太阳能光伏组件工艺流程
操作过程中常见问题
● 裁剪尺寸不对: ❖ 尺寸偏短,物料无法使用 ❖ 尺寸偏长,物料浪费
● 防护措施不当: ❖ 裁剪EVA和TPT/TPE/背板时,不戴防静电手套,手上的污渍、 汗渍易粘在上面,较难清除。 ❖ 焊带浸泡烘干时,要带好防护。 ❖ 裁切焊带和焊接汇流条时要戴好手指套。
❖ 常见缺陷:蛇形弯、表面颗粒、涂锡不均等。
—准备组—
太阳能光伏组件工艺流程
12
● EVA
❖ 常用的EVA胶膜种类: 1)快速固化EVA 2)慢速固化EVA
太阳能光伏组件制作工序流程
太阳能光伏组件制作工序流程下载温馨提示:该文档是我店铺精心编制而成,希望大家下载以后,能够帮助大家解决实际的问题。
文档下载后可定制随意修改,请根据实际需要进行相应的调整和使用,谢谢!并且,本店铺为大家提供各种各样类型的实用资料,如教育随笔、日记赏析、句子摘抄、古诗大全、经典美文、话题作文、工作总结、词语解析、文案摘录、其他资料等等,如想了解不同资料格式和写法,敬请关注!Download tips: This document is carefully compiled by theeditor. I hope that after you download them,they can help yousolve practical problems. The document can be customized andmodified after downloading,please adjust and use it according toactual needs, thank you!In addition, our shop provides you with various types ofpractical materials,such as educational essays, diaryappreciation,sentence excerpts,ancient poems,classic articles,topic composition,work summary,word parsing,copy excerpts,other materials and so on,want to know different data formats andwriting methods,please pay attention!太阳能光伏组件,也称为太阳能电池板,是将太阳光能转换为电能的重要设备。
- 1、下载文档前请自行甄别文档内容的完整性,平台不提供额外的编辑、内容补充、找答案等附加服务。
- 2、"仅部分预览"的文档,不可在线预览部分如存在完整性等问题,可反馈申请退款(可完整预览的文档不适用该条件!)。
- 3、如文档侵犯您的权益,请联系客服反馈,我们会尽快为您处理(人工客服工作时间:9:00-18:30)。
红绿灯
路灯 10KW电站
皮包
手电
3
一、太阳能电池组件
太阳能电池组件
通过特殊工艺,将太阳电池片、正面盖板、背板封装成一个整体,
从而构成一个实用的太阳能发电器件,我们称其为组件或太阳能组件
。它的功能是将光能转换为电能。
4
二、工艺流程
组件工艺流程图 Out Technological Process Chart
14
三、主要材料介绍
常见膜层结构
简称 PVF PVDF ECTFE
THV
化学名 聚氟乙烯(Tedlar)
分子结构式 -(CH2-CHF)n-
聚偏氟乙烯
-(CH2-CF2)n-
三氟氯乙烯-乙烯共聚物
四氟乙烯-六氟丙烯-偏氟乙烯 共聚物(THV)
-(CH2-CH2)n-(CFClCF2)m-
-(CF2-CF2)n-(CF (CF3)-CF2)m(CH2-CF2)o-
3.2 EVA
EVA是乙烯-醋酸乙烯酯共聚物,它是由乙烯(E)和 乙酸乙烯(VA)共聚而制得,英文名称为:Ethylene Vinyl Acetate,简称为EVA。一般来说,EVA树脂的性能 主要取决于分子链上乙酸乙烯的含量。因构成组分比例可 调从而符合不同的应用需要,乙酸乙烯(VA content)的 含量越高,其透明度,柔软度及坚韧度会相对提高。
国内最先进的全自动组件流水线。先进的设备和严格的检验是组件质量的保障。 5
三、主要材料介绍 3.1 焊带 光伏组件焊接过程中的重要原材料,焊带质量的好坏将直接影响到光 伏组件电流的收集效率,对光伏组件的功率影响很大。 常见的包装方式:轴式、盘式。
常见缺陷:蛇形弯、表面颗粒、涂锡不均等。
12
三、主要材料介绍
2)脱层 发生脱层的原因可能有:
(1)EVA在长期自然条件(空气,湿气)等的作用下粘合力慢慢地降低; (2)层压工艺控制不好,使EVA的交联度没有控制在一个比较合理的范围内(一般认为 是75%-85%),EVA的弹性受到影响。
脱层不但会影响组件的外观,而且脱层光学的损失增加,从而影响组件的效率。另外 脱层发生在组件的边缘时,EVA会迅速氧化。
太阳能光伏组件工艺流程
中节能太阳能科技(镇江)有限公司 2016年8月
聚合点滴 创生无限 Going Green, Investing Green
www. cecep. cn
一、太阳能电池组件
太阳能是洁净、可再生能源,是传统化石能源最为重要的替代能源之一。开发 利用太阳能已成为世界上许多国家可持续发展的重要战略决策。
被采用的背板品牌 Isovolta、SFC、 Krempel、台虹
东洋铝业、Krempel
Honeywell
3M
四、我们的优势
4.1 优质的原材料供应
采用业内知名厂商的原材、高附加值
电池片:防PID电池片(自产、外购),有效降低电池片衰减异常产生;
背板:伊索、台虹 TPT TPE TPO TPA TPCW 耐候、老化性能强,水汽透过率低、
四、我们的优势—差异化
工艺控制------不同区域的产品推广
通过优化工艺水平,研发出多种适用
于不同区域的组件产品,为不同区域的 客户量身定制最符合其需求的产品。
பைடு நூலகம்
沿海地区、高温高湿地区
使用【具有抗PID衰减功能的组件】
在温度85℃±2℃、湿度85%±5%,负 压1000V环境下测试96小时,最大衰减 仅0.71%,抗PID性能卓越。
功率衰减
解决方案
使用镀膜玻璃的组件,在原有功率的的基 础上多赠送1W,功率档位由0-5W调整为1-6W。
功率档位的优化,可以保证组件在极端环 境下的衰减依然可以满足首年2.5%的衰减需求, 保证客户的利益。
14
3)醋酸腐蚀电极 EVA老化产生的乙酸会腐蚀太阳电池的背板、电极和焊带等金属部分,严重的腐蚀一是 可以造成断路,直接导致组件的失效,二是在系统电压比较高时,某处的断路点还会 发生打火的现象,频繁的打火会使局域温度上升到很高,甚至引起玻璃的熔化
13
三、主要材料介绍 3.3 背板
背板位于太阳能电池板的背面,对电池片起保护和支撑作用,具有可靠 的绝缘性、阻水性、耐老化性。
高寒、沙漠地区
使用【耐候性能优异的组件】
采用耐候性能优异的耐紫外EVA及双 层氟材料背板,并配备达额定电流的 接线盒,适用于高寒、沙漠地区。
14
四、我们的优势—差异化
工艺控制------不同区域的产品推广
BIPV、农业大棚运用 沙漠、海洋、高原等气 候恶劣地区
使用【常规双玻】和【彩色双玻】
14
四、我们的优势—差异化
工艺控制------不同区域的产品推广
防水、抗风沙、抗高温及抗紫外线特性优异。 外形美观、透光率高。
14
四、我们的优势—功率保障
功率降档,让客户省钱更放心! 项目地估算第一年发电量时,通常需要考虑的因素如下:
·倾斜面太阳光辐照量修正 ·组件表面灰尘等异物挡光的影响 ·温度对光伏组件输出的影响 ·光伏组件的自身衰减 ·组串内组件的匹配损失 ·方阵前后排之间的阴影遮挡损失 ·直流线路损失; ·逆变器转换效率损失 ·本地变压器损耗; ·交流线路损失; ·主变压器损耗 ·电站自用电损耗、停机时间损失
14
四、我们的优势 4.5 严谨的生产工艺
新产品制作完全依据IEC61215、IEC61730导则进行设计并进行全序列测试; 批量投产前周密部署首件制作过程,记录和总结过程可能存在的问题点; 人员岗前专业化技能培训,合格上岗; 制程质量、工艺全程督导人员依据标准作业,及时纠偏; 材料分批按点进行测试检验,一致性、稳定性得到保证; 单订单闭环 。总结整个生产过程异常,记录备案,避免再发生。
聚合物材料中没有单种材料完全满足光伏背板要求,因此一般用几层性能 互补的材料粘结或涂覆在一起。
TPT
14
三、主要材料介绍 背板的结构及特点
通常背板主要由三层构成:含氟膜(或其替代物)+PET层(或其替代物) +与EVA粘结层(有含氟膜、改性EVA、PE、PET等)。
经典TPT结构如右图所示: 特点: 优异的耐候性 较低的水汽透过率 良好的电绝缘性 一定的粘结强度 良好的耐磨性
高绝缘性
EVA:first、海优威。防PID性能,高绝缘性,胶黏性能优越。
型材:喷砂氧化工艺,绝缘性优越,使用寿命长。汉龙、广跃
焊带:常规、高效焊带。低阻值、效率高。华友、斯维克、太阳、众达
接线盒:主流采用灌胶式。高阻水性能和散热性能
硅胶:天山、创景
胶带:Desa
玻璃:镀膜91.6%、非镀膜93.6%并存,满足客户不同需求
EVA
13
三、主要材料介绍 3.2.1 EVA的作用
1)封装电池片,防止外界环境对电池片的电性 能造成影响; 2)增强组件的透光性; 3)将电池片,钢化玻璃,TPT 粘接在一起,具有一定的 粘接强度;
13
三、主要材料介绍
3.2.2 EVA老化原因分析
1)变黄 生色变黄主要是由老化降解中产生的共轭基团所致,而引起变色的因素主要有: A:EVA自身受光热氧发生降解 B:残留的交联剂和抗氧剂的作用 EVA的变黄会导致组件透光率的下降,进而影响组件的输出效率。
14
四、我们的优势 4.2 完备的认证体系保障
14
四、我们的优势 4.3 强大的技术平台和持续改进的创新保证
14
四、我们的优势
4.4 先进的生产设备
焊接机:西班牙Grorosabel,全面兼容三栅、四栅。焊接稳定性佳,一致 性得到保证。 检测装置:双EL配置,过程、包装双重保障,双800万像素,细微观察隐裂 等异常; 装框机:德国REIS全自动组框机,配合desa胶带,满足机械强度的需求, 美观性大大提高; 测试机:AAA级PASAN测试机,测试重复性、均匀性2%以内,测试稳定性得 到保证。