宣钢低铁水消耗炼钢技术的应用分析
宣钢2#高炉低风温操作技术研究

宣钢2#高炉低风温操作技术研究2017年9月以来宣钢2#高炉热风炉持续恶化,双预热退出热风炉系统,送风温度大幅下降,本文分析了热风温度下降的原因。
在低风温条件下,研究高炉操作制度,优化送风参数,调整上部装料制度,实现了高炉稳定顺行,指标优化。
标签:高炉;热风炉;低风温;操作制度研究1 前言宣钢2#2500m?高炉自2010年9月建成投产,配备了3座改进型高温内燃式热风炉,预留第四座热风炉位置,使用单一高炉煤气作为燃烧介质,19孔高效格子砖。
热风炉采用双预热装置,设置高温烟气+高温燃烧炉+板式空气、煤气双预热装置,高炉煤气预热到180~200℃,助燃空气预热到450~500℃。
热风炉球顶温度1400℃,烟道温度7kPa,净高炉煤气含尘量质量标准≯10mg/m3,助燃空气压力>7kPa,确保在燃烧全高炉煤气的条件下实现1250℃高风温的目标。
热风炉结构特点是悬链线形拱顶,“眼睛”型燃烧室,采用组合砖及高温耐磨刚玉浇注料结构自立式隔墙,内衬设置合理的滑动结构和膨胀结构,矩型陶瓷燃烧器。
2 热风炉风温下降原因分析2#高炉开炉后,热风炉初期单燒使用煤气量100000 Nm3/h ~120000Nm3/h,空气量90000 Nm3/h左右,在煤气压力8Kpa时煤气调节阀全开,热风炉能够提供较高的风温。
2016年6月公司转炉煤气有余量,考虑全公司煤气平衡,减少煤气放散,2#高炉热风炉开始配加转炉煤气10000Nm3/h左右。
配加转炉煤气后,风温呈下降趋势,此时风温1060℃~1100℃,基本上能满足高炉生产要求,2017年9月份后,热风温度显著下降,冬季时风温只有950℃~1000℃,对高炉操作影响较大。
分析热风温度下降的原因:(1)2017年10月热风炉煤气换热器因换热板之间积满灰尘、腐蚀,换热效率下降,不能正常工作,退出热风炉系统后,热风温度呈下降趋势。
造成换热器积灰、腐蚀的原因是转炉煤气含尘较高,转炉煤气回收标准是含尘≤30mg/m3,远远高于高炉煤气低于10mg/m3的标准。
低成本高效率LF精炼工艺创新与应用

低成本高效率LF精炼工艺创新与应用摘要:随着钢铁工业的快速发展, 要求钢材向品质优越、多功能、高技术含量和高附加值方向发展,钢水炉外精炼处理技术迅速发展。
LF精炼是转炉炼钢与连铸工艺之间的过渡环节,既要满足转炉炼钢的快节奏,又要为连铸提供合格的钢液。
LF精炼能否在生产节奏要求时间内使钢水成分、温度、洁净度达到相应的技术要求,已成为炼钢厂生产的限制环节。
因此在了解LF精炼工艺特点的基础上,强化其冶金功能,以满足生产的要求。
本文分析了低成本高效率LF精炼工艺创新与应用。
关键词:低成本高效率;LF精炼工艺创新;应用世界金融危机爆发后,西方国家对我国钢铁产品征收高额关税,导致国内钢材严重过剩。
为占领更多市场份额,各钢铁企业纷纷降价销售,以致大多数钢铁企业亏损,买方市场观望气氛甚浓,对产品质量趋于苛刻。
为适应市场发展趋势,提高产品竞争力,各公司在不断提高产品质量的同时,也在深入挖潜降耗。
其中电耗是钢铁生产中的重要能耗指标,是衡量一个企业生产效率高低的指标之一,电耗受生产过程多种因素制约和影响,与工艺、设备、人员、生产前的准备工作等各因素密不可分。
一、LF 精炼工艺的特点1.石墨电极埋弧加热。
LF炉以石墨电极与钢水之间产生的高温电弧为热源,对钢水进行加热,升温速度为4~5℃/min。
加热时将石墨电极插入泡沫渣层中,进行埋弧操作,高温电弧在渣层内产生。
泡沫渣对高温电弧起到屏蔽作用,一方面减少了高温电弧对钢包的热辐射,保护了炉衬;另一方面钢水和炉渣可以有效的吸收电弧热,提高了热效率。
2.高碱度合成精炼渣。
生产中要求LF精炼渣为高碱度、高还原性、低熔点的白渣,此外还要有良好的流动性、合适的扩散系数和表面张力等理化性能。
炉渣的化学成分会影响LF的精炼效果。
钢水中的硫可以脱到0.005%以下。
理论上炉渣碱度越高,脱硫效果越好;但碱度过高,炉渣黏度将增大,流动性变差。
实际生产中通常将SiO2降得很低,以提高炉渣碱度,通过调整炉渣中的Al2O3来改变炉渣的流动性,由于炉渣的流动性也比较好,炉渣的熔点也比较低,LF精炼渣通常具有较高的还原性。
钢铁冶炼中精益生产管理的运用-生产管理论文-管理学论文
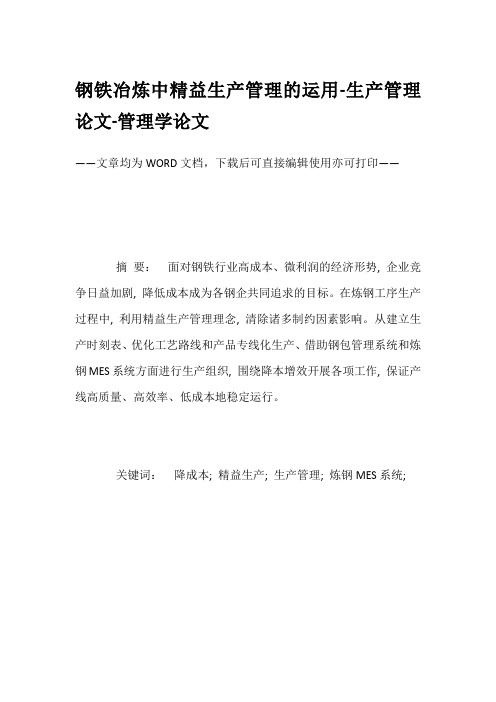
钢铁冶炼中精益生产管理的运用-生产管理论文-管理学论文——文章均为WORD文档,下载后可直接编辑使用亦可打印——摘要:面对钢铁行业高成本、微利润的经济形势, 企业竞争日益加剧, 降低成本成为各钢企共同追求的目标。
在炼钢工序生产过程中, 利用精益生产管理理念, 清除诸多制约因素影响。
从建立生产时刻表、优化工艺路线和产品专线化生产、借助钢包管理系统和炼钢MES系统方面进行生产组织, 围绕降本增效开展各项工作, 保证产线高质量、高效率、低成本地稳定运行。
关键词:降成本; 精益生产; 生产管理; 炼钢MES系统;Abstract:In the face of high cost and micro profit economic situation in iron and steel industry, the competition of enterprises is intensified and the reduction of the cost has become the common goal for the steelmaking companies.In the steelmaking production process, the lean production management concept is used to clear the influence of many constraint factors.Through the establishment of the production schedule, the optimization of process routes and product dedicated production, and the help of ladle management system and MES system for steelmaking production organization etc, various works were focused on the cost decreasing and benefit increasing to ensure the stable operation of the production line of high quality, high efficiency and low cost.Keyword:reducing costs; lean production; production management; MES system for steelmaking;在竞争激烈的市场环境下, 高效率低成本生产、提高产品质量和客户满意度成为钢铁企业提高竞争力的重要手段。
4-铁水预处理工艺

第四章铁水预处理工艺本章要点:工艺概况(全貌、历史、现状)基本原理应用(炼钢基本理论)主要工艺过程(关键工艺技术)新技术、发展趋势和存在问题(兴趣点)1、铁水预处理概述铁水预处理是指高炉铁水在进入炼钢炉之前预先脱除某些杂质的预备处理过程。
分为普通铁水预处理和特殊铁水预处理两大类。
普通铁水预处理包括:铁水脱硫、铁水脱硅和铁水脱P。
特殊铁水预处理一般是针对铁水中含有的特殊元素进行提纯精炼或资源综合利用,如铁水提钒、提铌、脱铬等预处理工艺。
铁水预处理容器的选择根据铁水预处理容器的选择,脱硫工艺可分为:•混铁车喷吹法•铁水罐法•铁水包法发展趋势:采用铁水包作为铁水脱硫预处理的容器铁水脱硫喷吹工艺铁水脱硫喷吹工艺铁水预处理的化学冶金学意义化学冶金学意义:创造最佳的冶金反应环境!钢铁冶金工艺优化:高炉⎯→分离脉石、还原铁矿石铁水预处理⎯→脱硅、脱磷、脱硫转炉⎯→脱碳、升温钢水炉外精炼⎯→去夹杂、合金化铁水预处理(脱硫)的优越性(1) 满足用户对超低硫、磷钢的需求,发展高附加值钢种:如:船板钢、油井管钢:[S]、[P]<0.005 %管线钢、Z向钢、IF钢:[S] ≤0.002~0.004 % (2) 减轻高炉脱硫负担,放宽对硫的限制,提高产量,降低焦比;(3)炼钢采用预处理后的低磷、低硫铁水冶炼,可获得巨大的经济效益。
能提高转炉生产率、降低炼钢成本、节约能耗。
转炉脱磷、脱硫任务减轻,渣量大大降低,造渣料急剧减少,渣中TFe降低,铁损减少,锰回收率急剧增加,锰铁消耗降低,转炉吹炼时间缩短,炉龄延长。
(4) 炉外铁水预处理脱磷、脱硫可保持同炉内一样良好的热力学条件,还可通过采用搅拌措施,大大改善动力学条件,以较少的费用获得很高的脱磷、脱硫效率。
(5) 高炉某些特殊炉况下要造酸性渣如排碱,铁水含硫偏高,炉外要进行补充脱硫。
(6) 铁水深度预处理是目前冶炼纯净钢最经济的、最可靠的技术保障,已成为生产优质低磷、低硫钢必不可少的经济工序。
高炉炼铁对炉料质量的要求及优化配矿技术
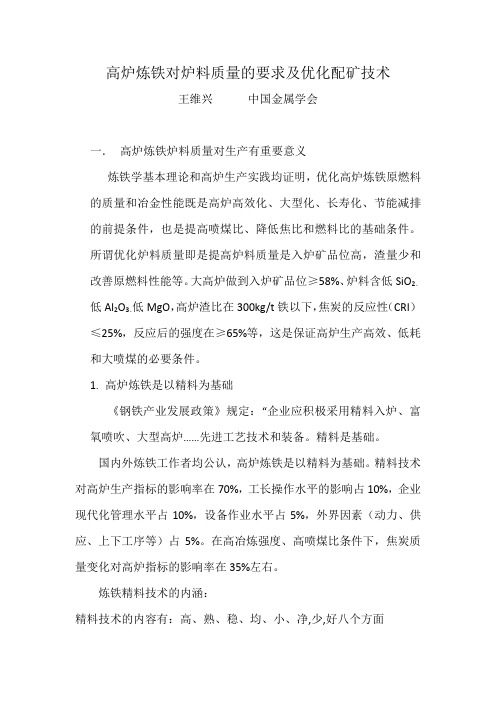
高炉炼铁对炉料质量的要求及优化配矿技术王维兴中国金属学会一.高炉炼铁炉料质量对生产有重要意义炼铁学基本理论和高炉生产实践均证明,优化高炉炼铁原燃料的质量和冶金性能既是高炉高效化、大型化、长寿化、节能减排的前提条件,也是提高喷煤比、降低焦比和燃料比的基础条件。
所谓优化炉料质量即是提高炉料质量是入炉矿品位高,渣量少和改善原燃料性能等。
大高炉做到入炉矿品位≥58%、炉料含低SiO2、低Al2O3、低MgO,高炉渣比在300kg/t铁以下,焦炭的反应性(CRI)≤25%,反应后的强度在≥65%等,这是保证高炉生产高效、低耗和大喷煤的必要条件。
1.高炉炼铁是以精料为基础《钢铁产业发展政策》规定:“企业应积极采用精料入炉、富氧喷吹、大型高炉……先进工艺技术和装备。
精料是基础。
国内外炼铁工作者均公认,高炉炼铁是以精料为基础。
精料技术对高炉生产指标的影响率在70%,工长操作水平的影响占10%,企业现代化管理水平占10%,设备作业水平占5%,外界因素(动力、供应、上下工序等)占5%。
在高冶炼强度、高喷煤比条件下,焦炭质量变化对高炉指标的影响率在35%左右。
炼铁精料技术的内涵:精料技术的内容有:高、熟、稳、均、小、净,少,好八个方面⑴高:入炉矿含铁品位高,原燃料转鼓指数高,烧结矿碱度高。
入炉矿品位高是精料技术的核心,其作用:矿品位在57%条件下,品位升高1%,焦比降%~%,产量增加%~%,吨铁渣量减少30公斤,允许多喷煤粉15公斤.;入炉铁品位在52%左右时,品位下降1%,燃料比升高%~%。
高碱度烧结矿是碱度在~2,2(倍),其转鼓强度高、还原性好。
⑵熟:指熟料(烧结和球团矿)比要高,一般>80%。
⑶稳:入炉的原燃料质量和供应数量要稳定。
要求炉料含铁品位波动±<%,碱度波动±<(倍),FeO含量波动±≤%,合格率大于80%~98%等。
详见表4和表5。
⑷均:入炉的原燃料粒度要均匀。
解析转炉炼钢技术的应用及革新途径

工作探索解"转炉炼&技(的应用,革新/0刘冈U(河钢宣钢一钢轧厂,河北张家口075000)摘要:我们国家开展各项工业生产活动的过程中,需要使用到很多钢铁材料,所以铁材料的质量对于整个钢铁企业生产活动有着重要作用。
好的钢铁可以推动炼钢技术的革新和发展,也能在整体上提高炼钢企业的核心竞争实力,所以先对转炉炼钢的技术应用进行分析,之后进一步研究了转炉炼钢技术的革新手段和方法,能炼钢企业的进作用。
关键词:转炉;炼钢;工技术;应用;发展1转炉炼钢技术的相关应用1.1的炼钢技术减少残渣的炼钢技术主要是重复利用脱离了碳元素的残渣,在整个炼钢阶段,因为之前要在炉内进行脱碳这一步骤,于是有较多的炉渣残存下来,但是之前的工艺很难有效的清理掉转炉中的残渣。
而现在,通过新技术来减少残渣,把残渣保留于炉内,直接用于下一次转炉炼钢工作,这是对以往技术的创新和完善。
除此之外,之前的技术手段很难有效地兑铁和高效脱磷,但通过减少残渣的炼钢技术可以有效地对转炉实现脱磷或是脱碳。
1.2尘埃的技术我们国家在转炉炼钢过中要实施中的除:,但是现在是有转炉炼钢以往的除技术,而除技术难以到工作节约能源减少排放的目的。
这年来,我国节约源和的国,以除尘技术有了较的完善,节约能源和减少排放这一前进。
炼钢多的除工艺,这技术是来源于国外,但我们国家实对理用。
1.3阻挡的技术钢铁转炉工作钢到钢这一中,残渣的技术有助于渣减少,通过炼还能进钢中少,磷现,而高钢的除此之外,残渣的技术有于或脱用次的减少,高,了转炉行\的来,转炉炼钢过中残渣的技术需要用,这一要钢口,通过能下渣的外,而实现操控,进一保钢的\1.4脱磷元的炼钢技术下,用多的脱磷是转炉和铁三脱预制结合、双渣%或者转炉双联方法。
而转炉双联主要是指通过两台转炉作行,中一台用于脱磷作,等到脱磷结束之后,将钢铁放在另一台转炉中;而双渣主要是通过一台转炉来完两次造渣工作。
炼钢厂通过对以往炼钢技术进行革新,高了钢数量以及碳量,炼钢厂中整体钢质有高。
钢铁冶金学(炼钢部分).
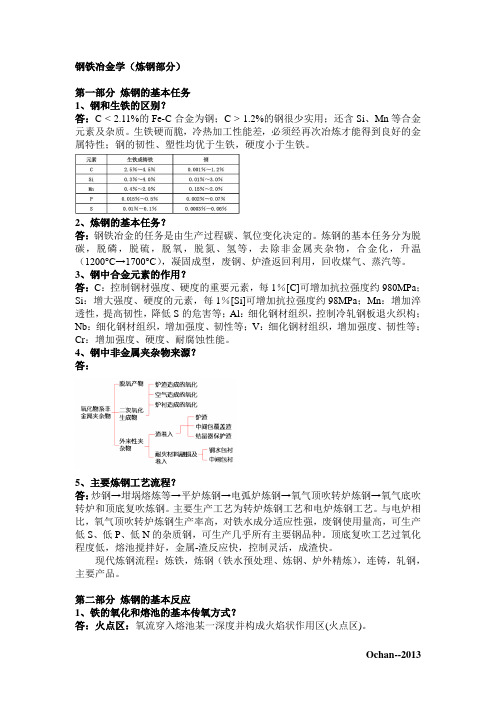
钢铁冶金学(炼钢部分)第一部分炼钢的基本任务1、钢和生铁的区别?答:C < 2.11%的Fe-C合金为钢;C > 1.2%的钢很少实用;还含Si、Mn等合金元素及杂质。
生铁硬而脆,冷热加工性能差,必须经再次冶炼才能得到良好的金属特性;钢的韧性、塑性均优于生铁,硬度小于生铁。
2、炼钢的基本任务?答:钢铁冶金的任务是由生产过程碳、氧位变化决定的。
炼钢的基本任务分为脱碳,脱磷,脱硫,脱氧,脱氮、氢等,去除非金属夹杂物,合金化,升温(1200°C→1700°C),凝固成型,废钢、炉渣返回利用,回收煤气、蒸汽等。
3、钢中合金元素的作用?答:C:控制钢材强度、硬度的重要元素,每1%[C]可增加抗拉强度约980MPa;Si:增大强度、硬度的元素,每1%[Si]可增加抗拉强度约98MPa;Mn:增加淬透性,提高韧性,降低S的危害等;Al:细化钢材组织,控制冷轧钢板退火织构;Nb:细化钢材组织,增加强度、韧性等;V:细化钢材组织,增加强度、韧性等;Cr:增加强度、硬度、耐腐蚀性能。
4、钢中非金属夹杂物来源?答:5、主要炼钢工艺流程?答:炒钢→坩埚熔炼等→平炉炼钢→电弧炉炼钢→氧气顶吹转炉炼钢→氧气底吹转炉和顶底复吹炼钢。
主要生产工艺为转炉炼钢工艺和电炉炼钢工艺。
与电炉相比,氧气顶吹转炉炼钢生产率高,对铁水成分适应性强,废钢使用量高,可生产低S、低P、低N的杂质钢,可生产几乎所有主要钢品种。
顶底复吹工艺过氧化程度低,熔池搅拌好,金属-渣反应快,控制灵活,成渣快。
现代炼钢流程:炼铁,炼钢(铁水预处理、炼钢、炉外精炼),连铸,轧钢,主要产品。
第二部分炼钢的基本反应1、铁的氧化和熔池的基本传氧方式?答:火点区:氧流穿入熔池某一深度并构成火焰状作用区(火点区)。
吹氧炼钢的特点:熔池在氧流作用下形成的强烈运动和高度弥散的气体-熔渣-金属乳化相,是吹氧炼钢的特点。
乳化可以极大地增加渣-铁间接触面积,因而可以加快渣-铁间反应。
铁水预处理工艺

投资成本(—)
低
一般
较高
铁水预脱硫条件优于钢水脱硫条件,原因:
1.铁水中含有较高的C、Si、P等元素,提高了铁水中 硫的活度系数; 2.铁水中氧含量低,提高渣铁之间硫分配比,脱硫效 率高; 3.铁水含氧量低,因而可以使用强脱硫剂强化脱硫而 不会造成强烈氧化; 4.铁水脱硫费用低于高炉、转炉和炉外精炼的脱硫费 用。
4.3.3 铁水预脱硫的意义 4.3.4 铁水预脱硫的基本原理
A 金属、氧化物及碳化物脱硫 B 碱性渣脱硫 4.3.5 铁水预脱硫的方法 投掷法:将脱硫剂投入铁水中脱硫 喷吹法:用载气将脱硫剂喷入铁水中脱硫 搅拌法(KR法):通过中空机械搅拌器向铁水
内加入脱硫剂,搅拌脱硫
脱硫工艺的技术比较
脱硫工艺方法
2.Mg/CaC2复合脱硫剂 喷吹Mg/CaC2复合脱硫剂的体系,由于CaC2与[O]
反应生成CaO,MgS(固)不能稳定存在于该体系中,由于 Mg/CaC2复合脱硫剂体系与Mg/CaO复合脱硫体系的脱 氧、脱硫平衡反应是相同的,因此对脱氧、脱硫能力 而言,喷吹这两种复合脱硫剂效果是一样的。
但是,由于CaC2比CaO 昂贵且不安全,因此从脱 硫成本及储运、使用的安全性方面考虑,使用Mg/ CaO复合脱硫剂更安全、成本更低。
高碱度烧结矿
颗粒
0
20-40
O2+烧结矿 50%
40-80
反应速率常数 (min-1) 0.25
0.06
处理后 [Si]%
0.13 0.10 ≤0.10%
4.3 铁水预脱硫工艺 4.3.1 国外铁水预脱硫技术的发展背景与现状
历史背景:60年代,氧枪转炉炼钢的崛起工业的发展 给钢铁材料质量提出了更高要求。
- 1、下载文档前请自行甄别文档内容的完整性,平台不提供额外的编辑、内容补充、找答案等附加服务。
- 2、"仅部分预览"的文档,不可在线预览部分如存在完整性等问题,可反馈申请退款(可完整预览的文档不适用该条件!)。
- 3、如文档侵犯您的权益,请联系客服反馈,我们会尽快为您处理(人工客服工作时间:9:00-18:30)。
宣钢低铁水消耗炼钢技术的应用分析 刘永军 (河北钢铁集团宣钢公司炼钢厂,河北 宣化075100) 摘 要 本文介绍了宣钢炼钢厂通过实施温度补偿技术、推广凝渣补炉技术、模拟副枪操作提高终点命中率控制水平以及通过控制活度氧值实现对铸坯质量缺陷的有效控制,对宣钢实施低铁水消耗炼钢技术的应用进行了理论分析和实践检验。 关键词 炼钢 铁水消耗 分析
一、概述 百吨炉区初建于2002年5月,经过几年的升级改造,目前的主要生产工艺装备情况如下表。
表1 百吨转炉工艺装备主要参数 序号 参数名称 单位 110t转炉 120t 转炉 1 转炉装入量 t 110 150 2 炉壳全高 mm 8020 9060 3 炉壳外径 mm 5636 6530 4 高宽比 1.423 1.387 5 炉膛全高 mm 6840 7921 6 炉膛内径 mm 4000 4858 7 熔池深度 mm 1326 1418 8 新炉内容积 m3 83 126 9 炉 容 比 m3/t 0.83 0.951 10 炉底透气元件 套 4 8
表2 百吨炉区连铸机工艺装备参数 序号 参数名称 单位 4#、5#机 6#机 1 铸机半径 m R8 R9 2 流间距×流数 mm 1200×8 1200×12 3 铸坯断面 mm×mm 150×150、165×225 150×150、200×285 4 铸机年产量 万吨 150 200 5 中包个数 个 1 2 6 设计中包寿命 包 30 30 7 钢水容量 吨 26 30 8 结晶器长度 mm 900(电搅) 900(电搅) 9 其它装置 塞棒自动控制 塞棒自动控制
二、 经济热铁水消耗的确定 2.1经济热铁水消耗的确定原则 转炉炉内热平衡是确定经济热铁水消耗的基本原则,否则,若热铁水消耗不合理,铁水中非铁元素氧化放热不足以提高钢水温度到终点要求温度时,铁元素随即氧化放热,既增加铁损,又因炉渣氧化性强影 - 1 -
响终点钢水质量。 2.2经济热铁水消耗的确定 根据炼钢厂的生产条件,通过热平衡计算,得出如下热平衡表3。
表3 热 平 衡 表 热收入项 热支出项 项目 热量 百分比% 项目 热量 百分比% 铁水的物理热 295162.155 58.138 钢水带出的物理热 313785 61.806 元素氧化及成渣热 121529.135 41.862 钢渣带出的物理热 57344 11.295 炉气带出的物理热 47271 9.31 各种散热 20920 4.121 冷却剂耗热 68371.29 13.467 总热量收入 507691.29 100 总热量支出 507691.29 100
再根据废钢、生铁的冷却效应,得出全废钢、全生铁做冷却剂情况下的经济热铁水消耗表4。 表4 经济热铁水消耗 项 目 总装入量,吨 平均炉产量,吨 热铁水量,吨/炉 热铁水消耗kg/t 全废钢做冷却剂 115 103.5 96.26 930 全生铁做冷却剂 115 103.5 90.05 870
三、炼钢厂实际热铁水消耗控制情况 2006年以来,因钢材价格的节节攀高,公司生产经营也随之发生转变,其中,热铁水消耗的控制也是如此,具体见表5。 表5 热铁水消耗实际执行情况(kg/t) 项目 上半年 下半年 全年 2006年 909.575 915.685 912.630 2007年 889.983 889.406(7~10月) 889.970
从表5可见:2007年上半年较2006年下半年热铁水消耗降低了25.702kg/t;2007年下半年较上半年热铁水消耗降低了0.577kg/t。 不管是2006年或是2007年,平均热铁水消耗均在采用全生铁与全废钢做冷却剂的经济热平衡范围内,也就是说,炼钢厂通过合理调整冷料搭配,辅以其他相关措施,综合考虑金属料价差,基本可以实现转炉炉内热量平衡。 四、降低热铁水消耗的措施方向及面临的问题 4.1 降低热铁水消耗的措施方向 从炉内升温计算公式可以看出,炉内升温与热量收入总量及热量支出项(钢水热、炉渣成渣热、炉衬吸热、炉气等热损失)有关。
△t=(.)Qmc - 2 -
△t----升温值,℃ Q-----热量收入,Kj m----金属、炉渣、炉衬的质量,kg C----金属、炉渣、炉衬的质量热容,KJ/kg.℃. 在转炉炼钢中,钢水升温所吸收的热被视为有效热,该部分热占总支出热的比例称为热效率:
总热效率=QQ有效 ×100% Q有效---------有效热,kJ Q-------------总热量支出kJ 因此要想节铁增钢,一方面必须提高转炉的热收入,另一方面还要努力降低过程热量损失,从而提高炉内有效热。 4.2 降低热铁水消耗面临的问题 4.2.1生铁块代替废钢入炉,造成入炉料中生铁数量明显增加,延长了吹炼时间,增加了入炉原料的化学烧损;生铁块的化学烧损比废钢多5%-7%,需要增大造渣量,导致转炉喷溅严重,引起渣道事故频繁发生。 4.2.2 由于外购生铁块在成份上难以保证,造成个别炉次转炉一倒模拟副枪操作时磷、硫居高不下,多次补吹导致转炉炉衬侵蚀严重,炉况波动可能造成穿炉等重大工艺事故。(转炉一倒模拟副枪操作是目前未装备转炉副枪设备,为实现转炉冶炼终点碳温协调而在冶炼进行过程中多倒一次炉的冶炼操作模式。) 4.2.3 生铁块在炉内熔化困难,在快节奏的条件下,不能全部熔化,经常造成转炉一倒时低温或生铁块粘附前大面,因低温造成倒钢事故以及出钢时返碳严重导致成品碳出格炉次明显增多。 4.2.4 生铁块代替废钢入炉,造成冶炼终点钢水成分、温度不均匀;钢水氧化性较强,直接影响终点钢水质量、给品种钢冶炼带来很大困难。 五、 降低热铁水消耗的措施 降低热铁水消耗是以不牺牲钢质和恶化炉况为前提,因此,降低热铁水消耗一方面在努力提高转炉综合热效率的同时,还必须抓好转炉过程及脱氧合金化控制,抓好转炉的使用与维护。 5.1实施温度补偿技术降低热装铁水消耗,增加炉内物理及化学热收入 5.1.1 生铁与废钢对炉内热量的影响 因生铁的冷却效应小于废钢,碳含量远高于废钢,故生铁熔化吸收的物理热小于废钢,而碳氧化释放出的化学热远高于废钢。
表6 生铁与废钢对热量的不同影响 项目 生铁 废钢 相同条件下生铁比废钢 冷却效应 0.7 1.0 熔化吸收热量少30% C含量,% ≥3.5 ≤0.50 反应释放出热量多7倍
对装入制度中冷料的搭配结构进行优化调整,采用部分生铁块代替部分废钢,以其化学热来补偿冶炼过程炉内的热量损失,为炉内热量的进一步提高起到了重要作用。 5.1.2为提高生铁块入炉比例,确保过程热量充足,采取了如下措施: 5.1.2.1 吹炼过程使用发热剂,吹炼前通过往废钢斗内加碳化硅或者在混铁炉出铁过程中加入碳化硅,来稳 - 3 -
定温度的升高过程,提高一倒温度,减少钢水的吹损。实践证明,吨钢每加入0.5公斤碳化硅,可以提高一倒温度4℃,减少钢水吹损0.7kg/t钢。 表7 铁水发热剂效果 对比类别 出混铁炉铁水温度,℃ 加入量,kg/炉 等待时间,分 入转炉铁水温度,℃ 温降,℃
使用炉次 4.13081318~1295 50
7.710~5
13021311~1287
4.610~5
未使用炉次 1.1308
1316~1293 0
1.7
9~5
12951301~1275
1.1317~6
5.1.2.2 为提高铁水物理热,将混铁炉煤气量由原来的400m3/h提高到800 m3/h,进一步提高铁水物理热。并采用一炼铁水、白庙铁水倒入大罐入混铁炉的方法使出混铁炉铁水温度增加了20-30℃,铁水温度由1250℃增大到1270℃。 5.1.2.3做好停炉时炉衬保温工作,利用煤氧枪开火保温,减少炉衬温降。 5.2严把铁水、生铁块入厂质量关,降低入炉总辅料消耗,减少炉内热损失。 随时掌握进厂铁水的质量情况,包括铁水温度,成份、带渣量。要求炼钢车间工长要及时向厂调询问铁水分析,根据分析来指导生产,在出现分析与实际相差较大时,当班生产调度要以最快的速度通知公司总调,来协调公司技监中心(监查站),炼铁厂的专业人员到混铁炉现场取样核实。对不合格的铁水根据混铁炉存铁情况进行让步接受,确保出混铁炉铁水成份合格。 针对生铁块供货厂家多,质量不稳定,硫含量高,及时规定了两炉区接受外购生铁块入厂的规定。要求两炉区在接受外购生铁块时以本厂原料车间的分析单为据,对不符规定的生铁块拒收,同时通知原料车间进行退库或混合处理(混合处理时炼钢车间要派专人监督)。另外,厂派专人到原料处生铁库跟踪生铁块的入库检验,及时将其质量信息反馈到厂,厂内配合技监中心,派专人对进厂生铁块成分进行联合抽查,稳定了正常生产节奏。 5.3留渣双渣法过程控制,改善熔池反应动力学条件。 结合外采生铁块磷、硫高,而且熔点低、熔化速度慢的特点,在进行完凝渣补炉后的过程冶炼控制选择双渣法。根据冶炼钢种的不同,选择[C]在0.30-0.50%范围内进行一倒模拟副枪操作,通过多增加一次倒炉过程,改善冶炼过程熔池反应的动力学条件;同时,选择[C]在0.30-0.50%范围内进行一倒模拟副枪操作,也有利于确保终点碳、终点温度、终点磷三者之间的协调,优化转炉冶炼的终点控制水平。 5.4 提高冶炼过程操作水平,减少后吹次数 为减缓节铁对钢水终点质量的冲击,开展了进一步提升操作水平。主要是提高过程温度和成分的命中率,缓解后吹次数增加造成的钢水过氧化。
85.9891.4484.4379.7876.5379.1880.34
82.3882.84
80.2981.05
82.06
81.582.2192.6758085
9095
200423456789101112200523月出钢率,%
出钢率
图3 二倒出钢率 2006 7 8 9 10 11 12 2007 2 3 4 5 6 7 8