低NOx高温空气燃烧技术
空气分级燃烧降低氮氧化物生成的原理
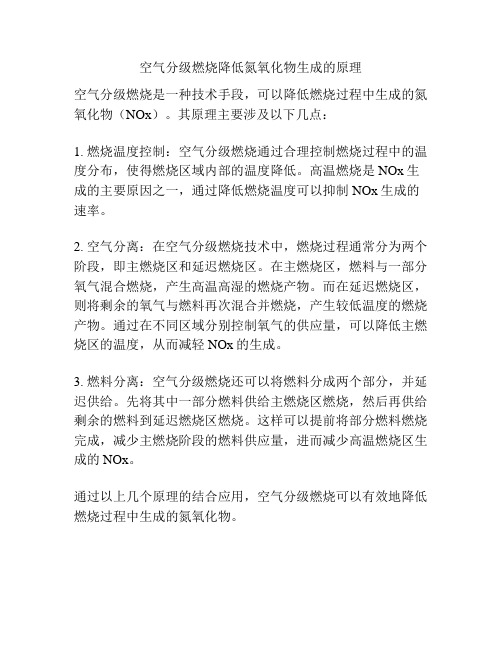
空气分级燃烧降低氮氧化物生成的原理
空气分级燃烧是一种技术手段,可以降低燃烧过程中生成的氮氧化物(NOx)。
其原理主要涉及以下几点:
1. 燃烧温度控制:空气分级燃烧通过合理控制燃烧过程中的温度分布,使得燃烧区域内部的温度降低。
高温燃烧是NOx生成的主要原因之一,通过降低燃烧温度可以抑制NOx生成的速率。
2. 空气分离:在空气分级燃烧技术中,燃烧过程通常分为两个阶段,即主燃烧区和延迟燃烧区。
在主燃烧区,燃料与一部分氧气混合燃烧,产生高温高湿的燃烧产物。
而在延迟燃烧区,则将剩余的氧气与燃料再次混合并燃烧,产生较低温度的燃烧产物。
通过在不同区域分别控制氧气的供应量,可以降低主燃烧区的温度,从而减轻NOx的生成。
3. 燃料分离:空气分级燃烧还可以将燃料分成两个部分,并延迟供给。
先将其中一部分燃料供给主燃烧区燃烧,然后再供给剩余的燃料到延迟燃烧区燃烧。
这样可以提前将部分燃料燃烧完成,减少主燃烧阶段的燃料供应量,进而减少高温燃烧区生成的NOx。
通过以上几个原理的结合应用,空气分级燃烧可以有效地降低燃烧过程中生成的氮氧化物。
低氮燃烧技术

低氮燃烧技术1 水泥窑炉系统NO X形成机理大致介绍2 现有低氮燃烧技术大致介绍3 低氮燃烧技术的效果4 改变燃料物化性能5 提高生料易烧性6、新型干法水泥应对脱硝的相应措施1、水泥窑炉系统NO X形成机理大致介绍1.1NO X的生成机理窑炉内产生的NO X主要有三种形式,高温下N2与O2反应生成的热力型NO X、燃料中的固定氮生成的燃料型NO X、低温火焰下由于含碳自由基的存在生成的瞬时型NO X.1.2热力型NO X:由于是燃烧反应的高温使得空气中的N2与O2直接反应而产生的,以煤为主要燃料的系统中,热力型NO X为辅。
➢一般燃烧过程中N2的含量变化不大,根据泽里多维奇机理,影响热力型NOX 生成量的主要因素有温度、氧含量、和反应时间。
➢热力型NOX产生过程是强的吸热反应,温度成为热力型NOX生成最显著影响因素。
研究显示,温度在1500K以下时,NO生成速度很小,几乎不生成热力型NO,1800K以下时,NO生成量极少,大于1800K时,NO生成速度每100K约增加6-7倍。
➢温度在1500K以上时,NO2会快速分解为NO,在小于1500K时,NO将转变为NO2,一般废气中NO2占NO X的5-10%,排入大气中NO最终生成NO2,所以在计算环境影响量时,还是以NO2来计算。
可以说,窑炉内的温度及燃烧火焰的最高温度是影响热力型NO X生成量的一个重要指标,也最终决定了热力型NO X的最大生成量。
因此,在窑炉设计中,尽量降低窑炉内的温度并减少可能产生的高温区域,特别是流场变化等原因而产生的局部高温区。
燃烧器设计中,要具备相对均匀的燃烧区域来保证燃料的燃烧,降低火焰的最高温度。
这些都是有效降低热力型NO X的有效办法。
➢热力型NOX生成量与氧浓度的平方根成正比,氧含量也是影响热力型NO X 生成量的重要指标。
随O2浓度增加和空气预热温度的增加,NO X生成量上升,但会有一个最大值。
O2浓度过高时,过量氧对火焰有冷却作用。
目前国内流行的低NOx燃烧技术

目前国内流行的低NOx燃烧技术用改变燃烧条件的方式来降低NOx的排放,统称为低NOx燃烧技术。
在各类降低NOx排放的技术中,低NOx燃烧技术采纳最广、相对简单、经济而且有效。
目前要紧有以下几种:1. 低过量空气燃烧程尽可能在接近理论空气量的条件下进行,随着烟气中过量氧的减少,能够抑制NOx的生成。
这是一种最简单的降低NOx排放的方式。
一样可降低NOx排放15-20%。
但如炉内氧浓度太低(3%以下),会造成浓度急剧增加,增加化学不完全燃烧热损失,引发飞灰含碳量增加,燃烧效率下降。
因此在锅炉设计和运行时,应选取最合理的过量空气系数。
2 .空气分级燃烧是将燃料的燃烧进程分时期完成。
在第一时期,将从主燃烧器供入炉膛的空气量减少到总燃烧空气量的70-75%(相当于理论空气量的80%),使燃料先在缺氧的富燃料燃烧条件下燃烧。
现在第一级燃烧区内过量空气系数α<1,因此降低了燃烧区内的燃烧速度和温度水平。
因此,不但延迟了燃烧进程,而且在还原性气氛中降低了生成NOx的反映率,抑制了NOx在这一燃烧中的生成量。
为了完成全数燃烧进程,完全燃烧所需的其余空气那么通过布置在主燃烧器上方的专门空气喷口OFA(over fire air)――称为"火上风"喷口送入炉膛,与第一级燃烧区在"贫氧燃烧"条件下所产生的烟气混合,在α>1的条件下完成全数燃烧进程。
由于整个燃烧进程所需空气是分两级供入炉内,故称为空气分级燃烧法。
弥补了简单的低过量空气燃烧的缺点。
在第一级燃烧区内的过量空气系数越小,抑制NOx的生成成效越好,但不完全燃烧产物越多,致使燃烧效率降低、引发结渣和侵蚀的可能性越大。
因此为保证既能减少NOx的排放,又保证锅炉燃烧的经济性和靠得住性,必需正确组织空气分级燃烧进程。
级燃烧方式改造现有煤粉炉,应付前墙或前后墙布置燃烧器的原有炉膛进行改装,将顶层燃烧器改作"火上风"喷口,将原先由顶层燃烧器送入炉膛的煤粉中形成富燃料燃烧,从而NOx生成。
低NOx燃烧技术专业资料
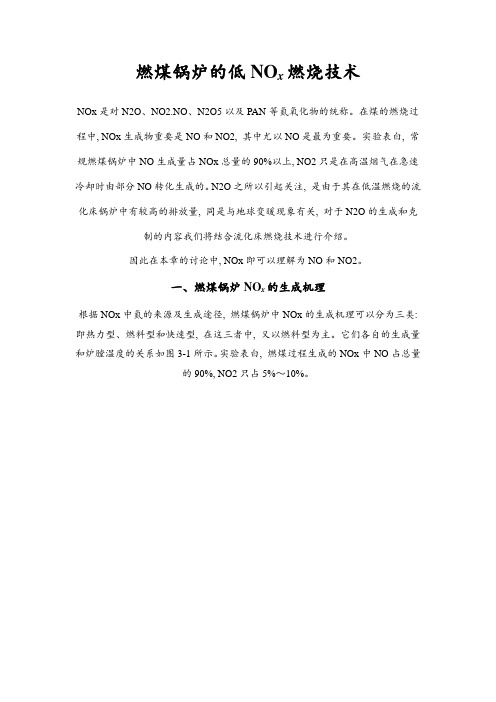
燃煤锅炉的低NO x燃烧技术NOx是对N2O、NO2.NO、N2O5以及PAN等氮氧化物的统称。
在煤的燃烧过程中, NOx生成物重要是NO和NO2, 其中尤以NO是最为重要。
实验表白, 常规燃煤锅炉中NO生成量占NOx总量的90%以上, NO2只是在高温烟气在急速冷却时由部分NO转化生成的。
N2O之所以引起关注, 是由于其在低温燃烧的流化床锅炉中有较高的排放量, 同是与地球变暖现象有关, 对于N2O的生成和克制的内容我们将结合流化床燃烧技术进行介绍。
因此在本章的讨论中, NOx即可以理解为NO和NO2。
一、燃煤锅炉NO x的生成机理根据NOx中氮的来源及生成途径, 燃煤锅炉中NOx的生成机理可以分为三类: 即热力型、燃料型和快速型, 在这三者中, 又以燃料型为主。
它们各自的生成量和炉膛温度的关系如图3-1所示。
实验表白, 燃煤过程生成的NOx中NO占总量的90%, NO2只占5%~10%。
1.热力型NOx热力型NOx是参与燃烧的空气中的氮在高温下氧化产生的, 其生成过程是一个不分支的链式反映, 又称为捷里多维奇(Zeldovich)机理→(3-1)O2O2→+O+NONN(3-2)2→+N+NOOO(3-3)2如考虑下列反映→+(3-4)N+NOHOH则称为扩大的捷里多维奇机理。
由于N≡N三键键能很高, 因此空气中的氮非常稳定, 在室温下, 几乎没有NOx生成。
但随着温度的升高, 根据阿仑尼乌斯(Arrhenius)定律, 化学反映速率按指数规律迅速增长。
实验表白, 当温度超过1200℃时, 已有少量的NOx生成, 在超过1500℃后, 温度每增长100℃, 反映速率将增长6~7倍, NOx的生成量也有明显的增长, 如图3-1所示。
但总体上来说, 热力型NOx的反映速度要比燃烧反映慢, 并且温度对其生成起着决定性的影响。
对于煤的燃烧过程, 通常热力型NOx不是重要的, 可以不予考虑。
一般来说通过减少火焰温度、控制氧浓度以及缩短煤在高温区的停留时间可以克制热力型NOx的生成。
低氮燃烧技术原理

低氮燃烧技术原理
低氮燃烧技术,是指在燃烧过程中将NOx的产生控制在一定范围内的一种技术。
对于燃煤锅炉,低氮燃烧主要是指减少燃料中的氮化合物的生成量。
燃烧过程中,生成的NOx有两种形态:一种是NOX,一种是氮氧化物。
当燃烧器中的空气过剩系数与燃料种类、负荷、煤种等因素相匹配时,NOX就会很低;当燃烧过程中存在高温区时,温度较高时,燃料中氮化合物被氧化成氮氧化氮,这样NOX就会急剧升高;当燃烧过程中存在还原性气氛时,燃料中的氮氧化合物被还原成氮气;当燃烧器结构设计不合理,空气过剩系数过大或燃料种类与负荷不匹配时,燃烧器中的氧气过量系数过小,这时燃烧反应生成的氮氧会以NOX形式向空气中逃逸。
为减少NOX排放,国内外均采用降低燃料氮化合物生成量的方法来控制锅炉的NOx排放。
主要措施是优化燃烧过程、改进空气系统及改善燃烧条件等。
1.合理选择燃料及负荷
合理选择燃料是控制锅炉NOx生成量的有效途径。
—— 1 —1 —。
低氮燃烧原理
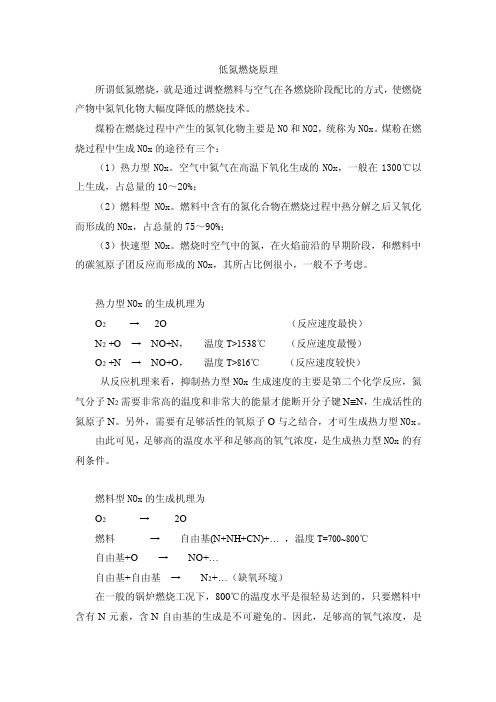
低氮燃烧原理所谓低氮燃烧,就是通过调整燃料与空气在各燃烧阶段配比的方式,使燃烧产物中氮氧化物大幅度降低的燃烧技术。
煤粉在燃烧过程中产生的氮氧化物主要是NO和NO2,统称为NOx。
煤粉在燃烧过程中生成NOx的途径有三个:(1)热力型NOx。
空气中氮气在高温下氧化生成的NOx,一般在1300℃以上生成,占总量的10~20%;(2)燃料型NOx。
燃料中含有的氮化合物在燃烧过程中热分解之后又氧化而形成的NOx,占总量的75~90%;(3)快速型NOx。
燃烧时空气中的氮,在火焰前沿的早期阶段,和燃料中的碳氢原子团反应而形成的NOx,其所占比例很小,一般不予考虑。
热力型NOx的生成机理为O2 →2O (反应速度最快)N2 +O →NO+N,温度T>1538℃(反应速度最慢)O2 +N →NO+O,温度T>816℃(反应速度较快)从反应机理来看,抑制热力型NOx生成速度的主要是第二个化学反应,氮气分子N2需要非常高的温度和非常大的能量才能断开分子键N≡N,生成活性的氮原子N。
另外,需要有足够活性的氧原子O与之结合,才可生成热力型NOx。
由此可见,足够高的温度水平和足够高的氧气浓度,是生成热力型NOx的有利条件。
燃料型NOx的生成机理为O2 →2O燃料→自由基(N+NH+CN)+… ,温度T=700~800℃自由基+O →NO+…自由基+自由基→N2+…(缺氧环境)在一般的锅炉燃烧工况下,800℃的温度水平是很轻易达到的,只要燃料中含有N元素,含N自由基的生成是不可避免的。
因此,足够高的氧气浓度,是生成燃料型NOx的有利条件根据以上分析,NOX生成条件总结如下:(1)首先要生成自由N原子或含N自由基:对热力型NOx,其来源为N≡N,破坏分子键需极高的温度来提供足够的能量;对燃料型NOx,其来源为含N有机物热解,键能小,对温度要求低。
(2)其次要有氧与自由N原子或含N自由基结合:相对与N,氧更倾向于与C、H等结合,只有氧浓度较高时,NOx才易生成;缺氧环境下的自由N或含N自由基,会结合成N≡N,从而减少自由N。
低NOx燃烧技术原理及其技术性能分析

低 NOx 燃烧技术原理及其技术性能分析摘要:简要介绍了燃煤电厂NOx产生机理以及目前主流的低NOx燃烧技术原理。
关键词:低NOx燃烧技术;燃烧调整;锅炉燃烧效率;1低NOx燃烧技术原理及技术性能分析1.1空气分级燃烧空气分级燃烧技术(Air Staging)最早是在美国发展起来的,是目前国内外普遍应用,比较成熟的低NOx燃烧技术。
其基本原理是将燃烧所需空气分成两级送入,一级送入过量空气系数小于1,对于燃煤锅炉一般为理论空气量的70%~75%。
其余空气经由布置在燃烧器上游的专门空气喷口OFA(Over Fire Air)送入炉膛继续完成燃烧。
人为地形成准双区燃烧,即主燃烧区和燃烧完全区[6]。
主燃烧区内由于缺氧使燃烧处于“富燃料燃烧(贫氧燃烧)”状态,燃烧速度和温度降低,抑制了热力型NOx的生成。
此外,燃烧过程中生成的CO、NO、以及燃料中氮分解产生的CO、NO、HCN和NH等化合物相互复合作用同样也抑制了3燃料型NOx的生成。
燃烧完全区内燃烧所需其余空气以二次空气输入,调整过量空气系数(过量空气系数大于1)使未燃尽燃料燃烧完全。
此时虽然送入空气量较多,同样会使一些中间产物被氧化成NO,但由于空气分级技术此时反应区已由温度高的主燃烧区转移到温度低的燃烧完全区,抑制了燃料型NOx的生成。
采用空气分级燃烧技术后可使NOx排放量降低30%~60%。
尽管空气分级燃烧弥补了简单的降低过量空气系数燃烧所导致的燃料未完全燃烧损失和飞灰含碳量增加的缺点,但是,若主燃烧区,燃烧完全区两级空气比例分配不合理,或者燃烧混合条件不好,则会增加不完全燃烧带来的损失。
同时,主燃烧区的还原性气氛将导致灰熔点降低从而引起锅炉结渣和受热面腐蚀。
1.2燃料分级燃烧燃料分级燃烧通常采用的形式是燃料再燃烧技术,将燃烧过程设在三个区(主燃区、再燃区和燃尽区)进行,也称为三级燃烧技术,如图2-3所示。
其所依据原理为主燃区形成的NOx会在次燃烧区和烃根CHi、未完全燃烧产物(CO、C、。
低氮氧化物燃烧技术

低氮氧化物燃烧技术:低氧燃烧技术,降低助燃空气预热温度,烟气循环燃烧,分段燃烧技术,再燃技术,浓淡燃烧技术。
选择性催化还原法脱硝:主要以氨做还原剂,通常催化剂安装在独立的反应器内,反应器位于省煤器之后,或者空气预热器之前。
4NH3+4NO+O2--4N2+6H2O 8NH3+6NO2--7N2+12H2O
选择性非催化还原法:尿素或氨基化合物注入烟气作为还原剂将NOX还原为N2。
4NH3+6NO--5N2+6H2O CO(NH2)2+2NO+0.5O2--2N2+CO2+2H2O
燃烧法控制VOCS污染,燃烧工艺:直接燃烧,热力燃烧,催化燃烧
生物法控制VOCS污染:是附着在滤料介质中的微生物在适宜的环境条件下,利用废气中的有机成分作为碳源和能源,维持其生命活动,并将有机物同化为CO2.H2O和细胞质的过程。
VOCS从气相传递到液相,VOCS从液相扩散到生物膜表面,VOCS在生物膜内部的扩散,生物膜内的降解反应,代谢产物排出生物膜。
生物洗涤塔:悬浮生长,连续相。
经有机物驯化的循环液有洗涤塔顶部布液装置喷淋而下,与沿塔而上的气相主体逆流接触,使气相中的有机物和氧气转入液相,进入再生器,被微生物氧化分解,得以降解。
生物滴滤塔:附着生长,非连续相。
VOCS气体由塔底进入,在流动过程中与已接种挂膜的生物滤料接触而被净化。
生物过滤塔:附着生长,非连续相。
VOCS由塔顶进入过滤塔,在流动过程中与已接种挂膜的生物滤料接触而被净化,净化后的气体由塔底排出。
集气罩的基本形式:密闭罩,排气柜,外部集气罩,接受式集气罩。
- 1、下载文档前请自行甄别文档内容的完整性,平台不提供额外的编辑、内容补充、找答案等附加服务。
- 2、"仅部分预览"的文档,不可在线预览部分如存在完整性等问题,可反馈申请退款(可完整预览的文档不适用该条件!)。
- 3、如文档侵犯您的权益,请联系客服反馈,我们会尽快为您处理(人工客服工作时间:9:00-18:30)。
收稿日期:2000-09-08;修订日期:2000-11-27作者简介:朱 彤(1969-),男,浙江杭州人,同济大学副教授,博士.文章编号:1001-2060(2001)03-0328-04低NO x 高温空气燃烧技术朱 彤1,饶文涛2,刘敏飞1,张毅勐1,张鹤声1(1.同济大学热能工程系,上海 200092;2.上海宝钢研究院设备研究所,上海 201900)摘 要:低NO x 高温空气燃烧技术将传统的低NO x 燃烧技术与高温蓄热式燃烧系统有机地结合起来,具有热效率高、炉内温度分布均匀、NO x 排放量低等特点。
本文介绍了高温空气燃烧技术,重点分析了高温空气燃烧技术中的低NO x 排放的原理,并对两种采用烟气再循环和分级燃烧技术的低NO x 高温空气燃烧器进行阐述。
关键词:低NO x ;高温空气燃烧;蓄热式燃烧器;燃烧技术中图分类号:TK223.23 文献标识码:A1 引言80年代初,Hot Work 公司和British Gas 公司开发了一种在工业炉和锅炉上节能潜力巨大的陶瓷蓄热式燃烧器(RCB ———Regenerative Ceramic Burner ),用于小型玻璃熔炉上。
其后,RCB 被应用于美国和英国的钢铁和熔铝行业中。
尽管当时这种燃烧器具有NO x 排放量大和系统可靠性差等问题,但由于它能使烟气余热利用达到接近极限的水平,节能效益巨大,因此在美国、英国、日本等国家得以推广应用[1]。
90年代初,蓄热式空气预热技术在我国的工业炉窑上得到成功的应用,并研制出了自己的专利技术,取得了显著的经济效益。
有关高校、研究部门还对蓄热体材料、结构、传热机理等进行了研究[2]。
但当时人们并没有把它和新型燃烧技术联系起来,仅仅当作研制一种用于余热回收的特殊烧嘴,因此,也就没有把这种燃烧方式与高温燃烧所可能导致的大量NO x 排放相联系[3]。
本文着重介绍高温空气燃烧技术中的低NO x 技术及其原理。
2 高温空气燃烧技术蓄热式燃烧系统(High -cycle Regenerative c om -bustion System 简写为HR S )一般要求烧嘴成对安装,可相对布置,也可在同一侧,见图1。
当烧嘴A 工作时,加热工件后的高温废气经由烧嘴B 排出,加热蓄热体B ,将排烟温度降低到200℃以下甚至更低。
经过一定时间间隔(20s ~200s )后,切换阀使助燃空气流经蓄热体B ,充分吸收废气所排放的显热,通过烧嘴B 完成燃烧过程;同时,烧嘴A 和蓄热体A 转换为排烟和蓄热装置。
通过这种交替运行方式,实现蓄热式燃烧和空气的高温预热,可见,助燃空气吸收废气的显热愈多,则系统热效率愈高。
日本研究人员用蜂窝式蓄热体回收废气余热,使被加热的空气温度达到1000℃~1100℃,而加热炉的排烟温度降为150℃~200℃,大大提高了炉子的热效率。
图1 蓄热式燃烧系统原理图然而依据现有理论可知,随着送入炉膛的空气温度提高,势必提高燃料燃烧的理论燃烧温度,将使热力型NO x 的排放量急剧增大,与环境保护的要求背道而驰。
如何解决这个矛盾是摆在热能工作者面前的一个攻关课题。
80年代末,日本人提出了一种新概念燃烧技术———高温空气燃烧技术[4](High Temperature Air Combustion 简写为HTAC ,或Highly Preheated Air Combustion 简写为HPAC ),该技术主要包括两项基本技术手段:一是燃烧用空气最大限度回收(或称极第16卷(总第93期) 热能动力工程 2001年5月限回收)废气的显热;二是采用燃料在低氧气氛下燃烧技术来降低NO x的生成量。
为防止蓄热器和切换阀的烟尘粘污,目前应用HTAC技术的工业炉中绝大部分使用的是气体燃料。
在日本一些现代化冶金企业的商业应用结果表明:HATC技术可节能40%~50%,单位能耗量减少30%,NO x排放量降低到40~70mg/m3的水平,炉膛内温度分布均匀,相关生产设备的尺寸大幅度减小,燃烧噪音降低。
3 低NO x燃烧技术燃料燃烧过程中生成的NO x,按其形成可分为三种:热力型NO x、快速型NO x和燃料型NO x。
气体燃料燃烧过程主要生成的是热力型NO x。
传统的抑制热力型NO x的燃烧技术有:低氧燃烧法、分段燃烧法、烟气再循环法等。
这三种方法均可理解为偏离化学当量燃烧法,即在局部的燃烧区域中化学当量比不在燃烧反应化学当量比范围,从而抑制NO x的生成。
在高温空气燃烧技术中,由于燃烧用空气被预热到很高的温度(≥800℃),大大超过了燃气的着火温度,因而燃气只要遇到氧就可发生剧烈化学反应,着火、燃烧的稳定性极好,日本长谷川敏明对丙烷燃烧过程的研究表明:当空气温度高于900℃、含氧量5%时,仍可获得稳定的燃烧火焰[5]。
假如助燃空气中氧浓度比较高,则燃料中的C、C m H n、CO、H2等可燃成分与氧混合加快,反应生成C O2和H2O,同时也将大量生成NO x。
假如助燃空气中氧浓度比较低,则燃烧过程将受到燃气与氧的混合过程控制。
由于燃气与氧气的燃烧反应活化能低于氧原子与氮气的反应活化能,所以,燃气首先与氧气发生燃烧反应;只有当氧气有剩余时,才进行氧原子和氮原子的反应,生成NO x。
只要合理控制炉内氧浓度的分布,使氧浓度在整个炉膛空间分布均匀且较低,则燃烧过程将充满整个炉膛空间,不会出现局部炽热点,抑制了燃烧过程的最高温度,使整个炉膛内温度分布均匀。
Jianwei Yuan和Ichiro Naruse的数值模拟结果表明:氧浓度为4%时(采用氮气稀释空气),火焰最高温度与平均温度的比值不大于1.1,而氧浓度为21%时,燃烧器出口附近火焰最高温度与平均温度的比值为1.57[6]。
与传统火焰温度分布相比,高温低氧燃烧过程中火焰的最高温度相对较低,但整个炉膛内的平均温度较高,强化了炉内换热。
实际研究表明,当燃烧温度低于1300℃时,热力型NO x生成量比较少。
这样,尽管空气被预热到很高温度,但由于火焰的最高温度相对较低,则抑制了NO x的生成,如空气预热到1150℃,空气含氧由21%降到2%时,NO x的生成量由3750mg/m3减少到54mg/m3,见图2[7]。
图2 不同含氧量下空气预热温度与氮氧化物生成量关系4 低NO x高温空气燃烧器4.1 FDI型燃烧器和FL OX型燃烧器FDI(Fuel Direct Injection)型燃烧器是日本研制的低NO x高温空气燃烧器[8],热功率多在1MW以下,见图3。
它主要是利用一组喷管作为燃烧器的烧嘴,所喷出的高速气流卷吸炉内的烟气,形成炉内烟气再循环,从而降低空气射流中的氧浓度,抑制NO x的生成。
实验研究表明,提高空气射流速度,或者扩大空气喷口之间的间距,并将喷管平行布置(空气喷管交角为0°),以推迟燃气与空气的混合,都可以减少NO x的排放,试验结果见图4。
图3 FDI型燃烧器结构·329·第3期 朱 彤,等:低NO x高温空气燃烧技术图4 空气喷口距离与空气流速对氮氧化物生成量的影响德国研制的FLOX 燃烧器[9](Flameless OxidationBurner )与FDI 燃烧器的工作原理一致,将普通高速燃烧器的环形空气喷口改为一组围绕燃气喷口的多个小喷口,扩大空气射流与炉内烟气的接触面积,增大空气射流对炉内烟气的卷吸量,降低空气射流中的氧浓度,并且通过加大空气喷口间距推迟空气与燃气的混合,从而降低火焰的最高温度。
由图5可见,空气预热到750℃,普通高速燃烧器的火焰最高温度高于2000℃,而FLOX 燃烧器的火焰最高温度只有1400℃左右。
因此,FLOX 燃烧器的NO x 排放量较低是完全可以理解的。
图5 普通燃烧器与FLOX 燃烧器的比较4.2 HRS -DL 型燃烧器日本研制的HRS -DL 型燃烧器结构[10]见图6,热功率多在5MW 以下。
其特点是:(1)空气从烧嘴中心区直接以高速喷出,促进炉内烟气再循环;(2)燃气喷口不放在烧嘴砖通道内,而是缩在烧嘴砖的后面,有效地防止了蓄热期流入的高温烟气对喷口的氧化作用或结焦;(3)一次燃气(F1)沿烧嘴砖通道的内表面喷出,二次燃气(F2)是在烧嘴通道的端面直接喷向炉内,调节F1和F2的比例可以使火焰的形态和炉子的内形相适应。
图6 HRS -DL 型燃烧器结构从应用结果来看,空气流速越高,NO x 含量越低。
F1方式主要用于冷炉升温(炉温800℃以下),正常情况下(炉温800℃以下)就切换成F1和F2组合方式。
F1的燃烧属于富氧燃烧,在高温条件下,将很快完成,同时生成一部分NO x ,所以,要求一次燃气量F1比F2少得多。
燃烧后的烟气在流经优化设计的喷口后,形成高速烟气射流和周围的卷吸回流流动。
而大量燃气则通过二次燃气通道F2喷入炉内,此时,二次燃气将与含氧浓度较低的烟气混合。
尽管使用了高温空气,但没有出现局部的炽热高温区,燃烧是在温度相当均匀的区域内进行,抑制了NO x 的生成。
综上所述,HRS -DL 型燃烧器综合采用了分级燃烧和烟气再循环的技术手段。
总之,低NO x 高温空气燃烧器与传统的低NO x 燃烧器相比,其喷口结构基本相似,但射流速度更高,喷口间距更大,以保证燃气与空气混合点的位置在更低的氧浓度范围内,这是因为空气预热后的温度远高于燃气着火的温度,保证了燃气着火和燃烧的稳定性。
5 结语低NO x 高温空气燃烧技术将传统的低NO x 燃烧技术与蓄热式燃烧系统有机地结合起来。
蓄热式燃烧系统不仅最大限度回收烟气所排放出的显热,提高助燃用空气的温度,而且它为燃气低氧燃烧过程中的着火、燃烧的稳定性提供了保障,因而可以组织过量空气系数略大于1.0的低氧燃烧,大幅度降低NO x 的排放。
高温低氧空气燃烧技术正在全世界引起极大的关注,在气体、液体燃料燃烧技术开发中具有极大的潜力,在固体燃料气化、生物质燃料的(下转第321页)·330·热能动力工程 2001年达到某一中间浓度所需的时间,t=mm s ·lnC∞-C0caC∞-C如果一个反应系统m s为1kg/s,循环倍率为20,那么系统的物料量m应在100kg以上,并假定初始亚硫酸钙和CaO的含量均为零,由式(10)可粗略计算出亚硫酸钙和CaO达到与平衡浓度的不同比值所需时间,见表3。
表3 亚硫酸钙和CaO达到某一中间浓度所需时间(初始浓度均为零)所达平衡浓度的百分比/%7080909599所需时间/s120161230300460 事实上,在动态过程中,亚硫酸钙的生成率N*sul 和脱硫效率ηs不是常数,一个脱硫反应所生成的固体物也不可能瞬间反应在系统中混合均匀,因此实际过程中所需要的时间比计算值长,对实际过程上述计算结果还需进行修正。