变形铝及铝合金板带材缺陷
铝合金结构焊接质量缺陷及处理方法

铝合金结构焊接质量缺陷及处理方法铝合金结构在工程领域中被广泛应用,而焊接是制造铝合金结构中常用的连接方法之一。
然而,焊接过程中可能会出现质量缺陷,影响结构的强度和稳定性。
本文将介绍一些常见的焊接质量缺陷及其处理方法。
1. 焊缝裂纹:焊缝裂纹是焊接过程中常见的质量缺陷之一。
裂纹可能出现在焊缝中或与焊缝平行。
裂纹的形成可能是由于焊接过程中的应力集中、材料的变形或焊缝设计不当等原因引起的。
处理方法包括优化焊接参数、使用合适的焊接材料和设计合理的焊缝形状。
2. 焊接变形:焊接过程中,热量会引起材料的膨胀和收缩,导致结构产生变形。
焊接变形可能会导致尺寸偏差、强度降低或导致零件之间的不匹配。
为了减少焊接变形,可以采取以下措施:使用预热、控制焊接速度、合理排布焊接顺序和使用局部焊接等方法。
3. 焊接气孔:焊接气孔是焊接过程中可能出现的气体残留物。
气孔的存在会降低焊缝的强度和密封性。
避免气孔的方法包括:保证焊接材料和焊接区域的清洁、使用适当的焊接电流和气体保护、控制焊接速度等。
4. 焊接夹渣:焊接夹渣是指焊缝中残留的金属或非金属夹杂物。
夹渣的存在会降低焊缝的强度和质量。
为了避免焊接夹渣,应选择合适的焊接材料和填充材料,并确保焊接区域干净。
5. 焊接缩孔:焊接缩孔是指焊缝中存在的空洞或孔洞。
焊接缩孔可能是由于焊接过程中的材料收缩过程中产生的缺陷引起的。
控制焊接工艺参数、选择合适的填充材料和使用适当的焊接技术可以减少焊接缩孔的发生。
综上所述,了解铝合金结构焊接质量缺陷及其处理方法对于确保结构的质量和稳定性至关重要。
通过优化焊接参数、合理设计焊缝和采取适当的焊接技术,可以有效地减少焊接质量缺陷的发生。
铝合金压铸常见缺陷及形成原因

铝合金压铸件常见外观缺陷
外观:网状毛翅原因
特征
产生原因
防止措施
1 压铸模型腔表面龟裂
1 加强模具的日常保养
2
压铸模材质不当或热处理工艺 不正确
2
确选用压铸模材料及热处理工艺
网状发丝一样凸
3 压铸模冷热温差变化大
起或凹陷的痕迹,随
压铸次数增加而不断
扩大和延伸。
4 浇注温度过高
压铸模要定期或压铸一定次数后退 3 火,消除内应力;合理选择模具冷
3
分型面上杂物未清理干净
3 清洁型腔及分型面
4 模具强度不够造成变形
4 增加模具厚度和支撑柱
5
镶块、滑块磨损与分型面不平 齐
5
修整模具
铝合金压铸件常见内部缺陷 内部:气孔
特征:解剖后外观检查或探伤检查,气孔具有光滑的表面、形状为圆形。
铝合金压铸件常见内部缺陷
内部:气孔原因
特征
产生原因
防止措施
合金液导入方向不合理或金属
狭小而长,在外力作
用下有发展趋势。冷 4 .模具,特别是型芯温度太低 4 提高模温,模温要稳定
裂:开裂处金属没被氧
化.热裂:开裂处金属已
被氧化。
5
铸件壁存有剧烈变化之处,收 缩受阻,尖角位形成应力
5
改变铸件结构,加大圆角,加大出 模斜度,减少壁厚差
6 留模时间过长,应力大
6 缩短开模及抽芯时间
7 顶出时受力不均匀
7
变更或增加顶出位置,使顶出受力 均匀
铝合金压铸件常见外观缺陷
外观: 变形、磕碰
变形
磕 碰 前
磕 碰 后
特征:压铸件几何形状与图纸不符或整体变形/局部变形。
铝合金挤压型材缺陷明细表
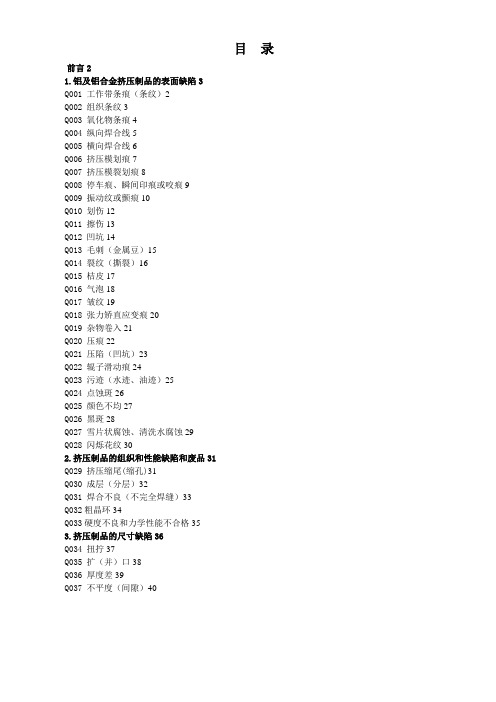
目录前言21.铝及铝合金挤压制品的表面缺陷3Q001 工作带条痕(条纹)2Q002 组织条纹3Q003 氧化物条痕4Q004 纵向焊合线5Q005 横向焊合线6Q006 挤压模划痕7Q007 挤压模裂划痕8Q008 停车痕、瞬间印痕或咬痕9Q009 振动纹或颤痕10Q010 划伤12Q011 擦伤13Q012 凹坑14Q013 毛刺(金属豆)15Q014 裂纹(撕裂)16Q015 桔皮17Q016 气泡18Q017 皱纹19Q018 张力矫直应变痕20Q019 杂物卷入21Q020 压痕22Q021 压陷(凹坑)23Q022 辊子滑动痕24Q023 污迹(水迹、油迹)25Q024 点蚀斑26Q025 颜色不均27Q026 黑斑28Q027 雪片状腐蚀、清洗水腐蚀29Q028 闪烁花纹302.挤压制品的组织和性能缺陷和废品31Q029 挤压缩尾(缩孔)31Q030 成层(分层)32Q031 焊合不良(不完全焊缝)33Q032粗晶环34Q033硬度不良和力学性能不合格353.挤压制品的尺寸缺陷36Q034 扭拧37Q035 扩(并)口38Q036 厚度差39Q037 不平度(间隙)40前言1.在铝及铝合金的挤压生产过程中,产生的各种缺陷,主要可分为三类,即挤压制品的表面缺陷、挤压制品的形位尺寸缺陷、挤压制品的内部组织缺陷。
2.挤压制品的表面缺陷,在生产现场产生最多,废品率也最高。
最主要的有条纹(色差)、毛刺(金属豆)、擦伤、划伤、挤压裂纹、起皮、气波、挤压模纹(或假停车痕)、纵向焊合线、模向焊合线、点蚀斑、矫直辊痕、污迹(水迹、油迹)等。
3.挤压制品的尺寸缺陷,在生产中所占废品率也很高,主要有尺寸不合格、弯曲、扭拧、波浪、扩(并)口、间隙起标等。
4.挤压制品的组织缺陷主要有缩尾、粗晶环、成层和焊合不良等。
这些缺陷往往使整根、整批产品报废,必须注意防止,特别是工业铝材的生产中应该特别注意。
5.下面以列表的方式对各种缺陷的名称(英文对照按美国AA标准和数据技术语篇)、起因、定义、特征及对策进行较为全面的说明,供广大技术人员、生产人员、质检人员作为工作和学习参考。
铝及铝合金板GB-T3194-1998

铝及铝合金板、带材厚度及其允许偏差(摘自GB/T3194-1998) 铝及铝合金普通级板、带材厚度允许偏差
航空工业用铝合金高精级板带材厚度允许偏差
非航空工业用铝合金高精级板带材厚度允许偏差
注:1 GB/T3194-1998将产品分为板材、带材、大规格板(宽度大于1500mm或长度大于4000mm),变断面板(厚度沿板材方向均匀变化的板)。
2尺寸分级:非航空工业用板材厚度、航空工业用板材厚度、宽度、长度、不平度等项目分为普通级和高精级;对角线、侧边弯曲度只有高精级;带材只有厚度、宽度指标分普通级与高精级,变断面板材不分级。
3航空工业用高精级板材的合金牌号为:2014、2024、201、2A14、2A12、2A11、7075、7A04、7A09等。
4普通级板带厚度允许偏差,如果对于非对称偏差的板材,需要对称偏差时,由双方协商采用相应带材的偏差。
5航空工业用和非航空工业用高精级板、带材厚度允许偏差采用单向偏差“+”或“-”时,其值为表中数值的2倍;表中未规定部分的偏差按本表普通级的相应规定。
6厚度大于40mm普通级板材,在用整个铸块轧制后,不切头尾,整块交货。
7变断面板材公称长度以薄端、厚端的公称厚度和平均楔形度计算。
板带轧制制品表面缺陷产生的主要原因

缺陷名称热轧层裂张嘴,缠辊夹灰,起皮,起泡裂边,裂纹,分层辊印及压抗,金属以及非金属压入划伤及擦伤表面腐蚀,油斑以及水迹产生的主要原因1铸锭的质量不好,存在铸造弱面2轧制表面变形3润滑条件差1铸锭表面质量不好,以及铸锭中的气孔,锁孔,冷隔以及夹杂物在轧制过程中暴露所致2坯料铣面的时候刀痕太深,来料划伤严重,在划沟内落入了脏物以及退火是氧化;有显微裂纹,并沿显3包铝板蚀洗,焊合不好;4铸锭加热温度过高,时间过长或者吸气5辊面,轧件表面粘有脏物6冷却润滑剂不干净,或者过滤精度低1铸锭中有气孔,缩孔或者脆性杂物已经铸造裂纹,热轧后坯料内部产生裂纹2铸锭加热的过程中温度过高,气氛不良产生裂纹,加热温度过低,边部冷却太快产生裂纹3热轧时候加工率分配不合理,辊形控制不好,冷却润滑不良,延伸不均匀,热轧立辊轧边不当冷却张力4铝合金边部包铝或者包铝焊合不好5轧制时表面层与里层延伸不一致6坯料边部有小裂口,褶皱等缺陷7轧前退火不够,边部晶粒粗大或者氧化严重未来得及铣干净1轧辊扎件表面沾有金属以及氧化物等杂物,形成压入或轧后杂物脱离表面形成压痕2轧辊表面硬度低,或者磨损严重出现麻坑,或压折,粘辊后出现的伤痕3冷却润滑剂不干净,或者过滤的精度低1辊道货其他接触部位有坚硬物2扎件出辊的速度,辊道或卷取机速度不同步,冷轧张力辊,压紧辊不转造成的划伤3卷曲过松或者过紧,冷轧开卷张力过大,或者张力波动哎大,使带材层间相对错动1乳液或者润滑油有腐蚀性,或退火性能差产生油斑2混入了机械油,冷却润滑剂不干净3酸洗时带材表面残留水或者酸4产品放置的时间过长,周围空气潮湿或者有害气体的腐蚀裂纹,并沿显微裂纹氧化立辊轧边不当冷却张力过大。
铝合金加工材料的缺陷

铝合金加工材料的废品(缺陷)及成品率控制铝合金加工材料在生产过程中或经成品检测后,发现其质量指标有一项或多项不符合技术标准或技术协议,影响使用性能的,称为产品缺陷。
根据缺陷对产品质量和使用性能的影响可分为严重的、轻微的两种:轻微的缺陷是可修复的缺陷,经返工或修复后仍可满足使用要求或基本符合技术标准的规定,是可以交付使用的,如表面气泡、擦划伤、印痕、起皮等。
严重的缺陷是指不可修复的缺陷,一般称为废品或绝对废品,如过烧、贯穿气孔、裂纹、性能不合格、尺寸超差等。
废品是不能出厂交付使用的,应废弃或重熔。
2.1.22铝合金加工材料废品(废料)的分类铝合金加工材料的废品,也称废料。
废品一般分为几何废品和技术(工艺)废品。
几何废品是铝合金加工材料在生产过程中产生的不可避免的废料,如挤压的残料,铸锭的切头、切尾,拉伸时制品两端的夹头,厚板的切头、切尾,板、带箔材的切边和切头、切尾,模缎件的切飞边,铸锭和制品切取定尺、短料和切头、切尾的锯口消耗的铝屑,切取必要的试样一级试模时消耗的铝锭等。
几何废料是不可避免的,只能尽量减少,而不可能消除。
技术废品(废料)也称工艺废品(废料),是铝合金加工材料在生产过程中因工艺不合理、设备出现问题,工人操作不当而产生的人为废品。
它和几何废品不同,通过技术改进、加强管理,可以有效地克服和杜绝技术废品的产生。
技术废品可以分为以下几种:(1)组织废品。
如过烧、粗晶环、粗大晶粒、缩尾、夹渣、内部裂纹、贯穿气孔、疏松、氧化膜、流纹不顺等。
(2)力学性能不合格废品。
如强度、硬度太低,不符合国家标准;或塑性太低,没有充分软化,不符合技术要求。
(3)表面废品。
如成层、气泡、外表裂纹、橘皮、组织条纹、黑斑、纵向焊合线、横向焊合线、擦划伤、金属压入等。
(4)几何尺寸废品。
如波浪、扭拧、弯曲、平面间隙、尺寸超差和形位精准不符合技术标准要求等。
2.1.2.2成品率的计算方法成品率是企业的一个主要经济质量指标,成品率的高低反映一个企业的技术质量、管理水平的好坏。
铝板卷常见质量缺陷及原因实图讲解

铝板卷常见质量缺陷及原因实图讲解一个月的铝锭带你快速致富:上月你订10吨恭喜你夫妻双双欧美游;上月你订50吨,恭喜老板哈弗H6包牌带回家;上月订100吨,4S店奥迪A4提回家;上月订200吨,宝马5系相中哪款带回家!上个月订1000吨,郊区别墅是你家……上个月你对他爱搭不理,这个月铝价让你高攀不起!虽是玩笑之意,但也传达着市场的情绪。
铝价这种上涨的趋势,使下游很多企业都在观望。
闲暇之余,适合来点干货。
距离上次为大家推送《怎样分辨铝箔好坏?史上最全铝箔质量缺陷集锦 | 实图讲解》已有些时日,今天,小慧带着“涨姿势”系列继续归来,为大家带来的是铝板卷常见的缺陷及原因,赶紧收起来吧!1.复合层脱落定义:复合材料包铝层离开基体并脱落形成的不规则缺陷。
主要原因:包铝层与基体金属之间有异物,导致包铝层无法焊合,并进一步产生包铝层脱落。
2.压花由于带材折皱、断带等原因导致轧辊辊面不规则色差在轧制过程中周期性地印到带材表面的色差现象。
3.波浪边部波浪和中间波浪示意图二肋波浪和碎浪示意图定义:板、带材由于不均匀变形而形成的各种不同的不平整现象的总称。
板、带边部产生的波浪称为边部波浪,中间产生的波浪称为中间波浪,在中间和边部之间的既不在中间又不在两边的波浪称为二肋波浪,尺寸较小且通常呈圆形的波浪称为碎浪。
主要产生原因:a. 辊缝调整不平衡,辊型控制不合理;b. 润滑冷却不均,使板、带变形不均;c. 道次压下量分配不合理;d. 来料板型不良;e. 卷取张力使用不均。
4.翘边定义:经轧制或剪切后,带材边部翘起。
主要产生原因:a. 轧制时压下量过大;b. 轧制时润滑油分布不均匀;c. 剪切时剪刃调整不当。
5.侧边弯曲定义:板、带的纵向侧边呈现向某一侧弯曲的非平直状态。
主要产生原因:a. 轧机两端压下量不一样;b. 轧机送料不正;c. 板、带来料两侧厚度不一致;d. 轧辊预热不良或乳液流量控制不当;e. 工艺润滑剂浓度过高,产生打滑;f. 剪切前带材存在波浪,经剪切后波浪展开。
铝合金43种缺陷
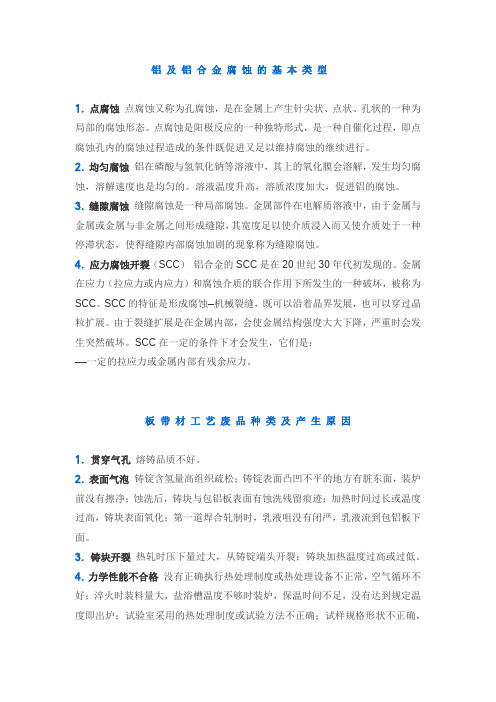
铝及铝合金腐蚀的基本类型1.点腐蚀点腐蚀又称为孔腐蚀,是在金属上产生针尖状、点状、孔状的一种为局部的腐蚀形态。
点腐蚀是阳极反应的一种独特形式,是一种自催化过程,即点腐蚀孔内的腐蚀过程造成的条件既促进又足以维持腐蚀的继续进行。
2.均匀腐蚀铝在磷酸与氢氧化钠等溶液中,其上的氧化膜会溶解,发生均匀腐蚀,溶解速度也是均匀的。
溶液温度升高,溶质浓度加大,促进铝的腐蚀。
3.缝隙腐蚀缝隙腐蚀是一种局部腐蚀。
金属部件在电解质溶液中,由于金属与金属或金属与非金属之间形成缝隙,其宽度足以使介质浸入而又使介质处于一种停滞状态,使得缝隙内部腐蚀加剧的现象称为缝隙腐蚀。
4.应力腐蚀开裂(SCC)铝合金的SCC是在20世纪30年代初发现的。
金属在应力(拉应力或内应力)和腐蚀介质的联合作用下所发生的一种破坏,被称为SCC。
SCC的特征是形成腐蚀—机械裂缝,既可以沿着晶界发展,也可以穿过晶粒扩展。
由于裂缝扩展是在金属内部,会使金属结构强度大大下降,严重时会发生突然破坏。
SCC在一定的条件下才会发生,它们是:——一定的拉应力或金属内部有残余应力。
板带材工艺废品种类及产生原因1.贯穿气孔熔铸品质不好。
2.表面气泡铸锭含氢量高组织疏松;铸锭表面凸凹不平的地方有脏东面,装炉前没有擦净;蚀洗后,铸块与包铝板表面有蚀洗残留痕迹;加热时间过长或温度过高,铸块表面氧化;第一道焊合轧制时,乳液咀没有闭严,乳液流到包铝板下面。
3.铸块开裂热轧时压下量过大,从铸锭端头开裂;铸块加热温度过高或过低。
4.力学性能不合格没有正确执行热处理制度或热处理设备不正常,空气循环不好;淬火时装料量大,盐浴槽温度不够时装炉,保温时间不足,没有达到规定温度即出炉;试验室采用的热处理制度或试验方法不正确;试样规格形状不正确,试样表面被破坏。
5.铸锭夹渣熔铸品质不好,板片内夹有金属或非金属残渣。
6.撕裂润滑油成分不合格或乳液太浓,板片与轧辊间产生滑动,金属变形不均匀;没有控制好轧制率,压下量过大;轧制速度过大;卷筒张力调整得不正确,张力不稳定;退火品质不好;金属塑性不够;辊型控制不正确,使金属内应力过大;热轧卷筒裂边;轧制时润滑不好,板带与轧辊摩擦过大;送卷不正,带板一边产生拉应力,一边产生压应力,使边沿产生小裂口,经多次轧制后,从裂口处继续扩大,以至撕裂;精整时拉伸机钳口夹持不正或不均,或板片有裂边,拉伸时就会造成撕裂;淬火时,兜链兜得不好或过紧,使板片压裂,拉伸矫直时造成撕裂。