粉体的合成制备方法
11粉体材料及其制备技术全文

V
x
2 w
(
s
f
)g
18
测量方法
一束光照射到样品池, 内部的粉末悬浮体对光 产生吸收
随着时间的延续,悬浮液 中的颗粒逐渐沉积,悬浮 液的透光性随之增强。
于是就得到了光吸收率随时间的变化关系曲线
由于沉降时间与颗粒 尺寸存在一定的关系, 因此可以根据这一曲 线确定颗粒尺寸的分 布。 不难理解,沉降法实质上是一种间接的粉体 粒度分析方法。
颗粒浓度低,以至于在探测区内以单颗粒的形式 出现。
颗粒通过均匀的场区,从孔中心处穿过,并且颗 粒尺寸不大于孔的半径。
与电解质相比颗粒有较大的有效电阻。实际上, 通常也是这种情况,因为颗粒有表面电势,即使 是导电的颗粒也会有较大的电阻。
如果满足了以上条件,从而使得脉冲电压的大 小正比于颗粒的体积,就可以通过测量脉冲电压的 大小以及出现的频率来确定颗粒的体积及其分布。
在大量的研究中形成了一个共识:材料晶粒越细, 材料的力学性能就越优越。因此,人们在陶瓷及 粉末冶金领域正不断地努力,力求制备出更细微 的粉末原料。
粉末材料除了作为烧结材料的原料外,还以填充 物的形式大量使用。
粉末材料还可以直接应用。
粉体材料的应用领域举例
❖农业:粮食加工、化肥、粉剂农药、饲料等 ❖矿业:金属矿石的粉碎研磨、非金属矿的深加工等 ❖冶金:粉末冶金、冶金原料处理等 ❖印刷:油墨生产、复印用的碳粉等 ❖医药:粉剂、中药精细化、喷雾施药 ❖化工:涂料、油漆 ❖能源:煤粉燃烧、固体火箭推进剂 ❖机械:微粉磨料、铸造砂型等 ❖材料:
颗粒尺寸的定义可能不同,取决于所采用 的分析技术,比如不同的当量径。
测量颗粒尺寸的方法不同,如颗粒粒径可 以表示为众数值、中位值或者平均值,这 些表达的含义是必须弄清楚的
碳化硅粉体的制备及改性技术
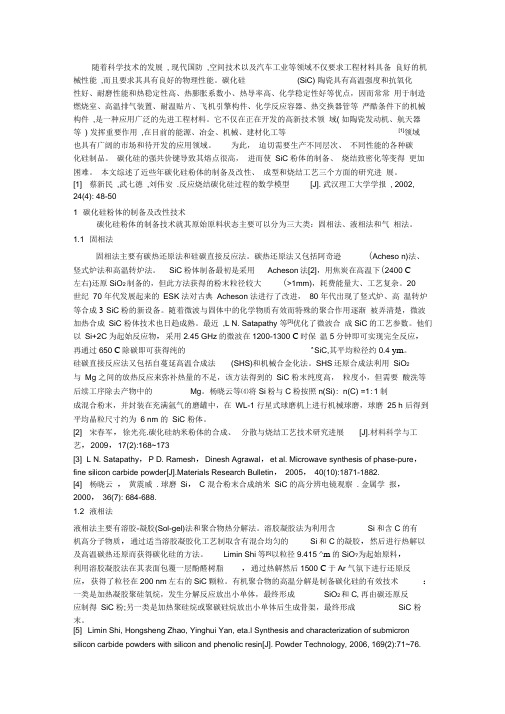
随着科学技术的发展, 现代国防,空间技术以及汽车工业等领域不仅要求工程材料具备良好的机械性能,而且要求其具有良好的物理性能。
碳化硅(SiC) 陶瓷具有高温强度和抗氧化性好、耐磨性能和热稳定性高、热膨胀系数小、热导率高、化学稳定性好等优点,因而常常用于制造燃烧室、高温排气装置、耐温贴片、飞机引擎构件、化学反应容器、热交换器管等严酷条件下的机械构件,是一种应用广泛的先进工程材料。
它不仅在正在开发的高新技术领域( 如陶瓷发动机、航天器等) 发挥重要作用,在目前的能源、冶金、机械、建材化工等[1]领域也具有广阔的市场和待开发的应用领域。
为此,迫切需要生产不同层次、不同性能的各种碳化硅制品。
碳化硅的强共价键导致其熔点很高,进而使SiC 粉体的制备、烧结致密化等变得更加困难。
本文综述了近些年碳化硅粉体的制备及改性、成型和烧结工艺三个方面的研究进展。
[1] 蔡新民,武七德,刘伟安.反应烧结碳化硅过程的数学模型[J]. 武汉理工大学学报, 2002,24(4): 48-501 碳化硅粉体的制备及改性技术碳化硅粉体的制备技术就其原始原料状态主要可以分为三大类:固相法、液相法和气相法。
1.1 固相法固相法主要有碳热还原法和硅碳直接反应法。
碳热还原法又包括阿奇逊(Acheso n)法、竖式炉法和高温转炉法。
SiC粉体制备最初是采用Acheson法[2],用焦炭在高温下(2400 C左右)还原SiO2制备的,但此方法获得的粉末粒径较大(>1mm),耗费能量大、工艺复杂。
20世纪70 年代发展起来的ESK 法对古典Acheson 法进行了改进,80 年代出现了竖式炉、高温转炉等合成3-SiC粉的新设备。
随着微波与固体中的化学物质有效而特殊的聚合作用逐渐被弄清楚,微波加热合成SiC 粉体技术也日趋成熟。
最近,L N. Satapathy 等[3]优化了微波合成SiC的工艺参数。
他们以Si+2C为起始反应物,采用2.45 GHz的微波在1200-1300 C时保温5分钟即可实现完全反应,再通过650 C除碳即可获得纯的^SiC,其平均粒径约0.4 ym。
纳米粉体材料的制备
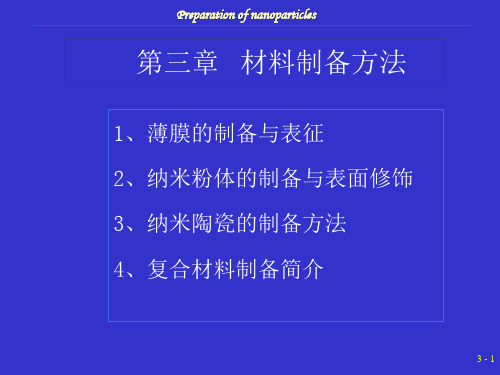
3-8
Preparation of nanoparticles
(一)溶胶制备工艺
1、 有机途径
组成: 母体——醇盐,浓度10~50%;
溶剂——乙醇; 催化剂——盐酸、醋酸等 螯合剂——乙酰丙酮 水——用量一定要控制
特点:水、溶剂挥发,干燥龟裂;
薄膜厚度受限; 但可反复涂覆。
3-9
Preparation of nanoparticles
优缺点
A 样品的晶型结构完整,原料便宜;
B 设备简单、适于批量生产;
C 粉末易团聚,制备较为困难。
3 - 36
Preparation of nanoparticles
2) 水热法(高温水解法)
定义:指在高温(100~1000℃)高压(10~100Mpa)下,利用
溶液中物质化学反应进行的合成。
水的作用:作为一种组分参与反应(即是溶剂又是矿化
研究进展:己制备出多种单质、无机化合物和复合材料超细微粉
末;目前已进入规模生产阶段,美国的MIT(麻省理工学)于1986 年已建成年产几十吨的装置。
3 - 33
Preparation of nanoparticles
4 液相法 特点:化学组成可控 → 高纯、均相 成核速度可控 → 合成温度低 形状大小可控 → 纳米颗粒
分类:溶胶凝胶法;沉淀法;水热法等。
3 - 34
Preparation of nanoparticles
1)沉淀-共沉淀法
定义:含阳离子的溶液中加入沉淀剂后,使离子沉淀的 方法。(以沉淀反应为基础) 分类: 单组分沉淀:溶液只含一种阳离子,得到单组分沉淀。 单相共沉淀:溶液含多种阳离子,沉淀为化合物 (固溶体)。 共沉淀:溶液中含多种阳离子,沉淀产物为混合物。
【精品文章】碳化锆(ZrC)陶瓷粉体的制备方法综述
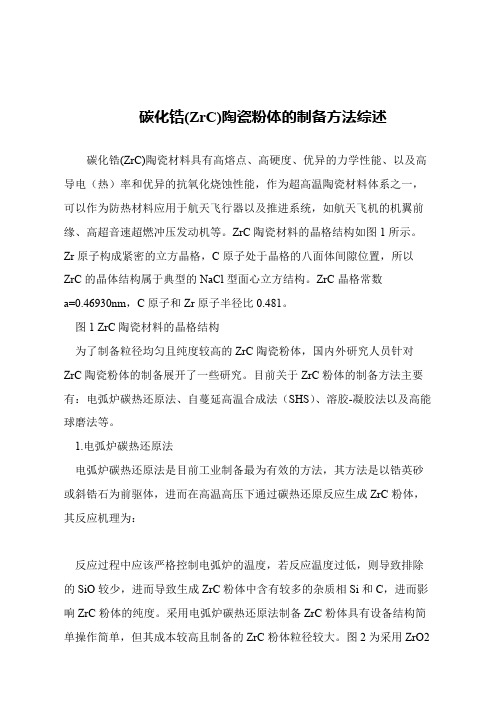
碳化锆(ZrC)陶瓷粉体的制备方法综述
碳化锆(ZrC)陶瓷材料具有高熔点、高硬度、优异的力学性能、以及高导电(热)率和优异的抗氧化烧蚀性能,作为超高温陶瓷材料体系之一,可以作为防热材料应用于航天飞行器以及推进系统,如航天飞机的机翼前缘、高超音速超燃冲压发动机等。
ZrC陶瓷材料的晶格结构如图1所示。
Zr原子构成紧密的立方晶格,C原子处于晶格的八面体间隙位置,所以ZrC的晶体结构属于典型的NaCl型面心立方结构。
ZrC晶格常数
a=0.46930nm,C原子和Zr原子半径比0.481。
图1 ZrC陶瓷材料的晶格结构
为了制备粒径均匀且纯度较高的ZrC陶瓷粉体,国内外研究人员针对ZrC陶瓷粉体的制备展开了一些研究。
目前关于ZrC粉体的制备方法主要有:电弧炉碳热还原法、自蔓延高温合成法(SHS)、溶胶-凝胶法以及高能球磨法等。
1.电弧炉碳热还原法
电弧炉碳热还原法是目前工业制备最为有效的方法,其方法是以锆英砂或斜锆石为前驱体,进而在高温高压下通过碳热还原反应生成ZrC粉体,其反应机理为:
反应过程中应该严格控制电弧炉的温度,若反应温度过低,则导致排除的SiO较少,进而导致生成ZrC粉体中含有较多的杂质相Si和C,进而影响ZrC粉体的纯度。
采用电弧炉碳热还原法制备ZrC粉体具有设备结构简单操作简单,但其成本较高且制备的ZrC粉体粒径较大。
图2为采用ZrO2。
陶瓷粉体的制备及性能测定实验
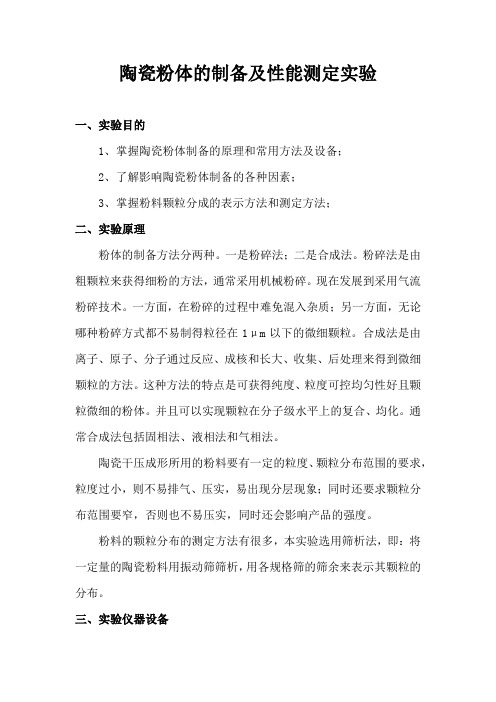
陶瓷粉体的制备及性能测定实验一、实验目的1、掌握陶瓷粉体制备的原理和常用方法及设备;2、了解影响陶瓷粉体制备的各种因素;3、掌握粉料颗粒分成的表示方法和测定方法;二、实验原理粉体的制备方法分两种。
一是粉碎法;二是合成法。
粉碎法是由粗颗粒来获得细粉的方法,通常采用机械粉碎。
现在发展到采用气流粉碎技术。
一方面,在粉碎的过程中难免混入杂质;另一方面,无论哪种粉碎方式都不易制得粒径在1μm以下的微细颗粒。
合成法是由离子、原子、分子通过反应、成核和长大、收集、后处理来得到微细颗粒的方法。
这种方法的特点是可获得纯度、粒度可控均匀性好且颗粒微细的粉体。
并且可以实现颗粒在分子级水平上的复合、均化。
通常合成法包括固相法、液相法和气相法。
陶瓷干压成形所用的粉料要有一定的粒度、颗粒分布范围的要求,粒度过小,则不易排气、压实,易出现分层现象;同时还要求颗粒分布范围要窄,否则也不易压实,同时还会影响产品的强度。
粉料的颗粒分布的测定方法有很多,本实验选用筛析法,即:将一定量的陶瓷粉料用振动筛筛析,用各规格筛的筛余来表示其颗粒的分布。
三、实验仪器设备1、陶瓷粉体制备设备:颚式破碎机、双罐快速球磨机、振动球磨机、湿法球磨机、行星球磨机、气流粉碎机。
2、陶瓷粉体性能检测仪器:振动筛、激光粒度分布测定仪。
四、粉碎设备的使用陶瓷工业广泛使用的粉碎设备有:(1) 颚式破碎机:用于大块原料的粗加工。
粒度粗、进料和出料的粉碎比较小(约为4)而且细度调节范围也不大;(2) 轮碾机:属中碎设备。
物料在固定碾盘和滚动的碾轮之间相对滑动,在碾轮的重力作用下被研磨和压碎。
粉碎比较大(约10以上)。
不适合碾磨含水量大于15%的物料;(3) 球磨机:为陶瓷工业使用最广泛的细碎设备。
湿球磨粉碎效率更高。
物料在旋转的筒内与比重较大的介质(球、棒)相互撞击和研磨而被磨细。
影响球磨效率的主要因素如下:①球磨机转速:球磨介质在离心力的作用下上升到滚筒的上部,自由落下砸在磨料上时,球磨的效率最高。
纳米粉体的制备方法

纳米粉体的制备方法一、纳米粉体应具备的特性1、化学成分配比准确:尽量符合化学计量,避免烧结出现液相或阻碍烧结;2、纯度高:出现液相或影响电性能;3、成分分布均匀:尤其微量掺杂;4、粒度要细,尺寸分布范围要窄;结构均匀,密度高;5、无团聚体:软团聚,硬团聚。
二、制备方法分类化学法化学法是指通过适当的化学反应,从分子、原子、离子出发制备纳米物质,它包括化学气相沉积法、化学气相冷凝法、溶胶一凝胶法、水热法、沉淀法、冷冻干燥法等。
化学气相沉积(CVD)是迄今为止气相法制备纳米材料应用最为广泛的方法,该方法是在一个加热的衬底上,通过一种或几种气态元素或化合物产生的化学元素反应形成纳米材料的过程,该方法主要可分成热分解反应沉积和化学反应沉积。
该法具有均匀性好,可对整个基体进行沉积等优点。
其缺点是衬底温度高。
随着其它相关技术的发展,由此衍生出来的许多新技术,如金属有机化学缺陷相沉积、热丝化学气相沉积、等离子体辅助化学气相沉积门、等离子体增强化学气相沉积及激光诱导化学气相沉积等技术。
化学气相冷凝法(CVC)主要通过有机高分子热解获得纳米粉体,具体过程是先将反应室抽到或更高真空度,然后注入惰性气体He,使气压达到几百帕斯卡,反应物和载气He从外部系统先进入前部分的热磁控溅射CVD装置由化学反应得到反应物产物的前驱体,然后通过对流达到后部分的转筒式骤冷器,用于冷却和收集合成的纳米微粒。
化学沉淀法是在金属盐类的水溶液中控制适当的条件使沉淀剂与金属离子反应,产生水合氧化物或难溶化合物,使溶液转化为沉淀,然后经分离、干燥或热分解而得到纳米级超微粒。
化学沉淀法可分为直接沉淀法、均匀沉淀法、共沉淀法和醇盐水解沉淀法。
物理法早期的物理制备方法是将较粗的物质粉碎,如低温粉碎法、超声波粉碎法、冲击波粉碎法、蒸气快速冷却法、蒸气快速油面法等等。
近年来发展了一些新的物理方法,如旋转涂层法将聚苯乙烯微球涂敷到基片上,由于转速不同,可以得到不同的空隙度.然后用物理气相沉积法在其表面上抗积一层膜,经过热处理,即可得到纳米颗粒的阵列。
纳米BaTiO_3粉体制备方法的研究进展_毕威卿(1)
0前言BaTiO3是一种制造PTC、电子滤波器等电子元件的强介电材料,具有十分广阔的应用前景。
随着电子产业的不断发展,对纳米BaTiO3粉体的制备要求越来越高。
我国钛酸钡粉体的制备工艺在许多方面不及处于世界领先水平的美国与日本[2],但我国学者已经取得一定进展。
本文综述了主要制备方法。
1固相法固相法是最为传统的制备方法[3],于1964年试验成功。
烧结法是组成钛酸钡的各种金属元素的氧化物或他们的酸性盐混合、磨细,下一步在1100℃经固相反应得到所需粉体。
固相烧结法具有工艺简单、设备可靠、方法成熟等优点。
但是所得粉体无法到达高纯、均匀、粒径分布小、不易团聚等要求。
2液相法2.1水热法水热法是在压力容器中,将含Ba和Ti的前驱体水浆体进行反应制得钛酸钡粉体的方法。
由于早期使用的钛化合物活性差,需要在380-500℃,30-50MPa的压力下进行反应,高压高温为制备技术的应用带来了障碍。
冯秀丽等[5]以廉价的氢氧化钡和偏钛酸为原料,按比例加入蒸馏水,在集热式恒温加热磁力搅拌仪加热搅拌。
一段时间后将产物酸洗、水洗、醇洗,在烘箱中烘干,最后在研钵研磨得钛酸钡粉体。
反应机理为:H2TiO3,+Ba(OH)2==BaTiO3+2H2O。
通过对原料钡钛比、反应时间、反应温度等条件进行研究,得出常压水热法钛酸钡粉体的最佳制备条件为反应原料的钡钛比为1.4,反应温度是100℃,反应时间为6h,溶液pH为12。
所制备出的钛酸钡粉体为立方相,粉体一次平均粒径为40.9nm。
R·Roy提出了微波与水热结合技术,并成功利用此法合成了多种氧化物陶瓷和粉体材料[6-9]。
此法能在极短的时间内使温度上升至结晶温度,沉淀凝胶快速溶解然后均匀成核,缩短了结晶时间,节约了能量。
付乌有等[10]采用微波-水热法制备了纳米钛酸钡粉体,并用TEM 等手段对晶体结构和形貌进行了研究,得出结论:利用微波-水热法可以在60-160℃的条件下制得粒径20-30nm的纳米钛酸钡晶体,并且在一定范围内纳米晶体的介电常数具有比较好的稳定性。
10.钛酸钡粉体制备方法(55)解析
39
七、双氧水共沉淀法
该法主要是以偏钛酸为钛原料,用 双氧水、氨水及硝酸钡为添加剂,经 转化共沉淀得到纳米晶或亚微米钛酸 钡前驱体,再经热分解制备纳米或亚 微米钛酸钡。
40
其反应方程式为:
H2TiO3+H2O2+2NH3→(NH4)2Ti4O4+H2O
(NH4)2Ti4O4+Ba(NO3)2→BaTiO4↓
34
工艺流程及原理为:将等摩尔 的氯化钡溶液及四氯化钛水溶液 混合后 , 与六摩尔当量的碳酸氢 铵反应 , 得到胶体二氧化钛和碳 酸钡沉淀相互包裹的沉淀 , 经分 离洗涤、烘干、煅烧后得到钛酸 钡粉体。
35
该方法工艺简单,但氯根很难洗 净,容易带入杂质,特别是钙离 子,纯度偏低。还有一问题是加 料速度过快,会产生大量的气泡, 反应难以于控制,同时前驱体的 过滤也较困难。
30
粉料中含少量碳酸钡。若制备过程在 惰性气氛中进行,则碳酸钡含量减少, 但不能完全消除。因为干燥过程中,粉 体与空气中的二氧化碳反应也能形成少 量碳酸钡,随煅烧温度的提高到 1000℃ 时,碳酸钡全部分解,粉体为纯的钛酸 钡相。 该方法的优缺点为:制备的颗粒团 聚较少,颗粒分散性好,粒径分布也较 均匀,但含少量碳酸钡。
18
水热合成法是把含有钡和钛的前体 (一般是氢氧化钡和水合氧化钛)水浆 体,置于较高的温度和压力下(相对于 常温、常压),使它们发生化学反应。 经过一定时间后,钛酸钡粉体就在这 种热水介质中直接生成。该法制备的 晶粒发育完整,粒度分布均匀,颗粒 之间很少团聚。
19
采用氢氧化钡和偏钛酸为原料合成钛 酸钡,在反应过程中会生成少量的BaCO3, 但在其后的煅烧阶段少量的碳酸钡会进一 步与偏钛酸反应,还有少量的碳酸钡用醋酸 洗涤,再水洗即可除掉;煅烧温度 600700℃,降低了煅烧温度;分析结果显 示,所得产品纯度高,粒径小,能满足电 子工业对高质量钛酸钡粉体的需求。
合成陶瓷流程
合成陶瓷流程一、介绍合成陶瓷是一种由人工合成的高性能陶瓷材料,具有优异的物理、化学和机械性能。
在制备合成陶瓷的过程中,需要经历粉体制备、成型、烧结和表面处理等步骤。
二、粉体制备合成陶瓷的制备首先需要制备合适的粉体。
常用的粉体制备方法包括溶胶凝胶法、高能球磨法和气相沉积法等。
其中,溶胶凝胶法是一种将溶胶转化为凝胶,并通过热处理得到陶瓷粉体的方法。
高能球磨法则是通过高能球磨机对原料进行机械碾磨,使其细化和均匀混合。
气相沉积法则是将气体中的原料通过化学反应使其沉积在基体上。
三、成型成型是将粉体制备成所需形状的过程。
常用的成型方法有压制成型、注射成型和挤出成型等。
压制成型是将粉体放入模具中,施加压力使其成型。
注射成型则是将粉体与粘结剂混合后,通过注射机将其注入模具中,并在模具中硬化。
挤出成型则是将粉体与粘结剂混合后,通过挤出机将其挤出成所需形状。
四、烧结烧结是将成型后的陶瓷坯体进行高温处理,使其形成致密的结构。
烧结过程中,陶瓷坯体会经历初烧、烧结和冷却三个阶段。
初烧是在低温下除去粘结剂和残留的有机物质。
烧结则是在高温下使粉体颗粒之间发生结合,形成致密的陶瓷结构。
冷却则是将烧结后的陶瓷坯体缓慢降温,避免产生内应力。
五、表面处理表面处理是为了改善陶瓷材料的性能和外观而进行的处理过程。
常用的表面处理方法有抛光、涂层和热处理等。
抛光是通过研磨和抛光工艺,使陶瓷表面光滑、平整。
涂层则是在陶瓷表面涂覆一层特殊的材料,用于增强其抗磨损、抗腐蚀等性能。
热处理是将陶瓷材料置于高温下,使其发生相变或晶界强化,提高其力学性能。
六、总结合成陶瓷的制备过程包括粉体制备、成型、烧结和表面处理等步骤。
通过粉体制备获得合适的陶瓷粉体,然后通过成型将其制备成所需形状。
烧结过程中,陶瓷坯体经历初烧、烧结和冷却三个阶段,形成致密的陶瓷结构。
最后,通过表面处理改善陶瓷材料的性能和外观。
合成陶瓷的制备过程需要严格控制各个环节,以获得高质量的陶瓷材料。
材料化学9粉体材料及其制备技术
颗粒当量径:将颗粒以某种等量关 系转化为球形,相应得到的球的直 径称为颗粒的当量径。
颗粒当量径的定义及计算公式
1. 等体积球当量径:与颗粒具有相同体积的
球的直径
dV
3
6V
2. 等表面积球当量径:与颗粒具有相同表面
积的球的直径
dS
S
3. 比表面积球当量径:与颗粒具有相同的比
纳米磁性金属的磁化率是普通金属的20倍,饱和磁矩则是 普通的二分之一。
一些纳米颗粒的导电性能明显改善,甚至成为 高 TC 的超导体。
颗粒大小的表征
颗粒大小和形状是粉体材料最重要的物性表征量 。
颗粒的大小一般用粒径来表示。在分析粉体的粒 径时,应明确单颗粒粒径与颗粒聚集体 (粉末) 粒径的含义以及它们之间的区别
激光粉体粒度分析仪原理
激光粒度仪已经商品化,市场上主要 机型的量测范围大致是 0.05 ~ 10 m
粉体粒径也可以用光学显微镜直接量测
将粉体样品均匀平铺在光学显微镜的视场 内进行观察,可以近似确定粉体的粒径及 其分布,测试范围大致在 0.5 ~ 100 微米。
目前显微镜分析法得到了很大的改进:现 代电子技术与显微镜方法相结合,用摄像 机拍摄经显微镜放大的颗粒图像,图像信 号进入计算机内存后,计算机自动地对颗 粒的形貌特征和粒度进行分析和计算
注意这一公式中含有两个自 由变量。为实现筛网的标准 化,人们制定了一些规则。
主模系列 副模系列
根据以上规则,就可以得到一个标准筛系列: 32,42,48, 60,65,80,100,115,150,170,
200,270,325,400 目。 其中最细的是 400 目筛,孔径为 0.038 mm。
- 1、下载文档前请自行甄别文档内容的完整性,平台不提供额外的编辑、内容补充、找答案等附加服务。
- 2、"仅部分预览"的文档,不可在线预览部分如存在完整性等问题,可反馈申请退款(可完整预览的文档不适用该条件!)。
- 3、如文档侵犯您的权益,请联系客服反馈,我们会尽快为您处理(人工客服工作时间:9:00-18:30)。
粉体的合成制备方法发展状况 如今,粉体的合成制备经过多年的发展,制备合成方法已经变得各种各样按理论也可分为物理和化学方法等纳米粒子的制备方法很多,可分为物理方法和化学方法。 1.物理方法 (1)真空冷凝法 用真空蒸发、加热、高频感应等方法使原料气化或形成等离子体,然后骤冷。其特点纯度高、结晶组织好、粒度可控,但技术设备要求高。 2)物理粉碎法 通过机械粉碎、电火花爆炸等方法得到纳米粒子。其特点操作简单、成本低,但产品纯度低,颗粒分布不均匀。 (3)机械球磨法 采用球磨方法,控制适当的条件得到纯元素纳米粒子、合金纳米粒子或复合材料的纳米粒子。其特点操作简单、成本低,但产品纯度低,颗粒分布不均匀。 2. 化学方法 (1)气相沉积法 利用金属化合物蒸气的化学反应合成纳米材料。其特点产品纯度高,粒度分布窄。 (2)沉淀法 把沉淀剂加入到盐溶液中反应后,将沉淀热处理得到纳米材料。其特点简单易行,但纯度低,颗粒半径大,适合制备氧化物。 (3)水热合成法 高温高压下在水溶液或蒸汽等流体中合成,再经分离和热处理得纳米粒子。其特点纯度高,分散性好、粒度易控制。 (4)溶胶凝胶法 金属化合物经溶液、溶胶、凝胶而固化,再经低温热处理而生成纳米粒子。其特点反应物种多,产物颗粒均一,过程易控制,适于氧化物和Ⅱ~Ⅵ族化合物的制备。 (5)微乳液法 两种互不相溶的溶剂在表面活性剂的作用下形成乳液,在微泡中经成核、聚结、团聚、热处理后得纳米粒子。其特点粒子的单分散和界面性好,Ⅱ~Ⅵ族半导体纳米粒子多用此法制备。 按照反应物的相可分为三类气相合成法,固相合成法和液相合成法。 一、气相合成法 (1)电阻加热法是通过电阻加热来实现气相粉体制备的方法,典型工艺如蒸发冷凝工艺及化学气相沉积工艺。前者可制备多种金属纳米粉体;后者可制备氧化物粉体,也可制备氮化物和碳化物等非氧化物粉体。 (2)电子束加热法 同样有蒸发冷凝和CVD两种工艺,只是以电子束加热。该法是从制模工艺发展而来,为避免形成薄膜材料,采用流动油面积。 (3)化学火焰法 是通过一般化学燃烧来合成粉体的方法,具体工艺分为两种:一是直接将气态反应剂加入到氧化氛围中燃烧,适用于各种放热反应;二是在已有化学火焰中加入金属粉或雾状金属盐溶液,使其被加热蒸发、分解、还原及化合。 (4)等离子法 利用等离子高温射流加热反应剂使其发生化学反应,是一种重要的合成粉体工艺。等离子作为热源有明显的优点:温度很高,中心接近10000度;高度电离状态的等离子体可以增强化学反应;等离子体较一般燃烧火焰更为清洁;等离子体能量集中、边界明显,容易造成骤冷条件,这对纳米粉的制备很有意义。等离子体可制备氧化物,碳、氮等非氧化物及金属等单质和复合粉体。 (5)激光法 又被称为激光诱导化学气相沉积法LICVD或LCVD。是通过反应气体分子对特定波长激光能量的吸收而诱导发生合成反应制粉。此外,也有基于蒸发冷凝原理的激光剥蚀法,所用原料----靶材即为所制备粉体的本位材料。 二、固相合成法 (1)粉体的固相合成是只通过一般的固相操作而完成粉体合成的一大类工艺方法。所谓固相操作主要指:初始原料中至少有一种是固态;产物颗粒是在固相表面生成而不是在气相或液相中成核长大的。主要工艺: (2)热分解法 利用固体原料的热分解而生成新固相的方法。常用做热分解原料的有碳酸盐、草酸盐、硫酸盐和氢氧化物,原料可以是天然矿物,但更多的是人工合成的化学试剂。 (3)复合氧化物固相反应-烧结法 将各组分氧化物粉混合后置于一定的高温下进行热处理,是各组分在颗粒间扩散,并发生固相反应,由于颗粒长大和固体联桥团聚现象严重,需经粉碎才能获得所需粒度的复合氧化物粉体。 (4)还原-化合法 利用一种氧亲和力更高的还原剂去还原某元素的氧化物,再将其进行碳化、氮化或硼化等,从而获得该元素相应的非氧化物粉体,常用的还原剂是碳。 (5)自蔓延高温合成法 利用化学反应的强热效应来使反应剂升到足够高的温度,实现并完成合成反应。最适用于难溶,高硬的共价键化合物和他们的复合物,以及金属键化合物。 (6) 电爆炸发 是在一根细金属丝上通过高功率的脉冲电流,使其气化,成核生长获得超微粉体。该法可制的几乎所有金属盒合金类超微粉体,控制气氛也可制的其化合物粉体。 (7) 机械力化学法 在高能磨机中,通过对反应体系施加机械能,诱导其发生扩散及化学反应等一系列化学和物理化学过程,达到合成新品种粉体的目的。 三、液相合成法 粉体的液相合成是指通过在液相中的化学反应,从液相中析出固相颗粒的一大类工艺方法。主要工艺有: (1) 沉淀法 是一种最常用的液相制粉方法,在工业上大量应用该方法生产各种粉体。许多液相反应都能生成固相沉淀物,如氧化还原反应,酸碱中和反应,离子交换反应,盐类分解反应,分解反应等。 沉淀法是在原料溶液中添加适当的沉淀剂,使得原料液中的阳离子形成各种形式的沉淀物,然后再经过滤、洗涤、干燥,有时还需加热分解等工艺过程制得纳米粉体的方法。沉淀法具有设备简单、工艺过程易控制、易于商业化等优点,能制取数十纳米的超细粉。沉淀法可分为共沉淀法、直接沉淀法、均匀沉淀法和水解沉淀法等。从液相中沉淀出的主要是氢氧化物或金属盐类,需要将沉淀物高温煅烧转化成氧化物。 1.共沉淀法 如果原料溶液中有2种或2种以上的阳离子,它们以均相存在于溶液中,加入沉淀剂进行沉淀反应后,就可得到成分均一的沉淀,这就是共沉淀法。它是制备含有2种以上金属元素的复合氧化物超微粉的重要方法。采用共沉淀法制备纳米粉体,反应混合物需充分混合,使反应两相间扩散距离缩短,以利于晶核形成;同时要注意控制生成产物的化学计量比。目前,共沉淀法已被广泛用于制备钙钛型材料、尖晶石型材料、敏感材料、铁氧体及萤光材料的超微粉 2.直接沉淀法 这种方法是使溶液中的金属阳离子直接与沉淀剂发生化学反应而形成沉淀物。以SrTiO3超细粉的制备为例,将TiCl4的水解产物与SrCl2溶液在强碱性水溶液中于90℃下反应,直接生成SrTiO3沉淀,沉淀经过滤、洗涤和烘干后,得到粒径为20~40nm的SrTiO3超细粉。 3.均匀沉淀法 为了避免直接添加沉淀剂而产生的体系局部浓度不均匀现象,均匀沉淀法是在溶液中加入某种物质,这种物质不会立刻与阳离子发生反应生成沉淀,而是在溶液中发生化学反应缓慢地生成沉淀剂。只要控制好沉淀剂的生成速度,就可避免浓度不均匀现象,使体系的过饱和度维持在适当的范围内,从而控制粒子的生长速度,制得粒度均匀的纳米粒子。 4.水解沉淀法 通过调节原料溶液的PH值或者通过改变原料液温度而使金属离子水解产生沉淀。水解沉淀法以无机盐为原料,具有原料便宜易得、成本低的优势,是最经济的制备方法。除此之外,它还具有诸多优点,最显著的一点就是可以在常温常压条件下,采用简单的设备,于原子、分子水平上通过反应、成核、成长、收集或处理而获得高纯度的、组分均一的、尺寸达几十纳米的超细粉体。此外它还可以精确控制化学组成,容易添加微量的有效成分,制成粉体的表面活性好,易控制颗粒的形状和粒径。但是,因为必须通过液固分离才能得到沉淀物,要完全洗净无机杂质离子较困难;另一个需要特别重视的问题是容易形成团聚体,如控制不当,团聚将会严重影响粉体的后续使用
(2)水热合成法 是在一定的高温,高压下,一些氢氧化物或盐类在水中的溶解度大于相对应的氧化物的溶解度,于是氢氧化物或盐类融入水中,同时析出氧化物。所需的氢氧化物可先合成好,或将反应前驱体直接加到反应釜中加温,加压生成氧化物。水热法制备纳米粉体是在特制的密闭反应容器里,采用水溶液作为反应介质,通过对反应容器加热,创造一个高温、高压反应环境,使前驱物在水热介质中溶解,进而成核、生长,最终形成具有一定粒度和结晶形态的晶粒。水热法原理上是利用了许多化合物在高温和高压的水溶液中表现出与在常温下不同的性质(如溶解度增大,离子活度增强,化合物晶体结构易转型及氢氧化物易脱水等)。 水热法能直接制得结晶良好的粉体,不需作高温灼烧处理,避免了在此过程中可能形成的粉体硬团聚,而且通过改变工艺条件,可实现对粉体粒径、晶型等特性的控制,因此,水热法合成的陶瓷粉体具有分散性好,无团聚或少团聚,晶粒结晶良好,晶面显露完整等特点;同时,因经过重结晶,所以制得的粉体纯度高。近年来水热法已被广泛地应用于各种粉体的制备。然而,水热法毕竟是高温、高压下的反应,对设备要求高,操作复杂,能耗较大,因而成本偏高。而且,实现工业化连续生产较困难。 (3)熔盐合成法 从熔盐中合成粉体,可直接生成所需要求的物相。其液相介质为熔融的盐类,如氯化物,硝酸盐,铁酸盐等具有较低熔点的无机盐类。反应物可是盐类,也可是氧化物碳酸盐等。 (4)溶胶--凝胶法 选择前驱体和溶剂制成溶胶,前驱体应包含所制粉体的主要成分,通常为金属的醇盐,也可用适合的无机盐类。另可选择适合的金属盐类融入溶剂中,并可于溶胶均匀混合。通过水解和缩合反应形成胶体颗粒,并导致凝胶的形成,最后通过适当的温度煅烧和粉碎获得粉料,也可在蒸压釜中进行水热反应,脱水形成氧化物粉体。溶胶-凝胶工艺是60年代发展起来的一种超细粉体的制备工艺,它是指金属有机或无机化合物经过溶胶-凝胶化和热处理形成氧化物或其他固体化合物的方法。近年来,不少专家学者对制备纳米粉体的溶胶-凝胶工艺进行了大量的研究。根据水与醇盐比例的大小,即加入水量的多少,粉体的制备过程一般设计为2种工艺路线:粒子凝胶法和聚合凝胶法。研究表明,溶剂种类、水与醇盐的比例(即加水量)、水解温度、催化剂的种类和用量、陈化温度等参数都会影响所形成的溶胶的质量,进而影响超细粉体的性能。在制备过程中,可以通过调节这些参数获得最佳制备工艺条件。 与沉淀法合成纳米粉体一样,采用溶胶-凝胶工艺具有反应温度低(通常在常温下进行)、设备简单、工艺可控可调等特点,此外,溶胶-凝胶工艺还避免了沉淀法中以无机盐为原料产生的阴离子污染问题,提高了纳米粉体的纯度。但是该法也存在原料成本高的不足,而且为了除去化学吸附的羟基和烷基团,粉体煅烧工序必不可少。