铸造工艺学课程设计
铸造工艺课程设计_说明书

铸造工艺课程设计讲明书名目1前言1.1本设计的意义机械制造工艺学课程设计是在我们学完了大学的全部本原课、技术本原课以及大局限专业课之后进行的.这是我们在进行毕业设计之前对所学各课程的一次深进的综合性的总复习,也是一次理论联系实际的练习,因此,它在我们四年的大学生活中占有重要的地位。
1.1.1本设计的目的铸造工艺课程设计是学完了铸造工艺本原课程后,对铸造工艺过程进一步了解的练习性的教学环节,是学习深化与升华的重要过程,是对学生综合素养与工程实践的能力培养应在指导教师指导下独立完成一项给定的设计任务,编写符合要求的设计讲明书,并正确绘制有关图表。
在课程设计工作中,应综合运用多学科的理论、知识与技能,分析与解决工程咨询题。
应学会依据技术课题任务,进行资料的调研、收集、加工与整理和正确使用工具书;培养学生掌握有关工程设计的程序、方法与技术典型,提高工程设计计算、图纸绘制、编写技术文件的能力;培养学生掌握实验、测试等科学研究的根基方法;锻炼学生分析与解决工程实际咨询题的能力。
通过课程设计,应能树立正确的设计思想;培养学生严厉认确实科学态度和严谨求实的工作作风;在工作设计中,应能树立正确的工程意识与经济意识,树立正确的生产瞧点、经济瞧点与全局瞧点。
1.1.2本设计的意义该课程设计是学完本课程之后的一项重要的实践,是我们步进社会的一次深刻的链接,考察了我们独立设计,计算,绘图和分析的能力,同时提高了我们查阅各种设计手册的能力,通过该课程设计我们了解铸造工艺设计的一般步骤,需要用到的一些结构都需要我们认真查阅后绘制到图纸上,通过课程设计我们学会了许多课本上没有的知识。
1.2本设计的技术要求工艺设计学生要在的时刻〔3周〕内,必须完成一个中等复杂程度零件的铸造工艺设计,并完成采纳机器造型的要紧铸造技术文件汇〔编〕制工作。
采纳CAD出图,如有条件能够进行三维设计和动态模拟。
华铸CAE10.0模拟软件能够开放使用。
具体任务包括:零件图1张〔A4〕,铸造工艺图1张〔A3彩色〕,模板装配图1张〔A4〕,芯盒图〔或装配图〕1张〔A4〕,铸型装配图1张〔A4〕,铸造工艺卡1张〔A4〕,设计讲明书1份〔A4〕1.3本课题的开发觉状由计算机、网络技术、传感技术、人工智能所构成的信息技术近年来在铸造生产中得到更为广泛的应用,这正在改变着铸造生产的面貌,能够讲现代铸造技术的要紧特征确实是根基将传统的铸造工艺与信息技术融为一体。
铸造工艺学课程设计案例

成果报告需以PDF格式提交,同时附上所有相关数据和图表。
报告内容
报告需包含设计思路、工艺流程、数据分析及结论等部分,要求 内容详实、逻辑清晰。
成果展示形式和内容安排建议
展示形式
鼓励采用多媒体形式进行展示,如PPT、视频等。
内容安排
建议按照设计背景、设计思路、工艺流程、数据 分析、结论与展望等顺序进行展示。
时间安排
每个小组展示时间不超过20分钟,需提前做好时 间规划。
课程设计评价标准及成绩评定方法
01
评价标准
将从设计创新性、实用性、技术 难度、报告质量等方面进行综合 评价。
02
成绩评定方法
03
优秀作品选拔
采用百分制评分,其中设计创新 性占30%、实用性占20%、技术 难度占20%、报告质量占30%。
铸造材料选择
根据零件使用要求、生产批量和成本 等因素,选择合适的铸造合金,如铸 铁、铸钢、铝合金等。
性能要求
铸造合金应具有良好的流动性、收缩 性、偏析倾向小等性能,以保证铸件 质量。同时,合金成分和性能应符合 相关标准或技术条件的规定。
03
案例分析:典型铸件生产工艺设计
铸件结构分析与设计优化建议
根据评分结果,选拔出优秀作品 进行表彰和奖励。
THANKS
感谢观看
推广新技术和新材料
积极推广先进的铸造技术和新材料,如3D打印技术、高性能铸造合 金等,提高铸件的精度和性能。
加强人才培养
加强铸造领域的人才培养和引进,提高从业人员的专业素质和技能水 平,为铸造行业的发展提供有力的人才保障。
06
课程设计成果展示与评价标准
课程设计成果提交要求说明
提交时间
所有成果需在课程结束前一周内提交,逾期将不予受理。
带轮铸造工艺课程设计
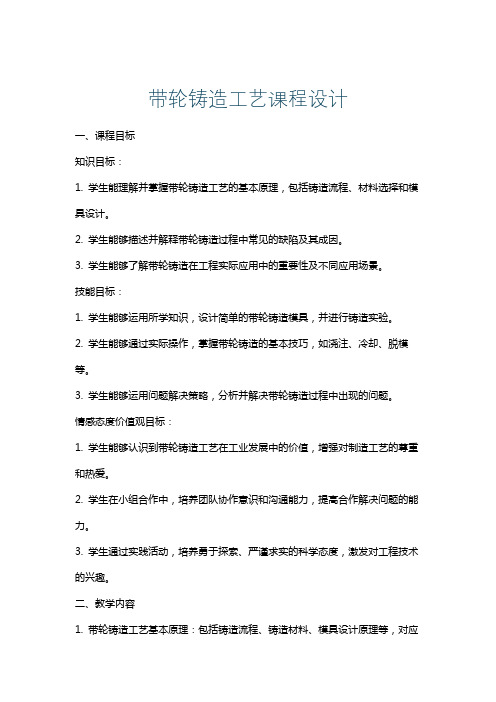
带轮铸造工艺课程设计一、课程目标知识目标:1. 学生能理解并掌握带轮铸造工艺的基本原理,包括铸造流程、材料选择和模具设计。
2. 学生能够描述并解释带轮铸造过程中常见的缺陷及其成因。
3. 学生能够了解带轮铸造在工程实际应用中的重要性及不同应用场景。
技能目标:1. 学生能够运用所学知识,设计简单的带轮铸造模具,并进行铸造实验。
2. 学生能够通过实际操作,掌握带轮铸造的基本技巧,如浇注、冷却、脱模等。
3. 学生能够运用问题解决策略,分析并解决带轮铸造过程中出现的问题。
情感态度价值观目标:1. 学生能够认识到带轮铸造工艺在工业发展中的价值,增强对制造工艺的尊重和热爱。
2. 学生在小组合作中,培养团队协作意识和沟通能力,提高合作解决问题的能力。
3. 学生通过实践活动,培养勇于探索、严谨求实的科学态度,激发对工程技术的兴趣。
二、教学内容1. 带轮铸造工艺基本原理:包括铸造流程、铸造材料、模具设计原理等,对应教材第三章第一节。
- 铸造流程:砂型铸造、金属型铸造、压力铸造等。
- 铸造材料:铸铁、铸钢、铝合金、铜合金等。
- 模具设计原理:分型面、收缩率、浇注系统、冷却系统等。
2. 带轮铸造缺陷及其成因:分析常见缺陷如气孔、夹渣、变形等,对应教材第三章第二节。
- 气孔、夹渣、砂眼等缺陷的成因及防止措施。
- 变形、裂纹等缺陷的成因及矫正方法。
3. 带轮铸造实际应用:介绍带轮在各类机械设备中的应用,对应教材第三章第三节。
- 不同类型的带轮及其应用场景。
- 带轮铸造在工业发展中的重要作用。
4. 带轮铸造实验操作:进行实际操作,掌握铸造技巧,对应教材第三章实践环节。
- 设计简单的带轮铸造模具并进行铸造实验。
- 掌握浇注、冷却、脱模等基本操作技巧。
5. 教学进度安排:共4课时。
- 第1课时:带轮铸造工艺基本原理。
- 第2课时:带轮铸造缺陷及其成因。
- 第3课时:带轮铸造实际应用。
- 第4课时:带轮铸造实验操作。
三、教学方法本课程采用以下多样化的教学方法,以充分激发学生的学习兴趣和主动性:1. 讲授法:教师通过生动的语言和形象的表达,讲解带轮铸造工艺的基本原理、缺陷成因和实际应用等理论知识,使学生系统地掌握课程内容。
金属工艺铸造课程设计
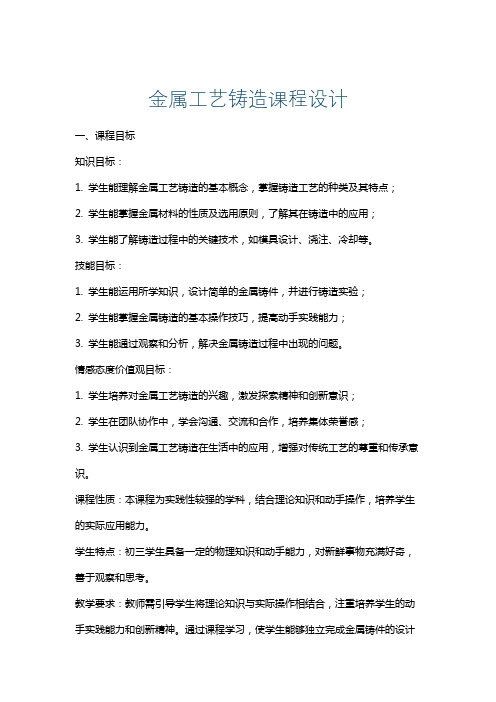
金属工艺铸造课程设计一、课程目标知识目标:1. 学生能理解金属工艺铸造的基本概念,掌握铸造工艺的种类及其特点;2. 学生能掌握金属材料的性质及选用原则,了解其在铸造中的应用;3. 学生能了解铸造过程中的关键技术,如模具设计、浇注、冷却等。
技能目标:1. 学生能运用所学知识,设计简单的金属铸件,并进行铸造实验;2. 学生能掌握金属铸造的基本操作技巧,提高动手实践能力;3. 学生能通过观察和分析,解决金属铸造过程中出现的问题。
情感态度价值观目标:1. 学生培养对金属工艺铸造的兴趣,激发探索精神和创新意识;2. 学生在团队协作中,学会沟通、交流和合作,培养集体荣誉感;3. 学生认识到金属工艺铸造在生活中的应用,增强对传统工艺的尊重和传承意识。
课程性质:本课程为实践性较强的学科,结合理论知识和动手操作,培养学生的实际应用能力。
学生特点:初三学生具备一定的物理知识和动手能力,对新鲜事物充满好奇,善于观察和思考。
教学要求:教师需引导学生将理论知识与实际操作相结合,注重培养学生的动手实践能力和创新精神。
通过课程学习,使学生能够独立完成金属铸件的设计与制作,提高综合运用知识的能力。
同时,关注学生在课程学习中的情感态度价值观的培养,使他们在学习过程中形成积极向上的人生态度。
二、教学内容1. 金属工艺铸造基本概念:包括铸造的定义、分类及其特点,使学生了解铸造工艺的广泛应用。
教材章节:第一章 金属工艺铸造概述2. 金属材料的性质及选用:介绍常见金属材料的物理和化学性质,以及选用原则,为学生设计铸件提供参考。
教材章节:第二章 金属材料及选用3. 铸造工艺过程:讲解铸造过程中的关键技术,如模具设计、浇注、冷却等,让学生掌握铸造的基本操作。
教材章节:第三章 铸造工艺过程4. 铸造缺陷及其防止:分析铸造过程中可能出现的缺陷,探讨缺陷防止措施,提高学生解决实际问题的能力。
教材章节:第四章 铸造缺陷与防止5. 铸件设计:结合所学知识,指导学生进行简单的铸件设计,培养学生的创新意识和实际应用能力。
阀体铸造工艺学课程设计

阀体铸造工艺学课程设计一、教学目标本课程的教学目标是使学生掌握阀体铸造工艺的基本理论、方法和应用,具备分析和解决阀体铸造过程中问题的能力。
1.理解阀体铸造的基本原理和工艺流程。
2.掌握阀体铸造中的关键技术,如模具设计、铸造材料选择、铸造缺陷分析等。
3.了解阀体铸造行业的现状和发展趋势。
4.能够运用所学知识对阀体铸造过程进行设计和优化。
5.能够使用相关设备和工具进行阀体铸造实验,并对实验结果进行分析。
6.具备阀体铸造工艺的初步研发能力。
情感态度价值观目标:1.培养学生的创新意识和团队合作精神。
2.增强学生对阀体铸造行业的认同感和责任感。
3.培养学生关注社会、关注环保的意识。
二、教学内容本课程的教学内容主要包括阀体铸造工艺的基本理论、方法和应用。
1.阀体铸造工艺的基本原理:包括铸造过程的基本概念、铸造力的作用、铸造应力与变形等。
2.阀体铸造工艺的模具设计:包括模具的结构与设计原则、模具材料的选择、模具的制造与维护等。
3.阀体铸造材料:包括铸造金属的性能、铸造合金的制备与处理、铸造材料的选用原则等。
4.阀体铸造缺陷分析与控制:包括铸造缺陷的类型、产生原因及预防措施等。
5.阀体铸造过程中的质量控制:包括铸造过程的质量管理、质量检测与评定等。
6.阀体铸造工艺的优化与创新:包括铸造工艺的优化方法、新技术和新工艺的应用等。
7.阀体铸造行业的现状与发展趋势:包括国内外阀体铸造行业的发展状况、行业标准与政策等。
三、教学方法本课程采用讲授法、讨论法、案例分析法和实验法等多种教学方法。
1.讲授法:通过教师的讲解,使学生掌握阀体铸造工艺的基本理论和方法。
2.讨论法:学生就阀体铸造过程中的问题进行讨论,培养学生的思考和表达能力。
3.案例分析法:通过分析阀体铸造实例,使学生学会分析问题、解决问题的方法。
4.实验法:让学生亲自动手进行阀体铸造实验,培养学生的动手能力和实践能力。
四、教学资源本课程的教学资源包括教材、参考书、多媒体资料和实验设备等。
铸造工艺课程设计哪有疲

铸造工艺课程设计哪有疲一、课程目标知识目标:1. 学生能掌握铸造工艺的基本概念,了解不同铸造方法的优缺点;2. 学生能理解铸造过程中金属材料的熔炼、浇注、冷却和凝固等基本原理;3. 学生能了解铸造缺陷的类型及其产生原因,并掌握预防和改进措施;4. 学生能掌握铸造工艺参数对铸件质量的影响,提高铸造工艺设计的实际操作能力。
技能目标:1. 学生能运用铸造工艺知识,进行简单的铸造工艺设计和分析;2. 学生能运用所学知识,对铸造缺陷进行识别、分析和解决;3. 学生能在教师的指导下,完成铸造实验操作,提高实际动手能力。
情感态度价值观目标:1. 培养学生对铸造工艺的兴趣,激发他们探索金属材料和铸造技术奥秘的热情;2. 培养学生严谨的科学态度,使他们认识到铸造工艺在制造业中的重要性;3. 培养学生的团队合作精神,提高沟通与协作能力,为将来的职业生涯打下基础。
本课程针对高中年级学生,结合铸造工艺的学科特点,注重理论知识与实践操作相结合。
课程旨在使学生在掌握铸造工艺基本知识的基础上,提高实际操作能力,培养学生的创新意识和解决问题的能力。
通过本课程的学习,为学生未来在制造业和相关领域的发展奠定基础。
二、教学内容本章节教学内容主要包括以下五个部分:1. 铸造工艺概述:介绍铸造工艺的定义、分类及其在制造业中的应用,使学生了解铸造工艺的基本概念和发展趋势。
2. 铸造原理:讲解金属材料的熔炼、浇注、冷却和凝固等基本原理,分析铸造过程中各阶段的影响因素,为后续工艺设计打下基础。
3. 铸造方法及特点:介绍砂型铸造、金属型铸造、压力铸造等常见铸造方法,分析各种铸造方法的优缺点,指导学生根据实际需求选择合适的铸造方法。
4. 铸造缺陷及其防治:列举常见的铸造缺陷,分析缺陷产生的原因,探讨预防和改进措施,提高学生分析和解决问题的能力。
5. 铸造工艺设计:讲解铸造工艺参数对铸件质量的影响,引导学生运用所学知识进行铸造工艺设计,培养实际操作能力。
铸造工艺设计课程设计

课程设计报告课程设计名称:学生姓名:学院:专业及班级:学号:指导教师:年月日目录一、造型材料选择 (1)二、铸造工艺参数设计 (1)1.加工余量的选择 (2)2.铸件孔是否铸出的确定 (2)3.起模斜度的确定 (2)4.铸造圆角的确定 (3)5. 铸造收缩率的确定 (3)6.考虑加工余量后的尺寸 (4)三、造型方法的设计 (4)1.环形型芯外形 (5)2.环形型芯尺寸 (5)3.中心孔木质芯盒造型 (6)4.1/4环形木质芯盒造型 (7)四、木模的设计 (8)1.木模的外形设计 (8)2.木模的设计尺寸 (9)五、浇注系统和冒口设计 (10)1.浇注系统选择··················································································10.2冒口的选择 (10)六、铸型装配图设计 (11)一、造型材料和铸造合金的选择1. 造型和造芯材料由于本次课程设计的铸件是中等批量生产,所以造型和造芯的方法应采用灵活多样,适应性强的手工造型。
金属工艺铸造课程设计
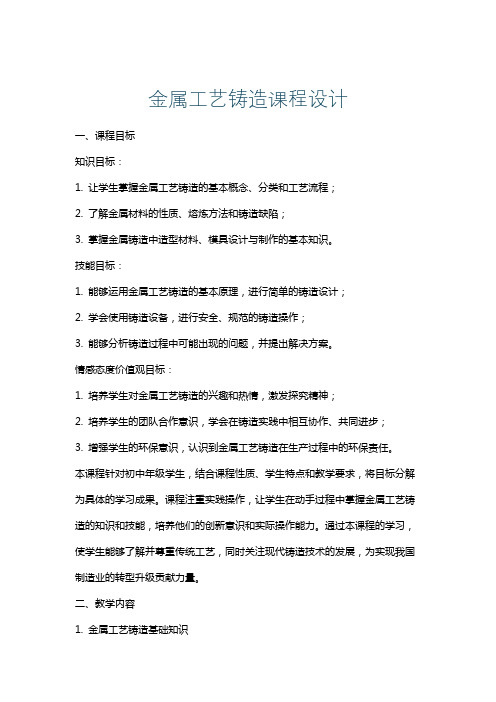
金属工艺铸造课程设计一、课程目标知识目标:1. 让学生掌握金属工艺铸造的基本概念、分类和工艺流程;2. 了解金属材料的性质、熔炼方法和铸造缺陷;3. 掌握金属铸造中造型材料、模具设计与制作的基本知识。
技能目标:1. 能够运用金属工艺铸造的基本原理,进行简单的铸造设计;2. 学会使用铸造设备,进行安全、规范的铸造操作;3. 能够分析铸造过程中可能出现的问题,并提出解决方案。
情感态度价值观目标:1. 培养学生对金属工艺铸造的兴趣和热情,激发探究精神;2. 培养学生的团队合作意识,学会在铸造实践中相互协作、共同进步;3. 增强学生的环保意识,认识到金属工艺铸造在生产过程中的环保责任。
本课程针对初中年级学生,结合课程性质、学生特点和教学要求,将目标分解为具体的学习成果。
课程注重实践操作,让学生在动手过程中掌握金属工艺铸造的知识和技能,培养他们的创新意识和实际操作能力。
通过本课程的学习,使学生能够了解并尊重传统工艺,同时关注现代铸造技术的发展,为实现我国制造业的转型升级贡献力量。
二、教学内容1. 金属工艺铸造基础知识- 铸造概念、分类及工艺流程- 金属材料的性质与选择- 教材章节:第一章 金属工艺铸造概述2. 铸造工艺及设备- 熔炼方法及设备- 铸造造型材料及制备- 铸造模具设计与制作- 教材章节:第二章 铸造工艺及设备3. 铸造缺陷与质量控制- 铸造缺陷的类型及成因- 铸造质量控制方法- 教材章节:第三章 铸造缺陷与质量控制4. 金属工艺铸造实践- 安全操作规程与注意事项- 简单铸造设计及操作- 分析并解决铸造过程中出现的问题- 教材章节:第四章 金属工艺铸造实践教学内容注重理论与实践相结合,以教材为依据,按照教学大纲逐步展开。
在教学过程中,教师应关注学生对基础知识的掌握,通过实践环节培养学生的动手能力和解决问题的能力。
教学进度安排合理,确保学生在课程学习中逐步达到教学目标。
三、教学方法本课程采用多样化的教学方法,旨在激发学生的学习兴趣,提高他们的主动性和实践能力。
- 1、下载文档前请自行甄别文档内容的完整性,平台不提供额外的编辑、内容补充、找答案等附加服务。
- 2、"仅部分预览"的文档,不可在线预览部分如存在完整性等问题,可反馈申请退款(可完整预览的文档不适用该条件!)。
- 3、如文档侵犯您的权益,请联系客服反馈,我们会尽快为您处理(人工客服工作时间:9:00-18:30)。
铸造工艺学课程设计题目:工艺学课程设计学院:专业:材料成型机控制工程班级:学号:姓名:指导老师:前言铸造工艺学课程是培养学生熟悉对零件及产品工艺设计的基本内容、原则、方法和步骤以及掌握铸造工艺和工装设计的基本技能的一门主要专业课。
课程设计则是铸造工艺学课程的实践性教学环节,同时也是我们铸造专业迎来的第一次全面的自主进行工艺和工装设计能力的训练。
在这个为期两周的过程里,我们有过紧张,有过茫然,有过喜悦,从中感受到了学习的艰辛,也收获到了学有所获的喜悦,回顾一下,我觉得进行铸造工艺学课程设计的目的有如下几点:通过课程设计实践,树立正确的设计思想,增强创新意识,培养综合运用铸造工艺学课程和其他先修课程的的理论与实际知识去分析和解决实际问题的能力。
通过制定和合理选择工艺方案,正确计算零件结构的工作能力,确定尺寸,掌握了浇冒口的作用及其原理,具有正确设计浇冒口系统的初步能力;掌握铸造工艺和工装设计的基本技能。
熟悉型砂必须具备的性能要求,原材料的基本规格及作用,并初步具备分析和解决型砂有关问题的能力。
熟悉涂料的作用、基本组成及质量的控制;了解提高铸件表面质量和尺寸精度的途径。
了解合金在铸造过程中容易产生的铸造缺陷以及采取相关的防止途径,并初步具备分析、解决这类缺陷的基本解决途径学习进行设计基础技能的训练,例如:计算、绘图、查阅设计资料和手册等。
1目录第一章零件铸造工艺分析......................................................4 1.1零件基本信息.................................................................................4 1.2材料成分要求.................................................................................4 1.3铸造工艺参数的确定 (4)1.3.1铸造尺寸公差和重量公差 (5)1.3.2机械加工余量 (5)1.3.3铸造收缩率 (5)1.3.4拔模斜度...........................................................................5 1.4其他工艺参数的确定 (5)1.4.1工艺补正量 (5)1.4.2分型负数 (5)1.4.3非加工壁厚的负余量 (5)1.4.4反变形量 (5)1.4.5分芯负数..............................................................................6 第二章铸造三维实体造型...............................................................6 2.1上冠件图纸技术要求 (6)2.2上冠件结构工艺分析 (6)2.3基于UG零件的三维造型 (6)2.3.1软件简介 (6)2.3.2零件的三维造型图..................................................................6 第三章铸造工艺方案设计...............................................................7 3.1工艺方案的确定 (7)3.1.1铸造方法 (7)3.1.2型(芯)砂配比 (8)3.1.3混砂工艺 (8)3.1.4铸造用涂料、分型剂及修补材料................................................8 3.2铸造熔炼 (8)3.2.1熔炼设备 (9)3.2.2熔炼工艺..............................................................................9 3.3分型面的选择.................................................................................9 3.4砂箱大小及砂箱中铸件数目的确定...................................................10 3.5砂芯设计及排气 (11)3.5.1芯头的基本尺寸 (11)3.5.2芯撑、芯骨的设计 (12)3.5.3砂芯的排气...........................................................................12 第四章浇冒系统的设计及计算.........................................................12 4.1浇注系统的类型及选择.....................................................................12 4.2浇注位置的选择 (12)24.3浇注系统各部分尺寸的计算 (13)4.3.1合金铸造性能分析 (13)4.3.2铁液在型内的上升速度 (13)4.3.3浇注系统截面尺寸设计............................................................14 4.4冒口设计计算 (14)4.4.1铸件工艺出品率 (14)4.4.2出气孔 (15)4.4.3冒口的作用及位置确定............................................................15 4.5冷铁设计及尺寸计算 (15)4.5.1冷铁的选用及作用 (15)4.5.2冷铁的尺寸及放置位置的选择……………………………………………15 总结……………………………………………………………………………………17 参考文献………………………………………………………………………………18 附图3第一章零件铸造工艺分析1.1 零件基本信息零件名称:上冠铸件。
零件材料:HT200。
产品生产纲领:成批量生产或者小批量生产。
结构:属厚、薄相差悬殊的大型回转体结构。
上冠零件图:图1.1 上冠零件图1.2 材料成分要求根据相关资料查得HT200具体成分及其含量如表1.2.1所示。
表1.2.1 HT200化学成分表(质量分数,%)C Si Mn P S Cr 3.3~3.55 1.95~2.15 0.60~0.90 0.15~0.30 ?0.08 ?0.121.3铸造工艺参数的确定1.3.1铸造尺寸公差和重量公差该铸件材质为HT200,手工造型,经查得,铸件的尺寸公差等级为13级;重量公差等级为13级,该铸件的重量公差为10,。
1.3.2机械加工余量该铸件为铸铁件,砂型人工造型,经查加工余量等级为H,经查得,该铸件法兰端面以及锥面的加工余量为13mm、孔的加工余量为8mm。
41.3.3铸造收缩率由于铸件的固态收缩(线收缩)将使铸件各部分尺寸小于模样原来的尺寸,因此,为了使铸件冷却后的尺寸与铸件图示尺寸一致,则需要在模样或芯盒上加上其收缩的尺寸。
加大的这部分尺寸为铸件的收缩量,一般用铸造收缩率表示。
经查可知该锥体铸件的线收缩率为1.0,。
1.3.4拔模斜度由于该铸件为锥形而且锥度大非常易于拔模,因此锥体部分不设拔模斜度,而在立壁处可设置3mm的起模斜度以便拔模。
拔模斜度的示意如图1.2和1.3。
图1.2外立壁拔模斜度示意图图1.3内立壁拔模斜度示意图1.4其他工艺参数的确定1.4.1工艺补正量对中小批量的铸件由于选用的收缩尺寸与实际的收缩率不符,或由于铸件产生变形、操作中不可避免的误差等原因使加工后铸件的尺寸小于图样要求尺寸,为提高尺寸精度,要在铸件相应的非加工表面上增加金属层厚度来弥补,但由于该件在垂直分型面的立壁上都设有较大的拔模斜度,故不放工艺补正量。
1.4.2分型负数干砂型、表面烘干型、自硬砂型以及砂型尺寸超过2m以上的湿型才应用分型负数。
而此铸件采用树脂自硬砂造型且砂箱尺寸小于2m,故不留分型负数。
1.4.3非加工壁厚的负余量由于该铸件采用木模,手工造型、造芯过程中,为取出木模要进行敲模,同时木模受潮时会膨胀,这些情况会使型腔尺寸增大,从而造成非加工壁厚增加,为保证铸件尺寸的准确性应该减小厚度尺寸,但由于该件在无拔模斜度,且该件不是很大故不放非加工壁厚的负余量。
1.4.4反变形量铸造较大的平板类、床身等类铸件时由于冷却速度的不均匀性,铸件冷却后常出现变形。
为了解决挠曲变形问题,在制作模样时,按铸件可能产生变形的相反方向做出反变形模样,使铸件冷却后变形的结果正好将反变形抵消,得到符合设计要求的铸件。
一般中小型壁厚差别不大且结构上刚度较大时,不必留反变形量。
由于该铸件为中小型铸件,所以不需留反变形量。
51.4.5分芯负数对于分段制造的长砂芯或分开制造的大砂芯,在接缝处应留出分芯间隙量,即在砂芯的分开面处,将砂芯尺寸减去间隙尺寸,被减去的尺寸即为分型负数。
此铸件没有分段制造的长砂芯,故可不设分芯负数。
第二章铸件三维实体造型2.1上冠件图纸技术要求:(1)铸件应作正回火处理;(2)铸件材料及机械性能应符合JB/T10264-2001的要求;(3)粗加工后按GB7233-87标准作超声波探伤检查,达?级要求;过流面加工后按GB/T9444-1988进行磁粉探伤,达?级要求;(4)同炉浇铸试验棒,回厂做化学成分和机械性能复核试验;(5)过流面用样板检查;(6)请刻出叶片进出水边与上冠的交点圆线。
2.2上冠件结构工艺分析:上冠件属壁厚相差悬殊的回转体结构,其主要壁厚为50mm,最小壁厚为25mm,最大壁厚为275mm,零件的外形轮廓尺寸为上法兰直径1510,法兰另一端直径, 217.2,该件质量为1665kg。
由零件图可知,该零件外形不是很复杂,内腔结构也不,复杂,壁厚不均匀,材料为灰铁,流动性较好,收缩大,在浇注时容易产生浇不足、冷隔、缩孔和缩松、热裂、内应力以及变性和冷裂等缺陷。
该件为中大型铸件,可采用砂型铸造中湿型铸造,操作方便,劳动量较小。
2.3基于UG零件的三维造型2.3.1软件简介UG NX是由Siemens PLM Software发布的集CAD/CAM/CAE一体化解决方案软件,它涵盖了产品设计、工程和制造中的全套开发流程。
NX 产品开发解决方案完全支持制造商所需的各种工具。
NX 与 UGS PLM 的其他解决方案的完整套件无缝结合,这些对于 CAD 、 CAM 和 CAE 在可控环境下的协同、产品数据管理、数据转换、数字化实体模型和可视化都是一个补充。