C1第二节塑性变形与强化机制
第七章-塑性变形

F0
★ ,均表示金属发生塑性变形的能力。 ★ 前者表示均匀变形能力,后者表示局部变形的能力。 ★ 无论强度或塑性指标,均与微观组织特征及状态有关。
§ 7-1 单晶体的塑性变形
一、弹性变形
1.宏观规律
在工程应力-应变曲线中的oe段, 与e 成线性关系
=Ee 或 t =Gg
当t =tk,滑移系启动,位错所受的力为: fk=tk·b
当t≥tk,则 f ≥fk,位错能够发生滑移。
fk 称为位错滑移的临界推动力。 f 的方向为位错线各点的法矢量方向,指向未滑移区。
tp
2G
1
2a
e (1)b
G为切变模量;为泊松比;a为滑移面间距;b为滑移方向上的原子间距。
P-N力:
tp
2G
1
2a
e (1)b
讨论:
● 若t≥tp,位错滑移。若取 =(低碳钢),则tp ≈10-3~10-4G,与实测 tk同数量级。
● 原子面密度越大的晶面,a越大;原子越密排的晶向,b越小。因此最 密排晶面及最密排晶向的tp 最小。
滑移的位错机制
在切应力作用下滑移面上下两部分原子的错动是位错逐步滑移的最终结果。
刃型位错滑移示意图
位 错 的 滑 移 示 意 图
位错滑移规律概括:
♣ 仅牵涉一列原子键的破坏,所需切应力小。 ♣ 刃型位错线运动方向与b平行,螺型位错线运动方向与b垂直。 ♣ 异号位错线运动方向相反;晶体运动方向均与b平行。 ♣ 位错线移出晶体表面形成一个b的变形台阶;n个位错形成n个b的变形台阶。 ♣ 位错较多的晶面才有可能发生较高程度的滑移,因此滑移线分布是不均匀的。 ♣ 螺型位错b的可动性大于刃型位错,可发生交滑移(如fcc晶体的双交滑移)。
工程材料--金属的塑性变形与再结晶-塑变对金属组织和性能的影响
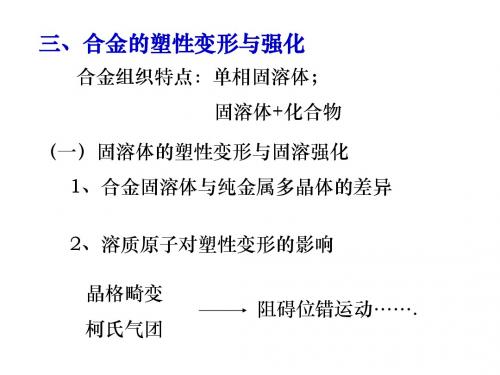
②预冷变形度ε的影响
预变形度与再结晶晶粒的关系
(三)常见强化机制总结
1、细晶强化
2、固溶强化
3、加工硬化(位错强化、形变强化) 4、第二相强化
第四节
金 属 的 热 加 工
一、金属热加工概念
1、金属学上冷、热加工的区别
T≥T再(≈0.4Tm),无加工硬化——叫热加工
T < T再,有加工硬化——叫冷加工
例:纯Pb, T再=0.4*(328+273)-273=-33℃
纯W, T再=1200 ℃
2、热加工实质
冷变形强化 再结晶软化 两者交替进行的综合过程
二、热加工的作用
1、改变形状,使之符合要求 2、消除(或减轻)铸造缺陷 细化晶粒 3、改善组织 成分、组织均匀化
4、形成流线 ①流线定义: 第二相沿变形方向被拉长 ②流线对性能的影响:各向异性 ③流线在工件中的合理分布
1、多相合金与单相合金固溶体的差异
2、第二相对塑性变形的影响
硬相本身阻碍位错运动
相界面晶格畸变阻碍位错运动
3、变形抗力
相界面积↑→ σb、HB ↑
4、多相合金的变形能力与第二相有关
包括: 数量、大小、形状、分布 △数量、大小的影响:越少、越小→ 对变形 能力削弱↓
△形状、分布的影响:
①硬相呈网状分布时: σs ↓ ,δ、ak↓ ↓ ②硬相呈片状时: 片越薄、片间距越小 → σs 、HB↑的同时 δ、ak↓ 越少 ③硬相呈颗粒时:σs 、HB↑的同时δ、ak↓ 越少。且硬质点越小,越圆,越均匀分布越好。 弥散强化:指由于第二相以细小质点的形态 分布于基体中使合金显著强化的现象。
锻钢曲轴中的流线分布
5、形成带状组织 ①带状组织定义:热轧低碳钢中珠光体和铁素体 沿轧制方向呈带状或层状分布。 ②带状组织对性能影响——使机械性能↓ ③带状组织的消除: 扩散退火/正火
塑性成形一二章重点概念整理(精)

塑性是一种在外力作用下,是金属材料发生塑性变形而不破坏其完整性的能力。
塑性成形是指金属材料在一定外力作用下利用其塑性而使其成形并获得一定力学性能的加工方法。
一次加工的方法:轧制、挤压、拉拔。
塑性变形机理 :一、晶内变形滑移 :指晶体在力的作用下,晶体的一部分沿一定的晶面和晶向相对于晶体的宁一部分发生相对滑动或切变。
滑移系 :一格滑移面和其上的一个滑移方向体心立方 :12面心立方 :12密排六方 :3孪生 :是指晶体在切应力的作用下,晶体的一部分沿着一定的晶面和一定的晶向发生均匀切变。
二、晶间变形冷塑性变形对金属组织和性能的影响 :一、组织的变化 :1. 晶粒形状的变化 2. 晶粒内产生的亚结构 3. 晶粒位向改变二、性能的变化 :加工硬化 :指金属随着变形程度的增加,金属的强度、硬度增加,而塑性韧性降低。
加工硬化是强化金属的重要途径。
金属热态下的塑性变形 :一、热塑性变形时的软化过程 :动态回复、动态再结晶、静态回复、静态再结晶、亚动态再结晶、二、金属热塑性变形机理主要有:晶内滑移,晶内孪生,晶界滑移和扩散蠕变等。
热塑性变形对金属组织和性能的影响 :改善晶粒组织、锻合内部缺陷、破碎并改善碳化物和非金属夹杂物在钢中的分布、形成纤维组织、超塑性变形 :在一些特定条件下,如一定的化学成分、特定的显微组织、特定的变形温度和应变速率等, 金属会表现出异乎寻常的高塑性状态,即所谓超常的塑性变形。
超塑性 :某些合金在特定的变形条件下具有均匀变形能力,其伸长率可以达到百分之几百、甚至几千,这就是超塑性。
超塑性种类 :细晶超塑性、相变超塑性。
影响细晶超塑性的主要因素 :应变速率的影响、变形温度的影响、组织的影响。
变形温度对金属塑性的影响 :总趋势 :随着温度升高,塑性增加,但是这种增加并非简单的线性上升, 再加热过程的某些温度区间,往往由于相态或晶粒边界状态的变化而出现脆性区、使金属的塑性降低。
温度升高使金属塑性增加的原因 :1. 发生回复或再结晶 2. 原子动能增加,使位错活动性提高、滑移系增多,从而改善了晶粒之间变形的协调性。
材科基考点强化(第7讲 塑性形变)

主要考点考点1:弹性形变考点2:单晶体的塑性变形考点3:施密特定律考点4:多晶体的塑性变形(细晶强化)考点5:固溶体合金的塑性变形(固溶强化)考点6:复相合金的塑性变形(弥散强化)考点7:塑性变形后材料组织的变化考点8:塑性变形后材料性能的变化考点9:综合题考点1:弹性形变。
例1(名词解释):弹性形变、滞弹性和弹性变形能。
考点2:单晶体的塑性变形。
例1(名词解释):孪晶。
例2:常温下金属塑性变形有哪些主要机制?它们间的主要差异是什么?例3(判断题):金属晶体中,密排六方晶体比面心立方晶体的塑性好,更适宜塑性加工。
考点3:施密特定律。
例1(名词解释):临界分切应力。
例2(名词解释):施密特(Schmid )因子。
例3:单晶体的临界分切应力值与( )有关。
A .外力相对滑移系的取向B .拉伸时的屈服应力C .晶体的类型和纯度D .拉伸时的应变大小例4(判断题):根据施密特定律,晶体滑移面平行于拉力轴时最容易产生滑移。
例5:已知纯铜的{111}[110]滑移系的临界切应力c τ为1Mpa ,考点4:多晶体的塑性变形(细晶强化)。
例1:多晶体塑性变形时,至少需要( )独立的滑移系。
A .3个B .8个C .5个例2:实际金属材料的性能在不同方向并不存在差异,这是因为( )。
A .晶体不同方向性能相同B .晶体的各向异性现在测量不出来C .金属材料结构不是晶体D .大量晶粒随机取向掩盖了各向异性例3:解析Hall-Petch (霍尔-佩奇)公式。
例4:有两块相同成分的固溶体合金,其区别仅为一块晶粒较粗大,另一块晶粒较细小。
试回答下列问题:(1)哪块合金的塑性更好,为什么?(2)在冷塑性变形量相同的情况下,哪一块合金变形所消耗的变形功更大,为什么?(3)当加热这两块经冷塑性变形的合金时,哪一块合金更易发生再结晶,为什么?例5:已知当退火后纯铁的晶粒大小为16个/2mm 时,屈服强度s σ=100MPa ;当晶粒大小为4096个/2mm 时,s σ=250MPa ,试求晶粒大小为256个/2mm 时,屈服强度s σ的值。
2011塑性变形机制(1)
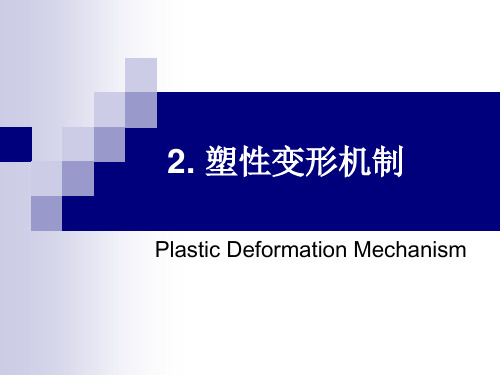
滑移面(Slip Plane)和滑移方向 和滑移方向(Slip 滑移面(Slip Plane)和滑移方向(Slip Direction):
塑性变形时位错只沿着一定的晶面和晶向运动, 塑性变形时位错只沿着一定的晶面和晶向运动,晶体沿某 些特定的晶面及方向相对错开, 些特定的晶面及方向相对错开,这些晶面和晶向分别称 滑移面” 滑移方向” “滑移面”和“滑移方向”。 滑移面与滑移方向称为滑移要素 滑移面与滑移方向称为滑移要素 滑移面应是面间距最大的密排面(面间距最大, 滑移面应是面间距最大的密排面(面间距最大,面间结合 密排面 力最弱,切变阻力最小),滑移方向方向是原子的最密排 ),滑移方向方向是原子的最 力最弱,切变阻力最小),滑移方向方向是原子的最密排 方向(原子间距最小,柏氏矢量最小,滑移阻力最小)。 方向(原子间距最小,柏氏矢量最小,滑移阻力最小)。
A A0
滑移方向
S S
A
滑移面上沿滑移方向的分切应力: 滑移面上沿滑移方向的分切应力:
τ = S cos λ = σ cos ϕ cos λ
滑移面上的正应力: 滑移面上的正应力:
(2(2-2)
σ n = S cos ϕ = σ cos 2 ϕ
由(2-2),σ↑,则 τ↑ ),σ↑, σ↑
外力在滑移方向的分切应力
机械工程中的材料塑性变形与强度研究

机械工程中的材料塑性变形与强度研究材料的塑性变形和强度是机械工程中一个重要的研究领域。
塑性变形是指材料在受力的作用下发生的可逆性形变,而强度则是材料抵抗外力破坏的能力。
研究材料的塑性变形与强度旨在了解材料的性能以及优化材料的应用。
1. 材料塑性变形的机制材料的塑性变形是通过晶格滑移和晶间面滑移等机制实现的。
晶格滑移是指晶格中原子的相互滑移和重排,这种滑移在材料受力时可以使其发生可逆性的塑性变形。
而晶间面滑移是指材料中晶格间的变形和滑移,这种滑移在受力作用下可以使材料发生不可逆的塑性变形。
2. 材料塑性变形的影响因素材料的塑性变形受多种因素的影响,其中最主要的因素是温度、晶体方向和应变速率。
温度的升高可以增加材料的塑性,使其更容易发生塑性变形。
晶体方向也会影响材料的塑性变形,一些晶体方向对应力集中,容易发生滑移和变形。
应变速率是指受力下材料发生塑性变形时的变形速率,较高的应变速率会导致材料塑性变形的难度增加。
3. 材料强度的研究材料的强度是指其抵抗外力破坏的能力。
研究材料的强度旨在了解材料在不同应力下的破坏行为,进而改进材料的结构和性能。
强度的研究可以通过实验和模拟计算来进行。
实验可以通过拉伸试验、压缩试验等方式来测定材料的强度。
而模拟计算则可以根据材料的力学性质和力学模型进行,通过数值计算得到材料在不同应力下的应变和变形情况。
4. 材料塑性变形与强度的关系材料的塑性变形与强度有密切的关系。
塑性变形能力较强的材料往往具有较高的强度,因为它们能够承受更大的外力使其发生塑性变形。
对于一些需要具备较高强度的应用,如航天器、汽车等,需要选择具有良好塑性变形能力的材料,以承受各种复杂的外力条件。
总结起来,机械工程中的材料塑性变形与强度研究是一个复杂而繁多的领域。
研究材料的塑性变形和强度不仅能够提升材料的应用性能,也对于设计和制造具有高抗破坏能力的工程结构具有重要意义。
了解材料的塑性变形和强度机制,对于推动机械工程领域的发展起到关键作用。
金属材料塑性变形机制与特点

第三章 塑性变形
单击添加副标题
3.1金属材料塑性变形机制与特点
单击添加副标题
3.1.1 金属晶体塑性变形的机制 3.1.2 多晶体材料塑性变形特点
3.1.1 金属晶体塑性变形的机制
定义 fcc: {111} <110>; bcc: {110} {112} {123} <111> 滑移系 hcp: {0001} 定义 hcp 滑移系少,故常以孪生方式进行 fcc bcc 孪生变形量是很有限的,它的作用改变晶体取向,以便启动新的滑移系统,或使难于滑移的取向改变为易于滑移的取向。
位错运动速率与外力有强烈依存关系。
01
02
03
屈服现象产生与下述三个因素有关:
冷变形金属的真应力-应变关系
颈缩条件分析
韧性的概念及静力韧度分析
3.3真应力-应变曲线及形变强化规律
当应力超过屈服强度之后,塑性变形并不像屈服平台那样连续流变下去,而需要继续增加外力才能继续进行,于是应力-应变曲线上表现为流变应力不断上升,出现了所谓形变强化现象。材料在形变强化阶段的变形规律用其应力-应变曲线(也叫流变曲线)描述。
物理屈服现象首先在低碳钢中发现,尔后在含有微量间隙溶质原子的体心立方金属,如Fe、Mo、Nb 、Ta等,以及密排六方金属,如Cd和Zn中也发现有屈服现象。
01
对屈服现象的解释,早期比较公认的是溶质原子形成Cottrell气团对位错钉扎的理论。以后在共价键晶体如硅和锗,以及无位错晶体如铜晶须中也观察到物理屈服现象。
则定义二者的比值: α——软性系数, α↑→τmax↑→应力状态越软,金属易于 先产生塑性变形。 α↓→应力状态越硬→金属易于产生脆性 断裂。
测硬度时,其应力状态相当于三向不等压缩,因此,硬度试验时的加载方式属于很软的应力状态。
金属塑性成形原理---第二章_金属塑性变形的物理基础
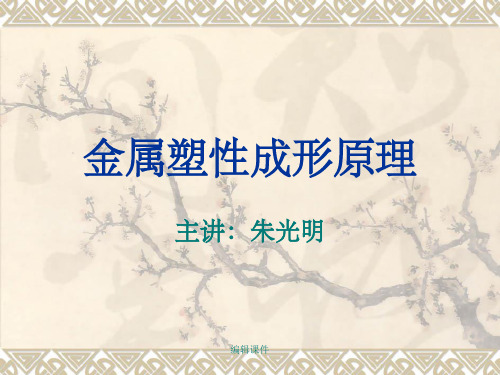
位错的攀移
❖ 螺型位错无攀移
❖ 正攀移——正刃型位错位错线上移
负刃型位错位错线下移
编辑课件
位错的交割
❖ 两根刃型位错线都在各自的滑移面上移动,
则在相遇后交截分别形成各界,形成割阶后
仍分别在各自的平面内运动。
❖ 刃型位错和螺型位错交割时,在各自的位错
线上形成刃型割阶,位错线也能继续滑移。
❖ 螺型位错和螺型位错交割时,相交后形成的
❖ 假设:理想晶体两排原子相距为a,同排原子间距
为b。原子在平衡位置时,能量处于最低的位置。
在外力τ作用下,原子偏离平衡位置时,能量上升,
原子能量随位置的变化为一余弦函数。
❖ 通过计算晶体的临界剪切应力,并与实际的临界
剪切应力进行比较,人们发现,理论计算的剪切
强度比实验所得到的剪切强度要高一千倍以上。
编辑课件
典型的晶胞结构
编辑课件
典型的晶胞结构
编辑课件
三种晶胞的晶格结构
编辑课件
一、塑性变形机理
实际金属的晶体结构
❖ 单晶体:各方向上的原子密度不同——各向
异性
❖ 多晶体:晶粒方向性互相抵消——各向同性
❖ 塑性成形所用的金属材料绝大多数为多晶
体,其变形过程比单晶体复杂的多。
编辑课件
多晶体塑性变形的分类
加工中,会使变形力显著增
加,对成形工件和模具都有
III.抛物线硬化阶段:
一定的损害作用;但利用金
与位错的交滑移过程有关,
θ3
随应变增加而降低,应力应变
属加工硬化的性质,对材料
曲线变为抛物线。
进行预处理,会使其力学性
能提高
编辑课件
2.2 金属热态下的塑性变形