金属的塑性变形和强化
金属材料的强化方法
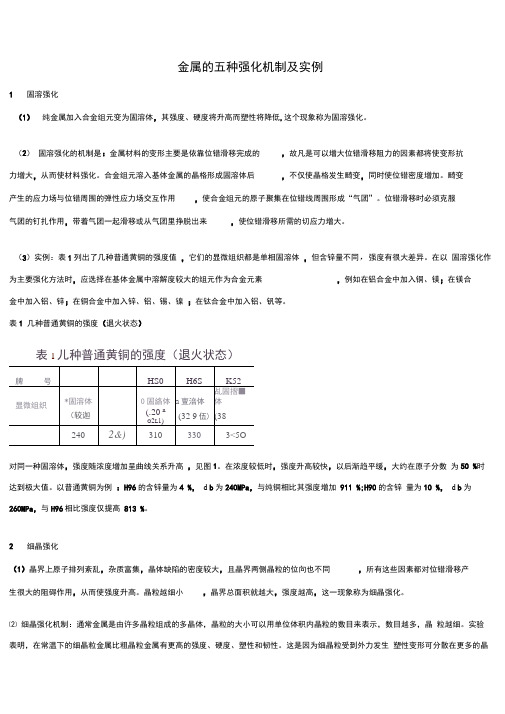
金属的五种强化机制及实例1固溶强化(1)纯金属加入合金组元变为固溶体,其强度、硬度将升高而塑性将降低,这个现象称为固溶强化。
(2)固溶强化的机制是:金属材料的变形主要是依靠位错滑移完成的,故凡是可以增大位错滑移阻力的因素都将使变形抗力增大,从而使材料强化。
合金组元溶入基体金属的晶格形成固溶体后,不仅使晶格发生畸变,同时使位错密度增加。
畸变产生的应力场与位错周围的弹性应力场交互作用,使合金组元的原子聚集在位错线周围形成“气团”。
位错滑移时必须克服气团的钉扎作用,带着气团一起滑移或从气团里挣脱出来,使位错滑移所需的切应力增大。
(3)实例:表1列出了几种普通黄铜的强度值,它们的显微组织都是单相固溶体,但含锌量不同,强度有很大差异。
在以固溶强化作为主要强化方法时,应选择在基体金属中溶解度较大的组元作为合金元素,例如在铝合金中加入铜、镁;在镁合金中加入铝、锌;在铜合金中加入锌、铝、锡、镍;在钛合金中加入铝、钒等。
表1 几种普通黄铜的强度(退火状态)表1儿种普通黄铜的强度(退火状态)对同一种固溶体,强度随浓度增加呈曲线关系升高,见图1。
在浓度较低时,强度升高较快,以后渐趋平缓,大约在原子分数为50 %时达到极大值。
以普通黄铜为例:H96的含锌量为4 %, d b为240MPa,与纯铜相比其强度增加911 %;H90的含锌量为10 %, d b为260MPa,与H96相比强度仅提高813 %。
2细晶强化(1)晶界上原子排列紊乱,杂质富集,晶体缺陷的密度较大,且晶界两侧晶粒的位向也不同,所有这些因素都对位错滑移产生很大的阻碍作用,从而使强度升高。
晶粒越细小,晶界总面积就越大,强度越高,这一现象称为细晶强化。
⑵ 细晶强化机制:通常金属是由许多晶粒组成的多晶体,晶粒的大小可以用单位体积内晶粒的数目来表示,数目越多,晶粒越细。
实验表明,在常温下的细晶粒金属比粗晶粒金属有更高的强度、硬度、塑性和韧性。
这是因为细晶粒受到外力发生塑性变形可分散在更多的晶粒内进行,塑性变形较均匀,应力集中较小;此外,晶粒越细,晶界面积越大,晶界越曲折,越不利于裂纹的扩展。
金属材料的塑性变形行为及其动力学机理
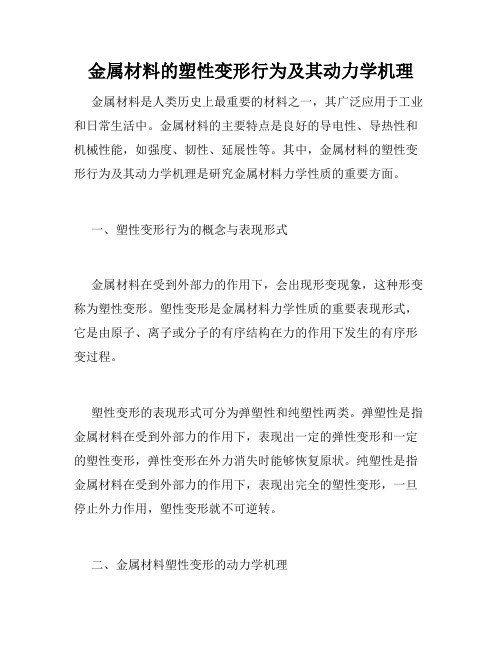
金属材料的塑性变形行为及其动力学机理金属材料是人类历史上最重要的材料之一,其广泛应用于工业和日常生活中。
金属材料的主要特点是良好的导电性、导热性和机械性能,如强度、韧性、延展性等。
其中,金属材料的塑性变形行为及其动力学机理是研究金属材料力学性质的重要方面。
一、塑性变形行为的概念与表现形式金属材料在受到外部力的作用下,会出现形变现象,这种形变称为塑性变形。
塑性变形是金属材料力学性质的重要表现形式,它是由原子、离子或分子的有序结构在力的作用下发生的有序形变过程。
塑性变形的表现形式可分为弹塑性和纯塑性两类。
弹塑性是指金属材料在受到外部力的作用下,表现出一定的弹性变形和一定的塑性变形,弹性变形在外力消失时能够恢复原状。
纯塑性是指金属材料在受到外部力的作用下,表现出完全的塑性变形,一旦停止外力作用,塑性变形就不可逆转。
二、金属材料塑性变形的动力学机理金属材料塑性变形的动力学机理主要包括滑移和剪切。
滑移是指晶格内部原子、离子或分子在外部应力作用下,在一定的晶格面和方向上沿晶格平面错开,使得整个晶体沿应力方向发生了塑性形变。
可以把滑移想象成晶格平面的滑动,其中滑动较容易发生的是(111)面和(100)面。
滑移不仅适用于单晶材料,也适用于多晶和多晶固溶体材料。
剪切是指在晶体中沿着一个晶面剪切另一个晶面而引起塑性形变。
剪切主要涉及到晶界和变形区的相互作用,其中晶界可以作为剪切面。
剪切的能量消耗要比滑移大得多,但是它对温度敏感性比滑移小,容易引起大规模位错滞后和晶界移动。
在金属材料中,滑移和剪切是相互竞争的,它们的作用对金属的塑性变形和强度产生了重要影响。
三、金属材料塑性变形的调节和增强方法金属材料塑性变形的调节和增强主要包括合金化、微结构控制和纳米加工等方法。
合金化是一种有效的方法,可以通过合理选择合金元素来控制晶体结构和化学成分,从而调控金属材料的塑性变形。
例如,添加易形变的合金元素可以促进位错堆积,增加位错密度和位错强度,从而提高金属材料的塑性变形。
简述金属材料常见的强化机制
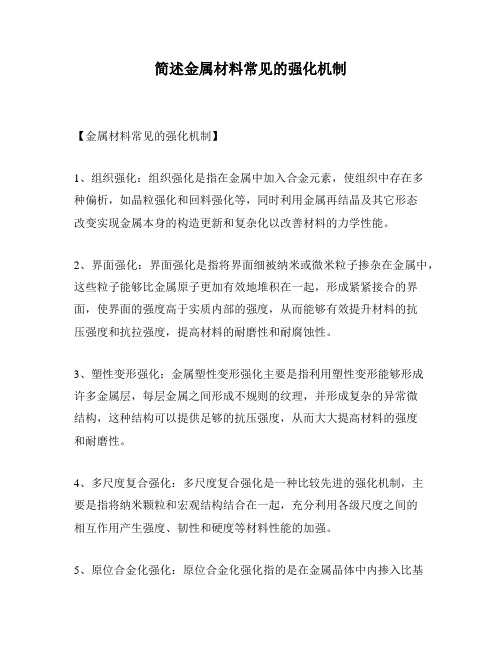
简述金属材料常见的强化机制
【金属材料常见的强化机制】
1、组织强化:组织强化是指在金属中加入合金元素,使组织中存在多
种偏析,如晶粒强化和回料强化等,同时利用金属再结晶及其它形态
改变实现金属本身的构造更新和复杂化以改善材料的力学性能。
2、界面强化:界面强化是指将界面细被纳米或微米粒子掺杂在金属中,这些粒子能够比金属原子更加有效地堆积在一起,形成紧紧接合的界面,使界面的强度高于实质内部的强度,从而能够有效提升材料的抗
压强度和抗拉强度,提高材料的耐磨性和耐腐蚀性。
3、塑性变形强化:金属塑性变形强化主要是指利用塑性变形能够形成
许多金属层,每层金属之间形成不规则的纹理,并形成复杂的异常微
结构,这种结构可以提供足够的抗压强度,从而大大提高材料的强度
和耐磨性。
4、多尺度复合强化:多尺度复合强化是一种比较先进的强化机制,主
要是指将纳米颗粒和宏观结构结合在一起,充分利用各级尺度之间的
相互作用产生强度、韧性和硬度等材料性能的加强。
5、原位合金化强化:原位合金化强化指的是在金属晶体中内掺入比基
体原子更贵重的合金,因为这种原位合金能够有效改变铁素体组织的形貌,使晶体变得硬而脆,从而提高材料的强度和耐蚀性。
6、热处理强化:热处理强化是指将原材料经历不同的热处理过程,从而实现对材料金属晶体的形貌的改变,从而调整材料的力学性能,改变组织构造,提高材料的硬度和耐腐蚀性。
金属的强化方法及机理
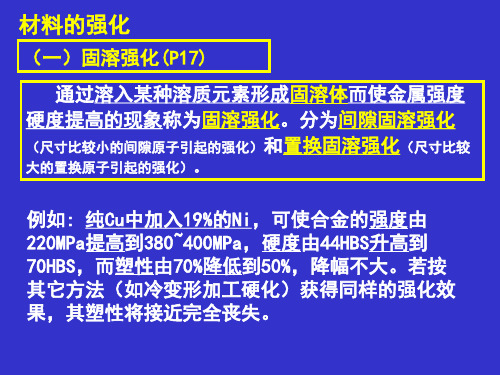
把某一成分的合金加热到固溶度曲线以B元 素析出,得到过饱和α固溶体,这就是固溶处理。
经固溶处理后的合金在室温下放置或加热到低于溶解度曲线的某 一温度保温,合金将产生脱溶析出,即B将以新相的形式从过饱和 α相中弥散析出,这个过程即是时效。通常将在室温下放置产生 的时效称为自然时效;将加热到室温以上某一温度进行的时效称 为人工时效。
金属材料经冷塑性变形后,其强度与硬度随变形 程度的增加而提高,而塑性、韧性则很快降低的 现象为加工硬化或形变强化。
例如:自行车链条板(16Mn钢板)
原始厚度3.5mm
150HB
五次冷轧后1.2mm 275HB
b=520MPa b>1000MPa
又如:冷拔高强度钢丝和冷卷弹簧是利用加工变 形来提高他们的强度和弹性极限;坦克和拖拉机 的履带、破碎机的颚板以及铁路的道叉等也都是 利用加工硬化来提高他们的硬度和耐磨性的。
实验证明,金属的屈服强度与其晶粒尺寸之 间有下列关系:
σs=σ0+ K/d1/2 此式称为霍耳-配奇公式。
式中:σ0 ——为常数,相当于单晶体的屈服强度; d——为多晶体中各晶粒的平均直径; K——为晶界对强度影响程度的常数, 与晶界结构有关。
σs ——开始发生塑性变形的最小应力
细晶强化机制:晶界是位错运动过程中的障碍。 晶界增多,对位错运动的阻碍作用增强,致使位 错在晶界处塞积(即位错密度增加),金属的强 度增加;在单个晶粒内部,塞积的位错群的长度 减小,应力集中较小,不足于使位错源开动,必 须增加外力。
2、加工硬化机制
金属的塑性变形是通过滑移进行的。在塑性变形 过程中,由于位错塞积(位错运动过程中遇到障 碍受阻)、位错之间的弹性作用、位错割阶等造 成位错运动受阻,从而使材料的强度提高。
简述金属材料的四种强化机制
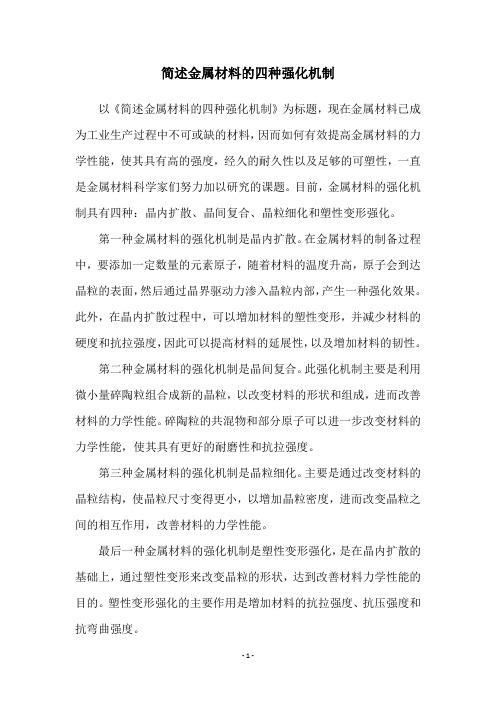
简述金属材料的四种强化机制
以《简述金属材料的四种强化机制》为标题,现在金属材料已成为工业生产过程中不可或缺的材料,因而如何有效提高金属材料的力学性能,使其具有高的强度,经久的耐久性以及足够的可塑性,一直是金属材料科学家们努力加以研究的课题。
目前,金属材料的强化机制具有四种:晶内扩散、晶间复合、晶粒细化和塑性变形强化。
第一种金属材料的强化机制是晶内扩散。
在金属材料的制备过程中,要添加一定数量的元素原子,随着材料的温度升高,原子会到达晶粒的表面,然后通过晶界驱动力渗入晶粒内部,产生一种强化效果。
此外,在晶内扩散过程中,可以增加材料的塑性变形,并减少材料的硬度和抗拉强度,因此可以提高材料的延展性,以及增加材料的韧性。
第二种金属材料的强化机制是晶间复合。
此强化机制主要是利用微小量碎陶粒组合成新的晶粒,以改变材料的形状和组成,进而改善材料的力学性能。
碎陶粒的共混物和部分原子可以进一步改变材料的力学性能,使其具有更好的耐磨性和抗拉强度。
第三种金属材料的强化机制是晶粒细化。
主要是通过改变材料的晶粒结构,使晶粒尺寸变得更小,以增加晶粒密度,进而改变晶粒之间的相互作用,改善材料的力学性能。
最后一种金属材料的强化机制是塑性变形强化,是在晶内扩散的基础上,通过塑性变形来改变晶粒的形状,达到改善材料力学性能的目的。
塑性变形强化的主要作用是增加材料的抗拉强度、抗压强度和抗弯曲强度。
总之,金属材料的四种强化机制分别是晶内扩散、晶间复合、晶粒细化和塑性变形强化,各自在工业生产中发挥了重要作用,研究者们还将持续努力,以进一步提升金属材料的力学性能。
金属材料的变形机制与塑性行为

金属材料的变形机制与塑性行为金属材料在工程领域中起着重要的作用,而金属的塑性行为和变形机制则是决定其力学性能的重要因素之一。
本文将探讨金属材料的变形机制与塑性行为。
1. 弹性与塑性首先,我们需要了解金属材料的弹性与塑性。
弹性是指金属在受力后能够恢复原状的性质,即应力与应变呈线性关系。
而塑性则是指金属在受力后会发生永久性形变的性质,即应力与应变不再呈线性关系,金属会发生塑性变形。
2. 变形机制金属材料发生塑性变形时,涉及到多种变形机制,其中最重要的包括滑移、扩散和晶体重新排列。
滑移是一种比较常见的金属变形机制。
金属内部的晶体通过滑动来实现变形。
在外力作用下,应变施加到晶体中的部分原子上,这些原子会沿着滑移面滑动,使晶体发生塑性变形。
扩散是指原子在晶体中的扩散过程。
扩散可以使原子重新排列,从而为滑移提供必要的能量。
正是因为扩散的存在,滑移机制才能够进行。
晶体重新排列是指晶体中原子重新排列的过程。
当外力作用于金属时,晶体内的原子会发生重新排列,以使晶体更好地适应外力。
在这个过程中,晶体内的原子会发生位错的形成和移动。
3. 晶体结构与塑性行为晶体结构是决定金属塑性行为的重要因素之一。
晶体的晶格结构有不同的排列方式,其中最常见的有面心立方和体心立方结构。
不同的晶体结构具有不同的变形机制。
体心立方结构的金属通常具有较高的强度和较低的塑性。
这是因为体心立方结构的金属在变形时,需要克服与晶格点的最近邻原子有较大的距离。
相比之下,面心立方结构的金属相对塑性较好,因为该结构中原子之间的间距较小,变形更容易发生。
此外,晶体晶格中的缺陷也会影响金属的塑性行为。
例如,在晶体中存在的位错是金属变形的主要缺陷之一。
位错会使金属的应力集中,进而导致金属发生塑性变形。
4. 温度对塑性的影响温度是另一个影响金属塑性的重要因素。
晶体在不同温度下具有不同的塑性行为。
一般来说,高温下金属的塑性较好,而低温下金属的塑性较差。
高温下,金属的活动性增强,位错的移动更容易发生。
金属的塑性变形、纤维组织及其对金属性能的影响
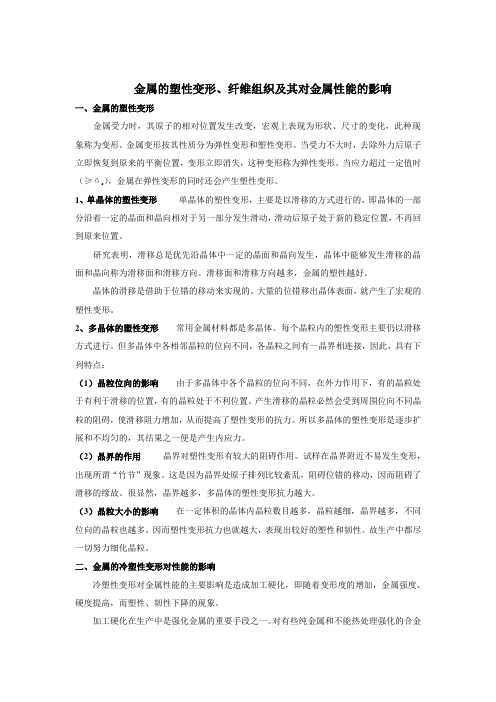
金属的塑性变形、纤维组织及其对金属性能的影响一、金属的塑性变形金属受力时,其原子的相对位置发生改变,宏观上表现为形状、尺寸的变化,此种现象称为变形。
金属变形按其性质分为弹性变形和塑性变形。
当受力不大时,去除外力后原子立即恢复到原来的平衡位置,变形立即消失,这种变形称为弹性变形。
当应力超过一定值时(≥бs),金属在弹性变形的同时还会产生塑性变形。
1、单晶体的塑性变形单晶体的塑性变形,主要是以滑移的方式进行的,即晶体的一部分沿着一定的晶面和晶向相对于另一部分发生滑动,滑动后原子处于新的稳定位置,不再回到原来位置。
研究表明,滑移总是优先沿晶体中一定的晶面和晶向发生,晶体中能够发生滑移的晶面和晶向称为滑移面和滑移方向。
滑移面和滑移方向越多,金属的塑性越好。
晶体的滑移是借助于位错的移动来实现的。
大量的位错移出晶体表面,就产生了宏观的塑性变形。
2、多晶体的塑性变形常用金属材料都是多晶体。
每个晶粒内的塑性变形主要仍以滑移方式进行。
但多晶体中各相邻晶粒的位向不同,各晶粒之间有一晶界相连接,因此,具有下列特点:(1)晶粒位向的影响由于多晶体中各个晶粒的位向不同,在外力作用下,有的晶粒处于有利于滑移的位置,有的晶粒处于不利位置。
产生滑移的晶粒必然会受到周围位向不同晶粒的阻碍,使滑移阻力增加,从而提高了塑性变形的抗力。
所以多晶体的塑性变形是逐步扩展和不均匀的,其结果之一便是产生内应力。
(2)晶界的作用晶界对塑性变形有较大的阻碍作用。
试样在晶界附近不易发生变形,出现所谓“竹节”现象。
这是因为晶界处原子排列比较紊乱,阻碍位错的移动,因而阻碍了滑移的缘故。
很显然,晶界越多,多晶体的塑性变形抗力越大。
(3)晶粒大小的影响在一定体积的晶体内晶粒数目越多,晶粒越细,晶界越多,不同位向的晶粒也越多。
因而塑性变形抗力也就越大,表现出较好的塑性和韧性。
故生产中都尽一切努力细化晶粒。
二、金属的冷塑性变形对性能的影响冷塑性变形对金属性能的主要影响是造成加工硬化,即随着变形度的增加,金属强度、硬度提高,而塑性、韧性下降的现象。
金属的塑性变形和强化

⾦属的塑性变形和强化第六章⾦属的塑性变形和强化练习与思考题1 什么叫强化?可能采⽤那些强化⼿段来强化⾦属?采⽤各种⽅式使得⾦属塑性变形时位错运动的阻⼒增⼤,即可实现⾦属材料的强化。
如冷变形的加⼯硬化,添加合⾦的固溶强化和析出沉淀强化,细晶强化,亚结构强化,多相组织的相变强化等。
2 ⾯⼼⽴⽅单晶体的应⼒应变曲线的硬化系数θ为什么各个阶段各不相同?θⅡ最⼤的原因是什么?第I阶段⼀般认为只有⼀个滑移系开动,强化作⽤不⼤,θI较⼩,为易滑移阶段;第Ⅱ阶段为线性强化阶段,出现了多系滑移;多系滑移产⽣⼤量位错,使得位错运动阻⼒明显增⼤,尤其是⾯⾓位错的出现,强烈的阻⽌位错源开动,并强最⼤。
烈阻⽌其他滑移⾯上的位错运动,从⽽使得这⼀阶段硬化指数θⅡ第Ⅲ阶段出现了交滑移,从⽽拜托了⾯⾓位错的封锁,使原被塞积的位错继续运动,使得位错的⾃由路程增⼤。
即在加⼯硬化的同时,存在着动态回复的软化过程,从⽽造成θⅢ随着γ增⼤⽽逐渐降低的现象。
3 晶界对塑性变形有什么影响?晶界对塑性变形过程的影响,主要是在温度较低时晶界阻碍滑移进⾏引起的障碍强化作⽤和变形连续性要求晶界附近多系滑移引起的强化作⽤。
为使多晶体塑性变形过程不破坏晶界连续性,相邻的晶粒必须协调变形。
多晶体塑性变形⼀旦变形传播到相邻的晶粒,就产⽣了多系滑移。
位错运动遇到的障碍⽐单系滑移多,阻⼒要增加。
存在晶界及晶界两侧晶粒取向有差别,多晶体的塑性变形有着很⼤的不均匀性。
在单个晶粒内,晶界变形要低于晶粒中⼼区域;由于细晶组织中晶界占的⽐例要⼤于粗晶组织中的晶界,细晶组织的强化效果⾼于粗晶组织。
4 多系滑移为何能起到强化作⽤?⾦属多晶体塑性变形⼀开始为什么就出现了多系滑移的强化?多系滑移产⽣⼤量位错,位错间相互作⽤使得位错运动阻⼒明显增⼤,尤其是⾯⾓位错的出现,强烈的阻⽌位错源开动,并强烈阻⽌其他滑移⾯上的位错运动。
多晶体材料中,某⼀晶粒产⽣滑移变形⽽不破坏晶界连续性,相邻的晶粒必须协调变形。
- 1、下载文档前请自行甄别文档内容的完整性,平台不提供额外的编辑、内容补充、找答案等附加服务。
- 2、"仅部分预览"的文档,不可在线预览部分如存在完整性等问题,可反馈申请退款(可完整预览的文档不适用该条件!)。
- 3、如文档侵犯您的权益,请联系客服反馈,我们会尽快为您处理(人工客服工作时间:9:00-18:30)。
第六章金属的塑性变形和强化练习与思考题1 什么叫强化?可能采用那些强化手段来强化金属?采用各种方式使得金属塑性变形时位错运动的阻力增大,即可实现金属材料的强化。
如冷变形的加工硬化,添加合金的固溶强化和析出沉淀强化,细晶强化,亚结构强化,多相组织的相变强化等。
2 面心立方单晶体的应力应变曲线的硬化系数θ为什么各个阶段各不相同?θⅡ最大的原因是什么?第I阶段一般认为只有一个滑移系开动,强化作用不大,θI较小,为易滑移阶段;第Ⅱ阶段为线性强化阶段,出现了多系滑移;多系滑移产生大量位错,使得位错运动阻力明显增大,尤其是面角位错的出现,强烈的阻止位错源开动,并强最大。
烈阻止其他滑移面上的位错运动,从而使得这一阶段硬化指数θⅡ第Ⅲ阶段出现了交滑移,从而拜托了面角位错的封锁,使原被塞积的位错继续运动,使得位错的自由路程增大。
即在加工硬化的同时,存在着动态回复的软化过程,从而造成θⅢ随着γ增大而逐渐降低的现象。
3 晶界对塑性变形有什么影响?晶界对塑性变形过程的影响,主要是在温度较低时晶界阻碍滑移进行引起的障碍强化作用和变形连续性要求晶界附近多系滑移引起的强化作用。
为使多晶体塑性变形过程不破坏晶界连续性,相邻的晶粒必须协调变形。
多晶体塑性变形一旦变形传播到相邻的晶粒,就产生了多系滑移。
位错运动遇到的障碍比单系滑移多,阻力要增加。
存在晶界及晶界两侧晶粒取向有差别,多晶体的塑性变形有着很大的不均匀性。
在单个晶粒内,晶界变形要低于晶粒中心区域;由于细晶组织中晶界占的比例要大于粗晶组织中的晶界,细晶组织的强化效果高于粗晶组织。
4 多系滑移为何能起到强化作用?金属多晶体塑性变形一开始为什么就出现了多系滑移的强化?多系滑移产生大量位错,位错间相互作用使得位错运动阻力明显增大,尤其是面角位错的出现,强烈的阻止位错源开动,并强烈阻止其他滑移面上的位错运动。
多晶体材料中,某一晶粒产生滑移变形而不破坏晶界连续性,相邻的晶粒必须协调变形。
理论计算证明,相邻晶粒通过滑移协调一个可以变成任意形状的晶粒的变形,至少需六个滑移系统。
所以多晶体塑性变形一旦形传播到相邻的晶粒,就产生了多系滑移。
位错运动遇到的障碍比单系滑移多,阻力增加很快。
5 细化晶粒对金属材料的力学性能有什么影响?细化晶粒可以解决哪些问题?有哪些途径可以细化晶粒?根据Hall-Petch关系,流变应力与晶粒直径方根的倒数(D-1/2)有明显的线性关系。
σs=σi+KD-1/2式中σs——屈服应力; D——平均晶粒直径;σi、K——实验常数。
细化晶粒非常重要,在工程上有重要的应用(1)在高强度的钢种中,细化晶粒可以提高其韧性;有助于防止脆性断裂发生,可降低脆性转化温度,提高材料使用范围。
(2)在低强度钢中(如低碳结构钢),利用细化晶粒来提高屈服强度有明显效果。
尤其是超细晶组织对提高强度和韧性作用更突出。
(3)在超塑性变形时,细化晶粒可以得到理想的超塑性变形。
因为超塑性变形的控制机理为晶间滑动机理,等轴细小晶粒更有利于晶间滑动变形。
晶粒细化的途径有以下几种:1)改变结晶过程中的凝固条件,尽量增加冷却速度,另一方面调节合金成分以提高液体金属过冷能力,使形核率增加,进而获得细化的初生晶粒。
2)进行塑性变形,严格控制随后的回复和再结晶过程以获得细小的晶粒组织。
采用低温轧制和随后控制冷却,是得到细晶组织的有效生产工艺。
3)利用固溶体的过饱和和分解或粉末烧结等方法,在合金中产生弥散分布的第二相以控制基体组织的晶粒长大。
4)通过同素异形转变的多次反复快速加热冷却的热循环处理来细化晶粒。
6 什么是屈服效应?其在变形金属的外观上有何反应?体心立方金属单向拉伸过程出现上下屈服点和屈服平台的现象,称之为屈服效应。
其原因是位错与间隙原子形成的柯氏气团的反复钉扎的相互作用。
屈服效应会在变形金属的外观上有所反应,当金属变形量恰在屈服延伸区内时,金属表面会产生粗糙不平的表面缺陷,称之为吕德斯带。
吕德斯带的形成:是外应力作用下,某些位置位错钉扎不牢,它们首先摆脱溶质原子的气团,开始运动、变形是集中在局部区域,在金属外观上的反映就是一种带状的表面粗糙的缺陷。
吕德斯带的消除:(1)加入少量的AI、Ti等强氮、碳化物形成元素,固定C、N,使之不能有效钉扎位错。
(2)在钢板冲压前进行小量的预变形(稍大于屈服延伸区的变形程度),使被溶质原子钉扎住的位错大部分基本脱钉.7 什么是形变时效和动态形变时效?形变时效:体心立方金属第一次加载屈服后卸载,停留一段时间再加载,重新出现屈服效应现象。
其屈服极限、强度极限和硬度均有所提高,而塑性与疲劳极限等则要下降,容易发生脆断。
a-第一次实验;b-卸载后立即加载实验;c-卸载后停留一段时间再加载实验蓝脆:碳钢在150~350℃范围内变形时,存在着动态形变时效现象,因而降低塑性,使金属变脆。
这个温度区间试样或工件表面很容易生长蓝色的氧化膜,有发蓝的现象。
8 处于不同时效阶段的沉淀强化合金的应力应变曲线有何特点?如图所示,应力应变曲线可分为四个阶段,即溶质原子的偏聚阶段、偏聚区有序化阶段、过渡相阶段和平衡阶段。
溶质原子的偏聚阶段:GPⅠ区所对应的一段曲线。
在GPⅠ区,随着时效时间增长,强度增加。
偏聚区有序化阶段:GPⅡ区(体心点阵形成)。
形成共格相θ``强化曲线达到峰值时,沉淀相中有80-90%是θ``相。
过渡相阶段:θ′相出现后,共格关系开始破坏,强化作用不如θ“相,标志着过时效开始。
平衡阶段:长时间时效后,沉淀相完全转变成粗大体心正方结构的有序稳定平衡θ相,完全失去共格关系,导致软化,强化作用比不上固溶强化。
9 沉淀析出相质点越小,沉淀强化合金的强化效果越好吗?第二相析出强化作用机理主要有两种:切过第二相的强化机理和绕过机理,如下图所示。
位错切过第二相质点时,位错运动的阻力将随质点尺寸加大而增加,如曲线B所示;位错绕过第二相质点时,位错运动的阻力将随质点尺寸减小而增加,如曲线A所示。
最佳的粒子尺寸:位错总是选择需要克服阻力最小的方式通过.故当质点相当于两曲线交点P所对应的尺寸大小时,得到最佳的强化效果。
10 影响金属材料塑性的因素有哪些?影响金属材料塑性的因素可分为内在因素和变形的外部条件。
其中内在因素又可分为材料的组织结构和其化学成分。
变形的外部条件为变形温度、变形速度、应力状态、变形的均匀性等。
(1)组织结构对塑性的影响不同晶体结构的金属塑性不同。
面心、体心立方塑性较好、而密排六方滑移系少,塑性较差;纯金属和合金比较,一般纯金属有较好的塑性;单相合金同多相合金材料比较,一般是单相合金材料的塑性好-些。
各相的性质不同,变形的难易程度是不同的;存在第二相的材料,第二相质点的性质、数量、大小、形态和分布对材料的塑性都有很大的影响;晶粒细小均匀的组织比晶粒粗大不均匀的组织塑性好。
特别是冷变形时这种影响的差别更显著;变形组织比铸态组织塑性好。
(2)成分对塑性的影响a)低熔点S化物及其共晶通常分布于晶界上。
在900℃左右变形过程中产生热脆(红脆);b)钢中含0.15~0.30%的铜时,热加工过程中钢的表面会产生龟裂,称为铜脆。
c)钢中含P量不大时,在热加工范围内对塑性影响不大。
在冷状态下时,磷使钢的强度增高。
塑性降低,产生冷脆现象。
P含量超过0.1%时,冷脆现象很明显。
磷还引起高温回火脆性,d)Pb、Sn、As、Sb、Bi,它们都是低熔点元素,俗称“五害” ,对塑性影响很坏。
它们在钢中的溶解度都很小,剩余量分布于晶界。
它们在加热时熔化而使钢材塑性破坏。
e)氢对钢热加工时的塑性没有明显的影响,因为加热到1000℃左右时,过饱和的氢易于从钢中析出。
但含氢量较高的钢,热加工后快速冷却时会产生白点。
冷加工时会产生氢脆现象。
f)低碳钢中固溶的N和C量增大时,形变时效现象显著,在300℃左右加工时会出现蓝脆现象。
(3)外部变形条件的影响a)变形温度对塑性的影响一般规律是温度升高,塑性改善。
原因: 温度升高,热激活作用增强,位错的活动性能提高,温度升高可能出现新的滑移系统,可能使扩散塑性变形机理同时起作用,使塑性变形容易进行。
温度升高有利于回复和再结晶软化过程的发展,可使变形过程造成的破坏和缺陷修复,从而提高了塑性。
b)应变速率对塑性的影响应变速率对塑性的影响是比较复杂的,应变速率效应: 应变速率增加,位错运动没有足够的时间,不利于异号位错的合并、重排,不利于回复和再结晶过程的进行,不利于变形过程中形成的内裂修复。
加工硬化加剧。
温度效应: 应变速率增加,变形热来不及散发,提高了变形温度,促进变形过程中产生的排列混乱的位错重新排列为某些低能组态,利于异号位错合并,位错密度可降低一些。
温度提高促进回复和再结晶,促进裂纹修复, 促使扩散塑性变形机理发生作用。
分析应变速率对塑性的影响时,不能脱离温度的影响区,c)应力状态对塑性的影响从提高塑性的角度来看,各种应力状态中三向压应力最好,两压一拉次之,两拉一压更次之,三向拉应力对塑性潜能的发挥最不利。
d)不均匀变形对塑性的影响变形不均匀而出现的应力叫附加应力。
附加应力的出现影响了变形体的应力分布。
e)其他因素对塑性的影响变形状态、尺寸因素、周围介质等都对塑性有影响。