金属塑性变形理论第9讲变形不均匀原因及防止措施
金属常见加工工艺缺陷的特征、原因、影响及措施

四.由于操作不当导致冲裂
1.毛胚落料时纤维方向不正确 钢件毛坯落料的方向恰好与零件变形方向垂直就容易在冷弯时造成沿纤维方向撕裂。一般
冲裂数量较大,且冲裂部位具有规律性。 2.冲模错位 上下模位置不正确,不但会使零件冲裂,严重时还会把模具冲坏。此类裂纹一般出现在模
具间隙小的一边,由于间隙过小,钢板在模内滑移变形受阻,局部表面将产生严重擦伤。
5.加工精度不符合
切削加工后,构件尺寸、形状或位置、精度不符合工艺图纸或设计要求。不仅直接影响工 件装配质量、而且影响工件正常工作时应力状态分布、而降低工件抗失效性能。
6.表面机械损伤
切削加工过程中,构件表面相撞擦伤、碰伤、压伤……
金属零件冷冲拉常见缺陷的特征、原因、影响、措施
1.破裂
宏观裂纹。一般属拉伸系数太小,拉伸应力较大,容易产生拉裂;进行翻边工序时,如果 翻边的直径超过容许值,也会使孔的边缘造成破裂。板料冲裂一般与变形度和材料晶粒度有关。 如含碳量小于 0.2%的碳钢变形度达到 8~20%时,中间退火会导致晶粒长大,不均匀晶粒度则 导致冲裂。
产生的原因主要是表面氮浓度富集,化合物虽连续粗大网络状分布。在磨削时倾向于脱落 的氮化层的显微结构特点是沿奥氏体晶界存在稠密的网状氮化物,它的存在使晶格畸变加剧, 在位错与晶界处三向应力增大,在磨削力、热应力及组织应力的作用下,粗大的氮化物网络边 界区切口效应敏感性增大,造成综合应力叠加,当这种应力超过渗层的强度极限时,即产生脆 性破裂与剥落。当晶界强度大于晶内强度时,则裂纹沿晶扩展产生脆裂及剥落;当晶界强度等 于晶内强度时,则裂纹的扩展呈穿晶脆裂及剥落。
滚动轴承常见失效形式及原因分析
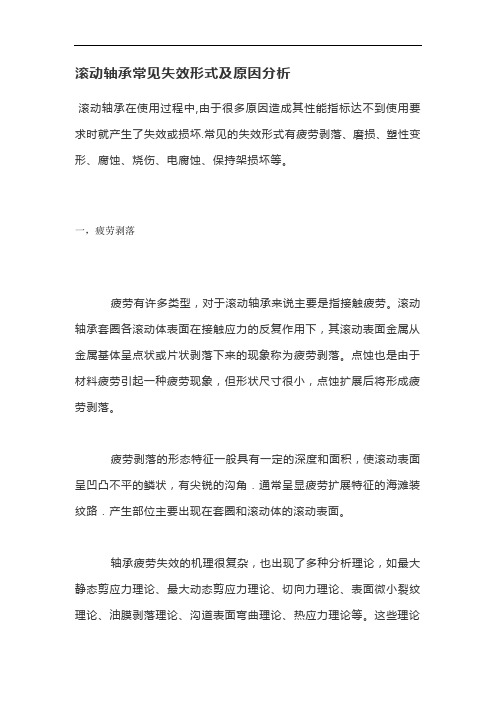
滚动轴承常见失效形式及原因分析滚动轴承在使用过程中,由于很多原因造成其性能指标达不到使用要求时就产生了失效或损坏.常见的失效形式有疲劳剥落、磨损、塑性变形、腐蚀、烧伤、电腐蚀、保持架损坏等。
一,疲劳剥落疲劳有许多类型,对于滚动轴承来说主要是指接触疲劳。
滚动轴承套圈各滚动体表面在接触应力的反复作用下,其滚动表面金属从金属基体呈点状或片状剥落下来的现象称为疲劳剥落。
点蚀也是由于材料疲劳引起一种疲劳现象,但形状尺寸很小,点蚀扩展后将形成疲劳剥落。
疲劳剥落的形态特征一般具有一定的深度和面积,使滚动表面呈凹凸不平的鳞状,有尖锐的沟角.通常呈显疲劳扩展特征的海滩装纹路.产生部位主要出现在套圈和滚动体的滚动表面。
轴承疲劳失效的机理很复杂,也出现了多种分析理论,如最大静态剪应力理论、最大动态剪应力理论、切向力理论、表面微小裂纹理论、油膜剥落理论、沟道表面弯曲理论、热应力理论等。
这些理论中没有一个理论能够全面解释疲劳的各种现象,只能对其中的部分现象作出解释。
目前对疲劳失效机理比较统一的观点有:>>>>1、次表面起源型次表面起源型认为轴承在滚动接触部位形成油膜的条件下运转时,滚动表面是以内部(次表面)为起源产生的疲劳剥落。
>>>>2、表面起源型表面起源型认为轴承在滚动接触部位未形成油膜或在边界润滑状态下运转时,滚动表面是以表面为起源产生的疲劳剥落。
>>>>3、工程模型工程模型认为在一般工作条件下,轴承的疲劳是次表面起源型和表面起源型共同作用的结果。
疲劳产生的原因错综复杂,影响因素也很多,有与轴承制造有关的因素,如产品设计、材料选用、制造工艺和制造质量等;也有与轴承使用有关的因素,如轴承选型、安装、配合、润滑、密封、维护等。
具体因素如下:(1)制造因素a.产品结构设计的影响产品的结构设计是根据使用性能目标值来确定的,这些目标值如载荷容量、寿命、精度、可靠性、振动、磨损、摩擦力矩等。
材料科学基础A习题答案第5章[1]解析
![材料科学基础A习题答案第5章[1]解析](https://img.taocdn.com/s3/m/5ef3bfa0d0d233d4b14e698a.png)
材料科学基础A习题第五章材料的变形与再结晶1、某金属轴类零件在使用过程中发生了过量的弹性变形,为减小该零件的弹性变形,拟采取以下措施:(1)增加该零件的轴径。
(2)通过热处理提高其屈服强度。
(3)用弹性模量更大的金属制作该零件。
问哪一种措施可解决该问题,为什么?答:增加该零件的轴径,或用弹性模量更大的金属制作该零件。
产生过量的弹性变形是因为该金属轴的刚度太低,增加该零件的轴径可减小其承受的应力,故可减小其弹性变形;用弹性模量更大的金属制作该零件可增加其抵抗弹性变形的能力,也可减小其弹性变形。
2、有铜、铝、铁三种金属,现无法通过实验或查阅资料直接获知他们的弹性模量,但关于这几种金属的其他各种数据可以查阅到。
请通过查阅这几种金属的其他数据确定铜、铝、铁三种金属弹性模量大小的顺序(从大到小排列),并说明其理由。
答:金属的弹性模量主要取决于其原子间作用力,而熔点高低反映了原子间作用力的大小,因而可通过查阅这些金属的熔点高低来间接确定其弹性模量的大小。
据熔点高低顺序,此几种金属的弹性模量从大到小依次为铁、铜、铝。
3、下图为两种合金A、B各自的交变加载-卸载应力应变曲线(分别为实线和虚线),试问那一种合金作为减振材料更为合适,为什么?答:B合金作为减振材料更为合适。
因为其应变滞后于应力的变化更为明显,交变加载-卸载应力应变回线包含的面积更大,即其对振动能的衰减更大。
4、对比晶体发生塑性变形时可以发生交滑移和不可以发生交滑移,哪一种情形下更易塑性变形,为什么?答:发生交滑移时更易塑性变形。
因为发生交滑移可使位错绕过障碍继续滑移,故更易塑性变形。
5、当一种单晶体分别以单滑移和多系滑移发生塑性变形时,其应力应变曲线如下图,问A、B中哪一条曲线为多系滑移变形曲线,为什么?应力滑移可导致不同滑移面上的位错相遇,通过位错反应形成不动位错,或产生交割形成阻碍位错运动的割阶,从而阻碍位错滑移,因此其应力-应变曲线的加工硬化率较单滑移高。
金属塑性变形的不均匀性-文档资料
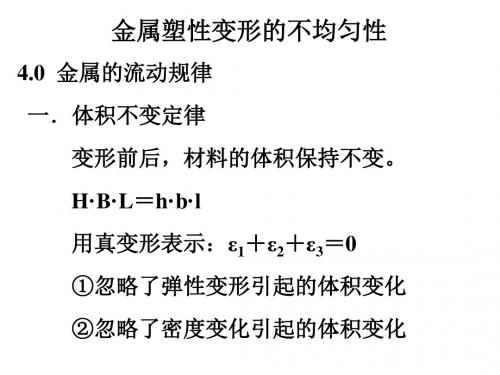
1.f 对应力分布的影响
①接触表面 轴向应力(单位压力):σZ 第1层:σ1=σs 产生塑性变形 第2层:σ2=σs+ σ1’ 第3层:σ3=σs + σ1’ + σ2’ ……….. 由外层到内层轴向应力逐渐升高。
二.附加应力 —— 由变形不均匀引起的在物体内部自相平 衡的应力
1.分类 附加应力分为三种
① 第一类附加应力 在变形物体大部分体积之间彼此平衡的附加 应力,由宏观的不均匀变形产生。 以凸辊轧制矩形坯为例说明
轧件边缘部分a: 压下量小,延伸小
轧件中间部分b: 压下量大,延伸大
由于轧件是一整体,纵向 延伸趋于一致。所以 b对a有一拉伸的应力,使 a伸长,a产生σ附(+) a对b有一压缩的应力,使 b缩短,b产生σ附(-)
径向应力:σr 由外层到内层σr 逐渐升高
② 中心面 沿高度方向,由接触面至变形体中部,外摩擦 的影响逐渐减弱。 即:离接触面越远,径向流动阻力越小,要使
它变形所需的单位压力越小,其应力分布 是逐渐减小的。 另: 离中心面越远,径向流动阻力越小,应力 越小。
2.f 对应变分布的影响 ① 接触表面 边缘:径向流动阻力小,ε大
中部变形小, σ附(+) 这二种拉应力叠加,可能造成中间部分金属开裂
三.工具和工件形状的影响(△h不均) 由于△h不均匀,造成μ不均匀,产生σ附 下面以凹辊轧制矩形坯为例来讨论 在椭圆孔型中轧制矩形坯时,中部△h小, 边缘△h大,故沿宽度方向纵向延伸不均匀。 中部:μ小,产生σ附(+) 开裂 两边:μ大,产生σ附(-) 皱折(波纹) 两端:呈自由延伸,鱼尾状
1
滚动轴承常见的失效形式及原因

滚动轴承常见的失效形式及原因滚动轴承常见的失效形式及原因分析滚动轴承在使用过程中由于很多原因造成其性能指标达不到使用要求时就产生了失效或损坏.常见的失效形式有疲劳剥落、磨损、塑性变形、腐蚀、烧伤、电腐蚀、保持架损坏等。
疲劳有许多类型,对于滚动轴承来说主要是指接触疲劳。
滚动轴承套圈各滚动体表面在接触应力的反复作用下,其滚动表面金属从金属基体呈点状或片状剥落下来的现象称为疲劳剥落。
点蚀也是由于材料疲劳引起一种疲劳现象,但形状尺寸很小,点蚀扩展后将形成疲劳剥落。
疲劳剥落的形态特征一般具有一定的深度和面积,使滚动表面呈凹凸不平的鳞状,有尖锐的沟角. 通常呈显疲劳扩展特征的海滩装纹路.产生部位主要岀现在套圈和滚动体的滚动表面.轴承疲劳失效的机理很复杂,也岀现了多种分析理论,如最大静态剪应力理论、最大动态剪应力理论、切向力理论、表面微小裂纹理论、油膜剥落理论、沟道表面弯曲理论、热应力理论等。
这些理论中没有一个理论能够全面解释疲劳的各种现象,只能对其中的部分现象作出解释。
目前对疲劳失效机理比较统一的观点有:次表面起源型认为轴承在滚动接触部位形成油膜的条件下运转时,滚动表面是以内部(次表面)为起源产生的疲劳剥落。
表面起源型认为轴承在滚动接触部位未形成油膜或在边界润滑状态下运转时,滚动表面是以表面为起源产生的疲劳剥落。
工程模型认为在一般工作条件下,轴承的疲劳是次表面起源型和表面起源型共同作用的结果。
疲劳产生的原因错综复杂,影响因素也很多,有与轴承制造有关的因素,如产品设计、材料选用、制造工艺和制造质量等;也有与轴承使用有关的因素,如轴承选型、安装、配合、润滑、密封、维护等。
具■体因素如下:A制造因素|1 、产品结构设计的影响:产品的结构设计是根据使用性能目标值来确定的,这些目标值如载荷容量、寿命、精度、可靠性、振动、磨损、摩擦力矩等。
在设计时,由于各种原因,会造成产品设计与使用的不适用或脱节,甚至偏离了目标值,这种情况很容易造成产品的早期失效。
金属常见加工工艺缺陷的特征、原因、影响及措施

度下,金属再结晶退火加热温度过高或时间过长所致。晶粒粗大或粗细不均会导致在变形量较 大的部位产生裂纹,且裂纹多沿粗细混晶交界区择优分布。
三.由于材料成分、性能不合格
1.成分不合格 冷冲用钢板的化学成份应严格控,特别是碳、硫、磷元素极为重要。碳元素在钢中形成渗
2.带状组织 钢中带状组织是由铁素体和珠光体相间分布组成。它是由于碳、磷、硫晶间偏析,在热压
力加工中使之沿着金属变形方向被拉长,呈带状分布的夹杂物。 由于带状组织的取向平行于钢材轧制方向,而铁素体和珠光体的强度及塑性差异悬殊,因
此,冷冲时当钢件的变形方向与钢板带状组织相垂直,容易产生拉裂和撕裂。由于钢板带状组 织引起的冲裂,裂纹平行于钢板轧制方向,裂纹粗大,显微观察时裂纹多沿珠光体边缘分布、 取向平行于带状组织。
3.鳞片状毛刺
以较低或中等切削速度切削塑性金属时,加工表面往往会出现鳞片状毛刺,尤其对圆孔采 用拉削方法更易出现,若拉削出口毛刺没有去除,则将成为使用中应力集中的根源。
4.“R”加工过小
零件拐角半径小,尤其是横截面形状发生急骤的变化,会在局部发生应力集中而产生微裂 纹并扩展成疲劳裂纹,导致疲劳断裂。
3.涡流
金属在锻造过程中由于剧烈的热变形使金属组织发生晶粒结晶重新定向排列,形成结晶织 构和金属中的非金属夹杂物、树枝晶偏析、第二相质点等沿热加工方向形变延伸呈带状分布, 形成了锻件的纤维状组织即锻造流线。
产生的原因主要是表面氮浓度富集,化合物虽连续粗大网络状分布。在磨削时倾向于脱落 的氮化层的显微结构特点是沿奥氏体晶界存在稠密的网状氮化物,它的存在使晶格畸变加剧, 在位错与晶界处三向应力增大,在磨削力、热应力及组织应力的作用下,粗大的氮化物网络边 界区切口效应敏感性增大,造成综合应力叠加,当这种应力超过渗层的强度极限时,即产生脆 性破裂与剥落。当晶界强度大于晶内强度时,则裂纹沿晶扩展产生脆裂及剥落;当晶界强度等 于晶内强度时,则裂纹的扩展呈穿晶脆裂及剥落。
锻造裂纹产生的原因及解决 方法
锻造裂纹产生的原因及解决方法锻造裂纹产生的原因及解决方法2011-04-2509:28裂纹是锻压生产中常见的主要缺陷之一,通常是先形成微观裂纹,再扩展成宏观裂纹。
锻造工艺过程(包括加热和冷却)中裂纹的产生与受力情况、变形金属的组织结构、变形温度和变形速度等有关。
锻造工艺过程中除了工具给予工件的作用力之外,还有由于变形不均匀和变形速度不同引起的附加应力、由温度不均匀引起的热应力和由组织转变不同时进行而产生的组织应力。
应力状态、变形温度和变形速度是裂纹产生和扩展的外部条件;金属的组织结构是裂纹产生和扩展的内部依据。
前者是通过对金属组织及对微观机制的影响而对裂纹的发生和扩展发生作用的。
全面分析裂纹的成因应当综合地进行力学和组织的分析。
(一)形成裂纹的力学分析在外力作用下物体内各点处于一定应力状态,在不同的方位将作用不同的正应力及切应力。
裂纹的形式一般有两种:一是切断,断裂面是平行于最大切应力或最大切应变;另一种是正断,断裂面垂直于最大正应力或正应变方向。
至于材料产生何种破坏形式,主要取决于应力状态,即正应力σ与剪应力τ之比值。
也与材料所能承受的极限变形程度εmax及γmax有关。
例如,①对于塑性材料的扭转,由于最大正应力与切应力之比σ/τ=1是剪断破坏;②对于低塑性材料,由于不能承受大的拉应变,扭转时产生45°方向开裂。
由于断面形状突然变化或试件上有尖锐缺口,将引起应力集中,应力的比值σ/τ有很大变化,例如带缺口试件拉伸σ/τ=4,这时多发生正断。
下面分析不同外力引起开裂的情况。
压力加工生产中,在下列一些情况,由外力作用可能引起裂纹:弯曲和校直、脆性材料镦粗、冲头扩孔、扭转、拉拔、拉伸、胀形和内翻边等,现结合几个工序说明如下。
弯曲件在校正工序中(见图3-34)由于一侧受拉应力常易引起开裂。
例如某厂锻高速钢拉刀时,工具的断面是边长相差较大的矩形,沿窄边压缩时易产生弯曲,当弯曲比较严重,随后校正时常常开裂。
吉林大学工程材料第2章 金属的塑性变形和再结晶
1、晶粒正常长大: 再结晶后的晶粒均匀、稳速地长大的现象。发生在
再结晶晶粒细小且均匀时。(希望的长大方式)
2、晶粒异常长大:
再结晶后的晶粒不均匀,急剧长大的现象。在再结晶 粒大小不均时,大晶粒吞并小晶粒,将得到异常粗大的 晶粒,也称“二次再结晶”。
d晶↑ 晶界面积↓ 能量↓∴晶粒长大是自发的 过程。因为粗晶是弱化,所以要避免晶粒长大,特别要
方向 σb(MPa) σ0.2(MPa) δ(%) ψ(%) αk(KJ/M2)
平行 701 垂直 659
460
17.5 62.8
608
431
10.0 31.0
294
34
四 、热加工的不足
在实际生产中,热加工与冷加工相比也有不足处
(1)热加工需要加热,不如冷加工简单易行。 (2)热加工制品的组织与性能不如冷加工均匀和易 于控制。
目的:1. 消除加工硬化 使、σ、HB↓ δ%、 %、ak↑ 2. 消除内应力,但保留加工硬化,使理化性能↑
对于冷加工后的金属,由于10%的变形能储存在 金属中,在加热时,随着温度的升高,原子活动能力 提高,在变形能的作用下,就要发生组织和性能的变 化,其主要包括三个阶段:回复、再结晶及晶粒长大。
18
底面对角线
1 面×3 方向=3
7
4、滑移机理
临界切应力(c): 能够发生滑移的最小切应
力叫做为)。当切应力()满足 c时滑移才 能发生。
铜的滑移临界切应力:理论计算 1500 Mpa 实际测试 1 MPa
滑移是由于滑移面上的位错运动造成的。
8
位错运动造成滑移示意图
9
10
二、 多晶体金属的塑性变形
700℃
第9讲等效应力及等效应变
2019/9/19
1
加载条件
简单加载
在加载过程中,应力张量各分量按同样的
比例增加,也称为比例加载。即
ij
c
0 ij
。例:
5
已知
0 ij
0
0
0 10 0
0 0 15
,c 2 ,则
ij
10 0
0
0 20 0
0 0 30
简单加载的特点:加载过程中,应力主轴不动。
de
2 9
d1
d 2 2
d 2
d3 2
d3
d1 2
此式表示的应变增量 d e
就是主轴时的等效应变增量,非主轴等效应变
增量如下:
de
2 9
d x d y
2
d y d z
2
d x d z
在变形过程中由于加工硬化的结果,随着变形程度的增大,变形抗力增大。一般 可采用下述关系式来确定(幂指数硬化曲线)。
e Ben
B——强化系数,与材料有关的常数 n——硬化指数,
2019/9/19
25
e
B
n e
e
e
2019/9/19
26
(2)对于有初始屈服应力 s 的冷变形金属材料,可较好地表达为
2019/9/19
21
单向拉伸
1 0、 2 3 0; 2 3 1 2
e 1 s
e
1
ln
l1 l0
2019/9/19
22
单向压缩
3 0、1 2 0;1 2 3 2
箱形梁焊接扭曲变形的控制措施
箱形梁焊接扭曲变形的控制措施摘要:在钢结构制造当中,对箱型梁的焊接是最为常见的结构形式。
虽然其外形很简单,形状看起来也是方方正正的,但正是因为这个原因,它对焊接后变形的控制要求的更为严格。
所以,我们需要对箱形梁在焊接过程中出现的一些变形的因素进行相关的分析和研究,并采取一些有效的修复措施,以此来对箱形梁在焊接的过程中所发生的焊接变形进行控制,从而使箱形梁的焊接更为牢固可靠,也使箱形梁在更为广泛的领域内得到更为广泛的应用,从而更好地服务于人类,创造出更多的价值。
关键词:箱型梁;焊接过程;焊接变形引言箱型梁主要是指其截面形状与普通箱子截面无异,因而称之为箱型梁。
箱型梁通常由几个部分组合在一起形成的,如盖板和腹板、隔板、底板这四个方面组合而成。
箱型梁具有一定的先进性和优越性,其属于力学性能方面的经济断面组合结构,常会应用在龙门吊机、起重船等较为大型的承重结构。
1 箱形梁的结构和特点一般情况下来说,箱形梁主要是通过盖板、腹板、底板还有隔板所组成的,其截面的形状和我们通常所见到的箱子的截面形状是一样的,所以我们都称之为箱形梁。
箱形梁具有优越的力学性能,而且这种断面结构还经济实用,所以,在当今社会,其应用比较广泛,尤其是应用到了大型的承重结构之上,比如大型吊机、起重机以及船业设备等等。
箱形梁的承载量比较大,而且它还能够承受动载荷。
因此,对焊接的质量要求比较严格,一般来说,我们需要对其四条主焊缝进行百分之百超声波的一级探伤。
对于像是大型的吊机、起重机以及船业设备等来说,其箱形梁所连接的部位比较多,制作的精度比较高,外形的尺寸比较大,所以它一般都具有比较高标准的要求,而这也是箱形梁和其他刚接结构焊接方式相区别的地方。
2 箱型梁焊接变形的控制方法2.1箱型梁组对顺序的合理化依照箱型梁的具体形态和结构特点,对其组装顺序进行合理的安排,主要步骤如下:①应先将下底板完全铺设好后,方可在处于下底板上划处的上腹板和其相连接,做合线的腊线工作。
- 1、下载文档前请自行甄别文档内容的完整性,平台不提供额外的编辑、内容补充、找答案等附加服务。
- 2、"仅部分预览"的文档,不可在线预览部分如存在完整性等问题,可反馈申请退款(可完整预览的文档不适用该条件!)。
- 3、如文档侵犯您的权益,请联系客服反馈,我们会尽快为您处理(人工客服工作时间:9:00-18:30)。
金属塑性变形理论
Lesson Nine
Theory of metal plastic deformation
第九讲 Lesson Nine
• 张贵杰
• Zhang Guijie
• Tel:0315-2592155 • E-Mail: zhguijie@vip.sina
• Ⅰ区表示由外摩擦影响而产生的难变形区;
• Ⅱ区表示与作用力成45°角的最有利方位的易变 形区;
• Ⅲ区表示变形程度居于中间的自由变形区。
20.11.2020
6
Lesson Nine
镦粗时摩擦力对变形及应力分布的影响
20.11.2020
7
应力分布不均
Lesson Nine
• 外摩擦不仅影响变形,而且使接触面上的应力 (或单位压力)分布不均匀,沿试样边缘的应力 等于金属的屈服极限,从边缘到中心部分,应力 逐渐升高。
20.11.2020
Lesson Nine 20
变形体内部温度分布不均
Lesson Nine
• 变形物体的温度不均匀,会造成金属各部分变形 和流动的差异。变形首先发生在那些变形抗力最 小的部分。一般,在同一变形物体中高温部分的 变形抗力低,低温部分的变形抗力高。这样,在 同一外力的作用下,高温部分变形量大,低温部 分变形量小。而变形物体是一整体,限制了物体 各部分不均匀变形的自由发展,从而产生相互平 衡的附加应力。
主要内容
Main Content
• 变形不均匀的基本概念 • 变形不均匀的原因 • 减小变形不均匀的措施 • 残余应力
20.11.2020
3
5.2 变形不均匀的原因
• 接触面上的外摩擦 • 变形区的几何因素 • 工具与工件的轮廓形状 • 变形体内部温度分布不均 • 变形体的外端 • 金属性质不均的影响
20.11.2020
20.11.2020
12
Lesson Nine
翻平宽展
20.11.2020
鼓形宽展
13
粘着现象
Lesson Nine
• 实验结果表明,圆柱体金属在镦粗过程中,若接 触摩擦较大和高径比H/D较大时,则在端面的中 心部位有一区域,在此区域上金属质点对工具完 全不产生相对滑动而粘着在一起。此现象称为粘 着现象。此粘着在一起的区域称为粘着区。此粘 着现象也影响到金属的一定深度,这样就构成了 以粘着区为基底的圆锥形或近似圆锥形的体积, 此体积称为“难变形区”。
• 河北理工大学金属材料与加工工程系
• Department of Metal Material and Process
Engineering
20.11.2020 • Hebei Polytechnic University, Tangshan 063009
2
Lesson Nine
第五章 塑性变形的不均匀性
20.11.2020
14
Lesson Nine
难变形区
20.11.2020
15
变形区的几何因素
Lesson Nine
• 在金属塑性加工中存在着外摩擦,变形的不均匀 分布情况与变形区几何因素(如H/d、H/L、H/B等) 有密切关系。实验表明:镦粗圆柱体时,当试样 原始高度与直径比H/d<2.0时才发生上述的单鼓 形不均匀变形。当坯料高度较大且变形程度甚小 时(当H/d>2.0时),则往往只产生表面变形,而 中间层的金属不产生塑性变形或塑性变形甚小, 结果导致形成双鼓形。
Lesson Nine
20.11.2020
4
接触面上的外摩擦
Lesson Nine
• 在工具和变形金属之间的接触面上必然存 在摩擦。由于摩擦力的作用,在一定程度 上改变了金属的流动特性并使应力分布受 到影响。
20.11.2020
5
镦粗时的分区
Lesson Nine
• 圆柱体镦粗时,由于接触面上有摩擦存在,在接 触表面附近金属流动困难,圆柱形坯料转变成鼓 形。在此情况下,可将变形金属整个体积大致分 为三个区:
20.11.2020
16
Lesson Nine
双鼓形Βιβλιοθήκη 20.11.202017
工具与工件的轮廓形状
Lesson Nine
• 工具(或坯料)形状是影响金属塑性流动 方向的重要因素。工具与金属形状的差异, 是造成金属沿各个方向流动的阻力有差异, 因而金属向各个方向的流动(即变形量) 也有相应差别。
20.11.2020
18
Lesson Nine
a
b
c
• 如图所示,在圆形砧或V型砧中拔长圆断面坯料时, 工具的侧面压力使金属沿横向流动受到很大的阻碍, 被压下的金属大量沿轴向流动,这就使拔长效率大大 提高。当采用图c所示的工具时,则产生相反的结果, 金属易于横向流动。
20.11.2020
19
• 在许多情况下,当工具的形 状已得到了严格的控制时, 为获得变形均匀的产品,还 必须要考虑原始坯料形状的 影响。如果坯料的尺寸和形 状的选择不当也会使物体产 生不均匀变形。
• 另外,沿物体高度方向由接触面至变形体的中部, 应力的分布是逐渐减小的,这是因外摩擦的影响 逐渐减弱所致。
20.11.2020
8
Lesson Nine
带孔的玻璃锤头镦粗塑料实验
20.11.2020
9
侧面翻平
Lesson Nine
• 变形物体在压缩时,由于接触摩擦的作用,在出 现单鼓形的同时,还会出现侧表面的金属局部地 转移到接触表面上来的侧面翻平现象。随着压下 率的增加,aa和bb部分由侧表面逐步地转移到端 面上来。此侧面翻平现象发生在侧表面面积的减 小量大于接触面面积的增加量的时候。如果接触 面面积增加量大于侧面的减小量时,则因新的接 触面的形成将不再吸收侧面的多余面积。
20.11.2020
10
Lesson Nine
20.11.2020
圆柱体垂直剖面上坐标网格在镦 粗过程中的变化
11
Lesson Nine
• 由此可见,物体在压缩时接触面积的增加,可由 接触表面上金属质点滑动和侧面质点翻平两部分 组成。侧面金属翻平量的大小取决于接触摩擦条 件和变形物体的几何尺寸。接触面上的摩擦越大, 接触面上的金属质点越不易滑动,因而侧面金属 转移上来的数量就越多。试样的高度越大,侧面 金属越易于转移到接触表面上来。当试样的高度 大于直径时,接触面积的增加将主要是由侧面金 属的转移所造成。