金属材料性能与塑性变形
金属材料的力学行为与塑性变形从宏观到微观的分析

金属材料的力学行为与塑性变形从宏观到微观的分析金属材料的力学行为与塑性变形是材料力学领域的重要研究内容,涉及到宏观力学行为与微观结构之间的关系。
本文将从宏观到微观分析金属材料的力学行为与塑性变形,并阐述其中的相关理论和实验。
一、宏观力学行为金属材料的宏观力学行为包括拉伸试验、压缩试验和弯曲试验等。
其中,拉伸试验是最常用的实验方法。
在拉伸试验中,金属材料的应力-应变曲线能够揭示其力学性能。
应力-应变曲线通常包含弹性阶段、屈服阶段、塑性阶段和断裂阶段。
弹性阶段代表材料在受力后可以恢复原来形状;屈服阶段是金属材料发生塑性变形的阶段,通过屈服点可以得到屈服强度;塑性阶段是金属材料继续发生塑性变形的阶段;断裂阶段是金属材料失去承载能力而发生破裂的阶段。
二、塑性变形机制金属材料的塑性变形机制是指在外力作用下,原子或晶体发生位置变动,使材料产生塑性变形。
常见的塑性变形机制包括滑移、扩展和再结晶等。
滑移是金属材料最主要的塑性变形机制。
滑移是指晶体内原子按某个晶面上的位错线方向移动,导致晶体塑性变形。
滑移可以在晶体中沿多个晶面形成滑移系,形成复杂的位错网络,提高金属材料的塑性变形能力。
另外,金属材料的塑性变形还受到晶粒尺寸、晶界和孪生等因素的影响。
晶粒尺寸越小,晶界越多,材料的塑性变形能力越强。
孪生是晶体在破裂方式与滑移不同的情况下发生的一种特殊塑性变形方式。
三、微观结构与力学行为的关系金属材料的力学行为与其微观结构之间存在着密切的关系。
晶体结构、位错和晶界等是影响金属材料力学行为的重要因素。
晶体结构决定了金属材料的力学性能。
常见的晶体结构有面心立方结构、体心立方结构和密排六方结构等。
不同晶体结构对应的金属材料具有不同的力学性能。
位错是晶体中的缺陷,是金属材料塑性变形的主要因素之一。
位错在晶体中传播和互相吸引会导致金属材料出现塑性变形。
晶界是晶体与晶体的交界面,也是影响金属材料力学性能的重要因素之一。
晶界可以抵抗位错的移动,从而影响金属材料的塑性变形能力。
一、4.塑性变形及其性能指标
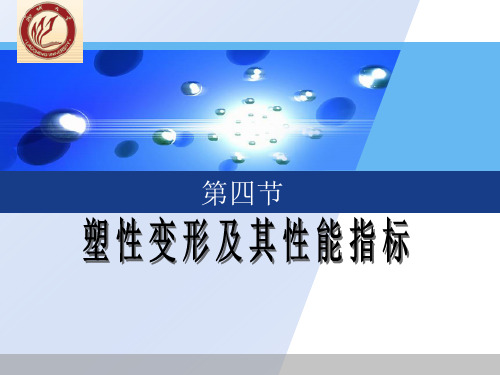
LOGO
4.6.1 缩颈
描述:一些金属材料和高分子材料在拉伸时,变 形集中于局部区域的特殊状态,它是在应变硬化 与截面减小的共同作用下,因应变硬化跟不上塑 性变形的发展,使变形集中于试样局部而产生的。
LOGO
4.6.2 产生缩颈的工程应力
应变硬化 系数K
应变硬化 指数n
n b K e
LOGO
小结
金属材料的屈服强度是一个对成分、组织、 应力状态、温度等极为敏感的力学性能。 改变金属材料的成分或热处理都可使屈服 强度产生明显变化。
对金属材料感兴趣的同学可以参考金属学方 面的参考书和资料。
LOGO
4.5 应变硬化
定义:材料在应力作用下进入塑性变形阶段后, 随着变形量的增大,形变应力不断提高的现象称 为应变硬化。 应变硬化是材料阻止继续塑性变形的一种力学性
LOGO
4.2.2.3 屈服强度的应用
屈服强度是工程技术上最重要的力学性能 指标之一。
作为防止过量塑性变形的参考依据。 根据屈服强度与抗拉强度比的大小,衡量材 料进一步产生塑性变形的倾向。如:金属冷 加工和防止脆断。
LOGO
4.3 影响金属材料屈服强度的因素 4.3.1 晶体结构 金属材料的屈服过程主要是位错的运动。 纯金属单晶体的屈服强度从理论上讲是位错 开始运动所需的临界切应力,由位错运动所 受的各种阻力决定,包括:晶格阻力、位错 间交互作用产生的阻力等。
LOGO
4.1 塑性变形机理
材料的塑性变形:是微观结构的相邻部分 产生永久性位移,但并不引起材料破裂的 现象。
LOGO
4.1.1 金属材料的塑性变形
LOGO
4.1.1.1 金属材料变形的机理
晶体的滑移
晶体的孪生
金属材料的变形机制与塑性行为

金属材料的变形机制与塑性行为金属材料在工程领域中起着重要的作用,而金属的塑性行为和变形机制则是决定其力学性能的重要因素之一。
本文将探讨金属材料的变形机制与塑性行为。
1. 弹性与塑性首先,我们需要了解金属材料的弹性与塑性。
弹性是指金属在受力后能够恢复原状的性质,即应力与应变呈线性关系。
而塑性则是指金属在受力后会发生永久性形变的性质,即应力与应变不再呈线性关系,金属会发生塑性变形。
2. 变形机制金属材料发生塑性变形时,涉及到多种变形机制,其中最重要的包括滑移、扩散和晶体重新排列。
滑移是一种比较常见的金属变形机制。
金属内部的晶体通过滑动来实现变形。
在外力作用下,应变施加到晶体中的部分原子上,这些原子会沿着滑移面滑动,使晶体发生塑性变形。
扩散是指原子在晶体中的扩散过程。
扩散可以使原子重新排列,从而为滑移提供必要的能量。
正是因为扩散的存在,滑移机制才能够进行。
晶体重新排列是指晶体中原子重新排列的过程。
当外力作用于金属时,晶体内的原子会发生重新排列,以使晶体更好地适应外力。
在这个过程中,晶体内的原子会发生位错的形成和移动。
3. 晶体结构与塑性行为晶体结构是决定金属塑性行为的重要因素之一。
晶体的晶格结构有不同的排列方式,其中最常见的有面心立方和体心立方结构。
不同的晶体结构具有不同的变形机制。
体心立方结构的金属通常具有较高的强度和较低的塑性。
这是因为体心立方结构的金属在变形时,需要克服与晶格点的最近邻原子有较大的距离。
相比之下,面心立方结构的金属相对塑性较好,因为该结构中原子之间的间距较小,变形更容易发生。
此外,晶体晶格中的缺陷也会影响金属的塑性行为。
例如,在晶体中存在的位错是金属变形的主要缺陷之一。
位错会使金属的应力集中,进而导致金属发生塑性变形。
4. 温度对塑性的影响温度是另一个影响金属塑性的重要因素。
晶体在不同温度下具有不同的塑性行为。
一般来说,高温下金属的塑性较好,而低温下金属的塑性较差。
高温下,金属的活动性增强,位错的移动更容易发生。
金属的塑性变形、纤维组织及其对金属性能的影响
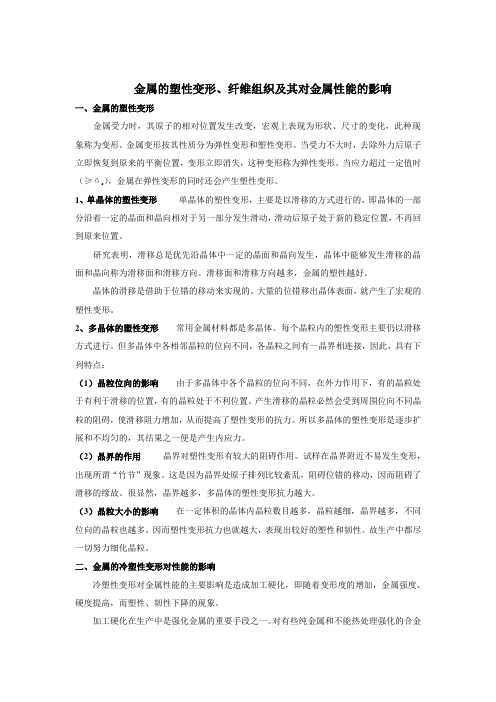
金属的塑性变形、纤维组织及其对金属性能的影响一、金属的塑性变形金属受力时,其原子的相对位置发生改变,宏观上表现为形状、尺寸的变化,此种现象称为变形。
金属变形按其性质分为弹性变形和塑性变形。
当受力不大时,去除外力后原子立即恢复到原来的平衡位置,变形立即消失,这种变形称为弹性变形。
当应力超过一定值时(≥бs),金属在弹性变形的同时还会产生塑性变形。
1、单晶体的塑性变形单晶体的塑性变形,主要是以滑移的方式进行的,即晶体的一部分沿着一定的晶面和晶向相对于另一部分发生滑动,滑动后原子处于新的稳定位置,不再回到原来位置。
研究表明,滑移总是优先沿晶体中一定的晶面和晶向发生,晶体中能够发生滑移的晶面和晶向称为滑移面和滑移方向。
滑移面和滑移方向越多,金属的塑性越好。
晶体的滑移是借助于位错的移动来实现的。
大量的位错移出晶体表面,就产生了宏观的塑性变形。
2、多晶体的塑性变形常用金属材料都是多晶体。
每个晶粒内的塑性变形主要仍以滑移方式进行。
但多晶体中各相邻晶粒的位向不同,各晶粒之间有一晶界相连接,因此,具有下列特点:(1)晶粒位向的影响由于多晶体中各个晶粒的位向不同,在外力作用下,有的晶粒处于有利于滑移的位置,有的晶粒处于不利位置。
产生滑移的晶粒必然会受到周围位向不同晶粒的阻碍,使滑移阻力增加,从而提高了塑性变形的抗力。
所以多晶体的塑性变形是逐步扩展和不均匀的,其结果之一便是产生内应力。
(2)晶界的作用晶界对塑性变形有较大的阻碍作用。
试样在晶界附近不易发生变形,出现所谓“竹节”现象。
这是因为晶界处原子排列比较紊乱,阻碍位错的移动,因而阻碍了滑移的缘故。
很显然,晶界越多,多晶体的塑性变形抗力越大。
(3)晶粒大小的影响在一定体积的晶体内晶粒数目越多,晶粒越细,晶界越多,不同位向的晶粒也越多。
因而塑性变形抗力也就越大,表现出较好的塑性和韧性。
故生产中都尽一切努力细化晶粒。
二、金属的冷塑性变形对性能的影响冷塑性变形对金属性能的主要影响是造成加工硬化,即随着变形度的增加,金属强度、硬度提高,而塑性、韧性下降的现象。
金属材料的塑性变形与回弹性能

金属材料的塑性变形与回弹性能金属材料的塑性变形与回弹性能是重要的材料力学性能指标,关乎到金属材料在工程应用中的可塑性和稳定性。
塑性变形是指金属材料在外力作用下会发生永久性变形的能力,而回弹性能则是指金属材料在撤去外力后能够恢复到原始形状的能力。
本文将从塑性变形和回弹性能的定义、影响因素以及控制方法等方面展开论述。
一、塑性变形的定义及影响因素塑性变形是指金属材料在外力作用下,由于晶体结构的滑移和位错的运动而发生的永久性变形。
塑性变形的大小取决于材料的塑性性能以及应力的强度,可以通过应变值来进行表征。
影响金属材料塑性变形的因素有很多,其中包括材料的晶体结构和晶格缺陷,材料的成分和结构等。
晶体结构的滑移是金属材料发生塑性变形的主要机制,而晶格缺陷如位错则会影响晶体的滑移过程。
此外,材料的成分和结构也会对塑性变形起到重要的影响,例如晶粒尺寸的大小、材料的纯度等都会对材料的塑性变形性能产生显著的影响。
二、回弹性能的定义及影响因素回弹性能是指金属材料在外力撤除后能够恢复到原始形状的能力。
回弹性能的好坏反映了金属材料的弹性模量和塑性变形程度。
金属材料的回弹性能受到多种因素的影响,包括金属材料的弹性模量、外力加载的速率以及材料的塑性变形程度等。
弹性模量是描述材料抵抗形变能力的指标,高弹性模量的金属材料具有较好的回弹性能。
外力加载的速率越快,金属材料的回弹性能越差。
此外,材料的塑性变形程度也会影响回弹性能,通常情况下,塑性变形越大,回弹性能也会相对较差。
三、控制塑性变形与回弹性能的方法为了控制金属材料的塑性变形和回弹性能,可以采取以下方法:1.合理选择材料和处理工艺:通过选择合适的金属材料和采取适当的处理工艺,可以改善材料的塑性变形和回弹性能。
例如,通过热处理可以优化材料的晶体结构,提高材料的塑性变形和回弹性能。
2.控制外力加载的速率:外力加载的速率对金属材料的塑性变形和回弹性能有着显著影响。
适当控制外力加载的速率,可以减小材料的塑性变形和提高回弹性能。
改善金属材料性能的主要方法

改善金属材料性能的主要方法改善金属材料性能的主要方法包括合金化、热处理、塑性变形、表面处理和纳米材料应用等。
下面详细介绍这些方法及其作用。
首先是合金化。
合金化是通过向金属中添加其他元素,以改善金属的性能。
常见的合金元素有碳、硅、磷、锰、铬、镍、钼等。
合金化可以改变金属的晶体结构和相变温度,提高材料的强度、硬度、耐腐蚀性和热稳定性等性能。
例如,将钢中的碳含量控制在一定范围内,可以得到高强度、高韧性的淬火态钢;将铝中加入适量的铜、锰、镁等元素,可以获得高强度、耐蚀性好的铝合金。
其次是热处理。
热处理是指将金属材料加热至一定温度,然后冷却至室温的工艺。
热处理可以使金属材料的晶粒尺寸、晶界结构以及组织性能发生变化,从而改变材料的力学性能。
常见的热处理方法有退火、固溶处理、时效处理等。
退火可以消除材料内部应力,降低硬度,提高塑性和延展性,改善加工性能。
固溶处理是将合金加热至固溶温度,使合金元素溶解到金属基体中,然后通过快速冷却固化,使合金元素均匀分布在基体中,从而提高强度和硬度。
时效处理是将固溶处理后的合金在一定温度下保持一段时间,使固溶体析出出現析出相的長英,进一步提高强度和硬度。
第三是塑性变形。
塑性变形是通过机械力的作用,使金属材料发生塑性变形并改变组织结构和性能的方法。
常见的塑性变形方法有拉伸、压缩、挤压、弯曲等。
塑性变形可以改善材料的力学性能,提高韧性和塑性,并消除材料内部的缺陷和应力集中。
例如,将金属材料进行冷变形可以细化晶粒尺寸,提高硬度和强度,同时提高材料的延展性。
第四是表面处理。
表面处理是指通过对金属材料表面进行一系列化学或物理处理,改善材料的表面性能。
常见的表面处理方法有电镀、阳极氧化、喷涂、化学处理等。
表面处理可以提高金属材料的耐腐蚀性、耐磨性、耐疲劳性和耐热性等表面性能。
例如,通过电镀镀上一层防腐性能好的金属如镀锌,可以提高金属材料的抗腐蚀能力;通过阳极氧化对铝材进行表面氧化处理,可以得到一层耐磨、耐腐蚀的氧化层。
塑性变形对金属组织和性能的影响
塑性变形对金属组织和性能的影响1. 塑性变形对金属组织结构的影响(1)晶粒发生变形金属发生塑性变形后,晶粒沿形变方向被拉长或压扁。
当变形量很大时, 晶粒变成细条状(拉伸时), 金属中的夹杂物也被拉长, 形成纤维组织。
变形前后晶粒形状变化示意图(2)亚结构形成金属经大的塑性变形时, 由于位错的密度增大和发生交互作用, 大量位错堆积在局部地区, 并相互缠结, 形成不均匀的分布, 使晶粒分化成许多位向略有不同的小晶块, 而在晶粒内产生亚晶粒。
金属经变形后的亚结构(3)形变织构产生金属塑性变形到很大程度(70%以上)时, 由于晶粒发生转动, 使各晶粒的位向趋近于一致, 形成特殊的择优取向, 这种有序化的结构叫做形变织构。
形变织构一般分两种:一种是各晶粒的一定晶向平行于拉拔方向, 称为丝织构, 例如低碳钢经高度冷拔后, 其<100>平行于拔丝方向; 另一种是各晶粒的一定晶面和晶向平行于轧制方向, 称为板织构, 低碳钢的板织构为{001}<110>。
形变织构示意图2. 塑性变形对金属性能的影响(1)形变强化金属发生塑性变形, 随变形度的增大, 金属的强度和硬度显著提高, 塑性和韧性明显下降。
这种现象称为加工硬化, 也叫形变强化。
产生加工硬化的原因是:金属发生塑性变形时, 位错密度增加, 位错间的交互作用增强, 相互缠结, 造成位错运动阻力的增大, 引起塑性变形抗力提高。
另一方面由于晶粒破碎细化, 使强度得以提高。
在生产中可通过冷轧、冷拔提高钢板或钢丝的强度。
(2)产生各向异性由于纤维组织和形变织构的形成, 使金属的性能产生各向异性。
如沿纤维方向的强度和塑性明显高于垂直方向的。
用有织构的板材冲制筒形零件时, 即由于在不同方向上塑性差别很大, 零件的边缘出现“制耳”。
在某些情况下, 织构的各向异性也有好处。
制造变压器铁芯的硅钢片, 因沿[100]方向最易磁化, 采用这种织构可使铁损大大减小, 因而变压器的效率大大提高。
金属材料强度及变形性能分析
金属材料强度及变形性能分析简介:金属材料的强度和变形性能是决定材料使用和应用范围的重要性能指标。
强度指材料抵抗外力破坏的能力,而变形性能则表征材料在外力作用下的形变特性。
本文将重点分析金属材料的强度和变形性能,并对其影响因素进行深入探讨。
一、金属材料的强度分析:1. 抗拉强度:金属材料的抗拉强度是指材料在拉伸力作用下抵抗破坏的能力。
抗拉强度取决于材料的原子结构、晶粒尺寸、晶体缺陷等因素。
常见的金属材料如钢、铝、铜等具有不同的抗拉强度。
2. 屈服强度:屈服强度是金属材料在拉伸过程中,从线性弹性阶段到非线性弹性阶段的临界点。
屈服强度是材料首次发生可见塑性变形的应力水平。
屈服强度反映了金属材料在外力作用下的抗变形能力。
3. 延伸率和断裂伸长率:延伸率和断裂伸长率是反映材料延展性能的重要参数。
延伸率指的是材料在断裂前的拉伸程度,断裂伸长率是指材料在断裂时相对于原始长度的变化程度。
较高的延伸率和断裂伸长率意味着材料具有良好的可塑性和变形能力。
二、金属材料的变形性能分析:1. 弹性变形:弹性变形是指金属材料在外力作用下具有恢复性的形变。
弹性变形区域内,材料的形状通过去除外力而恢复到初始状态。
弹性变形的特点是应变与应力呈线性关系,且应力和应变之间的关系服从胡克定律。
2. 塑性变形:塑性变形是指金属材料在外力作用下发生的不可逆形变,形变后无法完全恢复到初始状态。
金属材料的塑性变形可以通过冷加工、热加工等方式实现。
塑性变形主要由材料内部的晶格滑移、位错等现象引起。
3. 硬化和回弹:硬化是指金属材料在塑性变形过程中变得更加坚硬和脆性的现象。
在连续塑性变形中,材料会经历晶格被位错锁定的过程,导致材料的硬度增加。
回弹是指金属材料在去除外力后,部分形变恢复到原始状态的现象。
三、影响金属材料强度和变形性能的因素:1. 材料的组成和制备工艺:不同元素的添加和不同的制备工艺会对金属材料的强度和变形性能产生重要影响。
2. 晶体结构和晶粒尺寸:晶体结构的不同会导致材料的强度和塑性发生变化,较大的晶粒尺寸能够提高材料的强度,但会降低塑性。
塑性变形对金属组织性能的影响
塑性变形对金属组织性能的影响塑性变形是指金属在外力作用发生不可恢复的变形。
因为金属在变形过程中承受很大的外力,所以金属的组织和性能一定会发生变化。
由于金属发生塑性变形时的温度不同,所以金属塑性变形可以根据变形温度分为冷变形,温变形,热变形。
在不同的温度下,金属发生塑性变形时其组织和性能会发生不同的变化。
1.冷塑性变形对金属组织和性能的影响金属发生塑性变形时其变形机制主要有位错的滑移,孪生,扭折,高温下还有晶界滑动和扩散蠕变等方式。
在这些变形方式下,金属的组织会在晶粒形状尺寸,亚结构等方面产生变化,还会产生变形织构等。
在位错的运动过程中,位错之间,位错与溶质原子,间隙原子,空位之间,位错与第二相质点之间都会发生相互作用,引起位错数量,分布的变化。
从微观角度来看,这就是金属组织结构在塑性变形过程中发生的主要变化。
随着金属变形的进行及程度的增加,金属内部的位错密度开始增加,这是因为位错在运动到各种阻碍处如晶界,第二相质点等会受到阻碍,位错就会不断塞积和增值,直到可以使得相邻晶粒内的位错发动才能继续运动。
同时位错运动时所消耗的能量中会有一小部分没有转换成热能散发出去,反而会以弹性畸变能的形式存储在金属内部,使金属内部的点阵缺陷增加。
金属冷塑性变形后还会造成金属内部的亚结构发生细化,如原来在铸态金属中的亚结构直径约为0.01cm,经冷塑性变形后,亚结构的直径将细化至0.001-0.00001cm。
同样金属晶体在塑性变形过程中,随着变形程度的增大,各个晶粒的滑移面和滑移方向会逐渐向外力方向转动。
当变形量很大时,各晶粒的取向会大致趋向于一致,从而破坏了多晶体中各晶粒取向的无序性,也称为晶粒的择优取向,变形金属中这种组织状态则称为变形织构。
在塑性变形过程中随着金属内部组织的变化,金属的机械性能将产生明显的变化。
随着变形程度的增大,金属的硬度,强度显著升高,而塑性韧性则显著下降,这一变化称为加工硬化。
加工硬化认为是与位错的运动和交互作用有关。
塑性变形对材料组织与性能的影响
塑性变形对材料组织与性能的影响晶体发生塑性变形后,不仅其外形发生了变化,其内部组织以及各种性能也都发生了变化。
(1)显微组织的变化经塑性变形后,金属材料的显微组织发生了明显的改变,各晶粒中除了出现大量的滑移带、孪晶带以外,其晶粒形状也会发生变化,随着变形量的逐步增加,原来的等轴晶粒逐渐沿变形方向被拉长,当变形量很大时,晶粒已变成纤维状。
变形量很大时,晶粒拉长,出现纤维组织2 亚结构的变化•金属晶体在塑性变形的同时,位错密度迅速提高。
•经塑性变形后,多数金属晶体中的位错分布不均匀,当形变量较小时,形成位错缠结结构。
•当变形量继续增加时,大量位错发生聚集,使晶粒分化成许多位向略有不同的小晶块, 产生亚晶粒,即形成胞状亚结构。
•冷变形过程中形成亚结构是许多金属(例如铜、铁、钼、钨、钽、铌等)普遍存在的现象。
•一般认为亚结构对金属的加工硬化起重要作用,由于各晶块的方位不同,其边界又为大量位错缠结,对晶内的进一步滑移起阻碍作用。
因此,亚结构可提高金属和合金的强度。
•利用亚晶来强化金属材料是措施之一。
研究表明,胞状亚结构的形成与否与材料的层错能有关,一般来说,高层错能晶体易形成胞状亚结构。
而低层错能晶体形成这种结构的倾向较小。
这是由于对层错能高的金属而言,在变形过程中,位错不易分解,在遇到阻碍时,可以通过交滑移继续运动,直到与其它位错相遇缠结,从而形成位错聚集区域(胞壁)和少位错区域(胞内)。
层错能低的金属由于其位错易分解,形成扩展位错,不易交滑移,其运动性差,因而通常只形成分布较均匀的复杂网络结构。
3 性能的变化•(1)加工硬化(形变强化)•金属发生塑性变形, 随变形度增大, 金属的强度和硬度显著升高, 塑性和韧性明显下降。
这种现象称为加工硬化。
冷轧对铜及钢性能的影响强度指标增加、塑性指标下降。
金属的加工硬化特性可以从其应力-应变曲线上反映出来。
图是单晶体的应力-应变曲线,单晶体的塑性变形可划分为三个阶段描述:▪第I阶段,当切应力达到晶体的临界分切应力值时,滑移首先从一个滑移系中开始,由于位错运动所受的阻碍很小,因此该阶段称为易滑移阶段。
- 1、下载文档前请自行甄别文档内容的完整性,平台不提供额外的编辑、内容补充、找答案等附加服务。
- 2、"仅部分预览"的文档,不可在线预览部分如存在完整性等问题,可反馈申请退款(可完整预览的文档不适用该条件!)。
- 3、如文档侵犯您的权益,请联系客服反馈,我们会尽快为您处理(人工客服工作时间:9:00-18:30)。
金属材料抵抗冲击载荷作用而不破坏的能力。
常用一次摆锤冲击试验来测定金属材料的冲击韧性。 2)冲击试样尺寸和形状 尺寸:10mm × 10mm × 55mm 形状:U形 - 脆性材料
V形 - 韧性材料
3)表示方法 ak = AK /S0 (J· -2) cm 式中: Ak—冲断试样所消耗的冲击功(J)
3)均匀组织;
4)减少材料内部缺陷;
5)改善零件的结构形式;
6)减少零件的表面粗糙度,提高表面光洁度;
7)采取各种表面强化的方法(例:表面淬火,喷丸等)
37
§3.金属单晶体的塑性变形 1.塑性变形方式:滑移;孪生 2.滑移及相关概念 ① 滑移: 晶体的一部分沿着一定的晶面和晶向相对另一部分发生相 对的平行滑动,滑动的距离为原子间距的整数倍。这种变形 方式称为~。
35
3.产生疲劳断裂破坏的原因
一般认为: 是由于材料内部有夹杂、表面划痕及其它能引 起应力集中的缺陷。 据统计:约有80%的机件失效为疲劳断裂破坏。 4.破坏的形式 通常在疲劳破坏前没有明显的变形,断裂前没有 预兆,所以疲劳破坏经常造成重大事故。
36
5.改善方法:
1)合理选择材料;
2)细化晶粒;
弹性变形阶段
缩颈阶段
屈服阶段
断裂。
强化阶段
断裂形式:
韧性断裂——纤维状断口 脆性断裂——冰糖块状断口 疲劳断裂——贝壳状断口
拉伸曲线图
21
3.强度指标( σe ;σs ;σb)
1)弹性极限
定义:指在外力作用下由弹性变形过渡到弹-塑性变形时的应力。 或指完全卸载后不产生永久变形时所能承受的最大应力。
1、 塑性变形对组织结构影响 (1)晶粒变形:等轴状→拉长成纤维组织、带状组织 └ 性能各向异性 ( 2)亚结构的细化 铸态:d = cm;塑变后:d = cm 原因:位错受阻后塞积、缠结→亚晶界 → 晶粒分化为许多 位向略有差异的小晶块。 └ 变形中的晶粒碎化
公式:
b
式中:
Fb S0
MP a
Fb— 指试样被拉断前所承受的最大外力, 即拉伸曲线上b点所对应的外力(N)。
S0 — 试样原始横截面面积(mm2)
25
二、塑性指标( δ%;Ψ %)
定义: 塑性—材料受力后在断裂之前产生塑性变形的能力。 (1)断后伸长率 公式: δ% = (Lu- L0)/L0 ×100% 式中: L0—试样原标距的长度(mm)
三、硬度指标
1.定义: 硬度—金属材料抵抗其它更硬的物体压入其内的能力。
它是材料性能的一个综合物理量。表示金属材料在一个小
的体积范围内抵抗弹性变形、塑性变形或破断的能力。 2.实验方法 1)布氏硬度(HB);2)洛氏硬度(HR);3)维氏硬度(HV)
27
1.布氏硬度(HB)
1)定义 使用一定直径的钢球(D=1.588mm),以规定实验力压入 试样表面,并保持规定时间(t =10~30s)后卸除实验力,然后测 量表面压痕直径(d),再查相应的表(压痕~硬度对照表)得到 测定的硬度值。 压痕直径(d)越小,数值越大,表示硬度越高。
44
§4.金属多晶体的塑性变形
特点:
⑴ 单个晶粒与单晶体一致; ⑵ 各晶粒的变形具有不同时性:分批、逐次。
原因:取向不同。
⑶ 变形具有不均匀性: 晶粒内部与边界或晶粒之间。
晶界
45
⑷ 多晶体变形抗(阻)力 > 单晶体
① 晶界阻碍位错运动;
② 位向差→晶粒之间须协调 └ 意义: 产生晶界强化
46
§5. 塑性变形对金属组织和性能的影响
采用金刚石压头直接测量压痕深度来表示材料的硬度值。
2)表示方法
h3 HR 100 0.002
例:45HRC
表示: 测得洛氏硬度值为45; 数值越大,表示硬度越高。
30
3)常用洛氏硬度标尺及适用范围
标尺 HRA HRC 压头 金刚石(圆锥体) 金刚石(圆锥体) 总载荷/Kg 100 150 有效值 60~85 20~67 被测试材料 硬质合金、表面淬火钢 一般淬火钢
4)优、缺点
优点:操作简单、快速,可直接在表盘上读出硬度值,
适宜测定成品及较薄零件及硬度高的材料; 缺点:但由于压痕较小,硬度代表性差些,如果材料中有偏析 或组织不均匀的情况,测得的硬度值重复性较差, 一般要求在不同部位测试多次,并取平均值。
31
3.维氏硬度(HV)
1)特点: 压头为金刚石的正四棱锥体,根据压痕单位面积上的载荷
⑴取决于金属本性,与外力无关,取向无关; ⑵ 组织敏感参数: 当金属不纯,变形速度愈大, 变形温度愈低,τk 愈大。 ④影响σs的因素: ⑴主要与τk 有关; ⑵与外力及取向有关。
40
⑷ 伴随晶体的转动和旋转,滑移面转向与外力平行的方向,
滑移方向旋向最大的切应力方向;
P 滑移面
滑移前 P
力偶
滑移后
2)分类
根据载荷作用方式不同: a)抗拉强度——主要的常用强度指标; b)抗压强度; c)抗剪强度; d)抗扭强度; e)抗弯强度。
19
1.拉伸试样
形状:根据国家标准(GB/T228——2002) 有:圆形、矩形、六方形。
20
2.力-伸长曲线(F ~ΔL)
表示:拉力与伸长量之间的关系曲线。
拉伸过程:
38
② 滑移特点
⑴ 发生在最密排晶面,滑移方向为最密排晶向;
⑵ 只在切应力下发生,存在临界分切应力—τk 。 ζ 弹 性 伸 长 ζ 弹 性 歪 扭 塑性变形 (滑移)
39
ζ
ζ η
断裂
η
η
η
⑶ 滑移两部分相对移动的距离是原子间距的整数
倍,但滑移后滑移面两边的晶体位向仍保持一致;
③影响τk 的因素:
(碳钢、有色金属等线材、型材、管材)
线材拉拔
管材拉拔
6
4)锻压 (碳钢、合金钢、特种钢坯料)
自由锻
模锻
7
பைடு நூலகம்
5)冷冲压
(低碳钢、合金钢板材)
8
一、塑性变形的基本概念
1.载荷
(1)定义
金属材料在加工及使用过程中所受的外力。
(2)类型
根据载荷作用性质不同:
a)静载荷 b)动载荷 —没有变化; —瞬间变化;
公式:
Fe e S0
MP a
式中:
Fe —试样不出现任何明显塑性变形时所受的最大载荷, 即拉伸曲线中e点所对应的外力(N); S0 —试样原始横截面面积(mm2)。
22
2)屈服强度
定义:--指在外力作用下开始产生明显塑性变形的最小应力。
公式:
Fs s S0
MP a
式中:
Fs--试样产生明显塑性变形时所受的最小载荷, 即拉伸曲线中S点所对应的外力(N); S0 --试样原始横截面面积(mm2)。
a)变形
零件在外力作用下形状和尺寸所发生的变化。 (包括:弹性变形和塑性变形)
b)断裂
零件在外力作用下发生开裂或折断的现象。
c)磨损
因摩擦使得零件形状、尺寸和表面质量发生变化的现象。
3
2.常见塑性变形形式
1)轧制 (板材、线材、棒材、型材、管材)
板材轧制
4
2)挤压
(低碳钢、有色金属等型材)
5
3)拉拔
41
3.滑移系及滑移系数的实际意义
(1)各晶体结构的滑移系
体心立方 (b.c.c) 面心立方 (f.c.c)
〔111〕 (110)
(111) 〔110〕
滑移面:{110} (110)、(011)、(101) (110)、(011)、(101) 滑移方向:〈111〉 滑移系数:6×2=12
滑移面:{111} (111)、(111)、(111)、(111)
(3)注意
内力和外力不同于作用力和反作用力。
11
3.应力
(1)定义
单位面积上所受到的力。
(2)计算公式
σ= F/ S( MPa/mm2 )
式中: σ——应力;
F ——外力;
S ——横截面面积。
12
二、金属的变形 金属在外力作用下的变形三阶段:
弹性变形 1.特点 弹性变形: 弹-塑性变形 断裂。
金属弹性变形后其组织和性能不发生变化。 塑性变形: 金属经塑性变形后其组织和性能将发生变化。 2.变形原理 金属在外力作用下,发生塑性变形是由于晶体内部 缺陷—位错运动的结果,宏观表现为外形和尺寸变化。 13
14
三、金属材料的冷塑性变形与加工硬化
1.冷塑性变形结果
外部:晶粒形状发生变化——沿着变形方向被压扁或拉长;
内部: 晶粒内部位错密度增加,晶格畸变加剧;
性能: 金属强度和硬度提高,塑性和韧性下降。 这种现象——称为“形变强化”或“加工硬化”。
15
2.加工硬化的应用
对于不能通过热处理强化的金属是一种重要的
23
对于大多数没有明显的屈服现象的金属材料。 定义:条件屈服强度: ( σ0.2 ) 规定:产生0.2%残余伸长时的应力作为条件屈服强度。
指出:
是工程技术中最重要的机械性能指标之一; 是设计零件时作为选用金属材料的重要依据。
24
3)抗拉强度
定义:指在外力作用下由产生大量塑性变形到断裂前所承受的
最大应力,故又称强度极限。
来计算硬度值。
根据试样大小、厚薄选择载荷:(F=0.098~9.8N) 适合测定极薄试样表面的硬度和表面硬化层的硬度高低。 2)表示方法: 例:640HV30 表示:实验力:30Kg;时间:10~15s 表面的硬度值:640HV
同样数值越大,表示硬度越高。
32
四、冲击韧性
(瞬间动载荷)
33
1)定义