第三章金属材料的塑性变形
合集下载
材料力学性能塑性变形

S S (1 2 R a)[ln( 1 a 2 R)]
《材料力学性能》 第三章 塑性变形
3.3.3 形变强化的实际意义
• 金属的加工硬化,对冷加工成型工艺是很重要 的。
• 对于工作中的零件,也要求材料有一定的加工 硬化能力,零件具有抵抗偶然超载的能力,是 安全使用的可靠保证。
• 形变强化是提高材料强度的重要手段,尤其对 不能进行热处理强化的材料。
§3.3 真应力-应变曲线及形变强化规律
真应力—真应变加线可用Hollomon方程来表示:
S K
n
K--强化系数;n--应变强化指数。 由上式可知,n值越大,材料对继续塑性变形得抗力愈高。 大多数金属材料的应变硬化系数为0.05~0.5之间。 应变强化速率与n意义的区别:
S K
n
Mb 条件抗扭强度 b W
真实抗扭强度
4 dM k 3 [3M k k ( )k ] d0 d
《材料力学性能》 第三章 塑性变形
扭转切应变
k d0
2l0
100%
对于塑性材料,因塑性变形很大,弹性变形可忽略, 上式求出的总应变看作残余切应变;对于脆性材料和 低塑性材料,弹性变形不能忽略,残余切应变还应减 去弹性切应变γy。
《材料力学性能》 第三章 塑性变形
3.2.3 应变时效 如果在屈服后一定塑性变 形处卸载,随即再拉伸加 载,则屈服现象不再出现, 若在卸载后在室温或较高 温度停留较长时间后再拉 伸,即物理屈服现象重现、 且新的屈服平台高于卸载 时应力—应变曲线。这种 现象称为应变时效。
《材料力学性能》 第三章 塑性变形
3.4.3 弯曲试验
1、弯曲试验分为三点弯曲和四点弯曲,试样主要有矩形 截面和圆形截面。
金属的塑性变形与再结晶(3)
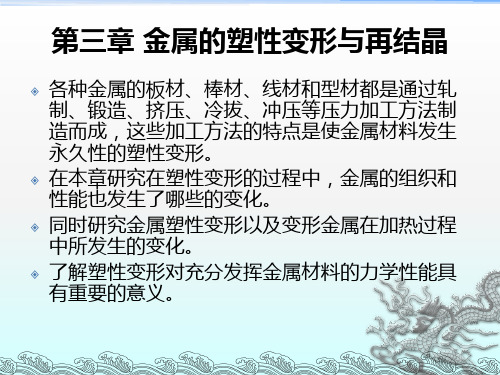
滑移实质上是位错在滑移面上运动的结果,在切 应力的作用下,晶体中存在的正刃位错逐步移动, 当这个位错移到晶体的右边缘时,移出晶体的上 半部就相对于下半部移动了一个原子间距,形成 一个原子间距的滑移量。
同一滑移面上若有大量的位错移出,则在晶体表 面形成一条滑移线。
位错在晶体中移动时所需切应力很小,因为当位错中心前 进一个原子间距时,一齐移动的只是位错中心少数原子, 而且其位移量都不大,形成逐步滑移,这就比一齐移动所 需的临界切应力要小得多,这称为“位错的易动性”。
研究表明,亚晶界的存在使晶体的变形抗力增加, 是引起加工硬化的重要因素之一。
3.形变织构
在塑性变形过程中,当金属按一定的方向变形量 很大时(变形量大于70%以上),多晶体中原来任 意位向的各晶粒的取向会大致趋于一致,这种有 序化结构叫作“变形织构”,又称为“择优取 向”,
金属材料的加工方式不同形成不同类型的织构: 拉拔时形成的织构称为丝织构,其特征是各个晶 粒的某一晶向平行于拉拔方向;轧制时形成的织 构称为板织构,其特征是不仅某一晶面平行于轧 制平面,而且某一晶向也平行于轧制方向。
3.变形引起的内应力
在金属塑性变形过程中,大约有10%的能量转化为内应力而残留在金属中, 使其内能增加。
这些残留于金属内部且平衡于金属内部的应力称为残余内应力。它是由于金 属在外力作用下各部分发生不均匀的塑性变形而产生的。
内应力一般可分为三种类型:Βιβλιοθήκη (1)宏观内应力(第一类内应力)
金属材料在塑性变形时,由于各部分变形不均匀,使整个工件或在较大的 宏观范围内(如表层与心部)产生的残余应力。
3.1.2多晶体金属塑性变形的特点
大多数金属材料是由多晶体组成的。 多晶体塑性变形的实质与单晶体一样。 要考虑到晶粒彼此之间在变形过程中的约束作用,以及晶界对塑性变形的影
同一滑移面上若有大量的位错移出,则在晶体表 面形成一条滑移线。
位错在晶体中移动时所需切应力很小,因为当位错中心前 进一个原子间距时,一齐移动的只是位错中心少数原子, 而且其位移量都不大,形成逐步滑移,这就比一齐移动所 需的临界切应力要小得多,这称为“位错的易动性”。
研究表明,亚晶界的存在使晶体的变形抗力增加, 是引起加工硬化的重要因素之一。
3.形变织构
在塑性变形过程中,当金属按一定的方向变形量 很大时(变形量大于70%以上),多晶体中原来任 意位向的各晶粒的取向会大致趋于一致,这种有 序化结构叫作“变形织构”,又称为“择优取 向”,
金属材料的加工方式不同形成不同类型的织构: 拉拔时形成的织构称为丝织构,其特征是各个晶 粒的某一晶向平行于拉拔方向;轧制时形成的织 构称为板织构,其特征是不仅某一晶面平行于轧 制平面,而且某一晶向也平行于轧制方向。
3.变形引起的内应力
在金属塑性变形过程中,大约有10%的能量转化为内应力而残留在金属中, 使其内能增加。
这些残留于金属内部且平衡于金属内部的应力称为残余内应力。它是由于金 属在外力作用下各部分发生不均匀的塑性变形而产生的。
内应力一般可分为三种类型:Βιβλιοθήκη (1)宏观内应力(第一类内应力)
金属材料在塑性变形时,由于各部分变形不均匀,使整个工件或在较大的 宏观范围内(如表层与心部)产生的残余应力。
3.1.2多晶体金属塑性变形的特点
大多数金属材料是由多晶体组成的。 多晶体塑性变形的实质与单晶体一样。 要考虑到晶粒彼此之间在变形过程中的约束作用,以及晶界对塑性变形的影
第三章_金属冷塑性变形解析
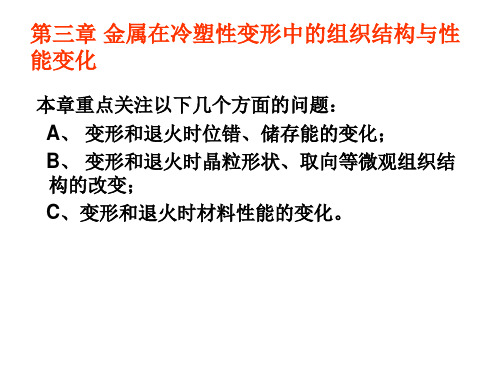
在变形过程中,随着变形程度的增加,位错密度 的变化规律如下:
bL
二、储存能的测定方法 储存能的确定是很难的。 其测量的方法有:热量法、X-射线法,还可根据 某些物理或机械性能来间接确定。
采用热量法测定储存能,我们还必须关注材料的 化学成分、晶粒尺寸、变形程度和变形温度。 总体情况是:1)变形程度增加,储存能增大; 2)变形方式不同,剩余功的变化会导致储存能的 变化;如铜,拉伸时是3.2-5.7 J/mol,压缩时是 3.8-8.3J/mol,拉拔时是-95J/mol。 3)低和中应变条件下,细晶的储存能比粗晶大, 但高应变条件下,储存能与晶粒无关。
轧制织构不仅有平行于轧制方向的特殊结晶学 方向,而且在轧制面上还有一个低指数平面。
面心立方晶格金属和合金有相当简单而又显著
的轧制织构,这就是{110}<112>;同时带有各不相
同的大量次级织构,在铜金属中,直到变形很大而
接近{112}<111>时,这些次级织构还都是杂乱的。
次级织构对再结晶织构退火的生长有影响。
图3.2 Stored energies of deformation for different orientations in the α fibre of cold-rolled iron and steel
3.2 金属组织结构的变化
• 金属塑性变形的物理实质基本上就是位错的运动, 位错运动的结果就产生了塑性变形。 • 在位错的运动过程中,位错、溶质原子、间隙位 置原子、空位、第二相质点都会发生相互作用, 引起位错的数量、分布和组态的变化。从微观角 度来看,这就是金属组织结构在塑性变形过程中 或变形后的主要变化。
第三章 金属在冷塑性变形中的组织结构与性 能变化
第三章 金属塑性变形的物理基础
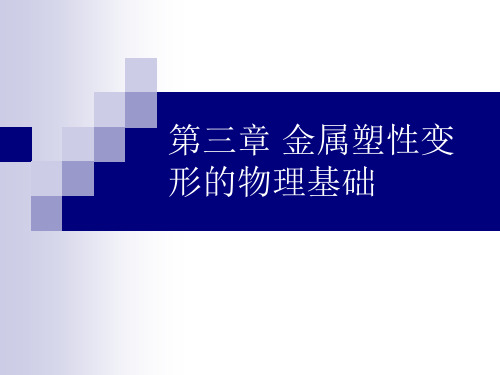
(1)塑性的基本概念
什么是塑性? 塑性是金属在外力作用下产生永久变形 而不破坏其完整性的能力。
塑性与柔软性的区别是什么? 塑性反映材料产生永久变形的能力。 柔软性反映材料抵抗变形的能力。
塑性与柔软性的对立统一
铅---------------塑性好,变形抗力小
不锈钢--------塑性好,但变形抗力高 白口铸铁----塑性差,变形抗力高
塑性指标的测量方法
拉伸试验法 压缩试验法 扭转试验法 轧制模拟试验法
拉伸试验法
Lh L0 100%
L0 F0 Fh 100%
F0
式中:L0——拉伸试样原始标距长度; Lh——拉伸试样破断后标距间的长度; F0——拉伸试样原始断面积; Fh——拉伸试样破断处的断面积
%
晶粒5 晶粒4 晶粒3
晶粒2
晶粒1
位置,mm
图5-6 多晶铝的几个晶粒各处的应变量。 垂直虚线是晶界,线上的数字为总变形量
四、合金的塑性变形
单相固溶体合金的变形 多相合金的变形
§3. 2 金属塑性加工中组织和性能变化 的基本规律
一、冷塑性变形时金属组织和性能的变化 二、热塑性变形时金属组织和性能的变化
2200
N/mm2
图4-6 正压力对摩擦系数的影响
0.5
μ
0.4
0.3
0.4
0.2 0.2
0.1
0
℃
200
400
600
800
图4-7 温度对钢的摩擦系数的影响
0
400
600
800 ℃
图4-8 温度对铜的摩擦系数的影响
测定摩擦系数的方法
夹钳轧制法 楔形件压缩法 塑性加工常用摩擦系数 圆环镦粗法
《金属材料与热处理》第三章金属的塑性变形对组织性能
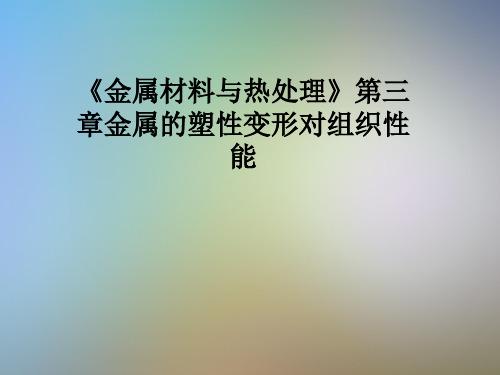
➢再结晶温度指的是最低再结晶温度(T再):用经过严
重冷塑性变形的金属,经1小时加热后能完全再结晶的 最低温度来表示。
最低再结晶温度:
T再=0.4T熔点 式中温度单位为绝对温度(K)。
8
学习情境三:金属的塑性变形对组织性能的影响 3.2
(3)再结晶温度影响因素:
1)变形程度 ➢2)金金属属再纯结度晶前:塑纯性度变越形高的, 最相低对再变结形晶量温称度为也预就先越变低形 度➢。3)预;加先热变速形度越大, 金属的晶体缺陷就越多, 组织越不 稳➢➢杂再定质结, 最和晶低合是再金一结元扩晶素散温(过度高程也熔, 需就点一越元定低素时;)间阻才碍能原完子成扩;散和晶 ➢界➢当提迁预高移先加, 可变热显形速著度度提达会高一使最定再低大结再小晶结后在晶,较最温高低度温再;度结下晶发温生度;趋于某 一➢高原稳纯始定度晶值铝粒。(越99粗.9大9,9再%结)最晶低温再度结越晶高温。度为80 ℃; ➢工业纯铝(99.0%)最低再结晶温度提高到290 ℃。
3
学习情境三:金属的塑性变形对组织性能的影响 3.2
3、热加工晶粒大小控制措施
(1).控制较低的加工终了温度 (2).控制较大的变形程度 (3).控制较快的冷却速度
0
学习情境三:金属的塑性变形对组织性能的影响 3.2
3、产生残余内应力 ➢定义:外力去除后,金属内部残留下来的应力。
产生原因:金属发生塑性变形时,内部变形不均匀, 位错、空位等晶体缺陷增多,会产生残余内应力。
➢1)宏观内应力 ➢2)微观残余应力 ➢3)晶格畸变应力
1
学习情境三:金属的塑性变形对组织性能的影响 3.2
3
学习情境三:金属的塑性变形对组织性能的影响 3.1
第一节 金属的塑性变形
重冷塑性变形的金属,经1小时加热后能完全再结晶的 最低温度来表示。
最低再结晶温度:
T再=0.4T熔点 式中温度单位为绝对温度(K)。
8
学习情境三:金属的塑性变形对组织性能的影响 3.2
(3)再结晶温度影响因素:
1)变形程度 ➢2)金金属属再纯结度晶前:塑纯性度变越形高的, 最相低对再变结形晶量温称度为也预就先越变低形 度➢。3)预;加先热变速形度越大, 金属的晶体缺陷就越多, 组织越不 稳➢➢杂再定质结, 最和晶低合是再金一结元扩晶素散温(过度高程也熔, 需就点一越元定低素时;)间阻才碍能原完子成扩;散和晶 ➢界➢当提迁预高移先加, 可变热显形速著度度提达会高一使最定再低大结再小晶结后在晶,较最温高低度温再;度结下晶发温生度;趋于某 一➢高原稳纯始定度晶值铝粒。(越99粗.9大9,9再%结)最晶低温再度结越晶高温。度为80 ℃; ➢工业纯铝(99.0%)最低再结晶温度提高到290 ℃。
3
学习情境三:金属的塑性变形对组织性能的影响 3.2
3、热加工晶粒大小控制措施
(1).控制较低的加工终了温度 (2).控制较大的变形程度 (3).控制较快的冷却速度
0
学习情境三:金属的塑性变形对组织性能的影响 3.2
3、产生残余内应力 ➢定义:外力去除后,金属内部残留下来的应力。
产生原因:金属发生塑性变形时,内部变形不均匀, 位错、空位等晶体缺陷增多,会产生残余内应力。
➢1)宏观内应力 ➢2)微观残余应力 ➢3)晶格畸变应力
1
学习情境三:金属的塑性变形对组织性能的影响 3.2
3
学习情境三:金属的塑性变形对组织性能的影响 3.1
第一节 金属的塑性变形
3-1 金属的塑性变形
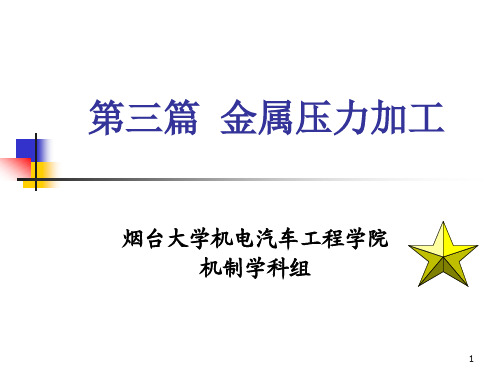
18
四、纤维组织
材料在压力加工中产生塑性 材料在压力加工中产生塑性 压力加工 变形时, 变形时,基体金属的晶粒形状和 沿晶界分布的杂质形状都发生了 变形,它们都将沿着变形方向被 变形, 拉长,呈纤维形状。 拉长,呈纤维形状。这种结构叫 纤维组织。 纤维组织。 纤维组织是变形后所形成的带有方向性的晶粒。 纤维组织是变形后所形成的带有方向性的晶粒。 是变形后所形成的带有方向性的晶粒
后 退
12
二、多晶体的塑性变形
多晶体是多个位向不同变形总和,除了晶内变形外, 多晶体是多个位向不同变形总和,除了晶内变形外, 是多个位向不同变形总和 还有晶间变形,及晶粒间互相移动及转动。 还有晶间变形,及晶粒间互相移动及转动。
特点: 特点:
变形过程复杂。 变形过程复杂。 变形抗力比单晶体大的多。 变形抗力比单晶体大的多。 多晶体塑变以晶内为主,晶间很小。 多晶体塑变以晶内为主,晶间很小。
5
3.挤压 3.挤压
金属坯料在挤压模内被挤出模孔而变形, 金属坯料在挤压模内被挤出模孔而变形,从 挤压模内被挤出模孔而变形 而获得所需制件的加工方法。 而获得所需制件的加工方法。 正挤压:金属流动方向与凸模送进的方向相同。 正挤压:金属流动方向与凸模送进的方向相同。 方向相同 反挤压:金属流动方向与凸模送进方向相反 方向相反。 反挤压:金属流动方向与凸模送进方向相反。 采用机械化生产方法具有很高的生产率。 采用机械化生产方法具有很高的生产率。
22
2) 金属组织的影响
纯金属和非饱和固溶体可锻性好。 纯金属和非饱和固溶体可锻性好。 可锻性好 金属化合物是硬脆的组成相, 金属化合物是硬脆的组成相,组织中的金属化合 是硬脆的组成相 物越多,可锻性越差。 物越多,可锻性越差。 比如纯铁、纯铜、纯铝、具有单相铁素 比如纯铁、纯铜、纯铝、 体或单相奥氏体的钢具有良好的可锻性, 体或单相奥氏体的钢具有良好的可锻性,但 是具有网状渗碳体的过共析钢可锻性较差。 是具有网状渗碳体的过共析钢可锻性较差。 铸铁中由于含有大量的渗碳体或石墨, 铸铁中由于含有大量的渗碳体或石墨, 其可锻性非常差,铸铁是根本不能锻造的。 其可锻性非常差,铸铁是根本不能锻造的。
《材料成型技术与基础》全套PPT电子课件教案-第03章 单晶体与多晶体的塑性变形等
拉拔时金属应力状态
第三章金属材料的塑性变形
本章小结
锻造、轧ቤተ መጻሕፍቲ ባይዱ、挤压、冲压等都是塑性变形。这些 塑性变形的目的不仅是为了得到零件的外形和尺寸, 更重要的是为了改善金属的组织和性能。
塑性变形的主要形式是滑移和孪生,是在切应力 的作用下进行的,塑性变形将产生形变强化,形成纤 维组织,具有各向异性。塑性变形后的 金属加热时会 产生回复或再结晶及晶粒长大,其形变强化现象消除。
滑移特点:①滑移是在切 应力作用下完成的;②滑 移时移动的距离是原子间 距的整数倍;③滑移的同 时由于正应力组成的力偶 作用,推动晶体转动,力 图使滑移面转向与外力一 致的方向。④滑移的实质 是位错运动的结果。因此 滑移的实际临界切应力远 远大于理论临界切应力。
第三章金属材料的塑性变形
单晶体滑移变形示意图
定义:经冷变形的金属当加热到T再时,会在变形最激 烈的区域自发形成新的细小等轴晶粒,叫做再结 晶这一过程实质上也是一个形核和长大的过程, 但晶格类型不变,只是改变了晶粒外形. T再T熔
※金属再结晶后,消除了残余应力和形变强化现象 晶粒长大 冷变形和热变形 金属纤维组织及其应用
第三章金属材料的塑性变形
第三章金属材料的塑性变形
单晶体和多晶体的塑性变形 金属的形变强化 塑性变形金属在加热时组织和性能的变化 塑性加工性能及影响因素 本章小结
第三章金属材料的塑性变形
单晶体的塑性变形 1.滑移 2.孪生 1.晶粒取向对塑性变形的影响 2.晶界对塑性变形的影响
第三章金属材料的塑性变形
锌单晶体的滑移变形示意图
第三章金属材料的塑性变形
未变形 弹性变形 弹塑性变形 塑性变形
位错运动引起的滑移变形示意图
第三章金属材料的塑性变形
金属塑性成形原理第三章金属塑性成形的力学基础第四节屈服准则
则,这个圆柱面就称为主应力空间中的米塞斯屈服表面。
屈雷斯加六角柱面
N
σ3
I1
I J
HGF
K
0
E
L
A
B
D C
σ1
C1
主应力空间中的屈服表面
屈服表面的几何
米塞斯圆柱面 意义:若主应力
空间中的一点应
力状态矢量的端
点位于屈服表面,
σ2
则该点处于塑性
状态;若位于屈
服表面内部,则
该点处于弹性状
态。
2、两向应力状态下的屈服轨迹
真实应力-应变曲线及某些简化形式
(1)理想弹性材料——图a,b,d (2)理想塑性材料——图b,c
(3)弹塑性材料
理想弹塑性材料-图b 弹塑性硬化材料-图d
(4)刚塑性材料
理想刚塑性材料-图c 刚塑性硬化材料-图e
s
1、实际金属材料在比例极限以下——理想弹性 一般金属材料是理想弹性材料
2、金属在慢速热变形时——接近理想塑性材料 3、金属在冷变形时——弹塑性硬化材料 4、金属在冷变形屈服平台部分——接近理想塑性
引等倾线ON l m n 1 3
在ON上任一点 1 2 3 m
过P点引直线 PM ON
OM表示应力球张量,MP表示 应力偏张量
矢量
OP OM MP
σ1
MP OP 2 OM 2
σ3 σ3
0
σ1
N
P M
2
3
s
σ2
主应力空间
σ3
OP
2
12
2 2
2 3
N
σ3
P
M
OM 1l 2m 3n
屈雷斯加屈服准则 未考虑中间应力 使用不方便
第三章 金属的塑性变形
变形速度得到恰当配合。
主要工艺:微细晶粒超塑性、相变超塑性
小结
1.认识单晶体金属塑性变形的主要方式-滑移的主 要特点;
2.认识多晶体金属塑性变形的特点和晶界与晶粒位 向对塑性变形的影响; 3.掌握金属在塑性变形过程中,结构、组织与性能 的变化规律,加工硬化产生的原因和实际意义;
滑移的同时必然伴随着晶体的转动。
孪生
孪生:在切应力作用下,晶体的一部分 相对于另一部分沿一定晶面(孪生面)和晶 向(孪生方向)发生切变的变形过程。
孪生的特点
金属晶体中变形部分与未变形部分在孪生面
两侧形成镜面对称关系。 发生孪生的部分(切变部分)称为孪生带或 孪晶。
孪生带的晶格位向发
生变化,发生孪生时 各原子移动的距离是 不相等的。
一、单晶体的塑性变形
塑性变形主要方式:滑移、孪生
单晶体
弹性变形
滑移变形
孪生变形
滑移变形在晶体表面留下变形痕迹 孪晶变形在晶体内部留下变形痕迹
滑移
滑移是在切应力作用下,晶体的一部分 沿一定的晶面(滑移面)上的一定方向(滑 移方向)相对于另一部分发生滑动。
滑移示意图
机械工程材料
滑移的特点
滑移与位错
多晶体由许多晶粒组成,各个晶粒位向不同,且存在许 多晶界,变形复杂。
2、多晶体的塑性变形
多晶体由许多晶粒组成,各个晶粒位向不同, 且存在许多晶界,变形复杂。
(A)晶界的影响
晶界起强化作用
( B)晶粒位向的影响
轴向拉力F,试样横截面积A , 外力F作用在滑移面上,沿滑 移 方向的分切应力为:
晶界的影响
金属在热轧时变形和再结晶的示意图
热加工对金属组织和性能的影响⑴
①改善铸锭组织,表现在:
主要工艺:微细晶粒超塑性、相变超塑性
小结
1.认识单晶体金属塑性变形的主要方式-滑移的主 要特点;
2.认识多晶体金属塑性变形的特点和晶界与晶粒位 向对塑性变形的影响; 3.掌握金属在塑性变形过程中,结构、组织与性能 的变化规律,加工硬化产生的原因和实际意义;
滑移的同时必然伴随着晶体的转动。
孪生
孪生:在切应力作用下,晶体的一部分 相对于另一部分沿一定晶面(孪生面)和晶 向(孪生方向)发生切变的变形过程。
孪生的特点
金属晶体中变形部分与未变形部分在孪生面
两侧形成镜面对称关系。 发生孪生的部分(切变部分)称为孪生带或 孪晶。
孪生带的晶格位向发
生变化,发生孪生时 各原子移动的距离是 不相等的。
一、单晶体的塑性变形
塑性变形主要方式:滑移、孪生
单晶体
弹性变形
滑移变形
孪生变形
滑移变形在晶体表面留下变形痕迹 孪晶变形在晶体内部留下变形痕迹
滑移
滑移是在切应力作用下,晶体的一部分 沿一定的晶面(滑移面)上的一定方向(滑 移方向)相对于另一部分发生滑动。
滑移示意图
机械工程材料
滑移的特点
滑移与位错
多晶体由许多晶粒组成,各个晶粒位向不同,且存在许 多晶界,变形复杂。
2、多晶体的塑性变形
多晶体由许多晶粒组成,各个晶粒位向不同, 且存在许多晶界,变形复杂。
(A)晶界的影响
晶界起强化作用
( B)晶粒位向的影响
轴向拉力F,试样横截面积A , 外力F作用在滑移面上,沿滑 移 方向的分切应力为:
晶界的影响
金属在热轧时变形和再结晶的示意图
热加工对金属组织和性能的影响⑴
①改善铸锭组织,表现在:
第3章 金属材料的塑性成形——压力加工
可锻性的优劣一般常用金属的塑性和变形抗力两个 指标来综合衡量。
其优劣主要取决于金属本身和变形时的外部条件。
影响可锻性的因素
(1) 金属的成分:纯金属好于合金,fcc好于bcc好 于hcp,低碳钢优于高碳钢,低碳低合金钢优于 高碳高合金钢;有害杂质元素一般使可锻性变坏
(2) 金属的组织:单相组织好于多相组织;铸态下 的柱状组织、粗晶粒组织、晶界上存在偏析或有 共晶莱氏体组织使可锻性变差
2、研究与开发塑性加工过程的计算机模拟技术与模具 CAD/CAE/CAM技术等。
3、研究与开发柔性成形技术、增量成形技术、净成形技 术、近净成形技术、复合成形技术等。
4、研究与开发使环境净化的加工技术,如低噪音、小/ 无震动、节省能源、资源或再利用的加工技术。
§3.2 金属的塑性加工成形性
金属的塑性加工成形性/可锻性(Forgeability) : 用来衡量金属在外力作用下发生塑性变形而不易 产生裂纹的能力,是金属重要的工艺性能之一;
(3) 加工条件 1) 变形温度:一般变形温度的升高,可提高金 属的可锻性;但注意过热、过烧问题
不同合金系8种典型金属的可锻性
Ⅰ—纯金属及单相合金(铅合金、 钼合金、镁合金);Ⅱ—纯金属及 单相合金(晶粒长大敏感者)(铍、镁 合金、钨合含、钛合金);Ⅲ—具 有不溶解组分的合金(高硫钢,含 硒不锈钢);Ⅳ—具有可溶组分的 合金(含氧化物的钼合金,含可溶 性碳化物和氮化物的不锈钢); Ⅴ—加热时形成有塑性第2相的合 金(高铬不锈钢);Ⅵ—加热时形成 低熔点第2相的合金(含硫的铁、含 锌的镁合金);Ⅶ—冷却时形成有 塑性第2相的合金(碳钢和低合金钢 、-钛合金和钛合金);Ⅷ—冷 却时形成脆性第2相的合金(高温合
可显著减小总变形力,用小设备加工大零件。
其优劣主要取决于金属本身和变形时的外部条件。
影响可锻性的因素
(1) 金属的成分:纯金属好于合金,fcc好于bcc好 于hcp,低碳钢优于高碳钢,低碳低合金钢优于 高碳高合金钢;有害杂质元素一般使可锻性变坏
(2) 金属的组织:单相组织好于多相组织;铸态下 的柱状组织、粗晶粒组织、晶界上存在偏析或有 共晶莱氏体组织使可锻性变差
2、研究与开发塑性加工过程的计算机模拟技术与模具 CAD/CAE/CAM技术等。
3、研究与开发柔性成形技术、增量成形技术、净成形技 术、近净成形技术、复合成形技术等。
4、研究与开发使环境净化的加工技术,如低噪音、小/ 无震动、节省能源、资源或再利用的加工技术。
§3.2 金属的塑性加工成形性
金属的塑性加工成形性/可锻性(Forgeability) : 用来衡量金属在外力作用下发生塑性变形而不易 产生裂纹的能力,是金属重要的工艺性能之一;
(3) 加工条件 1) 变形温度:一般变形温度的升高,可提高金 属的可锻性;但注意过热、过烧问题
不同合金系8种典型金属的可锻性
Ⅰ—纯金属及单相合金(铅合金、 钼合金、镁合金);Ⅱ—纯金属及 单相合金(晶粒长大敏感者)(铍、镁 合金、钨合含、钛合金);Ⅲ—具 有不溶解组分的合金(高硫钢,含 硒不锈钢);Ⅳ—具有可溶组分的 合金(含氧化物的钼合金,含可溶 性碳化物和氮化物的不锈钢); Ⅴ—加热时形成有塑性第2相的合 金(高铬不锈钢);Ⅵ—加热时形成 低熔点第2相的合金(含硫的铁、含 锌的镁合金);Ⅶ—冷却时形成有 塑性第2相的合金(碳钢和低合金钢 、-钛合金和钛合金);Ⅷ—冷 却时形成脆性第2相的合金(高温合
可显著减小总变形力,用小设备加工大零件。
- 1、下载文档前请自行甄别文档内容的完整性,平台不提供额外的编辑、内容补充、找答案等附加服务。
- 2、"仅部分预览"的文档,不可在线预览部分如存在完整性等问题,可反馈申请退款(可完整预览的文档不适用该条件!)。
- 3、如文档侵犯您的权益,请联系客服反馈,我们会尽快为您处理(人工客服工作时间:9:00-18:30)。
发生切变的部分称孪生带或孪 晶,沿其发生孪生的晶面称孪 生面。
15
孪生的结果使孪生面两侧的晶体呈镜面对称。
孪生示意图
16
与滑移相比:
孪生使晶格位向发生改变; 所需切应力比滑移大得多,变形速度极快,接近声速; 孪生时相邻原子面的相对位移量小于一个原子间距(滑移
是原子间距的整数倍)。 密排六方晶格金属:滑移系少,常以孪生方式变形。 体心立方晶格金属:只有在低温或冲击作用下才发生孪生变形。 面心立方晶格金属:一般不发生孪生变形。
这种弹性变形便成 为塑性变形晶粒的 变形阻力。
由于晶粒间的这种 相互约束,使得多 晶体金属的塑性变 形抗力提高。
19
(3)晶界的影响
当位错运动到晶界附近时, 受到晶界的阻碍而堆积起 来,称位错的塞积。要使 变形继续进行,则必须增 加外力,从而使金属的变 形抗力提高。
20
晶界对塑性变形的影响
Cu-4.5Al合金晶 界的位错塞积
利用形变强化现象来提高金属材料的强度,在工业上 应用甚广。例如冷拉钢丝。尤其是对于纯金属以及不 能用热处理强化的合金,这种方法格外重要。
冷态压力加工后位错密度大增,晶格畸变很大,电 阻有所增大,抗蚀性降低;冷变形产品尺寸精度高、 表面质量好,但塑性下降,进一步加工困难。
加工硬化(形变强化—强化材料的手段之一)
13
刃位错的运动
晶体通过位错运动产生滑移时,只需要在位错中心的少数原子发生移动, 它们移动的距离远小于一个原子间距,因而所需临界切应力小,这种现象 称作位错的易动性。
滑移过程中会生成许多位错:塑性变形量增加,晶体中位错密
度增大
14
(2) 孪生
孪生是指晶体的一部分 沿一定晶面和晶向相对 于另一部分所发生的切 变,发生在滑移系较少 或滑移受限制情况下。
P
单晶体受力后,外力在任何晶面
上都可分解为正应力(垂直晶 P
面)和切应力(平行晶面) 。
正应力只能引起弹性变形,当超过
P
原子间结合力时,晶体断裂。
只有在切应力的作用下金属晶体 才能产生塑性变形。
塑性变形的实质是:在应力的作 用下,材料内部原子相邻关系已 经发生改变,故外力去除后,原 子到了另一平衡位置,物体将留 下永久变形。
滑移的结果在晶体表面形成台阶,称滑移线,若干条 滑移线组成一个滑移带。
铜拉伸试样表面滑移带
10
4)滑移的同时伴随着晶体的转动。
转动的原因:晶体滑移后使正应力分量和切应力 分量组成了力偶.
11
韧性断口
12
2、滑移的机理
把滑移设想为刚性整体滑动——滑移面上每一个原子都同时移 到另一个平衡位置,外加的切应力必须同时克服滑移面上所有 原子间的结合力。所需理论临界切应力值比实际测量值大3-4个 数量级。 滑移是通过滑移面上位错的运动来实现的。
第三章 金属材料的塑性变形
❖ 3.1 单晶体和多晶体的塑性变形 ❖ 3.2 金属的形变强化 ❖ 3.3 塑性变形金属在加热时
组织和性能的变化 ❖ 3.4 塑性加工性能及其指标
3.1单晶体和多晶体的塑性变形
3.1.1 单晶体的塑性变形 3.1.2 多晶体金属塑性变形的特点
3.1.1 单晶体的
P
塑性变形
21
晶粒大小对塑性变形的影响
晶粒越细,晶界总面积越大,位错障碍越多;需要 协调的具有不同位向的晶粒越多,使金属塑性变形 的抗力越高,另外,一定的变形量由更多晶粒分散 承担,不会造成局部的应力集中,使在断裂前发生 较大的塑性变形,强度和塑性同时增加,金属在断 裂前消耗的功也大,因而其韧性也较好。
22
软 位
一些原来不能启动的滑移系开动,进而使
向
整个晶体的塑性变形协调发展。
晶粒所处的位向为易滑移的位向称为 “软位向” 反之谓“硬位向”。先发 生于软位向晶粒,然后到硬位向。
18
(2)晶粒位向差阻碍滑移
由于各相邻晶粒位向不同,当一个晶粒发生塑性变 形时,为了保持金属的连续性,周围的晶粒若不发 生塑性变形,则必以弹性变形来与之协调。
金属在冷变形时,强度、硬度↑ ,塑性、韧性↓。
加工硬化的原因 塑性变形 → 位错密度增加,相互缠结(亚晶界),运动阻力加大 → 变形抗力↑
4
1、滑移变形的特点 1) 滑移只能在切应力的
作用下发生。
5
2) 滑移常沿晶体中原子密度最大的晶面和晶向发生。 因原子密度最大的晶面和晶向之间原子间距最大, 结合力最弱,产生滑移所需切应力最小。
6
沿其发生滑移的晶面叫做滑移面; 沿其发生滑移的晶向叫做滑移方向; 它们通常是晶体中的密排面和密排方向。 一个滑移面和其上的一个滑移方向构成一个滑移系。 滑移系越多,金属发生滑移的可能性越大,塑性也 越好,其中滑移方向对塑性的贡献比滑移面更大。
P : 载荷 :正应力 :切பைடு நூலகம்力
外
力
分 解
在 晶 面
切 应 力 作 用
锌 单 晶 的 拉 伸
上
下
照
的
的
片
变
形
3
塑性变形的形式:滑移和孪生 金属常以滑移方式发生塑性变形 (1) 滑移
滑移是指当应力超过材料的弹性极限后,晶 体的一部分沿一定的晶面和晶向相对于另一 部分发生滑动位移的现象。在应力去除后, 位移不能恢复,在金属表面留下变形的痕迹
17
3.1.2 多晶体金属塑性变形的特点
单个晶粒变形与单晶体相似,多晶体变形更复杂。
(1)不均匀的塑性变形
多晶体是由众多取向不一的单晶体组成。
在某一单向外力作用下各晶体的滑移面上
的分切应力不同,只有一些达到临界切应
硬
力的滑移系才发生滑移。由于晶体之间的
位 向
相互制约,首先滑移的晶体会引起自身或
相邻晶体的转动,从而使原来启动的滑移 系偏离最大切应力方向,而停止滑移。另
3.2 金属的形变强化
3.2.1 形变强化现象 3.2.2 塑性变形对组织及力学性能影响 3.2.3 塑性变形产生的残余应力
3.2.1 形变强化现象
金属经过冷态下的塑性变形后其性能发生很大的变化 ,最明显的特点是强度随变形程度的增加而大为提高,其 塑性却随之有较大的降低,这种现象称为形变强化,也称 为加工硬化或冷作硬化。
7
6
FCC
金属的塑性:fcc>bcc>chp
8
哪个滑移系先滑移?
当作用于滑移面上滑移方向的切应力分量c(分切应力)大于等于一定的临 界值(临界切应力,决定于原子间结合力),才可进行。
c
Fc A
oscos
取向因子
最先达到c的滑移系先开始滑移 滑移时
9
3) 滑移时,晶体两部分的相对位移量是原子间距的整 数倍。
15
孪生的结果使孪生面两侧的晶体呈镜面对称。
孪生示意图
16
与滑移相比:
孪生使晶格位向发生改变; 所需切应力比滑移大得多,变形速度极快,接近声速; 孪生时相邻原子面的相对位移量小于一个原子间距(滑移
是原子间距的整数倍)。 密排六方晶格金属:滑移系少,常以孪生方式变形。 体心立方晶格金属:只有在低温或冲击作用下才发生孪生变形。 面心立方晶格金属:一般不发生孪生变形。
这种弹性变形便成 为塑性变形晶粒的 变形阻力。
由于晶粒间的这种 相互约束,使得多 晶体金属的塑性变 形抗力提高。
19
(3)晶界的影响
当位错运动到晶界附近时, 受到晶界的阻碍而堆积起 来,称位错的塞积。要使 变形继续进行,则必须增 加外力,从而使金属的变 形抗力提高。
20
晶界对塑性变形的影响
Cu-4.5Al合金晶 界的位错塞积
利用形变强化现象来提高金属材料的强度,在工业上 应用甚广。例如冷拉钢丝。尤其是对于纯金属以及不 能用热处理强化的合金,这种方法格外重要。
冷态压力加工后位错密度大增,晶格畸变很大,电 阻有所增大,抗蚀性降低;冷变形产品尺寸精度高、 表面质量好,但塑性下降,进一步加工困难。
加工硬化(形变强化—强化材料的手段之一)
13
刃位错的运动
晶体通过位错运动产生滑移时,只需要在位错中心的少数原子发生移动, 它们移动的距离远小于一个原子间距,因而所需临界切应力小,这种现象 称作位错的易动性。
滑移过程中会生成许多位错:塑性变形量增加,晶体中位错密
度增大
14
(2) 孪生
孪生是指晶体的一部分 沿一定晶面和晶向相对 于另一部分所发生的切 变,发生在滑移系较少 或滑移受限制情况下。
P
单晶体受力后,外力在任何晶面
上都可分解为正应力(垂直晶 P
面)和切应力(平行晶面) 。
正应力只能引起弹性变形,当超过
P
原子间结合力时,晶体断裂。
只有在切应力的作用下金属晶体 才能产生塑性变形。
塑性变形的实质是:在应力的作 用下,材料内部原子相邻关系已 经发生改变,故外力去除后,原 子到了另一平衡位置,物体将留 下永久变形。
滑移的结果在晶体表面形成台阶,称滑移线,若干条 滑移线组成一个滑移带。
铜拉伸试样表面滑移带
10
4)滑移的同时伴随着晶体的转动。
转动的原因:晶体滑移后使正应力分量和切应力 分量组成了力偶.
11
韧性断口
12
2、滑移的机理
把滑移设想为刚性整体滑动——滑移面上每一个原子都同时移 到另一个平衡位置,外加的切应力必须同时克服滑移面上所有 原子间的结合力。所需理论临界切应力值比实际测量值大3-4个 数量级。 滑移是通过滑移面上位错的运动来实现的。
第三章 金属材料的塑性变形
❖ 3.1 单晶体和多晶体的塑性变形 ❖ 3.2 金属的形变强化 ❖ 3.3 塑性变形金属在加热时
组织和性能的变化 ❖ 3.4 塑性加工性能及其指标
3.1单晶体和多晶体的塑性变形
3.1.1 单晶体的塑性变形 3.1.2 多晶体金属塑性变形的特点
3.1.1 单晶体的
P
塑性变形
21
晶粒大小对塑性变形的影响
晶粒越细,晶界总面积越大,位错障碍越多;需要 协调的具有不同位向的晶粒越多,使金属塑性变形 的抗力越高,另外,一定的变形量由更多晶粒分散 承担,不会造成局部的应力集中,使在断裂前发生 较大的塑性变形,强度和塑性同时增加,金属在断 裂前消耗的功也大,因而其韧性也较好。
22
软 位
一些原来不能启动的滑移系开动,进而使
向
整个晶体的塑性变形协调发展。
晶粒所处的位向为易滑移的位向称为 “软位向” 反之谓“硬位向”。先发 生于软位向晶粒,然后到硬位向。
18
(2)晶粒位向差阻碍滑移
由于各相邻晶粒位向不同,当一个晶粒发生塑性变 形时,为了保持金属的连续性,周围的晶粒若不发 生塑性变形,则必以弹性变形来与之协调。
金属在冷变形时,强度、硬度↑ ,塑性、韧性↓。
加工硬化的原因 塑性变形 → 位错密度增加,相互缠结(亚晶界),运动阻力加大 → 变形抗力↑
4
1、滑移变形的特点 1) 滑移只能在切应力的
作用下发生。
5
2) 滑移常沿晶体中原子密度最大的晶面和晶向发生。 因原子密度最大的晶面和晶向之间原子间距最大, 结合力最弱,产生滑移所需切应力最小。
6
沿其发生滑移的晶面叫做滑移面; 沿其发生滑移的晶向叫做滑移方向; 它们通常是晶体中的密排面和密排方向。 一个滑移面和其上的一个滑移方向构成一个滑移系。 滑移系越多,金属发生滑移的可能性越大,塑性也 越好,其中滑移方向对塑性的贡献比滑移面更大。
P : 载荷 :正应力 :切பைடு நூலகம்力
外
力
分 解
在 晶 面
切 应 力 作 用
锌 单 晶 的 拉 伸
上
下
照
的
的
片
变
形
3
塑性变形的形式:滑移和孪生 金属常以滑移方式发生塑性变形 (1) 滑移
滑移是指当应力超过材料的弹性极限后,晶 体的一部分沿一定的晶面和晶向相对于另一 部分发生滑动位移的现象。在应力去除后, 位移不能恢复,在金属表面留下变形的痕迹
17
3.1.2 多晶体金属塑性变形的特点
单个晶粒变形与单晶体相似,多晶体变形更复杂。
(1)不均匀的塑性变形
多晶体是由众多取向不一的单晶体组成。
在某一单向外力作用下各晶体的滑移面上
的分切应力不同,只有一些达到临界切应
硬
力的滑移系才发生滑移。由于晶体之间的
位 向
相互制约,首先滑移的晶体会引起自身或
相邻晶体的转动,从而使原来启动的滑移 系偏离最大切应力方向,而停止滑移。另
3.2 金属的形变强化
3.2.1 形变强化现象 3.2.2 塑性变形对组织及力学性能影响 3.2.3 塑性变形产生的残余应力
3.2.1 形变强化现象
金属经过冷态下的塑性变形后其性能发生很大的变化 ,最明显的特点是强度随变形程度的增加而大为提高,其 塑性却随之有较大的降低,这种现象称为形变强化,也称 为加工硬化或冷作硬化。
7
6
FCC
金属的塑性:fcc>bcc>chp
8
哪个滑移系先滑移?
当作用于滑移面上滑移方向的切应力分量c(分切应力)大于等于一定的临 界值(临界切应力,决定于原子间结合力),才可进行。
c
Fc A
oscos
取向因子
最先达到c的滑移系先开始滑移 滑移时
9
3) 滑移时,晶体两部分的相对位移量是原子间距的整 数倍。