铝合金表面电化学沉积制备
铝合金阳极氧化电解着色是铝合金表面处理中重要的方法之一
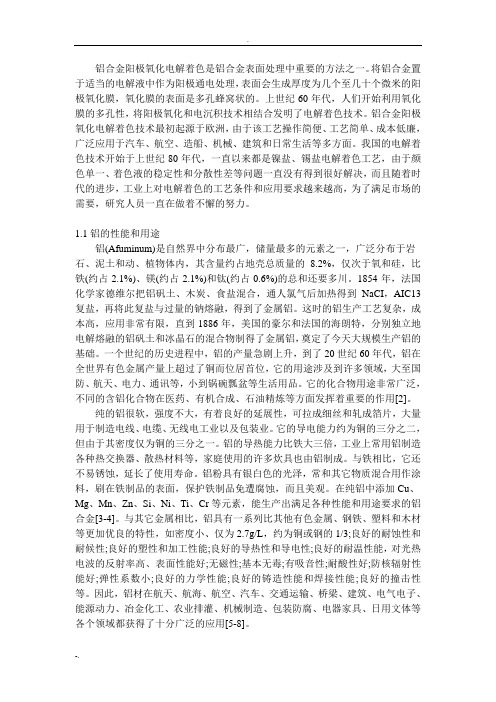
铝合金阳极氧化电解着色是铝合金表面处理中重要的方法之一。
将铝合金置于适当的电解液中作为阳极通电处理,表面会生成厚度为几个至几十个微米的阳极氧化膜,氧化膜的表面是多孔蜂窝状的。
上世纪60年代,人们开始利用氧化膜的多孔性,将阳极氧化和电沉积技术相结合发明了电解着色技术。
铝合金阳极氧化电解着色技术最初起源于欧洲,由于该工艺操作简便、工艺简单、成本低廉,广泛应用于汽车、航空、造船、机械、建筑和日常生活等多方面。
我国的电解着色技术开始于上世纪80年代,一直以来都是镍盐、锡盐电解着色工艺,由于颜色单一、着色液的稳定性和分散性差等问题一直没有得到很好解决,而且随着时代的进步,工业上对电解着色的工艺条件和应用要求越来越高,为了满足市场的需要,研究人员一直在做着不懈的努力。
1.1铝的性能和用途铝(Afuminum)是自然界中分布最广,储量最多的元素之一,广泛分布于岩石、泥土和动、植物体内,其含量约占地壳总质量的8.2%,仅次于氧和硅,比铁(约占2.1%)、镁(约占2.1%)和钛(约占0.6%)的总和还要多川。
1854年,法国化学家德维尔把铝矾土、木炭、食盐混合,通人氯气后加热得到NaCI,AIC13复盐,再将此复盐与过量的钠熔融,得到了金属铝。
这时的铝生产工艺复杂,成本高,应用非常有限,直到1886年,美国的豪尔和法国的海朗特,分别独立地电解熔融的铝矾土和冰晶石的混合物制得了金属铝,奠定了今天大规模生产铝的基础。
一个世纪的历史进程中,铝的产量急剧上升,到了20世纪60年代,铝在全世界有色金属产量上超过了铜而位居首位,它的用途涉及到许多领域,大至国防、航天、电力、通讯等,小到锅碗瓢盆等生活用品。
它的化合物用途非常广泛,不同的含铝化合物在医药、有机合成、石油精炼等方面发挥着重要的作用[2]。
纯的铝很软,强度不大,有着良好的延展性,可拉成细丝和轧成箔片,大量用于制造电线、电缆、无线电工业以及包装业。
它的导电能力约为铜的三分之二,但由于其密度仅为铜的三分之一。
电化学沉积铝
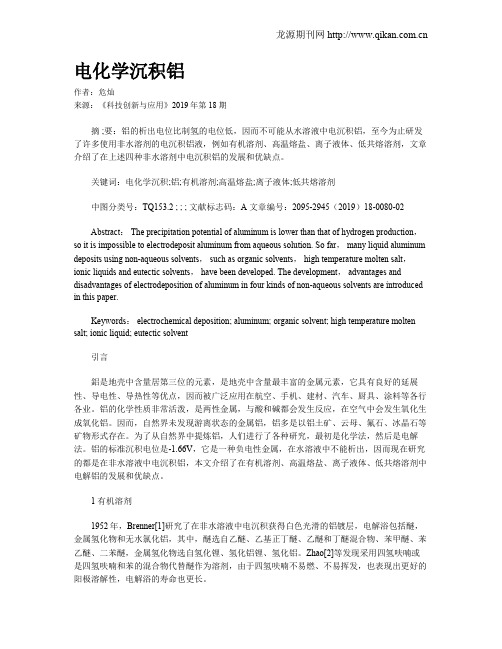
电化学沉积铝作者:危灿来源:《科技创新与应用》2019年第18期摘 ;要:铝的析出电位比制氢的电位低,因而不可能从水溶液中电沉积铝,至今为止研发了许多使用非水溶剂的电沉积铝液,例如有机溶剂、高温熔盐、离子液体、低共熔溶剂,文章介绍了在上述四种非水溶剂中电沉积铝的发展和优缺点。
关键词:电化学沉积;铝;有机溶剂;高温熔盐;离子液体;低共熔溶剂中图分类号:TQ153.2 ; ; ; 文献标志码:A 文章编号:2095-2945(2019)18-0080-02Abstract: The precipitation potential of aluminum is lower than that of hydrogen production,so it is impossible to electrodeposit aluminum from aqueous solution. So far, many liquid aluminum deposits using non-aqueous solvents, such as organic solvents, high temperature molten salt,ionic liquids and eutectic solvents, have been developed. The development, advantages and disadvantages of electrodeposition of aluminum in four kinds of non-aqueous solvents are introduced in this paper.Keywords: electrochemical deposition; aluminum; organic solvent; high temperature molten salt; ionic liquid; eutectic solvent引言鋁是地壳中含量居第三位的元素,是地壳中含量最丰富的金属元素,它具有良好的延展性、导电性、导热性等优点,因而被广泛应用在航空、手机、建材、汽车、厨具、涂料等各行各业。
铝合金电镀工艺流程
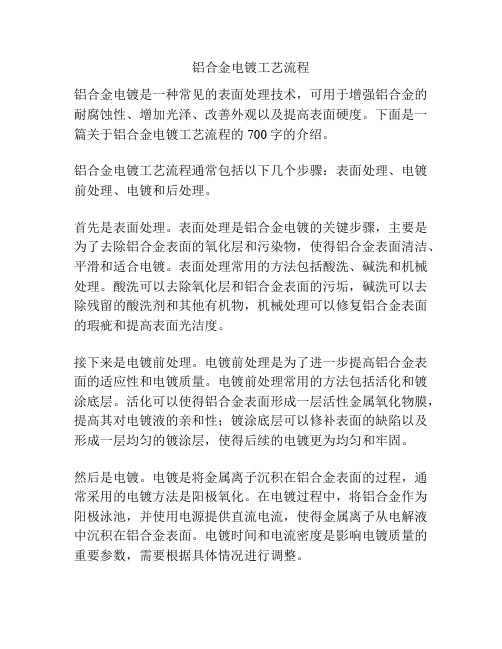
铝合金电镀工艺流程铝合金电镀是一种常见的表面处理技术,可用于增强铝合金的耐腐蚀性、增加光泽、改善外观以及提高表面硬度。
下面是一篇关于铝合金电镀工艺流程的700字的介绍。
铝合金电镀工艺流程通常包括以下几个步骤:表面处理、电镀前处理、电镀和后处理。
首先是表面处理。
表面处理是铝合金电镀的关键步骤,主要是为了去除铝合金表面的氧化层和污染物,使得铝合金表面清洁、平滑和适合电镀。
表面处理常用的方法包括酸洗、碱洗和机械处理。
酸洗可以去除氧化层和铝合金表面的污垢,碱洗可以去除残留的酸洗剂和其他有机物,机械处理可以修复铝合金表面的瑕疵和提高表面光洁度。
接下来是电镀前处理。
电镀前处理是为了进一步提高铝合金表面的适应性和电镀质量。
电镀前处理常用的方法包括活化和镀涂底层。
活化可以使得铝合金表面形成一层活性金属氧化物膜,提高其对电镀液的亲和性;镀涂底层可以修补表面的缺陷以及形成一层均匀的镀涂层,使得后续的电镀更为均匀和牢固。
然后是电镀。
电镀是将金属离子沉积在铝合金表面的过程,通常采用的电镀方法是阳极氧化。
在电镀过程中,将铝合金作为阳极泳池,并使用电源提供直流电流,使得金属离子从电解液中沉积在铝合金表面。
电镀时间和电流密度是影响电镀质量的重要参数,需要根据具体情况进行调整。
最后是后处理。
后处理是在电镀完成后对铝合金进行一系列的处理,以提高电镀层的质量和保护铝合金不受环境影响。
常见的后处理方法包括封孔、涂漆和抛光。
封孔可以降低电镀层的孔隙度和增加其密度,提高防腐蚀性能;涂漆可以保护电镀层不受外界侵蚀和氧化;抛光可以提高电镀层的光泽和平滑度,使其外观更加美观。
总的来说,铝合金电镀是一种常见的表面处理技术,其工艺流程包括表面处理、电镀前处理、电镀和后处理。
通过这一系列步骤的处理,可以使得铝合金表面得到清洁、平滑和具有电镀层的保护,增加其耐腐蚀性和美观度。
在进行铝合金电镀时,需要根据具体情况调整工艺参数,以确保电镀质量和效果。
电沉积有机涂层工艺

电沉积有机涂层工艺
电沉积有机涂层工艺是一种常见的表面处理技术,它可以在金属表面上形成一层有机涂层,以提高金属的耐腐蚀性、耐磨性和美观性。
这种工艺通常用于汽车、航空航天、电子、建筑等领域。
电沉积有机涂层工艺的基本原理是利用电化学反应,在金属表面上沉积一层有机涂层。
这种涂层通常由有机物质和金属离子组成,可以通过改变电解液的成分和电流密度来控制涂层的厚度和性质。
电沉积有机涂层工艺的优点在于可以在金属表面上形成均匀、致密、附着力强的涂层,同时还可以控制涂层的厚度和性质,以满足不同的应用需求。
此外,这种工艺还可以在低温下进行,不会对金属基材造成热损伤。
电沉积有机涂层工艺的应用范围非常广泛。
在汽车行业中,它可以用于制造车身、发动机和底盘等部件,以提高它们的耐腐蚀性和耐磨性。
在航空航天领域中,它可以用于制造飞机、卫星和导弹等部件,以提高它们的耐腐蚀性和抗氧化性。
在电子行业中,它可以用于制造电路板和电子元件,以提高它们的导电性和耐腐蚀性。
在建筑领域中,它可以用于制造钢结构和铝合金门窗等部件,以提高它们的耐腐蚀性和美观性。
电沉积有机涂层工艺是一种非常重要的表面处理技术,它可以为各个领域的金属制品提供优良的保护和装饰效果。
随着科技的不断进
步,这种工艺的应用前景将会越来越广阔。
电泳的工艺流程铝合金电泳

电泳的工艺流程铝合金电泳电泳的工艺流程铝合金电泳首先:电泳涂装(electro-coating)是利用外加电场使悬浮于电泳液中的颜料和树脂等微粒定向迁移并沉积于电极之一的基底表面的涂装方法。
电泳涂装的原理发明于是20世纪30年代末,但开发这一技术并获得工业应用是在1963年以后,电泳涂装是近30年来发展起来的一种特殊涂膜形成方法,是对水性涂料最具有实际意义的施工工艺。
具有水溶性、无毒、易于自动化控制等特点,迅速在汽车、建材、五金、家电等行业得到广泛的应用。
电泳涂装是把工件和对应的电极放入水溶性涂料中,接上电源后,依靠电场所产生的物理化学作用,使涂料中的树脂、颜填料在以被涂物为电极的表面上均匀析出沉积形成不溶于水的漆膜的一种涂装方法。
电泳涂装是一个极为复杂的电化学反应过程,其中至少包括电泳、电沉积、电渗、电解四个过程。
电泳涂装按沉积性能可分为阳极电泳(工件是阳极,涂料是阴离子型)和阴极电泳(工件是阴极,涂料是阳离子型);按电源可分为直流电泳和交流电泳;按工艺方法又有定电压和定电流法。
目前在工业上较为广泛采用的是直流电源定电压法的阳极电泳。
1-经表面处理后的工件;2-电源;3-工件;4-喷水冲洗;5-槽液过滤;6-沉积槽;7-循环泵电泳涂装与其他涂装方法相比较,具有下述特点:(1)采用水溶性涂料,以水为溶解介质,节省了大量有机溶剂,大大降低了大气污染和环境危害,安全卫生,同时避免了火灾的隐患;(2)涂装效率高,涂料损失小,涂料的利用率可达90%,95%;(3)涂膜厚度均匀,附着力强,涂装质量好,工件各个部位如内层、凹陷、焊缝等处都能获得均匀、平滑的漆膜,解决了其他涂装方法对复杂形状工件的涂装难题;(4)生产效率高,施工可实现自动化连续生产,大大提高劳动效率;(5)设备复杂,投资费用高,耗电量大,其烘干固化要求的温度较高,涂料、涂装的管理复杂,施工条件严格,并需进行废水处理;(6)只能采用水溶性涂料,在涂装过程中不能改变颜色,涂料贮存过久稳定性不易控制。
铝及铝合金的电化学氧化
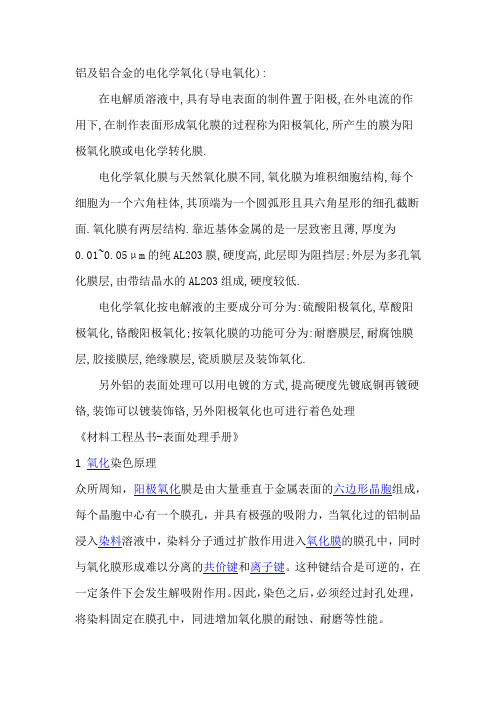
铝及铝合金的电化学氧化(导电氧化):在电解质溶液中,具有导电表面的制件置于阳极,在外电流的作用下,在制作表面形成氧化膜的过程称为阳极氧化,所产生的膜为阳极氧化膜或电化学转化膜.电化学氧化膜与天然氧化膜不同,氧化膜为堆积细胞结构,每个细胞为一个六角柱体,其顶端为一个圆弧形且具六角星形的细孔截断面.氧化膜有两层结构.靠近基体金属的是一层致密且薄,厚度为0.01~0.05μm的纯AL2O3膜,硬度高,此层即为阻挡层;外层为多孔氧化膜层,由带结晶水的AL2O3组成,硬度较低.电化学氧化按电解液的主要成分可分为:硫酸阳极氧化,草酸阳极氧化,铬酸阳极氧化;按氧化膜的功能可分为:耐磨膜层,耐腐蚀膜层,胶接膜层,绝缘膜层,瓷质膜层及装饰氧化.另外铝的表面处理可以用电镀的方式,提高硬度先镀底铜再镀硬铬,装饰可以镀装饰铬,另外阳极氧化也可进行着色处理《材料工程丛书-表面处理手册》1 氧化染色原理众所周知,阳极氧化膜是由大量垂直于金属表面的六边形晶胞组成,每个晶胞中心有一个膜孔,并具有极强的吸附力,当氧化过的铝制品浸入染料溶液中,染料分子通过扩散作用进入氧化膜的膜孔中,同时与氧化膜形成难以分离的共价键和离子键。
这种键结合是可逆的,在一定条件下会发生解吸附作用。
因此,染色之后,必须经过封孔处理,将染料固定在膜孔中,同进增加氧化膜的耐蚀、耐磨等性能。
2 阳极氧化工艺对染色的影响在氧化染色整个流程中,因为氧化工艺原因造成染色不良是比较普遍的。
氧化膜的膜厚和孔隙均匀一致是染色时获得均匀一致颜色的前提和基础,为获得均匀一致的氧化膜,保证足够的循环量,冷却量,保证良好的导电性是举足轻重的,此外就是氧化工艺的稳定性。
硫酸浓度,控制在180—200g/l。
稍高的硫酸浓度可促进氧化膜的溶解反应加快,利于孔隙的扩张,更易于染色;铝离子浓度,控制在5—15 g/l。
铝离子小于5g/l,生成的氧化膜吸附能力降低,影响上色速度,铝离子大于15g/l时,氧化膜的均匀性受到影响,容易出现不规则的膜层。
铝合金表面处理工艺完整版
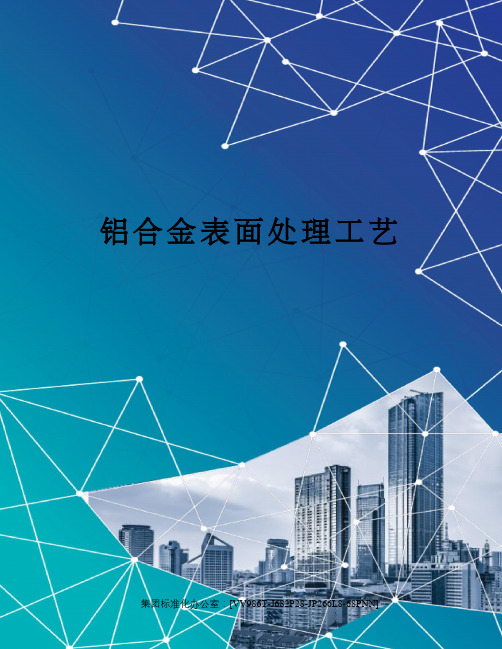
铝合金表面处理工艺集团标准化办公室:[VV986T-J682P28-JP266L8-68PNN]【工艺知识】铝材表面处理工艺大全介绍总则表面处理:它是通过机械和化学的方法处理后,能在产品的表面上形成一层保护机体的保护层。
在自然界中能达到稳定状态,增加机体的抗蚀性和增加产品的美观,从而提升产品的价值。
表面处理种类的选择首先要从使用环境,使用寿命,人为欣赏的角度出发,当然经济价值也是考虑的核心所在。
表面处理的流程包括前处理,成膜,膜后处理。
包装,入库。
出货等工序,其中前处理包括机械处理,化学处理。
机械处理包括喷吵,抛丸,打磨,抛光,打蜡等工序。
机械处理目的使产品表面剔除凹凸不平,补救表面其它外观不良现象。
化学处理使产品表面的油污锈迹去除,并且形成一层能使成膜物质更好的结合或和化成活性金属机体,确保镀层有一个稳定状态,增加保护层的结合力,从而达到保护机体的作用。
铝材表面处理铝材常见的化学处理有铬化,喷漆,电镀,阳极氧化,电泳等工艺。
其中机械处理有拉丝,抛光,喷吵,打磨等工艺。
——————第一节?铬化铬化会便产品表面形成一层化学转化膜,膜层厚度在0.5-4um,这层转化膜吸附性好,主要作为涂装底层。
外观有金黄色,铝本色,绿色等。
这种转化膜导电性能好,是电子产品的最好选项,如手机电池内导电条,磁电设备等。
该膜层适合所有铝及铝合金产品。
但该转化膜质软,不耐磨,因此不利于做产品外部件利用。
铬化工艺流程:脱脂—>铝酸脱—>铬化—>包装—>入库铬化适合于铝及铝合金,镁及镁合金产品。
品质要求:1)颜色均匀,膜层细致,不可有碰伤,刮伤,用手触摸,不能有粗糙,掉灰等现象。
2)膜层厚度0.3-4um。
——————第二节,阳极氧化阳极氧化:可以使产品表面形成一层均匀,致密的氧化层,(Al2O3。
6H2O俗名钢玉)这种膜能使产品的表面硬度达到(200-300HV),如果特种产品可以做硬质阳极氧化,产品表面硬度可达400-1200HV,因而硬质阳极氧化是油缸,传动,不可缺的表面处理工艺。
- 1、下载文档前请自行甄别文档内容的完整性,平台不提供额外的编辑、内容补充、找答案等附加服务。
- 2、"仅部分预览"的文档,不可在线预览部分如存在完整性等问题,可反馈申请退款(可完整预览的文档不适用该条件!)。
- 3、如文档侵犯您的权益,请联系客服反馈,我们会尽快为您处理(人工客服工作时间:9:00-18:30)。
显较宽! 许多文献 [?, ?@ , ?D ] 认为,".—A—". 伸缩 振动峰的宽化现象是由于 ".—A—". 与 ".—A—81 吸收峰间相互重叠引起的! ;;+ /= > ? 为—".A— 的
[ ?, ?@ ] ,说明硅烷膜 伸缩振动峰,对应于—".AJ 基团
中仍然存在未参与缩合的醇羟基! 硅烷膜中的各吸 收峰列 于 表 ?! 从 图 ? 可 看 出,通 过 电 沉 积 工 艺 ’()"硅烷试剂与铝合金基体表面发生了化学键合 作用,生成—".A81 键,而非简单的物理吸附;并 且,通过硅烷间的缩合生成了—".A".—键,即通过 电沉积工艺实现了成膜! 另外,从膜内仍然保留 —".A# —键可以看出,硅烷试剂的水解可能并不完全!
#) 实验部分
# $ #) 硅烷膜的制备 先将铝合金基体抛光至镜面,经除油、水洗后吹干,置于干燥器内备用$ 硅烷溶液由体积比为 &;X %;X < 的无水乙醇、去离子水和硅烷试剂组成$ 充分搅拌后用醋酸 Y 醋酸钠缓冲试剂调至 Z, [ C@ ; , 在<; \ 下水解 CU K 后进行使用$ 为了比较,分别采用传统浸涂法与电沉积法进行硅烷化处理$ 在浸 涂法中,将铝合金电极浸入到硅烷溶液中,浸泡 %) G?Q 后匀速取出,经高压 ’% 气均匀吹干后放入烘箱 中,于 9)) \ 下固化 9; G?Q 后实现成膜$ 与浸涂法唯一不同的是,电沉积时,在电极表面施加一定的 恒定电位 ( 开路电位分别大约为 ] )@ ; , ] )@ ( , ] )@ U , ] 9@ ) 及 ] 9@ % !,均相对于参比电极) ,其余步
收稿日期: %));E);E9<$ 基金项目:国家自然科学基金 ( 批准号: ;);&9)F) ) 和浙江省自然科学基金 ( 批准号:=C)C%F; ) 资助$ 联系人简介:胡吉明 ( 9F&C 年出生) ,男,博士,副教授,从事电化学与金属腐蚀与防护研究$ -EGB?#:HIJGKLM NJL$ IOL$ PQ
(3C6/ !# $()*+,) ./3D- 542 8(9: 5%6;
8SI0QR&.0T SFTU,! V /= > ? ! @ *+* @ *5* @ ;3G ? 3+D 8II.WT=2T& —A#JD —#J@ — —#JD —#AA > #0==2T& 8IX==2&Q./ I&Q2&/H.TW 8IX==2&Q./ I&Q2&/H.TW "X==2&Q./ I&Q2&/H.TW "F1&I 0Y /FQS0ZX1./ F/.U 8SI0QR&.0T SFTU,! V /= > ? ! ? ?5D ? 5@* ;;+ 8II.WT=2T& —".A".—,—".A81 —".A".— —".AJ #0==2T& ".A I&Q2&/H.TW ".A I&Q2&/H.TW ".A I&Q2&/H.TW
#0—,+ ( 12345026) 7 89 — ,+ ( :95;3 14<=;>9)
#0—,—89 ( 0659<=;>9) 7 +’ ,
(%) (’) (?)
#0—,+ 7 #0—,+ #" #0—,—#0 7 +’ , 其中参与缩合反应的硅醇则由硅烷试剂经水解 [ 反应 (? ) ] 得到: #0—,@+? 7 +’ , #" #0—,+ 7 @+? ,+
[ ?? ] ! 以拟合得到的极化电阻值 ( !R ) 量化 +5 =JK,测试温度为 @+ M ! 阻抗数用 $NO.P/Q& 软件进行拟合
试样的耐腐蚀性能! 试样的测试面积约为 @ /=@ !
"# 结果与讨论
" ! !# 硅烷膜的结构 测试了此电位下制得的 ’()" 硅烷膜的反射吸收红外光谱,图 ? 给出了测试结果! @ *+* /= > ? 处
万方数据
??@@
高 等 学 校 化 学 学 报 [ [ [ [ [ [ [ [ [ [ [ [ [ [ [ [ C01! @4 [
骤上同! 电沉积过程采用三电极体系:以饱和甘汞电极 ( "#$ ) 为参比电极,%& 片为对电极,为消除溶 液电阻,在工作电极与参比电极之间使用了鲁金毛细管! 所用的 ’()" 试剂 ( 纯度 *+, ) 均购自武汉大 学有机硅新材料有限公司,试剂未经后续纯化直接使用! 其它试剂均为分析纯! ! ! "# 硅烷膜的表征 采用 -./012& 345 型反射红外 ( 6(789:7) 光谱仪测试基体表面的结构基团信息,入射角为 ;5<! 测 试所用分辨率为 3 /= > ? ,扫描次数为 ?@5 次,以未处理的裸铝合金为背景! 硅烷膜的表面形貌用扫描 电子显微镜 ( "$)) 观察,测试在美国 6$: 公司生产的 ":7:A- 场发射扫描电子显微镜上完成,加速电 压为 @+ BC,照片放大倍率为 ? 555 倍! 膜电极的耐蚀性通过测试其在质量分数为 DE +, -F#1 水溶液 中的电化学阻抗谱 ( $:") 进行评价! $:" 测试在 :)G2 型阻抗测试仪上进行,所用的测试软件为 (HF12I 阻抗测试系统! 所有测试在开路电位下进行,施加 ?5 =C 的交流幅值,频率扫描范围为 ?5 + JK L
-
A A ,+ 离子的促进作用可能是 - &B . C 下制备得到硅烷膜厚度增大且结构更为致密的原因之一) 当 电位继续变负,由于阴极电流显著增大,电极表面的水的另一分解产物 +’ 气的产生量明显增加,并通 过硅烷膜逸出表面,这可能是导致图 ’ ( @) 中膜表面产生多孔的原因) 在实验中发现,当电位达到 - %B D C 时有肉眼可察的 +’ 气产生) 可见,选择合适的沉积电位在硅烷膜电沉积制备中十分重要) 上述结果表明,与传统工艺相比,电沉积制备工艺改变了硅烷膜的组织形貌,进而可能影响膜覆 盖电极的耐蚀性能) % ) %& 硅烷膜的耐蚀性能 通过 $E# 测试对电沉积制备硅烷膜的耐蚀性进行了表征) 图 ? 为经 F"8# 处理后铝合金电极在 G;@3 溶液中的阻抗谱图,图 ? 中比较了不同沉积电位的影响;为了对比,图 ? 同时给出了未经处理的 裸铝合金 ( 空白试样) 及通过传统浸涂工艺得到试样 ( 即在开路电位 ,@H I J - &B K C 下制备所得) 的 测试结果) 从阻抗复平面 [图 ? ( () ] 看出,所有经过硅烷化处理后样品的阻抗数值均大大超过未经处 理的空白样品 ( 图 ? 曲线 !) ,即其耐蚀性得到大幅度的提高;另外,与浸涂法相比,采用阴极电位沉积 所得硅烷膜的耐蚀性能有明显提高,并且随着沉积电位的负移阻抗幅值先增大后减小,在沉积电位 " I - &B . C 时低频容抗弧的半径达到最大,硅烷膜的耐蚀性能最好)
[ ?] >? 处为—#J@ —的不对称伸缩振动峰, 为—A# —不对称伸缩振动峰,对应的基团为—A#J D ! @ *5* /=
@ ;3G /= > ? 则为—#JD 的对称伸缩振动峰! ? 3+D /= > ? 处为—#AA > 基团的伸缩振动峰,说明膜内含有
[ ?] ,其中 ? ?5D /= > ? 峰明 缓冲试剂的成分! ? ?5D L ? 5@* /= > ? 间的吸收峰对应 ".—A—". 的伸缩振动
[ (] [ &] 数进行了优化 $ 9FF< 年,S"" 等 利用该技术首先沉积制备了硅烷膜,其目的是为了提高基体与粘 [ U] 在金和 /83 玻璃上实现了甲基三甲氧基硅烷 ( .8.7) 的电沉积制备,并将 接剂的结合力$ .BQO#IT 等 [ F] 该种成膜技术首次应用于金属的表面防护中 $ 但他们选用的硅烷种类 ( 如四乙氧基硅烷 8-37 及苯
( 9$ 浙江大学化学系,杭州 <9))%& ; %$ 中国科学院金属研究所金属腐蚀与防护国家重点实验室,沈阳 99))9( ) 摘要* 采用电化学技术在 1=9% 铝合金表面沉积制备了十二烷基三甲氧基硅烷 ( >8.7 ) 膜$ 反射吸收红外光 谱表明,>8.7 硅烷试剂与铝合金基体表面发生了化学键合作用,生成—7?30# 键实现成膜$ 通过对膜覆盖 电极在质量分数为 <@ ;A 的 ’B+# 溶液中的电化学阻抗谱 ( -/7) 测试结果表明,与开路电位下相比,采用阴极 电位沉积方法得到硅烷膜的耐蚀性能有明显提高,且存在一个最佳 “ 临界电位” ,在此电位下沉积得到的硅 烷膜具有最高的耐蚀性$ 扫描电镜观察结果表明,在 “ 临界电位” 下制备得到的硅烷膜的结构最致密$ 给出 了硅烷膜覆盖电极的阻抗模型及相关参数的拟合结果$ 关键词* 硅烷化处理;电化学沉积;>8.7;1=9% 铝合金;防腐蚀 中图分类号* 3(C( ;8D9&C@ <(* * * * 文献标识码* 0* * * * 文章编号* )%;9E)&F) ( %))( ) )(E99%9E);
!"#$ %&
% ) ) ( 年( 月
高等学校化学学报 *
* * * * * +,-./+01 2345’01 36 +,/’-7- 4’/!-57/8/-7* * * * * *