Jeffcott转子-轴承系统的非线性动力学特性分析
5自由度磁悬浮轴承—转子系统非线性动力学研究
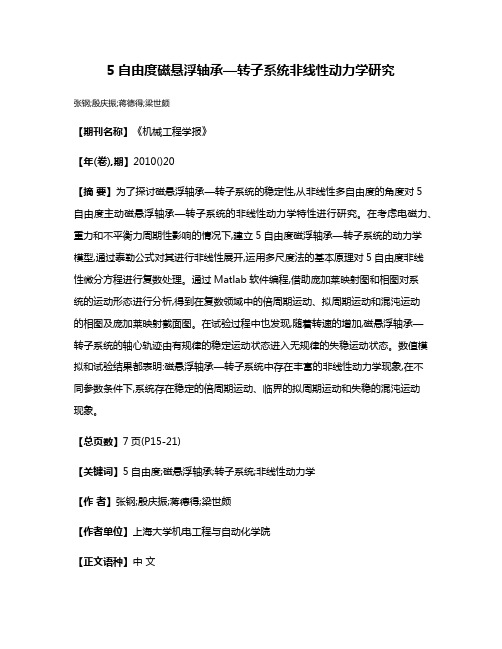
5自由度磁悬浮轴承—转子系统非线性动力学研究张钢;殷庆振;蒋德得;梁世颇【期刊名称】《机械工程学报》【年(卷),期】2010()20【摘要】为了探讨磁悬浮轴承—转子系统的稳定性,从非线性多自由度的角度对5自由度主动磁悬浮轴承—转子系统的非线性动力学特性进行研究。
在考虑电磁力、重力和不平衡力周期性影响的情况下,建立5自由度磁浮轴承—转子系统的动力学模型,通过泰勒公式对其进行非线性展开,运用多尺度法的基本原理对5自由度非线性微分方程进行复数处理。
通过Matlab软件编程,借助庞加莱映射图和相图对系统的运动形态进行分析,得到在复数领域中的倍周期运动、拟周期运动和混沌运动的相图及庞加莱映射截面图。
在试验过程中也发现,随着转速的增加,磁悬浮轴承—转子系统的轴心轨迹由有规律的稳定运动状态进入无规律的失稳运动状态。
数值模拟和试验结果都表明:磁悬浮轴承—转子系统中存在丰富的非线性动力学现象,在不同参数条件下,系统存在稳定的倍周期运动、临界的拟周期运动和失稳的混沌运动现象。
【总页数】7页(P15-21)【关键词】5自由度;磁悬浮轴承;转子系统;非线性动力学【作者】张钢;殷庆振;蒋德得;梁世颇【作者单位】上海大学机电工程与自动化学院【正文语种】中文【中图分类】TH133.3【相关文献】1.主动磁悬浮轴承-转子系统的非线性动力学研究 [J], 张钢;梁世颇;殷庆振;张彪;刘莹;刘汝卫2.大自由度的转子-滑动轴承系统非线性动力学分析(Ⅱ) [J],3.大自由度的转子—滑动轴承系统非线性动力学分析 [J], 李志刚;张直明4.磁悬浮转子-轴承碰摩系统的非线性动力学行为 [J], 徐璐;饶晓波;褚衍东5.大自由度的转子-滑动轴承系统非线性动力学分析(Ⅱ) [J], 李志刚;张直明因版权原因,仅展示原文概要,查看原文内容请购买。
文献翻译-非线性动力学的实验和转子轴承系统支持的行为的数值研究

附录A英文原文Experimental and Numerica Studies on Nonlinear Dynam Behavior of Rotor System Supported by Ball BearingsBall bearings are important mechanical components in high-speed turbomachinery that is liable for severe vibration and noise due to the inherent nonlinearity of ball ing experiments and the numerical approach, the nonlinear dynamic behavior of a flexible rotor supported by ball bearings is investigated in this paper. An experimental ball bearing-rotor test rig is presented in order to investigate the nonlinear dynamic performance of the rotor systems, as the speed is beyond the first synchroresonance frequency. The finite element method and two-degree-of-freedom dynamic model of a ball bearing are employed for modeling the flexible rotor s ystem. The discrete model of a shaft is built with the aid of the finite element technique, and the ball bearing model includes the nonlinear effects of the Hertzian contact force, bearing internal clearance, and so on.The nonlinear unbalance response is observed by experimental and numerical analysis.All of the predicted results are in good agreement with experimental data, thus validating the proposed model. Numerical and experimental results show that the resonance frequency is provoked when the speed is about twice the synchroresonance frequency, while the subharmonic resonance occurs due to the nonlinearity of ball bearings and causes severe vibration and strong noise. The results show that the effect of a ball bearing on the dynamic behavior is noticeable in optimum design and failure diagnosis of high-speed turbomachinery. [DOI: 10.1115/1.4000586]Keywords: ball bearing, rotor, experiment, nonlinear vibrationA.1 IntroductionBall bearings are one of the essential and important components in sophisticated turbomachinery such as rocket turbopumps, aircraft jet engines, and so on. Because of the requirement of acquiring higher performance in the design and operation of ballbearings-rotor systems, accurate predictions of vibration characteristics of the systems, especially in the high rotational speed condition, have become increasingly important.Inherent nonlinearity of ball bearings is due to Hertzian contact forces and the internal clearance between the ball and the ring.Many researchers have devoted themselves to investigating the dynamiccharacteristics associated with ball bearings. Gustafsson et al. [1] studied the vibrations due to the varying compliance of ball bearings. Saito [2] investigated the effect of radial clearance in an unbalanced Jeffcott rotor supported by ball bearings using the numerical harmonic balance technique. Aktürk et al. [2] used a three-degree-of-freedom system to explore the radial and axial vibrations of a rigid shaft supported by a pair of angular contact ball bearings. Liew et al. [4] summarized four different dynamic models of ball bearings, viz., two or five degrees of freedom, with or without ball centrifugal force, which could be applied to determine the vibration response of ball bearing-rotor systems. Bai and Xu [5] presented a general dynamic model to predict dynamic properties of rotor systems supported by ball bearings. De Mul et al. [6] presented a five-degree-of-freedom (5DOF) model for the calculation of the equilibrium and associated load distribution in ball bearings. Mevel and Guyader [7] described different routes to chaos by varying a control parameter. Jang and Jeong [8] proposed an excitation model of ball bearing waviness to investigate the bearing vibration. Then, considering the centrifugal force and gyroscopic moment of ball, they developed an analytical method to calculate the characteristics of the ball bearing under the effect of waviness in Ref. [9]. Tiwari et al. [10,11] employed a two-degree-of-freedom model to analyze the nonlinear behaviors and stability associated with the internal clearance of a ball bearing.Harsha [12-14], taking into account different sources of nonlin-earity, investigated the nonlinear dynamic behavior of ball bearing-rotor systems. Gupta et al. [15] studied the nonlinear dynamic response of an unbalanced horizontal flexible rotor supported by a ball bearing. With the aid of the Floquet theory, Bai et al. [16] investigated the effects of axial preload on nonlinear dynamic characteristics of a flexible rotor supported by angular contact ball bearings. Using the harmonic balance method, Sinou [17]performed a numerical analysis to investigate the nonlinear unbalance response of a flexible rotor supported by ball bearings.In the abovementioned studies, main attention has been paid to the ball bearing modeling and the dynamic properties analysis according to simple bearing-rotor models. With theoretical analysis and experiment, Yamamoto et al. [18] studied a nonlinear forced oscillation at a major critical speed in a rotating shaft,which was supported by ball bearings with angular clearances.Ishida and Yamamoto [19] studied the forced oscillations of a rotating shaft with nonlinear spring characteristics and internal damping. They found that a self-excited oscillation appears in the wide range above the major critical speed. A dynamic model was derived, and experiments are carried out with a laboratory test rig for studying the misaligned effect of misaligned rotor-ball bearing systems in Ref. [20]. Tiwari et al. [21] presented an experimental analysis to study the effect of radial internal clearance of a ball bearing on the bearingstiffness of a rigid horizontal rotor. These experimental results validated theoretical results reported in their literatures [10,11]. Recently, Ishida et al. [22] investigated theoretically and experimentally the nonlinear forced vibrations and parametrically excited vibrations of an asymmetrical shaft supported by ball bearings. Mevel and Guyader [23] used an experimental test bench to confirm the predicted routes to chaos in their previous paper [7]. It is noticeable of lack of experiments on nonlinear dynamic behavior of flexible rotor systems supported by ball bearings. In Ref. [24], the finite element method was used to model a LH2 turbopump rotor system supported by ball bearings. Numerical results show that the subharmonic resonance, as well as synchroresonance, occurs in the start-up process. It is found that the subharmonic resonance is an important dynamic behavior and should be considered in engineering ball bearing-rotor system design. But, the experimental and numerical studies of the subharmonic resonance in ball bearing-rotor systems are very rare.With respect to the above, the present study is intended to cast light on the subharmonic resonance characteristics in ball bearing-rotor systems using experiments and numerical approach. An experiment on an offset-disk rotor supported by ball bearings is carried out, and the finite element method and two-degree-of-freedom model of a ball bearing are employed for modeling this rotor system. The predicted results are compared with the test data, and an investigation is conducted in the nonlinear dynamic behavior of the ball bearings-rotor system.2 Experimental InvestigationAn experimental rig is employed for studying the nonlinear dynamic behavior of ball bearing-rotor systems, as shown in Fig.1. The horizontal shaft is supported by two ball bearings at both ends, and the diskis mounted unsymmetrically. The shaft is coupled to a motor with a flexible coupling. The motor speed is controlled with a feedback controller, which gets the signals from an eddy current probe. Four eddy current probes, whose resolution is 0.5 m, are mounted close to the disk and bearing at the right end in the horizontal and vertical directions, respectively. The displacement signals, obtained with the help of probes, are input into an oscilloscope to describe the motion orbit, and a data acquisition and processing system were used to analyze the effects of ball bearings on the nonlinear dynamic behavior. The data acquisition and processing system utilizes a full period sampling as the data acquisition method. Its sampling rate is 500 kHz maximum, and sample size is 12 bits. The system provides eight channels for vibratory response acquisition and 1 channel for rotational speed acquisition. All channels are simultaneous.The limitation with the presented experimental setup is that the maximum attainable speed is 12,000 rpm. The first critical speed of the rotor system falls in the speed span, as the shaft is flexible and its fist synchroresonance frequency is near 66 Hz (3960rpm).Thus, the dynamic behavior can be studied as the speed is beyond twice the synchroresonance frequency.3 Rotor Dynamic ModelThe bearing-rotor system combines an offset-disk and two ball bearings, which support the rotor at both ends. The sketch map of the system is described in Fig. 2, where the frame oxyz is the inertial frame. The corresponding experiment assembly is shown in Fig. 3.3.1 Equations of Motion . Define ux and uy as the transverse deflections along the ox and oy directions, and x θ and y θ as the corresponding bending angles in the oxz and oyz planes, respectively. When x u 1, y u 1,x 1θ , and y 1θ denote the displacements of the ball bearing center location at the left end, the complex variables 1u and 1θ can be assumed asDenote the displacements of the disk center by 2u and 2θ, and the displacements of the ball bearing center location at the right end by 3u and 3θ. Using the finite element method, the equations of motion for the rotor system can be written as [25,26]where []M , []C , []K , and []G are the mass, damping, stiffness, and gyroscopic matrix of the rotor system, respectively, ω is the rotational speed, and {}u is the displacement vector{}g F and {}u F are the vectors of gravity load and unbalance forces.{}bF is the vector of nonlinear forces associated with ball bearings.3.2 Ball Bearing Forces. A ball bearing is depicted in a frame of axes oxyz in Fig.4. The contact deformation for the j-th rolling element j δis given aswhere i c and o c are the internal radial clearance between the inner,outer race, and rolling elements, respectively, in the direction of contact, and ubx and uby are the relative displacements of the inner and outer race along the x and y directions, respectively. As shown in Fig. 4, the angular location of the j-th rolling element j ϕ can be obtained fromWhere N , c ω, t , and 0ϕ are the number of rolling elements, cage angular velocity, time, and initial angular location, respectively. The cage angular velocity can be expressed as [27]where b D and p D are the ball diameter and bearing pitch diam- eter,respectively. α is the contact angle, which is concerned with the clearance and can be obtained as follows:Referring to Fig. 4, i r and o r are the inner and outer groove radius,respectively.If the contact deformation j δ is positive, the contact force could be calculated using the Hertzian contact theory; otherwise, no load is transmitted. The contact force j Q between the j-th ball and race can be expressed as follows:where b k is the contact stiffness that can be given bywhere bi k and bo k are the load-deflection constants between the inner and outer ball race, respectively[28]. Summing the contact forces for each rolling element, the total bearing reaction fb in a complex form is4 Experimental and Numerical AnalysisAs shown in Fig. 2, the experimental assembly and the finite element model used in the dynamic analysis represent the ball bearing-rotor system with the following geometrical properties:length between the disk center and left end bearing center mm L 1201=; length between the disk center and right end bearing center mm L 1202=; and the shaft diameter mm D 10=. In addition, the elastic shaft material is steel of density 37950m kg =ρ,Young’s modulus GPa E 211=, and Poisson’s ratio 3.0=v . The ball bearings at both ends are the same model, 7200AC, and its parameters are listed in Table 1.The unbalance load is acted wit h the aid of the mass fixed on the disk. By virtue of this act, the mass eccentricity of the disk can be definitely ascertained. As the mass eccentricity of the disk is 0.032 mm, the vibratory response at different rotational speed is determined via a numerical integration and Newton –Raphson iterations of the nonlinear differential equation (2). Note that the clearances used to simulate the bearings are measured ones. The horizontal and vertical displacements signals near the disk are acquired at different times, along with the increased rotational speed. Thus, the amplitudes of vibration at different speeds are determined according to the test data, and overall amplitudes are illustrated in Fig. 5, as the rotor system is run from 2000=ω rpm to 10,000 rpm. The prediction results compared with experimental data are shown in Fig. 5. It can be found that all of the predicted results are in good agreement with experimental data, thus validating the proposed model. The first predicted resonance peak—the so called forward critical speed in linear theory,located at3960=ω rpm, matches the experimental date near 3960=ω rpm quite well. Moreover, the other amplitude peak appearing in the rotational speedrange7700=ω rpm to 8100 rpm can be found in both experimental and numerical analysis results.The corresponding frequency value of this peak is just the frequency doubling of the system critical speed.The Floquet theory can be used for analyzing the stability and topological properties of the periodic solution of the ball bearingrotor system. If the gained Floquet multipliers are less than unity,the periodic solution of the system is stable. If at least one Floquet multiplier exists with the absolute value higher than unity, the periodic solution is unstable and the topological properties of response alter into nonperiodic motion [29]. The leading Floquet multipliers and its absolute value at 7600=ω rpm, 8029 rpm, and 8200 rpm are shown in Table 2. It is found that the leading Floquet multiplier of the system remains in the unit circle, which indicates a synchronous response, as the rotational speed is less than 7700 rpm. Stability analysis shows that the imaginary part of the two leading Floquet multipliers move in opposite directions along the real axis near 7700=ω rpm. When the speed exceeded 7700=ω rpm, the leading Floquet multiplier crosses the unit circle through -1, as shown in Table 2. The periodic solution loses stability and undergoes a period-doubling bifurcation to a period-2 response, which indicates that a subharmonicresonance occurs. The subharmonic resonance keeps on from 7700=ω rpm to 8100 rpm. At 8100=ω rpm, the leading Floquet multiplier moves inside the unit circle through -1. Imply that the subharmonic resonance vanishes and the synchronous response returns. The synchronous response then continues to exist forspeeds above 8100=ω rpm.The waterfall map of frequency spectrums comparisons for prediction and experiment results are illustrated in Fig. 6. It can be found that agreement between the prediction and the experimental data is remarkable. The frequency component 66.9 Hz, near the forward resonance frequency, emerges and its amplitude rises significant when the rotational speed is near 8029 rpm. It is shown that the resonance frequency is provoked when the speed is about twice the critical speed of the ball bearing-rotor system, and the subharmonic resonance occurs. The experimental and numerical analysis indicate that the representative nonlinear behavior and the subharmonic resonance arise from the nonlinearity of ball bearings, Hertzian contact forces, and internal clearance.The orbit and frequency spectrum at 8029=ω rpm are plotted in Fig. 7. Not only the prediction orbit but also the experiment results imply that the response is a period-2 motion, which is illustrated in Fig. 7(a). The predicted frequency components, consisting of 8.133=ω Hz (8029 rpm) and 9.662=ω Hz (4014rpm), coincide with experimental data. It indicates that the periodic response loses stability through a period-doubling bifurcation to a period-2 response. Thus, the subharmonic resonance occurs due to the effects of ball bearings. It can cause severe vibration and strong noise. Moreover, the subharmonic resonance could couple with other destabilizing effects on engineering rotor systems such as Alford forces, internal damping, and so on, and induce the rotor to lose stability and damage.5 ConclusionsAn experimental rig is employed to investigate the nonlinear dynamic behavior of ball bearing-rotor systems. The corresponding dynamic model is established wi th the finite element method and 2DOF dynamic model of a ball bearing, which includes the nonlinear effects of the Hertzian contact force and bearing internal clearance. All of the predicted results are in good agreement with experimental data, thus validating the proposed model. Numerical and experimental results show that the resonance frequency is provoked, and the subharmonic resonance occurs due to the nonlinearity of ball bearings when the speed is about twice the synchroresonance frequency. The subharmonic resonance cannot only cause severe vibration and strong noise, but also induce the rotor to lose stability and damage, once coupled with other destabilizing effects on high-speed turbomachinery such as Alford forces, internal damping, and so on. It is found that the effect of the Hertzian contact forces could also induce a subharmonic resonance, even if the internal clearance was not present. But, the response amplitude and subharmonic component of the rotor system without internal clearance are less than that with both Hertzian contact forces and internal clearance. Otherwise, the clearance may be unavoidable under high-speed operations, where the bearings are axially preloaded since the effect of unbalanced load is significant at high speed. Thus, the nonlinearity of ball bearings,Hertzian contact forces, and internal clearance should be taken into account in ball bearing-rotor system design and failure diagnosis.AcknowledgmentThe authors would like to acknowledgment the support of the National Natural Science Foundation of China (Grant No.10902080) and Natural Science Foundation of Shaanxi Province(Grant Nos. SJ08A19 and 2009JQ1008).References[1] Gutafsson, O., and Tallian, T., 1963, “Resear ch Report on Study of the Vibration Characteristics of Bearings,” SKF Ind. Inc. Technical Report No.AL631023.[2] Saito, S., 1985, “Calculation of Non-Linear Unbalance Response of Horizontal Jeffcott Rotors Supported by Ball Bearings With Radial Clearances,” ASME J.Vib., Acou st., Stress, Reliab. Des., 107(4), pp. 416–420.[3] Aktürk, N., Uneeb, M., and Gohar, R., 1997, “The Effects of Number of Balls and Preload on Vibrations Associated With Ball Bearings,” ASME J. Tribol.,119, pp. 747–753.[4] Liew, A., Feng, N., and Hahn, E., 2002, “Transient Rotordynamic Modeling of Rolling Element Bearing Systems,” ASME J. Eng. Gas Turbines Power,124(4), pp. 984–991.[5] Bai, C. Q., and Xu, Q. Y., 2006, “Dynamic Model of Ball Bearing With Internal Clearance and Waviness,” J. Sound Vib., 294(1-2), pp. 23–48.[6] De Mul, J. M., Vree, J. M., and Maas, D. A., 1989, “Equilibrium and Associated Load Distribution in Ball and Roller Bearings Loaded in Five Degrees of Freedom While Neglecting Friction—Part I: General Theory and Application to Ball Be arings,” ASME J. Tribol., 111, pp. 142–148.[7] Mevel, B., and Guyader, J. L., 1993, “Routes to Chaos in Ball Bearings,” J.Sound Vib., 162, pp. 471–487.[8] Jang, G. H., and Jeong, S. W., 2002, “Nonlinear Excitation Model of Ball Bearing Waviness in a Rigid Rotor Supported by Two or More Ball Bearings Considering Five Degrees of Freedom,” ASME J. Tribol., 124, pp. 82–90.[9] Jang, G. H., and Jeong, S. W., 2003, “Analysis of a Ball Bearing With Waviness Considering the Centrifugal Force and Gyroscopic Moment of the Ball,”ASME J. Tribol., 125, pp. 487–498.[10] Tiwari, M., Gupta, K., and Prakash, O., 2000, “Effect of Radial Internal Clearance of a Ball Bearing on the Dynamics of a Balanced Horizontal Rotor,” J.Sound Vib., 238(5), pp. 723–756.[11] Tiwari, M., Gupta, K., and Prakash, O., 2000, “Dynamic Response of an Unbalanced Rotor Supported on Ball Bearings,” J. Sound Vib., 238(5), pp.757–779.[12] Harsha, S. P., 2005, “Non-Linear Dynamic Response of a Balanced Rotor Supported on Rolling Element Bearings,” Me ch. Syst. Signal Process., 19(3),pp. 551–578.[13] Harsha, S. P., 2006, “Rolling Bearing Vibrations—The Effects of Surface Waviness and Radial Internal Clearance,” Int. J. Computational Methods in Eng Sci. and Mech., 7(2), pp. 91–111.[14] Harsha, S. P., 2006, “Nonlinear Dynamic Analysis of a High-Speed Rotor Supported by Rolling Element Bearings,” J. Sound Vib., 290(1–2), pp. 65–100.[15] Gupta, T. C., Gupta, K., and Sehqal, D. K., 2008, “Nonlinear Vibration Analysis of an Unbalanced Flexible Rotor Supported by Ball Bearings With Radial Internal Clearance,” Proceedings of the ASME Turbo Expo, Vol. 5, pp. 1289–1298.[16] Bai, C. Q., Zhang, H. Y., and Xu, Q. Y., 2008, “Effects of Axial Preload of Ball Bearing on theNonlinear Dynamic Characteristics of a Rotor-Bearing System,” Nonlinear Dyn., 53(3), pp. 173–190. [17] Sinou, J. J., 2009, “Non-Linear Dynamics and Contacts of an Unbalanced Flexible Rotor Supported on Ball Bearings,” Mech. Mach. Theory, 44(9), pp.1713–1732.[18] Yamamoto, T., Ishida, Y., and Ikeda, T., 1984, “Vibrations of a Rotating Shaft With Rotating Nonlinear Restoring Forces at the Major Critical Speed,” Bull.JSME, 27(230), pp. 1728–1736.[19] Ishida, Y., and Yamamoto, T., 1993, “Forced Oscillations of a Rotating Shaft With Nonlinear Spring Characteristics and Internal Damping (1/2 Order Subharmonic Oscillations and Entrainment),” Nonlinear Dyn., 4(5), pp. 413–431.[20] Lee, Y. S., and Lee, C. W., 1999, “Modeling and Vibration Analysis of Misaligned Rotor-Ball Bearing Systems,” J. Sound Vib., 224(1), pp. 17–32.[21] Tiwari, M., Gupta, K., and Prakash, O., 2002, “Experimental Study of a Rotor Supported by Deep Groove Ball Bearing,” Int. J. Rotating Mach., 8(4), pp.243–258.[22] Ishida, Y., Liu, J., Inoue, T., and Suzuki, A., 2008, “Vibrations of an Asymmetrical Shaft With Gravity and Nonlinear Spring Characteristics (IsolatedResonances and Internal Resonances),” ASME J. Vib. Acoust., 130(4),p.041004.[23] Mevel, B., and Guyader, J. L., 2008, “Experiments on Routes to Chaos in Ball Bearings,” J. S ound Vib., 318, pp. 549–564.[24] Bai, C. Q., Xu, Q. Y., and Zhang, X. L., 2006, “Dynamic Properties Analysis of Ball Bearings—Liquid Hydrogen Turbopump Used in Rocket Engine,”ACTA Aeronaut. Astronaut. Sinica, 27(2), pp. 258–261. [25] Nelson, H., 1980, “A Finite Rotating Shaft Element Using Timoshenko Beam Theory,” ASME J. Mech. Des., 102(4), pp. 793–803.[26] Zhang, W., 1999, Basis of Rotordynamic Theory, Science Press, Beijing,China, Chap. 3.[27] Harris, T. A., 1984, Rolling Bearing Analysis, 2nd ed., Wiley, New York.[28] Aktürk, N., 1993, “Dynamics of a Rigid Shaft Supported by Angular Contact Ball Bearings,” Ph.D. thesis, Imperial College of Science, Technology and Medicine, London, UK.[29] Zhou, J. Q., and Zhu, Y. Y., 1998, Nonlinear Vibrations, Xi’an Jioatong University Press, Xi’an, China.附录B英文翻译非线性动力学的实验和转子轴承系统支持的行为的数值研究深沟球轴承在高速流体机械部件承担严重的振动和噪声的固有的非线性是很重要的。
转子—轴承系统的非线性动力学的研究
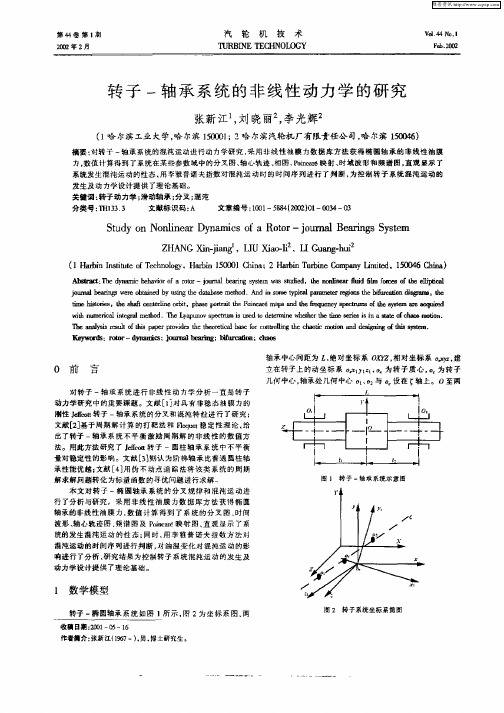
也 : oo —d mte; 0l I el; I∞6 ; h o rtr 3 is jI m Ⅱ ] hg 埘 I m cas  ̄ r
0 前
言
轴承 中心间距为 , 绝对 坐标 系 O Y 相 对坐标 系 D , X Z. 建 立在 ̄-  ̄的动坐 标 系 _ 1【 为 转子 质心 . 为转 子 y - 1 , Y 几何 中心 , 轴承处几何 中心 D 、2 1 D 与 设在 轴 上 0至两
T eaa h Il rslo ts l蛐 eut h f i №
poie h ho ta bs o otln h ho c rv st eri l a d et ec ef cn oi ecat r r lgt i
0 mdd嘲 l o t s yt I a e fi s m. l fs e
( 哈 尔滨工业大学, 尔滨 100 ; 哈 尔滨汽轮机厂有限责任公 司, 尔滨 1 06 1 哈 51l 2 3 哈 5 4) o
摘要 : 对转 子 一轴 承系统的混 沌运动进行动 力学研 究 , 用非线性 油膜 力数据 库方法 获得椭 圆轴承 的非线性 油膜 采 力. 数值 计算得到 了系统在某些参数域 中的分叉图 、 轴心轨迹 、 相图 、o er P i a ̄映射、 n 时域 波形和频 谱图 , 直观 显示 了
对 转子 一轴 承系统 进行 非线 性动 力学分 析一直是 转子
动力学 研究 中的重要课题 。文献 [ 1 对具 有非稳态 油膜力的 刖性 J et转子 一轴承系统 的分 叉和 混沌特 性进行 了研究 ; dr t o
文献[3 2基于周期 解计算 的打靶法 和 F qe稳定 性理论 , l ut o 给
维普资讯
第 4卷 第 1 4 期
机床主轴_滚动轴承系统非线性动力学分析

振 动 与 冲 击第27卷第9期JOURNAL OF V I B RATI O N AND SHOCKVol .27No .92008 机床主轴2滚动轴承系统非线性动力学分析基金项目:国家重点基础研究发展计划“973”项目(2005CB724101)和国家自然科学基金项目(10702040)资助收稿日期:2007-12-14 修改稿收到日期:2008-02-01第一作者张伟刚男,硕士生,1981年生张伟刚, 高尚晗, 龙新华, 孟 光(上海交通大学机械系统与振动国家重点实验室,上海 200240) 摘 要:通过对机床主轴2滚动轴承系统的研究,建立了一个基于Hertz 接触力模型的6自由度系统动力学微分方程,初步探讨在非平衡力作用下,具有负游隙的机床主轴-滚动轴承系统的非线性动态特性和稳定性。
结果表明,由于游隙和变刚度的影响,随控制参数频数比的变化,系统将出现失稳和复杂的非线性现象;通过对比正、负游隙下的系统响应,可得到负游隙有助于提高机床主轴-滚动轴承系统稳定性的结论,该结论与其他学者[10]实验所证明的轴承预紧有助于提高主轴-轴承系统的固有频率,进而提高系统稳定性的结论相吻合。
关键词:滚动轴承;非线性动力学;游隙;稳定性中图分类号:O322;TH133 文献标识码:A 现代制造业对高速、高精度的要求使得我们有必要对机床主轴-轴承系统的非线性动态特性进行深入的分析和研究。
而轴承滚子和轴承内、外圈之间的非线性接触力是机床主轴-轴承系统振动响应的主要非线性因素。
为此,众多研究者在该非线性接触力对主轴-轴承系统动态特性的影响方面展开了广泛的研究。
Ya ma mot o [1]通过研究滚动轴承游隙对Jeffcott 转子振动特性的影响,发现其振动幅度会随着轴承游隙的增加而降低;在此工作基础上,Ti w ari 等[2-5]研究了轴承游隙及变刚度对非平衡Jeffcott 转子非线性动态特性的影响;Sopanen 和M ikkola [6,7]对转子-轴承系统建立了一个6自由度的力学模型,通过对该系统动力学模型的研究,分析游隙对系统固有频率和振动响应的影响;在以上的研究中,转速皆假定为常数,L i ouli os和Ant oniadis [8]研究变转速对转子-轴承系统动态特性的影响,结果表明:即使转子转速发生很小的波动,也可能导致系统动态特性发生很大变化。
含轴承内环间隙的转子非线性动力学建模
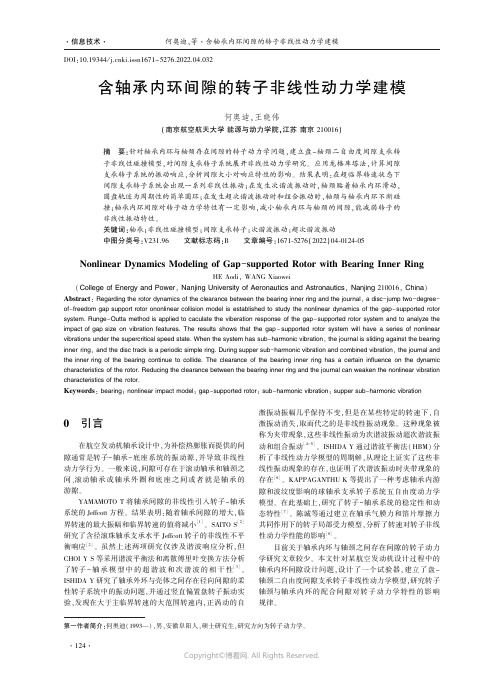
将内环间隙配合转子系统简化为盘-轴颈二自由度
(2) 得到:
k s1 =
间隙支承转子非线性碰撞模型ꎬ简化准则为:保留右端轴
B
(2)
a
= k s1
k s2 =
2
l
ab
式中:E s 是转子的弹性模量ꎻI s 是转子横截面积的惯性矩ꎮ
f0
D
a2 b2
3E s I s
颈的质量ꎬ忽略轴的质量ꎬ只考虑轴的刚度ꎮ 简化后的内
MATLAB 中的 ODE45 求解器求解ꎬ单盘转子系统参数如
表 1 所示ꎮ
表 1 单盘转子系统参数
颈轨迹离散点ꎮ
因为在动力学方程 中 很 难 表 述 图 4 所 示 的 碰 撞 模
转轴长度 l / m
转轴直径 / m
盘直径 / m
0.9
0.016
0.48
盘距左端距离 a / m
泊松比
密度 / (kg / m )
系统的 Jeffcott 方程ꎮ 结果表明:随着轴承间隙的增大ꎬ临
界转速的最大振幅和临界转速的值将减小
[1]
ꎮ SAITO S
[2]
研究了含径滚珠轴承支承水平 Jeffcott 转子的非线性不平
衡响应
[2]
ꎮ 虽然上述两项研究仅涉及谐波响应分析ꎬ但
动和组合振动 [4-5] ꎮ ISHIDA Y 通过谐波平衡法( HBM) 分
合ꎬ为了研究轴承内环间隙对转子动力学的影响ꎬ设计了
如图 1 所示的偏执单盘转子系统ꎮ 在转子右端支承处ꎬ采
用了含轴承内环间隙的装配方式ꎬ右端轴颈可以在间隙中
移动ꎮ
在非线性动力学建模过程中ꎬ引入如下假设:1) 轴承
无游隙ꎬ轴承外环和轴承座无间隙ꎬ轴承内环支承在弹性
有限宽轴承-转子系统碰摩的非线性动力学特性

( 2 )
在无量纲化 过程 中的 为油膜平均间隙,R为轴承半径, 为轴径长度 ,S o 为S mmefl数 , re d
叩 为润滑 动力粘度 , 为无量 纲转速 ,p 为无 量纲质量偏 心 , 为反映 了润滑油粘度 、轴承间隙 及长径 比等多种 因素影 响的一个综合参数。
动稳定 性的影响 。文 【 中介绍 了一种通过 变分原理得 到的有 限宽轴承 油膜力公式 ,此 方法具 7 1
有 较 深 的 数 学基 础 。
2 有 限 宽轴 承一 子 系 统 碰 摩 的非 线 性 动 力 学 模 型 转
对 于图 1 所示 的转子一 轴承结构 ,运用变分原理并经 过推 导得到的油膜力为
非 线性 动 力 学 现 象 ,为 解 决 实 际 工 程系 统 中遇 到 的 问题 ,如 故 障 诊 断 等 提 供 了一 定 的理 论 依 据 。 关键 词 :有 限 宽 轴 承一 子 :碰 摩 油 膜 力 :变 分 方 法 ; 非 线 性 动 力 学 转 中 图 分类 号 : 2 ; 03 2 TH13 3 文 献标 识 码 :A
m蕾= me O £ Q C S +厶 , m = me i £ 一mg Q Q s Q+ n
() 1
为使结果不受量纲影 响,从而具有更为普遍 的意义 ,按文【将方程() 8 ] 1 无量纲化 ,可 得 方 程() 1的无量纲形式为
:
鲁+c, : p . p 鲁+s 一. 。 s i 1 n 0
£ 为径 向位移, 和£ 分别为径 向速度和周 向速度 , 为油膜厚度 ,A 为长径 比,西 为姿态角 。
图1 中D为轴承 中心 ,0 为轴 径 中心 ,m为转子质量 之半 ,e 为转 子质量偏 心 ,Q 为轴径 的
弹性转子-轴承系统的非线性动力学研究

(2)该类转子一轴承系统在某一转速时在一定
偏心量作用下,具有发生不利于系统运行的分叉和 概周期运动的可能性,在该类转子设计和运行时要 使工作转速避开该类区域。
作者简介:张新江.1967年生.哈尔演工业大学能源学院动力机 械及工程专业博士研究生。
收稿日期:1999—12—24
Analysis of nonlinear dynamics to
疋/a圻=B/d为无量纲非线性油膜力分量,p为
润滑油枯度,G=gl-/∞2为无量纲外载荷,r=oJr 为无量纲时间,e为偏心量,c为轴承半径间隙,L为
轴承长度,置为轴承半径,d=篙警(詈)2(去)2为
口3=詈,正坼由文献[6]确定。
嘁ld修正数,m-・=里詈二旦,nI_0,。:=O生72,
个具有非线性油膜力的弹性转子一轴承系统稳态
I”一:小:(”柚+去正
卜一嚣九-言(,--y2)+知~。
I*:一盖t:一2。a。2(x:一t)+Pcosr
【舻一薏,:一警(y:-y1)叩inr—G
其中,托=Xz/c、yl=Yi/c为无量纲坐标,五=
值方法,对具有非线性油膜力的Jeffcott转子一轴承
系统进行了分叉研究;G.Adiletta[2,31从理论和试验 两方面进行了较为详细的论述;S.Boel曲I卅则认为阶 梯轴承比普通圆柱轴承性能优越;刘恒【51用伪不动 点追踪法将该系统的周期解求解问题转化为标量函 数的寻优问题进行求解。本文的主要工作是研究一
庞加莱映射方法对其动力学特性随莱一参数变化时稳定性的改变进行了分析,计算结果表明,系统 具有发生倍周期分又及概周期运动的可能。用数值方法得到系统在某些参数域中的分又图,直观显 示了系蜿在某盛参数城中的运行状态。
机动飞行器内碰摩转子的非线性动力学研究
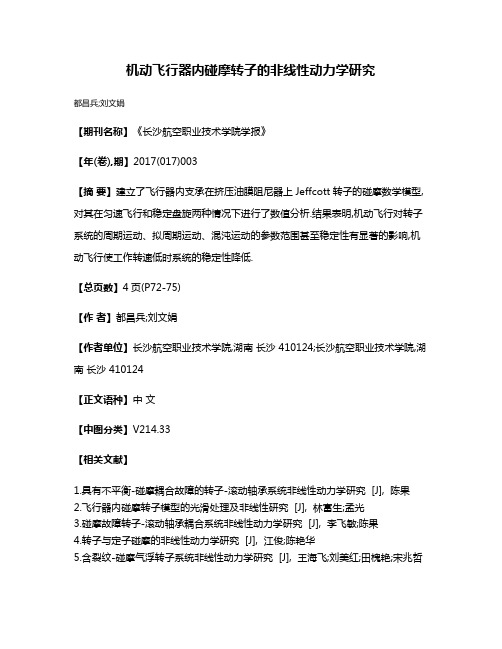
机动飞行器内碰摩转子的非线性动力学研究
都昌兵;刘文娟
【期刊名称】《长沙航空职业技术学院学报》
【年(卷),期】2017(017)003
【摘要】建立了飞行器内支承在挤压油膜阻尼器上Jeffcott转子的碰摩数学模型,对其在匀速飞行和稳定盘旋两种情况下进行了数值分析.结果表明,机动飞行对转子系统的周期运动、拟周期运动、混沌运动的参数范围甚至稳定性有显著的影响,机动飞行使工作转速低时系统的稳定性降低.
【总页数】4页(P72-75)
【作者】都昌兵;刘文娟
【作者单位】长沙航空职业技术学院,湖南长沙 410124;长沙航空职业技术学院,湖南长沙 410124
【正文语种】中文
【中图分类】V214.33
【相关文献】
1.具有不平衡-碰摩耦合故障的转子-滚动轴承系统非线性动力学研究 [J], 陈果
2.飞行器内碰摩转子模型的光滑处理及非线性研究 [J], 林富生;孟光
3.碰摩故障转子-滚动轴承耦合系统非线性动力学研究 [J], 李飞敏;陈果
4.转子与定子碰摩的非线性动力学研究 [J], 江俊;陈艳华
5.含裂纹-碰摩气浮转子系统非线性动力学研究 [J], 王海飞;刘美红;田槐艳;宋兆哲
因版权原因,仅展示原文概要,查看原文内容请购买。