车身侧发动机罩铰链结构设计优化
车身后减振器安装点动刚度优化设计

摘要:某公司上市车型在研发过程中,将后轮减振器铝骨架更改为铁骨架,导致车身后减振器安装点动刚度下降低于目标值。
文章针对这一问题的分析解决过程进行了详细描述,列举出解决问题过程中的3个方案,3个方案均对后轮罩结构进行合理的优化,其中方案1与方案2对整体动刚度的提高效果微弱,方案3通过增加结构整体连接性、增大零件尺寸及对零件增加侧翻边等方法提高了该安装点的动刚度,对后续车型的该处结构设计具有指导意义。
关键词:安装点;动刚度;后轮罩;结构优化Optimization of Dynamic Stiffness for Body Mounting Point of Rear Shock AbsorberAbstract : In the research and development process of a company's listed vehicle, due to changing the material of the rear wheel shock absorber framework, the dynamic stiffness of the mounting point of the body rear shock absorber decreased, whichwas lower than the target value. In this paper, the analysis and solution process of this problem is described in detail, and three solutions are listed in the process of solving the problem. The three solutions all optimize the structure of the rear wheel housingreasonably. Among them, the improvement of the overall dynamic stiffness of scheme 1 and scheme 2 is weak. The scheme 3 improves the dynamic stiffness of the mounting point by increasing the overall connectivity of the structure, increasing the size of the parts and increasing the side flanging of the parts, which has a guiding significance for the structural design of thesubsequent models.Key words : Mounting point; Dynamic stiffness; Rear wheel housing; Structural optimization动刚度要求在动载荷作用下构件应有足够抵抗变 形的能力。
汽车白车身结构设计规范
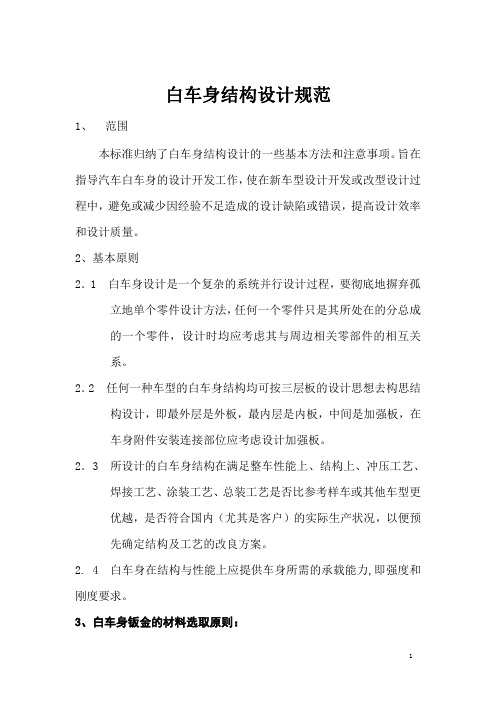
白车身结构设计规范1、范围本标准归纳了白车身结构设计的一些基本方法和注意事项。
旨在指导汽车白车身的设计开发工作,使在新车型设计开发或改型设计过程中,避免或减少因经验不足造成的设计缺陷或错误,提高设计效率和设计质量。
2、基本原则2.1白车身设计是一个复杂的系统并行设计过程,要彻底地摒弃孤立地单个零件设计方法,任何一个零件只是其所处在的分总成的一个零件,设计时均应考虑其与周边相关零部件的相互关系。
2.2任何一种车型的白车身结构均可按三层板的设计思想去构思结构设计,即最外层是外板,最内层是内板,中间是加强板,在车身附件安装连接部位应考虑设计加强板。
2.3所设计的白车身结构在满足整车性能上、结构上、冲压工艺、焊接工艺、涂装工艺、总装工艺是否比参考样车或其他车型更优越,是否符合国内(尤其是客户)的实际生产状况,以便预先确定结构及工艺的改良方案。
2.4白车身在结构与性能上应提供车身所需的承载能力,即强度和刚度要求。
3、白车身钣金的材料选取原则:3.1汽车覆盖件所用材料一般是冷轧钢板。
3.2按国家标准选取钣金材料3.3钣金按表面质量分有I,II两级:I级质量最好,适用于外板;II 级次之,适用于内板与加强板3.4钣金按冲压拉延等级分有P,S,Z,F,HF,ZF六级:P:普通拉深级,适用于拉延深度浅的零件;S:深拉深级,适用于拉延深度一般的零件;Z:最深拉深级,适用于拉延深度较深的零件;F:复杂拉深级,适用于结构复杂且拉延深度较深的零件;HF:很复杂拉深级,适用于结构较复杂且拉延深度较深的零件;ZF:最复杂拉深级,适用于结构非常复杂且拉延深度较深的零件;3.5钣金按强度等级分有:普通强度,高强度,超高强度;3.6按宝钢标准选取钣金材料3.6.1钢板及钢带按用途分:牌号用途DC01(St12)一般用(水箱外壳,制桶等)DC03(St13)冲压用(汽车门、窗、白车身件等)DC04(St14、St15)深冲用(汽车门、窗、白车身件等)DC05(BSC2)特深冲用(汽车门、窗、白车身件等)DC06(St16、St14-T、BSC3)超深冲用(汽车门、窗、白车身件等)3.6.2钢板及钢带按表面质量分:级别代号较高级的精整表面FB(O3)高级的精整表面FC(O4)超高级的精整表面FD(O5)3.6.3钢板及钢带按表面结构分:表面结构代号麻面D光亮表面B3.6.4使用部位及选用牌号标记使用部位牌号标记备注1外覆盖件DC04-XX-FD Q/BQB403—2003DC04-XX-FB Q/BQB403—2003 2内板大件(复杂、深)3内板大件(一般)DC03-XX-FB Q/BQB403—20034其它结构件DC03-XX-FB Q/BQB403—20033.6.5牌号标记说明Q/BQB403——2003材料厚度企业标准号此牌号为冷连轧、深冲用、高级精表面质量的低碳汽车用钢板。
浅析汽车开闭件结构设计
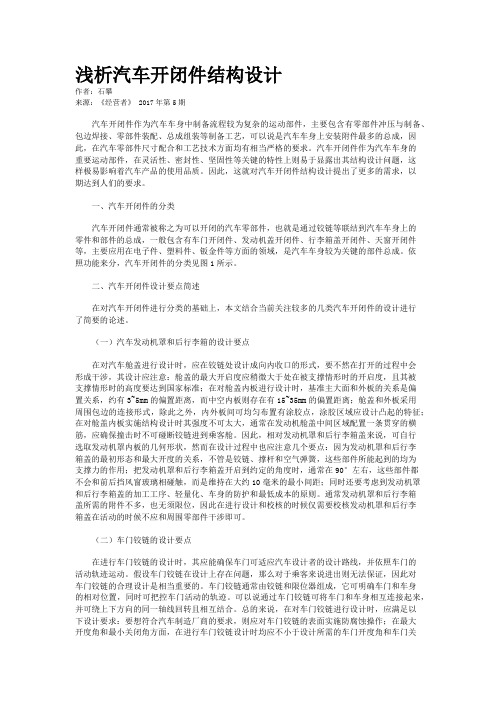
浅析汽车开闭件结构设计作者:石攀来源:《经营者》 2017年第5期汽车开闭件作为汽车车身中制备流程较为复杂的运动部件,主要包含有零部件冲压与制备、包边焊接、零部件装配、总成组装等制备工艺,可以说是汽车车身上安装附件最多的总成,因此,在汽车零部件尺寸配合和工艺技术方面均有相当严格的要求。
汽车开闭件作为汽车车身的重要运动部件,在灵活性、密封性、坚固性等关键的特性上则易于显露出其结构设计问题,这样极易影响着汽车产品的使用品质。
因此,这就对汽车开闭件结构设计提出了更多的需求,以期达到人们的要求。
一、汽车开闭件的分类汽车开闭件通常被称之为可以开闭的汽车零部件,也就是通过铰链等联结到汽车车身上的零件和部件的总成,一般包含有车门开闭件、发动机盖开闭件、行李箱盖开闭件、天窗开闭件等,主要应用在电子件、塑料件、钣金件等方面的领域,是汽车车身较为关键的部件总成。
依照功能来分,汽车开闭件的分类见图1所示。
二、汽车开闭件设计要点简述在对汽车开闭件进行分类的基础上,本文结合当前关注较多的几类汽车开闭件的设计进行了简要的论述。
(一)汽车发动机罩和后行李箱的设计要点在对汽车舱盖进行设计时,应在铰链处设计成向内收口的形式,要不然在打开的过程中会形成干涉,其设计应注意:舱盖的最大开启度应稍微大于处在被支撑情形时的开启度,且其被支撑情形时的高度要达到国家标准;在对舱盖内板进行设计时,基准主大面和外板的关系是偏置关系,约有3~5mm的偏置距离,而中空内板则存在有15~35mm的偏置距离;舱盖和外板采用周围包边的连接形式,除此之外,内外板间可均匀布置有涂胶点,涂胶区域应设计凸起的特征;在对舱盖内板实施结构设计时其强度不可太大,通常在发动机舱盖中间区域配置一条贯穿的横筋,应确保撞击时不可碰断铰链进到乘客舱。
因此,相对发动机罩和后行李箱盖来说,可自行选取发动机罩内板的几何形状,然而在设计过程中也应注意几个要点:因为发动机罩和后行李箱盖的最初形态和最大开度的关系,不管是铰链、撑杆和空气弹簧,这些部件所能起到的均为支撑力的作用;把发动机罩和后行李箱盖开启到约定的角度时,通常在90°左右,这些部件都不会和前后挡风窗玻璃相碰触,而是维持在大约10毫米的最小间距;同时还要考虑到发动机罩和后行李箱盖的加工工序、轻量化、车身的防护和最低成本的原则。
乘用车车身零部件轻量化设计典型案例

乘用车车身零部件轻量化设计典型案例随着环境保护意识的提高和汽车工业的快速发展,乘用车的车身零部件轻量化设计成为了汽车制造业的一个重要课题。
轻量化设计不仅可以降低车辆的整体重量,提高燃油经济性,还可以减少对环境的影响。
下面将介绍几个乘用车车身零部件轻量化设计的典型案例。
1. 利用高强度材料:使用高强度的材料可以在不增加重量的情况下提高零部件的强度和刚性。
例如,许多乘用车现在采用了高强度钢材来替代传统的钢材。
高强度钢材可以提供相同强度的零部件,但重量更轻。
此外,还有一些先进的复合材料,如碳纤维增强塑料(CFRP)和铝合金等,也被广泛应用于车身零部件的制造中。
2. 结构优化设计:通过采用结构优化设计方法,可以将零部件的结构进行优化,以减少不必要的材料使用,从而降低整体重量。
例如,在车身的设计过程中,可以使用拓扑优化方法来确定最佳的结构形状,以最小化材料的使用量。
3. 部分集成设计:通过将不同的零部件进行部分集成设计,可以减少连接部件的数量,降低整体重量。
例如,一些车辆现在采用了一体成型的车顶和车身侧板设计,通过减少连接接口,可以减轻车身重量。
4. 利用轻量化技术:现代乘用车越来越多地采用一些先进的轻量化技术来设计车身零部件。
例如,采用铝合金替代传统的钢材可以显著减轻车身重量。
此外,还有一些其他的轻量化技术,如混合材料结构、可变厚度设计和3D打印等,也被广泛应用于乘用车的车身零部件设计中。
总之,乘用车车身零部件轻量化设计是当前汽车制造业的一个重要课题。
通过使用高强度材料、结构优化设计、部分集成设计和轻量化技术等方法,可以实现乘用车的轻量化,降低车辆油耗,减少对环境的影响。
这些典型案例的应用不仅可以提高汽车的性能和节能性,还可以为未来的汽车制造业发展提供借鉴和启示。
四S1QODT-车身变形测量矫正和修复

2.中心量规
车身旳许多变形尤其是综合性变形,用测量长度往往体现得不十分 明显,所反应出旳问题也不够直观。如当车身或车架与汽车纵轴线旳对 称度发生变化时,就极难用测距法对变形作出精确旳诊疗。假如使用中 心量规,就能够比很好地处理此类测量问题。常见旳中心量规有平行杆 式(见图4-8)和吊链式(见图4-9)。
(2)初步夹紧固定和检验矫正措施 常用旳车辆固定措施有两种: ◆夹在车上旳压焊焊件上。 ◆在机械部件或悬架固定部位用螺栓固定。 在夹持器不能正确地固定到变形部位旳情况下,能够临时焊接上一 小块钢板,如图4-39所示,修理完后再将它拆下来。
挤压损坏是由正面碰撞造成旳,但保险杠几乎不会发生垂直变形。
4.错移损坏
错移损坏是车辆旳一侧向前或向后移动,整个车架或承载车身由长 方形变成平行四边形。
错移是因为车体角上受到前部或后部剧烈旳碰撞造成旳,因为修理 太费时间,得不偿失,经常造成承载车身报废,见图4-23所示。
错移损坏会影响整个车架或车身,而不只是车架纵梁。发动机罩和 行李箱、接近后车轮后侧围板处、乘坐舱或卡车地板也可能出现折皱, 而且一般伴随有挤压和下凹损坏,见图4-24所示。
二.车身变形测量法
1.钢卷尺、专用测距尺测量长度
测量距离所使用旳量具是钢卷尺、专用测距尺等。钢卷尺测 量简便、易行,但测量精度低、误差大,仅合用于那些对精度要 求不高旳场合,尤其是当测量点之间不在同一平面或其间有障碍 时,就极难用钢卷尺测量两点间旳直线距离,如图4-4(b)所示。 使用图4-4(a)所示旳专用测距尺,能够根据不同位置将端头探 入测量点,应用起来十分灵活、以便。
发动机扭振减振器的结构优化
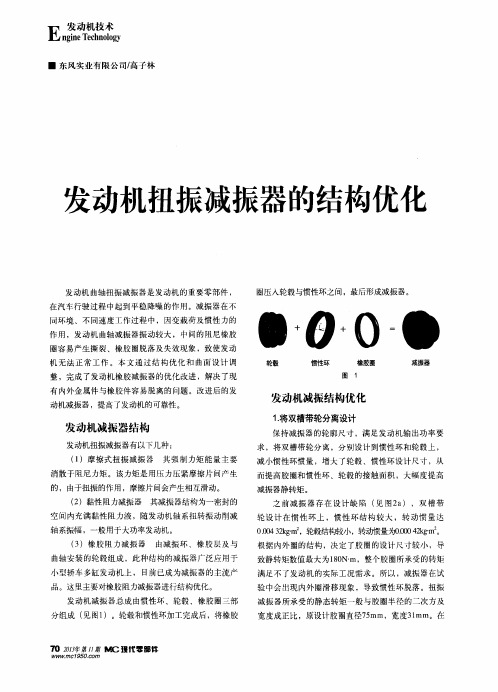
3 . 轮毂 内腔 结构优 化
对 轮 毂及 惯性 环 内 、外部 仿 形结 构进 行 更改 ,主 要是 采 用 力的分 解 原则 。在 力 的分 解 中 ,被 分 解的 那 个力 ( 合力 )是 实 际存 在的 ,有 对应 的 施 力物体 ,以
振器外环与轮毂之间采用一种三角形结构 ,在三角形
En
y
பைடு நூலகம்
■ 东风实业有限公 司/ 高子林
发动机扭振减振器的结构优化
圈压入轮毂 与惯性 环之 间,最后 形成减振 器。
发动 机 曲轴扭 振减 振 器是发 动机 的 重要零 部件 , 在汽 车行 驶过程 中起 到平 稳 降噪 的作用 。减振 器 在不 同环 境 、不 同速度 工作过 程 中 ,因变 载荷及 惯性 力的 作用 ,发 动机 曲轴 减振 器振 动较 大 ,中 间的阻尼 橡胶 圈容 易产 生撕 裂 、橡胶 圈脱 落及 失效现 象 ,致使 发动 机 无 法 正 常 工 作 。 本文 通 过 结 构 优 化 和 曲面 设 计 调 整 ,完 成 了发动 机橡 胶减振 器 的优化 改进 ,解 决 了现 有 内外 金属 件与 橡胶 件容 易脱离 的 问题 。改进 后 的发
拉 脱力 。
带轮分离,分别设计到惯性环和轮毂上,减小惯性环
惯量 ,增大 了轮 毂 外 圈设计 尺 寸 ,从 而提 高胶 圈和 内 外 圈的接 触 面积 ,大 幅 度提 高减 振 器静 转矩 。更 改后 的设 计在 试 验 中得 到可 靠性 验 证 ,完全 满 足发 动机 的
性 能要求 。
( b )改 进后 设计
( a )改进 前 设计
边 有较 长 的直 线接 触面 ,保 证减 振 器 内外 圈装 配后 达 到装 配尺寸及几 何公差要求 。
关于机盖总成外观凹陷的研究与优化

关于机盖总成外观凹陷的研究与优化孙静瑶;张遥;刘春阳【摘要】汽车前机舱盖设计受造型和性能双方面影响,文章在保证造型要求下从关闭状态下外板凹坑、外板凹陷刚度、行人头部撞击伤害值三因素分析,通过将机盖内板溃缩孔与机盖内板横向加强筋阶梯布置,机盖锁前移缩短外板支撑的跨距等方法,优化发动机罩结构,同时保证产品在行人保护法规中的得分要求.【期刊名称】《汽车实用技术》【年(卷),期】2018(000)001【总页数】3页(P48-50)【关键词】发动机罩;外板凹坑;外板抗凹陷刚度;行人保护【作者】孙静瑶;张遥;刘春阳【作者单位】长城汽车股份有限公司技术中心,河北省汽车工程技术研究中心,河北保定 071000;长城汽车股份有限公司技术中心,河北省汽车工程技术研究中心,河北保定 071000;长城汽车股份有限公司技术中心,河北省汽车工程技术研究中心,河北保定 071000【正文语种】中文【中图分类】U462.1前言随着汽车在我国的迅速普及,汽车市场竞争日趋激烈,如何缩短产品整改周期,降低开发成本,对设计人员提出了更高要求,CAE技术的应用,能够使设计问题提前暴露,减少设计问题在试制、生产阶段发生的概率,降低产品开发损失。
本文在设计阶段,对发动机罩各项指标进行了定义,通过CAE软件对发动机罩进行了系统分析,对设计结构进行改进及优化。
发动机舱盖是保护发动机舱的主要零部件,对发动机舱起到防水、防尘、隔热、降噪的作用,其造型也是整车外观效果的重要部分,发动机舱盖结构上要实现开启和关闭,并在特定角度实现支撑停留,须具有一定的刚度,除此以外,发动机罩需满足国家法规要求,实现安全碰撞、行人保护等功能,设计时必须综合考虑。
因此发动机罩结构性能的优良直接影响整车的被动安全性与乘坐舒适性,对于发动机舱盖的设计要求是刚性强、质量轻、隔热效果好。
1 发动机罩问题分析本文结合生产开发过程,对三项相互制约的指标进行研究解决。
⑴生产阶段,在发动机罩间隙面差调整过程中,机盖关闭状态下存在外板光影不顺。
某前置后驱车型C点布置优化设计

AUTOMOBILE DESIGN | 汽车设计某前置后驱车型C点布置优化设计程坤 黄晓珍上汽通用五菱汽车股份有限公司 广西柳州市 545007摘 要: 汽车C点处于发动机舱和驾驶舱之间,它既是造型外饰的重要特征点,也是总布置设计的关键硬点。
在汽车新产品开发过程中往往会出现造型设计的C点位置和总布置设计位置冲突,从而导致设计方案反复刺穿项目节点的问题。
本文对C点布置主要影响因素进行了分析研究,并基于某前置后驱车型整车设计开发中出现的C点布置问题,提出了C点优化设计方案,解决了前下视野小、遮阳板及内后视镜操作不便、仪表板触及困难、发动机舱零部件售后维修不便等问题,对后续新车型总布置设计开发提供经验教训,避免出现类似问题导致设计反复。
关键词:C点 总布置 造型1 引言随着国内民众生活水平的提升,汽车市场竞争日渐激烈,为快速抢占市场先机,汽车新产品的成本和周期是非常关键的因素,而总布置的高效合理设计可以有效缩短整车开发周期并降低整车开发成本。
本文阐述了整车总布置设计中的C点布置及其定义,对C点布置的相关因素进行了研究,并结合某前置后驱新车型的开发,对C点布置中出现的问题进行了原因分析及优化设计,为后续整车C点布置设计提供了经验参考。
可以有效避免因布置方案反复而导致的开发周期延长问题。
C点是汽车纵向中心面上引擎盖或其他零件的最高点在前挡玻璃外表面上的水平投影点,定义参考《SAE J1100 NOV 2009 Motor Vehicle Dimensions》中Cowl Point 描述[1],一般乘用车中C点大部分为汽车纵向中心面上发动机罩盖后沿点在前挡风玻璃上的投影点,如图1所示。
图1 C点示意图Cowl PointA2 C点布置影响因素汽车C点位于发动机舱及驾驶舱交界处,它既是造型外饰硬点也是整车总布置关键硬点,在汽车设计开发中至关重要。
影响C点布置的因素较多,涉及发动机舱动力总成、底盘零件和仪表模块总成布置以及造型设计,汽车新产品开发时需要综合考虑所有影响因素,工程和造型需要反复沟通确认达成一致意见。