印染废水处理论文外文翻译
两篇印染废水处理的外文翻译
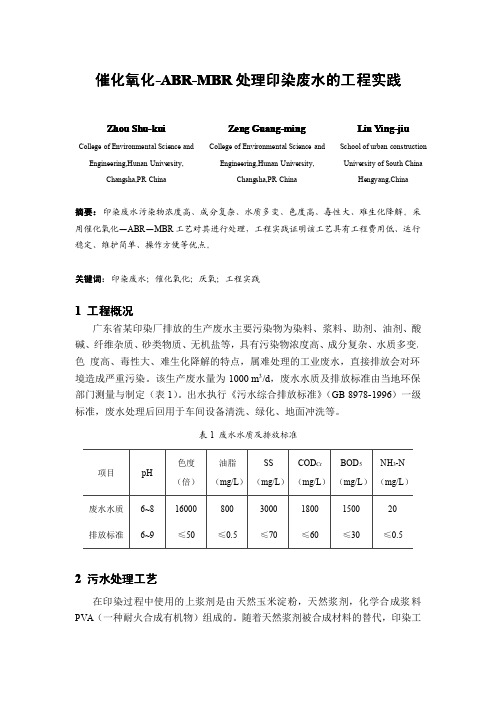
5 处理效果
该工程 2007 年 5 月竣工后,经试运行 3 个月,于 9 月正式投入正常运行, 从运行 1 年的情况来看,系统运行稳定、处理效果显著,出水水质良好。经环境 监测站在不同的时期测得出水水质各项指标均己达《污水综合排放标准》 (GB 8978-1996)一级排放标准,测得的部分结果如表 2 所示。
-1-
苏州科技学院本科毕业设计(外文翻译 1)
距采用 1 cm , 一天清理 2 次,以保证排水畅通。废水先经格栅去除大块杂物后, 自流入隔油池。 (2)调节池 钢混结构,尺寸 8 m ×6 m×2.5 m , 1 座,HRT 2.3 h。废水在调节池内一方 面利用气浮作用将油脂进一步除去,另一方面将废水充分混合,均匀水质水量。 (3)催化氧化池 内设组合式催化氧化装置 2 台,尺寸 6 m ×4 m×3 m ,处理能力为 25 m3 /h, 其关键装置是一个管式催化氧化单元。管径采用 200(根据情况可大可小)的不 锈钢管或 PVC 管,管内壁涂有光催化功能的 TiO2 涂层, 这种装置单位体积/ 表面 积大,1 m3 液体管内表面积达 20 m 2。管内沿管径轴向安装紫外灯管,废水进入 管中通过管道推流混合,不用搅拌装置。废水在管内流动与管内壁的 TiO2 涂层 接触,在其表面发生光催化氧化反应,同时 H2O2 在紫外光作用下也产生各种氧 化反应, 最终达到去除污染物的目的。 该设备适用范围广, 可改善废水可生化性; 操作简单,清洗方便,不会发生 结垢和有机物粘附现象;催化表面积大,催化 效率高;紫外光能利用充分,大大降低单位处理能耗。 (4)沉淀池 钢混结构,尺寸 5 m×5 m ×3 m, 2 座,HRT 3 h。 (5) ABR 池 2 座,钢混结构,尺寸 8 m×6.5 m × 4 m,HRT 10 h,池内放置大比表面积 的球状悬浮生物填料。废水经催化氧化处理去除部分有机物,改善废水可生化性 和脱色后,经排放到 pH 中和池加碱调到中性,再进入 ABR 池。 (6) MBR 池 2 座,钢混结构,尺寸 8 m× 6 m × 4 m , HRT 8 h ,流量为 12 m3/h 。 MBR 池为板框抽吸淹没式结构,膜组件为孔径约 0.2μm 的 PVDF 中空纤维膜。平常 通过周期性地间歇操作和通风来减少膜污染,每 6 个月进行一次化学清洗,用 0.1% 的 NaClO 和 4%的 NaOH 将膜组件浸泡 24 h 。 (7)中间水池 2 座,钢混结构,尺寸 6 m× 3.5 m ×4 m,HRT 8 h。 (8)回用水池 2 座,钢混结构,尺寸 6 m× 3.5 m ×4 m,HRT 8 h。 (9)污泥处理系统。 污泥池 2 座,钢混结构,尺寸 6 m ×4 m×3 m ,压滤机 2 台,污泥泵 4 台。 沉淀污泥排放到污泥池后,用污泥泵打入板框压滤机,经压滤后的干渣外运到固 废处理站处理,压滤出水回废水调节池。
印染厂回用水标准

印染厂回用水标准Water pollution is a serious issue globally, with the textile industry being one of the major contributors. 印染厂是家产业种大量用水的企业,同时也是水污染的主要源头之一。
In order to address this problem, it is crucial for printing and dyeing factories to strictly adhere to water reuse standards. 为了解决这一问题,印染厂必须严格遵守回用水标准。
Implementing these standards not only helps protect the environment, but also ensures the sustainability of the industry in the long run. 实施这些标准不仅有助于保护环境,还能确保产业的可持续发展。
One of the main reasons why printing and dyeing factories need to follow water reuse standards is to reduce the amount of wastewater discharged into rivers and lakes. 对于印染厂而言,遵守回用水标准的一个主要原因是为了减少排放到河流和湖泊中的废水量。
By reusing water in various processes, factories can significantly decrease their water consumption and minimize the negative impact on aquatic ecosystems. 通过在各个工序中重复使用水,工厂可以显著降低用水量,并最大程度地减少对水生态系统的负面影响。
印染废水处理论文外文翻译

本文由xukexin0601贡献doc文档可能在W AP端浏览体验不佳。
建议您优先选择TXT,或下载源文件到本机查看。
十八章外文翻译印染废水处理论文摘要:本文分析了印染废水处理的所面临的问题,以及介绍了印染废水处理方法的研究进展与动向。
并指出不同印染废水处理方法的组合是印染废水处理的有效方法。
关键词:印染废水;处理方法纺织印染工业作为中国具有优势的传统支柱行业之一,20 世纪90 年代以来获得迅猛发展,其用水量和排水量也大幅度增长。
据不完全统计,我国日排放印染废水量为3000-4000kt,是各行业中的排污大户之一。
加强印染废水的处理可以缓解我国水资源严重匮乏的问题,对保护环境、维持生态平衡起着极其重要的作用。
1 印染废水处理面临的问题1.1 排放标准的日益严格随着社会经济的不断发展和人们环境意识的提高,我国加大了对印染污水的治理。
根据《纺织染整工业水污染物排放标准》,除Ⅲ类污水排放指标变化不大外,国家增加了Ⅰ类和Ⅱ类污水印染废BOD、COD、色度、悬浮物、氨氮、苯胺类、二氧化氯等指标的排放限定。
而印染废水水质一般平均为COD800-2000mg/L,色度200-800 倍,pH 值10-13,BOD/COD 为0.25-0.4,因此印染废水的达标排放是印染行业急需要解决的问题。
1.2 印染废水处理难度增加 1.2.1 印染废水组分复杂印染废水是指印染加工过程中各工序所排放的废水混合而成的混合废水。
主要包括:预处理阶段(如烧毛、退浆、煮练、漂白、丝光)排放的退浆、煮练、漂白、丝光废水;染色阶段排放的染色废水;印花阶段排放的印花废水和皂洗废水;整理阶段排放的整理废水。
印染废水水质随原材料、生产品种、生产工艺、管理水平的不同而有所差异,导致各个印染工序排放后汇总的废水组分非常复杂。
随着染料工业的飞速发展和后整理技术的进步,新型助剂、染料、整理剂等在印染行业中被大量使用,难降解有毒有机成分的含量也越来越多,有些甚至是致癌、致突变、致畸变的有机物,对环境尤其是水环境的威胁和危害越来越大。
印染废水处理工程设计
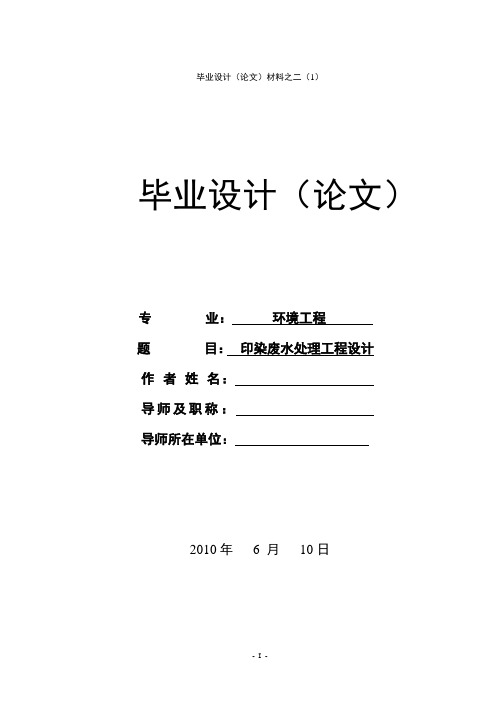
国有大中型纺织印染企业基本建有废水处理装置,并相当一部分正常运行,其处理成本为0.7~1.0元/吨左右。而多数乡镇企业则很少修建污染处理装置,其污染不容忽视。
据统计,1994年纺织工业全年排放废水量达8.7亿立方米(不含乡镇企业)居全国各行业第四位,其中印染废水约占80%。印染废水是一种色度较高,以人工合成有机物为主、浓度较高的有机废水,亦属于较难处理的工业废水。我国的染料生产水平于国外差距较大,染料上染率低,助剂投配量较大,加大了纺织印染行业的污染负荷。
毕业设计(论文)材料之二(1)
毕业设计(论文)
专 业:环境工程
题 目:印染废水处理工程设计
作 者 姓 名:导师及职称:
导师所在单位:
2010年6月10日
本科生毕业设计(论文)任务书
2011届院
专业
学生姓名:
Ⅰ
毕业设计(论文)题目
中文:印染废水处理工程设计
英文:Design of Dye Wastewater Treatment Project
对于大型纺织厂而言,纺织工业废水处理常用的流程为一级好氧处理工艺[2]。最近,一些大型纺织生产厂采用了二级厌氧-好氧技术。经厌氧-好氧处理后,废水的COD和BOD去除率可分别达到70%和95%。
大多数中小型纺织厂没有生物处理设施。只有在一些厂中采用了沉淀或一级处理以减少废水中悬浮固体的浓度和一部分BOD。一些中小型纺织厂还采用了化学处理法(如絮凝)。必须强调的是,化学处理法由于要投加化学药剂,其成本一般是较高的。工业生产实践表明,单纯用化学法处理纺织工业废水很难达到排放标准的要求。
染布厂污水处理流程

染布厂污水处理流程染布厂污水处理流程英文介绍:The wastewater treatment process in a dyeing factory is crucial for ensuring efficient removal of pollutants and safe discharge of treated water. Here is a brief overview of the typical wastewater treatment process in a dyeing factory:Preliminary Treatment: Raw wastewater from the dyeing process undergoes initial treatment to remove large solids and debris.Screening: The wastewater passes through screens to remove any remaining solid particles or fibers.Sedimentation: The water is then allowed to settle in sedimentation tanks, where heavier particles settle to the bottom.Biological Treatment: The pretreated wastewater enters biological treatment units, such as activated sludge tanks, where microorganisms break down organic pollutants.Aeration: Air is introduced into the biological treatment units to support the activity of the microorganisms.Clarification: The treated water is then passed through clarification tanks, where remaining solids settle and are removed.Filtration: Further filtration may be employed to remove any remaining suspended particles.Disinfection: The water is disinfected to kill any remaining harmful microorganisms.pH Adjustment: The pH of the water is adjusted to ensure it meets discharge standards.Final Discharge: The treated water, now meeting the required discharge standards, is safely discharged into the environment.染布厂污水处理流程中文介绍:染布厂的污水处理流程对于确保有效去除污染物和安全排放处理后的水至关重要。
污水处理的英文文献翻译(1)
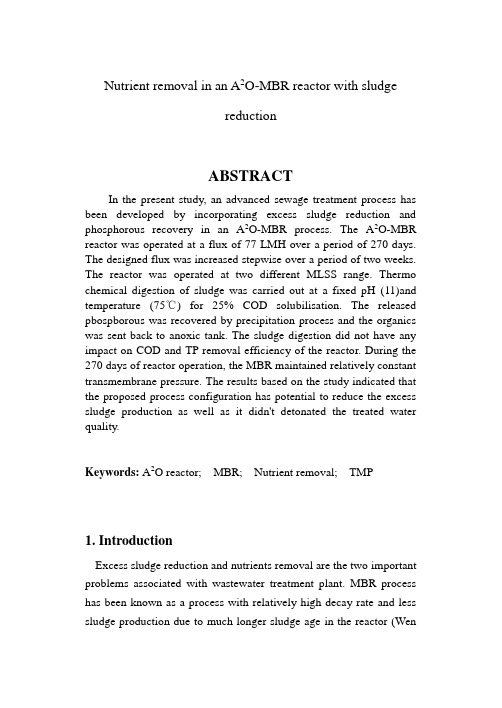
Nutrient removal in an A2O-MBR reactor with sludgereductionABSTRACTIn the present study, an advanced sewage treatment process has been developed by incorporating excess sludge reduction and phosphorous recovery in an A2O-MBR process. The A2O-MBR reactor was operated at a flux of 77 LMH over a period of 270 days. The designed flux was increased stepwise over a period of two weeks. The reactor was operated at two different MLSS range. Thermo chemical digestion of sludge was carried out at a fixed pH (11)and temperature (75℃) for 25% COD solubilisation. The released pbospborous was recovered by precipitation process and the organics was sent back to anoxic tank. The sludge digestion did not have any impact on COD and TP removal efficiency of the reactor. During the 270 days of reactor operation, the MBR maintained relatively constant transmembrane pressure. The results based on the study indicated that the proposed process configuration has potential to reduce the excess sludge production as well as it didn't detonated the treated water quality.Keywords: A2O reactor; MBR; Nutrient removal; TMP1. IntroductionExcess sludge reduction and nutrients removal are the two important problems associated with wastewater treatment plant. MBR process has been known as a process with relatively high decay rate and less sludge production due to much longer sludge age in the reactor (Wenet al., 2004). Sludge production in MBR is reduced by 28-68%, depending on the sludge age used (Xia et al.,2008). However, minimizing the sludge production by increasing sludge age is limited due to the potential adverse effect of high MLSS concentrations on membrane (Yoon et al., 2004). This problem can be solved by introducing sludge disintegration technique in MBR (Young et al., 2007). Sludge disintegration techniques have been reported to enhance the biodegradability of excess sludge (Vlyssides and Karlis, 2004). In overall, the basis for sludge reduction processes is effective combination of the methods for sludge disintegration and biodegradation of treated sludge. Advances in sludge disintegration techniques offer a few promising options including ultrasound (Guo et al., 2008), pulse power (Choi et al.,2006), ozone (Weemaes et al., 2000), thermal (Kim et al., 2003), alkaline (Li et al., 2008) acid (Kim et al., 2003) and thermo chemical(Vlyssides and Karlis, 2004). Among the various disintegration techniques, thermo chemical was reported to be simple and cost effective (Weemaes and Verstraete, 1998). In thermal-chemical hydrolysis, alkali sodium hydroxide was found to be the most effective agent in inducing cell lysis (Rocker et al., 1999). Conventionally, the nutrient removal was carried out in an A2O process. It has advantage of achieving, nutrient removal along with organic compound oxidation in a single sludge configuration using linked reactors in series (Tchobanoglous et al., 2003). The phosphoroes removal happens by subjecting phosphorous accumulating organisms (PAO) bacteria under aerobic and anaerobic conditions (Akin and Ugurlu, 2004). These operating procedures enhance predominance PAO, which are able to uptake phosphorous in excess. During the sludge pretreatment processes the bound phosphorous was solubilised and it increases the phosphorousconcentration in the effluent stream (Nishimura, 2001).So, it is necessary to remove the solubilised phosphorus before it enters into main stream. Besides, there is a growing demand for the sustainable phosphorous resources in the industrialized world. In many developed countries, researches are currently underway to recover the phosphoroes bound in the sludge's of enhanced biological phosphorus removal system (EBPR). The released phosphorous can be recovered in usable products using calcium salts precipitation method. Keeping this fact in mind, in the present study, a new advanced wastewater treatment process is developed by integrating three processes, which are: (a) thermo chemical pretreatment in MBR for excess sludge reduction (b) A2O process for biological nutrient removal (c) P recovery through calcium salt precipitation. The experimental data obtained were then used to evaluate the performance of this integrated system.2. Methods2.1. WastewaterThe synthetic domestic wastewater was used as the experimental influent. It was basically composed of a mixed carbon source, macro nutrients (N and P), an alkalinity control (NaHCO3) and a microelement solution. The composition contained (/L) 210 mg glucose, 200 mg NH4C1, 220 mg NaHCO3, 22一34 mg KH2PO4, microelement solution (0.19 mg MnCl2 4H20, 0.0018 mg ZnCl22H2O,0.022 mg CuCl22H2O, 5.6 mg MgSO47H2O, 0.88 mg FeCl36H2O,1.3 mg CaCl2·2H2O). The synthetic wastewater was prepared three times a week with concentrations of 210±1.5 mg/L chemical oxygen demand (COD), 40±1 mg/L total nitrogen (TN) and 5.5 mg/L total phosphorus (TP).2.2. A2O-MBRThe working volume of the A2O-MBR was 83.4 L. A baffle was placed inside the reactor to divide it into anaerobic (8.4 L) anoxic (25 L) and aerobic basin (50 L). The synthetic wastewater was feed into the reactor at a flow rate of 8.4 L/h (Q) using a feed pump. A liquid level sensor, planted in aerobic basin of A2O-MBR controlled the flow of influent. The HRT of anaerobic, anoxic and aerobic basins were 1, 3 and 6 h, respectively. In order to facilitate nutrient removal, the reactor was provided with two internal recycle (1R). IRl (Q= 1)connects anoxic and anaerobic and IR 2 (Q=3) was between aerobic and anoxic. Anaerobic and anoxic basins were provided with low speed mixer to keep the mixed liquid suspended solids (MLSS) in suspension. In the aerobic zone, diffusers were used to generate air bubbles for oxidation of organics and ammonia. Dissolved oxygen (DO) concentration in the aerobic basin was maintained at 3.5 mg/1 and was monitored continuously through online DO meter. The solid liquid separation happens inaerobic basin with the help of five flat sheet membranes having a pore size of 0.23 pm. The area of each membrane was 0.1 m2. They were connected together by a common tube. A peristaltic pumpwas connected in the common tube to generate suction pressure. In the common tube provision was made to accommodate pressure gauge to measure transmembrane pressure (TMP) during suction. The suction pump was operated in sequence of timing, which consists of 10 min switch on, and 2 min switch off.2.3. Thermo chemical digestion of sludgeMixed liquor from aerobic basin of MBR was withdrawn at the ratio of 1.5% of Q/day and subjected to thermo chemical digestion. Thermo chemical digestion was carried out at a fixed pH of 11(NaOH) and temperature of 75℃for 3 h. After thermo chemical digestion the supernatant and sludge were separated. The thermo-chemicallydigested sludge was amenable to further anaerobic bio-degradation (Vlyssides and Karlis, 2004), so it was sent to theanaerobic basin of the MBR2.4. Phosphorus recoveryLime was used as a precipitant to recover the phosphorous in the supernatant. After the recovery of precipitant the content was sent back to anoxic tank as a carbon source and alkalinity supelement for denitrification.2.5. Chemical analysisCOD, MLSS, TP, TN of the raw and treated wastewater were analyzed following methods detailed in (APHA, 2003). The influent and effluent ammonia concentration was measured using an ion-selective electrode (Thereto Orion, Model: 95一12). Nitrate in the sample was analyzed using cadmium reduction method (APHA, 2003).3. Results and discussionFig. 1 presents data of MLSS and yield observed during the operational period of the reactor. One of the advantages of MBR reactor was it can be operated in high MLSS concentration. The reactor was seeded with EBPR sludge from the Kiheung, sewage treatment plant, Korea. The reactor was startup with the MLSS concentration of 5700 mg/L. It starts to increase steadily with increase in period of reactor operation and reached a value of 8100 mg/L on day 38. From then onwards, MLSS concentration was maintained in the range of 7500 mg/L by withdrawing excess sludge produced and called run I. The observed yields (Yobs) for experiments without sludge digestion (run I) and with sludge digestion were calculated and given in Fig. 1. The Yobs for run I was found to be 0.12 gMLSS/g COD. It was comparatively lower than a value of 0.4 gMLSS/g CODreported for the conventional activated sludge processes (Tchoba-noglous et al., 2003). The difference in observed yield of these two systems is attributed to their working MLSS concentration. At high MLSS concentration the yield observed was found to be low (Visva-nathan et al., 2000). As a result of that MBR generated less sludge.The presently used MLSS ranges (7.5一10.5 g/L) are selected on the basis of the recommendation by Rosenberger et al. (2002). In their study, they reported that the general trend of MLSS increase on fouling in municipal applications seems to result in no impact at medium MLSS concentrations (7一12 g/L).It is evident from the data that the COD removal efficiency of A2O system remains unaffected before and after the introduction of sludge digestion practices. A test analysis showed that the differences between the period without sludge digestion (run I) and with sludge digestion (run II and III) are not statistically significant.However, it has been reported that, in wastewater treatment processes including disintegration-induced sludge degradation, the effluent water quality is slightly detonated due to the release of nondegradable substances such as soluble microbial products (Ya-sui and Shibata, 1994; Salcai et al., 1997; Yoon et al., 2004). During the study period, COD concentration in the aerobic basin of MBR was in the range of 18-38 mg/L and corresponding organic concentration in the effluent was varied from 4 to 12 mg/L. From this data it can be concluded that the membrane separation played an important role in providing the excellent and stable effluent quality.Phosphorus is the primary nutrient responsible for algal bloom and it is necessary to reduce the concentration of phosphorus in treated wastewater to prevent the algal bloom. Fortunately its growth can be inhibited at the levels of TP well below 1 mg/L (Mer-vat and Logan, 1996).Fig. 2 depicts TP removal efficiency of the A2O-MBR system during the period of study. It is clearly evident from the figure that the TP removal efficiency of A/O system was remains unaffected after the introduction of sludge reduction. In the present study, the solubilised phosphorous was recovered in the form of calcium phosphate before it enters into main stream. So, the possibility of phosphorus increase in the effluent due to sludge reduction practices has been eliminated. The influent TP concentration was in the range of 5.5 mg/L. During thefirst four weeks of operation the TP removal efficiency of the system was not efficient as the TP concentration in the effluent exceeds over 2.5 mg/L. The lower TP removal efficiency during the initial period was due to the slow growing nature of PAO organisms and other operational factors such as anaerobic condition and internal recycling. After the initial period, the TP removal efficiency in the effluent starts to increase with increase in period of operation. TP removal in A2O process is mainly through PAO organisms. These organisms are slow growing in nature and susceptible to various physicochemical factors (Carlos et al., 2008). During the study period TP removal efficiency of the system remains unaffected and was in the range of 74-82%.。
写一篇关于印染厂排未经处理的废气的话题英语作文
印染厂未经处理废气排放英语作文1英文作文:In recent years, the issue of untreated waste gas emissions from printing and dyeing factories has become increasingly prominent. This not only poses a serious threat to the environment but also has a significant impact on people's lives.For example, in some areas near printing and dyeing factories, residents have begun to experience various health problems. Many people suffer from persistent coughing and difficulty breathing. The unprocessed waste gas contains harmful substances such as sulfur dioxide and nitrogen oxides, which can cause respiratory diseases and even endanger people's lives. Moreover, the waste gas emissions also have a negative impact on the environment. They can reduce air quality, making the sky over the factory area always hazy. This not only affects people's daily lives but also disrupts the ecological balance. Birds and other wildlife may be forced to leave the area due to the poor air quality.To address this problem, both the government and enterprises need to take action. The government should strengthen supervision and inspection of printing and dyeing factories. Stringent regulations should be implemented to ensure that factories install purification equipment and treat waste gas properly. At the same time, the government should also increase penalties for factories that violate environmental protection regulations. Enterprises, on the other hand, should be responsible for their actions. They should invest in advanced purification equipment and technologies to reduce waste gas emissions. By doing so, they can not only protect the environment but also enhance their corporate image.In conclusion, untreated waste gas emissions from printing and dyeing factoriesare a serious problem that requires the joint efforts of the government and enterprises. Only by taking effective measures can we protect the environment and people's health.中文翻译:近年来,印染厂未经处理的废气排放问题日益突出。
印染废水处理外文文献
Full terms and conditions of use: /terms-and-conditions-of-access.pdf This article may be used for research, teaching and private study purposes. Any substantial or systematic reproduction, re-distribution, re-selling, loan or sub-licensing, systematic supply or distribution in any form to anyone is expressly forbidden. The publisher does not give any warranty express or implied or make any representation that the contents will be complete or accurate or up to date. The accuracy of any instructions, formulae and drug doses should be independently verified with primary sources. The publisher shall not be liable for any loss, actions, claims, proceedings, demand or costs or damages whatsoever or howsoever caused arising directly or indirectly in connection with or arising out of the use of this material.
印染污水培训中英文
漂白 Bleach
丝光 Mercerizing
ห้องสมุดไป่ตู้
染色 Dyeing
整理 Arrangement
印染废水特征污染物分析 Characteristic pollutant analysis of the printing and dyeing BOD 来自有机物,如染料、浆料、表面活性剂等。 BOD comes from organic matters, such as dyes, pastes, surfactants, etc. COD 来自染料、还原漂白剂、醛、还原净水剂、淀粉整理剂等。 COD comes from the dye, the reducing bleaching agent, the aldehyde, the reducing water purifying agent, the starch finishing agent, etc. 重金属毒物来自铜、铅、锌、铬、汞、氰离子等。 Heavy metal toxins from copper, lead, zinc, chromium, mercury, cyanide ion, etc. 色度来自染料、颜料在废水中呈现的颜色。 The color comes from the dye and pigment in the waste water.
印染工艺产污分析 Pollution analysis of printing and dyeing process 工序 Process
退浆 Desizing 煮练 Scouring
添加物 Additives
淀粉酶或硫酸 Amylase or sulfuric acid 氢氧化钠、清洁剂 Sodium hydroxide, cleaner 双氧水、氯、次氯酸、碱 Hydrogen peroxide, chlorine, hypochlorous acid and alkali 氢氧化钠 Sodium hydroxide 表面活性剂、元明粉、保险粉等化学剂 Chemical agent such as surfactant, sodium sulphate, insurance powder 软化剂、淀粉、树脂、甲醛等化学剂 Softener, starch, resin, formaldehyde and other chemical agent
印染废水处理的英语
印染废水处理的英语英文回答:Textile Wastewater Treatment.Textile wastewater treatment is a critical environmental issue due to the significant amounts of hazardous chemicals and pollutants discharged into water bodies. These pollutants can harm aquatic life, contaminate drinking water sources, and pose risks to human health.Effective textile wastewater treatment involves amulti-step process that aims to remove or reduce pollutants to acceptable levels before discharging the treated water into the environment. The treatment process typically begins with a preliminary treatment stage, where large solids and suspended particles are removed using physical methods such as screening and sedimentation.The next step involves chemical treatment, wherecoagulants and flocculants are added to destabilize pollutants and promote their agglomeration into larger flocs. These flocs are then removed through sedimentation or flotation.Biological treatment is often employed as the next stage, where microorganisms break down organic pollutants into simpler, less harmful substances. Activated sludge, trickling filters, and anaerobic digestion are commonly used biological treatment technologies.Advanced treatment processes, such as membrane filtration, electrocoagulation, and ozonation, may be necessary to remove residual pollutants or meet stringent regulatory requirements.中文回答:印染废水处理。
- 1、下载文档前请自行甄别文档内容的完整性,平台不提供额外的编辑、内容补充、找答案等附加服务。
- 2、"仅部分预览"的文档,不可在线预览部分如存在完整性等问题,可反馈申请退款(可完整预览的文档不适用该条件!)。
- 3、如文档侵犯您的权益,请联系客服反馈,我们会尽快为您处理(人工客服工作时间:9:00-18:30)。
本文由xukexin0601贡献doc文档可能在W AP端浏览体验不佳。
建议您优先选择TXT,或下载源文件到本机查看。
十八章外文翻译印染废水处理论文摘要:本文分析了印染废水处理的所面临的问题,以及介绍了印染废水处理方法的研究进展与动向。
并指出不同印染废水处理方法的组合是印染废水处理的有效方法。
关键词:印染废水;处理方法纺织印染工业作为中国具有优势的传统支柱行业之一,20 世纪90 年代以来获得迅猛发展,其用水量和排水量也大幅度增长。
据不完全统计,我国日排放印染废水量为3000-4000kt,是各行业中的排污大户之一。
加强印染废水的处理可以缓解我国水资源严重匮乏的问题,对保护环境、维持生态平衡起着极其重要的作用。
1 印染废水处理面临的问题1.1 排放标准的日益严格随着社会经济的不断发展和人们环境意识的提高,我国加大了对印染污水的治理。
根据《纺织染整工业水污染物排放标准》,除Ⅲ类污水排放指标变化不大外,国家增加了Ⅰ类和Ⅱ类污水印染废BOD、COD、色度、悬浮物、氨氮、苯胺类、二氧化氯等指标的排放限定。
而印染废水水质一般平均为COD800-2000mg/L,色度200-800 倍,pH 值10-13,BOD/COD 为0.25-0.4,因此印染废水的达标排放是印染行业急需要解决的问题。
1.2 印染废水处理难度增加 1.2.1 印染废水组分复杂印染废水是指印染加工过程中各工序所排放的废水混合而成的混合废水。
主要包括:预处理阶段(如烧毛、退浆、煮练、漂白、丝光)排放的退浆、煮练、漂白、丝光废水;染色阶段排放的染色废水;印花阶段排放的印花废水和皂洗废水;整理阶段排放的整理废水。
印染废水水质随原材料、生产品种、生产工艺、管理水平的不同而有所差异,导致各个印染工序排放后汇总的废水组分非常复杂。
随着染料工业的飞速发展和后整理技术的进步,新型助剂、染料、整理剂等在印染行业中被大量使用,难降解有毒有机成分的含量也越来越多,有些甚至是致癌、致突变、致畸变的有机物,对环境尤其是水环境的威胁和危害越来越大。
总体而言,印染废水的特点是成分复杂、有机物含量高、色度深化学需氧量(COD)高,而生化需氧量(BOD5)相对较低,可生化性差,排放量大。
1.2.2 印染废水处理方法的局限性80 年代以前,我国印染废水的可生化性较高,CODcr 浓度常在800mg/L 以下,采用传统的生物与物化联合处理系统,出水即可达到排放标准。
近二十年来,印染废水水质发生了很大的变化。
传统的印染废水处理方法,如吸附、悬浮、过滤、混凝等具有设备简单,操作简便和工艺成熟的优点,但是这类处理方法通常是将有机物从液相转移到固相或气相,不仅没有完全消除有机污染物和消耗化学药剂,而且造成废物堆积和二次污染;生物法只能除去印染废水中的BOD,对于COD 特别是有毒难降解有机物和色度的出去效果不明显。
单一的处理方法已不能满足当前印染废水发展的要求。
2 印染废水处理研究进展与动向 2.1 传统方法和工艺的改进 2.1.1 吸附法吸附法特别适合低浓度印染废水的深度处理,具有投资小、方法简便、成本低的特点,适合中小型印染厂废水的处理。
传统的吸附剂主要是活性碳,活性碳只对阳离子染料、直接染料、酸性染料、活性染料等水溶性染料具有较好的吸附性能,但是不能去除水中的胶体疏水性染料,并且再生费用高,使活性碳的应用受到限制。
近几年,研究的重点主要在开发新的新的吸附剂以及对传统的吸附剂进行改良方面。
2.1.2 混凝法混凝法具有投资费用低、设备占地少、处理容量大、脱色率高等优点。
混凝剂有无机混凝剂、有机混凝剂及生物混凝剂等。
传统混凝法对疏水性染料脱色效率很高。
缺点是需随着水质变化改变投料条件,对亲水性染料的脱色效果差,COD 去除率低。
如何选择有效的混凝脱色工艺和高效的混凝剂,则是该技术的关键。
2.1.3 化学氧化法化学氧化是目前研究较为成熟的方法。
氧化剂一般采用Fenton 试剂(Fe2 ,H2O2)、臭氧、氯气、次氯酸钠等。
按氧化剂的不同,可将化学氧化分为:臭氧氧化法和芬顿试剂氧化法。
臭氧氧化法不产生污泥和二次污染,但是处理成本高,不适合大流量废水的处理,而且CODcr 去除率低。
通常很少采用单一的臭氧法处理印染废水,而是将它与其它方法相结合,彼此互补达到最佳的废水处理效果。
汪晓军等[13]用臭氧-曝气生物滤池工艺处理模拟废水2.1.4 电化学法电化学法具有设备小、占地少、运行管理简单、CODcr 去除率高和脱色好等优点,但是沉淀生成量及电极材料消耗量较大,运行费用较高。
传统的电化学法可分为电絮凝法、电气浮法、电氧化法以及微电解、电解内法等。
国外许多研究者从研制高电催化活性电极材料着手,对有机物电催化影响因素和氧化机理进行了较系统的理论研究和初步的应用研究,国内在这一领域的研究还刚刚起步。
2.1.5 生物处理法生物处理法主要包括好氧法和厌氧法。
目前国内主要采用好氧法进行印染废水处理。
好氧法又分为活性污泥法和生物膜法。
活性污泥既能分解大量的有机物质,又能去除部分色度,还可以微调pH 值,运转效率高且费用低,出水水质较好,适合处理有机物含量较高的印染废水;生物膜法对印染废水的脱色作用较活性污泥法高。
但是生物法存在着三个自身无法解决的问题:①剩余污泥的处里费用较高;②单一运用生物法己不能满足实际运用的需要;③有时需要在其前端加一道提高废水可生化性的预处理,提高了投资及运行成本。
单一的好氧生物处理只能去除废水中的部分易降解的有机物,色度问题无法解决。
为了降低消耗及去除废水中较难降解的有机污染物,出现了厌氧-好氧新型处理工艺和生物强化技术。
厌氧-好氧法可先由厌氧过程中的产酸阶段,去除部分较易降解的有机污染物,将较难降解的大分子有机物分解为较简单的小分子有机物,再通过好氧生物处理过程进一步去除。
厌氧-好氧法处理难生化降解的印染废水具有除污染效率高、运行稳定和较强的耐冲击负荷能力等特点。
有研究报道,采用厌氧-好氧工艺处理印染废水,在进水CODcr 为1085mg/L,BODS 为315mg/L 的情况下,二者的去除率分别可达83.9 和76.2,再经硫化床自然氧化和混凝沉淀处理,去除悬浮物,排水可达排放标准。
由于传统的生物方法对色度的去除往往不够理想,国内外许多学者致力于培育或改良高降解活性菌种用于印染废水处理,产生了生物强化技术。
其机理为向废水处理系统中投加自然界中的优势菌种或通过基因组合技术产生的高效菌种,增强生物量,强化生物量的反应,以去除某一种或某一类有害物质为目的。
目前,生物强化技术最普遍的应用方式是直接投加对目标污染物具有特效降解能力的微生物。
2.2 高新技术的应用和实践2.2.1 光化学氧化法光化学氧化法由于其反应条件温和(常温、常压)、氧化能力强和速度快等优点。
光化学氧化可分为光分解、光敏化氧化、光激发氧化和光催化氧化四种。
目前研究和应用较多的是光催化氧化法。
光催化氧化技术能有效地破坏许多结构稳定的生物难降解的有机污染物,具有节能高效、污染物降解彻底等优点,几乎所有的有机物在光催化作用下可以完全氧化为CO2、H2O 等简单无机物。
但是光催化氧化方法对高浓度废水效果不太理想。
关于光催化氧化降解染料的研究主要集中在对光催化剂的研究上。
其中,TiO2 化学性质稳定、难溶无毒、成本低,是理想的光催化剂。
传统的粉末型TiO2 光催化剂由于存在分离困难和不适合流动体系等缺点,难以在实际中应用。
近年来,TiO2 光催化剂的搀杂化、改性化成为研究的热点。
2.2.2 膜分离技术膜分离技术处理印染废水是通过对废水中的污染物的分离、浓缩、回收而达到废水处理目的。
具有不产生二次污染、能耗低、可循环使用、废水可直接回用等特点。
膜分离技术虽然具有如此多的优点,但也存在着尚待解决的问题,如膜污染、膜通量、膜清洗、以及膜材质的抗酸碱、耐腐蚀性等问题,所以,现阶段运用单一的膜分离技术处理印染废水,回收纯净染料,还存在着技术经济等一系列问题。
现在膜处理技术主要有超滤膜,纳米滤膜和反渗透膜。
膜处理对印染废水中的无机盐和COD 都有很好的去除作用。
3 结语随着排放标准的日益严格,各国学者在印染废水的处理技术方面进行了深入的探索。
相信随着科学技术的不断进步,印染废水的处理工艺将逐渐完善,投资省、运行费用低、操作简单的处理技术将给印染废水的处理带来新的希望。
Dyeing Wastewater Treatment Abstract: This paper analyzes the treatment of dyeing wastewater issues facing, and describes methods of dyeing wastewater treatment progress and trends. And pointed out that different methods of dyeing wastewatertreatment is a combination of effective treatment of dyeing wastewater. Keywords: Dyeing wastewater; treatment As the textile industry has the advantage of one of the traditional pillar industries, the 20th century was the rapid development since the 90s, its water consumption and discharge are greatly increased. According to incomplete statistics, China's daily discharge dyeing wastewater capacity 3000-4000kt, is the big one of the sewage industry. Strengthen the printing and dyeing wastewater treatment can ease the severe shortage of water resources issues, protection of the environment, maintain ecological balance plays a very important role. A printing and dyeing wastewater treatment problems 1.1, the increasingly stringent emission standards With the development of social economy and people's environmental awareness, our increased investment in printing and dyeing wastewater treatment. According to "textile dyeing and finishing of industrial water pollutant discharge standards", in addition to class Ⅲeffluent changed little, the state increased the class Ⅰand Ⅱdyeing wastewater effluent BOD, COD, color, suspended solids, ammonia, aniline, Chlorine dioxide emission limits and other indicators. The general water quality printing and dyeing wastewater average COD800-2000mg / L, chroma 200-800 times, pH, 10-13, BOD / COD for the 0.25-0.4, so printing is a printing and dyeing wastewater discharge standards in the industry need to solvethe problem. 1.2 The difficulties in printing and dyeing wastewater treatment 1.2.1 components of complex printing and dyeing wastewater Printing and dyeing wastewater refers to the process of dyeing process wastewater discharged by each process a mixture of mixed wastewater. Include: pre-processing stage (such as singeing, desizing, scouring, bleaching, mercerization) emissions desizing, scouring, bleaching, mercerization wastewater; dyeing stage of dyeing wastewater discharge; printing stage of waste water and discharge printing soaping wastewater; finishing stages of finishing wastewater discharge. Quality printing and dyeing wastewater with raw materials, production varieties, production technology and management level vary, leading to various printing and dyeing process wastewater discharge summary after the component is very complex. With the rapid development of industrial dyes and finishing technology, new additives, dyes, finishing agents in the dyeing industry, being used extensively in refractory toxic organic content are more and more, and some are carcinogenic, mutation, resulting in distortion of the organic matter, on the environment especially the water environment of threats and hazards is growing. Overall, the printing and dyeing wastewater is characterized by complex composition, organic matter content is high, dark color and chemical oxygen demand (COD),whereas the biochemical oxygen demand (BOD5) is relatively low, poor biodegradability, emission volume. 1.2.2 the limitations of printing and dyeing wastewater treatment 80 years ago, our printing and dyeing wastewater biodegradability higher, CODcr often concentration 800mg / L the following, using the traditional biological and physico-chemical co-treatment system, effluent discharge standards can be achieved. Past two decades, water quality printing and dyeing wastewater has undergone great changes. Traditional printing and dyeing wastewater treatment methods, such as adsorption, suspension, filtration, coagulation and other features simple, easy tooperate and process the advantagesof maturity, but such treatment is usually to transfer organic matter from liquid to solid or gas, not only did not complete elimination of organic pollutants and consumption of chemicals and pollution caused by waste accumulation and secondary; biological methods can only remove the printing and dyeing wastewater BOD, COD, especially for toxic and refractory organics and color out of little effect. Single approach can not meet the current requirements of the development of dyeing wastewater. 2 Printing and Dyeing Wastewater Treatment and Trends 2.1 traditional methods and process improvement 2.1.1 Adsorption Assay suitable for low-depth treatment of dyeing wastewater with lowinvestment, which is simple and low cost, suitable for small and medium sized printing and dyeing wastewater. Traditional activated carbon adsorbent is mainly activated carbon only cationic dyes, direct dyes, acid dyes, reactive dyes and other water-soluble dye has good adsorption properties, but not removal of colloidal hydrophobic dyes, and the high cost of renewable so that the application of activated carbon is limited. In recent years, research focused mainly on the development of new adsorbents and new adsorbent for improvement on the traditional side. 2.1.2 Coagulation Coagulation with low investment costs, equipment, small footprint, processing capacity, decolorization rate and so on. Coagulants are inorganic coagulants, organic coagulants and biological coagulant. Traditional coagulation decolorization efficiency on hydrophobic high. It requires change with changes in feed water quality conditions, the decolorization effect of hydrophilic poor, COD removal rate. How to choose an effective coagulation process and efficient coagulant, it is the key to the technology. 2.1.3 Chemical Oxidation Study of chemical oxidation is more mature approach. Oxidant commonly used Fenton reagent (Fe2, H2O2), ozone, chlorine, sodium hypochlorite, etc.. According to the different oxidants, chemical oxidation can be divided into: ozone oxidation and Fenton's reagent oxidation. Ozonationdoes not produce sludge and secondary pollution, high costs, however, not suitable for large flow waste water treatment, and CODcr removal rate. Seldom a single ozone treatment of dyeing wastewater, but will combine it with other methods, complementary to each other to achieve the best wastewater treatment effects. Wang Xiaojun et al [13] with ozone biological aerated filter wastewater treatment process 2.1.4 Electrochemical Electrochemical method has the equipment, small, small footprint, simple operation and management, CODcr removal rate and the bleaching of high and good, but the precipitation formation and consumption of large electrode materials, higher operating costs. The traditional electrochemical methods can be divided into electric flocculation, electric float, electro-oxidation and micro-electrolysis, electrolysis within the law. Many foreign researchers from the developing electrode materials with high electrocatalytic activity to proceed, on the organic electro-catalytic oxidation mechanism of influencing factors and a more systematic application of theoretical study and preliminary research, the domestic research in this field has just started. 2.1.5 biological treatment Biological treatment include aerobic and anaerobic methods. Currently the main method of dyeing wastewater using aerobic treatment. Divided into aerobic activated sludge and biofilm. A large number of both activated sludge decomposition of organic material, but also remove some color, you can fine-tune the pH value, high efficiency and low cost of operation, effluent quality is better suited to deal with printing and dyeing wastewater with higher organic matter content; biofilm decolorization of dyeing wastewater than the activated sludge process. However, there are three biological methods can not solve its own problems: ①Department of residual sludge in higher costs; ②single-use biological Ji can not meet the needs of practical application; ③sometimes necessary to add afront-end to improve its wastewater biodegradability pretreatment, to improve the investment and operating costs. Only a single aerobic biological treatment to remove part of readily biodegradable wastewater organic matter, color can not solve the problem. In order to reduce consumption and waste removal more difficult to degrade organic pollutants in the emergence of anaerobic - aerobic treatment process and the new biological technology. Anaerobic - aerobic anaerobic process can start with the acid production phase to remove part of the easily degradable organic pollutants, degradation of macromolecules will be more difficult to decompose organic matter to simpler organic molecules, and through aerobic biological treatment process to further remove. Anaerobic - aerobic treatment of biodegradable wastewater was difficult with the removal of pollution, high efficiency, stable and strong resistance capacity and so on. Studies have reported that anaerobic - aerobic process of dyeing wastewater, the influent CODcr to 1085mg / L, BODS to 315mg / L in the case, both the removal rate up to 83.9 and 76.2, respectively, and then by fluidized bed natural oxidation and coagulation treatment to remove suspended solids, water up to emission standards. The traditional biological method of color removal is often not ideal, many domestic and foreign scholars dedicated to nurturing high-degradation activity of bacteria or improved treatment of dyeing wastewater, resulting in a bioaugmentation. The mechanism for the wastewater treatment system to increase the dominant species in nature or produced through genetic technology and efficient combination of bacteria, increased biomass, enhanced biomass response to removal of a particular hazardous substance or class of purpose. At present, the biological technology is the most common application form directly to the target dosage degradation of pollutants with the effects of microorganisms. 2.2 The application and practice of high-tech 2.2.1 Photochemical Oxidation Photochemical oxidation due to its mild reaction conditions (ambient temperature and pressure), oxidation capability and speed advantages. Photochemical oxidation of decomposition can be divided into light, photosensitization oxidation, light excitation of four oxidation and photocatalytic oxidation. More current research and application ofphotocatalytic oxidation is. Photocatalytic oxidation can effectively destroys many structural stability Di difficulty to the degradation of organic pollutants, Juyou energy efficiency, pollution and other degradation Chedi advantages, almost all of the organic matter in the next Ke Yi Guang complete oxidation catalyst for the CO2, H2O and other inorganic Jian Dan material. However, the photocatalytic oxidation effect of high concentrations of waste water is not ideal. On the photocatalytic degradation of dyes in the light focused on the study of catalysts. Which, TiO2 chemical stability, insoluble non-toxic, low cost, is an ideal photocatalyst. Conventional powder-type TiO2 photocatalyst separation because of the difficulties and shortcomings such as not suitable for mobile systems, it is difficult to apply in practice. In recent years, TiO2 photocatalyst mixed technology, modification of a hot topic. 2.2.2 Membrane Separation Technology Membrane separation technology of dyeing wastewater by the pollutants in wastewater the separation, concentration and recovery of waste water treatment to achieve the purpose. With no secondary pollution, low energy consumption, can be recycled, wastewater reuse, etc directly. Although membrane separation technology has so many advantages, but there are also unresolved problems, such as membrane fouling, membrane flux, membrane cleaning, and acid resistant membrane material, corrosionresistance and other problems, so at this stage the use of a single membrane separation technology of dyeing wastewater, recycling pure dyes, there are still technical and economic andother issues. Now membrane ultrafiltration membrane treatment technologies, nano-filtration membrane and reverse osmosis membrane. Membrane Treatment of dyeing wastewater salts and COD removal are very good role. 3 Conclusion With increasingly stringent emission standards, national scholars in the printing and dyeing wastewater treatment technologies in-depth exploration. We believe that with the continuous progress of science and technology, printing and dyeing wastewater treatment process will be gradual improvement, investment, low cost, simple processing technology Wastewater treatment will bring new hope.1。