模具侧向抽芯
模具抽芯

第八节:抽芯机构设计一`概述当塑料制品侧壁带有通孔凹槽,凸台时,塑料制品不能直接从模具内脱出,必须将成型孔,凹槽及凸台的成型零件做成活动的,称为活动型芯。
完成活动型抽出和复位的机构叫做抽苡机构。
(一)抽芯机构的分类1.机动抽芯开模时,依靠注射检的开模动作,通过抽芯机来带活动型芯,把型芯抽出。
机动抽芯具有脱模力大,劳动强度小,生产率高和操作方便等优点,在生产中广泛采用。
按其传动机构可分为以下几种:斜导柱抽芯,斜滑块抽芯,齿轮齿条抽芯等。
2.手动抽芯开模时,依靠人力直接或通过传递零件的作用抽出活动型芯。
其缺点是生产,劳动强度大,而且由于受到限制,故难以得到大的抽芯力、其优点是模具结构简单,制造方便,制造模具周期短,适用于塑料制品试制和小批量生产。
因塑料制品特点的限制,在无法采用机动抽芯时,就必须采用手动抽芯。
手动抽芯按其传动机构又可分为以下几种:螺纹机构抽芯,齿轮齿条抽芯,活动镶块芯,其他抽芯等。
3.液压抽芯活动型芯的,依靠液压筒进行,其优点是根据脱模力的大小和抽芯距的长短可更换芯液压装置,因此能得到较大的脱模力和较长的抽芯距,由于使用高压液体为动力,传递平稳。
其缺点是增加了操作工序,同时还要有整套的抽芯液压装置,因此,它的使用范围受到限制,一般很小采用。
(二)抽芯距和脱模力的计算把型芯从塑料制品成型僧抽到不妨碍塑料制品脱出的僧,即型芯在抽拔方向的距离,称为抽芯距。
抽芯距应等于成型孔深度加上2-3MM.一.抽芯距的计算如图3-102所示。
计算公式如下:S=Htgθ(3-26)式中S------ 抽芯距(MM)H------ 斜导柱完成抽芯所需的行程(MM)θ----- 斜导柱的倾斜角,一般取15·~20·2.脱模力的计算塑料制品在冷却时包紧型芯,产生包紧力,若要将型芯抽出,必须克服由包紧力引起的磨擦阻力,这种力叫做脱模力,在开始抽芯的瞬间所需的脱模力为最大。
影响脱模力因素很多,大致归纳如下;(1) 型芯成型部分表面积和断面几何形状:型芯成型部分面积大,包紧力大,其模力也大;型芯的断面积积形状时,包紧力小,其脱模也小;型芯的断面形状为矩形或曲线形时,包运费力大,其脱模力也大。
十字头塑件无顶出侧向分级抽芯注射模设计

・
塑 料 注 射 模 技 术 ・
S 憾 I由 超 1梗 , 田 趋 目具 N 国 r
CHI A . N  ̄UR N I M O U LD I
十字头塑件无顶 出侧 向分级抽 芯注射模设计
西仪 集 团有 限责 任 公 司工模 具厂 ( 西西安 陕 708) 10 2 刘 黛鹂
1 制品 工 艺分 析
十字 头塑 件是 搭 建农 用 塑 料 薄 膜 大棚 时 , 骨 架 其 之 间 的连接 件 , 其外形 如 图 1所示 。
设 计成 塑料 件, 用 注塑 成 型 。 采 这种 外形 塑件 的 注射模 需 要 多 面 抽 芯 , 仅 夹 持 圈 的型 芯 要 抽芯 , 有纵 横 不 还 交错 的螺 钉 过孑 都 需 要侧 抽 芯 , 具 总体 结构 设 计有 L 模 相 当难 度 , 比较 复 杂 , 了简 化 结 构 , 约 成 本 , 也 为 节 对 其 模具 总 体结 构 的确定 分 别论 述 如下 。
图 1 十 字头 塑 件
型 芯放 在 开 模 方 向 , 由开 模 力 实 现 其 抽 芯 , 余 方 向 其 塑件 为纵 横 交错 呈 十字 形 、 用来 夹 持 骨 架杆 件 的 开 E圆圈 , 圆 圈开 E的末 端 设 有 凸缘 ,了使 纵 向夹持 圈真 正 起 夹持 作 用 , 须 让 L 必 的成 型 由侧抽 芯完 成 。 连 续贯 通 的夹持 圈所需 抽拔 该
【 要 】针 对十 字 头塑件 外形 特殊 , 用方形斜 导 柱无顶 出、 向分级抽 芯 结构模 具 , 具结 摘 采 侧 模
构 简便 、 效 。 有 关键 词 : 向分级 抽 芯 ; 顶 出; 侧 无 方形斜 导柱 ; 弹簧 ; 复位 ; 涉 干
侧抽芯机构的模具设计.ppt

塑料成型工艺 与模具设计
二、相关知识
4、侧抽芯机构的设计 (1)斜导柱设计
a.斜导柱的形状及技术要求
材料:T8、T10或20 渗碳淬火; 硬度>HRC55
塑料成型工艺 与模具设计
二、相关知识
4、侧抽芯机构的设计 (1) 斜导柱设计 a.斜导柱的形状及技术要求
下图可减小斜导柱与滑块的摩擦,b=0.8d
(1) 斜导柱设计 c.斜导柱长度计算
L l1 l2 l4 l5 D tan ha S抽 (5 ~ 10)mm
2
cos sin
塑料成型工艺 与模具设计
二、相关知识
4、侧抽芯机构的设计 (1) 斜导柱设计 d.斜导柱直径计算
斜导柱直径(d)取决于它 所受的最大弯曲力(F弯)
Ft Fc Ap( cos sin ) 脱模力和抽拔力
塑料成型工艺 与模具设计
问题:
观察下列塑件有什么特点?
塑件上有侧向孔、侧向凸凹、侧向的凸台
塑料成型工艺 与模具设计
一、 项目导入
某企业小批量生产食品盒盖,要求盒盖有足够的强度和耐磨性能,外 表面无瑕疵、美观、性能可靠,要求设计一套成型该塑件的模具。通 过本项目,完成对塑件材料的选择及对材料使用性能和成型工艺性能 的分析。
按注射机的最大注射量确定型腔数n1 n1 ≤
式中: k — 最大注射量的利用系数,一般取0.8;
mmax— 注射机的最大注射量,cm3; mj— 浇注系统及飞边体积或质量,cm3; mi— 单个塑件的体积或质量,cm3。
分析结论:采用一模两腔。由于产品结构简单,凹模和型芯结构简单,加工 方便,确定采用整体式凹模和型芯,在凹模上装配两个小型芯。成型零件尺寸 计算:略,参看项目1。
塑料模具_抽芯机构讲解
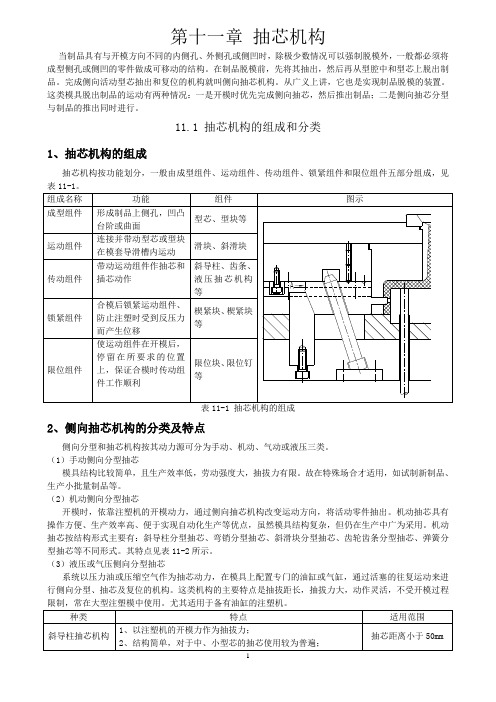
第十一章抽芯机构当制品具有与开模方向不同的内侧孔、外侧孔或侧凹时,除极少数情况可以强制脱模外,一般都必须将成型侧孔或侧凹的零件做成可移动的结构。
在制品脱模前,先将其抽出,然后再从型腔中和型芯上脱出制品。
完成侧向活动型芯抽出和复位的机构就叫侧向抽芯机构。
从广义上讲,它也是实现制品脱模的装置。
这类模具脱出制品的运动有两种情况:一是开模时优先完成侧向抽芯,然后推出制品;二是侧向抽芯分型与制品的推出同时进行。
11.1 抽芯机构的组成和分类1、抽芯机构的组成抽芯机构按功能划分,一般由成型组件、运动组件、传动组件、锁紧组件和限位组件五部分组成,见表11-1 抽芯机构的组成2、侧向抽芯机构的分类及特点侧向分型和抽芯机构按其动力源可分为手动、机动、气动或液压三类。
(1)手动侧向分型抽芯模具结构比较简单,且生产效率低,劳动强度大,抽拔力有限。
故在特殊场合才适用,如试制新制品、生产小批量制品等。
(2)机动侧向分型抽芯开模时,依靠注塑机的开模动力,通过侧向抽芯机构改变运动方向,将活动零件抽出。
机动抽芯具有操作方便、生产效率高、便于实现自动化生产等优点,虽然模具结构复杂,但仍在生产中广为采用。
机动抽芯按结构形式主要有:斜导柱分型抽芯、弯销分型抽芯、斜滑块分型抽芯、齿轮齿条分型抽芯、弹簧分型抽芯等不同形式。
其特点见表11-2所示。
(3)液压或气压侧向分型抽芯系统以压力油或压缩空气作为抽芯动力,在模具上配置专门的油缸或气缸,通过活塞的往复运动来进行侧向分型、抽芯及复位的机构。
这类机构的主要特点是抽拔距长,抽拔力大,动作灵活,不受开模过程11.2 抽芯机构的设计要点1、模具抽芯自锁自锁:自由度F≥1,由于摩擦力的存在以及驱动力方向问题,有时无论驱动力如何增大也无法使滑块运动的现象称为抽芯的自锁。
在注塑成型中,对于机动抽芯机构,当抽芯角度处于自锁的摩擦角之内,即使增大驱动力,都不能使之运动,因此,模具设计时必须考虑避免在抽芯方向上发生自锁。
注塑模具设计抽芯

§4.5侧向分型与抽芯机构
四、斜滑块分型抽芯机构
2.导杆导滑的分型抽芯机构
导杆导滑外侧分型抽芯
24
§4.5侧向分型与抽芯机构
四、斜滑块分型抽芯机构
2.导杆导滑的分型抽芯机构
导杆导滑内侧分型
25
§4.5侧向分型与抽芯机构
五、其它抽芯机构
弯销分型抽芯机构
斜槽导板分型抽芯机构
直摆杆抽芯机构
多角度抽芯机构
三、斜导柱分型抽芯机构
适于抽拔距离短、抽拔力小的情况,应用广泛。
常见形式
干涉现象
先行复机构
定距分型机构
3
§4.5侧向分型与抽芯机构
三、斜导柱分型抽芯机构
1.斜导柱抽芯的常见形式
斜销在定模、滑块在动模
4
§4.5侧向分型与抽芯机构
三、斜导柱分型抽芯机构
1.斜导柱抽芯的常见形式
斜销在动模、滑块在定模
连杆先行复位机构
弹簧先行复位机构
11
§4.5侧向分型与抽芯机构
三、斜导柱分型抽芯机构
5.先行复位机构
三角滑块式先行复位机构
12
§4.5侧向分型与抽芯机构
三、斜导柱分型抽芯机构
5.先行复位机构
摆杆先行复位机构
13
§4.5侧向分型与抽芯机构
三、斜导柱分型抽芯机构
5.先行复位机构
连杆先行复位机构
14
滑块在定模的情况下,为了保证塑件留在动模一侧,开模 前要先抽出侧向型芯,因此要采用定距分型拉紧机构。
41
§4.5侧向分型与抽芯机构
六、斜导柱抽芯分型机构的设计与制造
2.斜导柱抽芯分型机构设计
抽拔力和抽芯距
抽拔力:与脱模力相同 抽芯距(S抽):
塑料模具选修课件:第11章 侧向分型与抽芯机构

第十章侧向分型与抽芯机构§10.1 侧向分型与抽芯机构的分类及组成§10.2 抽芯力与抽芯距的确定§10.3 斜导柱侧向分型与抽芯机构§10.4 弯销侧向分型与抽芯机构§10.5 斜导槽侧向分型与抽芯机构§10.6 斜滑块侧向分型与抽芯机构§10.7 齿轮齿条侧向分型与抽芯机构§10.8 弹性元件侧向分型与抽芯机构§10.9 手动侧向分型与抽芯机构§10.10 液压或气动侧向分型与抽芯机构观察下列塑件有什么特点?塑件上有侧向孔、侧向凸凹、侧向凸台——“倒扣”(undercut)侧孔Ø侧型芯:当塑件上具有与开模方向不同的内外侧孔或侧凹等结构阻碍塑件直接脱模时,必须将成型侧孔或侧凹的零件做成活动结构的零件。
Ø侧向抽芯机构:侧向成型杆、成型块应在开模时首先从制件中抽出,才能推出制品。
完成侧向成型杆及成型块抽芯、复位的机构统称侧向抽芯机构。
§10.1 侧向分型与抽芯机构的分类及组成1、侧向分型与抽芯机构的分类–按动力来源分类:Ø机动侧向分型与抽芯机构Ø液压或气动侧向分型与抽芯机构Ø手动侧向分型与抽芯机构1)机动侧向分型与抽芯机构–机动抽芯依靠注射机的开模力(或推出力),通过传动机构改变运动方向,将侧向的活动型芯抽出;合模时,又靠传动零件使侧向成型零件复位。
–特点:模具结构比较复杂,但抽芯不需人工操作,抽拔力较大,具有灵活、方便、生产效率高、容易实现全自动操作、无需另外添置设备等优点,在生产中被广泛采用。
l机动侧向抽芯机构按结构形式的分类:Ø斜导柱(斜销)侧向分型与抽芯机构Ø弯销侧向分型与抽芯机构Ø斜导槽侧向分型与抽芯机构Ø斜滑块侧向分型与抽芯机构Ø齿轮齿条侧向分型与抽芯机构Ø弹性元件侧向分型与抽芯机构2)液压或气动侧向分型与抽芯机构–侧向分型的活动型芯可以依靠液压传动或气压传动的机构抽出。
模具毕业设计75壳体侧抽芯注塑模设计

目录1 前言 (1)2 绪论 (2)2.1概述 (2)2.2我国塑料模现状 (2)2.3 我国塑料模的发展趋势 (3)3 塑件成型工艺分析 (5)3.1 塑件图 (5)3.2 塑件工艺分析 (5)3.2.1 精度等级 (5)3.2.2 脱模斜度 (5)3.2.3 塑件圆角 (6)3.3 ABS塑料性能特性与工艺参数 (6)3.3.1 ABS化学与物理特性 (6)3.3.2 ABS塑料的成型条件 (7)4 拟定模具结构形式 (8)4.1 型腔数目的确定 (8)4.2 分型面的选择 (9)5注塑机型号的确定 (11)5.1 注塑容量的计算 (11)5.2锁模力的计算 (11)5.3 注塑机的选用 (12)5.4 有关参数的校核 (13)5.4.1由注塑机料筒速率校核模具的型腔数 (13)5.4.2 注射压力的校核 (13)5.4.3 锁模力的校核 (13)5.4.4 开模行程的校核 (14)6 浇注系统的设计 (14)6.1 主流道的设计 (15)6.2 分流道的设计 (17)6.3 冷料穴的设计 (19)6.4 浇口的设计 (20)6.4.1浇口类型的选择 (20)6.4.2 浇口尺寸的确定 (22)6.4.3 浇口剪切速率的校核 (23)6.5 排气系统的设计 (23)7 成型零件设计 (23)7.1 成型零件的结构设计 (24)7.2 成型零件钢材的选用 (25)7.3 成型零件工件尺寸的计算 (26)7.4 型腔壁厚和底板厚度的计算 (29)7.4.1 侧壁厚度计算 (29)7.4.2 底板厚度计算 (30)8 模架的确定 (32)9 导向机构的确定 (32)10 脱模机构的设计 (34)10.1 脱模力的计算 (34)10.2 脱模机构的结构设计 (35)11 侧向抽芯的设计 (37)11.1 抽芯距与抽芯力的计算 (37)11.2 斜导柱圆形截面直径的计算 (40)11.3 斜导柱圆长度的计算 (40)11.4 斜滑杆的设计 (41)12 模温调节系统的设计 (42)12.1 冷却系统的设计 (42)13 数控程序的编制 (47)14 设计小结 (49)参考文献 (50)致谢 (51)1 前言模具是工业生产的基础工艺装备,被称为工业之母。
注塑模具斜侧抽芯机构的设计

Science &Technology Vision科技视界0前言在塑料模具产品中,有些产品的侧壁存在孔和凸台,产品成型后这些部位阻碍产品的出模,产品没有办法顶出,这种现象在模具设计中属称倒扣。
在模具设计中倒扣有很多中类型有内倒扣、外倒扣,而外倒扣还分为与PL 面平行型的水平倒扣和与PL 面成一定角型的斜型倒扣,其中斜型倒扣在模具设计中是最难解决的一种倒扣,本文以夹式台灯的上夹盖为例,论述斜型倒扣的斜侧滑块机构设计。
1模具及塑料产品分析图11.1塑料产品分析如图1所示的产品材料为ABS,塑料件属于外观件,如图所提示的斜孔与产品的水平方向的角度为45度,斜孔的倒扣深度为3mm,必须采用斜侧抽芯机构才可以顺利脱模。
1.2模具分析从塑料产品的结构分析可以看出该塑件模具的结构特点为:塑料产品的倒扣成型应设计在定模侧;制件属于外观件;倒扣深度不深并具成型面积不大。
2斜侧抽芯机构设计与原理分析图2夹式台灯夹盖的模具结构图1.浇口套;2.定模固定板;3.A 板;4.拔杆;5.斜侧滑块;6.斜侧滑块镶件7.拉料杆;8.定模仁;9.动模仁;10.B 板;11.顶针;12.弹簧;13.限位螺丝;14.面针板;15.底针板;16.动模固定板;17.大拉杆;18.导套根据夹式台灯上下盖的产品要求设计出来的模具结构图如图2所示,从该结构图可以看出,斜侧抽芯机构主要是由拔杆、斜侧滑块、斜侧滑块镶件等三大部件组成整个结构,拔杆与斜侧滑块部件主要是由T 型槽进行配合。
在模具注塑成型后,由于2定模固定板与3型腔板(A 板)之间有12弹簧的弹力作用下,模具分型面PL1先开,由于4拔杆固定在2定模固定板上,所以随着分型面PL1的分开斜锁紧块向开模方向作垂直(与地平面垂直)运动,运动距离在限位螺丝13的限位下,分开6.5mm 的距离后PL1处暂不分开状态。
在PL1分开6.5mm 后,由于拔杆与斜侧滑块是以T 型槽进行配合,所以斜侧滑块与斜侧滑块镶件在拔杆的运动力下,作与分型线夹角45度的运动,使得斜侧滑块镶件与产品分开,如图3所示的效果。
- 1、下载文档前请自行甄别文档内容的完整性,平台不提供额外的编辑、内容补充、找答案等附加服务。
- 2、"仅部分预览"的文档,不可在线预览部分如存在完整性等问题,可反馈申请退款(可完整预览的文档不适用该条件!)。
- 3、如文档侵犯您的权益,请联系客服反馈,我们会尽快为您处理(人工客服工作时间:9:00-18:30)。
1
图 1.1.1 行位设计要点 一 设计时应考虑下列各点:
1.1 压块藏位 A 最小深度大于 1/3 的压块高度 1.2 压块高度 B,宽度 C 按表 2.1.1 选用,长度以实际行 位的长度来决定,并保证开模后压块能压住 2/3L 的行位。 压块螺丝用M6.M8.M10。特殊情况除外。 1.3 斜导柱角度 E 为(10°15°20°25°) 1.4 行位斜角 F 比斜导柱角大 2° 1.5 用圆头斜导柱,直径 D 可用8,10,12,14,16,20,24。 与行位孔的配合间隙单边为 0.5 1.6 设计时行位行程 T 要比所需行程 S 预多(2~5)mm
16
i. 行位座与弯梢装配时,要特别注意尺寸 B 与 B1 的关系,应为 B>B1,但为了装配 的顺畅,也可将其行位座后模板部分全部挖通。
图 3.10.4 4.双"T"槽的计算公式及注意事项:
17
如上图中 S3=H*tg; (H 为行位下降的高度即小拉杆行程;为弯梢角度) S2=2*cos; (2 为弯梢与行位间隙,一般为 0.5mm) S=S3-S2=H*tg-2*cos=(H*sin-2)/cos; (S 为行位水平运动距离) S4=1/cos; (1 行位入子与行位间隙隙;为行位镶件倾斜角度) S1=(H*sin-1)/sin(+); (为勾槽间隙,一般为 0.5mm;S1 为行位镶件脱离倒 勾距离) 注意事项: a. 装配要求:行位镶件与倾斜的镶件孔装配,要特别注意尺 寸 A 与 A1 的关系,
14
图 3.10.2 15
3.设计注意事项
图 3.10.3 a.上固定板的厚度 H2≧1.5D(D 为大拉杆直径;大拉杆直径计算同三板模大拉杆
计算;H2 上固定板的厚度 b.弯梢镶入上固定板深度 H≧2/3H2 c.注口衬套头部要做一段锥度,以便合模。且要装在上固定板上,以防止成型机
止的喷嘴脱离注口衬套,产生拉丝现象不便取出,影响下一次注射。 d.弯梢在前模板内要逃料。 e.耐磨板要高出前模板 0.5mm,保护前模板。以及支撑弯梢防止拨块受力变形。 f.小拉杆限位行程 S2/3H1,以利合模。(H1 为行位高度) g.弯梢前端最好装固定块,易调整,易加工,构成三点支撑,增加拨块强度。 h.要使耐磨块装配顺利,要求点 E 在点 D 右侧。如下图所示:
带动行位做抽芯运动.
4
3.2: 组合式行位
图 3.2.1
说明: 1 优点:型芯由镶件与行位固定,容易加工,便于安装与改模,利于排气,提
高产品表面质量. 2 缺点:因各组件是组合式的,所以加工精度要高,以保证产品精度,行位滑
动顺畅. 3 适用场合:此种机构适用于行位多镶件、镶针时。
注意行位的冷却水道不得与连接螺丝干涉。
5
3.3: 延时行位(设计时加大斜导柱避空孔)
说明:
1
优点: 可控制行位在开模至一定距离后才开始做抽芯运动,从而使产品顺利脱 离前模,避免产品跟前模
2 缺点:须控制好开模距离 L,以避免行位产生干涉现象而无法开模。
3 适用场合:此种机构适用于一般啤件扣前模
6
3.4: 前模斜弹行位
说明:
前模斜弹行位的结构一般由导滑件、弹弓、限位件、行位、后模、耐磨板组成。宽度超过 250mm 时,需在行位底中间加导向条。 当行位 Z 宽度超过 100mm 时,要考虑做两支斜导柱。
图 2.1.2
3
行位的组合形式 3.1: 普通行位
说明:
图 3.1.1
1 优点:此种型式行位结构简单、加工方便、易装配,抽芯稳定
2 缺点:设计时应考虑行位的大小,从而决定是用斜导柱或是 T 形块、燕尾槽
9
3.7: 前模行位(1)
图 3.7.1 说明:
1 优点:可以使啤件的前模倒扣完成抽芯后,主分型面再开模.结构简单,制作方便. 2 缺点:设计时要控制好模具的开模顺序及行位的定位锁紧方式. 3 适用场合:适用于一般的前模行位.
10
3.8: 带顶针行位
注意:
图 3.8.1
1 优点:可用顶针控制行位在绝大部分脱离啤件一段距离后行位才全部脱离啤件,
提高啤件成形质量.可减轻行位自重.铲鸡可原身出, 亦可镶一块小铲基,以
便于加工斜导柱孔.
2 缺点:行位较大,体积较重,要注意行位的导向和定位.
3 适用场合: 此种机构在行位较大,啤件侧面薄壁深孔时可使用,为防止啤件抽芯
时变形或损坏.
11
3.9: 前模行位(2)
产品一侧歪斜且
内侧有齿形扣位 12
扣鸡组件
行位概述及构成
一: 行位
用途:塑造成品内外部的倒扣位置 钢材:多数情况不能与内模同料,若需与内模同料,行位必须氮化。
二: 行位的构成
Ⅰ 滑块一般由以下几部分组成:(见下图 1.1.1) 1. 动力部分如:斜导柱. 弯梢. 油缸. T 形块等; 2. 锁紧部分如:铲鸡. 弯梢等; 3. 定位部分如:波仔螺丝. 内置弹弓. 外置弹弓. 滑块扣等; 4. 导滑部分如:导滑耐磨板. 压条等; 5. 成形部分如:滑块等。
开模时,在拉勾和弹弓的作用下使行位在导滑件的 T 形槽滑动,同时行位
沿抽芯方向移动完成抽芯动作。此时拉勾脱离耐磨板 1,由行程螺丝定位。
a=15°、18°、20°、23° S1S+(3~5) S1S2+2
S1─ 行位抽芯长度;S─ 啤件凹位的深度;S2─ 拉勾的行程
7
4.5 拉勾(前模斜弹行位)
图4.19
2 缺点:产品倾斜部位角度不可太大, 30º.结构复杂,加工难度高
3 适用场合: 产品结构比较特殊,一端以一定角度歪斜面,且有内侧扣位
13
3.10: 前模行位(3)
1. 应用特点 a.制品倒勾成型在前模侧 b.制品外观不允许有夹线 c.行位成型面积不大 如下图所示:
图 3.10.1 2.前模遂道行位简图如下
表 4.5
说明: 1 材料用油钢,淬火至 HRC54~58; 2 未注内转角处需倒角 0.5,以免淬火后裂开。 8
3.6: 液压抽芯
说明: 1 优点:行位抽芯稳定可靠,行程比较大 2 缺点:油缸一般安装在模具外面,体积较大,在运输、模具安装时要注意跟其它
物体发生碰撞而损坏油缸. 3 适用场合:适用于行位行程大于 40mm 的行位抽芯
说明:
1 优点:可完成产品的斜向内侧倒扣的抽芯.开模时,前模斜抽铲鸡在前模斜抽
连接块的作用下做斜向抽芯运动,从而带动前模斜抽行位 1 和 2 向内侧运动,完
成螺纹形扣位抽芯。继续开模至一定距离后,前模斜抽压块脱离扣鸡组件的控制,
在前模斜抽行位的作用下与前模斜抽连接块一起做斜向抽芯运动,从而完成整个
抽芯动作。