提高中厚板成材率的措施
中厚板产能提升分析及改进措施

中厚板产能提升分析目标:日轧制量达到5000t/日,月均日产稳定在4500t/日以上;月轧制量13.5万吨/月,月商品量大于12万吨。
一、生产能力1、产品结构2、加热轧制能力3、实际生产水平4、产能提升目标二、问题分析中厚板年修及工程技改技措项目投产后,通过中间冷却和轧线自动化系统优化,单块钢的轧制节奏由原来的19.3块/小时提升至23.8块/小时,达到国内平均水平22~24块/小时。
轧机能力略大于加热炉能力,已具备品种钢大于4500吨/天和日产5000吨能力。
影响日产量的因素:板坯单重、轧制节奏、作业率,主要是轧制节奏,关键是轧制计划的集批生产。
1、板坯单重:受坯型限制及品种钢占比增加,板坯单重减小。
1)普板单重较正常水平10.5t/块减小1吨,主要是中厚板产量大于4#铸机产能,普板改用1#和3#铸机补充250*1490坯型,2月份共轧制2万吨;2)风电钢机型增大,钢板厚度、宽度及单件重增加,受坯型限制,在组板设计时可增加的倍尺数量减少,2月份板坯单重小于8.5吨的品种钢共轧制1万吨。
2、轧制节奏:实际轧制节奏小于加热炉和轧机能力。
1)轧制计划未做到集批生产,三炉品种规格不匹配,块与块的间隙时间增加20~30秒,加热轧制节奏降低10%:炼钢未按炉按状态倒运,中厚板P01库堆放混乱,日计划审核把关不严,板坯质量缺陷及改判率;2)轧制模型及生产操作:轧机负荷分配,轧制操作方式,操作工技能水平,设备状态及运行稳定性。
3、作业率:日历作业率和有效作业率偏低。
1)检修模型:每月定修两大两小,16+8+12+8=48小时,国内平均水平每月2次共24小时,多两次共24小时;设备状态不稳定,检修力量不足,影响检修质量和设备状态,被迫以时间换空间。
2)精轧换辊频次:平均换辊吨位5200吨,每月22次,低于目标值1.5天一换,主要影响因素是品种钢宽板占比高和轧制计划未集批生产。
3)故障热停频次:热停频次2.7次/天,最好水平及国内平均1.5次/天,点检质量、生产操作、设备状态、定修质量等影响生产设备运行稳定性。
中厚板成材率的影响因素与改进措施

中厚板成材率的影响因素与改进措施赵 岩(河北钢铁集团邯钢公司 河北邯郸 056015)摘 要:中厚板成材率的影响因素包括品种规格结构、氧化烧损量、板型控制、钢板厚度负偏差控制、剪切量以及废品率等,在定量分析各因素对成材率影响量的基础上,提出了提高成材率的具体方法。
通过优化板坯加热过程、合理使用AGC厚度控制系统以及平面形状控制系统对厚度和板型进行控制、优化剪切余量控制等一系列措施,邯钢中板厂的中厚板成材率得到稳步提高。
关键词:中厚板;成材率;负差;改进措施INFLUENCING FACTORS AND IMPROVING MEASURES OF MEDIUM AND HEAVY STEEL PLATEZhao Yan(Handan Iron and Steel Group Company Limited of HBIS, Handan 056015,China)Abstract:The influencing factors of the yield of medium thick plate include the variety and specification structure, the amount of oxidized burning, the control of plate shape, the negative deviation control of plate thickness, the shear amount and the rejection rate, etc. On the basis of the quantitative analysis of the influence of each factor on the yield, the specific methods to improve the yield of medium thick plate were put forward. Through optimizing slab heating process, using AGC thickness control system and plane shape control system to control thickness and plate shape, optimizing shear margin control and a series of measures, the yield of medium thick plate in Hangang Middle Plate Plant has been improved steadily.Key words:media and heavy plate;yield rate;negative deviation;improving measures0 前言板材成材率是反映中厚板厂设备水平、人员操作水平和综合管理水平的重要指标。
提高中厚板成材率的方法探讨

分析 和研 究 , 是非 常必要 的 。 2 影 响 中厚板 成 材率 的主 要原 因
量 , 原 料 的 选 择 更 有 利 于 提 高 中厚 板 成 材 率 。 使 配 坯 时要 严 格 根 据 成 品 规 格 合 理 选 择 坯 料 , 于 对
后 缺 陷 。对 检查 的 各种 缺 陷 进行 认 真 清理 。切
中厚 板 生 产 过 程 中 金 属 损 失 有 两 种 类 型 : 一
是物理损耗 , 括切头 、 尾 、 边 , 程废品 、 包 切 切 过 取
Hale Waihona Puke 料 、 尺 和 火 焰 切 割 等 T 序 的 质 量 会 直 接 影 响 产 配 品质量 和成 材率 。
成 材率 是 1原 料能 够 轧 制 }合 格 钢 材重 量 的 t } { 百 分 数 , 反 映 了 钢 材 生 产 过 程 中的 金 属 收 得 情 它
况 。影 响 中 厚板 成 材 率 的主 要 原 因是 生 产 过程 中
不能满足配坯要求的规格 , 必须进行评 审 。选择
坯料 时 应 以单 重 最 大 、 产量 最 高 、 材 率最 佳 为 首 成
选。
的 各 种 金 属 损 失 , 属 损 失 是 中厚 板 厂 生 产 中最 金 重 要 的 消 耗 , 常 金 属 损 失 占产 品成 本 的一 半 以 通 上 , 低 金属 损 失 对节 约 金属 , 高 中厚 板 成 材率 降 提
有重 要 意义 。
() 高钢坯处理 质量 : 原料准备开始 , 3提 从 加 强 质 量 管 理 , 高 钢 坯 处 理 质 量 。减 少 结 疤 等 轧 提
— —
提高中厚板成材率的措施
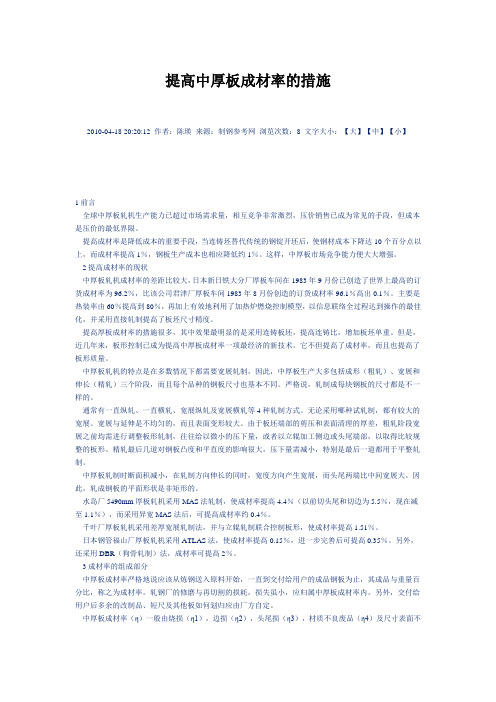
提高中厚板成材率的措施2010-04-18 20:20:12 作者:陈瑛来源:制钢参考网浏览次数:8 文字大小:【大】【中】【小】1前言全球中厚板轧机生产能力已超过市场需求量,相互竞争非常激烈,压价销售已成为常见的手段,但成本是压价的最低界限。
提高成材率是降低成本的重要手段,当连铸坯替代传统的钢锭开坯后,使钢材成本下降达10个百分点以上,而成材率提高1%,钢板生产成本也相应降低约1%。
这样,中厚板市场竞争能力便大大增强。
2提高成材率的现状中厚板轧机成材率的差距比较大,日本新日铁大分厂厚板车间在1983年9月份已创造了世界上最高的订货成材率为96.2%,比该公司君津厂厚板车间1983年8月份创造的订货成材率96.1%高出0.1%。
主要是热装率由60%提高到80%,再加上有效地利用了加热炉燃烧控制模型,以信息联络全过程达到操作的最佳化,并采用直接轧制提高了板坯尺寸精度。
提高厚板成材率的措施很多,其中效果最明显的是采用连铸板坯,提高连铸比,增加板坯单重。
但是,近几年来,板形控制已成为提高中厚板成材率一项最经济的新技术。
它不但提高了成材率,而且也提高了板形质量。
中厚板轧机的特点是在多数情况下都需要宽展轧制,因此,中厚板生产大多包括成形(粗轧)、宽展和伸长(精轧)三个阶段,而且每个品种的钢板尺寸也基本不同。
严格说,轧制成每块钢板的尺寸都是不一样的。
通常有一直纵轧、一直横轧、宽展纵轧及宽展横轧等4种轧制方式。
无论采用哪种试轧制,都有较大的宽展。
宽展与延伸是不均匀的,而且表面变形较大。
由于板坯端部的剪压和表面清理的厚差,粗轧阶段宽展之前均需进行调整板形轧制,往往给以微小的压下量,或者以立辊加工侧边或头尾端部,以取得比较规整的板形。
精轧最后几道对钢板凸度和平直度的影响很大,压下量需减小,特别是最后一道都用于平整轧制。
中厚板轧制时断面积减小,在轧制方向伸长的同时,宽度方向产生宽展,而头尾两端比中间宽展大。
因此,轧成钢板的平面形状是非矩形的。
浅析中厚板毛边板成材率提高的措施

浅析中厚板毛边板成材率提高的措施发布时间:2021-07-02T14:17:15.380Z 来源:《中国科技信息》2021年8月作者:黄可言李章勇[导读] 根据毛边板的交货特点和柳钢中板厂设备情况,要提供毛边板成材率用好平面形状控制系统,使钢板矩形化。
降低钢板同板差,提升负公差轧制率。
柳州钢铁股份有限公司总调度室黄可言李章勇摘要:根据毛边板的交货特点和柳钢中板厂设备情况,要提供毛边板成材率用好平面形状控制系统,使钢板矩形化。
降低钢板同板差,提升负公差轧制率。
关键词:定尺MAS、展宽MAS、同板差、负公差轧制。
前言:根据目前市场形势,柳钢中板厂毛边板的生产量已经超过50%,而毛边板交货特点是没有剪切量的回收,所以毛边板成材率的提高直接产生较大的经济效益,对减低生产成本起决定性作用,提高毛边板成材率势在必行,而根据柳钢中板厂设备实际情况,如何提高毛边板成材率有以下方面。
1 MAS平面形状控制在线应用的优化,使钢板矩形化。
通过平面控制系统展宽MAS控制钢板圆头量,通过定尺 MAS控制钢板头中尾宽度。
1-1优化展宽MAS的动态压下量以下图片是优化展宽MAS动态压下量前后钢板头部形状对比图,其中钢板厚度为14mm,坯宽1810毫米、钢种为Q235B,展宽MAS段使用的动态压下量为4.7厘米,从图中可以看出,优化前钢板圆头较大,圆头量500-600之间,优化后圆头值在100-200之间,从数据说明,所以该钢种的动态压下量为4.7厘米是理想的控制数据。
优化动态压下量后成材率贡献以下是优化动态压下量后不同坯料,不同成品规格成材率的提高比例对比表格。
表1.展宽MAS对于成材率的贡献从表1可以看出,通过优化展宽使MAS得轧制成品的圆头大幅度减小,轧制越薄得钢板,头部圆头减少量越多,对于提高钢板成材率的效果越明显。
从表中可以看出,优化展宽MAS平均可以提高成材率0.5%左右。
1-2优化定尺MAS的动态压下量通过优化定尺MAS的动态压下量使钢板宽度方向尽量一致。
提高中厚板成材率途径的探讨与实践

关键词
Re e r h a d Pr c ie o m p o i g t e Yil fM e i m a e s a c n a tc fI r vn h ed o d u Pl t
C e h n e Z a g S e g o g n in o g h n Z e y , h n h n h n a d L a g D n ( e t l rna d S e T c n l yR s a h Is tt H I ; 1C nr o n t l e h o g eer nt u B S aI e o c i e
不匹 配 , 造成 待 温时间较 长 因此 , 据生 产品种 根
第 6期
陈振业等: 提高中厚板成材率途径的探讨与实践 14 负偏 差轧制 .
。 3・ 2
的化学成分 , 坯料规格 , 制定合理的加热工艺制度
和装 钢制 度 , 坯 料 的加 热 温 度严 格 地 控 制 在规 将 定范 围 内 , 同时在 保证 加热 质量 的前提 下 , 缩短加 热时 间是 减少 烧损 的有 效 途经 。 13 切损 . 切 损包括 切 头 、 切尾 、 切边及 由于钢板 局部 质
~
企业 的品种结 构 、 原料条 件 、 产品规 格 、 备状 况 、 设
坯 料设 计水平 、 员素质 及管理 水平 等密 切相关 。 人
在 生 产技 术 方 面 , 主要 是 品种 结 构 、 负偏 差 轧制 、 板型控 制 、 损 率 、 判率 、 品率 以及 烧 损 。而 切 改 废 品种结 构 由市 场需求 、 备条 件决 定 , 设 而坯 料设计
== =: 一
提 高 中厚 板成 材 率途径 的探讨 与 实践
陈振 业 张胜宏 梁 栋
宽厚板成材率影响因素和改善措施详析
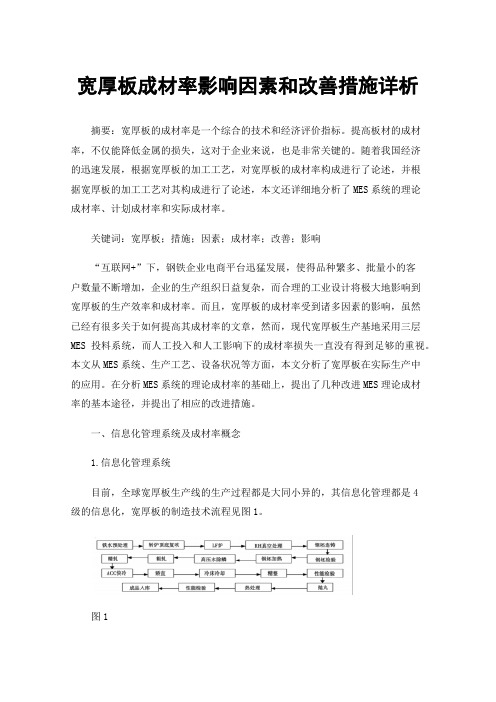
宽厚板成材率影响因素和改善措施详析摘要:宽厚板的成材率是一个综合的技术和经济评价指标。
提高板材的成材率,不仅能降低金属的损失,这对于企业来说,也是非常关键的。
随着我国经济的迅速发展,根据宽厚板的加工工艺,对宽厚板的成材率构成进行了论述,并根据宽厚板的加工工艺对其构成进行了论述,本文还详细地分析了MES系统的理论成材率、计划成材率和实际成材率。
关键词:宽厚板;措施;因素;成材率;改善;影响“互联网+”下,钢铁企业电商平台迅猛发展,使得品种繁多、批量小的客户数量不断增加,企业的生产组织日益复杂,而合理的工业设计将极大地影响到宽厚板的生产效率和成材率。
而且,宽厚板的成材率受到诸多因素的影响,虽然已经有很多关于如何提高其成材率的文章,然而,现代宽厚板生产基地采用三层MES投料系统,而人工投入和人工影响下的成材率损失一直没有得到足够的重视。
本文从MES系统、生产工艺、设备状况等方面,本文分析了宽厚板在实际生产中的应用。
在分析MES系统的理论成材率的基础上,提出了几种改进MES理论成材率的基本途径,并提出了相应的改进措施。
一、信息化管理系统及成材率概念1.信息化管理系统目前,全球宽厚板生产线的生产过程都是大同小异的,其信息化管理都是4级的信息化,宽厚板的制造技术流程见图1。
图12.成材率定义成材率是用1t原料所能生产的合格钢的百分百重量,反映了钢铁行业的金属回收状况。
计算公式如式1所示:式中:b-成材率/%;Q-原料重量/t;W-生产过程中金属损失量/t;G-合格产品重量/t;K-金属消耗系数。
根据体积×密度(7.797x103kg/m3或7.812x103kg/m3)的理论重量来计算投料件的重量。
根据客户的要求,生产的钢板的重量按照实际的重量或理论上的重量,理论上的装运密度是7.85x103kg/m3。
3.MES系统理论成材率理论成材率是由MES系统的维修者负责的。
MES系统的理论成材率是由板料尺寸的计算原理得出的,而MES系统则能依据这一原理得出最佳的计算公式。
提高中厚板成材率的方法探讨

6 0 %以上 , 并获得较高的产率和回收率 , 分别达到 8 2 . 0 1 %、 9 5 %, 因此 , 笔者认为用焙烧一 磁选工艺对莫托萨 拉铁矿选矿是可行的。
品, 那就需要 3 张钢板 ; 但是 , 如果企业可以进行两种产 品的混合切割 , 那 么就只需要切割5 张钢板来生产 A产
剩下的坯料就可以用来切割 B 产品, 这样 B 产品只需 业对资源的有效利用率, 但目 前我国 众多中小钢铁企业 品, 在中 厚板成材率方面仍处于劣势。 要额外再拿 2 张钢板切割就足够了, 同样是生产一样多
( 3 ) 还原焙烧一 磁选工艺流程简单 , 莫托沙拉赤铁矿
铁矿要达到这样的结果, 对原矿必须细磨, 因为该矿石为 显微磷片状结构, 结晶粒度仅为0 . 0 1 ~ 0 . 0 3 m m , 非常细。
试验过程 中还发现磁团聚现象很严重 , 两段磁选间需加 脱磁装置。
焙烧后可磨性好, 磨矿成本低, 回收率较高, 为有效利用 资源和控制建厂投资提供了前提条件, 可做为今后莫托
行磁选机试验 , 由于实验室磁选机最大场强为 1 4 0 0 O e ,
无法提高到1 6 0 0 O e , 只能按此场强进行试验, 试验结果 见表 8 , 铁精矿多元素分析见表9 。
表 9 铁精矿 多元素分析 单位
磁选机试验结果表明, 经过两段磁选, 铁精矿品位
二、 中厚板成材率的影响因素
1 . 烧损 因素
的产品, 前者分开切割使用了8 张钢板, 而后者混合切割
只需要7 张钢板 , 可见 , 品种多样化和是否有效组合也会
- 1、下载文档前请自行甄别文档内容的完整性,平台不提供额外的编辑、内容补充、找答案等附加服务。
- 2、"仅部分预览"的文档,不可在线预览部分如存在完整性等问题,可反馈申请退款(可完整预览的文档不适用该条件!)。
- 3、如文档侵犯您的权益,请联系客服反馈,我们会尽快为您处理(人工客服工作时间:9:00-18:30)。
提高中厚板成材率的措施
2010-04-18 20:20:12 作者:陈瑛来源:制钢参考网浏览次数:8 文字大小:【大】【中】【小】
1前言
全球中厚板轧机生产能力已超过市场需求量,相互竞争非常激烈,压价销售已成为常见的手段,但成本是压价的最低界限。
提高成材率是降低成本的重要手段,当连铸坯替代传统的钢锭开坯后,使钢材成本下降达10个百分点以上,而成材率提高1%,钢板生产成本也相应降低约1%。
这样,中厚板市场竞争能力便大大增强。
2提高成材率的现状
中厚板轧机成材率的差距比较大,日本新日铁大分厂厚板车间在1983年9月份已创造了世界上最高的订货成材率为%,比该公司君津厂厚板车间1983年8月份创造的订货成材率%高出%。
主要是热装率由60%提高到80%,再加上有效地利用了加热炉燃烧控制模型,以信息联络全过程达到操作的最佳化,并采用直接轧制提高了板坯尺寸精度。
提高厚板成材率的措施很多,其中效果最明显的是采用连铸板坯,提高连铸比,增加板坯单重。
但是,近几年来,板形控制已成为提高中厚板成材率一项最经济的新技术。
它不但提高了成材率,而且也提高了板形质量。
中厚板轧机的特点是在多数情况下都需要宽展轧制,因此,中厚板生产大多包括成形(粗轧)、宽展和伸长(精轧)三个阶段,而且每个品种的钢板尺寸也基本不同。
严格说,轧制成每块钢板的尺寸都是不一样的。
通常有一直纵轧、一直横轧、宽展纵轧及宽展横轧等4种轧制方式。
无论采用哪种试轧制,都有较大的宽展。
宽展与延伸是不均匀的,而且表面变形较大。
由于板坯端部的剪压和表面清理的厚差,粗轧阶段宽展之前均需进行调整板形轧制,往往给以微小的压下量,或者以立辊加工侧边或头尾端部,以取得
比较规整的板形。
精轧最后几道对钢板凸度和平直度的影响很大,压下量需减小,特别是最后一道都用于平整轧制。
中厚板轧制时断面积减小,在轧制方向伸长的同时,宽度方向产生宽展,而头尾两端比中间宽展大。
因此,轧成钢板的平面形状是非矩形的。
水岛厂5490mm厚板轧机采用MAS法轧制,使成材率提高%(以前切头尾和切边为%,现在减至%),而采用异宽MAS法后,可提高成材率约%。
千叶厂厚板轧机采用差厚宽展轧制法,并与立辊轧制联合控制板形,使成材率提高%。
日本钢管福山厂厚板轧机采用ATLAS法,使成材率提高%,进一步完善后可提高%。
另外,还采用DBR(狗骨轧制)法,成材率可提高2%。
3成材率的组成部分
中厚板成材率严格地说应该从炼钢送入原料开始,一直到交付给用户的成品钢板为止,其成品与重量百分比,称之为成材率。
轧钢厂的修磨与再切割的损耗,损失虽小,应归属中厚板成材率内。
另外,交付给用户后多余的改制品、短尺及其他板如何划归应由厂方自定。
中厚板成材率(η)一般由烧损(η1),边损(η2),头尾损(η3),材质不良废品(η4)及尺寸表面不良废品(η5)5部分损失后所组成。
即
η=1-(η1+η2+η3+η4
+η5)
4中厚板成材率的分析
中厚板成材率以日本较为先进,全国水平已达到94%。
详见表1。
表1 中厚板成材率分析———————————————————————————————————————
序项目1950年早期附设日本平日本某我国2004
年2000年新2003年
号以前有立辊均值厂1992 最佳业绩附设立辊后占百
年指标轧边分比
———————————————————————————————————————
1 烧损,~~~~~10
%
2 切边,~~~~~9/10
%
3 切头~~~~~
尾试样,%
4废次品~1.0~~~~10
%
小计~~~~~10/10
成材85~92 88~95 ~90~92 ~
率,%
———————————————————————————————————————
2004年我国成材率水平有很大的提高,如酒钢为%,天津中板为%,济钢中板为%,济钢厚板为%,新余为%,安阳为%,南钢为%,韶钢为%等都达到92%以上水平。
我国新设计厂采用立辊轧机时只达到93%,显然是太低了。
废次品中尺寸不合占50%,表面缺陷占25%,内部缺陷及力学性能不合占10%,其他占15%。
不计入改量,重处理及短尺料等。
板形控制中采用MAS法提高成材率%,ATLAS法提高%,DBR法提高2%,TFP法提高1%~3%,BB法(仅指钢锭)提高达3%。
按照切头尾及切边不同情况,近似矩形板,切头尾及切边含量很少,成材率可达96%以上;不切边或齐边板,只切头尾,不切边或铣边,成材率可达97%以上;矩形板,既不切头尾,也不切边,只有烧损和试样消耗,成材率可达98%以上。
5影响中厚板成材率的主要因素
(1)使用原料的影响很大,钢锭与连铸板坯的成材率相差达8个百分点之多。
如要求二次开坯,则成材率又要减少5个百分点左右。
另外,原料尺寸与单重不对口,多余料的损失也很可观。
原料内部质量,化学成分不合,有害元素过高等造成钢板力学性能超标,往往是钢板报废的主要起因。
(2)轧机型式与性能对成材率也有直接影响。
三辊劳特式轧机有斜轧工艺,成材率比二辊式轧机还低,而二辊式刚度低,比四辊式又低。
高刚度轧机比低刚度轧机成材率高。
附设有立辊轧机的比没有立辊轧机的成材率可提高1%~3%。
轧机尺寸大的比尺寸小的成材率高一些。
(3)薄的钢板比厚的成材率高,特厚板的成材率更低。
(4)品种不同,成材率差别很大,强度低、变形抗力小、比较好轧的比强度高、变形拉力大、比较难轧的成材率高。
(5)中厚板采用板形控制后成材率会有较大的提高。
表2为各种板形控制的成材率与金属损耗情况。
表2 各种板形控制的成材率及其金属损耗—————————————————————————————————————
序号控制方式成材率损耗部分,%
%烧损切头尾切边废品余量计划富裕量合计
—————————————————————————————————————
1 板形控
制0 0
近似矩形、0 0
切头尾及切
边余量很少
齐边,不
切0 0 0
边或铣边,
只切头尾
矩形,不
切0 0 0 0
头尾及边
2 板形不控制
—————————————————————————————————————
(6)轧制方式对成材率的影响也非常大。
一直纵轧到底方式:板坯宽等于板宽,不转钢、不展宽、长向伸长、成材率高。
一直横轧到底方式:板坯长等于板宽、转钢、不展宽、宽向伸长、成材率高。
宽展纵轧方式:板坯宽向展宽至板宽后伸长轧制,需转二次钢,坯长宽均不限制,坯长为板长、成材率低。
宽展横轧方式:板坯长度轧至板宽,转钢横轧伸长轧制成板,转一次钢,板坯长度为板宽,成材率低。
(7)工厂管理水平,人的操作素质对成材率高低有直接影响,往往会产生很大的差别。
6提高成材率的措施
(1)烧损方面:热装热送,炉子燃烧控制,低温出钢,加大坯厚。
(2)切边方面:附设立辊轧机,采用轧边工艺,板宽双倍尺轧制,剖分剪剖分,减少切边裕量,减少镰刀弯、有镰刀弯时采用分段后切边。
(3)切头尾方面:加大坯料,多倍尺长度轧制,矩形板轧制,减少鱼尾与舌头。
(4)试样方面:根据标准要求来集试样板,特殊军工板取样较多,有每板取样,且要求取样部位,切损会大大增加。
(5)轧机大型化、刚度大:轧机大时,原料长且宽、单重大。
可宽度双倍尺、长度多倍尺轧制,减少了切边与切头尾量。
(6)加大原料方面:坯厚尽量大,已达400mm厚。
尽量长,已达辊身长减去150mm。
(7)加大冷床长度、不设热剪机。
(8)尺寸检测装置完善,操作自动化,生产管理一贯制。
(9)从源头抓起,竭力降低废品、次品及改尺品率。
(10)严格控制最小差轧制。