高炉重力除尘灰铁焦分离回收项目 (1)
简介除尘灰及价格

本文摘自再生资源回收-变宝网()简介除尘灰及价格变宝网8月18日讯除尘灰可以分为烟气除尘灰和环境除尘灰,例如烧结机头高温烟气、高炉和转炉煤气系统的除尘,这类除尘灰是烟气除尘灰。
今天小编带大家去了解除尘灰的相关信息。
一、除尘灰的概括工业企业等排放的大气污染物经过布袋除尘器等除尘设备处理,大部分颗粒物废气经收集得到的飞灰,其成分与所收集的颗粒物气体有关,钢铁企业会产生大量除尘灰、氧化铁皮等等,一般都有很好的利用价值。
环境除尘是为减少环境粉尘污染所设置的,例如原料装卸、转运等岗位的除尘,这类除尘灰是环境除尘灰。
一般来说,环境除尘灰是在常温下聚集的,其介质粉尘性质无大变化,比较好利用,对生产基本无危害。
工艺除尘灰则是高温物化反应的产物,形成于高温之中,其理化性质发生变异,利用难度较大,对生产危害较大。
高炉煤气除尘全部采用了干法除尘,产生的一次除尘灰(重力除尘器)和二次除尘灰(煤气净化布袋除尘器)主要成分是铁和碳,全部返烧结作为烧结原料。
转炉煤气电除尘灰含铁量50%以上,一次除尘(设备:蒸发冷却器,作用:除尘、降温)灰(粒度较粗〕作为烧结原料,二次除尘(除尘设备:静电除尘器,作用:除尘降温)灰(粒度较细)一部分作为烧结原料回收利用,一部分作为竖炉球团原料回收利用。
作为球团原料配比控制在服以下对球团矿产质量指标影响不大。
电炉除尘灰含铁量利用冷压块技术部分回收利用。
长期以来大量除尘灰、泥在烧结循环利用,存在着许多问题。
一是除尘灰品种、数量多,成分复杂差异大,难以做到定量配料,造成烧结矿物化性能指标下降。
二是除尘灰、泥烧结性能差,钢铁企业多年来的生产经验。
烧结生产能力降低。
三是烟气除尘灰中K、Na、CLZn 等元素富集危害烧结炼铁生产,造成烧结台车糊蓖条,风机叶片挂泥,除尘器效率降低,烟尘污染加重,设备维护量加大,高炉因有害元素富集而影响顺行和寿命甚至造成事故也是不乏先例的.四是除尘灰、泥一直用敞车运输、落地,在装、卸现场及运输途中造成多次扬尘,污染环境。
中冶京诚-回转窑处理钢铁企业含锌粉尘技术介绍

三、回转窑工艺介绍 2)降低工序能耗 回转窑工序能耗较大,为降低能耗,可以回收窑尾 烟气余热,降低工序能耗。以脱锌为主要目的,窑渣产 品只是返回烧结工艺配料用,不追求窑渣中铁的金属化 率时,可以通过在窑尾末端引入空气,使得金属铁再氧 化而提供过程所需要的热量,从而可减少配碳量,降低 能耗。
3)提高产品质量 部分钢铁企业的含锌粉尘,同时还含有一定量的碱金 属及卤化物,影响次氧化锌产品质量,可以采用先湿法 脱碱金属及卤化物后,再进入回转窑工艺进行还原脱锌。
回转窑处理钢铁企业含锌粉尘 技术介绍
炼铁与储运工程技术所 2015年1月11日
主要内容
1 2 3
粉尘处理背景
处理含锌粉尘工艺技术比较 回转窑工艺介绍 结语
4
一、粉尘处理背景
钢铁厂粉尘是钢铁工业的主要固体废弃物之一,目前钢铁企业粉尘的 回收及综合利用已经受到国家及行业内部的重视。 钢铁企业粉尘的产量为钢产量的8%一12%:2012年我国粗钢产量 7.165亿t,即每年产生的含铁尘泥量达7 000万t以上 。 钢铁工业的含铁固废粉尘中含有多种金属,若不能将之有效分离则会 造成多方面危害,但若能对之环保、经济、高效地进行分离,则可变 废为宝,转变为宝贵的资源。 钢铁粉尘主要元素为铁和碳,可返回烧结回收利用。但是部分粉尘还 含有锌、铅、钾和钠等对高炉有害元素,占总粉尘量30%。需进行处 理后合理利用。
谢
谢
烟气处理 系统
回转窑处理 系统
原料输送系 统
回转窑 工艺
炉渣处理系 统
三、回转窑工艺介绍
典型的回转窑综合处理含锌粉尘工艺可以分为三个系统:回转窑 直接还原系统、锌焙砂处理系统、窑渣选铁系统。
1、将除尘灰与还原剂按一定配 比混合后,加入回转炉内。 2、回转炉挥发反应区温度为 1100~1300℃,排出烟气温度为 >400℃,原料中金属锌、铅、锡 等被还原,进入气相中并被氧化 成氧化物,随后进入烟尘处理系 统收集。 3、窑渣水碎后送炉渣处理系统。
高炉渣干式粒化及显热回收的技术分析_张延平
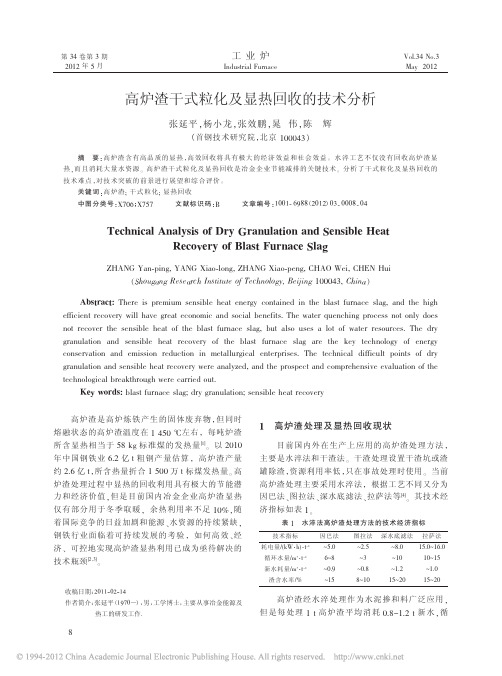
流程是使用高速混合气体吹散熔渣使其粒化,并利 用吸热化学反应将高炉渣显热以化学能的形式储存 起来,然后将反应物输送到热交换器中,进行逆向化 学反应释放热量,参与热交换的化学物质可以循环 使用。整个循环热回收的过程如图 4 所示。用高速喷 出 的 CH4 和 H2O 混 合 气 体 对 液 态 高 炉 渣 流 进 行 冷 却粒化,两者进行强烈的热交换,液态高炉渣因受到 风力的破碎和强制冷却作用,其温度迅速下降并粒 化成细小的颗粒。 生成的气体进入下一反应器,在 一定条件下,H2 和 CO 气体反应生成甲烷和水蒸气, 放出热量。 高温 CH4 和水蒸气的混合气体经过热交 换器冷却,重新返回循环使用。 热交换出来的热量 经处理后可供发电、高炉热风炉等使用。
炼铁除尘灰及炼钢污泥的利用研究
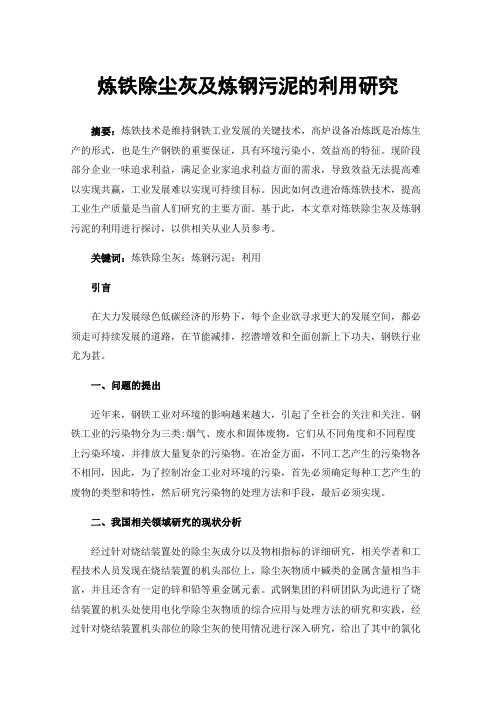
炼铁除尘灰及炼钢污泥的利用研究摘要:炼铁技术是维持钢铁工业发展的关键技术,高炉设备冶炼既是冶炼生产的形式,也是生产钢铁的重要保证,具有环境污染小、效益高的特征。
现阶段部分企业一味追求利益,满足企业家追求利益方面的需求,导致效益无法提高难以实现共赢,工业发展难以实现可持续目标。
因此如何改进冶炼炼铁技术,提高工业生产质量是当前人们研究的主要方面。
基于此,本文章对炼铁除尘灰及炼钢污泥的利用进行探讨,以供相关从业人员参考。
关键词:炼铁除尘灰;炼钢污泥;利用引言在大力发展绿色低碳经济的形势下,每个企业欲寻求更大的发展空间,都必须走可持续发展的道路,在节能减排,挖潜增效和全面创新上下功夫,钢铁行业尤为甚。
一、问题的提出近年来,钢铁工业对环境的影响越来越大,引起了全社会的关注和关注。
钢铁工业的污染物分为三类:烟气、废水和固体废物,它们从不同角度和不同程度上污染环境,并排放大量复杂的污染物。
在冶金方面,不同工艺产生的污染物各不相同,因此,为了控制冶金工业对环境的污染,首先必须确定每种工艺产生的废物的类型和特性,然后研究污染物的处理方法和手段,最后必须实现。
二、我国相关领域研究的现状分析经过针对烧结装置处的除尘灰成分以及物相指标的详细研究,相关学者和工程技术人员发现在烧结装置的机头部位上,除尘灰物质中碱类的金属含量相当丰富,并且还含有一定的锌和铅等重金属元素。
武钢集团的科研团队为此进行了烧结装置的机头处使用电化学除尘灰物质的综合应用与处理方法的研究和实践,经过针对烧结装置机头部位的除尘灰的使用情况进行深入研究,给出了其中的氯化钾、一氧化铅、硫化钾以及复合型肥料等物质提取工作的一整套思路和想法。
莱钢集团针对烧结装置机头部位除尘灰物质中氯化钾物质的提取工作开展了一系列研究工作,经过对于烧结装置机头部位除尘灰物质中各种成分和结构的分析和讨论,研究出了一类可以用来提取氯化钾的工艺方法、并且给出了相应的工艺参数,通过此方法得到的氯化钾产品,其纯度可以实现92%以上、回收的效率超过了80%,因此这类工艺方法能够实现比较理想的效益,值得在同行业中进行推广。
金属冶炼炉渣的处理与回收
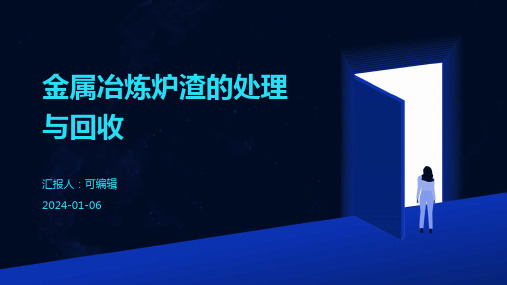
还原熔炼
在高温下用还原剂将炉渣 中的金属还原成金属单质 或低氧化物,再从熔融态 中分离出来。
炉渣的生物处理
生物浸出
利用微生物的氧化还原作用将炉渣中 的有用金属溶解出来,再通过提取、 沉淀、结晶等方法回收金属。
生物吸附
利用微生物的吸附作用将溶液中的金 属离子吸附在细胞表面或内部,再通 过细胞分离和金属提取的方法回收金 属。
金属冶炼炉渣的处理 与回收
汇报人:可编辑 2024-01-06
目 录
• 金属冶炼炉渣的来源与特性 • 金属冶炼炉渣的处理方法 • 金属冶炼炉渣的回收利用 • 金属冶炼炉渣处理与回收的挑战与前景 • 新技术与研究方向 • 实际案例分析
01
金属冶炼炉渣的来源与特性
炉渣的来源
金属矿石的熔炼
在高温熔炼过程中,矿石中的金属与杂质形成熔融态 ,随着杂质与金属分离,形成炉渣。
国际先进炉渣处理与回收技术案例
概况
本案例介绍了几种国际上先进的炉渣处理与回收技术,包括高温熔 融技术、等离子熔融技术、微波处理技术和化学还原技术等。
技术特点
这些技术具有处理效果好、回收率高、环保性能强等特点,能够有 效地将炉渣中的有价元素提取出来,同时减少对环境的污染。
应用前景
随着环保意识的提高和资源短缺的压力增大,这些国际先进的炉渣处 理与回收技术在国内将具有广阔的应用前景。
运营成本高
处理过程中需要消耗大量的能源和化学药剂, 导致运营成本增加。
经济效益不明显
由于技术限制和回收品质量问题,金属冶炼炉渣处理与回收的经济效益不明显 。
政策与环境影响
政策支持不足
目前政府对金属冶炼炉渣处理与回收产业的政策支持力度不够。
环境监管严格
XX钢铁有限公司2×20万吨转底炉固废处理环保项目初步设计安全专篇
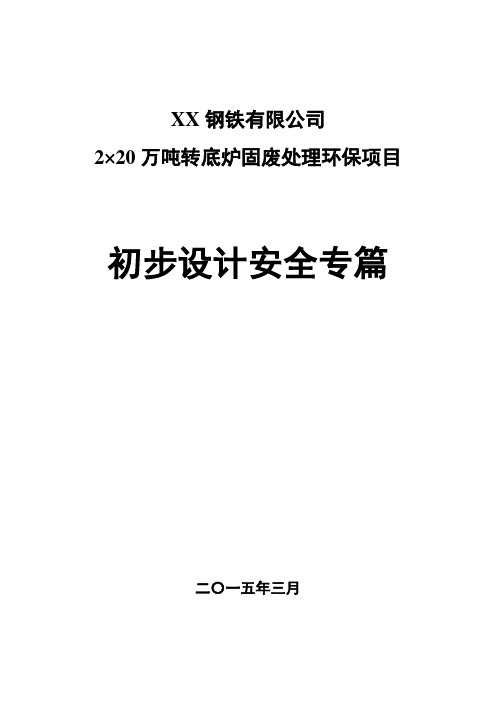
2.3.1建设项目地理位置及选址
XX坐落在XX省XX市XX火车站西侧,XX南岸,XX铁路从公司门前通过,公司铁路专用线与其相连。南距XX高速公路5km,东距XX大线1.5km,西距XX公路5km,北距XX市区10km,地理位置优越,交通便利。
本工程的建设场地确定在XX公司新区的西北角,建设场地的南侧为规划的焦化场地,西北侧为XX铁路线,东侧与竖炉、烧结单元隔路相望,总占地面积约5.81万m2。
16)《爆炸和火灾危险环境电力装置设计规范》GB 50058-2014
17)《起重机械安全规程第1部分:总则》GB 6067.1-2010
18)《起重机设计规范》GB/T 3811-2008
19)《危险化学品重大危险源辨识》GB 18218-2009
20)《压力容器》GB 150.1~150.4-2011
2.3.2建设规模
2×20万t转底炉固废处理项目含2条转底炉生产线,年锌粉尘处理能力2×200000t/a(干基),产品为金属化球团和氧化锌粉,年产金属化球团约28万t,氧化锌粉0.75万t。
工程分两期建设,本项目为一期工程,建设1条转底炉生产线,年产金属化球团约14万t,氧化锌粉0.375万t。
2.3.3工艺流程
15)《XX省安全生产应急管理规定》XX省人民政府令〔2012〕15号
16)《XX省安全生产应急管理规定》XX省人民政府令〔2012〕第15号
1.3.3
1)《生产设备安全卫生设计总则》GB5083-1999
2)《生产过程安全卫生要求总则》GB12801-2008
3)《钢铁冶金企业设计防火规范》GB 50414-2007
2.2建设项目性质、任务及范围
性质:新建。
高炉煤气干法除尘灰提锌工艺技术探讨

高炉煤气干法除尘灰提氧化锌工艺技术探讨阮积海(广西柳州钢铁(集团)公司技术中心,)摘要介绍了涟源某氧化锌冶炼厂的生产工艺及生产过程中产生的环境污染及治理技术,同时就以高炉煤气干法除尘灰为原料提取氧化锌的生产工艺进行技术(环保)探讨。
1 前言柳钢共有8座高炉,其中最大高炉炉容为1250m3,冶炼过程中产生的高炉煤气均采用干法进行净化除尘,每年由此产生的干法除尘灰达4万多吨(布袋除尘灰),目前该除尘灰的处理方式是直接销售给柳州附近的砖厂代替粉煤灰烧砖,或者是销售给氧化锌冶炼厂配料提锌。
柳钢非钢环保公司经过调研后,打算以高炉煤气干法除尘灰为原料进行深加工提取氧化锌。
经过对涟源某有色金属冶炼厂进行实地考察后,现对以高炉煤气干法除尘灰为原料提取氧化锌的工艺进行技术(环保)探讨。
2 考察介绍2.1 考察对象考察的对象是涟源某有色金属冶炼厂,是一家私营企业。
该厂采用火法工艺提炼氧化锌,共有二条回转窑生产线,原料来源为含锌矿、工业锌渣、煤粉以及部分涟钢高炉除尘灰,每天所耗原料40吨,年产氧化锌1200~1500吨。
2.2生产工艺该厂采用火法工艺提炼氧化锌,首先含锌矿、工业锌渣、煤粉经加水湿润后用抓斗机抓取均匀并成块状,然后通过皮带输送机将块状原料运至回转窑窑头点火燃烧,在高温作用下(回转窑内温度可达1100℃),原料中的锌经过氧化还原反应,以气熔胶、颗粒物等状态进入废气中,在引风机的作用下,经多组管槽冷却系统冷却(槽中装有冷却水)、最后进入布袋收尘器回收产品。
燃烧后的炉渣经窑尾排渣口进入冲渣池冷却,少量废气通过窑尾顶部的风管引入一个简陋的沉降室回收粉尘后排放。
回转窑中燃料燃烧所需的氧通过回转窑尾部的鼓风机鼓风供应。
其工艺流程如下图2.3环境污染及治理(1)废气: 废气污染主要来自二个方面,一是原料转运及配料过程产生的扬尘,从在现场看粉尘污染很小,但有关人员介绍,天气干燥时扬尘污染相当严重。
另一方面就是原料在回转窑燃烧冶炼过程中产生的烟尘和废气,由于产品存在于烟尘中,经过布袋收尘器收尘净化后,外排烟气的粉尘浓度大大降低。
不锈钢除尘灰再生利用的可行性分析
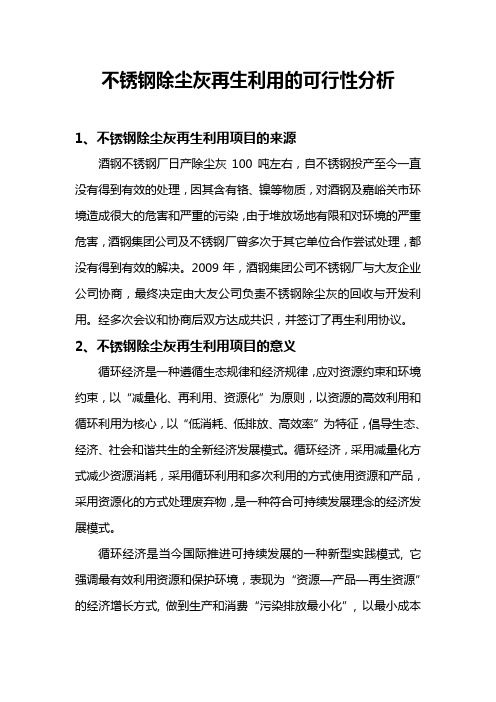
不锈钢除尘灰再生利用的可行性分析1、不锈钢除尘灰再生利用项目的来源酒钢不锈钢厂日产除尘灰100吨左右,自不锈钢投产至今一直没有得到有效的处理,因其含有铬、镍等物质,对酒钢及嘉峪关市环境造成很大的危害和严重的污染,由于堆放场地有限和对环境的严重危害,酒钢集团公司及不锈钢厂曾多次于其它单位合作尝试处理,都没有得到有效的解决。
2009年,酒钢集团公司不锈钢厂与大友企业公司协商,最终决定由大友公司负责不锈钢除尘灰的回收与开发利用。
经多次会议和协商后双方达成共识,并签订了再生利用协议。
2、不锈钢除尘灰再生利用项目的意义循环经济是一种遵循生态规律和经济规律,应对资源约束和环境约束,以“减量化、再利用、资源化”为原则,以资源的高效利用和循环利用为核心,以“低消耗、低排放、高效率”为特征,倡导生态、经济、社会和谐共生的全新经济发展模式。
循环经济,采用减量化方式减少资源消耗,采用循环利用和多次利用的方式使用资源和产品,采用资源化的方式处理废弃物,是一种符合可持续发展理念的经济发展模式。
循环经济是当今国际推进可持续发展的一种新型实践模式, 它强调最有效利用资源和保护环境,表现为“资源—产品—再生资源”的经济增长方式, 做到生产和消费“污染排放最小化”, 以最小成本获得最大的经济效益和环境效益。
不锈钢冶炼产生大量除尘灰,由于不能得到有效的处理,一般露天堆放,随风飘荡,严重污染大气环境及水质,镍、铬等元素对环境危害更为严重,但铬、镍等贵重元素,价格昂贵,回收利用具有重要的经济意义;因此不锈钢除尘灰的循环再生利用具有非常重要的环保和社会意义,同时也属于国际和国家鼓励类的循环经济项目。
综合开发利用除尘灰对于节约资源,改善环境, 实现废弃物的资源化利用,促进经济效益增长方式的转变具有重要意义。
3、国内不锈钢除尘灰再生利用现状在不锈钢冶炼过程中,产生大量粉尘经过除尘装置处理,收集其中的粉尘即除尘灰,大部分除尘难以处理,尤其是不锈钢厂排出的除尘灰。
- 1、下载文档前请自行甄别文档内容的完整性,平台不提供额外的编辑、内容补充、找答案等附加服务。
- 2、"仅部分预览"的文档,不可在线预览部分如存在完整性等问题,可反馈申请退款(可完整预览的文档不适用该条件!)。
- 3、如文档侵犯您的权益,请联系客服反馈,我们会尽快为您处理(人工客服工作时间:9:00-18:30)。
高炉重力除尘灰铁焦分离回收项目
可
行
性
研
究
报
告
六盘水兴力源煤焦有限公司
二0一三年六月
目录
一、总论 (1)
二、环境保护 (4)
三、项目实施进度计划 (4)
四、投资估算 (4)
五、技术经济分析及评价 (5)
六、项目结论 (6)
一、总论
1、项目名称:高炉重力除尘灰铁焦分离回收项目
2、项目主办单位:六盘水兴力源煤焦有限公司
3、项目建设的必要性
经我公司调研水钢炼铁厂现有4座高炉生产,年产生铁490万吨,年产生重力除尘灰约9万吨。
主要由磁铁矿、赤铁矿、焦粉、铁酸钙及其它矿物组成,铁矿物以Fe3O4和Fe2O3为主,其它金属矿物以氧化物的形式存在,有害元素S、Pb 、Zn、As、K2O 、Na2O较高。
炼铁厂高炉重力除尘灰主要成分为:TFe:25%-30%,FeO:5%-7%,CaO:3%-4%,SiO2:5%-7%,S:0.4%-0.8%,Pb:0.8%-1.2%,Zn:2%-5%,K2O:0.15%-0.28%,Na2O:0.12%-0.26%,含碳量(C):20—25%。
可见高炉重力除尘灰中铁、碳是可用资源,同时有害元素较高对合理使用也带来一定的困难。
当今世界,资源日趋紧张,谁拥有资源,谁有效利用资源,谁就能赢得更大生存空间。
所以,现代钢铁企业高炉重力除尘灰的有效处理成为其资源回收、节能减排、企业增效工作的重要环节。
目前,国内钢铁企业重力除尘灰处理有四种方式:(1)抛弃处理。
该方法造成资源浪费,同时垃圾堆场大,严重污染环境。
(2)直接返回烧结配矿,这种方法从表面上看是节约了重力除尘灰加工成本又利用了资源,但由于重力除尘灰铁品位低、有
害元素含量高、粒级粗细不均、化学成分差异较大,尤其是经历了高温过程,矿物晶形发生了改变,粘结性较差,且具有斥水性、不易成球等因素,一方面影响烧结透气性,对烧结矿质量及产量产生一定的影响,碳得不到有效利用;其二是降低了烧结矿品位,增加高炉焦比;更为严重的是造成Pb、Zn、K 2O、Na2O等有害元素在高炉富集,对高炉设备造成严重损坏及高炉炉况失常。
a.由于重力除尘灰是一种灰粉率和有害元素含量极高的微颗粒原料直接返回烧结,影响烧结炉的透气性和烧结矿结块率,从而影响烧结的产量和质量。
b.低品位高粉尘率的重力除尘灰做烧结矿的原料,不但增加了烧结生产中的能源消耗,同时增加了除尘风机粉尘排放的成本,增加粉尘排放和环境污染。
c.更为严重的是炼铁过程中的有害元素、铅、锌沸点低,几乎不能被铁吸收,根据国内炼铁行业对高炉有害元素平衡统计技术资料,资料表明在350―750立方的高炉原料中的铅、锌有96.81%会进入高炉。
重力除尘灰和布袋除尘灰中1500立方以上的高炉中铅、锌等元素有93.48%的量进入高炉重力除尘灰和布袋除尘灰中,如果直接将重力除尘灰和布袋除尘灰返回烧结,势必造成铅,锌等有害元素不断在高炉富集,这些元素在高炉中越积越多,对高炉造成严重的损害,以致造成严重的设备事故。
如:宝钢1996年发生锌富集的恶性事件,高炉产量下降约25%。
焦比上升6%造成了生产组织极为困难;在如:梅山钢铁公司1995
年-1998年一段时间中重力除尘灰和布袋除尘灰中的铅,锌含量约为0.57%-0.9%。
因重力除尘灰中铅、锌含量低,没有引起足够的重视,重力除尘灰没有做加工处理直接配入烧结矿原料中使用,最终导致重力除尘灰中锌含量上升到7%以上,造成冷却设备和风口等严重损坏,影响高炉正常生产操作,增加了休风检修率,缩短高炉大修周期,影响高炉使用寿命,类似以上重力除尘灰直接返回烧结使用,而造成的富锌铅侵蚀炼铁高炉本体和设备而导致的恶性事故案例极为普遍,实践证明铅、钾、钠等有害元素是损害高炉的主要杀手,而富铅、锌的重力除尘灰的循环反复返回使用又造成有害元素在炉内及设备中的堆积侵蚀的源头,实践证明高炉重力除尘灰未经加工处理直接返回烧结配料的方法并不可取,而水钢炼铁厂就是此类方法直接返回烧结配矿。
(3)低价销售处理。
部分钢铁厂将重力除尘灰以20—60元不等的价格出售给制砖厂,仅利用了重力除尘灰中的碳,资源利用不完全,影响企业效益。
(4)简单回收处理。
有些钢铁厂将重力除尘灰进行简单磁选处理,虽选出了部分铁粉,但分离不彻底,量很少,品位低,且焦粉没有分离出,很不经济。
很多钢铁企业对除尘灰的综合利用开展了大量的研究试验工作,在碳、铁回收,去除有害元素方面取得了较好的效果。
炼铁厂目前重力除尘灰全部烧结配料,从综合经济效益的提高应学习其它企业的经验,采用铁焦分离回收技术,提高综合经济效益,
减轻有害元素对高炉的危害,是非常必要的。
4、项目建设的可行性
六盘水兴力源煤焦有限公司与国内高等院校合作,拥有成熟的重力除尘灰分离工艺技术。
公司在吸取同类选矿经验的基础上,创造性地利用浮选、磁选及重力选矿相结合的选矿工艺,能最大限度地回收重力除尘灰中的铁矿粉、焦粉,回收率较高,达到了节能减排、资源回收的最佳效果。
二、环境保护
(1)本工艺流程设备低速运转,机械噪声无超标。
(2)本工艺流程采用湿加工,加工场地内无扬尘,湿加工用水经沉淀循环利用,加工场地经硬化无生产水渗入地下,整个生产区无任何污水外排,实现污水零排放,对周边环境不会产生任何影响。
(3)生产用药剂为无毒药剂,不影响作业人员健康。
(4)保证一定绿化面积,按花园式工厂建设。
三、项目实施进度计划
工程建设实施阶段为:现场施工、试车投产等,预计需4个月。
四、投资估算
项目投资估算为:1220万元。
项目估算包括:场地征租费、生产区土建费用、设备费、安装费、供电供水、环保绿化、办公室、职工宿舍、仓库、流动资金。
按建设两套重力除尘灰回收处理系统考虑,每套的投资估算610万。
五、技术经济分析及评价
1、基础数据
年产生铁490万吨,每年排放重力除尘灰在9万吨。
利用该技术,按铁回收率80%、碳回收率60%计算,每年重力除尘灰可回收铁精粉(52%)3.66万吨,焦粉(固定碳68%)1.69万吨,分离出尾渣3.65万吨(除尘灰成分为:TFe:27.5%,CaO:3.5%,SiO2:6.0%,C:22.5%,烧损25%)。
烧结率73%,年入炉烧结矿622万吨,烧结矿品位54.3%,综合入炉品位55.47%,入炉焦比342kg/t。
按上述除尘灰成分计算,烧结矿R2为2.05时的单烧品位为31.11%,当重力除尘灰全部用于烧结配料时,烧结矿品位将降低为53.97%,高炉综合入炉品位降低为55.23%。
从重力除尘灰单烧品位看,其经济价值是很低的。
2、经济效益计算
(1)每年回收铁精粉3.66万吨及焦粉1.69万吨,按市场价
铁精粉600元/吨、焦粉550元/吨计计算,可实现年回收收入3200万元。
扣除重力除尘灰资源费9万吨×100=900万,实现增值2300万。
(2)重力除尘灰全部用于烧结配料,高炉综合入炉品位降低0.24%,入炉焦比将升高1.23 kg/t,年多耗焦炭6300吨,年增加费用756万元(焦炭1200元/吨)。
(3)如果重力除尘灰直接返烧结将增加烧结燃料消耗和焦炭消耗[90000-﹝90000重力灰×0.6回收率﹞]=36000吨×300公斤/吨=10800吨),增加消耗10800×1200=1296万(焦炭1200元/吨)。
(4)年加工费用54000吨×320元/吨=1728万元。
(5)年效益:(2300+756+1296)-1728=2624万元。
3、初步评价
该项目年为水钢创效益为2624万元,效益显著。
六、项目结论
该项目技术成熟、经济效益显著,建设周期短,有较好的效益。