热处理变形基础知识
临界变形热处理

临界变形热处理
临界变形热处理,是一种常用的金属热处理方法,旨在改善材料的力学性能和耐磨性。
通过控制材料的加热温度和冷却速率,使其达到特定的临界点,从而在晶体结构和晶界中引入位错,改变材料的内部结构和性能。
临界变形热处理的过程可以简单分为加热阶段和冷却阶段。
在加热阶段,材料被加热到临界温度,使其达到高温状态。
此时,材料的晶体结构开始发生变化,原子开始迁移,晶粒开始长大。
同时,位错也会在晶体中形成,并扩散到晶界上。
在临界变形热处理的冷却阶段,材料被迅速冷却,使其快速达到室温。
这种快速冷却的方式可以有效地固定位错和晶界结构,从而增加材料的硬度和强度。
此外,冷却速率还会影响材料的晶粒尺寸和晶界形态,进而影响材料的韧性和耐腐蚀性。
临界变形热处理在金属加工和制造过程中具有广泛的应用。
它可以用于提高材料的强度和硬度,延长材料的使用寿命。
同时,临界变形热处理还可以改善材料的塑性和可加工性,使其更容易进行后续加工操作。
临界变形热处理是一项复杂而精细的工艺,需要严格控制加热温度、冷却速率和保温时间等参数。
同时,还需要根据不同材料的特性和要求来选择合适的处理方式。
只有在正确的处理条件下,才能获得
理想的材料性能和结构。
临界变形热处理是一种重要的金属热处理方法,可以通过控制加热和冷却过程来改善材料的性能。
它在工业生产中具有广泛的应用,能够提高材料的强度、硬度和耐磨性,从而延长材料的使用寿命。
但是,在实际应用过程中,我们需要根据具体情况来选择合适的处理参数和方法,以确保处理效果的最佳化。
热处理基础知识

一、热处理1、正火:将钢材或钢件加热到临界点AC3或ACM以上的适当温度保持一定时间后在空气中冷却,得到珠光体类组织的热处理工艺。
2、退火:将亚共析钢工件加热至AC3以上20—40度,保温一段时间后,随炉缓慢冷却(或埋在砂中或石灰中冷却)至500度以下在空气中冷却的热处理工艺。
3、固溶热处理:将合金加热至高温单相区恒温保持,使过剩相充分溶解到固溶体中,然后快速冷却,以得到过饱和固溶体的热处理工艺。
4、时效:合金经固溶热处理或冷塑性形变后,在室温放置或稍高于室温保持时,其性能随时间而变化的现象。
5、固溶处理:使合金中各种相充分溶解,强化固溶体并提高韧性及抗蚀性能,消除应力与软化,以便继续加工成型。
6、时效处理:在强化相析出的温度加热并保温,使强化相沉淀析出,得以硬化,提高强度。
7、淬火:将钢奥氏体化后以适当的冷却速度冷却,使工件在横截面内全部或一定的范围内发生马氏体等不稳定组织结构转变的热处理工艺。
8、回火:将经过淬火的工件加热到临界点AC1以下的适当温度保持一定时间,随后用符合要求的方法冷却,以获得所需要的组织和性能的热处理工艺。
9、钢的碳氮共渗:碳氮共渗是向钢的表层同时渗入碳和氮的过程。
习惯上碳氮共渗又称为氰化,以中温气体碳氮共渗和低温气体碳氮共渗(即气体软氮化)应用较为广泛。
中温气体碳氮共渗的主要目的是提高钢的硬度,耐磨性和疲劳强度。
低温气体碳氮共渗以渗氮为主,其主要目的是提高钢的耐磨性和抗咬合性。
10、调质处理(quenching and tempering):一般习惯将淬火加高温回火相结合的热处理称为调质处理。
调质处理广泛应用于各种重要的结构零件,特别是那些在交变负荷下工作的连杆、螺栓、齿轮及轴类等。
调质处理后得到回火索氏体组织,它的机械性能均比相同硬度的正火索氏体组织更优。
它的硬度取决于高温回火温度并与钢的回火稳定性和工件截面尺寸有关,一般在HB200—350之间。
11、钎焊:用钎料将两种工件加热融化粘合在一起的热处理工艺。
金属材料及热处理基础知识.ppt
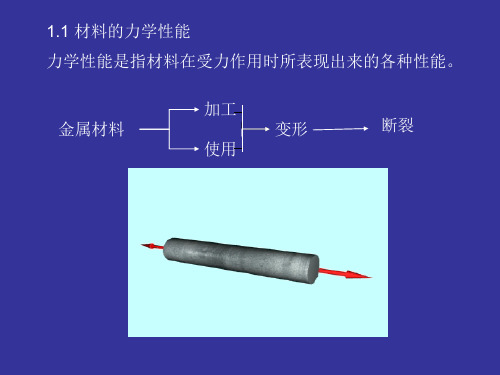
2 .洛氏硬度
以顶角为120度的金刚石圆锥体或直径1.588mm的淬火 钢球作为压头,以一定的压力使其压入材料表面,测量压痕 深度来确定其硬度,即为洛氏硬度。被测材料硬度,可直接 在硬度计刻盘读出。
洛氏硬度常用的有三种,分别以HRA、HRB、HRC来表示。 洛氏硬度符号、试验条件和应用表
下贝氏体:无方向性的针状铁素体上弥散分布着细小颗粒的 渗碳体
7、魏氏组织
魏氏组织是在比较大的过冷度下形成的。奥氏体过冷到这 一温度区内,便会形成魏氏组织。魏氏组织铁索体是以切变机 理形成的其生长往往都是由晶界网状铁索体分枝,许多铁赢体 片平行地向晶粒内部长大。铁素体片之间的奥氏体随后变成珠 光体。魏氏组织会降低钢的塑性和韧性,尤其是冲击韧性。
3.维氏硬度 测定维氏硬度的原理基本上和布氏硬度相同,区别在于压头
采用锥面夹角为136度的金刚石正四棱锥体,压痕是四方锥形。 维氏硬度值用HV表示。
压痕面
4. 里氏硬度
原理:当材料被一个冲击体撞击时,较硬材料使冲击体产生 的反弹速度大于较软者。
5. 硬度与强度值的对应关系 由于硬度值综合反映了材料在局部范围内对塑性变形等 的抵抗能力,故它与强度值也有一定关系。 工程上:
冷却速度对晶粒大小的影响
快速冷却,形核点多,晶粒细小 冷却速度慢,均匀长大,晶粒粗大
1.2.2 铁碳合金的基本组织 铁 碳含量>2%--弱而脆
铁碳合金
铁素体—碳熔于α铁或δ铁中的固溶体 F
钢 奥氏体—碳熔于γ铁中的固溶体 A 强而韧 碳含量 0.02%-2%
渗碳体—铁碳金属化合物含碳6.67% Fe3C
许用应力 o
n
安全系数
热处理知识

热处理热处理是将金属材料放在一定的介质内加热、保温、冷却,通过改变材料表面或内部的金相组织结构,来控制其性能的一种金属热加工工艺。
基本简介热处理是将金属材料放在一定的介质内加热、保温、冷却,通过改变材料表面或内部的金相组织结构,来控制其性能的一种金属热加工工艺。
发展简史在从石器时代进展到铜器时代和铁器时代的过程中,热处理的作用逐渐为人们所认识。
早在公元前770至前222年,中国人在生产实践中就已发现,铜铁的性能会因温度和加压变形的影响而变化。
白口铸铁的柔化处理就是制造农具的重要工艺。
公元前六世纪,钢铁兵器逐渐被采用,为了提高钢的硬度,淬火工艺遂得到迅速发展。
中国河北省易县燕下都出土的两把剑和一把戟,其显微组织中都有马氏体存在,说明是经过淬火的。
随着淬火技术的发展,人们逐渐发现淬冷剂对淬火质量的影响。
三国蜀人蒲元曾在今陕西斜谷为诸葛亮打制3000把刀,相传是派人到成都取水淬火的。
这说明中国在古代就注意到不同水质的冷却能力了,同时也注意了油和尿的冷却能力。
中国出土的西汉(公元前206~公元24)中山靖王墓中的宝剑,心部含碳量为0.15~0.4%,而表面含碳量却达0.6%以上,说明已应用了渗碳工艺。
但当时作为个人“手艺”的秘密,不肯外传,因而发展很慢。
1863年,英国金相学家和地质学家展示了钢铁在显微镜下的六种不同的金相组织,证明了钢在加热和冷却时,内部会发生组织改变,钢中高温时的相在急冷时转变为一种较硬的相。
法国人奥斯蒙德确立的铁的同素异构理论,以及英国人奥斯汀最早制定的铁碳相图,为现代热处理工艺初步奠定了理论基础。
与此同时,人们还研究了在金属热处理的加热过程中对金属的保护方法,以避免加热过程中金属的氧化和脱碳等。
1850~1880年,对于应用各种气体(诸如氢气、煤气、一氧化碳等)进行保护加热曾有一系列专利。
1889~1890年英国人莱克获得多种金属光亮热处理的专利。
二十世纪以来,金属物理的发展和其他新技术的移植应用,使金属热处理工艺得到更大发展。
热处理变形基础知识
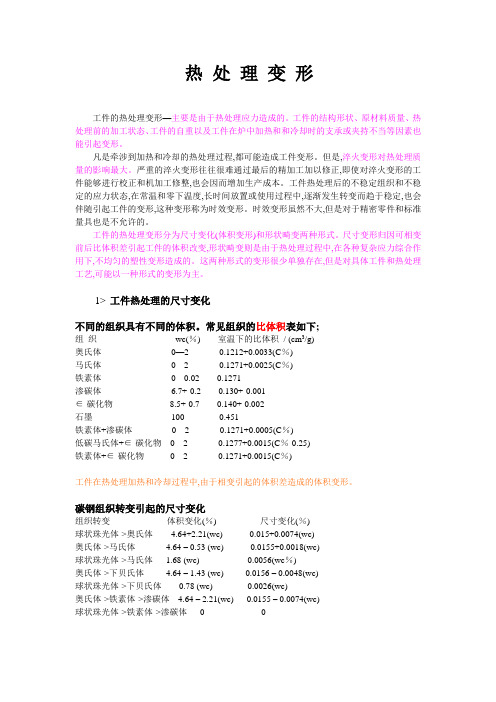
热处理变形工件的热处理变形—主要是由于热处理应力造成的。
工件的结构形状、原材料质量、热处理前的加工状态、工件的自重以及工件在炉中加热和和冷却时的支承或夹持不当等因素也能引起变形。
凡是牵涉到加热和冷却的热处理过程,都可能造成工件变形。
但是,淬火变形对热处理质量的影响最大。
严重的淬火变形往往很难通过最后的精加工加以修正,即使对淬火变形的工件能够进行校正和机加工修整,也会因而增加生产成本。
工件热处理后的不稳定组织和不稳定的应力状态,在常温和零下温度,长时间放置或使用过程中,逐渐发生转变而趋于稳定,也会伴随引起工件的变形,这种变形称为时效变形。
时效变形虽然不大,但是对于精密零件和标准量具也是不允许的。
工件的热处理变形分为尺寸变化(体积变形)和形状畸变两种形式。
尺寸变形归因可相变前后比体积差引起工件的体积改变,形状畸变则是由于热处理过程中,在各种复杂应力综合作用下,不均匀的塑性变形造成的。
这两种形式的变形很少单独存在,但是对具体工件和热处理工艺,可能以一种形式的变形为主。
1>工件热处理的尺寸变化不同的组织具有不同的体积。
常见组织的比体积表如下;组织wc(%) 室温下的比体积/ (cm3/g)奥氏体0—2 0.1212+0.0033(C%)马氏体0---2 0.1271+0.0025(C%)铁素体0---0.02 0.1271渗碳体 6.7+-0.2 0.130+-0.001∈-碳化物8.5+-0.7 0.140+-0.002石墨100 0.451铁素体+渗碳体0---2 0.1271+0.0005(C%)低碳马氏体+∈-碳化物0---2 0.1277+0.0015(C%-0.25)铁素体+∈-碳化物0---2 0.1271+0.0015(C%)工件在热处理加热和冷却过程中,由于相变引起的体积差造成的体积变形。
碳钢组织转变引起的尺寸变化组织转变体积变化(%) 尺寸变化(%)球状珠光体->奥氏体- 4.64+2.21(wc) - 0.015+0.0074(wc)奥氏体->马氏体 4.64 – 0.53 (wc) - 0.0155+0.0018(wc)球状珠光体->马氏体 1.68 (wc) 0.0056(wc%)奥氏体->下贝氏体 4.64 – 1.43 (wc) 0.0156 – 0.0048(wc)球状珠光体->下贝氏体0.78 (wc) 0.0026(wc)奥氏体->铁素体->渗碳体 4.64 – 2.21(wc) 0.0155 – 0.0074(wc)球状珠光体->铁素体->渗碳体0 02>工件热处理的形状畸变工件热处理的形状畸变有多种原因。
热处理基础知识问答

热处理基础知识问答1、什么是热处理将固态金属或合金采取适当方式进行加热,保温一定的时间,以一定的冷却速度冷却以改变其组织,从而获得所需性能的一种工艺方法。
2、热处理的目的是什么通过适当的热处理工艺改变钢的内部组织结构,来控制相变过程中组织转变的程度和转变产物的形态,从而改善钢的性能。
3、热处理的条件是什么必须有固态相变转变的合金才可以进行热处理。
4、热处理的工艺过程是什么(1)加热:临界点+△T值(2)保温(3)冷却:临界点-△T值一定冷却速度5、主要参数有哪些(1)加热温度T(2)保温时间t(3)冷却速度V,冷却介质决定冷却速度,如:水、盐水、碱水、空气6、按处理阶段及目的可分为哪几种(1)预处理目的是消除偏析、内应力,为最终热处理或后续的加工获得平衡组织。
(2)最终处理作为工件处理的最后工序,获得最终组织。
7、按热处理工艺参数可分为哪几种(1)普通热处理这是生产中最常用的热处理工艺,如退火、正火、淬火、回火等。
这类的热处理一般不会额外的加入其他元素,主要是通过自身组织转变来得到所需要的性能。
(2)化学热处理这类在热处理在齿轮、轴等耐磨件上会经常用到。
工件进行化学热处理时,会在表面一层渗入其他的元素,而对心部的成分不会产生什么影响。
一般渗入什么元素,我们就称为渗×处理,如表面渗C、渗N,C、N共渗等。
(3)表面热处理综合了上述两类热处理的特点,即热处理时不加入其他元素,而且只是针对表面进行的热处理,不影响心部的组织,如表面淬火,但其要求工件的含碳量较高。
8、什么是退火退火是将金属和合金加热到适当温度,保持一定时间,然后缓慢冷却的热处理工艺。
退火后组织亚共析钢是铁素体加片状珠光体;共析钢或过共析钢则是粒状珠光体。
总之退火组织是接近平衡状态的组织。
9、退火的目的是什么(1)降低钢的硬度,提高塑性,以利于切削加工及冷变形加工。
(2)细化晶粒,消除因铸、锻、焊引起的组织缺陷,均匀钢的组织和成分,改善钢的性能或为以后的热处理作组织准备。
热处理必备基础知识整理
热处理知识:一、强化1、细晶强化:细小等轴晶的晶界长,杂质分布较分散,各方向的力学性能差异小,晶粒越细小,强度、硬度、塑性、韧性都好。
2、固溶强化:由于溶质原子进入溶剂晶格的间隙或结点,使晶格发生畸变,使固溶体硬度和强度升高,这种现象叫固溶强化现象。
3、第二相强化:当合金中有第二相金属化合物质点存在时,使质点周围基体(固溶体)金属产生晶格畸变,同时增加了基体与第二相的界面,两者都使位错运动阻力增大,故使合金的强度、硬度提高。
合金硬度、强度优于纯金属,因为2、3、4、热处理强化(相变强化):利用重结晶的方法使相或组织发生变化。
二、相和组织1、铁素体:碳在α-Fe(体心立方结构的铁)中的间隙固溶体。
2、奥氏体:碳在γ-Fe(面心立方结构的铁)中的间隙固溶体。
3、渗碳体:碳和铁形成的稳定化合物(Fe3c)。
4、珠光体:铁素体和渗碳体组成的机械混合物(F+Fe3c 含碳0.8%)5、莱氏体:渗碳体和奥氏体组成的机械混合物(含碳4.3%)三、热处理知识1、热处理:把金属材料在固态范围内通过一定的加热,保温和冷却以改变其组织和性能的一种工艺。
2、退火:将金属或合金的材料或制件加热到相变或部分相变温度,保温一段时间,然后缓慢冷却的一种热处理工艺。
3、正火:将钢加热到完全相变以上的某一温度,保温一定的时间后,在空气中冷却的一种热处理工艺。
4、淬火:将钢加热到相变或部分相变温度,保温一段时间后,快速冷却的热处理工艺。
5、回火:将经过淬火的钢,重新加热到一定温度(相变温度以下),保温一段时间,然后冷却的热处理工艺。
6、调质处理:将钢件淬火,随之进行高温回火,这种复合工艺称调质处理。
7、表面热处理:改变钢件表面组织或化学成分,以其改面表面性能的热处理工艺。
1.退火(炉冷)――半成品热处理、预先热处理将钢加热到一定温度并保温一段时间,然后使它慢慢冷却,称为退火。
退火的目的:(完全退火、等温退火)是为了消除过热组织、残余应力,同时可降低硬度,提高塑性和韧性,改善切削加工性能。
热处理基础知识
3. 淬火
(1)定义: 把零件加温到临界温度 以上30 ~ 50℃,保温一段时间,然 后快速冷却 ( 水冷 )。
(2)目的: 为了获得马氏体组织, 提高钢的硬度和耐磨性。
(3)工艺参数:
(4)常用的淬火冷却介质
名称
最大冷却速度时 平均冷却速度/(℃•s-1)
所在温 冷却速度 650~550 300~200
固体渗碳法示意图
泥封
盖
渗碳箱
试棒
零件 渗碳剂
气体渗碳法示意图
5) 渗碳后的热处理工艺
温 度 930℃
渗碳
850℃
加
热
淬
火
方案1
方案2
时间
(4)渗氮
1)定义:向钢的表面渗入氮原子的过程。
2)目的:获得具有表硬里韧及抗蚀性能 的零件。
3)用钢: 中碳合金钢。 4)方法:气体渗氮。
渗碳与渗氮的工艺特点
1.3 钢的热处理
( Heat Treatment of Steel )
概述 钢在加热时的组织转变 钢在冷却时的组织转变 钢的普通热处理工艺 钢的表面热处理工艺 机械制造过程中的热处理
1.3.1 热处理及其作用
1. 热处理的定义: 将钢在固态下进行不 同的加热、保温和冷却,以改变其内部 组织,从而获得所需性能的一种工艺。
温
保温
度热
加
临界温度
冷 却
时间
2.热处理的目的: 通过改变钢的内部组织 来改善钢的性能,如强度、硬度、塑性、 韧性、耐磨性、耐蚀性、加工性能等。
3.热处理的分类
普通 热处理
退火;正火; 淬火;回火;
感应加 热淬火热处理ຫໍສະໝຸດ 表面淬火表面 热处理
热处理讲稿-热处理基础
射线,在空间传递热量的现象,称为辐射传热。
2. 传热的一般规则
a. 热源与被加热零件之间存在温度差是必要条件。工 件在加热过程中,三种传热方式同时存在,只是强弱 程度不同。
b. > 600℃时,炉子的传热方式以辐射为主,辐射能 力与温度四次方成正比。温度越高,辐射传热能力越 激烈、越强。所以炉温越高,工件升温速度越快,所 需的加热时间就越短。
a. 过冷奥氏体连续转变曲线的位置,比等温 冷却转变曲线的位置靠右下,这说明连续转 变时温度要低一些,孕育期要长一些。
b. 比起等温转变来,连续转变是在一个温度 范围内进行,获得的组织不均匀,往往是几 种组织的混合物。
c. 共析钢连续转变是不发生贝氏体相变,只 有珠光体和马氏体转变。
3.3 合金元素对过冷奥氏体转变的影响 a. 钢在冷却过程中,绝大部分合金元素
少,便宜,应用较广。缺点是完全燃烧部分生成H2O和 CO2,脱碳倾向较大。 b. 吸热式气氛——将气体燃料和空气以一定的比例(体 积比11:1以下)混合,在一定的温度和催化剂作用下, 靠外部加热(一般为960 ℃ ~ 1050 ℃ )才能裂解、进 行反应,所生成的气氛称为吸热式气氛。可燃、易爆, 具有还原性。由于能控制气氛的碳势,故应用最广。
2. 熔盐介质 a. 以熔融状态的中性盐类能导电的性质,将电能转换为热能传递 给工件。盐浴的传热方式以对流和传导为主。由于热容量很大,
故加热速度很快。工件与空气隔离,氧化脱碳极少。盐浴作为等 温和分级淬火的冷却介质,
b.硝盐浴是常用的盐浴,因为熔点低,所以流动性好,有足够的冷 却能力。按不同比例配制的混合盐(如 55%KNO3+45%NaNO2 +1-3%水),可用于200 ℃ ~400℃等温淬火冷却,在盐浴中加 水为了提高冷却能力。
变形铝合金时效热处理相关知识汇总
变形铝合金时效热处理相关知识汇总(1)时效 aging经固溶处理或冷变形后的合金,在室温或高于室温下,组织和性能随时间延续而变化,硬度、强度增高,塑性、韧性降低的现象。
在室温下发生时效称自然时效。
高于室温发生时效称人工时效。
时效现象除铝铜合金外,在钢、铜合金,铁基、镍基、钴基高温合金中普遍存在,是提高合金强度的重要方法。
低碳钢冷变形后在常温长时放置即出现屈服强度提高。
硬铝合金经高温(520℃)淬火后在100~200℃时效,可获得最佳的强化效果。
马氏体时效钢,沉淀硬化不锈钢,铁基、镍基、钴基高温合金均可在固溶处理后选择不同温度时效处理,可以从中获得最佳的组织和性能。
(2)时效处理 aging treatment过饱和固溶体合金在室温或加热至一定温度保温,使溶质组元富集或析出第二相的热处理工艺。
常温下时效称自然时效。
高于室温加热时效称人工时效。
时效析出第二相获得强化的现象称时效强化。
低于或高于强化峰值温度的时效分别称为亚时效与过时效处理。
形变后时效称形变时效或直接时效。
在应力下时效称应力时效。
强化效果取决于析出第二相的类型、数量、尺寸、形态、稳定性等因素。
广泛用于铝合金、钛合金、高温合金、沉淀硬化钢、马氏体时效钢等。
铝合金时效硬化峰值出现在溶质组元的富集 G-P区(Ⅱ)末期。
时效处理是强化合金的有效方法,可显著提高合金的强度和硬度,调整时效温度、时间可使合金的组织、性能满足使用要求,获得高的屈服强度、蠕变强度、疲劳性能等。
含铜4%的铝合金经自然时效后强度为400MPa,比退火状态强度大一倍。
时效硬化合金使用时,使用温度不应超过其时效温度。
(3)时效硬化 age hardening经固溶处理的过饱和固溶体在室温或室温以上时效处理,硬度或强度显著增加的现象。
原因是过饱和固溶体在时效过程中发生沉淀、偏聚、有序化等反应的产物,增加了位错运动的阻力形成的。
位错与析出产物交互作用下硬化机制有位错剪切析出相粒子,基体与粒子间相界面积增加,使外力转变为界面能; 析出相与基体的层错能差异; 基体与析出粒子的切变模量不同。
- 1、下载文档前请自行甄别文档内容的完整性,平台不提供额外的编辑、内容补充、找答案等附加服务。
- 2、"仅部分预览"的文档,不可在线预览部分如存在完整性等问题,可反馈申请退款(可完整预览的文档不适用该条件!)。
- 3、如文档侵犯您的权益,请联系客服反馈,我们会尽快为您处理(人工客服工作时间:9:00-18:30)。
热处理变形工件的热处理变形—主要是由于热处理应力造成的。
工件的结构形状、原材料质量、热处理前的加工状态、工件的自重以及工件在炉中加热和和冷却时的支承或夹持不当等因素也能引起变形。
凡是牵涉到加热和冷却的热处理过程,都可能造成工件变形。
但是,淬火变形对热处理质量的影响最大。
严重的淬火变形往往很难通过最后的精加工加以修正,即使对淬火变形的工件能够进行校正和机加工修整,也会因而增加生产成本。
工件热处理后的不稳定组织和不稳定的应力状态,在常温和零下温度,长时间放置或使用过程中,逐渐发生转变而趋于稳定,也会伴随引起工件的变形,这种变形称为时效变形。
时效变形虽然不大,但是对于精密零件和标准量具也是不允许的。
工件的热处理变形分为尺寸变化(体积变形)和形状畸变两种形式。
尺寸变形归因可相变前后比体积差引起工件的体积改变,形状畸变则是由于热处理过程中,在各种复杂应力综合作用下,不均匀的塑性变形造成的。
这两种形式的变形很少单独存在,但是对具体工件和热处理工艺,可能以一种形式的变形为主。
1>工件热处理的尺寸变化不同的组织具有不同的体积。
常见组织的比体积表如下;组织wc(%) 室温下的比体积/ (cm3/g)奥氏体0—2 0.1212+0.0033(C%)马氏体0---2 0.1271+0.0025(C%)铁素体0---0.02 0.1271渗碳体 6.7+-0.2 0.130+-0.001∈-碳化物8.5+-0.7 0.140+-0.002石墨100 0.451铁素体+渗碳体0---2 0.1271+0.0005(C%)低碳马氏体+∈-碳化物0---2 0.1277+0.0015(C%-0.25)铁素体+∈-碳化物0---2 0.1271+0.0015(C%)工件在热处理加热和冷却过程中,由于相变引起的体积差造成的体积变形。
碳钢组织转变引起的尺寸变化组织转变体积变化(%) 尺寸变化(%)球状珠光体->奥氏体- 4.64+2.21(wc) - 0.015+0.0074(wc)奥氏体->马氏体 4.64 – 0.53 (wc) - 0.0155+0.0018(wc)球状珠光体->马氏体 1.68 (wc) 0.0056(wc%)奥氏体->下贝氏体 4.64 – 1.43 (wc) 0.0156 – 0.0048(wc)球状珠光体->下贝氏体0.78 (wc) 0.0026(wc)奥氏体->铁素体->渗碳体 4.64 – 2.21(wc) 0.0155 – 0.0074(wc)球状珠光体->铁素体->渗碳体0 02>工件热处理的形状畸变工件热处理的形状畸变有多种原因。
加热过程中残余应力的释放,淬火时产生的热应力、组织应力以及工件自重都会使工件发生不均匀的塑性变形而造成形状畸变。
工件细长,炉底不平,工件在炉中呈搭桥状态放置时,当加热至奥氏体化温度下保温过程中,常因自重产生蠕变畸变,这种畸变与热处理应力无关。
工件在热处理前由于各种原因可能存在内应力,例如,细长零件经过校直,大进给量切削加工,以及预先热处理操作不当等因素,都会在工件中形成残余应力。
热处理加热过程中,由于钢的屈服强度随温度的升高而降低,当工件中某些部位的残余应力达到其屈服时,就会引起工件的不均匀塑性变形而造成形状畸变和残余应力的松弛。
加热时产生的热应力,受钢的化学成分、加热的速度、工件的大小形形状的影响很大。
导热性差的高合金钢,加热速度过快,工件尺寸大、形状复杂、各部分厚薄不均匀,会致使工件各部分的热膨胀程度不同而形成很大的热应力,导致工件不均匀塑性变形,从而产生形状畸变。
与工件加热时情况相比,工件冷却时产生的热应力和组织应力对工件的变形影响更大。
热应力引起的变形主要发生在热应力产生的初期,这是因为冷却初期工件内部仍处于高温状态,塑性好,在瞬时热应力作用下,心部因受多向压缩易发生屈服而产生塑性变形。
冷却后期,随工件温度的降低,钢的屈服强度升高,相对来说塑性变形变得更加困难,冷却至室温后,冷却初期的不均匀塑性变形得以保持下来造成工件的变形。
3>热处理变形的一般规律淬火变形的趋势Ms以上时,变形主要由热应力所引起高度大于直径的圆柱体状工件---高度缩短,直径变粗,最终造成腰鼓状变形。
直径大于厚度的圆盘件---厚度增大,直径缩小。
壁厚小于高度的带圆孔的圆(方)孔柱体---内孔收缩,外径增大,高度缩短(壁厚显腰鼓状)。
壁厚小于高度的带圆孔的圆(方)孔扁体---内孔收缩,外径增大(壁厚显腰鼓状)。
正方体---趋向球形。
Ms以下时,变形主要由瞬时组织应力所引起工件变形的趋势是沿最大尺寸方向伸长,沿最小尺寸方向收缩,表面内凹,棱角变尖。
对于长度大于直径的圆柱体工件,具体表现为心部被拉长,直径变细,长度增加。
壁厚小于高度的带圆孔的圆(方)孔柱体---内孔胀大,外径收缩,高度增加(壁厚反腰鼓状)。
壁厚小于高度的带圆孔的圆(方)孔扁体---内孔增大,外径收缩(壁厚显反腰鼓状)。
正方体---平面内凹,棱角突出。
实际生产中,淬火冷却时既有瞬时热应力,也有瞬时组织应力,由于它们引起的变形相反,工件最终的变形,是两种应力引起的变形叠加。
体积效应作用变形及尺寸变化轴类---d + , L + 或d - , L - ;扁平体---d + , L + 或d - , L - ;圆(方)孔柱体---d + , D + , L + 或 d - , D - , L - ;圆(方)孔扁体---d + , D + 或 d - , D - ;正方体--- d + , L + 或d - , L - ;4>影响热处理变形的因素工件在热处理过程中体积和形状的改变,是由于钢中组织转变时的比体积变化所引起的体积膨胀,以及热处理应力引起的塑性变形所造成。
因此,热处理应力愈大,相变愈不均匀,则变形愈大,反之则小。
为减小变形,必须力求减小淬火应力和提高钢的屈服强度。
化学成分对热处理变形的影响钢的化学成分通过影响钢的屈服强度、Ms点、淬透性、组织的比体积和残余奥氏体量等影响工件的热处理变形。
钢的碳含量直接影响热处理后所获得的各种组织的比体积(室温下不同组织的比体积与碳含量间的关系---图略, 碳钢的碳含量与Ms点和残余奥氏体之间的关系---图略)随着钢的碳含量的增加,马氏体的体积增大,屈服强度升高。
淬透性和马氏体比体积的增大,增大了淬火组织应力和热处理变形;而残余奥氏体量的增多和屈服强度的升高,减小了比体积变化,导致组织应力下降和热处理变形的减小。
碳含量对工件热处理变形的影响是上述矛盾因素综合作用的结果。
碳含量对淬火时体积变化量的影响(试样尺寸:¢25*100)钢号淬火温度淬火介质高度变化%直径中间处两端处08 940 14C水- 0.06 + 0.07 - 0.1455 820 14C水+0.38 - 0.02 + 0.21T10 780 14C水- 0.05 + 0.18 + 0.1208钢试样的淬火变形趋势是长度缩短,试样中部直径增大,端部直径缩小,呈腰鼓状,这是因为虽然低碳钢Ms点高,发生马氏体相变时,钢的屈服强度低,塑性好,易变形,但是由于马氏体比体积小,组织应力不大,不会引起大的塑性变形,相反热应力引起的变形量相对较大,最终表现为热应力型变形。
55钢试样,组织应力成为引起变形的主导因素,结果试样的变形为中部直径缩小,端部直径增大,长度增大。
当碳的质量分数进一步增加到0.8%以上时,由于Ms点的降低,残余奥氏体量的增加,其变形又呈长度缩短,直径增大的热应力型变形。
并且由于高碳钢屈服强度的升高,其变形量要小于中碳钢。
对碳素钢来说,在大多数情况下,以T7A钢的变形量为最小。
当碳的质量分数大于0.7%时,多趋向于缩小;但碳的质量分数小于0.7%时,内径、外径都趋向于膨胀。
一般来说,在完全淬透的情况下,由于碳素钢的Ms点高于合金钢的Ms点,其马氏体相变在较高温度下开始。
由于钢在较高温度下具有较好的塑性,加之碳素钢本身屈服强度相对较低,因而带有内孔(或型腔)类的碳素钢件,变形较大,内孔(或型腔)趋于胀大。
合金钢由于强度较高,Ms点较低,残余奥氏体量较多,故淬火变形较小,并主要表现为热应力型的变形,其钢件内孔(或型腔)趋于缩小。
因此,在与中碳钢同样条件下淬火时,高碳钢和高合金钢工件往往以内孔收缩为主。
合金元素对工件热处理变形的影响主要反映在对钢的Ms点和淬透性的影响上。
大多数合金元素,例如,锰、铬、硅、镍、钼、硼等,使钢的Ms点下降,残余奥氏体量增多,减小了钢淬火时的比体积变化和组织应力,因此,减小了工件的淬火变形。
合金元素显著提高钢的淬透性,从而增大了钢的体积变形和组织应力,导致工件热处理变形倾向的增大。
此外,由于合金元素提高钢的淬透性,使临界淬火冷却速度降低,实际生产中,可以采用缓和的淬火介质淬火,从而降低了热应力,减小了工件的热处理变形。
硅对Ms点的影响不大,只对试样变形起缩小作用;钨和钒对淬透性和Ms点影响也不大,对工件热处理变形影响较小。
故工业上所谓微变形钢,均含有较多量的硅、钨、钒等合金元素。
原始组织和应力状态对热处理变形的影响工件淬火前的原始组织,例如,碳化物的形态、大小、数量及分布,合金元素的偏析,锻造和轧制形成的纤维方向都对工件的热处理变形有一定影响。
球状珠光体比片状珠光体比体积大,强度高,所以经过预先球化处理的工件淬火变形相对要小。
对于一些高碳合金工具钢,例如,9Mn2V、CrWMn和GCr15钢的球化等级对其热处理变形开裂和淬火后变形的校正有很大影响,通常以2.5-5级球化组织为宜。
调质处理不仅使工件变形量的绝对值减小,并使工件的淬火变形更有规律,从而有利于对变形的控制。
条状碳化物分布对工件的热处理变形有很大影响。
淬火后平行于碳化物条带方向工件膨胀,与碳化物条带相垂直的方向则收缩,碳化物颗检愈粗大,条带方向的膨胀愈大。
对于Cr12类型钢和高速钢等莱氏体钢来说,碳化物的形态和分布对淬火变形的影响尤为显著。
由于碳化物的热膨胀系数小,约为基体的70%,因而在加热时,沿条带状分布的碳化物方向上,膨胀较小的碳化物抑制了基体的伸长,而冷却时,收缩较小的碳化物又会阻碍基体的收缩。
由于奥氏体化加热温度较缓慢,碳化物对基本膨胀的抑制作用较弱,故条带状分布的碳化物对工件淬火加热变形的方向性影响较小;但在淬火冷却时,由于冷却速度快,碳化物对基体收缩的抑制作用增大,所以淬火后沿碳化物条带方向呈现较大的伸长。
经过轧制和锻造的材料,沿不同的纤维方向表现出不同的热处理变形行为。
纤维方向不明显的正火态试样沿纵、横方向的尺寸变化差别较小;而退火态试样,有明显带状组织存在时,沿纤维方向和垂直于纤维方向的尺寸变化则显著不同。