控轧控冷
控轧控冷总论
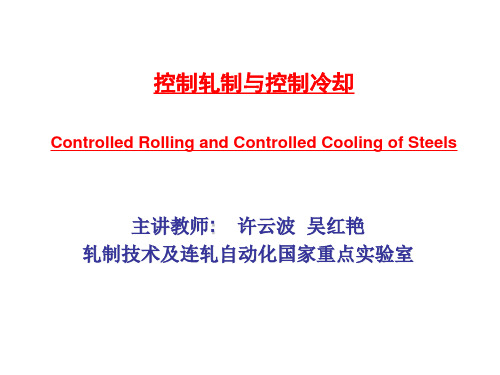
钢的形变热处理
• 钢的形变热处理(TMCP)是指如下工艺过程:控制奥氏体化温度、
变形温度和变形量, 获得理想的奥氏体初始状态; 变形后利用余热控
制冷却, 获得所希望的显微组织, 从而达到控制金属性能的目的。 • 控制轧制和控制冷却技术结合起来,能够进一步提高钢材的强韧性和
获得合理的综合性能,并能够降低合金元素含量和碳含量,节约贵重
艺综合在一起, 成为一个紧密联系的材料体系。
控制轧制的分类 – – – 奥氏体再结晶控制轧制(I 型控制轧制) 奥氏体未再结晶控制轧制(II 型控制轧制) (+)两相区控制轧制
1.1 控制冷却的概念
• 通过控制热轧钢材轧后的冷却条件来控制奥氏体组织状态、控制相变条件、 控制碳化物析出行为、控制相变后钢的组织和性能。 • 现代在线控制冷却工艺的一个重要的金属学特征就是对变形了的未再结晶 奥氏体或再结晶奥氏体进行控制轧制,可根据不同的需要进行不同的组织
控制轧制与控制冷却
Controlled Rolling and Controlled Cooling of Steels
主讲教师: 许云波 吴红艳 轧制技术及连轧自动化国家重点实验室
目
1. 总论
2. 钢的高温变形行为
录
3. 钢的热变形后的相变行为
4. 强韧性能的基本概念及有关理论
5. 钢材的控制轧制理论基础及应用
6. 钢材轧后控制论却技术的基础及应用
7. 钢材的控制轧制和控制冷却技术的结合及应用
1总 论
• 目的: – 了解钢材热加工过程中的形变机理,相变与析出,再结晶行为、强韧化 机制等控制轧制控制冷却工艺的基本原理
– 了解钢材在热加工过程(热轧)的组织演变规律
– 初步具备对不同规律进行定量化或半定量化处理分析的能力 – 在实际生产和科研中应用控制轧制原理 • 金属塑性成型(轧钢): – 定义:金属在外力的作用下,产生塑性变形的过程,它不仅可使金属获 得所必需的尺寸和形状,而且也使之获得所必需的组织和性能。 – 目标:尺寸和外形满足产品标准的公差要求;性能满足产品标准的公差 要求。
新一代TMCP技术控轧控冷

新一代TMCP技术
RAL.NEU
RAL
TMCP技术的发展和创新
• TMCP是20世纪最伟大的钢铁技术成果之一 • 开发引领未来社会发展和人类需求的新一代钢 铁材料 • 需要付出巨大的努力,充分利用新的科技成 果,站在巨人的肩膀上进行钢铁生产过程的脱 胎换骨的革命
RAL
TMCP技术的发展和创新
RAL
高速连轧的温度制度-“趁热打铁”
新一代的TMCP采用适宜的正常轧制温度 进行连续大变形,在轧制温度制度上不再坚持 “低温大压下”的原则。与“低温大压下”过程相 比,轧制负荷可大幅度降低,设备条件的限制 可放松。轧机建设不必追求高强化,大幅度降 低建设投资。
RAL
高速连轧的温度制度-“趁热打铁”
适宜的轧制温度,大大提高轧制的可操作 性,避免轧制工艺事故,例如卡钢、堆钢等, 同时也延长了轧辊、导卫等轧制工具的寿命。 提高产量、降低成本 对于一些原来需要在粗轧和精轧之间实施 待温的材料,可以直接轧制
RAL
“趁热打铁”及其优点
由于新一代的TMCP避免了“低温大压下”,使得传统的“趁 热打铁”的思想得以贯彻实行,这对于减轻生产设备负荷、确 保轧制过程稳定、改善加工过程的可操作性、提高材料的可加 工性、降低轧制能耗等具有十分重要的意义。由于可以少加或 者不加微合金元素和合金元素,所以可以节省大量的资源和能 源,实现减量化的轧制,降低钢材生产成本,这对于钢铁工业 的可持续发展和协调发展具有重要的作用。
RAL
TMCP特征
• 低温大压下——轧制负荷、生产率、设备投 资、轧制稳定性 • 微合金化——提高成本、焊接性能恶化、冶炼连铸-轧制工艺复杂、轧制负荷增大 • 水是最廉价的合金元素——高冷却速率的开发 利用、冷却路径的利用、冷却的均匀性
控制轧制与控制冷却

奥氏体晶粒的大小对钢材的力学性能有显著的 影响。一般用晶粒度表示晶粒的大小。因此, 影响。一般用晶粒度表示晶粒的大小。因此,测定奥 氏体的晶粒度通常作为鉴定钢材质量的指标之一。 氏体的晶粒度通常作为鉴定钢材质量的指标之一。
铁 碳 平 衡 相 图
二、钢的控制轧制
控制轧制是以钢的化学成分调整或添加微合 金元素Nb Nb、 Ti为基础 为基础, 金元素Nb、V、Ti为基础,在热轧过程中对钢 坯加热温度、 开轧温度、 变形量、 坯加热温度 、 开轧温度 、 变形量 、 终轧温度 等工艺参数实行合理控制, 等工艺参数实行合理控制 , 以细化奥氏体和 铁素体晶粒, 并通过沉淀强化、 铁素体晶粒 , 并通过沉淀强化 、 位错亚结构 强化充分发掘钢材内部潜力, 强化充分发掘钢材内部潜力 , 提高钢材力学 性能和使用性能。 性能和使用性能。
控轧控冷的物理冶金基础
轧后冷却速率对γ 轧后冷却速率对γ→α相变及其细化晶粒的 影响: 影响: 研究表明,提高轧后冷却速度能明显降低Ar 研究表明,提高轧后冷却速度能明显降低Ar3, 可抵消奥氏体晶粒细化及相变前形变给晶 粒细化带来的不利影响, 粒细化带来的不利影响,有力地增加了相 变细化晶粒作用。 变细化晶粒作用。这要求在控轧实践中对 冷却制度进行控制。 冷却制度进行控制。
控轧控冷的物理冶金基础
钢中溶质原子及第二相粒子: 钢中溶质原子及第二相粒子:在钢中适当添加 Nb、Ti等微合金元素 细化奥氏体晶粒. 等微合金元素, Nb、Ti等微合金元素,细化奥氏体晶粒. 这种利用高温形变再结晶与微合金元素溶解这种利用高温形变再结晶与微合金元素溶解析出的相互作用使晶粒充分细化的机制便是 控轧中控制奥氏体晶粒尺寸的主要的物理冶 金基础. 金基础.
控轧控冷的物理冶金基础
控轧控冷技术在钢材生产中的应用
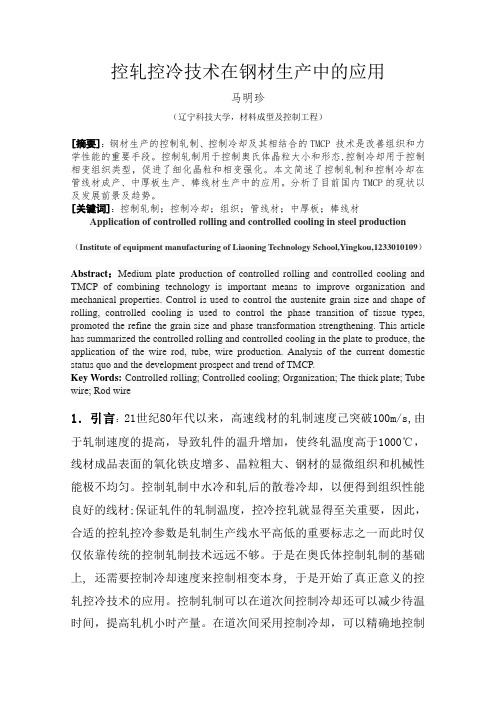
控轧控冷技术在钢材生产中的应用马明珍(辽宁科技大学,材料成型及控制工程)[摘要]:钢材生产的控制轧制、控制冷却及其相结合的TMCP 技术是改善组织和力学性能的重要手段。
控制轧制用于控制奥氏体晶粒大小和形态,控制冷却用于控制相变组织类型,促进了细化晶粒和相变强化。
本文简述了控制轧制和控制冷却在管线材成产、中厚板生产、棒线材生产中的应用。
分析了目前国内TMCP的现状以及发展前景及趋势。
[关键词]:控制轧制;控制冷却;组织;管线材;中厚板;棒线材Application of controlled rolling and controlled cooling in steel production(Institute of equipment manufacturing of Liaoning Technology School,Yingkou,1233010109)Abstract:Medium plate production of controlled rolling and controlled cooling and TMCP of combining technology is important means to improve organization and mechanical properties. Control is used to control the austenite grain size and shape of rolling, controlled cooling is used to control the phase transition of tissue types, promoted the refine the grain size and phase transformation strengthening. This article has summarized the controlled rolling and controlled cooling in the plate to produce, the application of the wire rod, tube, wire production. Analysis of the current domestic status quo and the development prospect and trend of TMCP.Key Words:Controlled rolling; Controlled cooling; Organization; The thick plate; Tube wire; Rod wire1.引言:21世纪80年代以来,高速线材的轧制速度己突破100m/s,由于轧制速度的提高,导致轧件的温升增加,使终轧温度高于1000℃,线材成品表面的氧化铁皮增多、晶粒粗大、钢材的显微组织和机械性能极不均匀。
钢材的控制轧制和控制冷却PPT课件

第11页/共72页
控轧控冷技术发展过程
• 60年代中期,英国钢铁研究会对钢的成分与钢的力学性能之间的关系进行了系 列研究,提出了相应的控制轧制理论;
• 在开发控制轧制工艺时,人们致力于降低终轧温度; • 近些年来,控制冷却工艺已经成功地运用到棒材、螺纹钢、钢管及型钢生产和合
金钢生产中,并取得了明显的经济效益和社会效益。
§1 钢的强化和韧化
对于钢材来说,在大多数情况下其力学性能是最重要的,其中强度性能又居首位。 除了强度之外,钢材还要求一定的韧性和可焊性能,这两个指标和强度是相互关 联甚至互相矛盾的,很难单方面改变某一指标而其它不变。 结构钢的最新发展方向是高强、高韧和良好的焊接性能,控制控冷是满足这一 要求的一种较好的工艺。
§1.1 钢的强化机制
二、固溶强化
(solid solution strengthening)
1、基本概念
• 固溶强化:当合金元素(溶质)固溶 到基体金属(溶剂)中形成固溶体时, 合金的强度和硬度则会提高,称为固 溶强化。如黄铜(Cu-Zn)强度要高于
第30页/共72页
§1.1 钢的强化机制
2、强化机理
第22页/共72页
§1.1 钢的强化机制
金属和合金塑性变形包含晶内变 形和晶间变形。晶内变形是通过各种 位错运动而实现的晶内一部分相对于 另一部分的剪切运动,最基本的是滑 移、孪生和扭折。
控轧与控冷期末重点

控轧与控冷一:名词解释控制轧制:是指在热轧过程中通过对加热制度,变形制度和温度制度的合理控制,使热塑性变形和固态相变结合,以获得细小的晶粒组织,使钢材具有优异综合力学性能的轧制新工艺。
控制冷却:是指控制轧后钢材的冷却速度达到改善钢材组织和性能的目的。
金属强化:通过合金化,塑性变形和热处理等手段提高强度的方法。
微合金钢:合金元素总含量小于0.1%的钢。
变形抗力:在一定条件下,塑性变形时单位面积上抵抗变形的力。
韧性:材料在塑性变形和断裂全过程中吸收能量的能力。
IF钢:又称无间隙原子钢,由于C,N含量低,在加入一定量TI,Nb使钢被固定成碳化物,氮化物或者碳氮化物,从而使钢无间隙存在。
不锈钢:在大气和酸、碱、盐等腐蚀性介质中呈现钝态,耐蚀而不生锈的高铬合金钢。
双相钢:以铁素体相为基,由分散岛状马氏体或贝氏体为强化相的低碳钢。
在线常化:在热轧无缝钢生产中,在轧管延伸工序后,将钢管按常化处理要求冷却到某一温度后,再进行加热炉生产,然后进行减径轧制,按照一定冷却速度冷却至常温。
非调质钢:就是将调质钢的化学成分进行调整,并对轧制工艺过程进行控制,不进行调质,而其性能达到调质钢的水平,以省略调质工序。
铁素体轧制:轧件进入精轧前,必需完成奥氏体向铁素体的转变,使精轧过程完全在铁素体温度范围内进行。
1·控制冷却的工艺特点答:1、节约能耗,简化工艺,降低生产成本。
2、可以降低奥氏体的相变温度,细化室温组织。
3、可以降低碳当量,从而改善材料的焊接性能、低温韧性、冷成型性能4、道次间控冷,可以减少待温时间,提高产量。
2.影响金属强度(韧度)的因素,提高强度(韧度)的措施?答:影响钢材强韧性的因素:1、化学成分 2、气体和夹杂物 3、晶粒细化4、沉淀析出 5、形变 6、相变组织提高措施:1、细化晶粒 2、冶炼:采用真空搅拌,减少有害成分3、控轧:使形变强化,提高材料强韧性4、热处理:阻止晶粒长大,使晶粒细化,提高强韧性3·控制冷却分为几个阶段,其目的是什么?答:一般分为一次冷却,二次冷却,三次冷却(空冷)一:目的就是控制相变前奥氏体的组织状态,为相变做组织上的准备二:目的就是通过控制冷却速度和冷却终止温度来控制相变过程,以保证快冷后得到钢材所要求的金相组织三:目的阻止碳化物析出,保持其碳化物固溶状态,以达到固溶强化的目的4·微量合金元素的作用答:加热时阻止奥氏体晶粒长大;抑制奥氏体再结晶;细化铁素体晶粒;影响钢的强韧性能。
控轧控冷工艺在盘螺降锰中的应用
控轧控冷工艺在盘螺降锰中的应用发表时间:2018-05-21T16:52:35.757Z 来源:《基层建设》2018年第4期作者:宣文娟[导读] 摘要:通过对控轧控冷工艺的应用,能够促进其组织细化和晶粒细化,进而增加盘螺的韧性和强度,保证其抗拉强度和屈服强度较高。中天钢铁集团有限公司江苏常州 213011摘要:通过对控轧控冷工艺的应用,能够促进其组织细化和晶粒细化,进而增加盘螺的韧性和强度,保证其抗拉强度和屈服强度较高。通过实际应用可以得出,在盘螺降锰中应用控轧控冷工艺,效果显著,其屈服度和强度的比例能够很好的满足抗震钢筋的需求,有效的减少了资源消耗,且合金使用成本也明显降低,进而企业的经济效益得到明显增加。关键词:盘螺;控轧控冷;工艺改进一、控轧控冷工艺概述控轧控冷工艺属于一种板材生产技术,其技术核心主要就是在板材轧制的过程中,通过对冷却条件、轧制过程中、加热温度等工艺参数进行合理控制,进而改变板材的焊接、韧性以及强度性能。随着科学技术的快速发展,控轧控冷工艺已经逐渐巩固和完善。
轧控冷可以简单的理解为控制轧制和冷却过程,在Ti、v、Nb等复合低碳微合金钢中得到良好的应用。控制轧制的基础是对钢材的化学成分进行调节,进而控制变形制度、轧制温度、加热温度等工艺参数,对相变产物组织形式和奥氏体状态进行合理控制,进而有效的提升钢材组织性能;控制冷却指的是对钢材轧制后的冷却条件进行控制,通过控制相变条件、奥氏体组织状态以及碳化物析出行为,来改变其性能。通过对控轧控冷工艺的使用,能够显著的提高钢材的综合性能和强韧性,并降低其中的碳元素含量和合金元素含量,通过对贵重合金元素的节约,生产钢材的成本大大降低。相较于普通生产工艺来说,在应用控轧控冷工艺之后,钢板的屈服强度和抗拉强度大约能提升60Mpa左右,在板形保持、冷却均匀性、合金元素节省、碳元素含量降低等多个方面都具有明显优势。二、生产螺纹钢盘条的工艺流程盘螺的生产工艺流程为:第一步热装和冷装连铸钢坯,第二步是在加热炉中进行加热,第三步是出钢机出炉,第四步是通过出炉辊道进行运输,第五步是6架粗轧机组,第六步是切头、事故碎断1群剪,第七步是4架预精轧机组,第八步是预水冷箱,第九步是切头、事故碎断2飞剪,第十步是10架精轧机组,第十一步是3组水冷箱及均温段,第十二步是夹送辊,第十二步是吐丝机,第十三步是延迟型斯太尔摩运输线,第十四步是集卷站集卷,第十五步是P/F钩式悬挂运输机,第十六步是打包,第十七步是称重,第十八步是挂标签,最后是入成品库。三、在盘螺降锰中对控轧控冷工艺的应用(一)常规轧制在相关制作规范中要求,盘螺的抗拉强度需要≥540Mpa,屈服强度需要≥400Mpa,根据实验步骤的不同可以生产出成分不同的两批方坯,主要是坯料中锰成分含量不同。通过常规轧制可以得出,高猛成分盘螺的强度平均是438Mpa,平均锰含量为1.32%;低锰成分盘螺的强度平均是423Mpa,平均锰含量为1.06%。(二)轧后控冷工艺轧制轧后控冷工艺指的是对钢材轧后的余热进行利用,给予相应的冷却速度,对其相变过程进行合理控制,其中不需要对其进行热处理,在其冷却过程进行控制的目的是为了模拟出铅浴淬火过程,进而保证线材能够具有一定的索氏体组织,该组织的综合机械性能比较好。对于线材轧后冷却控制来说,可以将其分为空冷段相变冷却和水冷段强制冷却两个阶段。空冷区和水冷区两个部分共同构成控制冷却工艺,经过水冷控制线材达到相应温度之后,就能够进行吐丝,在风冷线上直条线材呈散圈状分布,实现风冷处理。在本次研究过程中,在常规工艺轧制之后,小批量的低锰成分盘螺通过控轧控冷工艺进行试制,通过传统高猛盘螺比较可以得出以下几个结论:(一)控制加热温度加热炉中的加热时间和加热温度,会在很大程度上对钢坯的性能的组织产生直接影响。虽然终轧温度对钢坯组织性能所产生的影响比较大,但是加热温度的不同会对冷却过程中线材的组织机理转变形成影响。一般来说,根据盘螺性质的独特性,其加热温度需要控制在(1100±5O)℃的范围内,并将开轧温度控制在970~C左右。(二)控制轧制温度在盘螺塑性变形过程中,精轧是最后一个环节,而对于精轧环节来说,实质上也是奥氏体形成再结晶的重要阶段,而且轧制的温度会直接影响到奥氏体再结晶形核的具体个数,随着轧制温度的升高,再结晶形核的个数就会逐渐减少,但是如果想实现盘螺最终珠光体或组织索氏体出现细化,提高其强度和韧性的话,其再结晶形核的个数则是越多越好,这也就表示应该降低轧制温度。因此,在满足工艺条件的基础上,应该尽可能的降低入精轧的温度,一般可以将其控制在830℃左右。(三)控轧控冷系统在精轧之前,需要1组预水冷水箱,长度和恢复段长度分别为8m、12m,水箱的降温能力为100℃。在精轧之后,需要3组控冷水箱,每组长度和恢复段长度都是8m,水箱的降温能力为100℃。另外还需要佳灵、风门、保温罩、大风量风机(10台)、斯太尔摩控制冷却线等装置。(四)控制吐丝温度控制吐丝温度是开始相变温度控制的重要方面。冷却段数量的多少会对吐丝温度的大小产生直接影响,并对奥氏体晶粒的具体尺寸产生间接影响。当轧件在经过精轧处理之后,奥氏体就会逐渐转变为其他相,但是在转变之前,奥氏体还存在着晶粒长大、再结品、恢复等过程,而在这一过程中会受到时间、温度等多种因素的影响,这也就是所谓的吐丝温度控制。在一般情况下,时间越长、温度越高,所形成的奥氏体晶粒也会之间增大。这也就表示,盘螺在出现相变之前,吐丝温度会影响着奥氏体品粒的尺寸大小。在相关调查研究结果中显示,随着逐渐增加的吐丝温度,盘螺的强度指标会增加;随着逐渐降低的吐丝温度,盘螺的塑性指标会增加,最佳的吐丝温度在810℃一850℃范围内。(五)控制冷却速度对冷却速度进行控制,实质上就是控制辊道和冷却风机的速度,其中辊道速度会在很大程度上受到轧件速度、直径、线还间距等因素的影响,其中最关键的是需要对线还间距进行有效控制,而盘螺直径与线还间距密切相关,这也就表示最终的冷却效果实质上是由线还间距距离决定的。在生产实践中可以得出,当辊道冷却速度使不同盘螺环距离>40mm的话,在快速冷却时候的速度就是获得细珠光体的最佳速度;当其距离为40mm的时候,两者之间热量的影响能够达到最小化,进而风机的风量会决定着冷却速度。由此可以得出,标准型冷却工艺参数的最佳间距值为40mm,这也就是控制辊道速度的界限值。除此之外,逐渐增加的辊道速度,并错开盘条搭接点,将热点影响消除,进而使同圈强度均匀性提高。以免在冷却速度比较低的话,析出Fe3C,这样就会限制拉拔。四、工艺改进根据目前使用的机械轧制设备和工艺,为了提高冷却工艺和控制轧制温度,还需要采取相应的措施做出进一步的改进和优化,这可以通过以下一个方面来实现:一是适当的增加风机风量:二是用水冷导槽代替盘圆出口空过导槽;三是住精轧奇架中加入冷却水路,将其末端压力控制在1.0MPa,这样一来轧制温度和吐丝温度都会有所降低;四是及时的更换水冷箱。保证其冷却性能的良好;五是将冷却水管加入中轧出口,保证钢表面的前后温度差为20℃。五、结束语盘螺属于一种热轧带肋钢筋,是通过高速线材轧机批量生产出来的,盘条是其主要的交货状态,一般规格比较小。对于盘螺来说,其强度比较大,与光圆钢筋相比较来说,其握紧力比较好,因此在各个行业和领域中都得到广泛应用,具有比较大的市场需求量。但是目前生产盘螺的成本比较高,企业难以获得良好的经济效益和社会效益,因此就必须加强对工艺的改进和优化,降低其中的锰含量。为了更好的保证盘螺的韧性和强度,就必须加强度控轧控冷工艺的应用,这样在满足标准要求的同时,能够最大限度的减少成本投入。参考文献:[1]郑团星,郭继亮,邱雄文,等.螺纹盘条生产技术的开发与应用[J].钢铁研究,2013,(3):50—52.。
控轧与控冷
控轧与控冷1钢的强化和韧化1.1钢的强化机制通过合金化、塑性变形和热处理等手段提高金属强度的方法称为金属的强化。
金属学方面可应用的强化机制可以有以下几种:置换的或间隙固溶的异质原子以点状障碍物的形式起作用(固溶强化、激冷强化);位错以线状障碍物形式起作用(通过冷加工变形的强化);晶粒界作为面状的障碍物形式起作用(通过晶粒细化);非内聚的析出和内聚的析出显示为空间障碍物形式起作用(弥散强化、沉淀强化)。
1.1.1固溶强化要提高金属的强度可使金属与另一种金属(或非金属)形成固溶体合金。
固溶体合金或以固溶体为基的合金(如碳钢等)一般具有较纯金属高的强度。
这种采用添加溶质元素使固溶体强度升高的现象称为固溶强化。
钢中最主要的合金元素Mn、Si、Cr、Ni、Cu和P都能构成置换固溶体,并促使屈服强度和抗拉强度呈线性增加。
除了置换元素外,C、N等元素在Fe中形成间隙固溶体,但它们在铁中的溶解度都很低,而且随着温度的下降而大大下降。
因此C、N在固溶含量内对屈服强度和抗拉强度的增长影响都很小。
假定合金元素的叠加作用呈线性关系,就可以列出下式用以计算由化学成分引起的强度值。
屈服强度σS(MPa)=9.8{12.4+28C+8.4Mn+5.6Si+5.5Cr+4.5Ni+8.0Cu+55P+[3.0-0.2(h-5)]}抗拉强度σb(MPa)=9.8{23.0+70C+8.0Mn+9.2Si+7.4Cr+3.4Ni+5.7Cu+46P+[2.1-0.14(h-5)]}式中h为产品厚度,各元素含量以百分含量代入。
根据大量的实验结果可得到下表1-1的数据。
1.1.2位错强化图1-1表明实际晶体的强度比理论晶体小得多,但同时随着晶内缺陷或晶格崎变的程度的增加而使强度提高。
塑性变形意味着在位错运动之外还不断形成新的位错,因此位错密度值随着变形而不断提高,一直可达到1012/cm 2。
如果要继续塑性变形就要提高应力值,也就是说材料被加工硬化了。
控扎控冷
1、控制扎制:是在热轧过程中通过对金属加热制度、变形制度和温度制度的合理控制,使热塑性变形与固态相变结合,以获得细小晶粒组织,使钢材具有优异的综合力学性能的轧制新工艺。
2、控制冷却:是控制扎后钢材的冷却速度达到改善钢材组织和性能的目的。
第一篇:第一章1、钢的强化机制:a、固溶强化(分为间隙固溶和置换固溶,添加溶质元素使固溶体强度升高的现象,机理是溶质原子溶入铁的机体中,造成机体晶格畸变,从而使机体的强度提高,以及溶质原子与运动位错间的相互作用,阻碍了位错的运动,从而使材料的强度提高)b、形变强化(决定于位错运动受阻)c、沉淀强化和弥散强化(细小的沉淀物分散于基体之中,阻碍位错运动,而产生强化作用,这就是沉淀强化。
弥散强化与沉淀强化并无太大区别,只是后者是内生的沉淀相,前者为外加质点。
d、细晶强化(晶粒愈细小,晶界就愈多,晶界阻力也愈大,为使材料变形所施加的切应力就要增加,因而使材料的屈服强度提高)e、亚晶强化(低温加工的材料因动态、静态回复形成亚晶,亚晶的数量、大小与变形温度、变形量有关。
亚晶强化的原因是位错密度提高)f、相变强化(通过相变而产生的强化效应称为相变强化)2、韧性:是材料塑性变形和断裂(裂纹形成和扩展)全过程中吸收能量的能力。
材料的冲击韧性指标包括冲击功Ak脆转变温度Tc3、影响材料韧性的因素:a、化学成分的影响b、气体和夹杂物的影响c、晶粒细化的影响d、沉淀析出的影响e、形变的影响f、相变组织的影响第二章1、奥氏体热加工时的真应力-真应变曲线及其组织结构变化示意图,该曲线分为三个阶段(1)、第一阶段:塑性变形量小时,随着变形量增加变形抗力增加,直至达到最大值。
(2)、第二阶段:在第一阶段动态软化抵消不了加工硬化,随着变形量的增加金属内部畸变能不断升高,达到一定程度后在奥氏体内将发生另一种转变,即动态再结晶。
(3)、第三阶段:当第一轮动态再结晶完成以后,在真应力-真应变曲线上将出现两种情况,a、一种是变形量虽不断增加而应力值基本不变,呈稳态变形。
- 1、下载文档前请自行甄别文档内容的完整性,平台不提供额外的编辑、内容补充、找答案等附加服务。
- 2、"仅部分预览"的文档,不可在线预览部分如存在完整性等问题,可反馈申请退款(可完整预览的文档不适用该条件!)。
- 3、如文档侵犯您的权益,请联系客服反馈,我们会尽快为您处理(人工客服工作时间:9:00-18:30)。
关于对控轧控冷与正火的认识1、TMCP技术TMCP(Thermo Mechanical Controlled Processing: 热机械控制工艺)技术是以控制轧制和控制冷却技术相结合的特点,也就是低温轧制和在线热处理的综合处理手段,在控制形变组织的基础上,又控制随后的冷却速度,获得理想的相变组织。
其要点是将连铸坯低温加热到1000℃左右,在具有较小晶粒的奥氏体区开始轧制,在适当的Ar3温度附近的亚稳态奥氏体区或γ+α两相区变形。
随后控制冷却,使加工后未再结晶组织进行恒温转变,通过晶粒内变形带上形成的大量晶核,实现细晶铁素体的转变。
在同样的变形量下,恒温转变温度越低,铁素体的形核率越高,组织晶粒越细。
TMCP技术的实质就是传统的形变热处理工艺在轧制生产中在线完成,从而得到高强度化及高韧性化。
各种轧制程序的模式图,如图1—1所示:(1)控制轧制的类型[3]控制轧制(Controlled Rolling)是通过严格控制热轧工艺参数,充分发挥微合金元素的作用,以达到细化晶粒、改善钢的组织结构和机械性能的目的,从而可直接轧制成材和取消一些热处理工序,取得节能降耗的效果。
最初的控制轧制是在奥氏体低温区进行大的压下量,它是指在比常规轧制温度稍低的条件下,采用强化压下和控制冷却措施来提高热轧钢材的强度和韧性等综合性能的一种轧制方法。
现在人们对控制轧制广义地解释为是通过微合金化处理,从轧前的加热到最终轧制道次结束为止的整个轧制过程实行最佳控制的全新工艺,以控制奥氏体状态和相变产物的组织状态,达到改变钢板的综合机械性能的目的。
控制轧制技术多用于结构钢生产中,因为对结构钢的要求是高强度、高韧性和良好的焊接性能。
而为使结构钢获得最佳综合性能,最好的方法是使钢的晶粒细化,主要是细化铁素体晶粒,它可以通过两种途径来完成:一种是细化奥氏体晶粒,然后通过相变得到细化的铁素体晶粒;另一种是直接细化铁素体晶粒。
这两种方法的机理是不同的,细化奥氏体的机理首先要细化原始奥氏体晶粒,即从加热温度、加热时间和加入微量合金元素这三方面入手,然后采用形变再结晶的方法。
而直接细化铁素体晶粒主要是在(γ十α)两相区轧制。
为此将控轧形式分为三种,即奥氏体再结晶,奥氏体未再结晶区和(奥氏体+铁素体)两相区控制轧制。
在奥氏体高温区(即再结晶区)进行控轧(I型控轧),通常是在950℃以上温度范围进行大量变形,当奥氏体变形达到临界动态再结晶变形量时,变形奥氏体晶粒在轧制道次之间进行再结晶,即、奥氏体晶粒通过轧制—再结晶—轧制—再结晶的反复进行而逐渐得到细化,随着变形量的加大,得到的奥氏体晶粒越细小均匀。
但在奥氏体再结晶区终轧后所得到的铁素体晶粒尺寸最小只能达到8一9级。
在奥氏体低温区(即未再结晶区)进行控制轧制(II型控轧),轧制温度范围一般为950℃~Ar3。
由于再结晶需要一个临界温度T再,在T再以下温度轧制时,变形量再大也不能产生再结晶现象。
一般将T再至相变点Ar3这一区域内称为奥氏体未再结晶区。
在此区域内轧制时,变形奥氏体晶粒不发生再结晶,而是沿轧制方向伸长,在奥氏体晶粒内产生形变带和大量位错,晶粒内部的变形带等价于晶界,且意味着一个奥氏体晶粒可以被形变带分割成几个小部分,显著增加了有效晶界(Sv=奥氏体晶界+形变带)。
而增加奥氏体有效晶界面积又是细化相变后的铁素体晶粒的极重要的措施。
当未再结晶区的压下率为20%时,Sv仅增加1.7%;而当压下率达到80%时,Sv则增大一倍多,(图1—2)为压下率与形变带密度、晶界有效面积Sv的关系图,由图可见增加未再结晶区累积压下量对细化晶粒可以起促进作用,因为此时不仅由于奥氏体晶界的增加而提高了α的形核密度,而且也在奥氏体晶粒内形变带上出现大量的α晶核。
相变形核部位的增加,使相变后的铁素体组织更细小、均匀。
当未再结晶区压下率大于40%时,形变带密度随压下量的增加而迅速增加,形变带将成为铁素体形核的有利位置,因此相变后的α晶粒随着奥氏体未再结晶区总压下率的增加而变细,其细化程度可达11—12级。
但是如果在未再结晶区内的变形量不足,就会得到粗细不均的铁素体晶粒。
和I型控轧相比,在II型控轧阶段终轧后的材料强度将提高,脆性转化温度将下降。
(γ+α)两相区轧制,这是在Ar3以下的(γ+α)两相区轧制,未相变的奥氏体晶粒更加伸长,在晶内形成变形量更大的形变带,铁素体在形变带和晶界上形核,转变成细小等轴的晶粒;另一方面,己相变后的铁素体晶粒在受压时,晶粒内部位错增高形成亚结构,因此在两相区轧制后的组织中,既有由变形的未再结晶奥氏体转变的等轴细小铁素体晶粒,还有被变形拉长的铁素体晶粒,所以相变结束时形成的组织更加细小。
同时,在低温区的变形,促进了含Nb、Ti、V等微合金化钢中碳化物的析出(变形诱导析出)。
在两相区轧制,析出物增多、细小的铁素体亚晶数量增多以及位错密度的增加,都有利于屈服强度增加和脆性转化温度下降。
故控制轧制后使钢材的显微组织结构细化或超细化,从而使钢材的强度提高、韧性改善。
控制轧制与相应的显微组织变化模型,如图1—3所示图1—2 奥氏体再结晶温度以下轧制晶界面积增加和变形带密度图1—3 控制轧制与相应的显微组织变化模型(2)控制冷却控制冷却(Controlled Cooling,缩写cc)其实质是对控制轧制后的奥氏体用高于空冷的速度从Ar3以上的温度冷却至相变温度区域,对铁素体进行控制冷却,并使其进一步细化。
控制冷却引起的Ar3降低,对再结晶后的奥氏体进行控制冷却时,铁素体发生某种程度的晶粒细化,但效果并不显著。
如对未再结晶奥氏体进行控制冷却,则不仅在变形后的奥氏体晶界面或变形带产生晶核,在奥氏体晶粒内也产生铁素体核,实现了铁素体的大幅度晶粒细化。
控冷将控轧后钢板快冷,控制其相变与碳化物析出,在不降低韧性条件下提高强度;在不降低强度条件下,减少碳当量,从而改善焊接性。
控制冷却离不开控冷装置,控冷装置中喷水方式选择是一个关键,采用较多的是水幕、层流、雾化、喷花四种方式。
有单一的喷水方式,也有两种或多种喷水方式相配合,以达到快速、均匀、不同工艺的要求。
国内外典型中厚板控冷装置,各种型式基本齐全,有单一ACC、有ACC和DQ共用,有ACC和DQ分开,也有预留将来上DQ可能性的。
2、控轧、控冷提高性能的机理2.1控制轧制控制轧制的目的就是在热轧条件下,通过细化铁素体晶粒,生产出具有韧性好,强度高的钢材。
所以,控制轧制工艺的优点首先在于在提高强度的同时,可以提高低温韧性。
例如,正常轧制工艺铁素体晶粒最好的情况也是7一8级,直径>20μm,而控制轧制工艺得到的铁素体晶粒为12级,其直径为5μm,这样细的晶粒是控制轧制最突出的优点。
(1)细晶强化细晶强化是一种既能提高钢材强度又能提高韧性的强化手段。
控制轧制就是通过严格控制轧制过程的工艺参数,减小奥氏体相变后铁素体晶粒的尺寸来达到细化晶粒,改善组织结构,从而提高钢强韧性的目的。
晶粒细化对于钢的强度、韧性等性能指标的强化,其理论依据如下面的公式所示:①屈服强度σs:σs=σ0 + K×D-1/2②韧性断裂强度σC:σC= (2G r/k)×D-1/2:③脆性转变温度T转变T转变=A - mD-1/2式中:G —材料切变模量;r —材料的表面能;k —常数;D —铁素体晶粒直径.A, m —常数;从以上公式不难看出,钢材的屈服强度、断裂强度与铁素体晶粒尺寸的D-1/2成正比,即晶粒尺寸越细小,屈服强度和断裂强度越高。
钢材的脆性转变温度与晶粒尺寸的D-1/2成线性关系,铁素体晶粒越细,脆性转变温度越低,低温韧性越好。
相反,钢材的组织越粗大,则钢的强度、特别是低温韧性就差。
(2)微合金化元素无论是控轧还是控冷,目的都是为了使得钢板的晶粒度增加,使晶粒细化从而达到强化的目的。
而在钢中起到细化晶粒和析出强化作用的是微合金化元素。
微合金化元素主要有Nb、V、Ti、Al。
这些元素目前在钢中微合金化作用已得到广泛应用,加入量均在0.1%以下。
桥梁用微合金化钢是充分运用微合金化元素综合作用典型代表,其中铌是取得良好的控轧效果最有效的微合金化元素之一。
其量的最佳配比是研究的关键。
我国从1979年引入钢的微合金化技术以来,经历了用微合金化技术改造我国原有的低合金高强度钢体系、微合金化技术与控轧控冷技术结合开发微合金化新产品等阶段,进步十分显著。
①微合金化元素的强化机理在控制轧制工艺中微合金元素(Nb、Ti、V等)得到广泛应用,这是因为Nb、Ti、V等元素能与C、N元素结合成碳化物、氮化物或碳氮化物。
这些化合物在高温下溶解,在低温下析出,因此加热时阻碍奥氏体晶粒长大,轧制时抑制再结晶及再结晶后晶粒长大,低温时起到沉淀强化的作用。
在细化晶粒和析出强化起主要作用。
②微合金化元素的溶解[11]铌(Nb)在奥氏体中的一般溶解度关系可用下式表示:lg[Nb][C]= —6770/T+2.26lg[Nb][N]= —8500/T+2.80通常含妮钢加热到1200℃、均热2h后,钢中90%的铌可固溶于奥氏体中。
这种固溶铌在加热过程中可阻碍奥氏体晶粒长大,在轧制中会在位错、亚晶界、晶界上沉淀析出铌的碳、氮化物,阻碍奥氏体动态再结晶,这些都有利于晶粒细化。
钒在奥氏体中的一般溶解度关系可用下式表示:lg[V][C]= —9500/T+6.72lg[V][N]= —8830/T+3.46与铌和钛相比,钒的溶解温度较低,它几乎不形成奥氏体中的析出物。
其阻止再结晶的作用较弱,仅在900℃以下才对再结晶起推迟作用,具有轻微的细化组织作用和一定的沉淀强化作用。
钛在奥氏体中的一般溶解度关系可用下式表示:lg[Ti][C]== —7000/T+2.75lg[Ti][N]= —15200/T+3.9可见,TIC与NbC的固溶温度十分接近,而TIN的固溶温度很高,在一般加热温度下固溶量极低。
热力学计算表明[8],在设定的成分条件下,加热温度在1250~1300℃时有80%~100%的Ti溶解, 100%的Nb溶解;加热温度在1200~1250℃时,有60%~80%的Ti溶解, 100%的Nb溶解;加热温度在1150~1200℃时,有40%~60%的Ti 溶解, 90%以上的Nb溶解。
因此, V, Nb强化钢在1200℃左右的加热是足够的,但如果以高Ti含量作为强化,必须提高加热温度。
综合考虑Nb, Ti,V等碳、氮化物的溶解和析出行为并结合热力学计算结果,将板坯加热温度控制在1200~1250℃。
③微合金化元素在控制轧制中的作用Ⅰ、加热时阻止奥氏体晶粒的长大随温度的提高,保温时间的延长,奥氏体晶粒变粗大,对钢材机械性能不利。
加入Nb、V、Ti等元素阻止奥氏体晶粒长大,提高钢的粗化温度。