齿轮渗碳及热处理工艺规程
渗碳淬火热处理工艺
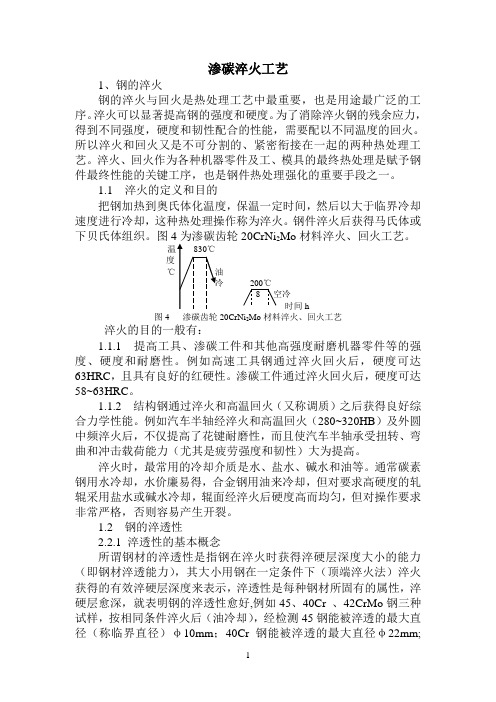
渗碳淬火工艺1、钢的淬火钢的淬火与回火是热处理工艺中最重要,也是用途最广泛的工序。
淬火可以显著提高钢的强度和硬度。
为了消除淬火钢的残余应力,得到不同强度,硬度和韧性配合的性能,需要配以不同温度的回火。
所以淬火和回火又是不可分割的、紧密衔接在一起的两种热处理工艺。
淬火、回火作为各种机器零件及工、模具的最终热处理是赋予钢件最终性能的关键工序,也是钢件热处理强化的重要手段之一。
1.1 淬火的定义和目的把钢加热到奥氏体化温度,保温一定时间,然后以大于临界冷却速度进行冷却,这种热处理操作称为淬火。
钢件淬火后获得马氏体或下贝氏体组织。
图4为渗碳齿轮20CrNi2Mo材料淬火、回火工艺。
度200℃8 空冷时间h图4 渗碳齿轮20CrNi2Mo材料淬火、回火工艺淬火的目的一般有:1.1.1 提高工具、渗碳工件和其他高强度耐磨机器零件等的强度、硬度和耐磨性。
例如高速工具钢通过淬火回火后,硬度可达63HRC,且具有良好的红硬性。
渗碳工件通过淬火回火后,硬度可达58~63HRC。
1.1.2 结构钢通过淬火和高温回火(又称调质)之后获得良好综合力学性能。
例如汽车半轴经淬火和高温回火(280~320HB)及外圆中频淬火后,不仅提高了花键耐磨性,而且使汽车半轴承受扭转、弯曲和冲击载荷能力(尤其是疲劳强度和韧性)大为提高。
淬火时,最常用的冷却介质是水、盐水、碱水和油等。
通常碳素钢用水冷却,水价廉易得,合金钢用油来冷却,但对要求高硬度的轧辊采用盐水或碱水冷却,辊面经淬火后硬度高而均匀,但对操作要求非常严格,否则容易产生开裂。
1.2 钢的淬透性2.2.1 淬透性的基本概念所谓钢材的淬透性是指钢在淬火时获得淬硬层深度大小的能力(即钢材淬透能力),其大小用钢在一定条件下(顶端淬火法)淬火获得的有效淬硬层深度来表示,淬透性是每种钢材所固有的属性,淬硬层愈深,就表明钢的淬透性愈好,例如45、40Cr 、42CrMo钢三种试样,按相同条件淬火后(油冷却),经检测45钢能被淬透的最大直径(称临界直径)φ10mm;40Cr钢能被淬透的最大直径φ22mm;42CrMo钢能被淬透的最大直径φ40mm。
主减速从动齿轮低压真空渗碳热处理工艺

Q S 0 . 2 3 ≤ 1 . 1 0 ≤ 0 . 0 2 0 1 . 0 0 ≤ 0 . 0 1 5 ≤
1 9 27 ^ 0- 3 0 — 0. 02 5 1 3O ^ 0. 25 — — 0_ 2 5 0. 05 0
材料 牌 号 C
表1 材料化量分数,%)
Cr Ni A1 Cu
要求 ,为 了实现低成本 、高性 能 ,主减 速从动齿轮 采用 环保的低压真 空渗碳 、高压气体淬 火技术进行热 处理 。 该 工艺 相 对于 常规 的 可控 气 氛渗 碳 热处 理 有以 下
本文主要针对MI X 主减速从动齿轮采用低压真空 渗碳、高压气体直接淬火热处理过程 中,齿面金相组
织控 制 、热 处理变形 及工艺优化 进行 了探讨 。
材料及热处理技术要求
材料牌号及化学成分 ( 熔炼分析)见表1 ,材料淬
透性 参见表2 。 M 1 X 主 减速 从 动齿 轮热 处理 技 术要 求有 :表 面 硬
5 . 1 氐 压真空渗碳过程渗碳介质的流量设定
设 定依据为处理零 件的表面积 ,因此为 了准确设定 和控制渗碳介 质的流量 ,最好采 用质量流量计 。M1 X 主 减速齿轮 采用乙炔渗碳 ,计算乙炔流量 的经验公式为 : 乙炔流量 ( N L / h )= 1 2 5 0( N L / h )+ 1 2 5( N L / h ・ m m )× 零件表面积 ( m m 2 )× 零件数量/ 1 0 。 。一般情况下 ,实 际
实际工艺取 2 0 0 0 N L / h 。
越高。但并不是所有钢材都适合采用高温渗碳工艺。 根据我厂真空渗碳的经验 ,M1 X 主减速从动齿轮采用
9 4 0 ℃渗 碳 ,渗碳 介质为 乙炔 ( C H : ) ,对应 的F l u x 值 为
齿轮轴零件机械制造工艺规程

1.齿轮轴零件的机械制造工艺规程1.1 零件工艺分析和确定生产类型1.1.1拟定工艺路线由给定的零件图可以看出,该零件图的是齿轮轴类零件,部分加工表面的精度等级达到5级,粗糙度达到0.4μm,因此先大致拟定如下工艺路线:①锻造毛坯,正火②对整个毛坯件进行粗车③对整个毛坯件进行半精车④热处理⑤精车⑥滚齿⑦钻孔,攻丝⑧调质处理⑨对50mm处进行磨削1.1.2确定零件的生产类型根据下式计算--------(1-1) 式中N----零件的生产纲领Q----产品的年产量m----每台(辆)产品中该零件的数量a%----备品率,一般取2%-4%b%----废品率,一般取0.3%-0.7%根据上式就可以计算求得该零件的年生产纲领,在通过查表,就能确定该零件的生产类型。
本设计中,Q=5000,m=1件/台,备品率和废品率为3%和0.5%,将数据代入上式得N=5176件/年,查表可知该零件为轻型零件,本设计中齿轮轴零件的生产类型为大批量生产。
1.2毛坯的选择,绘制毛坯图1.2.1选用锻件为毛坯,采用模锻成型的方法制造毛坯。
1.2.2确定毛坯尺寸及机械加工余量本锻件采用普通级,根据零件图的基本尺寸查表可初步得粗车,半精车,粗磨和精磨外圆的单边加工余量分别为6mm,1.1mm,0.4mm 和0.1mm。
又粗精加工分开时,对于粗车外圆的余量允许小于原表中余量的70%,故可取粗车余量为4.8mm,总的的余量为6.4mm。
再根据手册即可得锻件机械加工余量和公差为:单边加工余量半径a=6r=5±2。
于是,可初步得锻件图的尺寸,如图1-1所±2,长度方向aL示(图中粗实线表示锻件的外形,双点划线表示零件轮廓)。
1.3毛坯图的确定1.3.1计算毛坯加工余量和尺寸公差⑴根据图1-1和计算式---------------(1-2)设锻件最大直径为100mm,长为230mm,则图1-1 齿轮轴零件的锻件图根据上述计算数据,查表可确定零件的形状复杂系数为s,属于简单级别。
齿轮热处理工艺【详尽版】
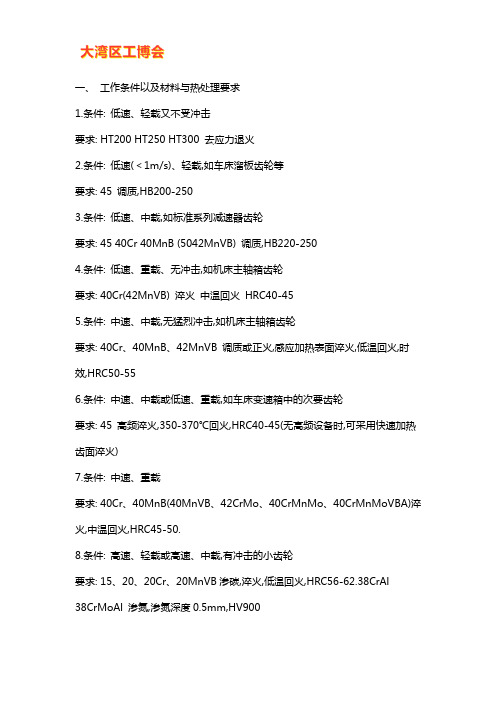
一、工作条件以及材料与热处理要求1.条件: 低速、轻载又不受冲击要求: HT200 HT250 HT300 去应力退火2.条件: 低速(<1m/s)、轻载,如车床溜板齿轮等要求: 45 调质,HB200-2503.条件: 低速、中载,如标准系列减速器齿轮要求: 45 40Cr 40MnB (5042MnVB) 调质,HB220-2504.条件: 低速、重载、无冲击,如机床主轴箱齿轮要求: 40Cr(42MnVB) 淬火中温回火HRC40-455.条件: 中速、中载,无猛烈冲击,如机床主轴箱齿轮要求: 40Cr、40MnB、42MnVB 调质或正火,感应加热表面淬火,低温回火,时效,HRC50-556.条件: 中速、中载或低速、重载,如车床变速箱中的次要齿轮要求: 45 高频淬火,350-370℃回火,HRC40-45(无高频设备时,可采用快速加热齿面淬火)7.条件: 中速、重载要求: 40Cr、40MnB(40MnVB、42CrMo、40CrMnMo、40CrMnMoVBA)淬火,中温回火,HRC45-50.8.条件: 高速、轻载或高速、中载,有冲击的小齿轮要求: 15、20、20Cr、20MnVB渗碳,淬火,低温回火,HRC56-62.38CrAl38CrMoAl 渗氮,渗氮深度0.5mm,HV9009.条件: 高速、中载,无猛烈冲击,如机床主轴轮.要求: 40Cr、40MnB、(40MnVB)高频淬火,HRC50-55.10.条件: 高速、中载、有冲击、外形复杂和重要齿轮,如汽车变速箱齿轮(20CrMnTi淬透性较高,过热敏感性小,渗碳速度快,过渡层均匀,渗碳后直接淬火变形较小,正火后切削加工性良好,低温冲击韧性也较好)要求: 20Cr、20Mn2B、20MnVB渗碳,淬火,低温回火或渗碳后高频淬火,HRC56-62.18CrMnTi、20CrMnTi(锻造→正火→加工齿轮→局部镀同→渗碳、预冷淬火、低温回火→磨齿→喷丸)渗碳层深度1.2-1.6mm,齿轮硬度HRC58-60,心部硬度HRC25-35.表面:回火马氏体+残余奥氏体+碳化物.中心:索氏体+细珠光体11.条件: 高速、重载、有冲击、模数<5要求: 20Cr、20Mn2B 渗碳、淬火、低温回火,HRG56-62.12.条件: 高速、重载、或中载、模数>6,要求高强度、高耐磨性,如立车重要螺旋锥齿轮要求: 18CrMnTi、20SiMnVB 渗碳、淬火、低温回火,HRC56-6213.条件: 高速、重载、有冲击、外形复杂的重要齿轮,如高速柴油机、重型载重汽车,航空发动机等设备上的齿轮.要求: 12Cr2Ni4A、20Cr2Ni4A、18Cr2Ni4WA、20CrMnMoVBA(锻造→退火→粗加工→去应力→半精加工→渗碳→退火软化→淬火→冷处理→低温回火→精磨)渗碳层深度1.2-1.5mm,HRC59-62.14.条件: 载荷不高的大齿轮,如大型龙门刨齿轮要求: 50Mn2、50、65Mn 淬火,空冷,HB≤24115.条件: 低速、载荷不大,精密传动齿轮.要求: 35CrMO 淬火,低温回火,HRC45-5016.条件: 精密传动、有一定耐磨性大齿轮.要求: 35CrMo 调质,HB255-302.17.条件: 要求抗磨蚀性的计量泵齿轮.要求: 9Cr16Mo3VRE 沉淀硬化18.条件: 要求高耐磨性的鼓风机齿轮.要求: 45 调质,尿素盐浴软氮化.19.条件: 要求耐、保持间隙精度的25L油泵齿轮。
20CrMnTi热处理工艺
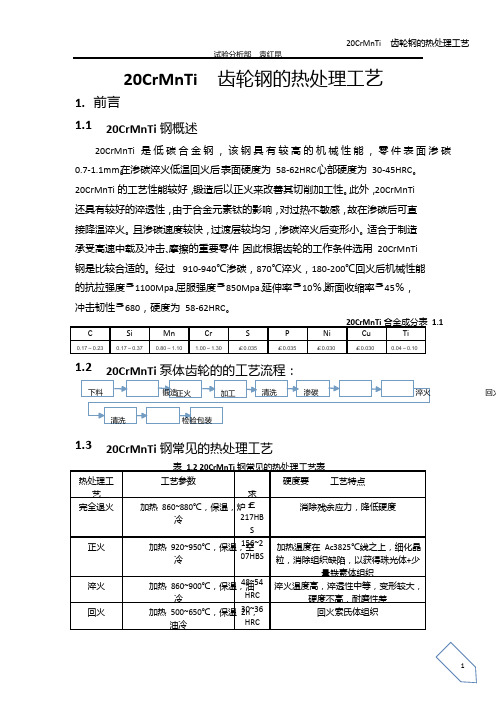
20CrMnTi 齿轮钢的热处理工艺1. 前言1.1 20CrMnTi 钢概述20CrMnTi 是低碳合金钢,该钢具有较高的机械性能,零件表面渗碳 0.7-1.1mm 。
在渗碳淬火低温回火后,表面硬度为58-62HRC ,心部硬度为30-45HRC 。
20CrMnTi 的工艺性能较好,锻造后以正火来改善其切削加工性。
此外,20CrMnTi 还具有较好的淬透性,由于合金元素钛的影响,对过热不敏感,故在渗碳后可直 接降温淬火。
且渗碳速度较快,过渡层较均匀,渗碳淬火后变形小。
适合于制造 承受高速中载及冲击、摩擦的重要零件,因此根据齿轮的工作条件选用20CrMnTi 钢是比较合适的。
经过910-940℃渗碳,870℃淬火,180-200℃回火后机械性能 的抗拉强度³1100Mpa 、屈服强度³850Mpa 、延伸率³10%、断面收缩率³45%, 冲击韧性³680,硬度为58-62HRC 。
20CrMnTi 合金成分表1.1 C Si Mn Cr S P Ni Cu Ti0.17~0.230.17~0.370.80~1.101.00~1.30£0.035£0.035£0.030£0.0300.04~0.101.2 20CrMnTi 泵体齿轮的的工艺流程:1.3 20CrMnTi 钢常见的热处理工艺表1.2 20CrMnTi 钢常见的热处理工艺表热处理工艺 工艺参数硬度要求工艺特点完全退火加热860~880℃,保温,炉 冷£217HB S消除残余应力,降低硬度正火加热920~950℃,保温,空 冷156~2 07HBS 加热温度在Ac3825℃线之上,细化晶 粒,消除组织缺陷,以获得珠光体+少 量铁素体组织淬火 加热860~900℃,保温,油 冷 48~54 HRC 淬火温度高,淬透性中等,变形较大, 硬度不高,耐磨性差回火加热500~650℃,保温2h , 油冷30~36HRC 回火索氏体组织下料 锻造 正火清洗淬火回火加工渗碳包装清洗检验气体渗碳加热900~920℃,以0.15~0.2mm/h计保温时间加热温度不超过920℃,以避免晶粒长大渗碳后淬火与回火淬火:加热820~850℃,保温后油冷60~63HRC心部保持良好韧性的同时,表层获得高的强度、硬度、耐磨性与耐蚀性回火:加热180~200℃,保温2h,空冷表:56~62HRC心:35~40HRC气体碳氮共渗共渗温度840~860℃,出炉油冷60~65HRC心部保持良好韧性的同时,表层获得高的强度、硬度、耐磨性与耐蚀性回火温度160~180℃,出炉空冷表:58~62HRC心:35~40HRC固体渗硼渗硼温度900℃,保温4h,油冷(渗硼剂:85%SiC+10%B4C+5%KBF4) 。
20CrMnTi热处理工艺
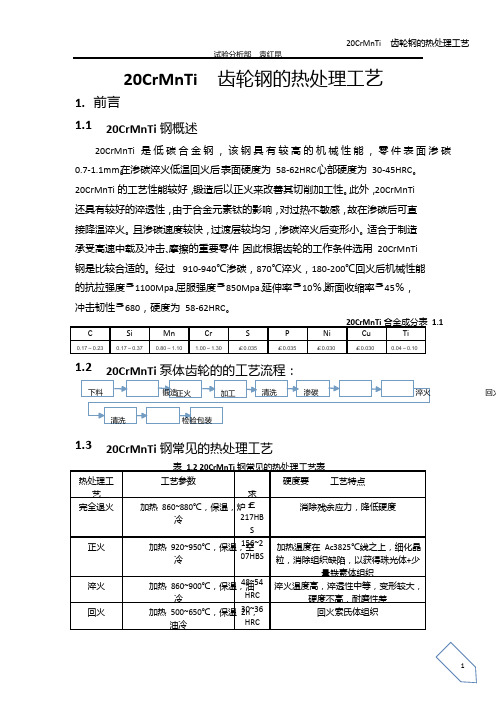
20CrMnTi 齿轮钢的热处理工艺1. 前言1.1 20CrMnTi 钢概述20CrMnTi 是低碳合金钢,该钢具有较高的机械性能,零件表面渗碳 0.7-1.1mm 。
在渗碳淬火低温回火后,表面硬度为58-62HRC ,心部硬度为30-45HRC 。
20CrMnTi 的工艺性能较好,锻造后以正火来改善其切削加工性。
此外,20CrMnTi 还具有较好的淬透性,由于合金元素钛的影响,对过热不敏感,故在渗碳后可直 接降温淬火。
且渗碳速度较快,过渡层较均匀,渗碳淬火后变形小。
适合于制造 承受高速中载及冲击、摩擦的重要零件,因此根据齿轮的工作条件选用20CrMnTi 钢是比较合适的。
经过910-940℃渗碳,870℃淬火,180-200℃回火后机械性能 的抗拉强度³1100Mpa 、屈服强度³850Mpa 、延伸率³10%、断面收缩率³45%, 冲击韧性³680,硬度为58-62HRC 。
20CrMnTi 合金成分表1.1 C Si Mn Cr S P Ni Cu Ti0.17~0.230.17~0.370.80~1.101.00~1.30£0.035£0.035£0.030£0.0300.04~0.101.2 20CrMnTi 泵体齿轮的的工艺流程:1.3 20CrMnTi 钢常见的热处理工艺表1.2 20CrMnTi 钢常见的热处理工艺表热处理工艺 工艺参数硬度要求工艺特点完全退火加热860~880℃,保温,炉 冷£217HB S消除残余应力,降低硬度正火加热920~950℃,保温,空 冷156~2 07HBS 加热温度在Ac3825℃线之上,细化晶 粒,消除组织缺陷,以获得珠光体+少 量铁素体组织淬火 加热860~900℃,保温,油 冷 48~54 HRC 淬火温度高,淬透性中等,变形较大, 硬度不高,耐磨性差回火加热500~650℃,保温2h , 油冷30~36HRC 回火索氏体组织下料 锻造 正火清洗淬火回火加工渗碳包装清洗检验气体渗碳加热900~920℃,以0.15~0.2mm/h计保温时间加热温度不超过920℃,以避免晶粒长大渗碳后淬火与回火淬火:加热820~850℃,保温后油冷60~63HRC心部保持良好韧性的同时,表层获得高的强度、硬度、耐磨性与耐蚀性回火:加热180~200℃,保温2h,空冷表:56~62HRC心:35~40HRC气体碳氮共渗共渗温度840~860℃,出炉油冷60~65HRC心部保持良好韧性的同时,表层获得高的强度、硬度、耐磨性与耐蚀性回火温度160~180℃,出炉空冷表:58~62HRC心:35~40HRC固体渗硼渗硼温度900℃,保温4h,油冷(渗硼剂:85%SiC+10%B4C+5%KBF4) 。
常见汽车级机床用零件机加热处理工艺路线
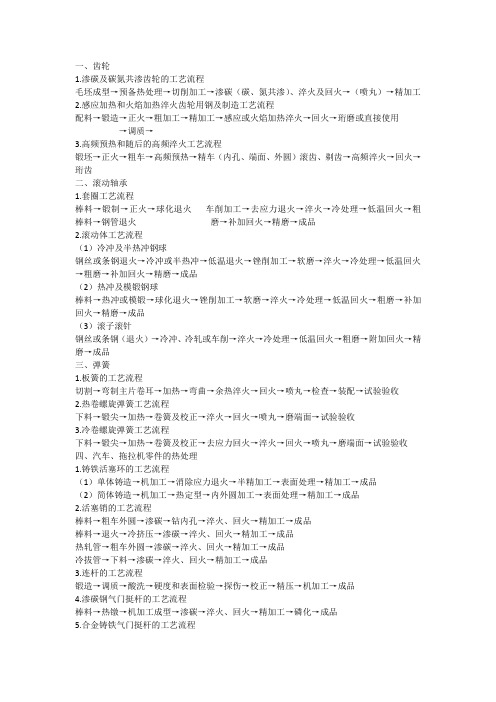
一、齿轮1.渗碳及碳氮共渗齿轮的工艺流程毛坯成型→预备热处理→切削加工→渗碳(碳、氮共渗)、淬火及回火→(喷丸)→精加工2.感应加热和火焰加热淬火齿轮用钢及制造工艺流程配料→锻造→正火→粗加工→精加工→感应或火焰加热淬火→回火→珩磨或直接使用→调质→3.高频预热和随后的高频淬火工艺流程锻坯→正火→粗车→高频预热→精车(内孔、端面、外圆)滚齿、剃齿→高频淬火→回火→珩齿二、滚动轴承1.套圈工艺流程棒料→锻制→正火→球化退火车削加工→去应力退火→淬火→冷处理→低温回火→粗棒料→钢管退火磨→补加回火→精磨→成品2.滚动体工艺流程(1)冷冲及半热冲钢球钢丝或条钢退火→冷冲或半热冲→低温退火→锉削加工→软磨→淬火→冷处理→低温回火→粗磨→补加回火→精磨→成品(2)热冲及模锻钢球棒料→热冲或模锻→球化退火→锉削加工→软磨→淬火→冷处理→低温回火→粗磨→补加回火→精磨→成品(3)滚子滚针钢丝或条钢(退火)→冷冲、冷轧或车削→淬火→冷处理→低温回火→粗磨→附加回火→精磨→成品三、弹簧1.板簧的工艺流程切割→弯制主片卷耳→加热→弯曲→余热淬火→回火→喷丸→检查→装配→试验验收2.热卷螺旋弹簧工艺流程下料→锻尖→加热→卷簧及校正→淬火→回火→喷丸→磨端面→试验验收3.冷卷螺旋弹簧工艺流程下料→锻尖→加热→卷簧及校正→去应力回火→淬火→回火→喷丸→磨端面→试验验收四、汽车、拖拉机零件的热处理1.铸铁活塞环的工艺流程(1)单体铸造→机加工→消除应力退火→半精加工→表面处理→精加工→成品(2)简体铸造→机加工→热定型→内外圆加工→表面处理→精加工→成品2.活塞销的工艺流程棒料→粗车外圆→渗碳→钻内孔→淬火、回火→精加工→成品棒料→退火→冷挤压→渗碳→淬火、回火→精加工→成品热轧管→粗车外圆→渗碳→淬火、回火→精加工→成品冷拔管→下料→渗碳→淬火、回火→精加工→成品3.连杆的工艺流程锻造→调质→酸洗→硬度和表面检验→探伤→校正→精压→机加工→成品4.渗碳钢气门挺杆的工艺流程棒料→热镦→机加工成型→渗碳→淬火、回火→精加工→磷化→成品5.合金铸铁气门挺杆的工艺流程合金铸铁整体铸造(间接端部冷激)→机械加工→淬火、回火→精加工→表面处理→成品合金铸铁整体铸造(端部冷激)→机械加工→消除应力退火→精加工→表面处理→成品钢制杆体→堆焊端部(冷激)→回火→精加工→成品钢制杆体→对焊→热处理→精加工→表面处理→成品6.马氏体型耐热钢排气阀的工艺流程马氏体耐热钢棒料→锻造成型→调质→校直→机加工→尾部淬火→抛光→成品7.半马氏体半奥氏体型耐热钢(Gr13Ni7Si2)排气阀的工艺流程棒料→顶锻→精压→热处理→精加工→成品8.奥氏体耐热钢排气阀的工艺流程棒料→顶锻→精压→阀面和尾部堆焊耐热合金→热处理→杆部滚压或软氮化→精加工→成品9.半轴调质的工艺流程合金结构钢棒料→锻造成形→正火或退火→机械加工→调质→校直→精加工→成品10.半轴的表面淬火的工艺流程棒料→锻造成形→预先热处理→校直→机械加工→表面淬火→校直→精加工→成品11.柱塞副和喷油嘴偶件的工艺流程热扎退火棒料→自动机加工成型→热处理→精加工→时效→成品12.拖拉机履带板(1)40SiMn2履带板的热处理热轧成形→下料→机加工→热处理→成品(2)ZGMn13履带板的热处理铸造成型→热处理→成品五、金属切削机床零件的热处理1.机床导轨(1)MM7125平面磨床立柱镶钢导轨锻造→正火→机加工→消除应力退火→机加工→淬火→回火→磨(2)M9025工具曲线磨床镶钢导轨锻造→退火→机加工→淬火→回火→磨(3)S788轴承磨床镶钢导轨机加工→消除应力退火→机加工→渗碳→淬火→回火→磨→时效(4)MZ208轴承磨床镶钢导轨锻造→退火→机加工→消除应力退火→机加工→淬火→冰冷处理→回火→磨→时效2.机床主轴(1)CA6104车窗主轴(45钢)下料→粗加工→正火→机加工→高频淬火→回火→磨(2)T68、T611镗床的镗杆及MGB132磨床的主轴(35CrMoAlA钢)下料→粗车→调质→精车→消除应力处理→粗磨→渗氮→粗磨(3)SGC630精密丝杠车床主轴(12CrNi3A)锻造→正火→机加工→渗碳→正火→校直→消除应力→机加工→头部淬火→颈部淬火→回火→磨→时效(4)X62W万能升降台铣床主轴(球墨铸铁QT60-2)铸造→机加工→淬火→回火(5)M1040无心磨床主轴(球墨铸铁QT60-2)铸造→机加工→正火→机加工3.丝杠(1)7级或7级精度一下的一般丝杠(45钢)下料→正火或调质→校直→消除应力处理→机加工(2)6级或6级以上精密不淬硬丝杠(T10或T12钢)球化退火→机加工→消除应力处理→机加工→时效→精加工(3)中大型精密淬硬丝杠(CrWMn)锻造→球化退火→机加工→消除应力→机加工→消除应力→机加工→淬火、回火→冰冷处理→回火→探伤→机加工→时效→精加工→时效→精加工(4)中小型精密淬硬丝杠(9Mn2V)锻造→球化退火→机加工→消除应力→机加工→淬硬淬火→回火→冰冷处理→回火、探伤→机加工→时效→精加工→时效→精加工(5)滚珠丝杠(GCr15,GCr15SiMn)4.弹簧卡头(1)卧式多轴自动车床夹料卡头(9SiCr)锻造→退火→机加工→淬火→回火→机加工→磨开口→胀大定型(2)卧式多轴自动车床送料卡头(T8A钢)锻造→退火→机加工→淬火→回火→磨(3)仪表机床小型专用卡头(60Si2)退火→机加工→淬火→回火→磨(4)磨阀辨机床专用卡头(65Mn)锻造→正火→高温→回火→机加工→淬火→回火→机加工5.摩擦片(1)X62W万能升降台铣床摩擦片(A3)机加工→渗碳→淬火→回火→机加工→回火(2)DLMO电磁离合器摩擦片(65Mn)冲片→淬火→回火→磨(3)电磁离合器摩擦片(6SiMnV)锻造→退火→切片→淬火→回火→磨6.FW250万能分度头主轴(45)锻造→正火→机加工→淬火→回火→机加工7.万能分度头蜗杆(20Cr)正火→机加工→渗碳→机加工→淬火→回火→机加工8.三爪卡盘卡爪(45)正火→机加工→淬火→回火→高频淬火→回火→法蓝→磨加工9.三爪卡盘丝(45)锻造→正火→机加工→淬火→回火→法蓝→磨六、活塞1.20CrMnMo钢制活塞的热处理锻造→正火→检验→机加工→渗碳→检验→正火→淬火→清洗→回火→检验→喷砂→磨削2.钒钢活塞的热处理下料→锻造→检验→预先淬火→球化退火→检验→机加工→淬火→回火→检验→磨削七、凿岩机钎尾锻造→退火→检验→渗碳→检验→淬火→回火→清洗→检验→磨削。
三种常用渗碳合金钢齿轮材料的性能及热处理工艺探讨

4 ) 齿 轮材 料较 好 的切 削加 工性 及热 处理 2 Mo 、 1 8 C r 2 N i 4 W、 2 0 C r Mn T i 是 我公 司齿 轮
WA N G X i u — Q i n
( He b e i T i a n z e He a v y Ma c h i n e r y C o . ,L t d .Ha n d a n 0 5 6 2 0 0 。 C h i n a )
Ab s t r a c t : Ac c o r d i n g t o t h e p r a c t i c a l p r o d u c t i o n r e q u i r e me n t s ,r e l a t e d p op r e r t i e s a n d h e a t - t ea r t me n t p r o c e s s c h a r a c t e i r s t i c s o f 1 7 Cr 2 Ni 2 Mo ,1 8 C r 2 Ni  ̄ W a n d 2 0 C r Mn T i ,t I l I e e e o mmo n l y u s e d i mp o r t a n t g e a r ma t e r i a l s ,w e e r i n t r o d u c e d a n d d i s c u s s e d ,t h i s c a n b e b e n e i f t e d t o p r o v i d e he t t h e o y r b a s i s a n d p r a c i t c a l r e f e r e n c e f o r c h o o s i n g ma t e r i ls a ,w h i c h p e f r o r ma n c e me e t d i f f e en r t d e ma n d, i mp ov r i n g a n d o p t i mi z i n g he t t r a d i t i o n a l h e a t t r e a t me n t p oc r e s s . Ke y wo r d s ::1 7 C r 2 Ni 2 Mo : 8 Cr 2 Ni 4 W; 2 0 Cr Mn T i : p op r e r t y : h e a t — t r e a t me n t
- 1、下载文档前请自行甄别文档内容的完整性,平台不提供额外的编辑、内容补充、找答案等附加服务。
- 2、"仅部分预览"的文档,不可在线预览部分如存在完整性等问题,可反馈申请退款(可完整预览的文档不适用该条件!)。
- 3、如文档侵犯您的权益,请联系客服反馈,我们会尽快为您处理(人工客服工作时间:9:00-18:30)。
4.6.2.放大500倍观察,残余奥氏体含量应不超过15%。
4.6.3.表面晶界氧化层深应小于0.001英寸(0.025mm)。
东风汽车公司
康明斯C系列发动机标准
康明斯标准号
71105
4.4.回火
零件从室温加热至350°F(177°C)以上,保温1小时以上,空冷至室温。
4.5.机械性能
4.5.1.有效硬化层深度测量
节圆和齿根圆角处到50HRC的有效硬化层深度,按照表1:有效硬化层深度,节圆和齿根圆角-公制;或表2:有效硬化层深度,节圆和齿根圆角-英制。对于表中没有给出的尺寸值可用直接插入法求出。成品齿轮的硬化层深度可用下述方法测定:
下列适用的文件可从康明斯工程标准10054——标准组织地址,所列的相应机构获取。
a. ASTM E 18,
b. ASTM E 112,
c. ASTM E 140,
d. ASTM E 384,
e.康明斯工程标准10054,标准组织地址
f.康明斯工程标准10056,术语汇编
g.康明斯工程标准10551,成品齿轮的货源认可
0.51
2.50
0.41
1.00
0.41
2.00
0.34
0.79
0.34
1.50
0.27
0.60
0.27
表2:有效硬化层深度,节圆和齿根圆角-英制
节圆
齿根圆角
法向径节
最小(英寸)
最大(英寸)
最小(英寸)
4
0.035
0.070
0.035
6
0.025
0.060
0.025
8
0.020
0.050
0.020
10
4.7.3.轧制的钢材和锻件应清洁、无氧化皮。材料正确,无皱皮、裂纹、伤痕等外部缺陷,也无缩孔、内裂纹和偏析等内部缺陷。
东风汽车公司
康明斯C系列发动机标准
康明斯标准号
71105
共4页
齿轮渗碳及热处理工艺规程
-012
第4页
附录A:图
节线(横向)
齿根圆角
(横向)
注:
如果节线位置不易确定,可近似用如图所示齿顶与齿根之间的一半距离定位。
4.1.3.按本标准加工的材料,奥氏体晶粒度应不粗于ASTM No.5级(按照ASTM E 112测定)。
4.2.化学成分
在气体环境和适宜温度下渗碳足够时间,使齿轮整个表面形成0.70~0.90%的表面碳浓度,并满足本标准或工程图纸规定的性能要求。
4.3.淬火
渗碳后,炉冷至适宜温度[一般为1500~1550°F(816~843°C)],在充分搅拌的油中淬火。齿轮可加压淬火或柱塞淬火,以控制扭曲。
0.016
0.040
0.016
12
0.0Hale Waihona Puke 40.0330.014
16
0.011
0.025
0.011
20
0.009
0.020
0.009
4.5.2.表面硬度
按照ASTM E 18,表面硬度应满足表3要求:
规定的最小有效硬化层深度
硬度标示
要求
0.010英寸(0.25mm)
HR15N
89.0-91
0.015英寸(0.38mm)
HR30N
75.0-79
0.020英寸(0.51mm)
HR40N
63.0-69.0
0.030英寸(0.76mm)
HRC
57.0-62.0
4.5.3.心部硬度
按照ASTM E 18,心部硬度应为25~45HRC。
心部硬度应在齿面宽度的中部截面上的根圆与齿的中心线交叉部位测定。(见图A2)
4.6.微观组织
康明斯C系列发动机标准
康明斯标准号
71105
共4页
齿轮渗碳及热处理工艺规程
-012
第2页
表1:有效硬化层深度,节圆和齿根圆角-公制
节圆
齿根圆角
法向模数
最小(mm)
最大(mm)
最小(mm)
5.00
0.73
1.61
0.73
4.00
0.67
1.55
0.67
3.50
0.55
1.35
0.55
3.00
0.51
1.27
h.康明斯工程标准16154,荧光磁粉探伤
3.定义:
本标准无专门定义。标准内使用的康明斯工程标准专用术语见康明斯工程标准10056——术语汇编。
4.详述
4.1.意义和用途
4.1.1.本标准包括了齿轮气体渗碳和淬火后要求达到的特性。
4.1.2.本工艺方法主要用于获得“韧”的低碳马氏体芯部,和硬的高碳回火马氏体表层。
东风汽车公司
康明斯C系列发动机标准
康明斯标准号
71105
共4页
齿轮渗碳及热处理工艺规程
-012
第1页
1.范围
本标准适用于齿轮的气体渗碳与淬火。
典型加工材料:符合CES 31013(8620H)或CES 31067 [SAE EX15H(前版本)4120H(新SAE/AISI版本)]的合金钢。
2.适用的文件
图1:有效硬化层深度
齿中心线
齿端
齿宽
齿宽中线
节圆
齿根圆
图2:心部硬度
共4页
齿轮渗碳及热处理工艺规程
-012
第3页
4.6.4.心部的显微组织应与规定的合金和截面尺寸从全奥氏体区淬火所获得的显微组织相一致。
4.7.其它要求
4.7.1.成品齿轮的目视-磁粉探伤按照CES 16154进行。
4.7.2.任何偏离本工艺标准的齿轮必须按照货源鉴定标准CES 10551进行检验后才能接收。所有工艺过程的细节均应控制,并由生产厂的工艺更改控制系统形成文件。
a.垂直于齿宽,在齿宽的中部切取一个法向截面。
b.在淬、回火后的齿轮的节圆和齿根圆角处,测有效硬化层深度(见图A1)。有效硬化层深度是用符合ASTME384要求的努氏或维氏硬度计(500克负荷),测定横截面从表面一直到获得HRC50的最大垂直深度。允许按照ASTM E140进行硬度换算。
东风汽车公司