电液位置伺服系统设计方法
机械电液伺服控制系统设计研究
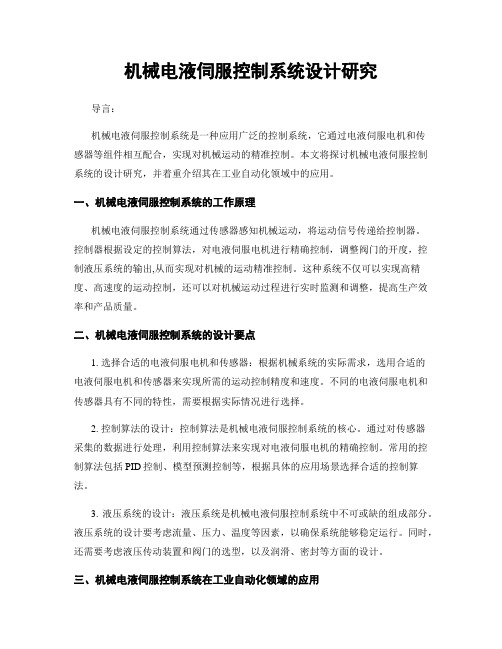
机械电液伺服控制系统设计研究导言:机械电液伺服控制系统是一种应用广泛的控制系统,它通过电液伺服电机和传感器等组件相互配合,实现对机械运动的精准控制。
本文将探讨机械电液伺服控制系统的设计研究,并着重介绍其在工业自动化领域中的应用。
一、机械电液伺服控制系统的工作原理机械电液伺服控制系统通过传感器感知机械运动,将运动信号传递给控制器。
控制器根据设定的控制算法,对电液伺服电机进行精确控制,调整阀门的开度,控制液压系统的输出,从而实现对机械的运动精准控制。
这种系统不仅可以实现高精度、高速度的运动控制,还可以对机械运动过程进行实时监测和调整,提高生产效率和产品质量。
二、机械电液伺服控制系统的设计要点1. 选择合适的电液伺服电机和传感器:根据机械系统的实际需求,选用合适的电液伺服电机和传感器来实现所需的运动控制精度和速度。
不同的电液伺服电机和传感器具有不同的特性,需要根据实际情况进行选择。
2. 控制算法的设计:控制算法是机械电液伺服控制系统的核心。
通过对传感器采集的数据进行处理,利用控制算法来实现对电液伺服电机的精确控制。
常用的控制算法包括PID控制、模型预测控制等,根据具体的应用场景选择合适的控制算法。
3. 液压系统的设计:液压系统是机械电液伺服控制系统中不可或缺的组成部分。
液压系统的设计要考虑流量、压力、温度等因素,以确保系统能够稳定运行。
同时,还需要考虑液压传动装置和阀门的选型,以及润滑、密封等方面的设计。
三、机械电液伺服控制系统在工业自动化领域的应用机械电液伺服控制系统在工业自动化领域中有着广泛的应用。
例如,在机床制造领域,机械电液伺服控制系统可以实现对工件的高精度加工,提高加工效率和加工质量。
在装配生产线上,机械电液伺服控制系统可以实现对物料输送、装配工序等的精确控制,提高生产线的运行效率和产品的质量。
此外,在航空航天、机器人、医疗设备等领域,机械电液伺服控制系统也有着广泛的应用。
例如,在航空航天领域,机械电液伺服控制系统可以实现对飞行器的姿态控制;在机器人领域,机械电液伺服控制系统可以实现对机器人的运动控制,提高机器人的操作精度和自动化水平;在医疗设备领域,机械电液伺服控制系统可以实现对医疗设备的运动控制,提高手术操作的准确性和安全性。
电液伺服系统的建模与控制研究

电液伺服系统的建模与控制研究引言:电液伺服系统(Electro-Hydraulic Servo System)是一种广泛应用于机械领域的控制系统,其通过电气信号控制液压元件,实现对物体位置、速度和力的精确控制。
随着工业自动化技术的不断发展,电液伺服系统在工业生产中的重要性越来越突出。
本文将从电液伺服系统的建模与控制两个方面展开研究,深入探讨其原理和应用。
一、电液伺服系统的建模电液伺服系统的建模是研究其工作原理和特性的基础。
建模是将实际系统转化为数学模型,通过模型分析和仿真研究系统的性能。
电液伺服系统的建模过程涉及到液压传动、机械传动、电气传动以及控制算法等多个方面。
1. 液压传动的建模液压传动是电液伺服系统中最关键的部分,其负责将电信号转化为液压信号,并通过液压元件传递给执行机构。
液压元件包括液压泵、阀门、缸筒等。
液压泵将液体加压,并通过阀门控制液体的流动。
液压缸通过泵送的压力作用,实现对物体位置、速度和力的控制。
液压传动的建模需要考虑压力、流量、阀门开度等方面的变化,利用流体力学和控制理论进行数学描述。
2. 机械传动的建模机械传动是将液压力转化为机械力,实现力的传递和位置的控制。
机械传动包括齿轮传动、皮带传动、曲柄机构等,其目的是将液压系统提供的力矩和转速传递给负载。
机械传动的建模需要考虑传动效率、摩擦损耗等因素,通过机械动力学和力学原理进行数学描述。
3. 电气传动的建模电气传动是将输入信号转化为电气信号,并通过电子元件和电机来实现力和速度的控制。
电气传动包括信号转换、功率放大、速度控制等。
常见的电气传动元件有电阻、电容、电感等,电机则是实现力和速度控制的核心部件。
电气传动的建模需要考虑电路理论和电机原理,通过电路分析和电机模型进行数学描述。
4. 控制算法的建模控制算法是电液伺服系统中实现控制和调节的关键。
常见的控制算法有比例控制、PID控制、模糊控制等。
控制算法的建模需要考虑系统的动态特性和控制目标,通过控制理论和信号处理进行数学描述。
电液位置伺服控制系统实验
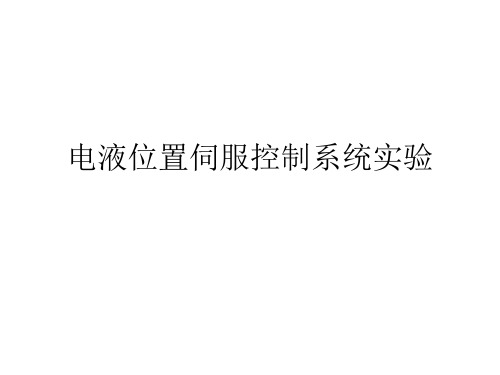
2
s2
2.834 2 0.866 1 2 s s s 1 2 14 .726 14 .726
正常参数时的ωc=2.78, ωh=14.8,Kg=19.1
增大Ki
正常参数
C (s) 4.611 R( s) 1 2 0.866 2 s 14 .726 2 s 14 .726 s 1
斜坡输入1
正弦输入
正弦输入,幅值5,频率1
正弦输入,幅值5,频率2.95
3 液压系统原理
压力传感器2
伺服缸
压力传感器3
平衡阀 电磁换向阀
蓄能器
电液伺服阀 压力传感器1
流量计2
流量计1 精滤器 电磁溢流阀
电机泵组
M
粗滤器 精滤器
4 系统控制原理
数据采集
参考输入
控制器
数模转换
功率放大
伺服阀
伺服缸
K i 73.746 KV 2.834 K d 1 26.022
K d1 h 代入系数得到 K d 1 26 .022 14 .726 h a a 0.12 (b K d 2 ) (b K d 2 ) (0.2 2.861) h h 0.866 2 K d1 a 2 K d 1 a 2 26.022 0.12
mmax 为能量输出单元在线 性范围内的最大值
r0,ml 为输入信号在线性范 围内的最大值
阶跃输入2.5
阶跃输入5
阶跃输入9
阶跃输入12
系统开环传递函数
KV C (s) R(s) 1 2 2 h s 2 s s 1 h h
Ki KV K d1
2)阀控缸微分方程
机电一体化——电液控制系统设计

6.电液控制系统设计6.1概述电液控制系统是常用机电一体化系统之一。
它是将计算机电控和液压传动结合在一起,既发挥了计算机控制或电控制技术的灵活性,又体现了液压传动的优势,充分显示出大功率机电控制技术的优越性。
电液控制系统的种类很多,可以从不同的角度分类,而每一种分类方法都代表一定的特征:1)根据输入信号的形式和信号处理手段可人为数字控制系统、模拟控制系统、直流控制系统、电液开关控制系统。
2)根据输入信号的形式和信号处理手段可分为数字控制系统、模拟控制系统、直流控制系统、交流控制系统、振幅控制系统、相位控制系统。
3)根据被控量的物理量的名称可分为置控制系统、速度控制系统、力或压力控制系统等。
4)根据动力元件的控制方式可分为阀控系统和泵控系统。
5)根据所采用的反馈形式可分为开环控制系统、闭环系统和半闭环控制系统。
本章主要介绍电液控制系统的组成、控制元件,系统数字模型以及系统的设计。
6.2电液控制元件电液控制元件主要包括电液伺服阀、电液比例阀、电液数字阀以及由数字阀组成的电液步进缸、步进马达、步进泵等。
它胶是电液控制系统中的电-液能量转换元件,也是功率放大元件,它能够将小功率的电信号输入转换为大功率的液压能(流量与压力)或机械能的输出。
在电液控制系统中,将电气部分与液压部分连接起来,实现电液信号的转换与放大,主要有电液伺服阀、电液比例阀、电液数字阀以及各种电磁开关阀等。
电液控制阀是电液控制系统的核心,为了正确地设计和使用电液控制系统,就必须掌握不同类型电液控制阀的原理和性能。
6.2.1控制元件的驱动6.2.1.1电气—机械转换器电气—机械转换器有“力电机(马达)”、“力矩电机(马达)”以及直流伺服电动机和步进电动机等,它将输入的电信号(电流或电压)转换为力或力矩输出,去操纵阀动作,推行一个小位移。
因此,电气-机械转换器是电液控制阀中的驱动装置,其静态特性和动态特性在电液控制阀的设计和性能中都起着重要的作用。
电液控制-机液伺服系统

四、液压转矩放大器
Hale Waihona Puke 反馈机构为 螺杆、螺母 液压马达轴完全跟 踪阀芯输入转角而 转动。但输出力矩 比输入力矩要大得 多,故称液压转矩 放大器。
电液步进马达
以惯性负载为主时,可分析得
方框图为:
则系统方框图为:
§系统稳定性分析
液压伺服系统的动态分析和设计一般都是以稳定性要求为 中心进行的。
令G(s)为前向通道的传递函数,H(s)为反馈通道的传递函 数,由以上的方框图可得系统的开环传递函数为:
含有一个积分环节,故系统为Ⅰ型系统。
可绘制开环系统伯德图,如下图所示:
对伯德图的分析
幅值穿越频率ωc≈Kv 相位穿越频率ωc=ωg 为了使系统稳定, 必须有足够的相位裕 量和增益裕量。 由图可见,相位裕 度已为正值,为使幅 值裕度为正值,可计 算求得要求: K 2
与全闭环系统相比,半闭环系统的稳定性好得多,但精度较低。
综上所述,由于结构柔度的影响,产生了结构谐振和液压谐 振的耦合,使系统出现了频率低、阻尼比小的综合谐振,综合谐 振频率ωn和综合阻尼比ξn常常成为影响系统稳定性和限制系统频 宽的主要因素,因此提高具有重要意义。 提高ωn 就需要提高结构谐振频率ωs,就要求负载惯量减小 (但已由负载特性决定),结构刚度增大(提高安装固定刚度和 传动机构刚度,尤其是靠近负载处的传动机构的结构刚度)。 增大执行元件到负载的传动比,可提高液压固有频率;提高 液压弹簧刚度的方法也可提高液压固有频率,从而提高综合谐振 频率。
反馈从活塞输出端Xp取出时,构成为半闭环系统,其方框图 为:
此时系统开环传函中含有二阶微分环节,当ωs2和ωn靠得很 近时,会有零极点相消现象,使综合谐振峰值减小,从而改善 系统稳定性,如曲线b所示。 系统闭环传函为:
《泵控电液位置伺服系统的滑模控制方法研究》

《泵控电液位置伺服系统的滑模控制方法研究》篇一一、引言随着现代工业自动化水平的不断提高,对位置伺服系统的性能要求也日益严格。
泵控电液位置伺服系统作为工业自动化领域的重要一环,其控制方法的优劣直接关系到系统的动态响应速度、稳定性和精度。
传统的控制方法在某些特定情况下可能无法满足高精度控制的需求,因此,研究新型的控制方法成为了一个重要的研究方向。
本文将重点研究滑模控制方法在泵控电液位置伺服系统中的应用。
二、泵控电液位置伺服系统概述泵控电液位置伺服系统主要由电机、泵、阀、执行机构等部分组成。
其工作原理是通过电机驱动泵,将液压能转化为机械能,再通过阀的控制实现执行机构的精确位置控制。
该系统具有高精度、高动态响应和高稳定性等特点,在工业自动化领域有着广泛的应用。
三、滑模控制方法原理滑模控制是一种非线性控制方法,其基本思想是设计一个滑模面,使得系统状态轨迹能够在该滑模面上滑动,从而达到控制目的。
滑模控制具有响应速度快、对模型误差和外界扰动具有较强的鲁棒性等优点。
在泵控电液位置伺服系统中应用滑模控制方法,可以有效地提高系统的控制精度和稳定性。
四、滑模控制在泵控电液位置伺服系统中的应用1. 滑模面设计:根据泵控电液位置伺服系统的特点,设计合适的滑模面。
该滑模面应能够反映系统的动态特性和稳态特性,使得系统状态轨迹能够在该滑模面上平滑地滑动。
2. 控制器设计:根据滑模面的设计,构建相应的控制器。
控制器应能够根据系统当前状态和目标位置,计算出合适的控制量,使得系统状态轨迹能够快速、准确地到达目标位置。
3. 稳定性分析:对控制系统进行稳定性分析,确保系统在受到模型误差和外界扰动时仍能保持稳定。
4. 实验验证:通过实验验证滑模控制在泵控电液位置伺服系统中的有效性。
将滑模控制方法与传统的控制方法进行对比,分析其在动态响应速度、稳定性和精度等方面的性能。
五、实验结果与分析通过实验验证,本文提出的滑模控制在泵控电液位置伺服系统中取得了良好的效果。
汽轮机电液位置伺服系统的设计与仿真
lct ft e c n r l y tm. T e ma h maia d l o l p r f h lcr - y ru i e v y tm r sa l h d a d smua e o i o h o t se y os h t e t lmo es fal a t o e ee t h d a l s r0 s se wee e t bi e n i lt d c s t o c s
Ab t a t sr c :T e d gtl lc r — y r ui o to y t m fi d sr ls a t r i ewa e i n d,t e ee to h d a l e v Mv h i i e t h d a l c n r l se o u t a t m bn s d sg e ae o c s n i e u h l cr - y r u i s r ov e c a d c n r l rwee s l ce . Du l ls d lo p r a h a d P C a h o e o o t ls se wee u e mp e t er s o s e n o t l r ee td oe a o e ・o p a p o c n L s te c r fc n r y t m l s d t i mv h e p n e v — c o o
工业 汽轮机是大型装置 中的关键动力设备 ,具有
高温 、高压 、高转速等特点 ,其控制 系统承担着转速 和负荷调 节及工况控制的任务 ,直接影响着机性高 ,能适应复杂 的 运行工况 ,而且操作 、调整和修 改都 比较方便。
( )模拟式电气 液压 控制 系统 ( n o l t — 3 A a gEe r l co H dal ot l E 。随着 电气元 件可 靠性的提 yru cC n o,A H) i r 高 ,2 O世纪 5 O年代 中期 ,出现 了不依靠机械液压式 调节系统作后备的纯 电调系统 ,开始采用 的纯电调 系
电液位置伺服控制系统实验
减小Ki
正常参数
Ki减小为40
Ki变小,ωc=1.53<2.78, ωh=14.8不变,Kg=24.5>19.1
增大Kd1
正常参数
Kd1变大为35
Kd1变大,ωc=2.1<2.78, ωh=17.1>14.8 ,Kg=21.8>19.1
减小Kd1
正常参数
Kd1减小为20
Kd1变小,ωc=3.45>2.78, ωh=12.9<14.8 ,Kg=16.8<19.1
2)阀控缸微分方程
负载流量线性化方程 流量连续性方程
忽略阀腔和管道总容积,油液的压缩性影响忽略
液压缸活塞的动力学平衡方程
3)缸输出位移对伺服阀输入电信号的传递函数 或写成:
2 伪微分反馈控制算法
对输出信号C 微分的积分仍是C,这就说明没有必要对C 进行微分
2
微分反馈控制方框图
伪微分反馈控制方框图
增大Kd2
正常参数
Kd2变大为3.3
Kd2变大,ωc=2.78不变, ωh=14.8不变,Kg=20.4>19.1
减小Kd2
正常参数
Kd2减小为0.6
Kd2变小,ωc=2.95基本不变, ωh=14.8不变,Kg=7.51<19.1
斜坡输入1
正弦输入
正弦输入,幅值5,频率1
正弦输入,幅值5,频率2.95
为能量输出单元在线 性范围内的最大值
为输入信号在线性范 围内的最大值
2
系统开环传递函数
代入系数得到
正常参数时的ωc=2.78, ωh=14.8,Kg=19.1
增大Ki
正常参数
Ki变大为120
Ki变大,ωc=4.39>2.78, ωh=14.8不变,Kg=15<19.1
电液伺服系统的设计与实现
电液伺服系统的设计与实现随着科技的不断发展,机械设备的功能和性能要求也越来越高。
而在众多机械设备中,电液伺服系统以其优良的性能和高效的工作模式,已经成为了广泛应用的设备之一。
本文将就电液伺服系统的设计和实现进行讨论,以期提高其性能和工作效率。
一、电液伺服系统的组成电液伺服系统是由3个部分组成的:电子控制单元、电液传动系统和执行机构。
1. 电子控制单元电子控制单元包括控制器和信号处理器,控制器是整个系统的核心。
它可以接收来自传感器的反馈信息,根据内部程序计算出控制信号,并输出到执行机构,实现对执行机构的精确控制。
2. 电液传动系统电液传动系统是整个电液伺服系统的动力源,它包括电液转换器、电动机、泵、油箱、阀门等组成。
电动机通过传动装置,驱动泵产生压力液体,液体经过阀门进入执行机构,实现机械臂等动作。
3. 执行机构执行机构是电液伺服系统的输出节点,它通过接收液压驱动,转换为机械运动。
在典型的电液伺服系统中,执行机构通常包括液压缸、液压马达、液压单元等。
二、电液伺服系统的优点1. 精度高因为电液伺服系统可以接收来自传感器的反馈信息,根据内部程序计算出控制信号,并输出到执行机构,实现对执行机构的精确控制,所以其控制精度很高,可以满足高精密度机械设备的要求。
2. 动态性能好电液伺服系统的调节速度快,反应灵敏。
它不仅可以适应于各种工况的需要,而且可以根据需要进行控制和调节。
相比之下,其他传动系统难以满足这些要求。
3. 可扩展性强电液伺服系统的结构比较清晰,它根据要求可以进行功能扩展。
同时,它也可以与其他的控制系统进行集成,如PLC、CAN总线等。
三、电液伺服系统的设计电液伺服系统的设计必须根据所需的实际应用来进行,下面简单介绍了一些设计方法。
1. 系统参数计算电液伺服系统的设计一定要进行系统参数计算,以确保正确的系统工作。
主要包括负载惯性、运动速度、加速度、油液流量、泵、马达的型号、离合器等参数的计算。
2. 控制系统设计控制系统设计是电液伺服系统设计的核心问题。
电液伺服控制课程设计
电液伺服控制课程设计一、课程目标知识目标:1. 理解电液伺服系统的基本原理,掌握其主要组成部分及功能;2. 掌握电液伺服系统的数学模型,了解其动态特性和稳态特性;3. 学会分析电液伺服系统的性能指标,了解影响性能的主要因素;4. 掌握电液伺服系统的控制策略,了解不同控制算法的优缺点。
技能目标:1. 能够运用所学知识对电液伺服系统进行数学建模;2. 能够设计简单的电液伺服控制系统,并进行性能分析;3. 能够运用仿真软件对电液伺服系统进行仿真实验,验证控制策略的有效性;4. 能够对实际电液伺服系统进行调试和优化,提高系统性能。
情感态度价值观目标:1. 培养学生对电液伺服控制系统及其应用的兴趣,激发创新意识;2. 培养学生严谨的科学态度,注重理论与实践相结合;3. 培养学生团队协作精神,提高沟通与交流能力;4. 增强学生对我国液压事业的认同感,树立为国家和民族工业发展贡献力量的信念。
课程性质:本课程为专业技术课程,以理论教学与实践操作相结合的方式展开。
学生特点:学生具备一定的电工电子基础,具有较强的学习能力和动手能力。
教学要求:注重理论联系实际,强化实践教学,提高学生的实际操作能力。
将课程目标分解为具体的学习成果,以便在教学过程中进行有效评估和调整。
二、教学内容1. 电液伺服系统原理及组成部分- 液压基础知识回顾- 电液伺服系统的定义、分类及应用- 主要组成部分(液压泵、液压缸、伺服阀、传感器等)及其功能2. 电液伺服系统的数学建模- 系统的动态方程建立- 系统的稳态方程建立- 模型参数的识别与验证3. 电液伺服系统性能分析- 系统稳定性分析- 系统快速性分析- 系统精确性分析4. 电液伺服控制策略- 常用控制算法(PID控制、模糊控制、自适应控制等)- 控制算法的优缺点分析- 控制策略的设计与优化5. 电液伺服系统仿真与实验- 仿真软件的使用方法- 搭建仿真模型与实验平台- 仿真与实验结果的对比分析6. 电液伺服系统调试与优化- 系统调试方法与技巧- 常见故障分析与处理- 系统性能优化方案教学内容安排与进度:根据课程目标和教材章节,分阶段进行教学,确保内容的系统性和连贯性。
- 1、下载文档前请自行甄别文档内容的完整性,平台不提供额外的编辑、内容补充、找答案等附加服务。
- 2、"仅部分预览"的文档,不可在线预览部分如存在完整性等问题,可反馈申请退款(可完整预览的文档不适用该条件!)。
- 3、如文档侵犯您的权益,请联系客服反馈,我们会尽快为您处理(人工客服工作时间:9:00-18:30)。
FL max Fc Ff Fa (450 1950 1000) N 3400 N
1.2 液压执行机构数学模型
工作台由液压马达经减速器和滚珠丝杠驱动。根据力矩平衡方程,减速器输入 轴力矩TL 为:
式中:t为丝杠导程,i=为减速器传动比,和分别为齿轮减速器输入轴d. 由运动传递原理知,液压马达最大转速为: iv
系统方块原理图
1.1 工作台负载分析
工作台负载主要由切削力,摩擦力和惯性力三部分组成。根据机床的实际 情况,取切削力= 450 N;摩擦力具有“下降”特性,为简化模型,可认为与速 度无关,为定值,取最大值=1950 N;惯性力按最大加速度考虑,则:
Fa mt a max 1000 1N
假定系统是在最恶劣的负载条件(即所有负载力都存在且速度最大)下工作,则 总负载力为:
式中: vmax
为工作台的最大运动速度。
nmax
max
t
由液压马达输出力矩表达式可知,液压马达所需排量 Qm
Qm 2 Dm 2 TL / pL
为
式中: 为液压马达负载压力,MPa,一般取 PL 2 Ps / 3 为液压系统压力,MPa;Dm 为液压马达弧度排量 m3 / rad 已知:i=2, t 1.2 102 m / r ps 63 105 Pa 由式(2)、式(4)计算得: Dm 0.8 106 m3 / rad q 所以,液压马达负载流量 为:L Qm nmax (5) pV ps pL max (6) 伺服阀压降pV 为: 考虑泄漏等影响, qL 增大15%, qL =4.6 L/min。 qL qL 根据和,查手册得额定流量,选择液控型变量柱塞泵和电液伺服阀。
1.3 电液伺服控制系统的传递函数
放大器增益Ka为: 式中:Δ I为输出电流,A;Ue为输入电压,V。 电液伺服阀的传递函数由样本查得为:
式中: 为伺服阀流量;Ksv为伺服阀的流量增益。经计算, 额定流量Pn=8L/min的阀在供油压力时,空载流量 q0m=1.27×10-4 m3/s,所以阀的额定流量增益Ksv =q0m/ In=4216×10-6则伺服阀的传递函数为: 因为负载特性没有弹性负载,因此液压马达和负载的 传递函数为:
、
、
取 则,液压阻尼比为:
,
得:
1.24将Dm
、
值代入式(10)得: 位移传感器和放大器的动态特性可以忽略,其传递函数可以用它 们的增益表示。传感器增益 Kf为: 为反馈电压信号; 式中: 为工作台位移,mm。 减速齿轮与丝杠的传递函数为:
、
系统仿真
由图 2 可以确定伺服系统的开环传递函数为:
式中:Kv为系统开环增益。
小组成员:
指导教师:孔祥东 张伟
目录
引言
系统概述
系统模型 系统仿真
结论
感想
引言
电液伺服系统是一种由电信号处理装置和液压动 力机构组成的反馈控制系统。电液位置伺服系统 是最基本和最常用的一种液压伺服系统,如机床 工作台的位置、板带轧机的板厚控制等。在其他 物理量的控制系统中,如速度控制和力控制等系 统中,也常有位置控制小回路作为大回路中的一 个环节。 电液位置伺服系统主要用于解决位置跟随的控制 问题,其根本任务就是通过执行机构实现被控量 对给定量的及时和准确跟踪,并具有足够的控制 精度。通过对系统的静态与动态分析,让我们更 多的了解体统的性能特点,电液位置伺服系统的 设计和仿真也越来越受重视。
G (s) H (s) s( Kv s 2 0.5 s2 2 1.24 1)( s 1) 2 2 600 600 388 388
2
K v K a 4216 106 1.25 106 9.56 10 4 100 504 K a
式中:Ka为放大器增益。 根据以上确定的传递函数,用 Simulink 可绘制出机床工作台液压伺服系统 的仿真模型,如图 2 所示,仿真参数如表 1 所示。
式中:
为系统输入信号。系统的速度误差
式中:v 为工作台运动速度 对于干扰来说,系统是 0 型的。启动和切削不处于同一动作阶段,静摩擦干 扰就不必考虑。伺服放大器的温度零漂为 0.5%~1%、伺服阀的零漂和滞环为 1 %~2%、执行元件的不灵敏区为 0.5%~1%。假定上述干扰量之和为±2%,由 此引起的系统的位置误差 5
式中:ω h为液压固有频率,Hz;ξ h为液压阻尼比 式中:β C为系统的有效体积弹性摸数,MPa;Vt为液压马达的容积,m3; Jt为工作台质量算到液压马达轴的转动惯量为Jt考虑齿轮、丝杠和液压马 达的惯量取 ,并取液压马达的容积 ,则液压固有频率为: 假定阻尼比仅由阀的流量-压力系数产生。零位流量-压力系数 Kc0 近似计算为:
能在稳定性、频带宽度及稳态误差等性能指标方面满足设计任务的要求。
图 4 数控机床工作台液压伺服系统 仿真结果(Ka=0.179)
图 5 系统的开环系统 Nichols 图
结论
从对电液位置伺服系统设计与动态 仿真的过程可以看出,电液位置伺 服控制系统具有自身设计方法和特 点。应用MATLAB对液压控制系统 进行动态仿真,可以有效预见系统 的输出,达到对系统工作状态的了 解,具有方便、直观和准确的优点 ,有利于系统参数的选择优化,对 电液位置伺服控制系统设计具有一 定的参考意义。
、
图a
图 3 数控机床工作台液压伺服 系统开环 Bode 图
图b
2. 闭环系统的频宽
机床工作台液压伺服系统的闭环系统 Nichols仿真曲线如图 5 所 示,由曲线中-3 dB 与 Nichols 线的交点分析得出:闭环系统频带宽 f 3dB =26.3Hz 度
3. 系统的稳态误差分析
系统的位置误差
3.系统的工作原理
多功能接口卡提供正确 的取样时间以及接受各种 传感器的信号,信号经过 计算机的软件处理后,再 由多功能接口卡输出电压 信号控制电液伺服阀。电 液位置伺服系统的工作原 理图如图1所示。
系统模型
下图为某数控机床工作 台位置伺服系统的系统 方框原理图。由于系统 的控制功率较小、工作 台行程较大,所以采用 阀控液压马达系统。
>10 Hz
仿真结果分析
1. 系统稳定性
根据系统开环传递函数做出 Ka=1 时仿真 Bode图 (图 3)有:
、
,相位裕量和增益裕量有负值,此时不稳定。 为了使系统稳定,考虑将图中0dB线上移,使相位裕量 ,由 得开环增益为: ,此时增益裕量 穿越频率 ,由式可得放大器增益
为: 式所确定的 Ka是通过计算所得的,做出Ka=0.179 时开环系统 的 Bode 图,如图3(b)所示,可以看出: ,相位裕量和增益裕量为正值,系统是一个稳定系统。 所以,Ka=0.179 就是所求的放大器增益。Ka=0.179时,系统的仿真输出结 果如图4所示,当输入 时输出 系统是稳定的。
系统参数
参数 参数值
工作台擦力 Ff
1950N
最大切削力 Fc
450N
工作台最大行程 smax
0.5 m
工作台最大速度 vmax
8×10-2m/s
工作台最大加速度 amax
1 m/s2
静态位置误差(位置分辨力)ef
<±0.05 mm
速度误差 er
<1 mm
频带宽度 f-3dB
2.系统的特点
输出功率大
控制精度高 响应速度快
信号处理灵活
易于实现各种 参量的反馈
系统概述
1.系统的组成
电液位置伺服系统主要由三部 分组成:机械装置,液压伺服 装置以及控制装置。机械装置 由工作台、滑轨织成。液压伺 服装晋由梓制装晋和负载液压 缸、流量伺服阀、压力伺服阀、 油源等组成。电液位置伺服系 统主要由三部分组成控制装置 由传感器、解码器、多功能接 口卡、计算机等组成。
感想
通过对电液位置控制系统设计的分析, 了解到了对电液位置控制系统的研究方法。在 本项目的完成过程中,对课本知识有的更深刻 的理解,并对课本知识的应用更深一步的认识。 这次的课程设计,对于培养我们理论联系实际 的设计思想、训练综合运用课程的理论,结合 生产实际反应和解决工程实际问题的能力,巩 固、加深和扩展有伺服系统方面的知识等方面 有重要的作用。也更加熟练的应用了也提高了 对MALAB的应用熟练程度,讨论的过程中, 遇到很多问题在大家团结协作,共克时艰,取 得了很大的收获
e f 3.35 10 m
对指令输入来说,系统是 I 型的,最大速度
vmax 8 102 m / s 时的速度误差为 er 8.9 104 m
er 8.9 104 m
综上所述,所设计的系统能达到的性能指标为: e 3.35 105 m f
f 3dB =26.3Hz