电液位置伺服控制系统设计方法
基于DSP-NNCPID的电液位置伺服控制系统的设计

( 湖北汽车工业学院 电子信息系, 湖北 十堰 4 20 ) 4 0 2
摘 要 : 文 以 电液 位置 伺服 机械 手第 一 关节为研 究对 象 , 出一 种基 于 N C—PD的 P 本 提 N I C机 +D P控 制 方 S
案 。详 细说 明 了系统硬件 电路 各部 分 的设计 和 系统 软件 各模 块 的设 计 。利 用神 经 N I I N —PD控 制 器 的 自
电路 和输 出放大 驱动 电路 以及 上位 机 P c等组 成 。实 现定位 和伺 服跟 踪控 制 。 收稿 日期 :0 0— 4— 1 2 1 0 0
Li ng YuHong a
( e a m n o l t nc C m nct nE gn eig H b i uo oi n ute D pr et f e r i t E c o s& o mu i i n ier , u e A tm t eId sis ao n v r Is tt, u e S i n4 2 0 , hn ) ntue H b i hy 4 0 2 C ia i a
rm tr e js n.T ecnrl ytm o eN C— I o t l r hw a tego oio akpe a ee ̄sl a ut t h o t s fh N PD C nr l o s h th odps i t c r— f d me os e t oe S t tn r
制 系统响应 快 和高精 度 的要求 。
1 电液位 置伺 服 系统 构 成
以喷漆机械手第一关节为对象 , 构造了研究实验装置 , 如图 l 所示。其中反馈器件采用精密导 电塑料 电位计 。整个控制系统以 D P为核心、 S 由喷漆机械手第一关节 、 位置传感器 、2 A D和 D A 信号调理 1位 / /、
电液伺服系统及其控制文档
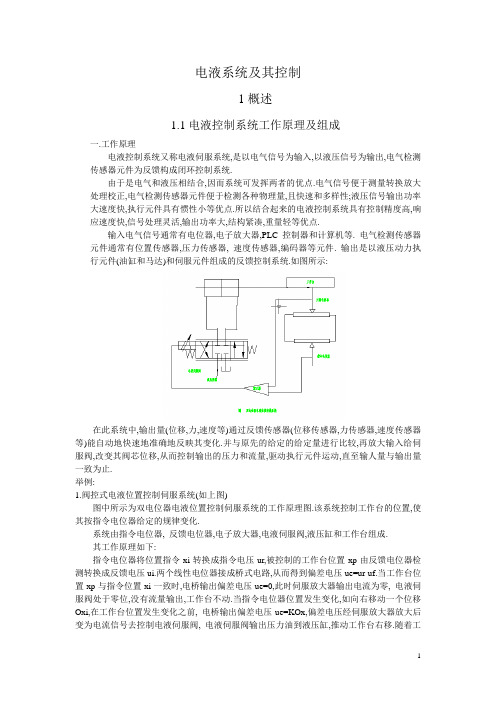
电液系统及其控制1概述1.1电液控制系统工作原理及组成一.工作原理电液控制系统又称电液伺服系统,是以电气信号为输入,以液压信号为输出,电气检测传感器元件为反馈构成闭环控制系统.由于是电气和液压相结合,因而系统可发挥两者的优点.电气信号便于测量转换放大处理校正,电气检测传感器元件便于检测各种物理量,且快速和多样性;液压信号输出功率大速度快,执行元件具有惯性小等优点.所以结合起来的电液控制系统具有控制精度高,响应速度快,信号处理灵活,输出功率大,结构紧凑,重量轻等优点.输入电气信号通常有电位器,电子放大器,PLC控制器和计算机等. 电气检测传感器元件通常有位置传感器,压力传感器, 速度传感器,编码器等元件. 输出是以液压动力执行元件(油缸和马达)和伺服元件组成的反馈控制系统.如图所示:在此系统中,输出量(位移,力,速度等)通过反馈传感器(位移传感器,力传感器,速度传感器等)能自动地快速地准确地反映其变化.并与原先的给定的给定量进行比较,再放大输入给伺服阀,改变其阀芯位移,从而控制输出的压力和流量,驱动执行元件运动,直至输人量与输出量一致为止.举例:1.阀控式电液位置控制伺服系统(如上图)图中所示为双电位器电液位置控制伺服系统的工作原理图.该系统控制工作台的位置,使其按指令电位器给定的规律变化.系统由指令电位器, 反馈电位器,电子放大器,电液伺服阀,液压缸和工作台组成.其工作原理如下:指令电位器将位置指令xi转换成指令电压ur,被控制的工作台位置xp由反馈电位器检测转换成反馈电压ui.两个线性电位器接成桥式电路,从而得到偏差电压ue=ur-uf.当工作台位置xp与指令位置xi一致时,电桥输出偏差电压ue=0,此时伺服放大器输出电流为零, 电液伺服阀处于零位,没有流量输出,工作台不动.当指令电位器位置发生变化,如向右移动一个位移Oxi,在工作台位置发生变化之前, 电桥输出偏差电压ue=KOx,偏差电压经伺服放大器放大后变为电流信号去控制电液伺服阀, 电液伺服阀输出压力油到液压缸,推动工作台右移.随着工作台的移动, 电桥输出偏差电压逐渐减小,当工作台移动Oxp等于指令电位器位移Oxi时, 电桥输出偏差电压为零, 工作台停止移动.反之亦然.系统的工作原理方块图如下:2.泵控式电液速度控制伺服系统该系统的液压动力执行元件由变量泵和液压马达组成,变量泵既是液压能源又是液压控制元件.由于操纵变量机构所需要的力较大,通常采用一个小功率的液压放大装置作为变量控制机构.如图所示为一泵控式电液速度控制伺服系统的原理图.图中所示系统采用阀控式电液位置控制机构作为泵的变量控制机构. 液压马达的输出速度由测速发电机检测,转换为反馈电压信号uf,与输入指令电压信号ur相比较,得出偏差电压信号ue=ur-uf,作为变量控制机构的输入信号.当速度指令为ur0时, 负载以某个给定的转速w0工作,测速机输出反馈电压uf0,则偏差电压ue0=ur0-uf0,这个偏差电压对应于一定的液压缸位置,从而对应于一定的泵流量输出,此流量为保持负载转速w0所需的流量.如果负载变化或其它原因引起转速变化时,则uf 不等于uf0,假如w大于w0,即uf大于uf0,则ue=ur0-uf小于ue0,使液压缸输出位移减小,使泵输出流量减小,液压马达转速自动下调至给定值.反之,如果转速下降,则uf小于uf0,则ue=ur0-uf大于ue0,使液压缸输出位移增大,使泵输出流量增大,液压马达转速自动回升至给定值.结论: 速度指令一定时, 液压马达转速保持恒定;速度指令变化时, 液压马达转速也相应变化.系统的工作原理方块图如下:二.电液伺服控制系统组成1.输入元件---其功用是给出输入信号加于系统的输入端.可以是机械的,电气的等如靠模,电位器,计算机等.2.反馈测量元件---测量系统输出并转换为反馈信号.如各类传感器(位置传感器,压力传感器,速度传感器等).3.比较元件---将输入信号与反馈信号进行比较,给出偏差信号.4.放大转换元件---将偏差信号放大,转换成液压信号.妲伺服放大器,电液伺服阀等.5.执行元件---产生调节动作加于控制对象上,如液压缸和液压马达等.6.控制对象---被控制的设备等,即负载.7.液压能源装置及各种校正装置等.1.2电液伺服控制的分类电液伺服控制系统可按不同的原则分类,基本上有五大类.一.按被控对象的物理量名称分类1.位置伺服控制系统主要是控制被控对象的位置精度的伺服控制系统,妲机床工作台的位置,板带轧机的板厚,振动试验台等系统.2.速度伺服控制系统主要是控制被控对象的速度精度的伺服控制系统,如原动机的调速,雷达天线的速度控制等.3.力伺服控制系统以力为被调量的伺服控制系统,如材料试验机,轧机张力控制系统等.二.按执行元件的控制方式分类1.阀控式伺服控制系统利用伺服阀控制的伺服控制系统称为阀控式伺服控制系统.它又可分为阀控缸系统和阀控马达系统两种.其优点是响应速度快,控制精度高,结构简单.缺点是效率低.2.容积式伺服控制系统利用变量泵或变量马达控制的伺服控制系统称为容积式伺服控制系统.它又可分伺服变量泵系统和伺服变量马达系统.三.按系统输入信号的变化规律分类1. 定值控制系统当系统输入信号为定值时称为定值控制系统.它的任务是将系统的实际输出量保持在希望值上.2. 程序控制系统当系统输入信号为按预先给定的规律变化时称为程序控制系统..3. 伺服控制系统伺服控制系统又称随动系统,其输入信号是时间的未知函数,而输出量能够准确快速地复现输入量的变化规律.四.按信号的方式分类1.模拟信号控制系统系统中全部信号都是连续的模拟量的系统称之.2.数字信号控制系统系统中全部信号都是数字量的系统称之.3. 数字-模拟混合控制系统系统中部分信号是数字量部分信号是模拟量的系统称之.五.按信号传递介质的形式分类1.机液伺服控制系统输入信号给定,反馈测量和比较均用机械构件实现的系统称之.2.电液伺服控制系统用液压动力元件,偏差信号的检测校正和初始放大等均用电气电子元件实现的系统称之.1.3电液伺服控制的优缺点一. 电液伺服控制的优点1.液压元件功率-重量比和力矩-惯量比(力-质量比)大,因而结构紧凑,体积小,重量轻,用于中大型功率系统优点更明显.比较举例:电气元件:最小尺寸取决于有效磁通密度,而有效磁通密度又受磁性材料的磁饱和限制;功率损耗产生的发热量散发又比较困难.因此功率-重量比和力矩-惯量比小,结构尺寸大.液压元件:功率损耗产生的发热量由油带到散热器去散热,其最小尺寸取决于最大工作压力,而工作压力可以很高(通常可达32MPa),因而元件尺寸小,重量轻, 功率-重量比和力矩-惯量比大.同功率:液压泵重量/电动机重量=10%-20%液压泵尺寸/电动机尺寸=12%-13%液压马达功率重量比=10倍相当容量的电动机液压马达力矩-惯量比=10-20倍电动机2.液压动力元件快速性好,系统响应快.加速能力强,能高速起动和制动.3.液压伺服系统抗负载的刚度大.二. 电液伺服控制的缺点1.液压元件抗污染能力差,对工作介质清洁度要求高.工作介质随温度变化而变化,对系统性能有影响.2. 液压元件制造精度高,成本高,且若元件的密封制造使用不当,易外漏,造成环境污染.3.液压能源传输不如电气系统方便2 电液伺服阀电液伺服阀是电液伺服系统中的主要元件,它既是电液转换元件,又是功率放大元件.它能够把微小的电信号转换成大功率的液压能(流量和压力),是电液伺服控制系统的核心和关键.电液伺服阀的输入信号是由电气元件来完成的,由它再转换成液压流量和压力,输出给执行机构,实现对执行机构各物理量的控制.2.1电液伺服阀的组成与分类一.组成电液伺服阀通常由力矩马达,液压放大器,反馈机构三部分组成.以下图的两级中力反馈式电液伺服阀为例,简单介绍如下:图中上半部为力矩马达,下半部为液压放大器(由四通滑阀组成的液压放大器), 反馈机构则由反馈杆11组成.它们的作用分别是:1.力矩马达(力马达)将输入的电信号转换成力矩或力控制液压放大器运动.2.液压放大器控制液压能源流向执行机构的流量和压力.3.反馈机构使伺服阀输出的流量和压力获得与输入信号相应的特性.二.分类电液伺服阀的种类很多,按不同的结构和机能常有以下几种分类:1.按输出量的控制功能分有:电液流量伺服阀---主要控制输出的液流流量特性,即在额定输入信号范围内,具有线性流量控制特性.电液压力伺服阀---在额定输入信号范围内,具有线性压力控制特性.电液压力-流量伺服阀---在额定输入信号范围内,具有线性压力-流量控制特性.2.按液压放大器的级数分有:单级伺服阀---只有一级放大元件.结构简单,价格低廉,但输出力和力矩小,输出流量小,对负载变化敏感.用于低压小流量和负载变化不大的场合.两级伺服阀---有两级放大元件.它克服了单级伺服阀的缺点,是最常用的型式.三级伺服阀---由一个两级伺服阀作前置级,控制第三级功率滑阀.通常只用于大流量(200L/min)以上的场合.3.按第一级阀的结构分有:滑阀---第一级阀的结构是滑阀.此类阀流量和压力增益高,输出流量大,对油清洁度要求较低.但加工复杂,分辨率低,响应慢,滞环较大,阀芯受力大.喷咀挡板--- 第一级阀的结构是喷咀挡板. 此类阀灵敏,动态响应快,线性度好.但对油清洁度要求高,挡板受力小,驱动功率小.射流管--- 第一级阀的结构是射流管阀. 此类阀抗污染强,但动态响应慢,受油温响应大.4.按反馈形式分有:滑阀位置反馈---利用滑阀的位置反馈的阀,常用的有直接位置反馈,机械位置反馈,位置电反馈,位置力反馈等.直接位置反馈---阀芯位移通过反馈杆与挡板相连,构成滑阀位移力反馈.常用于两级伺服阀.机械位置反馈---将功率级滑阀的位移通过机械机构反馈到前置级.位置电反馈---将功率级滑阀的位移通过位移传感器反馈到伺服阀的放大器输入端,实现功率级滑阀阀芯定位.2.2 力矩马达力矩马达是将电信号转换成机械运动的一种电气-机械转换.一.力矩马达工作原理利用电磁原理,由永久磁铁(或激磁线圈)产生极化磁场,而电信号通过控制线圈产生控制磁场,两个磁场相互作用,产生与控制信号成比例并能反映控制信号的极性的力或力矩,使其运动部分产生直线位移或角位移的机械运动.二.力矩马达分类1. 根据运动形式分1) 角位移马达--力马达,可移动件是直角位移.2) 直线位移马达—力马达,可移动件是直线位移.2.按可动件结构分1)动铁式---可动件是衔铁.2)动圈式---可动件是控制线圈.3.按极化磁场产生的方式分1)永磁式---利用永久磁铁建立极化磁通.2)非极磁式---无专门的极磁线圈,两个控制线圈差动连接,利用常值电流产生极化磁通.3)固定电流极磁式---利用固定电流通过极磁线圈建立极化磁场.三.力矩马达要求1.能产生足够的输出力和行程,且要求体积小,重量轻.2.动态性能好,响应速度快.3.直线性好,死区小,灵敏度高,磁滞小.4.抗震,抗冲击,不受环境温度和压力影响.四.典型力矩马达1. 永磁动铁式力矩马达1)组成下图所示为一种常用的永磁动铁式力矩马达工作原理图,它由永久磁铁(2),上下导磁体(3,5),衔铁(4),弹簧管(1),控制线圈(两个控制线圈套在衔铁上).2)工作原理永久磁铁将上下导磁体磁化,一个为N极, 一个为S极.无信号电流时,即两个控制线圈的电流i1=i2,衔铁在上下导磁体的中间位置,由于力矩马达结构是对称的, 永久磁铁在四个工作气隙中所产生的极化磁通是一样的,使衔铁两端所受的电磁吸力相同,力矩马达无力矩输出.当有信号电流通过控制线圈时,线圈产生控制磁通(其大小和方向取决于信号电流的大小和方向).假设i1>i2,如上图所示,在气隙1,3中控制磁通与极化磁通方向相同,而在气隙2,4中控制磁通与极化磁通方向相反,因此气隙1,3中其控制磁通与永久磁铁磁通合成大于气隙2,4中控制磁通与极化磁通的合成,于是衔铁上产生顺时针方向的电磁力矩,使衔铁绕弹簧管转动中心顺时针方向转动.当弹簧管变形产生的反力矩与电磁力矩相平衡时,衔铁停止转动.如果信号电流反向,则电磁力矩也反向,衔铁向反方向转动.电磁力矩的大小与信号电流的大小成比例,衔铁的转角也与信号电流成比例.因此调节信号电流便可调节电磁力矩的大小,也就调节衔铁的转角大小.2.永磁动圈式马达1)组成永久磁铁,可动线圈,对中弹簧等.2)工作原理图所示为一种常见的结构原理图图中,永久磁铁在工作气隙中形成极化磁通,当控制信号电流加到线圈上时,线圈就会受到电磁力的作用克服弹簧力和负载力而运动.线圈的位移与控制电流成比例.因此输入信号电流就会得到电磁力,且呈正比关系,具有线性特性.3.动铁式力矩马达与动圈式力马达比较动铁式力矩马达动圈式力马达磁滞大磁滞小工作行程小工作行程大输出力矩大,弹簧刚度大,. 输出力矩小,固有频率低.固有频率高同功率体积小, 价格高同功率体积大,价格低五.力矩马达的数学模型(电磁力矩计算)1) 永磁动铁式力矩马达的数学模型(电磁力矩计算)电磁力矩是由于控制线圈输入电流,在衔铁产生了控制磁通而形成的.因此需先求出力矩马达的控制电流.通过力矩马达的磁路分析可求出电磁力矩的计算公式.a.力矩马达的控制电流参看永磁动铁式力矩马达的工作原理图,在其工作时, 两个控制线圈由一个放大器供电,其常值电压Eb在每个控制线圈中产生的常值电流I0大小相等方向相反.当放大器有输入电压时,两个控制线圈的电流分别为:I1= I0+iI2= I0-i式中i1 i2--- 每个控制线圈中的电流;I0---每个控制线圈中的常值电流i---每个控制线圈中的信号电流;两个控制线圈的差动电流为Δi=i1-i2=2I=i c(1)I c ---输入马达的控制电流b. 衔铁中产生的控制磁通根据力矩马达的磁路原理图,应用磁路的基尔霍夫第二定律可得气隙的合成磁通, 继而应用磁路的基尔霍夫第一定律求出衔铁磁通:φa=φ1-φ2=2φgθ(a/Lg)+Δi(Nc/ Rg)式中φa ---衔铁磁通;φg ---衔铁在中位时气隙的极化磁通;θ---衔铁转角; a ---衔铁转动中心到磁极面中心的距离;Lg ---衔铁在中位时每个气隙的长度;Rg ---工作气隙的磁阻;NcΔi---永久磁铁产生的控制磁动势;c. 作用在衔铁上的电磁力矩根据马克斯威尔公式计算衔铁在磁场中所受的电磁吸力,可得由控制磁通和极化磁通相互作用在衔铁上产生的电磁力矩简化式为Td=KtΔi+Kmθ式中Td ---作用在衔铁上的电磁力矩;Kt---力矩马达的中位电磁力矩系数;Km---力矩马达的中位磁弹簧刚度;从式中可看出,在衔铁中产生的控制磁通以及由此产生的电磁力矩比例于差动电流.2) 永磁动圈式力马达的数学模型(电磁力矩计算)参见永磁动圈式力马达的工作原理图,力矩马达的可动线圈悬置于工作气隙中,永久磁铁在工作气隙中形成极化磁通,当控制电流加到线圈上时,线圈就会受到电磁力的作用而运动.其运运动方向和电流方向按左手定则判断.线圈上的电磁力克服弹簧力和负载力,产生一个与控制电流成比例的位移.由于电流方向与磁通方向垂直,根据载流导体在均匀磁场中所受的电磁力公式,可得力马达线圈所受的电磁力:F=BgлDNcic=Ktic式中F---线圈所受的电磁力;K t---电磁力系数F=BgлDNcN c---控制线圈的匝数.B g---工作气隙中的磁感应强度;D---线圈的平均直径;I c---通过线圈的控制电流.结论: 永磁动圈式力马达的电磁力与控制电流成正比,具有线性特性.2.3 液压放大元件电液伺服阀另一个组成部分是液压放大器,它是一种以机械运动来控制流体动力的元件.它将力矩马达(或力马达)输出的机械运动(转角或位移)转换为液压信号(液体的流量和压力)输出,并进行了功率放大.液压放大元件是伺服系统中的一种主要控制元件,其静动态特性对系统的性能影响很大.且结构简单,单位体积输出功率大,工作可靠和动态性能好.一.液压放大元件的种类液压放大元件有滑阀,喷咀挡板阀和射流管阀等.二.滑阀滑阀是靠节流原理工作的.它借助于阀芯与阀套间的相对运动改变节流口面积的大小,对流体流量或压力进行控制.滑阀结构形式多,控制性能好,在电液系统中应用最广泛.1.滑阀的结构及分类(1)按进出阀的通道数划分它与液压方向阀的通道数一样,有四通阀,三通阀和二通阀.四通阀有一个进油口,一个回油口,两个控制口.可用来控制双作用液压缸或马达.如图a所示.三通阀有一个进油口,一个回油口,一个控制口.只可用来控制差动液压缸.如图b所示.图b 三通阀图c 二通阀二通阀一个进油口,只有一个可变节流口,须和一个固定节流孔配合使用,才能用来控制差动液压缸. 如图c所示.(2)按滑阀的工作边数划分a.四边滑阀--与上对应四通阀有四个可控的节流口,又称四边滑阀,控制性能最好.如上图a所示.b. 双边滑阀--三通阀有两个可控的节流口,又称双边滑阀, 控制性能居中. 如上图b所示.c. 单边滑阀--单边滑阀只有一个可控的节流口, 控制性能最差.(3)按滑阀的预开口型式划分按滑阀阀芯在中位时,阀芯凸肩与阀套槽宽的几何尺寸关系划分有:a.正开口--阀芯凸肩与阀套槽宽的几何尺寸是负重叠的(即阀芯凸肩宽度大于阀套槽宽),参见图a.b.零开口--阀芯凸肩与阀套槽宽的几何尺寸是零重叠的(即阀芯凸肩宽度等于阀套槽宽),参见图b.c.负开口--阀芯凸肩与阀套槽宽的几何尺寸是正重叠的(即阀芯凸肩宽度小于阀套槽宽),参见图c.图a 正开口图b 零开口图c 负开口.阀的预开口形式对其性能,特别是零位附近特性影响很大.如下图所示:零开口阀具有线性流量增益特性,性能比较好.负开口阀由于流量增益特性有死区,将引起稳态误差,有时还可能引起游隙,从而产生稳定性问题.正开口在正开口区内外的流量增益变化大,压力灵敏度低,零位泄漏量大.图不同开口形式的流量特性1-零开口2-正开口3-负开口2.滑阀静态特性滑阀静态特性是指稳态情况下,阀的负载流量qL, 负载压力pL和滑阀的位移xv三者之间的关系,即qL=f(pL, xv).它表示滑阀的工作能力和性能,对系统的静动态特性计算有重大意义.阀的静态特性可用方程(压力-流量方程),曲线或特性参数(阀的系数)表示.(1) 滑阀静态特性a.压力-流量方程滑阀的控制流量可由滑阀节流口流量公式表示,其流量是阀芯位移和节流口的压降的函数.为了使问题简化,在推导压力-流量方程时,作了以下假设:a)液压能源是理想的恒压源,供油压力Ps为常数,回油压力P0为零.b)忽略管道和阀腔内的压力损失.c)假定液体是不可压缩的.d)假定阀各节流口流量系数相等.e)阀的窗口都是匹配和对称的.根据节流口流量公式,以四边滑阀为例,可推导出压力-流量方程:负载流量为QL=CdA2√1/ρ(ps - pL)- CdA1√1/ρ(ps + pL)式中Cd-为流量系数,ρ-为油密度, (ρ=870Kg/m3)A1- 为节流口1的面积;A2-为节流口2的面积;ps –为恒压油源压力pL-为负载压力,pL=p1-p2.供油流量为Qs=CdA2√1/ρ(ps - pL)+ CdA1√1/ρ(ps + pL)b.滑阀的静态特性曲线a)流量特性曲线阀的流量特性是指负载压降等于常数时, 负载流量与阀芯位移之间的关系,其图形表示即为流量特性曲线. 负载压降为0时的流量特性称空载流量特性.相应的曲线为空载流量特性曲线,如图a所示.图a 空载流量特性曲线图图b 压力特性曲线b)压力特性曲线阀的压力特性是指负载压降等于常数时, 负载压降与阀芯位移之间的关系,其图形表示即为压力特性曲线.通常所指的压力特性是指负载流量为0时的压力特性,相应的曲线为压力特性曲线,如图b所示.c)压力-流量特性曲线阀的压力-流量特性曲线是指阀芯位移一定时, 负载流量与负载压降之间关系的图形. 如下图所示为理想零开口四边滑阀的压力-流量特性曲线族.它全面描述了阀的稳态特性,并可获得阀的全部性能参数.阀在最大位移下的压力-流量特性曲线可以表示阀的工作能力和规格.当负载所需的压力和流量能被阀在最大位移下的压力-流量特性曲线所包围时,阀就能满足负载的要求阀的压力-流量特性曲线(2)零开口四边滑阀的静态特性a. 理想零开口四边滑阀的静态特性理想零开口滑阀是指径向间隙为零,工作边锐利的滑阀,如图所示.由于径向间隙为零,工作边锐利,因而在讨论静态特性时可不考虑它们的影响.且认为节流阀口为矩形,其面积A=W xv, (W-面积梯度xv-阀芯位移).a)理想零开口四边滑阀的压力-流量方程 理想零开口四边滑阀的压力-流量方程:QL=Cd W xv -(1)b)压力-流量曲线根据无因次压力-流量方程绘制压力-流量曲线如下图所示.因阀窗口是匹配且对称的,所以压力-流量曲线对称于原点.当阀在正常工作状态是按图中Ⅰ,Ⅲ象限曲线.只有在瞬态情况下,才会处于Ⅱ,Ⅳ象限曲线.⎪⎪⎭⎫ ⎝⎛-Lv v s p p χχρ1。
电液位置伺服控制系统实验
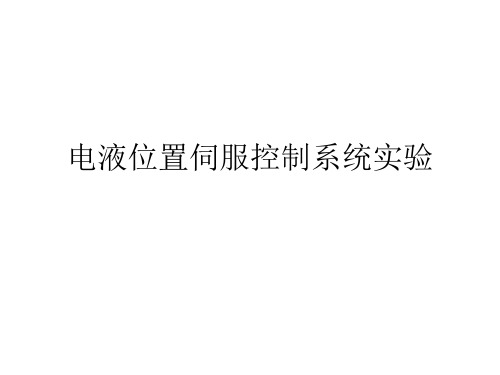
2
s2
2.834 2 0.866 1 2 s s s 1 2 14 .726 14 .726
正常参数时的ωc=2.78, ωh=14.8,Kg=19.1
增大Ki
正常参数
C (s) 4.611 R( s) 1 2 0.866 2 s 14 .726 2 s 14 .726 s 1
斜坡输入1
正弦输入
正弦输入,幅值5,频率1
正弦输入,幅值5,频率2.95
3 液压系统原理
压力传感器2
伺服缸
压力传感器3
平衡阀 电磁换向阀
蓄能器
电液伺服阀 压力传感器1
流量计2
流量计1 精滤器 电磁溢流阀
电机泵组
M
粗滤器 精滤器
4 系统控制原理
数据采集
参考输入
控制器
数模转换
功率放大
伺服阀
伺服缸
K i 73.746 KV 2.834 K d 1 26.022
K d1 h 代入系数得到 K d 1 26 .022 14 .726 h a a 0.12 (b K d 2 ) (b K d 2 ) (0.2 2.861) h h 0.866 2 K d1 a 2 K d 1 a 2 26.022 0.12
mmax 为能量输出单元在线 性范围内的最大值
r0,ml 为输入信号在线性范 围内的最大值
阶跃输入2.5
阶跃输入5
阶跃输入9
阶跃输入12
系统开环传递函数
KV C (s) R(s) 1 2 2 h s 2 s s 1 h h
Ki KV K d1
2)阀控缸微分方程
电液伺服控制系统

组成电液比例控制系统的基本元件: 1)指令元件 2 比较元件 3 电控器 4 比例阀 5 液压执行器 6 检测反馈元件
第6章 电液伺服控制系统
4
6.1 概述
6.1.2 电 液 比 例 控 制 系 统 的 特 点 及 组成
第6章 电液伺服控制系统
5
6.1 概述
电液比例控制的主要优点是: 1)操作方便,容易实现遥控 2 自动化程度高,容易实现编程控制 3 工作平稳,控制精度较高 4 结构简单,使用元件较少,对污染不敏感 5 系统的节能效果好。
6.功率放大级
功率放大级式比例控制放大器的 核心单元。由信号放大和功率驱动电路 组成。
根据功率放大级工作原理不同,分 为:模拟式和开关式。
第6章 电液伺服控制系统
29
6.3 电液比例电控技术
(1)模拟式功率放大级
第6章 ห้องสมุดไป่ตู้液伺服控制系统
30
6.3 电液比例电控技术
(2)开关式功率放大级
第6章 电液伺服控制系统
比例放大器根据受控对象、功率级工作原理不同,分为: 1 单路和双路比例控制放大器 2 单通道、双通道和多通道比例控制放大器 3 电反馈和不带电反馈比例控制放大器 4 模拟式和开关式比例控制放大器 5 单向和双向比例控制放大器 6 恒压式和恒流式比例控制放大器
第6章 电液伺服控制系统
16
6.3 电液比例电控技术
第6章 电液伺服控制系统
18
6.3 电液比例电控技术
第6章 电液伺服控制系统
19
6.3 电液比例电控技术
2.输入接口单元 (1)模拟量输入接口
2 数字量输入接口 3 遥控接口
第6章 电液伺服控制系统
20
机电一体化——电液控制系统设计

6.电液控制系统设计6.1概述电液控制系统是常用机电一体化系统之一。
它是将计算机电控和液压传动结合在一起,既发挥了计算机控制或电控制技术的灵活性,又体现了液压传动的优势,充分显示出大功率机电控制技术的优越性。
电液控制系统的种类很多,可以从不同的角度分类,而每一种分类方法都代表一定的特征:1)根据输入信号的形式和信号处理手段可人为数字控制系统、模拟控制系统、直流控制系统、电液开关控制系统。
2)根据输入信号的形式和信号处理手段可分为数字控制系统、模拟控制系统、直流控制系统、交流控制系统、振幅控制系统、相位控制系统。
3)根据被控量的物理量的名称可分为置控制系统、速度控制系统、力或压力控制系统等。
4)根据动力元件的控制方式可分为阀控系统和泵控系统。
5)根据所采用的反馈形式可分为开环控制系统、闭环系统和半闭环控制系统。
本章主要介绍电液控制系统的组成、控制元件,系统数字模型以及系统的设计。
6.2电液控制元件电液控制元件主要包括电液伺服阀、电液比例阀、电液数字阀以及由数字阀组成的电液步进缸、步进马达、步进泵等。
它胶是电液控制系统中的电-液能量转换元件,也是功率放大元件,它能够将小功率的电信号输入转换为大功率的液压能(流量与压力)或机械能的输出。
在电液控制系统中,将电气部分与液压部分连接起来,实现电液信号的转换与放大,主要有电液伺服阀、电液比例阀、电液数字阀以及各种电磁开关阀等。
电液控制阀是电液控制系统的核心,为了正确地设计和使用电液控制系统,就必须掌握不同类型电液控制阀的原理和性能。
6.2.1控制元件的驱动6.2.1.1电气—机械转换器电气—机械转换器有“力电机(马达)”、“力矩电机(马达)”以及直流伺服电动机和步进电动机等,它将输入的电信号(电流或电压)转换为力或力矩输出,去操纵阀动作,推行一个小位移。
因此,电气-机械转换器是电液控制阀中的驱动装置,其静态特性和动态特性在电液控制阀的设计和性能中都起着重要的作用。
电液控制-机液伺服系统

四、液压转矩放大器
Hale Waihona Puke 反馈机构为 螺杆、螺母 液压马达轴完全跟 踪阀芯输入转角而 转动。但输出力矩 比输入力矩要大得 多,故称液压转矩 放大器。
电液步进马达
以惯性负载为主时,可分析得
方框图为:
则系统方框图为:
§系统稳定性分析
液压伺服系统的动态分析和设计一般都是以稳定性要求为 中心进行的。
令G(s)为前向通道的传递函数,H(s)为反馈通道的传递函 数,由以上的方框图可得系统的开环传递函数为:
含有一个积分环节,故系统为Ⅰ型系统。
可绘制开环系统伯德图,如下图所示:
对伯德图的分析
幅值穿越频率ωc≈Kv 相位穿越频率ωc=ωg 为了使系统稳定, 必须有足够的相位裕 量和增益裕量。 由图可见,相位裕 度已为正值,为使幅 值裕度为正值,可计 算求得要求: K 2
与全闭环系统相比,半闭环系统的稳定性好得多,但精度较低。
综上所述,由于结构柔度的影响,产生了结构谐振和液压谐 振的耦合,使系统出现了频率低、阻尼比小的综合谐振,综合谐 振频率ωn和综合阻尼比ξn常常成为影响系统稳定性和限制系统频 宽的主要因素,因此提高具有重要意义。 提高ωn 就需要提高结构谐振频率ωs,就要求负载惯量减小 (但已由负载特性决定),结构刚度增大(提高安装固定刚度和 传动机构刚度,尤其是靠近负载处的传动机构的结构刚度)。 增大执行元件到负载的传动比,可提高液压固有频率;提高 液压弹簧刚度的方法也可提高液压固有频率,从而提高综合谐振 频率。
反馈从活塞输出端Xp取出时,构成为半闭环系统,其方框图 为:
此时系统开环传函中含有二阶微分环节,当ωs2和ωn靠得很 近时,会有零极点相消现象,使综合谐振峰值减小,从而改善 系统稳定性,如曲线b所示。 系统闭环传函为:
电液位置伺服控制系统实验

减小Ki
正常参数
Ki减小为40
Ki变小,ωc=1.53<2.78, ωh=14.8不变,Kg=24.5>19.1
增大Kd1
正常参数
Kd1变大为35
Kd1变大,ωc=2.1<2.78, ωh=17.1>14.8 ,Kg=21.8>19.1
减小Kd1
正常参数
Kd1减小为20
Kd1变小,ωc=3.45>2.78, ωh=12.9<14.8 ,Kg=16.8<19.1
2)阀控缸微分方程
负载流量线性化方程 流量连续性方程
忽略阀腔和管道总容积,油液的压缩性影响忽略
液压缸活塞的动力学平衡方程
3)缸输出位移对伺服阀输入电信号的传递函数 或写成:
2 伪微分反馈控制算法
对输出信号C 微分的积分仍是C,这就说明没有必要对C 进行微分
2
微分反馈控制方框图
伪微分反馈控制方框图
增大Kd2
正常参数
Kd2变大为3.3
Kd2变大,ωc=2.78不变, ωh=14.8不变,Kg=20.4>19.1
减小Kd2
正常参数
Kd2减小为0.6
Kd2变小,ωc=2.95基本不变, ωh=14.8不变,Kg=7.51<19.1
斜坡输入1
正弦输入
正弦输入,幅值5,频率1
正弦输入,幅值5,频率2.95
为能量输出单元在线 性范围内的最大值
为输入信号在线性范 围内的最大值
2
系统开环传递函数
代入系数得到
正常参数时的ωc=2.78, ωh=14.8,Kg=19.1
增大Ki
正常参数
Ki变大为120
Ki变大,ωc=4.39>2.78, ωh=14.8不变,Kg=15<19.1
电液伺服系统的建模与控制

电液伺服系统的建模与控制1. 引言电液伺服系统是一种广泛应用于工业控制领域的系统,它可以通过控制液压执行器的输出来实现对机械运动的精确控制。
本文将介绍电液伺服系统的建模与控制方法,以帮助读者更好地了解和应用这一技术。
2. 电液伺服系统的概述电液伺服系统由液压执行器、电液伺服阀、传感器和控制器等组成。
液压执行器负责将液压能转化为机械能,电液伺服阀负责控制液压执行器的动作,传感器用于反馈系统状态信息,控制器根据传感器的反馈信息对电液伺服阀进行控制。
3. 电液伺服系统的建模建模是控制系统设计的第一步,对于电液伺服系统也是不可或缺的。
电液伺服系统的建模既可以基于理论模型,也可以基于实验数据进行。
3.1 理论模型在理论模型建模中,我们需要考虑液压执行器、电液伺服阀和控制器的动态特性。
液压执行器的动态特性可以用惯性、摩擦、密封等参数来描述。
电液伺服阀的动态特性可以用阀门的流量-压力特性和阀门饱和现象来描述。
控制器的动态特性通常可以用传统的PID控制算法进行建模。
3.2 实验模型在实验模型建模中,我们需要通过实验得到系统的频率响应和传递函数,并将其转化为数学模型。
这种方法对于实际系统的建模更加准确,但也需要大量的实验数据和较高的技术要求。
4. 电液伺服系统的控制控制是电液伺服系统中最关键的环节之一。
常用的电液伺服系统控制方法有位置控制、速度控制和力控制等。
4.1 位置控制位置控制是电液伺服系统中最基本的控制方法之一。
通过控制电液伺服阀的输出来控制液压执行器的位置。
传感器将执行器的位置信息反馈给控制器,控制器根据反馈信息进行调节,使得系统实现期望的位置跟踪。
4.2 速度控制速度控制是电液伺服系统中常用的控制方法之一。
通过控制电液伺服阀的输出来控制液压执行器的速度。
传感器将执行器的速度信息反馈给控制器,控制器根据反馈信息进行调节,使得系统实现期望的速度跟踪。
4.3 力控制力控制是电液伺服系统中一种高级的控制方法。
- 1、下载文档前请自行甄别文档内容的完整性,平台不提供额外的编辑、内容补充、找答案等附加服务。
- 2、"仅部分预览"的文档,不可在线预览部分如存在完整性等问题,可反馈申请退款(可完整预览的文档不适用该条件!)。
- 3、如文档侵犯您的权益,请联系客服反馈,我们会尽快为您处理(人工客服工作时间:9:00-18:30)。
电液位置伺服控制系统设计方法
电液位置伺服系统是最基本和最常用的一种液压伺服系统,如机床工作台的位置、板带轧机的板厚、带材跑偏控制、飞机和船舶的舵机控制、雷达和火炮控制系统以及振动试验台等。
在其它物理量的控制系统中,如速度控制和力控制等系统中,也常有位置控制小回路作为大回路中的一个环节
电液位置伺服系统主要是用于解决位置跟随的控制问题,其根本任务就是通过执行机构实现被控量对给定量的及时和准确跟踪,并要具有足够的控制精度。
电液伺服系统的动态特性是衡量一套电液伺服系统设计及调试水平的重要指标。
它由电信号处理装置和若干液压元件组成,元件的动态性能相互影响,相互制约及系统本身所包含的非线性,致使其动态性能复杂。
因此,电液伺服控制系统的设计及仿真受到越来越多的重视。
液压伺服系统的基本设计步骤
○1分析整理所需的设计参数,明确设计要求;○2拟定控制方案,构成控制系统原理图;○3确定动力元件参数(如供油压力、执行元件规格、伺服阀容量)和其他组成元件;○4分析计算系统的静、动态特性,确定回路放大系数和设计校正措施等。
○5根据技术要求设计出系统以后,需要检查所设计的系统是否满足全部性能指标,如不满足,可通过调整参数或改变系统结构(即校正)等方法重复设计过程,直至满足要求为止。
因为设计是试探性的,所以设计方法具有很大的灵活性,在设计中结合MATLAB的SIMULINK软件进行仿真,对系统的参数进行调整和可靠性作进一步验证,最终可以得出比较可靠的电液伺服系统。
(一)组成控制系统原理图
由于系统的控制功率比较小、工作台行程比较大,所以采用阀控液压马达系统。
系统方块原理如图1
(二)由静态计算确定动力元件参数,选择位移传感器和伺服放大器
1.绘制负载轨迹图
负载力由切削力c F ,摩擦力f F 和惯性力a F 三部分组成。
摩擦力具有“下降”特性,为了简化,可认为与速度无关,是定值,取最大值f F = 1500N 惯性力按最大加速度考虑
a max F 800t m a N ==
假定系统是在最恶劣的负载条件下工作(即所有负载力都在存在,且速度最大)下工作,则总负载力为
max f F F F F =l c a =++400+1500+800=2700N
2.选取供油压力 5s P 6310Pa =⨯
3.求取液压马达排量
设齿轮减速比'm i=/2m θθ=,丝杠导程2
1.210/t m r -=⨯,则所需液压马达力矩为 2
2700 1.210 2.58222
L L F t T N m i ππ-⨯⨯===⋅⨯ 取L s 2P =P 3,则液压马达弧度排量为-63L 5s 3T 3 2.58D ==0.610m /2P 26310
m rad ⨯=⨯⨯⨯ 液压马达每转排量为-63-632D 20.610m / 3.710m /m m Q r r ππ==⨯⨯=⨯
计算出的液压马达排量需标准化。
按选取的标准化值再计算负载压力L P 值。
本例液压马达排量计算符合标准化。
4.确定伺服阀规格
液压马达的最大转速为2max max 2
2810800/min 13.3/1.210iv n r r s t --⨯⨯====⨯ 所以负载流量为-6-6max q 3.71013.3/49.2110l m Q n r s ==⨯⨯=⨯
此时伺服阀的压降为
55L s Lmax s -6T 2.58P P P 631020.010D 0.610
v m P Pa Pa =-=-=⨯-=⨯⨯ 考虑到泄漏等影响,将q l 增大15%,取q l = 3.4L/min 。
根据q l 和v P ,查得额定流量为
6L/min 的阀可以满足要求,该阀额定电流为33010n I A -=⨯
5.选择位移传感器增益 100V/m f K =, 放大器增益a K 确定
(三)计算系统的动态品质
1.确定各组成元件的传递函数,画出系统的方块图
因为负载特性没有弹性负载,因此液压马达和负载的传递函数为
021
2(1)m m h h h D s s s w w θξθ=++
工作台的质量折算到液压马达轴的转动惯量为 2-22-42t t 2222m t 800 1.210J ===7.2910kg m 4i 42
ππ⨯⨯⨯⋅⨯() 考虑到齿轮,丝杠和液压马达的惯量。
取t J =-33t J =1.210kg m ⨯⋅,并取液压马达的容积 -63t V =1010m ⨯,则液压的固有频率为
h w 假定阻尼比仅由阀的流量—压力系数产生。
零位流量—压力系数0k c 可计算取得。
取22.5110W m -=⨯,6r 510c m -=⨯ ,μ=21.810-⨯Pa ,得
伺服阀的传递函数有样本查得
sv 22k =s 20.5I +s+1600600
θ⨯ 额定流量n q =6L/min 的阀的供油压力5s P 6310Pa =⨯时,空载流量
430m q =60.9510/m s -=⨯ 所以阀的额定流量增益4
3630m q 0.9510/316210/0.03
sv n k m s A m s A I --⨯==⋅=⨯⋅。
则伺服阀的传递函数为 6
022q 316210s 20.5+s+1600600
I -⨯=⨯ 位移传感器和放大器的动态特性可以忽略,其传递函数可以用它们的增益表示。
传感器增益为 100/f
f p U k V m
X == 放大器增益为 a e
I k U = A/V 减速齿轮与丝杠的传递函数为
84/c w rad s = 2
41.210/9.5610/222P S m X t
K m rad m rad i θππ--⨯====⨯⨯ 根据以上确定的传递函数,可画出机床工作台液压伺服系统的方块图,如图5所示
图5数控机床工作台液压伺服系统方块图
2.绘制系统开环伯德图并根据稳定性确定开环增益
由方块图5绘制V K =1时的开环伯德图,见图6.。
然后将图中零分贝线下移至'O ,使相位欲量050γ=,此时增益欲量11g K DB =,穿越频率84/c w rad s =,开环增益3990V K DB == 1/S
由方块图5得开环增益
664421610 1.25109.5610100V a K K --=⨯⨯⨯
⨯⨯⨯⨯1/s=504a K 1/s
所以放大器增益为
3.求闭环系统的频宽
由图6所示的开环伯德图,通过尼克尔斯图可以求得系统的闭环伯德图,如下图7所示
由该图可得闭环系统的频宽为
5433.3510,8.910,26.3f r dB e m e m f HZ
---=±⨯=⨯=3316526.322dB dB f HZ HZ ωππ
--===
四.计算系统的稳态误差
对于干扰来说,系统是零型的。
启动和切削即不处于同一动作阶段,静摩擦干扰就不必考虑。
伺服放大器的温度零漂(0.5%~1%n I ),伺服阀零漂和滞环(1%~2%n I ),执行元件的不灵敏区(0.5%~1%n I )。
假定上述干扰之和为±2%n I ,由此引起的位置误差为 50.020.020.03 3.35100.179100
n f a f I e m m K K -±±⨯=
==±⨯⨯
对指令输入来说,系统是I 型的,最大速度2max 810/m s ν-=⨯时的速度误差为 2
4max
8108.91090r v e m m K ν--⨯===⨯ 由上面的计算可知,所设计的系统达到的性能指标为5433.3510,8.910,26.3f r dB e m e m f HZ ---=±⨯=⨯=可以满足设计任务的要求。