蓄热式熔铝炉节能技术
蓄热式燃烧技术在钢铁企业的应用
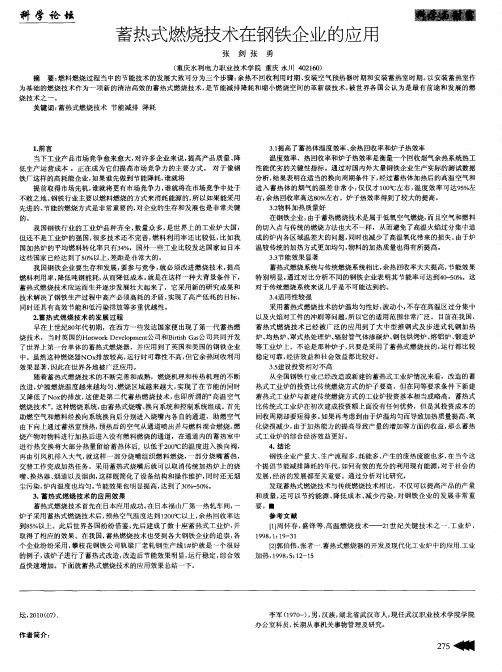
我 国钢铁行业的工业炉 品种齐全, 数量众 多, 是世 界上的工业炉大 国, 但还不是工业炉 的强 国, 很多技术还不完善 , 燃料利用 率还比较低 , 比如我
国加热炉 的平均燃料转化率只有3 4 %,国外 一些 工业 比较 发达 国家如 日本 这些国家已经达到了5 0 %以上 , 差距是非常大的。 我 国钢铁企业要生存和发展 , 要参与竞争 , 就 必须改进燃烧技术 , 提 高 燃料利用率, 降低吨钢能耗 , 从而降低成本 。 就是在这样一种大背景条件 下, 蓄热式燃烧技术应运而生并逐步发展壮大起来了,它采用 新的研 究成果和
稳定可靠, 经济效益和社会效益都 比较好。 3 . 5 建设投资相对 不高 从全国钢铁行业 已经改造或新建的蓄热式工业炉情况来看 ,改造的蓄
燃烧技术 ” 。 这种燃烧 系统 , 由蓄热式烧 嘴、 换 向系统和控 制系统组成 。 首先 助燃空气和燃料经换 向系统换 向后分别进入烧嘴 内各 自的通 道,助燃 空气 由下 向上通过蓄热室预热 , 预热后的空气从通道喷出并与燃料混合燃烧 。 燃
烧产物对物料进行加热后进入没有燃 料燃烧 的通道,在通道 内的蓄热室 中 进行热交换将大部分热量 留给蓄热体后,以低于2 0 0  ̄ E 的温度进 入换 向阀, 再 由引风机排入大气 , 就这样一部分烧嘴组织燃料燃烧 , 一部分烧嘴蓄热 , 交替工作完成加热任务 。采用蓄热式烧嘴后就可 以取消传统加热 炉上 的烧 嘴、 换热器、 烟 道以及烟 囱, 这样既简化 了设备结构和操作维护 , 同时还无烟 尘污染, 炉内温度也均匀 , 节能效果也 明显提高, 达到了3 0 %  ̄ 5 0 %。 3 . 蓄热式 燃烧技 术的应用效果 蓄热式燃烧技术 首先在 日本应用成功 。 在 日本福 山厂第一热轧车间, 一 炉 子采用蓄热式燃烧技术后, 预热 空气温度达到1 2 0 0  ̄ C以上 , 余热 回收率达 到8 5 %以上 。此 后世 界各国纷 纷借鉴 , 先后建成 了数十座蓄热式工业炉 , 并 取得 了相应的效果。在我 国, 蓄热燃烧技术也受到各大钢铁企业 的追崇 , 各 个企业纷纷采用, 攀枝花钢铁公司轨粱厂老轧钢生产线1 # 炉就是一个很好 的例子, 该炉子进行 了蓄热式改造, 改造后节能效果明显, 运行稳定 , 综合效 益快速增加。下面就蓄热式燃烧技术的应用效果总结一下。
热坯热送、高效蓄热式加热炉等节能项目在江阴华西钢铁公司高线厂的应用

B 钢坯横称装置
旧油平台及汽化冷却平台
净环水给水接点 净环水回水接点
进料中心线
压缩空软气化接水点接点 汽包平台
650轧机
出料中心线
输出蒸汽接点
出炉辊道
浊环水接点
仪表室
2CS
仪表室 C
图1
由图1我们可以看到: 改造前的工艺流程是:推钢加热炉→650轧机→350吨热剪→夹送辊、卡断剪→连轧机组 轧制,整个设计是按轧制线布置的。
策划
5.结论
通过这一系列的技术改造,虽然总投资在5000 万左右,但在投产后一年多就已经收回全部投资,该 工程成效显著,通过了国家发改委、财政部工业炉窑 项目的节能审核,获奖400多万元,节能减排效果巨 大。
策划
• 华西钢铁公司高线厂于2001年建成投产,在筹建之 初由于没有炼钢,钢坯主要是靠外购,为了满足不 同尺寸钢坯的轧制问题,在连轧前布置了一架650 轧机用于开坯,钢坯的加热采用推钢式加热炉(燃 重油),在开厂之初效益还可以,随着2005年炼钢 项目的投产及市场竞争的加剧,对加热炉区域的进 行技术改造既有现实条件的可能,同时也是势在必 行,在2008年高线厂投入了5000万元的技改资金, 对加热炉区域进行了系统的全面改造,效果十分明
摘要
• 为了达到降本节支、节能降耗,华西高线厂对加热炉 区的设备进行了大范围的系统节能改造,主要项目为 连铸坯热坯热送、高炉煤气蓄热式加热炉加热、保温 移钢辊道、淘汰650轧机等一系列的配套改造,节能降 耗效果十分明显,效果显著。
关键词
热坯热送 蓄热式加热炉 出炉保温辊道 高压水除鳞 移钢机
1
策划
1.前 言
改造后的工艺流程是:150×150×12米的连铸坯→提钢机→检验站前热送辊道→检验站 检验→检验后热送辊道→保温缓冲区→炉前辊道→蓄热式加热炉加热→出炉钢坯高压水除 鳞→出炉保温辊道→移钢机移钢→进入轧制线辊道→夹送辊、卡断剪→连轧机组轧制。
论熔铝炉的燃料选择与燃烧器应用

指标也不 同. 因此 。 对企业而言选择 适合的燃料与燃烧器 实现 以最 小的能 源消耗获取最大的熔铝速率 , 而达到 熔铝炉设备能源利用率最优 化的 目 从
关键词 : 熔铝炉; 能源 ; 燃料 消耗量 : 熔化率; 吨铝能耗 ; 熔化成本
热器总是难 以解决个难题, 使用效果也很不理想 。 因此, 的熔铝炉吨铝能耗是 比铰高的, 传统 通常吨 铝能耗都在 30 M~ 30H左右。 00 J40^ 炉子热效率大 都在 3 左右。 ∞ 近年来 。 蓄热式燃烧器的应用改变 了这个 岛 , 面 通过采用这种燃烧器, 熔铝炉烟气的 排放 温度 可 降 至 2 0 0 ̄ C以下其 吨铝 能耗 仅 为 2 0 MJ 10 或更低。 相差 1 3 。 -倍 然而 , 天然气前期投入大 , 且受地域 限制; 而 蓄热式烧嘴的蓄热体采用的是氧化铝小球 , 煤因其燃烧后排放的烟气中含有大量的 粉尘和含 通过定期的更换氧化铝球有效地解决了烟气成分 硫气体, 需要进行烟气除尘及净化处理 , 也受到一 过脏的问题 。 的。 定的限制。 在具体应用中应注意以下几方面: a 与常规燃烧器相比, I熔铝炉热工过程分析 3燃烧器的应用 采用蓄热式燃烧器的熔 熔铝炉是典型的周期是高温熔炼设备 , 一般 在熔铝炉设计中, 燃烧器的选型及 合理布置 铝炉炉膛尺寸应尽可能 的大一些 , 只有这样 , 才能 来说从铝锭人炉到熔炼结束 ,大致可分为以下几 是重要环节之一 , 由于铝金属黑度较小 , 接受辐射 提供 足够的 燃烧 空间。 实现较大的小时熔化率; 式燃烧器换向瞬间 , 火焰对炉膛的冲击 个阶段 : 装料期 、 熔化初期 、 熔化中期 、 熔化后期 、 传热力较弱,因此在熔铝炉设计中应尽可能强化 升温期、 精炼期及保温期。 对流传热, 提高火焰对铝金属的对流效果。 主要通 比较大 , 应设有开放式的 辅助烟道, 来保证熔铝炉 装料通常是在热炉条件下进行的, 这时, 烧 过以下 r I 介方面来实现: 在合理的工况下运行; 嘴通常设在关闭或小火状态 , 随着冷炉料的加入 , 3 优先选择高出口速度并具有—定的火焰 . 1 。 蓄热式燃烧器换向频繁, 对各元器件的可靠 炉温下降很快 , 装料时间越长, 炉温下降越多。 长度 燃烧器以提高对流换热能力 ; 拘 性要求较高; 刚装人炉的铝锭在炉内成堆状态, 随着温度 3 2加大燃烧器的安装倾角, 强制使火焰与铝 d 蓄热式燃烧器应配有火焰大小连续调节及 上升 , 料堆表面的炉料开始熔化 , 熔融的铝业 向下 金属之间形成冲击作用 ; 控制功能 , 与常规燃烧器相比, 由于蓄热式燃烧器 流动, 当温度达到 6 0 左右时 , 0 ̄ C 支撑料堆的强度 3 合理安排排烟孔位置, 3 尽可能使火焰沿铝 火焰更大 , 燃烧温度更高 , , 否则 精炼保温时会出 液表面流动并延长高温烟气在炉内的时间; 消失 , 炉内呈水平镜面。 现更高烧损率。 在料堆没人液面以前 , 火焰直接冲击在料堆 3 . 4尽可能采用余热回收技术, : 提高 J ( 焰理论 结束语 上, 由于强冲击作用 , 炉内对流传 效果 占 主导作 温度 ; 熔铝炉的燃料选择与燃烧器的选择涉及的内 用, 热效率最高 , 炉料熔化最快, 炉温上升缓慢。随 虽然, 在火焰的冲击下, 局部会出现金属过烧 容是多方面的, 因此, 在实际生产中, 我们要因地 着料堆逐渐没 八 液面 , 液面下的熔体呈固液混合 现象 , 但由于强化传热后 , 可以大大缩短总的熔化 制宜, 根据各地的实际情况来选择。 状态, 对流转热作用逐渐下降 , 炉膛温度 E 升速度 时间, 炉内总的金属烧损两不但不会增加 , 反而会 参 考文献 逐涛『 快不达到设定温度, 力 日 辐射作用逐渐 匕 升。 略有减 少 。 【 王秉铨. 1 1 工业炉设计手册 . 田北京: 机械工业 出版 2 0. 在炉 内 液面化平以后 , 一方面由于传热效果 多年以来,高速烧嘴及换热器一直是先进熔 社 . 0 4 的降低, 另一方面又由固液转化 的需要 , 熔化过程 铝炉燃烧技术的标准配置, 但实际生产总 , 由于熔 【 素逸 能源与节能技术嗍 . 2 潆 北京: 中国电力出版 变得更加缓慢, 需要时间更长, 消耗热量更多。同 铝炉灰附着及恶劣的烟气侵蚀的缘故 , 熔铝炉换 社 O 时, 排出的烟气温度也最高。 当炉内固体铝全部转化呈液态铝以后 , 熔体 对热负荷的需要大幅减少, 铝液温度快速 匕 此 升, 时极易出现熔体过热现象。 ( 上接 3 9页 J 系统 使用 过程 所产 生 的相 学 ,o 8 20. 精炼及保 关误差也不可忽视 ,因此如何尽可能地减少误 【] .P / 6昊俊 G SI NS辅 助航 空摄 影 测 量 原 理及 应 用 热负荷的供应主要是补充炉体散热损失。 差, 更好地服务于航 空摄影测量 , 是未来 工作 中 研究[ I 京: D. 北 解放 军信息工程大学,0 6 20. 从熔化的过程分析可 以看出, 在铝的熔化过 的重点 。 【】Hi rIg nad P n N nert n 7 l ne sn .G S a d IS Itga o ma i wih t Ka ma itrn o r c o ee e cn l n F le i g f r Die t Ge r fr n i g 程中,各阶段热负荷的需求 睛况及热传导方式均 参 考 文献 有很 大差异 。 【 李德仁 .P I ] G S用 于摄 影测量 与遥 感[ ] M. 北京: 0 Aron m gr 【 】 ed t ei a e f i re I aey R.G oei sln rr- b c T l 2熔铝炉的能源 测 绘 出版 社 , 9 6 19 . p r, 0 . o t 03 2 目 ,国内熔铝炉所用能源多数是以煤 、 前 柴 【 袁修孝 .P 辅助 空中三 角测量原理及应 用 【] c alCa r i tl a n n teue 2 】 GS 8Mihe r ,Ds Sa m n ,O h s me k l 油、 重油、 天然气和煤气为主。 而煤是储 存量最多, 『 . 京: 绘 出版 社 , 0 1 M1 北 测 20 . o GP /n ril etro o e tt n aa tr f SI eta xe r r nai p rmees i i o 分布最广 的燃料, 常用的煤指标有水分 、 灰分、 挥 【 袁修 孝.P 辅助 空中三 角测量及其质量控 i i o htga mer [ ] E P r- 3 ] GS n a b me p oorm t R.O E E Wok r y 发分和发热量。不同产地, 不同类别的煤, 质量等 制[】 D. : 武汉 武汉 大学 ,9 9 19 . so h p, I t g ae S n o Ore t t n Ha n v r ne td e s r i nai , n o e r o 级相差很大。液体燃料有很多优点 ,主要含热量 [ 李 学友. / G S 4 】 I D P 辅助航 空摄影测量原理、 2 o1 MU o . 高、 废物含量小、 灰分低、 燃烧热效率高, 同时便于 方法及 实践 [1 D.北京:解放 军信 息工程 大学, 作者 简介 : 国体 (9 6 , 河 南理 工 袁 18 ~) 男, 0 运输。 柴油价格贵限制了它的 使用 , 重油因价格低 2 05. 大学测绘与 国土信 息工程 学院硕 士研究 生, 主 廉而使用的较多。 气体燃料燃烧完全且易于控制 , 『】 5张丽娜. 密单点定位技 术在 I G S辅 助 要 研 究 方 向 为 城 市 地 理 信 息 系统 。 精 M P 容易实现烧嘴的空气 , 燃料 自动比例调节 , 还可以 航 空摄 影 中 的 应 用 研 究 {] 汉 : 国 地 质 大 D. 武 中
熔炼炉和静置炉的基本要求

熔炼炉和静置炉的基本要求[1992]894号“铝加工厂建设标准”和YSJ 011--9l“铝加工厂工艺设计规范”铝合金熔炼炉的主要任务就是高效率的熔化铝锭、废料和其他炉料,配制铝合金。
铝合金熔炼炉的发展史,实际上就是针对存在的问题不断改进提高炉子效率的历史。
对现代铝合金熔炼炉的基本要求是:1)热工性能好。
即熔化速度快,热效率高,单位产量燃料消耗少。
2)操作性能好。
即炉温均匀,炉温、炉压、炉内气氛可以方便调节控制,装料、搅拌便于实现机械化作业,对燃料变化的适应性强。
3)性能价格比高。
即设备占地面积小,单位产量设备投资低、使用寿命长,维修成本低,金属损耗少,使用燃料便宜易得。
4)环保安全。
即设备噪音低,炉子密封性好,排烟好,操作环境好;设备在点火、燃烧、熄火过程中要有可靠的安全保障。
按照建标[1992]894号“铝加工厂建设标准”和YSJ 011--9l“铝加工厂工艺设计规范”的要求,铝及铝合金的熔化,宜采用火焰炉,热效率应大于40%。
容量l5 t及以上的火焰熔化炉宜采用圆形或其他先进炉型,配以换热器,燃烧系统宜采用自动控制。
容量l5 t以下的火焰熔化炉可采用比例控制烧嘴。
静置炉用于接受在熔炼炉中熔炼好的熔体,并在其中进行精炼、静置和调整熔体温度,在铸造过程中对熔体起保温作用。
因此,熔体的最终质量在许多情况下与静置炉的类型和结构有关。
对静置炉的基本要求是:1)炉内水蒸气含量少。
2)熔池内熔体的温差小、保温良好并能准确控制炉温。
3)具有一定的升温能力。
4)容量与熔炼炉相适应。
5)结构简单、操作方便。
按照建标[1992]894号“铝加工厂建设标准”和YSJ 011--91“铝加工厂工艺设计规范的要求,静置炉(保温炉)宜采用电阻炉。
当电源不足或炉子容量较大时,也可采用火焰炉,并应设置炉温自动控制装置。
二、变形铝合金熔炼炉分类和优缺点比较1.熔炼炉的分类常用变形铝合金熔炼炉分类方法很多,按使用热源的种类分,有电炉和燃料炉(燃煤炉、燃油炉、燃气炉)两大类。
江西省发展改革委关于江西悦达铝业有限公司年产10万吨再生铝合金项目节能审查的批复

江西省发展改革委关于江西悦达铝业有限公司年产10万吨再生铝合金项目节能审查的批复文章属性•【制定机关】江西省发展和改革委员会•【公布日期】2022.04.02•【字号】•【施行日期】2022.04.02•【效力等级】地方规范性文件•【时效性】现行有效•【主题分类】节能管理正文江西省发展改革委关于江西悦达铝业有限公司年产10万吨再生铝合金项目节能审查的批复宜春市发展改革委:报来《关于呈报江西悦达铝业有限公司年产10万吨再生铝合金项目节能报告的请示》(宜市发改环资〔2022〕9号)收悉。
经审查,现就有关事项批复如下:一、原则同意所报项目节能报告。
二、项目建设地点:宜春市丰城市循环经济园区。
三、项目建设规模:项目建成达产后,可形成年产扁铸锭8万吨、铝板2万吨的生产规模。
四、该项目年综合能源消费量为7626.36/9266.34吨标准煤(当量值/等价值)。
项目产品中的1XXX、3XXX扁铸锭(I类铝)综合能源单耗分别约为68.81千克标准煤/吨和68.9千克标准煤/吨,优于《变形铝及铝合金单位产品能源消耗限额第1部分:铸造锭》(YS/T694.1-2017)中“铸锭生产企业单位产品能源消耗先进值(厚度>400毫米、宽度>1500毫米,不含均匀化处理的I类铝或铝合金)70千克标准煤/吨”的要求;3XXX铝板(A类)综合能源单耗约为98.01千克标准煤/吨,优于《变形铝及铝合金单位产品能源消耗限额第2部分:板、带材》(YS/T694.2-2017)中“板、带材生产企业单位产品能源消耗先进值中热轧板(厚度>6毫米的A类铝及铝合金)100千克标准煤/吨”的要求。
五、宜春市应严格落实能耗双控要求,确保完成“十四五”能耗强度目标任务。
六、建设单位在落实节能报告各项措施基础上,应改进和加强以下节能工作:(一)选用高效节能设备。
应选用达到国家1级能效水平或同行业设备先进水平的蓄热式熔铝炉、热轧机、退火炉、淬火炉等设备,要将能效指标作为重要的技术指标列入设备招标文件和采购合同。
硅热法炼镁的节能新技术--蓄热式镁还原炉
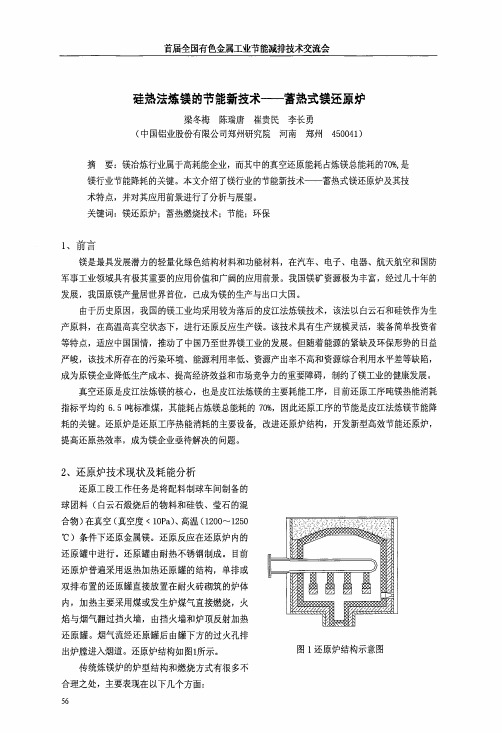
59
硅热法炼镁的节能新技术--蓄热式镁还原炉
作者: 作者单位: 梁冬梅, 陈瑞唐, 崔贵民, 李长勇 中国铝业股份有限公司郑州研究院 河南郑州 450041
本文链接:/Conference_6557648.aspx
58首届全国有色金属工业节能减排技术交流会4结束语将高温空气燃烧技术应用于能耗颇高的金属镁还原炉上可实现高温烟气余热的极限回收大幅提高还原炉的热效率在炉内创造出优良的均匀温度分布避免局部著可以获得很好的经济效益和环保效益该技术无疑会成为镁还原炉节能发展的新方向
3、新型节能蓄热式镁还原炉及其技术特点
新型蓄热式镁还原炉,是镁行业的新技术。蓄热式燃烧技术即高温空气燃烧技术,是20世纪 90年代以来国际燃烧领域开发并得到大力推广应用的一项全新燃烧技术。它突破了几百年来人们对 燃烧的传统认识,通过蓄热体极限回收烟气余热并将助燃空气预热到1000℃以上,与传统燃烧过 程不同,高温空气燃烧是一种动态反应,产生弥漫式火焰,不存在传统燃烧过程中出现的局部高温 高氧区,这样,即使是热值很低的燃料也能实现稳定着火和高效燃烧,具有高效节能、降低c0。和 Nox的排放等多种优点。该技术自问世起,在加热炉界得以迅速推广应用,取得了举世瞩目的节能环 保效益,是~项划时代的节能和环保技术b1。将高温蓄热燃烧技术应用于镁还原炉,无疑会为还原 炉的节能降耗带来新的曙光,对镁行业的健康发展产生深远影响。 新型节能蓄热式炼镁还原炉如图2所示,由炉体、炉膛、还原罐、蓄热室、管路、换向系统、 风机构成,采用空、煤气双预热方式,分别设置空气蓄热室和煤气蓄热室以及相应的空气换向阀和 煤气换向阀,经空气换向阀和经煤气换向阀排出的烟气由各自的引风机抽出。蓄热室填充热交换体
参考文献: [1]徐日瑶.硅热法炼镁生产工艺学[M].长沙:中南大学出版社,2003 [2]夏德宏, (3): 郭梁, 张刚等.硅热炼镁还原炉的用能分析与节能措施探讨[J].冶金能源.2005,
适用于重熔铝锭及废料的高效节能熔铝炉

适用于重熔铝锭及废料的高效节能熔铝炉杜新宇【摘要】为提高火焰熔铝炉的热效率,分析了目前常用熔铝炉型的工作原理及结构,找出各自的优缺点,指出火焰熔铝炉充分利用高温炉气是提高热效率的主要方法.针对现有火焰炉加热时局部温度过高、传热受限的弊端,设计了可上下调节、左右摆动的高速烧嘴.运用对流传热的牛顿定律,设计了适用于重熔铝锭及废料的加热与预热同时进行的双层膛火焰炉,增加了高温气流与炉料的接触面积,强化了对流传热的作用.新型熔铝炉充分利用了余热预热炉料和助燃空气,使熔铝炉的热效率提高到55%以上.【期刊名称】《轻合金加工技术》【年(卷),期】2015(043)005【总页数】5页(P25-29)【关键词】高温炉气;热效率;对流传热;高速烧嘴;预热膛【作者】杜新宇【作者单位】南阳理工学院,河南南阳473003【正文语种】中文【中图分类】TG232在能源危机的当今世界,节能降耗已成为世界瞩目的大问题。
虽然利用电能熔化铝合金其熔铝质量较好且环保,但电是二次能源,总的能源利用率不高,所以,目前世界各国仍以火焰炉作为熔化铝合金的首选。
传统的以辐射传热为主的熔铝炉热效率很低,能源浪费严重,为使铝合金熔炼做到高效低耗,节能环保,研究开发新炉型、新工艺仍是企业关注的焦点。
铝与其他金属相比,热力学属性有独特之处,总结来说“一低两高”,一低即黑度低,两高是熔化潜热高和比热容高。
铝的熔点680°,虽然较低,但由于有以上一低两高的特点,铝在熔炼过程中却能耗高,热效率低。
铝的黑度低,对辐射能的吸收能力仅相当于钢的1/4~1/7[1],传统的以辐射传热为主的熔铝炉其热效率只有15%~20%,大量热能流失,造成很大的能源浪费。
20世纪70年代,国外铝合金工作者提出了对流冲击传热快速熔铝的理论并付诸实施,发明了竖式熔铝炉,热效率提高至40%以上,是以辐射传热为主的熔铝炉热效率的两倍。
这种以对流传热为主的熔铝炉在世界各国推广,20世纪后期在我国也逐步得到应用。
电熔窑炉节能技术优化及应用

电熔窑炉节能技术优化及应用电熔窑炉是目前广泛应用于工业生产领域中的一种高温设备,其主要用于各种金属和非金属材料的熔化和热处理,同时也可以用于生产玻璃、陶瓷等产品。
但是,由于其运行中需要大量耗能,所以其能源消耗成为限制其应用范围的主要因素之一。
为了解决这一问题,研究人员对电熔窑炉的节能技术进行了深入探索和优化。
在实践应用中,主要采用以下几种方法:1、提高电熔窑炉的热效率电熔窑炉运行中会产生大量的热能,其中绝大部分都会散失。
因此,通过提高电熔窑炉内部的热效率来降低能源消耗就成为了一个非常有效的方法。
首先,可以采用有效的隔热材料对窑炉进行保温。
这样可以减少窑炉散热的程度,提高内部温度,并在一定程度上降低加热所需的电能,从而达到节能的目的。
其次,可以尝试采用先进的加热方式,通过提高电熔窑炉内部的温度来提高其热效率。
其中,利用感应加热技术,通过变压器和感应线圈将电能转化为热能,直接作用于金属物料内部来加热其熔化,可以大大提高电熔窑炉的热效率。
2、改进电熔窑炉的结构设计电熔窑炉的结构设计对其能源消耗也有着重要的影响。
因此,改进电熔窑炉的结构设计也可以成为一种有效的节能方法。
电熔窑炉的结构设计首先应该考虑到能够降低能量损失。
在设计时,可以采用多层绝缘体结构,使得其内部的热量不易流失,从而大大提高其热效率。
同时,合理设计窑炉进、出口的位置和尺寸,以保证制品出入和气流循环畅通,进一步提升电熔窑炉的能效。
3、合理使用电熔窑炉合理使用电熔窑炉也是节能的一个重要的方面。
操作人员需要从以下几个方面出发来减少电熔窑炉的能源消耗:(1)合理调节加热功率电熔窑炉的加热功率应该根据其工作状态和熔炼物料的特点进行调整。
过大的加热功率会造成能量浪费,同时也会增加生产成本,因此必须在使用时合理调节。
(2)减少窑炉空转时间在电熔窑炉开始工作前,需要花费一定的时间将其预热。
如果在这个过程中发生空转,将会造成大量的能量浪费。
因此,操作人员应尽量缩短空转时间,减少能源的消耗。
- 1、下载文档前请自行甄别文档内容的完整性,平台不提供额外的编辑、内容补充、找答案等附加服务。
- 2、"仅部分预览"的文档,不可在线预览部分如存在完整性等问题,可反馈申请退款(可完整预览的文档不适用该条件!)。
- 3、如文档侵犯您的权益,请联系客服反馈,我们会尽快为您处理(人工客服工作时间:9:00-18:30)。
蓄热式熔铝炉节能技术
Document number:WTWYT-WYWY-BTGTT-YTTYU-2018GT
蓄热式熔炉节能技术
一、熔炉的能耗与节能
国内加工行业熔炉使用传统的加热技术其能耗一般在75万大卡/吨左右;
在国外,吨能耗一般低于55万大卡。因此,国内的熔炉节能潜力还有很大的
空间。
判断熔炉能耗高低以及是否节能,从两个方面来看,第一,熔化率,第
二,炉子热效率。
熔化率是指单位时间单位熔池体积的熔化量(生产率),炉子升温速度越
快,炉子熔池越大则炉子的熔化率越高,在一般情况下,炉子生产率越高,则
熔化率的单位热量消耗就越低。炉子热效率是被加热熔化时吸收的热量与供入
炉内的热量之比。
为了降低能源消耗,应尽量提高炉子生产率,另一方面应充分回收利用出
炉废气的余热。同时对燃烧装置实行燃料与助燃空气的自动比例调节,以防止
空气量过剩或不足。减少炉体的蓄热和散热损失以及减少炉门开口等辐射热损
失。
早期的(现在也有一部分)熔炉一般离炉烟气直接排放,烟气温度在750℃以
上(图1)。
图
1
废
热
不
利
用
的
炉
子
为减少烟气带走的热量损失,人们在排烟管道上安装了热量回收装置即空气换
热器,将助燃空气预热到一定的温度(200℃左右)后参与燃料的燃烧,但换
热器后的排放温度还在500℃以上(图2)。
图2 安装空气预热器的炉子
采用蓄热式燃烧技术可以将烟气排放温度降低到150℃以下,助燃空气温度预
热到700℃以上,这样就大大地减少了离炉烟气所带走的热量,使炉子热效率
大幅度提高,燃料消耗大量减少,达到节能的目的(图3)。
图3 HTAC技术的工作原理图
根据工业炉热工原理,助燃空气温度每升高100℃,能节省燃料约5%;或者烟
气温度每降低100℃,能节省燃料约%。因此,采用蓄热式燃烧技术相对换热器
回收装置可以节能25%以上。
二.熔炼炉概述:
传统上有火焰炉、电阻炉、中频感应炉、反射炉以及坩埚炉等。为了获得
质量高又经济的铝合金溶液,各企业对熔炼设备的选择越来越重视,近几年
来,火焰炉、电阻炉、中频感应炉、反射炉都有所改进。熔炼炉结构的发展方
向是:操作自动化、应用更新化、原料节能化等。新型加热材料、新型耐火材
料和新溶剂得到新的应用。
1、 采用蓄热式烟气余热回收装置,交替切换空气和烟气,使之流经蓄热
体,能够最大程度上回收高温烟气热量,将助燃空气预热800度-1000度以
上,其余热回收率可达85%以上。
2、 合理组织燃烧工况,使炉内形成与传统火焰迥然不同的新型火焰型,创
造出炉内均匀的温度场分布。
3、 通过空气与燃料气流的合理组织,交替使用,是燃料在低氧环境中进行
燃烧,消除炉内局部高温区。
三、蓄热式燃烧系统工作原理
蓄热式烧嘴成对布置,相对的两个烧嘴为一组(A、B烧嘴)。从鼓风机出来
的常温空气由换向阀切换进蓄热式烧嘴A后,在流过蓄热式烧嘴A陶瓷小球蓄
热体时被加热,常温空气被加热到接近炉膛温度(一般为炉膛温度的80%~9
0%)。被加热后的高温空气进入炉膛后,卷吸周围炉内的烟气形成一股含氧
量大大低于21%的稀薄贫氧高温气流,贫氧高温空气与注入的燃料混合,实现
燃料在贫氧状态下燃烧;与此同时,炉膛内的热烟气经过蓄热式烧嘴B排出,
高温热烟气通过蓄热式烧嘴B时将显热储存在蓄热式烧嘴B内的蓄热体内,然
后以低于150℃的低温烟气经过换向阀排出。当蓄热体储存的热量达到饱和时
进行换向,蓄热式烧嘴A和B变换燃烧和蓄热工作状态,如此周而复始,从而
达到节能和降低NOX排放量等目的。
蓄热式燃烧技术改变了传统的燃烧方式,主要表现为燃料与空气以适当速
度从不同的喷嘴通道进入炉内,并卷吸炉内的燃烧产物,空气中的O2含量被稀
释,燃料在炉膛中高温(1 000℃以上)低氧浓度场(5%~%)工况下燃烧,此
种燃烧方式带来了许多优点:
(1)节能效果显着,比传统熔化炉平均节能25%以上
由于蓄热体“极限回收”了烟气中大部分的余热,并由参与燃烧的介质带
回炉内,大大降低了炉子的热支出,所以采用蓄热式燃烧技术的炉子比传统熔
化炉节能。
(2)消除了局部高温区,炉温分布均匀
燃料在高温低氧浓度工况下燃烧,在炉内形成没有明显火焰的弥漫燃烧,消
除了火焰产生的局部高温区,火焰边界几乎扩大到整个炉膛,使炉温更加均
匀。蓄热式烧嘴工作状态频繁交换,使燃烧热点的位置及炉气流动方向频繁改
变,强化了炉气对流,减小炉内死角,也使炉温更加均匀。
(3)提高加热质量
均匀的炉温使锭加热更均匀,降低了局部高温以及富氧环境对液的挥发和氧化
作用。
(4)延长炉子耐火材料使用寿命
炉温均匀和消除局部高温区使耐火材料受热均匀,并保证耐火材料始终工作在
合理的使用温度范围内。
(5)减少温室效应气体CO2排放量及NOX生量
燃料节省25%,相应的CO2排放量也减少25%。由于局部高温区的消除,有效的
降低了NOX的生成量。
四、蓄热体材料
蓄热体是蓄热式燃烧技术关键部分,它要求蓄热体具有蓄热量大、换热速
度好、高温强度好、阻力损失小、抗氧化抗渣性强,而且经济耐用。
陶瓷球的原理就是在蓄热室内填冲直径相同的许多陶瓷实心球,堆积呈固
定床,球径一般在15-25mm之间。
陶瓷球蓄热体比表面积240m2/m3,众多的小球将气流分割成很小流股,气
流在蓄热体中流过时,形成强烈紊流,有效地冲破了蓄热体表面的附面层,又
由于球径很小,传热半径小,热阻小,密度高,导热性强,加之换向系统设计
独特,故可实现频繁且快速的换向,固此,蓄热体可利用30次/H,高温烟气
流经蓄热体床层后便可将烟气降至150℃排放。常温空气流径蓄热体在相同路
径内即可预热至反比烟气温度低50℃,温度效率高达95%以上。另外,因为蓄
热体体积十分小巧,加之小球床的流通能力强,即使积灰的阻力增加也不影响
换热指标,陶瓷小球的更换,清洗非常方便,并可重复利用。
蓄热体材质 陶瓷材料
形状 球形
蓄热体体积 3m3
换向时间 120秒
空气预热温度 1000℃
高温烟气温度 1050℃
排烟温度 ≤150℃
材料比表面积(m2/m3) 240
球径 25mm
热回收率 约70%-80%
五、应用案例
下面以燃油、燃气蓄热式熔炉为案例,对采用某公司单蓄热(空气)技术
及专利设备(换向阀)等应用节能效果做比较和分析。
1.某厂熔化车间——新建项目
熔化材料:坯及再生材
炉子形式:矩形固定式
炉子容量:30T 炉膛工作温度:< 1 100℃
液温度:720℃~830℃ 熔体温差:≤±5℃
熔化期熔化率:h
熔池面积:×=
熔池深度:650mm
熔化期吨消耗:≤62 m3/吨
坯入炉温度:常温
燃料:天然气
发热值:8 500 kcal/Nm3
排烟温度:<150℃
蓄热材料:陶瓷小球
烧嘴型式:含点火及常明式蓄热式烧嘴
2.某业有限公司——改造项目
改造前:为常规的烧嘴技术,即采用机械式雾化油枪技术,熔化率为吨,
吨耗油76千克。经过改造后的熔化率达到5吨,熔热耗53千克,平均节油率
30%。
相关参数如下:
熔化材料:30%及合金锭、废料+70%电解液
炉子形式:矩形固定式、一扇组合大炉门、机械扒渣
炉子容量:25T
炉膛工作温度: < 1 100℃
液温度:730℃~860℃
熔化期熔化率:5t/h
熔池面积:5×4=20 m2
熔化期吨消耗:~53公斤/吨
熔料入炉温度:常温
燃料:0#轻柴油
发热值:10 200 kcal/kg
排烟温度:<150℃
六、总论:
从热平衡角度来说,采用蓄热式换热技术的熔化炉燃料节约率与炉子砌体的
蓄热量、炉体的表面散热损失有关。因为烧嘴是通过烟气回收余热的,炉体的
蓄热量减小,表面散热损失越少,则排烟余热量越大,燃料节约率就越高。
同时,由于熔炉间歇性工作特点,在不同工作状态时炉温、蓄热体中空气流
速、烟气出口温度有较大波动。这样烧嘴换向时间也应随工作状态变化而变
化,优化蓄热体的利用率,使余热回收达到更好的效果。
由于空气通过蓄热体后温度升高,带进炉内大量显热,使得燃料的理论燃烧温
度显着提高。在采用相同的炉型和燃料时,蓄热炉比常规炉有更高的综合加热
温度和更快的加热速度。
采用蓄热式换热技术,带来的直接经济效益主要是节省燃料。由于消除局部高
温区,炉温分布均匀,使耐火材料使用寿命延长,同时提高了加热质量,减少
了氧化烧损。由这些因素带来的经济效益也是相当可观的。
从环境保护角度来说,燃料节省25%,烟气中CO2等温室气体总量也相应减少了
25%。同时由于燃料在高温空气贫氧环境下,降低了NOX的产生。总之,蓄热技
术应用到熔炉上,起到了很好的节能效果;也降低了CO2和NOX的排放,减轻环
境污染。同时,蓄热技术还有待进一步研究,达到更好的节能、环保效果。
蓄热式熔铝炉
【节能技术】
河南鑫源铝业经销部