蓄热式熔铝炉的设计与应用
蓄热式熔铝炉资料
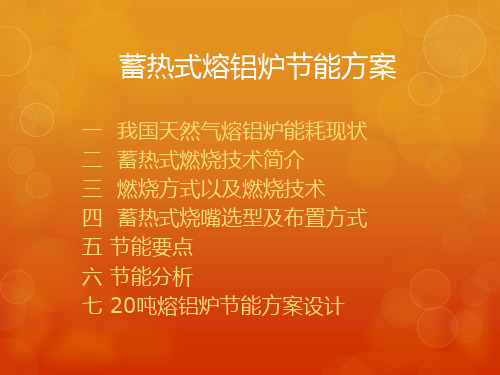
六 节能分析
我国天然气熔铝炉吨铝能耗75万大卡,折合天然气约88Nm3 , 过量空气系数1.17 需要空气量1030Nm3 产生烟气量1118Nm3 烟气温度1000℃ 烟气成分如图,1000℃烟气比热为1.51KJ/(m3℃) 空气平均温度22℃,比热为1.013KJ/(kg℃) 标况下空气密度1.293kg/m3 烟气带走热量约396680大卡
燃烧技术分类
二 燃气分级燃烧技术
没有定型的火焰,火焰无法控制,燃烧性能差, 燃气喷嘴易烧毁,辐射性能差,加热质量低。
二段式低NOx燃烧器
二段式低NOx燃烧器 该燃烧器的工作原理如图1所 示,是将燃烧用的空气分2次通 入燃烧区,从而使燃烧过程分两 个阶段完成,避免高温区过分集 中。二次空气是从还原区外围送 入的,在火焰尾部完成完全燃 烧。由于实行分段燃烧,避免了 高温区集中, 因而NOx的排放 浓度显著降低。
二 蓄热式燃烧技术简介
基本原理
烧嘴和蓄热体成对出现, 助燃空气通过其中一个烧嘴, 被加热后供燃烧用,另一个 烧嘴充当排烟的角色,同时 蓄热体被加热。当到达换向 时刻时,换向阀动作使系统 反向运行,烟气加热好的蓄 热体被用来加热空气,助燃 空气冷却的蓄热体又被离开 炉子的高温烟气加热,
技术形成
将高温空气喷射入炉 膛,维持低氧状态,同时将 燃料输送到气流中,产生燃 烧。空气温度预热到800℃ ~1000℃以上,燃烧区空气 含氧量在21%~2%,与传统燃 烧过程相比,高空气燃烧的 最大特点是节省燃料,减少 CO2和NOX的排放及降低燃烧 噪音,被誉为二十一世纪关 键技术之一。
蓄热式燃烧系统工作原理
三 燃烧方式分类
1扩散式燃烧 2部分预混式燃烧 3预混式燃烧
1扩散式燃烧
2部分预混式燃烧 3预混式燃烧
蓄热式燃烧系统在熔铝炉上的应用
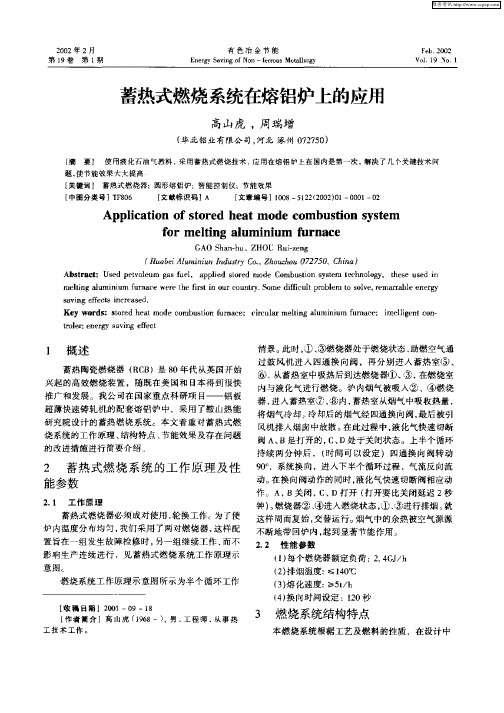
Ke r s s r d h a d o u t n f r a e cr u a l n l r ii m u a e i tl g n O - y wo d : t e e tmo e c mb si u n c ; i lrme t g a u nn u f r c ; ne l e tC N o o c i n i
ma t g au nu n f r a e wee t e f s i u o nr-S me d f c l p o l m o v , en ra l n ry l i l mi ir n c / h rt n o rc u t . o i iu t r b e t s le r r a r b ee eg n u ' i y o
情景。 此时, 、 ① ③燃烧器处于燃烧状态 , 助燃空气通 过鼓风机进入四通换 向阀,再分别进入蓄热室⑤ 、 ⑥, 从蓄热室中吸热后到达燃烧器①、 , ③ 在燃烧室 内与液化气进行燃烧。炉内烟气被吸人② 、④燃烧 器, 进入蓄热室⑦、 ⑧内 , 蓄热室从烟气 中吸收热量 , 将烟 气冷 却 冷却后 的 烟气 经 四通 换 向阀 , 后被 引 最
风机排 人 烟 囱中放散 。 此过 程 中, 在 液化气 快 速切断 阀 A、 B是 打开 的 , 、 C D处 于关 闭状态 。上 半个 循环 持 续 两 分钟 后 , ( 间 可 以设定 ) 四通 换 向 闻转 动 时 9。 0 ,系统换 向 ,进 入下半 个循 环过程 ,气 流反 向流 动。 在换 向阀动作 的 同时 , 化气 快速切 断 阀相应动 液 作 。A 、B关 闭 , 、D打开 ( C 打开要 比关 闭延迟 2 秒
20吨蓄热式熔铝炉技术参数及设备报价
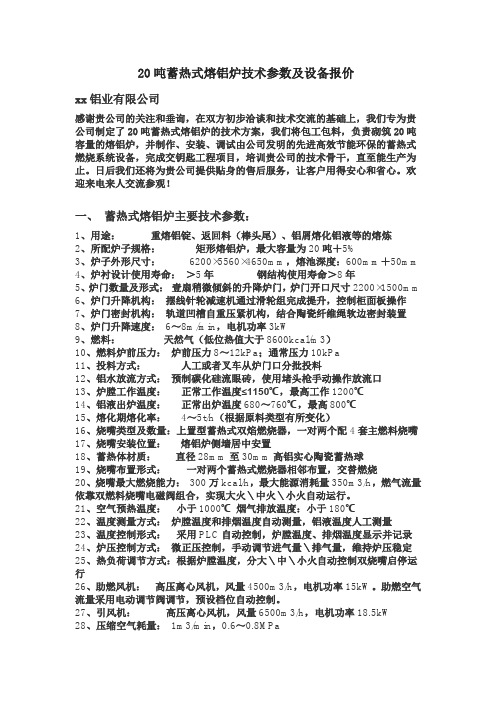
20吨蓄热式熔铝炉技术参数及设备报价xx铝业有限公司感谢贵公司的关注和垂询,在双方初步洽谈和技术交流的基础上,我们专为贵公司制定了20吨蓄热式熔铝炉的技术方案,我们将包工包料,负责砌筑20吨容量的熔铝炉,并制作、安装、调试由公司发明的先进高效节能环保的蓄热式燃烧系统设备,完成交钥匙工程项目,培训贵公司的技术骨干,直至能生产为止。
日后我们还将为贵公司提供贴身的售后服务,让客户用得安心和省心。
欢迎来电来人交流参观!一、蓄热式熔铝炉主要技术参数:1、用途:重熔铝锭、返回料(棒头尾)、铝屑熔化铝液等的熔炼2、所配炉子规格:矩形熔铝炉,最大容量为20吨+5%3、炉子外形尺寸:6200×5560×4650mm,熔池深度:600mm+50mm4、炉衬设计使用寿命:>5年钢结构使用寿命>8年5、炉门数量及形式:壹扇稍微倾斜的升降炉门,炉门开口尺寸2200×1500mm6、炉门升降机构:摆线针轮减速机通过滑轮组完成提升,控制柜面板操作7、炉门密封机构:轨道凹槽自重压紧机构,结合陶瓷纤维绳软边密封装置8、炉门升降速度:6~8m/min,电机功率3kW9、燃料:天然气(低位热值大于8600kcal/m3)10、燃料炉前压力:炉前压力8~12kPa;通常压力10kPa11、投料方式:人工或者叉车从炉门口分批投料12、铝水放流方式:预制碳化硅流眼砖,使用堵头枪手动操作放流口13、炉膛工作温度:正常工作温度≤1150℃,最高工作1200℃14、铝液出炉温度:正常出炉温度680~760℃,最高800℃15、熔化期熔化率:4~5t/h(根据原料类型有所变化)16、烧嘴类型及数量:上置型蓄热式双焰燃烧器,一对两个配4套主燃料烧嘴17、烧嘴安装位置:熔铝炉侧墙居中安置18、蓄热体材质:直径28mm至30mm高铝实心陶瓷蓄热球19、烧嘴布置形式:一对两个蓄热式燃烧器相邻布置,交替燃烧20、烧嘴最大燃烧能力:300万kcal/h,最大能源消耗量350m3/h,燃气流量依靠双燃料烧嘴电磁阀组合,实现大火\中火\小火自动运行。
蓄热式燃烧技术在再生铝熔化炉上的应用
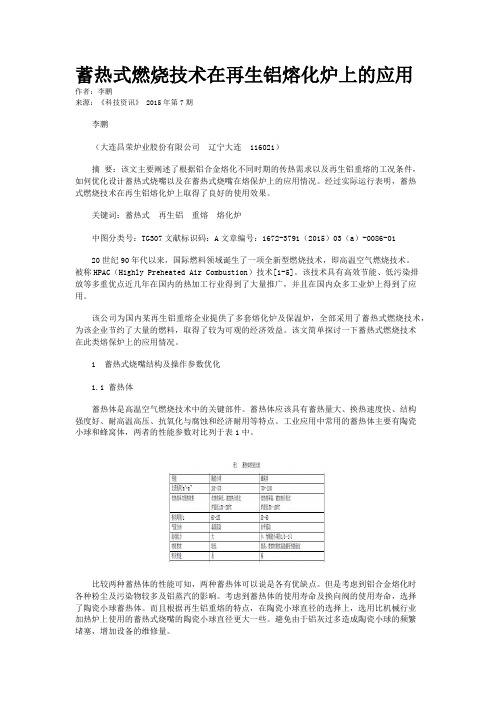
蓄热式燃烧技术在再生铝熔化炉上的应用作者:李鹏来源:《科技资讯》 2015年第7期李鹏(大连昌荣炉业股份有限公司辽宁大连 116021)摘要:该文主要阐述了根据铝合金熔化不同时期的传热需求以及再生铝重熔的工况条件,如何优化设计蓄热式烧嘴以及在蓄热式烧嘴在熔保炉上的应用情况。
经过实际运行表明,蓄热式燃烧技术在再生铝熔化炉上取得了良好的使用效果。
关键词:蓄热式再生铝重熔熔化炉中图分类号:TG307文献标识码:A文章编号:1672-3791(2015)03(a)-0086-0120世纪90年代以来,国际燃料领域诞生了一项全新型燃烧技术,即高温空气燃烧技术。
被称HPAC(Highly Preheated Air Combustion)技术[1-5]。
该技术具有高效节能、低污染排放等多重优点近几年在国内的热加工行业得到了大量推广,并且在国内众多工业炉上得到了应用。
该公司为国内某再生铝重熔企业提供了多套熔化炉及保温炉,全部采用了蓄热式燃烧技术,为该企业节约了大量的燃料,取得了较为可观的经济效益。
该文简单探讨一下蓄热式燃烧技术在此类熔保炉上的应用情况。
1 蓄热式烧嘴结构及操作参数优化1.1 蓄热体蓄热体是高温空气燃烧技术中的关键部件。
蓄热体应该具有蓄热量大、换热速度快、结构强度好、耐高温高压、抗氧化与腐蚀和经济耐用等特点。
工业应用中常用的蓄热体主要有陶瓷小球和蜂窝体,两者的性能参数对比列于表1中。
比较两种蓄热体的性能可知,两种蓄热体可以说是各有优缺点。
但是考虑到铝合金熔化时各种粉尘及污染物较多及铝蒸汽的影响。
考虑到蓄热体的使用寿命及换向阀的使用寿命,选择了陶瓷小球蓄热体。
而且根据再生铝重熔的特点,在陶瓷小球直径的选择上,选用比机械行业加热炉上使用的蓄热式烧嘴的陶瓷小球直径更大一些。
避免由于铝灰过多造成陶瓷小球的频繁堵塞,增加设备的维修量。
1.2 换向方式选择蓄热式燃烧的换向方式主要有两种,一种是一对烧嘴采用一个四通换向阀,这个四通换向阀的四个出口分别连接两只蓄热式烧嘴、助燃风机和排烟风机。
蓄热式换热技术在熔铝炉上的应用

蓄热式换热技术在熔铝炉上的应用1.蓄热技术概述随着设备与材料的进步,蓄热式换热技术有了革命性的发展和长足的进步。
目前在冶金企业的加热炉和钢包烘烤器上得到了广泛的应用。
本文通过介绍蓄热技术在熔铝炉上的应用,说明了蓄热式换热技术对提高化铝质量,加快化铝速度,减少污染物排放,降低能耗等方面的优势。
蓄热式换热技术在有色冶金行业上也将有广阔的应用前景。
2.蓄热式换热技术原理蓄热式烧嘴成对布置,相对两个烧嘴为一组(A组、B组烧嘴)。
从鼓风机出来的常温空气由换向阀切换进蓄热式烧嘴1、4后,在经过蓄热式烧嘴1、4陶瓷小球时被加热,在极短时间内常温空气被加热到接近炉膛温度(一般为炉膛温度的80-90%)。
被加热的高温热空气进入炉膛后,卷吸周围炉内的烟气形成一股含氧量大大低于21%的稀薄贫氧高温气流,同时往稀薄高温空气附近注入燃料,实现燃料在贫氧状态下燃烧;与此同时,炉膛内的热烟气经过另两个蓄热式烧嘴2、3排入大气,炉膛内高温热烟气通过蓄热式烧嘴2、3时将显热储存在蓄热式烧嘴2、3内的蓄热体内,然后以低于150℃的低温烟气经过换向阀排出。
当蓄热体储存的热量达到饱和时换向进行切换,蓄热式烧嘴在蓄热与工作状态之间进行交换,从而达到节能和降低NOX排放量等目的。
蓄热式换热技术改变了传统的燃烧方式,主要表现为燃料与空气以适当速度从不同的通道进入炉内,并与炉内燃烧产物混合,空气中21%的O2被稀释,燃料在炉膛中高温(1000℃以上)低氧浓度场(5~6.5%)工况下燃烧,此种燃烧方式带来了许多优点。
(1)节能效果显著,比传统熔炼炉节能30%以上由于蓄热体“极限回收”了烟气中大部分的余热,并由参与燃烧的介质带回炉内,大大降低了炉子的热支出,所以采用蓄热式换热技术的炉子比传统熔炼炉节能。
(2)消除了局部高温区,炉温分布均匀燃料在高温低氧浓度工况下燃烧,在炉内形成没有稳定火焰的扩散火焰,消除了稳定火焰产生的局部高温区;火焰几乎充满整个炉膛,使炉温更加均匀。
蓄热燃烧技术的应用

蓄热燃烧技术的应用蓄热燃烧技术是基于蓄热室的概念回收废气的余热,实现余热极限回收和助燃空气的高温预热,达到节能效果。
蓄热室最早发明于1858年,主要用在玻璃熔炉、平炉、熔铝炉等工业路上。
自20世纪70年代能源危机后,节能降耗得到各个国家的重视,蓄热式燃烧技术由于能够最大限度地回收出炉烟气的热量,大幅度地节约燃料、降低成本,同时还能减少CO2和NO x的排放量。
因此,该技术在国际上被称为二十一世纪的关键技术之一。
1.蓄热式燃烧器九十年代至今, 美、日、英等国开发出蓄热式燃烧器,并不断加以发展完善,实现了高效节能与低污染排放,现已成功地应用于加热炉、热处理炉、锻造炉等工业炉上。
蓄热式燃烧器是一种集燃烧器、换热器、排烟功能为一体的新型燃烧器,主要通过蓄热体,利用烟气热量将空气预热至高温,很大地提高热能利用率;同时又采用了分级燃烧和烟气回流技术,减少了燃烧污染的排放量。
蓄热式燃烧器主要有陶瓷蓄热室、燃料喷口、高温空气喷口、绝热管道、换向阀等组成。
燃烧器喷口既是火焰入口又是烟气排出口。
蓄热室大多紧靠在燃烧器上,蓄热体材料的主要成分是氧化铝,一般采用直径为十几毫米的陶瓷球。
近来已发展采用蜂窝陶瓷体作为蓄热体,蜂窝陶瓷蓄热体比陶瓷球蓄热体具有更大的比表面,蓄热效率更高。
蓄热式燃烧器必须成对安装,两个为一组。
其中包括两个相同的燃烧器,两个蓄热器、一套换向阀门和配套控制系统。
如图1所示。
A烧嘴工作时,燃料和空气由A 烧嘴喷入,燃烧生成的火焰加热物料,高温烟气进入B烧嘴,并通过辐射、对流传热将热量传给蓄热体,烟气温度降低到200℃以下经过换向阀排出。
然后换向工作,冷空气通过B烧嘴的蓄热室后,已含热量的蓄热体再以对流换热为主的方式将空气预热至高温(一般空气预热温度与排烟入口温度仅差50~150 ℃),而使传热蓄热体被冷却。
换向阀一般以30~200s的频率进行切换,使两个蓄热体处于蓄热与放热交替工作状态,周而复始地运行。
蓄热式熔铝炉节能技术
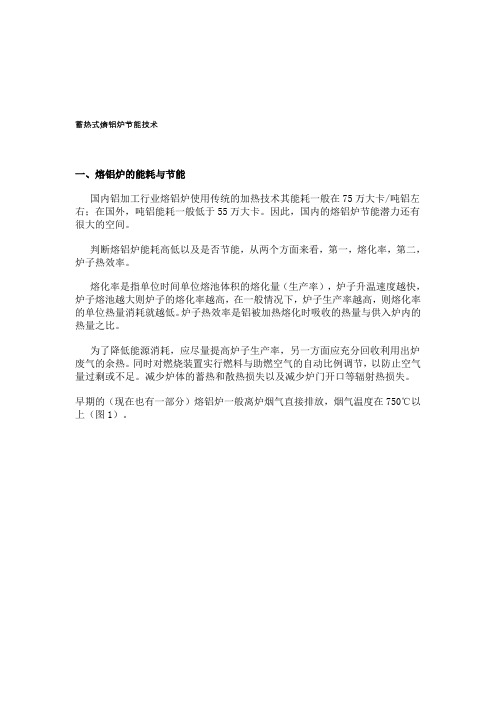
蓄热式熔铝炉节能技术一、熔铝炉的能耗与节能国内铝加工行业熔铝炉使用传统的加热技术其能耗一般在75万大卡/吨铝左右;在国外,吨铝能耗一般低于55万大卡。
因此,国内的熔铝炉节能潜力还有很大的空间。
判断熔铝炉能耗高低以及是否节能,从两个方面来看,第一,熔化率,第二,炉子热效率。
熔化率是指单位时间单位熔池体积的熔化量(生产率),炉子升温速度越快,炉子熔池越大则炉子的熔化率越高,在一般情况下,炉子生产率越高,则熔化率的单位热量消耗就越低。
炉子热效率是铝被加热熔化时吸收的热量与供入炉内的热量之比。
为了降低能源消耗,应尽量提高炉子生产率,另一方面应充分回收利用出炉废气的余热。
同时对燃烧装置实行燃料与助燃空气的自动比例调节,以防止空气量过剩或不足。
减少炉体的蓄热和散热损失以及减少炉门开口等辐射热损失。
早期的(现在也有一部分)熔铝炉一般离炉烟气直接排放,烟气温度在750℃以上(图1)。
图1 废热不利用的炉子为减少烟气带走的热量损失,人们在排烟管道上安装了热量回收装置即空气换热器,将助燃空气预热到一定的温度(200℃左右)后参与燃料的燃烧,但换热器后的排放温度还在500℃以上(图2)。
图2 安装空气预热器的炉子采用蓄热式燃烧技术可以将烟气排放温度降低到150℃以下,助燃空气温度预热到700℃以上,这样就大大地减少了离炉烟气所带走的热量,使炉子热效率大幅度提高,燃料消耗大量减少,达到节能的目的(图3)。
图3 HTAC技术的工作原理图根据工业炉热工原理,助燃空气温度每升高100℃,能节省燃料约5%;或者烟气温度每降低100℃,能节省燃料约5.5%。
因此,采用蓄热式燃烧技术相对换热器回收装置可以节能25%以上。
二.熔炼炉概述:传统上有火焰炉、电阻炉、中频感应炉、反射炉以及坩埚炉等。
为了获得质量高又经济的铝合金溶液,各企业对熔炼设备的选择越来越重视,近几年来,火焰炉、电阻炉、中频感应炉、反射炉都有所改进。
熔炼炉结构的发展方向是:操作自动化、应用更新化、原料节能化等。
蓄热燃烧器在当代熔铝炉上的应用

蓄热燃烧器在当代熔铝炉上的应用近20年来,通过热工职业者的试验切磋,熔铝炉的燃烧控制技能和余热接纳技能取得了突破性的前进。
以RCB、1150、HRS蓄热烧嘴()为代表的新式燃烧装置,在抬高生产率、低沉燃耗和浑浊物的排放量方面取得了很大的胜利。
本文以25t顶装料圆形炉为例,对新式RCB蓄热烧嘴的机关特点、应用性能和经济效益作扼要引见。
1 25t圆形炉的机关与技能性能1.1 圆形炉的机关与性能25t倾动式熔铝炉由圆形炉本体、可打开的球缺形炉盖、启盖机、炉底倾动机构、蓄热式燃烧器体系、烧嘴供风和引射风体系组成。
1.2 圆形炉的主要特点圆形炉的烧嘴按炉子中心圆的切线对象向下歪斜10°装置,使火焰直冲熔池,炉膛内形适于气流循环,无火焰死角,以担保对流加热成就好。
顶开盖可实现快速装料,每炉装料时间为15~20min,低沉劳动强度。
倾动式缩小了转注操纵时间,削减了熔体温度亏损。
圆形炉具有较小的比外观积,与矩形炉相比可低沉侧部蓄热散热亏损20%。
蓄热式烧嘴是成对设置装备摆设的高速烧嘴,25t圆形炉采取5套型号为RCB的蓄热烧嘴,单只烧嘴的供热本事为2.508GJ/h,火焰喷速快且周期换向,有利于炉气循环。
圆形炉采取钢机关框架,全耐火纤维喷涂的炉盖机关。
炉盖底圆直径6233mm,弦高760mm,耐火纤维的总厚度为300mm,此中普铝层厚度为120mm,高铝层厚度为180mm。
耐火纤维喷涂技能适于形状纷乱、异型部位的炉衬动工,具有动工速率快,筑炉劳动强度低,炉盖重量轻,蓄热少,升温快的长处。
RCB蓄热烧嘴装置有自动点火和火焰监测装置,当主燃烧器被点燃后,点火烧嘴可以自动关上。
烧嘴内衬为耐火质料,腐化介质对烧嘴和排烟器的应用寿命无不良影响。
与平凡自身预热烧嘴熔铝炉相比,可省去烟囱和付烟道,大大简化炉体机关。
2 蓄热烧嘴的机关与职业原理2.1 机关与原理蓄热式烧嘴与蓄热式炉相比,具有机关紧凑、换向时间短、排烟温度低、热接纳率高和预热温度摇动小的长处。
- 1、下载文档前请自行甄别文档内容的完整性,平台不提供额外的编辑、内容补充、找答案等附加服务。
- 2、"仅部分预览"的文档,不可在线预览部分如存在完整性等问题,可反馈申请退款(可完整预览的文档不适用该条件!)。
- 3、如文档侵犯您的权益,请联系客服反馈,我们会尽快为您处理(人工客服工作时间:9:00-18:30)。
蓄热式熔铝炉的设计与应用张路宁1,王春健2,武德刚3(1.沈阳工业学院,辽宁沈阳110015;2.渤海铝业有限公司,河北秦皇岛066000;3.鞍山市科学技术咨询中心,辽宁鞍山114000)摘要:介绍了蓄热式熔铝炉的设计与应用情况。
生产实践表明:通过采用蓄热式燃烧技术,熔铝炉的油耗指标由原来的120kg 柴油/t 铝降为54166kg 柴油/t 铝,节油率达54145%。
能耗指标达到了世界同类炉子的先进水平。
改造投资回收期6个月左右。
关键词:蓄热式燃烧;熔铝炉;燃烧器;四通换向阀;热效率中图分类号:TF066.1+2 文献标识码:B 文章编号:10021752(2002)020042031 概述与国外先进水平相比,我国目前现有熔铝炉,无论是自行设计的,还是由国外引进的,大多存在着炉子结构较为陈旧、能耗高的弊病。
这主要是因为熔铝炉的排烟道直接开设在熔池上方的炉膛上,排烟温度较高,几乎等于炉气温度。
这就使得使用通常的预热回收技术(如金属换热器、自身预热式烧嘴等)很难充分有效地回收烟气中热量,从而造成炉子热效率低,浪费燃料。
同时,又因造渣时所产生的烟气极具腐蚀性,常规预热回收设备的寿命也受到极大的限制。
渤海铝业有限公司每年熔铝炉、静止炉的燃油量约为2000~3000t ,单炉能耗指标为120~150kg 柴油/t 铝,而同类世界先进炉子的能耗指标在60kg 柴油/t 铝以下。
为了节能降耗,促进科技进步,提升炉子的装备水平,渤铝决定于2000年对两台旧式30t 熔铝炉进行全面的技术改造,由鞍山市科学技术咨询中心实施工程承包。
20世纪80年代在燃料燃烧领域出现了一项全新的燃烧技术-蓄热高温(预热)空气燃烧技术(High Temperature Air Combustion )。
它包括两项基本技术手段:一是燃烧产物显热最大限度回收(即极限回收);二是可实现燃料在低氧气氛下燃烧。
这一技术的出现,不仅使燃烧理论有了新的突破,也给传统的能源利用工业带来了变革性的发展,将这一技术应用到熔炼炉、工业炉上可大幅度降低能耗、减少烟气中有害气体排放。
1992~1998年的六年间,日本工业炉株式会社已在近150台工业窑炉上应用5 结语目前国内大多数铝电解槽平均寿命在4年左右。
而国外一些先进国家如法国彼施涅公司180kA 铝电解槽平均寿命达6~8年,比我国槽寿命高出两年以上。
这反映了我们在设计水平,材料质量、操作技术及装备水平方面有较大的差距。
这正是我们努力的方向。
通过一系列越来越符合实际的电解槽优化设计和电解槽的正确维护、操作管理是可以逐渐缩短这一距离的。
参考文献:〔1〕邱竹贤.预焙槽炼铝〔M 〕.冶金工业出版社.1980.〔2〕长铝公司科技部.铝电解生产文集(内部资料).〔3〕吕定雄等.我国开发大容量预焙铝电解槽的技术进步〔J 〕.铝镁通讯,2000,(4).〔4〕干益人.铝电解槽底部保温问题的分析与对策〔J 〕.轻金属,1999,(6).〔5〕黄永忠等.铝电解生产.中南工业大学出版社.(责任编辑 何允平)收稿日期:2001-09-01·24· 轻 金 属 2002年第2期其开发的几种类型的蓄热式高温空气燃烧器(烧嘴)近900台套〔1〕。
目前这项技术已在工业发达国家中开始推广应用。
早在1982年,参与本次技术改造的主要工程技术人员就开始了该项技术的研究开发工作,其中包括:不同形式蓄热体的传热及流动特性的研究、蓄热式烧嘴的结构及火焰特性的研究、空气/烟气及各种燃料换向阀的开发、燃烧控制系统研制等,并取得了许多成果。
在此基础上我们设计建造了渤海铝业公司的两座容量30t 熔铝炉,并于2000年9月顺利投产使用。
这是迄今为止国内自行设计建造,采用蓄热式燃烧技术最大的两座熔铝炉。
2 蓄热式燃烧的基本原理蓄热式高温(预热)空气燃烧系统主要由蓄热式燃烧器、蓄热室、烟气及燃料换向装置、控制系统等组成,图1给出了它的工作原理。
蓄热式烧嘴必须成对使用,两个烧嘴可以相对放置,亦可以成某一角度安装。
当烧嘴A 处于燃烧状态时,烧嘴B 则处于排烟状态。
高温烟气进入蓄热室B ,烟气显热被蓄热体吸收储存,烟气温度降至200℃以下经引风机排出。
一定时间间隔后,换向阀动作,烧嘴A 与烧嘴B 工作状态互换,助燃空气进入蓄热室B 立刻被预热到仅低于炉内温度50℃~150℃的温度水平。
烧嘴A 与烧嘴B 如此周而复始的交替工作,将烟气余热充分回收利用。
由于蓄热式燃烧系统的换向周期很短,因而炉内温度可以保持稳定。
蓄热式燃烧的原理并不复杂,但要想利用这一原理开发出有效可用的产品却存在着许多技术难题。
图1 蓄热式燃烧原理图3 工程设计特点3.1 炉体结构及烧嘴布置原炉炉盖为拱顶结构,经核算炉膛过高,这样非常不利于炉气充满炉膛。
改造后的炉盖采用了掉挂平顶结构,即降低了炉膛高度,也减少了炉盖重量。
原炉设置四个烧嘴,切向布置。
改后炉子采用一对蓄热式烧嘴,火焰交叉布置,强化了炉内对流传热。
3.2 CDR -J -350型蓄热式烧嘴的研制燃烧器是火焰炉最主要的设备,烧嘴性能的高低直接影响到炉子性能的好坏。
而要研究出高效蓄热式燃油烧嘴就必须解决许多技术难题。
为此我们做了大量的实验研究工作。
从雾化方式上划分,燃油烧嘴分为内混式和外混式。
与外混式相比,内混式烧嘴具有气耗率低、雾化质量高、单嘴能力大、燃料燃烧完全等优点。
但也存在着调节比小、燃油与雾化介质互相封堵等缺陷,这对于燃烧控制十分不利。
CDR -J -350型蓄热式烧嘴由于具有特殊的结构,从而解决了这一难题。
它的最大燃烧能力为350kg (油)/h ,最小仅为20kg (油)/h 。
试验结果表明,在雾化介质耗量较小的情况下,索太尔平均直径SMD (液雾颗粒粒度)小于40μm 。
由于蓄热式烧嘴既是燃烧设备也兼做排烟道,因而如何能够保证它在排烟时不被烧坏,同时油枪里残油又不至于被烤焦结碳,是蓄热式燃油烧嘴研制的又一难点。
CDR -J -350型蓄热式烧嘴从材质、结构两个方面入手,很好地解决了这一难题。
此外,CDR -J -350型蓄热式烧嘴还具有以下特点:⑴燃烧器不结焦;⑵燃烧器不堵塞;⑶火焰刚性强;⑷烧嘴砖采用过孔结构,抑制热态NO x 生成;⑸火焰喷射速度及形状满足加热工艺要求;⑹油枪拆装方便,便于维护。
3.3 CDR -R 型陶瓷球蓄热室蓄热室的热工指标随操作参数和结构参数的变化规律,称之为流动特性和传热特性。
在操作参数一定的情况下,两种特性取决于蓄热室的结构参数。
因此,蓄热室结构的设计是否合理直接影响到它的使用性能。
CDR -R 型蓄热室的设计主要考虑了蓄热体形·34·2002年第2期 张路宁,王春健,武德刚:蓄热式熔铝炉的设计与应用 状、比表面积、耐热冲击性、高温耐热强度、蓄热能力、透热深度、生产成本等因素。
蓄热体采用陶瓷耐热小球,比表面积达250m 2/m 3。
3.4 CDR -V 型四通空气/烟气换向阀具有独特结构的CDR -V 型四通空气/烟气换向阀,体积小、结构紧凑;换向动作时间小于2秒,工作平稳可靠;执行机构由进口气缸驱动,换向周期为1分40秒。
此外换向阀还具有良好的密封性能。
3.5 检测及控制系统为了完成对炉温、炉压、换向以及整个工艺过程的自动控制、自动检测、信号联锁、保护及故障诊断等实时任务,现场设备控制站采用德国SIEM ENS 公司的S7-300系列PLC 产品。
该产品性能、价格比在工控界占有很强的优势,具有易操作、易维护、可靠性高等优点,且注重开放性;过程,信息监控系统选用台湾研华公司的5862控机;炉前设有现场操作柜,显示炉了各控制、操作参数,可实施手工操作。
控制系统的组态软件为STEP7V510。
该软件是用于SIMA TIC S7可编程控制器的标准的组态工具;采用SIEM ENS 公司的WinCC 监控软件,开发工程师工作站、操作人员所需的人机界面及各种功能。
自行开发的工程控制应用软件,主要功能如下:⑴显示功能:“主菜单、监控画面、实测温度、压力、流量等参数、各种运行状态、提示及报警,加注文字、实时显示各种时间-温度过程曲线,不同曲线用不同颜色显示。
⑵控制功能:炉温、炉压、换向燃烧控制;联琐控制。
⑶报警功能:超温(炉温、蓄热室温度、排烟温度)、超压(炉压、油压、气压)、熄火、故障报警。
⑷存储功能:每炉全部过程数据、曲线按给定编号存入档案文件。
⑸打印功能:过程结束可即刻打印本炉报表及过程曲线;档案文件可在线或离线调出,复制成过程曲线或表格,以备质量分析所用。
4 改造后炉子性能指标熔炼炉砌体尺寸:内很:5000mm ;熔池深度:685mm ;炉膛高度:2325mm 。
装料量:30t设计熔化速率:正常条件下:5t/h ;最大产量时,7t/h 。
炉子热负荷:正常条件下:1014×106kJ /h ;最大产量时:1416×106kJ /h 烧嘴型式:蓄热式燃烧器;烧嘴个数:2个/台炉;燃料种类:柴油;雾化介质:压缩空气;点火烧嘴个数:2个/台炉;点火烧嘴燃料:石油液化气;蓄热体型式:耐火陶瓷球;蓄热球比表面积:250m 3/m 3;换向阀型式:四通空气/烟气换向阀;换向周期:1min40s ;单位油耗:60kg/t 铝;炉膛温度:1150℃;空气预热温度:低于炉温50℃~150℃;烟气排放温度:150~300℃;最大空气消耗量:4340Nm 3/h ;最大烟气排放量:4720Nm 3/h ;嘴前燃油压力:0105MPa ;雾化介质压力:012MPa5 炉子使用效果自2000年9月投产以来,炉子各项技术指标十分理想,燃烧系统工作正常,节能效益显著。
我们曾多次组织对炉子进行测定,并对炉子各项指标进行生产统计。
测定和统计结果表明:空气预热温度仅比炉温低100℃,温度效率达80%以上,排烟温度小于150℃;熔化速率最大时可达8t/h ;油耗指标由原来的120kg 柴油/t 铝降为54166kg 柴油/t 铝,节油率达54145%。
单炉测定油耗达到42kg 柴油/t 铝。
这些能耗指标均达到了世界同类炉子的先进水平。
两台炉子的年节油效益达700万元,改造投资回收期仅为6个月左右。
参考文献:〔1〕祁海鹰,徐旭常.中国开发应用高温空气燃烧技术的前景.HightTempererature Air Combustion.Beijing ,1999.(责任编辑 何允平)·44· 轻 金 属 2002年第2期。