多晶硅装置清洗 文档
多晶硅EDI设备清洗方案

多晶硅E D I设备清洗方案-CAL-FENGHAI-(2020YEAR-YICAI)_JINGBIANEDI设备清洗方案一、EDI的清洗方法:根据EDI的运行状态,EDI的清洗采用酸洗—消毒—碱洗的方法来清洗EDI模块。
1.清洗时,EDI的淡水室、浓水室和极水室都需要清洗。
即清洗液从“原水进”和”浓水进”清洗口进入EDI,从“产水”、“浓水出”、“极水出”回到清洗水箱。
(正洗)2.第一步酸洗:清洗水箱中配制% 盐酸溶液,循环30分钟。
冲洗:清洗水箱中酸洗液放掉后,将水箱中水冲洗至中性,然后将清洗进和回流管清洗到回流水至中性。
第二步消毒碱洗:水箱中配制% NaOH+%NaCL 的溶液,循环50分钟。
冲洗:清洗水箱中消毒液放掉后,清洗EDI至水箱中回流水至电导率降至100μs/cm以下。
警告:清洗过程中清洗压力最高不超过,膜块的电源禁止供电,清洗所需用水必须是RO或者EDI系统的产水。
二、清洗步骤:1.准备1)关闭EDI。
停止EDI运行,确定EDI模块的电源已被切断并把整流器转换钮转到“关闭”位置。
2)关闭下列阀门:原水进水阀、淡水产水阀、淡水冲洗排放阀、极水排放阀、浓水排放阀、浓水循环泵进出口阀。
3)将清洗水箱和相关的清洗管道清洗干净。
4)连接清洗管道。
把淡水产水、浓水排放、极水排放的清洗管线直接连接到清洗水箱上。
把原水进水、浓水进水清洗管线连接到EDI 系统的原水进水和浓水进水清洗接口上。
注意清洗管线必须牢固、紧密,以防止化学药品的喷溅。
2、浓水室酸洗1)约剂配制:在清洗水箱中注入大约1500L的反渗透产水作为溶剂,然后向其中缓缓加入大约60L (或73kg)37%的盐酸搅拌均匀配制成约%的盐酸溶液。
2)酸洗步骤(1)将清洗水泵出口软管连接到EDI系统浓水进口,EDI系统浓水出口用软管连接回流到清洗水箱,同时关闭EDI装置本身循环系统的进出阀门来避免药剂进入循环泵;(2)启动清洗泵以15m3/h(正常运行流速的一半)的流速循环清洗15分钟后停止清洗泵并关闭相应阀门让药剂在浓水室内浸泡15分钟左右,再次启动清洗泵循环清洗15分钟左右;(3)停止清洗并排净清洗箱和清洗泵;(4)浓水室冲洗:在清洗水箱中注入大约3000L反渗透水,启动清洗泵冲洗EDI浓水室,清洗流速约为15 m3/h(正常运行流速的一半),边冲洗边排放直到出水PH值接近7为止。
多晶硅清洗工艺流程
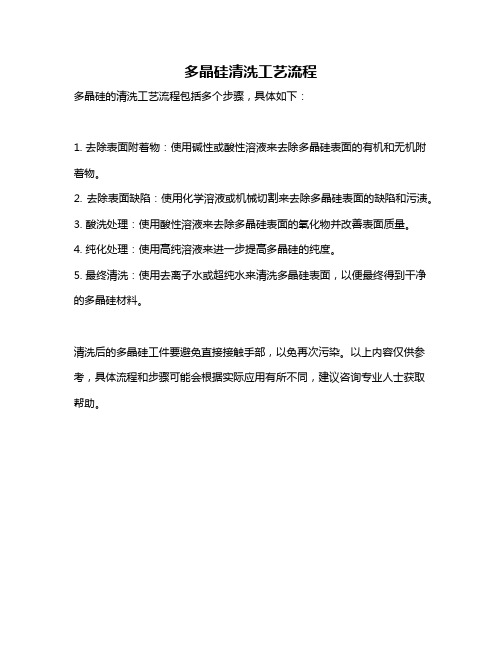
多晶硅清洗工艺流程
多晶硅的清洗工艺流程包括多个步骤,具体如下:
1. 去除表面附着物:使用碱性或酸性溶液来去除多晶硅表面的有机和无机附着物。
2. 去除表面缺陷:使用化学溶液或机械切割来去除多晶硅表面的缺陷和污渍。
3. 酸洗处理:使用酸性溶液来去除多晶硅表面的氧化物并改善表面质量。
4. 纯化处理:使用高纯溶液来进一步提高多晶硅的纯度。
5. 最终清洗:使用去离子水或超纯水来清洗多晶硅表面,以便最终得到干净的多晶硅材料。
清洗后的多晶硅工件要避免直接接触手部,以免再次污染。
以上内容仅供参考,具体流程和步骤可能会根据实际应用有所不同,建议咨询专业人士获取帮助。
多晶硅磁环清洗应急处置方案

多晶硅磁环清洗应急处置方案一、引言多晶硅磁环是一种重要的电子元件,广泛应用于电力、通信、计算机等领域。
然而,由于环境、操作等原因,多晶硅磁环可能会受到污染,影响其性能和使用寿命。
因此,建立一套科学、高效的清洗应急处置方案对于保障多晶硅磁环的质量至关重要。
二、清洗应急处置方案的重要性清洗应急处置方案的建立可以帮助企业在多晶硅磁环受到污染时迅速采取措施,保证产品质量,并减少经济损失。
合理的清洗方案可以有效去除污染物,提高多晶硅磁环的性能,延长使用寿命。
同时,清洗应急处置方案还可以规范操作流程,降低事故风险,保护工作人员的安全。
三、清洗应急处置方案的制定3.1 清洗前准备工作在进行多晶硅磁环清洗前,需要做好以下准备工作:1.确定清洗设备和工具:根据多晶硅磁环的尺寸和特性,选择合适的清洗设备和工具,如超声波清洗机、无尘室等。
2.准备清洗溶液:根据多晶硅磁环的污染情况,选择适当的清洗溶液,如去离子水、有机溶剂等。
3.确定清洗操作流程:制定清洗操作流程,包括清洗前准备、清洗操作步骤、清洗时间和温度等。
3.2 清洗操作步骤多晶硅磁环清洗的具体操作步骤如下:1.检查多晶硅磁环:在清洗前,对多晶硅磁环进行外观检查,确认是否有明显的污染或损坏。
2.清洗前处理:将多晶硅磁环放置在无尘室中,使用吹气枪或除尘器清除表面的尘土和杂质。
3.浸泡清洗:将多晶硅磁环放入清洗溶液中浸泡一定时间,使污染物溶解或分散。
4.超声波清洗:将浸泡的多晶硅磁环放入超声波清洗机中,开启超声波清洗功能,通过超声波的作用去除残留的污染物。
5.冲洗清洗:将清洗后的多晶硅磁环用去离子水冲洗,确保清除残留的清洗溶液。
6.干燥处理:使用干燥设备或自然晾干的方法,将多晶硅磁环彻底干燥。
7.检测验证:对清洗后的多晶硅磁环进行质量检测,确保清洗效果符合要求。
3.3 清洗应急处置方案的改进为了进一步提高多晶硅磁环清洗的效率和质量,可以考虑以下改进措施:1.优化清洗设备和工具:引进先进的清洗设备和工具,提高清洗效果和工作效率。
浅谈多晶硅生产中的设备清洗_朱顺云

青海科技2011年第5期5设备材料的选择由于金属氯化物的溶液显酸性,气态中有氯化氢的存在,设备材料的性质要有耐强腐蚀性。
通过氯碱工业的实际应用,钛及钛合金作为冷却器的材料是符合实际的。
在IM法制烧碱的装置中,金属纯钛主要用于制造电解槽阳极液系统的管道、分离器、循环槽、洗盐水储槽、湿氯系统和盐水脱氯系统中的部分设备,主要牌号是TA,其次是TA3。
钛是一种非常耐酸的金属,但其也有不足之处,在高温、高氯化物中,尤其是在Cl-存在下,会在设备的密闭面或缝隙处产生腐蚀,即所谓的缝隙腐蚀。
钛钯合金(Ti-0.15Pd)、Ti-0.3Mo-0.8Ni钛合金在缝隙腐蚀环境中具有良好的耐腐蚀性能,机械性能和化工性能优良,在有无氧的环境下都能够钝化,维持较正的电位而避免材料的腐蚀。
6技改前后的经济核算6.1技改前检修金属冷却器所投入的费用检修人数:10人;每月人均工资及各项保险费:3000元;每月人均防护用品费:350元;每月设备密封垫费用:600元/台,月检修30台,共计18000元;每年工业垃圾处理费:50000元。
单台设备费:106000元。
一年共需支出费用:10×3000×12+10×350×12+600×30×11+50000=650000元6.2技改后检修金属冷却器所投入的费用检修人数:5人;每月人均工资及各项保险费:3000元;每月人均防护用品费:300元;每月设备密封垫费用:100元/台,月检修30台,共计3000元;每年工业垃圾处理费:10000元。
单台设备费:360000元;单台辅助设备费:24000元。
一年共需支出费用:5×3000×12+5×300×12+100×30×11+10000=241000元6.3经济核算技改后一年节余费用:650000-241000=409000元;单台设备多投入费用:360000-106000=254000元;4台设备多投入费用:254000×4=1016000元;辅助设备费:54000元。
多晶清洗工艺与流程

多晶清洗工艺工程技术中心宋文涛2008.09摘要:1.概述2.一次清洗(扩散前清洗)3.二次清洗(去磷硅玻璃清洗)4.操作注意事项5.安全注意事项1.1整个产业链2.1一次清洗的目的:a. 去除切割硅片时硅片表面产生的损伤层,清除硅片表面的油类分子及金属杂质。
b.对硅片表面进行织构化处理,降低硅片表面对光的反射率。
酸制绒继续腐蚀继续腐蚀扫描电镜照片2.2一次清洗设备2.4一次清洗中各反应原理:制绒槽:HF-HNO3溶液,去除表面油污、切割损伤层以及制备绒面;反应如下:3Si + 18HF + 4HNO3 3H2SiF6+ 8H2O + 4NO碱洗槽:NaOH溶液,主要中和残留在硅片表面的酸,同时发生下列化学反应:Si+2NaOH+H2O =Na2SiO3+2H2酸洗槽:HF去除硅片在清洗过程中形成的很薄的SiO2 层,反应如下:SiO2+6HF = H2[SiF6]+2H2OHCL,HF同一些金属离子络合,使金属离子脱离硅片表面。
3.1二次清洗的目的:在形成PN结的扩散过程中,在硅片表面生长了一层一定厚度的磷硅玻璃,磷硅玻璃不导电,为了形成良好的欧姆接触,减少光的反射,在沉积减反射膜之前,必须把磷硅玻璃腐蚀掉。
3.3 二次清洗腐蚀原理:扩散中磷硅玻璃的形成:4 POCl3+ 3 O2= 2 P2O5+ 6 Cl2在较高的温度的时候,P2O5作为磷源与Si发生了如下反应:2 P2O5 +5 Si = 5 SiO2+ 4 P去除SiO2SiO2+6HF = H2[SiF6]+2H2O所以去磷硅玻璃清洗实质上就是去除硅片表面的SiO2。
4.操做注意事项:正确使用劳保用品,防患于未然控制溶液倒出的速度用力均匀叉子和片盒要有一定的角度轻微振动,有助于气泡释放表面疏水时,表明已合格均匀,缓慢5. 安全注意事项:HNO3、HF、NaOH、HCl、都是强腐蚀性的化学药品,其溶液、蒸汽会伤害到人的皮肤、眼睛、呼吸道,所以操作人员要按照规定穿戴防护服、防护面具、防护眼镜、长袖胶皮手套。
多晶硅生产设备安装前清洗

多晶硅生产设备安装前清洗一、多晶硅项目设备清洗的目的、意义多晶硅生产对环境及设备的清洁要求十分高。
生产工艺过程比较复杂。
尤其是塔器设备,对产品的质量影响极为重要。
为了保证一次性开车投产顺利,保证产品质量,在设备的安装过程中,对设备及管线等重要设备的清洗工作需要十分严谨。
在清洗过程中,使每个环节质量都达到标准,避免开车质量事故的发生,最大限度地降低调试费用。
针对不同的工艺要求、不同的设备材质以及不同的设备类型,清洗处理要求和达到的基本标准(要求达到无油、无水与无尘的三无要求)也不同。
同时符合《脱脂工程施工及验收规范》和《工业设备化学清洗质量标准》。
根据项目公司和十一设计院的具体要求本项目的清洗可分为一般清洗和洁净清洗。
多晶硅设备的清洗主要工艺为酸洗、脱脂、钝化、干燥等,其中最关键是脱脂工艺和干燥技术。
油脂和水对多晶硅的产品有巨大影响。
因此在多晶硅设备的清洗中,以脱脂工艺和干燥工艺为要点。
主要清洗还原炉、氢化炉、CDI设备;合成车间、还原氢化车间、精馏系统、中间罐、管道等主要设备。
并且为了保证脱脂和干燥的质量,多晶硅设备清洗需要对单台设备进行单台清洗并验收后,再进行安装。
二、污垢主要对多晶硅影响因素1、油脂:在多晶硅生产过程中,油分子对多晶硅的危害十分严重。
实际证明,整个工艺系统几ppm的油含量就可能造成多晶硅质量严重降低,甚至会造成系统污染累积。
因此,多晶硅设备的脱脂工艺尤为重要。
2、水分:水中含有大量的氯离子,氯离子对多晶硅制造工艺十分敏感。
设备及系统干燥工艺很关键。
3、氯离子残留:水和其他溶液在设备表面残留的氯离子对多晶硅系统设备影响巨大。
因此,在清洗后对设备进行纯水冲洗工艺十分重要。
4、氧化物、灰尘其他杂质:其他污垢的存在,对多晶硅的生产影响也很大。
因此,在设备清洗过程中,采用酸洗工艺对其他污垢进行清洗十分必要。
三、国内大、中型化工生产装臵清洗现状国外对设备、管道的清洗十分重视,有专门从事清洗的研究机构。
多晶硅设备清洗

XXX多晶硅企业3000t/a多晶硅项目主工艺系统清洗方案为确保XXX多晶硅企业3000t/a多晶硅项目能达到电子级多晶硅的生产标准,将生产系统内的所有设备、管道及附件、机泵、阀门、仪表等设备和材料,分为一般清洗和洁净清洗两种,并对工作流程、清洗内容做出以下技术方案。
适用标准:1、《工业设备化学清洗质量标准》(HG/T2387-2007);2、化工行业标准《脱脂工程施工及验收规范》(HG20202-2000);3、《腐蚀试样的制备、清洗和评定》以及对电子级设备的洁净标准(电子工业部颁发)。
一、工作流程1、非标压力容器设备类非标压力容器设备材质为碳钢的设备和材质为不锈钢的设备及内件的脱脂工作均由设备制造厂按照HG20202-2000《脱脂工程施工及验收规范》的要求进行处理,设备内部清洗工作均由设备制造厂按照HG/T2387-2007的要求进行处理。
非标压力容器设备出厂前均要严格把关,由设备制造厂和业主方验收人员充分做好设备出厂验收工作。
填写设备出厂验收单:对脱脂及钝化膜检验方法结果、干燥露点、封闭状态(盲板封闭)等要有明确记录,碳钢类设备要求充氮保护0.02Mpa。
容器类、反应器类、塔器类设备进厂后由业主方、监理方、安装施工单位、制造厂家共同进行设备内部洁净度验收,并填写《设备、材料化学清洗验收单》。
合格的直接移交施工单位进行安装,不合格者移交清洗公司进行处理,费用由制造厂承担。
换热类设备进厂由四方验收后直接移交清洗单位,由设备所属子项的承包安装单位进行箱体解体后做壳体气密性试验,合格后由清洗单位进行管程清洗并组织四方进行洁净度验收,填写《设备、材料化学清洗验收单》。
联合验收合格后由安装施工单位进行管箱组装和管程气密性试验。
合格后交付施工单位安装,碳钢设备要求氮气密封。
2、机泵、阀门、仪表类对于机泵、阀门、仪表类设备材料的酸洗钝化及清洗工作也均由设备制造厂按照HG20202-2000《脱脂工程施工及验收规范》的要求和HG/T2387-2007《工业设备化学清洗质量标准》的要求完成,业主方专人到制造厂进行酸洗钝化和清洗指导和监督,设备发货前由业主方和设备制造厂对完工设备进行内部洁净度验收并填写出厂验收单。
多晶硅设备清洗资料

多晶硅设备的清洗主要工艺为酸洗、脱脂、钝化、干燥等,其中最关键是脱脂工艺和干燥技术。
油脂和水对多晶硅的产品有巨大影响。
因此在多晶硅设备的清洗中,以脱脂工艺和干燥工艺为要点。
主要清洗还原炉、氢化炉、CDI设备、合成车间、还原氢化车间、精馏系统、中间罐、管道等主要设备。
并且为了保证脱脂和干燥的质量,多晶硅设备清洗需要对单台设备进行单台清洗并验收后,再进行安装。
一、污垢主要对多晶硅影响因素1、油脂:在多晶硅生产过程中,油分子对多晶硅的危害十分严重。
实际证明,整个工艺系统几PPM的油含量就可能造成多晶硅反应速度减慢,产量降低,甚至硅反应停止。
因此,多晶硅设备的脱脂工艺尤为重要。
2、水分:水中含有大量的氯离子,氯离子对多晶硅的反应十分敏感。
设备及系统干燥工艺很关键。
3、氯离子残留:水和其他溶液在设备表面残留的氯离子对多晶硅影响十分大。
因此,在清洗后对设备进行纯水冲洗工艺十分重要。
4、氧化物、灰尘其他杂质:其他污垢的存在,对多晶硅的生产影响也很大。
因此,在设备清洗过程中,采用酸洗工艺对其他污垢进行清洗十分必要。
二、国内大、中型化工生产装置清洗现状国外对设备、管道的清洗十分重视,有专门从事清洗的研究机构。
再国外,设计单位在设计化工工艺流程及要求时已经将清洗考虑了进去,并做了概算及投资。
清洗方式也有单一的水力清洗发单调发展到化学清洗、机械清洗等。
世界各国对清洗行业的组织形式是多种多样的,从单个零件到整个装置的清洗,既有专业化学清洗公司,也有企业自行组织的清洗队伍。
有的设备、管道及零部件需经常定期清洗,并且部分生产设备本身就装有固有的清洗装置,清洗技术的应用有了很大的进步。
生产多晶硅的工艺较多,各个国家生产厂家在开发新技术、进行技术改造的同时,通过对设备的清洗来降低能耗和保证多晶硅的产品质量。
提高设备运转率,延长使用寿命,争取以最低的能耗,生产出更多的多晶硅产品。
三、多晶硅装置开车前化学清洗的意义新建多晶硅装置中的设备、管线、精馏塔、槽、还原炉、氢化炉在制造、储存、运输和安装过程中会产生大量的污物。
- 1、下载文档前请自行甄别文档内容的完整性,平台不提供额外的编辑、内容补充、找答案等附加服务。
- 2、"仅部分预览"的文档,不可在线预览部分如存在完整性等问题,可反馈申请退款(可完整预览的文档不适用该条件!)。
- 3、如文档侵犯您的权益,请联系客服反馈,我们会尽快为您处理(人工客服工作时间:9:00-18:30)。
多晶硅装置开车前清洗技术多晶硅生产对环境及设备的清洁要求十分高。
生产工艺过程比较复杂。
尤其是塔器设备,对产品的质量影响极为重要。
为了保证一次性开车投产顺利,保证产品质量,在设备的安装过程中,对设备及管线等重要设备的清洗工作十分严谨。
在清洗过程中,使每个环节质量都达到标准。
避免开车质量事故的发生。
最大限度地降低调试费用,必须做好工艺设备和工艺管道安装前的清洗处理。
针对不同的工艺要求、不同的设备材质以及不同的设备类型,清洗处理要求和达到的基本标准(要求达到无油、无水与无尘的三无要求)也不同。
同时符合《脱脂工程施工及验收规范》和《工业设备化学清洗质量标准》并根据业主和成达公司的具体要求可分为一般清洗和洁净清洗。
多晶硅设备的清洗主要工艺为酸洗、脱脂、钝化、干燥等,其中最关键是脱脂工艺和干燥技术。
油脂和水对多晶硅的产品有巨大影响。
因此在多晶硅设备的清洗中,以脱脂工艺和干燥工艺为要点。
主要清洗还原炉、氢化炉、CDI设备、合成车间、还原氢化车间、精馏系统、中间罐、管道等主要设备。
并且为了保证脱脂和干燥的质量,多晶硅设备清洗需要对单台设备进行单台清洗并验收后,再进行安装。
二、污垢主要对多晶硅影响因素1、油脂:在多晶硅生产过程中,油分子对多晶硅的危害十分严重。
实际证明,整个工艺系统几ppm的油含量就可能造成多晶硅反应速度减慢,产量降低,甚至硅反应停止。
因此,多晶硅设备的脱脂工艺尤为重要。
2、水分:水中含有大量的氯离子,氯离子对多晶硅的反应十分敏感。
设备及系统干燥工艺很关键。
3、氯离子残留:水和其他溶液在设备表面残留的氯离子对多晶硅影响十分大。
因此,在清洗后对设备进行纯水冲洗工艺十分重要。
4、氧化物、灰尘其他杂质:其他污垢的存在,对多晶硅的生产影响也很大。
因此,在设备清洗过程中,采用酸洗工艺对其他污垢进行清洗十分必要。
一、概述多晶硅生产对环境及设备的清洁要求十分高。
生产工艺过程比较复杂。
尤其是塔器设备,对产品的质量影响极为重要。
为了保证一次性开车投产顺利,保证产品质量,在设备的安装过程中,对设备及管线等重要设备的清洗工作十分严谨。
在清洗过程中,使每个环节质量都达到标准。
避免开车质量事故的发生。
最大限度地降低调试费用,必须做好工艺设备和工艺管道安装前的清洗处理。
针对不同的工艺要求、不同的设备材质以及不同的设备类型,清洗处理要求和达到的基本标准(要求达到无油、无水与无尘的三无要求)也不同。
同时符合《脱脂工程施工及验收规范》和《工业设备化学清洗质量标准》并根据业主和成达公司的具体要求可分为一般清洗和洁净清洗。
多晶硅设备的清洗主要工艺为酸洗、脱脂、钝化、干燥等,其中最关键是脱脂工艺和干燥技术。
油脂和水对多晶硅的产品有巨大影响。
因此在多晶硅设备的清洗中,以脱脂工艺和干燥工艺为要点。
主要清洗还原炉、氢化炉、CDI设备、合成车间、还原氢化车间、精馏系统、中间罐、管道等主要设备。
并且为了保证脱脂和干燥的质量,多晶硅设备清洗需要对单台设备进行单台清洗并验收后,再进行安装。
二、污垢主要对多晶硅影响因素1、油脂:在多晶硅生产过程中,油分子对多晶硅的危害十分严重。
实际证明,整个工艺系统几ppm的油含量就可能造成多晶硅反应速度减慢,产量降低,甚至硅反应停止。
因此,多晶硅设备的脱脂工艺尤为重要。
2、水分:水中含有大量的氯离子,氯离子对多晶硅的反应十分敏感。
设备及系统干燥工艺很关键。
3、氯离子残留:水和其他溶液在设备表面残留的氯离子对多晶硅影响十分大。
因此,在清洗后对设备进行纯水冲洗工艺十分重要。
4、氧化物、灰尘其他杂质:其他污垢的存在,对多晶硅的生产影响也很大。
因此,在设备清洗过程中,采用酸洗工艺对其他污垢进行清洗十分必要。
三、国内大、中型化工生产装置清洗现状国外对设备、管道的清洗十分重视,有专门从事清洗的研究机构。
再国外,设计单位在设计化工工艺流程及要求时已经将清洗考虑了进去,并做了概算及投资。
清洗方式也有单一的水力清洗发单调发展到化学清洗、机械清洗等。
世界各国对清洗行业的组织形式是多种多样的,从单个零件到整个装置的清洗,既有专业化学清洗公司,也有企业自行组织的清洗队伍。
有的设备、管道及零部件需经常定期清洗,并且部分生产设备本身就装有固有的清洗装置,清洗技术的应用有了很大的进步。
生产多晶硅的工艺较多,各个国家生产厂家在开发新技术、进行技术改造的同时,通过对设备的清洗来降低能耗和保证多晶硅的产品质量。
提高设备运转率,延长使用寿命,争取以最低的能耗,生产出更多的多晶硅产品。
四、多晶硅装置开车前化学清洗的意义新建多晶硅装置中的设备、管线、精馏塔、槽、还原炉、氢化炉在制造、储存、运输和安装过程中会产生大量的污物。
这些污物主要有:油脂、扎制鳞片、氧化铁锈皮、泥沙、焊渣、焊药、防锈油及表面涂层等。
其中焊渣、焊药的主要成分为钛、锰、铬、铁等金属氧化物,而切削油和防锈油及表面涂层则是一些高分子有机物。
新建多晶硅设备进行化学清洗,不仅要进行高要求的除油脂处理,而且还要进行化学清洗和钝化保护处理。
随着缓蚀技术的发展,金属设备在化学清洗过程中的腐蚀损失已降到了很小,最终的钝化处理将有助于减小设备运行中的腐蚀。
另外,同酸洗时的腐蚀相比,轧制鳞片、氧化铁锈皮、泥沙、焊渣、防锈油及涂层等引起的设备运行事故更加具有危险性。
由于化学清洗之后,得到了干净的金属表面,因而能更快的生产出合格的产品,工厂由此获得的经济效益将大大超过清洗的投资费用。
目前,各种新建装置尤其是高温、高压设备、大型设备和生产工艺要求比较高的设备和管线,再投产前都要进行化学清洗。
不仅要清洗设备本体,而且要清洗那些与设备连接有可能把污物带入的其他管道和设备。
同样,我们认为多晶硅装置不仅要清洗工艺系统,其它附属设备的化学清洗和钝化处理对设备的运行安全和寿命意义重大,因此,我们建议所有的设备必须进行化学清洗。
五、多晶硅设备主要清洗项目1、还原炉、氢化炉的清洗脱脂钝化干燥2、CDI系统设备的清洗脱脂钝化干燥3、还原氢化车间设备的清洗脱脂钝化干燥4、合成车间设备的清洗脱脂钝化干燥5、精馏工序设备的清洗脱脂钝化干燥6、中间罐区的清洗脱脂钝化干燥7、管道系统的清洗脱脂钝化干燥六、附件1、奥氏体不锈钢设备的化学清洗和钝化2、不锈钢设备及零部件酸洗钝化技术(设备清洗必要性论文)附件一奥氏体不锈钢设备的化学清洗和钝化摘要: 从奥氏体不锈钢的钝化机理入手,分析了钝化膜存在的意义、破坏机理和防护措施,给出了参考的清洗钝化剂配方、清洗钝化工艺、操作注意事项,明确了奥氏体不锈钢钝化膜质量的检验方法。
关键词:奥氏体不锈钢;清洗;钝化;钝化膜;质量检验中图分类号: TG178文献标识码: C奥氏体不锈钢设备在加工、制作和使用过程中,因高温氧化、介质腐蚀等原因,其表面会产生明显颜色不均匀的斑痕或腐蚀痕迹,或出于美观要求,奥氏体不锈钢常常需要进行化学清洗和钝化处理,使设备表面形成完整均匀的表面钝化膜,以提高材料的美观性和耐腐蚀性能,延长不锈钢使用寿命。
本文从不锈钢钝化原理入手,就不锈钢清洗方法、钝化工艺以及表面钝化膜质量和均匀性检验开展讨论。
1奥氏体不锈钢酸洗钝化的原理奥氏体不锈钢具有良好的耐腐蚀性能和优良的冷热加工性能,广泛用于各类具有防腐蚀和美观要求的设备以及其它容器、设备和机具的制造,表面的钝化膜质量和均匀性,对其耐腐蚀影响很大。
1. 1钝化机理金属经氧化性介质处理,在其表面生成均匀致密的氧化膜,并使腐蚀速度比未处理前有显著下降的现象称金属的化学钝化。
钝化机理可以用薄膜理论解释为:钝化是由于金属与氧化性介质发生电化学反应,在金属表面上生成一层薄而致密、覆盖性良好、附着力强的氧化物膜层,即“钝化膜”;钝化膜独立存在, 通常是氧和金属的化合物, 主要成分为CrO3、FeO与NiO,它是不锈钢防腐蚀的基本屏障,是腐蚀介质扩散的阻挡层,而并不是把金属与腐蚀介质完全隔开,钝化膜具有动态特征,通常在有还原剂(如氯离子)情况下倾向于破坏膜,而在氧化剂(如空气)存在时能保持或修复膜[ 1 ] 。
1. 2钝化膜的破坏奥氏体不锈钢表面经氧化性介质钝化处理后其表面上形成的钝化膜,在具有起活化作用的Cl- 、Br- 、F- 等卤素离子存在的条件下,易遭到破坏而失去原有的耐蚀性能和装饰性能。
其中Cl- 对不锈钢钝化膜的破坏作用最强,同时Cl- 在水中普遍存在,这也就是奥氏体不锈钢设备使用过程中要求Cl- 质量分数不超过25 μg/g 的原因之一,同时要求奥氏体不锈钢不能用盐酸等高氯离子含量的酸进行酸洗。
奥氏体不锈钢在化学清洗后或压力容器水试压后,若不能及时将残水清除干净,也要求使用Cl- 质量分数不超过25μg/g的水冲洗设备。
2 奥氏体不锈钢的化学清洗和钝化奥氏体不锈钢酸洗和钝化常常是同步完成的,一般采用氧化性较强的硝酸为主剂的清洗钝化剂,如需要钝化的设备表面含有油脂、有机物和其他酸不易溶解的物质,为了提高酸洗和钝化膜质量,要求在钝化前,对被钝化表面进行除油清洗处理。
2. 1清洗钝化剂和酸洗钝化膏配方清洗钝化剂1: 20%硝酸+ 5%氢氟酸+ 75%水清洗钝化剂2: 5%硝酸+ 2%重铬酸钾+ 93%水清洗钝化剂3: 20%硝酸+ 10%氢氟酸+ 70%水酸洗钝化膏配方: 30%硝酸+ 2%氢氟酸,用硫酸钡搅拌成糊状。
均以质量比配制。
2. 2化学清洗和钝化工艺不同的设备需要采用不同的清洗钝化工艺,一般采用如下方法:(1) 小型零部件或形状复杂的工件和设备,适合于采用浸泡法。
优点是清洗钝化液反复使用,生成成本低,钝化时间灵活机动,清洗钝化效果直观;缺点是液体不流动,有时钝化效果不均匀,为使其均匀常采用提拉法。
(2) 其工艺流程为:水冲洗—酸洗钝化—水冲洗—除油—水洗—钝化膜检验—干燥。
(2)大型成套装置和设备内表面清洗钝化,如双氧水成套装置、换热器、容器、塔器、管网的清洗钝化处理,常采用全充满法或喷淋法。
采用此类工艺,优点是一次处理的设备数量大,涉及面广,清洗钝化剂可以反复使用,清洗钝化效果均匀;缺点是此法需要的清洗钝化剂用量较大,施工工艺复杂,操作难度大,需要操作人员具有一定的专业水准,多由专业清洗队伍负责完成。
其工艺流程为:配管建立清洗系统—注水循环冲洗—加温循环除油—水冲洗—常温循环酸洗钝化—水冲洗—钝化膜检验—设备复位。
(3)大型设备表面清洗钝化采用涂刷酸洗钝化膏的方法进行,如大型容器内外表面、塔器外壁、大口径管道外表面、板材表面等。
此方法优点是用料节省,成本低廉,操作工艺简单,适合于维修和安装现场,施工灵活;缺点是钝化效果不均匀,需要手工操作,劳动环境差,施工安全性差。
其工艺流程为:表面擦洗—涂刷清洗钝化膏—水冲洗—检验。
(4)设备内外表面或局部清洗钝化常采用擦洗法,如设备施焊区、热处理区、局部腐蚀区及外表面等。