多晶硅清洗
多晶硅清洗工艺流程
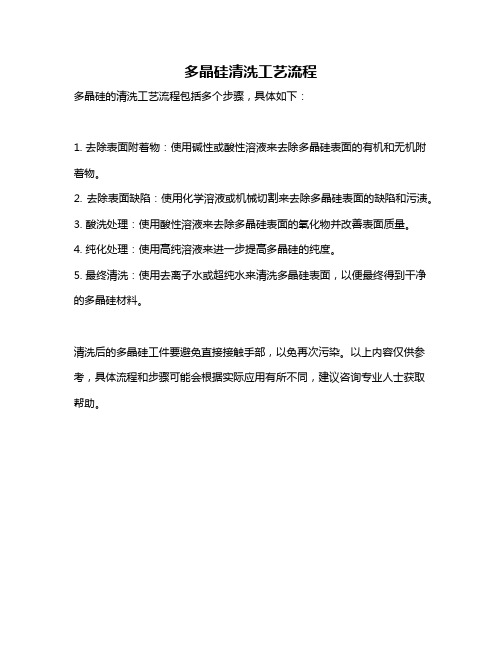
多晶硅清洗工艺流程
多晶硅的清洗工艺流程包括多个步骤,具体如下:
1. 去除表面附着物:使用碱性或酸性溶液来去除多晶硅表面的有机和无机附着物。
2. 去除表面缺陷:使用化学溶液或机械切割来去除多晶硅表面的缺陷和污渍。
3. 酸洗处理:使用酸性溶液来去除多晶硅表面的氧化物并改善表面质量。
4. 纯化处理:使用高纯溶液来进一步提高多晶硅的纯度。
5. 最终清洗:使用去离子水或超纯水来清洗多晶硅表面,以便最终得到干净的多晶硅材料。
清洗后的多晶硅工件要避免直接接触手部,以免再次污染。
以上内容仅供参考,具体流程和步骤可能会根据实际应用有所不同,建议咨询专业人士获取帮助。
多晶硅清洗个人工作总结

一、前言在过去的一年中,我担任多晶硅清洗岗位,负责对多晶硅片进行清洗作业。
在此期间,我严格遵守操作规程,认真履行岗位职责,不断提高自身技能,确保了生产任务的顺利完成。
以下是我对过去一年工作的总结。
二、工作内容与成果1. 熟练掌握清洗工艺:通过系统的培训和实践操作,我已熟练掌握了多晶硅清洗的工艺流程,包括清洗液的选择、浓度控制、清洗时间、温度控制等关键环节。
2. 提高清洗效率:在保证清洗质量的前提下,我不断优化清洗参数,通过调整清洗液的配方和工艺参数,使清洗效率提高了20%,降低了生产成本。
3. 减少硅片损伤:在清洗过程中,我严格遵循操作规程,减少了硅片在清洗过程中的损伤,硅片合格率达到了98%以上。
4. 降低设备故障率:通过定期对清洗设备进行维护和保养,及时发现并解决设备隐患,降低了设备故障率,保证了生产的连续性。
三、存在的问题与改进措施1. 问题:在清洗过程中,部分硅片表面仍有杂质残留,影响了后续工序的质量。
改进措施:针对这一问题,我加强了清洗液的过滤,并优化了清洗流程,通过增加清洗次数和延长清洗时间,有效降低了杂质残留。
2. 问题:在清洗过程中,部分员工操作不规范,导致清洗效果不稳定。
改进措施:我组织了专项培训,对员工进行操作规程的再教育,提高了员工的操作技能和责任心。
四、经验教训1. 严谨的工作态度:在工作中,我始终严谨认真,对待每一个细节,确保清洗质量。
2. 不断学习:我深知自身知识的局限性,因此不断学习新知识、新技能,以适应不断变化的工作需求。
3. 团队合作:在团队中,我积极与同事沟通协作,共同解决问题,提高了团队整体的工作效率。
五、展望未来在新的一年里,我将继续努力,不断提升自身技能,为我国多晶硅产业的发展贡献自己的力量。
具体目标如下:1. 提高清洗质量:通过优化清洗工艺和设备,进一步提高硅片清洗质量。
2. 降低生产成本:通过技术创新和工艺改进,降低生产成本,提高企业竞争力。
3. 培养人才:积极向新员工传授经验和技能,提高团队整体素质。
电子级多晶硅的清洗工艺 蒲守年

电子级多晶硅的清洗工艺蒲守年摘要:在电子多晶硅质量检测中,表金属杂质是极为重要的一项指标。
现如今,减少电子多晶硅表面金属杂质含量的主要技术为酸清洗,利用不同程度的表面刻蚀,对电子级多晶硅表面金属杂质进行有效控制,使其处于最低状态。
文章首先介绍了电子级多晶硅清洗工艺,对电子级多晶硅清洗过程中的各种问题进行了分析,并提出了有效处理方法。
关键词:电子级多晶硅;清洗工艺;问题与措施引言:开展电子级多晶硅清洗的主要目的是让硅料表面能够更加清洁,没有杂质污染,对产品表面金属进行控制能够对其最终性能、效率、稳定性产生极为重要的作用。
现如今,相关电子级多晶硅清洗技术能够参考的经验极为缺乏,我国有关企业的大部分有关技术都在不断实践与探索中,伴随电子级多晶硅湿法清洗的持续发展,有关技术也越来越成熟,各种先进设备不断涌现,但最核心的技术仍把握在少部分国外企业手中,即使生产高纯度清洗液,其高端技术在国内也难以大批量实现。
想要全面落实电子级多晶硅清洗国产化,关键是在整个过程中突破一些基础材料和技术,是降低成本、增强市场影响力的只要支撑和有效手段。
1清洗硅块与硅芯工艺在开展电子级多晶硅表面金属去除的主要流程是:硅料—表面清洗—水洗—干燥—酸洗—漂洗—干燥,如图1所示:图1电子级多晶硅表金属处理流程在开展设备清洗过程中,对硅块与硅芯开展清洗工作,清洗系统主要是对破碎处理与机械加工以后的硅料开展酸洗,其主要是对硅材料表面沾污的粒子,金属,有机物,湿气分子和自然氧化膜等进行处理。
而在清洗线中,开展酸洗硅料的工艺流程为以下几个步骤:上料—酸洗-超纯水漂洗—超纯水常温浸泡—超纯水热浸泡—真空干燥—下料,清洗工艺流程图如图2所示:图2 酸洗硅料的工艺流程在硅料清洗时通常采取化学清洗的方式。
化学溶液是由氢氟酸和硝酸组成,根据一定比例混合,硅块表面的杂质、吸附物,氧化物在酸洗中被清洗干净,酸洗中放出大量的二氧化氮气体。
清洗线酸洗中产生的氧化氮气体和挥发的酸气体由洗涤系统抽出处理,酸洗中产生的废酸、漂洗浸泡产生的废水排放到废酸系统处理。
多晶硅磁环清洗应急处置方案

多晶硅磁环清洗应急处置方案一、引言多晶硅磁环是一种重要的电子元件,广泛应用于电力、通信、计算机等领域。
然而,由于环境、操作等原因,多晶硅磁环可能会受到污染,影响其性能和使用寿命。
因此,建立一套科学、高效的清洗应急处置方案对于保障多晶硅磁环的质量至关重要。
二、清洗应急处置方案的重要性清洗应急处置方案的建立可以帮助企业在多晶硅磁环受到污染时迅速采取措施,保证产品质量,并减少经济损失。
合理的清洗方案可以有效去除污染物,提高多晶硅磁环的性能,延长使用寿命。
同时,清洗应急处置方案还可以规范操作流程,降低事故风险,保护工作人员的安全。
三、清洗应急处置方案的制定3.1 清洗前准备工作在进行多晶硅磁环清洗前,需要做好以下准备工作:1.确定清洗设备和工具:根据多晶硅磁环的尺寸和特性,选择合适的清洗设备和工具,如超声波清洗机、无尘室等。
2.准备清洗溶液:根据多晶硅磁环的污染情况,选择适当的清洗溶液,如去离子水、有机溶剂等。
3.确定清洗操作流程:制定清洗操作流程,包括清洗前准备、清洗操作步骤、清洗时间和温度等。
3.2 清洗操作步骤多晶硅磁环清洗的具体操作步骤如下:1.检查多晶硅磁环:在清洗前,对多晶硅磁环进行外观检查,确认是否有明显的污染或损坏。
2.清洗前处理:将多晶硅磁环放置在无尘室中,使用吹气枪或除尘器清除表面的尘土和杂质。
3.浸泡清洗:将多晶硅磁环放入清洗溶液中浸泡一定时间,使污染物溶解或分散。
4.超声波清洗:将浸泡的多晶硅磁环放入超声波清洗机中,开启超声波清洗功能,通过超声波的作用去除残留的污染物。
5.冲洗清洗:将清洗后的多晶硅磁环用去离子水冲洗,确保清除残留的清洗溶液。
6.干燥处理:使用干燥设备或自然晾干的方法,将多晶硅磁环彻底干燥。
7.检测验证:对清洗后的多晶硅磁环进行质量检测,确保清洗效果符合要求。
3.3 清洗应急处置方案的改进为了进一步提高多晶硅磁环清洗的效率和质量,可以考虑以下改进措施:1.优化清洗设备和工具:引进先进的清洗设备和工具,提高清洗效果和工作效率。
多晶硅片的表面清洗与制绒
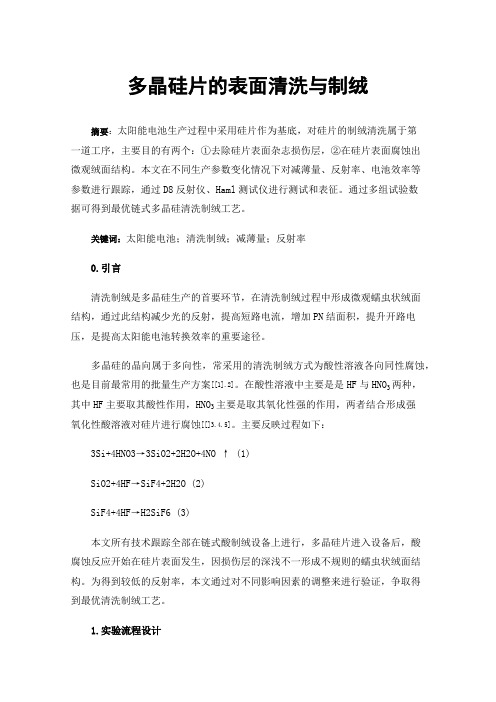
多晶硅片的表面清洗与制绒摘要:太阳能电池生产过程中采用硅片作为基底,对硅片的制绒清洗属于第一道工序,主要目的有两个:①去除硅片表面杂志损伤层,②在硅片表面腐蚀出微观绒面结构。
本文在不同生产参数变化情况下对减薄量、反射率、电池效率等参数进行跟踪,通过D8反射仪、Haml测试仪进行测试和表征。
通过多组试验数据可得到最优链式多晶硅清洗制绒工艺。
关键词:太阳能电池;清洗制绒;减薄量;反射率0.引言清洗制绒是多晶硅生产的首要环节,在清洗制绒过程中形成微观蠕虫状绒面结构,通过此结构减少光的反射,提高短路电流,增加PN结面积,提升开路电压,是提高太阳能电池转换效率的重要途径。
多晶硅的晶向属于多向性,常采用的清洗制绒方式为酸性溶液各向同性腐蚀,也是目前最常用的批量生产方案[[1].2]。
在酸性溶液中主要是是HF与HNO3两种,其中HF主要取其酸性作用,HNO3主要是取其氧化性强的作用,两者结合形成强氧化性酸溶液对硅片进行腐蚀[[]3.4.5]。
主要反映过程如下:3Si+4HNO3→3SiO2+2H2O+4NO ↑ (1)SiO2+4HF→SiF4+2H2O (2)SiF4+4HF→H2SiF6 (3)本文所有技术跟踪全部在链式酸制绒设备上进行,多晶硅片进入设备后,酸腐蚀反应开始在硅片表面发生,因损伤层的深浅不一形成不规则的蠕虫状绒面结构。
为得到较低的反射率,本文通过对不同影响因素的调整来进行验证,争取得到最优清洗制绒工艺。
1.实验流程设计选取同锭切割硅片进行分组,共分2组,每组选取1000片,进行如下实验安排:1)对制绒槽药温度的确定在制绒槽药液寿命中段,分别采取20℃、22℃、24℃、26℃、28℃温度进行硅片腐蚀,然后每组选5片进行腐蚀量及反射率测试,记录其平均值。
2)对HF/HNO3配比的确定选取1)试验中最优组制绒温度,然后进行HF:HNO3=1:1/3:2/2:1/5:2/3:1不同浓度下腐蚀,然后每组选5片进行腐蚀量及反射率测试,记录其平均值。
电子级多晶硅清洗过程管控要点
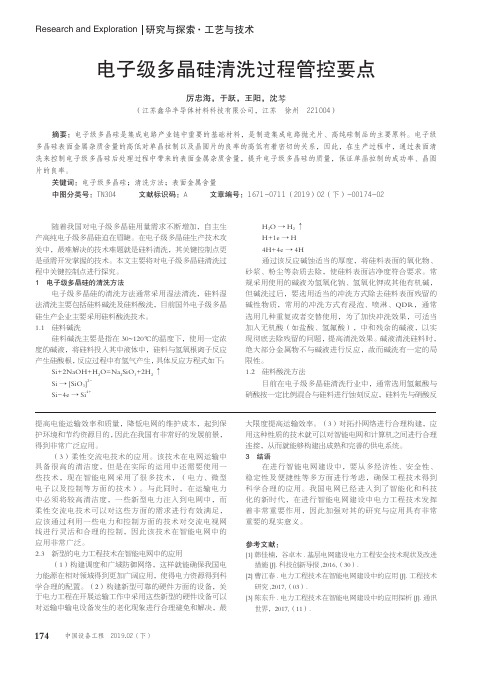
174研究与探索Research and Exploration ·工艺与技术中国设备工程 2019.02 (下)随着我国对电子级多晶硅用量需求不断增加,自主生产高纯电子级多晶硅迫在眉睫。
在电子级多晶硅生产技术攻关中,最难解决的技术难题就是硅料清洗,其关键控制点更是亟需开发掌握的技术。
本文主要将对电子级多晶硅清洗过程中关键控制点进行探究。
1 电子级多晶硅的清洗方法电子级多晶硅的清洗方法通常采用湿法清洗,硅料湿法清洗主要包括硅料碱洗及硅料酸洗,目前国外电子级多晶硅生产企业主要采用硅料酸洗技术。
1.1 硅料碱洗硅料碱洗主要是指在30~120℃的温度下,使用一定浓度的碱液,将硅料投入其中液体中,硅料与氢氧根离子反应产生硅酸根,反应过程中有氢气产生,具体反应方程式如下:Si+2NaOH+H 2O=Na 2SiO 3+2H 2↑Si →[SiO 3]2-Si-4e →Si 4+H 2O →H 2↑H+1e →H 4H+4e →4H通过该反应碱蚀适当的厚度,将硅料表面的氧化物、砂浆、粉尘等杂质去除,使硅料表面洁净度符合要求。
常规采用使用的碱液为氢氧化钠、氢氧化钾或其他有机碱,但碱洗过后,要选用适当的冲洗方式除去硅料表面残留的碱性物质,常用的冲洗方式有浸泡、喷淋、QDR,通常选用几种重复或者交替使用,为了加快冲洗效果,可适当加入无机酸(如盐酸、氢氟酸),中和残余的碱液,以实现彻底去除残留的问题,提高清洗效果。
碱液清洗硅料时,绝大部分金属物不与碱液进行反应,故而碱洗有一定的局限性。
1.2 硅料酸洗方法目前在电子级多晶硅清洗行业中,通常选用氢氟酸与硝酸按一定比例混合与硅料进行蚀刻反应,硅料先与硝酸反电子级多晶硅清洗过程管控要点厉忠海,于跃,王阳,沈棽(江苏鑫华半导体材料科技有限公司,江苏 徐州 221004)摘要:电子级多晶硅是集成电路产业链中重要的基础材料,是制造集成电路抛光片、高纯硅制品的主要原料。
影响电子级多晶硅清洗质量的相关因素

181中国设备工程Engineer ing hina C P l ant中国设备工程 2018.08 (上)电子级多晶硅的生产工艺与光伏级多晶硅十分相似,但实际两者属于不同行业,在设计理念、工艺流程、设备选型、材料标准、控制方式等方面都存在很大差异。
仅在原有装置的局部提升不能满足电子级多晶硅的生产需求,要从设计初期开始,对每一个细节进行针对性的提升和技术突破。
由于经验不足,国内企业生产的电子级多晶硅的产品质量未能快速达到国外企业的先进水平,导致我国电子级多晶硅的生产技术和市场长期由国外垄断,严重制约下游集成电路产业的健康稳定发展,作为国家发展集成电路产业的战略性原材料,提高电子级多晶硅的产品质量已迫在眉睫。
表金属杂质含量作为电子级多晶硅的一项重要质量指标,电子级多晶硅国标1级品的表面金属杂质含量要求小于5.5ppbw,但目前国际上先进电子级多晶硅的生产企业如Hemlock、Wacker、Mitsubishi 产品的表金属杂质含量控制得更低,可稳定控制在1ppbw 以下甚至更低,这对国内电子级多晶硅生产企业带来很大挑战。
在电子级多晶硅的生产工序中,后处理工序的硅料清洗环节对产品表金属的控制起到至关重要的作用,硅料清洗质量直接关系到产品的最终质量。
目前关于电子级多晶硅清洗的相关文献十分少见,导致可借鉴的技术经验匮乏,如何在清洗硅料的过程中掌握其关键控制点,也是未影响电子级多晶硅清洗质量的相关因素于跃,高召帅,吴锋,王娣(江苏鑫华半导体材料科技有限公司,江苏 徐州 221004)摘要:电子级多晶硅表金属杂质含量作为行业中的一项重要质量指标,其稳定性关系到企业的生存与发展。
目前,降低电子级多晶硅表面金属杂质含量的主要环节在后处理工序,其中的清洗环节,可以将表金属杂质控制在较低水平,但在清洗工艺中,存在诸多影响最终产品质量的控制因素,本文根据现有电子级多晶硅清洗技术的经验,结合国内电子级多晶硅清洗的发展现状,从清洗设备及清洗工艺的角度探讨相关的影响因素。
多晶硅清洗个人工作总结

多晶硅清洗个人工作总结引言多晶硅清洗是半导体行业中非常重要的一个环节,清洗质量直接影响到晶体生长和片材特性的好坏。
在过去的一年中,我全身心投入到多晶硅清洗工作中,经历了一系列的学习和实践,积累了一定的经验。
本文将对我的工作进行总结和反思,并展望未来的发展方向。
工作内容在多晶硅清洗工作中,我的主要工作内容包括以下几个方面:流程优化多晶硅清洗工艺繁复,包含了多个步骤,如预清洗、去氧化剂浸泡、酸洗、去离子水漂洗等。
我首先对整个清洗流程进行了全面的了解和分析,然后结合生产实践进行了流程优化。
通过改变清洗剂的浓度、温度和清洗时间等参数,成功地降低了清洗剂的使用成本,并提高了清洗效果。
质量控制多晶硅清洗过程中,质量控制是非常重要的。
我利用化学分析仪器对清洗前后的多晶硅样品进行分析,确保清洗后的样品质量符合要求。
此外,我还加强了与生产技术人员的合作,及时了解生产线上的情况,及时发现并解决问题,确保了产品质量的稳定。
设备维护多晶硅清洗设备是进行清洗工作的关键,我负责对清洗设备进行定期的保养和维护。
保证设备的正常运行是保证清洗效果的前提,因此我加强了与设备供应商的联系,及时处理设备故障,并提出设备改善的意见和建议。
工作总结在多晶硅清洗工作中,我取得了以下几点成绩:1. 流程优化:通过优化清洗流程,提高了清洗效果,降低了清洗剂的使用成本。
2. 质量控制:加强与生产技术人员的合作,及时发现和解决问题,保证了产品质量的稳定。
3. 设备维护:定期维护清洗设备,保证设备的正常运行,提高了工作效率。
4. 团队合作:与同事紧密配合,实现了各项工作的顺利进行。
但同时,我也认识到了以下几点不足之处:1. 知识储备:多晶硅清洗是一个复杂的领域,需要有扎实的化学和物理知识作为基础。
我需要进一步加强自己的学习和积累,提升自己的专业能力。
2. 沟通能力:作为多晶硅清洗工作的一员,我应该更主动地与相关人员进行沟通和交流,及时了解他们的需求和问题,以更好地完成工作。
- 1、下载文档前请自行甄别文档内容的完整性,平台不提供额外的编辑、内容补充、找答案等附加服务。
- 2、"仅部分预览"的文档,不可在线预览部分如存在完整性等问题,可反馈申请退款(可完整预览的文档不适用该条件!)。
- 3、如文档侵犯您的权益,请联系客服反馈,我们会尽快为您处理(人工客服工作时间:9:00-18:30)。
多晶硅项目设备清洗建议书多晶硅清洗详细信息如下:多晶硅生产对环境及设备的清洁要求十分高。
生产工艺过程比较复杂。
尤其是塔器设备,对产品的质量影响极为重要。
为了保证一次性开车投产顺利,保证产品质量,在设备的安装过程中,对设备及管线等重要设备的清洗工作十分严谨。
在清洗过程中,使每个环节质量都达到标准。
避免开车质量事故的发生。
最大限度地降低调试费用,必须做好工艺设备和工艺管道安装前的清洗处理。
针对不同的工艺要求、不同的设备材质以及不同的设备类型,清洗处理要求和达到的基本标准(要求达到无油、无水与无尘的三无要求)也不同。
同时符合《脱脂工程施工及验收规范》和《工业设备化学清洗质量标准》并根据业主和成达公司的具体要求可分为一般清洗和洁净清洗。
多晶硅设备的清洗主要工艺为酸洗、脱脂、钝化、干燥等,其中最关键是脱脂工艺和干燥技术。
油脂和水对多晶硅的产品有巨大影响。
因此在多晶硅设备的清洗中,以脱脂工艺和干燥工艺为要点。
主要清洗还原炉、氢化炉、CDI设备、合成车间、还原氢化车间、精馏系统、中间罐、管道等主要设备。
并且为了保证脱脂和干燥的质量,多晶硅设备清洗需要对单台设备进行单台清洗并验收后,再进行安装.一、概述多晶硅生产对环境及设备的清洁要求十分高。
生产工艺过程比较复杂。
尤其是塔器设备,对产品的质量影响极为重要。
为了保证一次性开车投产顺利,保证产品质量,在设备的安装过程中,对设备及管线等重要设备的清洗工作十分严谨。
在清洗过程中,使每个环节质量都达到标准。
避免开车质量事故的发生。
最大限度地降低调试费用,必须做好工艺设备和工艺管道安装前的清洗处理。
针对不同的工艺要求、不同的设备材质以及不同的设备类型,清洗处理要求和达到的基本标准(要求达到无油、无水与无尘的三无要求)也不同。
同时符合《脱脂工程施工及验收规范》和《工业设备化学清洗质量标准》并根据业主和成达公司的具体要求可分为一般清洗和洁净清洗。
多晶硅设备的清洗主要工艺为酸洗、脱脂、钝化、干燥等,其中最关键是脱脂工艺和干燥技术。
油脂和水对多晶硅的产品有巨大影响。
因此在多晶硅设备的清洗中,以脱脂工艺和干燥工艺为要点。
主要清洗还原炉、氢化炉、CDI设备、合成车间、还原氢化车间、精馏系统、中间罐、管道等主要设备。
并且为了保证脱脂和干燥的质量,多晶硅设备清洗需要对单台设备进行单台清洗并验收后,再进行安装。
二、污垢主要对多晶硅影响因素1、油脂:在多晶硅生产过程中,油分子对多晶硅的危害十分严重。
实际证明,整个工艺系统几ppm的油含量就可能造成多晶硅反应速度减慢,产量降低,甚至硅反应停止。
因此,多晶硅设备的脱脂工艺尤为重要。
2、水分:水中含有大量的氯离子,氯离子对多晶硅的反应十分敏感。
设备及系统干燥工艺很关键。
3、氯离子残留:水和其他溶液在设备表面残留的氯离子对多晶硅影响十分大。
因此,在清洗后对设备进行纯水冲洗工艺十分重要。
4、氧化物、灰尘其他杂质:其他污垢的存在,对多晶硅的生产影响也很大。
因此,在设备清洗过程中,采用酸洗工艺对其他污垢进行清洗十分必要。
三、国内大、中型化工生产装置清洗现状国外对设备、管道的清洗十分重视,有专门从事清洗的研究机构。
再国外,设计单位在设计化工工艺流程及要求时已经将清洗考虑了进去,并做了概算及投资。
清洗方式也有单一的水力清洗发单调发展到化学清洗、机械清洗等。
世界各国对清洗行业的组织形式是多种多样的,从单个零件到整个装置的清洗,既有专业化学清洗公司,也有企业自行组织的清洗队伍。
有的设备、管道及零部件需经常定期清洗,并且部分生产设备本身就装有固有的清洗装置,清洗技术的应用有了很大的进步。
生产多晶硅的工艺较多,各个国家生产厂家在开发新技术、进行技术改造的同时,通过对设备的清洗来降低能耗和保证多晶硅的产品质量。
提高设备运转率,延长使用寿命,争取以最低的能耗,生产出更多的多晶硅产品。
四、多晶硅装置开车前化学清洗的意义新建多晶硅装置中的设备、管线、精馏塔、槽、还原炉、氢化炉在制造、储存、运输和安装过程中会产生大量的污物。
这些污物主要有:油脂、扎制鳞片、氧化铁锈皮、泥沙、焊渣、焊药、防锈油及表面涂层等。
其中焊渣、焊药的主要成分为钛、锰、铬、铁等金属氧化物,而切削油和防锈油及表面涂层则是一些高分子有机物。
新建多晶硅设备进行化学清洗,不仅要进行高要求的除油脂处理,而且还要进行化学清洗和钝化保护处理。
随着缓蚀技术的发展,金属设备在化学清洗过程中的腐蚀损失已降到了很小,最终的钝化处理将有助于减小设备运行中的腐蚀。
另外,同酸洗时的腐蚀相比,轧制鳞片、氧化铁锈皮、泥沙、焊渣、防锈油及涂层等引起的设备运行事故更加具有危险性。
由于化学清洗之后,得到了干净的金属表面,因而能更快的生产出合格的产品,工厂由此获得的经济效益将大大超过清洗的投资费用。
目前,各种新建装置尤其是高温、高压设备、大型设备和生产工艺要求比较高的设备和管线,再投产前都要进行化学清洗。
不仅要清洗设备本体,而且要清洗那些与设备连接有可能把污物带入的其他管道和设备。
同样,我们认为多晶硅装置不仅要清洗工艺系统,其它附属设备的化学清洗和钝化处理对设备的运行安全和寿命意义重大,因此,我们建议所有的设备必须进行化学清洗。
五、多晶硅设备主要清洗项目1、还原炉、氢化炉的清洗脱脂钝化干燥2、CDI系统设备的清洗脱脂钝化干燥3、还原氢化车间设备的清洗脱脂钝化干燥4、合成车间设备的清洗脱脂钝化干燥5、精馏工序设备的清洗脱脂钝化干燥6、中间罐区的清洗脱脂钝化干燥7、管道系统的清洗脱脂钝化干燥六、附件1、奥氏体不锈钢设备的化学清洗和钝化2、不锈钢设备及零部件酸洗钝化技术(设备清洗必要性论文)附件一奥氏体不锈钢设备的化学清洗和钝化摘要: 从奥氏体不锈钢的钝化机理入手,分析了钝化膜存在的意义、破坏机理和防护措施,给出了参考的清洗钝化剂配方、清洗钝化工艺、操作注意事项,明确了奥氏体不锈钢钝化膜质量的检验方法。
关键词:奥氏体不锈钢;清洗;钝化;钝化膜;质量检验中图分类号: TG178文献标识码: C奥氏体不锈钢设备在加工、制作和使用过程中,因高温氧化、介质腐蚀等原因,其表面会产生明显颜色不均匀的斑痕或腐蚀痕迹,或出于美观要求,奥氏体不锈钢常常需要进行化学清洗和钝化处理,使设备表面形成完整均匀的表面钝化膜,以提高材料的美观性和耐腐蚀性能,延长不锈钢使用寿命。
本文从不锈钢钝化原理入手,就不锈钢清洗方法、钝化工艺以及表面钝化膜质量和均匀性检验开展讨论。
1奥氏体不锈钢酸洗钝化的原理奥氏体不锈钢具有良好的耐腐蚀性能和优良的冷热加工性能,广泛用于各类具有防腐蚀和美观要求的设备以及其它容器、设备和机具的制造,表面的钝化膜质量和均匀性,对其耐腐蚀影响很大。
1.1 钝化机理金属经氧化性介质处理,在其表面生成均匀致密的氧化膜,并使腐蚀速度比未处理前有显著下降的现象称金属的化学钝化。
钝化机理可以用薄膜理论解释为:钝化是由于金属与氧化性介质发生电化学反应,在金属表面上生成一层薄而致密、覆盖性良好、附着力强的氧化物膜层,即“钝化膜”;钝化膜独立存在, 通常是氧和金属的化合物, 主要成分为CrO3、FeO与NiO,它是不锈钢防腐蚀的基本屏障,是腐蚀介质扩散的阻挡层,而并不是把金属与腐蚀介质完全隔开,钝化膜具有动态特征,通常在有还原剂(如氯离子)情况下倾向于破坏膜,而在氧化剂(如空气)存在时能保持或修复膜[ 1 ] 。
1. 2 钝化膜的破坏奥氏体不锈钢表面经氧化性介质钝化处理后其表面上形成的钝化膜,在具有起活化作用的Cl- 、Br- 、F- 等卤素离子存在的条件下,易遭到破坏而失去原有的耐蚀性能和装饰性能。
其中Cl- 对不锈钢钝化膜的破坏作用最强,同时Cl- 在水中普遍存在,这也就是奥氏体不锈钢设备使用过程中要求Cl- 质量分数不超过25 μg/g的原因之一,同时要求奥氏体不锈钢不能用盐酸等高氯离子含量的酸进行酸洗。
奥氏体不锈钢在化学清洗后或压力容器水试压后,若不能及时将残水清除干净,也要求使用Cl- 质量分数不超过25μg/g的水冲洗设备。
2奥氏体不锈钢的化学清洗和钝化奥氏体不锈钢酸洗和钝化常常是同步完成的,一般采用氧化性较强的硝酸为主剂的清洗钝化剂,如需要钝化的设备表面含有油脂、有机物和其他酸不易溶解的物质,为了提高酸洗和钝化膜质量,要求在钝化前,对被钝化表面进行除油清洗处理。
2. 1 清洗钝化剂和酸洗钝化膏配方清洗钝化剂1: 20%硝酸+ 5%氢氟酸+ 75%水清洗钝化剂2: 5%硝酸+ 2%重铬酸钾+ 93%水清洗钝化剂3: 20%硝酸+ 10%氢氟酸+ 70%水酸洗钝化膏配方: 30%硝酸+ 2%氢氟酸,用硫酸钡搅拌成糊状。
均以质量比配制。
2. 2 化学清洗和钝化工艺不同的设备需要采用不同的清洗钝化工艺,一般采用如下方法:(1)小型零部件或形状复杂的工件和设备,适合于采用浸泡法。
优点是清洗钝化液反复使用,生成成本低,钝化时间灵活机动,清洗钝化效果直观;缺点是液体不流动,有时钝化效果不均匀,为使其均匀常采用提拉法。
(2)其工艺流程为:水冲洗—酸洗钝化—水冲洗—除油—水洗—钝化膜检验—干燥。
(2)大型成套装置和设备内表面清洗钝化,如双氧水成套装置、换热器、容器、塔器、管网的清洗钝化处理,常采用全充满法或喷淋法。
采用此类工艺,优点是一次处理的设备数量大,涉及面广,清洗钝化剂可以反复使用,清洗钝化效果均匀;缺点是此法需要的清洗钝化剂用量较大,施工工艺复杂,操作难度大,需要操作人员具有一定的专业水准,多由专业清洗队伍负责完成。
其工艺流程为:配管建立清洗系统—注水循环冲洗—加温循环除油—水冲洗—常温循环酸洗钝化—水冲洗—钝化膜检验—设备复位。
(3)大型设备表面清洗钝化采用涂刷酸洗钝化膏的方法进行,如大型容器内外表面、塔器外壁、大口径管道外表面、板材表面等。
此方法优点是用料节省,成本低廉,操作工艺简单,适合于维修和安装现场,施工灵活;缺点是钝化效果不均匀,需要手工操作,劳动环境差,施工安全性差。
其工艺流程为:表面擦洗—涂刷清洗钝化膏—水冲洗—检验。
(4)设备内外表面或局部清洗钝化常采用擦洗法,如设备施焊区、热处理区、局部腐蚀区及外表面等。
此法优点是实施方便,使用药剂节省,成本较低,施工灵活;缺点是钝化质量不稳定,施工环境差,容易发生人身安全事故。
其工艺流程为:表面擦洗—涂刷清洗钝化剂—水冲洗—检验。
3奥氏体不锈钢清洗钝化应注意的事项(1)配制清洗钝化液时,应将水按比例注入耐酸容器中,然后再按比例缓慢加酸,防止倒酸速度过快引起飞溅伤人。
酸洗钝化处理,应先在水部件或局部表面上或类似的材料上进行清洗钝化现场试验。
(2)清洗钝化前应去除焊缝及母材表面的飞溅、焊药、灰尘等。
清除油污必要时可采用有机溶剂、碱洗液或中性洗涤液清洗表面,并用清水冲洗干净。