SAE J400-2002 石击试验标准(免费版)
天然石材耐磨性试验方法比较
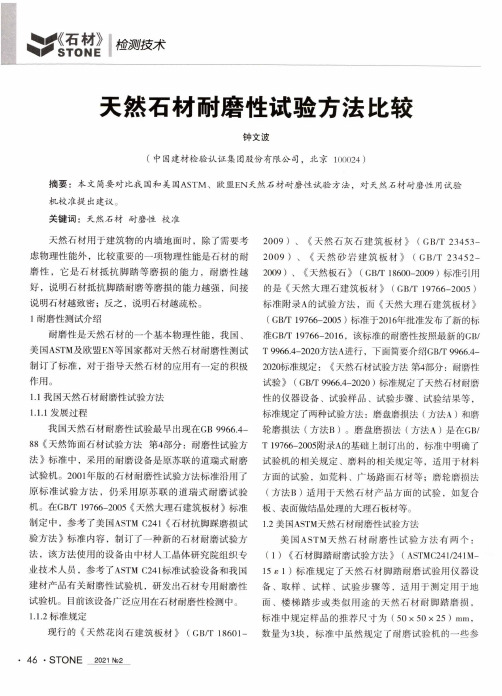
检测技术天然石材耐磨性试验方法比较钟文波(中国建材检验认证集团股份有限公司,北京100024)摘要:本文简要对比我国和美国ASTM、欧盟EN天然石材耐磨性试验方法,对天然石材耐磨性用试验机校准提出建议。
关键词:天然石材耐磨性校准天然石材用于建筑物的内墙地面时,除了需要考 虑物理性能外,比较重要的一项物理性能是石材的耐 磨性,它是石材抵抗脚踏等磨损的能力,耐磨性越 好,说明石材抵抗脚踏耐磨等磨损的能力越强,间接 说明石材越致密;反之,说明石材越疏松。
1耐磨性测试介绍耐磨性是天然石材的一个基本物理性能,我国、美国ASTM及欧盟EN等国家都对天然石材耐磨性测试 制订了标准,对于指导天然石材的应用有一定的积极 作用。
1.1我国天然石材耐磨性试验方法1.1.1发展过程我国天然石材耐磨性试验最早出现在GB 9966.4- 88《天然饰面石材试验方法第4部分:耐磨性试验方 法》标准中,采用的耐磨设备是原苏联的道瑞式耐磨 试验机。
2001年版的石材耐磨性试验方法标准沿用了 原标准试验方法,仍采用原苏联的道瑞式耐磨试验 机。
在GBA1 19766_2〇05《天然大理石建筑板材》标准 制定中,参考了美国ASTM C241《石材抗脚踩磨损试 验方法》标准内容,制订了一种新的石材耐磨试验方 法,该方法使用的设备由中材人工晶体研究院组织专 业技术人员,参考了ASTM C241标准试验设备和我国 建材产品有关耐磨性试验机,研发出石材专用耐磨性 试验机。
目前该设备广泛应用在石材耐磨性检测中。
1.1.2标准规定现行的《天然花岗石建筑板材》(GB/T 18601-2009 )、《天然石灰石建筑板材》(GB/T 23453- 2009 )、《天然砂岩建筑板材》(GB/T 23452- 2009)、《天然板石》(G B A T 18600-2〇09)标准引用 的是《天然大理石建筑板材》(GB/T 19766-2005 )标准附录A的试验方法,而《天然大理石建筑板材》(GB/T 19766-2005 )标准于2016年批准发布了新的标 准GB/T 19766-2016,该标准的耐磨性按照最新的GB/ T9966.4-2020方法A进行,下面简要介绍GB/T9966.4- 2020标准规定:《天然石材试验方法第4部分:耐磨性 试验》(G B A T9966.4-2020)标准规定了天然石材耐磨 性的仪器设备、试验样品、试验步骤、试验结果等,标准规定了两种试验方法:磨盘磨损法(方法A)和磨 轮磨损法(方法B)。
石油天然气工业井下工具封隔器和桥塞

石油天然气工业井下工具封隔器和桥塞1 范围本标准规定了石油天然气工业用封隔器和桥塞的要求。
本标准适用于石油天然气工业中套管和油管内使用的封隔器和桥塞。
2 规范性引用文件下列文件中的条款通过本标准的引用而成为本标准的条款。
对于注明日期的参考文件,只有引用的版本适用。
对于未注明日期的参考文件,最新版本适用于本标准(包括勘误的内容)。
GB/T 18851.2 高压无缝焊接钢管液体渗透试验GB/T 19000质量管理体系基础和术语(GB/T 19000-2008,ISO 9000:2005,IDT)GB/T 19830 石油天然气工业油气井套管或油管用钢管(GB/T 19830 -2011,ISO 11960:2005,IDT)GB/T 230.1 金属材料洛氏硬度试验第1部分:试验方法(范围包括A-K,N,T)GB/T 231.1 金属材料布氏硬度试验第1部分:试验方法GB/T 27025 检测和校准实验室能力的一般要求GB/T 2828.1 计数抽样检验程序第1部分:按接收质量限(AQL)检索的逐批检验抽样计划(GB/T 2828.1-2003,IS0 2859-1:1999,IDT)GB/T 3452.1 液力系统 O形密封圈第1部分:内径,截面积,公差和尺寸规范(GB/T3452.1-2005,ISO 3601-1:2002,IDT)GB/T 3452.3 液力系统 O形密封圈第3部分:质量检验标准(GB/T3452.3-2005,ISO 3601-3:2002,IDT)GB/T 4340.1,金属材料维氏硬度试验第1部分:试验方法GB/T 531.1硫化橡胶或热塑性橡胶压入硬度试验方法第1部分:邵氏硬度计GB/T 531.2 硫化橡胶或热塑性橡胶压入硬度试验方法第2部分:便携式橡胶GB/T 9445 无损检测人员资格鉴定与认证(GB/T 9445—2008,ISO 9712:2005,IDT)JB/T 4730 承压设备无损检测ASME 锅炉及压力容器第5部分:无损检测(Boiler and Pressure Vessel Code, Section V, Nondestructive Examination)ASME 锅炉及压力容器第9部分:焊接质量要求(Boiler and Pressure Vessel Code, Section IX, Welding and Brazing Qualifications)BS 2M 54,金属热处理温度控制规范(Specification for temperature control in the heat treatment of metals)SAE AMS-H-6875A,钢材的热处理(Heat Treatment of Steel Raw Materials)3 术语和定义GB/T 19000 界定的以及下列术语和定义适用于本文件。
GMW14700-CHINESE

GMW14700覆盖层碎石冲击性能1 范围注:本标准不能取代适用的法律和规章,除非已经取得了特定的许可。
注:如果出现英文版与国内语言冲突时,优先考虑英文版。
本标准描述的测试步骤用于评价覆盖层的碎石冲击性能。
方法A是将碎石冲击仪置于恒温的冰库中,方法B是将测试样板从冰箱中取出放入到处于室温下的碎石冲击仪中,而方法C是将碎石冲击仪置于一个恒温的房间内。
2 参考注:仅仅最新的认可标准是适用的,除非特别指定。
2.1 外部标准/规范SAE J4002.2 GM标准/规范无2.3 其他参考零件号,GME:92740433 测试仪器3.1 碎石冲击仪一种碎石发射仪器,在SAE J400中通过设计说明书描述了它的构造。
(满足本标准的相似类型商业仪器能够在下面列出的厂家得到:the Q-Panel Col. 800 Canterbury Rd., Cleveland, OH 44145; German representation: Pausch Meßtechnik GmbH, Nordstraße 32, 42781 Haan); Q-Panel Europe, Express Trading Estate, Farnsworth, Bolton, BL49TP England; Q-Panel China, RM1809/1810, Liangyou Building, 618 SHabgcheng Road, Pudong District, Shanghai, 200120 China.3.2 碎石-水-浸蚀冲击碎石大小至8到16mm。
重新使用碎石之前,移除小的碎块是很重要的。
(满足本标准的碎石能从下面列出的厂家获得:the Q-Panel Col. 800 Canterbury Rd., Cleveland, OH 44145.); German representation: Pausch Meßtechnik GmbH, Nordstraße 32, 42781 Haan)。
SAE标准中文版 - 美国汽车工程师协会标准中文版目录

SAE标准中文版 - 美国汽车工程师协会标准中文版目录SAE标准中文版美国汽车工程师协会标准中文版SAE标准中文版美国汽车工程师协会标准中文版目录代号名称1. SAE TSB002-1992 SAE技术报告的准备2. SAE TSB003-1999 SAE使用公制( Metric)单位的规则3. SAE TSB004-1998 技术委员会指南4. SAE J 10-2000 汽车和非道路车辆气制动储气罐性能要求和识别要求5. SAE J 17-2021 天然泡沫橡胶6. SAE J 18-2002 海绵橡胶和多孔橡胶制品7. SAE J 19-1997 汽车用乳胶浸渍制品和涂料8. SAE J 20-2021 冷却系统软管9. SAE J 20-1-2002 冷却软管(政府用于替代 MS52130部分而对 SAE J20进行的增补) 10. SAE J 20-2-2001 钢丝缠绕支撑冷却软管的正常使用( SAE J20的增补件)11. SAE J 30-1998 燃油和机油软管12. SAE J 31-1986 液压式铲车举升能力13. SAE J 33-2000 雪地车定义和术语―总则 14. SAE J 34-2001 机动游艇外部噪声测量规程 15. SAE J 38-1991 装载机举升臂支撑装置16. SAE J 43-1988 工业轮式装载机和铲车轴载荷 17. SAE J 44-2021 雪地车行车制动系统性能要求 18. SAE J 45-2021 雪地车制动系统试验规程 19. SAE J 46-1993 20. SAE J 47-1998 21. SAE J 48-1993 22. SAE J 49-1980车轮打滑制动控制系统道路试验规程摩托车潜在最大噪声声级液面指示器指南液压铲车技术参数的定义23. SAE J 51-1998 汽车空调软管24. SAE J 56-1999 道路车辆―带调节器的交流发电机―试验方法和一般要求 25. SAE J 57-2000 公路载货车轮胎噪声声级 26. SAE J 58-1998 带凸缘的 12角头螺钉27. SAE J 64-1995 雪地车识别代号28. SAE J 67-1998 铲斗,抓斗和挖斗额定容量 29. SAE J 68-1991 雪地车开关装置和部件试验 30. SAE J 75-1999 机动车制动液容器兼容性 31. SAE J 78-1998 钢制自攻螺钉 32. SAE J 79 制动盘和制动鼓热电偶安装 33. SAE J 80-1997 汽车用橡胶垫 34. SAE J 81-1997 滚丝螺钉35. SAE J 82-1998 机制螺钉机械和质量要求36. SAE J 88-1995 非道路工作机械外部噪声测量 37. SAE J 89-1995 雪地车坐椅动态缓冲性能标准38. SAE J 90-1995 汽车非金属垫圈材料标准分类体系 39. SAE J 92-1995 雪地车节气门控制系统 40. SAE J 95-1986 工业设备前照灯41. SAE J 96-1986 工业设备闪光警报灯第 1 页共 38 页SAE标准中文版美国汽车工程师协会标准中文版42. SAE J 98-1998 通用工业机械人员防护43. SAE J 99-2021 公路上使用的工业设备灯光和标志 44. SAE J 100-1999 A类车辆风窗玻璃阴影区域 45. SAE J 101-1989 汽车鼓式制动器液力分泵 46. SAE J 107-1996 摩托车操纵件和显示器47. SAE J 108-2000 摩托车制动系统试验代码48. SAE J 109-2000 摩托车和动力驱动自行车行车制动系统性能要求 49. SAE J 112a 电动风窗玻璃刮水器开关 50. SAE J 113 冷拔机械弹簧钢丝和弹簧51. SAE J 114-1994 座椅安全带织带磨损性能要求 52. SAE J 115-2021 安全标志53. SAE J 119-1987 纤维板褶皱弯曲试验54. SAE J 121M-1997 淬硬和回火螺纹紧固件的脱碳 55. SAE J 121-1997 淬硬和回火螺纹紧固件的脱碳56. SAE J 122-1998 螺母表面的不连续性57. SAE J 123-1994 用于疲劳载荷的螺栓,螺钉和双头螺栓的表面不连续性 58. SAE J 125-1988 铸铁温升性能59. SAE J 126-1986 冷、热轧钢板和钢带的选择和说明60. SAE J 128-1994 乘用车和轻型载货车乘员约束系统评价 61. SAE J 129-1981 发动机和传动系识别号码 62. SAE J 131-2021 摩托车转向信号灯63. SAE J 133-2021 商用挂车和半挂车牵引销性能64. SAE J 134-1993 乘用车和轻型载货车与挂车组成的列车制动系统道路试验代码65. SAE J 135-1993 乘用车与挂车组成的列车行车制动系统性能要求 66. SAE J 138 试验人体动力学研究摄影分析指南 67. SAE J 139-1999 点火系统术语68. SAE J 140-1995 座椅安全带硬件试验规程 69. SAE J 141-1995 座椅安全带硬件性能要求 70. SAE J 153-1987 操作人员预防措施 71. SAE J 156-2000 保险丝72. SAE J 159-2002 额定容量系统73. SAE J 160-2001 摩擦材料在暴露在温度升高的环境中时尺寸的稳定性 74. SAE J 163-2001 低压电线和电缆终端接头及铰接夹 75. SAE J 164-1997 散热器盖和加水口颈76. SAE J 167-2002 农用拖拉机顶部防护―试验规程和性能要求 77. SAE J 169-1985 非道路车辆操作人员空间内空调系统的设计指南 78. SAE J 174-1998 英制钢螺纹紧固件力矩 -应力试验规程 79. SAE J 174M-1998 公制钢螺纹紧固件力矩 -应力试验规程 80. SAE J 175-2021 道路车辆车轮冲击试验规程81. SAE J 176-1994 非道路自驱动工作机械快速加油设备 82. SAE J 179-2001 载货车盘式车轮和可拆卸轮辋―表识83. SAE J 180-2002 建筑和工业机械充电系统84. SAE J 182-1997 机动车辆基准标志和三维参考系85. SAE J 183-2002 发动机油性能和发动机维修分类(除节能方面外)第 2 页共 38 页SAE标准中文版美国汽车工程师协会标准中文版86. SAE J 184-1998 噪声数据获得系统的检定 87. SAE J 185-2021 非道路机械的接近系统 88. SAE J 187 载货车识别号码89. SAE J 188-2021 高体积膨胀型动力转向压力软管 90. SAE J 189-1998 低压动力转向回油软管91. SAE J 190-1998 钢丝编织动力转向压力软管92. SAE J 191-2021 低体积膨胀型动力转向压力软管 93. SAE J 192-2021 雪地车外部噪声等级94. SAE J 193-1996 球节及球座总成试验规程 95. SAE J 195-1988 机动车辆自动车速控制器96. SAE J 198-2021 载货车、大客车及多用途车风窗玻璃刮水系统 97. SAE J200-2001 橡胶材料分类体系98. SAE J 201-1997 乘用车和轻型载货车在用制动器性能试验规程 99. SAE J207-1985 汽车金属装饰件和结构件的镀铬和镍 100.101. SAE J 211-1-2021 冲击试验用仪器―第 1部分―电子仪器 102. SAE J 211-2-2001 冲击试验用仪器―第 2部分―摄影仪器 103. SAE J 212-1998 乘用车制动系统测功机试验规程 104. SAE J 213-1997 摩托车分类 105.106. SAE J 216-1999 乘用车玻璃―电路107. SAE J 217-1994 不锈钢 17-7PH弹簧钢丝和弹簧 108. SAE J 218-1981 乘用车识别术语109. SAE J 220-1998 起重机起重臂限位装置 110. SAE J 222-2000 驻车灯(前位置灯)111. SAE J 224-1980 碰撞变形分类112. SAE J 225-2021 商用车制动系统扭矩平衡试验代码 113. SAE J 226-1995 发动机预热器114. SAE J 228-1995 空气流量参考标准115. SAE J 229-1993 乘用车行车制动器结构总成试验规程 116. SAE J 230-1994 不锈钢, SAE 30302,弹簧钢丝和弹簧 117. SAE J 232-1994 工业旋转割草机 118. SAE J 234 电动风窗玻璃清洗器开关 119. SAE J 235 电动鼓风机电机开关120. SAE J 238-1998 螺母和锥形弹簧垫圈总成 121. SAE J 240-2002 汽车蓄电池寿命试验122. SAE J 243 汽车密封胶,粘结剂和缓冲胶剂的试验方法 123. SAE J 244-1992 柴油机进气或排气流量测量 124. SAE J 246-2000 球面和凸缘管接头 125. SAE J247-1987 测量车内噪声脉冲的仪器 126. SAE J 249-1988 机械制动灯开关127. SAE J 250 合成树脂塑料密封胶―不干型 128. SAE J 253-1989 前照灯开关129. SAE J 254-1993 废气排放测量用仪器和测量技术第 3 页共 38 页SAE标准中文版美国汽车工程师协会标准中文版130. SAE J 257-1997 商用车制动器额定功率要求131. SAE J 259 点火开关132. SAE J 264-1998 视野术语133. SAE J 265-2002 柴油机燃油喷嘴总成―8,9,10和 11型 134. SAE J 266-1996 乘用车和轻型载货车稳态方向控制试验规程 135. SAE J 267-1999 车轮/轮辋―载货车―性能要求和试验规程 136. SAE J 268-1989 摩托车后视镜 137. SAE J 272-1981 车辆识别号码体系 138. SAE J 273-1981 乘用车识别号码体系 139. SAE J 274-1989 悬架弹簧额定承载能力 140. SAE J 276-2002 铰接式装载机和拖拉机转向锁 141. SAE J 277-1995 雪地车电气系统设计电压的维持 142. SAE J 278-1995 雪地车制动灯143. SAE J 279-1995 雪地车尾灯(后位置灯)144. SAE J 280-1984 雪地车前照灯145. SAE J 283-1999 带三点式挂接装置的农用拖拉机液压举升能力试验规程 146. SAE J 284-2002 农用、建筑和工业装备安全警报信号 147. SAE J 285-1999 汽油分配泵喷嘴148. SAE J 286-1996 SAE第 2号离合器摩擦试验机械指南 149. SAE J 287-1988驾驶员手控制区域 150. SAE J 288-2002 雪地车燃油箱151. SAE J 291-1980 制动液温度的确定152. SAE J 292-1995 雪地车及车灯、反射装置和相关装备 153. SAE J 293-1995车辆坡道驻车性能要求154. SAE J 294-1993 GVWR大于 4 500公斤( 10 000 lb)车辆的行车制动器总成试验规程 155. SAE J 297-2002 工业装备操作人员控制件 156. SAE J 299-1993 制动距离试验规程157. SAE J 300-1999 发动机机油黏度分级158. SAE J 301-1999 新的或已修订技术报告的有效日期 159. SAE J 304-1999 发动机机油试验160. SAE J 306-1998 汽车齿轮润滑剂黏度分级 161. SAE J 308-1996 轴和手动变速器润滑剂 162. SAE J 310-2000 汽车润滑脂163. SAE J 311-2000 乘用车自动变速器液 164. SAE J 312-2001 车用汽油 165. SAE J 313-1998 柴油166. SAE J 314-2002 毛毡―羊毛和部分羊毛 167. SAE J 315-1985 纤维板试验规程 168. SAE J 318-2021 汽车气制动管接头169. SAE J 321-1999 推土机牵引机械操作人员防护轮罩170. SAE J 322-1996 非金属装饰材料―确定抗硫化氢腐蚀性的试验方法 171. SAE J 323-1998 确定柔性塑料材料冷裂性的试验方法 172. SAE J 326-1986 液压反铲挖掘机术语173. SAE J 328-1994 乘用车及轻型载货车车轮性能要求和试验规程第 4 页共 38 页SAE标准中文版美国汽车工程师协会标准中文版174. SAE J 331-2000 摩托车噪声声级 175. SAE J 332-2002 176. SAE J 335-1995 177. SAE J 336-2001 178. SAE J 339-1994测量乘用车和轻型载货车轮胎一致性的试验机械多位小型发动机排气系统点火抑制载货车驾驶室内部噪声声级座椅安全带织带磨损试验规程179. SAE J 342-1991 大型发动机火花防止器试验规程180. SAE J 343-2001 SAE 100R系列液压软管和软管总成试验和试验规程 181. SAE J 345a 干或湿路面乘用车轮胎最大和抱死时车轮制动力 182. SAE J 347-2002 7型(9.5 mm)柴油机燃油喷嘴总成 183. SAE J 348-1990 车轮三角垫木184. SAE J 349-1991 黑色金属杆,棒,管和丝的表面缺陷检查 185. SAE J 350-1991 中型发动机火花防止器试验规程186. SAE J 356-1999 可以抑制焊瘤的弯曲,双层扩口和卷边正火低碳钢 187. SAE J 357-1999 发动机油的物理和化学特性 188. SAE J 358-1991 非破坏性试验 189. SAE J 359-1991 红外线试验190. SAE J 360-2001 载货车和大客车坡道驻车性能试验规程 191. SAE J 361-1996 汽车内饰件和外饰件视觉评价规程 192. SAE J 363-1994 滤清器座的安装193. SAE J 365-1994 装饰材料抗擦伤性试验方法194. SAE J 366-2001 重型载货车和大客车外部噪声声级195.196. SAE J 369-2021 车辆内部聚合物材料燃烧特性―试验方法 197. SAE J 370-1998 建筑和工业机械用螺栓和内六角螺钉尺寸198. SAE J 371-1993 非道路自驱动工作机械的放油、注油和油位螺塞 199. SAE J 373-1993 单片和双片弹簧加载式离合器壳内尺寸 200. SAE J 374-2002 车顶抗压试验规程201. SAE J 375-1994 负荷半径式悬臂角指示系统 202. SAE J 376-1985 起重机举升负载指示装置 203. SAE J 377-2001 车辆通行声音信号装置 204. SAE J 378-1988 船用发动机布线 205. SAE J 379-1996 制动衬片高氏硬度206. SAE J 380-2002 摩擦材料比重207. SAE J 381-2000 载货车,大客车和多用途车风窗玻璃除雾系统试验规程和性能要求 208. SAE J 383-1995 机动车辆座椅安全带固定点设计建议 209. SAE J 384-1994 机动车辆座椅安全带固定点试验规程 210. SAE J 385-1995 机动车辆座椅安全带固定点性能要求 211. SAE J 386-1997 非道路工作机械操作人员约束系统 212. SAE J 387-1995 机动车辆灯光术语 213. SAE J 390-1999 双向尺寸214. SAE J 391-1981 颗粒物尺寸定义215.216. SAE J 393-2001 商用车辆车轮,轮毂,轮辋术语 217. SAE J 397-1995 防护结构试验室评价―偏转极限值第 5 页共 38 页感谢您的阅读,祝您生活愉快。
机械冲击试验标准

机械冲击试验标准
机械冲击试验标准用于评估产品或材料在冲击负荷下的性能和耐久性。
这些标准通常由国际、国家或行业组织制定,以确保测试的一致性和可比性。
以下是一些常见的机械冲击试验标准,根据您的具体需求,您可能会选择适用的标准:
1.ASTM D5628-18:这是由美国材料和试验协会(ASTM)发布的
标准,用于评估材料的高速撞击性能。
它包括各种不同的试验
方法,以评估材料的抗冲击性。
2.ISO 179-2:这是由国际标准化组织(ISO)发布的标准,用于
测定塑料材料在高速冲击下的韧性。
ISO 179-2定义了冲击强
度的测试程序和规范。
3.ASTM E208-16:这是ASTM发布的金属材料在室温下的冲击测
试标准,包括几种不同的试验方法,如冲击韧性测试。
-STD-810H:这是美国国防标准,用于评估军事设备在各种
环境条件下的性能,包括机械冲击。
它包括多个测试方法,以
评估设备的耐冲击性。
5.IEC 60068-2-27:这是国际电工委员会(IEC)发布的标准,用
于评估电子和电气设备的冲击性能,包括高冲击和低冲击。
6.ANSI/IEEE C62.41.2-2002:这是用于电力系统设备的IEEE标准,
包括各种电气设备的冲击性能评估。
这些标准通常提供了关于试验样品准备、试验条件、测试设备和数据分析的详细指南。
具体选择哪个标准取决于您所测试的材料、产品
或设备类型以及应用领域。
在进行机械冲击试验时,确保按照适用的标准进行测试,以确保结果的可靠性和可比性。
SAE J标准目录中文
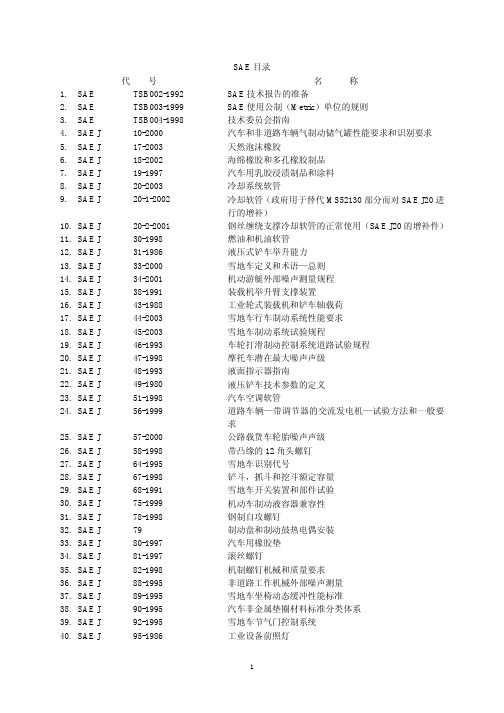
代号 180-2002 182-1997 183-2002 184-1998 185-2003 187 188-2003 189-1998 190-1998 191-2003 192-2003 193-1996 195-1988 198-2003 200-2001 201-1997 207-1985
名
称
机械制动灯开关
合成树脂塑料密封胶—不干型
前照灯开关
废气排放测量用仪器和测量技术
商用车制动器额定功率要求
点火开关
视野术语
柴油机燃油喷嘴总成—8,9,10 和 11 型
乘用车和轻型载货车稳态方向控制试验规程
车轮/轮辋—载货车—性能要求和试验规程
摩托车后视镜
车辆识别号码体系
乘用车识别号码体系
悬架弹簧额定承载能力
技术委员会指南
汽车和非道路车辆气制动储气罐性能要求和识别要求
天然泡沫橡胶
海绵橡胶和多孔橡胶制品
汽车用乳胶浸渍制品和涂料
冷却系统软管
冷却软管(政府用于替代 MS52130 部分而对 SAE J20 进
行的增补)
钢丝缠绕支撑冷却软管的正常使用(SAE J20 的增补件)
燃油和机油软管
液压式铲车举升能力
雪地车定义和术警报灯
通用工业机械人员防护
公路上使用的工业设备灯光和标志
A 类车辆风窗玻璃阴影区域
汽车鼓式制动器液力分泵
摩托车操纵件和显示器
摩托车制动系统试验代码
摩托车和动力驱动自行车行车制动系统性能要求
电动风窗玻璃刮水器开关
冷拔机械弹簧钢丝和弹簧
座椅安全带织带磨损性能要求
安全标志
纤维板褶皱弯曲试验
淬硬和回火螺纹紧固件的脱碳
美国汽车工程学会标准

美国汽车工程学会标准(SAE)目录标准号标准名称SAE J 10-2007汽车和非道路车辆气制动储气罐性能要求和识别要求4SAE J 17-2003 天然泡沫橡胶11SAE J 20-2006 冷却系统软管18SAE J 20-1-2009 冷却软管(政府用于替代MS52130部分内容而对SAE J20进行的增补) 5 SAE J 20-2-2009 冷却软管钢丝缠绕支撑软管的正常使用(政府用于替代MS51008部分内容而对SAE J20进行的增补) 4SAE J 30-2008 燃油和机油软管38SAE J 31-2007 液压式铲车举升能力8SAE J 33-2009雪地车定义和术语总则6SAE J 34-2005 机动游艇外部噪声测量规程6SAE J 38-1991装载机举升臂支撑装置3SAE J 44-2009 雪地车行车制动系统性能要求3SAE J 45-2009 雪地车制动系统试验规程7SAE J 46-1993 车轮打滑制动控制系统道路试验规程12SAE J 47-2005 摩托车可能的最大噪声声级8SAE J 48-2007 液面指示器指南3SAE J 49-1980液压铲车技术参数的定义9SAE J 51-2004 汽车空调软管11SAE J 56-1999道路车辆交流发电机调节器试验方法和性能要求7SAE J 57-2000 公路载货车轮胎噪声声级10SAE J 58-1998 带凸缘的12角头螺钉9SAE J 67-1998铲斗、抓斗和挖斗额定容量5SAE J 68-2004 雪地车开关装置和部件试验5SAE J 75-2006机动车制动液容器兼容性2SAE J 78-1998 钢制自攻螺钉15SAE J 79-1972 制动盘和制动鼓热电偶安装3SAE J 80-2004 汽车用橡胶垫5SAE J 81-1997 滚丝螺钉11SAE J 82-1998 机制螺钉机械和质量要求6SAE J 88-2006 非道路工作机械外部噪声测量11SAE J 89-2007 雪地车坐椅动态缓冲性能标准6SAE J 92-1995 雪地车节气门控制系统6SAE J 95-2007 工业设备前照灯3SAE J 96-2005 工业设备闪光警报灯2SAE J 98-2004 通用工业机械人员防护8SAE J 99-2003 公路上使用的工业设备灯光和标志4SAE J 100-2005 A类车辆风窗玻璃阴影区域4SAE J 101-2006汽车鼓式制动器液力分泵11SAE J 107-1996 摩托车操纵件和显示器4SAE J 108-2007 摩托车制动系统道路试验规程8SAE J 109-2007 摩托车和动力驱动自行车行车制动系统性能要求4SAE J 112a-1977 电动风窗玻璃刮水器开关4SAE J 114-1994 座椅安全带织带磨损性能要求3SAE J 115-2003 安全标志9SAE J 119-2005 纤维板褶皱弯曲试验5SAE J 121-1997 淬硬和回火螺纹紧固件的脱碳5SAE J 121M-1997 淬硬和回火公制螺纹紧固件的脱碳公制5SAE J 122-1998 螺母表面的不连续性11SAE J 123-1994 用于疲劳载荷的螺栓、螺钉和双头螺栓的表面不连续性11SAE J 125-1988 铸铁温升性能11SAE J 126-1986 冷、热轧钢板和钢带的选择和说明12SAE J 128-1994 乘用车和轻型载货车乘员约束系统评价11SAE J 129-1981发动机和传动系识别号码3SAE J 131-2003 摩托车转向信号灯5SAE J 133-2003 商用挂车和半挂车鞍座牵引主销性能4SAE J 134-1993 乘用车和轻型载货车与挂车组成的列车制动系统道路试验代码21 SAE J 135-1993 乘用车与挂车组成的列车行车制动系统性能要求5SAE J 138-1969 试验项目的动力学研究摄影分析指南4SAE J 139-1999 点火系统术语5SAE J 140-1995 座椅安全带硬件试验规程12SAE J 141-1995 座椅安全带硬件性能要求6SAE J 151-2008 冷却系统卸压3SAE J 153-1987 操作人员预防措施5SAE J 156-2005保险丝4SAE J 159-2002 额定容量系统6SAE J 160-2001摩擦材料在暴露在温度升高的环境中时尺寸的稳定性8SAE J 163-2006低压电线和电缆终端接头及铰接夹3SAE J 164-2005散热器盖和加水口颈7SAE J 167-2002 农用拖拉机顶部防护试验规程和性能要求4SAE J 169-1985 非道路车辆操作人员空间内空调系统的设计指南4SAE J 174-1998英制钢螺纹紧固件力矩应力试验规程5SAE J 174M-1998公制钢螺纹紧固件力矩应力试验规程5SAE J 175-2003 道路车辆车轮冲击试验规程3SAE J 176-2006 非道路自驱动作业机械快速加油设备4SAE J 179-2007 载货车盘式车轮和可拆卸轮辋标识4SAE J 180-2002 建筑和工业机械充电系统10SAE J 182-2005 机动车辆基准标志和三维坐标系2SAE J 183-2006发动机油性能和发动机维修分类(除节能方面外) 58SAE J 184-1998 噪声数据获得系统的检定20SAE J 185-2003 非道路机械的出入系统13SAE J 187-1970载货车识别代码3SAE J 188-2003 高体积膨胀型动力转向压力软管5SAE J 189-2003 低压动力转向回油软管5SAE J 190-1998钢丝编织动力转向压力软管5SAE J 191-2003 低体积膨胀型动力转向压力软管6SAE J 193-1996 球节及球座总成试验规程13SAE J 195-1988 机动车辆自动车速控制器3SAE J 198-2003 载货车、大客车及多用途车风窗玻璃刮水系统14 SAE J 200-2008 橡胶材料分类体系62SAE J 201-1997 乘用车和轻型载货车在用制动器性能试验规程6 SAE J 207-1985 汽车金属装饰件和结构件的镀铬和镍18SAE J 211-1-2007 冲击试验用仪器第1部分:电子仪器26SAE J 211-2-2008 冲击试验用仪器第2部分:摄影仪器10SAE J 213-2004 摩托车分类4SAE J 216-1999 乘用车玻璃电路4SAE J 217-1994 不锈钢177PH弹簧钢丝和弹簧3SAE J 218-1981 乘用车识别术语4SAE J 220-1998 起重机起重臂限位装置3SAE J 222-2006 驻车灯(前位置灯) 7SAE J 224-1980 碰撞变形分类26SAE J 225-2003 商用车制动系统扭矩平衡试验代码9SAE J 226-1995 发动机预热器6SAE J 228-1995 空气流量参考标准6SAE J 229-1993 乘用车行车制动器结构总成试验规程5SAE J 230-1994 不锈钢、SAE 30302、弹簧钢丝和弹簧6SAE J 232-2009 工业旋转割草机22SAE J 234-1977 电动风窗玻璃清洗器开关3SAE J 235-1971 电动鼓风机电机开关3SAE J 238-1998螺母和锥形弹簧垫圈总成6SAE J 240-2007汽车蓄电池寿命试验3SAE J 243-1971 汽车密封胶、粘结剂和缓冲胶剂的试验方法30 SAE J 244-1992柴油机进气或排气流量测量8SAE J 246-2000 球面和凸缘管接头23SAE J 247-1987 测量车内噪声脉冲的仪器7SAE J 249-1988 机械制动灯开关24SAE J 250-1959 合成树脂塑料密封胶不干型4SAE J 253-1989 前照灯开关26SAE J 254-1993 废气排放测量用仪器和测量技术20SAE J 257-1997 商用车制动器额定功率要求7SAE J 259-1971 点火开关12SAE J 264-2004 视野术语19SAE J 265-2002 柴油机燃油喷嘴总成8、9、10和11型36SAE J 266-1996 乘用车和轻型载货车稳态方向控制试验规程32 SAE J 267-2007 车轮/轮辋载货车性能要求和试验规程9 SAE J 268-2004 摩托车后视镜3SAE J 272-2008车辆识别代号6SAE J 277-2004 雪地车电气系统设计电压的维护4SAE J 278-2006 雪地车制动灯5SAE J 280-2006 雪地车前照灯4SAE J 283-2009 带三点式挂接装置的农用拖拉机液压举升能力试验规程6SAE J 284-2002 农用、建筑和工业装备安全警报信号3SAE J 285-2007 汽油分配泵喷嘴7SAE J 286-2006 SAE第2号离合器摩擦试验机械指南7SAE J 287-2007 驾驶员手控制区域30SAE J 288-2008 雪地车燃油箱3SAE J 291-1980 制动液温度的确定3SAE J 292-2008 雪地车及车灯、反射装置和相关装备4SAE J 293-2004 车辆坡道驻车性能要求3SAE J 294-2004 GVWR大于4500kg(10000 lb)车辆的行车制动器总成试验规程9 SAE J 297-2002 工业装备操作人员控制件4SAE J 299-2009 制动距离试验规程3SAE J 300-2009 发动机机油黏度分级9SAE J 301-2006 新的或已修订技术报告的有效日期1SAE J 304-2007 发动机机油试验8SAE J 306-2005 汽车齿轮润滑剂黏度分级10SAE J 308-2007 轴和手动变速器润滑剂10SAE J 310-2005 汽车润滑脂19SAE J 311-2000 乘用车自动变速器液9SAE J 312-2001 车用汽油40SAE J 313-2004 柴油46SAE J 314-2007 毛毡羊毛和部分羊毛9SAE J 315-2004 纤维板试验规程13SAE J 318-2003 汽车气制动管接头7SAE J 322-2009 非金属装饰材料确定抗硫化氢腐蚀性的试验方法3SAE J 323-2009 确定塑料冷裂性的试验方法5SAE J 326-1986 液压反铲挖掘机术语7SAE J 328-2005 乘用车及轻型载货车车轮性能要求和试验规程7SAE J 331-2000 摩托车噪声声级6SAE J 332-2002 检测乘用车和轻型载货车轮胎一致性的试验设备6SAE J 335-1995 多位小型发动机排气系统点火抑制13SAE J 336-2001 载货车驾驶室内部噪声声级4SAE J 339-1994 座椅安全带织带磨损试验规程4SAE J 342-1991 大型发动机火花防止器试验规程9SAE J 343-2004 SAE 100R系列液压软管和软管总成试验和试验规程9SAE J 345a-1969 干湿路面乘用车轮胎最大和抱死时车轮制动力8SAE J 347-2002 7型(9、5 mm)柴油机燃油喷嘴总成4SAE J 348-1990 车轮三角垫木5SAE J 349-1991 黑色金属杆、棒、管和丝的表面缺陷检查7SAE J 350-1991 中型发动机火花防止器试验规程11SAE J 356-2006 可控焊接火花的低碳钢管的弯曲、双层扩口和焊瘤8SAE J 357-2006 发动机油的物理和化学特性15SAE J 358-1991 非破坏性试验7SAE J 359-1991 红外线试验4SAE J 360-2008 载货车和大客车坡道驻车性能试验规程8SAE J 361-2003 汽车内饰件和外饰件视觉评价规程12SAE J 363-1994 滤清器座的安装5SAE J 365-2004 装饰材料抗擦伤性试验方法5SAE J 366-2001 重型载货车和大客车外部噪声声级5SAE J 369-2007 车辆内部聚合物材料燃烧特性试验方法7SAE J 371-2006 非道路自驱动工作机械的放油、注油和油位螺塞4SAE J 373-1993 单片和双片弹簧加载式离合器壳内尺寸3SAE J 374-2009 车顶抗压试验规程4SAE J 375-1994 负荷半径或悬臂角指示系统4SAE J 376-1985 起重机举升负载指示装置4SAE J 377-2007 车辆声音信号装置25SAE J 378-2004 船用发动机布线17SAE J 379-2009 制动衬片高氏硬度6SAE J 380-2009 摩擦材料比重4SAE J 381-2009 载货车、大客车和多用途车风窗玻璃除雾系统试验规程和性能要求10 SAE J 383-1995 机动车辆座椅安全带固定点设计规程8SAE J 384-1994 机动车辆座椅安全带固定点试验规程5SAE J 385-1995 机动车辆座椅安全带固定点性能要求4SAE J 386-2006 非道路工作机械操作人员约束系统27SAE J 387-2007 机动车辆灯光术语9SAE J 390-1999 双向尺寸6SAE J 391-1981 颗粒物尺寸定义2SAE J 392-2007 摩托车和电机驱动电气系统设计压力维护3SAE J 393-2001 商用车辆车轮、轮毂、轮辋术语11SAE J 397-2009 防护结构试验室评价偏转极限值4SAE J 398-2005 乘用车、多用途车和轻型载货车燃油箱加注口条件8SAE J 399-1985 经阳极电镀的铝制汽车部件3SAE J 400-2002 表面涂层的耐剥落试验11SAE J 401-2000 钢的选择和使用6SAE J 402-2005 锻制钢和轧制钢的SAE编号系统8SAE J 403-2009 SAE碳素钢的化学成分10SAE J 404-2009 SAE合金钢的化学成分6SAE J 405-1998 SAE锻制不锈钢的化学成分7SAE J 406-2009 钢的可淬性确定方法47SAE J 409-1995 产品分析热处理或铸钢化学成分分析的容许变差9SAE J 411-1997 碳素钢和合金钢11SAE J 412-1995 钢的热处理和一般特性26SAE J 413-2002 热处理可锻钢的机械性能6SAE J 415-1995 热处理术语定义13SAE J 417-1983 硬度试验和硬度值换算11SAE J 419-1983 脱碳的测量方法8SAE J 420-1991 磁粉检查5SAE J 422-1983 用显微镜确定钢所含物质的方法7SAE J 423-1998 硬化层深度测量方法7SAE J 425-1991 用涡电流法进行电磁试验6SAE J 426-1991 液体渗透剂试验方法5SAE J 427-1991 渗透辐射检查8SAE J 428-1991 超声波检查5SAE J 429-1999 外螺纹紧固件机械性能和材料要求16SAE J 430-2007 非螺纹紧固件碳素钢实心铆钉机械性能和材料要求8SAE J 431-2000 汽车灰铸铁件22SAE J 434-2004 汽车可锻(球墨)铸铁件12SAE J 435-2007 汽车铸钢件6SAE J 437a-1969 工具和模具钢的选用和热处理12SAE J 438b-1970 工具和模具钢5SAE J 439a-1977 硬质合金刀具9SAE J 441-2009 切割钢丝喷丸4SAE J 442-2008 喷丸处理用试验带、支架和钢带8SAE J 443-2003 使用标准喷丸试验带的规程4SAE J 444-2005 喷丸处理和喷砂清洗用铸丸和铸粒的规格4SAE J 445-2005 金属喷丸和喷粒的机械性能试验7SAE J 447-1995 机动车辆车身及底盘部件的防腐68SAE J 448a-1963 表面质地8SAE J 449a-1963 表面质地的控制7SAE J 450-2002 屈服强度和屈服点术语的使用3SAE J 451-1989 铝合金基本原理5SAE J 452-2003 SAE铸铝合金的一般信息化学组成、机械和物理性能21 SAE J 454-1991 锻制铝合金的数据27SAE J 457-1991 SAE锻制铝合金的化学组成、机械性能限值和尺寸公差3 SAE J 459-1991 轴承和轴瓦合金5SAE J 460-1991 轴承和轴瓦合金SAE轴承和轴瓦的化学组成5SAE J 461-2002 锻铜和铸铜合金47SAE J 462-1981 锻铜合金8SAE J 463-2002 锻铜和铜合金42SAE J 464-1989 镁合金3SAE J 465-1989 铸镁合金12SAE J 466-1989 锻镁合金9SAE J 467b-1968 特殊用途合金(超级合金) 17SAE J 468-1988 锌合金锭和压铸件锌合金的成分3SAE J 469-1989 锌模铸合金4SAE J 470c-1976 锻镍和与镍有关的合金18SAE J 471d-1973 粉末冶金黑色金属部件16SAE J 473a-1962 焊锡3SAE J 474-1985 电镀及抛光5SAE J 476a-1961 密封式管螺纹47SAE J 482-2006 高六角头螺母3SAE J 483-2006 槽顶(暗、盖帽式)螺母5SAE J 485-1998 安装开口销用螺栓和螺钉杆上的孔及螺母的槽3SAE J 490-1996 球节11SAE J 491-1987 转向球头销和球座总成10SAE J 492-2005 铆钉和铆接13SAE J 493-1961 杆端销和U形夹4SAE J 499a-1975 装配用零件软拉孔直齿内花键5SAE J 501-1948 轴端7SAE J 502-1972 半圆键6SAE J 503-1959 半圆键槽和键沟4SAE J 506-1995 套筒式半轴20SAE J 510-1992 机动车辆悬架用钢板弹簧美制单位14SAE J 511-1989 空气弹簧术语6SAE J 512-1997 汽车管接头38SAE J 513-1999 制冷剂管接头一般规范43SAE J 514-2004 液压管接头56SAE J 515-2001 液压O形环材料、特性和尺寸规范18SAE J 516-2009 液压软管接头31SAE J 517-2008 液压软管46SAE J 518-1993 液压凸缘管及4螺栓分裂凸缘型软管接头13SAE J 524-2007 弯曲和扩口用退火无缝低碳钢管5SAE J 525-2007 弯曲和扩口用退火焊接冷拉低碳钢管6SAE J 526-2000 焊接低碳钢管4SAE J 527-2000 铜焊双层壁低碳钢管6SAE J 530-1995 汽车用管接头15SAE J 531-1995 汽车用管子、加注口和排出螺塞13SAE J 532-1993 汽车用直螺纹加注口和排出螺塞13SAE J 533-2007 管的扩口7SAE J 534-2008 润滑剂管接头7SAE J 537-2000 蓄电池18SAE J 539-1993 柴油机电气系统电压2SAE J 541-1996 起动机电路的电压降2SAE J 542-1991 起动机的安装4SAE J 543-1995 起动机小齿轮和齿圈6SAE J 544-1996 电起动机试验规程5SAE J 548-1-2000 火花塞18SAE J 548-2-2000 火花塞安装座孔4SAE J 549-1999 火花塞提前点火率5SAE J 551-1-2006 车辆、船(最大15m)和机械电磁兼容性(50 Hz18 GHz)性能等级和测量方法21SAE J 551-5-2004 电动车宽带(9 kH30 MHz)磁场和电场强度性能等级和测量方法13 SAE J 551-11-2000 车辆抗电磁干扰性非道路车辆源13SAE J 551-12-1996 车辆抗电磁干扰性车载模拟发射机6SAE J 551-13-2003 车辆抗电磁干扰性大电流注入11SAE J 551-15-2009 车辆抗电磁干扰性静电放电(ESD) 13SAE J 551-16-2005 车辆抗电磁骚扰性(反射法)第16部分:抗电磁场22SAE J 551-17-2003 车辆抗电磁干扰性电线磁场7SAE J 553-2004 断电器39SAE J 554-1987 电保险丝(管式) 5SAE J 560-2009 载货车挂车跨接电缆7线电插头17SAE J 561-2006 孔式及叉式电接头19SAE J 563-2009 6 V和12 V点烟器插座29SAE J 564-1990 前照灯变光开关4SAE J 565-1989 半自动前照灯变光装置6SAE J 567-2006 灯泡保持系统3SAE J 572-2004 建筑和工业机械封闭式灯光部件的要求3SAE J 573-1998 微型灯泡18SAE J 575-2007 总宽度小于2032 mm的车辆用照明装置和部件的试验方法和装备17 SAE J 576-2007 光学部件用塑料材料、如机动车辆照明装置透镜和反射器5SAE J 577-2005 振动试验机操作程序32SAE J 578-2006 颜色规格8SAE J 581-2004 辅助行车灯6SAE J 583-2005 前雾灯9SAE J 584-2003 摩托车前照灯6SAE J 585-2008 总宽度小于2032 mm的机动车用尾灯(后位灯) 10SAE J 586-2007 总宽度小于2032 mm的机动车用制动灯11SAE J 587-2003 牌照板照明装置(后牌照板照明装置) 8SAE J 588-2008 总宽度小于2032 mm的机动车用转向信号灯17SAE J 589b-1977 转向信号灯开关4SAE J 591-2003 聚光灯4SAE J 592-2009 总宽度小于2032 mm的机动车用示宽灯6SAE J 593-2005 倒车灯5SAE J 594-2003 回复反射器9SAE J 595-2008 被认可的急救车、保养和维修车辆的闪光警示灯16SAE J 599-1997 灯光检查代码11SAE J 600-2009 前照灯目标试验设备6SAE J 602-2009 机械照准前照灯的照准装置7SAE J 604-1995 发动机术语总则7SAE J 609-2003 小型发动机安装法兰和动力输出轴9SAE J 614-1995 发动机和变速箱量油计标记3SAE J 617-1992 发动机飞轮壳和变速器壳结合法兰11SAE J 618-1991 单片弹簧加载离合器飞轮5SAE J 619-1993 双片弹簧加载离合器飞轮5SAE J 620-1993 与驱动环式偏心离合器的工业动力输出装置和发动机上安装的船用齿轮及单轴承发电机相配用的工业发动机飞轮4SAE J 621-1995 带驱动环式偏心离合器的工业功率输出装置5SAE J 626-1998 柴油机燃料喷射燃料喷射泵末端安装法兰10SAE J 629-2002 柴油机燃料喷射总成5型和6型法兰安装3SAE J 631-2007 散热器术语14SAE J 635-2008 风扇毂螺栓定位圆和导孔4SAE J 636-2001 V型皮带和皮带轮10SAE J 637-2001 汽车V型皮带传动12SAE J 638-1998 机动车辆暖风装置试验规程12SAE J 639-2005 车用空调系统机械蒸汽压缩系统制冷剂的安全性和保存20SAE J 640-2000 液力传动符号5SAE J 641-2000 液力传动术语9SAE J 643-2000 液力传动试验代码10SAE J 645-2009 汽车变速器术语3SAE J 646-2000 行星齿轮术语3SAE J 647-1997 变速器示意图7SAE J 648-2000 自动变速器液压控制系统术语3SAE J 649-2000 自动变速器功能术语3SAE J 651-2005 乘用车和轻型载货车自动变速器和自动驱动桥试验代码14SAE J 656-1988 汽车制动术语和定义8SAE J 661-1997 制动衬片质量控制试验规程8SAE J 662-2003 制动块倒角3SAE J 663-2007 制动衬片铆钉和制动块螺栓3SAE J 670-2008 车辆动力学术语73SAE J 671-1997 减振材料和车身底部涂层8SAE J 673-2005 汽车安全玻璃9SAE J 674-2005 机动车和机动车装备用安全玻璃材料3SAE J 678-1988 汽车速度表和里程表11SAE J 680-1988 载货车驾驶室仪表和控制件的位置和操作5SAE J 682-2003 后轮防溅和飞石防护3SAE J 683-1985 轮胎防滑链间隙载货车、大客车和车辆列车(郊区客车、城间客车和公共汽车除外) 3SAE J 684-2005 汽车挂车联接装置、铰链和安全链5SAE J 686-1999 机动车牌照板3SAE J 689-1996 乘用车和轻型载货车路缘间隙、接近和离去角及坡道倾翻角4SAE J 691-1990 载货车CA尺寸3SAE J 693-1989 载货车跨越双胎的总宽度3SAE J 694-2007 商用车盘式车轮/轮毂或轮鼓接触面尺寸17SAE J 695-1998 机动车辆的转向能力和跑偏13SAE J 697-1988 全挂车或台车的安全链4SAE J 699-1985 设计机动车辆维修设施时使用的车辆平均尺寸3SAE J 700-2001 商用挂车和半挂车牵引主销4SAE J 701-1984 载货车牵引车半挂车互换联接尺寸6SAE J 702-2008 载货车牵引车及载货车挂车制动和电气连接位置5SAE J 703-2006 载货车及载货车牵引车燃油系统8SAE J 704-2000 用于安装载货车变速器上的6螺栓和8螺栓动力输出装置的开口4SAE J 706-2003 绞盘等级9SAE J 709-1977 农用拖拉机轮胎载荷、扭矩系数和充气压力10SAE J 711-1991 今后设计农用拖拉机时轮胎选用表6SAE J 712-1999 工业用和农业用盘式车轮8SAE J 714-1993 工业用和农业用盘式车轮安装零部件3SAE J 732-2007 装载机规格定义7SAE J 738-2008 双斜横截口切削刃5SAE J 740-2006 切削刃和刀头的沉头方孔2SAE J 744-1996 液压泵和马达安装及传动尺寸7SAE J 745-2009 液压动力泵试验规程12SAE J 746-2009 液压马达试验规程7SAE J 747-1990 控制阀试验规程16SAE J 748-2008 液压方向控制阀(最大压力3000 psi) 4SAE J 751-1997 非道路用轮胎和轮辋分类建筑机械12SAE J 753-2006 维修周期表2SAE J 754a-1969 润滑剂类型建筑和工业机械4SAE J 755-2009 船用螺旋桨轴轴端和轮毂9SAE J 759-2007 灯光识别代码6SAE J 764-2006 铲土机装载能力试验规程6SAE J 765-1990 起重机装载稳定性试验代码8SAE J 771-1986 汽车印制电路13SAE J 772-2004 载货车变速器后端六角螺栓、八角螺栓及动力输出装置周围间隙11 SAE J 773-1998 锥形弹簧垫圈5SAE J 774-2006 紧急警报装置及其防护壳12SAE J 775-2004 发动机提升阀信息报告26SAE J 782b-1976 机动车辆座椅手册47SAE J 792a-1968 SAE喷抛清理手册43SAE J 800-1994 机动车辆座椅安全带总成的安装8SAE J 810-1996 钢板普通表面缺陷分类30SAE J 811-1981 金属机械预加应力表面滚压法及其他方法76SAE J 814-2007 发动机冷却剂20SAE J 815-2007 汽车座椅用聚氨酯泡沫加载挠度试验3SAE J 817-2009 工程设计可用性指南建筑和工业机械维修指南非道路工作机械9 SAE J 817-1-1991 工程设计可维修性指南建筑和工业机械可维修性定义非道路工作机械3SAE J 817-2-1991 工程设计可维修性指南建筑和工业机械可维修性索引非道路工作机械13SAE J 818-2007 装载机额定工作载荷2SAE J 819-1995 发动机冷却系统现场试验(空气沸腾) 5SAE J 820-1998 起重机缆索速度和功率试验代码5SAE J 823-1994 闪光器试验5SAE J 824-1995 发动机旋转和气缸定序2SAE J 826-2008 H点机械和设计工具规程和规格32SAE J 827-2005 高碳铸钢喷丸4SAE J 829-2005 油箱加注口盖和盖保持器4SAE J 830-1999 燃料喷射装置术语17SAE J 831-1998 电气定义4SAE J 835-1995 剖分式衬套设计和应用17SAE J 836-1970 汽车冶金连接件42SAE J 839-1998 乘用车侧门锁系统7SAE J 840-2007 制动蹄和衬片粘结剂试验规程13SAE J 843-1997 乘用车和轻型载货车制动系统道路试验代码15SAE J 844-2004 空气制动系统非金属管15SAE J 845-2007 被认可的急救、维修和保养车辆的声音警报装置11 SAE J 846-2009 液体导管和接头识别编码系统29SAE J 847-1987 挂车拖杆环和挂钩/连接装置性能6SAE J 848-2001 重型商用车和半挂车牵引鞍座主销2SAE J 849-2008 多节挂车的连接装置和附件的位置4SAE J 850-2009 固定刚性壁障碰撞试验7SAE J 851-2007 商用车轮辋可拆卸车轮、可拆卸轮辋和间隔圈尺寸6 SAE J 852-2009 机动车用前转向灯5SAE J 853-1981 车辆识别代号3SAE J 855-2009 纺织品和塑料拉伸和变形试验方法3SAE J 858-2006 片式电接头3SAE J 860-2009 有机装饰材料质量(重量)测量试验方法2SAE J 861-2003 有机装饰材料耐脱色试验方法6SAE J 862-1989 影响机械驱动的汽车速度表和里程表精度的因素6 SAE J 863-1986 薄钢板冲压时塑性变形测定法8SAE J 864-1993 用锉刀进行的表面硬度试验4SAE J 866-2002 制动衬片摩擦系数识别系统3SAE J 873-2007 建筑、林业和工业机械牵引力试验规程5SAE J 875-1999 挂车车轴校准5SAE J 876-2007 宽轮辋及车轮6SAE J 879b-1968 机动车座椅系统8SAE J 880-1997 商用车制动系评定试验规范13SAE J 881-1985 起重机滑轮和转鼓尺寸2SAE J 882-2007 汽车用纺织品和塑料厚度试验方法2SAE J 883-2008 确定汽车纺织品材料尺寸稳定性试验方法3SAE J 884-1991 农用拖拉机驱动轮胎液体配重平衡平台6SAE J 885-2003 与机动车设计相关的55SAE J 887-2004 校车报警灯8SAE J 891-2004 弹簧螺母26SAE J 892-1996 压紧弹簧螺母英制尺寸系列一般说明15SAE J 892M -1996 压紧弹簧螺母公制尺寸系列一般说明15SAE J 896-1983 发动机辅助传动装置用装配法兰3SAE J 899-2007 非道路自行推力机械操作者座椅尺寸4SAE J 900-1995 曲轴箱排放控制测试规范12SAE J 901-2007 万向节及传动轴术语定义应用指南40SAE J 902-2003 乘用车前风窗除霜系统10SAE J 903-1999 乘用车前风窗刮水系统13SAE J 905-2009 燃油过滤器试验方法34SAE J 910-1988 危险报警信号开关4SAE J 911-1998 冷轧钢板表面组织测量6SAE J 912-2007 汽车装饰材料的抗粘连性及相关特性的试验方法2SAE J 913-2004 汽车用织物及纤维材料的液体分散性试验方法3SAE J 914-2009 车长小于12m的车辆侧转向信号灯10SAE J 915-2007 自动变速箱手动操作步骤3SAE J 917-2004 船用推拉式控制缆索8SAE J 918c-1970 乘用车轮胎性能要求和试验方法9SAE J 919-2009 单独式操作者的非公路机械噪声测量13SAE J 920-1985 非公路工作机械技术公报7SAE J 922-1995 涡轮增压器术语8SAE J 923-2001 货车和客车驱动桥术语19SAE J 924-1995 止推垫圈的设计和应用18SAE J 927-1995 发动机上安装的变矩器的飞轮4SAE J 928-2006 电线接头插头及插座的类型4SAE J 930-1995 非公路机械蓄电池9SAE J 931-1986 液压动力回路滤清5SAE J 932-1985 常量应变及微量应变的定义2SAE J 933-2005 自攻螺钉的机械性能和质量要求2SAE J 934-1998 车辆乘员门铰链系统5SAE J 935-2009 高强度碳素钢和合金模压钢6SAE J 940-1994 碳素钢板和带钢术语10SAE J 941-2008 汽车驾驶员眼位33SAE J 942-1999 乘用车前风窗洗涤器系统8SAE J 947-2009 纤维板术语表5SAE J 948-2003 确定汽车车厢布、乙烯树脂和皮革的耐腐蚀性和汽车车厢布抽丝的试验方法5SAE J 949-2009 确定内饰材料和基底硬度(挠度系数)的试验方法2SAE J 951-1985 汽车面漆的佛罗里达曝光试验4SAE J 953-1999 乘用车后窗除霜系统14SAE J 958-2003 起重吊车术语和尺寸8SAE J 959-1991 举升起重机钢丝强度因素6SAE J 960-2008 船用操纵缆连接发动机离合器杠杆2SAE J 961-2008 船用操纵缆连接发动机节流阀杠杆2SAE J 964-2009 检测镜反射和混浊的推荐规程6SAE J 965-1966 研磨耐久性29SAE J 966-2000 测量乘用车轮胎每英里转数的试验规程3SAE J 967-2002 柴油机喷射设备校正液5SAE J 968-1-2002 柴油机喷射油泵试验第1部分:校正喷嘴和保持架总成14SAE J 968-2-2002 柴油机喷射油泵试验第2部分:孔板流量测量7SAE J 972-2009 移动障壁碰撞试验7SAE J 973-1999 点火系统测量规程11SAE J 974-2002 农用设备闪光报警灯3SAE J 975-1993 农用设备前照灯3SAE J 983-1998 起重机和缆索式挖掘机的基本操作控制杆的布置8SAE J 985-2009 后视镜设计中应考虑的视觉因素6SAE J 986-1998 乘用车及轻型货车噪声级别8SAE J 987-2003 绳索支持椼架臂式起重机试验方法25SAE J 990-2009 工业和农业割草机命名法4SAE J 993-1989 铝合金及其热调质命名系统12SAE J 994-2009 倒车电子警报装置性能试验15SAE J 995-1999 钢螺母的机械及材料要求8SAE J 997-2000 防止火花装置的试验碳5SAE J 999-1998 吊杆起重机动力脱离装置2SAE J 1001-2009 工业甩刀式割草机和动力耙11SAE J 1004-2004 发动机冷却系统术语词汇10SAE J 1012-1993 操作者工作舱增压系统试验规程4SAE J 1014-2009 集材机和履带式拖拉机用牵引绞盘术语及分类4SAE J 1015-1995 每小时吨公里试验规程9SAE J 1017-1986 压路机和压实机术语5SAE J 1024-1989 建筑及工程机械燃油加热热风装置4SAE J 1025-2000 测量载货车轮胎每公里/英里转数的试验规程3SAE J 1028-1998 机动起重机工作区定义5SAE J 1029-2007 建筑掘土机械的灯光及标识4SAE J 1033-1993 飞轮、飞轮壳及其配件的孔偏心和面偏差的测量6SAE J 1037-2006 前风窗洗涤器管4SAE J 1038-2007 儿童用雪地车的建议7SAE J 1042-2003 通用机械操作者的保护3SAE J 1044-2006 世界制造厂识别代号4SAE J 1050-2009 驾驶员视野的描述和测量24SAE J 1051-2008 非公路机械座垫挠性变形量的测量5SAE J 1052-2009 机动车辆驾驶员及乘员头部位置13SAE J 1053-1996 英制系列单线程钢制冲压螺纹设计15SAE J 1053M-1996 公制系列单线程钢制冲压螺纹设计17SAE J 1058-1999 标准钢板的厚度及公差6SAE J 1059-1984 车速表试验规程4SAE J 1060-2000 评价与机动车辆车轮有关的噪声和乘坐舒适性的主观等级量表3 SAE J 1061-2008 通用螺栓、螺钉、螺杆表面不连续性8SAE J 1062-2008 雪地车乘员手柄2SAE J 1063-1993 悬臂式起重机结构试验方法20SAE J 1065-2009 钢制液压管的额定工作压力13SAE J 1067-2007 七导线电缆9SAE J 1069-2007 非公路自驱式作业机械快速保养用机油更换系统2SAE J 1071-2003 平路机操作控制件4SAE J 1072-1977 烧结工具材料4SAE J 1073-1995 弹簧离合器旋转试验规程3SAE J 1074-2000 发动机噪声等级测量规程(D) 5SAE J 1075-2007 建筑工地噪声测量9SAE J 1076-1990 倒车灯开关4SAE J 1078-2007 分析确定液压伸缩式起重机悬臂能力的推荐方法39SAE J 1079-1995 偏心离合器旋转试验规程3SAE J 1081-2000 准标准钢5SAE J 1082-2008 燃料消耗量道路检测规程22SAE J 1083-2002 机械未经许可的启动或移动3SAE J 1085-1999 弹性绝缘体动力特性试验16SAE J 1086-1995 金属和合金的编号10SAE J 1087-2000 单向离合器术语8SAE J 1088-1993 测量小型通用发动机尾气排放的试验规程15SAE J 1091-2003 挖土机械操作者视野20SAE J 1093-2007 椼架式起重机吊杆系统分析规程13SAE J 1094-1992 尾气排放测量定容积取样系统48SAE J 1095-2009 轮辐和轮毂疲劳试验规程10SAE J 1096-2000 在定置条件下重型载货车外部噪声测量6SAE J 1098-1995 每小时吨公里的应用5SAE J 1099-2002 金属及非金属材料的低循环疲劳性能技术报告29SAE J 1100-2009 机动车辆尺寸127SAE J 1101-2007 摩托车停车稳定性试验规程4SAE J 1102-1995 车轮螺栓机械和材料要求6SAE J 1102M-2001 公制车轮螺栓机械和材料要求5SAE J 1105-2006 前向警告喇叭的电气性能、试验和应用13SAE J 1106-1975 乘用车轮胎稳态力和力矩特性测量用试验室试验机9SAE J 1107-1975 乘用车轮胎稳态力和力矩特性测量用试验室试验机和试验规程53 SAE J 1109-2007 绞接式橡胶轮集材机部件术语3SAE J 1111-2007 带抓斗的集材机部件术语6SAE J 1113-1-2006 车辆、船泊(船长等于15m)及机械(航空器除外)部件电磁兼容性测量规程及限制(16、6Hz到18GHz、所有导线) 37SAE J 1113-2-2004 车辆(航空器除外)电磁兼容性测量规程及限制─传导屏蔽范围15Hz到250KHZ全导线7SAE J 1113-3-2006 传导屏蔽范围250 kHz到400 MHz的直接射频功率10SAE J 1113-4-2004 电磁辐射区域的屏蔽大电流注入法12SAE J 1113-11-2007 电源线瞬间传导的屏蔽24SAE J 1113-12-2006 沿电源线外的线路传导和耦合电容耦合和电感耦合引发的电气干扰20SAE J 1113-13-2004 车辆部件电磁兼容性测量规程─第13部分:静放电屏蔽25SAE J 1113-21-2005 车辆部件电磁兼容性测量规程─第21部分: 30 MHz到18GHz电磁区的屏蔽、吸波暗室20SAE J 1113-22-2003 车辆部件电磁兼容性测量规程─第22部分:电源线电磁辐射区的屏蔽11SAE J 1113-24-2006 10kHz到200MHz的克劳福德微电子电池及10kHz到5GHz的多频微电子电池辐射电磁区的屏蔽18。
SAE J1455-1994 汽车电器试验标准

SAE Technical Standards Board Rules provide that: “This report is published by SAE to advance the state of technical and engineering sciences. The use of this report is entirely voluntary, and its applicability and suitability for any particular use, including any patent infringement arising therefrom, is the sole responsibility of the user.”SAE reviews each technical report at least every five years at which time it may be reaffirmed, revised, or cancelled. SAE invites your written comments and suggestions.QUESTIONS REGARDING THIS DOCUMENT: (412) 772-8512 FAX: (412) 776-0243TO PLACE A DOCUMENT ORDER; (412) 776-4970 FAX: (412) 776-0790SAE WEB ADDRESS 2.1.4R ELATED P UBLICATIONS—The following publications are provided for information purposes only and are not arequired part of this document.TAPPI T801-83TAPPI T802-813.Application3.1Environmental Data and Test Method Validity—The information included in the following sections is basedupon test results achieved by major North American truck manufacturers and component equipment suppliers.Operating extremes were measured at test installations normally used by manufacturers to simulate environmental extremes for vehicles and original equipment components. They are offered as a design starting point. Generally, they cannot be used directly as a set of operating specifications because some environmental conditions may change significantly with relatively minor physical location changes. This is particularly true of vibration, engine compartment temperature, and electromagnetic compatibility. Actual measurements should be made as early as practicable to verify these preliminary design baselines.The proposed test methods are currently being used for laboratory simulation or are considered to be a realistic approach to environmental design validation. They are not intended to replace actual operational tests under adverse conditions. The recommended methods describe standard cycles for each type of test. The designer must specify the number of cycles over which the vehicle electronic components should be tested.The number of cycles will vary depending upon equipment, location, and function. While the standard test cycle is representative of an actual short term environmental cycle, no attempt is made to equate this cycle to an acceleration factor for reliability or durability. These considerations are beyond the scope of this document.3.2Organization of Test Methods and Environmental Extremes Information3.2.1The data presented in this document are contained in Sections 4 and 5. Section 4, Environmental Factorsand Test Methods, describes the thirteen characteristics of the expected environment that have an impact on the performance and reliability of truck and bus electronic systems. These descriptions are titled:a.Temperatureb.Humidityc.Salt Spray Atmosphered.Immersion and Splash (Water, Chemicals, and Oils)e.Steam Cleaning and Pressure Washingf.Fungusg.Dust, Sand, and Gravel Bombardmenth.Altitudei.Mechanical Vibrationj.Mechanical Shockk.General Heavy-Duty Truck Electrical Environmentl.Steady State Electrical Characteristicsm.Transient, Noise, and Electrostatic Characteristicsn.Electromagnetic Compatibility/Electromagnetic InterferenceThey are organized to cover three facets of each factor:1.Definition of the factor2.Description of its effect on control, performance, and long-term reliability3. A review of proposed test methods for simulating environmental stress3.2.2I N S ECTION 5a.Underhood1.Engine (Lower Portion)2.Engine (Upper Portion)3.Bulkheadb.Interior (cab)1.Floor2.Instrument Panel3.Head Liner4.Inside Doorsc.Interior (aft of cab)1.Bunk Area2.Storage Compartmentd.Chassis1.Forward2.Reare.Exterior of Cab1.Under Floor2.Rear3.Top4.Doors3.3Combined Environments—The vehicle environment consists of many natural and induced factors.Combinations of these factors are present simultaneously. In some cases, the effect of a combination of these factors is more serious than the effect of exposing samples to each environmental factor in series. For example, the suggested test method for humidity includes high- and low-temperature exposure. This combined environmental test is important to vehicle electronic components when proper operation is dependent on seal integrity. Temperature and vibration is a second combined environmental test method that can be significant to components. During design analysis a careful study should be made to determine the possibility of design susceptibility to a combination of environmental factors that could occur at the planned mounting location. If the possibility of susceptibility exists, a combined environmental test should be considered.3.4Test Sequence—The optimum test sequence is a compromise between two considerations:3.4.1The order in which the environmental exposures will occur in operational use.3.4.2 A sequence that will create a total stress on the sample that is representative of operation stress.The first consideration is impossible to implement in vehicle testing since exposures occur in a random order.The second consideration prompts the test designer to place the most severe environments last. Many sequences that have been successful follow this general philosophy, except that the temperature cycle is placed or performed first in order to condition the sample mechanically.4.Environmental Factors and Test Methods4.1Temperature4.1.1D EFINITION—Thermal factors are probably the most pervasive environmental hazard to vehicle electroniccomponents. Sources for temperature extremes and variations include:4.1.1.1The vehicle's climatic environment, including the diumal and seasonal cycles—Variations in climate bygeographical location must be considered. In the most adverse case, the vehicle that spends the winter in Canada may be driven in the summer in the Arizona desert. T emperature variations due to this source range from −54 to +85 °C (−65 to +185 °F).4.1.1.2Heat sources and sinks generated by the vehicle's operation—The major sources are the engine anddrivetrain components, including the brake system. Wide variations are found during operation. For instance, temperatures on the surface of the engine can range from the cooling system 88 °C (190 °F) to the surface at the exhaust system at 816 °C (1500 °F). This category also includes conduction, convection, and radiation of heat because of the various modes of the vehicle's operation.4.1.1.3Self-heating of the equipment due to its internal dissipation—A design review of the worst casecombination of peak ambient temperature (see 4.1.1.1 and 4.1.1.2), minimized heat flow away from the equipment, and peak-applied steady-state voltage should be conducted.4.1.1.4Vehicle operational mode and actual mounting location—Measurements should be made at the actualmounting site during the following vehicular conditions while they are subjected to the maximum heat generated by adjacent equipment, and while they are at the maximum ambient environment:a.Engine startb.Engine idlec.Engine high speedd.Engine turn off (Prior history important.)e.Various engine/road conditions4.1.1.5Ambient conditions before installation due to storage and transportation extremes—Shipment in unheatedaircraft cargo compartments may lower the minimum storage (nonoperating) temperature to −50 °C (−58°F).The thermal environmental conditions that are a result of these conditions can be divided into three categories:a.Extremes - The ultimate upper and lower temperatures the equipment is expected to experience.b.Cycling - The cumulative effects of temperature cycling within the limits of the extremes.c.Shock - Rapid change of temperature. Figure 1 illustrates one form of vehicle operation that inducesthermal shock and is derived from an actual road test of two vehicles. Thermal shock is also inducedwhen vehicle electronic componentry at elevated temperature is exposed to sudden rain or roadsplash, or when it is moved from a heated shelter into a low (−40 °C/−40 °F) ambient temperatureenvironment.FIGURE 1—TIME INTO RUN-MINUTES VEHICLE WARM-UP CHARACTERISTICS The vehicle electronic component designer is urged to develop a systematic, analytic method for dealing with steady-state and transient thermal analysis. The application of many devices containing semiconductors is temperature limited. For this reason, the potential extreme operating conditions for each application must be scrutinized to avoid failure in the field.4.1.2E FFECT O N P ERFORMANCE—The damaging effects of thermal stock and thermal cycling include:4.1.2.1Cracking of printed circuit board or ceramic substrates.4.1.2.2Thermal stress of fatigue failures of solder joints.4.1.2.3Delamination of printed circuit boards and other interconnect system substrates.4.1.2.4Seal failures, including the breathing action of some assemblies, due to temperature-induced dimensionalvariation that permits intrusion of liquid or vapor borne contaminants.4.1.2.5Failure of circuit components due to direct mechanical stress caused by differential thermal expansion. 4.1.2.6The acceleration of chemical attack on interconnects, due to temperature rise, can result in progressivedegradation of circuit components, printed circuit board conductors, and solder joints.In addition to these phenomena, high temperature extremes can cause a malfunction by:4.1.2.7Exceeding the dissociation temperature of surrounding polymer or other packaging components.4.1.2.8Carbonizing of the packaging materials resulting in the eventual progressive failure of the associatedpassive or active components. This is possible in cases of excessively high temperature. In addition, noncatastrophic failure is possible because of electrical leakage in the resultant carbon paths.4.1.2.9Changing the active device characteristics with increased heat, including changes in gain, impedance,collector-base leakage, peak blocking voltage, collector-base junction second breakdown voltage, etc.4.1.2.10Changing the passive device characteristics, such as permanent or temporary drift in resistor value andcapacitor dielectric constants, with increased temperature.4.1.2.11Changing the interconnect and relay coil performance due to the conductivity temperature coefficient ofcopper.4.1.2.12Changing the properties of magnetic materials with increasing temperature, including Curie point effectsand loss of permanent magnetism.4.1.2.13Changing the dimensions of packages and components leading to the separation of subassemblies.4.1.2.14Changing the strength of soldered joints because of changes in the mechanical characteristics of thesolder.4.1.2.15The severe mechanical stress caused by ice formation in moisture bearing voids or cracks.4.1.2.16The very rapid and extreme internal thermal stress caused by applying maximum power to semiconductoror other components after extended cold soak under aberrant operating conditions such as 36 V battery jumper starts.4.1.3R ECOMMENDED T EST M ETHODS4.1.3.1Temperature Cycle Test—Recommended thermal cycle profiles are shown in Figures 2a, b, and c andrecommended extreme temperatures in T ables 1A and 1B. If temperature characterization has been performed according to 4.1.1.4 the measured temperature may be substituted for the values in Tables 1a and 1b for the purpose of this document. The test method of Figure 2a, a 24 h cycle, offers longer stabilization time and permits a convenient room ambient test period. Figure 2b, an 8 h cycle, provides more temperature cycles for a given test duration. It is applicable only to vehicle electronic components whose temperatures will reach stabilization in a shorter cycle time. Stabilization should be verified by actual measurements; thermocouples, etc. It is important that all parts of the test specimen be held at the specified maximum and minimum temperatures for at least 15 min, after reaching stability at that temperature. This is to maintain thermal or pressure stresses generated in the test specimen for a reasonable period of time. Figure 2c illustrates a test method for thermal shock.FIGURE 2A—24 HOUR THERMAL CYCLEFIGURE 2B—SHORT (8 HOUR) THERMAL CYCLEFIGURE 2C—THERMAL SHOCKTABLE 1A—ENVIRONMENTAL EXTREME SUMMARY HEAVY-DUTY CAB OVER ENGINE TRUCK/TRACTORLocation (1)1.Figure 3 - Pictorial Description of LocationsTemperaturesMinTemperatures OperatingTemperaturesMax (2)2.If temperature characterization has been performed according to 4.1.1.4, the measured temper-ature may be substituted for the values in Tables 1a and 1b for the purpose of this document.ENGINE1a Underhood - Lower −40 °C 56 °C over ambient −40 °F 100 °F over ambient 1b Underhood - Upper (3)3.Exhaust Manifold 816 °C 1500 °F−40 °C 222 °C over ambient −40 °F 400 °F over ambient 1c Underhood Bulkhead−40 °C 56 °C over ambient −40 °F 100 °F over ambientINTERIOR:2a Floor−40 °C 27 °C 66 °C −40 °F 80 °F 150 °F 2b Instrument Panel (4)4.Windshield (Daylight opening on top of instrument panel) Direct sunlight surface temperature 115 °C maximum 240 °F maximum−40 °C 24 °C 85 °C −40 °F 75 °F 185 °F 2c Headliner −40 °C 24 °C 79 °C −40 °F75 °F 175 °F2d Inside Door 3a Bunk Area−40 °C 24 °C 93 °C −40 °F 75 °F 200 °F 3b Storage Compartment−40 °C 24 °C 74 °C −40 °F 75 °F165 °F CHASSIS:4a Forward −40 °C 120 °C −40 °F 248 °F 4b Rear−40 °C 95 °C −40 °F 203 °FEXTERIOR:5a Under No Data 5b Back No Data 5c Door −40 °C 56 °C over ambient −40 °F 100 °F over ambient5d TopNo DataMaximum ambient temperature may reach 85 °C (185 °F)TABLE 1B—ENVIRONMENTAL EXTREME SUMMARY HEAVY-DUTYCONVENTIONAL ENGINE TRUCK/TRACTORLocation (1)1.Figure 3 - Pictorial Description of LocationsTemperaturesMinTemperatures OperatingTemperaturesMax (2)2.If temperature characterization has been performed according to 4.1.1.4, the measured temper-ature may be substituted for the values in Tables 1a and 1b for the purpose of this document.ENGINE1a Underhood - Lower −40 °C56 °C over ambient −40 °F100 °F over ambient 1b Underhood - Upper (3)3.Exhaust Manifold 816 °C 1500 °F−40 °C222 °C over ambient −40 °F400 °F over ambient 1c Underhood Bulkhead−40 °C56 °C over ambient −40 °F100 °F over ambientINTERIOR:2a Floor−40 °C 27 °C 75 °C −40 °F 80 °F 165 °F 2b Instrument Panel (4)4.Windshield (Daylight opening on top of instrument panel) Direct sunlight surface temperature 115 °C maximum 240 °F maximum−40 °C 24 °C 85 °C −40 °F 75 °F 185 °F 2c Headliner −40 °C 24 °C 79 °C −40 °F75 °F 175 °F2d Inside Door 3a Bunk Area−40 °C 24 °C 93 °C −40 °F 75 °F 200 °F 3b Storage Compartment−40 °C 24 °C 74 °C −40 °F 75 °F165 °F CHASSIS:4a Forward −40 °C 121 °C −40 °F 250 °F 4b Rear−40 °C 93 °C −40 °F 200 °FEXTERIOR:5a Under No Data 5b Back No Data 5c Door −40 °C 56 °C over ambient −40 °F 100 °F over ambient5d TopNo DataMaximum ambient temperature may reach 85 °C (185 °F)FIGURE 3—VEHICLE ENVIRONMENTAL ZONESSeparate or single test chambers may be used to generate the temperature environment described by the thermal cycles. By means of circulation, the air temperature should be held to within ±3 °C (±5 °F) at each of the extreme temperatures. The test specimens should be placed in a position, with respect to the airstream, where there is substantially no obstruction to the flow of air across the specimen. If two test specimens are used, care must be exercised to assure that the test samples are not subject to temperature transition rates greater than that defined in Figures 2a and 2b. Direct heat conduction from the temperature chamber heating element to the specimen should be minimized.NOTE—Airflow is a function of actual equipment location. Simulation of actual airflow and thermal transfer operation conditions should be considered in test design.Electrical performance should be measured under the expected operational minimum and maximum extremes of excitation, input and output voltage, and load at both the cold and hot temperature extremes.These measurements provide insight into electrical variations with temperature.4.1.3.2Thermal Shock Test—Thermal shock that can be expected in the vehicle environment is simulated by themaximum rates of change shown on the recommended thermal cycle profile portrayed in Figure 2c. The thermal shock test should begin with a 2 h presoak (−40 °C/−40 °F). The test item should be transferred to the hot chamber (85 °C/185 °F) where it should remain for 2 h, then transferred to the cold chamber (−40 °C/−40 °F) for 2 h. This cycle should be repeated at least five times. Each transfer should be accomplished in1 min or less.4.1.3.3Thermal Stress—Thermal stress is caused by repeat cycling through the thermal profiles of Figures 2a, b,and c. Many failures are due to fatigue. Slow cycles not repeated often will not demonstrate this. The number of cycles is a function of the vehicle electronic component application. Functional electrical testing during temperature transitions or immediately after temperature transitions, is a means of detecting poor electrical connections. The effect of thermal stress is similar to thermal shock but is caused by fatigue.NOTE—Although uniform oven temperatures are desirable, the only means of heat removal in some vehicle environments may be by special heat sinks or by free convection to surrounding air. Itmay be necessary to use conductive heat sinks with independent temperature controls in theformer case and baffles or slow speed air stirring devices in the latter to simulate such conditionsin the laboratory (see Section 3).4.1.4R ELATED S PECIFICATIONS—A generally accepted method for small part testing is defined in MIL-STD-202F,Method 107F, Thermal Shock, Method A or B, alternately MIL-STD-810D, Method 503.2. The short dwell periods at high temperature are satisfactory where temperature stabilization is verified by actual measurements.4.2Humidity4.2.1D EFINITIONS—(Contained in 4.2.2)4.2.2E FFECTS O N P ERFORMANCE—Both primary and secondary humidity sources exist in the vehicle. In additionto the primary source externally applied ambient humidity, the cyclic thermal-mechanical stresses caused by operational heat sources introduce a variable vapor pressure on the seals. Temperature gradients set up by these cycles can cause the dew point to travel from locations inside the equipment to the outside and back, resulting in additional stress on the seals.The actual relative humidity in the vehicle depends on factors such as operational heat sources, trapped vapors, air-conditioning, and cool-down effects. Recorded data indicates an extreme condition of 98% relative humidity at 38 °C (100 °F).Primary failure modes include corrosion of metal parts because of galvanic and electrolytic action, as well as corrosion caused by interaction with contaminated water and oxygen. Other failure modes include changes in electrical properties, surface bridging corrosion products and condensation between circuits, decomposition of organic matter because of attacking organisms (for example, mildew), and swelling of elastomers.4.2.3R ECOMMENDED T EST M ETHODS—The most common way to determine the effect of humidity on vehicleelectronic components is to over test and examine any failure for relevance to the more moderate actual operating conditions. The most common test is an 8 h active temperature humidity cycling under accelerated conditions (Figure 4a). A second test is an 8 to 24 h exposure at 103.4 kPa gage pressure (15 lbf/in2 gage) in a pressure vessel (Figure 4b). This is a quick and effective method for uncovering defects in plastic encapsulated semiconductors.FIGURE 4—RECOMMENDED HUMIDITY CYCLESAn optional frost condition may be incorporated during one of these humidity cycles. Electrical performance should be continuously monitored during these frost cycles to note erratic operation. Heat-producing and moving parts may require altering the frost condition portions of the cycle to allow a period of nonoperation induced frosting.4.2.4R ELATED S PECIFICATIONS—Many related humidity specifications are recommended for review and reference.The first: MIL-STD-810D, Method 507.2, Procedures I through III, Humidity, is a system-oriented test method. The second, a modified version of MIL-STD-202F, Method 103B, Humidity (Steady State), is intended to evaluate materials. The third, MIL-STD-202F, Method 106E, Moisture Resistance, is a procedure for testing small parts.4.3Salt Spray Atmosphere4.3.1D EFINITION—(Contained in 4.3.2)4.3.2E FFECT O N P ERFORMANCE—Vehicle electronic components mounted on the chassis, exterior, and underhoodare often exposed to a salt spray environment. In coastal regions, the salt is derived from sea breezes, and in colder climates, from road salt. Although salt spray is generally not found in the interior of the vehicle, it is advisable to evaluate the floor area for potential effects of saline solutions that were transferred from the outside environment by vehicle operators, passengers, and transported equipment.Failure modes due to salt spray are generally the same as those associated with water and water vapor.However, corrosion effects and alteration of conductivity are accelerated by the presence of saline solutions and adverse changes in pH.4.3.3R ECOMMENDED T EST M ETHODS—The recommended test method for measuring susceptibility of vehicleelectronic component to salt spray is the American Society for Testing and Materials (ASTM) Standard Method of Salt Spray (Fog) Testing Number B 117-73. Similar test methods are found in MIL-STD-202, Method 101D, and MIL-STD-810D, Method 509.2.The test consists of exposing the vehicle electronic component to a solution of five parts salt to 95 parts water, atomized at a temperature of 35 °C (95 °F). The component being tested should be exposed to the salt spray for a period of 24 to 96 h. The actual exposure time must be determined by analysis of the specific mounting location. When the tests are concluded, the test specimens should be gently rinsed in clean running water, about 38 °C (100 °F), to remove salt deposits from the surface, and then immediately dried.Drying should be done with a stream of clean, compressed dry air at about 175.8 to 241.3 kPa gage pressure (35 to 40 lbf/in2 gage). The vehicle electronic component should be tested under nominal conditions of voltage and load throughout the test.NOTE—The Pascal (Pa) is the designated SI (metric) unit for pressure and stress. It is equivalent to 1 N/m2.Where leakage resistance values are critical, appropriate measurements under wet and dry conditions may be necessary.4.3.4R ELATED S PECIFICATIONS—ASTM B 117-73 is the recommended test method.4.4Immersion and Splash (Water, Chemicals, and Oils)4.4.1D EFINITION—Vehicle electronic component mounted on or in the vehicle are exposed to varying amounts ofwater, chemicals, and oil. A list of potential environmental chemicals and oils includes:Engine Oils and AdditivesTransmission OilRear Axle OilPower Steering FluidBrake FluidAxle GreaseWasher SolventGasolineDiesel FuelFuel AdditivesAlcoholAnti-Freeze Water MixtureDegreasersSoap and DetergentsSteamBattery AcidWater and SnowSalt WaterWaxesKeroseneFreonSpray PaintPaint StrippersEtherDust Control Agents (magnesium chloride)Moisture Control Agents (calcium chloride)Vinyl PlasticizersUndercoating MaterialMuriatic AcidAmmoniaThe modified chemical characteristics of these materials when degraded or contaminated should also be considered.4.4.2E FFECT O N P ERFORMANCE—Loss of the integrity of the container can result in corrosion or contamination ofvulnerable internal components. The chemical compatibility can be determined by laboratory chemical analysis. Devices such as sensors, that may be immersed in fluids for a long period, should be subjected to laboratory life tests in these fluids.4.4.3R ECOMMENDED T EST M ETHODS—The vehicle electronic component designer should first determine whetherthe parts must withstand complete immersion or splash, and which fluids are likely to be present in the application. Immersion and splash tests are generally performed following other environmental tests because this sequence tends to aggravate incipient defects in seals, seams, and bushings that might otherwise escape notice.Splash testing should be performed with the equipment mounted in a normal operating position with any drain holes open. Any integral parts, such as electrical connectors, shall be in place. Areas of the equipment not subject to splash testing may be sealed or otherwise isolated. The test apparatus should be designed to provide 100% coverage of the test surface using 80 degrees flat fan nozzles located 20 to 25 cm(10 to 12 in) from the test surface. The apparatus should provide a source pressure of approximately200kPa gauge (29 psig) with a flow rate of 2650 cm3/min (0.7 gal/min). The equipment should be exposed to the spray for 5 min of a 10 min period for a total of two cycles.During immersion testing, utilizing water as the fluid, the component ordinarily is not operated due to setup logistics and techniques of this test. In this test, the vehicle electronic component in its normal exterior package is immersed in tap water at about 18 °C (65 °F). The test sample should be completely covered by the water. The sample is first positioned in its normal mounting orientation. It remains in this position for 5min and then rotated 180 degrees. It should remain in this position for 5 min and then rotated 90 degrees about the other axis where it remains for 5 min. Immediately after removal, the sample should be exposed toa temperature below freezing until the entire mass is below freezing. The sample is then returned to roomtemperature, air dried, functionally tested, and inspected for damage.More severe tests such as combined temperature, pressure, and continuous fluid contact must be considered for equipment subjected to extreme environments; for example, exposure to coolant water, brake fluid, and transmission oil. Caution must be used in specifying combined tests because they may be unrealistically severe for many applications.4.4.4R ELATED S PECIFICATIONS—None4.5Steam Cleaning and Pressure Washing4.5.1D EFINITION—(Contained in 4.5.2)4.5.2E FFECTS O N P ERFORMANCE—The intense heat from cleaning sprays and the caustic nature of chemicalagents used in washing solutions create a severe environment for devices and associated wiring and connectors mounted in the engine, chassis, and exterior areas. This exposure can cause a degradation of insulation and seals as well as cracking of vinyl connectors and component packaging. High pressure wash-down may produce results similar to salt spray in many truck interior.4.5.3R ECOMMENDED T EST M ETHOD—The electronic component under test shall be mounted in its normaloperating position with drain holes, if used, open. If an integral connector is used, it shall be mated. The test apparatus should be designed to provide 100% coverage of the exposed surface of the electronic component using flat fan spray nozzles located 20 to 30 cm (7.9 to 11.8 in) away. This apparatus should provide a source pressure of approximately 1400 kPa gage (203 lbf/in2 gage) with a flow rate of 9460 cm3/min (150gal/h). For the steam cleaning, the water temperature should be at 93 °C (200 °F). The test item should be exposed to the spray for 3 s of a 6 s period for a total of 375 cycles.A sample test device is illustrated in Figure 5.。
- 1、下载文档前请自行甄别文档内容的完整性,平台不提供额外的编辑、内容补充、找答案等附加服务。
- 2、"仅部分预览"的文档,不可在线预览部分如存在完整性等问题,可反馈申请退款(可完整预览的文档不适用该条件!)。
- 3、如文档侵犯您的权益,请联系客服反馈,我们会尽快为您处理(人工客服工作时间:9:00-18:30)。
SAE Technical Standards Board Rules provide that: “This report is published by SAE to advance the state of technical and engineering sciences. The use of this report is entirely voluntary, and its applicability and suitability for any particular use, including any patent infringement arising therefrom, is the sole responsibility of the user.”SAE reviews each technical report at least every five years at which time it may be reaffirmed, revised, or cancelled. SAE invites your written comments and suggestions.Copyright ©2002 Society of Automotive Engineers, Inc.All rights reserved. No part of this publication may be reproduced, stored in a retrieval system or transmitted, in any form or by any means, electronic, mechanical, photocopying,recording, or otherwise, without the prior written permission of SAE.TO PLACE A DOCUMENT ORDER:Tel: 877-606-7323 (inside USA and Canada)Tel: 724-776-4970 (outside USA)Fax: 724-776-0790Email: custsvc@SURFACE VEHICLE 400 Commonwealth Drive, Warrendale, PA 15096-0001RECOMMENDED PRACTICE J400REV.NOV2002Issued 1968-07Revised2002-11Superseding J400 DEC2001Test for Chip Resistance of Surface Coatings1.Scope—This SAE Recommended Practice covers a laboratory procedure for testing and evaluating theresistance of surface coating to chipping by gravel impact. The test is designed to reproduce the effect ofgravel or other media striking exposed paint or coated surfaces of an automobile and has been correlated withactual field results. The specific intent of the test is to evaluate organic surface coatings or systems on flat testpanels; however, It may be possible to extend this type of testing to finished parts or other types of materialssuch as anodized aluminum or plated plastics if the results are interpreted with respect to the limitations andintent implied by the original testing procedures and rating system.This document may involve hazardous materials, operations, and equipment. This document does not purportto address all of the safety problems associated with its use. It is the responsibility of whoever uses thisdocument to consult and establish safety and health practices and determine the applicability of regulatorylimitations prior to use.All dimensions are nominal unless otherwise noted.2.Reference 2.1Related Publication—The following publication is provided for information purposes only and is not arequired part of this document.2.1.1G ENERA L M O TORS P UB LICATION —Available from GM AC Rochester/GMC, P.O. 1360, Flint, MI 48501-8054.GMR-767—The Measurements of Chipping of Automotive Finishes, Hays, Donald R., Detroit, MI,General Motors Laboratories, 19683.Summary of Method—The test consists of projecting standardized road gravel by means of a controlled airblast onto a suitable test panel. The testing apparatus is called a gravelometer, designed to contain road gravel, a test panel holder, and a gravel projecting mechanism. The projecting mechanism, located in front of the test panel, consists of an air nozzle in the base of an inverted pipe tee. The stem of the pipe tee points upward and is located beneath a vibrating hopper into which the gravel is poured. The gravel, falling into the air blast, is projected toward and impacts upon the test panel, which is usually held perpendicular to the impinging gravel. All testing is conducted under controlled temperature conditions, generally room temperature (ambient) or –29 °C ± 3 °C (–20 °F ± 5 °F). After the gravel impact, tape is applied to remove any loose paint chips remaining on the panel, and the degree of chipping is determined by visual comparison with the SAE Chipping Rating Standards1, by counting the number and sizes of all chips, or by other methods deemed suitable between the contractual parties involved.4.Equipment and Materials4.1Gravelometer—A gravel projecting test apparatus which is constructed according to the design specificationsshown in Figure 1.FIGURE 1—TEST APPARATUS1.Available from Society of Automotive Engineers, Inc., 400 Commonwealth Drive, Warrendale, PA 15096-0001—Identified as EA-400.4.1.1O PE RATION/M AINTENANCE C HE CKLIST—The operation/maintenance checklist shown in Figure 2 shall becompleted at least once a month for testers that are operated on a weekly basis and once every 6 months for testers that are operated less frequently.NOTE—Values in chart are specific to the standard gravel testing protocol. Different specifications may be necessary for other media types.If the answer to any of the following questions is NO, discontinue testing until the problem has been corrected.FIGURE 2—CHECKLIST4.2Gravel—The gravel for this test shall be water-worn road gravel, not crushed limestone or rock. The gravelwill pass through 15.86 mm (5/8 in) space screen when graded, but be retained on 9.53 mm (3/8 in) space screen. It is important to note that mesh screen is not a substitute for space screen. The gravelometer has9.53 mm (3/8 in) space screen in the bottom to separate fractured pieces of rock and dust smaller than 9.53mm (3/8 in) so that the retained gravel on this screen may be reused. Because the gravel tends to blunt or fragment after repeated impacts, it should be changed at a regular frequency. For testers that are operated ona weekly basis, 2 pints of gravel shall be replaced with fresh gravel each month. For testers that are operatedon less frequent basis, 2 pints of gravel shall be replaced with fresh gravel at least every 6 months.Gravel must be washed prior to initial use.Other media may be used as agreed upon by contractual parties.NOTE—Pint measurements refer to a 1 pint container full to the top.4.3Paint Removal Tape—10 cm (4 in) wide or 5 cm (2 in) wide, 3M product #898 filament strapping tape orequivalent. Other tape may be used as agreed upon by contractual parties.NOTE—The adhesion strength of the tape use makes a significant impact on how much separated paint is removed.4.4Temperature Conditioning Equipment—Gravelometer tests are usually run at ambient or a lowertemperature, generally –29 °C (–20 °F), which shall be mutually agreed upon by contractual parties. Tests conducted at different temperatures will employ the following:4.4.1METHOD A—A cold room or chamber in which the gravelometer and test panels are maintained at thespecified temperature of testing.For freezers that employ a defrosting mechanism, document the method of defrosting and any temperature changes.4.4.2M ETHO D B—A freezer in which the test panels are cooled to5.6 °C (10 °F) below the test temperature beforethey are individually transferred and tested immediately in a gravelometer at room temperature located nearby.4.4.3M ETHO D C—Ambient: room maintained at a temperature between 20 °C (68 °F) and 30 °C (86 °F).4.5Transparent Grid—A chip counting aid constructed of transparent plastic approximately 3.2 mm x 12.7 cm(1/8 x 5 x 5 in), on which a 10.16 x 10.16 cm (4 x 4 in) grid of 2.54 cm (1 in) squares has been etched or scribed.4.6Chipping Rating Standards—A photographic transparency, depicting the size and shape of each chip. SeeFigure 3 for representation of this transparency. Figure 3 IS A REPRESENTATION ONLY.FIGURE 3—CHIPPING RATING STANDARDS (REPRESENTATION ONLY)4.7Test Specimens—It is recommended that three replicates of each test specimen be exposed in thegravelometer. The number of replicates will be agreed upon between contractual parties. The test specimens are typically flat and 10.16 x 30.48 cm (4 x 12 in) in size in order to fit into the panel holder of the gravelometer.The test panel material, the panel’s thickness or gauge, and preliminary surface treatments (such as phosphating or anodizing) should be the same for all tests in any series and as representative as possible of the actual part. Any deviations in these parameters may produce misleading test results.For profiled test specimens, or nonstandard test specimens, limits for uniform thickness, uniform backing, and uniform specimen holders must be determined and agreed upon by contractual parties.5.Setup and Procedures5.1Setup5.1.1Paint or process the test panels as specified for the systems under test.It should be noted that the chipping test results will be dependent upon the nature of the coating’s formulation, the method and degree of drying or curing of the various coats, and the film thickness involved.Uniformity of film thickness is extremely important, and each component of the system should be controlled as uniformly as possible.5.1.2The test specimens must reach the test temperature for a minimum of 15 minutes prior to testing inaccordance with the appropriate method specified in 4.5.In the conditioning environment, proper heat transfer can be facilitated by separating the test specimens so that the conditioned air can circulate freely about the specimen.5.1.3Fill a 0.473 L (1 pt) container to the top with grated/screened gravel.During exposure of multiple specimens, no more than 10 pt of gravel shall be allowed to collect on the sizing screen. Once 10 pt have collected on the screen, scrape the gravel across the screen so that the small rocks will fall beneath the screen. Remove the gravel that remains on top of the screen from the gravelometer for re-use. Remove and discard any stones that have lodged in the screen.5.1.4Other media can be used as agreed upon by contractual parties.5.1.5Adjust air pressure on the gravelometer to 483 kPa ± 21 kPa (70 psi ± 3 psi) with the air valve open.For older cabinet type gravelometers, keep lid to gravel chamber on the gravelometer closed during this operation as safety precaution.5.1.6Set feed rate so that the hopper empties in 7 to 10 s/pt.5.1.7Other air pressures can be used as agreed upon by contractual parties.5.2Procedure5.2.1O LD C AB INET T YPE G RAVELOMETERa.After the air pressure is adjusted, shut off air valve, and open the lid to the specimen chamber. Placeone test specimen conditioned at the desired test temperature in the panel holder with the coated sidefacing the gravel projecting mechanism. Mount the specimen as tightly as possible so as not to affectthe angle of the panel orientation or allow movement during the test.b.The specimen holder shall have an edge-supported backer plate. Other specimen mounting fixturesmay be used as agreed upon by contractual parties.c.Close lid to panel chamber.d.Open the gravel feed door and pour gravel from the one pint container obtained from step 5.1.3 intothe top of the gravel hopper. Do not allow gravel to fall into the nozzle entrance. Open the air valve toallow the air to project the gravel at the sample.NOTE 1—The gravel hopper must empty within 7 to 10 s. If gravel remains in the hopper after 10 s, stop the test and investigate the cause. The operator may not touch the gravel during the test or otherwisephysically help the gravel into the funnel.NOTE 2—It is important to note that the vibrator may become frozen when the chamber is installed in a cold room or freezer. If the vibrator is frozen, discontinue the test until the vibrator has thawed and isoperating correctly.NOTE 3—Shut off air valve, open lid to specimen chamber, and remove the test specimen.5.2.2M ODULAR G RAV ELOMETER W ITH E LECTRONIC F EED M ECHANISMa.Pull back on the specimen mounting clamp to open the specimen holder on the specimen holderassembly.b.Clamp to close the specimen holder.c.Pour gravel from the one pint container obtained from step 5.1.3 into hopper.d.Set the Test Timer.5.2.3There are two ways to operate a test on these units. A Timed Test is a test that shuts off the machine afterthe preset amount of time has passed. A Manual Test requires the operator to shut off the machine after the desired amount of time has passed.5.2.3.1Timed Testa.Make sure the control switch is set to STOP.b.Set the Test Timer to the desired test time. This is typically < 10 s.c.Turn the main power switch to ON.d.Flip the control switch to TIMED START.5.2.3.2Manual Testa.The manual test requires the operator to manually stop the test. Once started, it will not stop by itself.b.Make sure the control switch is on OFF.c.Switch the main power control switchd.Switch the control switch to MANUAL.e.After the desired amount of time has passed, flip the control switch to OFF.f.Once the test is complete, remove the test panel from the specimen holder by pulling back on thespecimen clamp and pulling out the test specimen.g.Remove the rocks from the return receptacle and screen before reuse.h.If necessary, allow panels to return to room temperature and dry with a soft cloth to remove anycondensed moisture.ing the tape referenced in 4.4, remove all loose or damaged paint.j.Cover the tested area of the specimen with a strip of tape or multiple strips of tape side by side. Firmly adhere the tape to the test specimen by applying uniform pressure. (Uniform pressure can be appliedby using items like a tongue depressor or a pencil eraser.) There can be no air bubbles trappedbeneath the tape.k.Remove the tape by pulling straight up.l.Apply new strip(s) of tape to the specimen and repeat the paint removal process in the opposite direction.m.Continue this procedure using new strips of tape until all loose or damaged paint is removed.n.Other tapes or loose paint removal methods may be used as agreed upon by contractual parties.o.Determine the degree of chipping by one of the following methods of the Gravelometer Rating System.6.Gravelometer Rating System6.1Methods AvailableNOTE—other methods may be employed as agreed upon between contractual parties.6.1.1There are two methods available for determining the degree of chipping from gravel on the tested panel(other media will require other evaluation methods.) In Method I, the exact number of chips in each size range is tabulated for the specified test area, while Method II utilizes a visual comparison of the tested panel with the SAE Chipping Rating Standards shown in Figure 3 which depict various degrees of chipping severity and are arranged sequentially from best to worst according to chipping size and frequency.Method I is the most precise and should be used where definitive accuracy is required or as the referee method in case differences arise between laboratories; however, it is more time-consuming than the visual comparison method.Method II is much faster and, while more of an approximation than the first method, can be used for many routine laboratory evaluations where the accuracy of Method I is not required. Method II also lends itself to field survey work where the chipped areas can be rated by direct comparison with the chipping Rating Standards.6.1.2With both methods, the chipped area to be evaluated on the tested panel should be the 10.16 x 10.16 cm(4 x 4 in) square that exhibits the center of the chipped pattern.6.2Basic Structure of Rating System—Generally, the basic structure of the chip rating system consists of oneor more number-letter combinations in which rating numbers 10-0 indicate the number of chips of each size and rating letter A-D designate the sizes of the corresponding chips. A point of failure notation may also be included in the rating if more descriptive refinement is desired.6.2.1N UMBER OF C HIPS—A whole rating number selected from the range of 10-0 in Table 1 is used to indicate thenumber of chips of each size in the 10.16 x 10.16 cm (4 x 4 in) test area.TABLE 1—NUMBER CATEGORIES FOR CHIP RATINGRating Number Number of Chips Rating Number Number of Chips100450–7491375–9982–42100–14975–91150–250610–240>250525–496.2.2S IZE OF C HIPS—The size of the chip is specified by a rating letter selected from A-D in Table 2. Due to theirregular nature of chipping, the size cannot always be measured exactly so it has to be approximated.TABLE 2—SIZE CATEGORIES FOR CHIP RATINGRating Letter Size of ChipsA>1 mm (>approximately 0.03 in)B1–3 mm (approximately 0.03–0.12 in)C3–6 mm (approximately 0.12–0.25 in)D>6 mm (>approximately 0.25 in)6.2.3P OINT OF F AILURE—The coating layer at which the most predominant chipping failure occurs is designated asthe point of failure. The notations in Table 3 can be used to designate this information if desired. Other notations may be used with agreement between contractual parties.TABLE 3—POINT OF FAILURE NOTATIONNotation Level of Failure Failure Type(S/P)Substrate to Primer Adhesional(S/T)Substrate to Topcoat Adhesional(P)Prime Cohesional(P/T)Primer to Topcoat Adhesional(T)Topcoat Cohesional6.3Details of Method I and Method II6.3.1M ETHO D I—E XACT C OUNTING P RO CEDURE6.3.1.1Counting can be facilitated by the use of a transparent overlay onto which has been etched a grid of2.54cm (1 in) squares. The grid is placed over the area to be treated as a guide to remembering the areasthat have been counted.6.3.1.2The operator examines the area within a 2.54 x 2.54 cm (1 x 1 in) square, decides on the size of each chipas encountered, and records it. Rate all 16 squares and record the results.6.3.1.3The actual number of chips counted for each size is then converted into the number-letter combinationsutilizing Tables 1 and 2. The number-letter rating is then arranged with the most numerous size first, followed by the next more numerous, etc. This may then be followed by the Point of Failure notation.For example, for a panel on which there are 20 chips less than 1 mm (A size), 40 chips of 1 to 3 mm (B size), and 3 chips of 3 to 6 mm (C size) with primer-topcoat failure, the number of chips on the rating would be 5B-6A-8C (P/T). This rating can be condensed by converting the total number of chips on the panel to the corresponding number category, which is then followed by the size designations in the same order. In this example, with a total of 63 chips, the rating would be summarized as 4 BAC (P/T).6.3.2M ETHO D II—V ISUAL C OMPARISON P RO CEDURE—The Chipping Rating Standards shown in Figure 3 areutilized.These have been prepared so the chips of only 1 size are shown in each illustration. The number of chips illustrated in each standard is the fewest number of chips in each rating number category; for example, the No. 5 standards all show 25 chips, the No. 3 standards show 75 chips. All of the No. 8 and No. 10 categories and the lower number D size categories have not been included in order to keep the photographs to a manageable number.6.3.2.1Visually compare the area to be rated with the standards.Since each standard exhibits only one chip and actual chipping seldom occurs in only one size, one or more standards should be superimposed until that combination of standards which more nearly resembles the panel is obtained. Record the standards that were used to achieve the match with the panel under examination.6.3.2.2As with Method I, the most numerous chips should be listed first, the next most numerous second, etc.Again, the number-letter ratings may be summarized to give a condensed single number rating based on the total number of chips of all sizes followed by the letter ratings to indicate the relative number of chips of each size.For example, a panel requiring the superimposition of a 6A standard, a 5B standard, and an 8C standard would be described as 5B-6A-8C (P/T) and summarized as 4 BAC (P/T).7.Precision—Because of the possibility of slight variations in the number, size, type, and distribution of gravel ineach test sequence, some variation in the raw counts of chips in the various size categories will be reflected in the data. However, when these counts are converted into the condensed rating of Method I or the rating that can be obtained by Method II, if the results differ by greater than one number-letter rating, they should by considered suspect.8.Reporting of Results—Reports of the gravelometer tests shall include the number-letter rating and allapplicable test conditions that deviated from the standard as outlined. In addition, reports should include the material type, thickness, and any preliminary surface treatment of the test panel together with the type of surface coating(s), baking, or pertinent processing schedules, and the film thicknesses of finishing system being evaluated.9.Notes9.1Marginal Indicia—The change bar (l) located in the left margin is for the convenience of the user in locatingareas where revisions have been made to the previous issue of the report. An (R) symbol to the left of the document title indicates a complete revision of the report.PREPARED BY THE SAE TEXTILES AND FLEXIBLE PLASTICS COMMITTEESAE J400 Revised NOV2002Rationale—Editorial revisions made to add frequency of use of checklist in 4.1.1 that was unintentionally left out of submitted document.Relationship of SAE Standard to ISO Standard—Not applicable.Application—This SAE Recommended Practice covers a laboratory procedure for testing and evaluating the resistance of surface coating to chipping by gravel impact. The test is designed to reproduce the effect of gravel striking exposed paint or coated surfaces of an automobile and has been correlated with actual field results. The specific intent of the test is to evaluate organic surface coatings or systems on flat test panels; however, it may be possible to extend this type of testing to finished parts or other types of materials such as anodized aluminum or coated plastics if the results are interpreted with respect to the limitations and intent implied by the original testing procedure and rating system.Reference SectionGMR-767—The Measurement of Chipping of Automotive Finishes, Hays, Donald R., Detroit, MI, General Motors Laboratories, 1968Developed by the SAE Textiles and Flexible Plastics Committee。