GB 8410汽车内饰材料的燃烧特性
汽车内饰材料燃烧试验仪技术规格书

汽车车内饰材料燃烧试验仪
基本简介:
1、汽车内饰材料燃烧试验主要是根据国标 GB8410-2006 及美标 FMVSS 571.302 等标准规定的 模拟燃烧性能安全试验项目。
2、汽车内饰材料燃烧试验是采用规定尺寸的本生灯和特定燃气源 (液化石油气或煤气),按 一定的火焰高度和一定的施焰角度对水平状态的汽车内饰材料施焰若干时间,以试品点燃、持续时间和燃烧长度等来评定其可燃性及着火危险性。
3、汽车内饰材料燃烧试验仪主要针对汽车内饰材料的可燃性进行定性评定。
适用于各种类型的汽车内饰材料生产厂家及其材料部件的研究、生产和质检部门,也适用于绝缘材料、工 程塑料或其它固体可燃材料行业。
技术参数:
1、 燃烧器:Φ9.5mm ± 0.3mm 长约 100mm 本生灯一个
2、 试验倾角:本生灯 90°垂直对着水平放置的样品燃烧
3、 火焰高度:20mm ± 2mm 到 100mm±2mm 可调(一般调为 38mm)
4、 施焰时间:0-999.9s±0.1s 可调(一般选择为 15s)
5、 燃烧气体:液化石油气或煤气
6、 温度范围:0~200℃ (显示测试状态下工作室内部温度)
7、 试验过程:试验程序手动控制
8、 参照标准:GB8410-2006,FMVSS 571.302
9、 工作室体积:385mm 宽×204mm 深×360mm 高(约 0.03m3)
10、设备外尺寸:550mm 宽×210mm 深×550mm 高。
内饰(缺)
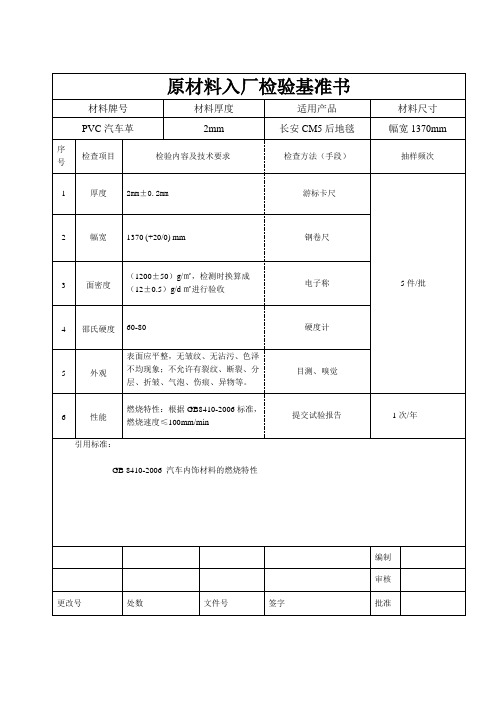
处数
文件号
签字
批准
原材料入厂检验基准书
材料牌号
材料厚度
适用产品
材料尺寸
PE发泡垫
8mm
CM5前地毯隔热垫
8*1230*200
序号
检查项目
检验内容及技术要求
检查方法(手段)
抽样频次
1
厚度
8mm±1mm
游标卡尺
5件/批
2
尺寸
150±2、580±3、880±4、1100±4
1230±4、200±2
钢卷尺
GB 8410-2006汽车内饰材料的燃烧特性
编制
审核
更改号
处数
文件号
签字
批准
5件/批
2
尺寸
≥1100mm
钢直尺
3
面密度
220g/㎡±22g/㎡
电子称
5
外观
表面应平整,无裂缝、破洞、沾污等不良外观现象。颜色为浅灰色,颜色一致,无明显色差
目测
10件/批
6
性能
燃烧特性:根据GB8410-2006标准,燃烧速度≤100mm/min
提交试验报告
1次/年
引用标准:
GB 8410-2006汽车内饰材料的燃烧特性
提交试验报告
1次/年
引用标准:
GB 8410-2006汽车内饰材料的燃烧特性
编制
审核
更改号
处数
文件号
签字
批准
原材料入厂检验基准书
材料牌号
材料厚度
适用产品
材料尺寸
220g/㎡无纺布
1mm
长安A101行李箱盖板
1100mm
序号
检查项目
汽车内开拉手设计浅析
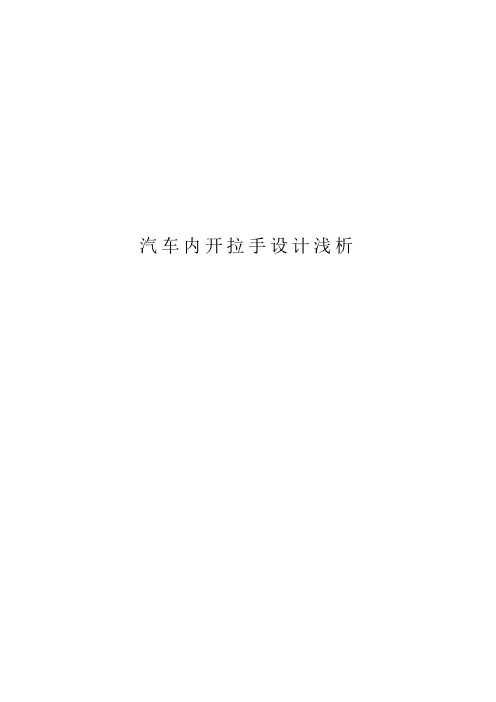
汽车内开拉手设计浅析目录目录 (3)一、内开拉手结构分析 (4)二、内开拉手设计要求 (4)三、生产问题分析 (10)一、内开拉手结构分析1-拉手手柄、2-扭簧、3-内开拉手盒、4-堵盖、5-转轴、6-锁止钮、7-缓冲钮二、内开拉手设计要求2.1法规要求作为内饰件,在设计时都应该考虑以下法规要求:(1)GB8410-2006汽车内饰材料的燃烧特性;标准中规定了汽车驾驶室和乘客舱用内饰材料水平燃烧特性的技术要求及实验方法,针对内饰零件,燃烧速率小于100mm/min内开拉手所用的材料应该满足该标准。
(2)GB11552-2009 汽车内部凸出物;按照要求内开拉手表面边缘半径曲率不小于3.2mm。
(3)汽车内部有毒有害物质检测要求;现在这项检测要求一般都被各主机厂作为标准检测项,有毒有害物质包括铅(Pb)汞(Hg)镉(Cd)六价铬(Cr)及多溴苯(PBB)和多溴二苯醚(PBDB)的含量有严格控制。
2.2工程可行性要求根据造型A面和客户产品需求,定义出模方向,然后根据表面皮纹要求,确定脱模角度,不同的皮纹对应不同的拔模角度,例如细皮纹通常采用3°粗皮纹采用7°(100%皮纹)。
合理的出模角度定义避免后期产品的皮纹拉伤。
分模线原则上不准出现在A面上,但若造型需要无法避免,应要求供应商对分模线外观进行控制。
这样可以避免新结构造成设计与制造问题,同时设计时尽量考虑前后门内开拉手共用设计,这样有利用后期质量与成本控制。
2.3材质要求内开拉手作为外观件,零件的表面要求决定着手柄本体的材料选择,一般内开拉手表面处理采用喷漆、电镀工艺,很少采用皮纹处理,结合表面处理通常采用材料为PA6或者PC+ABS。
图二2.4 安全间隙要求为了保证内开拉手开启顺畅,拉手与周边配合留足够间隙,一般间隙设计为1.5~2mm,不仅要考虑静态间隙,还要考虑运动操作时与钣金运动间隙要求,在开启过程中与钣金最小间隙≥5mm,常见检查方法,如下图所示。
汽车内饰面料阻燃加工

汽车内饰面料阻燃加工摘要:使用卤素系浴中阻燃剂T-889和磷系浴中阻燃剂T-888对涤纶汽车内饰面料进行染色加工,比较颜色变化和阻燃性能,得出阻燃剂可以提升涤纶面料的阻燃性,同时会对颜色有一定的影响,卤素系阻燃剂3%-6% o.w.f或磷系阻燃剂在用量6%可以较好的阻燃效果,达到汽车内饰材料的燃烧特性GB 8410-2006的要求。
关键词:汽车内饰;涤纶;浴中阻燃剂;阻燃测试1.前言目前涤纶面料在汽车座椅和顶棚类的内饰材料中占有很大的比例,主要由于涤纶纤维优良的物理性能决定的,涤纶拥有非常出色的尺寸安定性,较高的强度,耐腐蚀性和耐热性能,涤纶纤维软化点在230-240℃,熔点在257-260℃,相比较其他常用纤维,这是非常好的数据。
但涤纶纤维的极限氧指数(LOI)在21左右,而空气中的氧气含量也在21左右,也就是涤纶纤维的本身是没有足够阻燃性能的,而汽车内饰对阻燃的要求是非常高的,所以作为汽车内饰的涤纶面料在加工过程中会添加阻燃剂,以提供涤纶面料的阻燃性能,主要通过后续几种工艺进行添加,涤纶在纺丝的前添加阻燃剂,通过混炼进入涤纶粒子,加工成的涤纶面料就有比较好的阻燃效果,而且是耐久型的,可进行多次水洗,仍保持很好的阻燃效果;通过涤纶染色时伴随染料,同时上染到涤纶面料上,加工后会具有较好的阻燃效果,同时也有很好的耐水洗性,但会随着水洗的次数,阻燃效果缓慢下降;在涤纶定型过程中加入,有两大类阻燃剂,一类是盐类的阻燃剂,阻燃效果比较好,但没有耐水洗性,水洗后阻燃效果会消失,另一类是酯类的阻燃剂,也具有较好的阻燃效果,同时具有一定的耐水洗性;通过涂层的方法,使用阻燃剂混合树脂,调配均匀后涂层到涤纶面料的背面,可以达到较好的阻燃效果,同时可以增强面料的强度和耐磨耗性本试验主要讨论在涤纶染色中添加阻燃剂的工艺,比较两种不同类型的阻燃剂性能,及其对染色加工工艺的影响。
2.试验2.1试验用材料汽车内饰用面料(100%涤纶);分散染料黄/红/蓝 UNSE (Ciba 染料);分散染料Blue79(浙江闰土);pH稳定剂AD-45(苏州维明化工);分散均染剂(苏州维明化工);浴中阻燃剂T-888(磷系);浴中阻燃剂T-889(卤素系)2.2试验用仪器高温甘油染色机(厦门瑞比);实验室用定型机(Rapid);电脑测色仪SF600 PLUS-CT (Data-color);水平阻燃测试仪(南京江宁仪器)2.3试验加工工艺工艺流程:染色--水洗--定型染色(高温甘油染色机)分散黄 UNSE 0.07% o.w.f分散红 UNSE 0.14% o.w.f分散蓝 UNSE 0.18% o.w.f浴中阻燃剂 3% 6% 9% 12% o.w.f分散均染剂 1 g/LpH稳定剂AD-45 2 g/L(pH = 4.5)浴比 1:20130℃ x 45 min定型(实验室用定型机)165℃ x 2min2.4 测试与评级方法2.4.1 颜色测试颜色测试使用电脑测色仪进行测试。
3C认证汽车座椅及座椅头枕产品强制性认证实施规则

编号:CNCA—02C—063:2005 机动车辆产品强制性认证实施规则汽车座椅及座椅头枕产品2005-10-10发布 2005-12-01实施国家认证认可监督管理委员会发布目录1.适用范围2.认证模式3. 认证的基本环节4. 认证实施的基本要求4.1 认证的委托和受理4.2型式试验4.3初始工厂审查4.4认证结果评价与批准4.5 获证后监督5. 认证证书5.1认证证书的有效性5.2认证证书的变更5.3认证证书的暂停、注销和撤消6. 强制性产品认证标志的使用6.1准许使用的标志样式6.2变形认证标志的使用6.3加施方式6.4加施位置7. 收费附件1 认证委托时需提交的文件资料附件2 检测项目和检测依据附件3 强制性认证工厂质量保证能力要求1. 适用范围本规则适用于M、N类汽车的座椅产品(但不适用于折叠式座椅、侧向座椅、后向座椅和M2、M3类客车中A级、I级客车使用的座椅)及M1类车辆的前排外侧座椅头枕产品。
2. 认证模式型式试验+初始工厂审查+获证后监督3. 认证的基本环节3.1认证的委托和受理3.2型式试验3.3初始工厂审查3.4认证结果评价与批准3.5获证后监督(抽样)4. 认证实施的基本要求4.1认证的委托和受理4.1.1认证的单元划分同一生产厂生产的且在以下主要方面无差异的汽车座椅及座椅头枕产品视为同一单元:1)座椅总成的结构及形状,允许座椅护面的材料及颜色不同;2)座椅软垫和骨架总成的位移调节、锁止装置等零部件的结构、材料及尺寸;3)座椅软垫的结构和材料;4)座椅总成固定装置的结构;5)头枕骨架和泡沫的结构、尺寸及材料,允许头枕护面的材料和颜色不同;6)头枕连接件的结构和材料。
4.1.2认证委托时需提交的文件资料见附件1。
4.2 型式试验4.2.1型式试验的送样4.2.1.1型式试验送样的原则认证单元中只有一个型号的,送本型号的样品。
以多于一个型号的产品为同一认证单元委托认证时,应由认证机构从中选取具有代表性的一个型号,其他型号需要时作差异试验。
汽车内饰材料燃烧标准的对比分析研究
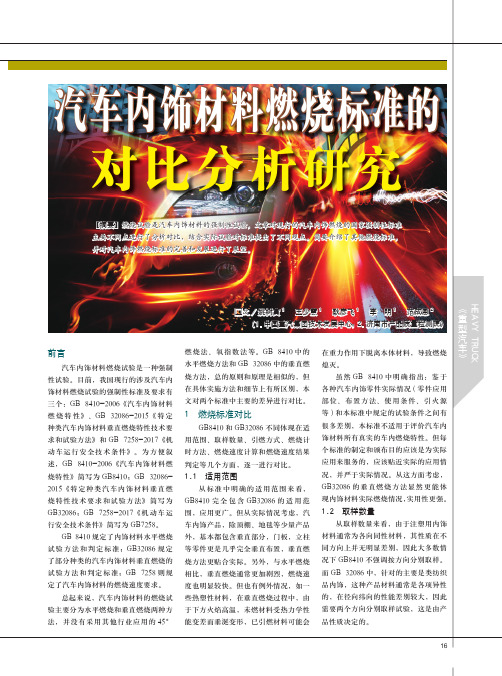
HEAVY TRUCK《重型汽车》16汽车内饰材料燃烧标准的对比分析研究【摘要】燃烧试验是汽车内饰材料的强制性试验,文章对现行的汽车内饰燃烧的国家强制性标准主要不同点进行了分析对比,结合实际试验对标准提出了不同观点。
简要介绍了其他燃烧标准,并对汽车内饰燃烧标准的完善和发展进行了展望。
□文/姚树寅1 王少慧1 耿彦飞1 李 明1 范成恩2(1.中国重汽集团技术发展中心;2.济南市产品质量检测院)前言汽车内饰材料燃烧试验是一种强制性试验。
目前,我国现行的涉及汽车内饰材料燃烧试验的强制性标准及要求有三个:GB 8410-2006《汽车内饰材料燃烧特性》、GB 32086-2015《特定种类汽车内饰材料垂直燃烧特性技术要求和试验方法》和GB 7258-2017《机动车运行安全技术条件》。
为方便叙述,GB 8410-2006《汽车内饰材料燃烧特性》简写为GB8410;GB 32086-2015《特定种类汽车内饰材料垂直燃烧特性技术要求和试验方法》简写为GB32086;GB 7258-2017《机动车运行安全技术条件》简写为GB7258。
GB 8410规定了内饰材料水平燃烧试验方法和判定标准;GB32086规定了部分种类的汽车内饰材料垂直燃烧的试验方法和判定标准;GB 7258则规定了汽车内饰材料的燃烧速度要求。
总起来说,汽车内饰材料的燃烧试验主要分为水平燃烧和垂直燃烧两种方法,并没有采用其他行业应用的45°燃烧法、氧指数法等。
GB 8410中的水平燃烧方法和GB 32086中的垂直燃烧方法,总的原则和原理是相似的,但在具体实施方法和细节上有所区别,本文对两个标准中主要的差异进行对比。
1 燃烧标准对比GB8410和GB32086不同体现在适用范围、取样数量、引燃方式、燃烧计时方法、燃烧速度计算和燃烧速度结果判定等几个方面,逐一进行对比。
1.1 适用范围从标准中明确的适用范围来看,GB8410完全包含GB32086的适用范围,应用更广。
GB 8410与GB 7258中内饰材料试验存在的问题与建议
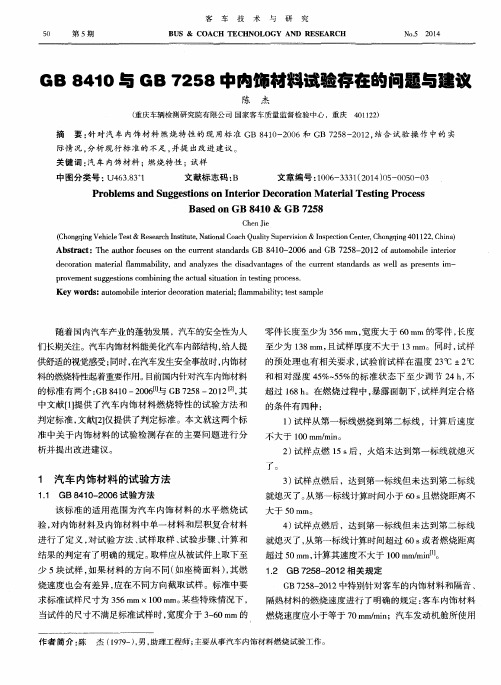
的标 准有两个 : G B 8 4 1 0 — 2 0 0 6 [ ‘ J 一 与G B 7 2 5 8— 2 0 1 2 圜 , 其
中文献[ 1 】 提供 了汽 车 内饰 材料燃烧 特性 的试 验方法 和 判定标准 , 文献 [ 2 】 仅提供 了判定标准 。本文就 这两个 标
的条件有 四种 :
p r o v e me n t s u g g e s t i o n s c o mb i n i n g t h e a c t u a l s i t u a t i o n i n t e s t i n g p r o c e s s .
Ke y wo r ds : a u t o mo b i l e i n t e r i o r d e c o r a t i o n ma t e r i a l ; l f a mma b i l i t y ; t e s t s a mp l e
随着 国内汽车产业 的蓬勃发展 ,汽车的安全 陛为人 们长期关注。汽车内饰材料能美化汽车内部结构 , 给人提
零件长度 至少 为 3 5 6 m l q ' l , 宽度大 于 6 0 m i l l 的零件 , 长度
至少为 1 3 8 m m, 且试 样厚度不大 于 1 3 mm。同时 , 试 样
4 ) 试样点燃 后 ,达到第一标 线但未 达到第二 标线
供舒适 的视觉感受 ; 同时, 在汽车发生安全事故时 , 内饰材
料的燃烧特 陛起着重要作用。 目前国内针对汽车 内饰材料
的预处 理也有相关要 求 , 试验前试 样在 温度 2 3 o C± 2  ̄ C
和相对湿 度 4 5 %~ 5 5 %的标 准状态 下至少 调节 2 4 h , 不 超过 1 6 8 h 。在燃烧 过程 中 , 暴露面朝下 , 试样判定合 格
2017 - 汽车内饰材料阻燃性能
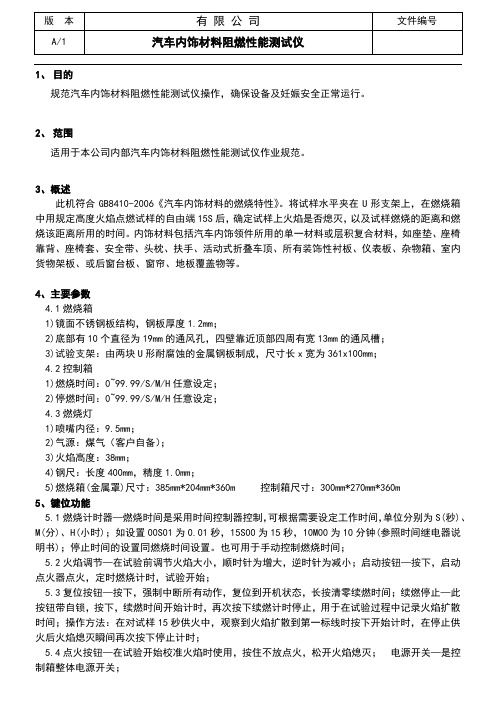
1、目的规范汽车内饰材料阻燃性能测试仪操作,确保设备及妊娠安全正常运行。
2、范围适用于本公司内部汽车内饰材料阻燃性能测试仪作业规范。
3、概述此机符合GB8410-2006《汽车内饰材料的燃烧特性》。
将试样水平夹在U形支架上,在燃烧箱中用规定高度火焰点燃试样的自由端15S后,确定试样上火焰是否熄灭,以及试样燃烧的距离和燃烧该距离所用的时间。
内饰材料包括汽车内饰领件所用的单一材料或层积复合材料,如座垫、座椅靠背、座椅套、安全带、头枕、扶手、活动式折叠车顶、所有装饰性衬板、仪表板、杂物箱、室内货物架板、或后窗台板、窗帘、地板覆盖物等。
4、主要参数4.1燃烧箱1)镜面不锈钢板结构,钢板厚度1.2mm;2)底部有10个直径为19mm的通风孔,四壁靠近顶部四周有宽13mm的通风槽;3)试验支架:由两块U形耐腐蚀的金属钢板制成,尺寸长x宽为361x100mm;4.2控制箱1)燃烧时间:0~99.99/S/M/H任意设定;2)停燃时间:0~99.99/S/M/H任意设定;4.3燃烧灯1)喷嘴内径:9.5mm;2)气源:煤气(客户自备);3)火焰高度:38mm;4)钢尺:长度400mm,精度1.0mm;5)燃烧箱(金属罩)尺寸:385mm*204mm*360m 控制箱尺寸:300mm*270mm*360m5、键位功能5.1燃烧计时器—燃烧时间是采用时间控制器控制,可根据需要设定工作时间,单位分别为S(秒)、M(分)、H(小时);如设置00S01为0.01秒,15S00为15秒,10M00为10分钟(参照时间继电器说明书);停止时间的设置同燃烧时间设置。
也可用于手动控制燃烧时间;5.2火焰调节—在试验前调节火焰大小,顺时针为增大,逆时针为减小;启动按钮—按下,启动点火器点火,定时燃烧计时,试验开始;5.3复位按钮—按下,强制中断所有动作,复位到开机状态,长按清零续燃时间;续燃停止—此按钮带自锁,按下,续燃时间开始计时,再次按下续燃计时停止,用于在试验过程中记录火焰扩散时间;操作方法:在对试样15秒供火中,观察到火焰扩散到第一标线时按下开始计时,在停止供火后火焰熄灭瞬间再次按下停止计时;5.4点火按钮—在试验开始校准火焰时使用,按住不放点火,松开火焰熄灭;电源开关—是控制箱整体电源开关;6、试验方法与要求6.1试样选择:试样的厚度为零件厚度,但不超过12mm。
- 1、下载文档前请自行甄别文档内容的完整性,平台不提供额外的编辑、内容补充、找答案等附加服务。
- 2、"仅部分预览"的文档,不可在线预览部分如存在完整性等问题,可反馈申请退款(可完整预览的文档不适用该条件!)。
- 3、如文档侵犯您的权益,请联系客服反馈,我们会尽快为您处理(人工客服工作时间:9:00-18:30)。
精品文档交流 GB 8410-2006 汽车内饰材料的燃烧特性
阻燃材料事业部GB8410-2006汽车内饰标准 发布于:2009-7-12 被浏览 1800 次 【打印】 【关闭】 GB 8410-2006 (代替GB 8410-1994) 前 言 本标准的第3章、第4章为强制性的,其余为推荐性的。 本标准对应于美国联邦机动车辆安全标准FMVSS 571.302《汽车内饰材料的燃烧特性》,本标准与FMVSS 571.302《汽车内饰材料的燃烧特性》一致性程度为非等效。 本标准代替GB 8410-1994《汽车内饰材料的燃烧特性》。 本标准与GB 8410-1994标准相比,主要变化如下: ——根据GB 3730.1-2001标准的要求,修改了第1章中汽车分类方法; ——按照GB/T 1.1-2000标准的要求,修改了第2章中术语部分的编排方式,并增加了英文内容; ——修改了层积复合材料定义,见2.2条; ——完善了内饰材料的定义,加宽了内饰材料的定义范围,见2.5条; ——修改了第3章的技术要求,取消了原标准技术要求中的3.1条及3.3条,将其内容体现在4.6条中; ——修改了试验用热源的要求,见4.2.4条; ——增加了零件弯曲无法制得平整试样时的试验要求,见4.3.2条; ——增加了零件形状和尺寸不符合取样要求时如何制备试样的要求,见第4.3.2条; ——增加了零件厚度不均时的取样要求,见第4.3.2条; ——增加了取样示例并附图示,见第4.3.2条; ——修改了试验程序中表面起毛试样试验前梳理的方向,见第4.4.1条; ——增加了试样慢燃时的试验方法,见第4.4.9条; ——增加了结果表示的内容,见第4.6条。 本标准由国家发展和改革委员会提出。 本标准由全国汽车标准化技术委员会归口。 本标准由中国第一汽车集团公司技术中心负责起草。 本标准主要起草人:王清国、李菁华。 本标准所代替标准的历次版本发布情况为: ——GB 8410-1987、GB 8410-1994。 GB 8410-2006 汽车内饰材料的燃烧特性 Flammability of automotive interior materials 1 范围 本标准规定了汽车内饰材料水平燃烧特性的技术要求及试验方法。 本标准适用于汽车内饰材料水平燃烧特性的评定。 鉴于各种汽车内饰零件实际情况(零件应用部位、布置方法、使用条件、引火源等)和本 精品文档交流
标准中规定的试验条件之间有许多差别,本标准不适用于评价汽车内饰材料所有真实的车内燃烧特性。 2 术语和定义 2.1 燃烧速度 burning rate 按本标准规定测得的燃烧距离与燃烧此距离所用时间的比值,单位为毫米每分钟(mm/min)。 2.2 层积复合材料 composite material 若干层相似或不同材料,其表面之间由熔接、粘接、焊接等不同方法使全面紧密结合在一起的材料。 2.3 单一材料 exclusive material 由同种材料构成的均匀的整体材料。 若不同材料断续连接在一起(例如缝纫、高频焊接、铆接),这种材料应认为不是层积复合材料,每种材料均属单一材料。 2.4 暴露面 exposed side 零件装配在车内面向乘员的那一面。 2.5 内饰材料 interior materials 汽车内饰零件所用的单一材料或层积复合材料,如座垫、座椅靠背、座椅套、安全带、头枕、扶手、活动式折叠车顶、所有装饰性衬板(包括门内护板、侧围护板、后围护板、车顶棚衬里)、仪表板、杂物箱、室内货架板或后窗台板、窗帘、地板覆盖层、遮阳板、轮罩覆盖物、发动机罩覆盖物和其他任何室内有机材料,包括撞车时吸收碰撞能量的填料、缓冲装置等材料。 3 技术要求 内饰材料的燃烧特性必须满足以下技术要求: 燃烧速度不大于100 mm/min。 4 试验方法 4.1 原理 将试样水平地夹持在U形支架上,在燃烧箱中用规定高度火焰点燃试样的自由端15 s后,确定试样上火焰是否熄灭,或何时熄灭,以及试样燃烧的距离和燃烧该距离所用时间。 4.2 试验装置及器具 4.2.1 燃烧箱 燃烧箱用钢板制成,结构示意图见图1,尺寸见图2。 燃烧箱的前部设有一个耐热玻璃观察窗,该窗可整块盖住前面,也可做成小型观察窗。 燃烧箱底部设10个直径为19 mm的通风孔,四壁靠近顶部四周有宽13 mm的通风槽。整个燃烧箱由4只高10 mm的支脚支承着。在燃烧箱顶部设有安插温度计的孔,此孔设在顶部靠后中央部位,中心距后面板内侧20 mm。 燃烧箱一端设有可封闭的开孔,此处可放人装有试样的支架,另一端则设一个小门,门上有通燃气管用的小孔,支撑燃气灯的支座及火焰高度标志板。 精品文档交流
燃烧箱底部设有一只用于收集熔融滴落物的收集盘(见图3)。此盘放置在两排通风孔之间而又不影响通风孔的通风。 4.2.2 试样支架 试样支架由两块U形耐腐蚀金属板制成的框架组成,尺寸见图4。 支架下板装有6只销子,上板相应设有销孔,以保证均匀夹持试样,同时销子也作为燃烧距离的起点(第一标线)和终点(第二标线)的标记。 另一种支架的下板不仅设有6只销子,而且支架下板布有距离为25 mm的耐热金属支承线,线径0.25 mm(见图5),该种支架在特定情况下使用。 安装后的试样底面应在燃烧箱底板之上178 mm。试样支架前端距燃烧箱的内表面距离应为22 mm,试验支架两纵外侧离燃烧箱内表面距离为50 mm(见图2和图4)。 4.2.3 燃气灯 燃气灯是试验用火源,燃气灯喷嘴内径为9.5 mm,其阀门结构应易于控制火焰高度,并易于调整火焰高度。 当燃气灯置于燃烧箱内时,其喷嘴口部中心处于试样自由端中心以下19 mm处(见图2)。 4.2.4 燃气 为保证试验结果的可比性,供给燃气灯试验用可燃性气体最好使用液化气,也可采用燃烧后热值约为35 MJ/m3~38 MJ/m3的其他可燃气体,例如天然气、城市煤气等。 当进行仲裁试验时,推荐使用液化气。 4.2.5 金属梳 金属梳的长度至少为110 mm,每25 mm内有7~8个光滑圆齿。 4.2.6 秒表 测量时间所用秒表准确度不低于0.5 s。 4.2.7 温度计 温度计量程应为150℃以上,准确度为1℃。 4.2.8 钢板尺 钢板尺量程400 mm 以上,准确度1 mm。 4.2.9 通风橱 燃烧箱应放在通风橱中,通风橱内部容积为燃烧箱体积的20倍~110倍,而且通风橱的长、宽、高的任一尺寸不得超过另外两尺寸中任一尺寸的2.5倍。 在燃烧箱最终确定位置的前后各100 mm处测量空气流过通风橱的垂直速度,该速度应在0.10 m/s~0.30 m/s之间。 4.3 试样 4.3.1 形状和尺寸 标准试样形状和尺寸见图6。试样的厚度为零件厚度,但不超过13 mm。 以不同种类材料进行燃烧性能比较时,试样必须具有相同尺寸(长、宽、厚)。通常取样时必须使试样沿全长有相同的横截面。 当零件的形状和尺寸不足以制成规定尺寸的标准试样时,则应保证下列最小尺寸试样,但要记录: a) 如果零件宽度介于3 mm~60 mm,长度应至少为356 mm。在这种情况下试样要尽量做成接近零件的宽度。 b) 如果零件宽度大于60 mm,长度应至少为138 mm。此时,可能的燃烧距离相当于从第一标线到火焰熄灭时的距离或从第一条标线开 精品文档交流
始至试样末端的距离。 c) 如果零件宽度介于3 mm~60 mm,且长度小于356 mm或零件宽度大于60 mm,长度小于138mm,则不能按本标准试验;宽度小于3 mm的试样也不能按本标准进行试验。 4.3.2 取样 应从被试零件上取下至少5块试样。如果沿不同方向有不同燃烧速度的材料,则应在不同方向截取试样,并且要将5块(或更多)试样在燃烧箱中分别试验。取样方法如下: a) 当材料按整幅宽度供应时,应截取包含全宽并且长度至少为500 mm的样品,并将距边缘100 mm的材料切掉,然后在其余部分上彼此等距、均匀取样。 b) 若零件的形状和尺寸符合取样要求,试样应从零件上截取。 c) 若零件的形状和尺寸不符合取样要求,又必须按本标准进行试验,可用同材料同工艺制作结构与零件一致的标准试样(356mm×l00mm),厚度取零件的最小厚度且不得超过13 mm进行试验。此试验结果不能用于鉴定、认证等情况,且必须在试验报告中注明制样情况。 d) 若零件的厚度大于13 mm,应用机械方法从非暴露面切削,使包括暴露面在内的试样厚度为13 mm。 e) 若零件厚度不均匀一致,应用机械方法从非暴露面切削,使零件厚度统一为最小部分厚度。 f) 若零件弯曲无法制得平整试样时,应尽可能取平整部分,且试样拱高不超过13 mm;若试样拱高超过13 mm,则需用同材料同工艺制作结构与零件一致的标准试样(356 mm×l00 mm),厚度取零件的最小厚度且不得超过13 mm进行试验。 g) 层积复合材料应视为单一材料进行试验,取样方法同上。 h) 若材料是由若干层叠合而成,但又不属于层积复合材料,则应由暴露面起13 mm厚之内所有各层单一材料分别取样进行试验,取样示例见图7。 如图7所示,材料A与材料B之间分界面未粘接,材料A单独进行试验。材料B在厚度13 mm以内,且与材料C紧密结合,所以材料B、C应作为层积复合材料,切取13 mm进行试验。 4.3.3 预处理 试验前试样应在温度23℃±2℃和相对湿度45%~55%的标准状态下状态调节至少24 h,但不超过168 h。 4.4 试验步骤 4.4.1 将预处理过的试样取出,把表面起毛或簇绒的试样平放在平整的台面上,用符合4.2.5规定的金属梳在起毛面上沿绒毛相反方向梳两次。 4.4.2 在燃气灯的空气进口关闭状态下点燃燃气灯,将火焰按火焰高度标志板调整,使火焰高度为38 mm。在开始第一次试验前,火焰应在此状态下至少稳定地燃烧1 min,然后熄灭。 4.4.3 将试样暴露面朝下装入试样支架。安装试样使其两边和一端被U形支架夹住,自由端与U形支架开口对齐。当试样宽度不足,U形支架不能夹住试样,或试样自由端柔软和易弯曲会造成不稳定燃烧时,才将试样放在带耐热金属线的试样支架上进行燃烧试验。 4.4.4 将试样支架推进燃烧箱,试样放在燃烧箱中央,置于水平位置。在燃气灯空气进