汽车内饰材料的分类及燃烧特性
汽车内饰材料的分类及燃烧特性分析
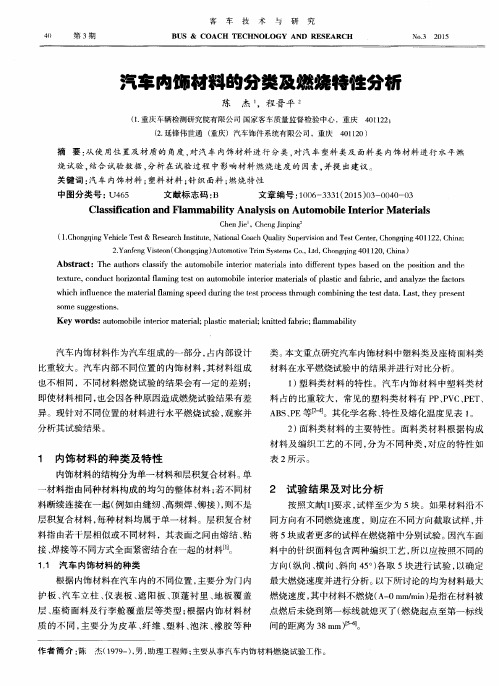
异 。现针对不 同位置的材料进行水平 燃烧试验 , 观察并
分析其试验结果 。
1 内饰 材 料 的种 类及 特 性
内饰材料的结构分 为单一材料和层积复合材料 。 单
一
表 2所 示
材料指 由同种 材料构成 的均匀 的整 体材料 ; 若不 同材
2 试 验 结 果 及 对 比分 析
按照文献 【 1 】 要求 , 试样至少 为 5 块 。如果材料沿不
C h e n J i e ,C h e n g J i n p i n g  ̄
( 1 . C h o n g q i n g V e h i c l e T e s t &R e s e a r c h I n s t i t u t e . N a t i o n a l C o a c h Q u a l i t y S u p e r v i s i o n a n d T e s t C e n t e r . C h o n g q i n g 4 0 1 1 2 2 . C h i n a ;
同方 向有不 同燃 烧速度 ,则应在不 同方 向截 取试样 , 并 将5 块 或者更多的试样在燃 烧箱 中分别试验 。 因汽车面 料 中的针织面料包含 两种编织二 r 艺, 所 以应按 照不 同的
关键 词 : 汽 车 内饰材 料 ; 塑 料 材料 : 针 织 面料 ; 燃 烧 特 性
中图分类号 : U4 6 5
文献标 志码 : B
文章编 号 : 1 0 0 6 — 3 3 3 1 ( 2 0 1 5 ) 0 3 — 0 0 4 0 — 0 3
Cl a s s i ic f a t i o n a nd Fl a mma b i l i t y Ana l y s i s o n Aut o mo b i l e I nt e r i o r Ma t e ia r l s
MVSS302汽车内饰材料的燃烧特性标准
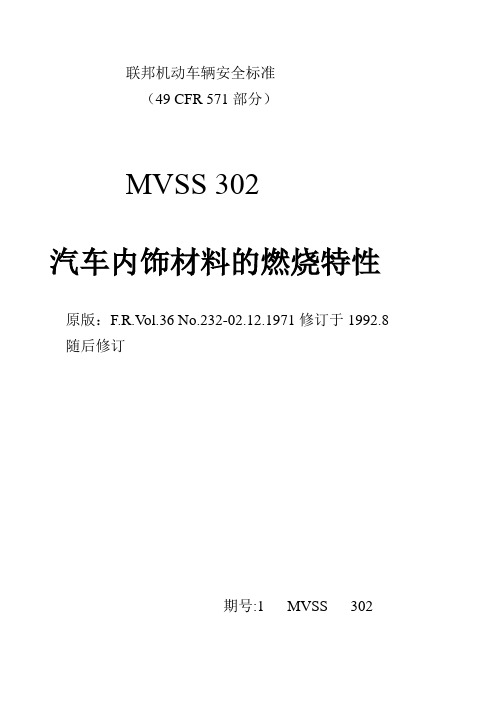
联邦机动车辆安全标准(49 CFR 571部分)MVSS 302汽车内饰材料的燃烧特性原版:F.R.V ol.36 No.232-02.12.1971修订于1992.8 随后修订期号:1 MVSS 302国家:U.S.A原版:F.R.V ol.36No.232-02.12.1971§571.302 标准No.302;汽车内饰材料的燃烧特性S1. 范围本标准指定了用于汽车内舱材料的抗燃性要求。
S2. 目的本标准的目的是为了减少因汽车起火特别是由于汽车内部因火柴或香烟所引起的起火而引起的伤亡。
S3. 应用本标准适用于轿车、多用途轿车、卡车和公共汽车。
S3A. 定义车内气室即汽车内舱内盛满新鲜空气的部分。
S4 要求S4.1 S4.2部分所描述的以下汽车内舱部分与S4.3部分的要求是一致的,汽车坐垫、座椅靠背、安全带、顶蓬、扶手、所有装饰性衬板包括门前、门后和侧边面板、搁板、弹性头垫、地板、遮阳板、窗帘、遮阳物、车轮外罩、发动机罩,垫罩和其他任何室内材料包括撞车时吸收碰撞能量的填料、缓冲装置等材料。
S4.1.1 [保留]S4.2 位于内舱气室的1/2英寸的单一材料或层积复合材料的任何部分应满足S4.3部分的要求。
S4.2.1完全不与其他材料相连接的材料在单独试验时应满足S4.3.S4.2.2 与其他材料完全相连接的材料在作为层积复合材料试验时应满足S4.3的要求。
见I83的示例说明。
材料A和B之间的分界面未粘接,材料A应单独进行试验,位于内舱气室的B材料厚度在1/2英寸内,材料B和材料C紧密结合,因此B和C是作为层积复合材料,切取材料C如图所示,厚度为1/2英寸。
S4.3 (a)当按S5试验时,S4.1和S4.2所描述的材料不会燃烧,也不会使火焰前端以4英寸每分钟的速度通过其表面。
无论如何,集中火焰前端的传递不适用于按照S5试验所切割的样品。
(b)如果材料从试验计时开始,60s内停止燃烧,且从开始计时点处的燃烧距离不大于2英寸,被认为满足S4.3(a)的燃烧速率要求。
GB 8410汽车内饰材料的燃烧特性

G B8410-200 6汽车内饰材料的燃烧特性阻燃材料事业部GB8410-2006汽车内饰标准发布于:2009-7-12 被浏览1800 次【打印】【关闭】GB 8410-2006 (代替GB 8410-1994)前言本标准的第3章、第4章为强制性的,其余为推荐性的。
本标准对应于美国联邦机动车辆安全标准FMVSS 571.302《汽车内饰材料的燃烧特性》,本标准与FMVSS571.302《汽车内饰材料的燃烧特性》一致性程度为非等效。
本标准代替GB 8410-1994《汽车内饰材料的燃烧特性》。
本标准与GB 8410-1994标准相比,主要变化如下:——根据GB 3730.1-2001标准的要求,修改了第1章中汽车分类方法;——按照GB/T 1.1-2000标准的要求,修改了第2章中术语部分的编排方式,并增加了英文内容;——修改了层积复合材料定义,见2.2条;——完善了内饰材料的定义,加宽了内饰材料的定义范围,见2.5条;——修改了第3章的技术要求,取消了原标准技术要求中的3.1条及3.3条,将其内容体现在4.6条中;——修改了试验用热源的要求,见4.2.4条;——增加了零件弯曲无法制得平整试样时的试验要求,见4.3.2条;——增加了零件形状和尺寸不符合取样要求时如何制备试样的要求,见第4.3.2条;——增加了零件厚度不均时的取样要求,见第4.3.2条;——增加了取样示例并附图示,见第4.3.2条;——修改了试验程序中表面起毛试样试验前梳理的方向,见第4.4.1条;——增加了试样慢燃时的试验方法,见第4.4.9条;——增加了结果表示的内容,见第4.6条。
本标准由国家发展和改革委员会提出。
本标准由全国汽车标准化技术委员会归口。
本标准由中国第一汽车集团公司技术中心负责起草。
本标准主要起草人:王清国、李菁华。
本标准所代替标准的历次版本发布情况为:——GB 8410-1987、GB 8410-1994。
汽车内饰物燃烧标准

汽车内饰件阻燃标准等级汽车内饰阻燃标准主要由国家或汽车制造商发布,其中大部分标准的测试方法都是比较接近,主要关注内饰材料的易燃性和燃烧速率,只要不超过一定的燃烧速率(一般为102mm/min)时,都是允许在汽车内使用的。
取样测试的部位为汽车内暴露面向下13mm内的单层或者复合层材料,若每层可以分离则需要单独测试。
内饰材料燃烧标准GB8410 - 汽车内饰材料的燃烧特性。
GB8410标准规定了汽车内饰材料水平火钳特性的技术要求及试验方法。
GB8410标准适用于汽车内饰材料水平燃烧特性的评定。
内饰材料不燃烧、可以燃烧但燃烧速度不大于100mm/min、火焰在60s内自行熄灭且燃烧距离不大于50mm。
燃烧速度:测得的燃烧距离与燃烧此距离所用时间的比值,单位为毫米每分钟(mm/min)。
从保证乘员安全的角度来讲,不燃烧当然是最好,而燃烧速度能够靠材料本身保证在一定的范围之内,也可以为乘员提供一定的生存时间和逃生的时间。
在实际的试验操作过程中,是以在规定时间内不能引燃或在第一个标志柱之前自行熄灭的视为不燃烧。
汽车内饰材料阻燃标准FMVSS302主要适用于汽车内饰材料的阻燃测试,UL94是广泛适用于塑料材料的阻燃测试。
针对产品用途范围不一样,且测试方法和要求也不一样。
不易燃。
医用防护服采用不易燃材料,并且离开火焰后燃烧不大于5s,该项目可以采用ZYYQ阻燃性能测试仪设备进行测试,ZYYQ阻燃性能测试仪智能化程度高,符合国家标准GB/T5455-1997《纺织品燃烧性能试验垂直法》,可用于有阻燃要求的服装织物、装饰织物、帐篷织物等阻燃性能的测定。
阻燃海绵由于含可燃的碳氢链段、密度小、比表面积大,未经阻燃处理的聚氨酯海绵是可燃物,遇火会燃烧并分解,产生大量的烟雾,给灭火带来困难。
特别是聚氨酯软泡开孔率较高,可燃成分多,燃烧时由于较高的空气流通性而源源不断地供给氧气,易燃且不易自熄。
聚氨酯海绵的许多应用领域非常广泛,如建筑材料、床垫、家具、保温材料、汽车座垫及内饰材料等,都需达到阻燃要求。
汽车内外饰件塑料材料分类及性能

汽车内外饰件塑料材料分类及性能首先,聚丙烯(PP)是最常用的汽车塑料材料之一,具有良好的韧性、抗冲击性和耐候性,同时还具有较高的耐化学腐蚀性。
聚丙烯制成的内饰件可以用于制造仪表板、门板、中央控制面板等。
聚丙烯也常用于制造外饰件,如车身侧裙板、前后保险杠等。
聚丙烯具有较好的成本效益,而且对环境友好。
其次,聚乙烯(PE)也是一种常用的汽车塑料材料。
聚乙烯具有较高的耐冲击性和拉伸强度,耐化学腐蚀性能也很好。
由聚乙烯制成的内饰件可以用于制造座椅背板、储物箱等。
聚乙烯制成的外饰件主要是车身包围材料、车顶行李架等。
聚乙烯具有较低的成本和较高的耐用性。
聚氯乙烯(PVC)是一种常用的汽车塑料材料,具有较高的耐燃性和耐化学腐蚀性。
PVC制成的内饰件通常用于制造门内饰板、车顶内饰板等。
PVC制成的外饰件主要是车顶包围材料、车顶行李架等。
PVC材料成本相对较低,且可塑性好,容易加工成形。
聚氨酯(PU)是一种具有较高强度和韧性的汽车塑料材料。
聚氨酯制成的内饰件主要用于制造座椅、把手等。
聚氨酯也常用于制造外饰件,如车顶行李架、车顶包围材料等。
聚氨酯具有良好的耐磨性和耐候性。
工程塑料(如ABS、PC、PA等)在汽车内外饰件中也得到广泛应用。
ABS具有较高的耐冲击性和耐磨性,常用于制造仪表板、门板、把手等。
PC具有较高的强度和热稳定性,常用于制造灯具、后视镜壳体等。
PA具有较高的抗拉强度和耐冲击性,常用于制造座椅骨架、储物箱等。
除了上述材料,还有一些特殊的塑料材料也广泛应用于汽车内外饰件中。
例如柔性PVC用于制造汽车座椅面料,聚碳酸酯(PC)用于制造汽车车窗玻璃,三元乙丙橡胶(EPDM)用于汽车密封条等等。
综上所述,汽车内外饰件塑料材料具有多种分类及性能。
不同的材料具有不同的优势和适用性,汽车制造商在选择材料时需要根据具体的需求和功能来选取合适的塑料材料。
GB 8410汽车内饰材料的燃烧特性

GB 8410-2006汽车内饰材料的燃烧特性阻燃材料事业部GB8410-2006汽车内饰标准发布于:2009-7-12被浏览1800次【打印】【关闭】GB 8410-2006(代替GB 8410-1994)前言本标准的第3章、第4章为强制性的,其余为推荐性的。
本标准对应于美国联邦机动车辆安全标准FMVSS571.302《汽车内饰材料的燃烧特性》,本标准与FMVSS571.302《汽车内饰材料的燃烧特性》一致性程度为非等效。
本标准代替GB 8410-1994《汽车内饰材料的燃烧特性》。
本标准与GB 8410-1994标准相比,主要变化如下:——根据GB3730.1-2001标准的要求,修改了第1章中汽车分类方法;——按照GB/T1.1-2000标准的要求,修改了第2章中术语部分的编排方式,并增加了英文内容;——修改了层积复合材料定义,见2.2条;——完善了内饰材料的定义,加宽了内饰材料的定义范围,见2.5条;——修改了第3章的技术要求,取消了原标准技术要求中的3.1条及3.3条,将其内容体现在4.6条中;——修改了试验用热源的要求,见4.2.4条;——增加了零件弯曲无法制得平整试样时的试验要求,见4.3.2条;——增加了零件形状和尺寸不符合取样要求时如何制备试样的要求,见第4.3.2条;——增加了零件厚度不均时的取样要求,见第4.3.2条;——增加了取样示例并附图示,见第4.3.2条;——修改了试验程序中表面起毛试样试验前梳理的方向,见第4.4.1条;——增加了试样慢燃时的试验方法,见第4.4.9条;——增加了结果表示的内容,见第4.6条。
本标准由国家发展和改革委员会提出。
本标准由全国汽车标准化技术委员会归口。
本标准由中国第一汽车集团公司技术中心负责起草。
本标准主要起草人:王清国、李菁华。
本标准所代替标准的历次版本发布情况为:——GB 8410-1987、GB 8410-1994。
GB 8410-2006汽车内饰材料的燃烧特性Flammability of automotive interior materials1范围本标准规定了汽车内饰材料水平燃烧特性的技术要求及试验方法。
汽车内饰材料阻燃性研究

汽车内饰材料阻燃性研究随着汽车的普及和人们对汽车安全的不断关注,汽车内饰材料的阻燃性已经成为了汽车行业研究的热点之一。
汽车内饰材料的阻燃性对于汽车的整体安全性具有重要的影响,因此对汽车内饰材料的阻燃性进行研究具有重要意义。
本文将对汽车内饰材料的阻燃性进行深入研究,并探讨其对汽车安全性的影响,以及未来的研究方向。
一、汽车内饰材料的阻燃性概述汽车内饰材料主要包括座椅、仪表板、地毯、内饰板等,这些材料在汽车中主要起到美观、舒适和保护的作用。
在发生火灾事故时,这些材料往往会成为火灾的燃料,从而使火势蔓延,对车内人员造成伤害。
汽车内饰材料的阻燃性就显得尤为重要。
阻燃性是指材料在遇到明火或者高温时,能够迅速熄灭火势或者延缓火势蔓延的能力。
提高汽车内饰材料的阻燃性,对于提高汽车的安全性具有非常重要的意义。
二、汽车内饰材料的阻燃性研究现状目前,关于汽车内饰材料的阻燃性研究已经取得了一定的进展。
从材料本身的角度来看,目前常用的汽车内饰材料主要包括塑料、皮革、织物等,这些材料在制造时已经考虑到了阻燃性的问题,因此在一定程度上具有阻燃性。
研究人员还通过添加阻燃剂、改变材料的结构等方式,进一步提高了汽车内饰材料的阻燃性能。
在火灾测试中,经过改良的汽车内饰材料可以迅速熄灭火势,减少火灾对车内人员的伤害。
从应用的角度来看,一些汽车制造商也在车辆制造时对内饰材料的阻燃性进行了一定的要求,从而提高了汽车内饰材料的整体阻燃性。
目前对于汽车内饰材料的阻燃性研究还存在着一些问题,比如材料的阻燃性能仍然有待提高,阻燃材料的成本相对较高等。
四、汽车内饰材料阻燃性研究的未来方向汽车内饰材料的阻燃性研究是一个具有挑战性的课题,需要在材料的选择、结构的设计、阻燃剂的添加等方面进行深入研究。
未来,在汽车内饰材料的阻燃性研究方面可以从以下几个方向进行深入研究。
在材料的选择方面,可以研究一些新型的阻燃材料,比如新型聚合物材料、纳米阻燃材料等,这些材料具有良好的阻燃性能,可以用于汽车内饰材料的制造,从而提高汽车内饰材料的整体阻燃性能。
汽车内饰燃烧 报告
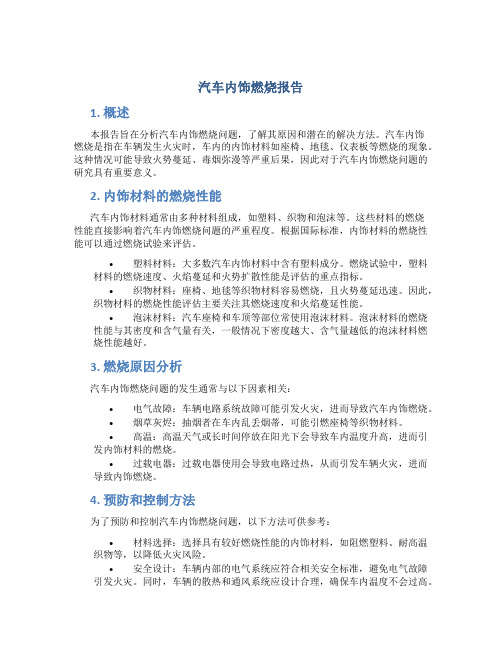
汽车内饰燃烧报告1. 概述本报告旨在分析汽车内饰燃烧问题,了解其原因和潜在的解决方法。
汽车内饰燃烧是指在车辆发生火灾时,车内的内饰材料如座椅、地毯、仪表板等燃烧的现象。
这种情况可能导致火势蔓延、毒烟弥漫等严重后果,因此对于汽车内饰燃烧问题的研究具有重要意义。
2. 内饰材料的燃烧性能汽车内饰材料通常由多种材料组成,如塑料、织物和泡沫等。
这些材料的燃烧性能直接影响着汽车内饰燃烧问题的严重程度。
根据国际标准,内饰材料的燃烧性能可以通过燃烧试验来评估。
•塑料材料:大多数汽车内饰材料中含有塑料成分。
燃烧试验中,塑料材料的燃烧速度、火焰蔓延和火势扩散性能是评估的重点指标。
•织物材料:座椅、地毯等织物材料容易燃烧,且火势蔓延迅速。
因此,织物材料的燃烧性能评估主要关注其燃烧速度和火焰蔓延性能。
•泡沫材料:汽车座椅和车顶等部位常使用泡沫材料。
泡沫材料的燃烧性能与其密度和含气量有关,一般情况下密度越大、含气量越低的泡沫材料燃烧性能越好。
3. 燃烧原因分析汽车内饰燃烧问题的发生通常与以下因素相关:•电气故障:车辆电路系统故障可能引发火灾,进而导致汽车内饰燃烧。
•烟草灰烬:抽烟者在车内乱丢烟蒂,可能引燃座椅等织物材料。
•高温:高温天气或长时间停放在阳光下会导致车内温度升高,进而引发内饰材料的燃烧。
•过载电器:过载电器使用会导致电路过热,从而引发车辆火灾,进而导致内饰燃烧。
4. 预防和控制方法为了预防和控制汽车内饰燃烧问题,以下方法可供参考:•材料选择:选择具有较好燃烧性能的内饰材料,如阻燃塑料、耐高温织物等,以降低火灾风险。
•安全设计:车辆内部的电气系统应符合相关安全标准,避免电气故障引发火灾。
同时,车辆的散热和通风系统应设计合理,确保车内温度不会过高。
•教育和宣传:加强对车主和乘客的安全教育,提高其对火灾危险的认识,减少火源的产生。
•定期检查:定期检查车辆电气系统和维护电器设备,确保其正常运行,降低电路故障的风险。
•禁止吸烟:车辆内禁止吸烟,以减少烟草灰烬引发火灾的可能性。
- 1、下载文档前请自行甄别文档内容的完整性,平台不提供额外的编辑、内容补充、找答案等附加服务。
- 2、"仅部分预览"的文档,不可在线预览部分如存在完整性等问题,可反馈申请退款(可完整预览的文档不适用该条件!)。
- 3、如文档侵犯您的权益,请联系客服反馈,我们会尽快为您处理(人工客服工作时间:9:00-18:30)。
汽车内饰材料的分类及燃烧特性
汽车内饰材料作为汽车组成的一部分,占内部设计比重较大。
汽车内部不同位置的内饰材料,其材料组成也不相同,不同材料燃烧试验的结果会有一定的差别;即使材料相同,也会因各种原因造成燃烧试验结果有差异。
现针对不同位置的材料进行水平燃烧试验,观察并分析其试验结果。
1内饰材料的种类及特性
内饰材料的结构分为单一材料和层积复合材料。
单一材料指由同种材料构成的均匀的整体材料;若不同材料断续连接在一起(例如由缝纫、高频焊、铆接),则不是层积复合材料,每种材料均属于单一材料。
层积复合材料指由若干层相似或不同材料,其表面之间由熔结、粘接、焊接等不同方式全面紧密结合在一起的材料。
1.1汽车内饰材料的种类
根据内饰材料在汽车内的不同位置,主要分为门内护板、汽车立柱、仪表板、遮阳板、顶蓬衬里、地板覆盖层、座椅面料及行李舱覆盖层等类型;根据内饰材料材质的不同,主要分为皮革、纤维、塑料、泡沫、橡胶等种类。
本文重点研究汽车内饰材料中塑料类及座椅面料
类材料在水平燃烧试验中的结果并进行对比分析。
1)塑料类材料的特性。
汽车内饰材料中塑料类材料占的比重较大,常见的塑料类材料有PP、PVC、PET、ABS、PE等。
2)面料类材料的主要特性。
面料类材料根据构成材料及编织工艺的不同,分为不同种类。
2试验结果及对比分析
按照要求,试样至少为5块。
如果材料沿不同方向有不同燃烧速度,则应在不同方向截取试样,并将5块或者更多的试样在燃烧箱中分别试验。
因汽车面料中的针织面料包含两种编织工艺,所以应按照不同的方向(纵向、横向、斜向45°)各取5块进行试验,以确定最大燃烧速度并进行分析。
以下所讨论的均为材料最大燃烧速度,其中材料不燃烧(A-0mm/min)是指在材料被点燃后未烧到第一标线就熄灭了(燃烧起点至第一标线间的距离为38mm)。
2.1塑料类内饰材料的试验结果
1)塑料类的汽车内饰材料主要用于门内护板、仪表板、立柱、遮阳板、城市客车座椅、行李舱覆盖层、地板覆盖层、客车地板等部位。
2)由于门内护板是由不同材质、不同厚度或不同形状的同种材质的材料焊接而成,因此,将其单独列出进行试验,例如某高配车型的门板划分为上装饰板、嵌饰板、扶手上体总成、扶手饰条、前下体饰板、杂物盒、后下体饰板、吸音棉。
2.2面料类内饰材料的试验结果
面料类内饰材料一般分为真皮、表层为人造革的复合材料和表层为针织面料的复合材料三种。
真皮面料中牛皮应用较广,人造革复合材料中PVC应用较广,针织面料复合材料中涤纶应用较广。
因此,选取以下三种材料进行试验。
2.3试验结果影响因素分析
试验结果显示,以上所有内饰材料的燃烧试验结果均小于100mm/min,符合文献[1]要求。
本文所研究的试验材料都是按不同比例添加了增塑剂、热稳定剂、抗静电剂、抗氧剂、阻燃剂等添加剂的改性材料。
试验结果的具体影响因素如下:
1)单一材料中,各类添加剂的组成比例或阻燃剂添加分量不同,会使得材料的燃烧特性发生变化,导致相同厚度的同种材料燃烧速度
存在较大差别。
2)单一材料中,材料自身的熔点影响燃烧速度,熔点低的材料比熔点高的材料更易燃烧,燃烧速度也更快。
3)层积复合材料中,材料自身的密度及各层材料间粘接的紧密程度也影响燃烧速度。
密度大的材料不易燃烧,密度小的材料容易燃烧,两者粘接在一起,燃烧速度会趋于中间速度。
粘接紧密的复合材料中空气减少,使得材料内部的助燃气体减少,材料更加不易燃烧。
4)层积复合材料中,面料内阻燃剂添加不均匀,会导致材料在试验中燃烧速度时快时慢或中途停止燃烧,整个试验过程无法保持匀速燃烧,使得燃烧结果存在较大差异。
5)层积复合材料中,一层或多层易燃材料的加入,使得原本不燃烧的复合材料变得可燃。
6)层积复合材料中的针织面料,在不同方向上有不同的纹路,导致同一面料在不同方向上的燃烧速度有差异。
因此,必须分别从纵向、横向、斜向45°进行切割取样,以全面反映面料在燃烧时可能出现的不同结果。
3结束语
进行的试验表明,塑料类汽车内饰材料的燃烧过程较为稳定。
发生火灾时,因其燃烧速度较慢,驾乘人员有更多逃生机会;但塑料类材料在燃烧时会产生有毒气体和滴落物,进而对人体造成伤害,因此,建议今后的研究中增加塑料材料燃烧时产生的有毒气体及滴落物的试验;面料类汽车内饰材料中表层为PVC的层积复合材料燃烧过程较为稳定,但燃烧时会产生大量烟雾和有毒气体,影响驾乘人员的视线并对呼吸道造成伤害,因此,建议今后增加该类材料的有毒气体及烟密度试验;对于表层为针织面料的层积复合材料,由于同一面料取样时切割方向不同也会产生不同燃烧速度,使得面料燃烧结果存在较大差异,因此,建议对同一针织面料分别从纵向、横向、斜向45°都至少取样5块,以比较全面地反映实际燃烧状态。