耐磨金属材料的最新研究进展
金属材料力学性能试验方法和试验设备的新进展

目前没计划
GB/T 7314-2005 金属材料 室温压缩试验方法
2005-05-13 2005-10-01 无相应国际标准
2013 年修订,拟采标 ASTM E9-09
GB/T 8358-2006 GB/T 10128-2007 GB/T 13239-2006 GB/T 22315-2008 GB/T 24191-2009 GB/T 24584-2009
金属弯曲力学性能试验方法
1993-06-01 1993-10-01 无相应国际标准
2012 年修订
表 3 金属高温长时试验标准采标及制修订情况
标准编号 GB/T 2039-2012 GB/T 10120-1996
标准名称 金属拉伸蠕变及持久试验方法 金属应力松弛试验方法
批准日期 2012-06-29 1996-09-27
采标情况
1999-03-23 1999-10-01 尚未采标
1998-10-16 1999-08-01 采标 ISO377:1997 2008-05-13 2008-11-01 采标 ISO 23718:2007 2009-06-25 2010-04-01 采标 ISO 25679:2005
制修订计划 暂时没计划(ISO 正在制定国际 标准,待完成后立即转化)
GB/T
24171.2-2009
金属材料 薄板和薄带 成形极限曲线的测定 第 2 部分:实验室成形极限曲线的测定
2009-06-25
2010-04-01 采标 ISO 12004-2:2008 目前没计划
GB/T 24172-2009 GB/T 24183-2009 GB/T 24524-2009 YB/T 5293-2006 GB/T 25047-2010 GB/T 25048-2010
增材制造金属材料的疲劳性能研究进展

第16卷第1期精密成形工程代俊林1,吴世品1,2*,张宇1,王雪娇1,马强3(1.天津职业技术师范大学,天津 300072;2.天津大学现代连接技术实验中心,天津 300350;3.天津金桥焊材集团有限公司,天津 300399)摘要:金属增材制造作为前沿热点制造技术之一,近年来在各种重要工业领域的研究和应用日益广泛。
利用增材制造技术制备金属材料的过程中,不可避免会造成材料表面粗糙、气孔、未熔合等缺陷,虽然工艺技术的改进可以在一定程度上减小缺陷程度,但至今仍无法完全消除这些缺陷。
增材制造金属材料的过程中,缺陷部位通常会成为应力集中源诱发疲劳裂纹的形核,造成金属材料的疲劳寿命下降。
首先从表面质量、内部缺陷及微观结构等方面阐述了增材制造金属材料疲劳性能的影响因素;其次从宏观与微观角度概括了疲劳裂纹萌生/扩展机理的研究现状与进展;总结了热处理、表面优化、电磁辅助以及超声辅助等疲劳延寿技术的研究进展;最后讨论了基于机器学习技术的疲劳寿命评估模型,同时展望了机器学习和人工智能技术在增材制造金属材料领域的应用前景,为推动增材制造金属材料的发展和应用提供了借鉴与参考价值。
关键词:增材制造;金属材料;缺陷;疲劳寿命;疲劳裂纹;疲劳寿命评估DOI:10.3969/j.issn.1674-6457.2024.01.001中图分类号:TG456 文献标志码:A 文章编号:1674-6457(2024)01-0001-14Research Progress on Fatigue Properties of Additive Manufactured Metal MaterialsDAI Junlin1, WU Shipin1,2*, ZHANG Yu1, WANG Xuejiao1, MA Qiang3(1. Tianjin University of Technology and Education, Tianjin 300072, China; 2. Center for Advanced Joining Technology, TianjinUniversity, Tianjin 300350, China; 3. Tianjin Golden Bridge Welding Materials Group Co., Ltd., Tianjin 300399, China)ABSTRACT: Metal additive manufacturing, also known as one of the prominent manufacturing technologies, has garnered sig-nificant attention and has been extensively investigated and used across diverse crucial industrial sectors in recent times. The additive manufacturing method inherently gives rise to various defects, including but not limited to surface roughness, porosity, and lack of fusion. Despite advancement in process technology, it remains unfeasible to entirely eradicate defects, but can reduce defects to a certain amount. During the additive manufacturing of metal materials, the defective parts usually become the source of stress concentration and induce fatigue crack nucleation, resulting in a decrease in the fatigue life of metal materials. The fac-tors affecting the fatigue performance of metals produced by additive manufacturing were described firstly from the surface quality, internal defects, and microstructure. Secondly, the research progress of fatigue crack initiation and expansion mecha-nism was summarized from the macroscopic and microscopic perspectives. Then, the current progress of fatigue life-extension收稿日期:2023-08-26Received:2023-08-26基金项目:天津市教委科研计划项目(2020KJ104)Fund:Tianjin Municipal Education Commission Scientific Research Program Projects (2020KJ104)引文格式:代俊林, 吴世品, 张宇, 等. 增材制造金属材料的疲劳性能研究进展[J]. 精密成形工程, 2024, 16(1): 1-13.DAI Junlin, WU Shipin, ZHANG Yu, et al. Research Progress on Fatigue Properties of Additive Manufactured Metal Materials[J]. Journal of Netshape Forming Engineering, 2024, 16(1): 1-13.*通信作者(Corresponding author)2精 密 成 形 工 程 2024年1月techniques such as heat treatment, surface optimization, electromagnetic-assisted and ultrasonic-assisted techniques were intro-duced. Finally, the fatigue life evaluation model utilizing machine learning technology was further examined, along with the po-tential application of machine learning and artificial intelligence technology in the domain of additive manufacturing of metal materials, providing experience and reference value for advancing the progress and utilization of metal additive manufacturing. KEY WORDS: additive manufacturing; metal materials; defects; fatigue life; fatigue cracks; fatigue life evaluation增材制造(Additive Manufacturing ,AM )作为现代制造领域前沿热点技术之一,是一种通过计算机辅助设备建立数字模型并逐层堆积材料用以完成最终所需产品的现代制造工艺方法[1-2]。
陶瓷金属化的方法机理及影响因素的研究进展

陶瓷金属化的方法机理及影响因素的研究进展化学镀是通过将金属或合金离子溶液与陶瓷材料表面进行化学反应,使金属或合金沉积在表面。
这种方法具有成本低、镀液容易净化和再生等优点,但其沉积的金属镀层摩擦系数较大,抗磨性能较差。
电镀是利用电解方法,在镀液中将金属或合金离子通过电流作用沉积在陶瓷材料表面。
与化学镀相比,电镀的金属镀层精密度更高、致密度更好,具有优良的耐磨性和耐蚀性,但电镀往往需要较高的温度和电流密度,生产过程较复杂。
热浸镀是将陶瓷材料放入预热的金属溶液中,利用热扩散和表面反应的原理,使金属或合金沉积在陶瓷表面。
这种方法简单、效率高,能够获得良好的陶瓷金属化效果,但是金属溶液的温度需要较高,容易造成材料变形。
物理气相沉积是利用化学气相沉积原理,将金属或合金薄膜沉积在陶瓷表面。
这种方法能够获得均匀致密的金属薄膜,具有很好的抗蚀性和导电性能,但其工艺复杂,设备要求较高。
陶瓷金属化的机理多种多样,主要包括物理相互作用、化学反应和扩散等。
物理相互作用主要包括金属颗粒与陶瓷材料表面的物理吸附和机械嵌入等,化学反应则是金属离子与陶瓷材料表面发生化学反应,扩散则是金属原子或离子通过热扩散进入陶瓷材料内部。
影响陶瓷金属化效果的因素主要包括金属离子浓度、温度、时间和陶瓷材料表面状态等。
金属离子浓度越高,金属沉积速度越快,但同时也容易引起局部电解腐蚀;温度对于金属离子的扩散和化学反应有重要影响,过高或过低的温度都会导致金属镀层质量不佳;时间越长,金属沉积层越厚,但是也会引起晶粒生长和断裂等问题;陶瓷材料表面状态的平整度和粗糙度对金属镀层的附着力和均匀性有重要影响。
总之,陶瓷金属化作为一种能够提高陶瓷材料表面性能的方法,具有广泛应用前景。
然而,目前仍存在一些问题需要进一步研究和解决,如镀层的结构与性能之间的关系、镀层的成本与工艺优化等,这些问题的解决将有助于提高陶瓷金属化技术的应用范围和效果。
纳米材料在防腐蚀领域中的应用研究进展

纳米材料在防腐蚀领域中的应用研究进展引言:腐蚀是一种常见而严重的问题,它会导致金属材料的性能下降甚至完全失效。
为了解决这个问题,科学家们一直在不断研究和开发新的防腐蚀技术和材料。
近年来,纳米材料在防腐蚀领域中的应用研究取得了显著的进展。
本文将重点介绍纳米材料在防腐蚀领域中的应用,并对其研究进展进行综述。
一、纳米材料在防腐蚀领域的优势1.增强防护层性能:纳米颗粒可以增加涂层的致密性和硬度,提高防护层的耐磨、耐蚀性能。
2.提高抗腐蚀性能:纳米材料具有较大比表面积和高表面能,可以提供更多的反应活性位点,有效抑制氧化还原反应,从而减缓金属腐蚀的速率。
3.调控物理与化学性质:通过调整纳米材料的组成、形貌和尺寸等特征,可以改变其物理和化学性质,从而实现对防腐蚀行为的调控。
二、纳米涂层在防腐蚀中的应用研究进展1.纳米复合涂层:将纳米颗粒与基础涂层材料复合,通过纳米颗粒的增强作用提高涂层的抗腐蚀性能。
研究表明,纳米复合涂层能够显著延缓金属腐蚀的进程,提高涂层的耐久性。
2.纳米二氧化硅涂层:二氧化硅是一种常见的纳米材料,具有优异的化学稳定性和耐高温性能。
研究发现,纳米二氧化硅涂层能够有效减缓金属腐蚀的速率,提高材料的耐蚀性。
3.纳米氧化铝涂层:氧化铝是一种常见的纳米材料,具有良好的耐腐蚀性能和高温稳定性。
研究表明,纳米氧化铝涂层能够显著提高金属的抗腐蚀性能,延缓腐蚀的发展。
三、纳米颗粒在防腐蚀涂层中的应用研究进展1.纳米金属颗粒:纳米金属颗粒具有高比表面积和丰富的氧化还原反应位点,可以有效阻止金属的腐蚀反应,延缓腐蚀的发展。
研究发现,纳米金属颗粒可以与涂层基质形成复合结构,大大提高涂层的防腐蚀性能。
2.纳米陶瓷颗粒:纳米陶瓷颗粒具有高硬度和良好的耐腐蚀性能,可以有效提高涂层的耐磨、耐腐蚀性能。
研究表明,纳米陶瓷颗粒可以均匀分布在涂层中,形成致密的保护层,提高金属材料的抗腐蚀性能。
3.纳米复合颗粒:通过调控纳米颗粒的成分和比例,可以实现对涂层防腐蚀性能的调控。
金属镍纳米材料研究进展
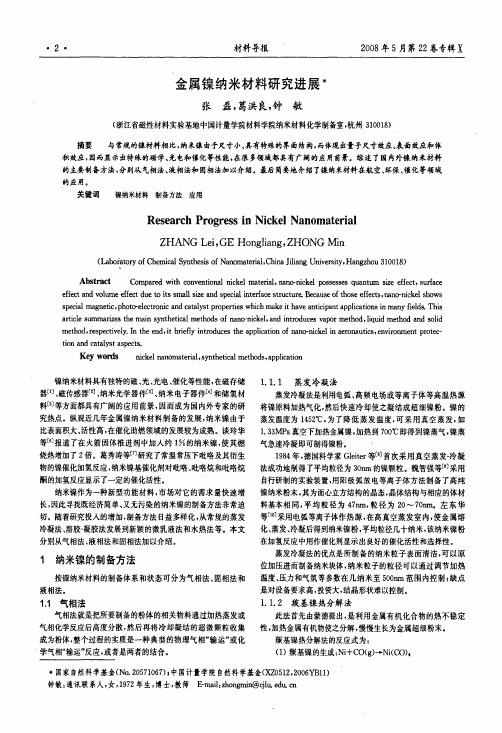
2材料导报2008年5月第22卷专辑X金属镍纳米材料研究进展*张磊,葛洪良,钟敏(浙江省磁性材料实验基地中国计量学院材料学院纳米材料化学制备室,杭州310018)摘要与常规的镍材料相比,纳米镍由于尺寸小、具有特殊的界面结构,而体现出量子尺寸效应、表面效应和体积效应,因而显示出特殊的磁学、光电和催化等性能,在很多领域都具有广阔的应用前景。
综述了国内外镍纳米材料的主要制备方法,分另4从气相法、液相法和固相法加以介绍。
最后简要地介绍了镍纳米材料在航空、环保、催化等领域的应用。
关键词镍纳米材料制备方法应用R ese a r ch Pr ogr es s i n N i ckel N a nom at er i a lZ H A N G Lei,G E H ongl i a ng,ZH O N G M i n(Laboi at or y of C he m i c a l Syn t hes i s of N a nom at e r i al,Chi na J i l iang U ni ver s i t y,H a ngz hou310018)A bs t ract C om par ed w i t h co nvent i on al ni ckel m at e r i al,nano-ni ekel po sses ses quan t um s i ze ef f ect,sur f aceeff ect a nd vol um e ef fect due t o i t s sm a l l s i ze and s peci al i nt erf ace st r uct ur e.B eca use of t h ose ef f ect s,nano-ni ckel s how s s peci al m agn et i c,phot o-e l ect r o ni c and cat al yst pr oper t i es w hi ch m ake i t ha ve ant i ci pant appl i ca t i ons i n m a ny f i elds.T hi sart i cle s um m a r i z es t he m ai n synt he t i cal m et hods of nano-ni ckel,and i nt r oduc es vapor m et h od,l i q ui d m et hod a nd s oli d m et hod,r espect i ve l y.I n t he end,i t br i ef l y i nt r oduc es t he appl i cat i on of nan o-ni ck el i n aer ona ut i cs,e nvi r o nm e nt pr o t ec-t i o n and cat al yst aspects.K ey w or ds ni ckel nano m at er i a l,synt h et i cal m et hods,appl i cat i on镍纳米材料具有独特的磁、光、光电、催化等性能,在磁存储器[1]、磁传感器‘“、纳米光学器件‘引、纳米电子器件叫和储氢材料[5]等方面都具有广阔的应用前景,因而成为国内外专家的研究热点。
金属材料表面微纳加工技术的研究与发展
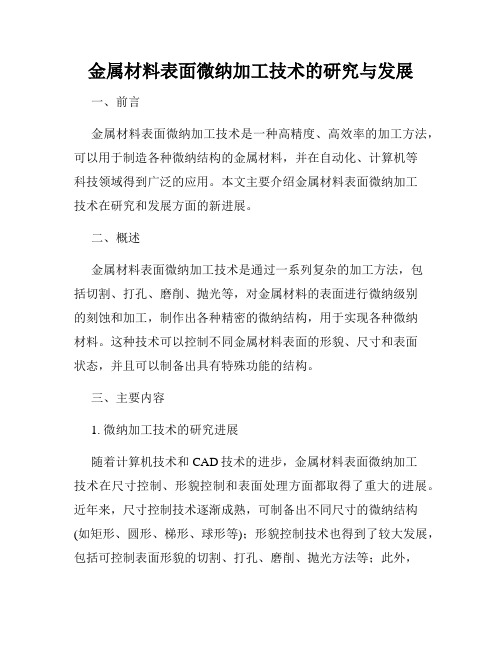
金属材料表面微纳加工技术的研究与发展一、前言金属材料表面微纳加工技术是一种高精度、高效率的加工方法,可以用于制造各种微纳结构的金属材料,并在自动化、计算机等科技领域得到广泛的应用。
本文主要介绍金属材料表面微纳加工技术在研究和发展方面的新进展。
二、概述金属材料表面微纳加工技术是通过一系列复杂的加工方法,包括切割、打孔、磨削、抛光等,对金属材料的表面进行微纳级别的刻蚀和加工,制作出各种精密的微纳结构,用于实现各种微纳材料。
这种技术可以控制不同金属材料表面的形貌、尺寸和表面状态,并且可以制备出具有特殊功能的结构。
三、主要内容1. 微纳加工技术的研究进展随着计算机技术和CAD技术的进步,金属材料表面微纳加工技术在尺寸控制、形貌控制和表面处理方面都取得了重大的进展。
近年来,尺寸控制技术逐渐成熟,可制备出不同尺寸的微纳结构(如矩形、圆形、梯形、球形等);形貌控制技术也得到了较大发展,包括可控制表面形貌的切割、打孔、磨削、抛光方法等;此外,表面处理技术也有较大进展,在光学、生物、信息等领域中有重要应用,如抗反射、耐磨损、防腐蚀等。
2. 微纳加工技术的应用领域金属材料表面微纳加工技术的应用领域非常广泛,包括基础研究和产业应用。
在基础研究方面,用于制造各种精密的微纳结构,和材料性能的表征;在产业应用领域,可以应用于纳米光电子、航空航天、汽车制造、医疗器械、生物工程等领域。
比如,可以制作出高精度的导航设备、激光干涉仪等。
3. 发展趋势未来,金属材料表面微纳加工技术的发展将会更加多样化和复杂化,一些新的材料和纳米结构的出现将会对微纳加工技术的应用提供更多的机会。
同时,由于环境保护和能源危机的问题,向微纳材料制备的绿色和可持续化的发展趋势将会成为研究重点,包括开发新的加工方法,改进原材料的利用和再生等。
为此,需要进一步发展和创新金属材料表面微纳加工技术,把它推向更高的前沿。
四、结论金属材料表面微纳加工技术在尺寸控制、形貌控制和表面处理等方面得到较大的发展,具有广泛的应用领域。
碳纤维增强碳化钨硬质合金的烧结方法和研究进展

碳纤维增强碳化钨硬质合金的烧结方法和研究进展1.引言碳化钨-钴(WC-Co)硬质合金是以碳化钨粉末为主要原料,Co做粘结剂而制成的一种合金。
因碳化钨-Co硬质合金具有高硬度、高强度和优良的耐磨性及抗氧化性,而被广泛的用于机械加工、采矿钻探、模具和结构耐磨件等领域[1]。
超细碳化钨-钴硬质合金是指合金中碳化钨晶粒平均尺寸为0.1~0.6μm,这使其具有高强度、高硬度和高韧性,有效地解决了传统硬质合金硬度与强度之间的矛盾。
碳化钨晶粒在100nm 以下的纳米硬质合金应当有更优良的性能。
1959年,Shindo A首先发明了用聚丙烯腈(PAN)纤维制造碳纤维。
美国在21世纪革命性的12项材料技术中,则将“新一代碳纤维、纳米碳管”排在第四位[2]。
碳纤维具有高强度、高模量、密度小,比强度高、耐高温、耐摩擦、导电、导热、膨胀系数小等优良性能。
正因如此,将碳纤维与树脂、金属、陶瓷等基体复合后得到的碳纤维复合材料,同样具有高的比强度、比模量、耐疲劳、耐高温、抗蠕变等特点。
近年来它们被广泛地应用于航空航天、汽车构件、风力发电叶片、油田钻探、体育用品、建筑补强材料等领域[3]。
超细碳化钨-钴硬质合金和碳纤维在某些方面的优异性能和在工业上的广泛应用,使得国内外很多研究学者对这两种材料进行了深入研究。
本文将主要从超细碳化钨-钴硬质合金的烧结手段及其对硬质合金性能的影响、致密化方式和效果,碳纤维增强复合材料的性能等方面对国内外文献进行综述。
2. 烧结方法目前国内外研发了许多制备超细碳化钨粉末的方法,主要有直接碳化法[4]、氢气还原WO X碳化法、流化床还原碳化法、气相沉积法、有机盐热分解碳化法、等离子电弧法、熔盐法和机械球磨法、液相还原法[5]等,目前应用于工业化规模生产的主要是前三种方法。
要使超细碳化钨粉末具备特殊性能,必须经过烧结这一关键步骤,烧结技术的不同将对硬质合金的性能产生重要影响。
而如何有效控制碳化钨晶粒在烧结过程中的长大行为成为制备超细晶和纳米晶硬质合金的关键技术。
耐磨复合镀层的研究进展

Fu h l 3 01,Chi a) s un l0 n
Ab t a t:t i n i o t ntme ho o c ii g c s r c I sa mp r a t d f ra qu rn omp s t a e i l l c r p a i g o l c r — o iem t ra sby e e t o l tn re e t o l s p a i g. The r c nt r s a c c e m e s o a i a omp ie o tn s we e ov r e d e s l tn e e e e r h a hive nt n ntwe r c ost c a i g r e viwe
Ke wo ds:e e tod p ii y r lc r e oston;e e tols pl tng;c lc r e s a i omp s t o tn o ie c a i g;a i a ntwe r
引 言
复 合 镀 技 术 是 制 备 金 属 基 复 合 材 料 的 一 种 方 法, 在工程 领 域 中获 得 了广泛 应用 。 复合镀 层是 利用 电沉积 或化 学 沉 积技 术 , 一种 或 多 种不 溶 性 固体 将 微 粒 均匀 夹杂 在 金属 镀 层 中而 形 成 的特 殊镀 层 , 镀 层 可 以同时具 有基 质金 属与 固体微 粒两类 物质 的综 合 性能 。 液 中加入 不 同种类 的微粒 , 以使镀 层具 镀 可 有 耐磨 、 自润 滑 、 耐蚀 、 饰 以及 电接 触等 不 同 的功 装 能[ ] 1 。本文 主要 对 近几 年 国内外 在耐 磨 复合 镀层
- 1、下载文档前请自行甄别文档内容的完整性,平台不提供额外的编辑、内容补充、找答案等附加服务。
- 2、"仅部分预览"的文档,不可在线预览部分如存在完整性等问题,可反馈申请退款(可完整预览的文档不适用该条件!)。
- 3、如文档侵犯您的权益,请联系客服反馈,我们会尽快为您处理(人工客服工作时间:9:00-18:30)。
耐磨金属材料的最新研究进展 关键词:耐磨材料;锰钢;抗磨白口铸铁;技术进展 摘 要:耐磨金属材料被广泛地应用于工业生产的各个领域, 而随着科学技术和现代工业的高速发展,由于金属磨损而引起的能源和金属材料消耗增加等所造成的经济损失相当惊人。近年来,对金属磨损和耐磨材料的研究,越来越引起国内外人们的广泛重视。本文概述了国内外耐磨金属材料领域研究开发的现状及取得的一系列新进展。
中图分类号:TG142.72
0 引言 随着科学技术和现代工业的高速发展,机械设备的运转速度越来越高,受摩擦的零件被磨损的速度也越来越快,其使用寿命越来越成为影响现代设备(特别是高速运转的自动生产线)生产效率的重要因素。尽管材料磨损很少引起金属工件灾难性的危害,但其所造成的能源和材料消耗是十分惊人的。据统计,世界工业化发达的国家约30%的能源是以不同形式消耗在磨损上的。如在美国,每年由于摩擦磨损和腐蚀造成的损失约1000亿美元,占国民经济总收入的4%。而我国仅在冶金、矿山、电力、煤炭和农机部门,据不完全统计,每年由于工件磨损而造成的经济损失约400亿元人民币[1]。因此,研究和发展耐磨材料,以减少金属磨损,对国民经济的发展有着重要的意义。
1 国外耐磨金属材料的发展 国外耐磨材料的生产和应用经过了多年研究与发展的高峰期,现已趋于稳定,并有自己的系列产品和国家标准、企业标准。经历了从高锰钢、普通白口铸铁、镍硬铸铁到高铬铸铁的几个阶段,目前已发展为耐磨钢和耐磨铸铁两大类。 耐磨钢除了传统的奥氏体锰钢及改性高锰钢、中锰钢以外,根据其含量的不同可分为中碳、中高碳、高碳合金耐磨钢;根据合金元素的含量又可分为低合金、中合金及高合金耐磨钢;根据组织的不同还可分为奥氏体、贝氏体、马氏体耐磨钢。而耐磨铸铁主要包括低合金白口铸铁和高合金白口铸铁两大类。二者中最具有代表性的是低铬白口铸铁和高铬白口铸铁,而且这两种材料目前在耐磨铸铁中占有主导地位。马氏体或贝氏体、马氏体组织的球墨铸铁在制作小截面耐磨件方面也占有一席之地,中铬铸铁则应用较少。从整体上看,合金白口铸铁的耐磨性优于耐磨铸钢,但后者韧性好,在诸如衬板、耐磨管道等方面有着广泛的应用[2]。
2 我国耐磨金属材料的发展 据统计,国内每年消耗金属耐磨材料约达300万吨以上,应用摩擦磨损理论防止和减轻摩擦磨损,每年可节约150亿美元。近年来,针对设备磨损的具体工况和资源情况,研制出多种新型耐磨材料。主要有改性高锰钢、中锰钢、超高锰钢系列,高、中、低碳耐磨合金钢系列,铬系抗磨白口铸铁系列,锰系、硼系抗磨白口铸铁及马氏体、贝氏体抗磨球墨铸铁,不同方法生产的双金属复合耐磨材料,表面技术处理的耐磨材料等。同时,在耐磨材料生产工艺设备上先后从日本、德国、比利时等国引进数条机械化自动化生产线。在引进基础上结合国情,发展了消失模铸造工艺设备、金属型覆砂工艺设备、挤压造型工艺设备、离心铸造工艺设备等新技术新设备等新型工艺设备。熔炼工艺上采用炉外精炼与连铸等新技术,使产品的内在质量、外观质量和性能都得到明显提高,同时,金属消耗也大幅度降低,一些厂家产品已达到或超过国际水平,出口东南亚、日本、南非、美国、澳大利亚等地,取得了良好的效益[3]。 耐磨材料的生产和应用已趋于稳定,但对基础理论和应用的科学研究仍在继续,还有更多的新型耐磨金属材料需要去探求。
3 几种耐磨金属材料的最新研究进展 3.1 锰钢 1.高锰钢 高锰钢作为历史最悠久的一种耐磨材料,其成分(质量分数)范围为:w(C)=0.9%~1.4%,w(Mn)=l0%~15%,w(Si)= 0.3%~0.8%,w(S) ≤0.05%,w(P) ≤0.10%。 高锰钢使用状态的组织为奥氏体,它具有良好的韧性和加工硬化能力。即在 强烈的冲击载荷或挤压载荷下,受力表面被加工硬化,硬度可从原始的200HB左右提高到500HB以上,而心部仍保持着良好的韧性。高锰钢的这种建筑在加工硬化基础上的优异的耐磨性能使它的使用受到限制,因此,要扩大高锰钢的应用范围,必须对其进行改进性研究,进一步提高其耐磨性[4-6] 。 目前,在高锰钢研究方面取得了一系列新进展,主要有: 采用合金化的方法,添加Cr、Mo引起固溶强化,加入钛形成碳化钛,可引起弥散强化,并能细化结晶组织,最终达到强化基体,提高其耐磨性和屈服强度的目的。实验表明,用这些方法加工出的用于冶金矿山的衬板,其使用寿命比高锰钢提高50%~70%。工艺方面,采用铸后利用余热淬化的手段来替代传统上使用加热再进行水韧处理的方法,不但能简化工艺,节约能源,缩短生产周期,而且经济效益显著[7-10]。 在轧制工艺方面,徐文亮等[11]提出了用深度轧制的方法对高锰钢进行预变形表面硬化处理,并分析和研究了其组织演变及性能变化。试验表明,经深度冷轧的高锰钢随着形变量的增加,其耐磨料磨损性能也随之增加。这是因为深度冷轧的高锰钢表面形成的高密度位错及孪晶组织,晶粒明显细化,改善了铸造高锰钢产生的各项异性、气孔等缺陷,能有效阻止磨粒造成的磨损表面的脆性剥落,同时,高锰钢良好的心部韧性也将减少其磨损过程中的疲劳剥落。该轧制方法对提高高锰钢使用效率及应用范围具有积极的现实意义 2.变质中锰耐磨钢 在磨损冲击功较小的情况下,中锰钢的耐磨性优于高锰钢的耐磨性。但在实际应用中,中锰钢在铸造和热处理的过程中易产生热裂,使铸件的成品率很低,且安全可靠性差。 近十几年来,在中锰耐磨钢研究方面,人们采用变质处理的方法,即向中锰钢中加入作为复合变质剂的Cr、Nb、Mg和稀土等元素,来改善显微组织与碳化物的形态和分布,取得了良好的效果。这主要是因为复合变质剂的加入能显著地提高材料的力学性能和位错密度,如稀土可净化钢液,使钢中夹杂物数量减少;而Cr、Mg等能促进碳化物球化,增强稀土吸附及稀土夹杂物与碳化物的非均质晶核的作用,同时也能阻止夹杂物、碳化物进一步长大,使其组织明显细化,成分偏析减小,从而使变质中锰钢韧性得到明显改善,耐磨性能显著提高。 在对中锰钢变质处理的基础上,朱瑞富等研究发现[12-14],采用铸态水韧热处理工艺技术,即利用金属的铸造余热对奥氏体锰钢进行水韧处理,既有利于节约能源,缩短生产周期,降低生产成本,又可实现水爆清砂,改善劳动条件,减少环境污染。现国内已有多家企业采用该项研究成果,并取得了较大的经济和社会效益。 3. 超高锰钢 近年来,人们已开始着手对具有稳定奥氏体组织的超高锰钢进行研究,主要是想在普通高锰钢标准成分的基础上通过提高碳、锰含量来达到改善锰钢组织,提高耐磨性的目的。 研究人员通过对Fe-C-Mn合金奥氏体的价电子结构进行分析发现,在含C、Mn原子的一个奥氏体晶胞内,C-Mn之间的结合力大于C-Fe之间的结合力[15]。这样,锰原子可通过对碳原子运动的拖曳提高碳的固溶度,而且利用锰不易和碳原子生成碳化物,来降低碳原子的扩散能力,抑制碳化物的析出。因此,同时提高碳、锰含量,不但可以提高锰钢的加工硬化能力,而且可保持高韧性的奥氏体组织,使其在使用时具有良好的耐磨性。 当前,变质处理技术在开发新的超高锰钢钢种的试验中,已经取得了很大进展。科研人员在对超高锰钢变质处理前后的组织进行研究发现[16-18],在未变质处理的组织中,晶粒较粗大,晶界共晶碳化物的网状特征非常明显;在变质处理的组织中,晶粒明显细化, 晶界碳化物的网状特征得到明显改善。这些成果的研发为改善超高锰钢组织并提高其耐磨性提供了新的途径。
3.2 抗磨白口铸铁 近年来,国外在耐磨白口铸铁的研究方面取得了一系列新进展。如美国,日本及欧洲各国20世纪初就开始采用镍硬铸铁,目前已发展到镍硬4#,铬含量由2%提高到9%,镍由4.5%提高到6.0%,共晶碳化物由M3C型变成M7C3型,力学性能显著提高,铸态厚截面即可获得马氏体组织,硬度在HRC62以上,并且具有一定韧性,主要应用于辊式磨的磨环和磨辊,可铸态使用,这对数吨重不便热处理的大铸件很有意义。因镍价格高,我国研究人员已研制中铬铸铁等新型耐磨材料以取代它。此外,国内科研人员研究出的高铬白口铸铁在国产设备上已投入应用,取得了显著的经济效益。 随着国内对铬系白口铸铁的研究不断深入,从合金化理论到生产工艺都取得了突破性进展,并获得了大量成果。低铬、中铬、高铬、超高铬磨球、衬板、锤头,高铬渣浆泵过流件,以及高铬铸铁与钢双金属复合铸造衬板、磨辊、轧辊等都已达到国际先进水平。1985年以来,我国铬系合金白口铸铁、镍铬合金白口铸铁已制定国家标准,耐磨白口铸铁技术已与国际接轨。球墨铸铁具有优良的力学性能,良好的耐磨性和抗冲击疲劳性能,在汽车、农机和建材等部门得到了广泛应用,目前,世界球铁产量已达百万吨以上。我国1982年制定了中锰抗磨球墨铸铁件标准(GB3180-82),近年来许多单位研制出马氏体基体、奥贝基体、马贝基体的磨球衬板,在建材和电力行业应用取得良好效果。我国自行研发的低合金白口铸铁,成本低,性能良好,在中、小冲击负荷下取得良好效果。近年来,结合我国资源情况,研究人员还开发研制了锰系白口铸铁,硼系白口铸铁。锰系白口铸铁分中锰(5%~6%)和高锰(7%~11%)两类,硼系白口铸铁分高碳低硼和低碳高硼两类,采用不同热处理工艺,得到相应的力学性能【3】。
3.3 其它 表面工程作为一个较新的研究领域,近年来硕果累累,其产业化也是方兴未艾。目前,我国在热喷涂涂层、EB-PVD 涂层、自蔓延高温合成涂层及扩散涂层等抗冲蚀磨损防护涂层方面的研究取得了很大进展。耐磨损作为表面工程材料(技术)的主要应用领域之一,特别是对于某些只有表面磨损的零件,表面工程更显出其重要意义。这些技术的发展,将使耐磨钢的开发前景广阔。 激光表面处理技术以加热速率高、温度高、热影响区小、可局部加热、处理后材料冷速快而晶粒细小、可机械化自动化操作、无污染等优点,越来越被人们所重视。研究人员已经开始将激光淬火、激光表面熔凝处理、激光表面合金化、激光熔覆等激光处理技术应用到耐磨钢领域,并取得了一定的进展。
4 结束语 1. 应重视已经标准化、系列化的耐磨材料的生产工艺和产品质量,继续开展低成本耐磨材料、耐磨复合材料、抗磨蚀材料、耐热耐磨材料、耐磨表面工程技术、磨损机理与失效分析方面的研究,真正掌握和稳定实施已成熟的生产工艺并推广应用新工艺新技术。 2.从冶金质量上狠下功夫,有效降低非金属夹杂物和气体含量,纯洁金属液,以提高铸件力学性能、耐磨性和使用性能;推广先进铸造工艺,改善铸件质量,生产优质耐磨金属材料; 3.我国高锰钢、抗磨白口铸铁等都制定了国家标准,耐磨合金钢也将制定国家标准,制造厂应参照国家标准,制定严格企业标准指导生产,同时完善测温、成分分析、力学性能测试、探伤等检测设备,建立完整的质量保证体系。