挡油盘模具设计
挡板注射模设计

摘要模具的制造有一下几大分类,可以称为塑料模具(又分铸压模具和吹塑模具)、、铸造模具、冲压模具橡胶模具和玻璃模具等。
其中,注塑模具和冲压模具用途极为广泛、技术熟练、占比重大。
经过对挡板注塑工艺的分析,设计了一副一模两腔的塑料模具。
里面详细的叙述了模具成型零件,其中包括型腔、模仁等设计和重要零件的工艺参数的选择与计算,浇注系统、拔模机构和冷却系统以及其它结构的设计过程。
并利用emx7.0完成了塑料模具开模模拟等分析。
关键词:注塑模具;PRO/E;CAD;挡板;AbstractUsually die by manufacturing the product category, can be divided into plasticmold (also divided into injection mold, pressure die casting and blow mold),stamping die, die casting mould, rubber and glass mould etc.. Among them,especially injection molds and stamping mold use, mature technology, occupies a large proportion of the. Through the correct analysis of the baffle in molding process, the mold two cavity plastic mold design. Details including cavity, molddesign and molding parts, process parameter selection and calculation of important parts, pouring system, cooling system and the design process of other structures, the selection principle of mould. And using emx7.0 to complete heanalysis of plastic mold tooling simulation.Key words:injeetion mould;Pro/E;CAD;Bezel;目录1绪论 (1)2 塑件成型特性 (2)2.1 注塑件实体 (2)2.2 材料的成型特性 (3)2.3 ABS材料的成型工艺参数 (3)3 设计方案及参数的确定 (4)3.1 注塑机的确定 (4)3.2 浇注系统设计 (5)3.2.1 主浇道设计 (6)3.2.2 冷料穴的设计 (7)3.2.3 分流道的设计 (8)3.2.4 浇口的设计 (8)3.3 分型面的设计 (9)3.4 排气系统的设计 (11)3.5 冷却系统的设计 (11)4 模具的结构设计 (12)4.1 成型零件的设计 (12)4.2 动、定模的工作尺寸计算 (12)4.2.1 型腔设计 (13)4.2.2 粗糙度设计 (13)4.2.3 X——综合修正系数设计 (14)4.2.3 形体尺寸公差设计 (14)4.3 机构的设计 (15)4.3.1 推出机构的设计 (15)4.3.2 推杆(复位杆)的设计 (15)4.3.3 导向机构的设计 (16)4.3.4 拉料杆的设计 (17)4.4 注射模标准模架的设计 (18)4.4.1 模架设计 (18)4.4.2 动模板的设计 (18)4.4.3 定模板的设计 (19)4.4.4 定模座板设计 (20)4.4.5 动模座板设计 (20)4.4.6 垫块设计 (21)4.4.7 推杆固定板设计 (21)4.4.8 推板的设计 (22)4.5 模具的整体设计 (23)参考文献 (25)致谢 (26)1 绪论由于现代注塑模技术的快速发展以及计算机技术的应用,我国工业生产中的模具已经成为生产各种工业产品不可缺少的重要设备和装备,由于注塑模具的快速发张,这会引导我国模具相关企业和我国模具行业的快速发展。
分油套注塑模具设计

分油套注塑模具设计1. 简介分油套注塑模具设计是一种常用于注塑加工的模具设计方法。
它通过在模具中设置分油套,实现塑料材料在注塑过程中的分流和分布,从而获得更好的注塑成形效果。
本文将详细介绍分油套注塑模具设计的原理、步骤和注意事项。
2. 原理分油套注塑模具设计的原理是通过在模具中设置油道和分油套来实现注塑料的分流和分布。
在注塑过程中,熔融塑料通过喷嘴进入模具腔内,在模具腔内受到压力作用进行充填和冷却。
如果没有合理设计的分油套,熔融塑料注入模具时容易出现浮砂、冷流痕等缺陷,使得注塑成形的质量下降。
分油套注塑模具设计的原理是通过设置油道来控制熔融塑料在模具中的流动方向,通过分油套来实现熔融塑料的分流。
具体来说,油道的设计要合理,以保证熔融塑料能够充满整个模具腔;分油套要设计在合适的位置,以实现熔融塑料在注塑过程中的均匀分布。
3. 设计步骤分油套注塑模具设计一般包括以下步骤:3.1. 模具设计参数确定首先需要确定模具的基本参数,包括产品尺寸、材料、注塑机型号等。
这些参数将直接影响到模具的设计。
3.2. 模具结构设计根据产品要求和模具设计参数,开始进行模具的结构设计。
这包括模具腔、模芯的设计,以及冷却系统、出模系统等组成部分的设计。
在设计过程中,需要合理安排分油套的位置和数量,确保能够实现熔融塑料的均匀分流。
3.3. 油道设计在模具结构设计的基础上,进行油道的设计。
油道应设置在模具的合适位置,以便实现熔融塑料的流动方向控制。
油道的直径、长度和数量都需要根据模具设计参数进行合理的计算和选择。
3.4. 分油套设计根据油道的设计和产品的成形要求,进行分油套的设计。
分油套的主要作用是对熔融塑料进行分流和分布,使得塑料能够均匀充填模具腔。
在设计过程中,需要考虑分油套的位置、尺寸和数量,以及与油道的连接方式等。
3.5. 模具详图设计完成上述步骤后,开始进行模具的详图设计。
详图设计需要考虑到模具的分工,将整个模具分为多个零部件,并进行详细的尺寸和结构的设计。
油箱壳体冲压工艺与模具设计

油箱壳体冲压工艺与模具设计由于油箱的外观质量要求式样越来越受到客户的重视,所以在油箱模具生产过程中,首先对油箱外壳体的冲压工艺的制定必须要合理,油箱模具的质量更要保证,才能够满足客户的生产需求。
通常车油箱外壳体是由两片对称的冲压成形件焊接而成的,钢板厚度为0.8mm。
这两片对称的冲压成形件的拉伸工艺有两种:一种是单片式拉伸成形,另一种为两片式拉伸成形。
这两种冲压工艺方法各有其特点。
只有根据油箱的形状来选择使用哪种冲压工艺,才能做到既能保证油箱外壳体冲压件质量,又能保证油箱制造费用较为经济。
1冲压工艺方案在确定壳体冲压工艺方案时,考虑到生产与设备条件的实际情况,为了提高生产效率,充分有效地利用设备资源,油箱上下壳体的冲压拟采用组合冲模成形,即油箱上下壳体2个冲压件的每道冲压工序都使用一副组合冲模来完成,故壳体冲压工艺方案可采用拉深、整形冲孔、翻孔冲孔切边3道工序,由3副组合冲模完成。
首先将板料分别下料。
拉深件三维数字模型可通过Dynaform软件进行成形模拟分析。
2零件成形工艺分析上壳体顶部有个较大的翻边圆口,圆口周边有若干个小孔,凸缘边入口圆角很小。
为了满足拉深时板料的塑性变形要求,拉深凹模的入口圆角必须增大。
经查资料,凹模的入口圆角取R8mm,由下一道工序整形到零件所要求的R0.8mm;下壳体局部深度高低差异较大,且在凸缘边上有一条加强筋,下壳体拉深难度大于上壳体。
下壳体拉深凹模的入口圆角也增大到R8mm,由下一道工序整形到所要求的R0.8mm。
下壳体局部深度高低变化较大,拉深时凸缘上局部板料产生塑性变形后流入模腔的快慢要求不一致,必须在板料要求流入较慢的凸缘边上设置拉深筋,增大板料径向流动阻力。
零件圆角由R8mm 整形至R0.8mm时,凸缘上的板料还会产生塑性变形,所以下壳体凸缘边上的加强筋不能在第一次拉深时成形出来,应由下一道工序整形圆角R0.8mm时连同加强筋一起成形出来。
为了减少整形R8mm圆角时凸缘上的板料产生过大径向流动,避免造成在整形R0.8mm圆角的过程中受到成形凸缘边上加强筋的影响,经计算在下壳体第一次拉深时应多拉深2mm深度。
数值模拟的挡泥板成形工艺与模具设计

数值模拟的挡泥板成形工艺与模具设计摘要:利用Dynaform对汽车制动盘挡泥板零件进行展开计算,分析了制动盘挡泥板成形过程中金属的流动及应力应变分布规律,利用数值模拟分析的结果得出零件能一次拉深成形,设计的模具结构合理紧凑,灵活可靠,提高了生产效率和零件成形质量的稳定性,关键词:挡泥板;数值模拟;级进冲压;压边力;模具设计0引言图1所示汽车制动盘挡泥板是某企业为某款轿车配套的零件,材料为SPCC,料厚t=0.8mm,大批量生产,零件要求各面衔接处平整光滑,任何部位不允许有严重起皱。
目前该企业采用的是单工序模成形该零件,由落料、拉深、修边冲孔、翻边4道工序完成,生产效率低,成形的零件质量不稳定,为适应大批量生产的要求,现决定采用多工位级进模完成零件的冲压成形。
1工艺分析SPCC是典型的冷轧材料,具有良好的冲压工艺性能。
零件底部有直径为ϕ12mm的4个小孔和直径为ϕ76.9mm的1个大孔,小孔与大孔之间的距离为4.1mm,大于1.5t,即最小孔径、最小孔边距均大于板料厚度的1.5倍,满足冲压工艺要求。
零件精度介于ST6~ST10,普通冲压即可满足要求。
但该零件是结构不对称的拉深件,其凸缘部分和底部的台阶形状给毛坯展开及拉深次数的确定带来困难,为此需要借助板料成形模拟软件Dynaform进行零件的尺寸展开和拉深次数的确定,同时又可以分析挡泥板成形过程的金属流动及应力应变分布规律。
图2所示为汽车制动盘挡泥板应力分布与壁厚分布数值模拟结果,从图2模拟结果可以看出,当压边力(含有凸缘部分的成形力)为30kN时,零件起皱发生在凸缘部分且比较严重,变薄比较严重的部位在底部台阶处,但变薄量未超差,即成形的主要缺陷是起皱,当将压边力调整到50kN时,起皱的现象消除,因此可以确定挡泥板的拉深次数一次即可。
这对于传统挡泥板多次拉深成形是一次创新,不但减少了工序,而且降低了生产成本,提高了生产效率,解决了后期排样设计的困难,使得排样更加合理,方便于模具结构的设计。
冲压模具设计及主要零部件加工课件 1.2 挡板的模具结构选择

1-螺帽2-导料螺钉 3-挡料销 4-弹簧 5-凸模固定板 6-销钉 7-模柄 8-垫板 9-止动销 10-卸料螺钉 11-上模座 12-凸模 13-导套 14-导柱 15-卸料板 16-凹模
17-内六角螺钉18-Βιβλιοθήκη 模座导 柱 式 冲 孔 模
1-上模座 2、18-圆柱销 3-导柱 4-凹模 5-定位圈 6、7、8、15-凸模 9-导套10-弹簧11-下模座 12-卸料螺钉 13-凸模固定板 14-垫板 16-模柄 17-止动销19、20-内六角螺钉 21-卸料板
任务结论
挡板模具结构选择:
1、导向:滑动后侧导柱模具 2、定位:导料销,挡料销 3、卸料:弹性卸料上出料
项目一 挡板落料模设计及主要零部件加工
任务二 挡板的模具结构选择
1.2 挡板的模具结构选择
一、单工序冲裁模
单工序冲裁模: 在压力机一次行程内只完成一个冲压工序的冲裁模。
1.落料模 (1)无导向单工序落料模 (2)导板式单工序落料模 (3)导柱式单工序落料模
2.冲孔模 导柱式冲孔模
1-上模座 2-凸模 3-卸料板 4-导料板 5-凹模 6-下模座 7-定位板
无导向单工序落料模
1-模柄 2-止动销 3-上模座 4、8-内六角螺钉 5-凸模 6-垫板 7-凸模固定板 9-导板 10-导料板 11-承料板 12-螺钉 13-凹模 14-圆柱销 15-下模座 16-固定挡料销 17-止动销 18-限位销 19-弹簧 20-始用挡料销
导板式单工序落料模
导柱式单工序落料模
二、级进模
1-模柄 2-螺钉 3-冲孔凸模 4-落料凸模 5-导正销 6-固定导料销 7-始用导料销
用导正销定距的冲孔落料级进模
三、复合模
挡料板零件的冷冲模具设计【毕业作品】

挡料板零件的冷冲模具设计摘要本次设计主要讲述了挡料板零件冷冲压模具设计,设计的内容是从零件的工艺分析到选取板材排样最后使冷冲压使模具成形的过程。
其中涉及了冷冲压概念和基本类型、冲压工序、模具类型、压力的选择、凸凹设计和模架的选择等。
通过对冲裁件的分析可知材料是45号钢,该材料具有良好的塑性和较好的弹性,冲裁性能比较较好,适合冲裁加工。
另外冲裁件形状简单而且规则,生产批量是中批量生产,所以经过冲裁方案的选择,选用级进模生产较为适合。
再经过计算分析完成模具的排样设计、定位方式、出件方式、凸凹的设计,最后是模具的装配。
关键词:冷冲压;模具结构;工艺分析;冲裁方案目录前言 (1)1 冲压模简介............................................................................ 错误!未定义书签。
1.1 冲压的概念特点及应用................................................... 错误!未定义书签。
1.2 冲压工艺的优缺点............................................................. 错误!未定义书签。
1.3 冲压的基本类型及模具类型 (3)1.4 冲压技术的发展趋势......................................................... 错误!未定义书签。
2 冲压件的工艺分析及工艺方案的确定................................ 错误!未定义书签。
2.1 材料分析............................................................................. 错误!未定义书签。
2.2 工艺分析 (5)2.2.1 工艺要求(工件图) (5)2.3 工艺方案的确定 (6)3 冲裁方案与排样设计 (7)3.1 冲裁方案的选择 (7)3.2 冲裁方案的确定 (10)3.3 冲裁间隙 (11)4 冲压模具总体结构设计 (12)4.1 模具类型 (12)4.2 操作和定位 (12)4.3 卸料和出件方式 (12)5 压力机的选择 (13)5.1 冲压力计算与选择压力机 (13)5.2 冲裁压力机中心的确定 (14)6 凹凸模设计与计算 (15)6.1 凹凸模设计 (15)6.2 凹凸模刃口尺寸的计算 (15)7 模具的总装图与零件图..................................................... 1错误!未定义书签。
塑料模具设计之挡圈
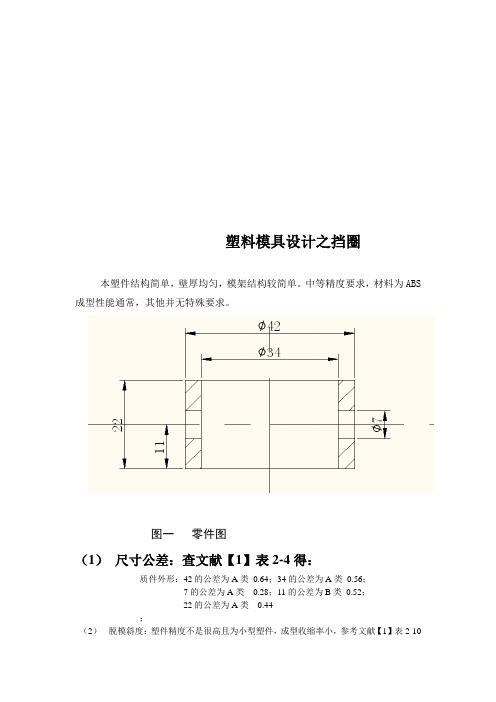
塑料模具设计之挡圈本塑件结构简单,壁厚均匀,模架结构较简单。
中等精度要求,材料为ABS 成型性能通常,其他并无特殊要求。
图一零件图(1)尺寸公差:查文献【1】表2-4得:质件外形:42的公差为A类0.64;34的公差为A类0.56;7的公差为A类0.28;11的公差为B类0.52;22的公差为A类0.44;(2)脱模斜度:塑件精度不是很高且为小型塑件,成型收缩率小,参考文献【1】表2-10选择该塑件上型芯与凹模的统一脱模斜度为1度。
注射成型过程:(1)干燥-螺杆塑化-充模-保压-冷却-脱模-塑件后处理。
(2)注射工艺参数:1)注射成型时各段温度:料筒后段温度:160-180;料筒中段温度:180-200;料筒前段温度:200-220;2)注射压力:ABS熔融的粘度比聚苯乙烯高,在注射是使用较高的注射压力。
但并非所有ABS制件都要施用高压,考虑到塑件不大,结构不算复杂,,厚度较小,能够用较低的注射压力。
关于螺杆式注射机通常去70Mpa-100Mpa。
3)注射速度;ABS塑料使用中等注射速度较好。
4)模具温度:挡圈属于中小型制件,形状较规则,故不用考虑专门对模具加热。
5)料量操纵:注塑机注塑ABS塑料时,其每次注射量仅达标准注射量的80%。
为了提高塑件质量及尺寸稳固,注射量选为标定注射量的50%为宜。
第二部分塑件的分析ABS塑料化学名称:苯乙烯共聚物比重:1.02克/立方厘米查表成型收缩率:0,3-0.8%。
材料分析:ABS无味无毒呈微黄色成型的塑件有较好的光泽具有良好的机械强度与一定的耐磨性、耐寒性、耐油性、耐水性,化学稳固性与电器性能,密度为:1.02-1.16g/cmm3 ABS:有一定的硬度与尺寸稳固性,易于加工,通过配色可配成任何颜色。
成型特点:ABS在升温时粘度增高,因此成型压力较高,故塑件上的脱模斜度宜稍大,ABS易吸水,成型加压前应进行干燥处理,ABS易产节痕,模具设计时应注意尽量减少浇注系统对料流的阻力,在正常的成型条件下的壁厚,熔料温度对收缩率影响极小,在要求塑件精度高时,模具温度可操纵在50-60摄氏度.而强调塑件光泽与耐热时,模具温度应操纵在60-80摄氏度。
刃型挡片冲压模设计

刃型挡片冲压模设计一、模具结构设计:1.模具类型:根据刃型挡片的形状和尺寸,选择合适的模具类型,常用的有开式模和闭式模。
开式模适用于简单的挡片形状,闭式模适用于复杂的挡片形状。
2.模具构造:模具构造应符合挡片的形状和尺寸要求。
常见的构造有上下模、顶出器、导向柱、钢珠柱等。
根据挡片的形状和尺寸要求,选择合适的构造。
3.增加引导装置:为了保证冲压过程中挡片的定位准确,可在模具中增加合适的引导装置,如导柱、导套等。
4.增加及降低台:为了提高冲压效率,可以在模具中增加及降低台,以避免在冲压过程中重新夹紧工件。
二、模具材料选择:1.工作部分材料:一般选择具有良好耐磨性和硬度的材料,如Cr12MoV、SKD11等。
2.基本部分材料:对于冲床常用的模具材料,如底板、模板等,可以选择具有一定强度和刚性的材料,如45#钢、优质碳素钢等。
三、加工工艺设计:1.材料布置:根据挡片的形状和尺寸要求,合理布置原材料的位置,以减少材料的浪费和加工的次数。
2.加工顺序:冲压模的加工顺序应从简到难,从外到内进行,以提高加工的效率和质量。
3.模具维护:模具使用一段时间后,会出现磨损和疲劳现象,为了保证模具的正常使用,需定期维护和保养模具。
四、模具使用注意事项:1.清洁保养:在使用完模具后,及时清洁和保养模具,防止腐蚀和损坏。
2.定期检查:定期检查模具的损坏和磨损情况,及时修复和更换模具。
3.润滑维护:模具使用过程中需要进行适当的润滑和维护,以减少磨损和延长模具的使用寿命。
总结:刃型挡片冲压模设计需要考虑模具结构设计、材料选择、加工工艺等方面的因素。
通过合理设计和选择,可以提高刃型挡片冲压的效率和质量,促进生产的顺利进行。
同时,模具的定期维护和使用注意事项也是确保模具长期可靠使用的重要环节。