浅析高速冲压模具
冲压模具特点及制造过程分析
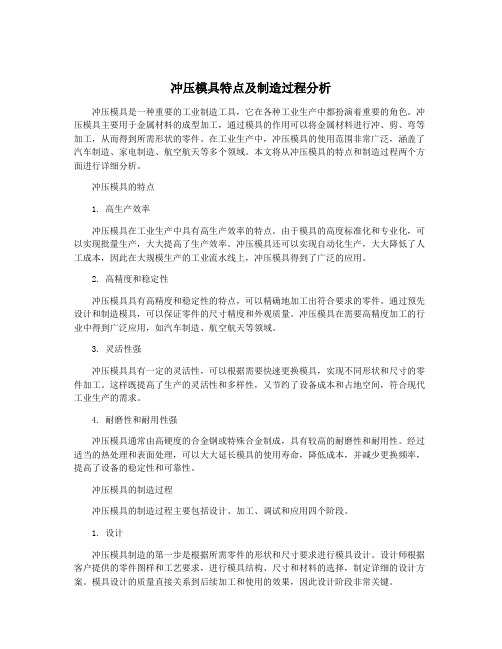
冲压模具特点及制造过程分析冲压模具是一种重要的工业制造工具,它在各种工业生产中都扮演着重要的角色。
冲压模具主要用于金属材料的成型加工,通过模具的作用可以将金属材料进行冲、剪、弯等加工,从而得到所需形状的零件。
在工业生产中,冲压模具的使用范围非常广泛,涵盖了汽车制造、家电制造、航空航天等多个领域。
本文将从冲压模具的特点和制造过程两个方面进行详细分析。
冲压模具的特点1. 高生产效率冲压模具在工业生产中具有高生产效率的特点。
由于模具的高度标准化和专业化,可以实现批量生产,大大提高了生产效率。
冲压模具还可以实现自动化生产,大大降低了人工成本,因此在大规模生产的工业流水线上,冲压模具得到了广泛的应用。
2. 高精度和稳定性冲压模具具有高精度和稳定性的特点,可以精确地加工出符合要求的零件。
通过预先设计和制造模具,可以保证零件的尺寸精度和外观质量。
冲压模具在需要高精度加工的行业中得到广泛应用,如汽车制造、航空航天等领域。
3. 灵活性强冲压模具具有一定的灵活性,可以根据需要快速更换模具,实现不同形状和尺寸的零件加工。
这样既提高了生产的灵活性和多样性,又节约了设备成本和占地空间,符合现代工业生产的需求。
4. 耐磨性和耐用性强冲压模具通常由高硬度的合金钢或特殊合金制成,具有较高的耐磨性和耐用性。
经过适当的热处理和表面处理,可以大大延长模具的使用寿命,降低成本,并减少更换频率,提高了设备的稳定性和可靠性。
冲压模具的制造过程冲压模具的制造过程主要包括设计、加工、调试和应用四个阶段。
1. 设计冲压模具制造的第一步是根据所需零件的形状和尺寸要求进行模具设计。
设计师根据客户提供的零件图样和工艺要求,进行模具结构、尺寸和材料的选择,制定详细的设计方案。
模具设计的质量直接关系到后续加工和使用的效果,因此设计阶段非常关键。
2. 加工模具加工包括铣削、车削、磨削、线切割、电火花加工等多种加工技术。
在加工过程中,需要按照设计要求将模具的各部分逐步加工成型,保证模具的匹配精度和表面质量。
浅析冲压模具的技术应用与发展趋势
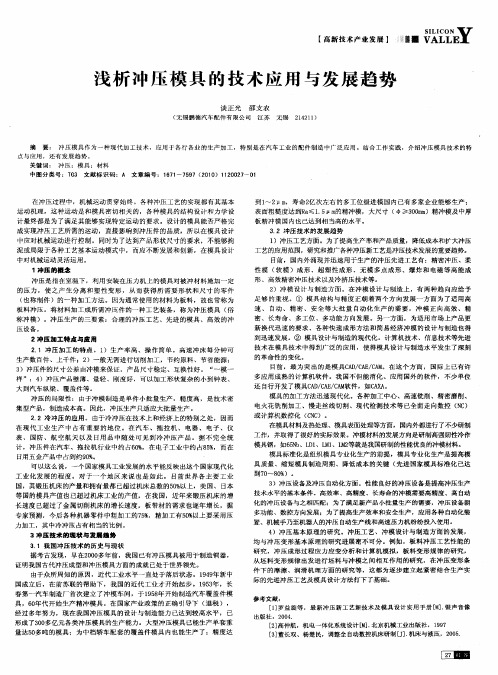
到 1 ,寿命 2 次左 右 的 多工 位级 进模 国 内已有 多家 企 业能 够 生产 ; ~2 m u 亿 表面 粗糙 度达 到R ≤15 的精冲 模 ,大尺 寸 ( ≥30m a . m p 0 m )精冲 模 及中 厚 板精 冲模 国内也 已达 到相 当 高的水 平 。
的革命 性 的变化 。 目前 ,最 为突 出的 是模 具 C O C E C M A / A / A 。在这 个 方 面 , 国际 上 已有 许
2 1 冲压 加 工 的 特点 。1 . )生 产 率 高 、操 作 简单 。高速 冲 床 每分 钟 可
生 产数 百件 、上 千件 ;2 )一般 无 需进 行切 削加 工 ,节约 原料 、节省 能源 :
3 2 冲压 技 术的 发展 趋势 .
成实现冲压工艺所需的运动,直接影响到冲压件的品质,所 以在模具设计 中应对 机械 运 动进 行 控 制 。同 时为 了达 到 产 品形 状尺 寸 的要 求 ,不 能 够拘 泥或 局 限 于各 种工 艺 基本 运 动模 式 中 ,而应 不 断 发展 和 创新 , 在模 具 设计
中对 机械 运动 灵 活运 用 。 1冲压 的 概念 冲压 是 指在 室温 下 ,利 用安 装在 压 力机 上 的模 具对 被冲 材 料旋 加 一定 的压 力 ,使 之 产 生 分 离 和 塑 性变 形 ,从 而 获 得 所 需 要 形 状和 尺 寸 的零 件 ( 称 制件 )的一 种加 工 方法 。因 为通 常使 用 的材 料 为板 料 ,故 也 常称 为 也 板料 冲 压 。将 材料 加 工成 所 需冲 压件 的一种 工 艺装 备 ,称 为 冲 压模 具 ( 俗 称 冲 模 ) 。冲压 生 产 的三 要素 :合理 的 冲压 工 艺 、先 进 的模 具 模来 保证 ,产 品尺寸 稳定 、 互换 性好 。 “ 一模 一 样 ” :4 )冲 压产 品壁 薄 、量轻 、 刚度 好 ,可 以加工 形状 复杂 的 小到钟 表 、 大 到汽 车纵 梁 、覆盖 件 等 。 冲 压 的局 限性 : 由于冲 模 制造 是 单件 小批 量 生产 ,精 度 高 ,是技 术 密 集 型产 品 ,制 造 成本 高 。因此 ,冲压 生产 只适 应大 批 量生 产 。 22 冷 冲压 的应 用 。 由于 冷冲 压在 技 术上 和经 济 上 的特别 之 处 ,因 而 .
冲压模具特点及制造过程分析
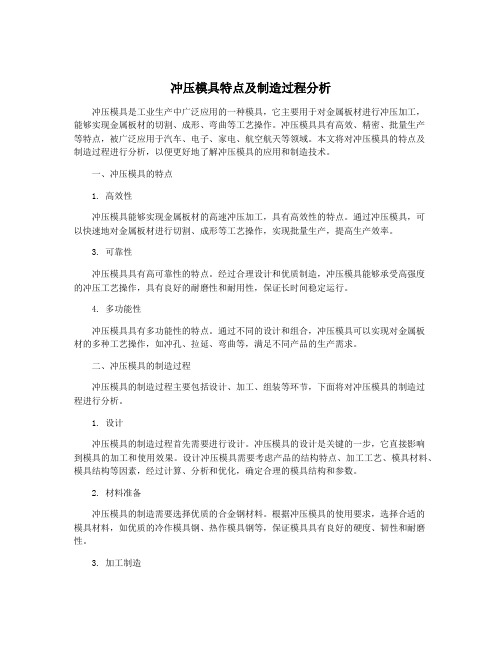
冲压模具特点及制造过程分析冲压模具是工业生产中广泛应用的一种模具,它主要用于对金属板材进行冲压加工,能够实现金属板材的切割、成形、弯曲等工艺操作。
冲压模具具有高效、精密、批量生产等特点,被广泛应用于汽车、电子、家电、航空航天等领域。
本文将对冲压模具的特点及制造过程进行分析,以便更好地了解冲压模具的应用和制造技术。
一、冲压模具的特点1. 高效性冲压模具能够实现金属板材的高速冲压加工,具有高效性的特点。
通过冲压模具,可以快速地对金属板材进行切割、成形等工艺操作,实现批量生产,提高生产效率。
3. 可靠性冲压模具具有高可靠性的特点。
经过合理设计和优质制造,冲压模具能够承受高强度的冲压工艺操作,具有良好的耐磨性和耐用性,保证长时间稳定运行。
4. 多功能性冲压模具具有多功能性的特点。
通过不同的设计和组合,冲压模具可以实现对金属板材的多种工艺操作,如冲孔、拉延、弯曲等,满足不同产品的生产需求。
二、冲压模具的制造过程冲压模具的制造过程主要包括设计、加工、组装等环节,下面将对冲压模具的制造过程进行分析。
1. 设计冲压模具的制造过程首先需要进行设计。
冲压模具的设计是关键的一步,它直接影响到模具的加工和使用效果。
设计冲压模具需要考虑产品的结构特点、加工工艺、模具材料、模具结构等因素,经过计算、分析和优化,确定合理的模具结构和参数。
2. 材料准备冲压模具的制造需要选择优质的合金钢材料。
根据冲压模具的使用要求,选择合适的模具材料,如优质的冷作模具钢、热作模具钢等,保证模具具有良好的硬度、韧性和耐磨性。
3. 加工制造冲压模具的加工制造包括粗加工、精密加工和表面处理等工艺。
首先进行了金属材料的锻造、铣削、切割等粗加工工艺,然后进行模具的精密加工,如磨削、电火花加工等,最后对模具的表面进行热处理、镀层等工艺处理,提高模具的耐磨性和使用寿命。
4. 组装调试冲压模具的制造完成后,需要进行组装调试。
将各个零部件按照设计要求进行组装,进行模具的调试和检验,验证模具的加工精度和性能,确保模具的正常使用。
冲压模具心得体会
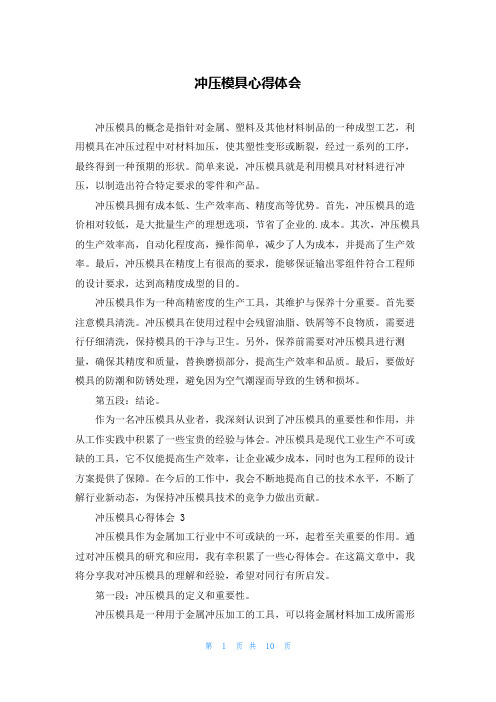
冲压模具心得体会冲压模具的概念是指针对金属、塑料及其他材料制品的一种成型工艺,利用模具在冲压过程中对材料加压,使其塑性变形或断裂,经过一系列的工序,最终得到一种预期的形状。
简单来说,冲压模具就是利用模具对材料进行冲压,以制造出符合特定要求的零件和产品。
冲压模具拥有成本低、生产效率高、精度高等优势。
首先,冲压模具的造价相对较低,是大批量生产的理想选项,节省了企业的.成本。
其次,冲压模具的生产效率高,自动化程度高,操作简单,减少了人为成本,并提高了生产效率。
最后,冲压模具在精度上有很高的要求,能够保证输出零组件符合工程师的设计要求,达到高精度成型的目的。
冲压模具作为一种高精密度的生产工具,其维护与保养十分重要。
首先要注意模具清洗。
冲压模具在使用过程中会残留油脂、铁屑等不良物质,需要进行仔细清洗,保持模具的干净与卫生。
另外,保养前需要对冲压模具进行测量,确保其精度和质量,替换磨损部分,提高生产效率和品质。
最后,要做好模具的防潮和防锈处理,避免因为空气潮湿而导致的生锈和损坏。
第五段:结论。
作为一名冲压模具从业者,我深刻认识到了冲压模具的重要性和作用,并从工作实践中积累了一些宝贵的经验与体会。
冲压模具是现代工业生产不可或缺的工具,它不仅能提高生产效率,让企业减少成本,同时也为工程师的设计方案提供了保障。
在今后的工作中,我会不断地提高自己的技术水平,不断了解行业新动态,为保持冲压模具技术的竞争力做出贡献。
冲压模具心得体会 3冲压模具作为金属加工行业中不可或缺的一环,起着至关重要的作用。
通过对冲压模具的研究和应用,我有幸积累了一些心得体会。
在这篇文章中,我将分享我对冲压模具的理解和经验,希望对同行有所启发。
第一段:冲压模具的定义和重要性。
冲压模具是一种用于金属冲压加工的工具,可以将金属材料加工成所需形状。
冲压模具的设计和制造直接影响产品的质量和效率,因此对于企业而言非常重要。
冲压模具的使用范围广泛,涉及到汽车、电子、家电、机械制造等多个领域。
高速冲压模具维护保养
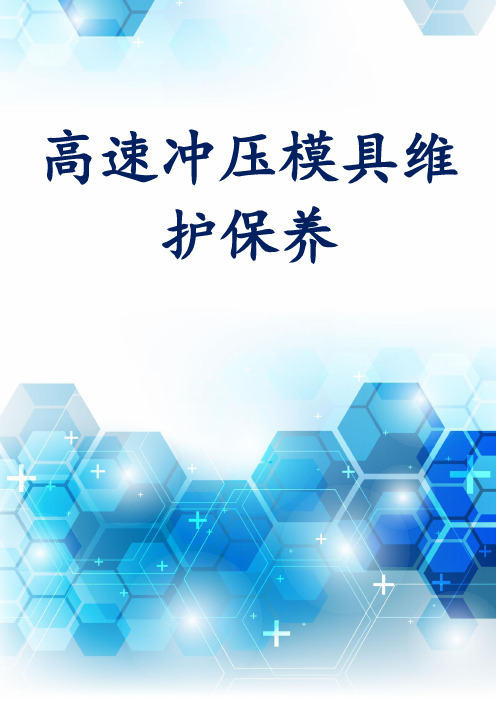
高速冲压模具维护保养高速冲压模具维护保养高速冲压模具是制造业中常用的一种设备,它在产品生产过程中起着至关重要的作用。
为了确保模具的正常工作和延长其使用寿命,维护保养工作变得尤为重要。
首先,定期的模具清洁是维护保养的基础。
高速冲压模具在长时间的工作过程中,会积累各种杂质和油渍。
这些污物会降低模具的工作效率,甚至损坏模具的工作表面,影响产品质量。
因此,定期对模具进行清洗是必要的,可以采用专业的清洗剂和工具,将模具表面的污物和油渍清洗干净。
其次,模具润滑是维护保养中的重要环节。
高速冲压模具在工作时需要承受很大的压力和摩擦力,如果没有良好的润滑,会导致模具的磨损和损坏。
因此,及时给模具加油是必要的,可以选择合适----宋停云与您分享----的润滑油或脂,涂抹在模具的工作表面和滑动部位,确保模具在工作时的顺畅运行。
此外,定期的模具检查和维修也是非常重要的。
高速冲压模具在长时间的工作中,可能会出现一些问题,比如磨损、疲劳和裂纹等。
如果不及时发现和修复,会导致模具的损坏和工作效率的下降。
因此,定期的模具检查和维修是必要的,可以通过专业的检测仪器和设备,检查模具的工作状况,及时发现问题,并进行修复和更换。
最后,正确的使用和操作也是维护保养的重要环节。
高速冲压模具在使用过程中,需要按照正确的工作步骤和操作要求进行使用,避免超过模具的负荷和工作范围,以及避免不当的碰撞和撞击。
同时,在模具操作中,需要保证工作环境的整洁和安全,避免杂物和异物进入模具内部,并确保操作人员的安全。
综上所述,高速冲压模具的维护保养工作是确保模具正常工作和延长其使用寿命的关键。
通过定----宋停云与您分享----期的清洁、润滑、检查和维修,以及正确的使用和操作,可以有效地提高模具的工作效率和产品质量,降低生产成本,为企业的发展和竞争力做出贡献。
----宋停云与您分享----。
冲压模具特点及制造过程分析
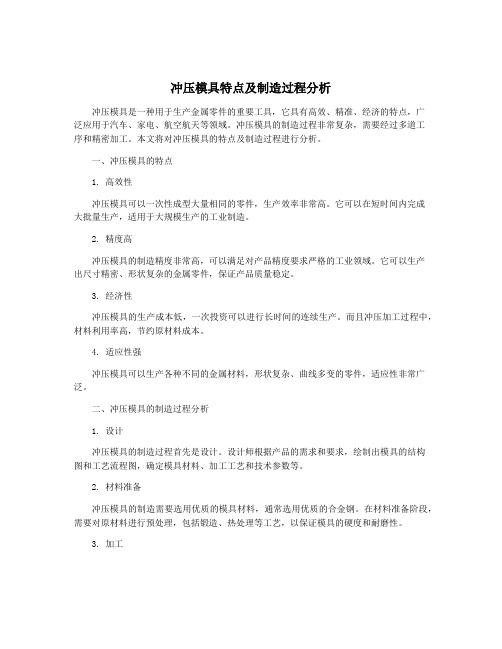
冲压模具特点及制造过程分析冲压模具是一种用于生产金属零件的重要工具,它具有高效、精准、经济的特点,广泛应用于汽车、家电、航空航天等领域。
冲压模具的制造过程非常复杂,需要经过多道工序和精密加工。
本文将对冲压模具的特点及制造过程进行分析。
一、冲压模具的特点1. 高效性冲压模具可以一次性成型大量相同的零件,生产效率非常高。
它可以在短时间内完成大批量生产,适用于大规模生产的工业制造。
2. 精度高冲压模具的制造精度非常高,可以满足对产品精度要求严格的工业领域。
它可以生产出尺寸精密、形状复杂的金属零件,保证产品质量稳定。
3. 经济性冲压模具的生产成本低,一次投资可以进行长时间的连续生产。
而且冲压加工过程中,材料利用率高,节约原材料成本。
4. 适应性强冲压模具可以生产各种不同的金属材料,形状复杂、曲线多变的零件,适应性非常广泛。
二、冲压模具的制造过程分析1. 设计冲压模具的制造过程首先是设计。
设计师根据产品的需求和要求,绘制出模具的结构图和工艺流程图,确定模具材料、加工工艺和技术参数等。
2. 材料准备冲压模具的制造需要选用优质的模具材料,通常选用优质的合金钢。
在材料准备阶段,需要对原材料进行预处理,包括锻造、热处理等工艺,以保证模具的硬度和耐磨性。
3. 加工冲压模具的加工过程包括粗加工和精密加工两个阶段。
粗加工工艺包括锻造、铣削、钻孔等加工工序,以初步形成模具的外形和结构。
精密加工工艺包括线切割、电火花加工、磨削加工等,以提高模具的精度和表面质量。
4. 装配冲压模具的装配是制造过程的最后一个阶段,主要包括模具各零部件的组装和调试。
模具的装配需要非常严格的工艺要求,确保模具的精度和稳定性。
5. 调试和检测冲压模具制造完成后,需要进行全面的调试和检测工作。
通过模具的调试和检测,可以确保模具的工作性能和产品质量符合设计要求。
通过上述分析,我们可以看出,冲压模具是一种高效、精密、经济、适应性强的工具,具有广泛的应用前景。
汽车冲压模具的技术分析
汽车冲压模具的技术分析汽车冲压模具是在汽车制造中应用广泛的一种零部件加工工艺,它采用高速冲压机械,将厚度不等的金属板材加工成汽车零部件。
本文将对汽车冲压模具的技术分析进行探讨,包括冲压模具的种类、工艺特点以及发展趋势等方面。
一、冲压模具的种类1、简单模具简单模具适用于厚度在3mm以下、重量低于1kg,形状简单的零部件加工。
该模具结构简单,制造成本低,但只能完成简单的加工任务。
2、复杂模具复杂模具适用于厚度在8mm以上、重量超过1kg、具有高难度形状的零部件加工。
该模具构造复杂、制造难度大、技术要求高,但其加工能力和精度也更高。
3、高速模具高速模具是为适应高速冲压机的需求而设计的模具,其加工速度比普通模具更快,能够大幅度提高生产效率。
该模具采用高强度耐磨钢材制作,表面装备耐磨涂层,能够耐高温高压,在加工过程中不易变形。
二、冲压模具的工艺特点1、高精度汽车零部件通常要求高精度,要求冲压模具能够准确地切割和成型材料。
因此,模具的设计和制造需要考虑工艺流程、材料特性和产品质量要求等因素。
目前,采用CAD/CAM设计和制造技术的冲压模具的精度能够达到微米级别。
2、高效率高效率是汽车冲压模具的又一重要特征。
随着汽车工业的发展,节约时间成了工业生产的一个绝对要素,冲压模具须有着一定的加工速度和生产率。
为了提高加工效率和生产率,采用高速冲压机和高速钢材制造模具是目前常用的方法。
3、高坚固性冲压模具的坚固性和刚度是关系到加工质量和寿命的重要组成部分。
汽车模具在工作过程中所承受的高压和高速冲击力是巨大的,因此要求模具所使用的钢材具有足够的抗压性和耐磨性。
4、低成本冲压模具的制造成本直接关系到企业的生存和竞争力。
因此,为了降低制造成本,应尽量采用先进的CAD/CAM技术,大幅度减少模具的设计和制造周期,应用先进的模具制造技术,提高模具加工的收益率。
三、冲压模具的发展趋势1、高速为了应对市场竞争,汽车工业需要提高生产效率和质量,而高速化是势必趋势。
高速精冲压力机的模具设计与优化
高速精冲压力机的模具设计与优化随着工业化的快速发展,高速精冲压力机在金属加工领域得到了广泛应用。
模具作为高速精冲压力机的重要组成部分,对其加工效率和质量起着至关重要的作用。
因此,对高速精冲压力机的模具设计与优化进行研究,成为提高加工效能和降低生产成本的重要手段。
一、高速精冲压力机的模具设计1. 模具材料选择与加工硬度模具材料的选择与加工硬度是直接影响模具寿命和加工质量的关键因素。
在高速精冲压力机的模具设计中,一般选用高硬度、高强度、高刚性的合金钢作为模具材料,以保证其在高速压力下具备足够的强度和硬度。
2. 模具结构设计模具的结构设计直接影响到产品的加工精度和模具的寿命。
在高速精冲压力机的模具设计中,应考虑以下要点:- 合理的切削角度和摩擦系数:切削角度的选择应根据工件的材料和形状进行综合考虑,以减小切削力和摩擦系数,提高模具寿命。
- 优化的冷却系统:冷却系统设计合理与否直接关系到模具的散热效果。
合理的冷却系统能够有效降低模具温度,提高模具的使用寿命。
- 减小模具间隙:合理减小模具间隙可以提高产品的加工精度和表面光洁度。
二、高速精冲压力机模具的优化1. 仿真分析技术在模具优化中的应用使用仿真分析技术对高速精冲压力机的模具设计进行优化,可以在计算机上进行虚拟试验,降低实验成本,加快开发周期。
通过对模具的应力、变形、切削力和振动等进行仿真分析,可以帮助设计师在早期阶段发现问题,并优化设计。
2. 材料强度的优化设计模具在工作过程中受到很大的力和压力,材料的强度是保证模具长久工作并降低断裂风险的关键。
在高速精冲压力机的模具优化中,可以通过优化材料的成分和热处理工艺,提高材料的力学性能,提高模具的强度和耐磨性。
3. 模具结构的优化设计模具结构的优化可以包括减小模具的重量、提高刚性、降低振动等方面。
通过优化模具的结构设计,可以减小模具的惯性力,提高模具的动态刚度和稳定性,从而实现高速高效的加工。
4. 设计人员的技术水平提升与团队的协作高速精冲压力机模具设计的优化需要设计人员具备较强的专业知识和技术水平。
高速精冲压力机的模具磨损机制分析与预测
高速精冲压力机的模具磨损机制分析与预测一、引言高速精冲压力机是现代工业生产中常用的机械设备之一,广泛应用于汽车制造、电子设备、家电等行业。
模具作为高速精冲压力机的关键部件,扮演着至关重要的角色。
然而,长时间高速运行下,模具会经受巨大的冲击和摩擦力,导致磨损、疲劳及裂纹等问题。
因此,理解高速精冲压力机的模具磨损机制,进行合理的分析和预测,对于提高模具使用寿命和生产效率具有重要意义。
二、模具磨损机制分析1. 冲击磨损在高速精冲压力机操作过程中,模具会受到来自上下模的冲击力。
由于高速冲击力的作用,模具表面会出现局部磨损现象。
主要原因包括:(1)冲击引起的金属材料局部位移,导致模具表面接触区域产生微小变形,造成细微的磨损。
(2)冲击引起的局部热量集中,导致模具表面产生凹坑、麻点等磨损形态。
(3)冲击力造成模具上的涂层脱落或剥落。
2. 疲劳磨损高速精冲压力机工作过程中,模具将长时间受到高频率的应力循环,这会导致疲劳磨损。
主要原因包括:(1)冲程过程中的应力导致模具内部结构发生塑性变形,使得模具表面出现微裂纹。
(2)应力循环作用下,微裂纹扩展成为裂纹,最终导致模具疲劳断裂。
(3)由于高速冲击力的作用,模具表面局部区域的硬度和强度差异加大,进一步加剧了可能发生的疲劳磨损。
3. 磨粒磨损在高速精冲压力机的使用过程中,金属粉尘、油脂、氧化物等杂质会引入模具接触表面,与模具材料形成磨粒,导致磨粒磨损。
主要原因包括:(1)金属材料的磨损会形成细小的颗粒,这些颗粒会随着模具的运动在接触面上产生摩擦磨损。
(2)模具表面的晶界、微观缺陷等处容易聚集润滑油脂、氧化物等杂质,并形成磨粒磨损。
(3)杂质的磨粒会引发局部的聚焦磨损,使得磨损程度进一步加深。
三、模具磨损预测方法为了预测高速精冲压力机模具的磨损情况,可以采用以下方法:1. 统计学方法通过对大量模具使用寿命数据进行统计分析,建立模具磨损的寿命分布模型,以预测未来模具的磨损情况。
冲压模具特点及制造过程分析
冲压模具特点及制造过程分析【摘要】冲压模具是冲压工艺中必不可少的工具,具有高效、精度高、生产成本低的特点。
本文从冲压模具的基本特点、主要制造过程、材料选择、设计考虑因素和应用领域等方面进行了分析。
冲压模具的制造过程直接影响着产品的质量和成本,因此需要精心设计和制造。
不同的材料选择和设计考虑因素会影响到模具的使用寿命和生产效率。
冲压模具广泛应用于汽车、家电、电子等领域,在现代工业生产中发挥着重要作用。
通过本文的介绍,读者可以更加深入地了解冲压模具的特点和制造过程,为相关行业的生产提供参考和指导。
【关键词】冲压模具、特点、制造过程、材料选择、设计考虑因素、应用领域、产品质量、成本、现代工业生产1. 引言1.1 冲压模具特点及制造过程分析冲压模具是一种用于生产金属零件的重要工具,在现代工业生产中发挥着重要作用。
冲压模具具有高效、精度高、使用寿命长等特点,能够满足不同形状、尺寸和数量的零件需要。
冲压模具的制造过程对产品质量和成本有着重要影响,因此对冲压模具的特点及制造过程进行分析至关重要。
冲压模具的主要特点包括:高精度、高效率、使用寿命长、操作简单、适应性强等。
冲压模具的制造过程主要包括模具设计、模具加工、热处理、装配和调试等步骤。
冲压模具的材料选择是关键的一步,常见的材料有工具钢、硬质合金等。
冲压模具的设计考虑因素包括零件形状、尺寸、材料、工艺要求等。
冲压模具广泛应用于汽车制造、家电制造、航空航天等领域。
冲压模具在现代工业生产中扮演着重要角色,其制造过程对产品质量和成本有着重要影响。
只有深入分析冲压模具的特点及制造过程,才能更好地应用于实际生产中,提高生产效率,降低生产成本,促进工业发展。
2. 正文2.1 冲压模具的基本特点1. 高效率:冲压模具在生产过程中可以快速、精确地完成加工任务,大大提高了生产效率。
2. 精度高:冲压模具可以在极短的时间内完成高精度的加工,保证了产品的质量和精度要求。
3. 制造成本低:由于冲压模具生产效率高,生产成本相对较低,适用于大规模批量生产。
- 1、下载文档前请自行甄别文档内容的完整性,平台不提供额外的编辑、内容补充、找答案等附加服务。
- 2、"仅部分预览"的文档,不可在线预览部分如存在完整性等问题,可反馈申请退款(可完整预览的文档不适用该条件!)。
- 3、如文档侵犯您的权益,请联系客服反馈,我们会尽快为您处理(人工客服工作时间:9:00-18:30)。
注意点:
1)一般先裁边,冲导正,打预断,压线,打凸点,撕口,(切口,拉伸),后冲孔落料,压毛边,成形,分两步折弯的,先成形一半,后成形另一半
2)在冲孔落料时,一般先冲小孔,后冲大孔;先冲落成形周边的废料,再落其它部位的余料:因為冲小孔若放在后面,那麼它在冲裁时,冲子四周对应料带上的部位可能有缺口(前面已冲过的孔),如此,冲子在冲压过程中,将会引起受力不均(会產生侧向力),本来小孔冲子强度专门弱,加之受力不均,极容易折断,因此这仅是大多数情况,有时依照实际情况需要,小孔冲隻能排在后面,只是方法依旧有的,假如冲子厚度实在太小,可入行补强:A:採用脱板周密导向;B:冲子採用PG(光学研磨)加工.
4:确定是否采纳裁边:
裁边一般用在连续模和落料模上,它的作用起粗定位,在试模时便
于送料;有的裁边还兼有冲外形的作用,假如模具先冲定位针孔,接著立即用引导针导正,一般不用裁边了;没有引导针的,要先裁边,用来定距,一般用在落毛胚的落料模中.
裁边的冲子形状有以下几种﹕
a:这种冲子常用於落料模和厚材裁边中,定位精度低,它的长=步距,宽隻要保証冲子强度即可,常取3.0~6.0
b:这种冲子头部有一个3/4的圆弧(R常取0.3~0.6),它的长<=步距,目的裁边废料卡在裡面,防止跳屑,常用於冲薄材高速模具c;这种冲子同B一样,是它的变羿,其中V形的作用用来卡隹裁边废料防止翻转跳屑,它的角度為50°~70°
d:这种冲子既裁边又兼落外形.
这种台阶头部目的起导向作用,减少侧向力.
5:预断,将要断,但未断的意思(一般放在工站前面)
由於小五金电子產品往往有电镀要求,為电镀方便,冲出来的小產品并不直接落料,而是打个预断留在料带上,电镀后,再用手或机械折两下即可取下来.预断:两面都要切,每边切进的深一般為材料厚度的4/1,如此隻需折两下(往上-往下)就能够產品摘下来;预断冲子和入子头部的宽度為0.02~0.05,角度50°~70°,其长度比预断线的长度每边大0.2~0.5即可.
讲明:為了便於加工和备料以及校模,一般每个厂的各块模板的厚度实行了标準化,厚度大小都规定了(专门情况除外),在连续模中由於是料带的形式,為了方便操纵料带的预压量和模板的平衡性,常在脱料板中间磨出一个料带槽:其槽的深度=材料厚度-0.03~0.05(也确实是讲预压量為3~5条),槽的宽度比料带的宽度大2~4mm即可.因此脱料板的厚度常随材料厚度变化而变化,其大小=脱料板规定厚度+材料厚度-0.03~0.05只是在工程模中,一般不需磨產品槽:因為工程模產品一般较大而不像连续模料带那样窄而细长,也确实是讲工程模脱料板厚度一般不变.
6:确导正孔的大小及位置
一般的连续模都要冲导正,以便后工序的精确定位,在工程模中常用產品零件上的内孔或外形来实现下一工序的定位,若既无内孔,外形又不能用来定位,那麼隻得借助工艺孔了:如第一工程打凸胞,第二工程落外形这种情况,那麼隻好在第一工程中在外形的对角同时冲两个工艺孔(孔大小与材料厚度有关:常用?3.0~6.0)以便下一工序的定位高速冲压模具设计知识
(1)
第一步:產品图的公差缩放缩放原理:由于產品冲出来之后,总是存微小的毛边:其内孔一般偏小,外形一般偏大,至于毛边的大小,
与冲裁间隙和冲子,刀口的锐利程度有关:冲裁间隙越大,毛边俞大,冲子,刀口钝化后,毛边也会增大,故冲子,刀口冲了一定的时刻后,常常需要将刃口磨去0.3~1.0,其毛边到底大多少也与材料厚度有关:一般薄材(T<=0.5)双边大0.01~0.02,厚材(T>0.5)大0.01~0.05
第二步:產品图的尺寸展开
展开原理:利用体积不变的原则:用某一截面的总面积去除以材料厚度可得到该方向的展开长度,事实上展开确实是同一尺寸也因各人经验而羿,没有绝对的一个数值,只要在公差范围即可.
展开要点:步骤如下
1:看明白產品图,想象出它的立体形状以及详细细节的形状(展开前的差不多要求)
2:弄清晰產品的材厚和材质
3:具体展开计算
1):用体积法(一般适合有变薄的弯曲)
2):用展开计算公式
由于產品在弯曲过程中有的地点被拉长或压缩但总能够找到某一层的弯曲线长度是不变的,这一不变的层叫中心层(不是中间层),我们确实是利用中心层来进行展开的;因此,我们要想入行展开,
就必须找出中心层,如图2设中心层系数為K,弯曲内半径為r,材料厚度為t,弯曲角為a,L1,L2為直线部分长度,展开长度值為L,,那麼则有L=L1+L2+2π(r+kt)a/360中心层系数K的大小依照实践经验可按下列公式选取
1):当r/t<=0.50时 k=0.25
2):当0.5<r/t<=1.0时 k=0.25~0.30
3):当1.0<r/t<=2时 k=0.30~0.35
4):当2.0<r/t<=4时 k=0.35~0.40
5):当r/t>4.0时 k=0.40~0.50
此公式适合一切材料厚度的弯曲展开计算,具体在实践应用中,当R/t取上限时, K也应取上限值,如当R/t=1.0时,K=0.30
4:当包圆时,现在展开计算公式已和上面不一样,因為包圆时,内圆受到挤压,外圆被拉伸,但挤压大於拉伸,因此材料变薄专门小,或者几乎不变,中性层接近中间层其展开长度中心层K的系数与材料厚度和包圆内r有关
1):当r/t<=3.0时,中心层系数K=0.45~0.55
2):当3.0<r/t<=6.0时,中心层系数K=0.55~0.65
3):当6.0<r/t<=15.0时,中心层系数K=0.65~0.70
4):当15.0<r/t<=30.0时,中心层系数K=0.70~0.50
5):当r/t>30.0时,中心层系数K=0.50
5:通过查表,找出中心层系数的大小,再进行展开计算也行,在此不作详细叙述
6:產品的圆角处理:產品上的圆角一般保持不变它,但若是尖角,当t<=0.5时,一般用最小圆角R0.15去拟化它;当t>0.5时,用最小圆角R0.2~0.3去拟化它,关于產品上R0.1的圆角,尽量用R0.15去代替;关于R<0.1的圆角或清角,假如是重要尺寸(改变会阻碍功能)则不变它,採用过切来达到要求.
第三步:料带排样设计
排样原理:一根料带通过冲孔落料压毛边拉伸抽蕊弯曲成形各个工序,最后形成產品
的过程,现在你做的如何组织这些工步:哪个在前,哪个在后,总共要多少工步,各工序之间互相调协,使其承前继后,合情合理
排样设计:步骤如下
1:确定產品展开尺寸后,依照產品的毛边方向,确定冲裁和成形方向,无毛边要求时一般不受限制;若產品上有毛边方要求时,这时一定要注意它的冲裁和成形方向:向下依旧向下成形)冲孔毛边留在刀口面,落料毛边留在冲子面:一般机箱外壳类零件出于使用美看和安全性能要求,其毛边要留在產品的里边(成形的内边)假如
图纸上有毛边要求时,则要按要求去做,没写毛边要求应尽量让毛边留在裡边,若成形更方便,也可留在外边.
2:依据產品展开尺寸,粗畋估算步距(PITCH=產品该方向最大长度+1.0~2.0-中间有连接带除外)用ARRAY命令作出横排,纵排,对称排,交错排,斜排(专门少用)几种方案,进行分析,比较,综合,在保証產品顺利生產出来的前提下,选择最佳方案.具体注意以下几点:
1):第一要考虑如此排成形是否容易和稳定,后一工步是否对前一工步已成形好的產生破坏作用,或者后一工步无法成形,冲子和渗透子强度是否足够
2):第二要考虑料带在模具中能否顺利送料,前一工步成形之后能否接着平稳送到下一工步包括考虑浮升高度和连接带的位置及强度浮升高度越低越好,一般不起过下模板厚度的1/2:因為太高易引起摆动,料带定位不淮和变形;连接带(又叫载体-CARRY)有以下几种形式:
1>:无连接带,属於无废料排样,零件外形往往具有对称性和互补性,通常採用单PIN切断落料或双PIN一个落料一个切断, 2>:边料连接带,是利用条料搭边废料作為载体的一种形式,这种载体传送料带强度较好,简单,要紧用於落料型排样中,
3>:单连接带,是在產品条料的一侧留出一定宽度的材料,并在适当位置与產品相连接,实现对產品条料的运送,一般适合切边型排样,
4>:双连接带,是在產品条料的两侧分不留出一定宽度的材料,并在适当位置与產品两边相连接,实现对產品条料的运送,它比单连带运送更顺利,料带定位精度更高,它适合產品两端都有接口可连,特不适合材料(t<=0.4)较薄时,料带运送强度较弱的情况
5>:中心连接带,与单载体相似,是在產品条料的中间留出一定宽度的材料,并与產品前后两边相连它比前者节约材料,在弯曲工件排样中应用较多;因為导正梢孔在中间常引起拉料,故常需在引导针中间交错加一些弹性顶料定位针,连接带的选取总结如下:
產品展开之后,认真分析產品的各个部位,哪些地点需要成形,哪些地点是仅仅落料,然后在落料的地点选择恰当的位置引出连接带,使之既能保証料带的平稳运送,又不阻碍產品的成形;至於选择什麼类型的连接带,要依照產品的特点而定. 确定產品展开尺寸后,依照產品的毛边方向,确定冲裁和成形方向,无毛边要求3):第三当碰到L形弯曲或產品单排时材料利用率太低,可考虑对称排交错排,如此对称成形受力均匀,成形稳定;或者材料利用率可大大提高。