航空复合材料疲劳性能研究
飞行器材料疲劳行为实验研究

飞行器材料疲劳行为实验研究在航空航天领域,飞行器的安全性和可靠性至关重要。
而飞行器材料的疲劳行为直接影响着飞行器的使用寿命和飞行安全。
为了深入了解飞行器材料在复杂工况下的疲劳性能,进行系统的实验研究是必不可少的。
飞行器在飞行过程中会承受多种载荷的作用,如气动压力、振动、温度变化等。
这些载荷的反复作用会导致材料内部产生微小的裂纹,并逐渐扩展,最终可能导致结构失效。
因此,研究飞行器材料的疲劳行为对于保障飞行器的安全运行具有重要意义。
在实验研究中,首先需要选择合适的材料进行测试。
常用的飞行器材料包括铝合金、钛合金、复合材料等。
这些材料具有不同的力学性能和疲劳特性,需要根据具体的应用场景进行选择。
实验设备是进行疲劳实验的关键。
常见的疲劳实验设备包括电液伺服疲劳试验机、电磁共振疲劳试验机等。
这些设备能够精确地施加各种载荷,并实时监测材料的响应。
在实验设计方面,需要考虑多种因素。
例如,载荷类型(拉伸、压缩、弯曲等)、载荷幅值、加载频率、环境条件(温度、湿度等)等。
通过合理设计实验参数,可以模拟飞行器在实际飞行中的工况,从而获得更准确的实验结果。
以铝合金为例,进行拉伸疲劳实验。
首先,将制备好的铝合金试样安装在疲劳试验机上,并设置好加载参数。
在实验过程中,通过传感器监测试样的应变和位移变化。
随着加载循环次数的增加,可以观察到试样表面逐渐出现微小的裂纹。
继续加载,裂纹会不断扩展,直至试样断裂。
在实验过程中,还需要对试样进行微观组织观察。
通过光学显微镜、电子显微镜等设备,可以观察到材料内部的微观结构变化,如位错运动、晶界滑移等。
这些微观结构的变化与材料的疲劳行为密切相关。
对于钛合金材料,由于其具有高强度和良好的耐腐蚀性,在飞行器中的应用越来越广泛。
在进行钛合金的疲劳实验时,需要特别关注其在高温环境下的性能。
高温会导致材料的强度降低,从而影响其疲劳寿命。
复合材料在飞行器中的应用也日益增多。
与传统金属材料相比,复合材料具有更高的比强度和比刚度,但也存在着一些独特的疲劳问题。
飞行器适航性与材料疲劳分析

飞行器适航性与材料疲劳分析在现代航空航天领域,飞行器的适航性和材料疲劳问题是至关重要的研究课题。
适航性关乎着飞行器的安全运行,而材料疲劳则是影响飞行器结构可靠性和寿命的关键因素。
飞行器适航性是指飞行器在预期的运行环境和条件下,能够安全飞行并且符合相关法规和标准的特性。
这涵盖了从设计、制造到运营维护的整个生命周期。
为了确保飞行器适航,需要进行严格的适航审定程序。
适航审定主要包括对飞行器的设计评估、试验验证以及持续适航管理。
在设计阶段,工程师必须考虑各种可能的飞行条件和潜在风险,如气象条件、机械故障、人为操作失误等,并采取相应的设计措施来保障飞行器的安全性。
材料疲劳则是由于材料在循环载荷作用下,逐渐产生局部永久性结构变化,在一定的循环次数后形成裂纹并扩展,最终导致材料失效的现象。
对于飞行器而言,材料疲劳是一个不容忽视的问题。
因为飞行器在飞行过程中会不断承受各种动态载荷,如气动压力、振动、冲击等,这些载荷的反复作用会使材料逐渐疲劳。
飞行器结构中常用的材料包括铝合金、钛合金、复合材料等。
铝合金具有良好的加工性能和耐腐蚀性能,但在高强度使用下容易出现疲劳问题。
钛合金强度高、耐高温,但成本较高。
复合材料具有优异的比强度和比刚度,但在复杂环境下的性能稳定性和疲劳特性还需要进一步研究。
在飞行器的设计和制造过程中,对材料疲劳的分析和预测是非常重要的。
这需要借助先进的实验技术和分析方法。
实验方面,通常会进行疲劳试验,包括高周疲劳试验和低周疲劳试验,以获取材料的疲劳性能数据。
分析方法则包括有限元分析、损伤力学分析等。
有限元分析可以模拟飞行器结构在不同载荷条件下的应力分布,从而预测可能出现疲劳裂纹的位置和扩展趋势。
损伤力学分析则从微观角度研究材料内部的损伤演化过程,为疲劳寿命预测提供理论基础。
为了提高飞行器的适航性和减少材料疲劳带来的风险,在设计阶段就需要采取一系列措施。
例如,优化结构设计,避免应力集中;采用合理的连接方式,减少局部疲劳损伤;选择合适的材料和加工工艺,提高材料的疲劳性能。
复合材料疲劳性能的实验研究

复合材料疲劳性能的实验研究在现代工程领域中,复合材料因其卓越的性能而备受关注。
复合材料具有高强度、高刚度、良好的耐腐蚀性等优点,广泛应用于航空航天、汽车、船舶等众多领域。
然而,在实际应用中,复合材料往往会承受循环载荷的作用,其疲劳性能就成为了一个至关重要的研究课题。
复合材料的疲劳性能不同于传统材料,它受到多种因素的影响。
首先,复合材料的组分和微观结构对疲劳性能有着显著的影响。
例如,增强纤维的类型、含量、分布以及基体的性能都会改变复合材料的疲劳行为。
其次,制造工艺也会对其疲劳性能产生作用。
不同的成型方法可能导致复合材料内部存在不同程度的缺陷和残余应力,从而影响其疲劳寿命。
为了深入研究复合材料的疲劳性能,我们进行了一系列精心设计的实验。
实验中,选用了常见的碳纤维增强环氧树脂基复合材料作为研究对象。
首先,对试样进行了严格的制备和预处理,以确保实验结果的准确性和可靠性。
在疲劳实验中,采用了先进的疲劳试验机,并设定了不同的加载频率、应力幅和应力比等参数。
通过控制这些参数,可以模拟复合材料在实际使用中所面临的各种疲劳工况。
在实验过程中,利用高精度的传感器实时监测试样的应变、位移等参数,并将数据传输至计算机进行存储和分析。
经过大量的实验数据积累和分析,我们发现了一些有趣的现象和规律。
首先,随着应力幅的增加,复合材料的疲劳寿命明显缩短。
这是因为较大的应力幅会导致材料内部的损伤更快地累积和扩展。
其次,加载频率对疲劳寿命也有一定的影响。
在较低的加载频率下,复合材料有更多的时间进行能量耗散和损伤修复,从而表现出相对较长的疲劳寿命。
进一步对疲劳失效后的试样进行微观分析发现,疲劳裂纹的萌生和扩展机制非常复杂。
在纤维与基体的界面处,由于应力集中容易产生微裂纹。
这些微裂纹会随着循环载荷的作用逐渐扩展,最终导致材料的失效。
此外,纤维的断裂、基体的开裂以及纤维与基体的脱粘等现象也在疲劳失效过程中起到了重要的作用。
通过对复合材料疲劳性能的实验研究,我们不仅深入了解了其疲劳行为的规律和机制,还为复合材料的设计和应用提供了重要的依据。
复合材料的疲劳性能与性能研究

复合材料的疲劳性能与性能研究在现代工程领域中,复合材料凭借其卓越的性能表现,已经成为众多关键应用中的首选材料。
然而,要充分发挥复合材料的优势,深入理解其疲劳性能和其他相关性能至关重要。
复合材料是由两种或两种以上具有不同物理和化学性质的材料组合而成。
常见的复合材料包括纤维增强复合材料(如碳纤维增强复合材料、玻璃纤维增强复合材料)和层合复合材料等。
这些材料通常具有高强度、高刚度、良好的耐腐蚀性和轻质等优点,使其在航空航天、汽车、船舶、体育用品等领域得到了广泛应用。
疲劳性能是评估材料在循环载荷作用下抵抗破坏能力的重要指标。
对于复合材料而言,其疲劳行为较为复杂,受到多种因素的影响。
首先,复合材料的组成成分,如增强纤维和基体材料的性质,对疲劳性能起着关键作用。
一般来说,高强度的纤维能够提供更好的抗疲劳能力,而基体材料的韧性和粘结性能则影响着纤维与基体之间的载荷传递效率。
其次,复合材料的制造工艺也会显著影响其疲劳性能。
例如,纤维的排列方向和分布均匀性、制造过程中的孔隙率和缺陷等,都会在疲劳过程中成为裂纹萌生和扩展的源头。
此外,加载条件,包括载荷的大小、频率、波形以及环境因素(如温度、湿度、化学介质等),也会对复合材料的疲劳寿命产生重要影响。
在研究复合材料的疲劳性能时,常用的实验方法包括疲劳试验和疲劳寿命预测模型。
疲劳试验通常在专门的试验机上进行,通过施加循环载荷来观察材料的失效行为,并记录疲劳寿命数据。
为了更准确地评估复合材料在实际使用条件下的疲劳性能,还会进行模拟实际工况的复杂加载和环境条件下的试验。
疲劳寿命预测模型则是基于实验数据和理论分析,试图建立起材料性能、载荷条件和疲劳寿命之间的定量关系。
常见的预测模型包括基于应力寿命(SN)曲线的方法、基于损伤力学的方法以及基于概率统计的方法等。
这些模型在一定程度上能够帮助工程师在设计阶段预估复合材料结构的疲劳寿命,从而优化设计,提高结构的可靠性。
除了疲劳性能,复合材料的其他性能也同样值得关注。
复合材料的抗疲劳性能研究

复合材料的抗疲劳性能研究在现代工程领域中,复合材料凭借其优异的性能,如高强度、高刚度、良好的耐腐蚀性等,得到了广泛的应用。
然而,要确保复合材料在长期使用中的可靠性和安全性,对其抗疲劳性能的研究至关重要。
复合材料的疲劳失效是一个复杂的过程,涉及到多种因素的相互作用。
首先,复合材料的组成成分和微观结构对其抗疲劳性能有着显著影响。
通常,复合材料由增强纤维和基体材料组成,纤维的类型、长度、分布以及与基体的结合强度等都会改变材料的疲劳特性。
例如,碳纤维增强复合材料具有较高的强度和刚度,但在疲劳过程中,纤维与基体之间的界面容易出现脱粘和微裂纹,从而降低其抗疲劳性能。
加载条件也是影响复合材料抗疲劳性能的重要因素。
不同的加载方式,如拉伸、压缩、弯曲、扭转等,会导致材料内部的应力分布和损伤机制有所不同。
而且,加载频率、应力幅和平均应力等参数的变化也会对疲劳寿命产生明显的影响。
高频加载可能会使材料产生热效应,加速疲劳损伤;而较大的应力幅和平均应力则会缩短疲劳寿命。
环境因素同样不可忽视。
温度、湿度、化学介质等外界环境条件会影响复合材料的性能。
高温可能导致基体软化、纤维性能下降,从而降低抗疲劳能力;湿度会使材料吸收水分,引起基体膨胀和界面弱化,进而影响疲劳寿命;化学介质的侵蚀则可能破坏材料的微观结构,加速疲劳失效。
为了研究复合材料的抗疲劳性能,科研人员采用了多种实验方法和分析技术。
疲劳试验是最直接的手段之一,通过对试样施加循环载荷,记录疲劳寿命和损伤演化过程。
常见的疲劳试验包括恒幅疲劳试验、变幅疲劳试验和随机疲劳试验等。
同时,借助显微镜、扫描电子显微镜(SEM)、X 射线衍射等技术,可以对疲劳损伤的微观形貌和结构变化进行观察和分析,深入了解疲劳失效的机制。
在理论研究方面,基于连续介质力学和损伤力学的理论模型被广泛应用于复合材料疲劳性能的预测。
这些模型考虑了材料的微观结构、加载条件和损伤演化规律,能够在一定程度上预测复合材料的疲劳寿命和性能变化。
新型复合材料在飞行器制造中的应用研究
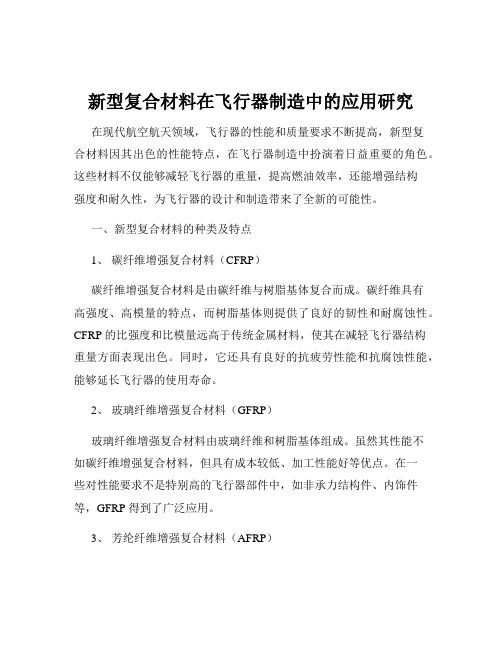
新型复合材料在飞行器制造中的应用研究在现代航空航天领域,飞行器的性能和质量要求不断提高,新型复合材料因其出色的性能特点,在飞行器制造中扮演着日益重要的角色。
这些材料不仅能够减轻飞行器的重量,提高燃油效率,还能增强结构强度和耐久性,为飞行器的设计和制造带来了全新的可能性。
一、新型复合材料的种类及特点1、碳纤维增强复合材料(CFRP)碳纤维增强复合材料是由碳纤维与树脂基体复合而成。
碳纤维具有高强度、高模量的特点,而树脂基体则提供了良好的韧性和耐腐蚀性。
CFRP 的比强度和比模量远高于传统金属材料,使其在减轻飞行器结构重量方面表现出色。
同时,它还具有良好的抗疲劳性能和抗腐蚀性能,能够延长飞行器的使用寿命。
2、玻璃纤维增强复合材料(GFRP)玻璃纤维增强复合材料由玻璃纤维和树脂基体组成。
虽然其性能不如碳纤维增强复合材料,但具有成本较低、加工性能好等优点。
在一些对性能要求不是特别高的飞行器部件中,如非承力结构件、内饰件等,GFRP 得到了广泛应用。
3、芳纶纤维增强复合材料(AFRP)芳纶纤维具有优异的抗冲击性能和耐高温性能,与树脂基体复合后形成的 AFRP 在防弹、抗冲击防护等方面具有独特的优势。
在飞行器制造中,AFRP 常用于制造飞机的舱门、机翼前缘等部位,以提高飞行器的抗冲击能力和安全性。
4、陶瓷基复合材料(CMC)陶瓷基复合材料具有耐高温、高强度、抗氧化等优异性能,适用于飞行器的高温部件,如发动机热端部件、燃烧室等。
CMC 能够承受高温燃气的冲刷和腐蚀,提高发动机的工作效率和可靠性。
二、新型复合材料在飞行器结构中的应用1、机翼和机身结构新型复合材料在机翼和机身结构中的应用可以显著减轻重量,提高结构效率。
例如,波音 787 客机的机身结构大量采用了 CFRP,其重量比传统铝合金机身减轻了 20%左右,大大降低了燃油消耗。
同时,复合材料的可设计性使得机翼和机身的气动外形能够得到更精确的优化,提高了飞行器的飞行性能。
复合材料层合板的疲劳寿命预测及试验研究

复合材料层合板的疲劳寿命预测及试验研究复合材料层合板是一种新型材料,具有高强度、高刚度、高韧性和轻质等优点。
在航空航天、汽车、船舶、电子、建筑等领域得到广泛应用。
然而,随着使用寿命的延长,复合材料层合板会出现疲劳损伤,从而降低其力学性能。
疲劳寿命是衡量复合材料层合板耐久性能的重要指标,因此,如何准确预测复合材料层合板的疲劳寿命成为了当前研究的热点问题。
一、复合材料层合板的疲劳损伤机理复合材料层合板的疲劳损伤主要有三种形式:疲劳裂纹、层间剥离和纤维失效。
疲劳裂纹是指由于反复的载荷作用产生的疲劳应力,使材料中的裂纹逐渐扩展,从而导致断裂。
层间剥离是指复合材料层合板中各层之间的粘结剪切层界面发生分离,最终导致层间脱粘。
纤维失效是指纤维断裂或拉断,导致复合材料层合板的强度和刚度下降。
二、复合材料层合板疲劳寿命预测方法为了准确预测复合材料层合板的疲劳寿命,需要对其力学性能进行测试和分析,确定其材料参数和疲劳性能。
一般采用有限元方法进行疲劳寿命预测,即将复合材料层合板的结构分解成有限数量的小单元,再利用计算机模拟每个小单元的力学性能,然后将这些小单元组合起来,得出整个结构体系的力学性能及其变化规律,从而得出疲劳寿命。
三、复合材料层合板疲劳寿命试验研究复合材料层合板疲劳试验是验证疲劳寿命预测结果的重要手段。
疲劳试验主要通过模拟实际使用条件,采用交变载荷或者脉冲载荷进行,测量材料的疲劳性能,并记录试验过程中的变形、裂纹扩展和层间剥离等信息。
通过试验可以得到复合材料层合板受不同载荷和振幅下的疲劳寿命,为研究和改善其力学性能提供参考。
四、复合材料层合板疲劳寿命预测和试验研究的应用复合材料层合板作为航空航天、汽车、船舶、电子、建筑等领域中的主要结构材料,其使用寿命和安全性是极为关键的。
通过复合材料层合板疲劳寿命预测和试验研究,可以为其设计和制造提供科学依据,为改善其力学性能提供技术支持和保障。
结语随着科技的不断推进,复合材料层合板在各个领域的应用越来越广泛。
航空器材料的疲劳与断裂特性研究

航空器材料的疲劳与断裂特性研究在航空领域,航空器的安全与可靠性是至关重要的。
而航空器材料的疲劳与断裂特性直接关系到飞机的使用寿命、飞行安全以及运营成本。
因此,对航空器材料疲劳与断裂特性的深入研究具有极其重要的意义。
航空器在飞行过程中,会经历各种复杂的载荷和环境条件。
比如,起飞和降落时的巨大冲击力,高空的低温、低压环境,以及飞行中的振动等。
这些因素都会对航空器材料造成持续的影响,导致材料逐渐出现疲劳损伤。
疲劳是指材料在循环载荷作用下,经过一定次数的循环后,发生局部永久性结构变化,并在一定的循环次数后形成裂纹、扩展直至最终断裂的过程。
疲劳破坏与静载破坏不同,它通常没有明显的塑性变形,往往在毫无预兆的情况下突然发生,给飞行安全带来极大的威胁。
航空器材料的疲劳特性受到多种因素的影响。
首先是材料本身的性质,包括化学成分、组织结构、强度和韧性等。
一般来说,高强度材料往往具有较低的韧性,更容易发生疲劳断裂。
其次,载荷的特性也起着关键作用。
载荷的大小、频率、波形以及加载顺序等都会影响材料的疲劳寿命。
例如,高频加载会使材料更快地出现疲劳损伤,而复杂的加载顺序可能导致累积损伤加剧。
再者,环境因素同样不容忽视。
腐蚀环境会加速材料的疲劳损伤,降低其疲劳寿命。
温度的变化也会影响材料的性能,高温可能导致材料强度下降,低温则可能使材料变脆。
断裂是材料在承受载荷时发生的突然破裂现象。
对于航空器来说,断裂可能导致灾难性的后果。
断裂特性的研究主要包括断裂韧性和裂纹扩展速率等方面。
断裂韧性是衡量材料抵抗裂纹扩展能力的重要指标。
具有高断裂韧性的材料能够在存在裂纹的情况下继续承受载荷,而不会轻易发生断裂。
在航空器设计中,选用具有高断裂韧性的材料可以提高结构的安全性。
裂纹扩展速率则描述了裂纹在材料中扩展的速度。
了解裂纹扩展速率对于预测材料的剩余寿命和制定维护计划至关重要。
通过对裂纹扩展速率的研究,可以确定在不同载荷和环境条件下,裂纹发展到危险程度所需的时间。
- 1、下载文档前请自行甄别文档内容的完整性,平台不提供额外的编辑、内容补充、找答案等附加服务。
- 2、"仅部分预览"的文档,不可在线预览部分如存在完整性等问题,可反馈申请退款(可完整预览的文档不适用该条件!)。
- 3、如文档侵犯您的权益,请联系客服反馈,我们会尽快为您处理(人工客服工作时间:9:00-18:30)。
link appraisement刘牧东(1990-)男,博士,工程师。
主要研究方向:直升机结构疲劳和损伤容限设计。
中国直升机设计研究所 结构强度研究室本文针对近年来航空复合材料疲劳性能研究现状,从试验、模型表征和寿命估算三个方面进行归纳和分析,并指出了目前尚未解决、中国科技信息2019年第1期·CHINA SCIENCE AND TECHNOLOGY INFORMATION Jan.2019◎航空航天而在压-压循环载荷作用下,复合材料层合板的剩余强度降低。
方光武等在对2D针刺C/SiC复合材料进行拉-拉疲劳试验,结果表明:2D针刺C/SiC复合材料具有较好的抵抗疲劳能力,随着加载循环次数的增加,其剩余强度先增大后减小。
Schon J根据飞机机翼实测载荷谱进行加载,对碳纤维/环氧树脂基复合材料连接件进行疲劳试验,试验结果表明:低于复合材料疲劳极限的应力循环对试样的疲劳寿命不产生影响,考虑这一因素,滤去载荷谱中的低应力循环能够加快试验进度且保证试验结果的有效性。
Zhang C等试验研究了2.5D-C/SiC复合材料的纵向和横向疲劳性能,发现纵向的疲劳极限是横向的1.5倍,这是由于纵向和横向的纤维束数量不同导致。
在试验的基础上,常采用扫描电镜(SEM)分析复合材料试样断口的微观结构,探寻循环载荷下航空复合材料损伤机理的变化。
冯培锋等对玻璃纤维和碳纤维增强复合材料层合板进行断口分析,发现在不同的应力水平加载下试样的损伤机理明显不同:在低应力水平加载下,试样断裂失效前出现大量的疲劳损伤,而在高应力水平下,试样经历的疲劳损伤较少。
Pandita SD和Verpoest I对平面编织和针织纤维复合材料的断口分析显示:平面编织纤维复合材料的疲劳失效形式与加载方向有关,其中轴向加载下以纤维失效为主,而偏轴加载下以基体失效为主;平面针织纤维复合材料的疲劳裂纹均在与载荷方向垂直的织物处萌生,之后沿着针织方向进行扩展。
王军等对T300和T700碳纤维增强复合材料进行断口分析,发现:与T300相比,T700碳纤维的延伸率较大,从而T700复合材料层合板的疲劳寿命分散性更小;同时,T700碳纤维表面更光滑,纤维与树脂基体的界面性能较弱,导致T700复合材料层合板断口处的分层和劈丝现象明显。
Zhang C等对2.5D-C/SiC复合材料的断口分析显示:复合材料的疲劳裂纹主要在纤维束交叉位置萌生,而疲劳裂纹的扩展导致了复合材料的断裂失效。
Luo Z等对SiC/SiC复合材料进行断口分析,发现:在超过材料比例极限的高应力水平加载下,疲劳载荷主要由纤维承受;在低于材料疲劳极限的低应力水平加载下,疲劳载荷主要由基体承受;而对于比例极限与疲劳极限之间的应力水平,其疲劳载荷由纤维和基体共同承受。
航空复合材料疲劳性能模型表征研究在循环载荷作用下,航空复合材料的疲劳性能常借用Basquin模型进行表征。
Caprino G和Giorleo G考虑应力比的影响对Basquin模型进行修正,并采用威布尔分布模拟失效概率,根据修正的Basquin模型绘制了复合材料疲劳性能S-N曲线,与试验数据吻合良好。
Petermann J和Plumtree A在Basquin模型的基础上,考虑复合材料开裂面上正应力和剪应力的影响,提出了单向复合材料层合板的统一疲劳寿命失效模型,能够评估单向层合板在不同方向和应力比加载下的疲劳性能,模型的有效性在试验中得到了验证。
Epaarachchi JA和Clausen PD同时考虑了加载频率和应力比的影响对Basquin模型进行非线性修正,修正模型的分析结果表明:在相同环境温度下,玻璃纤维增强复合材料的疲劳寿命分别随着加载频率和加载应力比的增大而线性提高。
Xiong JJ和Shenoi RA将n次循环后的剩余强度()R n引入Basquin模型,提出了复合材料疲劳性能n-S-R曲面模型,模型可以有效表征复合材料在不同应力水平和剩余强度下的疲劳寿命,计算结果与试验相差不大。
剩余刚度模型也常用于航空复合材料疲劳性能的表征,一些学者对此进行了研究,万志敏和赵承杰将复合材料层合板的性能作为随机变量进行表征,提出了剩余刚度衰减模型,建立了剩余刚度分布函数,并给出剩余刚度与疲劳寿命之间的关系,模型的预测结果与试验吻合良好。
Paepegem WV等和Tserpes KI等针对复合材料的面内循环加载问题,提出了表征刚度退化、应力分配和永久变形的剩余刚度模型,构建了复合材料的应力-应变-损伤函数关系,模拟疲劳演化规律。
Xiong JJ等在n-S-R曲面的基础上进一步提出应变控制下的复合材料剩余刚度曲面模型,考虑了n次循环后剩余刚度下降的影响,模型预测结果在碳纤维/环氧树脂基复合材料的试验中得到了验证。
此外,廉伟和姚卫星还提出了剩余刚度-剩余强度的关联模型,给出了基于剩余刚度和剩余强度的损伤定义间的关系,并通过试验对模型进行校验,分析表明:剩余刚度-剩余强度关联模型能较好地描述各类铺层复合材料的刚度退化规律,并能符合复合材料疲劳损伤的演化机制。
航空复合材料在循环载荷作用下的分层扩展性能常借用Paris模型进行表征,Schön J和Allegri G等考虑应力比对复合材料分层扩展性能的影响,在Paris模型的基础上,提出了修正的分层扩展速率表征模型,模型分析结果表明:随着应力比的提高,复合材料的分层扩展速率减慢;与Paris模型相比,修正模型的拟合精度更高,能更好地描述分层扩展性能的变化规律。
Shivakumar K等和Murri GB 在Paris模型的基础上引入能量释放率门槛值Ith G和分层断裂韧性IR G,同时考虑了分层扩展的近门槛区、稳定扩展区和快速扩展区3个阶段,提出了表征复合材料分层扩展性能的全范围模型,模型的预测精度高,但需要大量的试验数据确定待定参数,限制了在工程上的应用。
Yun XY等基于欧拉梁和断裂力学理论,考虑应力比效应的影响,提出了复合材料层合板II型分层扩展能量释放率II G∆的表示方法,并借助Paris模型表征II型分层扩展速率,分析结果的有效性在碳纤维/环氧树脂基复合材料的II型分层扩展试验中得到了验证。
此外,还借助内聚力模型表征航空复合材料的分层扩展性能,Barenblatt GI在描述疲劳裂纹的演化时引入了内聚力的概念,提出了内聚力模型,模型的主要参数有反映疲劳裂纹萌生的最大界面强度σc和反映裂纹扩展的断裂韧性Gc,从而将疲劳裂纹萌生和扩展相结合,能有效表征复合材料的分层扩展特性。
航空复合材料疲劳寿命估算研究航空复合材料的疲劳寿命常借助不考虑载荷交互作用的线性累积损伤Miner理论进行估算,Bond IP借助雨流计数法对实测载荷谱进行处理,之后采用Miner理论估算复杂时间加载历程下的疲劳寿命,结果的有效性在玻璃纤维复合材料试验中得到了验证。
Yao WX和Himmel N假定循环载(下转第33页)CHINA SCIENCE AND TECHNOLOGY INFORMATION Jan.2019·中国科技信息2019年第1期航空航天◎图5 综合飞控测试软件主界面表1 综合飞控计算机系统验证设备测试结果序号测试项测试内容测试结果1接口测试模拟量精度、离散量输入输出信号、ARINC 429信号、1553B 信号、电源输出检测正确2软件模块测试捷联航姿模块、激光惯导模块、大气/无线电高度模块、EICAS 模块、襟翼模块、驾驶仪伺服模块、EFIS 模块、油门杆伺服模块、故障注入模块各模块正确3功能测试上电测试、设备自检、系统测试功能正确4仿真测试静态测试、动态测试符合设计要求5系统联试测试整个设备在系统中的使用符合设计要求结束语针对综合飞控计算机地面开、闭环仿真试验,设计开发了半物理仿真平台,为综合飞控计算机的研制建立的一套完整的软硬件开发、检测、验收测试、维护的平台,并为综合飞控计算机提供了静、动态的地面仿真环境。
该系统能够在综合飞控计算机出厂前进行检测和验证,从而及早的消除了故障隐患,避免事故的发生,提高了设备的可靠性,确保后续飞行的安全。
荷造成的疲劳损伤与复合材料的剩余强度成正比,建立了疲劳损伤增量与瞬时剩余强度的函数关系,并采用线性累积损伤Miner 理论预测碳纤维增强复合材料的疲劳寿命,预测结果与试验吻合良好。
Choi SW 等基于恒载疲劳试验数据,采用Miner 理论计算各个应力水平造成的疲劳损伤,当损伤累积达到允许值1时,复合材料层合板发生断裂失效,获得实测载荷谱加载下的疲劳寿命,具有不错的预测精度。
Cain KJ 等和齐红宇等考虑应变等效原理构建复合材料刚度衰减与疲劳损伤的关系,并采用Miner 理论预测疲劳寿命,计算结果表明:复合材料层合板剪切方向上的疲劳累积损伤最大;疲劳累积损伤与微裂纹的聚合程度有关,当微裂纹聚合困难时疲劳累积损伤较小,而当微裂纹聚合成主裂纹时疲劳累积损伤较大,寿命预测结果与试验的最大相对偏差为12.2%。
刘关心等考虑循环载荷作用下复合材料层合板刚度和强度退化的影响构建出双参数疲劳模量的衰减模型,并采用Miner 理论估算其在变幅载荷作用下的疲劳寿命,具有较高的预测精度。
罗晓平和曹国廷以直升机复合材料桨叶为研究对象,建立ε-N 曲线模型,之后利用线性累积损伤Miner 理论预测疲劳寿命,并研究不同飞行任务剖面和桨叶载荷对疲劳寿命的影响,计算结果表明复合材料桨叶在常规飞行状态下为无限寿命设计,Miner 理论能有效评估直升机复合材料结构的疲劳寿命。
此外,一些学者还借助有限元仿真分析航空复合材料的疲劳性能,并采用Miner 理论预测寿命,Attia O 等和Tserpes KI 等借助有限元仿真模拟复合材料疲劳失效的渐进损伤过程,之后采用修正的Paris 模型和线性累积损伤Miner 理论估算疲劳寿命,计算结果与试验吻合良好。
Wahab MMA 等借助有限元仿真分析复合材料胶接结构的应变能释放率,并基于Paris 模型建立了失效循环的积分表示方法,之后采用Miner 理论估算疲劳寿命,由于没有考虑疲劳裂纹萌生和小裂纹扩展的影响,估算结果偏于保守。
徐颖等和郭葳等基于ANSYS 有限元软件,利用APDL 语言开发了复合材料层合板的疲劳渐进损伤分析程序,能够模拟不同铺层顺序和尺寸的层板试样疲劳裂纹萌生、裂纹扩展和失效的全过程,为复合材料疲劳寿命预测提供帮助。
广布疲劳损伤是工程结构中广泛存在的一种损伤形式,由于疲劳裂纹间的相互作用,导致结构的剩余强度下降,临界裂纹尺寸缩短,疲劳寿命明显减少,从而对结构安全造成严重影响。
针对金属结构的广布疲劳损伤问题,常基于断裂力学理论建立疲劳裂纹萌生的表征模型,并借助有限元仿真模拟应力场,之后采用蒙特卡洛随机理论分析疲劳裂纹的扩展和演化过程,估算金属结构的剩余寿命。