焊缝自动跟踪系统的设计
基于DSP的管道TIG焊焊缝跟踪系统

焊工 的经 验来选 择 。
1 焊 缝跟 踪 试 验 系 统
要 实现 管道焊接 的全 自动 化 ,首先 需要研 制焊缝 跟踪 系统 ,对焊 缝进行 识 别 ,并 通过调 节焊 炬位 置和 焊接 参 数来适应 各 种焊接 状态 。将视 觉传 感技术应 用 于焊缝 跟踪 是 当前 焊缝 跟踪 系统研 究 的主 流 。
本文 以水 下高压 管道 T I G焊 为背 景 , 提 出 了一种管 道焊缝 跟踪 系统 。该系统 包括 5轴 管道焊接 装 置及 其配 套 的控 制器 和视 觉传感 系统 ,可 以使焊炬 和视觉 传感 器 自动地 到达 即将焊接 的位 置 。视觉 传
0 引 言
在 海洋 石油 开发 中,诸如 钢塔 建造 以及水 、油 、气输送 等 工程项 目实 施要求 大规 模制造 和精确 地 焊接 管 道结构 。管 道焊接 中应 用最广 泛 的是 圆周 电弧焊 ,包 括打 底焊 和填 充焊 。管道坡 口的制造误 差 会 导致 变形和 偏心 ,且缝 隙大 小与焊 缝位 置不 匹配 。由于 打底成 形 的不规 则性 ,不 能将 焊接 参数和 焊 炬位 置 设置为恒 定 参数 。因此 , 实现 管道焊 接全 自动化 非常 困难 , 通 常需要 熟练 的焊 工进行 人工干 预 。
的清 晰程 度 ,有两个 办 法可 以用 来减 少这 种干 扰 【 5 ] ,一种 办法 是利 用某 一种 金属元 素 的线状 光谱来 过 滤氩 元 素 的线 状光 谱 ,这种 办 法要 求 带宽很 窄 的滤 光 镜 ;另一 种办 法是 过滤 线状光 谱 ,仅使 用强度 相 对较 低 的连续 光 谱 。 本文 中的滤 光系 统采 用 的是后 者 。 从 光谱 图上 可 以明显地 发现 , 在波 长大 于 8 6 0 n m 的近 红外 光谱 范 围 内,几乎 没有 线状 光谱 ,而连 续 光谱 的强度 也很 弱 ,如 图 2 f b ) 所 示 ,因此 ,这个 范
焊缝自动跟踪系统x 孙中皋1

[3 - 4 ]
带中心 ,提取出焊缝的特征点位置 ,将焊缝偏差信 号送入伺服电机控制系统 ,对焊缝进行实时跟踪 .
1 系统结构及工作原理
本系统硬件包括工业控制计算机 、 伺服电机 、 PLC 控制器 、 CCD 传感器 、 激光发生器 、 基于 PCI 总线的 DH - CG400 图像采集卡 、 KPCI824 模拟量 输出卡和 KPCI840 开关量输入输出卡等 , 系统结 构如图 1 所示 . 视觉传感器采用激光以一定角度 照射 , 摄像头垂直接 收 的 方 式 . 工 作 过 程 中 , CCD 摄像头采集到的图像由图像采集卡输入到工 业控制计算机 , 工控机处理图像求出焊缝的中心 位置并将偏差量送给伺服系统 , 通过跟踪结构调 整探伤仪和 CCD 摄像头的位置 ,从而对焊缝实现 实时跟踪 . 整个系统的操作和逻辑控制通过 PLC 控制器由操作台发送给 IΠ O 接口 . 焊缝跟踪原理 如图 2 所示 .
× 256 大小的图像所用时间不超过 50 ms , 完全满 足实时处理的要求 , 实现了焊缝偏差的实时检测 和调节 . 该系统的跟踪精度和调整能力都达到了 设计要求 ,已在工厂中实际应用 ,取得了令人满意 的效果 .
[1 ]SUG A Y,MUTO A , K UMAG AI M. Automatic tracking of welding line by autonomous mobile robot for welding of plates( tracking of linear and angled welding lines) [J ] . Transactions of the Japan Society of Mechanical Engineers , 1997 ,63(612) :2918 - 2924. [2 ] 鞠益兰 ,程金松 . 结构光式激光视觉传感器的焊缝跟踪系统 [J ] . 电焊机 ,2002 ,32 (5) :9 - 11. [3 ]AG APIOU G, K ASIOURAS C ,SERAFETINIDES A A. A detailed analysis of the MIG spectrum for the development of laser 2based seam tracking sensors[J ] . Optics &Laser Technology ,1999(31) :157 - 161. [4 ] 谢志孟 ,高向东 . 基于视觉传感的焊缝跟踪技术研究和展望 [J ] . 焊接 ,2005 (4) :5 - 9. [5 ] 徐 德 ,赵晓光 ,涂志国 ,等 . 基于结构光立体视觉的焊缝测量 [J ] . 焊接学报 ,2004 ,25 (5) :45 - 52. [6 ] 岳 宏 ,孙立新 ,蔡鹤皋 . 基于结构光的机器人焊接实时图像处理方法的研究 [J ] . 机器人 ,1999 ,21 (2) :144 - 147.
焊缝轨迹跟踪伺服控制系统设计与实现
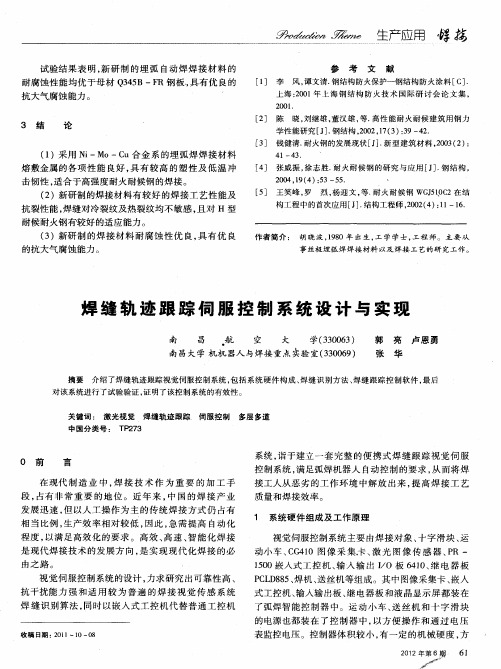
视 觉 伺 服控 制 系统 的设 计 , 力求 研 究 出 可靠 性 高 、
抗 干扰 能 力 强 和 适 用 较 为 普 遍 的 焊 接 视 觉 传 感 系 统
焊 缝 识 别算 法 , 同时 以嵌 入 式 工 控 机代 替 普 通 工 控 机
的 电源 也都 装 在 了控 制 器 中 , 以方 便 操 作 和 通 过 电 压
41 —4 3.
( )采用 N —Y 1 i o—C u合 金 系 的埋 弧 焊 焊 接 材 料
熔 敷 金属 的 各 项 性 能 良好 , 有 较 高 的 塑 性及 低 温 冲 具 击韧 性 , 合 于高 强度 耐火 耐候 钢 的焊接 。 适
[ ] 张威振 , 志胜. 4 徐 耐火 耐候 钢 的研究 与应用 [ ] 钢结 构 , J.
收 稿 日期 : 0 1—1 0 21 0— 8
表监 控 电压 。控 制器体 积 较 小 , 一定 的机 械 硬 度 , 有 方
21 0 2年第 6 期 6 1
对该系统进行 了试验验证 , 明了该控制 系统 的有效 性。 证 关键词 : 激 光视觉 焊缝轨迹跟踪
中国分类号 : T 2 3 P7
伺服控 制 多层多道
0 前
言
系统 , 于建 立 一 套 完 整 的便 携 式 焊缝 跟 踪 视 觉 伺 服 诣
控 制系 统 , 足 弧焊 机器 人 自动控 制 的要 求 , 而将 焊 满 从
接工 人从 恶 劣 的工 作 环 境 中解 放 出来 , 高 焊 接 工 艺 提 质量 和 焊接 效率 。
1 系统硬 件 组成及 工作 原 理
在 现 代 制 造 业 中 , 接 技 术 作 为 重 要 的 加 工 手 焊
基于图像传感的焊缝自动跟踪系统设计

( hreC u ldD vc )i a esno a sdi o et ni aeo e en.Weue C+ + ei esf C ag ope ei e m g sr s e cU c o g fh a1 sdV e w u n i m t s d s nt t g h o—
黄文怡 刘 立君 梁 波 殷子 强 , , ,
(. 1哈尔滨理工大学 材料科学与工程学 院 , 黑龙江 哈尔滨 104 ) 500
(. 2 大庆瑞好 能源科技有 限公 司, 黑龙江 大 庆 1 3 1 ) 6 3 1
摘
要 :本 文提 出 了一 种基 于 图像 传 感 的焊缝 自动 跟踪 系统. 系统 应 用 C D( hreC u l C C ag o pe d
而造成焊接质量下降甚至失败. 因此 , 焊接条件的这 种变 化要 求 焊 接 机 器 人 能 够 实 时检 测 出 焊缝 的偏 差, 并调整焊接路径和焊接参数 , 保证焊接质量的可 靠性. 所以对于焊缝 自动跟踪系统 的研究已经成为
ห้องสมุดไป่ตู้
中外焊接工作者研究 的重点之一 , 尤其是图像传感
器及计算机图像处理技术 的引入 , 大大促进 了焊接 系统 的智能 化 , 而其 中最 为关 键 的部 分则 是 图像处 理技术的合理应用 【3. 2 数字 图像处理技术 已愈来 - J 愈成为整个学科领域 中必不可少的手段 , 特别是由 于其高度 的灵活性和强劲 的功能 , 使计算机数字图 像的摄取处理和控制系统具有广泛优势. 研究和发
Ke r s: e m a k n y wo d s a t c i g;a o tc i e t y n r utma d n i i g;i g e sn i f ma e s n i g
焊机焊缝跟踪装置机构及控制设计

焊机焊缝跟踪装置结构及控制系统设计摘要:长直轨道焊接在工业焊接技术中的十分常见,但是焊接小车在焊接系统中是不可缺少的设备,其启动性能如何和运行速度是不是平稳直接影响到焊接质量。
本文设计的是一台应用于实际焊接场所的基于单片机控制的焊接小车,此设备主要应用于长直轨道的焊接场所中。
该焊接系统采用了单片机和外部硬件电路相结合的控制方式,当中单片机是该系统的控制核心,系统首先通过控制电路输出模拟信号,然后经模数转换器将其转换为数字信号,数字信号接到单片机相应的接口,通过编程对整个系统进行控制,电机前安排了驱动电路,作用于驱动步进电机,电机经过减速器把转矩输送到小车的轮轴上。
在焊接自动化系统中,焊接小车速度的控制直接影响着焊件的焊接质量,本系统对焊接速度的控制十分精确,十分精确地解决了这个问题。
本文提出的采用单片机控制步进电机的方案,可依据设计需要,通过控制电路的三个相应开关实现对焊接小车的转速、正反转、停止及启动等工作状态进行控制,具有实时性以及交互性的特点,从而提高了焊接生产效率。
关键词:焊接小车,单片机控制系统,步进电动机Abstract:Long straight track in the welding industry in welding technology are very common,and welding car in the welding system is essential equipment, how to start performance, speed dire ct impact on whether a smooth welding quality.This paper is designed for a welding places based on the actual control of the microcontrol ler welding car, the device used in the track's long straight welding in place. The welding system u ses a single chip and external hardware circuit combination of control, of which SCM is the core of the control system, the system first of all by controlling the circuit output analog signals, then the ADC will convert them to digital signal , The digital signal from the corresponding MCU interface, through the programming of the whole system of control, pre-arranged a motor drive circuit, used t o drive stepper motor, motor reducer, as the torque transmitted to the car's axle On.Welding Automation System, welding car speed control direct impact on the welding of the welding quality of the welding speed of the system of control is very accurate, very good soluti on to this problem. The proposed use of SCM stepper motor control programmes, as required, from the three corresponding control circuit switching to achieve the speed of the car welding, positive a nd stop and start the work, such as state control, with real-time and Interactive features, improvedwelding productivity.Key words:Welding car,SCM Control System,Stepper motor第一章绪论一、焊缝跟踪装置研究的现实意义依照国家统计局发布的《2012年国民经济和社会发展统计公报》,我国2012年粗钢产量为7.2 亿吨,按照我国焊接用钢量为30%的比率计算,焊接结构的钢材量接近2.7 亿吨。
基于CCD焊缝自动跟踪系统的设计

基于CCD焊缝自动跟踪系统的设计
郭文斌;程耀瑜;刘清文
【期刊名称】《微计算机信息》
【年(卷),期】2008(24)21
【摘要】本文所研究的是为了保证焊接的质量而进行的焊缝自动跟踪系统,采用面阵CCD视觉传感器来摄取焊接点前焊缝图像,通过采集卡把图像采集到内存,进行图像处理,获得焊缝与焊枪的偏差量,再经由上位机向PLC发送控制信号,来达到精确焊缝跟踪的目的.
【总页数】3页(P304-305,314)
【作者】郭文斌;程耀瑜;刘清文
【作者单位】030051,山西,太原,仪器科学与动态测试教育部重点实验室中北大学;030051,山西,太原,仪器科学与动态测试教育部重点实验室中北大学;030051,山西,太原,仪器科学与动态测试教育部重点实验室中北大学
【正文语种】中文
【中图分类】TP472
【相关文献】
1.基于CCD传感器的螺旋焊管焊缝自动跟踪系统 [J], 杨乐;王惠萌
2.基于模糊控制的焊缝自动跟踪系统的设计 [J], 吴冬春;李金友
3.基于图像传感的焊缝自动跟踪系统设计 [J], 黄文怡;刘立君;梁波;殷子强
4.基于线性CCD的埋弧焊焊缝自动跟踪系统设计 [J], 吴希杰
5.基于CCD图像处理的CO_2焊自动跟踪系统设计 [J], 朱六妹;宋国军;王伟;邹奇仕
因版权原因,仅展示原文概要,查看原文内容请购买。
焊缝跟踪和焊缝寻位的原理
焊缝跟踪和焊缝寻位的原理
一、焊缝跟踪原理
焊缝跟踪是焊接过程中的一项重要工作,它能够确保焊接质量和工艺
参数的一致性。
其原理是通过焊缝检测传感器或视觉传感器对焊接过
程中的焊缝进行实时监测,根据预置的规程控制焊接电流和速度实现
焊接质量的稳定性。
焊缝跟踪系统一般由控制器、传感器、信号接口等组成。
其中,传感
器可分为近红外传感器、激光传感器、摄像头传感器等,根据不同的
焊接场景选择相应的传感器。
通过掌握焊接过程中的实时参数,如焊
接速度、电流强度、电压等,可以及时调整焊接参数,确保焊接质量。
二、焊缝寻位原理
焊缝寻位是焊接前的重要工作,它可以在焊接前精确定位焊接部位,
降低焊接质量测评成本,提高焊接效率。
焊缝寻位技术可以通过机械
手臂、计算机视觉、激光测量等方式实现。
消费电子产品采用的主要焊缝寻位技术是机械手臂寻位,通过机械臂
精确控制焊枪位置,实现对焊接部位的寻位。
另外,一些大型生产厂
家也使用了激光测量的方法,在焊接前使用激光传感器对焊接部位进行测量,确定焊接位置。
三、焊缝跟踪与焊缝寻位的关系
焊缝跟踪和焊缝寻位是两个不同的概念,但它们在焊接中有着密切的关系。
首先,焊缝寻位可以为焊缝跟踪提供准确的焊接部位信息,避免焊接过程中出现偏差。
同时,焊缝跟踪技术也可以为焊缝寻位的自动化提供支持,通过对焊接过程中的数据分析,优化焊缝寻位方案,提高寻位精度和效率。
总之,焊缝跟踪和焊缝寻位是两项相互依存的技术,在焊接过程中都发挥着重要作用,提高焊接质量,降低成本。
基于激光视觉的焊缝跟踪系统方案
基于激光视觉的焊缝跟踪系统一、焊缝自动跟踪系统构成基于激光视觉传感,具有主动性、非接触、能获取物体的三维信息、灵敏度精度高、抗电磁场干扰能力强等优点,被认为是焊缝检测的主要发展方向。
线激光法是一种直接获取深度图像的方法,它可以获取焊缝的二维半信息。
基于激光视觉的焊缝跟踪系统如图1所示,主要有3个组成部分,分别是视觉传感、图像处理和跟踪控制。
CCD摄像机垂直对准工件,激光器倾斜布置,激光器打出的激光,经柱透镜形成一光片照射到工件上形成一条宽度很窄的光带。
当该光带被工件反射或折射后,经滤光片保留激光器发出的特定波长的光,而滤除其他波长的光,最后进入CCD摄像机成像。
由于坡口各处与工件在垂直方向深度不同,故从垂直工件的方向看去,反射光成一折线,折线反映了光纹中心与焊缝坡口中心的三维位置关系。
计算机对采集图像进行图像预处理,减少图像中的噪声污染,并加强焊缝特征信息信号,通过一定的算法提取焊缝特征点,得到焊缝与电弧偏差。
此偏差作为跟踪控制系统的输入条件,依据控制算法进行处理,最后获得驱动信号控制焊炬运动,实现焊缝跟踪过程实时控制。
图1 系统构成二、焊缝自动跟踪硬件设计1.激光器在本系统中决定采用半导体激光器。
半导体激光器是以半导体为工作介质,具有超小形、高效率、结构简单、价格便宜、工作速度快、波长范围宽等一系列优点。
本视觉系统中采用的激光器是红光一字线激光器,由点激光二极管发光通过一柱透镜变换成直线形的激光条纹。
有文献通过测量MIG焊弧光的光谱范围,提出弧光的范围为150~970nm。
通过比较弧光波长与普通激光二极管波长,认为弧焊传感器中所用激光二极管的中心波长最好为467nm,594nm,610nm,632nm和950nm。
从而可选择适当波长的激光感器以减少弧光对激光的干扰。
参考多篇文献,本系统选用弧光干扰最小中心波长650 nm的条形半导体激光器。
2.摄像头CCD和滤光片本系统采用面阵型CCD工业摄像头,主要考虑其性能稳定,工作可靠的特点,要求CCD 尺寸1/3",帧率25fps以上。
自动焊缝跟踪系统的设计与实现
自动焊缝跟踪系统的设计与实现摘要:本文介绍了一种基于旋转电弧传感器的焊接机器人系统。
系统采用惯量小,成本低,灵活性大的新型十字滑块系统作为机械传动机构;旋转电弧传感器的位置精度高,焊缝偏差小,使用各类焊缝类型;配合步进电机完成整个系统位移单元的传动,并进行位置伺服。
环境预检测系统完成工作环境的检测,确保系统的安全运行,DSP主控系统完成整个系统的管理和控制,并设计了包括软件保护,机械限位保护,报警保护,电源管理保护在内的各种保护措施。
为了方便系统的维护和升级,预留了标准的串口和以太网接口,可以方便对系统进行扩展升级。
关键词:焊缝跟踪;旋转电弧传感器;位置伺服;十字滑块目录1项目背景 (1)2设计要求和需求分析 (1)3系统总指标分析 (2)3.1 系统静态指标 (2)3.2系统动态指标 (2)3.3运动精度指标 (2)3.4智能性指标分析 (2)3.5可扩展性指标分析 (2)3.6应用指标 (2)3.7环境要求 (3)3.8装配指标分析 (3)4 模块设计指标和方案分析 (3)4.1总体设计方案 (3)4.2主控系统指标分析和方案比较 (4)4.3机械结构指标分析和方案比较 (4)4.4 反馈系统模块指标分析和方案比较 (6)4.5运动控制模块指标分析和方案比较 (7)4.6机械保护模块的指标分析和方案比较 (7)4.7环境检测保护模块指标分析和方案比较 (8)4.8接口扩展模块指标分析和方案比较 (8)4.9 电源管理模块指标分析和方案比较 (8)4.10 焊接指标分析与方案论证 (9)5硬件系统方案的实现 (9)5.1总控制核心系统的实现 (9)5.2机械传动结构方案的实现 (10)5.3反馈系统模块的实现 (14)5.3.1 电弧传感器的分类及选型 (14)5.3.2 旋转电弧传感器结构与工作原理 (17)5.3.3 跟踪与纠偏原理 (18)5.4运动控制模块的方案实现 (20)5.4.1步进电机的选取 (20)5.4.2步进电机驱动器的选取 (22)5.4.3直线步进电机的选取 (23)5.4.4直线步进电机驱动器的选取 (24)5.5 机械保护模块方案实现 (25)5.6环境检测系统的实现 (25)5.7接口扩展模块的方案实现 (27)5.8 电源管理模块方案的实现 (28)5.9报警模块的方案实现 (29)6软件控制平台的实现 (29)6.1传感器的控制算法和模型 (29)6.1.1 传感器与系统的初始化 (29)6.1.2 传感器的算法分析 (30)6.1.3 电弧长度模型与平面拟合算法分析 (31)6.2电机驱动的算法 (33)7 成本估计 (34)8 项目总结与改进 (34)8.1 项目总结 (34)8.2.1 旋转扫描电弧传感器的问题与改进 (35)8.2.2 系统与无线传感网络的通信 (35)8.2.3 系统的可移植性改进 (35)9 心得体会 (35)参考文献: (38)附件分工明细 (39)1项目背景焊接是一门材料连接技术,通过某种物理化学过程使分离的材料产生原子或者分子间的作用力而连接在一起,随着焊接技术的不断发展,它在生产中的应用日趋广泛,到目前为止已经成为一种重要的加工手段。
基于ARM微处理器的嵌入式焊缝智能跟踪系统的设计
ra - i eo e a i n ss e c o- ad 3- i R ir p o e sr h c a a e te a c r b ti e t f h e l tm p r t o y tm / s i n 2b tA Mm co r c s o ,w ih c nm k h r o o dn iy t e I
使机器人焊接优越性不能充分发挥 。
12嵌入式实时操作系统 [ . 6 1 嵌入式实时操作系统在 目前的嵌入式应用 中用得越来越
广泛 , 尤其在 功能复杂、 系统庞大 的应用中显得愈来愈重要 。
本系统用空心 电机旋转带动扫描焊炬, 由于焊接 电流 能 够反映特定坡 口的焊缝位置信息, 因此, 可以采用嵌入式 处 理器检测焊接 电流得到焊缝 的偏差情况, 并对焊缝 的传感 信
 ̄ i 燕 Jx i J
Li Xi y u ao an
( 赣南师范学院物理与电子信息学院,赣州
3 10 ) 400
(o l g f P y i sa dE e t o i n o m t o c e c ,G n a o m lU i e s t ,G n h u 3 1 0 ) C le e o h s c n l c r n c I fr a i n S i n e a n n N r a n v r i y a z o 4 0 0
代表性和使用最广泛的芯片,价格低廉,供货渠道好,采购 方便,使得 制造基于它 的板 子更 加容易 ,使用 JA 调试 。 TG ]
接质量也 能得到保证,因此, 弧焊机器 人被认为是焊接 自 动 化的一个重要方面 。 但是, 焊接过程 的复杂性和机器人智 能 化的缺乏 , 阻碍焊接过程 自动化的进行 。目前在 国内采用 的 大多是一种示教机器人 , 它具有很高的重复精度 , 但缺 乏适 应能力 。 示教再现式机器人在 批量焊接 时要 求有高精度 的夹 具, 工件的尺寸必须一致, 些要 求在 实际应用 中必须要 用 这 昂贵的代价才 能满足 。由于焊接条件的恶劣, 加之有些焊缝 窄, 精度要求高, 而且存在敏感的热畸变 问题, 焊道 可能会 偏离机器人原先示教 的路线,这样势必导致焊缝质量下降,
- 1、下载文档前请自行甄别文档内容的完整性,平台不提供额外的编辑、内容补充、找答案等附加服务。
- 2、"仅部分预览"的文档,不可在线预览部分如存在完整性等问题,可反馈申请退款(可完整预览的文档不适用该条件!)。
- 3、如文档侵犯您的权益,请联系客服反馈,我们会尽快为您处理(人工客服工作时间:9:00-18:30)。
焊缝自动跟踪系统的设计0804104班曲竹闽张宁一、设计内容有一块铁板上有一条裂缝,要求设计一套装置,能够自动沿缝运动,以便将裂缝焊好。
设计过程中应充分考虑焊接时产生的光和热对系统运行的影响,设计的装置能够沿缝从头到尾运动一边就认为可以把焊缝焊好。
设置的装置能适应的铁板尺寸由设计者确定,但原则上应适应任意裂缝。
系统工作前可人工辅助,但一旦工作应自动完成任务。
二、摘要本论文将设计一套可以自动跟踪焊缝的焊接系统,详细讨论焊接过程中常用的机械结构、传感器、执行机构、控制方法等问题,并详细叙述系统中各部件的选择和整套系统的工作过程和工作原理。
关键字:自动跟踪传感器执行机构控制系统三、正文(一)系统功能概述本套系统只设置了一个开关,即启动系统开关。
在焊接之前,需要人为将需要焊接的有裂缝的铁板放置在焊接平台上,并用固定装置加以固定。
之后开启启动系统开关,系统会自动初始化,并将焊接小车(焊枪和传感器等装置固定在一起形成的装置)运动到(0,0)点。
之后系统开始扫描,扫描过程中系统会驱动焊接小车扫描铁板,扫描结束后,系统会自动驱动焊接小车回到(0,0)点。
焊接小车返回零点后,系统会自动开始焊接。
焊接过程中系统会驱动小车沿焊缝运动,直至焊接小车运动到铁板边沿。
焊接技术后,系统自动回到初始化状态,等待下一次指令。
使用者可等待铁板冷却后松开夹紧装置,将铁板取下。
(二)系统设计方案在焊接系统设计的过程中,我们考虑到焊接时会产生大量的热和强光,会对系统造成十分强烈的干扰,所以在自动跟踪系统的传感器方面,我们选择了非接触式传感器,以避免由于焊接过程中产生的光和热影响传感器的正常工作。
然而,由于焊接环境不确定,使用何种焊接工艺亦不确定,所以我们根据所查资料,设计了2套自动跟踪焊缝的焊接系统,以便使用者根据不同的情况加以选择。
2套焊接系统的主体结构均相同,只是在传感器的选择方面一种使用了超声波传感器,而另一种使用了CCD光学传感器。
方案一:如图1所示,本焊接系统为双层长方体结构,长1米,宽0.5米,高1米。
下层为平面工作台,工作台上配有相应的机械夹紧装置,以保证在焊接过程中铁板的稳定性;上层为两条相互垂直的导轨机构,分别为x方向导轨和y方向导轨,用于系统的坐标定位。
焊接小车固定在y方向导轨之上,而y方向导轨可沿x方向导轨在x方向水平自由运动,这样可以实现焊枪在x-y平面任意位置的自由运动。
X方向上的导轨驱动机构为步进电机,安装于Y方向上导轨内侧,使其可以沿X方向移动,调节Y方向导轨的移动速度。
Y方向上的导轨驱动机构为无刷直流伺服电机,安装于焊接小车上,使其可以沿Y方向移动,均匀调节行走驱动的小车速度,即实现对焊接速度的调节。
将被测铁板水平放置在检测系统(即下层工作台)中,运动超声波检测(UT)技术,进行裂缝的形状,位置,大小的检测和定位的过程:图1 焊接系统结构图1、将超声波探头(2个)安装在探头架上。
采取左右两边一边一个,以用来校正和确定检测精度和确保设备的灵敏度。
2、调节该探头显示通道,在被测铁板上按水平方向调节扫描速度。
3、移动时探头到被测焊缝的距离等于缺陷回波在整个回波中的距离(此距离由该探头检测的范围精度确定,具体原理后面详细讲解)。
4、设置缺陷回波的图像显示精度,至少应包括一半焊缝宽度和热影响区5mm以上。
以正确的寻找到要进行焊接的焊缝,不会被其铁板内部细小的裂缝或其他不确定因素的干扰而造成焊接时的不稳定。
可以更好的提高设备的精度和可靠性。
同时根据有关标准规定调节设备灵敏度,并调节缺陷波闸门高度,使人工缺陷能够自动记录(移动时要保证探头至焊缝的距离与实际检测是一致)5、在被测铁板边启动电机移动探头,使探头对着铁板平行移动,移动速度应近似于焊接成型速度,找到缺陷回波,并进行记录。
6、往复移动探头,记录焊缝边缘回波的高度和边缘回波与缺陷波闸门相对位置,以便于在检测中对设备灵敏度及探头位置进行监控,进一步确保检测扫描的准确性和稳定性。
7、在正常检测时,应时刻注意使焊缝边缘回波高度达到标定时的高度,并且一旦设备灵敏度降低或探头移动造成边缘回波漂移时(即两个探头检测的数据图像出现较明显的偏差),仪器会自动报警,操作人员应当重新调整。
补充:第1,2,3,4步骤为第一次运行时设定的,以后运行都会参照第一次参数运行,如需要进行修改,则再重新按照步骤修改一遍。
8、将超声波传感器得到的裂缝信号(宽度,长度,位置)传回计算机,经过计算机处理后返回控制系统。
(具体系统后面会介绍)9、根据控制系统返回的偏差信号,控制相应的电机按照要求的转速进行运转和前行,从而控制焊接小车按照规定的路径(焊缝的位置)进行移动和焊接,并且超声波传感器不断进行扫描和控制,返回其反馈信号,不断调节焊接小车的路径,令其严格按照先前扫描的位置进行焊接,以提高焊接的准确性和可靠性。
10、当焊接小车运行到铁板边缘,即路径运行结束,则控制停止焊枪和传感器运行,并且控制焊接小车运行到坐标(0.0)位置,然后停止电机运行,提醒焊接结束(比如用灯或者响铃)。
11、系统进入待机状态,等待下一次指令。
方案二:如图1所示,焊接系统仍采用为双层长方体结构,长1米,宽0,5米,高1米。
下层为平面工作台,工作台上配有相应的机械夹紧装置,以保证在焊接过程中铁板的稳定性;上层为两条相互垂直的导轨机构,分别为x方向导轨和y方向导轨,用于系统的坐标定位。
焊接小车固定在y方向磁吸柔性轨道之上,而y方向导轨可沿x方向导轨在x方向水平自由运动,这样可以实现焊枪在x-y平面任意位置的自由运动。
X方向上的导轨驱动机构为步进电机,安装于Y方向上导轨内侧,使其可以沿X方向移动,调节Y方向导轨的移动速度。
Y方向上的导轨驱动机构为无刷直流伺服电机,安装于焊接小车上,使其可以沿Y方向移动,均匀调节行走驱动的小车速度,即实现对焊接速度的调节。
在焊接小车的同一平面内,固定CCD摄像机,用以在前期对焊缝的扫描定位和焊接过程中对焊道的扫描纠正,以提高焊接过程的准确性和可靠性。
调节CCD摄像机显示通道,并且调节扫描速度。
设置显示图像的精度,以确保能正确的寻找到要进行焊接的焊缝,而不会出现漏检和错检,而造成焊接时的不稳定。
可以更好的提高设备的精度和可靠性。
本套系统的工作过程如下:1、将有裂痕的铁板固定在工作台上,铁板一边应与x方向平行且顶点落在工作台的(0,0)点,这样可以确保扫描时是从铁板的边缘开始扫描的。
2、启动焊接系统开关,焊接系统开始运作,计算机会根据预定程序输出信号驱动电机,将自动将焊枪定位在工作台的(0,0)点。
3、开始扫描裂缝,计算机根据相关程序给出信号,驱动电机运动,并同时驱动CCD传感器开始扫描,确定裂缝上特征点坐标的方法为:固定焊枪在y方向的位移为零,使焊枪在x方向预先以设定好的速度沿x方向运动。
与此同时,固定在焊枪上的CCD摄像机开始扫描,并将铁板的图像信息传递给计算机。
4、扫描结束后,计算机记录扫描数据,并输出信号驱动焊枪自动回到(0,0)点等待焊接。
5、开始焊接裂缝,计算机将接收到信号按照预先制定的程序进行信息的处理,得到铁板裂缝出的一些特征点的坐标,并将这些信息输出给电机,使焊枪按照计算机得出的特征点运动,即开始焊接。
6、在焊接过程中,CCD摄像机仍在不停地扫描焊枪与裂缝之间的距离,并将这一距离作为系统的偏差信号输出给控制系统,以纠正系统的误差,保证焊枪与裂缝之间距离小于焊接要求的最大距离。
7、当焊枪运动到铁板边沿使,焊接结束,计算机根据程序设定,输出信号驱动焊枪自动回到(0,0)点,等待下次焊接。
根据系统的设计方案,可以绘制出系统工作的流程图。
图2本系统的主要采用计算机来输出控制信号驱动系统的执行装置运动,所以作者选择通过VC++编程来实现。
鉴于本次论文重在焊接系统的设计,所以具体程序不予给出,只给出CV++程序应该完成的任务的流程图,如使用者有需要,可以根据流程图找编程人员设计程序。
程序流程图见图3。
图3 VC++程序流程图为了获得高质量的焊缝,设计了采用脉宽调制(PWM)技术的伺服控制系统。
通过与快速响应的小型直流伺服电机相配合,能获得较宽的频带,既有利于提高系统的控制性能,实现快速动作和高精度随动,又能做到焊接小车在高、低速运行时电流脉动量都很小。
伺服控制系统的结构框架如图4所示:图4 伺服控制系统的结构框架上图中伺服控制系统共由10部分组成,核心部分为PWM电路及PI调节器。
PWM电路采用桥式结构和电压驱动方式。
PI调节器用于校正环节,使系统整定为二阶系统,即保证系统具有较强的抗干扰能力,又做到超调量小。
伺服控制系统以光电脉冲发生器作为速度检测元件,以速度检测电路获得的与速度相应的脉冲信号作速度反馈量,通过反馈环节实现控制系统的闭环控制。
(三)工作原理一个典型的焊接自动化系统主要由机械装置、传感器、执行装置和控制系统组成。
系统的各个部分需要有机的结合才能准确高效地实现具体功能,就像一个人一样:控制器好比人类的大脑,传感器就像人类的五官和皮肤,执行装置就好像人类的骨骼,而执行装置则相当于人类的手和足。
(1)机械装置:焊接裂缝的铁板,首先应将其固定,固定则需要一些机械夹紧装置,即夹紧器。
常用的夹紧器有磁力夹紧器、液压夹紧器、气压夹紧器和机械夹紧器。
由于本系统仅仅为了完成单一焊接铁板裂缝的功能,综合考虑经济因素,并且因为系统装置对夹紧器性能要求不高,故选择最简单廉价的机械加紧装置。
另外还需要一些钢架结构和铁板结构作为机身的主体结构。
(2)传感器:铁板固定好后,首先应该对铁板进行扫描,以确定焊缝上的点的坐标。
之后再控制焊枪沿扫描出的坐标移动,同时对焊缝进行跟踪以确保焊枪与焊缝之间的距离小于焊接要求的最小距离,以保证焊接的质量和精度。
所以焊接的自动检测就是其中的自动化过程的一个重要环节。
它能使用各种自动检测仪器,自动,灵敏的检测出焊接中的缺陷和不足,并与数据处理系统结合在一起,能迅速稳定地自动读取、存储、判断、分析和处理检测信息的一种专门技术。
而焊接的自动检测所需求的仪器就是各种的传感器,所以首先了解一下焊接过程经常使用的传感器的种类,基本原理和应用特点,以便在系统的构建过程中选择合适的传感器。
上表罗列了在焊接过程中常用的传感器的种类、基本原理和应用特点,总结归纳如下:焊缝跟踪过程中使用的传感器可分为直接电弧式、接触式和非接触式3大类。
接触式传感器一般在焊枪前方采用导杆或导轮和焊缝或工件的一个侧壁接触,通过导杆或导轮把焊缝位置的变化通过光电、滑动变阻器、力觉等方式转换为电信号,以供控制系统跟踪焊缝。
其特点为不受电弧干扰,工作可靠,成本低,曾在生产中得到过广泛应用,但跟踪精度不高,目前正在被其他传感方法取代。
电弧式传感器利用焊接电极与被焊工件之间的距离变化能够引起电弧电流(对于GMAW方法)或电弧电压(对于GTAW方法)变化这一物理现象来检测接头的坡口中心。