齿轮工艺流程
齿轮加工工艺流程
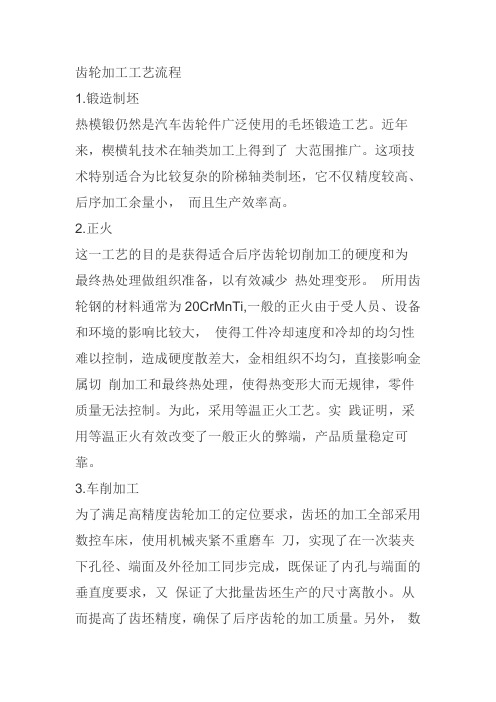
齿轮加工工艺流程1.锻造制坯热模锻仍然是汽车齿轮件广泛使用的毛坯锻造工艺。
近年来,楔横轧技术在轴类加工上得到了大范围推广。
这项技术特别适合为比较复杂的阶梯轴类制坯,它不仅精度较高、后序加工余量小,而且生产效率高。
2.正火这一工艺的目的是获得适合后序齿轮切削加工的硬度和为最终热处理做组织准备,以有效减少热处理变形。
所用齿轮钢的材料通常为20CrMnTi,一般的正火由于受人员、设备和环境的影响比较大,使得工件冷却速度和冷却的均匀性难以控制,造成硬度散差大,金相组织不均匀,直接影响金属切削加工和最终热处理,使得热变形大而无规律,零件质量无法控制。
为此,采用等温正火工艺。
实践证明,采用等温正火有效改变了一般正火的弊端,产品质量稳定可靠。
3.车削加工为了满足高精度齿轮加工的定位要求,齿坯的加工全部采用数控车床,使用机械夹紧不重磨车刀,实现了在一次装夹下孔径、端面及外径加工同步完成,既保证了内孔与端面的垂直度要求,又保证了大批量齿坯生产的尺寸离散小。
从而提高了齿坯精度,确保了后序齿轮的加工质量。
另外,数控车床加工的高效率还大大减少了设备数量,经济性好。
4.滚、插齿加工齿部所用设备仍大量采用普通滚齿机和插齿机,虽然调整维护方便,但生产效率较低,若完成较大产能需要多机同时生产。
随着涂层技术的发展,滚刀、插刀刃磨后的再次涂镀非常方便地进行,经过涂镀的刀具能够明显地提高使用寿命,一般能提高90%以上,有效地减少了换刀次数和刃磨时间,效益显着。
5.剃齿径向剃齿技术以其效率高,设计齿形、齿向的修形要求易于实现等优势被广泛应用于大批量汽车齿轮生产中。
6.热处理汽车齿轮要求渗碳淬火,以保证其良好的力学性能。
对于热后不再进行磨齿加工的产品,稳定可靠的热处理设备是必不可少的。
7.磨削加工主要是对经过热处理的齿轮内孔、端面、轴的外径等部分进行精加工,以提高尺寸精度和减小形位公差。
齿轮范成法加工工艺流程
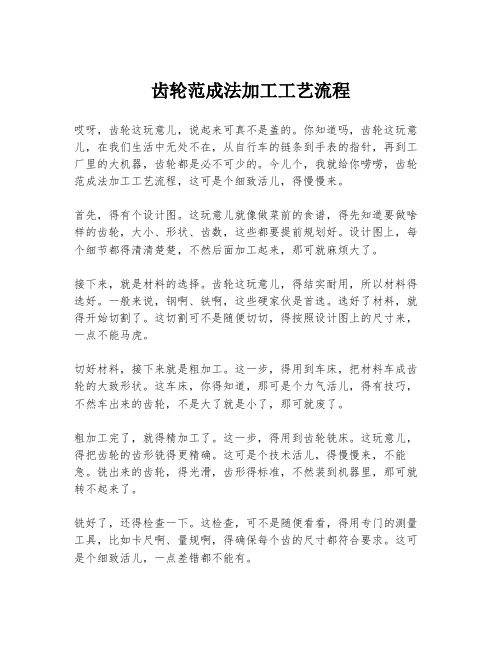
齿轮范成法加工工艺流程哎呀,齿轮这玩意儿,说起来可真不是盖的。
你知道吗,齿轮这玩意儿,在我们生活中无处不在,从自行车的链条到手表的指针,再到工厂里的大机器,齿轮都是必不可少的。
今儿个,我就给你唠唠,齿轮范成法加工工艺流程,这可是个细致活儿,得慢慢来。
首先,得有个设计图。
这玩意儿就像做菜前的食谱,得先知道要做啥样的齿轮,大小、形状、齿数,这些都要提前规划好。
设计图上,每个细节都得清清楚楚,不然后面加工起来,那可就麻烦大了。
接下来,就是材料的选择。
齿轮这玩意儿,得结实耐用,所以材料得选好。
一般来说,钢啊、铁啊,这些硬家伙是首选。
选好了材料,就得开始切割了。
这切割可不是随便切切,得按照设计图上的尺寸来,一点不能马虎。
切好材料,接下来就是粗加工。
这一步,得用到车床,把材料车成齿轮的大致形状。
这车床,你得知道,那可是个力气活儿,得有技巧,不然车出来的齿轮,不是大了就是小了,那可就废了。
粗加工完了,就得精加工了。
这一步,得用到齿轮铣床。
这玩意儿,得把齿轮的齿形铣得更精确。
这可是个技术活儿,得慢慢来,不能急。
铣出来的齿轮,得光滑,齿形得标准,不然装到机器里,那可就转不起来了。
铣好了,还得检查一下。
这检查,可不是随便看看,得用专门的测量工具,比如卡尺啊、量规啊,得确保每个齿的尺寸都符合要求。
这可是个细致活儿,一点差错都不能有。
最后,就是热处理和表面处理了。
这热处理,就是让齿轮变得更硬,更耐磨。
表面处理,就是让齿轮看起来更光滑,减少摩擦。
这俩步骤,虽然看起来不起眼,但对齿轮的使用寿命,那可是至关重要的。
好了,这就是齿轮范成法加工工艺流程。
说起来,这玩意儿虽然复杂,但每一步都马虎不得。
就像咱们做人一样,得脚踏实地,一步一个脚印。
齿轮虽小,但每个细节都关系到机器的正常运转,马虎不得。
所以啊,别看这小小的齿轮,它可是大有学问的。
咱们今天就聊到这儿,下次再给你唠点别的。
齿轮热处理工艺流程

齿轮热处理工艺流程
齿轮热处理是齿轮制造中非常重要的一环,它可以提高齿轮的机械性能和使用寿命。
该工艺流程主要包括以下几个步骤:
1. 去毛刺处理:将加工后的齿轮进行去毛刺处理,以保证后续的工艺流程正常进行。
2. 预热处理:将齿轮置于炉中进行预热处理,使其均匀受热,并去除内部应力。
3. 热处理:将齿轮置于炉中进行热处理,使其达到所需的硬度和强度。
4. 冷却处理:将热处理后的齿轮进行快速冷却,以提高其硬度。
5. 回火处理:将冷却后的齿轮进行回火处理,以减小硬度和强度,使其具有良好的韧性和可加工性。
6. 冷却处理:将回火后的齿轮进行缓慢冷却,以达到最终的机械性能要求。
以上便是齿轮热处理的工艺流程,其中每个步骤的参数和工艺条件都需要根据具体情况进行调整,以达到最佳的效果。
- 1 -。
齿轮生产工艺流程

齿轮生产工艺流程展成法是应用齿轮啮合的原理来进行加工的,用这种方法加工出来的齿形轮廓是刀具切削刃运动轨迹的包络线。
齿数不同的齿轮,只要模数和齿形角相同,都可以用同一把刀具来加工。
用展成原理加工齿形的方法有:滚齿、插齿、剃齿、珩齿和磨齿等方法。
其中剃齿、珩齿和磨齿属于齿形的精加工方法。
展成法的加工精度和生产率都较高,刀具通用性好,所以在生产中应用十分广泛。
一、滚齿(一)滚齿的原理及工艺特点滚齿是齿形加工方法中生产率较高、应用最广的一种加工方法。
在滚齿机上用齿轮滚刀加工齿轮的原理,相当于一对螺旋齿轮作无侧隙强制性的啮合,见图9-24所示。
滚齿加工的通用性较好,既可加工圆柱齿轮,又能加工蜗轮;既可加工渐开线齿形,又可加工圆弧、摆线等齿形;既可加工大模数齿轮,大直径齿轮。
滚齿可直接加工8~9级精度齿轮,也可用作7 级以上齿轮的粗加工及半精加工。
滚齿可以获得较高的运动精度,但因滚齿时齿面是由滚刀的刀齿包络而成,参加切削的刀齿数有限,因而齿面的表面粗糙度较粗。
为了提高滚齿的加工精度和齿面质量,宜将粗精滚齿分开。
(二)滚齿加工质量分析1.影响传动精度的加工误差分析影响齿轮传动精度的主要原因是在加工中滚刀和被切齿轮的相对位置和相对运动发生了变化。
相对位置的变化(几何偏心)产生齿轮的径向误差;相对运动的变化(运动偏心)产生齿轮的切向误差。
(1)齿轮的径向误差齿轮径向误差是指滚齿时,由于齿坯的实际回转中心与其基准孔中心不重合,使所切齿轮的轮齿发生径向位移而引起的周节累积公差,如图9—4所示。
齿轮的径向误差一般可通过测量齿圈径向跳动△Fr反映出来。
切齿时产生齿轮径向误差的主要原因如下:①调整夹具时,心轴和机床工作台回转中心不重合。
②齿坯基准孔与心轴间有间隙,装夹时偏向一边。
③基准端面定位不好,夹紧后内孔相对工作台回转中心产生偏心。
(2)齿轮的切向误差齿轮的切向误差是指滚齿时,实际齿廓相对理论位置沿圆周方向(切向)发生位移,如图9-5所示。
齿轮热压工艺流程

齿轮热压工艺流程
《齿轮热压工艺流程》
齿轮是机械传动中常用的零部件,其性能直接影响到整个机械设备的运行效率和稳定性。
齿轮的制造工艺中,热压是一种常用的加工方法,通过热压可以提高齿轮的密实度和耐磨性,提高其使用寿命和性能。
齿轮热压工艺流程主要包括以下几个步骤:
1. 材料准备:首先需要准备好齿轮制造所需要的材料,通常使用的材料包括碳素钢、合金钢等。
材料的选择需要根据具体的齿轮使用要求和工作环境来确定。
2. 齿轮加工:在材料准备好之后,需要进行齿轮的精密加工。
这一步是齿轮热压工艺流程中至关重要的一步,精密加工可以保证齿轮的尺寸精准和表面质量良好。
3. 加热处理:将预先制作好的齿轮放入专用的热处理炉中进行加热处理。
这一步是整个热压工艺中最关键的一步,通过加热可以使材料可塑性增强,为后续的热压做好准备。
4. 热压成型:经过加热处理后的齿轮放入热压机中进行成型。
通过高温和高压的作用,齿轮材料在模具的作用下逐渐形成所需要的形状和结构。
这一步的关键是控制好加热温度和压力,以确保齿轮的形状和性能达到要求。
5. 冷却处理:热压完成后的齿轮需要进行冷却处理,以使其稳定结构。
6. 表面处理:最后一步是对齿轮的表面进行处理,常见的表面处理方法包括镀锌、喷漆等,以提高齿轮的耐腐蚀性和美观度。
通过以上工艺流程,可以制造出性能优良、质量稳定的齿轮,来满足不同工业领域的需要。
齿轮热压工艺流程的成熟应用,为整个机械制造行业提供了强有力的支撑。
铜齿轮的制造工艺
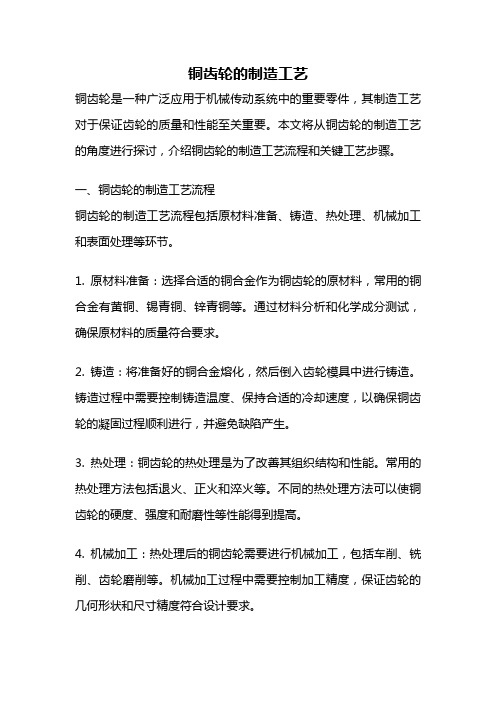
铜齿轮的制造工艺铜齿轮是一种广泛应用于机械传动系统中的重要零件,其制造工艺对于保证齿轮的质量和性能至关重要。
本文将从铜齿轮的制造工艺的角度进行探讨,介绍铜齿轮的制造工艺流程和关键工艺步骤。
一、铜齿轮的制造工艺流程铜齿轮的制造工艺流程包括原材料准备、铸造、热处理、机械加工和表面处理等环节。
1. 原材料准备:选择合适的铜合金作为铜齿轮的原材料,常用的铜合金有黄铜、锡青铜、锌青铜等。
通过材料分析和化学成分测试,确保原材料的质量符合要求。
2. 铸造:将准备好的铜合金熔化,然后倒入齿轮模具中进行铸造。
铸造过程中需要控制铸造温度、保持合适的冷却速度,以确保铜齿轮的凝固过程顺利进行,并避免缺陷产生。
3. 热处理:铜齿轮的热处理是为了改善其组织结构和性能。
常用的热处理方法包括退火、正火和淬火等。
不同的热处理方法可以使铜齿轮的硬度、强度和耐磨性等性能得到提高。
4. 机械加工:热处理后的铜齿轮需要进行机械加工,包括车削、铣削、齿轮磨削等。
机械加工过程中需要控制加工精度,保证齿轮的几何形状和尺寸精度符合设计要求。
5. 表面处理:为了提高铜齿轮的表面质量和耐腐蚀性,常常需要进行表面处理。
常见的表面处理方法有镀镍、镀铬和热处理等。
表面处理可以提高铜齿轮的表面硬度、耐磨性和抗腐蚀性。
二、铜齿轮制造工艺的关键步骤铜齿轮的制造工艺中,有几个关键的步骤需要特别注意,包括铸造过程中的温度控制、热处理过程中的时间控制、机械加工过程中的加工精度控制和表面处理过程中的工艺选择。
1. 铸造温度控制:铸造温度是影响铜齿轮凝固过程和组织结构形成的重要因素。
过高的温度会导致铜齿轮的晶粒粗化,影响其力学性能;过低的温度则会导致铜齿轮凝固不完全,产生缺陷。
因此,在铸造过程中需要控制合适的铸造温度。
2. 热处理时间控制:热处理时间是影响铜齿轮组织结构改变和性能提高的重要因素。
不同的热处理方法和工艺参数对应着不同的热处理时间。
在热处理过程中,需要控制合适的时间,确保铜齿轮能够达到预期的组织结构和性能要求。
汽车齿轮加工工艺流程
汽车齿轮加工工艺流程
1.材料准备:首先需要选择合适的材料,通常为优质合金钢或碳素钢。
然后对材料进行热处理,提高其机械性能和耐磨性。
2. 切削加工:将材料进行粗加工,包括车削、刨削、钻孔等。
通过这一步骤,使材料形成初步的形状和精度要求。
3. 齿形加工:将切削好的零件送入齿轮加工机床中,进行齿形加工。
这一步骤可以采用铣削、滚齿、剃齿等方式,制造出符合要求的齿形。
4. 精加工:将齿形加工好的零件进行精加工。
这一步骤通常使用磨削或滚压工艺,以确定齿轮的精度和表面质量。
5. 热处理:对齿轮进行热处理,提高其硬度和强度。
常用的热处理方法包括淬火、回火等。
6. 清洗和检验:清洗齿轮表面,将切削剂和其它杂质清除干净后,进行检验。
检验内容包括齿轮精度、硬度、表面质量等。
7. 组装:将检验合格的齿轮零件进行组装,形成完整的齿轮传动系统。
该步骤通常需要在无尘室进行,以保证齿轮传动的可靠性和稳定性。
以上就是汽车齿轮加工工艺流程的具体步骤。
不同的齿轮加工要求可能存在差异,但总体流程基本相同。
- 1 -。
汽车齿轮加工工艺流程
汽车齿轮加工工艺流程1.齿轮加工前的准备工作:a.选择合适的齿轮材料,通常使用的材料有钢、铸铁、铝合金等;b.根据设计要求,确定齿轮的型式、模数、齿数等参数;c.定义齿轮加工的工艺路线和技术要求。
2.齿轮加工的工艺路线:a.下料:将齿轮原料按照长度进行切割,得到初始长度的齿轮坯料;b.粗车:采用车床等机床对齿轮坯料进行车削,使之达到粗加工要求;c.热处理:对齿轮进行热处理,提高其硬度和强度,常用的热处理方法有淬火、渗碳等;d.精车:在车削之后,对齿轮进行精加工,提高其精度和表面质量;e.整齐齿:将精车之后的齿轮进行整齐齿加工,具体加工方式有滚齿、插齿等;f.其他加工:根据齿轮型式的不同,还可以进行加工外齿、钻孔、切割窜齿等;g.检验:对齿轮进行尺寸、形状、硬度等方面的检测,以确保其质量达到要求;h.表面处理:对齿轮进行表面处理,如镀铬、电镀等,提高其防腐性和美观性。
3.齿轮加工的机械设备:a.车削机床:主要用于齿轮的粗车和精车加工;b.滚齿机:用于整齐齿加工;c.齿形磨床:用于齿轮的磨加工,提高其精度和表面质量;d.热处理设备:用于齿轮的热处理,如炉子、盐浴炉等;e.检测设备:如三坐标测量机、硬度计等,用于对齿轮进行质量检测。
4.齿轮加工的关键技术:a.工艺参数的确定:包括车削速度、进给量等参数的选择;b.热处理工艺的控制:控制热处理温度、保温时间等,确保齿轮的硬度和强度达到要求;c.自动化加工技术:如数控车床、自动化滚齿等,提高加工效率和产品质量;d.表面处理技术:如电镀、热浸镀等,提高齿轮的表面质量和防腐性。
总结:。
齿轮配件工艺流程
齿轮配件工艺流程
《齿轮配件工艺流程》
齿轮配件是机械设备中常见的零部件,其工艺流程至关重要。
在齿轮配件的生产过程中,需要经历多道工艺流程才能最终完成,包括锻造、车削、磨削等环节。
首先是锻造工艺。
在生产齿轮配件时,常常需要通过锻造来获得所需的形状和尺寸。
在锻造工艺中,需要选用合适的原材料,并经过加热后用锤子或压力机进行塑性变形,最终获得所需的形状。
接下来是车削工艺。
在车削工艺中,需要将锻造后的工件进行精细加工,以保证齿轮的尺寸精准度和表面光洁度。
通过在车床上旋转工件并利用刀具进行切削,可以获得所需的尺寸和形状。
最后是磨削工艺。
在磨削工艺中,需要使用磨削机来对齿轮进行最后的加工,以获得更精细的表面光洁度和更高的精度。
通过磨削,可以进一步提高齿轮的质量和使用寿命。
除了以上三道主要工艺流程之外,齿轮配件的生产过程中还可能包括其他工艺环节,如热处理、表面处理等,以确保齿轮的性能和质量。
总的来说,齿轮配件的生产工艺流程十分复杂,需要各个环节精益求精,以确保最终产品的质量和性能。
只有严谨的工艺流
程和精湛的工艺技术,才能生产出优质的齿轮配件,为机械设备的正常运转提供可靠保障。
齿轮热处理工艺流程
齿轮热处理工艺流程
齿轮热处理工艺流程是指对齿轮进行加热、保温、冷却等一系列工艺处理,以改善其物理性能和机械性能的过程。
一般来说,齿轮热处理工艺流程包括以下步骤:
1. 预处理:齿轮在进入热处理前需要进行清洗、拆卸和去毛刺等预处理工作,以便于更好地进入加热工艺。
2. 加热:将齿轮放入加热设备中进行加热处理,通常采用气体或者电加热方式。
加热温度和时间根据齿轮的材料和大小来确定。
3. 保温:在齿轮达到所需的加热温度后,需要进行一段时间的保温处理,使其温度均匀分布,达到最佳的组织结构。
4. 冷却:对于齿轮的不同部位,需要采用不同的冷却方式,一般包括水淬、油淬、风淬等方法。
冷却速度的快慢也会影响齿轮的物理性能和机械性能。
5. 温度控制和回火:完成冷却后,需要对齿轮进行温度控制和回火,以进一步调整其组织结构和性能。
6. 后处理:对于经过热处理的齿轮,需要进行磨削、抛光和检测等后处理工作,以确保其质量和精度。
总之,齿轮热处理工艺流程是一个相对复杂的过程,需要根据齿轮的具体情况进行不同的处理方式和参数控制,以达到最佳的效果。
- 1 -。
- 1、下载文档前请自行甄别文档内容的完整性,平台不提供额外的编辑、内容补充、找答案等附加服务。
- 2、"仅部分预览"的文档,不可在线预览部分如存在完整性等问题,可反馈申请退款(可完整预览的文档不适用该条件!)。
- 3、如文档侵犯您的权益,请联系客服反馈,我们会尽快为您处理(人工客服工作时间:9:00-18:30)。
矿产资源开发利用方案编写内容要求及审查大纲
矿产资源开发利用方案编写内容要求及《矿产资源开发利用方案》审查大纲一、概述
㈠矿区位置、隶属关系和企业性质。
如为改扩建矿山, 应说明矿山现状、
特点及存在的主要问题。
㈡编制依据
(1简述项目前期工作进展情况及与有关方面对项目的意向性协议情况。
(2 列出开发利用方案编制所依据的主要基础性资料的名称。
如经储量管理部门认定的矿区地质勘探报告、选矿试验报告、加工利用试验报告、工程地质初评资料、矿区水文资料和供水资料等。
对改、扩建矿山应有生产实际资料, 如矿山总平面现状图、矿床开拓系统图、采场现状图和主要采选设备清单等。
二、矿产品需求现状和预测
㈠该矿产在国内需求情况和市场供应情况
1、矿产品现状及加工利用趋向。
2、国内近、远期的需求量及主要销向预测。
㈡产品价格分析
1、国内矿产品价格现状。
2、矿产品价格稳定性及变化趋势。
三、矿产资源概况
㈠矿区总体概况
1、矿区总体规划情况。
2、矿区矿产资源概况。
3、该设计与矿区总体开发的关系。
㈡该设计项目的资源概况
1、矿床地质及构造特征。
2、矿床开采技术条件及水文地质条件。