直接还原技术
达涅利ENERGIRON直接还原技术

世界金属导报/2010年/6月/22日/第014版设备制造达涅利ENERGIRON直接还原技术1简介本文根据CO2排放量分析,比较三种炼钢工艺对环境的影响:・传统联合炼钢厂,高炉-氧气顶吹转炉(BF-BOF)。
・现代联合炼钢厂,直接还原工艺(基于天然气)-电弧炉(DRP-EAF)。
・现代联合炼钢厂,直接还原工艺(基于可气化煤)-电弧炉(DRP-EAF)。
达涅利和HYL开发的ENERGIRON气基直接还原技术是先进的铁矿石冶炼工艺,此项技术的目标是:・通过减少温室气体排放降低对环境的影响。
・根据主要能量来源,利用各种工业气体,如天然气或煤气化产生的合成煤气或焦炉煤气。
炼钢产业的特征就是大量使用化石燃料,而化石燃料排放导致全球变暖的温室气体(GHG),给环境造成极大的影响,这些气体主要是CO2。
CO2的排放量和特点由炼钢厂使用主要燃料的特性所决定。
在传统联合炼钢高炉工艺中,用来还原氧化铁的主要能源是煤。
在现代联合炼钢DRP直接还原工艺中,用来还原氧化铁的主要能源可以是天然气或煤或任何工业气体。
2联合炼钢厂的CO2排放2.1传统联合炼钢厂的CO2排放图1显示的是传统联合炼钢厂典型的能量平衡。
这个工厂设备包括:炼焦炉设备、烧结车间、生产铁水(HM)高炉、氧气顶吹转炉(BOF)、钢包炉/真空脱气设备、生产热轧带卷(HRC)的薄板坯连铸机和带钢热轧机。
能从传统联合炼钢厂中回收的主要气态燃料副产品包括:烧结车间气体(sPG)、炼焦炉设备气体(COG)、鼓风炉气体(BFG)和氧气顶吹转炉气体(BOFG)。
传统联合炼钢厂的能量平衡显示大多数气态燃料主要用于产生能量或燃烧发热。
传统联合钢厂烟道气排放CO2每吨钢水约为2.104t。
2.2现代联合炼钢厂的CO2排放图2显示的是现代联合炼钢厂典型的能量平衡,这些ENERGIRON直接还原炼钢厂的主要燃料是天然气。
这个工厂包括:球团车间、生产直接还原铁(DRI)的ENERGIRON直接还原炼钢车间(DRP)、电弧炉(EAF)、钢包炉/真空脱气设备、生产热轧带卷(HRC)的薄板坯连铸机和带钢热轧机。
直接还原铁生产工艺
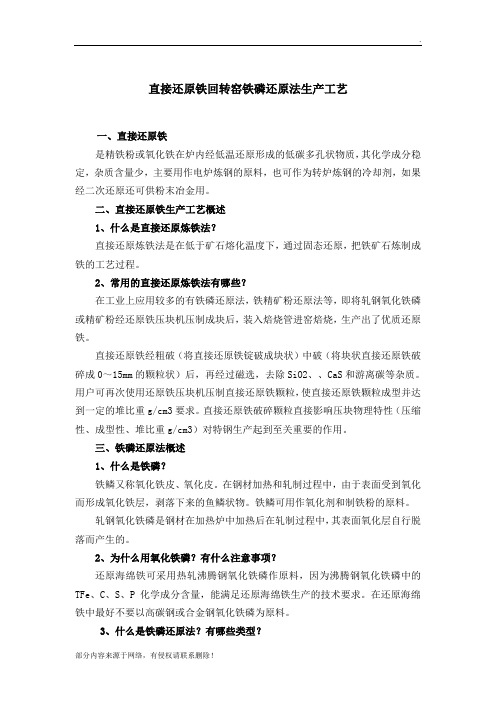
直接还原铁回转窑铁磷还原法生产工艺一、直接还原铁是精铁粉或氧化铁在炉内经低温还原形成的低碳多孔状物质,其化学成分稳定,杂质含量少,主要用作电炉炼钢的原料,也可作为转炉炼钢的冷却剂,如果经二次还原还可供粉末冶金用。
二、直接还原铁生产工艺概述1、什么是直接还原炼铁法?直接还原炼铁法是在低于矿石熔化温度下,通过固态还原,把铁矿石炼制成铁的工艺过程。
2、常用的直接还原炼铁法有哪些?在工业上应用较多的有铁磷还原法,铁精矿粉还原法等,即将轧钢氧化铁磷或精矿粉经还原铁压块机压制成块后,装入焙烧管进窑焙烧,生产出了优质还原铁。
直接还原铁经粗破(将直接还原铁锭破成块状)中破(将块状直接还原铁破碎成0~15mm的颗粒状)后,再经过磁选,去除SiO2、、CaS和游离碳等杂质。
用户可再次使用还原铁压块机压制直接还原铁颗粒,使直接还原铁颗粒成型并达到一定的堆比重g/cm3要求。
直接还原铁破碎颗粒直接影响压块物理特性(压缩性、成型性、堆比重g/cm3)对特钢生产起到至关重要的作用。
三、铁磷还原法概述1、什么是铁磷?铁鳞又称氧化铁皮、氧化皮。
在钢材加热和轧制过程中,由于表面受到氧化而形成氧化铁层,剥落下来的鱼鳞状物。
铁鳞可用作氧化剂和制铁粉的原料。
轧钢氧化铁磷是钢材在加热炉中加热后在轧制过程中,其表面氧化层自行脱落而产生的。
2、为什么用氧化铁磷?有什么注意事项?还原海绵铁可采用热轧沸腾钢氧化铁磷作原料,因为沸腾钢氧化铁磷中的TFe、C、S、P化学成分含量,能满足还原海绵铁生产的技术要求。
在还原海绵铁中最好不要以高碳钢或合金钢氧化铁磷为原料。
3、什么是铁磷还原法?有哪些类型?铁鳞还原法就是以铁鳞为原料的直接还原法生产工艺。
铁鳞还原法生产过程可分为粗还原与精还原。
在粗还原过程中,铁氧化物被还原,铁粉颗粒烧结与渗碳。
增高还原温度或延长保温时间皆有利于铁氧化物还原、铁粉颗粒烧结,但会生产部分渗碳。
鉴于在精还原过程中脱碳困难,在粗还原过程中,控制铁氧化物还原到未渗碳的程度是必要的。
直接还原技术现状及其在中国的进展展望
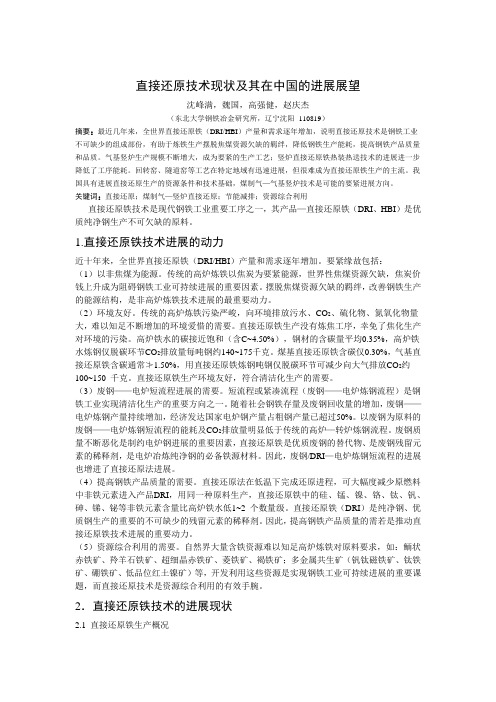
直接还原技术现状及其在中国的进展展望沈峰满,魏国,高强健,赵庆杰(东北大学钢铁冶金研究所,辽宁沈阳110819)摘要:最近几年来,全世界直接还原铁(DRI/HBI)产量和需求逐年增加,说明直接还原技术是钢铁工业不可缺少的组成部份,有助于炼铁生产摆脱焦煤资源欠缺的羁绊,降低钢铁生产能耗,提高钢铁产品质量和品质。
气基竖炉生产规模不断增大,成为要紧的生产工艺;竖炉直接还原铁热装热送技术的进展进一步降低了工序能耗。
回转窑、隧道窑等工艺在特定地域有迅速进展,但很难成为直接还原铁生产的主流。
我国具有进展直接还原生产的资源条件和技术基础,煤制气—气基竖炉技术是可能的要紧进展方向。
关键词:直接还原;煤制气—竖炉直接还原;节能减排;资源综合利用直接还原铁技术是现代钢铁工业重要工序之一,其产品—直接还原铁(DRI、HBI)是优质纯净钢生产不可欠缺的原料。
1.直接还原铁技术进展的动力近十年来,全世界直接还原铁(DRI/HBI)产量和需求逐年增加。
要紧缘故包括:(1)以非焦煤为能源。
传统的高炉炼铁以焦炭为要紧能源,世界性焦煤资源欠缺,焦炭价钱上升成为阻碍钢铁工业可持续进展的重要因素。
摆脱焦煤资源欠缺的羁绊,改善钢铁生产的能源结构,是非高炉炼铁技术进展的最重要动力。
(2)环境友好。
传统的高炉炼铁污染严峻,向环境排放污水、CO2、硫化物、氮氧化物量大,难以知足不断增加的环境爱惜的需要。
直接还原铁生产没有炼焦工序,幸免了焦化生产对环境的污染。
高炉铁水的碳接近饱和(含C~4.50%),钢材的含碳量平均0.35%,高炉铁水炼钢仅脱碳环节CO2排放量每吨钢约140~175千克。
煤基直接还原铁含碳仅0.30%,气基直接还原铁含碳通常≯1.50%,用直接还原铁炼钢吨钢仅脱碳环节可减少向大气排放CO2约100~150 千克。
直接还原铁生产环境友好,符合清洁化生产的需要。
(3)废钢——电炉短流程进展的需要。
短流程或紧凑流程(废钢——电炉炼钢流程)是钢铁工业实现清洁化生产的重要方向之一。
非高炉炼铁-直接还原

5
直接还原技术概况
直接还原炼铁工艺分为气基和煤基直接还原两大类,其 产品是固态海绵铁,主要供电炉炼钢用。
气基直接还原是用天然气经裂化产出的H2和CO作为还 原剂在竖炉、固定床罐式炉或流化床内将铁矿石中的氧化 铁还原成海绵铁。主要有Midrex法和HYL法。
煤基直接还原是用煤作还原剂在回转窑或转底炉内将矿 石中的氧化铁还原。
生产块矿矿山 Aguas Claras
Alegria Bailadila Bellary Hospet Brumadinho
Caue Cerro Bolivar
Conceica Corumba CVRD
El Pao Esperanza
Ferteco Feijao
表10 Midrex工厂曾使用的商品块矿石
15
MIDREX工艺过程
16
MIDREX流程图
17
18
2 Midrex直接还原工艺的原燃料
2.1 Midrex用燃料与还原剂
Midrex属于气基直接还原流程,还原气使用天然气经催化 裂化制取,裂化剂采用炉顶煤气。炉顶煤气含CO与H2约70%。 经洗涤后,约60%~70%加压送入混合室与当量天然气混合 均匀。混合气首先进入一个换热器进行预热。换热器热源是 转化炉尾气。预热后的混合气送入转化炉中的镍质催化反应 管组,进行催化裂化反应,转化成还原气。还原气含 (CO+H2)95%左右,温度为850~900℃。
>2500
小于500N/个/wt%
<5.0
<2.0
23
对于Midrex工艺直接还原来说,含铁原料的高温特性,如还原 速率、还原粉化性能、粘结趋势和高温还原强度等,对整个竖炉 生产的顺行以及技术经济指标都非常关键。表8列出了Midrex工 艺对球团矿和块矿高温冶金性能的要求。
《气基直接还原竖炉炉型研究》

《气基直接还原竖炉炉型研究》篇一一、引言随着钢铁工业的不断发展,钢铁制造技术也日新月异。
其中,气基直接还原技术以其高效率、低能耗和环保特性成为了全球范围内广泛关注的研究领域。
气基直接还原竖炉作为该技术的重要组成部分,其炉型设计对生产效率和产品质量具有重要影响。
本文旨在研究气基直接还原竖炉的炉型,通过对现有炉型的分析,为改进炉型设计和提高生产效率提供理论依据。
二、气基直接还原技术概述气基直接还原技术是一种将铁矿石通过还原剂(如天然气、煤制气等)在高温下进行还原反应,得到铁基产品的工艺。
该技术具有高效率、低能耗、低污染等优点,被广泛应用于现代钢铁制造中。
三、气基直接还原竖炉的炉型研究(一)现有炉型分析目前,气基直接还原竖炉的炉型多种多样,主要包括圆形、椭圆形、矩形等。
这些炉型各有优缺点,如圆形炉型热效率高,但热应力大;矩形炉型热应力小,但热效率相对较低。
针对不同地区和不同需求,需要选用合适的炉型。
(二)新炉型研究针对现有炉型的不足,本文提出一种新型的气基直接还原竖炉炉型。
该炉型结合了圆形和矩形炉型的优点,采用特殊的结构设计,以降低热应力和提高热效率。
同时,该炉型还考虑了原料的进料方式、反应区的分布、热能的利用等因素,以实现更高的生产效率和更好的产品质量。
(三)实验验证与结果分析为了验证新型炉型的可行性和效果,本文进行了一系列的实验研究。
实验结果表明,新型炉型在热效率、生产效率和产品质量等方面均表现出较好的性能。
与现有炉型相比,新型炉型具有更高的生产效率和更好的产品质量,且在能耗和环保方面也有明显优势。
四、结论与展望本文通过对气基直接还原竖炉的炉型进行研究,提出了一种新型的炉型设计。
实验结果表明,新型炉型在热效率、生产效率和产品质量等方面均表现出较好的性能。
因此,本文认为新型炉型具有较大的应用潜力,可为钢铁企业提供更好的生产效率和产品质量。
未来,随着钢铁工业的不断发展,气基直接还原技术将得到更广泛的应用。
基于生物质气基直接还原的多孔球团炼铁机理及强化还原作用机制研究(国家自然科学

基于生物质气基直接还原的多孔球团炼铁机理及强化还原作用机制研究(国家自然科学全文共四篇示例,供读者参考第一篇示例:首先我们需要了解什么是生物质气基直接还原技术。
生物质气基直接还原是指将生物质气与铁矿石直接接触并进行还原反应,生成高质量的铁料。
生物质气中富含的CO、H2等还原性气体具有良好的还原性能,使得其可以替代传统的煤气进行铁矿石还原。
利用生物质气进行直接还原不仅可以减少CO2排放,提高资源利用率,还可以减少对有限煤炭资源的依赖,是一种环保、可持续的新型炼铁技术。
在生物质气基直接还原的炼铁过程中,多孔球团起着重要作用。
多孔球团是由矿石与还原剂混合而成的球形颗粒,具有高强度和良好的还原性能。
在多孔球团中,铁矿石与生物质气进行接触和反应,通过直接还原生成金属铁。
多孔球团的形成和结构对炼铁过程的效率和产品质量具有至关重要的影响。
研究多孔球团的形成机制和结构特征对于优化生物质气基直接还原技术具有重要意义。
除了多孔球团的研究外,强化还原作用机制也是一个关键的研究方向。
强化还原是指通过添加某些物质,如助熔剂等,来提高还原反应的速率和程度。
在生物质气基直接还原炼铁过程中,强化还原作用可以有效地提高金属铁的回收率和产品质量,降低生产成本,是推动技术进步和工业发展的重要手段。
研究强化还原作用机制,探究添加物质对还原反应的影响,可以为生物质气基直接还原技术的应用提供更多的可能性和发展空间。
基于生物质气基直接还原的多孔球团炼铁机理及强化还原作用机制的研究具有重要的理论和实践意义。
通过深入研究和不断探索,我们可以更好地理解并利用生物质气这一清洁能源,推动炼铁工业的可持续发展,为构建绿色低碳的社会环境做出贡献。
相信在各方的共同努力下,生物质气基直接还原技术必将迎来更加美好的未来。
第二篇示例:随着工业化的发展,铁矿石资源的消耗日益增加,传统的高炉法生产钢铁过程中存在着诸多问题,如煤矿资源枯竭、污染排放等。
人们开始寻找替代品,以实现更加环保和可持续的铁矿石炼制技术。
直接还原铁生产技术及现状

直接还原铁生产技术及现状铁生产技术的发展历史可以追溯到公元前2000年左右,最初的铁制品是通过在炭火中烧烤铁矿石来获得的。
这种烧烤技术被称为古老的冶金学,也被认为是人类历史上最早的冶金技术之一古代的铁生产技术在公元前1000年左右经历了重大的革新,这是由于铁矿石的高温还原反应被发现。
这种高温反应是通过将铁矿石与木炭或石炭混合,并在高温环境下加热来进行的。
这项技术的发现使得铁成为了当时最重要的金属之一,但其生产量仍然相对较小。
在一些古代文明中,如中国、印度等,铁的制造和使用逐渐扩大,为社会的农业、战争和工艺生产做出了重要贡献。
到了公元前300年左右,铁生产技术再次得到了改进。
在罗马时代,一种称为“减氧法”的技术被发明,这个技术将铁矿石与木炭放入特殊的炉子中,并且通过控制加热和供氧来获取较高纯度的铁。
这项技术极大地提高了铁的生产效率,使得罗马帝国在铁材料的生产和使用方面取得了巨大的进展。
这种技术的使用也标志着对铁生产的进一步工业化,奠定了现代铁产业的基础。
到了中世纪,铁生产技术进一步发展,很大程度上得益于对炼铁炉的改进。
这些改进包括提高炉子的结构、使用更多供氧装置以及改进燃烧气体的预热系统等。
这些改进使得炼铁过程更为高效,并且提高了产量和纯度。
到了18世纪,随着燃烧技术和冶金科学的进展,铁生产技术又迈上了一个新的台阶。
在这个时候,由于煤炭的大量使用,炼铁工艺发生了革命性的变化。
在这种现代炼铁法中,矿石和煤炭被放入高炉中,在高温环境下进行化学反应。
通过这个工艺,大量的铁矿石可以得到还原,得到高质量的生铁。
这种先进的炼铁法被广泛应用于欧洲的工业革命中,推动了工业化的进程。
随着时间的推移,各种现代技术和创新被应用于铁的生产过程中,这些技术包括用电解法提纯铁、高炉法等。
现代大规模铁生产以高炉和电炉为主,这些炉子能够生成高品质的铁,用于制造各种铁制品。
此外,利用再生铁和废钢再生技术也成为现代铁产业的重要组成部分,以提高资源利用效率和减少环境影响。
直接还原技术

9 钢铁生产工艺新流程及其评价
传统流程 高炉+转炉
新流程
直接还原竖炉+电炉 直接还原回转窑+电炉 熔融还原+转炉
二 直接还原工艺及原理
1 气基直接还原法
煤气同时起两个作用
如何确定煤气量? 对冶金还原煤气要求:氧化度低,CH4,H2S含量少, 适量N2及一定温度 如竖炉:氧化度1~2%,N2:10-40%,CH4:,2%,温 度:900~1100℃ 煤气转化目的:把碳氢化合物转化为H2,CO 燃料:气,液,固 如天然气,液化石油气,重油 煤转化冶金还原煤气:工业未曾实施
非高炉炼铁能源
能源消耗
还原剂
燃料 (提供热量)
8 非高炉炼铁产品性质及应用
海绵铁(直接还原铁)
DRI, Direct Reduced Iron, Sponge Iron
粒铁
半熔化状态下还原熔炼出的产品
工艺:回转窑或特种电炉 用途:高炉原料 液铁(Smelting Reduction Iron)
7 非高炉炼铁法使用的原料及能源
含铁原料 1.1要求较高的含铁品位。 原因:(并非工艺本事),电炉炼钢要求,(电耗增 加,生产率降低及炉衬寿命缩短)。要求铁矿石 脉石含量<3%,最高不超过5% CaO:希望的成分 MgO:有利于提高矿石软化温度,改善还原性,提 高强度 Cu:有害元素,污染电炉钢质量,Cu全部进入进 入海绵铁 Zn:碱金属:对竖炉有害 矿石中水分和烧损:越少越好,耗热
三 熔融还原
1 熔融还原简介
定义(瑞典冶金学家:Eketorp):指非高炉炼铁 方法中那些冶炼液态生铁的工艺过程• 产品: 铁水 副产品:炉渣、煤气 (生铁、炉渣与高炉相同,但煤气的数量 和成分却差别较大) 开发目的:代替焦炭高炉
- 1、下载文档前请自行甄别文档内容的完整性,平台不提供额外的编辑、内容补充、找答案等附加服务。
- 2、"仅部分预览"的文档,不可在线预览部分如存在完整性等问题,可反馈申请退款(可完整预览的文档不适用该条件!)。
- 3、如文档侵犯您的权益,请联系客服反馈,我们会尽快为您处理(人工客服工作时间:9:00-18:30)。
直接还原铁技术直按还原铁和熔融还原铁的生产。
直接还原铁和熔融还原铁的冶炼统称为非高炉法炼铁。
(一)直接还原法生产生铁直接还原法是指在低于熔化温度之下将铁矿石还原成海绵铁的炼铁生产过程,其产品为直接还原铁(即DRI),也称海绵铁。
该产品未经熔化,仍保持矿石外形,由于还原失氧形成大量气孔,在显微镜下观察团形似海绵而得名。
海绵铁的特点是含碳低(<1%),并保存了矿石中的脉石。
这些特性使其不宜大规模用于转炉炼钢,只适于代替废钢作为电炉炼钢的原料。
直接还原法分气基法和煤基法两大类。
前者是用天然气经裂化产出H2和CO气体,作为还原剂,在竖炉、罐式炉或流化床内将铁矿石中的氧化铁还原成海绵铁。
主要有Midrex法、HYL Ⅲ法、FIOR法等。
后者是用煤作还原剂,在回转窑、隧道窑等设备内将铁矿石中的氧化铁还原。
主要有FASMET法等。
直接还原法的优点有:(1)流程短,直接还原铁加电炉炼钢;(2)不用焦炭,不受炼焦煤短缺的影响;(3)污染少,取消了焦炉、烧结等工序;(4)海绵铁中硫、磷等有害杂质与有色金属含量低,有利于电炉冶炼优质钢种。
直接还原法的缺点有:(1)对原料要求较高:气基要有天然气;煤基要用灰熔点高、反应性好的煤;(2)海绵铁的价格一般比废钢要高。
直接还原法已有上百年的发展历史,但直到20世纪60年代才获得较大突破。
进入20世纪90年代,其生产工艺日臻成熟并获得长足发展。
其主要原因是:(1)天然气的大量开发利用,特别是高效率天然气转化法的采用,提供了适用的还原煤气,使直接还原法获得了来源丰富、价格相对便宜的新能源。
(2)电炉炼钢迅速发展以及冶炼多种优质钢的需要,大大扩展了对海绵铁的需求。
(3)选矿技术提高,可提供大量高品位精矿,矿石中的脉石量降低到还原冶炼过程中不需加以脱除的程度,从而简化了直接还原技术。
当前世界上直接还原铁量的90%以上是采用气基法生产的。
我国天然气主要供应化工和民用,不可能大量用于钢铁工业。
由于我国煤炭储量相对丰富,20世纪90年代以来煤基直接还原法已在天津、辽宁、吉林、山东等地形成了一定的生产规模。
直接还原铁是指用直接还原法在低温固态下还原的金属铁。
按生产方法可分为煤基直接还原铁和气基直接还原铁;按用途可分为炼钢用直接还原铁和其它用直接还原铁;按产品形式可分为海绵铁(DRI)和热压块铁(HBI)。
目前国内直接还原铁没有国家统一标准生产规格,只有行业内的不成文的标准,最终元素含量仍是根据客户需求。
规格如下:一类化学成分为:TFe≥95%,SO2≤0.65%,S≤0.03%,P≤0.03%。
二类化学成分为:TFe≥92%,SO2≤5.0%,S≤0.03%,P≤0.03%。
三类化学成分为:TFe≥90%,SO2≤7.0%,S≤0.03%,P≤0.03%。
四类化学成分为:TFe≥88%,SO2≤10.0%,S≤0.03%,P≤0.03%。
另外,含铁量超过97%以上也属于海绵铁,但应用于粉末冶金领域,其形状分块状和粉状(一次还原铁粉),如深加工还可做二次还原铁粉,其含铁量将达到99%以上,价格也相应较高。
(二)熔融还原法生产生铁熔融还原法是指不用高炉而在高温熔融状态下还原铁矿石的方法,其产品是成分与高炉铁水相近的液态铁水。
开发熔融还原法的目的是取代或补充高炉法炼铁。
与高炉法炼铁流程相比,熔融法炼铁有以下特点:(1)燃料用煤而不用焦炭,可不建焦炉,减少污染。
(2)可用与高炉一样的块状含铁原料或直接用矿粉作原料。
如用矿粉作原料,可不建烧结厂或球团厂。
(3)全用氧气而不用空气,氧气消耗量大。
(4)可生产出与高炉铁水成分、温度基本相同的铁水,供转炉炼钢。
(5)除生产铁水外,还产生大量的高热值煤气。
目前世界上熔融还原法很多,其中只有Corex法技术比较成熟并已形成工业生产规模,其它诸法仍在发展和工业化过程中。
熔融还原法在我国尚未得到很大发展,目前处于实验室试验和半工业试验阶段。
直接还原铁是铁矿在固态条件下直接还原为铁,可以用来作为冶炼优质钢、特殊钢的纯净原料,也可作为铸造、铁合金、粉末冶金等工艺的含铁原料。
这种工艺是不用焦碳炼铁,原料也是使用冷压球团不用烧结矿,所以是一种优质、低耗、低污染的炼铁新工艺,也是全世界钢铁冶金的前沿技术之一。
直接还原炼铁工艺有气基法和煤基法两种,按主体设备可分为竖炉法、回转窑法、转底炉法、反应罐法、罐式炉法和流化床法等。
目前,世界上90%以上的直接还原铁产量是用气基法生产出来的。
但是天然气资源有限、价高,使生产量增长不快。
用煤作还原剂在技术上也已过关,可以用块矿,球团矿或粉矿作铁原料(如竖炉、流化床、转底炉和回转窑等)。
但是,因为要求原燃料条件高(矿石品位要大于66%,含SiO2+Al2O3杂质要小于3%,煤中灰分要低等),规模小,设备寿命低,生产成本高和某些技术问题等原因,致使直接还原铁生产在全世界没有得到迅速发展。
因此,高炉炼铁生产工艺将在较长时间内仍将占有主导地位。
1.直接还原铁的质量要求直接还原铁是电炉冶炼优质钢种的好原料,所以要求的质量要高(包括化学成份和物理性能),且希望其产品质量要均匀、稳定。
1.1 化学成份直接还原铁的含铁量应大于90%,金属化率要>90%。
含SiO2每升高1%,要多加2%的石灰,渣量增加30Kg/t,电炉多耗电18.5kwh。
所以,要求直接还原铁所用原料含铁品位要高:赤铁矿应>66.5%,磁铁矿>67.5%,脉石(SiO2+Al2O3)量<3%~5%。
直接还原铁的金属化率每提高1%,可以节约能耗8~10度电/t。
直接还原铁含C<0.3%,P<0.03%,S<0.03%,Pb、Sn、As、Sb、Bi等有害元素是微量。
1.2 物理性能回转窑、竖炉、旋转床等工艺生产的直接还原铁是以球团矿为原料,要求粒度在5~30mm。
隧道窑工艺生产的还原铁大多数是瓦片状或棒状,长度为250~380mm,堆密度在1.7~2.0t/m³。
生产过程中产生的3~5mm磁性粉料,必须进行压块,才能用于炼钢。
强度:取决于生产工艺方法、原料性能和还原温度。
改进原料性能和提高温度有利于提高产品强度。
产品强度一般>500N/cm²。
2.直接还原铁产生工艺技术介绍2.1 竖炉法气基竖炉法MIDREX、HYL法直接还原铁产生中占有绝对优势,该工艺技术成熟、设备可靠,单位投资少,生产率高(容积利用系数可达8~12t/m³·d),单炉产量大(最高达180万t/年)等优点。
经过不断改进,其生产技术不断完善,实现规模化生产。
(1) MIDREX技术Midrex法标准流程由还原气制备和还原竖炉两部分组成。
还原气制备:将净化后含CO与H2约70%的炉顶气加压送入混合室,与当量天然气混合送入换热器预热,后进入1100℃左右有镍基催化剂的反应管进行催化裂化反应,转化成CO24%~36%、H260%~70%、CH43%~6%和870℃的还原气。
后从风口区吹入竖炉。
竖炉断面呈圆形,分为预热段、还原段和冷却段。
选用块矿和球团矿原料,从炉顶加料管装入,被上升的热还原气干燥、预热、还原。
随着温度升高,还原反映加速,炉料在800℃以上的还原段停留4~6小时。
新海绵铁进入冷却段完成终还原和渗碳反应,同时被自下而上通入的冷却气冷却至<100℃。
还原铁的排出速度用出铁器调节。
产品典型成分如下:产品化学成分(%)工艺/成分 Tfe ηFe SiO2 Al2O3 CaO MgO C P SMidrex 91-93 92-95 2.0-5.5 0.5-1.5 0.2-1.6 0.3-1.1 0.7-2.5 0.07 0.01 -0.03 工艺多用球团和块矿混合炉料。
球团粒度9-16mm占95%,球团冷压强度>2450N/球,块矿粒度10~35mm占85%;要有高软化温度和中等还原性;化学成分铁量要高,酸性脉石低(≯3%-5%),CaO<2.5%,MgO<1.0%,TiO<0.15%,S<0.008%。
为放宽对矿石含硫要求,Midrex法改用净化炉顶气作冷却气。
在冷却海绵铁的同时被热海绵铁脱硫,从冷却段排出后再作为裂化剂,可容许用含硫0.02%矿石。
现今Midrex法作业指标为:产品金属化率86%~96%,有效容积利用系数10 t/m³·d,能耗10.47GJ/t,电114kWh/t,水1.64m³/t。
Arex法是Midrex法的新改进,天然气被氧气(或空气)部分氧化后送入竖炉,利用新生热海绵铁催化裂化,省去了还原气重整炉。
改进后吨铁电耗可降低50Kwh。
(2) HYL(罐式)法与HYL-Ⅲ(竖炉)法。
HYL法由4座罐式反应炉和1座还原气重整炉构成。
该工艺作业稳定、设备可靠。
产品含碳2%左右,不易再氧化,不发生炉料粘结;只因还原气要反复冷却、加热,系统热效率低,能耗偏高,气体消耗为20.93GJ/t;1975年后再没建新厂。
对HYL罐式法作出改革,保留原还原制备工艺,但将还原气重整转化与气体加热合一;4个罐式反应炉改为连续式竖炉,称HYL-Ⅲ竖炉法。
该工艺采用高氢还原气,高还原温度(900-960℃)和0.4-0.6MPa高压作业。
改善还原动力学,加速还原发应;含硫气不通过重整炉,延长了催化剂和催化管使用寿命;还原和冷却作业分别控制,能对产品金属化率和含碳量进行大范围调节,产品平均金属化率90.9%、控制碳量1.5%-3.0%,质量稳定;配置CO2吸收塔,选择性地脱除还原气中H2O和CO2,提高还原气利用率;重整炉产生高压蒸汽发电。
最低生产能耗为10.43-11.2 GJ/t,电耗90kWh/t。
HYL(罐式)法已逐渐被HYL-Ⅲ(竖炉)法取代,合计产量占世界总产量的25%左右。
该法的新改进是天然气进入反应器直接裂解,生产高碳(3.8%)DRI产品。
最近又推出HYL-Hytemp生产系统。
将热还原铁(650℃)气力输送到电炉车间,喷入电炉。
冶炼时间缩短,电极和耐火材料消耗降低,金属收率提高。
吨钢电耗降低112kW·h,电极消耗降低0.55kg,冶炼时间缩短16min,产率提高16%,吨钢成本可降低4.6美元。
2.2 气基流化工艺(1)F1NMEF工艺该工艺使用<12mm粒度矿粉(脉石<3%,低硅高铁),在流化床上干燥,被加热到100℃,送入反应器结构顶端的闭锁料斗系统中,加压1.1MPa后,通过4个串联液化床反应器,铁粉在重力作用下从上方反应器向下流动,与作为还原剂的重整天然气逆向而行。
产品含铁92%,金属化率92%~95%,含碳0.5%~3.0%,以FeC形式存在。
现世界上已有三套这种装置,1999年奥钢联建第一套,第二套在西澳BNP 公司,能力250万吨/年,埃及建的第三套,年能力115万吨。