机械钻孔(1)
机械制造的技术(下)习题(1)

机械制造的技术(下)习题(1)《机械制造技术》习题第⼗四章机械加⼯⼯艺规程的制订1-1 什么是⽣产过程、⼯艺过程和⼯艺规程?1-2 什么是⼯序、⼯位、⼯步和⾛⼑?试举例说明。
1-3 什么是安装?什么是装夹?它们有什么区别?1-4 单件⽣产、成批⽣产、⼤量⽣产各有哪些⼯艺特征?1-5 试为某车床⼚丝杠⽣产线确定⽣产类型,⽣产条件如下:加⼯零件:卧式车床丝杠(长为1617mm,直径为40mm,丝杠精度等级为8级,材料为Y40Mn);年产量:5000台车床;备品率:5%;废品率:0.5%。
1-6 什么是⼯件的定位?什么是⼯件的夹紧?试举例说明。
1-7 什么是⼯件的⽋定位?什么是⼯件的过定位?试举例说明。
1-8 试举例说明什么是设计基准、⼯艺基准、⼯序基准、定位基准、测量基准和装配基准。
1-9 有⼈说:“⼯件在夹具中装夹,只要有6个定位⽀承点,就是⽋定位”,“凡是少于6个定位⽀承点,就不会出现过定位”,上⾯这些说法都对吗?为什么?试举例说明。
1-10 分析图1-8所⽰定位⽅式,并回答以下问题:(1)各定位件所限制的⾃由度;(2)判断有⽆⽋定位或过定位现象,为什么?图1-8 习题1-10图第⼗六章机械加⼯质量及其控制4-1 什么是主轴回转精度?为什么外圆磨床头夹中的顶尖不随⼯件⼀起回转,⽽车床床头箱中中的顶尖则是随⼯件⼀起回转的?4-2 在镗床上镗孔时(⼑具作旋转主运动,⼯件作进给运动),试分析加⼯表⾯产⽣椭圆形误差的原因。
4-3 为什么卧式车床床⾝导轨在⽔平⾯内的直线度要求⾼于垂直⾯内的直线度要求?4-4 某车床导轨在⽔平⾯内的直线度误差为0.015/1000mm ,在垂直⾯内的直线度误差为0.025/1000mm ,欲在此车床上车削直径为φ60mm 、长度为150mm 的⼯件,试计算被加⼯⼯件由导轨⼏何误差引起的圆柱度误差。
4-5 在车床上精车⼀批直径为φ60mm 、长为1200mm 的长轴外圆。
已知:⼯件材料为45钢;切削⽤量为:120=νm/min, p α=0.4mm, f =0.2mm/r; ⼑具材料为YT15。
钻孔及其定位方法1
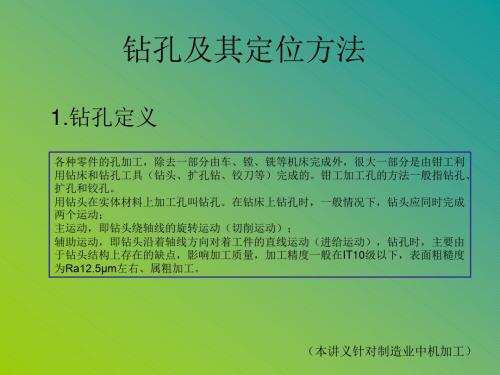
钻孔及其定位方法
11.钻孔时产生振动或孔不圆的原因及防止方法
1.钻头的后角太大,左、行两主切削刃不对称,摆差大,钻孔时则容易产生 振动和孔不圆,应正确刃磨钻头,适当减小后角可以加钻套。 减少钻头的 振动很摆动 2.工件表面不平或内部有缺陷。 工件表面不平整或有气孔、砂眼、夹渣等,工件内部有缺口、交叉孔,或工 件夹紧不牢,都是造成振动和几不圆的原因。因此,应当更换合格的毛坯, 改变工件结构或工序顺序,并保证工件装夹牢靠。 3.主轴轴承间隙太大。 车床主轴袖承间隙太大,钻孔时亦会引起振动和孔不圆。应当调整主轴轴承 间隙或更换轴承。 4.孔壁表面粗糙度值大
(本讲义针对制造业中机加工)
钻孔及其定位方法
14.钻头
钻头是钻孔用的刀削工具,常用高速钢制造,工作部分经热处理淬硬至62~ 65HRC。一般钻头由柄部、颈部及工作部分组成(实物与挂图)。 1.柄部:是钻头的夹持部分,起传递动力的作用,柄部有直柄和锥柄两种, 直柄传递扭矩较小,一般用在直径小于12mm的钻头;锥柄可传递较大扭矩 (主要是靠柄的扁尾部分),用在直径大于12mm的钻头。 2.颈部:是砂轮磨削钻头时退刀用的,钻头的直径大小等一般也刻在颈部。 3.工作部分:它包括导向部分和切削部分。导向部分有两条狭长、螺纹形状 的刃带(棱边亦即副切削刃)和螺旋槽。棱边的作用是引导钻头和修光孔壁; 两条对称螺旋槽的作用是排除切屑和输送切削液(冷却液)。切削部分结构 见挂图与实物,它有两条主切屑刃和一条柄刃。两条主切屑刃之间通常为 118°±2°,称为顶角。横刃的存在使锉削是轴向力增加。
(本讲义针对制造业中机加工)
钻孔及其定位方法
17.扩孔与铰孔
1.扩孔 扩孔用以扩大已加工出的孔(铸出、锻出或钻出的孔),它可以校正孔的轴线偏差,并使其获得正确的几何形 状和较小的表面粗糙度,其加工精度一般为IT9~IT10级,表面粗糙度、Ra=3.2~6.3μm。扩孔的加工余量一般 为0.2~4mm。 扩孔时可用钻头扩孔,但当孔精度要求较高时常用扩孔钻(用挂图或实物)。扩孔钻的形状与钻头相似,不同 是:扩孔钻有3~4个切削刃,且没有横刃,其顶端是平的,螺旋槽较浅,故钻芯粗实、刚性好,不易变形,导 向性好。 2.铰孔 铰孔是用铰刀从工件壁上切除微量金属层,以提高孔的尺寸精度和表面质量的加工方法。铰孔是应用较普遍的 孔的精加工方法之一,其加工精度可达IT6~IT7级,表面粗糙度Ra=0.4~0.8μm。 铰刀是多刃切削刀具(挂图或实物),有6~12个切削刃和较小顶角。铰孔时导向性好。铰刀刀齿的齿槽很宽, 铰刀的横截面大,因此刚性好。铰孔时因为余量很小,每个切削刃上的负荷著小于扩孔钻,且切削刃的前角 γ0=0°,所以铰削过程实际上是修刮过程。特别是手工铰孔时,切削速度很低,不会受到切削热和振动的影响, 因此使孔加工的质量较高。 铰孔按使用方法分为手用铰刀和机用铰刀两种。手用铰刀的顶角较机用铰刀小,其柄为直柄(机用铰刀为锥 柄)。铰刀的工作部分有切削部分和修光部分所组成。 铰孔时铰刀不能倒转,否则会卡在孔壁和切削刃之间,而使孔壁划伤或切削刃崩裂。 铰孔时常用适当的冷却液来降低刀具和工件的温度;防止产生切屑瘤;并减少切屑细末粘附在铰刀和孔壁上, 从而提高孔的质量。
标准钻孔对照表

标准钻孔对照表钻孔是机械加工中的一项基础操作,它涉及到各种不同的应用和行业。
准确地进行钻孔至关重要,因为它直接影响到零件的加工质量和装配精度。
为了确保钻孔的准确性和一致性,制定了一系列的标准钻孔对照表,这些对照表提供了不同规格的钻头直径、螺纹直径、孔深等参数的参考。
以下是一些常见的标准钻孔对照表的详细介绍:1. 公制标准钻孔对照表公制标准钻孔对照表是最常见的钻孔对照表之一,它以毫米为单位,提供了各种标准的钻头直径、螺纹直径和孔深数据。
这些数据通常用于金属加工,尤其是机械制造和模具制造行业。
公制标准钻孔对照表包括各种不同的螺纹规格,如M1.0、M1.2、M1.4、M1.6等,以及对应的钻头直径和孔深。
2. 英制标准钻孔对照表英制标准钻孔对照表以英寸为单位,主要用于英国和美国的工业中。
它提供了英制螺纹规格,如1/16英寸、1/8英寸、1/4英寸等,以及对应的钻头直径和孔深。
英制标准钻孔对照表对于英制系统的机械设计和制造非常重要。
3. 模数螺纹钻孔对照表模数螺纹钻孔对照表用于模数螺纹的加工,如M1、M2、M3等。
它提供了模数螺纹的直径、螺距和对应的钻头直径和孔深。
模数螺纹钻孔对照表对于精确的模具设计和制造至关重要。
4. 径节螺纹钻孔对照表径节螺纹钻孔对照表用于径节螺纹的加工,如5°、6°、7°等。
它提供了径节螺纹的直径、螺距和对应的钻头直径和孔深。
径节螺纹钻孔对照表对于汽车、船舶等行业的零件加工非常重要。
除了上述常见的钻孔对照表,还有许多其他的专业钻孔对照表,用于特定的行业和应用。
这些对照表通常可以在机械加工手册、螺纹标准书籍或在线资源中找到。
在实际应用中,使用标准钻孔对照表可以确保钻孔的准确性和一致性,提高生产效率和产品质量。
然而,由于加工条件和技术要求的不同,有时需要对标准钻孔对照表进行调整和优化,以满足特定的生产需求。
因此,理解和掌握标准钻孔对照表的同时,也需要根据实际情况进行合理的调整和应用。
作业题讲解2-1(尺寸链、定位误差)教材
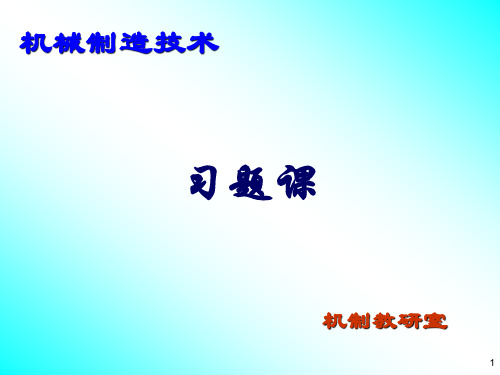
增环
A
封闭环
6±0.10 (A∑)
增环
26±0.05(A2)
36-0.05(A1)
减环
3)计算 基本尺寸 A∑= A2 +A- A1
6= 26+A-36
A=16 上偏差ESA∑= ESA2+ESA-EIA1
0.10= 0.05+ESA-(-0.05)
ESA=0 下偏差EIA∑= EIA2+EIA-ESA1
16-0.025、0.8+0.2为增环,d/2为减环。
d/2 16-0.025
2)计算 基本尺寸 0.5= 16 +0.8 –d/2
d/2= 16.3 上偏差0.3= 0+0.2-EId/2
EId/2= -0.1 下偏差0= -0.025+0-ESd/2
ESd/2= -0.025
d
/
2
16
.30.025 0.1
解: 1)确定封闭环:加工时间接保证的尺寸为t=4+0.16。画 出尺寸链图。
t H
14
0.012 0.004
14.25
0 0.05
2)判断增减环
:14
0.012 0.004
、H
为增环
,14.25
0 0.05
为减环。
3)计算
基本尺寸 4= H+14-14.25 H=4.25
上偏差0.16= ESH+0.012-(-0.05)
2.在车床上加工一批光轴的外圆,加工后经度量发现整 批工件有下列几何形状误差;①锥形(图2a);②鞍形( 图2b);③腰鼓形(图2c);④喇叭形(图2d)。试分别 说明可能产生上述误差的各种因素?
建筑施工技术课后答案

第4章地基加固与桩基施工技术1.地基处理方法一般有哪几种?各有什么特点?2.试述换土垫层法的适用情况、施工要点与质量检查?3.浅埋式钢筋混凝土基础主要有哪几种?4.试述桩基的作用和分类?5.钢筋混凝土预制桩在制作、起吊、运输和堆放过程中各有什么要求?6.打桩前要做哪些准备工作?打桩设备如何选用?7.试述打桩过程及质量控制?8.静力压桩有何特点?适用范围如何?施工时应注意哪些问题?9.现浇混凝土桩的成孔方法有几种?各种方法的特点及适用范围如何?10.灌注桩常易发生哪些质量问题?如何预防和处理?11.试述人工挖孔灌注桩的施工工艺和施工中应注意的主要问题?12.试述爆扩桩的成孔方法和施工中常见问题?13.桩基检测的方法有几种?验收时应准备哪些资料?参考答案:1.地基处理方法一般有哪几种?各有什么特点?答:(1)机械压实法:通过提高其密实度,从而提高其强度,降低其压缩性。
(2)强夯法:施工时,振动大,噪声大,对附近建筑物的安全和居民的正常生活有影响。
(3)换土垫层法:是将天然弱土层挖去,分层回填强度较高,压缩性较低且无腐蚀性的砂土、素土、灰土、工业废料等材料,压实或夯实后作为地基垫层。
(4)排水固结法:适用于淤泥、淤泥质土、冲填土等饱和粘土的地基处理。
(5)挤密法:主要适用于处理松软砂类土、素填土、杂填土、湿陷性黄土等。
(6)化学加固法:指的是采用化学浆液灌入或喷人土中,使土体固结以加固地基的处理方法。
2.试述换土垫层法的适用情况、施工要点与质量检查?答:换土垫层法是指把基础或建筑物下一定深度的软弱(性质差)的土层通过挖土置换成性质好的土层或砂石的地基处理方法。
垫层的实质是把基础下软弱的土层挖掉换填上物理力学性质好的材料,以减少建筑物的沉降,提高地基强度。
在我国软弱地基分布较广的东部沿海地区,这种古老而传统的方法在各类工程建设中得到了广泛的应用,并积累了丰富的经验。
目前我国常采用垫层有土垫层、灰土垫层、砂垫层、碎石(卵石)垫层、粉煤灰垫层、高炉渣垫层等。
发动机箱体的机械加工工艺及钻孔夹具设计1

摘要本设计是汽车变速箱箱体零件的加工工艺规程及一些工序的专用夹具设计。
汽车变速箱箱体零件的主要加工表面是平面及孔系。
一般来说,保证平面的加工精度要比保证孔系的加工精度容易。
因此,本设计遵循先面后孔的原则。
并将孔与平面的加工明确划分成粗加工和精加工阶段以保证孔系加工精度。
基准选择以变速箱箱体的输入轴和输出轴的支承孔作为粗基准,以顶面与两个工艺孔作为精基准。
主要加工工序安排是先以支承孔系定位加工出顶平面,再以顶平面与支承孔系定位加工出工艺孔。
在后续工序中除个别工序外均用顶平面和工艺孔定位加工其他孔系与平面。
支承孔系的加工采用的是坐标法镗孔。
整个加工过程均选用组合机床。
夹具选用专用夹具,夹紧方式多选用气动夹紧,夹紧可靠,机构可以不必自锁。
因此生产效率较高。
适用于大批量、流水线上加工。
能够满足设计要求。
关键词:变速箱;加工工艺;专用夹具AbstractThe design is about the special-purpose clamping apparatus of the machining technology process and some working procedures of the car gearbox parts. The main machining surface of the car gearbox parts is the plane and a series of hole. Generally speaking, to guarantee the working accuracy of the plane is easier than to guarantee the hole’s. So the design follows the principle of plane first and hole second. And in order to guarantee the working accuracy of the series of hole, the machining of the hole and the plane is clearly divided into rough machining stage and finish machining stage. The supporting hole of the input bearing and output bearing is as the rough datum. And the top area and two technological holes are as the finish datum. The main process of machining technology is that first, the series of supporting hole fix and machine the top plane, and then the top plane and the series of supporting hole fix and machine technological hole. In the follow-up working procedure, all working procedures except several special ones fix and machine other series of hole and plane by using the top plane and technological hole. The machining way of the series of supporting hole is to bore hole by coordinate. The combination machine tool and special-purpose clamping apparatus are used in the whole machining process. The clamping way is to clamp bypneumatic and is very helpful. The instruction does not have to lock by itself. So the product efficiency is high. It is applicable for mass working and machining in assembly line. It can meet the design requirements.Key words: Gearbox; machining technology; special-purpose clamping apparatus目录摘要 (I)ABSTRACT ...................................................... I I 目录......................................................... I II 第1章绪论 (1)1.1当前发展现状 (1)1.2 论文主要研究内容 (2)第2章发动机箱体工艺设计 (3)2.1箱体的分析 (3)2.1.1箱体的功用分析 (4)2.1.2箱体结构和功用的分析 (5)2.1.4箱体的技术分析 (6)2.1.5箱体的材料分析 (6)2.2发动机箱体毛坯的设计 (7)2.2.1确定毛坯种类及加工方法的选择 (7)2.2.2毛坯的工艺分析及要求 (8)2.2.3毛坯余量和公差的确定 (9)2.3工艺路线设计 (12)2.3.1加工方法的选择 (12)2.3.2箱体的材料及热处理 (12)2.3.3阶段的划分 (13)2.3.4工序的集中与分散 (13)2.3.5基准的选择 (14)2.3.6 拟定发动机箱体的工艺路线 (15)2.4 加工设备及工艺装备的选择 (17)2.5 加工工序设计 (19)第3章钻床专用夹具设计 (26)3.1夹具的设计内容 (26)3.1.1定位基准的选择 (26)3.1.2工件的夹紧及夹紧装置 (26)3.1.3夹具材料的选择 (30)3.1.4夹具精度分析 (28)3.2削边销 (26)3.3支承板 (26)3.4压板 (27)3.5夹具体中间支架 (28)3.6齿轮齿条偏心轮部分的设计 (26)3.7齿轮的设计 (27)3.8键的选择及校核............................ 错误!未定义书签。
钻孔工艺工序卡片 (1)

安徽农业大学工学院 09级机制一班机械加工工艺过程卡零件名称零件图号滑阀前盖工序号 工序名称及内容机床 夹具刀具 量具 工时名称型号名称规格名称 规格1 铸造 2时效3粗车φ25左端面凸台左面精车凸台右表面和Φ25右 端面 精车圆柱外侧面普通车床 CM6140气动可胀心轴弯头车刀45° 游标卡尺 125*0.024 钻、铰内孔 φ17 立式钻床 Z515 专用钻夹具 钻头 铰刀 Φ16.75Φ17 内径千分尺 50-175 5 粗铣凸台4个侧面 卧式铣床 X6132 专用铣夹具 圆柱铣刀 Φ50 游标卡尺 200*0.02 3.8S 6铣圆角4-R2卧式铣床X6132专用铣夹具 圆角铣刀R27粗铣槽130.24+x18 卧式铣床 X6132 专用铣夹具 三面刃铣刀 D=63 d=22 Z=14游标卡尺 200*0.028 粗镗内槽 卧式镗床 T68 专用镗夹具 弯头内孔镗刀 内径千分尺50-175 9 钻锪4个φ5.5孔 φ9柱孔 摇臂钻床 Z3025 专用钻夹具 麻花钻、锪刀 φ 5.5 φ 9 内径千分尺 50-175 23.44S 10 去尖角1x45° 普通车床 CM6140 气动心轴 弯头刀 4 5° 游标卡尺 200*0.05 11清洗打油清洗机设计者指导教师共1页第 1 页安徽农业大学工学院09机制一班机械加工工序卡片工序名称钻φ5.5孔锪φ9柱孔工序号9零件名称滑阀前盖零件图号零件重量同时加工零件数1材料毛坯牌号硬度形式尺寸HT15-33HRC50铸件48mmx56mmX42mm设备夹具名称型号专用钻夹具摇臂钻床Z3025工步号工步内容工艺装备主轴转速r/min切削速度m/min进给量mm/r切削深度mm进给次数工时s1钻φ5.5mm孔专用钻夹具φ5.5麻花钻φ9mm锪刀 160025 0.08 10 1 4.692锪φ9mmx5mm柱孔 160043 0.16 5 1 1.17设计者指导教师共 1 页第 1 页。
钻孔施工工艺流程及风险辨识与管控(1)

钻孔施工工艺流程及风险辨识与管控流程1:钻场安全确认风险描述:1.施工前未检查顶板、帮部、迎头支护情况,易造成人员伤害。
2.作业现场前后5m未设置警戒标识,易造成人员伤害或设备损坏。
3.安全撤离通道不畅通,发生灾害时人员容易绊倒或造成撤离不迅速,易造成人员伤害。
管控措施:1.施工前,必须严格执行“敲帮问顶”制度,及时处理顶、帮、活煤(矸石),确保顶板、帮部、迎头支护完好。
2.施工前,作业地点前后5m必须设置警戒标识。
3.施工前,确保作业现场安全撤离通道畅通。
流程2:安设一部专用电话风险描述:施工前未安设专用电话,当发生险情及事故时,无法及时汇报,会导致事故发生或危害程度增大。
管控措施:施工前必须安设一部专用电话,并保证通讯畅通。
流程3:平整作业场地风险描述:作业场地未做到平整,当设备行走或运行时,易造成设备倾倒伤人事故。
管控措施:施工前,必须安排人员对作业场地的浮煤、杂物清理干净,确保设备安全平稳行走或运行。
流程4:搬运钻机风险描述:1.钻机装卸车时,未做到停车制动后,进行捆绑与固定作业,易造成人员挤压或钻机侧翻伤人;2.在装卸车时,人员站位不正确,易造成钻机侧翻与车辆挤压伤人;3.搬运钻机时,未将钻机固定牢固,易造成钻机侧翻伤人或损坏设备事故。
管控措施:1.钻机装卸车时,车辆必须停车熄火,堰好阻车器,方可进行作业;2.在进行装卸作业时,人员必须站位正确;3.搬运钻机,必须将钻机捆绑牢固。
流程5:设备系统完善风险描述:1.在安装或拆除电气设备时,未严格执行停送电制度,电气设备未及时打接地;易造成设备误送电及漏电伤人事故。
2.电气设备投入运行前,未安设接地极时;易造成设备漏电伤人事故。
3.连接风水管路时,未使用专用卡子,易造成管路连接脱开伤人事故。
4.拆卸风水管路时,未对风水管路泄压,易造成管路内介质及管路摆动伤人事故。
5.根据设备功率匹配相应的电缆、开关,如选型不合理,易造成电气设备过载,烧毁设备、电缆,以及作业人员触电事故。
- 1、下载文档前请自行甄别文档内容的完整性,平台不提供额外的编辑、内容补充、找答案等附加服务。
- 2、"仅部分预览"的文档,不可在线预览部分如存在完整性等问题,可反馈申请退款(可完整预览的文档不适用该条件!)。
- 3、如文档侵犯您的权益,请联系客服反馈,我们会尽快为您处理(人工客服工作时间:9:00-18:30)。
¨
6.4mm,板的尺寸最大是18”X25”。
机械钻孔(1)
¨ ADVANCED CONTROL--是美国制造的钻机,型号是
¨ 钻头钻
TRUDRIL2550,有5个
¨ 轴承钻头,
速最高120Krpm,是
¨ 板的尺寸
钻孔能力由0.1mm-6
¨
最大是20.5”X31”
¨ ADVANCED CONTROL--美国制造的钻机,型号是TRUDRIL
机械钻孔(1)
四、钻孔的工艺参数控制:
钻孔的工艺参数包括: 钻头的转速N(影响切削速度V)(rpm/min) 进给速度F(feed Rate/min) 最大钻孔数Hits(max nit) 叠板块数PL/STK(panel/stack)
机械钻孔(1)
1、钻头的转速N:
切削速度是指钻咀外径的丝速度,理想的切削速度是
¨ 1、手动磨钻咀机
¨
由马达带动两个砂轮转动,分为初级及次级,待磨钻咀放入
¨
已调好翻磨钻尖角度的索咀夹头内,使用放大镜调好翻磨深
¨
度后,控制机台移动,带动夹着钻咀的索咀移向砂轮,经过
¨
初级及次级砂轮打磨钻尖位置
机械钻孔(1)
3rew
演讲完毕,谢谢听讲!
再见,see you again
2020/11/18
机械钻孔(1)
1、钻机的种类
¨ HITACHI--是日本制造的钻机,型号是6L180E,有6个钻头,钻
¨ 头
头钻速最高是160/125rpm,是空气轴承
¨ POSALUX--是瑞士制造的钻机,型号分别有M22、M23两种,
¨ 是80Krpm
有5个钻头,钻头钻速有两种,分别最
¨ 由0.1mm-
及100Krpm,是空气轴承钻头,钻孔能
机械钻孔(1)
3、最大钻孔数Hits
最大钻孔数取决于钻咀的材质,直径大小以及所钻板的层数来定 为便于控制,我们现用的最大钻孔数暂未将层数的因素在内。
新钻咀
钻孔
够Hits 数
翻磨
清洗后标
简单的判断Hits数法:所钻板材上表面铜箔连续出现毛刺,表明钻 咀必须要翻磨了。
机械钻孔(1)
4、叠板块数PL/STR
每叠板的块数主要取决于板的层数,板的厚度、钻机类 型、最小钻咀的直径以及板的内层特性(如HWTC)等。
机械钻孔(1)
钻孔的工艺参数,详细请阅WI: 0841-CG-001 0841-02-001
以及标识于每台机台上的钻孔表、LOT等。
机械钻孔(1)
五、钻机的工作原理:
钻机由CNC电脑系统控制机台移动,按所输入电脑的资料制 出客户所需孔的位置 控制方面分别有X、Y辆坐标及Z轴坐标,电脑控制机台适当 钻孔参数,F、N、Hits、D等,机器会自动按照资料,把所 的孔位置钻出来。
下工序
QE发钻孔资料
IPQC抽样检
机械钻孔(1)
三、钻孔所用的基本物料:
1、铝片 作用:防止钻孔上表面毛刺保护覆铜箔层不被压伤,提高孔位精度 要求:有利于钻头、钻咀的散热;不折断钻咀;冷却钻头,降低钻
2、底板 作用:防止钻孔披锋;防止损坏钻机台;减少钻咀损耗。 要求:板面要平滑、清洁;产生的碎屑要小;与待钻板大小一致。
机械钻孔(1)
¨
1.6mm至3.6mm用中粗糙度1200
¨
3.6mm至6.4mm用大粗糙度600/1200
机械钻孔(1)
¨ 2、自动磨钻咀机
¨
磨钻咀能力--0.3mm至3.175mm
¨翻磨钻咀角度--0.Fra bibliotekmm至3.175mm是130度
机械钻孔(1)
十、翻磨钻咀的工艺原理:
¨
翻磨钻咀机分为手动磨钻咀机及自动磨钻咀机
规大小相容。 孔质量——目检,应无火山口,钻不穿、塞孔等。 板面质量——应无胶迹,无批锋等缺陷。
机械钻孔(1)
七、钻孔常见的品质缺陷及原因分析:
缺陷:板有漏孔现象 原因:因钻咀拆断,操作员工忘记补钻孔
缺陷:板有歪孔现象 原因:管位钉松脱或偏移,或零位位置不确
缺陷:板多了不应该有的孔 原因:钻孔资料错误或补孔时找错位置
机械钻孔(1)
缺陷:钻孔后孔内有塞孔现象 原因:生产板孔被钻屑堵住,不能吸走,吸尘系统
吸尘不良所致或钻深设定不当
缺陷:板面有披锋 原因:覆盖板面的铝片变形不能平直覆盖或垫板弯曲不能平
直垫着板料
缺陷:基板钻孔未能钻穿 原因:钻咀长度不正确或钻机的深度数值调校不正确所致
缺陷:生产板孔内留有断钻咀尖 原因:使用不适当的钻孔参数钻孔或使用翻磨次数太多的钻
是滚珠
¨ 尺寸最大是18.5”X25”。
6.4mm,
机械钻孔(1)
六、钻孔品质检查及控制:
1、工具控制:
磁碟(钻带)
客户资料
PE制作
QE检查
合格
标签
绿胶片:
钻带
PE制作胶片 及标准板
不合格
QE检查
合格
标签
机械钻孔(1)
2、检查项目:
钻孔后检查并确保佑以下项目满足客户要求:
孔数——用绿胶片拍最底一块,应无漏孔或钻多孔。 孔位置——用绿胶片拍最底一块,应无歪孔及崩孔。 孔大小——用塞规塞最底一块,板边测试孔孔大小应与塞
横刀与主切削刀的磨损速度相同。
公式:
VΠ= . D. N 1000
(m/min)
其中:D——钻咀直径(mm) N——钻咀转速(rpm)
机械钻孔(1)
2、进给速度 F
进给速度表示钻咀单位时间的进刀量;F=N.F(mm/min) 式中:f-进给转速比(mm/r) N- 钻咀转速(r/min)
f 表示每一转的进刀量,f的取值范围为0.01-0.4mm;(一般取钻 咀直径的5-7%). 当f < 0.01mm时,切削刀因进给太小而刮研,会产生大量的热. 当f > 0.4mm时,切削刀变成冲孔,钻孔质量差且易断钻咀.
¨ 速最高是
104,有5个钻头,钻
¨ 头,钻孔能
120Krpm,是空气轴
¨ 尺寸最大是
力由0.1mm-6.4mm,
¨
16.7”X25”。
机械钻孔(1)
¨ ADVANCED CONTROL--美国制造的钻机,型号是TRUDRIL97,
¨ 钻头钻速最高70Krpm,
有4个钻
¨ 钻头,钻孔能力由0.3-
3、皱纹胶纸 作用:固定锯片及每叠板于机台,提高钻孔精度。 要求:每叠板四边固定,只覆盖板边,不能接触板面。
4、管位钉 作用:固定每叠板于机台,提高钻孔精度。 要求:不能松动;不能弯曲。直径与管位钉一致,不能太大或太小
5、钻咀 作用:通过钻机在高转速和一定落速带动下钻穿线路板。 要求:钻咀直径、钻杆直径、钻尖面要符合要求;钻咀要清洁;材 一定韧性、硬度及耐磨性能。
满足客户的要求。
实现层与层间的导通,以及将来的元件插焊。 为后工序的加工做出定位或对位孔。
机械钻孔(1)
二、钻孔的工艺流程:
A、双面板:
QE发钻孔资料
IPQC
切板 修边 锔板 钻定位孔 钻机钻孔 检查 锔板 冷却 下工序
B、多层板:
内层X-RAY钻孔
内层压板 钻定位孔 修边 钻机钻孔 检查 锔板
机械钻孔(1)
八、翻磨钻咀的工艺流程
¨ 旧钻咀收集钻咀分类直径及长度测量清洗钻咀翻磨 ¨ 不合格 ¨ 检查合格清洗标记入盒库存待发放
机械钻孔(1)
九、翻磨钻咀的工艺参数:
¨ 1、手动磨钻咀机
¨
磨钻咀能力--0.7mm至3.175mm是130度
¨
3.2mm至6.4mm是165度
¨
砂轮试用粗糙度--0.7mm至1.6mm用幼细粗糙度1200/20
机械钻孔(1)
2020/11/18
机械钻孔(1)
课程大纲
1、钻孔的目的。 2、钻孔所用的基本物料。 3、钻孔的工艺、流程。 4、钻孔的工艺参数。
5、钻机的工作原理。 6、钻孔品质检查及控制。 7、钻孔品质缺陷及原因分析 8、钻孔的工艺发展展望。
机械钻孔(1)
一、钻孔的目的:
在板料上钻出客户要求的孔,孔的位置及大小均需