超高强度钢板冲压件热成形工艺.
超高强度钢板热成形生产方案(一)

超高强度钢板热成形生产方案一、实施背景随着中国制造业的飞速发展,钢铁行业在国民经济中的地位愈加重要。
然而,国内超高强度钢的生产技术与国外先进水平还存在一定差距。
尤其在高品质、高强度、高可靠性方面,我们仍有大量的提升空间。
因此,进行超高强度钢的研发与生产,不仅是产业结构改革的需要,更是提升国家整体竞争力的必然要求。
二、工作原理超高强度钢的研发与生产,首先需要了解其工作原理。
一般来说,超高强度钢的强度高于500MPa,具有出色的抗冲击、抗疲劳性能。
其工作原理主要基于金属的强化机制,如固溶强化、细晶强化、析出强化等。
通过合理的成分设计和热处理工艺,可以显著提高钢材的强度和韧性。
三、实施计划步骤1.成分设计:根据需求和目标,设计合理的化学成分,如C、Si、Mn、Nb、V等元素的含量。
2.冶炼与连铸:通过高纯度冶炼技术,确保钢水中的杂质元素含量低于标准值。
连铸过程中,采用电磁搅拌技术,减小钢水温度梯度,降低裂纹倾向。
3.热处理:根据成分和性能要求,制定合适的热处理工艺。
如淬火、回火、冷却等步骤,以实现钢材的强化和韧化。
4.轧制与精整:通过多道次的轧制和精整,确保钢材的表面质量和尺寸精度。
5.性能检测与质量保证:对每一批次的钢材进行严格的性能检测,如拉伸试验、冲击试验、硬度检测等,确保产品质量达标。
四、适用范围超高强度钢因其出色的力学性能,适用于许多重要领域,如航空航天、汽车、建筑等。
特别是在对强度和可靠性要求极高的场合,如桥梁、高层建筑、高速列车等,其优势更加明显。
五、创新要点1.成分设计创新:通过引入新型合金元素,优化成分比例,达到提高强度和韧性的目的。
例如,添加一定量的Nb和V元素,可以显著提高钢材的抗拉强度和冲击韧性。
2.热处理技术创新:采用先进的热处理工艺,如两相区淬火、等温淬火等,以实现钢材的细晶强化和析出强化。
这些工艺不仅可以提高钢材的强度,还能保持良好的韧性。
3.生产流程优化:通过引入自动化和智能化设备,优化生产流程,提高生产效率。
超高强度钢板冲压件热成形工艺

超高强度钢板冲压件热成形工艺Company number:【0089WT-8898YT-W8CCB-BUUT-202108】.生产侵侵。
超高强度钢板冲压件热成形工艺热成形技术是近年来出现的一项专门用于生产汽车高强度钢板冲压件的先进制造技术。
本文介绍了该技术的原理,讨论了材料,工艺参数.模具等热成形工艺的主要影响因素,完成了汽车典型件热成形工艺试验试制。
获得了合格的成形件。
检测结果表明。
成形件的微观组织为理想的条状马氏体,其抗拉强度.硬度等性能指标满足生产要求。
1前言在降低油耗、减少排放的诸多措施中.减轻车重的效果最为明显.车重减轻10%.可节省燃油 3%一7%,因此塑料.铝合金.高强度钢板等替代材料在车辆制造中开始使用。
其中,高强度钢板可以通过减小板厚或者截面尺寸等方式减轻零件质量.在实现车辆轻量化和提高安全性方面比其他材料有明显优势,可以同时满足实现轻量化和提高安全性的要求,因此其在汽车领域内的应用越来越广泛。
热成形技术是近年来出现的一项专门用于成形高强度钢板冲压件的新技术,该项技术以板料在红热状态下冲压成形并同时在模具内被冷却淬火为特征.可以成形强度高达1500MPa的冲压件,广泛用于车门防撞梁.前后保险杠等保安件以及A柱,B柱.C柱.中通道等车体结构件的生产。
由于具有减轻质量和提高安全性的双重优势,目前.这一技术在德国.美国等工业发达国家发展迅速.并开发出商品化的高强钢热冲压件生产线.高强钢热冲压件在车辆生产中应用也很 .一吉林大学材料学院谷诤巍姜超●机械科学研究总院先进制造技术研究中心单忠德徐虹广泛。
国内汽车业对该项技术也十分认同,并有少数几个单位从国外耗巨资引入了相关技术与生产线, 为一汽-大众等汽车制造公司的部分车型配套热冲压件,关于该项技术的研究工作也已经开始。
本文阐述了热冲压成形工艺原理,对典型冲压件的热冲压成形工艺进行试验研究。
2热冲压成形工艺原理热成形工艺原理如图 1。
首先把常温下强度为500-600MPa的高强度硼合金钢板加热蛩J880-950℃.使之均匀奥氏体化. 然后送入内部带有冷却系统的模具内冲压成形.之后保压快速冷却淬火.使奥氏体转变成马氏体.成形件因而得到强化硬化.强度大幅度提高。
热冲压成型工艺流程 预热处理 冲压成形

热冲压成型工艺流程预热处理冲压成形
热冲压成型工艺流程主要包括以下步骤:
1. 预热处理:首先,将需要加工的钢板进行预热处理。
预热温度通常控制在800℃\~950℃之间,以保证钢板的均匀加热和塑性变形。
同时,为了防止钢板在加热过程中氧化,需要采用保护气体或真空加热方式。
2. 冲压成形:将预热的钢板放入冲压模具中,通过冲压机施加压力进行成型。
冲压过程中需控制好压力、速度和时间等参数,以保证钢板的塑性变形和模具的完好无损。
同时,为了确保成品的精度和质量,需要对冲压过程中的压力、速度和时间等参数进行实时监控和调整。
在热冲压成形过程中,钢板在加热和冷却的过程中会发生相变硬化,从而提高其强度和韧性。
这种技术也被称为“冲压硬化”技术。
经过热冲压成形后的钢板,其强度可以大幅提高,例如从初始的500\~600MPa提高到1500MPa,同时零件的硬度也可以达到50HRC。
但需要注意的是,热冲压成形后的钢板伸长率会有所下降。
此外,完成冲压加工后,还需要对板材进行回火处理,以消除加工过程中的残余应力,并提高板材的韧性和可塑性。
最后,还需要对成型件进行后处理,包括去毛刺、打磨、修整等操作,以及可能的涂装或喷涂处理,以确保成品的表面质量和尺寸精度符合要求。
总的来说,热冲压成型工艺流程是一个复杂而精细的过程,需要严格控制各个环节的参数和操作,以保证最终产品的质量和性能。
22MnB5超高强钢热冲压成形工艺及试验
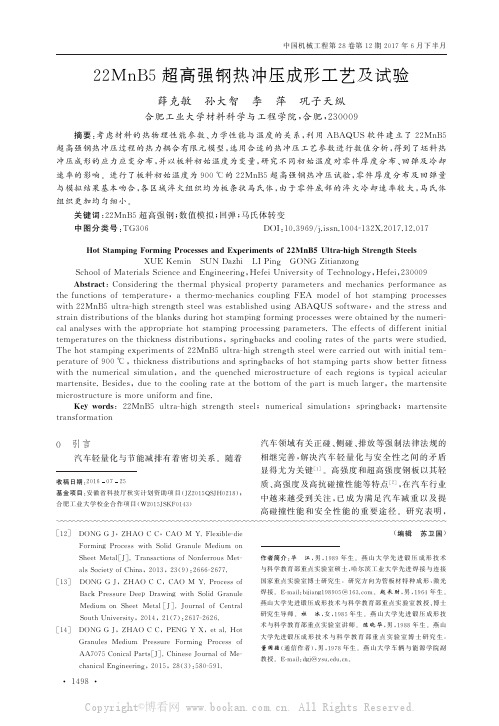
20℃ ,冲压速度为 20mm/s,保 压 12s,压 边 力 为
2.ห้องสมุดไป่ตู้
0 MPa. 有 限 元 分 析 步 骤 如 下:① 热 成 形 过 程
F
i
3 Hi
emp
e
r
a
t
u
r
et
h
e
rma
lp
r
op
e
r
t
i
e
so
f22MnB5
g.
ght
中,凹 模 保 持 不 动,压 料 板 对 板 料 施 加 压 边 力,凸
中国机械工程第 28 卷第 12 期 2017 年 6 月下半月
22MnB5 超高强钢热冲压成形工艺及试验
薛克敏 孙大智 李 萍 巩子天纵
合肥工业大学材料科学与工程学院,合肥,
230009
摘要:考 虑 材 料 的 热 物 理 性 能 参 数、力 学 性 能 与 温 度 的 关 系,利 用 ABAQUS 软 件 建 立 了 22MnB5
质、高强度及高抗碰撞性能等特点 [2],在汽车行业
中越来越受到关 注,已 成 为 满 足 汽 车 减 重 以 及 提
高碰撞性能 和 安 全 性 能 的 重 要 途 径.研 究 表 明,
[
12] DONG GJ,ZHAO C C,CAO M Y.F
t
i
onso
ft
heb
l
anksdu
r
i
ngho
ts
t
amp
i
ngf
o
rmi
ngp
r
oc
e
s
s
e
swe
r
超高强度钢板冲压件热成形工艺

超高强度钢板冲压件热成形工艺摘要:随着国民物质生活水平的提高,大家对汽车安全性的要求也越来越强烈,因此,高强度、超高强度钢板在汽车车身上的应用也越来越广泛。
然而,由于高强度、超高强度钢板在常温下强度较高,变形抗力比较大,导致利用常规冷冲压成形的方式很难成形,因此高强度、超高强度钢板热冲压成形技术就应运而生。
目前,高强度钢板热冲压成形零件已经广泛应用于国内外汽车车身的重要零件上。
关键词:热冲压成形;超高强度钢板;模具设计;冷却系统;数值模拟;一、热冲压成形工艺原理首先把常温下强度为500~600MPa的高强度硼合金钢板加热到880~950℃,使之均匀奥氏体化,然后送入内部带有冷却系统的模具内冲压成形,之后保压快速冷却淬火,使奥氏体转变成马氏体,成形件因而得到强化硬化,强度大幅度提高。
比如经过模具内的冷却淬火,冲压件强度可以达到1500MPa,强度提高了250%以上,因此该项技术又被称为“冲压硬化”技术。
实际生产中,热冲压工艺又分为两种,即直接工艺和间接工艺。
直接工艺,下料后,直接把钢板加热然后冲压成形,主要用于形状比较简单变形程度不大的工件。
对于一些形状复杂的或者拉深深度较大的工件,则需要采用间接工艺,先把下好料的钢板预变形,然后再加热实施热冲压,二、热冲压成形工艺的主要影响因素2.1材料热冲压成形工艺中采用的是一种特殊的具有自硬性的硼合金高强度钢板。
和现在的双相钢、相变诱导塑性钢、复相钢、马氏体钢等汽车高强度钢板不同,这些钢板常温下强度就很高,并且通常都采用冷冲压工艺制造零部件,成形前后零件的微观组织没有变化,强度等指标基本上保持不变。
而热成形工艺中使用的硼合金钢板是一种低碳微合金钢,添加了一定量的B元素,提高了钢板的淬火性能,成形后发生相变,强度等指标成倍提高。
另外,还添加了Ti,Cr,Mo,Cu,Ni等多种合金微量儿素,因而提高了材料的屈服强度以及其他力学性能,材料力学性能也很稳定。
典型的热冲压成形钢板22MnB5的下要成分,这种钢板常温下的强度不很高,抗拉强度仅有500700MPa,塑性、可成形性等性能也很好,而通过热成形工艺的加热、成形、冷却后,成形件被淬火,微观组织转变成马氏体,强度、硬度等指标大幅度提高,屈服强度可以达到1000MPa以上,抗拉强度达到1500MPa,硬度可以达到50HRC。
大型超高强钢热冲压成型装备关键技术及产业化应用
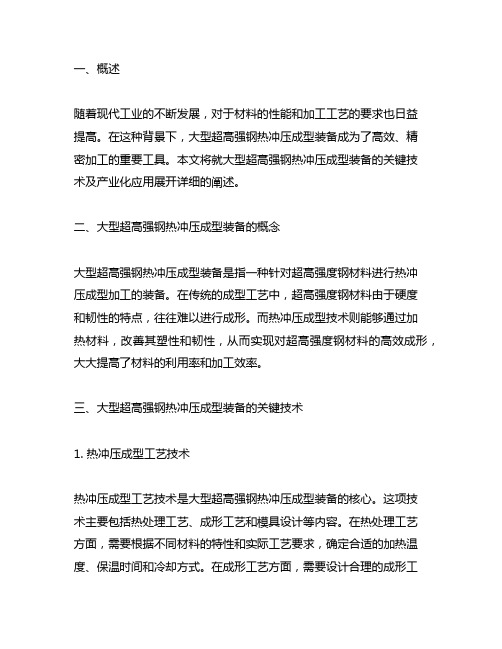
一、概述随着现代工业的不断发展,对于材料的性能和加工工艺的要求也日益提高。
在这种背景下,大型超高强钢热冲压成型装备成为了高效、精密加工的重要工具。
本文将就大型超高强钢热冲压成型装备的关键技术及产业化应用展开详细的阐述。
二、大型超高强钢热冲压成型装备的概念大型超高强钢热冲压成型装备是指一种针对超高强度钢材料进行热冲压成型加工的装备。
在传统的成型工艺中,超高强度钢材料由于硬度和韧性的特点,往往难以进行成形。
而热冲压成型技术则能够通过加热材料,改善其塑性和韧性,从而实现对超高强度钢材料的高效成形,大大提高了材料的利用率和加工效率。
三、大型超高强钢热冲压成型装备的关键技术1. 热冲压成型工艺技术热冲压成型工艺技术是大型超高强钢热冲压成型装备的核心。
这项技术主要包括热处理工艺、成形工艺和模具设计等内容。
在热处理工艺方面,需要根据不同材料的特性和实际工艺要求,确定合适的加热温度、保温时间和冷却方式。
在成形工艺方面,需要设计合理的成形工艺参数,包括压力、速度、温度等,从而确保成形过程的稳定性和高效性。
在模具设计方面,需要根据成形零件的形状和尺寸,设计合适的模具结构和加热方式,以实现对材料的精确成形。
2. 装备设计与制造技术大型超高强钢热冲压成型装备需要具备一定的加热、冷却和成形能力。
在装备设计方面,需要考虑材料的加热均匀性、成形的稳定性和模具的可靠性,从而确保整个成型过程的高效进行。
在装备制造技术方面,需要采用先进的加工工艺和材料技术,确保装备具备高强度、高稳定性和高耐用性,能够满足超高强度钢材料的加工需求。
3. 自动化控制技术自动化控制技术是大型超高强钢热冲压成型装备的重要保障。
通过自动化控制系统,可以实现对热处理、成形和模具等环节的精准控制,确保成型过程的稳定性和可靠性。
自动化控制系统还可以实现对装备运行状态的实时监测和故障诊断,提高了装备的运行效率和安全性。
四、大型超高强钢热冲压成型装备的产业化应用大型超高强钢热冲压成型装备的产业化应用已经在汽车、航空航天、轨道交通等领域得到广泛应用。
超高强度钢板的热冲压成形模具设计及优化方法

超高强度钢板的热冲压成形模具设计及优化方法摘要:热冲压成形技术,属于高强度的冲压技术一种制作方式,被广泛应用至超过强度类型钢板生产制造当中。
为能够更好地满足此类钢板的生产制造需求,注重对热冲压成形模具合理设计及其优化较为重要。
故本文主要探讨超高强度钢板热冲压成形模具相关设计和优化方法,仅供业内相关人士参考。
关键词:钢板;超高强度;热冲压;冲压成形;模具设计;优化方法前言现阶段,针对高强度类型钢板产品实际生产制造当中,往往需用到热冲压成形技术,可确保钢板生产制造更具精准性,为产品质量提供保证。
因而,对超高强度钢板热冲压成形模具相关设计和优化方法开展综合分析较为必要。
1、关于热冲压成形工艺概述热冲压成形工艺,属于零件的一种加工方式,坯料加热到特定温度后,借助冲压装置处于成形模具当中实施冲压与淬火同步处理,获取所需外形、金属类型材料相变的材料成型一种技术工艺或者方法。
2、模具设计和优化方法2.1设计分析针对超高强度钢板实际生产制造当中热冲压成形模具总体设计,其所涉及的内容相对较多,对凹凸模型实施角设计往往比较重要,受拉伸件将决定着部件实际大小,且该拉伸件显著影响着热冲压的整个拉裂过程。
现场实施锻造期间,对凹凸模板当中可预留好间隙,可促使板料与模具的关系得以增强,确保二者实现紧密连接,模具间隙如果有问题出现,则必然影响到模具冷却及其形成;设计者还需结合各项参数要求,对拉伸筋及延边圈等零件实施合理设计,确保各零件更具匹配度[1]。
同时,热冲压模具成形,其对于超高强度钢板方面有着高要求。
热冲压方面工艺制造实施过程,板料均需得到高强度的相应加热处理,确保其能够结晶。
再落实冲压成形方面的设计操作,维持一定静置时间,则零件尺寸、形状基本稳定。
而这一过程,往往对板料要求会相对较高,为避免材料自身强度下降,则加热过程需注重淬火处理,以此获取超过强度相应钢构件。
工艺成形整个过程,因热冲压、淬火应当同步落实,所以,该钢板务必经由热冲压整个热循环过程。
高强钢热冲压成型工艺流程 预热处理 冲压成形 淬火
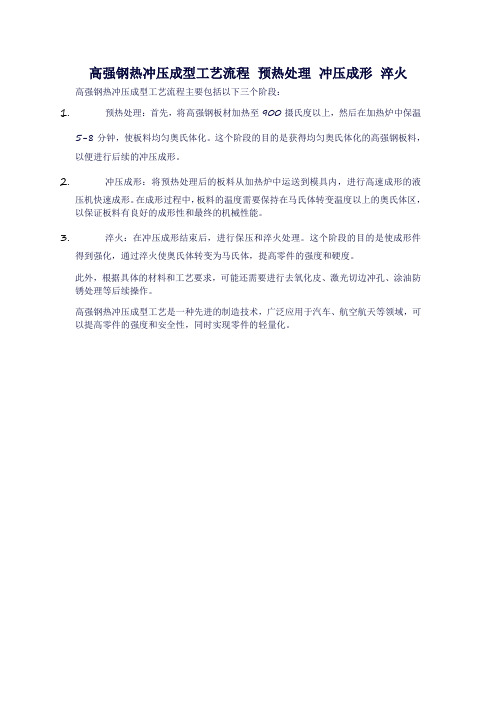
高强钢热冲压成型工艺流程预热处理冲压成形淬火高强钢热冲压成型工艺流程主要包括以下三个阶段:
1.预热处理:首先,将高强钢板材加热至900摄氏度以上,然后在加热炉中保温
5-8分钟,使板料均匀奥氏体化。
这个阶段的目的是获得均匀奥氏体化的高强钢板料,以便进行后续的冲压成形。
2.冲压成形:将预热处理后的板料从加热炉中运送到模具内,进行高速成形的液
压机快速成形。
在成形过程中,板料的温度需要保持在马氏体转变温度以上的奥氏体区,以保证板料有良好的成形性和最终的机械性能。
3.淬火:在冲压成形结束后,进行保压和淬火处理。
这个阶段的目的是使成形件
得到强化,通过淬火使奥氏体转变为马氏体,提高零件的强度和硬度。
此外,根据具体的材料和工艺要求,可能还需要进行去氧化皮、激光切边冲孔、涂油防锈处理等后续操作。
高强钢热冲压成型工艺是一种先进的制造技术,广泛应用于汽车、航空航天等领域,可以提高零件的强度和安全性,同时实现零件的轻量化。
- 1、下载文档前请自行甄别文档内容的完整性,平台不提供额外的编辑、内容补充、找答案等附加服务。
- 2、"仅部分预览"的文档,不可在线预览部分如存在完整性等问题,可反馈申请退款(可完整预览的文档不适用该条件!)。
- 3、如文档侵犯您的权益,请联系客服反馈,我们会尽快为您处理(人工客服工作时间:9:00-18:30)。
矿产资源开发利用方案编写内容要求及审查大纲
矿产资源开发利用方案编写内容要求及《矿产资源开发利用方案》审查大纲一、概述
㈠矿区位置、隶属关系和企业性质。
如为改扩建矿山, 应说明矿山现状、
特点及存在的主要问题。
㈡编制依据
(1简述项目前期工作进展情况及与有关方面对项目的意向性协议情况。
(2 列出开发利用方案编制所依据的主要基础性资料的名称。
如经储量管理部门认定的矿区地质勘探报告、选矿试验报告、加工利用试验报告、工程地质初评资料、矿区水文资料和供水资料等。
对改、扩建矿山应有生产实际资料, 如矿山总平面现状图、矿床开拓系统图、采场现状图和主要采选设备清单等。
二、矿产品需求现状和预测
㈠该矿产在国内需求情况和市场供应情况
1、矿产品现状及加工利用趋向。
2、国内近、远期的需求量及主要销向预测。
㈡产品价格分析
1、国内矿产品价格现状。
2、矿产品价格稳定性及变化趋势。
三、矿产资源概况
㈠矿区总体概况
1、矿区总体规划情况。
2、矿区矿产资源概况。
3、该设计与矿区总体开发的关系。
㈡该设计项目的资源概况
1、矿床地质及构造特征。
2、矿床开采技术条件及水文地质条件。