焙烧温度对异辛醇生成异辛酸性能的影响
焙烧温度对Fe/HZSM-5催化剂催化乙醇制备低碳烯烃性能的影响

催化 性能 有显 著 的影 响 , 烧 后 分 子 筛 的 酸 性 、 焙 孔 道结 构口删 以及骨 架 中铝 的状 态[ 等 均 发 生 显 1 著 的变化 。本课 题 以不 同温 度焙 烧 的 F / S 5 eHZ M一 为催化 剂 , 考察 焙 烧 温 度对 F / S 5催 化 剂催 eHZ M一
附 和 H 一 序 升 温 还 原 等 方 法 对 催 化 剂 的 物 化 性 能 进 行 表 征 , 微 型 固 定 床 反 应 器 上 考 察 焙 烧 温 度 对 程 在 F / S 5 化 剂 催 化 乙 醇 制 备 低 碳 烯 烃 性 能 的影 响 。结 果 表 明 : 烧 温 度 不 同 , 化 剂 的 表 面 酸 量 、 强 度 eHZ M一催 焙 催 酸 不 同 , e 催 化 剂 表 面 的分 散 度 不 同 ; 宜 的 焙 烧 温 度 能 够 显 著 提 高 催 化 剂 的 低 碳 烯 烃 选 择 性 、 制 芳 构 化 和 F 在 适 抑
李 娜 ,柳 彦 从 ,陆 江 银
( 疆 大 学 化 学 化 工 学 院 石 油 天 然 气 精 细 化 工 教 育 部 重 点 实验 室 ,乌鲁 木 齐 8 04 ) 新 3 0 6
摘 要 : 用 浸 渍 法 制 备 不 同 温 度 焙 烧 的 r/ S 5系 列 催 化 剂 , 用 x射 线 衍 射 、 采 eHZ M一 并 NH。程 序 升 温 脱 一
用 于石 油化 工领 域 。用 改 性 的 分 子 筛催 化 生 物 乙 醇 制备 低碳 烯烃 是 传 统石 油 裂 解 的 一条 可 替 代 路
线 , 为 当前 研究 的热点口 ] 成 。
程序 为 : 室温 升 至 1 0℃ 恒 温 0 5h, 升 至 指 定 2 . 再
异十八醇熔点

异十八醇熔点1. 介绍异十八醇(异辛醇,英文名:Isooctanol)是一种有机化合物,化学式为C8H18O,属于醇类。
它是一种无色液体,具有特殊的气味。
异十八醇在工业上广泛应用于溶剂、润滑剂、乳化剂等方面。
本文将重点讨论异十八醇的熔点,包括其定义、影响因素以及应用领域。
2. 熔点的定义熔点是指物质由固态转变为液态的温度。
对于异十八醇来说,熔点是指当它的固态结构被加热到一定温度时,开始转变为液态的温度。
3. 异十八醇的熔点异十八醇的熔点在常温下是非常低的,约为-80°C。
这意味着在室温下,异十八醇是以液态存在的。
由于其低熔点,异十八醇在常温下易于流动,使其广泛应用于溶剂等领域。
4. 影响异十八醇熔点的因素异十八醇的熔点受多种因素的影响,以下是其中一些重要的因素:4.1 分子结构分子结构是影响异十八醇熔点的关键因素之一。
分子结构中的官能团和取代基团会影响分子之间的相互作用力,从而影响熔点。
例如,分子中的羟基(-OH)会形成氢键,增加分子之间的相互作用力,使熔点升高。
4.2 分子量分子量也是影响异十八醇熔点的因素之一。
一般来说,分子量越大,分子间的相互作用力越强,熔点也相应升高。
4.3 杂质异十八醇中的杂质也会对熔点产生影响。
杂质的存在可能改变分子之间的相互作用力,导致熔点发生变化。
5. 异十八醇的应用由于其低熔点和溶解性等特点,异十八醇在多个领域有广泛的应用:5.1 溶剂异十八醇作为一种良好的溶剂,广泛应用于化学合成、油墨制造和涂料等工业领域。
其低熔点使其在常温下就能以液态存在,并且能够溶解许多有机物。
5.2 润滑剂由于其润滑性能,异十八醇被用作润滑剂的成分之一。
它可以减少摩擦和磨损,提高机械设备的效率和寿命。
5.3 乳化剂异十八醇也被广泛应用于乳化剂的制造中。
它能够促进不相溶物质之间的混合,使其形成稳定的乳液。
6. 总结异十八醇是一种常用的有机化合物,其熔点较低,常温下为液态。
熔点受分子结构、分子量和杂质等因素的影响。
异辛酸钾工艺

异辛酸钾工艺异辛酸钾工艺是一种用于生产异辛酸钾的工艺方法。
异辛酸钾是一种重要的有机化工产品,广泛应用于塑料助剂、制革工业、油墨和涂料等领域。
本文将介绍异辛酸钾工艺的原理和主要步骤。
异辛酸钾工艺的原料主要是异戊二烯和盐酸。
生产过程中,首先将异戊二烯与盐酸进行反应,生成氯化异辛烷。
然后,将氯化异辛烷与氢氧化钾反应,生成异辛酸钾。
在异辛酸钾工艺中,反应条件的控制非常重要。
首先是反应温度的控制,一般在160-180摄氏度之间。
反应温度过高会导致副反应的发生,产生杂质,降低产品的纯度。
反应温度过低则会降低反应速率,影响生产效率。
其次是反应时间的控制,一般为2-4小时。
过短的反应时间会导致反应不完全,影响产品的质量,而过长的反应时间则会增加生产成本。
异辛酸钾工艺中还需要注意反应物的配比。
异戊二烯和盐酸的摩尔比应该控制在1:2左右,过高或过低都会影响反应的进行。
此外,还需要控制氢氧化钾的用量,过量的氢氧化钾会导致产物中存在未反应的氢氧化钾,影响产品的质量。
在反应完成后,需要对产物进行后处理。
首先是对反应液进行中和,通常使用浓盐酸进行中和。
然后,通过蒸馏和结晶等工艺步骤对产物进行提纯。
最后,对提纯后的异辛酸钾进行干燥,得到最终的产品。
异辛酸钾工艺的优点是反应条件温和,反应时间短,生产效率高。
同时,该工艺能够高效利用原料,减少废物产生,具有较好的经济效益和环境效益。
然而,异辛酸钾工艺也存在一些问题。
首先是原料的纯度要求较高,如果原料中含有杂质,会影响产品的质量。
其次是反应过程中需要控制好反应条件,否则容易导致副反应的发生,影响产品的纯度。
此外,异辛酸钾是一种易腐蚀的化学品,对设备要求较高,需要选用耐腐蚀材料进行生产。
异辛酸钾工艺是一种用于生产异辛酸钾的重要方法。
通过控制好反应条件和反应物的配比,可以高效、经济地生产出高纯度的异辛酸钾产品。
在实际应用中,需要严格按照工艺要求进行操作,并加强设备的维护和管理,以确保产品的质量和生产的安全。
异辛醇聚氧乙烯醚磷酸酯的合成与应用

2 结果与讨论
液校正仪器 , 洗净电极 。称取012 g酸性磷酸酯于
100 mL烧杯中 , 以 30 mL 甲醇水溶液 ( 质量分数为 211 脂肪醇的选择
50 %) 溶解试样 ,加 3~5 滴甲基红指示剂 ,放入电极
脂肪醇的选择对合成磷酸酯的耐碱渗透性有很
及磁 力 搅 拌 棒 , 开 动 磁 力 搅 拌 器 , 用 011 molΠL 的 KOH 标准溶液滴定测量 ,并记录 KOH 标准溶液消 耗数及相应的 pH 值 。在 pH 值为 515 ~ 615 时有
1 实验部分
111 仪器与原料
ZD22 型电位滴定计 ;J TY210 电子天平 ;Datacolor 测色仪 ;JB902S 数字显示转速电动搅拌机 ;WMZK201 温度指示控制仪 ;秒表 ;标准帆布 。
C8 H17 ( EO) 4OH ; NaOH ; P2O5 。以上原料均为工 业品 。
渗透剂在纺织加工的许多工序中用途十分广 泛 。棉纺织品的前处理多数是湿加工 ,要使处理液 能均匀 、快速地分布或作用于织物内部 ,渗透剂是必 不可少的助剂 。前处理加工大多是在强碱浴中进 行 ,这就要求所用的渗透剂在强碱浴中仍能保持良 好的润湿渗透性 。要达到既能耐强碱 (200 gΠL) 又能 保持高效渗透的性能 ,普通的渗透剂 J FC 已不能满 足要求 ,必须寻求其他的耐强碱渗透剂 。
penetrative performance of phosphate
n (C8 H17 ( EO) 4OH) ∶n ( P2O5) ω(单酯) Πω(双酯)
2∶1
1152
渗透时间Πs 4
3∶1
1123
6
4∶1
0187
15
注 :异辛醇聚氧乙烯醚磷酸酯的质量浓度为 10 gΠL 。
催化剂对异氰酸酯反应活性的影响
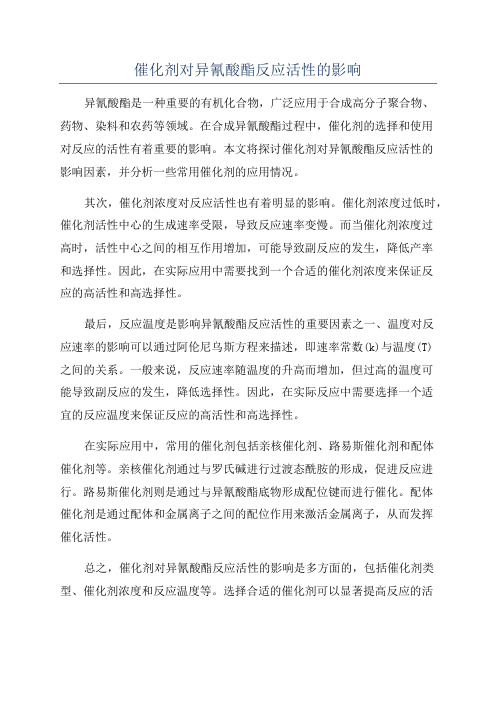
催化剂对异氰酸酯反应活性的影响异氰酸酯是一种重要的有机化合物,广泛应用于合成高分子聚合物、药物、染料和农药等领域。
在合成异氰酸酯过程中,催化剂的选择和使用对反应的活性有着重要的影响。
本文将探讨催化剂对异氰酸酯反应活性的影响因素,并分析一些常用催化剂的应用情况。
其次,催化剂浓度对反应活性也有着明显的影响。
催化剂浓度过低时,催化剂活性中心的生成速率受限,导致反应速率变慢。
而当催化剂浓度过高时,活性中心之间的相互作用增加,可能导致副反应的发生,降低产率和选择性。
因此,在实际应用中需要找到一个合适的催化剂浓度来保证反应的高活性和高选择性。
最后,反应温度是影响异氰酸酯反应活性的重要因素之一、温度对反应速率的影响可以通过阿伦尼乌斯方程来描述,即速率常数(k)与温度(T)之间的关系。
一般来说,反应速率随温度的升高而增加,但过高的温度可能导致副反应的发生,降低选择性。
因此,在实际反应中需要选择一个适宜的反应温度来保证反应的高活性和高选择性。
在实际应用中,常用的催化剂包括亲核催化剂、路易斯催化剂和配体催化剂等。
亲核催化剂通过与罗氏碱进行过渡态酰胺的形成,促进反应进行。
路易斯催化剂则是通过与异氰酸酯底物形成配位键而进行催化。
配体催化剂是通过配体和金属离子之间的配位作用来激活金属离子,从而发挥催化活性。
总之,催化剂对异氰酸酯反应活性的影响是多方面的,包括催化剂类型、催化剂浓度和反应温度等。
选择合适的催化剂可以显著提高反应的活性和选择性,从而实现高产率、高收率的合成目标。
对催化剂的研究和开发将进一步推动异氰酸酯反应的应用和发展。
焙烧温度及焙烧时间对异丁烯部分氧化合成甲基丙烯醛催化剂性能的影响

文章编号:100123555(2009)0620551207收稿日期:2009206202;修回日期:2009207209.作者简介:赵小岐,男,生于1980年,工程硕士,E 2mail:zhqky@hot m ail .com.焙烧温度及焙烧时间对异丁烯部分氧化合成甲基丙烯醛催化剂性能的影响赵小岐,罗 鸽,温 新,庄 岩,褚小东,邵敬铭(上海华谊丙烯酸有限公司研究所,上海200137)摘要:采用沉淀法制备了Mo 2B i 2Co 2Fe 2Cs 复合氧化物催化剂,并用于异丁烯部分氧化制备甲基丙烯醛反应,结合H 22TPR 、XRD 、BET 和TE M 表征,考察了焙烧温度以及焙烧时间对催化剂物理化学性质及催化性能的影响.研究结果表明,随焙烧温度升高,催化剂物相结构没有明显的改变,而催化剂颗粒则逐渐增大,氧化能力降低,且组分之间的协同作用减弱;当焙烧温度提高到540℃时,催化剂局部颗粒已出现烧结.催化剂活性随焙烧温度提高逐渐下降,而甲基丙烯醛选择性则在焙烧温度为520℃时达到最大值,焙烧温度对催化剂性能的影响可能因催化剂表面活性位密度不同所致.合适的焙烧温度为520℃,焙烧时间为5h,此时异丁烯转化率为98.4%时,MAL 选择性可达到87.2%,具有较好的反应效果.关键词:焙烧温度;焙烧时间;异丁烯;甲基丙烯醛中图分类号:O643.32文献标识码:A 甲基丙烯酸甲酯(MMA )是一种重要的有机化工中间体,可用于生产有机玻璃、塑料改性剂、高级环保涂料及粘结剂等,广泛地应用于国防、建筑和精细化工等领域[1].传统的MMA 生产方法为丙酮氰醇法,此法使用剧毒氢氰酸为原料,在生产过程中使用高腐蚀性硫酸和烧碱,且原子利用率低,原料成本高,因而各国均在探索更为绿色经济的MMA 合成路线[2,3].由异丁烯氧化法制备MMA 的工艺,因原料来源广泛、原子利用率高、环境污染小等优点,目前已备受关注[4,5].该工艺一般采用三步法完成:异丁烯在催化剂作用下部分氧化生成甲基丙烯醛(MAL ),然后MAL 在催化剂作用下氧化生成甲基丙烯酸(MAA ),最后在强酸催化剂存在下使MAA 酯化生成MMA.作为整个工艺的第一步反应,异丁烯部分氧化制备MAL 反应结果对于整个工艺路线的收率及产物纯度都有重要影响,而反应中高效催化剂的开发更是整个工艺路线的核心技术之一.目前用于这一步反应的催化剂多为钼铋[6,7]、钼锑[8,9]以及钼钒碲[10]等金属复合氧化物,且主要以钼铋体系为主,并添加铁、钴、碱金属等助剂,以提高催化剂的选择性和稳定性[11].另外,通过合理控制焙烧条件,特别是焙烧温度及焙烧时间,对复合氧化物催化剂结构及性能也会有很大的影响,但却鲜有文献对此进行系统研究.本文即结合H 22TPR 、XRD 、BET 、TE M 等多种表征手段,系统研究了催化剂焙烧温度及焙烧时间对催化剂结构及其用于异丁烯氧化制备MAL 反应性能的影响,以期获得高性能的催化剂,并对焙烧温度与焙烧时间对催化剂性能改变的原因进行了探讨.1实验部分1.1实验原料钼酸铵、硝酸铋、硝酸铯,均为分析纯,国药集团化学试剂公司;硝酸钴、硝酸铁,工业一级,太原欣力化学品有限公司.1.2催化剂制备按照Mo 10Co 5.0B i 2.5Fe 1.0Cs 0.5化学计量比,将一定量的钼酸铵溶于60℃水中,待其完全溶解后,依次加入适量的硝酸钴、硝酸铋、硝酸铁以及硝酸铯,并将温度升至80℃;之后在机械搅拌下加入氨水中和,调节pH 值为6,继续搅拌30m in 后,将所得物质移至170℃的烘箱中干燥过夜,之后经压片成形、研磨、筛分,取0.9~2.0mm 的颗粒22mL 第23卷第6期分 子 催 化Vol .23,No .6 2009年12月JOURNAL OF MOLECULAR C AT ALYSI S (CH I N A )Dec . 2009 装填于石英管中,在一定条件下焙烧即得催化剂.1.3催化剂评价装置催化剂性能评价在固定床连续反应装置中进行,反应器内径19mm ,装填催化剂15mL.原料叔丁醇(含量85wt .%)与空气、氮气混合,经预热器加热后进入反应器,加热后的叔丁醇气体接触到催化剂迅速脱水生成异丁烯[12,13],异丁烯与空气、氮气的混合气体流经催化剂床层进行反应,反应均在常压下进行,异丁烯:氧气:氮气:水=1:2:12:1.7(摩尔比),混合气体空速1350h 21,根据催化剂性能,调整合适的盐浴温度进行反应.1.4实验结果分析反应后产物通过在线气相色谱采样分析,根据分析结果评价催化剂性能.色谱为岛津公司生产的带热导和氢火焰双检测器的GC 214C 色谱仪,气相产物中的CO 和CO 2用Parapak Q 柱分析,液相产物中的异丁烯、MAL 、MAA 等用DBW ax 毛细管柱分析.进样箱250℃,检测器300℃,柱箱初温60℃,保持6m in,10℃/m in 的升温速率升到200℃,保持5m in .由于叔丁醇进入反应器会迅速脱水生成异丁烯,转化率与选择性都接近100%,因此整个计算过程都以异丁烯为基准,计算异丁烯转化率(X I B ),MAL 、MAA 选择性(S MAL,MAA )和CO 、CO 2选择性(S CO ,CO 2)的公式如下:X I B =(M 0,I B -M I B )/M 0,I B ×100%S MAL,MAA =M MAL,MAA /(X I B ×M 0,I B )×100%S CO,CO 2=M CO ,CO 2/(4×X I B ×M 0,I B )×100%其中,M 0,I B 和M I B 分别为初始时和未反应的异丁烯摩尔量,M MAL,MAA 为生成MAL 或MAA 的摩尔量,M CO ,CO 2为生成CO 或CO 2的摩尔量.1.5催化剂表征H 22TPR 采用天津先权公司生产的TP 250002II多用吸附仪测定.先通氮气将样品在200℃下处理2h,降至室温;通入流量为8mL /m in 的含10%H 2的N 2、H 2混合气,程序升温并记录还原曲线.温度范围:室温约800℃,升温速率10℃/m in .X 2射线粉末衍射(XRD )表征在德国B ruker AXS D82Advance 型粉末X 2射线衍射仪上进行.X 光源用G oebel 镜将发散X 光束汇聚为平行光以减少表面粗糙的影响,采用波长λ=1.5418!的Cu Kα线,石墨单色器,管电压为40k V,管电流为40mA.比表面积及孔结构采用M icr omeritics 公司的Tristar AS AP 2020型自动物理吸附仪测定,先测定样品在液氮温度2196℃下对N 2的物理吸附脱附等温线,再由BET 方程计算样品的比表面积(S B ET ).透射电镜(TE M )表征采用JE OL 2011型透射电子显微镜,加速电压为200k V.测试前样品经仔细研磨,并在乙醇中超声处理5m in,提拉挂网.待乙醇干后,将样品送入分析腔中测量.2结果与讨论2.1不同温度焙烧催化剂的H 22TPR 表征先对不同温度焙烧的催化剂进行了H 22TPR 表征,结果如图1所示.由图1可见,不同温度焙烧的催化剂均在370~750℃范围内有一系列的还原峰,图1不同温度焙烧催化剂的H 22TPR 表征Fig .1H 22TPR p r ofiles of catalysts calcinated at (1)500℃;(2)520℃;(3)540℃res pectively500℃焙烧的催化剂的第一个还原峰的起始位置为370℃,低于其它温度焙烧的催化剂,表明此催化剂的氧化能力最高(见表2催化剂的评价结果);500、520及540℃焙烧的催化剂的第一还原峰的峰高位置分别为512、557和575℃,说明焙烧温度越高,第一还原峰的位置依次向高温移动,表明了催化剂的氧化能力随着焙烧温度的提高而减弱.之后是多个还原峰叠加在一起,不能简单地归属为单个氧化物的还原峰,是由于催化剂组分之间产生协同作用并导致了H 2溢流效应的结果[14,15],并且温度越高这种协同作用越弱.H 22TPR 表明,焙烧温度是影响催化剂性能的一个重要因素,在不同的温度下焙烧,复合氧化物之间发生不同的协同作用,这一点与杂多化合物的协同作用相类似[16].255 分 子 催 化 第23卷 2.2焙烧温度对催化剂形貌的影响为了解焙烧温度对催化剂形貌的影响,对不同焙烧温度下的催化剂进行了TE M 表征,如图2所示.可以看到,焙烧后的颗粒呈现致密结构,低温500℃焙烧后的催化剂(图2(a ))颗粒粒径相对较小,粒径分布较为均匀,平均粒径为190n m 左右(见表1);经520℃焙烧后催化剂(图2(b ))颗粒粒径略有增大,平均粒径为210nm 左右;继续提高焙烧温度至540℃,焙烧后的催化剂(图2(c ))颗粒明显增大,且粒径分布不均匀,有的粒径小于200nm ,而有的粒径甚至达到1000nm 以上(图2(d )),说明局部催化剂颗粒已烧结.另外,不同温度焙烧的催化剂S AE D 照片均呈现出明锐的衍射点,典型图片如图2(d )右上角所示,说明经焙烧后催化剂颗粒均具有良好的晶态结构.图2不同温度焙烧后催化剂的TE M 照片Fig .2TE M i m ages of catalysts after different calcinati on te mperature(a )500℃;(b )520℃;(c )540℃;(d )540℃partly 表1给出了不同焙烧温度得到的催化剂的比表面积及孔结构情况.由上述的TE M 表征可看出,催化剂的孔道主要来自于颗粒堆积形成的二次孔,因而孔径随焙烧温度提高几乎没有变化.另外,催化剂的比表面积均较小,低于2m 2/g .随焙烧温度的提高,比表面积呈下降趋势:焙烧温度为500℃时,催化剂比表面积为1.9m 2/g;而当焙烧温度为540℃时,催化剂比表面积降至0.6m 2/g .因催化剂孔径几乎没有变化,因而比表面下降说明催化剂颗粒变大,这也与上述的TE M 表征结果相一致.355第6期 赵小岐等:焙烧温度及焙烧时间对异丁烯部分氧化合成甲基丙烯醛催化剂性能的影响表1不同温度焙烧的催化剂BET 结果Table1Surface A rea,pore volu me and pore dia meter of catalystsCalcinati on Te mperature ℃Surface A rea m 2/gPore Volu me c m 3/gPore D iameter n m5001.90.0036.95101.80.0036.85201.60.0026.85301.00.0027.35400.60.0016.52.3焙烧温度对催化剂物相结构的影响为了解焙烧温度对催化剂物相结构有无影响,对不同焙烧温度下的催化剂进行了XRD 表征,如图3所示.可以看到,经不同温度焙烧后的催化剂XRD 图谱中衍射峰数目及位置没有明显变化,图谱图3不同温度焙烧后催化剂的XRD 图Fig .3X 2ray diffracti on patterns of catalysts after differentcalcinati on temperature中除对应Co 6Mo 12B i 1.5O x 晶相的衍射峰外,主要有对应Co MoO 4、B i 2Mo 3O 12及B i 6MoO 12的衍射峰,说明在500℃~540℃焙烧温度范围内,催化剂中并未有新的物相生成.需要说明的是,虽然催化剂组成中有组分Fe,在文献[17]中也观察到有Fe MoO 4晶相的生成,但本文XRD 图谱中并未有对应Fe MoO 4晶相的衍射峰.可能一方面因Fe 含量较低,Fe MoO 4晶相含量较少;另一方面,晶相Fe MoO 4与Co MoO 4的衍射峰位置非常相近,分别为2θ=26.4o 、2θ=26.5o,因而Fe MO 4的衍射峰被Co MoO 4覆盖所致.随焙烧温度升高,各衍射峰逐渐变得尖锐;上述的S AE D 图片结果表明,催化剂颗粒均具有良好的晶态结构,因而衍射峰强度的变化说明催化剂粒径逐渐增大,这也与TE M 及BET 表征结果相一致.2.4焙烧温度对催化剂性能的影响固定焙烧时的空气流速及焙烧时间,考察了不同温度焙烧后催化剂的性能,结果见表2.众所周知,烯烃选择性氧化反应是强放热反应,如表2所示,反应温差一般都在30℃以上,有时甚至高达43℃;并且不同催化剂因性能不同,反应温差有很大差别.所以反应时即使将反应控制温度保持一致,但因催化剂性能不同,导致实际温差会有较大差异,由此必然也会对反应结果造成很大影响.为了判断出不同催化剂的真实反应效果,我们根据反应转化率达到98.0%时,反应所需要的温度以及此时目标产物MAL 选择性及几种主要副产物MAA 、CO 、CO 2选择性来比较催化剂性能的好坏.当催化剂焙烧温度为500℃时,即使在347℃的低温下反应,转化率仍高达99.3%,并且此时剧烈放热,温升高达43℃;为便于与其它催化剂比较,将转化率降至98.0%左右,必须将反应温度降至335℃,说明该催化剂活性较高.随着催化剂焙烧温度提高至510℃,催化剂活性随之降低,为达到98.0%左右的转化率,需要将反应温度提高至360℃.并且随着催化剂焙烧温度进一步增大,达到98.0%左右转化率时需要的反应温度也逐步上升,表明催化剂活性随焙烧温度提高呈下降趋势.当焙烧温度提高到540℃时,催化剂活性已大大下降,即使将反应温度提高到420℃,转化率仍只有96.2%.从产物分布来看,除目的产物MAL 外,副产物主要有CO 、CO 2、MAA ,另外,还有少量的乙醛、丙酮、丙烯醛等.目前普遍认为,MAA 由MAL 进一步氧化生成,CO 、CO 2则为原料深度氧化产生[18,19].当焙烧温度为500℃、转化率为98.1%时,MAL 选择性较低,仅82.8%;产物中完全氧化产物即CO 与CO 2含量较高,总选择性达到9.2%,并且此时MAL 进一步氧化的产物MAA 含量也较高,达到2.1%.随着焙烧温度提高,MAL 选择性呈增大趋势,而副产物CO 与CO 2总选择性则逐渐455 分 子 催 化 第23卷 降低.当焙烧温度提高至520℃、转化率为98.4%时,MAL 选择性达到最大值,为87.2%,而CO 与CO 2总选择性CO x 则降至最低,为5.7%;随着焙烧温度继续增大,MAL 选择性又逐渐下降,而副产物CO x 选择性又逐渐增大,当焙烧温度为540℃时,即使在96%的转化率下,MAL 选择性已降为84.6%,副产物CO x 选择性又升至6.2%.表2焙烧温度对催化剂活性及选择性的影响Table 2Effect of calcinati on te mperature on the activity and selectivityCalcinati on Te mperature (℃)Reacti on Te mperature (℃)Hot Te mperature (℃)X I B (%)S MAL (%)S MAA (%)S C O (%)S C O2(%)S COx 3(%)50034739099.379.72.02.210.512.733537898.182.82.12.17.19.251036040398.385.91.81.94.86.752037540698.487.21.22.23.55.753039543398.385.01.02.43.96.354042044896.284.61.12.43.86.2 Note:3t otal selectivity of C O and C O 2,the same bel ow . 由上述的XRD 表征结果可看出,随焙烧温度的提高,催化剂中并没有新的物相出现,催化剂晶相结构也未有明显变化,因而催化剂性能随焙烧温度的改变与晶相结构的变化无关.由上述的H 22TPR 、TE M 、BET 及XRD 表征可看出,随焙烧温度提高,催化剂颗粒粒径逐渐增大,氧化能力降低、组分之间的协同作用也降低,并且比表面积也呈下降趋势,特别是当焙烧温度提高到540℃时,催化剂部分颗粒出现烧结,催化剂比表面积降至1.0m 2/g 以下.由此可以推测,当焙烧温度较低(如500℃)时,因催化剂粒径较小,在相同催化剂组成时暴露出的活性位数量较多,也即催化剂表面活性位密度较大,此时催化剂必然具有较高的活性,因而只需在低温335℃下反应,反应转化率即可达到98.1%.但此时,因催化剂表面活性位密度较大,反应后的产物MAL 很容易被临近的表面活性晶格氧继续氧化,生成MAA 甚至完全氧化产物CO 以及CO 2,因而副产物MAA 及CO x 选择性较高.随着焙烧温度的提高,催化剂颗粒逐渐增大,相同催化剂组成时暴露出的活性位数量也相应降低,因而催化剂活性呈现下降趋势,达到相同转化率98.0%左右,所需要的反应温度逐渐上升;当催化剂焙烧温度为520℃时,需要的反应温度已升至375℃.并且随着活性位数量的降低,表面活性位密度下降,目的产物MAL 进一步氧化的几率也减少,因而MAL 选择性逐渐增大,而进一步氧化的产物MAA 及完全氧化产物CO x 选择性则降低.但是随着催化剂焙烧温度的进一步提高,一方面催化剂颗粒继续长大,另一方面,由TE M 表征可看出,局部一些催化剂颗粒已烧结,使得催化剂表面活性位数量大大下降,需要较高的反应温度才能达到一定的转化率;如焙烧温度为540℃时,反应温度即使提高到420℃,反应转化率仍只能达到96.2%.并且此时因反应温度过高,原料异丁烯易于发生水合反应,产物中乙醛、丙酮等副产物含量有显著增加.所以由上述可看出,在反应条件固定的情况下,催化剂表面活性位密度只有在一定范围内才能达到较高的MAL 选择性,也即活性位需要有一定的分离,这也与文献[21,21]中的结论相一致.通过控制合适的焙烧温度,可以调整催化剂晶体颗粒的大小,从而获得合适的活性位分离,得到适宜的表面活性位密度,使催化剂具有较佳的反应性能.研究结果表明,合适的焙烧温度为520℃左右.2.5焙烧时间对催化剂性能的影响为进一步提高催化剂的反应性能,固定焙烧温度为520℃,进一步考察了焙烧时间对催化剂性能的影响,结果列于表3中. 随焙烧时间的延长,催化剂活性呈下降趋势.当焙烧时间为3h 时,反应温度只需为360℃即可使反应转化率达到98.0%;当焙烧时间延长至6h 时,需要将反应温度提高到380℃,才能使反应转555第6期 赵小岐等:焙烧温度及焙烧时间对异丁烯部分氧化合成甲基丙烯醛催化剂性能的影响化率达到97.5%;进一步延长焙烧时间为7h,需要将反应温度提高到390℃,才能使转化率达到97.6%.MAL选择性随焙烧时间的变化呈现出先增大后减小的趋势,当焙烧时间为5h时,MAL选择性最好,为87.2%.所以当焙烧温度为520℃时,合适的焙烧时间为5h.表3焙烧时间对催化剂性能的影响Table3Effect of Calcinati on Ti m e(h)on the activity and selectivityCalcinati on Te mperature(℃)Reacti onTe mperature(℃)HotTe mperature(℃)X I B(%)S MAL(%)S MAA(%)S C O(%)S C O2(%)S C Ox(%)336039498.083.42.12.45.57.9 437040398.485.71.82.04.56.5 537540698.487.21.22.23.55.7 638041297.586.51.42.53.45.9 739042197.685.11.42.63.76.33结 论3.1焙烧温度对催化剂物相结构没有明显影响,但对催化剂粒径、氧化能力及比表面积影响较大.随着焙烧温度的提高,催化剂晶粒长大,氧化能力降低,比表面积下降;当焙烧温度达到540℃时,局部催化剂颗粒已烧结.3.2焙烧温度对催化剂性能影响较大.随焙烧温度提高,催化剂活性逐渐下降,而产物分布也有很大变化.当焙烧温度较低时,深度氧化产物MAA 及完全氧化产物CO、CO2含量较多,MAL选择性较差;随焙烧温度逐渐提高至540℃左右,目标产物MAL选择性达到最大值;但随焙烧温度进一步提高,副产物乙醛、丙酮含量增多,MAL选择性又下降.催化剂性能的变化可能与表面活性位分离有关.3.3合适的催化剂焙烧条件为:焙烧温度520℃,焙烧时间5h,此时反应盐浴温度为375℃,反应转化率98.4%时,MAL选择性达到87.2%,具有较好的反应效果.参考文献:[1] Yang Hua(杨 华).Fine Che m ical Industrial Raw M a2terials&Inter m ediates(精细化工原料及中间体)[J],2006,(11):32~36[2] Hou Zhi2yang(侯志扬).Fine Che m ical Industrial RawM aterials&Inter m ediates(精细化工原料及中间体)[J],2008,(8):30~34[3] W ang Yu2r ong(王玉荣),Hu Zhi2xiang(胡志香).Che m ical Techno2Econo m ics(化工技术经济)[J],2005,23(2):14~19[4] L iM ing2xiu(李铭岫),Han Zhan2gang(韩占刚),YangShu2tao(杨述韬).J.M ol.Catal.(China)(分子催化)[J],2003,17(6):439~443[5] Yang Xue2p ing(杨学萍).Che m ical Industry and Engi2neering P rogress(化工进展)[J],2004,23(5):506~530[6] L i Q iang(李 强),W ang Lei(王 蕾),Yan Rui2yi(闫瑞一),et al.Che m ical Industry and Engineering(化学工业与工程)[J],2007,24(5):433~438[7] S ong N ian2xue,Rhodes Colin,K.Bartley Jonathan,etal.Journal of Catalysis[J],2005,(236):282~291 [8] Takeza wa,H ideyasu,Kur oda,et Patent[P]:6867163,2005,03~15[9] J Moens L,Ruiz P,Del m on B,et al.A ppl.Catal.A:General[J],1998,171(1):131~143[10]Guan J ing2qi,Song Ke,Xu Haiyan,et al.CatalysisCo mm unications[J],2009,(10):528~532[11]W ang Lei,L i Zeng2xi,Zhang Suo2jiang,et al.ChineseJ.Che m.Eng.[J],2005,13(5):705~708[12]Zhao Guo2sheng(赵国胜),Yang Bo2lun(杨伯伦),Yang Xiao2hui(杨小辉).Journal of Che m ical Engineer2ing of Chinese U niversities(高校化学工程学报)[J],2004,18(6):719~723[13]Sun Shi2lin(孙世林),L i J i2chun(李吉春),HuangJ ian2feng(黄剑峰).Gansu Science and Technology(甘肃科技)[J],2007,23(1):137~139[14]Cai Tie2jun(蔡铁军),Deng Q ian(邓 谦),HuangDeng2fa(黄德发),et al.Chinese J.Inorg.Che m(无机化学学报)[J],2002,18(6):602~606[15]Peng Zhen2shan,Yu Chan2lin,Cai Tie2jun,et al.Jour2nal of N atural Gas Che m istry[J],2004,13(3):172~655 分 子 催 化 第23卷 176[16]Cai Tie 2jun (蔡铁军),Yu Chang 2lin (余长林),DengQ ian (邓 谦),et al .Chin J Catal (催化学报)[J ],2003,24(12):951~956[17]Zhang Hai 2lang (张海朗),Tian W ei (田 伟).M odernChe m ical Industry (现代化工)[J ],2008,28(10):47~50[18]Yoshihiko M.A ppl .Catal .A:General [J ],1999,181(2):323~329[19]W ang Lei (王 蕾),L i Zeng 2xi (李增喜),Zhang Suo 2jiang (张锁江),et al .The Chinese Journal of Process Engineering (过程工程学报)[J ],2007,7(1):202~208[20]W ang Yang (汪 洋),Chen Feng 2qiu (陈丰秋),ZhanXiao 2li (詹晓力),et al .Progress in Che m istry (化学进展)[J ],2006,18(1):7~18[21]Bordes E .Topics in Catal .[J ],2001,15(224):131~137Effect of Calci n ati on Te mperature and Ti m e the Properti es ofCat alysts for the Parti a l Oxi dati on of Isobutylene to M ethacrole i nZHAO Xiao 2qi,LUO Ge,W E N Xin,ZHUANG Yan,CHU Xiao 2dong,SHAO J ing 2m ing(R esearch Institute of Shanghai Huayi A crylic A cid Co .L td,Shanghai 200137,China )Abstract:The composite oxides of Mo 2B i 2Co 2Fe 2Cs were synthesized by p reci p itati on method and app lied in the partial oxidati on of is obutylene t o methacr olein .The effect of calcinati on te mperature and ti m e on the physicoche m i 2cal p r operties of catalysts were studied by H 22TPR,XRD,BET,and TE M.It was found that,as the calcinati onte mperature increased,the structure of the catalyst changed slightly and the particle size increased gradually and synergy bet w een components weakened .W hen calcinated at 540℃,the catalyst particles were partially sintered .The catalytic activity decreased gradually with increasing calcinati on te mperature and methacr olein selectivity reached the maxi m u m value at 520℃.The effect of calcinati on te mperature on catalytic perf or mance could be at 2tributed t o the different density of surface active site .The p r oper calcinati on te mperature was suggested at 520℃and calcinati on ti m e was 5h .W ith this method,the is obutylene conversi on rate was 98.4%and selectivity t o MAL was 87.2%.Key words:Calcinati on te mperature;Calcinati on ti m e;Is obutylene;Methacr olein755第6期 赵小岐等:焙烧温度及焙烧时间对异丁烯部分氧化合成甲基丙烯醛催化剂性能的影响。
异辛酸生产工艺

异辛酸生产工艺
异辛酸是一种无色透明的液体,具有辛辣刺激的气味。它主要
用于制造塑料、涂料、油漆等工业产品。下面是关于异辛酸生
产工艺的简要介绍。
1. 原料准备:异戊二烯(C5H8)是异辛酸的主要原料。通过
裂解石脑油(一种石油副产品)或蒸馏石油类的混合物,可以
获得异戊二烯。其他辅助原料包括醇和酸。
2. 催化剂选择:生产异辛酸的关键是选择合适的催化剂。通常
采用酸性催化剂,如硫酸或磷酸。这些催化剂能够促进化学反
应,并提高产量和效率。
3. 反应过程:异辛酸的生产主要通过气相氧化反应进行。将异
戊二烯与氧气在催化剂的存在下进行反应,生成异辛酸。该反
应通常在高温和高压下进行,以提高反应速率和产量。
4. 分离和纯化:在反应结束后,需要对反应产物进行分离和纯
化。通过蒸馏和冷凝,可以将异辛酸从反应混合物中分离出来。
然后,通过进一步的处理,如结晶、洗涤和析出,可以提高异
辛酸的纯度。
5. 储存和包装:最后,异辛酸需要储存和包装。在储存过程中,
需要注意避免阳光直射和高温环境,以避免异辛酸的质量受损。
通常采用钢罐或塑料桶进行包装。
总的来说,异辛酸的生产工艺是一个复杂的过程,需要合适的
原料和催化剂,并在适当的条件下进行反应和分离纯化。这个
工艺需要高温、高压和精确的控制,以保证产品的质量和产量。
随着科技的不断进步,异辛酸的生产工艺也在不断改进和优化,
以提高效率和环保性。
磷酸二异辛酯生产工艺

磷酸二异辛酯生产工艺
磷酸二异辛酯是一种重要的有机化学品,广泛应用于合成润滑油、溶剂、塑料和橡胶等领域。
本文将介绍磷酸二异辛酯的生产工艺。
磷酸二异辛酯的生产工艺通常采用酯交换反应进行。
具体步骤如下:
将异辛醇与磷酸进行酯化反应,生成异辛醇磷酸酯。
该反应通常在反应釜中进行,反应温度控制在120-140摄氏度,反应时间为4-6小时。
在反应过程中,可以添加催化剂,如硫酸、磷酸或酸性离子交换树脂,以加速反应速度。
接下来,将异辛醇磷酸酯与异辛酸酯进行酯交换反应,生成磷酸二异辛酯。
该反应通常在反应釜中进行,反应温度控制在180-200摄氏度,反应时间为8-10小时。
在反应过程中,可以使用过量的异辛醇作为溶剂,以提高反应效率。
反应结束后,通过蒸馏和洗涤等步骤,将磷酸二异辛酯从反应混合物中分离出来。
通常采用真空蒸馏的方法,将磷酸二异辛酯从反应混合物中蒸馏出来,得到纯净的产物。
需要注意的是,在整个生产过程中,要确保反应条件的控制和催化剂的选择。
合理的反应温度和时间可以提高反应速率和产率,而适当的催化剂可以促进反应进行。
为了确保产品的质量,还需要对产物进行分析和检测。
常用的分析
方法包括气相色谱、液相色谱和质谱等。
通过这些分析方法,可以检测产品的纯度、杂质含量和组成等指标。
总结起来,磷酸二异辛酯的生产工艺主要包括酯交换反应和分离纯化两个步骤。
在实际生产中,需要合理选择反应条件和催化剂,并进行产品质量的监控和控制。
通过优化工艺参数和提高产品质量,可以实现磷酸二异辛酯的高效生产。
- 1、下载文档前请自行甄别文档内容的完整性,平台不提供额外的编辑、内容补充、找答案等附加服务。
- 2、"仅部分预览"的文档,不可在线预览部分如存在完整性等问题,可反馈申请退款(可完整预览的文档不适用该条件!)。
- 3、如文档侵犯您的权益,请联系客服反馈,我们会尽快为您处理(人工客服工作时间:9:00-18:30)。
2. 3 XRD结果 为了了解焙烧温度对催化剂物相结构有无影响, 对不同焙烧温度下的催化剂进行了 XRD 表征。由
图 1可见, 在所有样品中, 2 为 37. 4 , 46. 0 , 67. 0 位置显示为六方晶系 A l2O3特征谱图。对照标准谱图 发现 A l2 O3为 -A l2 O 3, 焙烧温度较低时, 其 XRD 谱峰宽化, 峰强较弱, 说明此时 A l2O 3晶粒细小, 晶形发育 不完整, 并且可能含有一定的非晶成分。随着焙烧温度的提高, A l2O 3衍射峰的峰型由宽变窄, 峰强由弱变 强。这说明 A l2O 3晶粒尺寸逐渐长大, 晶型逐渐趋于完好。在焙烧温度达到 1 000 时, 观察到刚玉的特 征峰, 部分的 A l2O3发生相变生成刚玉结构。不同焙烧温度的样品中都未观察到 ZnO 晶体的衍射峰, 表明 锌的氧化物可能具有良好的分散性, 并未生成大颗粒的晶体。另外, 在焙烧温度超过 500 时, 可以观察 到 ZnA l2O4尖晶石的特征峰 ( 2 = 31. 7 , 37. 0 ), 随着焙烧温度的升高, ZnA l2O4尖晶石的峰型逐渐尖锐。 这说明高温焙烧的催化剂上存在 ZnO 与载体 A l2O3间的相互作用, Zn2+ 进入载体表面的四面体或八面体 空位, 形成 ZnA l2 O4尖晶石物种。这种相互作用随着焙烧温度的提高而增强, 文献 [ 5, 6 ] 中报道过类似状况。 2. 4 SEM 结果
以发现, 600 焙烧的催化剂 A l2O3晶粒尺寸有所增大, 在 A l2O3晶体上覆盖着一层直径在 0. 3 nm 左右的 规则片状物。由于 -A l2O3为缺陷的尖晶石结构, 其择优暴露的 ( 110) 面上存在 2种晶格空位, 负载的金 属阳离子可以选择性的嵌入这些空位中, 形成尖晶石晶相。因此结合催化剂的 XRD 谱, 认为这些片状结 构是负载的 Zn进入 A l2 O3晶格后生成的 ZnA l2 O 4尖晶石。根据相关文献记载 [ 7- 10] , 尖晶石在多种氧化反 应中具有催化作用, 因此可以认为反应活性随着焙烧温度的提升与尖晶石结构的生成有密切的联系。图 2( c) 是 Zn /A l2O3 ( 800) 催化剂 SEM 图, 从图中可以看出, A l2O 3晶体碎裂成大小不一的颗粒, 催化剂在高 温焙烧下开始烧结, 但是仍然可以观察到部分片状的尖晶石结构。此时催化剂具有最高的催化活性, 表 明此时 Zn /A l2O3催化剂的烧结并不是影响催化活性的唯一因素。这与 BET 表征的结果一致。当焙烧温 度升高到 1 000 , 从图 2( d) 中可以观察到催化剂表面破碎程度加剧, 表面形成了更细碎的颗粒。结合
A /m2 g- 1 310. 9 337. 7 282. 5 200. 9 172. 9 145. 7 116. 5 70. 7
V / cm3 g- 1 0. 49 0. 58 0. 56 0. 57 0. 57 0. 56 0. 56 0. 53
d /nm 6. 16 6. 75 7. 63 10. 89 12. 57 14. 94 18. 59 29. 80
使催化剂比表面积下降, 催化活性降低。因此焙烧温
度 900 和 1 000 时催化剂比表面积较低, 烧结是
图 1 不同焙烧温度的催化剂的 XRD 谱
造成其在异 辛醇氧 化反 应中活 性降低 的主要 原因。 F ig. 1 XRD o f cata lysts ca lc ined at d ifferent tem pera tures
西 安科 技 大 学 学报
2011 年
1. 2 催化剂的表征 X射线粉末衍射 ( XRD) 测试仪器为日本理学公司的 D /m ax- 2400型转靶式 X- 射线衍射仪, 入射光
源为 Cu靶 K 射线, 入射波长为 0. 154 05 nm, 扫描范围选取 20~ 70 , 扫描速率 10 /m in. BET 比表面积 和孔结构在美国康塔的 AUTOSORB - 1自动吸附仪上测定, N2作吸附质。催化剂形貌表征采用日本电子 JEC - 1600扫描电镜 ( SEM ) 。 1. 3 催化剂的性能评价
X ( C8H18OH ) 24. 1 23. 4 21. 4 26. 3 30. 9 42. 4 30. 2 26. 6
Y ( C7H16COOH ) 8. 0 10. 6 11. 5 13. 8 14. 3
18. 14 15. 7 12. 3
S ( C7H16COOH ) 33. 2 45. 3 54. 8 54. 3 46. 3 2. 3 51. 9 46. 2
表 1 不同焙烧温度 ZnO /A l2O3催化剂的催化反应性能
Tab. 1 Reac tiv ity on the ZnO /A l2 O3 catalysts calcined a t d ifferent tem peratures
%
Sam p le ZnO / -A l2O 3 ( 300 ) ZnO / -A l2O 3 ( 400 ) ZnO / -A l2O 3 ( 500 ) ZnO / -A l2O 3 ( 600 ) ZnO / -A l2O 3 ( 700 ) ZnO / -A l2O 3 ( 800 ) ZnO / -A l2O 3 ( 900 ) ZnO / -A l2O 3 ( 1 000)
* 收稿日期: 2010- 11 - 25 基金项目: 国家自然科学基金项目 ( 20776118) ; 陕西省教育厅产业化培育项目 ( 07JC 19 ) 通讯作者: 赵彬侠 ( 1964 - ), 女, 陕西澄城人, 教授, 工学博士, 主要从事有机废水处理及有机中间体合成方面的研究.
20 6
图 2是经 400 和 800 焙烧制备的催化剂的 SEM 结果。从图 2( a) 可以看出, 400 焙烧的催化剂 表面为单一相的 A l2O 3晶体, 颗粒尺寸在 1~ 1. 5 nm 左右, 颗粒均匀, 无其他物相出现。而观察图 2( b)可
图 2 不同焙烧温度制备的 Zn /A l2O 3催化剂的 SEM 图 F ig. 2 SEM im ages o f Zn /A l2O 3 catalysts ca lc ined a t different tem peratures ( a) Zn /A l2O 3 ( 400 ) ( b) Zn /A l2O 3 ( 600) ( c) Zn /A l2O 3 ( 800 ) ( d) Zn /A l2O3 ( 1 000 )
结, 比较面积下降, 催化活性降低。
关键词: 异辛酸; 异辛醇; ZnO / -A l2O 3; 尖晶石; 负载型催化剂
中图分类号: O 643. 3
文献标志码: A
0前 言
醇的氧化是现阶段国内外有机合成领域中研究的热点问题 [ 1] , 该氧化过程无论是在精细化工、有机 合成或是在医药工业中都极为重要, 其中具有代表性的是将异辛醇氧化成异辛酸。异辛酸是一种用途广 泛的有机化工材料, 可用于涂料、塑料、制革、医药、化纤、农药等方面。异辛酸主要用做涂料催干剂, 它能 与多种金属发生反应生成异辛酸金属盐, 也可用做不饱和聚酯树脂促进剂、催化剂、塑料稳定剂等 [ 2] 。而 在传统的生产过程中, 国内厂家大多使用强氧化剂, 由于氧化剂自身的毒性和强腐蚀性导致在生产中存 在着诸多安全性问题。因此使用绿色、清洁的氧化剂, 如 O 2, H 2O 2, 符合当代化学发展的环保需要, 醇的 绿色氧化研究重点是在此类氧化剂作用条件下的催化氧化反应过程。如何在温和条件下, 使用对环境友 好, 且性能高、廉价、清洁、可回收的催化剂, 从上世纪 80年代至今一直是研究的焦点 [ 3] 。
2. 2 催化剂的 BET表征结果
表 2是不同温度焙烧的 ZnO / -A l2O3催化剂的氮 吸附测定结果。由表可见, 随着焙烧温度的 升高, 载
体的比表面积在 400 时先增大, 随后逐渐减小。孔
径随着焙烧 温度的 升高缓 慢增大, 在 焙烧温 度超过
800 时迅速增大。
一般情况下, 高温焙烧 很容易造成催 化剂烧结,
与 300~ 700 焙烧的催化剂相比, 800 焙烧的 ZnO / -A l2O3催化剂比表面积并不是最高的, 但是其催化 活性却最高, 说明除了比表面积外, 催化剂的表面结构也是影响催化剂活性的重要因素。这点将在下文
中讨论。
第 2期
路 程等: 焙烧温度对异辛醇生成异辛酸性能的影响
2 07
表 2 不同温度焙烧的催化剂的比表面积、孔体积和孔径 T ab. 2 Surface Area, pore vo lum e and pore d iam eter of cata lysts calc ined at d ifferen t temp era 升高焙烧温度, 使催化剂晶粒尺寸增大, 比较面积减小; Zn进
入载体 A l2 O3的晶格形成 ZnA l2 O4尖晶石晶相, 其与催化剂的活性密切相关。催化剂活性随着焙 烧温度升高而增强, 焙烧温度 800 , 催化剂具有最佳催化性能。当焙烧温度继续升高, 催化剂烧
在三口瓶中进行异辛醇氧化反应。向瓶中加入 50 m l异辛醇, 2 g催化剂。在回流冷凝条件下加热至 指定温度, 通入氧气, 并在搅拌条件下恒温反应 7 h. 将反应产物用 GC900A 气相色谱进行检测 ( SE - 30毛 细管色谱柱, 柱箱温度 230 )。
2 结果与讨论
2. 1 不同焙烧温度催化剂的反应性能 表 1给出了加入不同 ZnO / -A l2O3 ( t ) 催化剂的异辛醇转化率、异辛酸收率和选择性。由表可见, 在