循环流化床煤气化工艺的原理和特点
我国循环流化床煤气化技术工艺研究现状
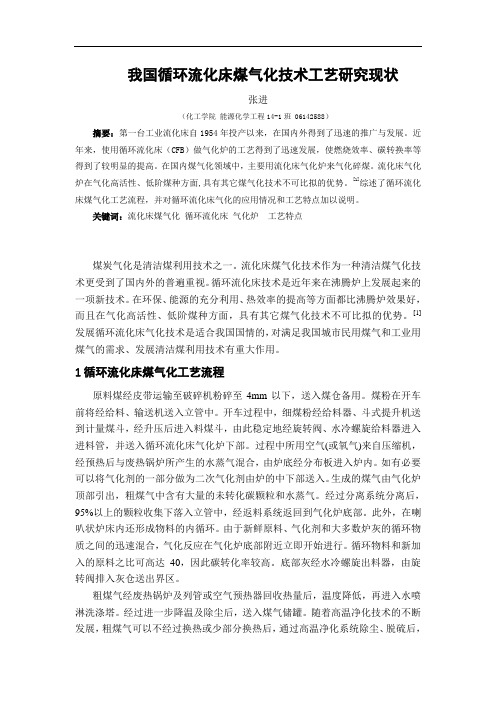
我国循环流化床煤气化技术工艺研究现状张进(化工学院能源化学工程14-1班 06142588)摘要:第一台工业流化床自1954年投产以来,在国内外得到了迅速的推广与发展。
近年来,使用循环流化床(CFB)做气化炉的工艺得到了迅速发展,使燃烧效率、碳转换率等得到了较明显的提高。
在国内煤气化领域中,主要用流化床气化炉来气化碎煤。
流化床气化炉在气化高活性、低阶煤种方面,具有其它煤气化技术不可比拟的优势。
[1]综述了循环流化床煤气化工艺流程,并对循环流化床气化的应用情况和工艺特点加以说明。
关键词:流化床煤气化循环流化床气化炉工艺特点煤炭气化是清洁煤利用技术之一。
流化床煤气化技术作为一种清洁煤气化技术更受到了国内外的普遍重视。
循环流化床技术是近年来在沸腾炉上发展起来的一项新技术。
在环保、能源的充分利用、热效率的提高等方面都比沸腾炉效果好,而且在气化高活性、低阶煤种方面,具有其它煤气化技术不可比拟的优势。
[1]发展循环流化床气化技术是适合我国国情的,对满足我国城市民用煤气和工业用煤气的需求、发展清洁煤利用技术有重大作用。
1循环流化床煤气化工艺流程原料煤经皮带运输至破碎机粉碎至4mm以下,送入煤仓备用。
煤粉在开车前将经给料、输送机送入立管中。
开车过程中,细煤粉经给料器、斗式提升机送到计量煤斗,经升压后进入料煤斗,由此稳定地经旋转阀、水冷螺旋给料器进入进料管,并送入循环流化床气化炉下部。
过程中所用空气(或氧气)来自压缩机,经预热后与废热锅炉所产生的水蒸气混合,由炉底经分布板进入炉内。
如有必要可以将气化剂的一部分做为二次气化剂由炉的中下部送入。
生成的煤气由气化炉顶部引出,粗煤气中含有大量的未转化碳颗粒和水蒸气。
经过分离系统分离后,95%以上的颗粒收集下落入立管中,经返料系统返回到气化炉底部。
此外,在喇叭状炉床内还形成物料的内循环。
由于新鲜原料、气化剂和大多数炉灰的循环物质之间的迅速混合,气化反应在气化炉底部附近立即开始进行。
循环流化床原理及运行

循环流化床原理及运行循环流化床主要由床体、循环器、气固分离器、换热器以及气体和固体的供给与排出系统等组成。
其工作原理是将气体和粗颗粒固体以较高的速度由床体底部引入,通过气固的强烈的接触,将反应所需的物质传递至固体表面,然后通过气体与粗颗粒固体的分离器将固体从气体中分离出来,然后再将固体颗粒经过循环器回流至床底,形成循环。
在循环流化床中,床体内的固体颗粒会被流化空气携带起来,在床体内形成一种类似于流体的状态。
床体中的气体通过气体分布板均匀地从底部引入,在床内形成均匀的气流。
当气体通过床体时,由于流体动力学的特性,固体颗粒被悬浮在气体中,形成浮动着的连续相。
在这种状态下,气体与颗粒之间的传质和传热效率大大提高,从而增加了反应的速率和效率。
循环流化床的运行过程可以分为固体颗粒的循环和气体的循环两个主要步骤。
在固体颗粒的循环过程中,气体通过固体颗粒床体将颗粒携带起来,并从循环器中回流至床底。
循环器中的固体颗粒经过多级分离装置的分离后,被分为两部分,一部分再次回流到床底,一部分从床体上部排出。
这样不断循环地将固体颗粒带到床体中,使床体保持一定的固体浓度。
在气体的循环过程中,气体从床体底部引入床体,通过床体上升,经过一定的高度后,在床上部进入气固分离器。
在气固分离器中,气体与固体颗粒进行分离,固体颗粒沉降至底部,而气体则从顶部排出。
排出的气体可根据需要进行再利用或者进行后续处理。
循环流化床具有很好的传质和传热性能,能够有效地控制反应的温度和反应速率。
由于固体颗粒的循环,床内固体颗粒的平均停留时间较短,减少了固体颗粒的积聚和结焦现象,延长了固体颗粒的寿命。
此外,循环流化床还具有较好的反应均匀性和操作灵活性,可广泛应用于化工、冶金、环保等领域。
总之,循环流化床通过将气体和固体颗粒进行高速流化,形成浮动着的连续相,以此来完成气体固体反应。
其原理是通过气体与固体颗粒之间的强烈接触和传质传热效果,实现反应的高效率和高速率。
循环流化床煤气化工艺的原理和特点
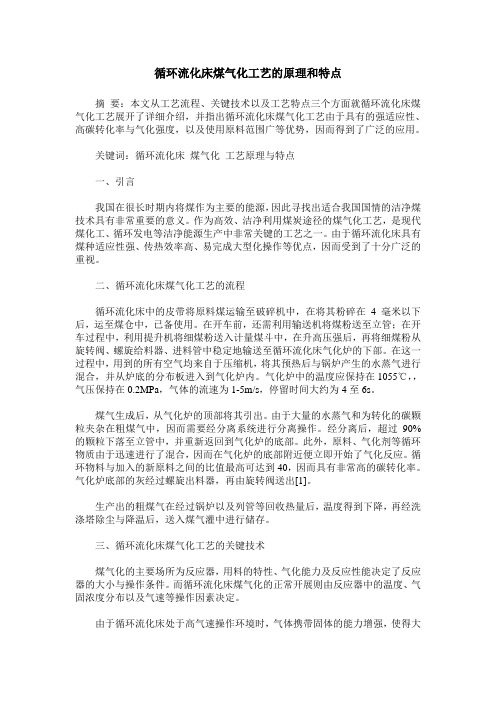
循环流化床煤气化工艺的原理和特点摘要:本文从工艺流程、关键技术以及工艺特点三个方面就循环流化床煤气化工艺展开了详细介绍,并指出循环流化床煤气化工艺由于具有的强适应性、高碳转化率与气化强度,以及使用原料范围广等优势,因而得到了广泛的应用。
关键词:循环流化床煤气化工艺原理与特点一、引言我国在很长时期内将煤作为主要的能源,因此寻找出适合我国国情的洁净煤技术具有非常重要的意义。
作为高效、洁净利用煤炭途径的煤气化工艺,是现代煤化工、循环发电等洁净能源生产中非常关键的工艺之一。
由于循环流化床具有煤种适应性强、传热效率高、易完成大型化操作等优点,因而受到了十分广泛的重视。
二、循环流化床煤气化工艺的流程循环流化床中的皮带将原料煤运输至破碎机中,在将其粉碎在4毫米以下后,运至煤仓中,已备使用。
在开车前,还需利用输送机将煤粉送至立管;在开车过程中,利用提升机将细煤粉送入计量煤斗中,在升高压强后,再将细煤粉从旋转阀、螺旋给料器、进料管中稳定地输送至循环流化床气化炉的下部。
在这一过程中,用到的所有空气均来自于压缩机,将其预热后与锅炉产生的水蒸气进行混合,并从炉底的分布板进入到气化炉内。
气化炉中的温度应保持在1055℃,,气压保持在0.2MPa,气体的流速为1-5m/s,停留时间大约为4至6s。
煤气生成后,从气化炉的顶部将其引出。
由于大量的水蒸气和为转化的碳颗粒夹杂在粗煤气中,因而需要经分离系统进行分离操作。
经分离后,超过90%的颗粒下落至立管中,并重新返回到气化炉的底部。
此外,原料、气化剂等循环物质由于迅速进行了混合,因而在气化炉的底部附近便立即开始了气化反应。
循环物料与加入的新原料之间的比值最高可达到40,因而具有非常高的碳转化率。
气化炉底部的灰经过螺旋出料器,再由旋转阀送出[1]。
生产出的粗煤气在经过锅炉以及列管等回收热量后,温度得到下降,再经洗涤塔除尘与降温后,送入煤气灌中进行储存。
三、循环流化床煤气化工艺的关键技术煤气化的主要场所为反应器,用料的特性、气化能力及反应性能决定了反应器的大小与操作条件。
循环流化床锅炉的工作原理
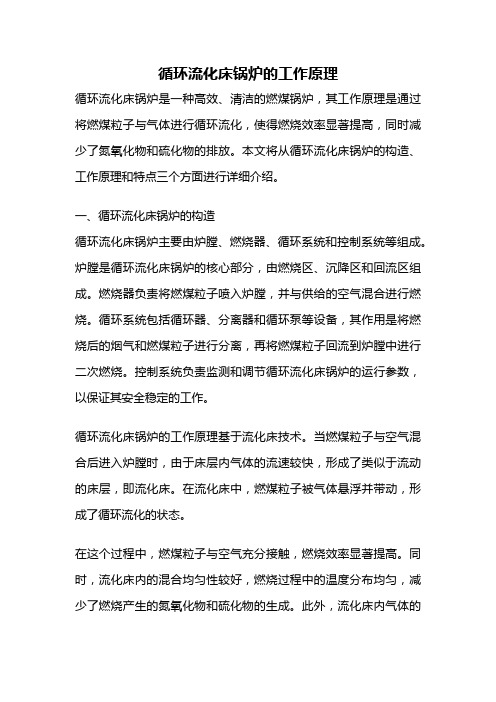
循环流化床锅炉的工作原理循环流化床锅炉是一种高效、清洁的燃煤锅炉,其工作原理是通过将燃煤粒子与气体进行循环流化,使得燃烧效率显著提高,同时减少了氮氧化物和硫化物的排放。
本文将从循环流化床锅炉的构造、工作原理和特点三个方面进行详细介绍。
一、循环流化床锅炉的构造循环流化床锅炉主要由炉膛、燃烧器、循环系统和控制系统等组成。
炉膛是循环流化床锅炉的核心部分,由燃烧区、沉降区和回流区组成。
燃烧器负责将燃煤粒子喷入炉膛,并与供给的空气混合进行燃烧。
循环系统包括循环器、分离器和循环泵等设备,其作用是将燃烧后的烟气和燃煤粒子进行分离,再将燃煤粒子回流到炉膛中进行二次燃烧。
控制系统负责监测和调节循环流化床锅炉的运行参数,以保证其安全稳定的工作。
循环流化床锅炉的工作原理基于流化床技术。
当燃煤粒子与空气混合后进入炉膛时,由于床层内气体的流速较快,形成了类似于流动的床层,即流化床。
在流化床中,燃煤粒子被气体悬浮并带动,形成了循环流化的状态。
在这个过程中,燃煤粒子与空气充分接触,燃烧效率显著提高。
同时,流化床内的混合均匀性较好,燃烧过程中的温度分布均匀,减少了燃烧产生的氮氧化物和硫化物的生成。
此外,流化床内气体的流动还能带走燃烧过程中产生的烟尘,减少了烟尘的排放。
循环流化床锅炉采用循环系统将燃煤粒子回流到炉膛中进行二次燃烧。
在循环器中,燃煤粒子和一部分未燃烧的烟气被分离,未燃烧的烟气经过回流再次参与燃烧,提高了燃烧效率。
经过多次循环后,燃煤粒子中的可燃物质基本被燃烧完全,烟气中的污染物排放得到有效控制。
三、循环流化床锅炉的特点循环流化床锅炉具有以下几个特点:1. 高效节能:循环流化床锅炉采用了循环燃烧技术,燃烧效率高,热效率通常可达到90%以上,节能效果显著。
2. 环保低排放:循环流化床锅炉采用了流化床技术,燃烧过程中的氮氧化物和硫化物排放量较低,符合环保要求。
3. 燃料适应性强:循环流化床锅炉对燃料适应性较强,可燃烧煤炭、生物质、废弃物等多种燃料,灵活性高。
流化床原理及特点
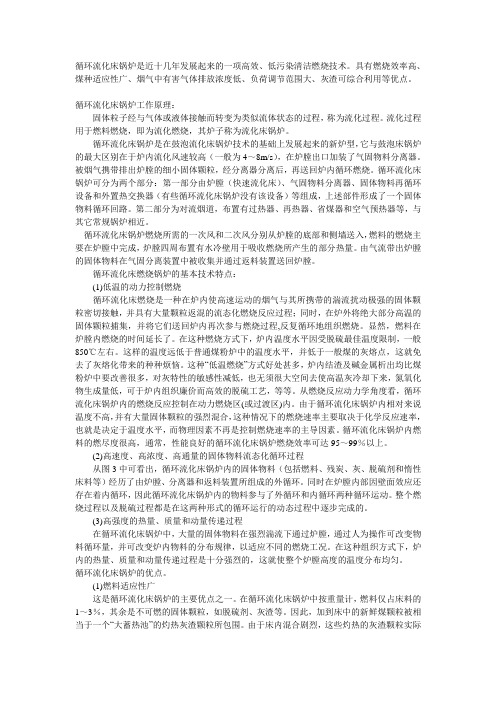
循环流化床锅炉是近十几年发展起来的一项高效、低污染清洁燃烧技术。
具有燃烧效率高、煤种适应性广、烟气中有害气体排放浓度低、负荷调节范围大、灰渣可综合利用等优点。
循环流化床锅炉工作原理:固体粒子经与气体或液体接触而转变为类似流体状态的过程,称为流化过程。
流化过程用于燃料燃烧,即为流化燃烧,其炉子称为流化床锅炉。
循环流化床锅炉是在鼓泡流化床锅炉技术的基础上发展起来的新炉型,它与鼓泡床锅炉的最大区别在于炉内流化风速较高(一般为4~8m/s),在炉膛出口加装了气固物料分离器。
被烟气携带排出炉膛的细小固体颗粒,经分离器分离后,再送回炉内循环燃烧。
循环流化床锅炉可分为两个部分:第一部分由炉膛(快速流化床)、气固物料分离器、固体物料再循环设备和外置热交换器(有些循环流化床锅炉没有该设备)等组成,上述部件形成了一个固体物料循环回路。
第二部分为对流烟道,布置有过热器、再热器、省煤器和空气预热器等,与其它常规锅炉相近。
循环流化床锅炉燃烧所需的一次风和二次风分别从炉膛的底部和侧墙送入,燃料的燃烧主要在炉膛中完成,炉膛四周布置有水冷壁用于吸收燃烧所产生的部分热量。
由气流带出炉膛的固体物料在气固分离装置中被收集并通过返料装置送回炉膛。
循环流化床燃烧锅炉的基本技术特点:(1)低温的动力控制燃烧循环流化床燃烧是一种在炉内使高速运动的烟气与其所携带的湍流扰动极强的固体颗粒密切接触,并具有大量颗粒返混的流态化燃烧反应过程;同时,在炉外将绝大部分高温的固体颗粒捕集,并将它们送回炉内再次参与燃烧过程,反复循环地组织燃烧。
显然,燃料在炉膛内燃烧的时间延长了。
在这种燃烧方式下,炉内温度水平因受脱硫最佳温度限制,一般850℃左右。
这样的温度远低于普通煤粉炉中的温度水平,并低于一般煤的灰熔点,这就免去了灰熔化带来的种种烦恼。
这种“低温燃烧”方式好处甚多,炉内结渣及碱金属析出均比煤粉炉中要改善很多,对灰特性的敏感性减低,也无须很大空间去使高温灰冷却下来,氮氧化物生成量低,可于炉内组织廉价而高效的脱硫工艺,等等。
循环流化床纯氧气化技术介绍

工 程 示 范 及 推 广
0.25 t/d(2008)
2.5 t/d(2008)
5 t/d(2012)
17
5t/d循环流化床富氧/纯氧气化中试试验研究
试验台简介: 2012年建成 炉膛高度:17m 炉膛直径:450mm
运行特性: 给煤量:4~7t/d 运行煤种:褐煤、烟煤、弱粘结性煤 累计运行:近500小时
项目
循环流化床煤气炉
煤气热值(kcal/Nm3)
1350
煤气产量(Nm3/h)
40000
耗煤量(kg/h)
~14.5
酚水量(kg/h)
0
焦油量(kg/h)
0
固体废物(kg/h)
~2650
噪声(dBA)
<75
两段式煤气炉 1500
6×6000 ~14.5 3730 4970 ~1350 <100
本技术与两段炉相比,没有焦油酚水排放,劳动环境明显改善 13
净化工业燃气,1150kcal/Nm3
江苏宿迁项目: 2X25000Nm3/h 工艺特点:粉煤原料生产回转窑冶炼加 热过程的热荒煤气 煤处理量: 240t/d,气化炉内径3.2 m
2013年8月投入商业运行,满负荷运行
热荒煤气,低位热值1150-1250kcal/Nm3
8
技术示范
信发华宇40000Nm3/h项目
阶段 Ⅰ Ⅱ Ⅲ Ⅳ Ⅴ VI
名称 点火启动 燃烧升温及蓄热 富氧气化规律探索 富氧气化试验 分级配风试验 返料器给煤试验
运行时间 9小时50分钟
41小时 19小时40分钟 6小时25分钟 22小时30分钟 1小时40分钟
20
试验全过程温度曲线
循环流化床燃烧原理

循环流化床燃烧原理
循环流化床燃烧是一种高效的燃烧技术,其原理是将燃料和空气在一定的条件下混合,形成细小的颗粒状物质,在循环流化床内进行燃烧。
循环流化床燃烧技术具有高效、低污染、可适应性强等优点,被广泛应用于煤炭、生物质等领域。
其原理主要包括以下几个方面:首先,循环流化床内的流体化气固两相流动状态可以保证燃料和空气充分混合,从而提高燃烧效率,减少污染物的排放。
其次,循环流化床内的床层温度均匀,可以有效防止燃烧温度过高或过低,从而保证燃烧过程的稳定性和安全性。
再次,循环流化床内的燃料和物料可以高度循环利用,节约能源,减少燃料消耗和废弃物的产生,有利于环境保护和可持续发展。
最后,循环流化床燃烧技术具有较强的适应性,可以适用于不同类型的燃料,如煤炭、生物质等,提高了其应用范围和实用性。
总之,循环流化床燃烧技术是一种高效、低污染、可持续的燃烧技术,具有广泛的应用前景。
- 1 -。
黄台炉循环流化床气化技术

黄台炉循环流化床气化技术全文共四篇示例,供读者参考第一篇示例:黄台炉循环流化床气化技术是一种先进的生物质能源利用技术,通过在高温、高压和氧气不足的条件下将生物质材料进行气化,将其转化为合成气,进而产生燃烧或发电所需的能源。
这项技术不仅可以有效利用生物质资源,减少环境污染,还有助于实现能源的可持续利用。
流化床气化技术是指在一定的流化速度下,通过对气化床中的颗粒物料进行搅拌和混合,使之形成类似于流体的状态,从而提高反应速率和热传导效果。
而黄台炉循环流化床气化技术则在这一基础上进一步实现了气化床内部气态组分的混合均匀和循环往复运动,从而提高了气化效率和产气质量。
黄台炉循环流化床气化技术具有以下几个显著特点:一、高效节能:循环流化床技术可以有效地减少废气和废热的排放,实现废热再利用,提高能源利用效率。
而且由于气化反应在高温、高压和氧气不足条件下进行,可以最大化地保留生物质原料中的碳元素,减少能源消耗。
二、资源综合利用:循环流化床气化技术可以利用多种生物质资源进行气化,如秸秆、木屑、废弃物等,实现资源的综合利用。
废弃物气化后可以产生高温热能、合成气等多种产品,实现废物资源化的目的。
三、环保节能:流化床气化技术采用循环流化床反应器,反应温度高、气氛调控好,能减少有害气体和颗粒物的排放,减轻对大气和环境的污染。
废热回收和再利用也有助于节能减排。
四、灵活可控:黄台炉循环流化床气化技术具有较强的操作灵活性和反应可控性,可以根据不同的生物质原料和气化条件,来调节反应器内的气气、气溶胶和颗粒物的混合均匀,以及产气量和气化效率。
五、成本优势:循环流化床气化技术相对于传统燃煤气化技术而言,设备投资、运行成本和维护费用都更低廉,利用寿命更长,更经济实用。
因此在生物质能源产业中有着广泛的应用前景。
黄台炉循环流化床气化技术是一项具有巨大潜力和发展前景的能源转化技术,可以有效推动生物质资源的利用,减少环境污染,实现绿色和可持续发展。
- 1、下载文档前请自行甄别文档内容的完整性,平台不提供额外的编辑、内容补充、找答案等附加服务。
- 2、"仅部分预览"的文档,不可在线预览部分如存在完整性等问题,可反馈申请退款(可完整预览的文档不适用该条件!)。
- 3、如文档侵犯您的权益,请联系客服反馈,我们会尽快为您处理(人工客服工作时间:9:00-18:30)。
循环流化床煤气化工艺的原理和特点
摘要:本文从工艺流程、关键技术以及工艺特点三个方面就循环流化床煤气化工艺展开了详细介绍,并指出循环流化床煤气化工艺由于具有的强适应性、高碳转化率与气化强度,以及使用原料范围广等优势,因而得到了广泛的应用。
关键词:循环流化床煤气化工艺原理与特点
一、引言
我国在很长时期内将煤作为主要的能源,因此寻找出适合我国国情的洁净煤技术具有非常重要的意义。
作为高效、洁净利用煤炭途径的煤气化工艺,是现代煤化工、循环发电等洁净能源生产中非常关键的工艺之一。
由于循环流化床具有煤种适应性强、传热效率高、易完成大型化操作等优点,因而受到了十分广泛的重视。
二、循环流化床煤气化工艺的流程
循环流化床中的皮带将原料煤运输至破碎机中,在将其粉碎在4毫米以下后,运至煤仓中,已备使用。
在开车前,还需利用输送机将煤粉送至立管;在开车过程中,利用提升机将细煤粉送入计量煤斗中,在升高压强后,再将细煤粉从旋转阀、螺旋给料器、进料管中稳定地输送至循环流化床气化炉的下部。
在这一过程中,用到的所有空气均来自于压缩机,将其预热后与锅炉产生的水蒸气进行混合,并从炉底的分布板进入到气化炉内。
气化炉中的温度应保持在1055℃,,气压保持在0.2MPa,气体的流速为1-5m/s,停留时间大约为4至6s。
煤气生成后,从气化炉的顶部将其引出。
由于大量的水蒸气和为转化的碳颗粒夹杂在粗煤气中,因而需要经分离系统进行分离操作。
经分离后,超过90%的颗粒下落至立管中,并重新返回到气化炉的底部。
此外,原料、气化剂等循环物质由于迅速进行了混合,因而在气化炉的底部附近便立即开始了气化反应。
循环物料与加入的新原料之间的比值最高可达到40,因而具有非常高的碳转化率。
气化炉底部的灰经过螺旋出料器,再由旋转阀送出[1]。
生产出的粗煤气在经过锅炉以及列管等回收热量后,温度得到下降,再经洗涤塔除尘与降温后,送入煤气灌中进行储存。
三、循环流化床煤气化工艺的关键技术
煤气化的主要场所为反应器,用料的特性、气化能力及反应性能决定了反应器的大小与操作条件。
而循环流化床煤气化的正常开展则由反应器中的温度、气固浓度分布以及气速等操作因素决定。
由于循环流化床处于高气速操作环境时,气体携带固体的能力增强,使得大
量的固体被带出了反应器,因此必须安装相关的气固装置与返料装置对固体进行收集与返回。
循环流化床的气固分离装置一般伴有高温惯性分离器与高温旋风分离器,采用多级分离的方式。
固体颗粒的循环则依靠返料装置实现,立管与返料阀为返料装置的组成部分,立管主要防止气流出现反窜的现象,而返料阀则对固体颗粒的流动起着开闭及调节的作用。
立管的封闭状态、返料的性能,以及反应器床内压的波动情况等与返料阀运行的稳定性、立管的设计与操作情况等有着紧密联系[2]。
四、循环流化床煤气化工艺具有的特点
1.具有非常强的煤种适应性
循环流化床气化炉适用于各种类型的固体燃料,同时也适用于气体或液体燃料。
准备原料的过程非常简单,只需将煤粉碎至6毫米以下,将生物体及木材等切碎至40毫米以下即可。
因此可以不用将碎粉煤加工至成型快或是细粉状,便可直接进行使用,不但将准备煤的工序简单化,而且大大降低了投资成本,非常适合于煤炭机械化的开采水平。
2.气化强度高
在循环流化床气化炉中加入的原料煤占床层内很小比例的物料量,而且与气化剂、高温的颗粒能迅速发生完全混合。
此外,由于传质与传热条件良好,因而新加入的常温原料能在短时间内达到气化所需的温度,再加上床内聚集着大量起着载热体作用的流化固体物料,因而充分解决了因局部高温导致的结渣问题。
循环流化床在接近灰熔聚高温的条件下依然可以进行正常操作,且整个床层均处于高温气化的状态,因而相比于一般的鼓泡流化床,其气化强度超出了2-3倍。
同时,单位面积具有较高的气体流通量,设备及原料的利用率均较高,生产能力大,因而具有低投资、低耗能、低维修费用的优点。
3.原料碳的转化率高
在循环流化床不同的高度均可加入反应的气体,并通过循环回收将细粉带出,从而增加了颗粒在流化床内的反应时间。
循环流化床不但具有外循环,而且具有内循环,位于床中心区域颗粒的运动方向向上,而位于边壁处物料的运动方向则向下。
由于循环的比值最高可达几十倍,因而原料碳的转换率得到了极大程度的提高,有效避免了常规流化床气化炉中,因排出的煤气及灰渣带出原料碳,造成损失的问题。
4.强化了工艺传热与传质的性能
循环流化床内不存在气泡,具有良好的气固接触性能,气相速度明显高于固相速度,且两相之间具有非常大的相对滑动速度实现了煤气化工艺传热、传质性能的强化。
由于具有相近的组成,容易建立科学合理的浓度梯度与温度梯度,有效克服了一般鼓泡流化床中,因存在大量的气泡导致气固相出现不良接触,传热、
传质等受到阻碍,以及床中出现严重气固相返混的不足之处[3]。
5.具有良好的环保效益
循环流化床的煤气中,含有非常少的氨、氰、焦油等有害物质,且产生的废水容易处理。
操作人员可将固硫剂加入炉料中,从而发挥出非常好的脱硫效果。
此外,发生气化反应的温度比较低,通常在850℃-1100℃之前,可有效抑制氧化氮的生成。
灰渣在低温状态下进行燃烧具有良好的化学活性,掺烧石灰石能有效增加灰渣中石膏的含量。
因此,产生的干灰渣可用作轻质混凝土,以及硅酸盐水泥的熟料等建筑材料。
五、结语
综上可知,常压循环流化床煤气化工艺由于具有的强适应性、高碳转化率与气化强度,以及使用原料范围广等优势,因而在全世界范围内得到了高度的重视。
从理论与实际应用角度出发,循环流化床技术在煤气化方面具有独特的优势,相信通过深入的开发和研究,此项工艺技术一定会在工业生产中发挥着越来越重要的作用。
参考文献:
[1]屈利娟.流化床煤气化技术的研究进展[J].煤炭转化,2012,10(02):265-266.
[2]房倚天,李海滨,张建民,等.循环流化床技术在煤气化过程中的应用前景[J].煤化工,2013,12(04):235-237.
[3]王洋,房倚天,马小云,等.煤气化技术的发展——煤气化过程的分析和选择[J].东莞理工学院学报,2011,8(04):623-625.。